280kt/a氨醇系统开车及运行总结
化工装置开车一次性成功个人总结(康小强)

化工装置开车一次性成功个人总结(康小强)全力以赴检修凝心聚力开车——开车一次性成功个人总结自8月10日停车以来迎来了首次大检修工作,经过一个多月的时间,在车间主任刘凯的加强催促和每位造气人的共同努力下,圆满完成了本次大检修,于9月17日各装置陆续开车并取得了一次性成功。
此刻,车间的每一位员工无不为此感到欣喜而自豪。
在此次检修工作中既是对自己的一种能力的考验,更是一次宝贵的锻炼和学习的机会,为了给往后工作提供经验,弥补不足,我认真总结自己的工作,以此来统一思想,提高认识,立足本职岗位,竭尽所能积极主动地完成今后的各项工作。
按照公司开车计划安排, 9月17日造气车间各装置进行水联用建立,拉开开车序幕,在车间领导的精心指挥下,在全体员工共同努力下,到目前以运行接近一周,实现本次开车一次成功和安全零事故目标。
通过这次开车,使员工,对装置的认识理解有了质的飞跃,实践操作能力了有效的提高,对操作中如何准确的判断存在的问题,及时的处理,积累了大量的操作经验。
但是装置开车还存在着不少的差距,也暴露了许多的不足之处。
针对此次开工,结合实际,进行总结,对进一步积累经验,优化操作,力争实现效益最大化。
现将这次开车的个人工作总结如下:优点总结:1、在开车确认阶段能够按点快速的对各调节阀,各管线阀门核对,不遗漏任何一处,坚决以企业的十字坐标为中心,尽心尽责,为开车一次性成功奠定了基础。
2、通过大检修阶段的培训学习,岗位操作能力逐步提高,能够及时做到事故处理,如焦油污水槽的液位控制,膨胀气压力控制等。
3、在开车过程中始终牢记安全,加强了巡检质量,及时发现隐患并整改,避免了事故,确保了安全事故零目标。
不足之处:1、中控现场之间的沟通工作不及时,有时电话由于电量等等问题无法做到及时沟通。
在操作中调节阀调节幅度较大。
没有综合的考虑各个参数之间的相互影响。
如对含尘煤气水换热器温度的控制中,只顾追求C02温度控制,忽略第一缓冲槽等后续温度控制,对极好的收油造成了影响,缺少系统性、综合性的意识。
合成氨精制新技术醇烃化工艺开车技术总结

合成氨精制新技术醇烃化工艺开车技术总结我公司投资建设的由湖南安淳高新技术有限公司设计的120Kt总氨/年醇烃化工艺于2009年12月投入运行,并一次开车成功,取代了物耗高、能耗高有污染的铜洗工艺,装置采用DCS系统控制,现运行正常稳定,经济及环境效益明显,下面将工艺情况介绍如下:1 工艺流程来自氢氮气压缩机五段出口13.5Mpa的净化气进入甲醇油水分离器,除去油污及压缩冷凝水后,少部分气体从大盖顶上引进气体混合分布器Ⅰ和零米冷激分布器;约占入塔总气量30%的气体进入甲醇塔的下部,内外筒环隙,由下而上进入冷束管,冷束管出来的气体进入混合分布器Ⅱ,与出上绝热层的高温气体混合进入第二绝热层反应。
约占总入塔气量70%的气体进塔前预热器,被塔前预热器加热的气体,从甲醇塔的底部进入塔内,进塔气体进入塔内换热器管内,与出塔气体换热后,经中心管进入触媒表面,依次通过上绝热层、第二绝热层、下部绝热层,从下部换热器外壳进入换热器管间,由上折流而下,与入塔气体换热后出塔,进入塔前预热器管内换热,换热后的气体进入水冷器,出水冷器气体进醇分,将生成的甲醇分离下来,送精馏工段精制。
来自醇分离器后的气体从烃化塔的下部进烃化塔的内外筒环隙,自下而上出塔,进入塔前预热器,被加热的气体二次进塔,从塔的下部进入塔内换热器管间,与出塔气体换热后经中心管进入触媒层表面反应,出上绝热层的气体,进入气体混合分布器,与极小一部分从大盖外引进混合分布器的冷气体(升温还原时用以控制下绝热层的触媒温度,正常生产不用冷激气),混合进入下绝热层,出下绝热层的气体进入塔下部换热器管内,与二次进塔气体换热以后出塔,出塔气体进入烃分离器,分离掉烃后气体进入水冷器冷却,然后进氨冷器进一步冷却,再经水分离器分离后去压缩机六进。
