怎样制定机械加工的标准
机械行业生产工艺标准

机械行业生产工艺标准一、引言机械行业是指通过机械设备来加工、制造和加工零件或组装成品的行业。
在机械制造过程中,生产工艺标准是确保产品质量和生产效率的重要因素。
本文将介绍机械行业常见的生产工艺标准,包括工艺流程、操作规范、材料选择和质量要求等方面。
二、工艺流程1. 设计和规划:在机械产品制造前,需要进行详细的设计和规划工作。
设计阶段要考虑产品的功能、结构和工艺要求,并进行必要的模拟和验证。
2. 材料准备:根据设计要求,选择合适的原材料,并进行相应的材料预处理,包括锻造、淬火、热处理等。
3. 加工工艺选择:根据产品的结构和要求,选择合适的加工工艺,包括铣削、车削、磨削、切削等。
4. 加工操作:按照工艺要求,进行具体的加工操作,包括工件的定位、夹紧、加工刀具的选择、切削速度和进给量的控制等。
5. 检测和质量控制:在加工过程中,进行相应的检测和质量控制,包括尺寸测量、表面质量检查和功能性能测试等。
6. 组装和调试:完成加工后,根据产品的要求进行组装和调试,确保产品的性能和质量。
7. 成品检验和包装:对成品进行全面的检验,并进行相应的包装和标识,以满足产品出厂要求。
三、操作规范1. 安全操作规范:在机械制造过程中,操作人员必须遵守相关的安全操作规范,包括穿戴防护设备、正确使用机械设备、保持工作场所的整洁和安全等。
2. 加工工艺规范:在加工过程中,操作人员必须按照预定的工艺要求进行操作,包括合理布置工件和刀具、控制切削速度和进给量、定期清洁和保养设备等。
3. 检测和质量控制规范:在检测和质量控制过程中,操作人员必须按照标准的检测方法进行操作,确保检测结果的准确和可靠性。
4. 组装和调试规范:在组装和调试过程中,操作人员必须按照产品要求进行操作,包括正确组装零件、调试功能和性能等。
5. 成品检验和包装规范:在成品检验和包装过程中,操作人员必须按照标准的检验方法进行操作,确保成品的质量和可靠性。
四、材料选择1. 材料特性:根据产品的要求选择合适的材料,包括强度、硬度、耐磨性、耐蚀性、热稳定性等。
机械加工技术要求标准

机械加工技术要求标准机械加工技术是制造业中非常重要的一部分,它直接影响着产品的质量和性能。
为了确保机械零部件的加工质量,提高产品的精度和稳定性,制定了一系列的机械加工技术要求标准。
这些标准旨在规范机械加工过程中的各项技术要求,确保加工质量和效率。
首先,机械加工技术要求标准包括了对加工设备的要求。
加工设备应具备良好的稳定性和精度,能够满足不同工件的加工要求。
同时,对于数控机床等高精度设备,还需要具备高速、高效的加工能力,以适应现代制造业对高质量、高效率的要求。
其次,机械加工技术要求标准还包括了对加工工艺的要求。
在加工工艺中,需要严格控制加工参数,包括切削速度、进给速度、切削深度等,以确保加工精度和表面质量。
同时,还需要根据不同工件材料的特性,选择合适的刀具和切削液,以提高加工效率和延长刀具寿命。
另外,机械加工技术要求标准还包括了对加工人员的要求。
加工人员需要具备扎实的专业知识和丰富的实践经验,能够熟练操作各类加工设备,理解和掌握加工工艺要求,及时发现和解决加工过程中出现的问题,确保加工质量和安全生产。
此外,机械加工技术要求标准还包括了对加工质量的要求。
加工质量是衡量加工技术水平的重要标志,它直接关系着产品的质量和性能。
因此,机械加工技术要求标准对加工质量提出了严格的要求,包括尺寸精度、形位精度、表面质量等方面的要求,以确保产品能够满足设计要求和用户需求。
综上所述,机械加工技术要求标准是制造业中非常重要的一部分,它规范了加工设备、加工工艺、加工人员和加工质量的要求,有利于提高产品的质量和性能,推动制造业的发展。
