湿法氟化铝煅烧系统的高温腐蚀与耐腐蚀材料
不同湿度下铝合金在化工腐蚀介质中的性能研究

不同湿度下铝合金在化工腐蚀介质中的性能研究在化工行业中,铝合金作为一种重要的材料被广泛应用。
然而,湿度对于铝合金在化工腐蚀介质中的性能有着重要影响。
本文将通过研究不同湿度下铝合金的性能来探讨湿度对其腐蚀行为的影响。
一、引言湿度是指空气中所含水分的含量,是影响材料性能的重要因素之一。
在化工生产中,高湿度环境会加速铝合金的腐蚀速度,从而降低其使用寿命。
因此,研究不同湿度下铝合金的性能对于提高化工设备的使用寿命具有重要意义。
二、实验方法1. 样品制备选取常用的铝合金材料作为研究对象,并按照一定的尺寸和形状制备样品。
2. 实验设备使用恒温恒湿箱以及相应的湿度控制装置,能够控制湿度在一定范围内。
3. 实验方案将制备好的铝合金样品分别放置在不同湿度环境下,记录相应的湿度值。
4. 性能测试采用相应的实验方法,如电化学方法、重量损失方法等,对铝合金样品在不同湿度下的腐蚀行为进行测试。
三、实验结果与讨论通过实验得到的数据进行分析与讨论,可以研究不同湿度下铝合金在化工腐蚀介质中的性能。
1. 腐蚀速率在不同湿度环境下,通过记录铝合金样品的重量变化,计算得到腐蚀速率。
结果显示,随着湿度的增加,铝合金的腐蚀速率也逐渐增加。
2. 腐蚀形貌通过扫描电子显微镜观察铝合金样品表面的腐蚀形貌,可以发现不同湿度下腐蚀产物的形成情况。
高湿度环境下,铝合金表面容易形成大量的氧化物,从而加速腐蚀。
3. 电化学性能通过电化学方法研究铝合金在不同湿度下的极化曲线、电化学阻抗等参数,可以了解其电化学性质的变化。
结果显示,湿度的增加会导致铝合金的极化曲线向正向偏移,电化学阻抗减小,表明铝合金在高湿度环境中更容易发生腐蚀。
四、影响因素分析1. 湿度实验结果表明,湿度是影响铝合金腐蚀的主要因素之一。
高湿度环境下,空气中的水分能够与铝合金发生反应,形成氧化物,加速腐蚀速率。
2. 温度温度也是影响铝合金腐蚀的因素之一。
通常情况下,湿度和温度是相互关联的,高温环境下湿度往往也较高。
氟化铝对切削液性能的影响

氟化铝对切削液性能的影响一、引言随着机械制造业的快速发展,切削液作为机械加工过程中不可缺少的环节,对于加工质量、加工效率以及机器设备的寿命有着至关重要的作用。
然而,一些不良的工业生产过程不可避免地会给切削液带来一定的污染。
氟化铝作为一种深受工业生产领域欢迎的复合添加剂,其对切削液性能的影响已经引起了越来越多研究人员的关注。
二、氟化铝的化学性质和应用1.氟化铝的化学性质氟化铝(AlF3)是一种难熔的化合物,具有很好的稳定性和抗腐蚀性。
在热水中能溶解,但在冷水中不溶。
氟化铝具有良好的氧化还原性,可以与金属氧化物反应生成金属和氟化物。
氧化性强,可以与硫酸铵和其他硫酸盐反应。
2.氟化铝的应用氟化铝作为深受工业生产领域欢迎的复合添加剂,其应用范围广泛,主要有以下几个方面:(1)金属电解工业:氟化铝作为铝熔体电解过程中不可缺少的添加剂,可以提高电极反应效率,减少电极极化,并可减少耗能。
(2)玻璃钢制品:氟化铝也是制造玻璃钢制品不可缺少的添加剂之一,可以提高玻璃钢的强度和硬度,并可以增加其耐磨性。
