锂电池制作过程中常见异常及解决方案
锂电池故障及维修方法

锂电池故障及维修方法1. 故障:电池容量下降 / 维修方法:可使用恒流放电法进行电池再生当锂电池的容量大幅下降时,其性能就不能满足使用要求。
此时,采用恒流放电法,将电池放电至0伏特,不仅能够激活其所有电化学活性物质,而且可以消除电池内部的电池极面积不足、结构失效等问题,进而提高电池的容量和性能。
2. 故障:电池内阻过大 / 维修方法:可采用电池循环充放电法在使用锂电池过程中,经常会遇到电池内阻过大的现象。
此时,采用电池循环充放电法,即将电池充电至满电状态,然后放电到相对较低的电量。
在反复充放电使用过程中,可有效降低电池内阻,提高电池效率。
3. 故障:电池电量突然下降 / 维修方法:可采用锂电池电池病态诊断仪维修电池电量突然下降通常是由于电池内部化学反应过程异常所致。
在这种情况下,使用锂电池电池病态诊断仪对电池进行检测和诊断,从而确定电池的具体情况,随后针对性地进行维修,可以有效解决此问题。
4. 故障:电池温度异常 / 维修方法:可采用适宜的温度管理策略温度是影响锂电池寿命的重要因素。
电池异常温升可能导致电池内部化学反应变化,从而影响电池性能。
采用适当的温度管理策略可以有效控制电池的温度,提高其充放电效率和寿命。
5. 故障:电池化学反应发生变化 / 维修方法:可使用电化学还原法进行治理电池化学反应发生变化通常会导致电池性能严重下降。
在这种情况下,采用电化学还原法,即在电化学反应条件下,使用有机或无机还原剂还原电池内部化学物质,恢复电池的正常化学反应过程,进而提高其性能。
6. 故障:电池使用寿命过短 / 维修方法:可采用电池返修流程进行维修处理在使用锂电池过程中,由于一些原因,电池往往会出现寿命过短的问题。
此时,使用电池返修流程进行维修处理,包括电池同型号或者相似型号的电芯更换、历史问题的排查等,可以有效提高电池寿命。
7. 故障:电池使用过程中出现渗漏 / 维修方法:可采取零部件更换法进行修复如果锂电池内部的密封结构失效,电池就会出现漏电、渗漏等问题。
sci导师经验分享:锂离子电池常见问题、经典案例及解决思路汇总

sci导师经验分享:锂离子电池常见问题、经典案例及解决思路汇总锂离子电池是目前最常用的电池,广泛应用在各种电子产品和电动车辆中。
然而,在使用过程中,常常会出现一些问题,影响电池的性能和寿命。
在这里,我将分享一些锂离子电池常见问题、经典案例及解决思路,希望对大家有所帮助。
1. 容量衰减问题容量衰减是锂离子电池的一个常见问题,随着电池循环次数的增加,电池的容量会逐渐下降。
这可能是由于电解液中溶解的锂逐渐损失、正极材料的结构变化、电解液的分解或者电极材料的脱层等原因导致的。
为了延长电池的寿命,我们可以通过优化电池的设计、选择合适的材料和优化电池充放电控制策略来降低容量衰减的速度。
2. 过充和过放问题过充和过放是锂离子电池的另一个常见问题,过充会导致电池发热、气体产生,甚至发生爆炸;而过放则会导致电池损坏,降低电池的寿命。
为了避免过充和过放,我们可以通过添加合适的保护电路,控制充放电电压和电流以及定期对电池进行检测和维护来解决这一问题。
3. 电池老化问题随着电池使用时间的增加,电池材料会发生老化,电池内阻会增加,导致电池容量下降、充电时间延长、电池温升增大等问题。
为了延长电池的寿命,我们可以通过降低充放电速率、定期进行充放电循环、控制电池的工作温度等方法来减缓电池的老化速度。
