Directed and Elliptic Flow in 158 GeVNucleon Pb + Pb Collisions
环介导等温扩增联合横向流动试纸条可视化检测哈维氏弧菌的研究

环介导等温扩增联合横向流动试纸条可视化检测哈维氏弧菌的研究程蝶;柴方超;蔡怡;周前进;陈炯【摘要】Based on nucleotide enrichment by a loop-mediated isothermal amplification(LAMP)and chromatographic visualization by a lateral flow dipstick(LFD)assay,this work aims to develop a novel LAMP-LFD method for the rapid detection of Vibrio harveyi. Three pairs of primers were designed using the hemolysin gene(vhhA)of V. harveyi as detection target,and used in LAMP reaction,among which the forward inner primer vhhA-FIP was biotinylated. Similarly,a fluorescein isothiocyanate(FITC)-labeled probe vhhA-HP was designed to specifically hybridize with LAMP products. And then the hybridized LAMP products were visually detected by LFD. The optimized LAMP was performed at 63℃ for 40 min;and visual detection via LFD took 50 min. The results indicated that LAMP-LFD was able to specifically identify V. harveyi from other 9 pathogenic bacteria commonly existing in the aquatic animals,such as V. vulnificus. The detection limit of LAMP-LFD was 1.0×102 CFU/mL for V. harveyi pu re cultures(equivalent to 2 CFU per reaction),and 5×102 CFU/mL for V. harveyi contaminated tissues of large yellow croaker(equivalent to 20 CFU per reaction),both of which were 100 times lower than that of the conventional PCR method using both outer primers vhhA-F3/vhhA-B3. Therefore,this rapid and accurate LAMP-LFD method is a promising alternative in the surveillance and point-of-care test of V. harveyiin seafarming.%以哈维氏弧菌(Vibrio harveyi)为材料,利用环介导等温扩增技术(LAMP)进行核酸扩增,借助横向流动试纸条(LFD)完成产物检测,旨在建立一种可用于哈维氏弧菌快速检测的LAMP-LFD新技术。
Q Sepharose Fast Flow 产品说明书
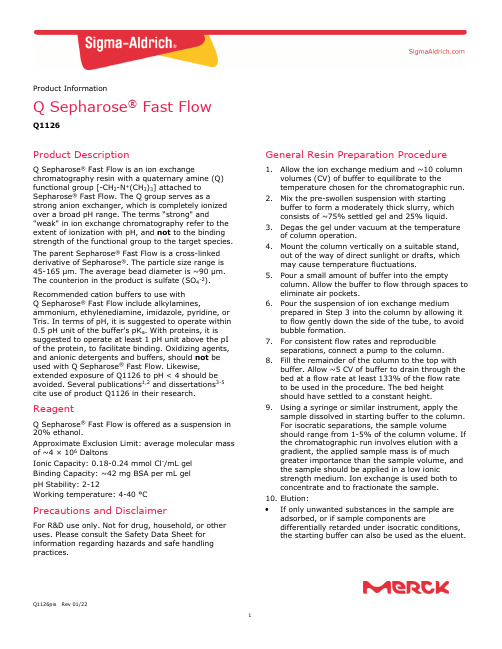
Q1126pis Rev 01/221Product InformationQ Sepharose ® Fast FlowQ1126Product DescriptionQ Sepharose ® Fast Flow is an ion exchangechromatography resin with a quaternary amine (Q) functional group [-CH 2-N +(CH 3)3] attached to Sepharose ® Fast Flow. The Q group serves as astrong anion exchanger, which is completely ionized over a broad pH range. The terms “s trong" and"weak" in ion exchange chromatography refer to the extent of ionization with pH, and not to the binding strength of the functional group to the target species. The parent Sepharose ® Fast Flow is a cross-linked derivative of Sepharose ®. The particle size range is 45-165 µm. The average bead diameter is ~90 µm. The counterion in the product is sulfate (SO 4-2). Recommended cation buffers to use with Q Sepharose ® Fast Flow include alkylamines,ammonium, ethylenediamine, imidazole, pyridine, or Tris. In terms of pH, it is suggested to operate within 0.5 pH unit of the buffer's pK a . With proteins, it is suggested to operate at least 1 pH unit above the pI of the protein, to facilitate binding. Oxidizing agents, and anionic detergents and buffers, should not be used with Q Sepharose ® Fast Flow. Likewise,extended exposure of Q1126 to pH < 4 should be avoided. Several publications 1,2 and dissertations 3-5 cite use of product Q1126 in their research.ReagentQ Sepharose ® Fast Flow is offered as a suspension in 20% ethanol.Approximate Exclusion Limit: average molecular mass of ~4 × 106 DaltonsIonic Capacity: 0.18-0.24 mmol Cl -/mL gel Binding Capacity: ~42 mg BSA per mL gel pH Stability: 2-12Working temperature: 4-40 °CPrecautions and DisclaimerFor R&D use only. Not for drug, household, or other uses. Please consult the Safety Data Sheet for information regarding hazards and safe handling practices. General Resin Preparation Procedure1. Allow the ion exchange medium and ~10 columnvolumes (CV) of buffer to equilibrate to thetemperature chosen for the chromatographic run. 2. Mix the pre-swollen suspension with startingbuffer to form a moderately thick slurry, which consists of ~75% settled gel and 25% liquid. 3. Degas the gel under vacuum at the temperatureof column operation.4. Mount the column vertically on a suitable stand,out of the way of direct sunlight or drafts, which may cause temperature fluctuations.5. Pour a small amount of buffer into the emptycolumn. Allow the buffer to flow through spaces to eliminate air pockets.6. Pour the suspension of ion exchange mediumprepared in Step 3 into the column by allowing it to flow gently down the side of the tube, to avoid bubble formation.7. For consistent flow rates and reproducibleseparations, connect a pump to the column. 8. Fill the remainder of the column to the top withbuffer. Allow ~5 CV of buffer to drain through the bed at a flow rate at least 133% of the flow rate to be used in the procedure. The bed height should have settled to a constant height.9. Using a syringe or similar instrument, apply thesample dissolved in starting buffer to the column. For isocratic separations, the sample volumeshould range from 1-5% of the column volume. If the chromatographic run involves elution with a gradient, the applied sample mass is of much greater importance than the sample volume, and the sample should be applied in a low ionicstrength medium. Ion exchange is used both to concentrate and to fractionate the sample. 10. Elution:• If only unwanted substances in the sample areadsorbed, or if sample components aredifferentially retarded under isocratic conditions, the starting buffer can also be used as the eluent.The life science business of Merck operates as MilliporeSigma in the U.S. and Canada.Merck and Sigma-Aldrich are trademarks of Merck KGaA, Darmstadt, Germany or its affiliates. All other trademarks are the property of their respective owners. Detailed information on trademarks is available via publicly accessible resources.© 2022 Merck KGaA, Darmstadt, Germany and/or its affiliates. All Rights Reserved. Q1126pis Rev 01/22 JJJ,MAM,GCY2•Normally, however, separation and elution are achieved by selectively decreasing the affinity of the molecules for the charged groups on the resin by changing the pH and/or ionic strength of the eluent. This procedure is termed gradient elution. 11. Regeneration: •Either (a) washing the column with a high ionic strength salt solution, such as 1 M NaCl, or (b) changing the pH to the tolerable low and high pH extremes, is usually sufficient to remove reversibly bound material.• When needed, lipids and precipitated proteins canbe removed by washing with 1 CV of 1-2 M NaCl, followed by 1 CV of 0.1 M NaOH in 0.5 M NaCl. • Rinse with several CV of water. Thenre-equilibrate the resin with starting buffer.• If base such as NaOH was used, adjust the pH ofthe resin to neutral before storing or using.12. Storage: Q Sepharose ® Fast Flow may be storedat 2-8 °C in water with 20% ethanol added as an antibacterial agent.General NotesCation versus Anion Exchanger• If sample components are most stable below their pI values, a cation exchanger should be used. • If sample components are most stable above their pI values, an anion exchanger should be used. •If stability is good over a wide pH range on both sides of the pI, either or both types of ion exchanger may be used.Strong versus Weak Ion Exchanger•Most proteins have pI values within the range 5.5-7.5, and can thus be separated on both strong and weak ion exchangers.•When maximum resolution occurs at an extreme pH and the molecules of interest are stable at that pH, a strong ion exchanger should be used. Choice of Buffer, pH, and Ionic Strength• The highest ionic strength which permits binding should normally be used.•The required buffer concentration varies fromsubstance to substance. Usually, an ionic strength of at least 10 mM is required to ensure adequate buffering capacity.•As salts (such as buffers) help to stabilize proteins in solution, their concentration should be highenough to prevent denaturation and precipitation.References1. López, G. et al ., Eukaryot. Cell , 14(6), 564-577(2015).2. Bhargava, V. et al ., Dev. Cell., 52(1), 38-52.e10(2020).3. Fu , Yinan, “Structure and dynamics ofPseudomonas aeruginosa ICP”. University ofGlasgow, Ph.D. dissertation, p. 126 (April 2009). 4. Redmond, Miranda , “The Role of N-TerminalAcidic Inserts on the Dynamics of the Tau Protein ”. University of Vermont, Ph.D. dissertation, p. 22 (May 2017).5. Taylor-Whiteley, Teresa Rachel , “RecapitulatingParkinson’s disease pathology in athree-dimensional neural cell culture mode ”. Sheffield Hallam University, Ph.D. dissertation, p. 58 (September 2019).NoticeWe provide information and advice to our customers on application technologies and regulatory matters to the best of our knowledge and ability, but without obligation or liability. Existing laws and regulations are to be observed in all cases by our customers. This also applies in respect to any rights of third parties. Our information and advice do not relieve ourcustomers of their own responsibility for checking the suitability of our products for the envisaged purpose. The information in this document is subject to change without notice and should not be construed as acommitment by the manufacturing or selling entity, or an affiliate. We assume no responsibility for any errors that may appear in this document.Technical AssistanceVisit the tech service page at /techservice .Standard WarrantyThe applicable warranty for the products listed in this publication may be found at /terms .Contact InformationFor the location of the office nearest you, go to /offices .。
汽轮机高压级叶顶间隙泄漏流的掺混作用分析

2017年第36卷第8期 CHEMICAL INDUSTRY AND ENGINEERING PROGRESS·2859·化 工 进展汽轮机高压级叶顶间隙泄漏流的掺混作用分析曹丽华,王佳欣,李盼,李勇(东北电力大学能源与动力工程学院,吉林 吉林 132012)摘要:对某带有高低齿汽封的汽轮机高压1.5级模型进行数值计算,分析了不同叶顶间隙下汽封出口腔内泄漏流的涡系变化以及泄漏流与主流掺混对下游静叶气动性能的影响,并定量计算了泄漏流引起的相关损失。
结果表明:泄漏流与主流在周向速度和径向速度上存在较大差异,二者掺混将导致动叶出口处汽流方向发生偏转,对下游静叶产生负攻角,引起级效率的下降。
在泄漏流引起的相关损失中,掺混损失占主要部分。
叶顶间隙的大小直接影响汽封腔内回流涡的尺寸,回流涡与汽封腔内泄漏流动能的耗散程度密切相关。
因此,在叶顶汽封设计中,应尽量减小叶顶间隙,增强密封腔内汽流扰动,减小泄漏流与主流的速度差异,以便提高汽轮机经济性。
关键词:汽轮机;叶顶泄漏流;高低齿汽封;叶顶间隙;掺混中图分类号:TK263 文献标志码:A 文章编号:1000–6613(2017)08–2859–07 DOI :10.16085/j.issn.1000-6613.2016-2377Analysis on mixing process of tip shroud leakage flow in high-pressurestage of steam turbineCAO Lihua ,WANG Jiaxin ,LI Pan ,LI Yong(School of Energy and Power Engineering ,Northeast Electric Power University ,Jilin 132012,Jilin ,China )Abstract :A numerical calculation was attempted based on a high-pressure 1.5-stage steam turbine with rotor labyrinth seal. The variation of leakage vortex system in shroud exit cavity and the effect of main flow mixing with leakage flow on the aerodynamic characteristics of downstream stator were analyzed. Besides ,the related losses generated by leakage flow were calculated. Results showed that there were large differences between main flow and leakage flow in the circumferential velocity and radial velocity. Main flow was deflected at the rotor blade exit when it mixed with the leakage flow ,which led to the negative angles of incidence on the subsequent stator and the decrease of the stage efficiency. The mixing loss was the main part among the related losses generated by leakage flow. The tip clearance directly affected the size of backflow vortex which was closely related to the kinetic energy dissipation of leakage flow. Therefore ,during the structure design process of the blade tip seal ,it is necessary to reduce the tip clearance ,enhance the disturbance of leakage flow in seal cavity ,and decrease the velocity difference between leakage flow and main flow to improve the economy of steam turbine.Key words :steam turbine ;tip leakage flow ;labyrinth seal ;tip clearance ;mixing动叶顶部和汽缸壁之间存在叶顶间隙,由于动叶前后存在压差,不可避免的出现泄漏流动。
首次观察到量子条件下的化学反应

首次观察到量子条件下的化学反应
佚名
【期刊名称】《分析测试学报》
【年(卷),期】2012(31)11
【摘要】在量子条件下观察到化学反应的进行,这是科学家们在半个世纪前就开始寻求得到的“真相”。
以色列魏茨曼科学研究所的团队现在利用两束低温超声束的“合并”,以实验第一次证明,在超低温条件下化学反应的速率可以发生戏剧性变化;其也为反应动力学学科提供一个超灵敏的探测器;
【总页数】1页(P1415-1415)
【关键词】化学反应;量子条件;超低温条件;科学研究所;力学学科;科学家;超声束;以色列
【正文语种】中文
【中图分类】O643.1
【相关文献】
1.首次观察到光合作用中能量转化的量子机制 [J], 科技日报
2.科学家首次观察到化学反应过渡态的形成 [J], ;
3.芝加哥大学首次观察到几何缩放量子态 [J], 董丽
4.量子显微镜首次观察到纳米光晶体内光的动态 [J],
5.科学家观察到量子条件下的化学反应 [J],
因版权原因,仅展示原文概要,查看原文内容请购买。
中能区椭圆流和转变能的系统质量依赖外文翻译