(3)铸造业:氟化铝在铸造工业中的应用也是比较广泛的,可以用作熔体捕铝剂、脱氧剂、脱硫剂以及合金成分调节剂等。
(4)切削液添加剂:氟化铝作为一种切削液添加剂,可以提高切削液的抗腐蚀性能和机械加工件表面质量,同时还可以减少切削液对机床、刀具及工件的腐蚀和磨损,增加其使用寿命。
三、氟化铝对切削液性能的影响1.氟化铝对切削液腐蚀性的影响研究表明,氟化铝能够显著提高切削液的抗腐蚀性能。
将氟化铝添加到切削液中,可以有效地降低切削液中的杂质含量,减少其对机械加工件的腐蚀和磨损。
同时,氟化铝具有良好的稳定性和耐腐蚀性,能够防止切削液在高温和高压下发生腐蚀反应,从而保护机床、刀具及工件的表面质量。
2.氟化铝对切削液摩擦性能的影响研究表明,氟化铝的添加可以显著改善切削液的摩擦性能。
在高速切削过程中,切削液对机械加工件表面的摩擦力越大,其表面热量也就越高,从而导致加工件表面的变形和磨损。
lifsi腐蚀铝 机理

lifsi腐蚀铝机理腐蚀是指金属在特定环境条件下与介质发生化学反应,导致金属表面发生破坏或改变的过程。
铝是一种常见的金属材料,但它在一些特定条件下容易受到腐蚀。
本文将讨论铝腐蚀的机理。
铝腐蚀的机理可以分为两种类型:一种是被动膜腐蚀,另一种是活性腐蚀。
被动膜腐蚀是指铝与氧气在空气中发生反应,形成一层非晶态氧化铝(Al2O3)膜,该膜可以防止继续的腐蚀。
这种膜具有一定的稳定性和防护性能,因此铝在大多数常见环境中是相对耐腐蚀的。
该膜的厚度通常为几纳米至几十纳米,但可以随着环境和条件的不同而有所变化。
然而,在一些特殊环境下,被动膜会被破坏,从而导致铝的活性腐蚀。
活性腐蚀是指铝表面的被动膜被破坏或未能形成,从而使铝直接与介质发生反应。
活性腐蚀一般发生在一些极端酸性或碱性介质中,例如浓硝酸、浓氢氟酸和氢氧化钠溶液。
在这些介质中,铝的表面会发生水解反应,生成氢气和相应的氢氧化物或氧化物。
这会破坏铝材料的内部结构,导致严重的腐蚀。
活性腐蚀的速度受到一系列因素的影响。
首先是介质的酸碱性和浓度。
一般来说,酸性介质会导致更快的腐蚀速度,而碱性介质会减缓腐蚀速度。
其次是温度。
高温下,腐蚀反应的速度会加快。
此外,金属的纯度、表面处理和应力等因素也会影响铝的腐蚀程度。
在工业中,我们可以采取一些措施来减少铝的腐蚀。
一种常见的方法是在铝表面涂覆一层保护性的涂层,例如电镀或喷涂。
这层涂层可以提供一层保护膜,防止铝直接与介质接触,从而减缓腐蚀速度。
另一种方法是选择合适的铝合金。
一些特殊的铝合金具有更高的抗腐蚀性能,可以在一些相对恶劣的环境下使用。
总之,铝腐蚀的机理是一个复杂的过程,包括被动膜腐蚀和活性腐蚀两种类型。
被动膜能够提供一定的防护,但在一些特殊环境下会被破坏,导致铝的活性腐蚀。
腐蚀速度受到介质的酸碱性、浓度、温度以及金属的纯度和应力等因素的影响。
在实际应用中,可以通过涂层或选择抗腐蚀性能更好的合金来减少铝的腐蚀。
湿法脱硫装置腐蚀环境及材料选用
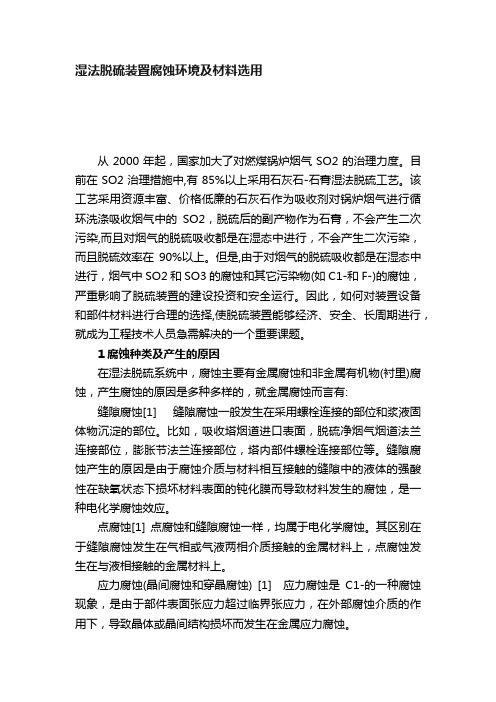
湿法脱硫装置腐蚀环境及材料选用从2000年起,国家加大了对燃煤锅炉烟气SO2的治理力度。
目前在SO2治理措施中,有85%以上采用石灰石-石膏湿法脱硫工艺。
