高速加工技术现状及发展趋势
我国机械加工技术的现状与发展的建议
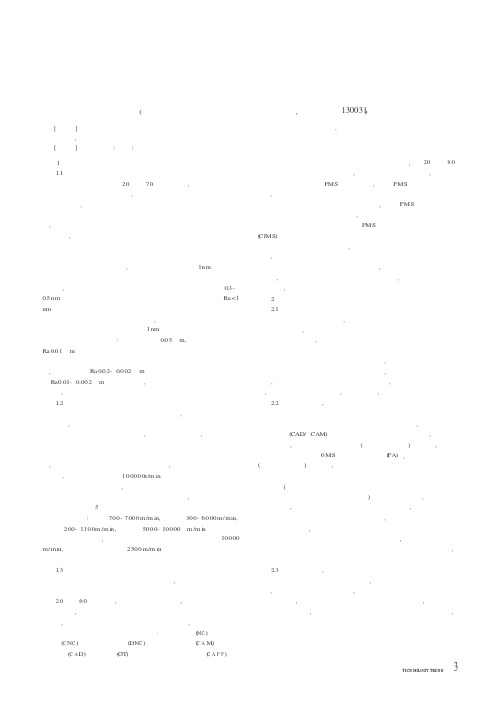
T NOLO GY TR N D1我国机械加工技术的发展现状和趋势1.1我国机械加工技术向着精密超精密性发展精密和超精密加工是在20世纪70年代提出的,在西方工业发达国家得到了高度重视和急速发展,在尖端技术和现代武器制造中占有非常重要的地位,是机械制造业最主要的发展方向之一。
精密和超精密加工在提高机电产品的性能、质量和发展高新技术中起着至关重要的作用,已成为在国际竞争中取得成功的关键技术。
目前,精密和超精密加工已在光电一体化设备仪器、计算机、通信设备、航天航空等工业中得到广泛应用。
在许多高新技术产品的设计中已大量提出微米级、亚微米级及纳米级加工精度的要求。
当前超精密加工的最高精度已达到了纳米,出现了纳米加工。
例如1nm 的加工精度已在光刻机透镜等零件的生产中实现。
随着超大规模集成电路集成度的增加,生产这种电路光刻机透镜的形位误差加工精度将达到0.3-0.5nm 。
人造卫星仪表轴承的孔和轴的表面粗糙度要求达到Ra <1nm 。
某些发动机的曲轴和连杆的加工精度要求也达到微米、亚微米。
目前超精密切削技术和机床的研究,也取得了许多重要成果。
用金刚石刀具和专用超精密机床可实现1nm 切削厚度的稳定切削。
中小型超精密机床达到的精度:主轴回转精度0.05μm ,加工表面粗糙度Ra 0.01μm 以下。
最近新发展的金属结合剂砂轮的在线电解修整砂轮的镜面磨削技术,可以加工出Ra 0.02-0.002μm 的镜面。
精密研磨抛光可以加工出Ra0.01-0.002μm 的镜面。
目前,量块、光学平晶、集成电路的硅基片等,都是最后用精密研磨达到高质量表面的。
1.2我国机械加工技术向着高速超高速加工的方向发展切削加工是机械加工应用最广泛的方法之一,而高速是它的重要发展方向,其中包括高速软切、高速硬切削、高速干切削、大进给切削等。
高速切削能大幅度提高生产效率,改善加工表面质量,降低加工费用。
高速超高速加工是伴随着高速主轴、高速加工机床结构、高速加工刀具及其润滑系统的不断改进而发展起来的。
试论数控高速切削加工技术的发展与应用研究
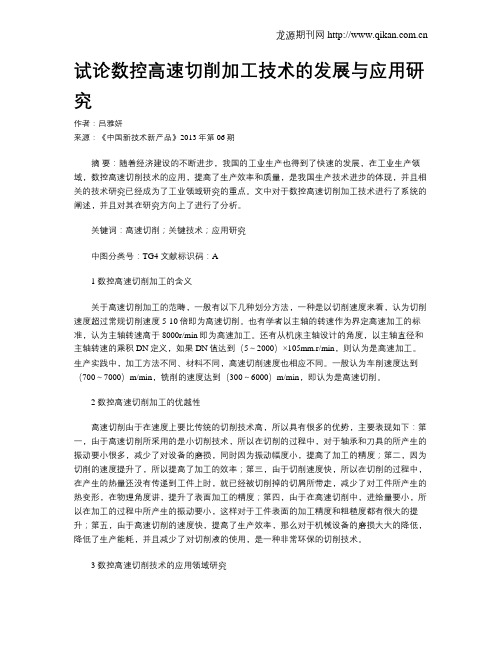
试论数控高速切削加工技术的发展与应用研究作者:吕雅妍来源:《中国新技术新产品》2013年第06期摘要:随着经济建设的不断进步,我国的工业生产也得到了快速的发展,在工业生产领域,数控高速切削技术的应用,提高了生产效率和质量,是我国生产技术进步的体现,并且相关的技术研究已经成为了工业领域研究的重点。
文中对于数控高速切削加工技术进行了系统的阐述,并且对其在研究方向上了进行了分析。
关键词:高速切削;关键技术;应用研究中图分类号:TG4 文献标识码:A1 数控高速切削加工的含义关于高速切削加工的范畴,一般有以下几种划分方法,一种是以切削速度来看,认为切削速度超过常规切削速度5-10倍即为高速切削。
也有学者以主轴的转速作为界定高速加工的标准,认为主轴转速高于8000r/min即为高速加工。