2 主要设备2.1甲醇塔Φ1200mm,是由一个直形异径冷管束,两个气体混合分布器,一个集气罩,把触媒层分成三轴一径,二个绝热段,一个内冷段,一个径向段组成,内装填甲醇催化剂,下部有一列管式换热器。
DNl 800 mm氨合成系统运行总结

DNl 800 mm氨合成系统运行总结0 前言江苏恒盛化肥有限公司氮肥厂目前的生产规模为年产合成氨220 kt/a、甲醇60 kt/a、尿素350kt/a。
为了扩大企业规模,达到合成氨300 kt/a、尿素400kt/a的生产能力.公司新增了1套合成氨生产能力为180 kt/a的DNl 800 mm氨合成系统。
该系统由湖南安淳高新技术有限公司设计,采用安淳高新技术公司设计生产的ⅢJD-2000型DNl 800 mm氨合成塔内件,共装XA-201型催化剂66.6 t,生产运行情况良好。
1 合成系统工艺流程及设备配置1.1 工艺流程合成系统工艺流程见图1。
由循环机油分来的气体分成2股:1股冷气(约10%)由合成塔底部环隙进入,沿内外筒环隙往上,从塔顶引出,与循环加热器加热后部分气体(占总气体的20%~25%)汇合,直接进入段间冷却器。
另一股冷气进入塔外循环加热器管间,加热到175~185℃,一部分气体(约60%~65%)进入合成塔下部换热器管内,气体加热到360~410 ℃,经中心管进入上绝热层反应,气体温度达到460~470℃,与段间冷却器出来的气体在气体混合器中混合,温度降到400~430℃进入分气筒,经过径向绝热段,再经过径向段间冷却器,径向流过塔中部径向筐。
从中部径向筐出来的气体,沿径向筐与内筒的环隙向下,从圆周方向斜向通过下绝热层从换热器外壳进入管间,温度降至310~340℃折流出塔。
出塔气进入废热回收器副产蒸汽,再依次进入热交换器管内、2个串联水冷器、冷交的管间及氨分,与管内的冷气体换热并在下部分离氨后进入卧式氨冷器管内,出氨冷器的气体与压缩来的、经补气氨冷和油分后的新鲜气混合,进入氨分进一步分离液氨后进冷交管内与水冷来管外热气换热,温度提高到25 ℃以上进入循环机加压后进入油分,依次循环,完成氨的合成与分离。
1.2 ⅢJD-2000型DNl 800mm合成塔内件ⅢJD-2000型DNl800合成塔内件是由催化剂筐、独立的瘦长型换热器、直型异径冷管束、气体混合分布器和集气罩组成的一轴三径内件,其特点有3个绝热段、1个内冷段,采用分流工艺,床层上下直通,内件底部设有2个自卸孔,催化剂可以自卸。
环己醇装置开车个人总结
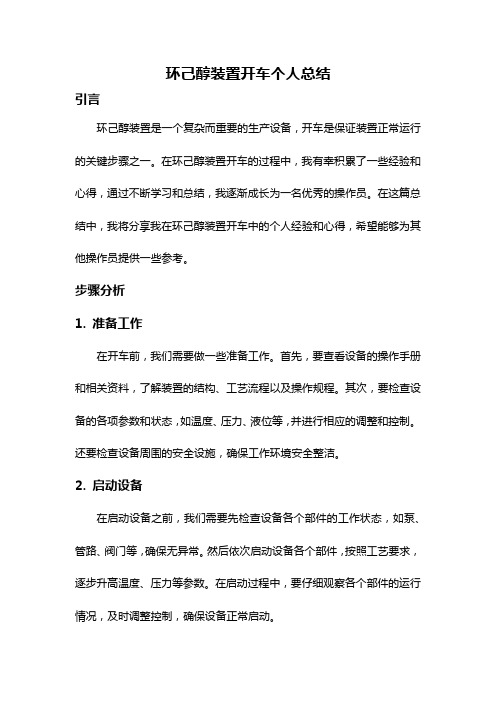
环己醇装置开车个人总结引言环己醇装置是一个复杂而重要的生产设备,开车是保证装置正常运行的关键步骤之一。
在环己醇装置开车的过程中,我有幸积累了一些经验和心得,通过不断学习和总结,我逐渐成长为一名优秀的操作员。
在这篇总结中,我将分享我在环己醇装置开车中的个人经验和心得,希望能够为其他操作员提供一些参考。
步骤分析1. 准备工作在开车前,我们需要做一些准备工作。
首先,要查看设备的操作手册和相关资料,了解装置的结构、工艺流程以及操作规程。
其次,要检查设备的各项参数和状态,如温度、压力、液位等,并进行相应的调整和控制。
还要检查设备周围的安全设施,确保工作环境安全整洁。
2. 启动设备在启动设备之前,我们需要先检查设备各个部件的工作状态,如泵、管路、阀门等,确保无异常。
