高速切削---实现绿色切削的有效途径
先进制造工艺技术高速切削

进给速度
合理设置进给速度,以保 证加工表面质量和刀具寿 命。
切削深度
根据刀具和工件材料特性, 选择合适的切削深度,以 获得良好的加工效果。
加工过程的监控与检测
01
切削力监测
通过实时监测切削力变化,可以 判断刀具磨损情况和调整切削参 数。
02
加工表面质量检测
03
刀具磨损监测
采用表面粗糙度仪、光学显微镜 等方法检测加工表面质量,以确 保加工精度和降低不良率。
高速切削适用于多种材料加工 ,包括钢、铸铁、有色金属等
,扩大了加工范围。
高速切削对机床的要求
高转速主轴
高进给系统
为了实现高速旋转的刀具,机床需要配备 高转速的主轴,通常转速范围在每分钟数 千转到数万转之间。
为了实现高速进给的切削方式,机床需要 配备高进给的传动系统和控制系统,确保 切削过程的稳定性和准确性。
刀具涂层
涂层技术能够提高刀具表面的硬度 和耐磨性,降低摩擦系数,从而提 高切削速度和加工效率。
刀具结构
采用合理的刀具结构和几何参数, 如刀尖圆弧半径、切削刃倾角等, 能够改善切削效果,减少刀具磨损。
切削液技术
切削液种类
选择合适的切削液对于降低切削 温度、减少刀具磨损和提高加工 表面质量至关重要。常用的切削 液有油基、水基和半合成切削液
集成电路芯片。
高速切削技术能够实现高精度、 高效率的加工,满足电子信息产 业对产品精度和一致性的高要求。
高速切削技术的应用还有助于提 高电子信息产品的性能和可靠性,
降低生产成本。
05 高速切削技术的发展前景 与挑战
高速切削技术的发展前景
高效加工
高速切削技术能够显著提高加工效率,缩短产品 制造周期,降低生产成本。
高速切削技术研究
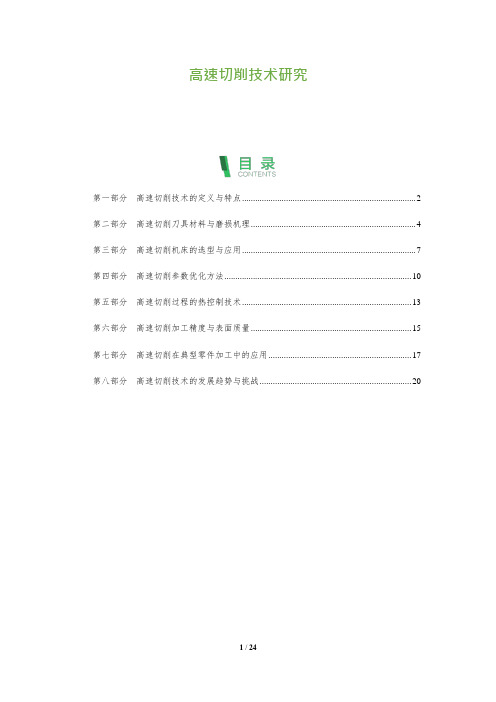
高速切削技术研究第一部分高速切削技术的定义与特点 (2)第二部分高速切削刀具材料与磨损机理 (4)第三部分高速切削机床的选型与应用 (7)第四部分高速切削参数优化方法 (10)第五部分高速切削过程的热控制技术 (13)第六部分高速切削加工精度与表面质量 (15)第七部分高速切削在典型零件加工中的应用 (17)第八部分高速切削技术的发展趋势与挑战 (20)第一部分高速切削技术的定义与特点高速切削技术是一种先进的制造工艺,它通过使用高转速的刀具和优化的切削参数来提高材料去除率、加工精度和表面质量。
该技术的核心在于实现高效率、高质量和高精度的加工过程。
在高速切削过程中,刀具以极高的速度旋转(通常超过每分钟数千转),同时进给速度也相应提高。
这种高速旋转产生的离心力有助于减小切削力和切削热,从而延长刀具寿命并减少工件的热变形。
此外,由于切削力的降低,高速切削还可以减少振动,进一步提高加工精度。
高速切削技术的优势主要体现在以下几个方面:1.高效率:与传统切削相比,高速切削可以显著提高材料去除率,缩短加工时间。
研究表明,高速切削可以提高生产效率达 30%至50%。
2.高精度:高速切削过程中的低切削力可以减少工件的振动,从而提高加工精度。
此外,由于切削热的影响较小,工件的热变形也得到了控制。
3.高质量表面:高速切削产生的切削热较低,这有助于减少工件的烧伤和裂纹,从而获得更好的表面质量。
4.刀具寿命延长:高速切削可以降低切削力,减少刀具磨损,从而延长刀具的使用寿命。
5.节能减排:高速切削技术可以实现更高的材料去除率,从而减少能源消耗和碳排放。
然而,高速切削技术也存在一些挑战,如刀具成本较高、对机床性能要求较高等。
因此,在实际应用中,需要根据具体加工需求和技术条件,合理选择切削参数和刀具,以确保高速切削技术的有效性和经济性。
总之,高速切削技术作为一种先进的制造工艺,具有高效率、高精度、高质量表面等优势,但在实际应用中需充分考虑其成本和设备要求。
机械制造中的机械加工高速切削技术

