反应注射成型工艺及其发展1.
注凝成型gelcasting工艺及其新发展

综合评述
注凝成型( gelcasting) 工艺及其新发展
薛义丹 徐廷献 郭文利 邹强
(天津大学先进陶瓷与加工技术教育部重点实验室 ,天津大学材料学院 ,天津 300072)
摘 要 简要概括了注凝成型的工艺过程及其特点 ,着重介绍了低毒性凝胶系统的选择 、注凝成
注凝成型不仅适用于大尺寸部件的成型 ,也 同样适用于复杂形状部件的成型 。但复杂部件在 脱 模 时 还 存 在 一 些 技 术 问 题 。MoldSDF ( mold shape deposition manufacturing) 是一种制作模具的 方法 , 它是基 本 累 加 的 过 程 。图 1 所 示 为 应 用 MoldSDF 制备一个简单部件的成型过程 。MoldS2 DF 工艺在制备复杂形状的陶瓷部件时有 2 个显 著的优势 : (1) MoldSDF 工艺成型的样品的所有表 面可进行重复的机械再加工 ,以求表面光洁 、形状 精确 ; (2) 浆料可一次性注入 ,这样可以消除模具 的层界现象 ,避免在坯体中产生缺陷 。注凝成型 法与 MoldSDF 相结合 ,可以生产各种复杂形状的 部件 ,并且生产的部件具有良好的显微结构和机 械性能 。Stanford 大学已经该方法成功制备了氮 化硅涡轮转子和不锈钢转子[17] 。
二烯丙基酒石酸钾铵
双 官 能
N - N 亚甲基双丙烯酰胺 聚乙烯 (乙烯. 乙二醇 XXX) 脂
团 甲基丙烯酸盐[ 酯 ]
DATDA
烯丙基
MBAM
丙烯酰胺
PEG(XXX) DA 丙烯酸脂
PEG(XXX) DMA 丙烯酸脂
4. 1. 2 天然大分子的应用 许多从动植物中提取出来的纯天然水溶液大
反应注射成型技术概述 1.

纤维增强材料:RRIM使用的主要有玻璃纤维、碳纤维、 尼龙纤维及不锈钢纤维等,其中用量最大的是玻璃纤维。
RRIM制品具有高模量、耐热性能好、线膨胀系数小等特 点,可替代钢材制作汽车车体和各种结构部件。
应用拓展:不再局限于聚氨酯体系,已广泛应用于不饱和 聚酯、环有机硅树脂和互穿聚合物网络等多种材料; 将RIM工艺用于橡胶与金属成型已成为高分子材料加工领域 的研究热点。
一、反应注射成型的原理及特点
一、反应注射成型的原理及特点
反应注射成型(RIM):最早是德国在20世纪50年代开 发的聚氨酯材料成型工艺,后由美国汽车行业进行实用化研 究,成功用于聚氨酯汽车保险杠制造。
RIM成型原理:将具有高化学活性、相对分子质量低的双 组分材料(如异氰酸酯和多元醇)混合后,在常温低压下注 入模具内,完成聚合、交联和固化等化学反应并固化成制品。
5)可生产厚壁制品,且壁厚与加强筋之比可达1:0.8, 此值高于其它成型工艺。
6)RIM工艺过程具有物料混合效率高、流动性好、原料 配制灵活、生产周期短的特点。
7)具有设备投资及生产成本低、制件外表美观,耐冲击 性好,设计灵活性大等优点,特别适用于汽车覆盖件等大 型塑件的成型加工。
RIM与其它塑料成型技术比较,具有以下特点:
