价值流标准表 (2)
价值流程图(PPT课件)
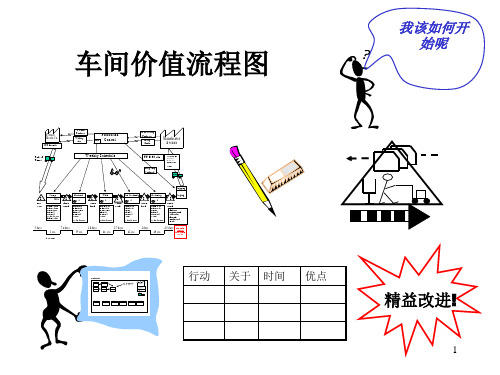
EPE = Time
BATCH = Pieces
Process Time Per Piece 每件工序时间(流程前置时间除以批量数量)………………………………………..…..…………….P…TP
= Time
Reject Rate废品率 (=产品因质量问题被拒的百分比)…………………………………..……..…….…………..
REJ
=%
Uptime 正常运行时间(工序运行的正常时间的百分比,除去休息及临时维修)………...…..…………
U/T
=%
Changeover Time 换件时间(从工件A转换到工件B的时间)….............................
C/O
= Time
Every Part Every_单件间隔____ (每一个部件流过工序的时间)………………………..….
▪未来图
标准化作业
拉动
拉动
FIFO
标准化作业
快速切换
19
第四步. 稳固各单元
▪精益商业系统工具 - 5S/可视化管理 - 标准化作业 - 减少偏差 - 全面生产性维护 - 快速切换
标准化作业
生产节 拍
4 32 1
标准化在
2 1 3 2 1 RM
制品
3 4 4 5 6 FG
5 67 8
工作顺序
20
第五步. 综合各单元
§由客户及混合模式
制造拉动的突破图
精益改进及突破
24
第二章–绘制当前状态图
价值流程图
客户
生产节拍 = 60 秒.
18, 400 件/月 -12,000 “左置” -6,400 “右置” 转运托架 = 20件 2班工作
【精益知识】价值流知识梳理,一看就懂!
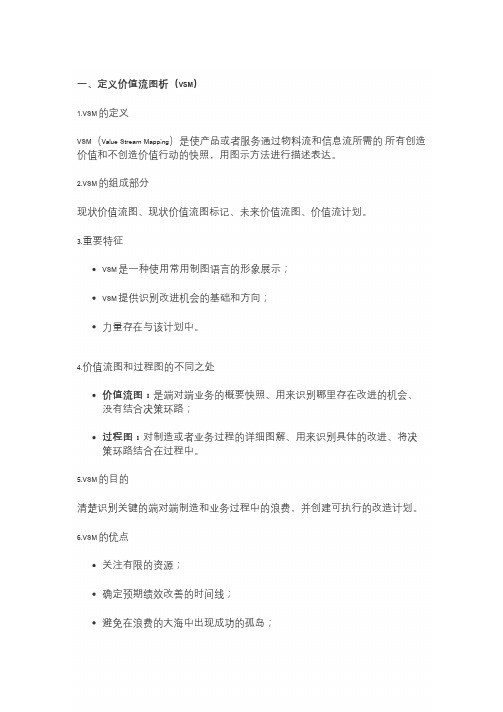
一、定义价值流图析(VSM)1.VSM的定义VSM(Value Stream Mapping)是使产品或者服务通过物料流和信息流所需的所有创造价值和不创造价值行动的快照,用图示方法进行描述表达。
2.VSM的组成部分现状价值流图、现状价值流图标记、未来价值流图、价值流计划。
3.重要特征VSM是一种使用常用制图语言的形象展示;VSM提供识别改进机会的基础和方向;力量存在与该计划中。
4.价值流图和过程图的不同之处价值流图:是端对端业务的概要快照、用来识别哪里存在改进的机会、没有结合决策环路;过程图:对制造或者业务过程的详细图解、用来识别具体的改进、将决策环路结合在过程中。
5.VSM的目的清楚识别关键的端对端制造和业务过程中的浪费,并创建可执行的改造计划。
6.VSM的优点关注有限的资源;确定预期绩效改善的时间线;避免在浪费的大海中出现成功的孤岛;使每个人都能对目前状态和未来远景有共同的了解。
7.什么时候使用VSM指出开始精益之旅的方向;执行由战略开发和关键业务必做事宜驱动的改进;获得端对端过程真正的跨职能理解。
8.价值流图析和战略的联系(图形表述)二、价值流图析过程1.VSM规划步骤2.选择产品族和服务族1)定义“价值流”:必须有所有的这些行动使产品或服务通过主要流程,从起始点到被顾客接收,该流程对于提供产品和服务来说必不可少。
2)识别价值流中的“价值对象”:A、单一实体或者信息对象,经过从起始点到顾客接收的价值流中所有的过程步骤;B、用来按图析沿价值流移动,并计算各生产过程的库存水平;C、用来展示其通过生产过程向顾客移动时如何创造价值流。
3)确定和选择产品族A、产品族:下游生产过程有相似加工步骤、使用共同设备的一组产品;B、产品族矩阵:一种数据分析工具,根据同样的生产过程和总需求百分比确定并将产品分入产品组;C、记录信息:产品族名称和描述、列出产品族中的SKU和描述、生产每周产品所需的过程次序、对每周产品的需求数量和频次;4)计算价值流的总需求产品组中所有产品的合计需求将被用来计算价值流的节拍时间;3.识别出“客户是谁”客户:其他使用产品的人(用户或者经销商)、下一工序、公司、老板。
精益思想的原则之二----价值流