还有从机床主轴设计的角度,以主轴直径和主轴转速的乘积DN定义,如果DN值达到(5~2000)×105mm.r/min,则认为是高速加工。
生产实践中,加工方法不同、材料不同,高速切削速度也相应不同。
一般认为车削速度达到(700~7000)m/min,铣削的速度达到(300~6000)m/min,即认为是高速切削。
2 数控高速切削加工的优越性高速切削由于在速度上要比传统的切削技术高,所以具有很多的优势,主要表现如下:第一,由于高速切削所采用的是小切削技术,所以在切削的过程中,对于轴承和刀具的所产生的振动要小很多,减少了对设备的磨损,同时因为振动幅度小,提高了加工的精度;第二,因为切削的速度提升了,所以提高了加工的效率;第三,由于切削速度快,所以在切削的过程中,在产生的热量还没有传递到工件上时,就已经被切削掉的切屑所带走,减少了对工件所产生的热变形,在物理角度讲,提升了表面加工的精度;第四,由于在高速切削中,进给量要小,所以在加工的过程中所产生的振动要小,这样对于工件表面的加工精度和粗糙度都有很大的提升;第五,由于高速切削的速度快,提高了生产效率,那么对于机械设备的磨损大大的降低,降低了生产能耗,并且减少了对切削液的使用,是一种非常环保的切削技术。
高速加工的发展及其关键技术

除 率 、 工 精 度 和 加 工 质 量 的 现 代 加 工 技 术 。 随 加 着 高 速 机床 与 高 速 刀 具 相 继 出 现 , 速 加 工 在 航 高 空 、 天 、 车 等 行 业 得 到 了 广 泛 应 用 , 产 生 了 航 汽 并
巨大 的经 济 效 益 。 高 速加 工 技 术 可 用 于 轻 质 金 属 、 色 金 属 及 有 塑 料 工 件 加 工 的全 过 程 , 加 工 钢 件 、 铁 及 难 加 在 铸
般认 为 , 速 加 工 各 种 材 料 的 切 削 速 度 范 高
பைடு நூலகம்
围 为 : 合 金 已 达 到 2 0 m mi- 7 0 m mi ; 铝 0 0 / n 5 0 / n 铸
收 稿 日 期 :0 2— 2— 5 20 0 2
作者 简 介 : 王金 凤 , , 女 副教 授 , 主要 从 事先 进制 造技 术 的教 学 与研究 。
文献 标 识码 : A
文 章 编 号 :0 7—9 3 2 0 ) 2—0 5 0 10 7 4(0 2 0 0 8— 4
高 速加 工 技 术 是 指 超 硬 材 料 刀 具 和 能 可 靠 地
铁 为 9 0n mi- 5 0 m mi ; 为 6 0 mi- 0r / n 00 / n 钢 0 m/ n
刀具 材料 等 关键 技 术。 关键 词 : 高速加 工 ; 高速 主轴 ; 直线 电动机 ; 具材 料 刀
Abs r c : h a e ic se h h r ce sis a d d v lp n f hg -p e c i ig ta t T e p p r d s u s s te c a a tr t n e eo me to ih s e d ma hn n i c
现代高速加工技术及装备

