汽车传动轴设计
汽车传动轴设计范文

汽车传动轴设计范文汽车传动轴是汽车动力传输系统中的关键组成部分,承担着将发动机产生的动力传递到车轮的任务。
传动轴设计的目标是实现高效率、低噪音和可靠性。
在设计传动轴时,需要考虑多个因素,包括传动轴的材料选择、传动轴的结构设计和传动轴的加工工艺等。
传动轴的材料选择是影响传动轴性能的重要因素之一、传动轴通常采用高强度合金钢或碳纤维复合材料制作。
高强度合金钢具有优异的强度和韧性,能够承受高强度的扭转和弯曲力。
而碳纤维复合材料具有高强度、低密度和优异的疲劳寿命,能够降低传动轴的重量并提高耐久性。
传动轴的结构设计是实现高效率传输的关键。
一般来说,传动轴的截面形状决定了其刚度和重量。
传动轴通常采用圆柱形的实心杆或中空杆设计。
实心杆传动轴具有较高的刚度,能够抵御大扭矩和弯曲力,但重量较大。
而中空杆传动轴由于空心结构的设计,能够降低传动轴的重量,并提高传动效率。
但对于承受较大扭矩和弯曲力的应用来说,中空杆传动轴的刚度较低,需要在设计中进行综合考虑。
除了结构设计,传动轴的加工工艺也对传动轴性能产生重要影响。
精确的加工工艺能够提高传动轴的平衡性、可靠性和传动效率。
在加工过程中,需要进行精确的尺寸控制、表面处理和动平衡处理。
尺寸控制是确保传动轴高度精度的关键。
表面处理能够提高传动轴的耐腐蚀性和抗磨性。
动平衡处理能够减少传动轴的振动和噪音,并提高传动效率。
除了上述因素,传动轴设计还需要考虑其他一些因素,如传动轴的长度、传动轴的安装方式和传动轴的支撑方式等。
传动轴长度的选择需要权衡传动效率和车辆布局的要求。
传动轴的安装方式一般分为固定式和可伸缩式两种,根据车型和传动需求进行选择。
传动轴的支撑方式包括悬挂式和支架式,需要根据车辆底盘结构和传动需求进行选择。
在传动轴设计中,还需要进行性能计算和结构优化。
性能计算可以通过计算机辅助工程软件进行,包括传动效率、传动轴的疲劳寿命和传动轴的振动等。
结构优化可以通过有限元分析方法进行,通过调整传动轴的结构参数,优化传动轴的性能和重量。
汽车传动轴设计范文

汽车传动轴设计范文首先,汽车传动轴的主要功能是传递动力。
在设计传动轴时,需要考虑到车辆的功率输出和转速范围。
一般而言,高功率车辆需要更加强固的传动轴来承受更大的转矩和压力。
此外,传动轴的设计还需要考虑到车辆的运行速度范围,以确保传动轴在高速情况下能够承受住转动力。
其次,汽车传动轴的设计对于车辆的平顺性和舒适性也有很大影响。
传动轴的设计需要考虑到轴的重量和平衡性,以减少振动和噪音。
一种常见的设计方法是在传动轴上使用平衡块来平衡轴的重量和减少振动。
此外,传动轴的设计还需要考虑到轴的刚度和弯曲性,以确保传动轴在运转过程中不会发生变形或弯曲,从而影响车辆的平顺性和舒适性。
另外,对于四驱车辆而言,传动轴的设计也需要考虑到车轮之间的差速问题。
差速器通常安装在传动轴上,它能够根据车轮速度的差异来实现差速作用,并帮助车辆更好地应对转弯情况。
因此,传动轴的设计需要考虑到差速器的安装位置和传动轴与差速器之间的连结方式。
此外,与传动轴密切相关的还有轴承和万向节的设计。
轴承的选材和设计对于减少传动轴的摩擦和磨损至关重要。
对于高速和高功率的车辆而言,可能需要采用更耐磨和耐高温的轴承材料来提高传动轴的使用寿命。
万向节的设计则用于传递动力和允许轴的角度变化,以适应车轮的悬挂和转向。
综上所述,汽车传动轴的设计对于汽车性能、安全和舒适性都起着至关重要的作用。
在设计传动轴时,需要兼顾动力传递、平顺性、舒适性和差速等因素,以确保传动轴能够满足车辆的需求。