机械制造中的机械加工高速切削技术高速切削是机械加工领域中的一项重要技术,它在工件加工过程中使用高速切削工具,以较大的进给速度和转速进行切削,提高了加工效率和加工质量。
本文将介绍机械加工高速切削技术的原理、特点以及在机械制造中的应用。
一、高速切削技术的原理高速切削技术是基于高速运动的切削工具和工件之间的相对运动原理。
在高速切削过程中,切削工具以较高的转速和进给速度与工件接触,形成切屑并进行切削。
相比传统的慢速切削,高速切削具有以下特点:1. 切削速度较快:高速切削在保持刀具刃口整齐的情况下,增大刀具转速和进给速度,从而大幅提高了切削效率。
2. 切削温度较低:高速切削由于切削时间短,切削工具与工件接触时间减少,从而减少了热量在切削区域的积累,使得切削温度低于常规切削。
3. 切削力较小:高速切削采用较高的转速和进给速度,在单位时间内切削的材料量相对较大,切削力得到了有效分散,从而降低了切削力的大小。
二、高速切削技术的应用1. 提高生产效率:高速切削技术在机械制造中广泛应用,能够显著提高生产效率。
通过提高切削速度和进给速度,生产厂商可以在较短时间内完成更多的加工任务,提高了机械加工的效率。
2. 提高加工精度:高速切削技术具有切削温度低、切削力小等特点,能够减小热变形和机械振动对工件加工精度的影响,提高了加工精度和表面质量。
3. 增加工件材料种类:高速切削技术在闪光电火花加工、超硬材料和薄壁工件高速切削等领域应用广泛。
高速切削通过较高的转速和进给速度,能够更好地适应不同材料的加工需求。
4. 降低加工成本:高速切削技术通过提高加工效率和降低切削力,可以减少切削时间和刀具磨损,从而降低了加工成本。
三、机械加工高速切削技术的挑战与发展高速切削技术在机械制造中的应用受到了一些挑战,如切削热问题、切削润滑和冷却问题等。
同时,随着高速切削技术的发展,一些新的切削方式如超声波切削、激光切削等也受到了广泛关注。
为了进一步推动高速切削技术的发展,需要加强研究,探索新的切削理论和方法。
高速切削的所罗门原理

一、高速切削的原始定义1931年,德国切削物理学家萨洛蒙(Carl.J.Salomon)博士提出了一个假设,即同年申请了德国专利(Machine with high cutting speeds)的所罗门原理:被加工材料都有一个临界切削速度V0,在切削速度达到临界速度之前,切削温度和刀具磨损随着切削速度增大而增大,当切削速度达到普通切削速度的5~6倍时,切削刃口的温度开始随切削速度增大而降低,刀具磨损随切削速度增大而减小。
切削塑性材料时,传统的加工方式为“重切削”,每一刀切削的排屑量都很大,即吃刀大,但进给速度低,切削力大。
实践证明随着切削速度的提高,切屑形态从带状、片状到碎屑状演化,所需单位切削力在初期呈上升趋势,而后急剧下降,这说明高速切削比常规切削轻快,两者的机理也不同。
二、现代高速切削技术的概念所罗门原理出发点是用传统刀具进行高速度切削,从而提高生产率。
到目前为止,其原理仍未被现代科学研究所证实。
但这一原理的成功应该不只局限于此。
高速切削技术是切削技术的重要发展方向之一,从现代科学技术的角度去确切定义高速切削,目前还没有取得一致,因为它是一个相对概念,不同的加工方式,不同的切削材料有着不同的高速切削速度和加工参数。
这里包含了高速软切削、高速硬切削、高速湿切削和高速干切削等等。
事实上,高速切削技术是一个非常庞大而复杂的系统工程,它涵盖了机床材料的研究及选用技术,机床结构设计和制造技术,高性能CNC控制系统、通讯系统,高速、高效冷却、高精度和大功率主轴系统,高精度快速进给系统,高性能刀具夹持系统,高性能刀具材料、刀具结构设计和制造技术,高效高精度测试测量技术,高速切削机理,高速切削工艺,适合高速加工的编程软件与编程策略等等诸多相关的硬件和软件技术。
只有在这些技术充分发展的基础上,建立起来的高速切削技术才具有真正的意义。