因此,加工企业和加工人员都应严格遵守这些标准,不断提升自身技术水平,提高产品的竞争力。
机械加工工时定额标准

机械加工工时定额标准
机械加工工时定额标准是指在机械加工过程中,对于每一道工序所需的标准工时的规定。
这一标准的制定对于企业的生产效率和成本控制具有重要意义。
在机械加工行业中,工时定额标准的制定需要考虑多方面因素,包括机械设备的性能、操作人员的技能水平、材料的特性以及加工工艺的复杂程度等。
首先,机械设备的性能对工时定额标准具有直接影响。
不同的机械设备在加工过程中所需的工时是不同的,而且随着设备的更新换代,工时定额标准也需要不断进行调整和更新。
因此,企业需要根据自身的生产设备情况,结合市场需求和技术发展趋势,不断完善工时定额标准,以确保生产效率的最大化。
其次,操作人员的技能水平也是影响工时定额标准的重要因素。
技术熟练的操作人员能够在相同的时间内完成更多的加工任务,而技术水平较低的操作人员则可能需要更长的时间。
因此,企业在制定工时定额标准时,需要考虑到操作人员的技能水平,并通过培训和技术提升来提高整体的生产效率。
另外,材料的特性和加工工艺的复杂程度也会对工时定额标准产生影响。
不同的材料在加工过程中所需的时间是不同的,而且随着加工工艺的复杂程度的增加,工时定额标准也会相应增加。
因此,企业需要对不同材料和不同加工工艺进行细致的分析和评估,以制定合理的工时定额标准。
总之,机械加工工时定额标准的制定需要综合考虑机械设备的性能、操作人员的技能水平、材料的特性以及加工工艺的复杂程度等多方面因素。
只有通过科学合理的制定,才能确保企业在机械加工过程中能够实现高效生产,降低成本,提高竞争力。
因此,企业需要重视工时定额标准的制定工作,并不断进行调整和优化,以适应市场需求和技术发展的变化。
机械加工工艺流程检验标准及规范
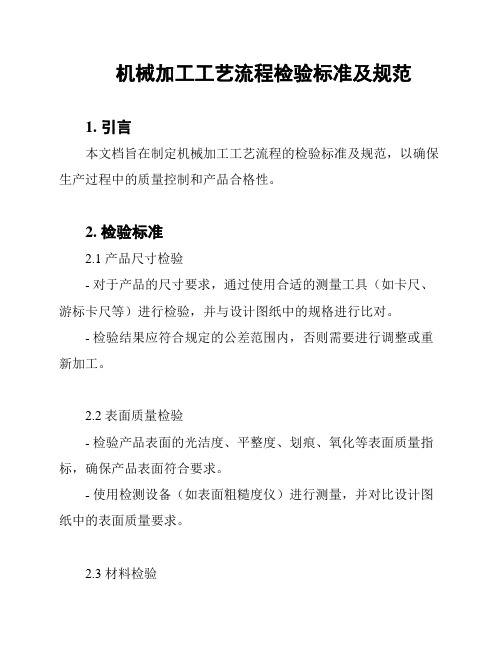
机械加工工艺流程检验标准及规范1. 引言本文档旨在制定机械加工工艺流程的检验标准及规范,以确保生产过程中的质量控制和产品合格性。
2. 检验标准2.1 产品尺寸检验- 对于产品的尺寸要求,通过使用合适的测量工具(如卡尺、游标卡尺等)进行检验,并与设计图纸中的规格进行比对。
- 检验结果应符合规定的公差范围内,否则需要进行调整或重新加工。
2.2 表面质量检验- 检验产品表面的光洁度、平整度、划痕、氧化等表面质量指标,确保产品表面符合要求。
- 使用检测设备(如表面粗糙度仪)进行测量,并对比设计图纸中的表面质量要求。
2.3 材料检验- 对使用的材料进行检验,确保其符合设计要求和相关标准。
- 检查材料的外观、密度、硬度等指标,并与相关标准进行对比。
2.4 装配与安装检验- 对于需装配和安装的零部件,进行装配和安装前的检验,确保其符合设计要求。
- 检验装配和安装的精度、间隙、螺纹连接等,并根据相应标准进行评估。
2.5 功能性检验- 对产品的功能进行检验,确保其符合设计要求。
- 进行实际操作或使用测试设备进行功能性测试,并进行性能指标评估。
3. 规范3.1 检验程序规范- 制定机械加工工艺流程的检验程序规范,定义各项检验的顺序和方法。
- 确保检验过程的可追溯性和一致性。
3.2 检验记录规范- 规定检验过程中产生的记录方法和要求。
- 记录检验结果、异常情况、处理措施等信息。
3.3 不合格品处理规范- 规定不合格产品的处理流程和责任分工,并制定相应的纠正和预防措施。
4. 结论制定机械加工工艺流程的检验标准及规范对于保证产品质量和生产效率具有重要意义。
本文档提出了产品尺寸、表面质量、材料、装配与安装、功能性等方面的检验标准,并规定了相应的检验程序和记录规范,以及不合格品的处理规范。