该工艺采用资源丰富、价格低廉的石灰石作为吸收剂对锅炉烟气进行循环洗涤吸收烟气中的SO2,脱硫后的副产物作为石膏,不会产生二次污染,而且对烟气的脱硫吸收都是在湿态中进行,不会产生二次污染,而且脱硫效率在90%以上。
但是,由于对烟气的脱硫吸收都是在湿态中进行,烟气中SO2和SO3的腐蚀和其它污染物(如C1-和F-)的腐蚀,严重影响了脱硫装置的建设投资和安全运行。
因此,如何对装置设备和部件材料进行合理的选择,使脱硫装置能够经济、安全、长周期进行,就成为工程技术人员急需解决的一个重要课题。
1腐蚀种类及产生的原因在湿法脱硫系统中,腐蚀主要有金属腐蚀和非金属有机物(衬里)腐蚀,产生腐蚀的原因是多种多样的,就金属腐蚀而言有:缝隙腐蚀[1] 缝隙腐蚀一般发生在采用螺栓连接的部位和浆液固体物沉淀的部位。
比如,吸收塔烟道进口表面,脱硫净烟气烟道法兰连接部位,膨胀节法兰连接部位,塔内部件螺栓连接部位等。
缝隙腐蚀产生的原因是由于腐蚀介质与材料相互接触的缝隙中的液体的强酸性在缺氧状态下损坏材料表面的钝化膜而导致材料发生的腐蚀,是一种电化学腐蚀效应。
点腐蚀[1] 点腐蚀和缝隙腐蚀一样,均属于电化学腐蚀。
其区别在于缝隙腐蚀发生在气相或气液两相介质接触的金属材料上,点腐蚀发生在与液相接触的金属材料上。
应力腐蚀(晶间腐蚀和穿晶腐蚀) [1] 应力腐蚀是C1-的一种腐蚀现象,是由于部件表面张应力超过临界张应力,在外部腐蚀介质的作用下,导致晶体或晶间结构损坏而发生在金属应力腐蚀。
2湿法脱硫系统的腐蚀状况在湿法脱硫系统中,腐蚀环境随介质参数的变化以及不同的运行方式而不同,湿法脱硫系统的腐蚀参数见表1。
3材料的选用在烟气脱硫装置中,防腐蚀材料选择的影响因素主要有:使用环境温度、材料选择的影响因素主要有:使用环境温度、材料使用部位pH 值、C1-浓度(包括可溶性F-浓度)以及耐磨性能等。
各类材料湿法腐蚀的溶液配比及腐蚀速率

腐蚀条件
水浴30℃以上 常温 常温 常温 常温 冰点下腐蚀 冰点下腐蚀 常温 常温 常温 常温 冰点下腐蚀 常温 冰点下腐蚀
腐蚀方式
从中间到边缘
从边缘到中间
腐蚀速率
1000A/25s
5000A/45s 4000A/2min30s 500A/10s 5000A/15s+15s先慢后快 2000A/1min40s 3000A/50s 5000A/2min30s-3min
配比
KOH:H2O:IPA=1:4:1 HF:NH4F:H2O=3:6:10 H3PO4(HF):H2O H3PO4:HNO3:H2O=20:2:5 I2:KI:H2O=1:4:10 HCl:HNO3:H2O=3:1:2 CH3OH:H3PO4:H2O2=3:1:1 HCl:H2O:NH4F=20:60:1 HCl:H2O=3:1 HF:NH4F:H2O=3:6:10 HNO3:H2O=2:1 HCl:H2O=1:10 HCl:H2O=2:1 HCl:Ch3COOH:H2O2=7:14:1
湿法腐蚀各材料溶液配比、 湿法腐蚀 湿法腐蚀各材料溶液配比、2) 玻璃 铝 金(Au) 磷化镓 砷化镓 钛 ITO 氮氧化硅 镍 锌 镓铟磷 铝镓铟磷
所用溶剂