现代高速加工技术及装备摘要:高速切削加工技术是高速主轴系统、高速切削加工理论等诸多相关的硬件与软件技术综合而成的,广泛应用于航空航天、汽车及模具制造业。
关键词:高速加工高速切削技术高速加工机床高速加工是20世纪数控技术之后的又一次革命性的技术发展。
从20世纪末进人实用化阶段以后,作为高效率的加工手段之一,在目前的制造业中得到了广泛的应用。
1 高速切削技术的内涵德国切削物理学家Carl Salomon在1929年进行了开创性的研究,指出在常规的切削速度范围内,切削温度随着切削速度的增大而提高。
对于每一种件材料,存在一个速度范围,在这个速度范围内,由于切削温度太高,任何刀具都无法承受,切削加工不可能进行。
但是,当切削速度再增大,超过这个速度范围以后,切削温度反而降低。
在超高速切削的条件下,切屑的形成过程和普通切削不同。
随着切削速度的提高,塑性材料的切屑形态将从带状、片状到碎屑不断演变。
单位切削力初期呈上升趋势,尔后急剧下降。
1.1 高速加工技术的优越性在高速切削加工范围,单位时间内材料切除率增加,大幅度提高加工效率。
切削力减少,有利于对刚性较差和薄壁零件的切削加工。
切屑以很高的速度排出,带走大量的切削热,有利于减少加工零件的内应力和热变形,提高加工精度。
同时高速切削加工可大大降低加工表面粗糙度。
1.2 高速切削速度的划分按不同加工工艺划分:车削700~7000m/min,铣削300~6000m/min,钻削200~1100m/min,磨削150~360m/s,这种划分比常规切削速度提高一个数量级,还有继续提高趋势。
2 高速加工技术的结构体系高速切削加工技术是一个复杂的系统工程,是诸多单元技术集成的一项综合技术。
2.1 高速加工中心主轴及高速切削刀柄高速主轴单元包括动力源、主轴、轴承和机架四个主要部分,是高速加工机床的核心部件,高速主轴一般做成电主轴的结构形式,其关键技术包括高速主轴轴承、无外壳主平衡等等。
国内外数控系统现状及发展趋势

国内外数控系统现状及发展趋势
数控系统是一种通过计算机控制机床运动的自动控制系统,其发展经历了几个阶段。
目前,国内外数控系统的最新发展趋势包括:
1. 智能化:随着人工智能技术的发展,数控系统也在向智能化方向发展。
智能化包括自适应控制、智能优化算法、故障诊断等方面。
2. 高速化:数控系统的高速化主要表现在快速的加工速度和高精度。
目前,高速、高精度的五轴联动数控系统已经成为主流。
3. 大数据:数控系统也需要应用大数据技术进行数据分析和处理,以实现更好的加工效率和质量控制。
4. 可视化:数控系统的可视化技术已经越来越成熟,这使得操作人员可以更直观、更方便地进行操作和控制。
5. 云计算:通过云计算技术,可以将数控系统的数据存储、计算和处理移到云端,实现远程监控和管理。
总之,随着数控系统技术的不断发展,其应用领域也在不断拓展,未来数控系统将成为工业自动化和智能制造的核心技术之一。
- 1 -。
高速切削加工技术的研究及其推广应用
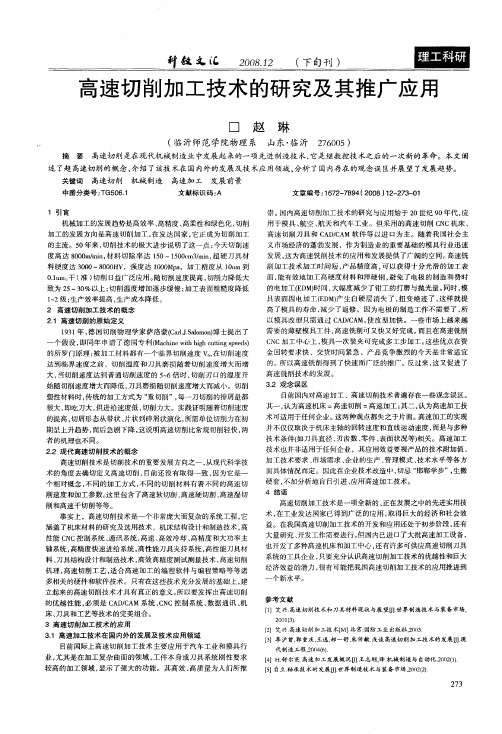
22 现 代 高速 切 削技 术 的概 念 .
目前 国内对高速加工 、高速切削技术普遍 存在一些观念误 区。