机械加工一般公差标准
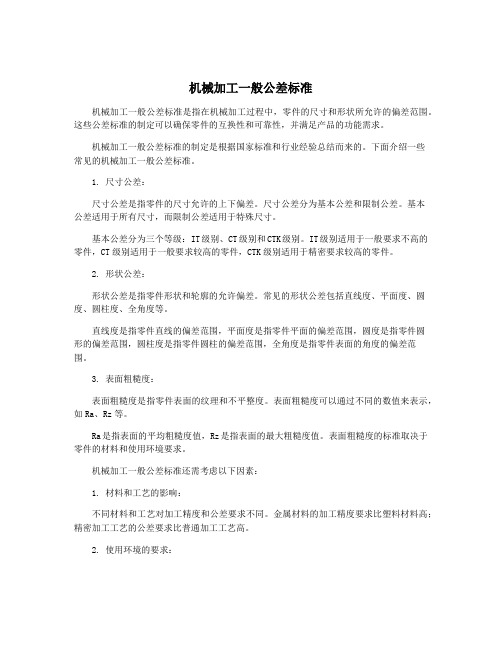
机械加工一般公差标准机械加工一般公差标准是指在机械加工过程中,零件的尺寸和形状所允许的偏差范围。
这些公差标准的制定可以确保零件的互换性和可靠性,并满足产品的功能需求。
机械加工一般公差标准的制定是根据国家标准和行业经验总结而来的。
下面介绍一些常见的机械加工一般公差标准。
1. 尺寸公差:尺寸公差是指零件的尺寸允许的上下偏差。
尺寸公差分为基本公差和限制公差。
基本公差适用于所有尺寸,而限制公差适用于特殊尺寸。
基本公差分为三个等级:IT级别、CT级别和CTK级别。
IT级别适用于一般要求不高的零件,CT级别适用于一般要求较高的零件,CTK级别适用于精密要求较高的零件。
2. 形状公差:形状公差是指零件形状和轮廓的允许偏差。
常见的形状公差包括直线度、平面度、圆度、圆柱度、全角度等。
直线度是指零件直线的偏差范围,平面度是指零件平面的偏差范围,圆度是指零件圆形的偏差范围,圆柱度是指零件圆柱的偏差范围,全角度是指零件表面的角度的偏差范围。
3. 表面粗糙度:表面粗糙度是指零件表面的纹理和不平整度。
表面粗糙度可以通过不同的数值来表示,如Ra、Rz等。
Ra是指表面的平均粗糙度值,Rz是指表面的最大粗糙度值。
表面粗糙度的标准取决于零件的材料和使用环境要求。
机械加工一般公差标准还需考虑以下因素:1. 材料和工艺的影响:不同材料和工艺对加工精度和公差要求不同。
金属材料的加工精度要求比塑料材料高;精密加工工艺的公差要求比普通加工工艺高。
2. 使用环境的要求:零件所使用的环境和所需功能要求的不同,决定了公差的大小。
高速旋转机械的零件需要更高的公差要求,以确保安全和性能。
3. 零件的功能要求:不同零件的功能要求不同,公差标准也会有所不同。
连接件的公差要求较高,以确保连接的牢固性;密封件的公差要求较高,以确保密封的可靠性。
机械加工一般公差标准是确保零件工作性能和质量的重要指标。
在制定公差标准时,需要考虑材料、工艺、使用环境和功能要求等因素,以保证零件的稳定性和可靠性。
机械加工行业标准

机械加工行业标准导言:机械加工行业是制造业中的关键领域之一,对产品质量和生产效率有着重要的影响。
为了确保机械加工行业顺利运行和促进企业间的技术交流与合作,制定和遵守一系列标准是非常必要的。
本文将从机械加工行业的不同层面出发,分析和讨论一些常见的规范、规程和标准。
一、产品质量标准在机械加工行业中,产品质量是企业长期发展的基础和保证。
制定和遵守产品质量标准是确保产品具有良好性能和可靠性的关键所在。
因此,制定适用于不同类型机械加工产品的质量标准是十分重要的。
1.1 材料要求机械加工产品的材料质量直接影响其机械性能和使用寿命。
因此,在材料选择和应用方面,制定相应的标准是非常重要的。
例如,对于不同类别的钢材和铝合金等材料,可以制定相关标准规定其化学成分、力学性能、耐磨性等指标,以确保材料质量满足要求。
1.2 加工精度要求机械零件的准确加工和装配是确保整机性能的关键。
不同类型的机械零件对精度的要求有所不同。
例如,飞机发动机零件对精度的要求相对较高,需要制定相应的标准规范,确保加工的零件满足设计要求。
1.3 表面处理要求机械零件的表面处理对于提高防腐蚀性能和延长使用寿命至关重要。
制定与表面处理相关的标准,如喷漆、电镀、热处理等技术规范,可以提高产品的质量和市场竞争力。
二、生产流程标准机械加工行业涉及的生产过程繁杂多样,需要制定相应的生产流程标准,以确保生产过程的连贯性和高效性。
2.1 设计过程标准在机械加工行业中,设计过程是最为核心的部分之一。
制定设计过程的标准可以规范设计师的工作流程和质量要求,确保产品设计满足客户需求和工艺要求。