毕业设计(论文)外文资料翻译系:核能与可再生能源专业:核工程与核技术 091姓名:林森学号: 0902500124外文出处: PHYSICAL REVIEW C 74(用外文写)014602(2006)附件: 1.外文资料翻译译文;2.外文原文。
指导教师评语:签名:附件1:外文资料翻译译文中能区椭圆流和转变能的系统质量依赖张英逊李祝霞1中国原子能科学研究院能源、邮政信箱275(18)、北京102413,中华人民共和国2中心理论核物理、国家实验室的兰州重离子加速器,兰州730000,中华人民共和国3理论物理研究所,中国学术的科学,北京100080,中华人民共和国(收录于2005年12月12日,2006年7月7日出版)椭圆流Z ≤2粒子在重离子碰撞的能量从数十到数百兆电子伏特每核子研究通过传输模型。
一个新版本的改进的量子分子动力学模型(ImQMD05)。
该模型采用了一个完整的 Skyrme 势能密度泛函数。
不同的等效相互作用的影响和介质修正的核子核子横截面的椭圆流进行了研究。
我们的结果表明,软核状态方程和入射能量依赖于介质核子核子横截面用于描述激发态的中能椭圆流函数。
椭圆流跃迁能的大小对中能的依赖关系也进行了探讨。
系统质量依赖跃迁能与系统质量相符合,指数为0.223。
中能重离子碰撞(HICs)研究领域的一个主要目标是提取更准确信息的核状态方程(EoS)。
最近,已经从重离子反应数据中对确定核物质状态方程取得重大进展。
集体流在有效的观测量中扮演了一个突出的角色。
大量的理论和实验工作耗费在了中能重离子碰撞中集体流的研究上面。
椭圆流已被证明是一个推倒状态方程和重离子碰撞力学多产的课题。
最近,激发函数椭圆流参数的能量从费米能级到相对论能量的197Au + 197Au 式中已经通过 FOPI, INDRA, 和 ALADIN 协作的测量,跃迁能从正到负的椭圆流被确认,它大约在 100MeV/u。
平均场和两体碰撞在这个能区中都扮着重要的角色。
NCP1582资料
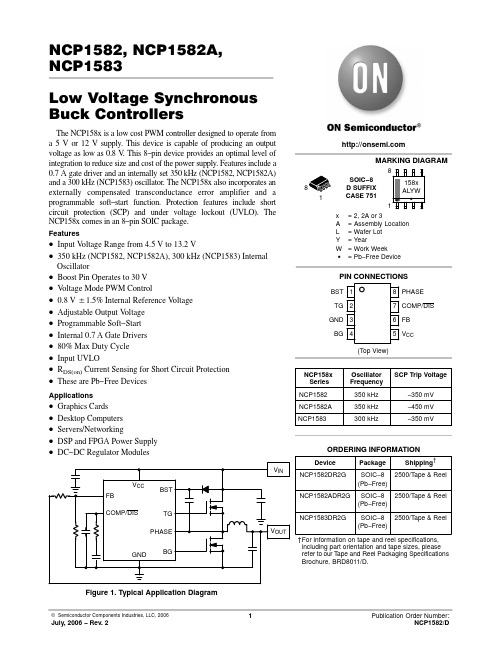
NCP1582, NCP1582A,NCP1583Low Voltage Synchronous Buck ControllersThe NCP158x is a low cost PWM controller designed to operate from a 5 V or 12 V supply. This device is capable of producing an output voltage as low as 0.8 V. This 8−pin device provides an optimal level of integration to reduce size and cost of the power supply. Features include a0.7 A gate driver and an internally set 350 kHz (NCP1582, NCP1582A) and a 300 kHz (NCP1583) oscillator. The NCP158x also incorporates an externally compensated transconductance error amplifier and a programmable soft−start function. Protection features include short circuit protection (SCP) and under voltage lockout (UVLO). The NCP158x comes in an 8−pin SOIC package.Features•Input V oltage Range from 4.5 V to 13.2 V•350 kHz (NCP1582, NCP1582A), 300 kHz (NCP1583) Internal Oscillator•Boost Pin Operates to 30 V•V oltage Mode PWM Control•0.8 V $1.5% Internal Reference V oltage•Adjustable Output V oltage•Programmable Soft−Start•Internal 0.7 A Gate Drivers•80% Max Duty Cycle•Input UVLO•R DS(on) Current Sensing for Short Circuit Protection •These are Pb−Free DevicesApplications•Graphics Cards•Desktop Computers•Servers/Networking•DSP and FPGA Power Supply•DC−DC Regulator ModulesFigure 1. Typical Application DiagramSOIC−8D SUFFIXCASE 7511MARKING DIAGRAMPIN CONNECTIONSx= 2, 2A or 3A= Assembly LocationL= Wafer LotY= YearW= Work WeekG= Pb−Free DeviceBST PHASETGGNDBGCOMP/DISFBV CC(Top View)Device Package Shipping†ORDERING INFORMATIONNCP1582DR2G SOIC−8(Pb−Free)2500/Tape & Reel†For information on tape and reel specifications, including part orientation and tape sizes, please refer to our T ape and Reel Packaging Specifications Brochure, BRD8011/D.NCP1582ADR2G SOIC−8(Pb−Free)2500/Tape & ReelNCP1583DR2G SOIC−8(Pb−Free)2500/Tape & Reel NCP158xSeriesOscillatorFrequencySCP Trip Voltage NCP1582350 kHz−350 mV NCP1582A350 kHz−450 mV NCP1583300 kHz−350 mVFigure 2. Typical VGA Card Application DiagramFigure 3. Detailed Block DiagramV CCTG BST PHASEBG GNDPIN FUNCTION DESCRIPTIONPin No.Symbol Description1BST Supply rail for the floating top gate driver. To form a boost circuit, use an external diode to bring thedesired input voltage to this pin (cathode connected to BST pin). Connect a capacitor (C BST) between this pinand the PHASE pin. Typical values for C BST range from 0.1 m F to 1 m F. Ensure that C BST is placed near the IC.2TG Top gate MOSFET driver pin. Connect this pin to the gate of the top N−Channel MOSFET.3GND IC ground reference. All control circuits are referenced to this pin.4BG Bottom gate MOSFET driver pin. Connect this pin to the gate of the bottom N−Channel MOSFET.5V CC Supply rail for the internal circuitry. Operating supply range is 4.5 V to 15 V. Decouple with a 1 m Fcapacitor to GND. Ensure that this decoupling capacitor is placed near the IC.6FB This pin is the inverting input to the error amplifier. Use this pin in conjunction with the COMP pin tocompensate the voltage−control feedback loop. Connect this pin to the output resistor divider (if used) ordirectly to Vout.7COMP/DIS Compensation Pin. This is the output of the error amplifier (EA) and the non−inverting input of the PWM comparator. Use this pin in conjunction with the FB pin to compensate the voltage−control feedback loop. Thecompensation capacitor also acts as a soft−start capacitor. Pull this pin low with an open drain transistor fordisable.8PHASE Switch node pin. This is the reference for the floating top gate driver. Connect this pin to the source of the top MOSFET.ABSOLUTE MAXIMUM RATINGSPin Name Symbol V MAX V MINMain Supply Voltage Input V CC15 V−0.3 VBootstrap Supply Voltage Input BST30 V wrt/GND15 V wrt/PHASE−0.3 VSwitching Node (Bootstrap Supply Return)PHASE24 V−0.7 V−5 V for < 50 nsHigh−Side Driver Output (Top Gate)TG30 V wrt/GND15 V wrt/PHASE−0.3 V wrt/PHASELow−Side Driver Output (Bottom Gate)BG15 V−0.3 V−2 V for < 200 ns Feedback FB 5.5 V−0.3 V COMP/DISABLE COMP/DIS 5.5 V−0.3 VMAXIMUM RATINGSRating Symbol Value Unit Thermal Resistance, Junction−to−Ambient R q JA165°C/W Thermal Resistance, Junction−to−Case R q JC45°C/W Operating Junction Temperature Range T J−40 to 150°C Operating Ambient Temperature Range T A−40 to 85°C Storage Temperature Range T stg−55 to +150°CLead Temperature Soldering (10 sec): Reflow (SMD styles only) Pb−Free(Note 1)260 peak°C Moisture Sensitivity Level MSL1−Stresses exceeding Maximum Ratings may damage the device. Maximum Ratings are stress ratings only. Functional operation above the Recommended Operating Conditions is not implied. Extended exposure to stresses above the Recommended Operating Conditions may affect device reliability.1.60−180 seconds minimum above 237°C.ELECTRICAL CHARACTERISTICS (0_C < T A < 70_C, −40_C < T J < 125_C (Note 2), 4.5 V < V CC < 13.2 V, 4.5 V < BST < 26.5 V, C TG= C BG= 1.0 nF(REF:NTD30N02), for min/max values unless otherwise noted.)Characteristic Conditions Min Typ Max Unit Input Voltage Range⎯ 4.513.2V Boost Voltage Range⎯ 4.526.5V Supply CurrentQuiescent Supply Current V FB = 1.0 V, No SwitchingV CC= 13.2 V− 1.0 1.75mA Boost Quiescent Current V FB = 1.0 V, No Switching−140−m A Under Voltage LockoutUVLO Threshold V CC Rising Edge 3.85 4.2V UVLO Hysteresis⎯−0.5V Switching RegulatorVFB Feedback Voltage, Control Loop in Regulation T A = 0 to 70°C−40 to 125°C0.7880.80.80.812VOscillator Frequency (NCP1582, NCP1582A)T A = 0 to 70°C−40 to 125°C300350350400kHzOscillator Frequency (NCP1583)T A = 0 to 70°C−40 to 125°C 275300300325kHzRamp−Amplitude Voltage− 1.1−V Minimum Duty Cycle−0−% Maximum Duty Cycle707580% Minimum Pulse Width Static Operating100150ns Blanking Time50ns BG Minimum On Time~500ns Error Amplifier (GM)Transconductance 5.0mmho Open Loop DC Gain5570−DBOutput Source Current Output Sink Current V FB = 0.8 VV FB > 0.8 V8080120120m Am AInput Offset Voltage−2.00 2.0mV Input Bias Current0.1 1.0m A Unity Gain Bandwidth 4.0Mhz Soft−StartSS Source Current V FB < 0.8 V 5.01015m A Switch Over Threshold100% of Vref Current LimitTrip Voltage (NCP1582, NCP1583)Vphase to ground−350mV Trip Voltage (NCP1582A)Vphase to ground−450mV Gate DriversUpper Gate Source Vgs = 6.0 V−0.7A Upper Gate Sink Vugate wrt Phase = 1.0 V 2.4W Lower Gate Source Vgs = 6.0 V−0.7A Lower Gate Sink Vlgate wrt GND = 1.0 V 2.2W PHASE Falling to BG Rising Delay V CC = 12 V, PHASE < 2.0 V, BG > 2.0 V−3090ns BG Falling to TG Rising Delay V CC = 12 V, BG < 2.0 V, TG > 2.0 V−3060ns Enable Threshold0.4V 2.Specifications to −40°C are guaranteed via correlation using standard quality control (SQC), not tested in production.TYPICAL OPERATING CHARACTERISTICSF S W , F R E Q U E N C Y (k H z )V r e f , R E F E R E N C E V O L T A G E (m V )−50−250255075100125T J , JUNCTION TEMPERATURE (°C)S O F T S T A R T S O U R C I N G C U R R E N T (m A )Figure 8. Soft Start Sourcing Current vs.TemperatureFigure 9. I−Limit vs. TemperatureT J , JUNCTION TEMPERATURE (°C)−50−250255075100125DETAILED OPERATING DESCRIPTION GeneralThe NCP158x is an 8−pin PWM controller intended forDC−DC conversion from 5.0 V & 12 V buses. The NCP158xhas a 0.7 A internal gate driver circuit designed to driveN−channel MOSFETs in a synchronous−rectifier bucktopology. The output voltage of the converter can beprecisely regulated down to 800 mV 1.5% when the V FB pinis tied to V OUT. The switching frequency is internally set. Ahigh gain operational transconductance error amplifier(OTA) is used.Duty Cycle and Maximum Pulse Width LimitsIn steady state DC operation, the duty cycle will stabilizeat an operating point defined by the ratio of the input to theoutput voltage. The NCP158x can achieve an 80% dutycycle. There is a built in off−time which ensures that thebootstrap supply is charged every cycle. The NCP158x,which is capable of a 100 nsec pulse width (min.), can allow a 12 V to 0.8 V conversion at 350 kHz.Input Voltage Range (V CC and BST)The input voltage range for both V CC and BST is 4.5 V to 13.2 V with respect to GND and PHASE, respectively. Although BST is rated at 13.2 V with respect to PHASE, it can also tolerate 26.5 V with respect to GND.External Enable/DisableWhen the Comp pin voltage falls or is pulled externally below the 400 mv threshold, it disables the PWM Logic and the gate drive outputs. In this disabled mode, the operational transconductance error amplifier’s (EOTA) output source current is reduced and limited to the Soft Start current of 10m A. Normal Shutdown BehaviorNormal shutdown occurs when the IC stops switching because the input supply reaches UVLO threshold. In this case, switching stops, the internal SS is discharged, and all GATE pins go low. The switch node enters a high impedance state and the output capacitors discharge through the load with no ringing on the output voltage.External Soft StartThe NCP158x features an external soft start function, which reduces inrush current and overshoot of the output voltage. Soft start is achieved by using the internal current source of 10 m A. (typ), which charges the external integrator capacitor of the transconductance amplifier. Figure 10 is a typical soft start sequence. This sequence begins once V CC surpasses its UVLO threshold. During Soft Start, as the Comp Pin rises through 400 mV, the PWM Logic and gate drives are enabled. When the feedback voltage crosses 800mV, the EOTA will be given control to switch to its higher regulation mode output current of 120m A. In the event of an overcurrent during soft start, the overcurrent logic will override the soft start sequence and will shut down the PWM logic and both the high side and low side gates.Figure 10. Soft Start ImplementationVEnableVIsource/SinkTiming Diagram NCP1582: Enable SequenceUVLOUnder V oltage Lockout (UVLO) is provided to ensure that unexpected behavior does not occur when V CC is too low to support the internal rails and power the converter. For the NCP158x, the UVLO is set to ensure that the IC will start up when V CC reaches 4.2 V and shutdown when V CC drops below 3.7 V. This permits operation when converting from a 5.0 input voltage.Current Limit ProtectionIn case of a short circuit or overload, the low−side (LS) FET will conduct large currents. The controller will shut down the regulator in this situation for protection against overcurrent. The low−side R DSon sense is implemented by comparing the voltage at the Phase node when BG starts going low to an internally generated fixed voltage. If the phase voltage is lower than SCP trip voltage, an overcurrent condition occurs and a counter is initiated. When the counter completes, the PWM logic and both HS−FET and LS−FET are turned off. The controller will retry to see if the short circuit or overload condition is removed through the soft start cycle. The minimum turn−on time of the LS−FET is set to be 500 ns. The trip thresholds have a −95 mV, +45 mV process and temperature variation.DriversThe NCP158x includes 0.7 A gate drivers to switch external N−channel MOSFETs. This allows the NCP158x to address high−power as well as low−power conversion requirements. The gate drivers also include adaptive