步进电机驱动方法的比较
电机驱动技术在机器人运动控制中的应用

电机驱动技术在机器人运动控制中的应用机器人技术的发展已经成为现代制造业的重要支柱。
而机器人的运动控制是使其得以实现各类任务的基础,而电机驱动技术作为机器人运动控制的核心,扮演着重要的角色。
本文将从电机驱动技术在机器人运动控制中的应用方面进行探讨。
一、直流电机驱动直流电机是机器人运动控制中常用的电机类型之一,具有结构简单、控制方便等优点。
在机器人的关节控制中,直流电机驱动技术被广泛应用。
通过改变电压和电流的控制方式,可以实现对直流电机转速和转向的精确调控。
同时,使用PID控制算法可以实现位置和速度的闭环控制,提高机器人关节运动的准确性和稳定性。
在机器人的整体运动控制中,直流电机驱动技术也扮演着重要的角色。
通过多个关节的协调运动,机器人可以实现复杂的动作,如抓取、搬运等。
直流电机的速度和位置控制技术可以精确控制机器人的运动轨迹和速度,确保机器人在执行任务时的准确性和安全性。
二、步进电机驱动步进电机是机器人运动控制中另一个常用的电机类型。
相比于直流电机,步进电机具有低成本、高转矩、易于控制等优点。
步进电机的驱动原理是通过依次通入电流来控制电机的旋转角度。
在机器人中,步进电机常用于实现机器人末端执行器的控制,如机械臂的运动控制、舵机的旋转控制等。
步进电机可以通过改变脉冲信号的频率和方向来精确控制电机的旋转角度,实现机器人末端执行器的位置控制。
三、伺服电机驱动伺服电机是机器人运动控制中更为高级的电机类型。
伺服电机结合了直流电机和位置反馈系统,可以实现更为精确的位置和速度控制。
伺服电机驱动技术在机器人中被广泛应用于各类高精度任务。
伺服电机的驱动需要借助编码器等位置反馈设备,将电机的实际位置反馈给控制系统,通过比较实际位置和期望位置来驱动电机实现精确的位置控制。
同时,伺服电机还可以通过增加轴向刚度和控制参数的调整来实现更高级的控制需求,如抗干扰性、运动平滑性等。
结语电机驱动技术在机器人运动控制中起着至关重要的作用。
步进电机的驱动参数设置

步进电机的驱动参数设置1.设置步进驱动器的细分数,通常细分数越高,控制分辨率越高。
但细分数太高则影响到最大进给速度。
一般来说,对于模具机用户可考虑脉冲当量为0.001mm/P(此时最大进给速度为9600mm/min)或者0.0005mm/P(此时最大进给速度为4800mm/min);对于精度要求不高的用户,脉冲当量可设置的大一些,如0.002mm/P(此时最大进给速度为19200mm/min)或0.005mm/P(此时最大进给速度为48000mm/min)。
对于两相步进电机,脉冲当量计算方法如下:脉冲当量=丝杠螺距÷细分数÷200。
2.起跳速度:该参数对应步进电机的起跳频率。
所谓起跳频率是步进电机不经过加速,能够直接启动工作的最高频率。
合理地选取该参数能够提高加工效率,并且能避开步进电机运动特性不好的低速段;但是如果该参数选取大了,就会造成闷车,所以一定要留有余量。
在电机的出厂参数中,一般包含起跳频率参数。
但是在机床装配好后,该值可能发生变化,一般要下降,特别是在做带负载运动时。
所以,该设定参数最好是在参考电机出厂参数后,再实际测量决定。
.单轴加速度:用以描述单个进给轴的加减速能力,单位是毫米/秒平方。
这个指标由机床的物理特性决定,如运动部分的质量、进给电机的扭矩、阻力、切削负载等。
这个值越大,在运动过程中花在加减速过程中的时间越小,效率越高。
通常,对于步进电机,该值在100 ~ 500之间,对于伺服电机系统,可以设置在400 ~ 1200之间。
在设置过程中,开始设置小一点,运行一段时间,重复做各种典型运动,注意观察,如果没有异常情况,然后逐步增加。
