压片成型机
双层压片机工作原理

双层压片机工作原理
双层压片机是一种用于制备片剂的设备,其工作原理如下:
1. 准备药粉:将需要制备的药物粉末按照一定的配方准备好,并确保粉末的颗粒大小均匀。
2. 填充药粉:将药粉填充至压片机的上层模具中,确保填充均匀且紧密。
3. 压制前压:在药粉填充完毕后,开始进行压制前的压力调整。
这个步骤旨在减小粉末在压制过程中的体积变化,使片剂更加均匀。
4. 主压:开始进行主压制。
压片机利用机械力将上层模具向下移动,使药粉受到一定的压力。
这个压力会使药粉中的颗粒紧密结合,形成片剂的形状。
5. 卸药:压制完成后,释放压力,将压制的片剂从模具中取出。
6. 注意事项:在压制过程中需要注意控制压力的大小,过大的压力可能导致片剂的破裂或变形,而过小的压力则可能导致片剂松散,无法达到所需的质量要求。
此外,还需要注意药粉的填充均匀性和压制时间的控制,以确保最终制备出的片剂质量良好。
实验六单冲压片机结构与使用

高度调节机构通常由高度调节螺钉和高度调节弹簧组成,用于调节上 模和下模的高度差。
03
单冲压片机工作原理
工作流程
准备阶段
将药物置于下模腔内,放置上 模源自并确保模腔闭合。压片阶段上模向下运动,通过压力将药 物压缩成片剂。
脱模阶段
上模上升,片剂从模腔中脱出 。
清理阶段
模腔和冲头进行清洗或润滑。
工作原理分析
阅读说明书
仔细阅读单冲压片机的使用说明书,了解操 作步骤和注意事项。
操作步骤
安装模具
将模具安装在单冲压片机的冲模固定板上 ,确保安装牢固。
取出成品
压片完成后,打开模具,取出压好的药片 。
添加原料
将所需原料加入模具中,确保原料填充均 匀。
开始压片
确认所有设置正确后,启动单冲压片机进 行压片操作。
调整参数
实验六单冲压片机结构与使用
目录
• 单冲压片机简介 • 单冲压片机结构 • 单冲压片机工作原理 • 单冲压片机的使用与操作 • 单冲压片机的维护与保养 • 单冲压片机的发展趋势与展望
01
单冲压片机简介
定义与特点
定义
单冲压片机是一种用于将药物或物料 压制成片剂的机械设备。
特点
结构简单、操作方便、适用范围广, 可适用于不同性质和规格的药物或物 料压制。
高精度与高稳定性
为了满足制药行业对药品质量和安全性的要求,单冲压片 机将不断提高设备的精度和稳定性,确保生产出的片剂一 致性好、可重复性强。
模块化与可定制化
为了满足不同客户和生产线的需求,单冲压片机将采用模 块化设计,方便客户根据自身需求进行定制化配置,提高 设备的适用性和灵活性。
市场发展前景
市场需求持续增长
压片机工作过程及其原理
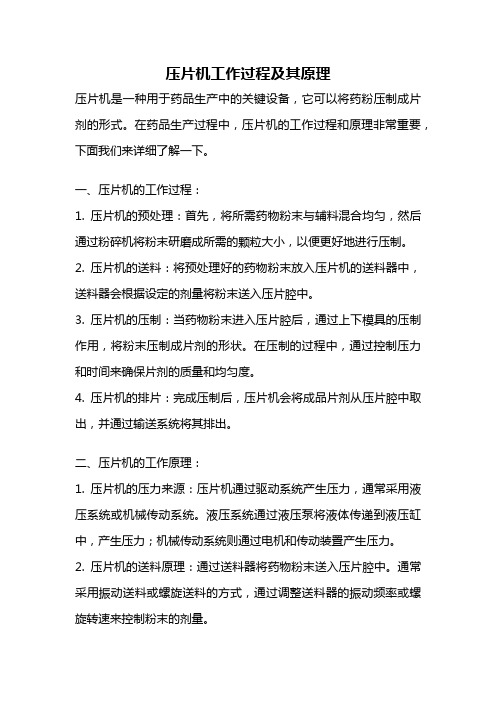
压片机工作过程及其原理压片机是一种用于药品生产中的关键设备,它可以将药粉压制成片剂的形式。
在药品生产过程中,压片机的工作过程和原理非常重要,下面我们来详细了解一下。
一、压片机的工作过程:1. 压片机的预处理:首先,将所需药物粉末与辅料混合均匀,然后通过粉碎机将粉末研磨成所需的颗粒大小,以便更好地进行压制。
2. 压片机的送料:将预处理好的药物粉末放入压片机的送料器中,送料器会根据设定的剂量将粉末送入压片腔中。
3. 压片机的压制:当药物粉末进入压片腔后,通过上下模具的压制作用,将粉末压制成片剂的形状。
在压制的过程中,通过控制压力和时间来确保片剂的质量和均匀度。