non−overlap circuitry. The non−overlap circuitry increase efficiency, which minimizes power dissipation, by minimizing the body diode conduction time.A detailed block diagram of the non−overlap and gate drive circuitry used in the chip is shown in Figure 11.Figure 11. Block Diagram of Gate Driverand Non−Overlap CircuitryPHASETG BSTV CC BGGNDCareful selection and layout of external components is required, to realize the full benefit of the onboard drivers.The capacitors between V CC and GND and between BST and SWN must be placed as close as possible to the IC. The current paths for the TG and BG connections must be optimized. A ground plane should be placed on the closest layer for return currents to GND in order to reduce loop area and inductance in the gate drive circuit.APPLICATION SECTIONInput Capacitor SelectionThe input capacitor has to sustain the ripple current produced during the on time of the upper MOSFET, so it must have a low ESR to minimize the losses. The RMS value of this ripple is:Iin RMS +I OUT D (1*D)Ǹ,where D is the duty cycle, Iin RMS is the input RMS current,& I OUT is the load current. The equation reaches its maximum value with D = 0.5. Losses in the input capacitors can be calculated with the following equation:P CIN +ESR CIN Iin RMS 2,where P CIN is the power loose in the input capacitors &ESR CIN is the effective series resistance of the input capacitance. Due to large d I /d t through the input capacitors,electrolytic or ceramics should be used. If a tantalum must be used, it must be surge protected. Otherwise, capacitor failure could occur.Calculating Input Start−up CurrentTo calculate the input start up current, the following equation can be used.I inrush +C OUT V OUTt SS,where I inrush is the input current during start−up, C OUT is the total output capacitance, V OUT is the desired output voltage,and t SS is the soft start interval.If the inrush current is higher than the steady state input current during max load, then the input fuse should be rated accordingly, if one is used.Calculating Soft Start TimeTo calculate the soft start time, the following equation can be used.t SS +(C P )C C)*D VI SSWhere C C is the compensation as well as the soft start capacitor,C P is the additional capacitor that forms the second pole.I SS is the soft start currentD V is the comp voltage from zero to until it reachesregulation.V compV outThe above calculation includes the delay from comp rising to when output voltage becomes valid.To calculate the time of output voltage rising to when it reaches regulation; D V is the difference between the comp voltage reaching regulation and 1.1 V .Output Capacitor SelectionThe output capacitor is a basic component for the fast response of the power supply. In fact, during load transient,for the first few microseconds it supplies the current to the load. The controller immediately recognizes the load transient and sets the duty cycle to maximum, but the current slope is limited by the inductor value.During a load step transient the output voltage initial drops due to the current variation inside the capacitor and the ESR. (neglecting the effect of the effective series inductance (ESL)):D V OUT−ESR +D I OUT ESR COUT ,where V OUT−ESR is the voltage deviation of V OUT due to the effects of ESR and the ESR COUT is the total effective series resistance of the output capacitors.A minimum capacitor value is required to sustain the current during the load transient without discharging it. The voltage drop due to output capacitor discharge is given by the following equation:D V OUT−DISCHARGE +D I OUT 2 L OUT2 C OUT (V IN D *V OUT ),where V OUT−DISCHARGE is the voltage deviation of V OUT due to the effects of discharge, L OUT is the output inductor value & V IN is the input voltage.It should be noted that ΔV OUT−DISCHARGE and V OUT−ESR are out of phase with each other, and the larger of these two voltages will determine the maximum deviation of the output voltage (neglecting the effect of the ESL).Inductor SelectionBoth mechanical and electrical considerations influence the selection of an output inductor. From a mechanical perspective, smaller inductor values generally correspond to smaller physical size. Since the inductor is often one of the largest components in the regulation system, a minimum inductor value is particularly important in space−constrained applications. From an electrical perspective, the maximum current slew rate through the output inductor for a buck regulator is given by:SlewRate LOUT +V IN *VOUT L OUT.This equation implies that larger inductor values limit the regulator’s ability to slew current through the output inductor in response to output load transients. Consequently,output capacitors must supply the load current until the inductor current reaches the output load current level. Thisresults in larger values of output capacitance to maintain tight output voltage regulation. In contrast, smaller values of inductance increase the regulator’s maximum achievable slew rate and decrease the necessary capacitance, at the expense of higher ripple current. The peak−to−peak ripple current is given by the following equation:Ipk *pk LOUT +V OUT (1*D)L OUT 350kHz,where Ipk−pk LOUT is the peak to peak current of the output.From this equation it is clear that the ripple current increases as L OUT decreases, emphasizing the trade−off between dynamic response and ripple current.Feedback and CompensationThe NCP158x allows the output of the DC−DC converter to be adjusted from 0.8 V to 5.0 V via an external resistor divider network. The controller will try to maintain 0.8 V at the feedback pin. Thus, if a resistor divider circuit was placed across the feedback pin to V OUT , the controller will regulate the output voltage proportional to the resistordivider network in order to maintain 0.8 V at the FB pin.FBThe relationship between the resistor divider network above and the output voltage is shown in the following equation:R 2+R 1 ǒV REFV OUT *V REFǓ.Resistor R1 is selected based on a design tradeoff between efficiency and output voltage accuracy. For high values of R1 there is less current consumption in the feedback network, However the trade off is output voltage accuracy due to the bias current in the error amplifier. The output voltage error of this bias current can be estimated using the following equation (neglecting resistor tolerance):Error%+0.1m A R 1V REF100%.Once R1 has been determined, R2 can be calculated.Figure 12. Type II Transconductance ErrorAmplifierR C Figure 12 shows a typical Type II transconductance error amplifier (EOTA). The compensation network consists of the internal error amplifier and the impedance networks ZIN (R 1, R 2) and external Z FB (R c , C c and C p ). The compensation network has to provide a closed loop transfer function with the highest 0 dB crossing frequency to have fast response (but always lower than F SW /8) and the highest gain in DC conditions to minimize the load regulation. A stable control loop has a gain crossing with −20dB/decade slope and a phase margin greater than 45°. Include worst−case component variations when determining phase margin. Loop stability is defined by the compensation network around the EOTA, the output capacitor, output inductor and the output divider. Figure 13. shows the open loop and closed loop gain plots.Compensation Network Frequency:The inductor and capacitor form a double pole at the frequencyF LC +12p @L O @C OǸThe ESR of the output capacitor creates a “zero” at the frequency,F ESR +12p @ESR @C O The zero of the compensation network is formed as,F Z +12p @R C C CThe pole of the compensation network is calculated as,F P +12p @R C @C PFigure 13. Gain Plot of the Error AmplifierG A I N (d B )FREQUENCY (Hz)100100010 k100 k1000 kThermal ConsiderationsThe power dissipation of the NCP158x varies with the MOSFETs used, V CC , and the boost voltage (V BST ). The average MOSFET gate current typically dominates the control IC power dissipation. The IC power dissipation is determined by the formula:P IC +(I CC @V CC ))P TG )P BG .Where:P IC = control IC power dissipation,I CC = IC measured supply current,V CC = IC supply voltage,P TG = top gate driver losses,P BG = bottom gate driver losses.The upper (switching) MOSFET gate driver losses are:P TG +Q TG @f SW @V BST .Where:Q TG = total upper MOSFET gate charge at V BST ,f SW = the switching frequency,V BST = the BST pin voltage.The lower (synchronous) MOSFET gate driver losses are:P BG.Where:Q BG = total lower MOSFET gate charge at V CC .The junction temperature of the control IC can then be calculated as:T J +T A )P IC @q JA .Where:T J = the junction temperature of the IC,T A = the ambient temperature,θJA = the junction−to−ambient thermal resistance of the IC package.The package thermal resistance can be obtained from the specifications section of this data sheet and a calculation can be made to determine the IC junction temperature. However,it should be noted that the physical layout of the board, the proximity of other heat sources such as MOSFETs and inductors, and the amount of metal connected to the IC,impact the temperature of the device. Use these calculations as a guide, but measurements should be taken in the actual application.Layout ConsiderationsAs in any high frequency switching converter, layout is very important. Switching current from one power device to another can generate voltage transients across the impedances of the interconnecting bond wires and circuit traces. These interconnecting impedances should be minimized by using wide, short printed circuit traces. The critical components should be located as close together as possible using ground plane construction or single point grounding. The figure below shows the critical power components of the converter. To minimize the voltage overshoot the interconnecting wires indicated by heavy lines should be part of ground or power plane in a printed circuit board. The components shown in the figure below should be located as close together as possible. Please note that the capacitors C IN and C OUT each represent numerous physical capacitors. It is desirable to locate the NCP158x within 1inch of the MOSFETs, Q1 and Q2. The circuit traces for the MOSFETs’ gate and source connections from the NCP158x must be sized to handle up to 2 A peak current.Figure 14. Components to be Considered forLayout SpecificationsRETURNNCP1582, NCP1582A, NCP1583 Design ExampleSwitching Frequency F SW = 350 KHZOutput Capacitance C ESR = 45 m W/EachOutput Capacitance C out = 6630 m FOutput Inductance L out = 0.75 m HInput V oltage V in = 12 VOutput V oltage V out = 3.3 VChoose the loop gain crossover frequency;F CO+110*F SW+35kHzThe corner frequency of the output filter is calculatedbelow;F LC+12*p*0.75m H*6630m FǸ+2.3kHzLet R C = 1500Check that the ESR zero frequency is not too high;F ESR+12*p@CESR@C O t F SW5This condition is mandatory for loop stability.Zero of the compensation network is calculated as follows;F Z+F LCC C+1Z C+12*p*2.3kHz*1500+46nFThe compensation capacitor also acts as the soft start capacitor. By adjusting the value of this compensation capacitor, the soft start time can be adjusted.Pole of the compensation network is calculated as follows;F P+5*F CO+175kHzC P+12*p*F P*R C+12*p*175kHz*1500+700pFThe recommended compensation values are;R C = 1500, C C = 46 nF, C P = 700 pFThe NCP158x bode plot as measured from the network analyzer is shown below.Figure 15. Typical Bode plot of the Open−loop Frequency Response of the NCP158x Top plot: Phase−Frequency (Phase Margin = 62.519°) Bottom plot: Gain−Frequency (UGBW= 5 MHz)NCP1582, NCP1582A, NCP1583 Demo Board PCB LayoutBill of MaterialsItem Number Part Reference Value Quantity MFG 1C1 C2 C3 C41500 m F4PANASONIC 2C5 C6 C722 m F3TDK3C8 1.0 m F1TAIYO YUDEN 4C9100 pF1AVX5C100.022 m F1KEMET6C110.1 m F1AVX7C12 C13 C14 C151800 m F4PANASONIC 8C16 C17 C18 C1910 m