4. 安全性问题安全性问题是锂离子电池的一个重要考虑因素,虽然锂离子电池具有高能量密度和高工作电压的优点,但是一旦受到损坏或操作不当,就容易发生过热、短路、爆炸等安全问题。
为了保证电池的安全性,我们可以通过加入保护电路、采用防爆设计、控制电池的温度和压力等方法来减少安全风险。
5. 充电速率问题充电速率是影响锂离子电池充放电性能的一个重要因素,很多时候电池在快速充放电的情况下会产生热量增加、容量减少和寿命缩短等问题。
为了提高电池的充电速率,我们可以通过优化电池材料、改进电池结构、调整充电控制策略等方法来提高电池的充电速率。
总的来说,锂离子电池是一种高性能电池,但是在使用过程中依然会出现一些问题。
锂电池涂布工序常见故障和解决方法汇总

锂电池涂布工序是锂电池生产中非常关键的一环,涂布工序的质量直接影响着锂电池的性能和安全性。
然而,在实际生产过程中,涂布工序常常会出现各种故障,影响整个生产线的正常运转。
本文将就锂电池涂布工序常见的故障进行梳理和总结,并提供相应的解决方法,以期为从事锂电池生产的工程师和技术人员提供一定的参考和帮助。
1. 涂布机出现涂布不均匀情况1.1 可能原因:涂布刀片磨损不均匀,导致涂布厚度不均匀;涂布辊与输送辊之间的间隙不一致;涂布材料的粘度不一致。
1.2 解决方法:定期更换涂布刀片,保持其锋利度;调整涂布辊与输送辊的间隙,确保一致;加强涂布材料的粘度控制,确保一致。
2. 涂布机出现漏涂现象2.1 可能原因:涂布刀片损坏或安装不良;输送辊转速过快,导致涂布材料无法被充分涂覆;涂布材料的粘度过高,无法完全附着在电极上。
2.2 解决方法:检查涂布刀片的完好度并及时更换;适当调整输送辊的转速,确保涂布材料可以被充分涂覆;控制涂布材料的粘度,避免过高。
3. 涂布机出现起泡现象3.1 可能原因:涂布材料的挥发性成分过快,导致涂布过程中产生气泡;涂布刀片与电极间的间隙不一致,导致气体无法顺利逸出。
3.2 解决方法:调整涂布材料的挥发性成分,避免过快;确保涂布刀片与电极间的间隙一致,避免气泡产生。
4. 涂布机出现堵塞现象4.1 可能原因:涂布材料中有杂质,导致管道堵塞;输送辊转速过慢,无法及时排出涂布材料。
4.2 解决方法:加强涂布材料的过滤工作,确保无杂质;适当调整输送辊的转速,确保涂布材料能够顺利流动。
5. 涂布机出现电极破损现象5.1 可能原因:输送辊表面粗糙,易划伤电极;涂布刀片安装不稳,易引起电极损伤。
5.2 解决方法:定期对输送辊进行维护和更换,确保表面光滑;定期检查涂布刀片的安装情况,确保稳定可靠。
总结:通过对锂电池涂布工序常见故障和解决方法的梳理和总结,我们可以看到,涂布工序的质量受到多种因素的影响,需要全面而细致的管理和维护。
锂电池几个常见的生产问题

锂电池几个常见的生产问题
锂电池的常见生产问题包括:
1. 电池内部短路:电池内部的正负极之间出现直接接触或非正常导电,导致电流畸变和能量损失。
这可能是由于材料的不均匀分布、外部金属污染、焊接不良等原因引起的。
2. 锂金属聚集:锂电池的负极是由锂金属构成的,在生产过程中,锂金属有可能在负极上聚集形成“锂树”的现象。
这会引起电池内部短路,并且会导致电池的容量下降和安全性问题。
3. 电解液泄漏:电解液是锂电池内部正负极之间传输离子的媒介物质,如果电解液泄漏,将导致电池容量下降、能量损失,甚至会引起电池的自燃和爆炸等严重安全问题。