1)RIM是能耗最低的工艺之一。因液态原料所需注射压 力和锁模力仅为普通注射成型的1/100~1/40,耗能少。
2)RIM模腔压力小,约为0.3~1.0MPa,设备和模具所需 的投资少。
3)RIM所用体系多种多样,如聚氨酯、聚脲、尼龙、双 环戊二烯等。
4)易于成型薄壁大型制件,且具有很好的涂饰性;液态 物料对模具表面的花纹、图案具有很好的再现性。
早期应用:聚氨酯弹性体和聚氨酯泡沫塑料,用于大型厚 壁制品生产。
注射成型技术研究进展

维普资讯
20 0 7年 第 2期 第3 4卷 总第 1 6 6 期
广
东
化
工
Ⅵ, w . he .om 、 gdc m c v
注射成型 技术研 究进展
王玉洁 ,黄 明福 ,陈晋南
( 北京理工大学 化工与环境学院,北京 10 8 ) 00 1
[ 摘 要] 简要介绍 了注塑机 的发展过程、结构和特点 ,重点介绍 了反应注射成 型、气体 辅助注射 成型、水辅助注射 成型、动
塑料通过 比较经济 的注射成型方法加工成各种塑料制件 。 注塑机是借 助于金 属压铸机的原理 ,以高速高压将塑料熔
体注入 到已闭合的模 具型腔内 ,经冷却定型 ,得到与模腔形状
一
果表 明,注射成型用塑料量约 占整个塑料 产量的 3 %l,并有 0 l J 逐年增长 的趋势 。注塑机是将热 塑性 塑料 或热 固性 塑料制成各
态注射成型等几种新型注射成型工艺的原理、特点及应用。最后展望注塑机和塑料注射成型技术 的发展。
[ 关键 词] 注塑机 ;注射 成型 ;新工 艺
Ad a c f sa c nI jcinModn e h oo y v n eo e r ho net ligT c n lg Re o
种塑料制件 的主要成型设备 。有专家指 出 ,我国今 后塑料机 械 产品的出 E将 以注 塑机为主 。从 出 E数量 上分析 ,预计注塑机 1 l 占 6. 04 %;从 出口创汇额来看 ,注塑机 占 7 . 41 %。往复螺杆式 注塑机是注射成型工艺技术方面 的一个重大突 破。 自往复螺杆 式注 塑机 问世 以来 ,人们认为它是一种 比较理 想的加工设备 , 所以机器 的基本结构没有发 生根本性 的变化 ,但 其技 术不断得
反应注射成型工艺
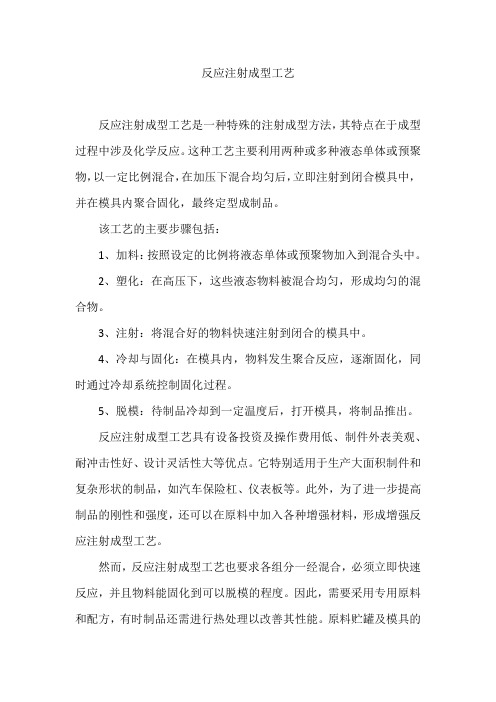
反应注射成型工艺
反应注射成型工艺是一种特殊的注射成型方法,其特点在于成型过程中涉及化学反应。
这种工艺主要利用两种或多种液态单体或预聚物,以一定比例混合,在加压下混合均匀后,立即注射到闭合模具中,并在模具内聚合固化,最终定型成制品。
该工艺的主要步骤包括:
1、加料:按照设定的比例将液态单体或预聚物加入到混合头中。
2、塑化:在高压下,这些液态物料被混合均匀,形成均匀的混合物。
3、注射:将混合好的物料快速注射到闭合的模具中。
4、冷却与固化:在模具内,物料发生聚合反应,逐渐固化,同时通过冷却系统控制固化过程。
5、脱模:待制品冷却到一定温度后,打开模具,将制品推出。
反应注射成型工艺具有设备投资及操作费用低、制件外表美观、耐冲击性好、设计灵活性大等优点。