F4KEMET9C20OPEN1−10C21OPEN1−11CR1BAS116LT11ON SEMICONDUCTOR 12L10.75 m H1TOKO13Q1 Q240N032ON SEMICONDUCTOR 14R14021DALE15R2OPEN1−16R3 1.02 K1DALE17R4OPEN1−18R6 R702DALE19R8OPEN1−20U1NCP158x1ON SEMICONDUCTORTYPICAL PERFORMANCE CHARACTERISTICSFigure 16. Start UpFigure 17. Gate Waveforms15 A Load SustainingFigure 18. Transient Response (0−10 A Step Load)8083868992123456789101112131415LOAD CURRENT (A)E F F I C I E N C Y (%)Figure 19. Transient ResponseFigure 20. Over Current Protection (22 A DC Trip)Figure 21. Efficiency vs. Load CurrentPACKAGE DIMENSIONSSOIC−8D SUFFIXCASE 751−07ISSUE AHNOTES:1.DIMENSIONING AND TOLERANCING PERANSI Y14.5M, 1982.2.CONTROLLING DIMENSION: MILLIMETER.3.DIMENSION A AND B DO NOT INCLUDEMOLD PROTRUSION.4.MAXIMUM MOLD PROTRUSION 0.15 (0.006)PER SIDE.5.DIMENSION D DOES NOT INCLUDE DAMBARPROTRUSION. ALLOWABLE DAMBARPROTRUSION SHALL BE 0.127 (0.005) TOTALIN EXCESS OF THE D DIMENSION ATMAXIMUM MATERIAL CONDITION.6.751−01 THRU 751−06 ARE OBSOLETE. NEWSTANDARD IS 751−07.DIMAMIN MAX MIN MAXINCHES4.805.000.1890.197MILLIMETERSB 3.80 4.000.1500.157C 1.35 1.750.0530.069D0.330.510.0130.020G 1.27 BSC0.050 BSCH0.100.250.0040.010J0.190.250.0070.010K0.40 1.270.0160.050M0 8 0 8N0.250.500.0100.020S 5.80 6.200.2280.244 YM0.25 (0.010)Z S X S____ǒmminchesǓSCALE 6:1*For additional information on our Pb−Free strategy and solderingdetails, please download the ON Semiconductor Soldering andMounting Techniques Reference Manual, SOLDERRM/D.SOLDERING FOOTPRINT*ON Semiconductor and are registered trademarks of Semiconductor Components Industries, LLC (SCILLC). SCILLC reserves the right to make changes without further notice to any products herein. SCILLC makes no warranty, representation or guarantee regarding the suitability of its products for any particular purpose, nor does SCILLC assume any liability arising out of the application or use of any product or circuit, and specifically disclaims any and all liability, including without limitation special, consequential or incidental damages.“Typical” parameters which may be provided in SCILLC data sheets and/or specifications can and do vary in different applications and actual performance may vary over time. All operating parameters, including “Typicals” must be validated for each customer application by customer’s technical experts. SCILLC does not convey any license under its patent rights nor the rights of others. SCILLC products are not designed, intended, or authorized for use as components in systems intended for surgical implant into the body, or other applications intended to support or sustain life, or for any other application in which the failure of the SCILLC product could create a situation where personal injury or death may occur. Should Buyer purchase or use SCILLC products for any such unintended or unauthorized application, Buyer shall indemnify and hold SCILLC and its officers, employees, subsidiaries, affiliates, and distributors harmless against all claims, costs, damages, and expenses, and reasonable attorney fees arising out of, directly or indirectly, any claim of personal injury or death associated with such unintended or unauthorized use, even if such claim alleges that SCILLC was negligent regarding the design or manufacture of the part. SCILLC is an Equal Opportunity/Affirmative Action Employer. This literature is subject to all applicable copyright laws and is not for resale in any manner.PUBLICATION ORDERING INFORMATION。
2010-26-EU-欧盟新排放指令

DIRECTIVESCOMMISSION DIRECTIVE 2010/26/EUof 31 March 2010amending Directive 97/68/EC of the European Parliament and of the Council on the approximation of the laws of the Member States relating to measures against the emission of gaseous and particulate pollutants from internal combustion engines to be installed in non-road mobile machinery(Text with EEA relevance)THE EUROPEAN COMMISSION, Having regard to the Treaty on the Functioning of the European Union,Having regard to Directive 97/68/EC of 16 December 1997 of the European Parliament and of the Council on the approxi mation of the laws of the Member States relating to measures against the emission of gaseous and particulate pollutants from internal combustion engines to be installed in non-road mobile machinery ( 1 ), and in particular Articles 14 and 14a thereof, Whereas:(1) Article 14a of Directive 97/68/EC sets out the criteria and the procedure for extending the period referred to in Article 9a(7) of that Directive. Studies carried out in accordance with Article 14a of Directive 97/68/EC show that there are substantial technical difficulties to comply with stage II requirements for professional use, multi- positional, hand-held mobile machinery in which engines of classes SH:2 and SH:3 are installed. It is therefore necessary to extend the period referred to in Article 9a(7) until 31 July 2013. (2) Since the amendment of Directive 97/68/EC in 2004, technical progress has been made in the design of diesel engines with a view to make them compliant with the exhaust emission limits for stages IIIB and IV. Electronically controlled engines, largely replacing me- chanically controlled fuel injection and control systems, have been developed. Therefore, the current general type- approval requirements in Annex I to Directive 97/68/EC should be adapted accordingly and general type-approval requirements for stages IIIB and IV should be introduced. (3) Annex II to Directive 97/68/EC specifies the technical details of the information documents that need to be submitted by the manufacturer to the type-approval authority with the application for engine type-approval. The details specified regarding the additional anti- pollution devices are generic and should be adapted to the specific after-treatment systems that need to be used to ensure that engines comply with exhaust emission limit stages IIIB and IV. More detailed information on the after-treatment devices installed on the engines should be submitted to enable type-approval authorities to assess the engine’s capability to comply with stages IIIB and IV.(4) Annex III to Directive 97/68/EC sets out the methodtesting the engines and determining their level of emissions of gaseous and particulate pollutants. The type-approval testing procedure of engines to demon strate compliance with the exhaust emission limits of stage IIIB and IV should ensure that the simultaneous compliance with the gaseous (carbon monoxide, hydro carbons, oxides of nitrogen) and the particulate emission limits is demonstrated. The non-road steady cycle (NRSC) and non-road transient cycle (NRTC) should be adapted accordingly. (5) Point 1.3.2 of Annex III to Directive 97/68/EC foreseesthe modification of the symbols (section 2.18 of Annex I), the test sequence (Annex III) and calculation equations (Appendix III to Annex III), prior to the introduction of the cold/hot composite test sequence. The type approval procedure to demonstrate compliance with the exhaust emission limits of stage IIIB and IV requires the intro duction of a detailed description of the cold start cycle. (6) Section 3.7.1 of Annex III to Directive 97/68/EC sets out the test cycle for the different equipment specifications. The test cycle under point 3.7.1.1 (specification A) needs to be adapted to clarify which engine speed needs to be used in the type approval calculation method. It is also necessary to adapt the reference to the updated version of the international testing standard ISO 8178-4:2007.( 1 ) OJ L 59, 27.2.1998, p. 1.(7) Section 4.5 of Annex III to Directive 97/68/EC outlines the emissions test run. This section needs to be adapted to take account of the cold start cycle. (8) Appendix 3 of Annex III to Directive 97/68/EC sets out the criteria for the data evaluation and calculation of the gaseous emissions and the particulate emissions, for both the NRSC test and the NRTC test set out in Annex III. The type approval of engines in accordance with stage IIIB and IV requires the adaptation of the calculation method for the NRTC test. (9) Annex XIII to Directive 97/68/EC sets out the provisions for engines placed on the market under a ‘flexible scheme’. To ensure a smooth implementation of stage IIIB, an increased use of this flexibility scheme may be needed. Therefore, the adaptation to technical progress to enable the introduction of stage IIIB compliant engines needs to be accompanied by measures to avoid that the use of the flexibility scheme may be hampered by notifi cation requirements which are no longer adapted to the introduction of such engines. The measures should aim at simplifying the notification requirements and the reporting obligations, and at making them more focused and tailored to the need for market surveillance authorities to respond to the increased use of the flexi bility scheme that will result from the introduction of stage IIIB. (10) Since Directive 97/68/EC provides for the type-approval of stage IIIB engines (category L) as from 1 January 2010 it is necessary to provide for the possibility to grant type approval from that date. (11) For reasons of legal certainty this Directive should enter into force as a matter of urgency. (12) The measures provided for in this Directive are in accordance with the opinion of the Committee estab lished in Article 15(1) of Directive 97/68/EC, HAS ADOPTED THIS DIRECTIVE: Article 1 Amendments to Directive 97/68/EC Directive 97/68/EC is amended as follows: 1. in Article 9a(7), the following subparagraph is added: ‘Notwithstanding the first subparagraph, an extension of the derogation period is granted until 31 July 2013, within the category of top handle machines, for professional use, multi- positional, hand-held hedge trimmers and top handle tree service chainsaws in which engines of classes SH:2 and SH:3 are installed.’;2. Annex I is amended in accordance with Annex I to this Directive;3. Annex II is amended in accordance with Annex II to this Directive;4. Annex III is amended in accordance with Annex III to this Directive;5. Annex V is amended in accordance to Annex IV to this Directive;6. Annex XIII is amended in accordance with Annex V to this Directive.Article 2Transitional provisionWith effect from the day following the publication of this Directive in the Official Journal, Member States may grant type-approval in respect of electronically controlled engines which comply with the requirements laid down in Annexes I, II, III, V and XIII to Directive 97/68/EC, as amended by this Directive.Article 3Transposition1. Member States shall bring into force the laws, regulations and administrative provisions necessary to comply with the Directive within 12 months after the publication of the Directive. They shall forthwith communicate to the Commission the text of those provisions.They shall apply those provisions from 31 March 2011.When Member States adopt those provisions, they shall contain a reference to this Directive or be accompanied by such a reference on the occasion of their official publication. Member States shall determine how such reference is to be made.2. Member States shall communicate to the Commission the text of the main provisions of national law which they adopt in the field covered by this Directive.Article 4Entry into forceThis Directive shall enter into force on the day following its publication in the Official Journal of the European Union .Article 5AddresseesThis Directive is addressed to the Member States. Done at Brussels, 31 March 2010. For the Commission The President José Manuel BARROSOANNEX IThe following section 8 is added to Annex I to Directive 97/68/EC:IIIBIVSTAGESANDFOR‘8. TYPEAPPROVALREQUIREMENTS8.1. This section shall apply to the type-approval of electronically controlled engines, which uses electronic control todetermine both the quantity and timing of injecting fuel (hereafter “engine”). This section shall apply irrespective of the technology applied to such engines to comply with the emission