4. 压片机的排片:完成压制后,压片机会将成品片剂从压片腔中取出,并通过输送系统将其排出。
二、压片机的工作原理:1. 压片机的压力来源:压片机通过驱动系统产生压力,通常采用液压系统或机械传动系统。
液压系统通过液压泵将液体传递到液压缸中,产生压力;机械传动系统则通过电机和传动装置产生压力。
2. 压片机的送料原理:通过送料器将药物粉末送入压片腔中。
通常采用振动送料或螺旋送料的方式,通过调整送料器的振动频率或螺旋转速来控制粉末的剂量。
3. 压片机的压制原理:压片机通过上下模具的压制作用将药物粉末压制成片剂。
模具通常具有特定的形状和尺寸,通过调整模具的设计和压制参数,可以控制片剂的大小、形状和硬度。
4. 压片机的排片原理:完成压制后,压片机通过输送系统将成品片剂排出。
输送系统通常包括输送带、输送辊等装置,通过调整输送速度和输送方式,可以实现高效的片剂排出。
总结:压片机在药品生产中起到了至关重要的作用,通过控制压力、时间、剂量等参数,可以实现对片剂质量的精确控制。
压片机的工作过程和原理相对简单,但对操作人员的技术要求较高。
只有掌握了压片机的工作原理和操作技巧,才能保证药品的质量和生产效率。
压片机注意事项有哪些
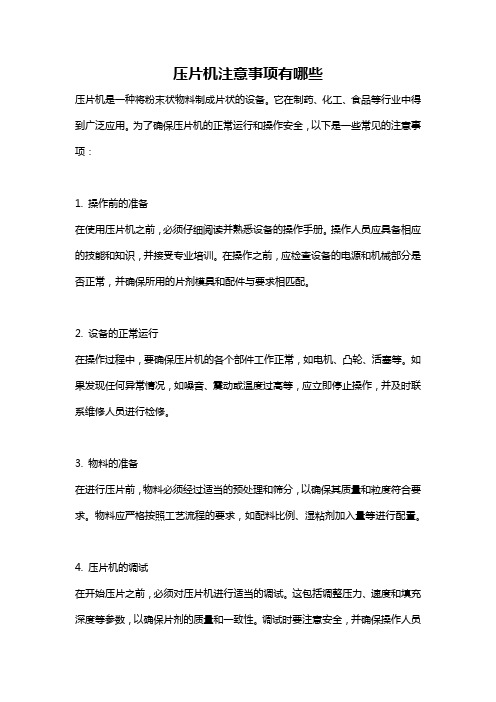
压片机注意事项有哪些压片机是一种将粉末状物料制成片状的设备。
它在制药、化工、食品等行业中得到广泛应用。
为了确保压片机的正常运行和操作安全,以下是一些常见的注意事项:1. 操作前的准备在使用压片机之前,必须仔细阅读并熟悉设备的操作手册。
操作人员应具备相应的技能和知识,并接受专业培训。
在操作之前,应检查设备的电源和机械部分是否正常,并确保所用的片剂模具和配件与要求相匹配。
2. 设备的正常运行在操作过程中,要确保压片机的各个部件工作正常,如电机、凸轮、活塞等。
如果发现任何异常情况,如噪音、震动或温度过高等,应立即停止操作,并及时联系维修人员进行检修。
3. 物料的准备在进行压片前,物料必须经过适当的预处理和筛分,以确保其质量和粒度符合要求。
物料应严格按照工艺流程的要求,如配料比例、湿粘剂加入量等进行配置。
4. 压片机的调试在开始压片之前,必须对压片机进行适当的调试。
这包括调整压力、速度和填充深度等参数,以确保片剂的质量和一致性。
调试时要注意安全,并确保操作人员不会接触到运动部件。
5. 清洁和维护定期进行设备的清洁和维护是确保压片机正常运行的关键。
清洁时要注意切勿使用腐蚀性或磨损性的清洁剂,以免损坏设备。
严格按照设备维护手册的要求进行维护,如更换润滑油、清理滤网等。
6. 安全操作在操作压片机时,必须严格遵守安全操作规程,如佩戴个人防护装备、正确使用工具和设备等。
在操作过程中,不得将手指、手臂或其他物体放入运动部件和压力区域,以避免事故的发生。
7. 操作记录和数据记录在每次操作完毕后,应及时记录和保存相关数据,如压力、速度、片剂重量等参数,以便于进行产品质量的追溯和分析。
操作记录和数据记录应妥善保存,并按照相关规定进行备份。
8. 紧急情况的处理在紧急情况下,如设备故障、停电等,操作人员应立即停止操作,并据情况采取相应的安全措施。
如需进行紧急维修或处理,应报告相关部门,并等待专业维修人员的指导。
9. 质量控制和检验在压片操作中,质量控制是非常重要的环节。
压片成型机(1)