它特别适用于生产大面积制件和复杂形状的制品,如汽车保险杠、仪表板等。
此外,为了进一步提高制品的刚性和强度,还可以在原料中加入各种增强材料,形成增强反应注射成型工艺。
然而,反应注射成型工艺也要求各组分一经混合,必须立即快速反应,并且物料能固化到可以脱模的程度。
因此,需要采用专用原料和配方,有时制品还需进行热处理以改善其性能。
原料贮罐及模具的
温度控制也是非常重要的。
总的来说,反应注射成型工艺是一种高效、灵活的塑料加工方法,广泛应用于汽车、电子、家电等领域。
随着技术的进步和工艺的完善,该工艺将在更多领域得到应用。
反应注射成型(RIM)聚氨酯特性与应用

(6)物料以液体形态注入模具,有利于生产断面形状复 杂的制品,可嵌入插入件一次成型,也可以在液体 原料中添入某些增强材料。
生产增强型反应注塑模制(RRIM——Reinforced Reaction lnjection Moulding)以及在模腔中预置增强 片材等生产结构增强型反应注塑模制品(SRIM—— Structural Reaction Injection Moulding)等。 可以制 备带有较厚加强筋的制品,普通塑料壁厚和加强筋 厚之比最大为1:0.3,而R1M工艺可生产高达1:0.8的 厚筋制品。
反应注射成型(RIM)聚氨酯的特性和 应用
(2)模具强度要求较低。物料呈液体状态注入 模具,模腔内压较低,模具承压能力较传统 塑料成型模要低得多。
(3)所用原料体系比较广泛。该项新工艺除了 适用于聚氨酯、聚脲材料的生产,同时还可 以用于环氧树脂、尼龙、双环戊二烯、聚酯 等材料的加工成型。 反应注射成型(RIM)聚氨酯的特性和
即按照预配方配料、预分散、预加热等,然后再输入发
泡机的工作罐中。原料在工作罐中必须进行工作温度的
精确调节,在循环和搅拌的过程中,使物料进一步达到
分散均匀,并使各原料体系完成所必须的工作参数的准
反应注射成型(RIM)聚氨酯的特性和 应用
RIM加工技术的优点包括以下几点:
⑴RIM加工技术能量消耗低。它与传统热塑型 合成材料加工成型相比,由于加工时物料为低 粘度液体状态,注模压力较低。反应放热量大, 模温较低,模具的夹持力突出。
反应注射成型(RIM)聚氨酯的特性和 应用
6.2 RIM-聚氨酯加工机械简 介
随着聚氨酯工业的迅速发展、应用领域的扩大和消 费量的激增,传统式的低压计量、混合装置的某些技 术缺陷暴露得越来越明显,在聚氨酯化学研究和相关 制造部门的紧急配合下,1976年,德国拜耳公司和 Hennecke公司首先推出了以高压冲击方式进行混合 和具有自动清洁功能为特征的高压反应注射计量、混 合、分配装备。由于这种装备具有许多低压机无法比 拟的优点,更适宜大规模工业化生产的需要,生产产 品类型多样,因此很受聚氨酯工业的欢迎,逐渐成为 聚氨酯行业使用的主要装备。
注射成型工艺的定义及应用
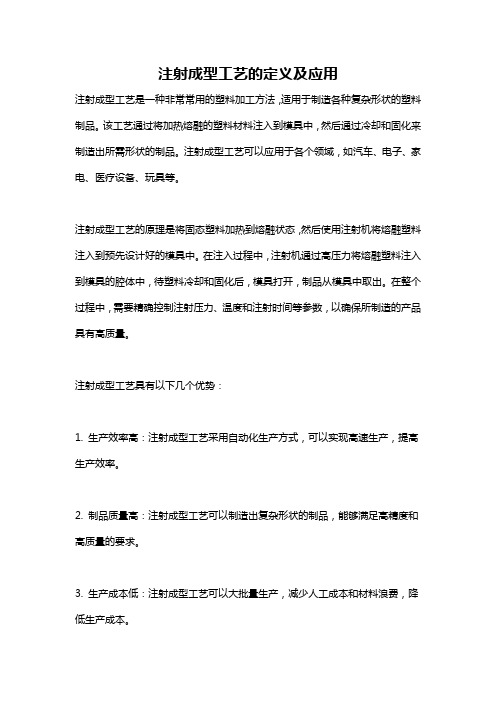
注射成型工艺的定义及应用注射成型工艺是一种非常常用的塑料加工方法,适用于制造各种复杂形状的塑料制品。