limit values set out in sections 4.1.2.5 and 4.1.2.6 of this Annex.8.2. DefinitionsFor the purpose of this section, the following definitions shall apply:8.2.1. “emission control strategy” means a combination of an emission control system with one base emission controlstrategy and with one set of auxiliary emission control strategies, incorporated into the overall design of an engine or non-road mobile machinery into which the engine is installed.8.2.2. “reagent” means any consumable or non-recoverable medium required and used for the effective operation of theexhaust after-treatment system.8.3. Generalrequirements8.3.1. Requirements for base emission control strategy8.3.1.1. The base emission control strategy, activated throughout the speed and torque operating range of the engine,shall be designed as to enable the engine to comply with the provisions of this Directive8.3.1.2. Any base emission control strategy that can distinguish engine operation between a standardised type approvaltest and other operating conditions and subsequently reduce the level of emission control when not operating under conditions substantially included in the type approval procedure is prohibited.8.3.2. Requirements for auxiliary emission control strategy8.3.2.1. An auxiliary emission control strategy may be used by an engine or a non-road mobile machine, provided thatthe auxiliary emission control strategy, when activated, modifies the base emission control strategy in response toa specific set of ambient and/or operating conditions but does not permanently reduce the effectiveness of theemission control system:(a) where the auxiliary emission control strategy is activated during the type approval test, sections 8.3.2.2 and8.3.2.3 shall not apply;(b) where the auxiliary emission control strategy is not activated during the type approval test, it must bedemonstrated that the auxiliary emission control strategy is active only for as long as required for thepurposes identified in section 8.3.2.3.8.3.2.2. The control conditions applicable to this section are all of the following:(a) an altitude not exceeding 1 000 metres (or equivalent atmospheric pressure of 90 kPa);(b) an ambient temperature within the range 275 K to 303 K (2 °C to 30 °C);(c) the engine coolant temperature above 343 K (70 °C).Where the auxiliary emission control strategy is activated when the engine is operating within the control conditions set out in points (a), (b) and (c), the strategy shall only be activated exceptionally.8.3.2.3. An auxiliary emission control strategy may be activated in particular for the following purposes:(a) by onboard signals, for protecting the engine (including air-handling device protection) and/or non-roadmobile machine into which the engine is installed from damage;(b) for operational safety and strategies;(c) for prevention of excessive emissions, during cold start or warming-up, during shut-down;(d) if used to trade-off the control of one regulated pollutant under specific ambient or operating conditions, formaintaining control of all other regulated pollutants, within the emission limit values that are appropriate forthe engine concerned. The purpose is to compensate for naturally occurring phenomena in a manner thatprovides acceptable control of all emission constituents.8.3.2.4. The manufacturer shall demonstrate to the technical service at the time of the type-approval test that theoperation of any auxiliary emission strategy complies with the provisions of section 8.3.2. The demonstration shall consist of an evaluation of the documentation referred to in section 8.3.3.8.3.2.5. Any operation of an auxiliary emission control strategy not compliant with section 8.3.2 is prohibited.8.3.3. Documentation requirements8.3.3.1. The manufacturer shall provide an information folder accompanying the application for type-approval at thetime of submission to the technical service, which ensures access to any element of design and emission control strategy and the means by which the auxiliary strategy directly or indirectly controls the output variables. The information folder shall be made available in two parts:(a) the documentation package, annexed to the application for type-approval, shall include a full overview of theemission control strategy. Evidence shall be provided that all outputs permitted by a matrix, obtained fromthe range of control of the individual unit inputs, have been identified. This evidence shall be attached to theinformation folder as referred to in Annex II;(b) the additional material, presented to the technical service but not annexed to the application for type-approval, shall include all the modified parameters by any auxiliary emission control strategy and theboundary conditions under which this strategy operates and in particular:(i) a description of the control logic and of timing strategies and switch points, during all modes ofoperation for the fuel and other essential systems, resulting in effective emissions control (such asexhaust gas recirculation system (EGR) or reagent dosing);(ii) a justification for the use of any auxiliary emission control strategy applied to the engine, accompanied by material and test data, demonstrating the effect on exhaust emissions. This justification may be basedon test data, sound engineering analysis, or a combination of both;(iii) a detailed description of algorithms or sensors (where applicable) used for identifying, analysing, or diagnosing incorrect operation of the NO x control system;(iv) the tolerance used to satisfy the requirements in section 8.4.7.2, regardless of the used means.8.3.3.2. The additional material referred to in point (b) of section 8.3.3.1 shall be treated as strictly confidential. It shallbe made available to the type-approval authority on request. The type-approval authority shall treat this material as confidential.ofoperationNO x control measures8.4. Requirementstoensurecorrect8.4.1. The manufacturer shall provide information that fully describes the functional operational characteristics of theNO x control measures using the documents set out in section 2 of Appendix 1 to Annex II and in section 2 of Appendix 3 to Annex II.8.4.2. If the emission control system requires a reagent, the characteristics of that reagent, including the type of reagent,information on concentration when the reagent is in solution, operational temperature conditions and reference to international standards for composition and quality must be specified by the manufacturer, in section 2.2.1.13 of Appendix 1 and in section 2.2.1.13 of Appendix 3 to Annex II.8.4.3. The engine emission control strategy shall be operational under all environmental conditions regularly pertainingin the territory of the Community, especially at low ambient temperatures.8.4.4. The manufacturer shall demonstrate that the emission of ammonia during the applicable emission test cycle ofthe type approval procedure, when a reagent is used, does not exceed a mean value of 25 ppm.8.4.5. If separate reagent containers are installed on or connected to a non-road mobile machine, means for taking asample of the reagent inside the containers must be included. The sampling point must be easily accessible without requiring the use of any specialised tool or device.8.4.6. Use and maintenance requirements8.4.6.1. The type approval shall be made conditional, in accordance with Article 4(3), upon providing to each operator ofnon-road mobile machinery written instructions comprising the following:(a) detailed warnings, explaining possible malfunctions generated by incorrect operation, use or maintenance ofthe installed engine, accompanied by respective rectification measures;(b) detailed warnings on the incorrect use of the machine resulting in possible malfunctions of the engine,accompanied by respective rectification measures;(c) information on the correct use of the reagent, accompanied by an instruction on refilling the reagentbetween normal maintenance intervals;(d) a clear warning, that the type-approval certificate, issued for the type of engine concerned, is valid only whenall of the following conditions are met:(i) the engine is operated, used and maintained in accordance with the instructions provided;(ii) prompt action has been taken for rectifying incorrect operation, use or maintenance in accordance with the rectification measures indicated by the warnings referred to in point (a) and (b);(iii) no deliberate misuse of the engine has taken place, in particular deactivating or not maintaining an EGR or reagent dosing system.The instructions shall be written in a clear and non-technical manner using the same language as is used in the operator’s manual on non-road mobile machinery or engine.8.4.7. Reagent control (where applicable)8.4.7.1. The type approval shall be made conditional, in accordance with the provisions of section 3 of Article 4, uponproviding indicators or other appropriate means, according to the configuration of the non-road mobile machinery, informing the operator on:(a) the amount of reagent remaining in the reagent storage container and by an additional specific signal, whenthe remaining reagent is less than 10 % of the full container’s capacity;(b) when the reagent container becomes empty, or almost empty;(c) when the reagent in the storage tank does not comply with the characteristics declared and recorded insection 2.2.1.13 of Appendix 1 and section 2.2.1.13 of Appendix 3 to Annex II, according to the installedmeans of assessment.(d) when the dosing activity of the reagent is interrupted, in cases other than those executed by the engine ECUor the dosing controller, reacting to engine operating conditions where the dosing is not required, providedthat these operating conditions are made available to the type approval authority.8.4.7.2. By the choice of the manufacturer the requirements of reagent compliance with the declared characteristics andthe associated NO x emission tolerance shall be satisfied by one of the following means:(a) direct means, such as the use of a reagent quality sensor.(b) indirect means, such as the use of a NO x sensor in the exhaust to evaluate reagent effectiveness.