其一 , 认为高速机床 = 高速切削 = 高速加工 ; 二 , 为高速加工技 其 认 术可适用于任何企业。 这两种观点都失之于片面 。 高速加工的实现 并不仅仅取决于机床主轴的 回转速度和直线运 动速度 , 而是与多种 技术条 件( 如刀具直径 、 齿数 、 刃 零件 、 表面状况等) 。高速加工 相关 技术也并非适用于任何企业 ,其应 用效 益要视 产品的技术附加值 、 加工技术要求 、 市场需求 、 企业的生产 、 理模式 、 管 技术水平 等各方
一
个假设 , 即同年 申请 了德国专 利( c ie 『 hg IL g pe s Mahn h ihctn ed) li s
的所罗 门原理 : 被加 l 材料都有一个临界切削速度 v , T 在切削速度 达到临界速度之前 ,切 削温度 和刀具磨 损随着切削速度增 大而增 大, 当切 削速度达到普通切 削速度 的 5 6倍 时, ~ 切削刃 口的温度 开 始随切削速度增大而降低 , 刀具磨损随切削速度增大而减小。切削
塑性材料时 , 传统 的加工方式为 “ 重切削”, 每一刀切削的排屑量都 很大 , 即吃刀大 , 但进给速度低 , 切削力大。实践证明随着切削速度 的提高 , 切屑形态从带状 、 片状到碎屑状演化 , 所需单 位切削力在初 期呈上升趋势 , 而后急剧下降 , 这说明高速切削 比常规切削轻快 , 两
面具体情况而定。因此在企业技 术改造 中 , 切忌 “ 邯郸学步”, 生搬 硬套 , 不加分析地 盲 目引进 、 应用 高速加 工技术 。
4 结 语
高速切削技术是切削技术的重要发展方向之一 , 从现代科学技 术的角度去确切定 义高速切削 , 目前还 没有取得一致 , 因为它是一 个相对概念 , 同的加 工方式 , 不 不同 的切 削材料有着不 同的高速切
高速冲压技术的研究

高速冲压技术的研究1. 引言高速冲压技术是一种在冲压过程中实现高效、高精度的加工方法。
随着现代制造业的快速发展,对产品质量和生产效率的要求越来越高,高速冲压技术作为一种重要的加工方式被广泛应用。
本文将详细介绍高速冲压技术的研究现状、发展趋势以及在不同工程领域中的应用。
2. 高速冲压技术的定义和特点高速冲压技术是一种利用冲压设备进行金属板材或线材的加工方法。
该技术采用高速、高频率的连续冲击力将板材变形,从而达到对材料进行切割、成形或定位等目的。
相比传统的冲压工艺,高速冲压技术具有以下特点:•高速性:高速冲压设备具备高转速、高动态响应、高加速度的特点,能够实现快速连续的冲击动作,从而提高生产效率。
•高精度性:高速冲压设备的控制精度较高,能够实现复杂的冲压运动路径和形状,保证产品的精度和质量。
•高柔性性:高速冲压设备具有较高的自适应能力,能够根据不同的工件要求进行自动调整和优化,满足多品种、小批量的生产需求。
3. 高速冲压技术的研究现状目前,全球范围内对于高速冲压技术的研究主要集中在以下几个方面:•高速冲压设备的研制与改进:研究人员在高速冲压设备的结构、材料和控制系统等方面进行不断的创新与改进,提高设备的性能和稳定性。