所以要发挥出高速切削的优越性能,必须是CAD/CAM系统、CNC控制系统、数据通讯、机床、刀具和工艺等技术的完美组合。
绿色技术在切削加工中的实施方案
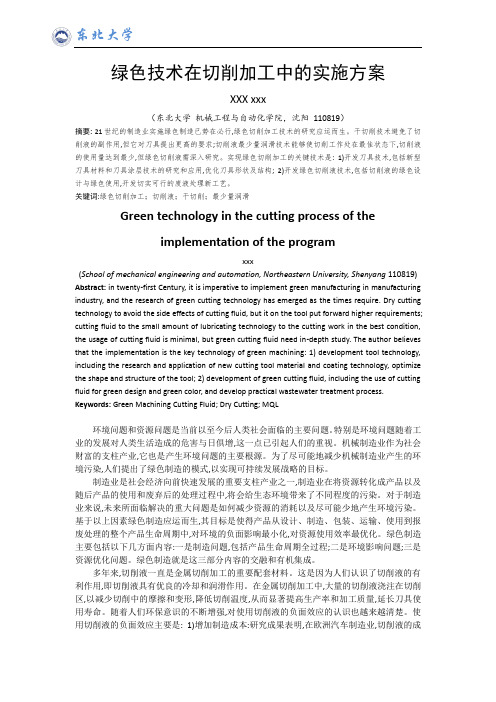
绿色技术在切削加工中的实施方案XXXxxx(东北大学机械工程与自动化学院,沈阳110819)摘要: 21世纪的制造业实施绿色制造已势在必行,绿色切削加工技术的研究应运而生。
干切削技术避免了切削液的副作用,但它对刀具提出更高的要求;切削液最少量润滑技术能够使切削工作处在最佳状态下,切削液的使用量达到最少,但绿色切削液需深入研究。
实现绿色切削加工的关键技术是: 1)开发刀具技术,包括新型刀具材料和刀具涂层技术的研究和应用,优化刀具形状及结构; 2)开发绿色切削液技术,包括切削液的绿色设计与绿色使用,开发切实可行的废液处理新工艺。
关键词:绿色切削加工;切削液;干切削;最少量润滑Green technology in the cutting process of theimplementation of the programxxx(School of mechanical engineering and automation, Northeastern University, Shenyang 110819) Abstract: in twenty-first Century, it is imperative to implement green manufacturing in manufacturing industry, and the research of green cutting technology has emerged as the times require. Dry cutting technology to avoid the side effects of cutting fluid, but it on the tool put forward higher requirements; cutting fluid to the small amount of lubricating technology to the cutting work in the best condition, the usage of cutting fluid is minimal, but green cutting fluid need in-depth study. The author believes that the implementation is the key technology of green machining: 1) development tool technology, including the research and application of new cutting tool material and coating technology, optimize the shape and structure of the tool; 2) development of green cutting fluid, including the use of cutting fluid for green design and green color, and develop practical wastewater treatment process. Keywords: Green MachiningCutting Fluid; Dry Cutting; MQL环境问题和资源问题是当前以至今后人类社会面临的主要问题。
主要的绿色切削工艺技术

主要的绿色切削工艺技术绿色切削工艺技术指的是在切削加工过程中,通过改进刀具、润滑剂、冷却剂、加工条件等手段,实现切削过程的高效、低能耗、环境友好和节能减排。