电解液泄漏可能是由于电池的密封性不够好、外部物理损伤等原因引起的。
4. 电池Aging(老化):随着使用时间的增长,锂电池会出现电化学性能的衰减,如容量衰减、内阻增加等。
这可能是由于电池材料的失活、电池结构的损坏等原因导致的。
5. 温度管理问题:锂电池的工作温度范围较窄,过高或过低的温度都会对电池的性能和寿命产生不良影响。
因此,在生产过程中,需要采取相应的措施来控制电池的温度,例如增加散热结构、使用温度感应材料等。
这些问题在锂电池的生产中要特别注意,并通过合理的设计、优化生产工艺和严格的质量控制来解决。
同时,采取适当的安全措施来防范潜在的安全风险。
锂电制程异常管理办法
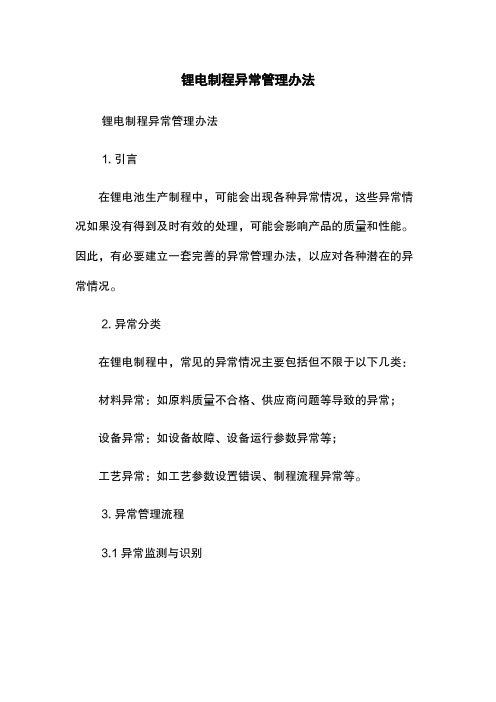
锂电制程异常管理办法锂电制程异常管理办法1. 引言在锂电池生产制程中,可能会出现各种异常情况,这些异常情况如果没有得到及时有效的处理,可能会影响产品的质量和性能。
因此,有必要建立一套完善的异常管理办法,以应对各种潜在的异常情况。
2. 异常分类在锂电制程中,常见的异常情况主要包括但不限于以下几类:材料异常:如原料质量不合格、供应商问题等导致的异常;设备异常:如设备故障、设备运行参数异常等;工艺异常:如工艺参数设置错误、制程流程异常等。
3. 异常管理流程3.1 异常监测与识别首先需要建立健全的异常监测系统,通过实时监测设备运行状态、工艺参数等,对异常情况进行及时识别。
监测系统可以采用传感器、监控软件等手段。
3.2 异常分类与评估一旦发现异常,需要及时对异常情况进行分类与评估,确定异常的性质和严重程度。
根据异常的类型和影响范围,制定相应的处理措施。
3.3 异常处理与记录针对不同类型的异常,制定相应的处理措施,包括紧急处理措施、原因分析、责任追究等。
在处理异常的过程中,需要及时记录异常情况、处理过程和结果,形成异常处理报告。
4. 异常处理措施4.1 预防为主在锂电制程中,预防异常的发生是最有效的措施。
可以通过加强原材料质量管理、设备维护保养、员工培训等手段,降低异常发生的概率。
4.2 紧急处理对于突发的异常情况,需要立即采取紧急处理措施,保障生产线的正常运行。
同时要及时通知相关部门和人员,协调处理。
4.3 原因分析与改进对于常见的异常情况,需要进行深入的原因分析,找出根本原因,并采取相应的改进措施,避免类似异常再次发生。
5. 异常管理的持续改进异常管理不是一次性任务,而是一个持续改进的过程。
需要建立健全的异常管理评估机制,定期对异常管理措施的有效性进行评估,发现问题及时改进,不断提高异常管理的水平。
6. 结语锂电制程异常管理办法对于提高产品质量、保障生产安全具有重要的意义。
只有建立完善的异常管理机制,才能有效应对各种潜在的异常情况,确保生产的顺利进行。
锂电池生产中各种不良原因及分析报告

各种不良原因的造成以及原因分析20130830一、短路:1、隔膜刺穿:1)极片边尾有毛刺,卷绕后刺穿隔膜短路(分切刀口有毛刺、装配有误);2)极耳铆接孔不平刺穿隔膜(铆接机模具不平);3)极耳包胶时未包住极耳铆接孔和极片头部(裁大片时裁刀口有毛刺);4)卷绕时卷针划破隔膜(卷针两侧有毛刺);5)圧芯时气压压力太大、太快压破隔膜(气压压力太大,极片边角有锐角刺穿隔膜纸)。
2、全盖帽时极耳靠在壳闭上短路:1)高温极耳胶未包好;2)壳壁胶纸未贴到位;3)极耳过长弯曲时接触盖帽或壳壁。