如果发现异常情况,则降低该值,并留50%~100%的保险余量。
4.弯道加速度:用以描述多个进给轴联动时的加减速能力,单位是毫米/秒平方。
它决定了机床在做圆弧运动时的最高速度。
这个值越大,机床在做圆弧运动时的最大允许速度越大。
通常,对于步进电机系统组成的机床,该值在400~1000之间,对于伺服电机系统,可以设置在1000 ~ 5000之间。
几种步进电机的驱动方式

步进电机常见的三种驱动方式包括全步进驱动、半步进驱动和微步进驱动。
全步进驱动简单易实现,适用于对转矩要求不高的场合;半步进驱动具有更高的分辨率和更平滑的运动,适用于对定位要求较高的场合;微步进驱动则是最精细的驱动方式,通过控制电流的大小和方向实现步进电机的转动,适用于对定位精度要求极高的场合。
选择适当的驱动方式需要根据具体应用需求来决定。
全步进驱动简单、成本低,适用于一些普通的工业自动化应用;半步进驱动在精确性和平稳性方面提供了更好的性能,适用于精密定位的应用;而微步进驱动则可以提供最高的分辨率和最平滑的运动,适用于高精密仪器和光学设备等领域。
全步进驱动是最常见的步进电机驱动方式之一。
它通过改变电流的方向和大小来实现步进电机的转动。
具体工作原理如下:1.单相全步进驱动:在单相全步进驱动中,通过向两个相邻线圈施加电流,使得步进电机转动一个步进角度。
该驱动方式简单易实现,但转矩较小。
2.双相全步进驱动:双相全步进驱动是一种更为常见的驱动方式。
它通过按照特定的顺序向两个线圈施加电流来实现步进电机的转动。
该驱动方式相比单相全步进驱动具有更高的转矩和更稳定的运行。
全步进驱动方式简单直观,适用于对转矩要求不高的场合。
2.半步进驱动半步进驱动是介于全步进驱动和微步进驱动之间的一种驱动方式。
在半步进驱动中,通过改变电流的方向和大小来实现步进电机的转动。
具体工作原理如下:1.与全步进驱动类似,半步进驱动也可以采用单相和双相两种驱动方式。
其中,双相半步进驱动是最常见的。
2.在双相半步进驱动中,首先向一个线圈施加电流,使得步进电机转动半个步进角度。
然后再向另一个线圈施加电流,使得步进电机再次转动半个步进角度。
通过交替改变电流的方向和大小,可以实现精确的定位。
半步进驱动方式相比全步进驱动方式,具有更高的分辨率和更平滑的运动。
适用于对定位要求较高的场合。
3.微步进驱动微步进驱动是步进电机中最精细的驱动方式,通过分段控制电流的大小和方向来实现步进电机的转动。
电机驱动电路模块(交、直流)-2016.8
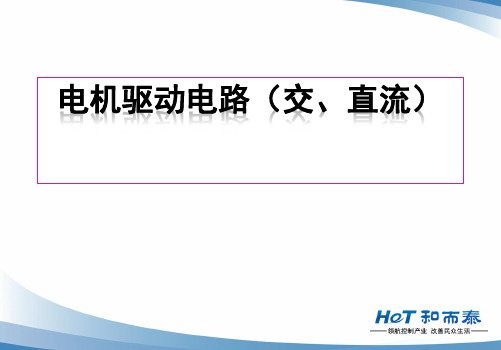
注: 以上相线顺序根据不同厂家、不同规格可以是不同的,具体请参阅相 应型号的规格书。
35BYJ46 主要几个技术要求:
1. 额定电压:12VDC 2. 直流电阻:130欧±7%(25 ℃ ) 3. 驱动方式:四相八拍(即A,B,C,D四根相线) 4. 减速比:1/85 5. 步距角: 7.5 °/85(每一拍角度值) 6. 自定位转矩>=600gf.cm 7. 牵入转矩: >=1500gf.cm(100HZ) 等等;
目录(目前我司常用的几大类): 一、步进电机 二、直流电机
三、PG交流电机(PID算法)
一、步进电机介绍:步进电机是将电脉冲信号转变为角位移或线位移的开环控制元件。在非
超载的情况下,电机的转速、停止的位置只取决于脉冲信号的频率和脉冲数,而不受负载变化的影响, 当步进驱动器接收到一个脉冲信号,它就驱动步进电机按设定的方向转动一个固定的角度,称为"步距角 ",它的旋转是以固定的角度一步一步运行的。可以通过控制脉冲个数来控制角位移量,从而达到准确定 位的目的;同时可以通过控制脉冲频率来控制电机转动的速度和加速度,从而达到调速的目的。