绿色切削工艺技术的发展旨在减少切削过程中的能源消耗和材料损耗,降低环境污染,提高加工效率和产品质量。
首先,绿色切削工艺技术在刀具的研发和使用方面积极探索。
切削工艺中,刀具是起到直接切削加工作用的关键工具,其性能直接影响到加工效率和加工质量。
因此,绿色切削工艺技术致力于改进刀具的刀具材料、刀具几何形状以及涂层技术等方面。
新材料的应用可以提高刀具的硬度、耐磨性和切削稳定性,从而延长刀具的使用寿命,减少切削过程中的刀具更换次数,降低能源消耗和材料损耗。
此外,绿色切削工艺技术还鼓励使用可再生材料和可回收材料制造刀具,以减少对环境的影响。
其次,在润滑剂和冷却剂的选择方面,绿色切削工艺技术提倡使用环境友好的润滑剂和冷却剂。
传统切削工艺中常使用的润滑剂和冷却剂通常含有有机溶剂和重金属等有害物质,对环境和人体健康造成一定的危害。
绿色切削工艺技术倡导使用水溶性润滑剂和冷却剂,避免有害物质的排放,减少污染物的产生。
此外,绿色切削工艺技术还可以通过改进润滑剂和冷却剂的使用方法,如微量喷雾、雾化和系统循环等,最大限度地利用和循环润滑剂和冷却剂,减少使用量和浪费,降低能源消耗和成本。
再次,在加工条件的控制方面,绿色切削工艺技术注重优化切削工艺参数,实现高效、精确的切削加工。
通过合理设置切削速度、进给速度和切削深度等参数,可以最大限度地减小切削力和切削温度,降低能量消耗和切削力对刀具的磨损,延长刀具的使用寿命。
同时,绿色切削工艺技术还注重加工过程中的监测和控制,通过实时监测切削过程中的刀具磨损和加工表面质量,及时调整切削参数,确保加工质量和效率。
总之,绿色切削工艺技术是切削加工领域的一项重要技术创新,旨在实现经济高效、低能耗、环保和可持续发展的目标。
随着技术的不断进步和应用的推广,绿色切削工艺技术将在制造业的发展中起到积极的推动作用,为构建绿色、智能的制造业新体系做出贡献。
绿色制造—高速干切削概述

绿色制造—高速干切削概述高速干切削是一种先进的切削加工技术,它在提高加工效率的同时,也有效地降低了环境污染和能源消耗。
本文将概述高速干切削技术的原理、应用领域以及对绿色制造的积极影响。
一、高速干切削的原理高速干切削是指在高速旋转的切削工具与工件接触时,不使用冷却液进行冷却和润滑的切削过程。
其原理是通过提高切削速度、降低加工温度和减少摩擦力来实现高效率的切削加工。
在高速干切削过程中,切削温度相对较低,切削力较小,从而减少了工具磨损和加工成本。
二、高速干切削的应用领域高速干切削技术广泛应用于机械制造、航空航天、汽车、电子、光学器件等领域。
例如,高速干切削技术在汽车制造中被用于发动机零部件的加工,可大幅提高生产效率和减少废液处理成本。
同时,在电子器件制造领域,高速干切削技术具备高精度和高表面质量等优势,被广泛应用于半导体芯片、光纤组件等的加工。
三、高速干切削对绿色制造的影响1. 节约能源:高速干切削不需要冷却液,大大减少了能源消耗。
与传统切削相比,高速干切削可节约能源30%以上,减少了对环境的负荷。
2. 降低环境污染:传统切削过程中,大量的冷却液被使用后会成为废液,对环境造成严重的污染。
而高速干切削技术无需冷却液,减少了废液的产生,降低了对水资源的消耗和水污染的风险。
3. 提高生产效率:高速干切削技术采用高速切削工具和高速传动设备,加工速度更快,提高了生产效率。
同时,由于无需处理废液等附加工序,工艺流程更加简化,进一步提高了生产效率。
4. 减少工具磨损:高速干切削的切削速度相对较高,与工件接触时间短,减少了工具磨损。
这可以延长工具的使用寿命,减少了资源消耗和废弃物的产生。
综上所述,高速干切削技术具有降低能源消耗、减少环境污染、提高生产效率和减少工具磨损的优势,为绿色制造的实践提供了重要的技术支持。