3、化成时过充短路:1)化成时,正负极不明确反充而短路;2)过压时短路;3)上柜时未装好或部电液少,充电时温度过高而短路。
4、人为将正负极短路:1)分容上柜时正负极直接接触;2)清洗时短路。
二、高阻:1、焊接不好:极耳与极片的焊接;极耳与盖有虚焊。
2、电液偏少:注液量不准确偏少;封口时挤压力度过大,挤出电液。
3、装配结构不良:极片之间接触不紧密;各接触点面积太小。
4、材质问题:极耳及外壳的导电性能;电液的导电率;石墨与碳粉的导电率。
三、发鼓:1、电池有水分:制造流程时间长;空气潮湿;极片未烘干;填充量过大,入壳后直接发鼓;极片反弹超厚,入壳后发鼓。
2、短路:过充或短路。
3、高温时发鼓;超过50°C温度发鼓。
四、低容量:1、敷料不均匀,偏轻或配比不合理。
2、生产时断片、掉料。
3、电液量少。
4、压片过薄。
五、极片掉料:1、烘烤温度过高,粘接剂失效。
2、拉浆温度过高。
3、各种材料因素:如P01、PVDF、SBR、CMC等性能问题。
4、敷料不均匀。
六、极片脆:1、面密度大,压片太薄。
2、烘烤温度过高。
3、材料的颗粒度,振头密度等。
各工位段不良原因的造成及违规操作一、配料:不良原因:1)各种添加剂与P01的配比;2)浆料中的气泡;导致拉浆时不良率增加,以及3)浆料中的颗粒;正负极活性物质的容量发挥和4)浆料的粘度。
极片掉料。
锂离子电池生产过程中的常见问题
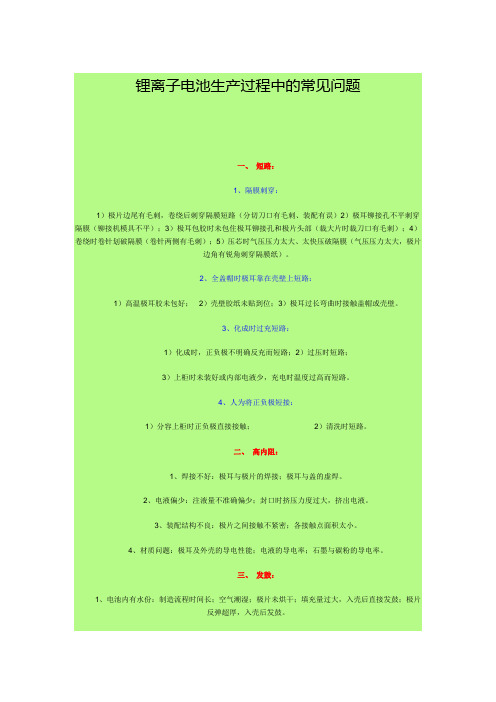
锂离子电池生产过程中的常见问题一、短路:1、隔膜刺穿:1)极片边尾有毛刺,卷绕后刺穿隔膜短路(分切刀口有毛刺、装配有误)2)极耳铆接孔不平刺穿隔膜(铆接机模具不平);3)极耳包胶时未包住极耳铆接孔和极片头部(裁大片时裁刀口有毛刺);4)卷绕时卷针划破隔膜(卷针两侧有毛刺);5)压芯时气压压力太大、太快压破隔膜(气压压力太大,极片边角有锐角刺穿隔膜纸)。
2、全盖帽时极耳靠在壳壁上短路:1)高温极耳胶未包好; 2)壳壁胶纸未贴到位;3)极耳过长弯曲时接触盖帽或壳壁。
3、化成时过充短路:1)化成时,正负极不明确反充而短路;2)过压时短路;3)上柜时未装好或内部电液少,充电时温度过高而短路。
4、人为将正负极短接:1)分容上柜时正负极直接接触;2)清洗时短路。
二、高内阻:1、焊接不好:极耳与极片的焊接;极耳与盖的虚焊。
2、电液偏少:注液量不准确偏少;封口时挤压力度过大,挤出电液。
3、装配结构不良:极片之间接触不紧密;各接触点面积太小。
4、材质问题:极耳及外壳的导电性能;电液的导电率;石墨与碳粉的导电率。
三、发鼓:1、电池内有水份:制造流程时间长;空气潮湿;极片未烘干;填充量过大,入壳后直接发鼓;极片反弹超厚,入壳后发鼓。
2、短路:过充或短路。
3、高温时发鼓;超过50℃温度发鼓。
四、低容量:1、敷料不均匀,偏轻或配比不合理。
2、生产时断片、掉料。
3、电液量少。
4、压片过薄。
五、极片掉料:1、烘烤温度过高,粘接剂失效。
2、拉浆温度过高。
3、各种材料因素:如P01、PVDF、SBR、CMC等性能问题。
4、敷料不均匀。
六、极片脆:1、面密度大,压片太薄。
2、烘烤温度过高。
3、材料的颗粒度,振实密度等。
锂电池的常见故障及修复方法

锂电池的常见故障及修复方法1、电动车没有显示,电池没有输出,电池不能充电等2、锂电池充电器故障造成的充不进电,充不满电,充电器不变灯,充电时间变短或变长等3、锂电池电压正常,骑行距离很短就断电,停一会又恢复骑行,循环出现时好时坏的状况4、锂电池保护板自身损坏引起的锂电池不能正常工作,电池保护板不工作造成的部分电池芯损坏等。