•高速冲压工艺的优化:通过分析和模拟高速冲压过程中的力学行为和热特性等因素,优化冲击力的传递和材料变形过程,提高冲压的效率和质量。
•材料特性的研究:研究人员通过分析材料的力学性能、塑性变形特性和断裂行为等特性,为高速冲压过程中的材料选择和变形控制提供理论依据。
•高速冲压模具的设计与制造:研究人员通过新材料、新工艺和新技术等手段,提高模具的耐用性和加工精度,为高速冲压提供可靠的模具支持。
4. 高速冲压技术的发展趋势随着科学技术的不断进步和制造业的快速发展,高速冲压技术在未来将呈现以下几个发展趋势:•多工艺集成:高速冲压技术将与其他加工工艺如激光切割、焊接等进行集成,实现自动化生产线的搭建,进一步提高生产效率和产品质量。
汽车制造业机械加工技术现状及发展趋

10 4 0 0 种5 5 0台高效 专 用设 备 ,汽 磨 具 )及数控 元器件依赖 进 口。 车制 造 国产 化 率 达 到9 %。 上世 纪 6
( ) 速 高 效 刀 具 技 术 。 主 要 3高
年 代 ,为 装备 第 二 汽 车 制造 厂 ( 生 备 ,其 生 产线 的工 艺 技术 及 装备 部 效 率 ,主要 涉及 到 信 息技 术 、 自动 产 载 货 车 )组 织 了 1 0 个 机 床 生 分 接 近 同期 世界 先 进 水平 。但 大 部 化 技 术 、经 营管 理 技术 及 系统 工 程 3多
含 总体 来 说 ,我 国机 械 加 工 设 备 表 现 在 高 性 能 刀具 材 料 的研 发 (
8 0年 代 ,我 们 汽 车 工 业 重 点 转 入 与世 界 先 进水 平 还 有 不 少 差距 ,主 表 面 涂层 材 料 ) ,刀 具 制造 工 艺 技
轿 车 ,国 内机 床 工 业 很 不适 应 ,产 要 表现在 以下方面 。 品及 制 造 技术 和 装 备 多 数 为 国外 引
1 我国汽车制造机械加工现 状
应 用 并 获好 评 ,大 连机 床 集 团并 购 床 和 自动化 技 术 ,柔 性 制造 系 统 和 l NGE OL 公司 后 ,近几 年 为汽 车 制 造 工 厂 ,设 备 采 用模 块 化 设 计 , RS L
发 动 机 工厂 提 供 了上 百 台高 速 加 工 能 同时生产 多个 结构不 同的产品 。
厂 提 供 了立 式加 工 中心 生 产 线 ,东 方 面 差距 很 大 ,对 现代 汽 车 制 造 装 剂 的 准 干式 切 削 ,减 少切 削 液 对 环
- 1、下载文档前请自行甄别文档内容的完整性,平台不提供额外的编辑、内容补充、找答案等附加服务。
- 2、"仅部分预览"的文档,不可在线预览部分如存在完整性等问题,可反馈申请退款(可完整预览的文档不适用该条件!)。
- 3、如文档侵犯您的权益,请联系客服反馈,我们会尽快为您处理(人工客服工作时间:9:00-18:30)。