随着高速干切削技术的进一步发展和应用,相信将在制造业领域取得更加显著的绿色效益和可持续发展。
高速切削加工技术ppt课件.pptx

我国高速切削加工技术最早应用于轿车工业,二十世纪八十年 代后期,相继从德国、美国、法国、日本等国引进了多条具有先进 水平的轿车数控自动化生产线,如从德国引进的具有九十年代中期 水平的一汽大众捷达轿车和上海大众桑塔纳轿车自动生产线,其中 大量应用了高速切削加工技术。生产线所用刀具材料以超硬刀具为 主,依靠进口。
近年来,我国航天、航空、汽轮机、模具等制造行业引进了 大量加工中心和数控镗铣床,都不同程度地开始推广应用高速切 削加工技术,其中模具行业应用较多。
例如上海某模具厂,高速铣削高精度铝合金模具型腔,半精 铣采用主轴转速18000rpm,切削深度2mm,进给速度5m/min; 精铣采用20000rpm,切削深度0.2mm,进给速度8m/min,加工 周期为6h,质量完全满足客户要求。
➢ 高速切削已成为当今制造业中一项快速发展 的新技术,在工业发达国家,高速切削正成 为一种新的切削加工理念。
➢ 人们逐渐认识到高速切削是提高加工效率的 关键技术。
高速切削的特点
➢ 随切削速度提高,单位时间内材料切除率增加,切削加工时间减 少,切削效率提高3~5倍。加工成本可降低20%-40%。
➢ 在高速切削加工范围,随切削速度提高,切削力可减少30%以上, 减少工件变形。对大型框架件、刚性差的薄壁件和薄壁槽形零件 的高精度高效加工,高速铣削是目前最有效的加工方法。
高速切削的加工工艺方法
目前高速切削工艺主要在车削和铣削,各类高速切削机床 的发展将使高速切削工艺范围进一步扩大,从粗加工到精加工 ,从车削、铣削到镗削、钻削、拉削、铰削、攻丝、磨削等。
随着市场竞争的进一步加剧,世界各国的制造业都将更加积 极地应用高速切削技术完成高效高精度生产。
高速切削加工在国内的研究与应用
- 1、下载文档前请自行甄别文档内容的完整性,平台不提供额外的编辑、内容补充、找答案等附加服务。
- 2、"仅部分预览"的文档,不可在线预览部分如存在完整性等问题,可反馈申请退款(可完整预览的文档不适用该条件!)。
- 3、如文档侵犯您的权益,请联系客服反馈,我们会尽快为您处理(人工客服工作时间:9:00-18:30)。
高速切削---实现绿色切削的有效途径文章主要介绍了高速加工的概念、所使用的刀具、冷却系统,并阐述了如何通过高速切削来实现绿色切削。
高速切削的概念ISO1940标准中规定,主轴转速高于8000r/min称为高速切削加工。
但在现实中一般认为,主轴转速10000r/min以上的切削才可称之为高速切削。
针对不同的切削方式其特征又有所不同,如车削速度在500m/min以上可称为高速车削,铣削速度在300m/min以上可称为高速铣削,钻削速度在200m/min以上可称为高速钻削等。
高速切削的发展高速切削的概念最早由德国的Garl.J.Salomon博士于1931年提出,但由于当时的技术、设备情况的限制,没能进行实验。
随着技术的发展,实验条件逐步完善,西方发达国家特别是美国于20世纪60年代以后开始重视其发展,并进行了一系列实验,20世纪80年代以后特别是20世纪90年代更是研究得如火如荼,产品的品种日益增多,技术日益完善,宣传和服务更加到位。
我国直到20世纪90年代以后才有了比较成熟的产品,如宁夏“小巨人”开发的VTC动柱式立式加工中心(主轴转速10000r/min)、北京机床研究所于2003年研制成的μ10005V立式加工中心等。
高速切削与绿色环保的联系随着人们环保意识的增强及加入世贸组织后发达国家针对我国绿色壁垒的设置,客观上要求机械产品在制造时尽可能少地消耗能源和污染环境。
而机械切削(下简称切削)是机械制造中消耗能源和污染环境的直接原因,所以,人们有针对性地提出了绿色切削(绿色制造)的概念。