氢氧化钾、异丙醇 氢氟酸、氟化铵 磷酸或氢氟酸 酸性:磷酸、硝酸 碘化钾(固体)、碘(固体) 盐酸、硝酸 醋酸、磷酸、双氧水 盐酸、氟化铵 盐酸 氢氟酸、氟化铵 硝酸 盐酸 盐酸 盐酸、醋酸、双氧水
铝表面氟化工艺

铝表面氟化工艺引言:铝是一种常见的金属材料,具有良好的导电性、导热性和耐腐蚀性。
然而,铝的表面易受到氧化和腐蚀的影响,降低了其使用寿命和性能。
因此,为了增强铝材料的耐腐蚀性和表面硬度,提高其使用寿命,铝表面氟化工艺应运而生。
一、铝表面氟化工艺的原理铝表面氟化是通过在铝表面形成一层氟化物膜来提高其耐腐蚀性和硬度。
氟化物膜主要由氟化铝和氧化铝组成,形成了一种致密的保护层,有效隔绝了铝与外界环境的接触,防止了氧化和腐蚀的发生。
二、铝表面氟化工艺的步骤1. 表面处理:首先,对铝表面进行清洗,去除表面的油污、灰尘和氧化物等杂质。
常用的清洗方法有碱洗、酸洗和机械打磨等,确保铝表面干净无污染。
2. 预处理:将清洗后的铝材料浸泡在预处理溶液中,如硝酸、氢氟酸等,以便进一步去除氧化物和提高铝表面的反应活性。
3. 氟化处理:将经过预处理的铝材料浸泡在氟化处理溶液中,溶液中一般包含氟化盐和一些活性添加剂。
在适当的温度和时间下,铝材料表面与氟化处理溶液发生反应,生成氟化物膜。
4. 氯化处理:有时为了进一步提高铝材料的耐腐蚀性能,可以将铝材料浸泡在氯化处理溶液中,以增加氟化物膜的厚度和致密性。
5. 清洗和干燥:将氟化处理后的铝材料进行清洗,去除残留的处理液和杂质,然后进行干燥处理,使铝材料表面干燥无水滴。
三、铝表面氟化工艺的优点1. 提高耐腐蚀性:铝表面氟化形成的氟化物膜具有良好的耐腐蚀性,能够有效隔绝铝与外界环境的接触,防止氧化和腐蚀的发生。
2. 增强硬度:氟化物膜的硬度较高,可以提高铝材料的表面硬度,增强其抗刮擦和抗磨损能力。
3. 改善润滑性:氟化物膜表面具有较低的摩擦系数和较好的润滑性,有助于减少铝材料的摩擦损失和磨损。
4. 美观耐用:经过氟化处理的铝材料表面光滑、均匀,具有一定的装饰效果,同时耐久性也得到了提高。
四、铝表面氟化工艺的应用领域铝表面氟化工艺广泛应用于航空航天、汽车制造、电子电器、建筑装饰等领域。
在航空航天领域,铝材料作为航空器的重要结构材料,其耐腐蚀性和耐磨损能力的提高对于保证航空器的安全和可靠性至关重要。
氟化铝的生产工艺

氟化铝的生产工艺(总2页)--本页仅作为文档封面,使用时请直接删除即可----内页可以根据需求调整合适字体及大小--氟化铝产品的生产工艺一、湿法生产工艺(属淘汰工艺):硫酸和萤石高温反应后产生的气体,直接吸收成30%~ 35%的氢氟酸,与氢氧化铝在90℃左右合成为AlF3?3H2O,经过滤后,进入高温脱水干燥,最后得氟化铝AlF3成品。
由于脱水时产生的水蒸汽回分解AlF3,因此,湿法氟化铝含量低,杂质多,水份含量高,堆密度低,流动性差。
基本上不适应现代电解槽使用。
化学指标为:F≥57%Al≥28% Na≤ %H2O≤7%。
二、干法生产工艺(干法氟化铝):1、粗酸干法:硫酸和萤石高温反应后产生的气体,经过粗洗后进入流化床,与干燥后的氢氧化铝反应,在高温下生成氟化铝。
由于粗洗后的氟化氢含量约96%,杂质较高,氟化铝产品的杂质也就比较高;特别是没有脱硅,使得氟化铝产品的二氧化硅含量达到%。