高速加工技术现状及发展趋势 1引言 对于机械零件而言,高速加工即是以较快的生产节拍进行加工。一个生产节拍:零件送进--定位夹紧--刀具快进--刀具工进(在线检测)--刀具快退--工具松开、卸下--质量检测等七个基本生产环节。而高速切削是指刀具切削刃相对与零件表面的切削运动(或移动)速度超过普通切削5~10倍,主要体现在刀具快进、工进及快退三个环节上,是高速加工系统技术中的一个子系统;对于整条生产自动线而言,高速加工技术表征是以较简捷的工艺流程、较短、较快的生产节拍的生产线进行生产加工。这就要突破机械加工传统观念,在确保产品质量的前提下,改革原有加工工艺(方式):或采用一工位多工序、一刀多刃,或以车、铰、铣削替代磨削,或以拉削、搓、挤、滚压加工工艺(方式)替代滚、插、铣削加工…等工艺(方式),尽可能地缩短整条生产线的工艺流程;对于某一产品而言,高速加工技术也意味着企业要以较短的生产周期,完成研发产品的各类信息采集与处理、设计开发、加工制造、市场营销及反馈信息。这与敏捷制造工程技术理念有相同之处。
高速加工技术产生于近代动态多变的全球化市场经济环境。在激烈的市场竞争中,要求企业产品质量高、成本低、上市快、服务好、环境清洁和产品创新换代及时,由此牵引高速加工技术不断发展。自二十世纪八十年代,高速加工技术基于金属(非金属)传统切削加工技术、自动控制技术、信息技术和现代管理技术,逐步发展成为综合性系统工程技术。现已广泛实用于生产工艺流程型制造企业(如现代轿(汽)车生产企业);随着个性化产品的社会需求增加,其生产条件为多品种、单件小批制造加工(机械制造业中,这种生产模式将占到总产值的70%),高速加工技术必将在生产工艺离散型或混和型企业中(如模具、能源设备、船舶、航天航空…等制造企业)得到进一步应用和发展。
二十世纪末期,我国变革计划经济体制,改革开放,建成有中国特色社会主义市场经济体制。实用的高速加工技术跟随引进的先进数控自动生产线、刀具(工具)、数控机床(设备),在机械制造业得到广泛应用,相应的管理模式、技术、理念随之融入企业。企业家们对现代信息技术和企业制度、机制在未来可持续发展、市场竞争中的重要地位和作用,认识日益深刻。社会主义市场经济环境,不仅促进企业转制、调整产业、产品结构和技改,还给企业展现出应用和发展高速加工技术良好而广阔的前景。
2我国引进数控轿车自动生产线中的高速加工技术 二十世纪八十年代以来,我国相继从德国、美国、法国、日本…等国引进了多条较先进的轿车数控生产自动线,使我国轿车制造工业得到空前发展。其中较典型的是来自德国的一汽--大众捷达轿车和上海大众桑塔纳轿车自动生产线,其处于国际二十世纪九十年代中期水平。其中应用了较多较实用的高速加工技术。从中可部分了解到世界高速加工技术的现状与发展趋势。本文重点介绍一汽--大众捷达轿车传、发生产线。
引进的捷达数控轿车自动生产线概况 一汽--大众捷达轿车自动生产线由冲压、焊接、涂装、总装、发动机及传动器等高速生产线组成。同步引进德国大众汽车公司并行工程管理模式与管理技术,经营各条自动线生产运行,年产轿车能力15万辆,制造节拍分/辆。其中发动机、传动器生产线共拥有627台各种机加工设备,进口253台,国产374台,其基本上属于数控刚性自动生产线。自产发动机零件9种,传动器零件27种,其余社会配套。年产发动机27万台,传动器18万台。生产国际二十世纪九十年代水平的4缸、6缸捷达奥迪轿车五汽门电喷发动机及配套的传动器,生产节拍30~40秒/ 1台,生产线部分采用风冷干式切削加工技术,其机械加工工艺流程反映了当代轿车制造业中最先进的技术水平。轿车营销以国内市场为主。由于没有轿车自主知识产权,新车型的研发,是以现有一汽--大众捷达轿车生产自动线为本,持续从德国大众汽车公司进口相关信息和技术(上海大众桑塔纳轿车自动生产线情况类同)。