所谓绿色切削就是指消耗尽可能少的刀具材料、切削液、加工时间和电力,尽可能少地污染环境,来达到某种特定的切削目的的一种切削方式。
由于高速切削的特点决定了高速切削可以节省切削液、刀具材料、切削工时,从而节约了自然资源,减少了对环境的污染,提高了生产效率和产品质量,达到“绿色切削”的目的。
高速切削的特点1.切削力小、振动频率低切削形成的过程分为挤压塑性变形和撕裂两个阶段,工件受切削力和切削热影响而发生塑性变形主要在这个阶段。
由此可知:切削速度越高,塑性变形的时间越短使剪切变形区域越窄,剪切角越大,变形因子越小以及切屑流出速度越快(切屑中的热量占切削热的80%)、传入工件和刀具中的热量越小,所以高速切削可使切削变形机率平均降低30-40%以上,十分适合于刚性较差和薄壁零件的切削加工。
从动力学角度分析频率的形成可知,切削力的降低将减小由于切削力产生的振动(即强迫振动)的振幅。
转速的提高使切削系统的工作频率远离机床的低阶固有频率,避免共振的发生。
因此,高速切削可大大降低加工表面粗糙度,提高加工质量。
2.机床本身特征高速切削机床应用了目前最先进的技术,是集机、光、电、气、液压为一体、采用目前所已知的最适合机床的复合材料所制成的尖端技术产品。
所以高速切削机床除主轴转速高外,相对于普通数控机床,其自动化程度(又称智能化)更高、功率更大、切削材料硬度较高(可高速切削HRC50-54甚或HRC60的材料)、精度更高(达到0.001mm甚至0.0001mm)、切削和进给速度更高(是普通数控机床的几倍甚至几十倍);由于广泛采用伺服电机,其传动系统机械结构简化且传动可靠;采用复合材料或人造大理石为基座或工作台(如瑞士MIKRON的UCP600)使机床刚性得到显著提高,这些都使零件的尺寸精度得以极大提高。
3.使用先进的刀具由于高速切削的毛坯比较规则或经过预处理,而且机床刚性好、切削力小、振动小,所以其刀具破损失效的概率极小甚至可以忽略不记。
高速切削时主轴转速高、切屑流出速度很快、切削过程极短,发生粘结的可能性很小。
根据刀具磨损的几种形式分析,只有相变磨损、扩散磨损、氧化磨损、热裂磨损等,而这些均属于热磨损范畴,所以,决定高速切削刀具失效的因素主要是刀具材料的热性能,如熔点、耐热性、抗氧化性、高温力学性能和抗热冲击性能等,其次为刀具的几何角度。
目前常用的刀具材料有以下几种:(1)涂层硬质合金刀具涂层硬质合金刀具是60年代出现的新型刀具材料。
它是采用化学气象沉积法或其他方法在硬质合金或高速钢表面涂附一薄层(约5~10μm)耐磨的难熔金属化合物,可在一定程度上提高刀具的综合切削性能,在同样情况下其切削速度比普通硬质合金或高速钢刀具高40%左右,对比情况如图一所示:涂层材料有TiC、TiN、AL2O3等几种或两种及两种以上的复合使用。
以下将分别予以说明:·TiC涂层TiC涂层具有很高的硬度与耐磨性,抗氧化性也较好,切削时能形成氧化钛薄膜降低摩擦系数,减小刀具磨损,使切削速度提高40%以上,比较适合高速切削。
TiC涂层与钢的粘结温度高,表面晶粒很细,切削时很少产生积屑瘤,比较适合于高速精密车削。
缺点是线膨胀系数与基体差别较大,因此,高速车削或铣削硬材料、高温合金或带夹杂物工件时,涂层易崩裂。
·TiN涂层TiN涂层在高温时能形成氧化膜,与铁基材料摩擦系数较小,抗粘结性能好、有效的降低了摩擦力与切削温度,TiN涂层刀片抗月牙洼及后刀面磨损能力比TiC涂层刀片强,最适合切削钢与易粘刀的材料,使加工表面粗糙度减小,切削速度提高。
此外TiN涂层抗碎裂性与抗热震性能也较好,这很适合于高速切削。
但其与基体结合强度低于TiC涂层,且涂层厚时易剥落,一般用于高速车削。
·TiC-TiN复合涂层兼具两种涂层的优点,先涂TiC,再涂TiN使结合强度提高、摩擦力、切削力、切削温度降低,对高速切削中的粗、精加工都很好。
如株硬集团的CN15、CN25(精)、CN35(粗)等。