压片成型机一、引言压片成型机是一种常见的制药设备,用于将药物粉末或颗粒通过压制成型,制成片状或其他固体形式。
本文将介绍压片成型机的工作原理、主要部件和操作流程。
二、工作原理压片成型机的工作原理基于压力和摩擦力。
主要包括以下几个步骤:1.进料和预压:药物粉末或颗粒通过进料口进入压片机,然后通过预压部分,使粉末或颗粒初步成形。
2.主压:在主压部分,药物粉末或颗粒受到高压力的作用,被压制成所需要的片状或固体形式。
主要的压制力来自压片机的压力系统,通常是液压系统。
3.排片与回收:完成主压后,片剂通过模具的出料口排出,进入下一道工序。
如果有未成型的粉末或颗粒没有完全压制,可以通过回收系统回收再次使用。
三、主要部件压片成型机通常包括以下主要部件:1.进料口:用于将药物粉末或颗粒输入压片机。
2.预压部分:对进料药物粉末或颗粒进行初步成形。
3.主压部分:通过应用高压力,将药物粉末或颗粒压制成所需要的片状或固体形式。
4.模具:用来给药物粉末或颗粒提供所需的形状和尺寸。
5.压力系统:通常是液压系统,用来提供所需的压制力。
6.排片口:用于排出已成形的片剂。
7.回收系统:用于回收未成型的粉末或颗粒。
四、操作流程以下是一般的压片成型机操作流程:1.准备工作:将所需的药物粉末或颗粒准备好,清洁和检查压片机的部件和模具。
2.设置参数:根据所需的片剂规格和要求,设置合适的参数,包括压力、压力保持时间和压片速度等。
3.开始运行:按下启动按钮,启动压片机,并观察运行状态。
4.监控和调整:根据实际情况,监控片剂的质量和产能,如果需要调整参数或操作,及时进行调整。
5.结束操作:完成生产任务后,关闭压片机,并进行清洁和维护工作。
五、安全注意事项在使用压片成型机时,需要注意以下安全事项:1.防护装置:必须确保防护装置完好,并正确使用。
避免手部或其他身体部位接触到运动部件。
2.操作规程:严格按照操作规程进行操作,禁止随意更改参数或操作。
3.维护保养:定期维护保养设备,确保设备处于良好的工作状态。
单冲压片机的压片原理

单冲压片机的压片原理
单冲压片机是一种常用的冲压设备,用于对金属或非金属材料进行冲压成型。
其工作原理主要分为以下几个步骤:
1.上死点位置:压片机的上模和下模紧密结合,形成一定的工作空间。
2.下行移动:压片机的上模开始下行移动,材料被夹在上模和下模之间。
3.下死点位置:上模完全与下模接触,形成冲压区域。
4.冲压:上模施加一定的力量,冲击压实材料,使其在冲模的作用下发生塑性变形。
5.上行移动:上模开始上行移动,材料被释放出来。
6.脱模:上模和下模之间的材料脱离,制成所需形状。
单冲压片机主要通过模具和机械力将材料冲压成所需形状,其压片原理是利用力学原理实现的。
通过上模的移动和施加力量,使材料在模具内发生塑性变形,最终成型。
不同的模具设计和压力设置可以制造出不同形状和尺寸的零件。
压片机操作方法详解

压片机操作方法详解
压片机是一种常用的制药设备,用于将药物粉末压制成固体药片。
以下是压片机的操作方法详解:
1. 开启电源:先确保电源开关处于关闭状态,然后将电源插头插入插座,再将电源开关打开。
2. 准备药物粉末:根据药方的要求,准备好需要压制成药片的药物粉末。
确保药物粉末的质量符合要求,并进行必要的筛选和混合。
3. 调整机器参数:根据药方的要求,调整压片机的压力、速度和模具的尺寸等参数。