此外,轴承和万向节的设计也是传动轴设计的重要考虑因素,它们对于传动轴的耐磨性、耐高温性和角度变化能力都有着重要影响。
因此,对于汽车制造商和工程师而言,对于传动轴设计的细节和原理的深入了解是非常必要的。
浅谈汽车传动轴设计的基本要求与考虑因素

浅谈汽车传动轴设计的基本要求与考虑因素
前言
随着科学技术的进步,汽车的发展已经步入了一个新的时代。
汽车电子器件(汽车空调控制器)也已成为汽车性能的标志。
汽车传动轴是汽车构造中重要的组成部分(汽车电子控制技术),所以对于汽车传动轴的设计就变得尤为重要。
那么,怎样设计一款高性能的汽车传动轴呢,作者通过搜集整理资料,从汽车传动轴设计的基本要求,需要考虑的因素以及对汽车传动轴设计优化等方面做了详细介绍。
汽车传动轴设计(汽车控制系统)的基本要求:
1.保证所连接的两根轴相对位置在预计范围内变动时,能可靠地传递动力。
2.保证所连接两轴尽可能等速运转。
3.由于万向节夹角而产生的附加载荷、振动和噪声应在允许范围内。
4.传动效率高,使用寿命长,结构简单,制造方便,维修容易等第三章五十铃万向传动轴结构分析及选型由于五十铃货车轴距不算太长,且载重量。
变速器与驱动桥之间的万向传动装置
汽车传动轴设计时需考虑的几个方面
空心传动轴具有较小的质量,能传递较大的转矩,比实心传动轴具有更高的临界转速,所以此传动轴管采用空心传动轴。
传动轴的长度和夹角及它们的变化范围,由汽车总布置设计决定。
设计时应保证在传动轴长度处在最大值时,花键套与花键轴有足够的配合长度;而在长度处于最小时,两者不顶死。
传动轴夹角大小会影响万向节十字轴和滚针轴承的寿命、万向传动效率和十字轴的不均匀性。
变化范围为3。
汽车传动轴经常处于高速旋转状态下,所以轴的材料查机械零件手册选取。
传动轴设计及应用解读

• 准等速万向节:是指输入轴和输出轴以近似等速传递运动 的万向节。双联式万向节、凸块式万向节和三销轴式万向 节等为准等速万向节。主要用于转向驱动桥。
• 等速万向节:等速万向节是指输入轴和输出轴以等速传递 运动的万向节。球笼式万向节和球叉式万向节等为等速万 向节。主要用于轿车和驱动桥。 • 挠性万向节:挠性万向节依靠其中弹性零件的弹性变形来 保证在相交两轴间传动时不发生干涉。它能减小传动系的 扭转振动、动载荷和噪声,结构简单,使用中不需润滑, 一般用于两轴间夹角不大和很小轴向位移的万向传动场合。
传动轴的动平衡
• 传动轴总成不平衡是传动系弯曲振动的一个激 励源,当高速旋转时,将产生明显的振动和噪 声。所以传动轴装配后必须100%进行动平衡 检验,并在传动轴两端焊平衡片校正不平衡量, 其剩余不平衡量不应低于GB 9293中规定的G40 平衡品质等级。 • 影响传动轴动平衡品质的因素: 1、万向节十字轴的轴向间隙; 2、传动轴滑动花键副中的间隙; 3、传动轴总成两端连接处定心精度; 4、高速回转时传动轴的弹性变形。
传动轴额定载荷的确定
• • 传动轴的额定载荷是根据车型的配置参数计算出来的。先按发动机最大扭矩 计算,再按车轮的最大附着力计算,取二者中的小值作为额定扭矩。 1、按发动机最大扭矩计算: Mg=Memax×ik1×ip1/n 式中 Mg—按发动机最大扭矩计算时传动轴承受的扭矩,N.m Memax—发动机最大扭矩,N.m ik1 —变速箱一档速比 ip1 —分动箱低档速比 n —使用分动器低档时的驱动轴数目 2、按车轮最大附着力计算: Mφmax=G×rk×ψ/io 式中 Mφmax—按附着力计算时传动轴承受的扭矩,N.m G—满载时驱动轴上的载荷,N rk —车轮的滚动半径,m ψ —轮胎与地面的附着系数(在良好的沥青路面上取0.8) io —减速器速比