(c) any other means, provided that its efficacy is at least equal to the one resulting by the use of the means ofpoints (a) or (b) and the main requirements of this section are maintained.’ANNEX IIAnnex II to Directive 97/68/EC is amended as follows:1. Section 2 of Appendix 1 is replaced by the following:POLLUTIONAIRAGAINSTTAKEN‘2. MEASURESyes/no(*)............................................................................................................gases:recyclingcrankcase2.1. Deviceforcoverednotbyheading)ifanother(ifanti-pollutiondevices2.2. Additionalandany,(*)yes/noconverter:2.2.1. Catalytic.......................................................................................................................................................................................2.2.1.1. Make(s):........................................................................................................................................................................................2.2.1.2. Type(s):converterselements................................................................................................................andcatalytic2.2.1.3. Numberofconverter(s):...............................................................................................thecatalyticofandvolume2.2.1.4. Dimensions-........................................................................................................................................................action:ofcatalytic2.2.1.5. Typeprecious........................................................................................................................................metals:of2.2.1.6. Totalchargeconcentration:...........................................................................................................................................................2.2.1.7. Relative.....................................................................................................................................material):and2.2.1.8. Substrate(structure...............................................................................................................................................................................2.2.1.9. Celldensity:2.2.1.10. Type of casing for the catalytic converter(s): .................................................................................................................2.2.1.11. Location of the catalytic converter(s) (place(s) and maximum/minimum distance(s) from engine): ............2.2.1.12. Normal operating range (K): ................................................................................................................................................2.2.1.13. Consumable reagent (where appropriate): .......................................................................................................................2.2.1.13.1. Type and concentration of reagent needed for catalytic action: .............................................................................2.2.1.13.2. Normal operational temperature range of reagent: ......................................................................................................2.2.1.13.3. International standard (where appropriate): ....................................................................................................................2.2.1.14. NO x sensor: yes/no (*)(*)yes/nosensor:2.2.2. Oxygen.......................................................................................................................................................................................2.2.2.1. Make(s):............................................................................................................................................................................................2.2.2.2. Type:.....................................................................................................................................................................................2.2.2.3. Location:(*)yes/noinjection:2.2.3. Airetc.):.........................................................................................................................................pump,2.2.3.1. Type(pulseair,air(*)yes/no2.2.4. EGR:etc.):pressure,........................................................................2.2.4.1. Characteristicspressure/low(cooled/uncooled,high(*)yes/no2.2.5. Particulatetrap:particulate.........................................................................................................thetrap:capacityof2.2.5.1. Dimensionsandparticulatetrap:.........................................................................................................................theandof2.2.5.2. Typedesignengine):..................................................................fromdistance(s)2.2.5.3. Locationand(place(s)maximum/minimumdescriptionand/ordrawing:regeneration,............................................................................ofor2.2.5.4. Methodsystempressure(kPa)and..................................................................................range:2.2.5.5. Normal(K)operatingtemperature(*)yes/nosystems:2.2.6. Otheroperation:...................................................................................................................................................and2.2.6.1. Description___________(*) Strike out what does not apply.’2. Section 2 of Appendix 3 is replaced by the following:POLLUTIONAGAINSTAIRTAKEN‘2. MEASURESyes/no(*)............................................................................................................gases:crankcase2.1. Deviceforrecyclingcoverednotbyheading)ifanotherany,anti-pollutiondevices(ifand2.2. Additional(*)yes/noconverter:2.2.1. Catalytic.......................................................................................................................................................................................2.2.1.1. Make(s):........................................................................................................................................................................................2.2.1.2. Type(s):and................................................................................................................converterselementscatalyticof2.2.1.3. Numberconverter(s):...............................................................................................thecatalyticofandvolume2.2.1.4. Dimensions-........................................................................................................................................................action:ofcatalytic2.2.1.5. Typeprecious........................................................................................................................................metals:of2.2.1.6. Totalchargeconcentration:...........................................................................................................................................................2.2.1.7. Relative.....................................................................................................................................material):and2.2.1.8. Substrate(structure...............................................................................................................................................................................2.2.1.9. Celldensity:2.2.1.10. Type of casing for the catalytic converter(s): .................................................................................................................2.2.1.11. Location of the catalytic converter(s) (place(s) and maximum/minimum distance(s) from engine): ............2.2.1.12. Normal operating range (K) .................................................................................................................................................2.2.1.13. Consumable reagent (where appropriate): .......................................................................................................................2.2.1.13.1. Type and concentration of reagent needed for catalytic action: .............................................................................2.2.1.13.2. Normal operational temperature range of reagent: ......................................................................................................2.2.1.13.3. International standard (where appropriate): ....................................................................................................................2.2.1.14. NO x sensor: yes/no (*)yes/no(*)sensor:2.2.2. Oxygen.......................................................................................................................................................................................2.2.2.1. Make(s):............................................................................................................................................................................................2.2.2.2. Type:.....................................................................................................................................................................................2.2.2.3. Location:(*)yes/noinjection:2.2.3. Airetc.):.........................................................................................................................................pump,2.2.3.1. Type(pulseair,air(*)yes/no2.2.4. EGR:etc.):pressure,........................................................................2.2.4.1. Characteristicspressure/low(cooled/uncooled,high(*)yes/no2.2.5. Particulatetrap:particulate.........................................................................................................thetrap:capacityof2.2.5.1. Dimensionsandparticulatetrap:.........................................................................................................................theandof2.2.5.2. Typedesignengine):..................................................................fromdistance(s)2.2.5.3. Locationand(place(s)maximum/minimumdescriptionand/ordrawing:regeneration,............................................................................ofor2.2.5.4. Methodsystempressure(kPa)and..................................................................................range:2.2.5.5. Normal(K)operatingtemperature(*)yes/nosystems:2.2.6. Otheroperation:...................................................................................................................................................and2.2.6.1. Description___________(*) Strike out what does not apply.’。
20AG高流压力调节器3 15 en 8.420.200.01说明书

Medium:Compressed air onlyMaximum inlet pressure:28 bar (406 psi) max. Pressure range:0,1 ... 3,5 bar (1 ... 50 psi),0,2 ... 8 bar (3 ... 116 psi) 0,7 ... 17 bar (10 ... 246 psi) (1/2” version only)Port sizes:1/2”, 3/4” or 1”Gauge port:1/8 PTF with PTF main ports Rc1/8 with ISO G main portsAmbient/Media temperature:-20 ... +80°C (-4 ... +176 °F) Version with gauge:-20° ... +65°C (-4° ... +149°F) Air supply must be dry enough to avoid ice formation at temperatures below +2°C (+35 °F)Materials:Body: Zinc alloyBonnet: Aluminium alloyBottom plug: Glass filled nylon for G 1/2, aluminium for G 3/4 and G 1 Adjusting screw: Steel-plated Elastomers: Synthetic rubberTechnical features>Port size G1/2 ... G1 >Ported regulators for general purpose and high flow pneumatic applications >Large diaphragm provides accurate and quick response to changing flow demands and line pressure>Balanced valve minimizes effect of variations in inlet pressure on outlet pressure >Extensive range of applicationsTechnical data, standard modelsG-*1) O utlet pressure can be adjusted to pressures in excess of, and less than, those specified. Do not use these units to control pressures outside of the specified ranges.*2) O ther seals or use other gases might be possible - please contact NorgrenFlow characteristicsInlet pressure: 10 bar, port size: 1/2” Range: 0,2 ... 8 barInlet pressure: 10 bar, port size: 1” Range: 0,2 ... 7 barAir flow Air flowO u t l e t p r e s s u r eO u t le t p r e s s u r e21Accessories Accessories86420Service kits20AG-X4-10020AG-4-100Panel mounted with plastic handwheel, 1/2” onlyBracket mounting2Gauge portDimensionsDimensions in mm Projection/First angleWarningThese products are intended for use in industrial compressed air systems only. Do not use these products where pressures and temperatures can exceed those listed under»Technical features/data«.Before using these products with fluids other than those specified,for non-industrial applications, life-support systems or other applications not within published specifications, consult IMI NORGREN. Through misuse, age, or malfunction, components used in fluid power systems can fail in various modes.The system designer is warned to consider the failure modes of all component parts used in fluid power systems and to provide adequate safeguards to prevent personal injury or damage to equipment in the event of such failure.System designers must provide a warning to end users in the system instructional manual if protection against a failure mode cannot be adequately provided.System designers and end users are cautioned to review specific warnings found in instruction sheets packed and shipped with these products.。
- 1、下载文档前请自行甄别文档内容的完整性,平台不提供额外的编辑、内容补充、找答案等附加服务。
- 2、"仅部分预览"的文档,不可在线预览部分如存在完整性等问题,可反馈申请退款(可完整预览的文档不适用该条件!)。
- 3、如文档侵犯您的权益,请联系客服反馈,我们会尽快为您处理(人工客服工作时间:9:00-18:30)。