2.2 加工工艺标准机械零件的加工工艺直接影响到产品的质量和成本。
制定和遵守加工工艺标准有助于提高产品加工效率和降低生产成本。
例如,针对不同类型零件的加工规范、加工顺序、切削参数等,可以制定相应的加工工艺标准。
2.3 环境管理标准机械加工过程中产生的废气、废水和废渣等对环境造成一定的影响。
机械加工工艺路线制定的原则与方法
机械加工工艺路线制定的原则与方法机械加工工艺路线的制定是指根据产品的加工要求、工艺性能、生产条件等因素,确定产品加工的详细步骤和工艺参数,以实现高效、经济地完成产品加工的过程。
制定机械加工工艺路线需要遵循一些原则和方法,下面对其进行详细探讨。
一、原则1.经济性原则:机械加工工艺路线制定首要考虑的是经济性原则,即通过合理的工艺路线设计和参数选择,以尽量减少制造成本,提高加工效率和产品质量。
具体体现在工艺路线的选择上,应选择能同时满足产品质量要求和经济性要求的路线。
2.合理性原则:机械加工工艺路线制定应尽量考虑各种因素的综合影响,确保加工过程的合理性。
例如,要根据工艺性能要求选择适宜的切削速度、进给量和切削深度等。
3.可行性原则:机械加工工艺路线制定要考虑生产条件的可行性,包括设备设施、材料选择等因素。
要能够在现有设备和技术条件下实施,并具有合理的可行性。
4.规范性原则:机械加工工艺路线制定要遵循相关的国家标准和规范,确保产品的质量和安全。
例如,符合产品标准要求、工艺过程的操作规范等。
二、方法1.分析产品要求:首先需要详细分析产品的加工要求,包括尺寸、形状、精度、表面质量等要求,以确定加工工艺的关键特点和难点。
2.选择加工方法:根据产品要求和加工性能要求,选择合适的加工方法,包括切削加工、磨削加工、成形加工等。
3.确定工艺路线:根据产品的加工要求、加工方法等因素,确定产品的加工顺序和工序。
要根据加工过程的依赖关系,避免出现不能回转的工序,尽量减少工序的数量。
4.选择工艺参数:根据产品要求和加工方法,选择合适的工艺参数,包括切削速度、进给量、切削深度、磨削粒度等。
要通过试验和经验总结,确定合适的参数范围,以保证加工质量和效率。
5.确定工艺装备:根据产品要求和加工工艺路线,确定所需的工艺装备和设备。
要考虑设备的性能、功能和适应性,满足产品加工的要求。
6.评估工艺方案:根据经济性、合理性、可行性和规范性原则,对制定好的工艺路线进行评估和比较。
机械加工检验标准及方法(1)
机械加工检验标准及方法(1)机械加工是现代工业生产中不可或缺的一环,机械加工检验是确保机械加工产品质量的重要环节。
为了确保机械加工产品的合格率,合理地制定适合生产的检验标准及方法是必要的。
本文将详细介绍机械加工检验标准及方法。
机械加工检验标准机械加工产生的产品有尺寸精度、表面质量、几何精度、材料硬度等多个方面的品质要求。
机械加工检验标准是指根据机械加工产品的不同品质要求,制定出一系列检验标准,用于对机械加工产品进行检验。
常见的机械加工检验标准有GB、ISO、JIS等标准。
在实际操作中,应根据机械加工产品的实际需求和使用要求,选择合适的检验标准进行检验。
同时,对于特定的机械加工产品,也可以根据实际需求制定符合实际情况的检验标准。
机械加工材料的检验方法机械加工材料的检验是确保机械加工产品质量的关键环节。
在机械加工成品的检验过程中,不仅要对成品进行检验,还要对原材料进行检验。
下面我们将详细介绍机械加工材料的检验方法。
金属材料的检验方法金属表面缺陷的检验钢材表面缺陷常见有裂纹、划痕、气泡、硅酸盐夹杂物等。
缺陷类型众多,方法不同。
一般来说,通过目视检查、手摸检查、探伤、磁粉探伤等方法可检测出钢材表面缺陷。
但有些缺陷需要通过仔细打磨能够去除,在制作机械零件时才可使用。