传动轴设计及应用

传动轴设计及应用首先,传动轴的设计需要考虑到以下几个方面的因素:材料选择、强度计算、匹配设计和制造工艺。
材料选择是传动轴设计的重要环节。
一般来说,传动轴要求具有高强度、良好的韧性和耐磨性。
常见的传动轴材料包括碳钢、合金钢和不锈钢等。
选择合适的材料可以保证传动轴的寿命和可靠性。
强度计算是传动轴设计中的重要一环。
传动轴工作时会承受扭矩和弯曲力,因此需要进行强度计算来确定传动轴的尺寸和形状。
一般情况下,传动轴的强度计算包括静态强度计算和疲劳强度计算两部分,其中疲劳强度计算对于传动轴的使用寿命至关重要。
匹配设计是指传动轴的轴径和连接方式的设计。
传动轴的轴径设计需要根据所传递的扭矩大小来确定,一般可以通过静态强度计算得到。
传动轴的连接方式有多种,常见的有键槽连接和销轴连接等。
选择合适的连接方式可以确保传动轴的可靠性和安全性。
制造工艺是传动轴设计中的最后一环。
传动轴通常需要进行多道工序的加工,如车削、铣削和热处理等。
制造工艺的选择和控制对于传动轴的尺寸精度和表面质量至关重要。
同时,传动轴的装配和调试也需要注意,以确保传动系统的正常运行。
传动轴的应用非常广泛。
汽车传动轴是其中最常见的应用之一、汽车传动轴通常由前后驱动轴、中间驱动轴和传动装置等组成,用于传递发动机的动力到车轮上。
传动轴的设计需要考虑到汽车的整体性能、可靠性和经济性。
此外,传动轴还广泛应用于船舶、工程机械、风电设备等领域,用于传递动力和扭矩,实现各种机械设备的运行和工作。
总之,传动轴是机械设备中非常重要的一种机械元件,其设计和应用涉及到材料选择、强度计算、匹配设计和制造工艺等方面的因素。
传动轴的设计需要考虑到所传递的动力和扭矩的大小,以确保传动系统的正常运行和工作。
传动轴的应用范围非常广泛,主要用于汽车、船舶、工程机械等领域。
传动轴的合理设计和应用可以提高机械设备的性能、可靠性和经济性。
传动轴和万向节设计
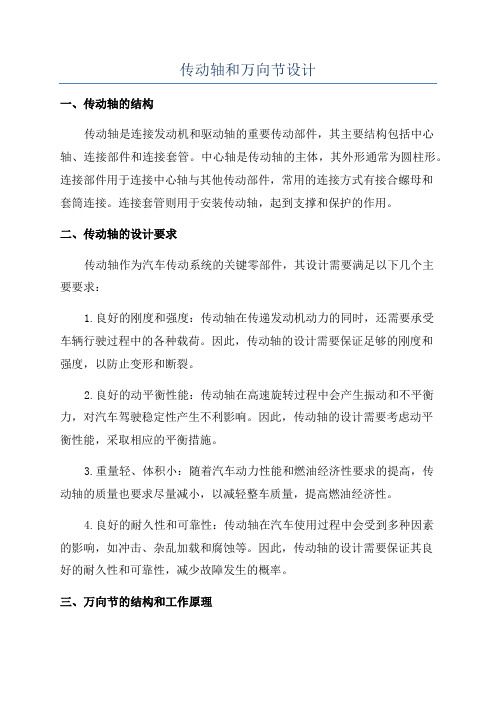
传动轴和万向节设计一、传动轴的结构传动轴是连接发动机和驱动轴的重要传动部件,其主要结构包括中心轴、连接部件和连接套管。
中心轴是传动轴的主体,其外形通常为圆柱形。
连接部件用于连接中心轴与其他传动部件,常用的连接方式有接合螺母和套筒连接。
连接套管则用于安装传动轴,起到支撑和保护的作用。
二、传动轴的设计要求传动轴作为汽车传动系统的关键零部件,其设计需要满足以下几个主要要求:1.良好的刚度和强度:传动轴在传递发动机动力的同时,还需要承受车辆行驶过程中的各种载荷。
因此,传动轴的设计需要保证足够的刚度和强度,以防止变形和断裂。
2.良好的动平衡性能:传动轴在高速旋转过程中会产生振动和不平衡力,对汽车驾驶稳定性产生不利影响。
因此,传动轴的设计需要考虑动平衡性能,采取相应的平衡措施。
3.重量轻、体积小:随着汽车动力性能和燃油经济性要求的提高,传动轴的质量也要求尽量减小,以减轻整车质量,提高燃油经济性。
4.良好的耐久性和可靠性:传动轴在汽车使用过程中会受到多种因素的影响,如冲击、杂乱加载和腐蚀等。
因此,传动轴的设计需要保证其良好的耐久性和可靠性,减少故障发生的概率。
三、万向节的结构和工作原理万向节用于连接传动轴和车轮之间,是一种能够在不同角度下实现传动的装置。
常见的万向节结构有三个球式和常角度式两种。
其中,三个球式万向节是一种可以实现任意角度传动的结构,由两个内圈、两个外圈和三个转动球组成。