该工艺通过将加热熔融的塑料材料注入到模具中,然后通过冷却和固化来制造出所需形状的制品。
注射成型工艺可以应用于各个领域,如汽车、电子、家电、医疗设备、玩具等。
注射成型工艺的原理是将固态塑料加热到熔融状态,然后使用注射机将熔融塑料注入到预先设计好的模具中。
在注入过程中,注射机通过高压力将熔融塑料注入到模具的腔体中,待塑料冷却和固化后,模具打开,制品从模具中取出。
在整个过程中,需要精确控制注射压力、温度和注射时间等参数,以确保所制造的产品具有高质量。
注射成型工艺具有以下几个优势:1. 生产效率高:注射成型工艺采用自动化生产方式,可以实现高速生产,提高生产效率。
2. 制品质量高:注射成型工艺可以制造出复杂形状的制品,能够满足高精度和高质量的要求。
3. 生产成本低:注射成型工艺可以大批量生产,减少人工成本和材料浪费,降低生产成本。
4. 环保节能:注射成型工艺不会产生废水废气等污染物,符合环保要求,同时也可以节约能源。
注射成型工艺广泛应用于各个行业,下面我将依次介绍几个应用领域:1. 汽车行业:汽车零部件如仪表盘、门板、车灯等都可以通过注射成型工艺来制造。
注射成型工艺可以实现复杂形状、轻量化和高韧性要求,满足汽车工业不断提高产品质量、降低成本的需求。
2. 电子行业:注射成型工艺在电子行业中的应用非常广泛,如手机壳、键盘、电视外壳、充电器等。
注射成型工艺可以制造出光滑、细腻的外观,为电子产品增加美观度和手感。
3. 家电行业:家电制品如冰箱、洗衣机、风扇等都可以采用注射成型工艺制造。
注射成型工艺可以实现产品结构复杂、组装方便、使用寿命长等特点,满足家电行业对产品功能和性能的要求。
4. 医疗设备:注射成型工艺在医疗设备制造中也有广泛应用,如注射器、输液器、雾化器等。
注射成型技术可以实现医疗器械的高精度制造,确保产品无菌、安全可靠。
可变纤维增强反应注射成型技术研究现状

中图分类号 :T 3 0 U 2
文献标识码 :A
文章编号 :10 0 9 (0 0 0 0 7 0 0 3— 9 9 2 1 )5— 0 1— 7
传统的高分子工业生产 中, 高分子材料的制备
和加 工成 型是 两个截 然不 同的工艺 过程 。制备 过程 主要 是化学 过程 : 单体 、 化剂及 其 他助 剂通 过 反应 催
具有许多优点 , 如生产效率高、 能耗低 , 模腔压力小
(. 0 3~10 a , 料 体 系 较 广 , 备 投 资 小 , 合 .MP ) 原 设 适 于 薄壁 、 型 、 大 复杂制 品 , 而且 产 品表面 质量 好 , 纹 花
收稿 日期 :2 0 .OO 0 91 - 6 作者简介 :陈丰 ( 9 2) 17 一 ,男 ,博士 ,副教授 ,主要研究方向为复合 材料及其 成型技术 。
生 产连续 、 无需 进 行 复 杂 的分 离提 纯 和 溶 剂 回收 等
后处理过程 、 节约能源和资源 、 环境污染小等诸多优 点。高分子反应加工分 为反应挤 出和反应 注射 成 型…两部分。 目前国内外对于反应挤出成型的研究