金属含量的检验从金属材料中提取样品,经过化学分析,就可以得到其组成。
从而判断其是什么金属及含量是否符合标准。
非金属材料的检验方法干燥状态的检验如混凝土等,在干燥状态下检测其强度。
取样检验如塑料等,可在规定的机器、水平面等条件下,按规定的方法将试样切割成均匀大小的试样,然后采用拉伸、弯曲等方法进行检验。
机械加工验收方法验收是机械加工产品交付使用前的最后一道程序。
通过验收可以确定机械加工产品是否符合质量标准,以及确认产品的使用性能是否符合用户要求。
机械加工产品的验收方法主要包括自检、互检和专家检查。
自检自检主要是由机械加工产品生产者自己进行,通过严格的自我检查,查找产品的问题,使其能够符合相应的质量标准。
机械加工技术要求规范
机械加工技术要求规范首先,机械加工技术要求具有良好的机械基础知识,包括机械零件的标志、读图能力、机械加工的基本原理和方法等。
了解机械设备的工作原理、结构和性能,对各种机械加工工艺有一定的认识。
同时,还要掌握机械加工中常用的测量和检验方法,能够正确选择和使用各种测量工具和检测仪器。
其次,机械加工技术要求有良好的制图技术,能够准确理解和分析工程图纸。
熟悉常用的制图标准和图纸符号,能够根据工程图纸进行正确的加工操作。
掌握绘图软件和CAD/CAM技术,能够进行三维模型的建立和程序的编写。
第三,机械加工技术要求熟悉各种金属材料的特性和性能。
了解不同材料的切削性能、热处理特性以及对于机械加工的影响。
对于不同材料的加工规范和工艺要求有清晰的认知,并能根据材料特性选择适当的切削工艺和切削参数。
第四,机械加工技术要求掌握各种机械加工方法和工艺。
熟悉各种机床的操作和调试,能够正确使用车床、铣床、钻床等工具进行机械加工。
掌握不同加工方法的优缺点,能够根据不同的工件要求选择最合适的加工方式。
第五,机械加工技术要求具备良好的工作习惯和安全意识。
遵守工作流程和操作规程,保证加工质量和工作效率。
关注工作环境和工作安全,做好个人防护措施,减少事故和损伤的发生。
最后,机械加工技术要求具有良好的团队合作意识和沟通能力。
在机械加工中,往往需要与其他工种的人员合作,例如产品设计师、工艺师、调模师等。
能够与他们进行有效的沟通和协调,确保加工过程的顺利进行。
总之,机械加工技术的规范对于提高机械加工效率和产品质量至关重要。
需要具备良好的机械基础知识、制图技术、材料知识、加工方法和工艺掌握,同时注重工作安全和团队合作意识。
只有具备这些要求,才能够胜任各种机械加工任务,提高工作效率和产品质量。
机械加工标准
机械加工标准机械加工是指利用机床、工具、刀具和对工件进行切削加工的一种方法。
在工程制造中,机械加工是非常重要的一个环节,它直接影响着零部件的质量、精度和使用寿命。
为了确保机械加工的质量,制定了一系列的机械加工标准,下面我们就来详细了解一下机械加工标准的相关内容。
首先,机械加工标准包括了工艺标准、尺寸标准、表面质量标准等内容。
工艺标准是指在机械加工过程中,所需遵循的加工工艺规范,包括了切削速度、进给量、刀具选择、冷却液使用等内容。
尺寸标准是指加工零件的尺寸公差、形位公差等内容,它直接关系到零件的装配和使用。
表面质量标准是指加工表面的粗糙度、平整度、光洁度等要求,它对零件的外观和功能都有着重要影响。
其次,机械加工标准的制定是为了保证加工零件的质量和精度。
在机械加工中,如果没有标准可依,操作人员很难把握加工的要求,容易导致加工零件质量不稳定,甚至出现不合格品。
因此,机械加工标准的制定是非常必要的,它可以统一加工要求,提高加工精度,保证零件质量。
再次,机械加工标准的执行需要严格遵守。
在实际的机械加工生产中,操作人员必须严格执行机械加工标准,严格按照工艺标准进行操作,严格控制尺寸公差,严格保证表面质量要求。