常角度式万向节则适用于需要固定角度传动的场合,常用于前驱汽车。
万向节的工作原理是通过球和轴之间的球座和滚道实现传递动力。
当传动轴转动时,球会在轴上转动,通过球面与内圈、外圈的滚道接触传递动力。
相对于三个球式万向节,常角度式万向节的结构相对简单,其工作原理类似。
四、常见问题及解决方法1.传动轴产生振动:造成传动轴振动的原因有很多,可能是由于不平衡、轴材质问题或连接部件松动等原因。
解决方法可以是进行动平衡修正或更换质量较好的传动轴。
汽车传动轴设计

目录摘要 (2)第一章概述 (3)1万向传动轴设计要求 (3)第二章万向节结构方案分析 (3)1万向节分为刚性万向节和挠性万向节 (3)2准等速万向节 (4)3等速万向节 (5)第三章万向传动的运动和受力分析 (6)1单十字轴万向节传动 (6)2双十字轴万向节传动 (8)第四章传动轴结构分析与设计 (9)1轴的结构设计 (10)2轴的强度验算 (11)3键的选择 (12)4验算轴承寿命 (12)第五章结束语 (16)第六章参考文献 (17)第七章致谢信 (17)【摘要】:在普通优化设计的基础上,根据可靠性设计准则,将空心传动轴的应力及强度视为随机变量,建立起空心传动轴的可靠性优化设计模型,结合实例说明可靠性优化设计方法比传统设计方法更可靠、经济。
从机械振动理论出发,用可靠性设计中的联结方程,得出了其在常用工况下按传动轴的临界转速进行可靠性设计的公式.并以实例对传动轴按上述准则进行可靠性设计,结果传动轴的重量比原设计减少了436%,可靠性达到0.9999876以上.【关键词】: 万向节万向节传动轴第一章概述万向传动轴一般是由万向节、传动轴和中间支承组成。
主要用于在工作过程中相对位置不断改变的两根轴间传递转矩和旋转运动。
万向传动轴设计应满足如下基本要求:1.保证所连接的两根轴相对位置在预计范围内变动时,能可靠地传递动力。
2.保证所连接两轴尽可能等速运转。
3.由于万向节夹角而产生的附加载荷、振动和噪声应在允许范围内。
4.传动效率高,使用寿命长,结构简单,制造方便,维修容易等。
变速器或分动器输出轴与驱动桥输入轴之间普遍采用十字轴万向传动轴。
在转向驱动桥中,多采用等速万向传动轴。
当后驱动桥为独立的弹性,采用万向传动轴。
第二章万向节第结构方案分析第一节万向节分为刚性万向节和挠性万向节。
刚性万向节可分为不等速万向节(如十字轴式)、准等速万向节(如双联式、凸块式、三销轴式等)和等速万向节(如球叉式、球笼式等)。
五十铃货车传动轴设计
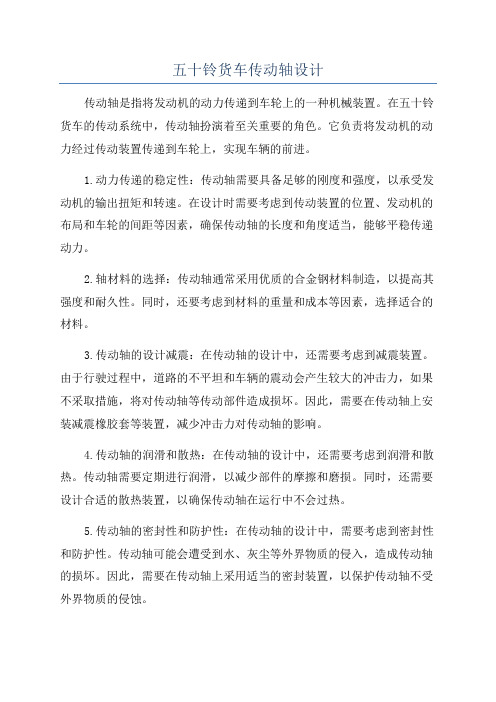
五十铃货车传动轴设计
传动轴是指将发动机的动力传递到车轮上的一种机械装置。
在五十铃货车的传动系统中,传动轴扮演着至关重要的角色。
它负责将发动机的动力经过传动装置传递到车轮上,实现车辆的前进。
1.动力传递的稳定性:传动轴需要具备足够的刚度和强度,以承受发动机的输出扭矩和转速。
在设计时需要考虑到传动装置的位置、发动机的布局和车轮的间距等因素,确保传动轴的长度和角度适当,能够平稳传递动力。
2.轴材料的选择:传动轴通常采用优质的合金钢材料制造,以提高其强度和耐久性。
同时,还要考虑到材料的重量和成本等因素,选择适合的材料。
3.传动轴的设计减震:在传动轴的设计中,还需要考虑到减震装置。
由于行驶过程中,道路的不平坦和车辆的震动会产生较大的冲击力,如果不采取措施,将对传动轴等传动部件造成损坏。
因此,需要在传动轴上安装减震橡胶套等装置,减少冲击力对传动轴的影响。
4.传动轴的润滑和散热:在传动轴的设计中,还需要考虑到润滑和散热。