一汽--大众轿车发动机、传动器(发、传)零件毛坯技术概况 一汽--大众捷达奥迪轿车发动机、传动器关键零件毛坯均为精密铸造成型的高强度铸铁、铸铝及精密模锻的结构钢件,部分零件采用精密粉末冶金烧结成形工艺。其高速加工技术要求在批产工艺过程中,材料可加工性能良好、稳定,零件毛坯切削余量控制在~4mm± mm以内。生产线运行初期,零件毛坯靠进口。自1997年起,国内相关企业经多次攻关,先后攻克批产零件毛坯的精密成型工艺技术、零件材料各化学元素选配及热处理工艺技术难题,旨在达到高速加工自动生产线(技术)对零件毛坯材料可加工性、尺寸精度一致性较高要求的技术指标,传动器零件毛坯国产化已达95%以上。
一汽--大众轿车发、传生产线高速切削刀具、高速机床及加工工艺 一汽大众捷达奥迪轿车发动机、传动器零部件生产线上,几乎所有的切削刀、辅具(工具)均为进口产品(来自49个外国公司),关键工序的设备(机床)也是进口的专用刚性数控产品。其典型技术特点简要分述如下:
刀具材料的选用:以超硬刀具材料为主。采用CBN、SiN陶瓷、Ti基陶瓷、TiCN涂层刀具材料加工高强度铸铁件,铣削速度达2200m/min;采用PCD、超细硬质合金刀具加工高Si-Al铸造件,铣削速度也达2200m/min,钻、铰削速度达80~240m/min;采用SiN陶瓷、Ti基陶瓷及TiCN涂层刀具加工精锻结构钢零件,车削速度达200m/min;采用高Co粉末冶金表面涂覆TiCN的高速钢整体拉刀、滚刀、剃齿刀,以及硬质合金机夹组合专用拉刀,加工各种精锻钢件、铸铁件,拉削速度10~25m/min,滚削速度110m/min,剃齿切速170m/min。
刀具典型结构与加工工艺:零件孔加工刀具采用多刃复合式(刀刃机夹、镶焊组合)结构,以铰、挤削替代磨削,在一次性走刀过程中完成孔的精加工,转速达,走刀速度达~3 m/min,精度可达5~7级,粗糙度μm(枪钻转速达,Ra2μm);零件平面铣削刀具多采用密齿、过定位、重复夹紧结构,径、轴向双向可调的高速密齿面铣刀。直径φ250~400mm,轴向跳动<±。零件装配平面的加工,是以铣代磨,粗糙度μm,不平度<;曲轴主轴颈、连杆轴颈加工,采用双工位车一拉削专用刀具。刀盘直径φ700mm,圆周装有40个硬质合金涂层刀片,每10片为一组,切削速度150 m/min,快进速度 min,切削余量~3mm/径向,班产350件;曲轴主轴轴承盖加工,采用侧置、排列式机夹复合成形拉削专用刀具,安装三种、共713片可转位硬质合金涂层(TiCN)刀片,进给速度25m/min,班产1750件,拉削切削余量~3mm;缸体曲轴及缸盖凸轮轴主轴的装配圆弧面、侧面的加工,采用组合式、轴向串联、机夹三面刃专用盘铣刀,由6~8个刀盘成组装配,共安装约146片机夹可转位涂层刀片,在一次径向走刀中,完成10个侧面的铣削加工,加工余量~2mm;传动器同步齿圈座的外圈渐开线齿及三等分