然后依次启动设备各个部件,按照工艺要求,逐步升高温度、压力等参数。
在启动过程中,要仔细观察各个部件的运行情况,及时调整控制,确保设备正常启动。
3. 运行监控设备启动后,我们需要进行运行监控,及时掌握设备的工作状态。
要注意监测各个关键参数的变化,如温度、压力、液位等,并及时调整控制,以保持设备的安全稳定运行。
同时要密切关注设备周围的动静,确保无异常情况发生。
4. 故障处理在设备运行过程中,难免会遇到各种故障和异常情况。
在处理故障时,我们首先要做到冷静应对,不慌不乱。
其次要快速定位故障原因,采取相应措施进行排除。
如果无法解决,要及时向相关人员报告,并进行紧急停车处理,确保设备和人员的安全。
5. 记录总结在设备运行结束后,我们要对整个开车过程进行记录和总结。
要详细记录设备的运行参数和工艺变化,以备后续分析和参考。
同时要总结经验和教训,记录故障处理的方法和效果,以供类似情况下的参考。
心得体会通过长时间的开车经验积累和总结,我逐渐领悟到一些重要的道理。
第一,要坚持严谨的工作作风,一丝不苟地按照规程操作。
在开车过程中,稍有差池就可能引发事故,造成巨大的经济和人员损失。
我公司醇烃化装置运行总结

我公司醇烃化装置运行总结胡志忠;吴林平【摘要】介绍合成氨精制由铜洗改为醇烃化的工艺流程,投运后出现的问题及处理情况.还总结了操作控制要点.【期刊名称】《化工设计通讯》【年(卷),期】2011(037)006【总页数】4页(P33-35,70)【关键词】醇烃化;铜洗;运行情况;操作要点【作者】胡志忠;吴林平【作者单位】江西双强化工有限公司,江西新余338000;江西双强化工有限公司,江西新余338000【正文语种】中文【中图分类】TQ113.26+4.3我公司合成总氨设计生产能力180kt/a。
主要是以湖南粉煤搭配腐殖酸钠加工成煤棒,经烘干后送造气炉燃烧,制取半水煤气,煤气经半脱、全低温变换、变脱、MDEA脱碳、净化精制,最后合成得到液氨。
我公司合成氨原料气净化精制以前采用传统的铜洗法。
铜洗是一种比较早的净化精制方法,缺点比较明显。
主要表现在工艺控制指标多,操作不稳定;化工原料使用种类多,生产运行费用高;现场环境差,污染严重;设备检修频繁,检修费用高等。
基于以上种种原因,为了降低生产成本,达到长周期稳定运行的目的,公司经多方考察,结合当前实际情况,最后决定采用湖南安淳高新技术有限公司推出的醇烃化工艺,于2007年12月开始施工、安装,2008年5月完成,同年6月投入运行。
现在对我公司醇烃化精制工艺使用情况作简单介绍。
1 工艺流程1.1 醇化工艺流程压缩送来的12.5MPa脱碳后原料气,经油分分离油污后,一部分气体进入醇化塔环隙,与冷管段反应热气换热,再经上升管升至混合分布器Ⅱ;另一部分进醇化预热器预热后,由底部进醇化塔换热器管内,与管间出塔气体换热,温度升至200~220℃,进入催化床层反应。
出第一段的气体进入混合分布器,与由冷管来的冷气混合,降温后进入第二段反应,反应后的气体进入混合分布器Ⅰ,与从大盖引入的少量冷气混合,进入第三段(冷管段)继续进行醇化反应。
反应后的气体经径向集气罩汇合,沿内件管壁与径向筐筒体之间的环隙,从圆周方向流向径向筐中部的换热器外壳,进入换热器管间,由上折流而下与管内从塔外热交来的气体换热,温度降低后出塔至塔外热交管内,与塔外油分来的冷气继续换热,自身温度降至80℃以下,去水冷器,进一步降温,再进入醇分离器,甲醇被分离下来,送入粗醇槽。
合成氨装置开车操作优化小结

从保护设备角度考虑认为对流二段的保护蒸汽一 定不能少,而对于脱碳系统再沸器超压的问题, 可采取减少进入脱碳系统的气量、关闭再沸器连 通阀等措施予以控制,重点是一定要保护好对流 二段的盘管。