传动轴需要定期进行润滑,以减少部件的摩擦和磨损。
同时,还需要设计合适的散热装置,以确保传动轴在运行中不会过热。
5.传动轴的密封性和防护性:在传动轴的设计中,需要考虑到密封性和防护性。
传动轴可能会遭受到水、灰尘等外界物质的侵入,造成传动轴的损坏。
因此,需要在传动轴上采用适当的密封装置,以保护传动轴不受外界物质的侵蚀。
综上所述,五十铃货车传动轴的设计需要综合考虑动力传递的稳定性、轴材料的选择、传动轴的减震、润滑和散热、密封性和防护性等多个因素。
只有在满足这些要求的前提下,才能设计出性能稳定、耐用可靠的传动轴。
- 1、下载文档前请自行甄别文档内容的完整性,平台不提供额外的编辑、内容补充、找答案等附加服务。
- 2、"仅部分预览"的文档,不可在线预览部分如存在完整性等问题,可反馈申请退款(可完整预览的文档不适用该条件!)。
- 3、如文档侵犯您的权益,请联系客服反馈,我们会尽快为您处理(人工客服工作时间:9:00-18:30)。
汽车传动轴设计一、任务分析根据传动轴的工作环境要求,在考虑传动轴的长度和断面尺寸时,应考虑是传动轴有足够高的临界转速,尺寸参数(长度、截面尺寸)和材料,考虑到空心的传动临界速度比实心要大,且省材料,所以都做成空心的…… 等等如此各方面的因素,利用优化设计理论和方法进行汽车传动轴的设计。
二、用优化的方法设计传动轴 2.1 设计变量其变量有:D 、d 、S 、L 、L ˊ、α1、α2D 、d —传动轴轴管的外径和内径,S —传动轴截面积,L —传动轴长度 L ˊ—所需传动距离,α1、α2—如图1.1所示夹角 其中α1、α2、 L ˊ均取决于汽车整体框架的设计, 对同一辆车而言L 一定, S 取决于D 、d , 即: )(422d D S -=π………………………………①按照优化设计思想,取相对独立的变量为设计变量,尽量减少设计变量个数。
因此:[]TTx x x d D S X 321,,,=⎥⎦⎤⎢⎣⎡=,2.2 确定目标函数一般来说,现在考虑得最多的是如何能够更省钱,所以可以考虑设目标是最省材料。
在汽车L 确定的情况下,所用的材料取决于S 。
接变速箱接后桥图1.1使S 的值在满足强度要求的情况下最小便成为了这次设计的目的。
即:)(4)(22d D x f -=π2.3 建立约束条件2.3.1传动轴应有足够高的临界转速临界转速:当传动轴的工作转速接近于其弯曲固有频率,即出现共振现象,所以通常将其弯曲固有频率对应的轴的速度称为临界转速。
若固有频率为f (Hz ) 则:k n =2πf rad/s=60 f r/minJ -抗弯惯性矩m kf π21=ρπLd D m ⋅-=)422(代入f 式,代入k n =60 f 整理后得2228102.1Ld D n k +⨯=设计传动轴时通常取0.2~2.1max=n n kn max -传动轴最高转速 m a x 222228353.152102.1n d D L d D n k ⋅≤+=+⨯=δ …………②δ—临界安全系数)(min x f 35384L EJ k =)(6444d D DJ -=π2.3.2传动轴应有足够的扭转强度设传动轴传递的最大转矩为Ts ,则截面上最大剪切应力[]τπτ≤-=⋅=)(16244max d D T D DI T s P s …………………………③ I p -极惯矩 32)(44d D I P -=π[]τ——许用应力,;2.3.3 传动轴应满足空心轴扭转失稳条件要求按最大扭转应力验算:2/3max )(292.0D d D E -≤τ……………………………………④E —传动轴材料的弹性模量,25/101.2mm N E ⨯=2.3.4 传动轴应满足制造工艺条件要求2.3≥-d D …………………………………………⑤ 2.3.5 传动轴外径尺寸不能过大可设 100≤D …………………………………………⑥ 根据以上的各条约束条件以及①式,可建立以下数学优化模型: []TTx x x d D S X 321,,,=⎥⎦⎤⎢⎣⎡=,)4)(min 22d D x f S -==(πmax 222228353.152102.1n d D L d D n k ⋅≤+=+⨯=δ[]τπτ≤-=⋅=)(16244max d D T D DI T s P s2/3max )(292.0Dd D E -≤τ 2.3≥-d D 100≤D三、优化算法的实现3.1优化设计理论优化设计方法是应用数学最优化远离解决实际问题的设计方法。
正对某一设计任务,以结构最合理,工作性能最佳,成本最低等为设计要求,在多种方案、多组参数、多种设计变量中确定主要设计变量的取值,使之满足最优设计要求。
在机械设计中,优化设计体现为最佳设计方案的确定和最佳参数的确定。
所谓优化设计,就是根据设计模型及初始设计参数,选定一种优化方法编出程序,上计算机算,求出优化参数及优化性能指标。
以我传动轴为例进行分析。
本设计的目标函数为二元函数,其函数值的大小及变化规律可用等值线画成一种直观的图形,可设为f(x1,x2)=C i 如此可得一系列平面曲线,这些曲线形象的表达了函数值大小变化的规律,并可最终得到函数的最小值点(即最优点)。
其极小化的择优过程,就是从X0点开始,按照一定的方向,以一定步长,一步一步地接近最优点,直到满足要求的条件为止。
3.2 优化方法的选用根据所列的数学优化模型条件可知,该问题唯一求解非线性有约束极小化问题。
故可以考虑选用优化设计中的复形法,这种算法是单形法的发展和改进,可用以求解非线性有约束极小化问题,并在一定程度上可以避免迭代过程中出现的退化现象。
对我的数学模型,复形法的择优基本思想大致为:(1)在确定初始设计X0的基础上,按一定的方法,共确定2n或n+2点,这些点必须都在设计可行域内。
(2)计算各点数值,并找出最大函数值对应的点X H。
(3)计算除点X H外的点集中心X c。
(4)联X H、X c并在其沿线上求出影射点。
(5)计算影射点X R的函数值,验算其是否满足全部约束。
如果不满足,可改变影射系数,直到全部满足,并达到f(X R)<f(X H)时止。
(6)然后用X R替换X H,构成新复形。
(7)重复以上有关步,直到满足收敛条件为止。
3.3 择优过程1)产生初始复形中的第一个点。
具体方法不限。
可取K=2n 个点,都应满足条件。
Kk n i a b a X i i ki i ki ,,2,1,,2,1)(⋅⋅⋅=⋅⋅⋅=-+=γ2)然后用伪随机数产生其它顶点,所得结果必须满足常量约束。
3)逐个检查各定点,然后构成复形。
检查上部所得点,是否全部满足不等式约束,满足则通过;如果不满足,则在以上所得基点上,再次沿X s 方向收缩一半,再次检查。
如此逐点反复检查,直到全部顶点满足为止。
4)计算函数值X H ,并找出点。
计算复形各顶点的函数值f(X k ),并找出函数值最大的点X H 。
5)计算出最大点X H 外的其余各顶点中心X c 。
hi X K X Ki i c ≠-=∑=,1116)求影射点αX 。
先检查X c 是否满足各不等式约束。
如已满足,则留;如不满足,则将α减半,在算出αX ,再次检查。
如此反复,直到满足为止。