这些参数决定了药片的质量和规格。
4. 安装模具:根据药片的规格和形状,选择合适的模具,并将其安装在压片机上。
确保模具安装稳固,并且没有破损或污染。
5. 预压操作:在药物粉末放置区放入适量的药物粉末,并用手柄或压片机的控制按钮进行初步压制操作。
这一步骤可以使药物粉末在模具中均匀分布,并去除空气和杂质。
6. 压制操作:将预压过的药物粉末放置在模具中,并关闭压片机的模具盖。
然后,根据压片机的指示或程序,启动压制操作。
压片机将施加压力将药物粉末压
制成固体药片。
7. 取出药片:压制完成后,打开模具盖,将制成的药片取出。
用金属托盘或其他容器接收药片,并进行质量检查。
8. 清洁和维护:在使用完压片机后,及时清洁和维护设备。
清除残留的药物粉末、杂质和污垢,并按照清洁和维护指南进行相应的维护。
以上就是压片机的操作方法详解。
正确的操作和维护可以确保压片机的正常工作和药片的质量。
请按照操作手册和相关规定进行操作,并遵守安全操作规程。
双出料压片机的基本原理及结构特点
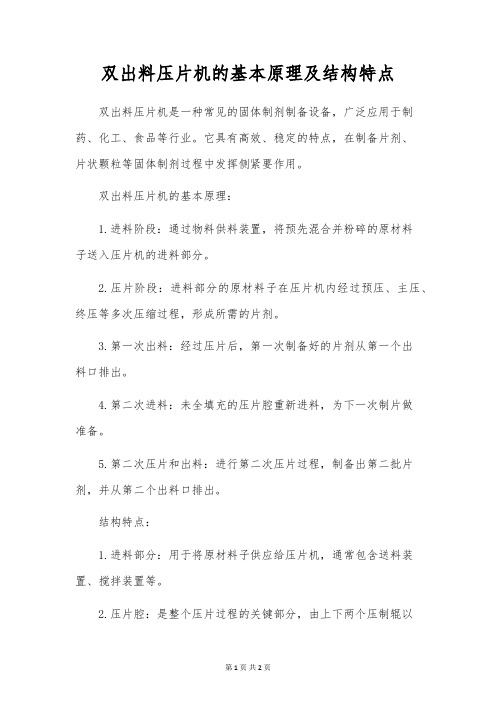
双出料压片机的基本原理及结构特点双出料压片机是一种常见的固体制剂制备设备,广泛应用于制药、化工、食品等行业。
它具有高效、稳定的特点,在制备片剂、片状颗粒等固体制剂过程中发挥侧紧要作用。
双出料压片机的基本原理:1.进料阶段:通过物料供料装置,将预先混合并粉碎的原材料子送入压片机的进料部分。
2.压片阶段:进料部分的原材料子在压片机内经过预压、主压、终压等多次压缩过程,形成所需的片剂。
3.第一次出料:经过压片后,第一次制备好的片剂从第一个出料口排出。
4.第二次进料:未全填充的压片腔重新进料,为下一次制片做准备。
5.第二次压片和出料:进行第二次压片过程,制备出第二批片剂,并从第二个出料口排出。
结构特点:1.进料部分:用于将原材料子供应给压片机,通常包含送料装置、搅拌装置等。
2.压片腔:是整个压片过程的关键部分,由上下两个压制辊以及四周的导向器、隔板等构成。
3.出料部分:用于将制备好的片剂排出,通常设有两个出料口。
4.运转装置:用于带动压片腔旋转,完成连续的制片过程。
双出料压片机的工作过程可以简单分为以下几个步骤:1.进料和预压:原材料子通过进料部分送入压片腔,经过预压装置进行初步压缩,使原材料子形成颗粒状。
2.主压:主压装置开始作用,将原材料子颗粒进一步压缩,形成密实的片剂。
3.第一次出料:第一批制备好的片剂从第一个出料口排出。
4.第二次进料和压片:未全填充的压片腔重新进料,为下一次的制片做准备。
随后进行第二次压片,形成第二批片剂。
5.第二次出料:第二批制备好的片剂从第二个出料口排出。
- 1、下载文档前请自行甄别文档内容的完整性,平台不提供额外的编辑、内容补充、找答案等附加服务。
- 2、"仅部分预览"的文档,不可在线预览部分如存在完整性等问题,可反馈申请退款(可完整预览的文档不适用该条件!)。
- 3、如文档侵犯您的权益,请联系客服反馈,我们会尽快为您处理(人工客服工作时间:9:00-18:30)。
压片成形机一、设计题目设计目的机械设计是根据使用要求对机械的工作原理、结构、运动方式、力和能量的传递方式、各个零件的材料和形状尺寸以及润滑方式等进行构思、分析和计算,并将其转化成为制造依据的工作过程。
机械设计是机械产品生产的第一步,是决定机械产品性能的最主要环节,整个过程蕴含着创新和发明。