直槽的加工,采用长1800mm的筒式专用外拉刀,一次走刀拉削成形,拉削速度10m/min,三工位班产1440件;发动机5种传动轴上的花键齿形(M=加工,采用双工位、成对配置的搓、挤无屑加工专用刀具,其一次往复运动,将花键齿形搓挤成形,班产共800件;传动器的齿轮加工,采用多头小直径涂层高速滚刀及径向剃齿刀滚、剃成形,以剃代磨,班产800件;差速器壳体内球面的镗削,采用机床主轴内置式、推拉杆轴向往复运动,带动镗刀头二维成半圆轨迹移动,叠加壳体廻转运动,一次走刀完成其球面成形镗削加工;缸体汽缸孔镗削采用双工位、机床主轴内置式、轴向往复运动推拉杆机构,往走刀--粗镗,复走刀--精镗,切削速度达800m/min;一些零件的轴端头外圆柱面加工,采用成形组合外圆铣、铰削专用工具,一次走刀多刃铣铰削完成外圆、端面粗加工,替代单刃车削加工工艺。…上述专用高速、高效刀具结构不胜枚举,与相应专用数控机床组合成的各加工工位,生产节拍为20~40秒。零部件的精度与质量60%~80%决定于这些专用刀具及数控机床的精度和质量,20%~40%决定于零件毛坯的精度与质量。生产流程中,质量监测工序为机后抽检。
发动机、传动器二条生产线共有250多台数控机床采用HSK高速空心工具柄,共计6个规格:32#、40#、50#、63#、80#、100#,其中以40#、50#、63#三种规格使用数量最多。HSK空心工具柄与上述各种多刃专用铣刀、复合式孔加工刀具组成高速工具系统,完成250多个工序、工位切削加工,其高速动平衡精度为≤。 安装筒式外形拉刀的专用数控机床及曲轴专用数控车--拉机床较为典型。前者的结构特点是:在三台60多吨推力的液压千斤顶上固定竖装三把柱状专用外形拉刀筒体,在数控(PC机)下,将同步齿圈座零件半成品,间歇式自下推入,由上顶出,使零件彼此摞叠逐一拉削、并全程通过拉刀筒体,完成该零件外圈渐开线直齿及1200三等分直槽的拉削加工工序。一台专机生产率可替代由13台---~16台高速滚齿机、插(铣)床组成的生产线;而后者的结构基本上是一台将中型数控车床改形而成的专机。其专用数控系统使曲轴回转的速度和转角,与盘式车拉刀齿的每90间隙式转角、逐刃跟进成车拉削的加工动作相匹配,使二者各自在回转一圈与往复分度900的车拉削加工运动过程中,动作相互协调、和谐。其工件的质量、精度基本决定于盘状拉刀径向精度及专机进刀定位精度。一台双工位车--拉数控专机可替代10台以上数控成形车床和5台以上内铣式曲轴加工机床。该线其它专用数控机床一般都要求刚度、功率足够,主轴回转精度达到2~5μm,定位精度:±2~5μm,直线运动精度:5~10μm/300mm。
一汽--大众数控轿车生产线还设有激光焊接、激光表面淬火…等特种数控专用设备。
纵观一汽--大众发动机、传动器生产线机械制造工艺技术,其刀具切削与进给速度未达到某些论文中介绍的高速切削概念指标,但其生产效率是属于高速加工的范畴。在生产实践中,这种相对低速切削而高效的加工技术,通过了市场竞争环境的严格考核。
我国所有引进的各条轿车自动生产线的管理、决策机制及产品设计分析、加工工艺技术基本上引用相应外国公司的模式和样品。其加工技艺数据库都是固化