)(H c c X X X X -+=αα7)计算影射点的函数值f(αX )。
并与最大点的函数值f(X H )比较。
如f(αX )< f(X H ):可用X a 替换X H 构成新的复形,然后转第四步。
如f(αX )≥ f(X H ):将影射系数a 再次减半,如果满足f(αX )< f(X H ),则转第四步。
否则,再将a 减半,直到满足或减至所设定的一小量ε为止,如还不满足,这以次坏点作最坏点,记作X SH 。
然后,再在X SH X c 连线的沿线上,求出影射点,即转第六步。
8)收敛判别。
反复执行以上过程,复形随之收敛,每次形成新复形时,皆应进行判别。
如:[]ε≤⎭⎬⎫⎩⎨⎧-∑=2/112)()(1K i ic X f X f K满足所选判别式时,可停算,所得计相对优化解。
收敛系数按要求精度确定。
3.4 优化程序试编以下为我试着用C 语言编写的一段优化约束的子程序:#include <math.h> #include <stdio.h> Main() { int n ,float pi=3.14159 , S(float d(n)) { double S;S=pi*(d(1)*d(1)-d(2)*d(2)); return S; }int cons(float d(n)) {if((d(1)<100)&&(d(1)-d(2)>=3.2)&&(squr(((d(1)-d(2)/d(1))^2)*0.292*2.1E5)&& ((16d(1)T)/(pi*(d(1)^4-d(2)^4))<=125)&&(152.353*squr(d(1)*d(1)+d(2)*d(2)))<=8000)) return 1 elsereturn 0 }或者也可以用matlab 等专用设计软件来进行优化程序的工作。
最后,如取初始值为:D=63.5mm , d=58.5mm , S=479.0932mmδ=2 ,n max =4000 r/min , mm N T s ⋅⨯=61002.1︰︰︰︰[]2τN=/125mm可得优化解为: D=59.34mm, d=56.14mm, S=290.25482mm ………………………………………………………………[]1四、总结这次完成汽车设计大作业,除了用到了汽车设计的内容,自学了优化设计的内容,另外用到的最多的就是机械设计方面的知识了。
适逢这学期做机械设计课程设计,感觉汽车设计大作业和机械设计课程设计的内容和过程大体一致,唯一不同的是,课程设计全过程中大部分的时间和精力都用在了校核各个零件的强度、刚度的上面;而通过做汽车设计大作业,学习了一点关于优化设计方面的内容,学到了利用计算机来代替繁重的脑力劳动,宠儿节省了设计的时间和出错的可能。
通过优化设计,我们在以后的设计中可以把更多的精力放在新工艺、新方法等的设计上。
由优化设计的方法进行机械的设计,这是这次作大作业收获最大的地方。
参考书目1.何献忠, 李萍等著,优化技术及其应用,北京:北京理工大学出版社,19952.张洪欣主编, 汽车设计, 北京:机械工业出版社,19993.张宝生, 李杰, 林明芳编著,汽车优化设计理论与方法,北京:机械工业出版社,20004.刘惟信, 孟嗣宗编著,机械最优化设计,北京:清华大学出版社,19865.刘惟信编著,机械最优化设计,北京:清华大学出版社,19946.[德]F·Schmelz, Graf V on H·-C·Seherr-Thoss, E·Aucktor 著,伍德荣,肖生发,陶建民译,万向节和传动轴,北京:北京理工大学出版社,1997。