为了综合运用机械原理课程的理论知识,分析和解决与本课程有关的实际问题,使所学的知识进一步巩固和加强,我们参加了此次的机械原理课程设计。
(1)总功能要求设计自动压片成形机,将具有一定湿度的粉状原料(如陶瓷干粉或药粉)定量送入压形位置,经压制成后脱离该位置。
机器的整个工作过程(送料-压形-脱离)均自动完成。
该机器可以压制陶瓷圆形片坯和药剂(片)等。
表1.2.1压片成形机设计数据(2)工作原理1、压片成型机工艺动作分解:⑴干粉料均匀筛入圆筒形型腔(图1.2.2a)。
⑵下冲头下沉3mm,预防上冲头进入型腔时粉料扑出(图1.2.2b)。
⑶上和下冲头同时加压(图1.2.2c),并保持一段时间。
⑷上冲头退出,下冲头随后顶出压好的片坯(图1.2.2d)。
⑸料筛推出片坯(图1.2.2a)。
原始数据1、冲头压力 100 000N 150 000N2、生产率 15片/min 20片/min3、机器运转不均匀系数 0.08 0.104、电机转速 970r/min 1450r/min 二.设计要求(1)设计要求⑴压片成形机一般至少包括连杆机构和凸轮机构和齿轮机构在内的三种机构。
⑵画出机器的运动方案简图与运动循环图。
拟订运动循环图时,执行构件的动作起止位置可根据具体情况重叠安排,但必须满足工艺上各个动作的配合,在时间和空间上不能出现干涉。
⑶设计凸轮机构,自行确定运动规律,选择基圆半径,校核最大压力角与最小曲率半径,计算凸轮轮廓线。
⑷设计计算齿轮机构,确定传动比,选择适当的摸数。
⑸对连杆机构进行运动设计。
并进行连杆机构的运动分析,绘出运动线图。
如果是采用连杆机构作为下冲压机构,还应该进行连杆机构的动态静力分析,计算飞轮转动惯量。
⑹编写设计计算说明书。
⑺学生可进一步完成机器的计算机演示验证和凸轮的数控加工等。
(2)上冲头和下冲头与料筛的设计要求图1.3.2设计要求⑴上冲头完成往复直移(与动铅垂上下),下移至重点后有短时间的间歇,起保压作用,保压时间为0.4s左右。
因为冲头上升后要留有料筛进入的空间,故冲头行程为90~100mm。
因为冲头压力比较大,因而加压机构应有增力功能(图1.3.2a)。
⑵下冲头先下沉3mm,然后上升8mm,加压后停歇保压,继而上升16mm,将成形片坯顶到与台面平齐后停歇,待料筛将片坯推离冲头后,再下移18mm,到待料位置(图1.3.2b)。
⑶料筛在模具型腔上方往复振动筛料,然后向左退回。
待批料成型并被推出型腔后,料筛在台面上右移约45~50mm,推卸片坯(图1.2.3c)。
设计提示⑴各执行机构应包括:实现上冲头运动的主加压机构和实现下冲头运动的辅助加压机构和实现料筛运动的上下料机构。
各执行机构必须能满足工艺的运动要求,可以有多种不同型式的机构选用。
⑵由于压片成形机的工作压力比较大,行程短,一般采用肘杆式增力冲压机构作为主体机构。
它是由曲柄摇杆机构滑块机构串接而成。
先设计摇杆滑块机构,为了保压,要求摇杆在铅垂位置的±2°范围内的滑块的位移量≦0.4mm。
据此可得摇杆长度:r≤1+λ−√λ2+(sin2°)式中:为摇杆滑块机构中连杆与摇杆长度之比,一般取1~2。
根据上冲头的行程长度,即可得摇杆的另一极限位置,摇杆的摆角以小于60°为宜。
设计曲柄摇杆机构时,为了“增力”,曲柄的回转中心可在摇杆活动链和垂于摇杆铅垂位置的直线上适当选取,以改善机构在冲头下极限位置附近的传力性能。