·TiC-AL2O3复合涂层先涂TiC再涂AL2O3,TiC使涂层粘结牢固,AL2O3使涂层具有陶瓷的耐磨性、良好的化学稳定性和抗氧化性。
该复合刀片能像陶瓷刀一样高速切削,同时又避免了陶瓷的脆性、易崩刃的特点,如株硬集团的CA15。
该涂层刀具极适合于高速切削,特别适合高速车削。
涂层刀具具有省贵重材料、易制造、使用时间长等特点,既符合环保的需要又为企业增加了经济效益,所以被广泛推荐使用。
(2)陶瓷刀具该材料以氧化铝为主要成分,在高温下烧结而成。
由于采用了新工艺使其纯度提高、晶粒细化,应用热压工艺、添加晶须等,克服了陶瓷的热冲击性差、强度与韧性低、脆性大的问题,能胜任难加工材料的高速切削,具有广阔的发展前景。
添加了碳化物(主要是TiC)后可提高抗热裂纹能力,可高速车削HRC60~62的淬硬工具钢、铬镍钼粉末冶金等“C”形屑塑性材料。
氮化硅陶瓷(以氮化硅为主要成分)刀具能对硬度同时,氮化硅陶瓷刀具的耐热性和抗高温氧化性特别好,即使在1200~1450切削温度时仍能保持一定的硬度和强度进行长时间切削。
在一定范围内高速车削时,切削温度的升高能改变工件材料的性能,提高陶瓷刀具的韧性,从而减少其破损,所以一般陶瓷刀具均采用干切削。
但陶瓷刀具对冲击和振动载荷比较敏感。
机床-工件-刀具工艺系统刚性弱是促使陶瓷刀具寿命降低或崩刃的主要原因。
所以,氮化硅陶瓷刀具只适用于高速切削。
(3)超硬刀具材料超硬刀具材料主要指人造金刚石(JR)和立方氮化硼(CBN)。
只使用于高速切削高温合金、热喷涂材料、硬质合金及其他难加工材料。
(4)选用合适的刀具几何角度根据切削情况,选择合适的刀具几何角度,可提高高速加工刀具耐用度及加工效率,如:氧化铝陶瓷刀具在干切削淬硬钢情况下美国Valenite公司推荐0.5x30°T形棱面,CBN刀具刃口采用斜面或倒圆及负倒角而不采用大倒棱等。
4.采用先进的冷却技术由于高速切削高速旋转的特点,若使用传统的冷却方法,冷却液很难达到冷却部位,起不到冷却与润滑的作用。
出于环保与节约的需要,低温气体冷却和MQL-最小油量润滑技术在高速切削中逐步得到了推广应用。
(1)低温气体冷却低温气体冷却技术就是采用液氮或冷气以高压直接喷涂于切削部位,起到冷却作用。
高速切削时的切削力为传统切削力和变频冲击力双重作用力的结合,而氮气下刀具与切屑及工件间更易产生TiN层,TiN具有减摩作用,铣削时,由于摩擦作用所产生的铣削力会减少,所以总切削力也随之下降,气体也更易到达切削部位,达到冷却目的,同时气体无污染且易得到,对环保更有利。
(2)MQL-最小油量润滑技术.MQL技术主要有气雾外部润滑和内部冷却两种,广泛应用于铸铁、钢、铝合金等的钻、铰、攻螺纹、深孔钻削以及高速车、铣等加工过程中。
气雾外部润滑是在0.5~0.6Mpa的压缩空气(用高压冷却泵产生)中添加少量高性能的润滑油(5-50mL/h),就像是把有限的少量润滑剂“涂到”切削位置上一样,使少量润滑剂得到最充分的利用。
与此同时,高压气体起到冷却和辅助断屑作用,以降低刀具温度,防止刀具冷焊。
如:德国福鸟(VOGEL)集中润滑系统的MQL微量润滑冷却系统采用(高压冷却泵)强制冷却,属内部冷却方式。
5.干式切削技术干式切削技术是随着陶瓷刀具的发展提出的,出与环保的考虑,完全不用切削液,采用辅助加热装置对工件表面局部加热(如激光加热、导电加热等)至一定温度,以改善材料的可加工性,降低切削力,有助于干式切削的实现。
但该技术对刀具的长时间耐热性(红硬性)提出了高要求,所以,目前只适用于在高温下可长时间保持强度、硬度的陶瓷刀具。
干式切削由于受目前工艺条件、工件材料和加工类型的影响,目前尚不是通用技术。
结语综合高速切削的特点,可以看出高速切削可以达到节约刀具材料和切削液,节省劳动力,节约自然资源,减少对环境的污染,是实现绿色切削的有效途径,被公认为21世纪制造业实现可持续发展的关键性技术之一。