这些杂质会影响电解铝的质量,增加电解时的电耗。
F≥61%Al≥30%Na≤%H2O≤%SiO2≤%P2O5≤%Fe2O3≤%SO42-≤%2、精酸干法:硫酸和萤石高温反应后产生的气体,经过粗洗、冷冻、脱气、精馏后进入蒸发器,此时氟化氢的含量一般为%;蒸发出的氟化氢气体(含量接近100%)进入流化床,与湿氢氧化铝反应,在高温下生成氟化铝。
由于氟化氢纯度高,这样生产的氟化铝质量很好,杂质很低,特别是二氧化硅含量只有%,五氧化二磷含量只有%,对电解铝的生产非常有利。
F≥62%Al≥32%Na≤%H2O≤%SiO2≤%P2O5≤%Fe2O3≤% SO42-≤%氟化铝,Aluminum fluoride 分子式:AlF3 分子量:性状:白色晶体或粉末。
25 ℃时的相对密度,微溶于水、酸及碱溶液,不溶于大部分有机溶剂,在氢氟酸溶液中有较大的溶解度。
无水氟化铝性质非常稳定;与液氨甚至与浓硫酸加热至发烟仍不起反应,与氢氧化钾共熔无变化,也不被氢气还原,加热不分解,但升华,升华温度1291℃。
氟化铝加压结晶工艺技术研究探析

[1]郝建堂.氟化铝加压结晶工艺技术研究探析[J].无机盐工业,2019,51(09):57-60.
[2]刘海霞.氟硅酸综合利用工艺技术研究进展[J].无机盐工业,2017,49(03):9-13.
[3]王世海.300kA铝电解槽工艺技术条件优化与新控制技术开发[D].中南大学,2008.
表4不同加料温度制备氟化铝的产品质量
结束语
通过优化液相法制备氟化铝的加压结晶工艺,不仅可以制备出产品质量好、表观密度高、结晶水含量低的氟化铝产品,而且缩短了产品制备周期,提高了装置生产能力,保证了产品的清洁同时,利用该工艺开发的高性能无机氟副产品低品位磷肥氟资源,不仅大大降低了生产成本,而且节约了萤石资源,实现低品位资源的高效综合利用,有效保障磷化工、氟化工和铝电解工业协调、健康、稳定发展,是未来氟化铝工业发展的必然选择。
表3不同结晶时间所得母液中氟化铝的质量浓度
3.3.4加料温度对氟化铝产品质量的影响
取氟硅酸溶液加入反应槽中,开启搅拌,加热升温至不同的温度。按照氟硅酸和氢氧化铝物质的量比为1.1∶1快速加入氢氧化铝原料,投料后于95~105℃反应30min,过滤得到氟化铝溶液和硅胶沉淀。将氟化铝溶液按照优化后的结晶工艺条件进行结晶实验(结晶温度为170℃,维持结晶压力为0.7MPa,结晶时间为3h,晶种加入量为15%),对比不同加料温度对氟化铝产品质量的影响,结果见表4。由表4可知:投加原料时的温度越高,合成得到氟化铝的表观密度越大,产品颗粒越大,其附着水含量越低;对比煅烧前后氟化铝的表观密度发现,煅烧后氟化铝的表观密度相对降低,说明在煅烧过程中,有晶体受热破裂现象。实验结果表明,投加原料的温度应控制在70~80℃,氟化铝煅烧过程应匀速缓慢升温。
2.氟化铝生产工艺
- 1、下载文档前请自行甄别文档内容的完整性,平台不提供额外的编辑、内容补充、找答案等附加服务。
- 2、"仅部分预览"的文档,不可在线预览部分如存在完整性等问题,可反馈申请退款(可完整预览的文档不适用该条件!)。
- 3、如文档侵犯您的权益,请联系客服反馈,我们会尽快为您处理(人工客服工作时间:9:00-18:30)。
.