n u c l -e x /9711001 7 N o v 1997Directed and Elliptic Flow in 158 GeV/Nucleon Pb + Pb CollisionsDraft 2.2H. Appelshäuser (7, #), J. Bächler(5), S .J. Bailey(16), L.S . Barnby(3), J. Bartke(6),R.A. Barton(3), H. Bialkowska(14), C.O. Blyth(3), R. Bock(7), C. Bormann(10), F.P. Brady(8),R. Brockmann(7,±), N. Buncic(5, 10), P. Buncic(5, 10), H.L. Caines(3), D. Cebra(8),G.E. Cooper(2), J.G. Cramer(16), P. Csato(4), J. Dunn(8), V. Eckardt(13), F. Eckhardt(12),M.I. Ferguson(5), H.G. Fischer(5), D. Flierl(10), Z. Fodor(4), P. Foka(7, 10), P. Freund(13),V. Friese(12), M. Fuchs(10), F. Gabler(10), J. Gal(4), M. Gazdzicki(10), E. Gladysz(6),J. Grebieszkow(15), J. Günther(10), J.W. Harris(17), S. Hegyi(4), T. Henkel(12), L.A. Hill(3),I. Huang(2, 8), H. Hümmler(10,+ ), G. Igo(11), D. Irmscher(2, 7), P. Jacobs(2), P.G. Jones(3),K. Kadija(18, 13), V.I. Kolesnikov(9), M. Kowalski(6), B. Lasiuk(11, 17), P. Levai(4),A.I. Malakhov(9), S. Margetis(2,∗), C. Markert(7), G.L. Melkumov(9), A. Mock(13),J. Molnar(4), J.M. Nelson(3), G. Odyniec(2), G. Palla(4), A.D. Panagiotou(1), A. Petridis(1),A. Piper(12), R.J. Porter(2), A.M. Poskanzer(2), S. Poziombka(10), D.J. Prindle(16),F. Pühlhofer(12), W. Rauch(13), J.G. Reid(16), R. Renfordt(10), W. Retyk(15), H.G. Ritter(2),D. Röhrich(10), C. Roland(7), G. Roland(10), H. Rudolph(2, 10), A. Rybicki(6),A. S andoval(7), H. S ann(7), A.Yu. S emenov(9), E. S chäfer(13), D. S chmischke(10),N. S chmitz(13), S . S chönfelder(13), P. S eyboth(13), J. S eyerlein(13), F. S ikler(4),E. S krzypczak(15), G.T.A. S quier(3), R. S tock(10), H. S tröbele(10), I. S zentpetery(4),J. S ziklai(4), M. Toy(2, 11), T.A. Trainor(16), S. Trentalange(11), T. Ullrich(17),M. Vassiliou(1), G. Vesztergombi(4), S. Voloshin(2,#, & ), D. Vranic(5, 18), F. Wang(2),D.D. Weerasundara(16), S. Wenig(5), C. Whitten(11), T. Wienold(2,#), L. Wood(8),T.A. Yates(3), J. Zimanyi(4), R. Zybert(3)(NA49 Collaboration)(1)Department of Physics, University of Athens, Athens, Greece.(2)Lawrence Berkeley National Laboratory, University of California, Berkeley, CA, US A.(3)Birmingham University, Birmingham, England.(4)KFKI Research Institute for Particle and Nuclear Physics, Budapest, Hungary.(5)CERN, Geneva, S witzerland.(6)Institute of Nuclear Physics, Cracow, Poland.(7)Gesellschaft für Schwerionenforschung (GSI), Darmstadt, Germany.(8)University of California at Davis, Davis, CA, US A.(9)Joint Institute for Nuclear Research, Dubna, Russia.(10)Fachbereich Physik der Universität, Frankfurt, Germany.(11)University of California at Los Angeles, Los Angeles, CA, USA.(12)Fachbereich Physik der Universität, Marburg, Germany.(13)Max-Planck-Institut für Physik, Munich, Germany.(14)Institute for Nuclear Studies, Warsaw, Poland.(15)Institute for Experimental Physics, University of Warsaw, Warsaw, Poland.(16)Nuclear Physics Laboratory, University of Washington, S eattle, WA, US A.(17)Yale University, New Haven, CT, USA.(18)Rudjer Boskovic Institute, Zagreb, Croatia.(Received , 1997)The directed and elliptic flow of protons and charged pions has been observedfrom the semi-central collisions of a 158 GeV/nucleon Pb beam with a Pb target.The rapidity and transverse momentum dependence of the flow has beenmeasured. The directed flow of the pions is opposite to that of the protons butboth exhibit negative flow at low p t. The elliptic flow of both is fairlyindependent of rapidity but rises with p t.PACS numbers: 25.75.-q, 25.75.LdThe azimuthal anisotropy of charged particle emission from the interaction of a 158 GeV/nucleon Pb beam with a Pb target has been studied in the two main Time Projection Chambers (TPCs) of CERN SPS experiment NA49.1The TPCs, situated downstream of two large dipole magnets, cover a large region of phase space forward of mid-rapidity. Identification of protons and pions is performed by measurements of energy loss of the detected particles in the gas of the TPCs. The large phase-space acceptance allows event-by-event study of the angular correlations of the particles from the interaction. It is thought that angular correlations generated by collective flow retain some signature of the effective pressure achieved at maximum compression in the interaction.2, 3 This is the first study of directed and elliptic flow as a function of rapidity and transverse momentum for collisions of the heaviest nuclei at the highest bombarding energy presently available.Usually three kinds of flow in the plane transverse to the beam are considered: radial transverse flow, directed flow, and elliptic flow. For central collisions which are azimuthally isotropic, only radial transverse flow is allowed. One of its effects is to raise the apparent temperature of the single-particle transverse momentum spectra. For non-central collisions, a plane can be determined for each event describing the azimuthal anisotropy of the event, and directed and elliptic flow can be identified from the azimuthal anisotropy of the particles with respect to this plane. In a Fourier expansion4-6of the azimuthal distribution of the particles with respect to this plane the amplitude of the first harmonic of the distribution corresponds to the directed flow which was discovered at the Bevalac.7 One of the measures of directed flow, the mean momentum in the flow direction, appears to peak at beam energies of about one GeV/nucleon and then decreases at higher energies.8 Except at the very lowest beam energies, the directed flow of the protons is thought to be on the side of the beam away from the target nucleus. On the other hand, the directed flow of the produced pions is often opposite to that of the protons because of shadowing effects. For a recent review of flow see ref. [9]. From the data presented here the decrease from the peak values at Bevalac-S IS energies to SPSenergies is a factor of about 400 for the mean polar flow angle and a factor of 5-10 for the mean momentum in the flow direction. Thus, directed flow is a much smaller effect at the SPS then a t lower beam energies. The amplitude of the second harmonic of the azimuthal distribution of particles with respect to the event plane measures the elliptic flow, the importance of which at high energies was first emphasized by Ollitrault.10 At Bevalac energies elliptic flow for both protons5 and produced pions11 was found to be oriented perpendicular to the directed flow and was called squeeze-out, but at high energies elliptic flow is expected to be in the plane of the directed flow3, 10, 12, and this has been found at the AGS.13 From the data presented here it will be shown that the elliptic flow at the SPS is comparable to that at Bevalac-S IS energies but oriented in the plane of the directed flow instead of perpendicular to the plane as at Bevalac energies.The data presented here consist of 50k events taken with a medium bias trigger as determined by the NA49 veto calorimeter which measures the energy within 0.3° of the beam. This trigger selected events with veto calorimeter energy14from 0.45 to 0.6 of the beam energy, and corresponds to an impact parameter selection of about 6.5 to 8.0 fm, as estimated from VENUS15 simulations.Particle identification was performed in the TPCs by measuring the specific energy loss in the gas and was used to identify highly enriched samples of protons and charged pions. The proton sample used in this analysis had laboratory momenta greater than 30 GeV/c. It had an observed rapidity distribution peaked between 4 and 5.25 and an observed mean multiplicity of about 20. By comparison with the yield of negative particles in the same energy-loss window i t was estimated that this proton sample was enriched to about 85% in protons. After removing this proton sample, the other positive and negative charged particles formed a sample called charged particles. However, the particles in the proton energy-loss window between 10 and 30 GeV/c were not included in either the proton sample or this charged particle sample. From this charged particle sample, those particles with rapidity (assuming the pion mass) from 4 to 6, and transverse momenta from 0.05 to 1.0 GeV/c were used to determine the orientation of the event plane. They had a mean observed multiplicity of about 170. They were also used for the results which are integrated over rapidity and p t. The sample identified as pions had momenta between 3 and 50 GeV/c and was thought to be highly enriched in pions based on fits of four Gaussian distributions (p, K, π, e) to the energy-loss spectra. This pion sample had an observed rapidity distribution peaked around 4 and a observed mean multiplicity of about 120. This pion sample was used for the results to be presented as a function of rapidity and p t.Both first harmonic and second harmonic event planes, called here respectively the plane and the ellipse, were determined event by event. The azimuthal laboratory angles of these planes were calculated with the following equation:Øn =∑wgt(Øi) si n (n Øi)∑wgt(Øi) cos(n Øi)(t a n-1)/n(1)where n = 1 for the plane, n= 2 for the ellipse, the sum goes over i for the charged particles used in the event plane determinations, Øi is the azimuthal laboratory angle of particle i, and the quantity wgt will be described below. The angle Ø1 = Øplane covers 0 to 2π and Ø2 = Øellipse covers 0 to π, using the signs of the sums to determine the quadrant. In other words, the angle is defined by the vector whose laboratory components in the plane perpendicular to the beam are, respectively, the numerator and denominator in the above equation. Notice that the angle of the ellipse is calculated by summing over 2Ø instead of Ø. Notice also that p t is not used in these equations, so that they represent the number weighted angles, not the momentum weighted angles. Also, because p t is not used in the above equations, the acceptance biases have to be removed only with respect to Ø, and not with respect to p t.To remove the biases due to acceptance correlations we have used three methods: event plane flattening by weighting, event plane flattening by shifting, and event mixing. Flattening of the event plane laboratory angular distribution by weighting involved using the inverse of the laboratory azimuthal distributions of the particles, summed over all events, as a 36 channel histogram for wgt(Øi) in the above equation. Flattening the distribution of the event planes by shifting involved setting wgt(Øi) in the above equation to one and then fitting the resultant azimuthal distributions of the event planes, summed over all events, to a Fourier expansion. Harmonics up to fourth order were used for the plane, but of these only the even harmonics entered into the fit for the ellipse. From the resultant coefficients of the fit one can derive an equation for shifting the event plane angles, event by event, to obtain flat distributions.16 With this method the distributions of Øplane and Øellipse are flat in the laboratory as shown in the top half of Fig. 1. All the results presented here used this shifting method of flattening even though the flow values and the resolution corrections were exactly the same using the weighting method.The mixed event method calculates the usual azimuthal distribution of the particles of interest with respect to the event plane of their own event, but then divides this distribution by the azimuthal distribution of these same particles with respect to the event plane of the previousevent. This method also gave the same results. In addition, we have obtained the same results by combining the methods: flattening first and then dividing the azimuthal correlations by those for mixed events. However, using the mixed event method with only one mixed event for each real event increases the error of the results by √2.The correlations of the selected particles with respect to the above defined event-by-event planes were found by evaluating the coefficients in the Fourier expansions of the azimuthal distributions (normalized to an average value of one) with respect to the two planes:1 +2 v 1obs cos(Ø - Øplane ) + 2 v 2obs cos(2(Ø - Øplane ))(2)1 + 2 v 2obs cos(2(Ø - Øellipse )).