肺宝用无霍尔传感器FOC电机:无霍尔FOC实现了启动平稳,超
静音,逆风启动等性能;下面了解下FOC电机的一些技术特征: FOC电机的特性: 1. 控制算法:无传感器FOC 2. 控制方式: 速度控制/恒DUTY PWM控制 3. 调制方式:空间矢量脉宽调制(SVPWM) 4. 电流采样方式: 2/3桥臂电阻取样; 5. 调制频率: 16KHZ; 6. 速度波动率: <0.5%; 极数4极; 7. 启动方式: 恒电流启动,软启动; 8. 保护功能:内部锁住保护(含电压堵住,自动断电及断电后自重启等 )、极性保护(VCC与GND反接时,不导通)、过流保护等; 9. 无传感器磁场定向控制(FOC)具有转速稳定度高、没有传感器误差 影响等诸多优点;
伺服驱动与步进驱动的差异比较
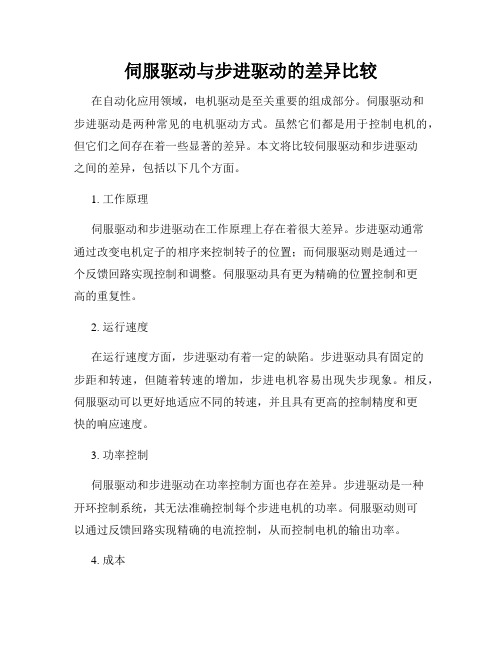
伺服驱动与步进驱动的差异比较在自动化应用领域,电机驱动是至关重要的组成部分。
伺服驱动和步进驱动是两种常见的电机驱动方式。
虽然它们都是用于控制电机的,但它们之间存在着一些显著的差异。
本文将比较伺服驱动和步进驱动之间的差异,包括以下几个方面。
1. 工作原理伺服驱动和步进驱动在工作原理上存在着很大差异。
步进驱动通常通过改变电机定子的相序来控制转子的位置;而伺服驱动则是通过一个反馈回路实现控制和调整。
伺服驱动具有更为精确的位置控制和更高的重复性。
2. 运行速度在运行速度方面,步进驱动有着一定的缺陷。
步进驱动具有固定的步距和转速,但随着转速的增加,步进电机容易出现失步现象。
相反,伺服驱动可以更好地适应不同的转速,并且具有更高的控制精度和更快的响应速度。
3. 功率控制伺服驱动和步进驱动在功率控制方面也存在差异。
步进驱动是一种开环控制系统,其无法准确控制每个步进电机的功率。
伺服驱动则可以通过反馈回路实现精确的电流控制,从而控制电机的输出功率。
4. 成本在成本方面,步进驱动通常会更便宜一些。
步进驱动的控制系统相对简单,容易用低成本部件实现;而伺服驱动则需要更为复杂和昂贵的控制系统。
5. 应用范围由于伺服驱动具有更高的控制精度和更快的响应速度,因此它们通常用于需要高精度定位和速度控制的应用程序中,例如机器人、数控机床和自动精密加工设备等。
而步进驱动通常用于较低要求的应用程序中,例如纺织、包装和印刷等行业。
结论尽管伺服驱动和步进驱动都是控制电机的有效方式,但它们之间存在着很大的差异。
伺服驱动具有更高的控制精度和更快的响应速度,更适用于需要高精度定位和速度控制的应用程序中。
而步进驱动则适用于对精度和速度要求较低的应用程序中,同时还具有更低的成本。
在选择驱动方式时,应根据应用程序的具体要求进行决策。
步进电机有几种工作方式

步进电机有几种工作方式在现代工业和自动化领域中,步进电机是一种常用的电动机之一。
步进电机具有结构简单、运行稳定、定位准确等优点,被广泛应用于各种设备和系统中。
根据不同的控制方式和工作原理,步进电机可以分为几种不同的工作方式。
1. 开环控制方式开环控制方式是步进电机最基本的工作方式之一。
在开环控制下,系统仅根据输入的脉冲信号来驱动步进电机,而没有反馈信号用于监测电机的实际运动情况。
这意味着系统无法实时调整电机的运行状态,容易出现失步或者误差累积的问题。
开环控制方式适用于一些对定位精度要求不高的场合,成本较低。
2. 半闭环控制方式半闭环控制方式在开环控制的基础上增加了位置传感器或编码器等反馈装置,用于监测步进电机的实际位置信息。
根据反馈信号,系统可以进行部分的位置校正,提高了系统的稳定性和定位精度。
半闭环控制方式适用于一些对定位精度要求较高的场合,但相比全闭环控制,其成本和复杂度较低。