开车过程中,对流四段烟气经常超温,当对 流四段盘管在烟气温度达到 400℃时,我们采取 了通部分天然气对盘管进行保护的措施;当后序 工段需要解决问题、开车时间延后时,则对这部 分保护气体进行回收。但经实践及论证,回收的 这部分气体因温度较高,易造成仪表元件损坏, 需要进一步地改造,综合各方面的因素考虑,最 终我们对对流四段盘管保护气体没有进行进一步 地回收利用。
· 27 ·
复工开 车 过 程 中, 合 成 冷 冻 系 统 运 行 正 常 后,尿素装置才能开车;短停或者合成冷冻系统 有问题时,尿素装置可以先开车,辅锅烟气温度 在任何时候都保证不超过 900℃;同时,复工开 车过程中,要合理调节蒸汽系统,交叉作业,以 保护设备为前提。 13 一段炉、二段炉温度的控制
图 1 转化及低变系统升温流程简图 16 配原料气烧嘴的优化操作
在一段炉温度达到 650~680℃时,开始进 行配原料气的工作,现场人员要将一段炉内 72 个烧嘴全部点燃,但每个烧嘴阀门不能全开,这 是由于此时一段炉的负荷低,每一根转化管的进
气不均匀,如此可防止炉管局部过热现象的发 生;调整每个烧嘴风门的开度和 4个大风门的挡 板开度,控制一段炉整体温差在 20℃以下。
第 6期 2018年 11月
中 氮 肥 MSizedNitrogenousFertilizerProgress
No6 Nov.2018
合成氨装置开车操作优化小结
280kt/a合成氨低温甲醇洗装置应用总结

变换系统来原料 气 原料气/ 闪蒸气换热器
1 工 艺 流 程 及 主 要 设 备
原 料气 工艺 流 程 如 图 1所示 , 低 温 甲 醇 洗 装 置 主要设 备 及参 数如 表 1所示 。 来 自变 换 工 段 温 度 约 4 0℃ 、 压力 3 . 1 MP a
Su n S h u a n g ho n g
( S h a n x i Y a n g m e i F e n g x i F e r t i l i z e r I n d u s t r y[ G r o u p ]C o . ,L t d . S h a n x i Y u n c h e n g 0 4 4 0 0 0 )
Abs t r ac t Th e t e c hn o l o g i c a l pr o c e s s ,e qu i p me n t c o n di t i o n a nd t e c h n i c a l f e a t u r e s o f a mmo n i a s y n t h e s i s l o w— t e mp e r a t u r e me t h a n o l wa s h p l a n t a r e i n t r o d u c e d,pr o b l e ms i n s t a r t — u p a n d t r e a t me n t me a s u r e s a r e s u mme d u p. Th e o pe r a t i o n f le x i b i l i t y o f t h e l o w— t e mp e r a t u r e me t h a n o l wa s h p l a n t i s
180kt/a氨合成系统设计安装及开车运行总结

对该 内件技术不完善的地方加以改进后重新设计 的产品 ,该新建合成系统开车至今 ,各项指标均 达到设计要求 。
1 1 采 用 ⅢJD新型 合成塔 内件 . —
15 白控 方案 .