根据摇杆的三个极限位置(±2°位置和另一个极限位置),设定与之对应的曲柄三个位置,其中两个对应于摇杆的两个极限位置,曲柄应在与连杆共线的位置,曲柄另一个位置可根据保压时间来设定,因此可根据两连架杆懂得三组对应位置来设计此机构。
设计完成后,应检查曲柄存在条件,若不满足要求,则重新选择曲柄回转中心。
也可以在选择曲柄回转中心以后,根据摇柄两个极限位置时曲柄和连杆共线的条件,确定连杆和曲柄长度。
在检查摇杆在铅垂位置±2°时,应该注意曲柄对应转角是否满足保压时间要求。
曲柄回转中心距摇杆铅垂位置越远,机构行程速比系数越小,冲头在下极限位置附近的位移变化越小,但机构尺寸越大。
⑶辅助加压机构可采用凸轮机构,推杆运动线图可以根据运动循环图确定。
设计时,要正确确定凸轮基圆半径。
为了便于传动,可以将筛料机构置于主体机构曲柄同侧。
整个机构系统采用一个电动机集中驱动。
要注意主体机构曲柄和凸轮机构起始位置间的相位关系,否则机器将不能正常工作。
⑷可以通过对主体机构进行运动分析,以及冲头相对于曲柄转角的运动线图,检查保压时间是否近似满足要求。
进行机构动态静力分析时,要考虑各杆(曲柄除外)的惯性力和惯性力偶,以及冲头的惯性力。
冲头质量m冲和各杆质量m杆(各杆质心位于杆长中点)以及机器运转不均匀系数均见表1,则各杆对质心轴的转动惯量可求。
认为上下冲头同时加压和保压时生产阻力为常数。
飞轮的安装位置由设计者自行确定,计算飞轮转动惯量时可以不考虑其他机构的转动惯量。
确定电动机所需要功率时还要考虑下冲头运动和筛料运动所需功率。
三.运动方案评估(上冲头为主)上冲头运动方案设计及选择方案一此设计优缺点:方案1采用的是凸轮机构的设计方案。
如图所示,该机构由2个可动构件和机架组成,包含1个高副和2个低副,其自由度F = 3*2 - 2*2 - 1*1 = 1,其自由度也等于原动件个数,故其运动也确定。
机构中,能满足上冲头的设计保压要求,不过在下压过程中只依靠从动件自身的重力,下压力不足,且传动性不及方案1好,并且由于从动件的形成较大,故凸轮在设计制造时的尺寸也会很大,而且凸轮与滚子之间为点接触易磨损。
所以予以否决。
方案二此设计优缺点:方案2采用的是气缸做为动力的设计方案。
如图所示该机构由7个可动构件和机架组成,包含10个低副,其自由度为F = 3*7 - 2*10 = 1,其自由度也等于原动件个数,故其运动也确定。
此机构只需一个很小的力就能产生很大的顶升力,但对材料的要求很高,要实现整套机器的运动需要多个油泵,成本较高,且速度较慢。
方案三此设计优缺点:方案3采用的是连杆机构的设计方案。
如图所示,该机构由5个可动构件和机架组成,包含6个转动副和1个移动副,共计7个低副。
故方案1所用机构的自由度F = 3*5 - 2*7 = 1,其自由度等于原动件个数,故其运动确定。
此方案3是在上冲头方案中最好的一个,既能提供较大的工作压力,行程较短,也能有保压功能,整体结构简单、轻盈,并能够轻松达到上冲头的行程要求。
也是本次设计采用的方案。
3.1 机构选择:驱动方式采用电动机驱动。
由已知的压片成形机的功能分解,分别选择相应的机构,以实现所需的各项功能。
见表3。
表3 压片成形机的机构选型3.2 运动协调设计:压片成形机是由曲柄滑块机构,凸轮机构组成。