3. 全闭环控制方式全闭环控制方式是步进电机的高级控制方式之一。
在全闭环控制下,系统不仅通过位置传感器获取电机的实际位置信息,还将这些信息反馈给控制器进行实时校正。
这样可以确保步进电机在高速运动或负载变化时仍能保持准确的位置控制,提高了系统的响应速度和稳定性。
全闭环控制方式适用于对精准定位和高速响应要求较高的场合,但相应地增加了系统的成本和调试难度。
4. 微步进控制方式除了以上三种基本的控制方式外,还有一种常见的控制方式是微步进控制。
微步进控制通过改变步进电机的相间电流波形,将每一步的细分成更小的微步,从而使电机的1转动更加平滑和精确。
相较于传统的全步进控制方式,微步进控制可以提高电机的分辨率和平稳性,但也会增加电机的功耗和控制复杂度。
不同的工作方式适用于不同的应用场合,用户可以根据自身需求和预算选择合适的步进电机控制方式。
在实际应用中,需综合考虑定位精度、速度要求、成本限制等因素,选择最适合的控制方式,以达到最佳的工作效果。
步进电机的计算方法

步进电机的计算方法1.根据驱动方式选择步进电机型号:步进电机主要分为两种驱动方式,即双相驱动和四相驱动。
双相驱动的步进电机具有较高的输出转矩,适用于需要较大负载的应用,而四相驱动的步进电机输出转矩较低,适用于速度要求较高的应用。
2.计算步进电机运转速度:步进电机的运转速度主要受到步进角度和脉冲频率的影响。
步进角度一般是固定的,常见的有1.8度和0.9度。
计算步进电机运转速度的公式为:速度=步进角度×脉冲频率。
3.计算步进电机的步进角度:步进电机的步进角度是指每接收到一个脉冲信号,电机旋转的角度。
常见的步进角度有1.8度和0.9度。
计算步进电机的步进角度的公式为:步进角度=360度÷步进电机的相数。
4.计算步进电机的电压和电流:步进电机在运行时需要供应一定的电压和电流来驱动。
计算步进电机的电压和电流的方法是根据电机的工作电压和绕组电阻。
电机的绕组电阻一般可以从电机的技术参数中获取。
计算步进电机的电压的公式为:电压=电流×电阻。
5.计算步进电机的输出功率:步进电机的输出功率是指电机在工作时提供的机械功率。
计算步进电机的输出功率的方法是根据电机的输出转矩和转速。
输出功率的公式为:输出功率=转矩×转速。
6.计算步进电机的加速度和减速度:步进电机的加速度和减速度是指电机从静止状态到达最大速度和从最大速度减速到停止状态所需要的时间。
计算步进电机的加速度和减速度的公式为:加速度(或减速度)=(最大速度-初始速度)÷时间。
7.计算步进电机的负载惯性:步进电机在运行时会受到负载惯性的影响,计算步进电机的负载惯性的方法为负载惯性=负载质量×负载半径的平方。
以上是步进电机的计算方法的一些基本介绍,根据实际需求,其他还有一些特殊的计算方法,比如控制系统的设计和驱动方式的选择等,需要根据具体情况进行进一步的研究和计算。
步进电机驱动之全桥驱动与斩波恒流

步进电机驱动之全桥驱动与斩波恒流先看两相绕组的全桥驱动电路,四路基本相同的驱动电路,抓取一组电路来分析:全桥驱动电路,其中Q7和Q8基极和发射极短接,相当于一个反向的二极管。
为了便于分析,将原理图简化后如下所示:查看IM2000S芯片手册,对全桥驱动芯片输入脚的定义如下:以上四个输入端:B相高低端全桥控制信号,用来控制离散的PN,NN的全桥或者半桥IC. 从上述可以知道,输出的是一个离散量,那么,是怎样控制电机,使电机获得一个sin和cos 的电流信号而驱动电机的呢?这里要深入理解一个概念:斩波恒流!斩波恒流的原理是:当环形分配器导通的时候,IC2使得TL和TH导通,电源通过TH和TL 和电机向下有电流输出,此时R左端的电压上升,当电流上升到给定电平时,比较器反转,输出为低,使得IC1截止,此时电感使电流缓慢下降,此时通过TL采样的电压变低,当电压低于给定电平时候,比较器反转,使得IC1再次导通,这样可以快速的波动,而使电感上的电流保持一个恒定的值。