15 1 主控室控制系统 .. 选用浙大 中控 的 J - 0 C X 3 X D S集散控制 系 0 统 。用户 界 面友好 ,所有 的命 令都 简化 为形 象直 观的功能图标 ,只需用 鼠标单击即可完成操作 , 使生产过程实时监控操作方便简洁 。 15 2 现场测量仪表 .. 集控压力采用 F G 5 4L F Y B K W0 V 一H B —B智能
14 优 化补 气与 循环机 位 置 .
采用安淳公司的技术 ,于 2 0 年 1 月一次开车 02 0 成功。(1 0 m合成 塔 内件是安淳公 司根据 2 0m )8
(1 0 m合成塔内件在各厂的实际使用情况 , 2 0m )4
补气位置在氨冷后 ,减少 了氨冷负荷 ,节约 了冷冻量 ;循环机位置放 在塔前 ,节 约 了冷冻
13 采 用管 壳式水冷 .
(1 0 r 2 0r n氨合成 系统 由湖南安淳高新技 )8 n 术有限公司设计 ,合成塔内件采用该公 司的ⅢJ . D型内件 。我公 司原 (1 0 m合成系统 也是 2 0m )4
采用管壳式水冷替代传统 的淋洒式水冷,减
少了占地面积,优化了设备布局 ,净化了环境。
维普资讯
第 4期
中 氮
肥
No. 4
20 0 7年 7月
M - ie to e o sFet i rP o rs Szd Ni g n u riz r g es r le
J1 07 u .2 0
10k/ 氨合成 系统设计安装及开车运行 总结 8 ta
- 1、下载文档前请自行甄别文档内容的完整性,平台不提供额外的编辑、内容补充、找答案等附加服务。
- 2、"仅部分预览"的文档,不可在线预览部分如存在完整性等问题,可反馈申请退款(可完整预览的文档不适用该条件!)。
- 3、如文档侵犯您的权益,请联系客服反馈,我们会尽快为您处理(人工客服工作时间:9:00-18:30)。
气体换热降温 , 出烃化塔气体中 ( O+ O ) C C : 降
至1 5×1 以下 。烃 后 气 经 预热 器 ( 内 ) 热 0 管 换 降温 到 一 0℃ 、 6 进入烃 化 分离器 分 离液 态醇 烃等
各项消耗水平低 。20k a 8 t 醇氨系统采用湖南安 / 淳公 司的醇烃化气体精制工艺和 ⅢJ D氨合成工 艺技 术 。
1 醇 烃 化 工 艺 流 程
醇烃化工艺流程见 图 1 。压缩机送来 2. a 20MP
物质后 , 再进入水冷器 、 氨冷器 降温 至 5~ 8℃ , 然 后进 入 烃化 水 分 离 器 分 离 水 和少 量 醇 烃 等 物 质后 , 作为合成氨 生产 的合格原 料气 再进入 氨
合成 系 统 。
( 间 ) 热 后 , 烃 化 塔 下 部 进 入 下 部 换 热 器 管 加 从
( 间 ) 温至 2 0— 2 管 提 1 2 0℃ 进入 烃 化催 化 剂 层进
行技术改造 , 调整甲醇分厂的产 品结构, 使其能够 同时生产 甲醇和尿素 , 提升企业抵御市场风险的 能力 。改造后 , 甲醇分厂总氨年产能 30k( 4 t其中
的原料气 经醇 化 补 气 氨 冷 器 降 温 到 ~5℃ , 醇 与 化循环气混合后进入醇化油分离器分离油水 , 先 通 过醇化 预热 器 ( 间 ) 温 至 10—10o 醇 管 提 5 6 C进 化 塔 , 塔 内换 热器 加热 至 20~ 2 经 1 20℃进入催 化
剂层反应。醇化反应后气体温度升至 25℃左 2 右, 经醇 化塔 内换 热器 出醇化塔 , 进醇化 预热 器 再 ( 管内) 与压缩 系统送来的粗原料气换 热降温后 进人醇化水冷器 , 进一步降温至 一 0℃后进醇分 4 离器分离 甲醇 , 醇化反应后气体 中 ( O+ O ) C C: 降至 00 % 一 .0 .3 0 3 %。醇后气再经烃化预热 器