锂电池的常见故障及修复方法现在济南锂电池为你讲解电动车锂电池的修复方法电动车锂电池修复的方法:1、重新配组:整组电池损环以后,我们往往对电动车锂电池进行充放电检测,在检验中往往会发现一组电池中有50%的电池并没有损坏。
其原因也就是在串连电池组中,个别的电池落后形成整组电池功能下降,以至于整组电瓶功能下降。
2、补水:对电动车锂电池使用了4个月左右的电池进行一次补水,可以延长电池的使用寿命,延长时间平均达到3个月以上。
应该注意的是,每次补水以后,电池都利用处于过充电状态把电池由“准贫液”转为“贫液”状态,而这个过充电对提高电池容量是有好处的。
3、消除硫化:采用电池修复设备,对电池进行消除硫化的处理。
4、微粒发生器:采取微粒发生器并联在电池上,对电池进行修复。
这种方法对修复电动车锂电池比较好,但是由于修复的比较彻底,所以,如果没有过放电,对于连续使用的电动车锂电池来说,往往是彻底消除了电池硫化的可能性。
5、电动车锂电池综合修复方法:对电动车锂电池采用定期检验,及时除硫和补水,单只电池充电、重新配组。
电池说明,如果是免维护,一般不需要加水。
如果需要加水,先检测一下电动车电池自身的电解液密度,根据不同的情况选择相应浓度或没有浓度的水进行补充,这样才能让电池容量有所增加或延长使用寿命。
- 1、下载文档前请自行甄别文档内容的完整性,平台不提供额外的编辑、内容补充、找答案等附加服务。
- 2、"仅部分预览"的文档,不可在线预览部分如存在完整性等问题,可反馈申请退款(可完整预览的文档不适用该条件!)。
- 3、如文档侵犯您的权益,请联系客服反馈,我们会尽快为您处理(人工客服工作时间:9:00-18:30)。
锂电池制作过程中常见异常及解决方案
一、浆料异常及解决方案
异常1:沉降,粘度变化大
原因:浆料不稳定的原因是吸水,粘接剂少,未分散好;
解决方法:调整原材料选型,主要是考虑比表,粘度等,调整搅伴工艺(主要转速,线速度,时间等),调整粘结剂用量,控制环境水分。
异常2:固含量低
原因:消耗NMP多,主要原因是正极比表大,正极径小,搅伴时间长,粘接剂固含量低;
解决方法:调整搅伴工艺(主要转速,线速度,时间等),调整正极选型,调整粘结剂选型。
异常3:难过筛
原因:大颗粒,主要原因是正极大颗粒,正极粘度高,吸水团聚;解决方法:控制材料颗粒,降低浆料粘度,防止吸水。
异常4:无流动性,变果冻
原因:吸水,主要原因是正极水分高,正极PH高,正极比表大,NMP水分高,环境湿度大,粘结剂水分高;
解决方法:控制环境湿度,控制原材料水分,降低原材料PH值。
二、辊压前极片异常解决方案
异常1:颗粒
原因:主要原因是有颗粒或团聚,原材料大颗粒,浆料粘度高,浆料团聚;
解决方案:减少材料大颗粒,降低浆料粘度,控制吸水;
异常2:裂纹
原因:是极片内NMP挥发慢,烘箱温度高,涂布速度快;
解决方法:降低前段烘箱温度,降低涂布速度;
异常3:气泡
原因:浆料有气泡主要是因抽真空不彻底,搁置时间短,抽真空时搅伴速度过快;
解决方法:延长抽真空时间,加入表面活性剂消泡;
异常4:划痕
原因:主要是浆料粘度高,来料大颗粒,浆料团聚,涂布刀口有干料;
解决方法:减少材料大颗粒,降低浆料粘度,控制吸水;
异常5:拖尾
原因:主要是粘度偏高或粘度偏低;