(3)The coefficient v 1obs is evaluated by <cos(Ø - Øplane )>, where <> indicates the mean value summed over the particles of interest for all events. The v 1obs is <p x /p t > whereas v 2obs is relatedto the eccentricity of the ellipse by <(p x /p t )2 - (p y /p t )2>, with x and y being the directions perpendicular to the beam with x in the event plane. The quantity v 2obs can be evaluated from<cos(2(Ø - Øplane ))>, and in fact, its sign gives the relative orientation of the plane and the ellipse. However, higher accuracy for the value of v 2obs was obtained by evaluating <cos(2(Ø -Øellipse ))>. Of course, when a particle had been used to calculate the direction of a plane, the auto-correlation effect in its distribution with respect to this plane was removed in the usual way by recalculating that plane's orientation without this particle.17The v 1obs and v 2obs values are the flow values relative to the observed event planes. To obtain the flow values relative to the true reaction plane one has to divide these values by a factor which corrects for the limited resolution of the measurement of the angle of the event planes.46, 18 To accomplish this the events were randomly divided into two sub-events and the correlations of the planes of the sub-events were evaluated. The square root of <cos(Øsub1 -Øsub2)> and of <cos(2(Øsub1 - Øsub2))> are the resolution corrections of the observed sub-event planes. The resolution corrections of the observed event planes of the full events were determined by correcting for the fact that the full events have twice the multiplicity of the sub-events. When the resolution corrections are small compared to one this can be done by multiplying the resolution corrections by √2. Instead we used the more general multiplicity dependence of the resolution correction given by eq. 13 and fig. 4 of ref. [4] to do this extrapolation. Table I lists the measured resolution correction factors for the sub-events as well as the extrapolated values for the full events.Table I. Corrections for theresolutions of the observed planes.sub-event full eventplane0.25 ± 0.0060.35 ± 0.009ellipse0.19 ± 0.0080.27 ± 0.011To evaluate our methods and, in particular, our ability to remove the acceptance correlations, we generated 50k events with a simple Monte-Carlo event generator which had no azimuthal correlations but reproduced the charged particle and proton multiplicities and p t spectra within our acceptance. These events were filtered through a GEANT model of the NA49 detector.19 In the GEANT simulation, all physics processes including decays were turned off so that these events should not have any correlations beyond those due to the acceptance geometry.The experimental azimuthal distributions of the charged particles are plotted with respect to the charged particle plane and ellipse in Fig. 1 bottom. Also shown are the results from the simple Monte-Carlo filtered for the NA49 acceptance. The graphs clearly show both directed flow in the forward hemisphere (with symmetry about 180°) and elliptic flow (with symmetry about 90°). In the bottom left graph the fit contains a second harmonic with positive amplitude which shows that the ellipse is aligned with the plane. This means that the elliptic flow is in-plane, not out-of-plane squeeze-out. This was verified by observing a positive correlation between the plane of one charged particle sub-event and the ellipse of the other.Data not shown indicate that the ellipses of the protons and the other charged particles are aligned, and that the directed flow of the protons appears to be small and opposite to that of the other charged particles. It was assumed that the proton directed flow is in the positive (direction of the impact parameter from the target nucleus) side of the event plane. A summary of the results is given in Table II, integrated over the rapidity and p t ranges indicated. This selection of charged particles is the same as that which was used to determine the event planes. The units of percent mean that the numbers have been multiplied by a factor of one hundred.Table II. Flow values integrated over the indicated y and p t ranges.Particle y p t (GeV/c) v1 (%) v2 (%)protons 3 - 60.0 - 2.0 1.1 ± 0.2 2.6 ± 0.3charged particles 4 - 60.05 - 1.0-3.0 ± 0.1 2.3 ± 0.1The rapidity and p t dependence of the flow of the protons and the identified pions are now evaluated relative to the same charged particle event planes used above. As above, all flow values are corrected for the resolutions of these planes. For the rapidity dependence a rather high p t window of 0.6 to 2.0 GeV/c was used for the protons but a low window of 0.05 to 0.35GeV/c was used for the pions. These windows were chosen to obtain the widest region of flat acceptance. The rapidity dependence of the flow is shown in Fig. 2 with reflection about mid-rapidity. In reflection, the signs of the v1values have been reversed in the backwardhemisphere, but not the v2values. The directed flow (v1) values exhibit characteristic S-shaped curves and the elliptic flow (v2) values appear to be flat for the pions but peaking somewhat near mid-rapidity for the protons. Here one can see that our choice of the sign of the event plane is plausible from the fact that the protons at high rapidity have positive directed flow, as one would expect for the baryons in the reaction plane. Fig. 3 shows the p t dependence of the flow in a rapidity window from 4.0 to 5.0. These curves should go to zero at zero p t where no transverse direction is defined. For the pions the lowest points indicate that the curves are tending to zero.At first sight the v1curves in Fig. 3 appear peculiar, especially for the pions, because they approach zero from the negative side. However, this behavior was predicted for protons by Voloshin20 as a consequence of the interaction of transverse radial flow and directed flow. Simply, in the presence of large transverse radial flow, a low p t particle can be produced only by the part of the moving source where the directed flow subtracts from the radial flow. If this is the correct explanation then the data also contain information on the transverse radial flow. However, especially for the pions, it is also possible that this behavior of the directed flow results from some kind of fireball shadowing effect, resonance decays, or Coulomb effects. Previously, elliptic flow has been observed using the NA49 Ring Calorimeter by analyzing the azimuthal anisotropy of the transverse energy in the pseudorapidity interval from 2 to 4 for an impact parameter of 7 to 8 fm.21 The correlation which was observed between the forward and backward event planes is not inconsistent with that seen here considering that transverse energy flow, not number flow, was studied, that neutral particles and charged baryons were included, and that the bins were in pseudorapidity. Also the elliptic flow of photons from π0 decay has been reported22 by WA93 for S + Au at the SPS. They find an anisotropy of the order of 5% for semi-central collisions.At the AGS, E877 reported18 v1 values of about 10% for protons and about 2% for pions. Their v2values13 for charged particles are, however, at most 2%. Thus, although the directed flow is smaller at the SPS, the elliptic flow may be larger.In summary, we have presented the first data on directed and elliptic flow for Pb + Pb collisions at 158 GeV/nucleon. Protons and pions exhibit significant, but opposite, directed flow at large rapidities. The elliptic flow signal was found to be fairly independent of rapidity for the pionsbut peaking somewhat near mid-rapidity for the protons. For both sets of particles the flow axis of the elliptic flow is in the plane of the directed flow. This excludes shadowing by spectator matter as the origin of the elliptic flow. Therefore we conclude that the elliptic flow in these semi-central collisions retains some signature of the pressure in the high density region created during the initial collision.Acknowledgments. This work was supported by the Director, Office of Energy Research, Division of Nuclear Physics of the Office of High Energy and Nuclear Physics of the US Department of Energy under Contract DE-ACO3-76S FOOO98, the US National S cience Foundation, the Bundesministerium fur Bildung und Forschung, Germany, the Alexander von Humboldt Foundation, the UK Engineering and Physical Sciences Research Council, the Polish State Committee for Scientific Research (2 P03B 01912), and the Polish-German Foundation.phi lab (deg)c o u n t s phi lab (deg)c o u n t s phi - phi plane (deg)n o r m a l i z ed c o u n t s phi - phi ellipse (deg)n o r m a l i z e d c o u n t s 2400250026002700280029002400250026002700280029000.980.9850.990.99511.0051.011.0151.021.0251.03045901351800.980.9850.990.99511.0051.011.0151.021.0251.0304590135180Fig 1. On the top are shown the flatness achieved with the shifting method for the plane (left)and ellipse (right) in the laboratory system. Note the suppressed zero on the vertical axis.On the bottom are shown the azimuthal distributions of the charged particles with respect to the plane (left) and ellipse (right) of the charged particles. The distributions have been normalized to an average value of one. The dashed points and curves near a value of one are for the simple Monte-Carlo. The curves are fits with cos(Ø) plus cos(2 Ø) (eq. 2) (left), and cos(2 Ø)(eq. 3) (right). On the right, the points above 90° have been reflected from those below 90°. The results are integrated for rapidity from 4.0 to 6.0 and p t from 0.05 to 1.0 GeV/c.-100246810F l o w (%)rapidity-3-2-1123F l o w (%)rapidityFig 2. The rapidity dependence of the directed (v 1) and elliptic (v 2) flow for the protons(0.6 < p t < 2.0 GeV/c) and pions (0.05 < p t < 0.35 GeV/c). The points between y=0 and mid-rapidity (y=2.92) have been reflected from the measurements in the forward hemisphere. The curves are to guide the eye.F l o w (%)p t(GeV/c)F l o w (%)p t (GeV/c)Fig 3. The transverse momentum dependence of the directed (v 1) and elliptic (v 2) flow for theprotons and pions with 4.0 < y < 5.0. The curves are to guide the eye.1 S. V. Afanasiev et al., NA49, NIM , to be submitted (1997) .2 H. Stöcker and W. Greiner, Phys. Reports 137, 277 (1986) .3 H. Sorge, Phys. Rev. Lett. 78, 2309 (1997) .4 S. Voloshin and Y. Zhang, Z. Phys. C 70, 665 (1996) This paper fits the laboratory azimuthal distribution with a Fourier expansion event-by-event. The present paper calculates, event-by-event, the distribution of particles with respect to event planes, but fits the Fourier expansion to these distributions summed over all events.5 H. H. Gutbrod et al., Plastic Ball, Phys. Rev. C 42, 640 (1990) .6 M. Demoulins et al., Phys. Lett. B 241, 476 (1990) .7 H. Å. Gustafsson et al., Plastic Ball, Phys. Rev. Lett. 52, 1590 (1984) .8 J. Chance et al., EOS, Phys. Rev. Lett. 78, 2535 (1997) .9 W. Reisdorf and H. G. Ritter, Ann. Rev. Nucl. Part. Sci. , in print (1997) .10 J. Y. Ollitrault, Phys. Rev. D 46, 229 (1992) .11 D. Brill et al., KaoS, Phys. Rev. Lett. 71, 336 (1993) .12 P. Filip, Acta Physica Slovaca 47, 53 (1997) .13 J. Barrette et al., E877, Phys. Rev. Lett. 73, 2532 (1994) .14 T. Alber et al., NA49, Phys. Rev. Lett. 75, 3814 (1995) .15 K. Werner, Phys. Letters B 208, 520 (1988) .16 J. Barrette et al., E877, Phys. Rev. C , in print (1997) , nucl-ex/9707002.17 P. Danielewicz and G. Odyniec, Phys. Lett. B 157, 146 (1985) .18 J. Barrette et al., E877, Phys. Rev. C 55, 1420 (1997) .19 P. Jacobs, NA49, Internal Note , #22 (1993) .20 S. A. Voloshin, Phys. Rev. C 55, R1630 (1997) .21 T. Wienold et al., NA49, Nucl. Phys. A 610, 76c (1996) .22 M. M. Aggarwal et al., WA93, Phys. Letters B403, 390 (1997) .± deceased.+ present address: Max-Planck-Institut für Physik, Munich, Germany.∗ present address: Kent State Univ., Kent, OH, USA.# present affiliation: Physikalisches Institut, Universität Heidelberg, Germany.& permanent affiliation: Moscow Engineering Physics Institute, Moscow, Russia.。