负责上冲头工作的曲柄周转一圈完成一次工作循环,同样下冲头盘形凸轮以同样的转速转一圈作为一个工作周期,制作出成品。
其他的送料、齿轮机构作为辅助机构。
最终压片成形机设计如下图:说明:此方案使用曲柄摇杆机构和摇杆滑块机构串接而成,结构简单、轻盈,能满足保压要求,并能够轻松达到上冲头的行程要求。
由于此方案中,料筛采用凸轮机构,可使其达到往复振动的运动效果;下冲头也采用凸轮机构,可达到保压效果,且此方案的稳定性较好,故选用此方案。
四、运动循环图设计(详见附录1)根据工艺动作拟定运动循环图●以上冲头加压机构主动件转角为横坐标,以各机构执行构件的位移为纵坐标画出位移曲线。
循环运动图上的位移曲线主要着眼于运动的起迄位置,而不必准确表示出运动规律。
●拟定运动循环图时,可执行构件的动作起迄位置可根据具体情况重叠安排,但必须满足工艺上各个动作的配合,在时间和空间上不能出现“干涉”。
●从运动的特性来看,上,下冲头的运动轨迹在同一条竖直移动导路上,并且与送料机构的运动轨迹垂直相交,所以应避免这三个机构各自的运动出现互相干涉的情况,如上,下冲头的运动速度的冲突,送料机构水平移动与上,下冲头竖直移动的运动冲突等,以确保各个机构的运动不发生冲突,从而保证各自设计功能的实现和机器正常的运作。
拟定运动循环图:见附录1五、连杆机构尺寸计算(见附录2)5.1 设计要求(1)上冲头行程为100mm左右(2)当摇杆角度和铅垂位置之间相差±2°时,滑块的位移小于0.4mm(即产生保压的功能)(3)摇杆的角度小于60度(4)曲柄摇杆机构必须具有一定急回特性,以致更多的时间用于加压5.2 设计过程(1)由于压片机的工作压力较大,行程较短,一般采用肘杆式增力冲压机构作为主体机构,它是由曲柄摇杆机构和摇杆滑块机构串联而成。
先设计摇杆滑块机构,为了保压,要求摇杆在垂直位置的±2°范围内,滑块的位移量≤0.4mm。
据此可得摇杆长度0.4r≤1+λ−√λ2+(sin2°)2摇杆滑块机构中连杆与摇杆长度之比,一般取1-2。
式中λ=λλ根据上冲头的行程长度,即可得摇杆的另一极限位置,摇杆的摆角以小于60°为宜。
设计机构时,为了“增力”,曲柄的回转中心可在摇杆活动铰链、垂直于摇杆垂直位置的直线上适当选取,以改善机构在冲头在下极限位置附近放的传力性能。
根据摇杆的三个极限位置(±2°位置和另一极限位置),设定与之对应的曲柄上个位置,其中对应摇杆的两个位置,曲柄应在于连杆共线的位置,曲柄的另一位置可以根据保压时间来设定,则可根据两连架杆的三组对应位置来设计此机构。
设计完成后,应该检查曲柄的存在条件,若不满足要求,则重新选择曲柄的回转中心。
也可以选择曲柄中心后,根据摇杆两极限位置时曲斌和连杆共线的条件,确定连杆和曲柄的长度,再检查摇杆在垂直位置±2°时,曲柄对应转角是否满足保压时间要求。
曲柄回转中心据摇杆垂直位置越远,机构行程速比系数越小,冲头在下极限位置附近的位移变化越小,但机构尺寸越大。
在这里我取λ=1.5,得r≤394r=240mm,冲头行程取100mm,算出摇杆的摆角等于44°。
(2)首先确定摇杆滑块机构中,滑块能运动到的最低点位置,该位置为上冲头所能下降到的极限位置,该位置位于滑块处于的的垂直导路上,然后再根据上冲头行程为100mm推出滑块的另一极限位置,该位置为上冲头所能达到的最高位置,由此时滑块所在的极限位置可推算出摇杆的一个极限位置C3,要干的另一极限位置C1位于铅锤位置左偏2°处。