异常 活跃 , 但对 于 反应 注射 成 型 的 研 究 和应 用 略显 不足 , 甚至 一度停 顿 , 中原 因可能是 由于材 料体 系 其
反应 注射 成型 技术 的开 发成 功 和如 D P C D等新 型 材 料 的研制 成功 都促 进 了反应 注射 成型 的发展 。
1 反应 注射成 型技术
反 应 注射 成 型 ( eco n co odn , R atnietnm lig 简称 i j i R M) 是 2 纪 7 I 0世 O年 代 初 在 聚 合 物 加 工 领 域 中 发 展起 来 的一 种新 型高 分 子 材料 成 型 技 术 , 过 三 经 十多年 的发展 , 最初 的反应 注 射成 型 , 历 了增 强 从 经 反应 注射 成 型 、 构反 应注射 成 型 , 展 到 目前最 先 结 发 进 的 可 变 纤 维 增 强 反 应 注 射 成 型 , 用 范 围不 断 应
注射成型工艺分析
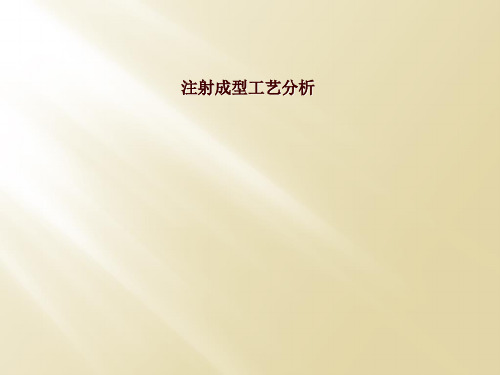
③ 充模。塑化好的塑料在注射机的螺杆或柱 塞的快速推进作用下,以一定的压力和速度经注 射机喷嘴和模具的浇注系统进入并充满模具型腔 的过程称为冲模。
④ 保压。在模具中熔体冷却收缩时,继续保 持施压状态的柱塞或螺杆迫使浇口附近的熔料不 断补充入模具中,使型腔中的塑料能成型出形状 完整而致密的塑件,这一阶段称为保压。
2.注射成型工艺过程 一个完整的注射成型工艺过程包括成型前准 备、注射过程及塑件的后处理。 (1)成型前的准备工作 为了使注射成型顺利进行,保证塑件质量,在 注射成型之前应进行一些准备工作: ① 原料的检验和预处理。在成型前应对原料
进行外观和工艺性能检验,内容包括色泽、粒度 及均匀性、流动性、热稳定性、收缩性、水分含 量等。
常用塑料中,需要较高模具温度的有聚碳酸酯、
聚砜和聚苯醚等;采用较低模具温度的有聚乙烯、 聚丙烯、聚氯乙烯、聚苯乙烯和聚酰胺等。
(2)压力 注射成型过程中的压力包括塑化压力和注射压 力,它们关系到塑料的塑化和塑件的质量。 ① 塑化压力 塑化压力是指采用螺杆式注射机时,螺杆顶部
熔体在螺杆旋转后退时所受的压力,亦称背压, 其大小可以通过注射机液压系统中的溢流阀来调 整。
①注射装置 注射装置是注射机最主要的组成部分之一,其 主要作用是将塑料均匀地塑化,并以足够的压力 和速度将定量的熔料注射到模具型腔中。注射装 置由塑化部件(包含螺杆、料筒和喷嘴)以及料 斗、计量装置、传动装置、注射和移动液压缸等 组成。 ② 合模装置 合模装置主要由前后固定模板、移动模板、连 接前后固定模板用的拉杆、合模油缸、连杆机构、 调模装置、顶出装置和安全保护机构组成。其作 用是保证模具闭合、开启及顶出制品。同时,在
塑化压力大小对熔体实际温度、塑化效率及成
形周期等均有影响。在其他条件相同的情况下, 增加塑化压力,会提高熔体的温度及其均匀性, 使色料的混合均匀,易于排出熔体中的气体。但 增加塑化压力会降低塑化速率,从而延长成型周 期,而且增加了塑料分解的可能性。