只有这样,才能保证加工出来的零件符合设计要求,达到预期的使用效果。
最后,机械加工标准的不断完善是一个持续的过程。
随着科学技术的不断发展,机械加工标准也在不断更新和完善。
新的材料、新的加工工艺、新的加工设备的出现,都需要及时修订和完善相关的机械加工标准,以适应新的生产需求。
总之,机械加工标准对于保证加工质量、提高生产效率、降低生产成本都起着非常重要的作用。
在实际生产中,我们要重视机械加工标准的制定和执行,不断完善和提高标准,以确保机械加工工作的顺利进行,为工程制造质量提供有力保障。
- 1、下载文档前请自行甄别文档内容的完整性,平台不提供额外的编辑、内容补充、找答案等附加服务。
- 2、"仅部分预览"的文档,不可在线预览部分如存在完整性等问题,可反馈申请退款(可完整预览的文档不适用该条件!)。
- 3、如文档侵犯您的权益,请联系客服反馈,我们会尽快为您处理(人工客服工作时间:9:00-18:30)。
怎样制定机械加工的标准
我们公司全部产品外协加工,老板为了控制供应商,让我制定机械加工标准。
我觉得机加工范围太广不好制定,我也只好制定一个,望大家提出意见!谈谈是怎样制定
机加工规范
1.目的
对机加工产品质量控制,以确保满足公司的标准和客户的要求。
2.范围
适用所有机加工产品,和对供应商机加工产品的要求及产品的检验。
3.定义
3.1 A级表面:产品非常重要的装饰表面,即产品使用时始终可以看到的表面。
3.2 B级表面:产品的内表面或产品不翻动时客户偶尔能看到的表面。
3.3 C级表面:仅在产品翻动时才可见的表面,或产品的内部零件。
4.机加工的要求
4.1机加工件材料要符合图纸,选用的材料的符合国家标准,具体要求见公司制定《不锈钢材料规范》《铝合金材料规范》《碳素结构钢材料规范》
4.2机加工件图纸未注尺寸公差参考国家标准线性尺寸的未注公差GB/T1804-f要求进行检验。
4.3机加工件图纸未注角度公差参考国家标准角度的未注公差GB/T11335-m要求进行检验。
4.4机加工件图纸未注形位公差参考国家标准形位的未注公差GB/T1184-H要求进行检验。
4.5图纸中尺寸标注为配合形式加工的,采用间隙配合,具体要求为:外配合为配合为配作对象最大尺寸+0.01~+0.10mm:内配合为配作对象最小尺寸-0.10~-0.01。
5.机加工质量的控制
5.1 零件加工按照图纸加工,对图纸有标示不清、模糊、错误和对图纸产生疑问的与公司工艺人员联系。
5.2 零件加工按照工艺流程去做。
5.3零件加工过程中遇到加工错误或尺寸超出公差范围要与公司工艺人员联系,公司工艺人员将会确认零件可以采用或不可采用。
5.4 需要划线加工的零件,加工后不允许有划线的痕迹。
5.5 所有机加工的零件要去毛刺、钻孔后要倒角、棱角要倒钝(特殊要求除外)。
5.6 碰到零件加工错误不应该善做主张对零件进行修改,应与公司工艺人员联系获得技术支持。
6.机加工外观的控制
6.1 机加工中由于控制不力和操作不当造成机械碰伤、表面划伤的不允许存在A级表面,允许存在B,C 级表面.。
6.2 变形、裂纹不允许存在A,B,C级表面。
6.3 需要表面处理的零件表面不允许有氧化层、铁锈、凹凸不平的缺陷。
7.机加工质量检验
7.1 外观检验:不允许有翘曲、变形、裂纹、划伤、碰伤、凹凸不平及表面粗糙度符合要求。
7.2 材料的检验:材料厚度符合国家标准,具体见公司制定的《不锈钢材料规范》《铝合金材料规范》《炭素结构钢材料规范》。
7.3 尺寸及公差的检验:零件的尺寸和公差符合图纸的要求。
7.4 螺纹、孔的检验:采用牙规、塞规检验或用螺钉检验,螺纹的底孔不大于标准底孔的
0.1mm。