热尾气 中微 量 的强 Hale Waihona Puke 蚀 介 质 H F, 。
S 姚i
凡 在 锻烧窑
S 凡 氏i
1
和
HF
的腐 蚀
F
一
进料段 也可 能有一 部分 被冷 的 湿结 晶 (含 水 8 % )吸 收 而成 为 新 的 强 腐 蚀 介 质
,
.
低 温 湿物料 中
的腐蚀
lA 凡
3姚 O 湿料 由进 料 溜槽 加入 窑 内
.
M 〔
e
F 〕 络 合物
一
,
破 坏 了 不 锈钢 的钝 化过 程 使 其 在
。
,
装 置 是 国 内 首次 引 进 奥 地 利
化 铝生产 工 艺
、 , 。 ,
CHE MI E
J I
N Z 湿法氟
钝 化 状 态 下 继 续 被 溶 解 破坏 态 F
一
。
湿 物料 中大量 的 游离
,
其 中 氟 化铝 锻烧 系统 经 过 国 际招
M IE L IN z 湿
法 氛 化 铝 生 产 工 艺 中锻 烧 系统 的 高 温 腐蚀 特 征 耐蚀 合 金 的 选 择要 点 两 种 耐 蚀 合 金 做 结 构 材 料 的 有 关
性能
、
试验 结 果 和 使 用 简 况
。
关键 词
湿 法 氛化 铝
腐独
结 构 材料
湖北 某 工程 3 O t / d ( 9 6 % 一 9 6 8 % A I3 F )氟 化铝
,
藉窑 内
、
1
.
2
晶间腐蚀 奥 氏 体 不锈 钢 发 生 晶 间 腐 蚀 时 合 金 晶粒 间 的 结
,
螺旋 导 料 板 进 人 干 燥 段 在 抄 板 作 用 下 不 断 地 散 布
翻 动 湿料 进 行 热 量 传 递
, 。
A凡 l
,
3玩 O 湿 结 晶 进 料 温
一
合力 已 被 破 坏 产 生 晶 界 裂 纹 在 没 有 荷 载 或 外 力 作
19 9 8 年 第 2 期
硫磷设 计
湿 法 氟 化 铝 缎烧 系 统 的 高温 腐蚀 与 耐 腐 蚀 材 料
高
(南 化 集 团设 计 院
波
2 南京 市 1
0 0 4) 8
摘
J
要
湿 法 氛 化 铝 燃 烧 系统 是 一 个 腐 蚀 因 素 复 杂 的 化 工 系统 阐 述 奥 地 利 C
, ,
,
E H
+
0 3
℃ 脱 除 物 理 水和 2
.
.
5践O
(结 晶 水 )
。
,
3眺 O HF
水 解产 物
出锻 烧 窑
。
一 气 体 作 为 强 腐 蚀 介 质 存 在 于 锻烧
,
个
2 A1 3 O
十
6 HF
个
(4 )
在 锻 烧段 约 5 8 0
3践 0
,
℃ 脱去 0 5 H 2 O (结 晶 水 )
窑 转 筒 内 的 干燥 尾 气 中 由 高 温 段 经 干 燥 段 逆 流 排
15 0
:
以 磷 酸 生 产 中 回收 的 氟 硅 酸 和 氢 氧 化 铝 为 原 料 制 取
氟 化铝 的 生 产 技 术 其 生 产 过 程 由 化 学 反 应 脱 硅
结晶和 l A马
3践 O 分 离
、
,
、
、
干燥 锻 烧 冷 却 等 组 成
, ,
、
。
+ 2 挂 个 ( ) l 一 践 坟 践 个( ) 犯 峨 一 印 ℃ F :0 践 3 月民 (3 ) 残 个 一 随着脱 水温度 的提 高 产 品 中微 量 的 氟 化铝 高 温 水
。
均 匀 腐 蚀 属 强 腐蚀 介 质
1
.