当环形分配器给出低电平时,IC1和IC2截止,电流通过D2流入电源,从而实现节能。
此时,再看上图,会发现:1、BHO和ALO为一个通路,AHO和BLO为一个通路,实现电流的正向和反向。
2、BHO和AHO的开关频率会比BL0,ALO大很多,BL0和ALO只有在正向和负方向反转的时候出现跳变,而BHO和AHO的频率会很快以实现恒流。
这里值得注意的一点是,上述过程仅仅是在一个细分时候,一个数模转换量上保持的恒流。
如果整步为256细分,则在256细分的每一个细分阶段实际上过程就是上文红色字体运行一遍的一个过程,而要使整个电机转动一圈,则需要完成一个SIN和COS的整个过程,如果上面的过程仍然无法理解,请参看步进电机细分方面的内容。
从整个驱动电路的系统上看,整个闭环是按照如下进行工作的:1、TC1002发出一个启动信号,使得全桥驱动芯片导通A+的MOS1和A-的MOS2形成回路,此时在A-上采集的电压通过比较器与正弦信号输出的给定参考电压形成对比,当电压超过参考电压时,比较器翻转,翻转信号反馈给TC1002,然后低电平的信号反馈给A+的MOS1,此时MOS关闭,电机上的电流通过A+的MOS1流回电源,从而完成周而复始的完成整步的1/N的一次恒流。
- 1、下载文档前请自行甄别文档内容的完整性,平台不提供额外的编辑、内容补充、找答案等附加服务。
- 2、"仅部分预览"的文档,不可在线预览部分如存在完整性等问题,可反馈申请退款(可完整预览的文档不适用该条件!)。
- 3、如文档侵犯您的权益,请联系客服反馈,我们会尽快为您处理(人工客服工作时间:9:00-18:30)。
步进电机 步进电机驱动方法的比较
单电压驱动是指在电机绕组工作过程中,只用一个方向电压对绕组供电。
如图2所示,L为电机绕组,VCC 为电源。
当输入信号In为高电平时,提供足够大的基极电流使三极管T处于饱和状态,若忽略其饱和压降,则电源电压全部作用在电机绕组上。
当In为低电平时,三极管截止,绕组无电流通过。
为使通电时绕组电流迅速达到预设电流,串入电阻Rc;为防止关断T时绕组电流变化率太大,而产生很大的反电势将T击穿,在绕组的两端并联一个二极管D和电阻Rd,为绕组电流提供一个泄放回路,也称“续流回路”。
单电压功率驱动电路的优点是电路结构简单、元件少、成本低、可靠性高。
但是由于串入电阻后,功耗加大,整个功率驱动电路的效率较低,仅适合于驱动小功率步进电机。
为了使通电时绕组能迅速到达设定电流,关断时绕组电流迅速衰减为零,同时又具有较高的效率,出现了高低压驱动方式。
如图3所示,Th、T1分别为高压管和低压管,Vh、V1分别为高低压电源,Ih、I1分别为高低端的脉冲信号。
在导通前沿用高电压供电来提高电流的前沿上升率,而在前沿过后用低电压来维持绕组的电流。
高低压驱动可获得较好的高频特性,但是由于高压管的导通时间不变,在低频时,绕组获得了过多的能量,容易引起振荡。
可通过改变其高压管导通时间来解决低频振荡问题,然而其控制电路较单电压复杂,可靠性降低,一旦高压管失控,将会因电流太大损坏电机。
自激式恒电流斩波驱动框图。
把步进电机绕组电流值转化为一定比例的电压,与D/A转换器输出的预设值进行比较,控制功率管的开关,从而达到控制绕组相电流的目的。
从理论上讲,自激式恒电流斩波驱动可以将电机绕组的电流控制在某一恒定值。
但由于斩波频率是可变的,会使绕组激起很高的浪涌电压,因而对控制电路产生很大的干扰,容易产生振荡,可靠性大大降低。
步进电机。