液 氨 20k、 4 t甲醇 10k)尿 素年产 能 40k。改 0 t 、 0 t
造后的装置于 2 1 年 7 1 一次性投料开车 00 月 0日
成功 , 经过 6个 多月 的生产运 行 , 各项工 艺指 标 和 产 量 均达 到或优 于工 艺设计 指标 , 运行 稳定 , 氨 吨
行反应 , 出催化床 后经 下部 换 热 器 ( 内 ) 醇后 管 与
1 6
氮肥
第4 卷 o
第2 期 2 1 年 2月 02
2 0k/ 8 ta氨 醇 系统 开 车及 运 行 总 结
王 斌 李 强 ( 山西 阳煤 丰喜肥 业 <集 团 >有 限责任公 司临猗分公 司 0 4 0 ) 4 1 0
0 前言
山西 阳煤 丰 喜 肥 业 ( 团 ) 限 责 任公 司 临 集 有 猗分 公 司 甲醇 分 厂 ( 以下 简 称 甲醇 分 厂 ) 原有 甲 醇 年产 能 2 0k。2 0 0 t 08年底 至 20 09年初 , 国际 受 金 融危机 影 响 , 国内 甲醇 市场低 迷 , 多 甲醇生 产 许 企 业相继 减 产 或停 产 。 为此 , 定 对 甲醇 装 置 进 决
1 醇化补充氨冷器 2 醇化补气油分离器 3 醇化塔 4 醇化预热器 5 醇化水冷器 6 醇分离器 . . . . . . 8 烃化塔 . 9 烃化预热器 . l. O 烃化物分离器 l. 1烃化水冷器 1. 2 烃化氨冷器
7 烃化 油分离器 . 1. 4 循环机
1. 3 烃化水分离器
图 1 醇烃化工艺流程
淋洒式 , 8 0m , F= 0 1台
D 0 42 6m 1台 NI10mm x1 1 m, D 0 410m 1台 N120mm x1 0 m, D 0 1 0 m, N1 0mmx1 0m 1台 4 2
换 器管 间 , 管 内冷 气 冷 至 3 0~ 4 ℃ , 合 成 被 2 30 从 塔 下部 出来 进 入废 热锅 炉 ( 产 25MP 蒸 汽 ) 副 . a , 换 热后 降温 至 20~20℃ , 热交换 器 和循 环水 0 1 经
器出来氨含量 25 体积分数) .%( 左右的未反应气
2 氨合成 系统工艺流程
氨合成系统工艺流程见 图 2 。从合成油分离
体 被分 成 2股 : 股 7 % ~8 % ( 积 分 数 , 一 5 0 体 下 同) 经塔 外热 交换 器 加热 至 15—10℃ , 入塔 7 9 进
小氮肥
一
表 1 醇烃化装置主要设备参数
设备名称
醇 化 塔
主要参数
DN2 0 0 mm 1 5 2 mm , 0 x2 9
股 2% 混 进
烃化塔
醇 化 预 热 器 醇 化 水 冷 器 烃 化 预 热 器 烃 化 水 冷 器 醇 化 补 充 氨 冷 器 烃 化 氨 冷 器 醇 分 离 器
气 体径 向进 入 内冷 段 反 应 , 后 再 径 向进 入 第 2 然 和第 3层径 向筐 与 内件 内壁 环 隙 , 由上 而 下 流 入
第 4段径 向绝 热 层进 行 反应 , 进 入 塔 内下 热 交 再
淋洒式 , 6 1台 F=1 0m , 0
D 0 N120mm×1 1 m, 94 0m 1台
第4 0卷
第 2期
21 0 2年 2月
1 7
内下 热 交 换 器 的 管 内 由 下 而 上 上 升 , 加 热 至 被
20— 8 再 经塔 内上 热交 换 器加 热至 3 0o 7 2 0o C, 7 C, 经 过 中心管 到 达催 化 床 零 米 , 由冷 管 出来 的 另 与
催化剂量 3 . , 5 0m 1台
DN1 8 0 mm ×2 2 0 1 4 5 mm ,
第 1段 轴 向绝热 反 应 , 经塔 内上 热 交 换 器 管 间 再
催化剂量 3 . , 13m 1台
D 0 ×1 3 m, N120mm 94 0m 1台
换热冷却后进入第 2 段径 向绝热反应 , 反应后 的