2
干 燥尾 气 中 H F 的 腐 蚀
3 H ZO 湿 结 晶 ( 含 水 8 % ) 在 1 1 0
,
A I凡
,
℃ 脱去物
媛 烧 系统 的腐 蚀 特 性
奥地 利 C H E M I E I N Z 湿法 氟化铝 生 产 工 艺是 l
理水 而结 晶 水 的 脱 除 是 个 化 学 过 程 其 主 要 反 应 为
C于 E MI I E
,
能 极 大 地 增 加 钝 化 状 态 下 合 金 的 腐 蚀 并 降低
F: 3 H ZO 湿 结 晶被逐 渐地 加热
, 、 ,
标 评标 优先 采 用 拥 有 化铝 工 业 的 当 代 水 平
, , 。
I L
N Z 技术 德国
、
合 金 的 钝 化能 力 I A 度
1
.
BA K 设 计 制造 的 锻 烧 系 统 它 代 表 着 世 界 ] 以X X 二
用下而机 械损坏 金 属 材料 因 此 而 发生 粉碎性 组 织 损 伤 丧 失 机 械 强 度 造 成 设 备 零 件 的脆 碎 或 脆 裂
, , 。 ,
,
,
度 为 30 ℃ 介 质 中腐 蚀性 离 子 F
对合金材料中的
e F
、
C
r
具 有 较 大的 亲 和力
同 它们 形成 稳 定 的
硫磷 设 计
:
锻烧 系 统 的 高 温 腐 蚀 主 要 由 三 部 分 组 成 湿 月凡
1 1
.
高 温时 含水 量高 的
HF
、
气 体对 不 锈 钢 和
。
S 凡 和干燥尾气 中的 结 晶中的 玫i
、 。
HF
合 金 的 腐蚀 要 比 含 水 量 低
的 I开 气 体 更 大
、
另外
,
腐蚀 晶 间 腐蚀 和 高 温 腐 蚀 ( 氧 化 硫 化 )
间 构 成 了燃 烧 炉 ( 燃 料 为 轻 柴 油 ) 炉内的
4
,
一
内 而 且 在 腐 蚀性 介质 中 长 期 使用 时 或 长 期 高温 使 用 后 经 缓 慢 冷 却 再 在 一 定 的 腐 蚀 性 介 质 中使 用 都
℃ 0 7 AI
.
月凡 3 玲 。
月B
0 7 H ZO 0 5
3
O
O
O
+
.
0 2
O
2
5
一以 飞1
5
O
十
0 5
O
,
过 滤 后 的 川 凡 3 坟 O 湿 料 加 入 锻 烧 窑 用 间 接 加热 的方 法 除 去 8 % 的 游 离 水 和 结 晶 水 的干燥 段约 2 即在 缎 烧 窑 内
解
,
6 0 0 t 二 ZA IF 3
1
.
1 9 9 8 年第 2 期
, 、 。
2
.
1
温 度 对脆 裂 的 影 响
,
筒 其 中 干 燥段 长 s m 缎 烧 段 长 1 3 m
,
干 燥 段 和锻
0 0 ℃ 的 敏 化 温 度范 围 奥 氏 体 不 锈 钢 在 40 0 一 9
烧 段 滚 筒 外 均 设 置 外 套 筒 锻 烧 段 的 外套 筒 与 滚 筒
氟
F
脱 水 在 高浓
影 响该 系统 的 腐 蚀 因素 众
,
一
和 加 热 的 共 同作 用 下 对 金 属 表 面 产 生 很 强 的
, 。
多 本 文 从 高 温 腐蚀 特 点 出 发 就 奥 氏 体 不 锈 钢 和 合 金 的 特 点 讨 论 有 关 的 金 属 元 素 对 该 系 统 耐 腐蚀 结 构 材料 的影 响及 国外 所选用 的材料 1