解决方法:调整粘度;
异常6:质量不稳定
原因:浆料不稳定的主要原因是浆料吸水,粘结剂胶水用量少,未分散好,涂布设备波动;
解决方法:控制吸水,调整设备,调整粘度;
三、辊压后极片异常及解决方案
异常1:断片,脆片
原因:使用压实过高的原因有烘烤时间长,温度高,粘结剂胶水变性,极片吸水;
解决方法:降低压实,极片烘烤时间缩短;
异常2:白点
原因:极片内层NMP挥发慢的原因是烘箱温度高,涂布速度快;解决方法:控制吸水(原材料,环境);
异常3:起皮,掉料
原因:脱粉主要是材料水分敏感,极片存储环境湿度大;
解决方法:控制吸水(原材料,环境);
四、电芯异常及解决方案
异常1:电芯工艺,电芯卷绕过松负极过量比设计不合理,安全系数低,正负未包裹正极,正负极片距离不均匀等原因;
解决方法:控制卷绕工艺一致性,提高负极过量化,修改正负极片长度设计,优化电芯制作工艺;
异常2:正极,混料过程不均匀,
解决方法:控制浆料一致性及涂布一致性;
异常3:负极,局部区域量少,浸润性差,压实过高或过低,颗粒太大,有效嵌锂面积小,材料配向性差或导电性差,面密度过高,混
料不均匀,粘接剂锂电胶水上浮等问题;
解决方法:控制浆料一致性及涂布一致性,优化负极过量比,控制原材料颗粒,优化负极配比,优化负极面密度,优化锂胶水粘合剂型号;
异常4:电解液,电导率低,粘度大,SEI膜阻抗大,电解液中有气泡,SEI膜不均匀等问题;
解决方法:提高电解液电导率,降低电解液粘度,优选成膜添加剂,控制电解气泡,控制化成工艺,保证成膜一致性;
异常5:隔膜,孔隙率低,隔膜对电解液浸润性差,孔隙分布不均匀等问题;
解决方法:优选孔隙率适合的隔膜,提高电解液的浸润性,控制隔膜来料,保证一致性;
异常6:充电制度,充电电流大,充电温度低,截止电压高,电芯内温度分布不均匀等问题;
解决方法:小电流化成,适当降低环境温度,适当降低充电截止电压,提高极片过流能力(宽极耳);
五、电性能异常分析及解决方案
异常1:平台低
原因:电解液粘度大,电芯内阻大,放电电流大,环境温度低等问题;
解决方法:电解液来料相关指标确认及优化,电芯内阻影响因素确认,控制环境温度及放电电流;
异常2:容量低:
原因:正极敷料量少,压实偏大,负极效率低,环境温度低,电芯吸水,电芯倍率差,电解液浸润性差等问题;
解决方法:正极敷料量确认,正极压实及挥发确认,负极压实及首效确认,电芯倍率及测试环境温度等确认,拆解失效电池分板界面情况及影响因素;
异常3:自放电大:
原因:原材料杂质多,极片微粉多,极片分切毛刺大,隔膜孔隙率大等问题;
解决方法:制程中各工序及设备控制,金属杂质来源查找并控制,各原材料的金属材质含量确认,隔膜及其他辅料性能确认;
异常4:高温存储差:
原因:电解液高温性能差,电芯水分含量偏高,正极残锂量高等问题;
解决方法:电解液水分配方成分确认,电芯制程水分控制,正极残锂量确认;
异常5:倍率差:
原因:导电剂少,正极粘结性差,电芯内阻大,压实偏大,隔膜性能影响,电解液电导率低等问题;
解决方法:配方及设计参数确认,电芯内阻相关因素确认,电芯制程的环境控制,拆解失效电池分析界面情况及影响因素;
异常6:循环差:
原因:负极析锂,过程吸水,隔膜透气性差,压实偏大,测试温度变化,注液量少,SEI膜成膜差等问题;
解决方法:压实及注液量等影响因素确认,负极过量比优化,电芯倍率及测试环境温度等确认,拆解失效电池分析界面情况及影响因素;。