7.5 零件的检验要全面到位防止不良的产品流入公司造成不必要的损失。
现在很多私人企业考虑的是加工得不行也得用的问题。
所以我们公司以前只要是能保压的东西尽量补焊。
首先是工期进度的问题,再就是报废的话前期加工费用的浪费。
所以私人企业的生存其实也是很无奈的,浪费不起啊。
建议参考一下下面的一些标准,可以把问题考虑得全面一点:
JB-T4328.6-1999电工专用设备机械加工通用技术条件
JB-T5000.9-1998重型机械通用技术条件切削加工件
JB-T5936-1991工程机械机械加工件通用技术条件
JB-T7164-1993凿岩机械与气动工具机械加工件通用技术条件
JB-T8828-2001切削加工件通用技术条件
JB-T9872-1999金属切削机床机械加工件通用技术条件
SB-T10148.2-1993粮油加工机械通用技术条件机械加工技术要求
YC-T10.1-2006烟草机械通用技术条件第1部分切削加工件
另外,对你的几个定义看不懂,难道你们的要求只是外观上的要求吗?没有配合方面的要求吗?
“善做主张”应该是“擅做主张”。
“4.3 机加工件图纸未注角度公差参考国家标准角度的未注公差GB/T11335-m要求进行检验”,现行的未注角度公差标准已经整合到GB-T1804-2000《一般公差未注公差的线性和角度尺寸的公差》中。
“按×××的要求进行检验”似乎不是很恰当,可以直接表示为例如“未注公差的线性尺寸的极限偏差值,按GB/T 1804-2000中的中等精度等级(m级)”,把加工和检验都包括进去。
4.5图纸中尺寸标注为配合形式加工的,采用间隙配合,具体要求为:外配合为配合为配作对象最大尺寸+0.01~+0.10mm:内配合为配作对象最小尺寸-0.10~-0.01
这样合适吗?是不是你们以前就是这样做的?不如直接在图纸上表示出来。
你说的“配合形式加工”是不是配作的意思?
5楼的师傅说的很好!
但对一般机加工零件的通用技术要求,是否可直接作如下规定:
1.未注尺寸公差按GB/T1804-2000中的中等精度等级(m级)。
2.未注形位公差按GB/T1184-1996中的中等精度等级(K级)。
对照表:
未注尺寸公差按GB/T1804-m
线性尺寸的极限偏差数值(GB/T1804-2000)(mm)
公差等级基本尺寸分段
0.5~3 >3~6 >6~30 >30~120 >120~400 >400~1000 >1000~2000
精密f ±0.05 ±0.05 ±0.1 ±0.15 ±0.2 ±0.3 ±0.5
中等m ±0.1 ±0.1 ±0.2 ±0.3 ±0.5 ±0.8 ±1.2
粗糙c ±0.2 ±0.3 ±0.5 ±0.8 ±1.2 ±2 ±3
最粗v -- ±0.5 ±1 ±1.5 ±2.5 ±4 ±6
倒圆半径和倒角高度尺寸的极限偏差(GB/T1804-2000)mm
公差等级基本尺寸分段
0.5~3 >3~6 >6~30 >30
精密f ±0.2 ±0.5 ±1 ±2
中等m
粗糙e ±0.4 ±1 ±2 ±4
最粗v
角度尺寸的极限偏差数值(GB/T1804-2000)
公差等级基本尺寸分段
~10 >10~50 >50~120 >120~400 >400
精密f ±1o ±30′±20′±10′±5′
中等m
粗糙e ±1o30′±1o ±30′±20′±10′
最粗v ±3o ±2o ±1o ±30′±20′
注:1o为1度
未注形位公差按GB/T1184-K
直线度和平面度未注公差值(GB/T1184-1996)(mm)
公差等级基本长度范围
≤10 >10~30 >30~100 >100~300 >300~1000 >1000~3000 H 0.03 0.05 0.1 0.2。