精益思想的原则之二-------价值流当下,大家已经能够准确的概括总结出“精益思想”,并为管理者提供一种类似北极星那样可靠的行动指南,以克服批量生产方式造成的天天乱糟糟的局面。
那么精益思想可以概括为5个原则:精确地定义特定产品的价值;识别出每种产品的价值流;使价值不间断地流动;让客户从生产者方面拉动价值;永远追求尽善尽美。
下面主要先来说明原则之一:识别出每种产品的价值流。
从历史上来讲,管理人员最主要的注意力一直集中在总量管理上(工艺、部门和企业),同事监督者许多种产品。
然而,真正需要的是对具体产品和服务的整个价值流进行管理。
定义:价值流是使一件特定产品(不论是一件商品、一项服务,或者如日增多的情况,商品和服务两者的结合)通过任何一项商务活动的三项关键性管理任务时所需的一组特定活动。
内容:1.在从概念设想,通过细节设计与工程,到投产的全过程中解决问题。
2.在从接订单到指定详细进度再到送货的全过程中信息管理。
3.在从原材料制成最终产品,送到用户手中的物质转化。
以上这三个方面即是价值流的全方面内容。
举例说明:生产可乐---订购可乐---制成可乐的全过程。
这一过程为:铝矿→还原厂→冶炼厂→热轧厂→冷轧厂→制罐厂→制罐厂仓库→罐装厂→灌装厂仓库→商场仓库→商场柜台→用户→回收→再熔炼。
如果没有运用精益思想来管理整个生产流程的话,有可能看到具体产品的每一个步骤时,实物生产的价值流就非常值得人们深思了。
据统计,实际创造价值的时间(3天)在从铝土矿到回收使用的全部时间(319天)中比例极小。
价值流上99%的时间中,价值一点也没有流动:等待中的浪费。
其次,罐子和制罐用的铝被拿起、放下30次。
从客户观点来看,这样做不增加任何价值:搬运中的浪费。
同样,铝和罐子要经过14个储存地点和仓库,其中有些是很大的仓库;罐子装上、卸下货盘4次:库存中的浪费和不必要的程序。
最后,有24%从冶炼厂出来的耗能高、价格昂贵的铝与客户全无关系:残次品的浪费。
价值流程图-VSM

人员
VSM的图示 –其它
首先要选定你的产品,也就是研究的对象。为了操作的方便性,可以利用分组把产品分成产品家族。最佳的工具是使用产品家族矩阵。要建立产品家族矩阵之前,首先列出所有的产品在左编的栏位,并且在顶层列出加工流程步骤。找出共同的加工步骤,其中对应到不同的的产品可以分类成同一个家族。
产品
绘出现状图的7个步骤
使用铅笔、橡皮擦和便条纸绘制直接绘制在大白报纸上,避免使用电脑软体绘制可以使用下列颜色,使价值流图更容易阅读蓝色 –流程黄色 –存货或缓冲粉红色 – Master schedule / Production control主生产排成/生产控制单元绿色 –供应商及客户记得永远由客户开始绘制绘制完物流/流程步骤后,要留下空间画存货,图的下方还要留地方画各步骤的时间
价值图的改善
未来价值图
价值流图是一个团队改善活动,一个人绘制出来的价值流图通常是错的适合物料、讯息、生产的流程问题适合跨部门协调(多个部门之间的转接、协同合作有问题时)适合描述某一个具体的工作或办公区域,不适合描述复杂的工厂 ,如果太复杂,可以尝试切割流程,画在多张纸上不要尝试把所有东西都放在同一张纸上,记得80/20法则针对重点要解决的问题处理针对重要物料和办公管理过程绘制即可VSM不是万能的,但是VSM确实是一个能快速创造价值 的有力工具
加工流程
步骤一:辨识产品族
选定流程范围
跨公司
单个工厂(我们公司)
跨职能
过程层次
具体任务
通常由此开始
步骤二:绘出现状图
Customer
辨识产品及用户需求定义物料流定义物料处理流程及作业(从外部用户/客户内部供应商)第一次建议先画出从开始到结束的价值流加上资讯方块定义资讯流及作业,并加上资讯方块完成资料方块,并描述重要的活动状态定义库存点,并标注是(c)可控制或是(v)变动找出质量检核点及返修闭环,包括质量绩效、返修资源等给定前置作业时间,并了解时间变异的程度
福特培训教材_价值流培训标准

3)哪里可以运用连续流动流程?
4)为控制上游制程的生产,需要采用超市拉动系统? 5)在哪里来排定生产计划(步调控制的制程)? 6)如何均衡化配比? 7)释放量是多少? 8)哪些是必需的制程改善?(切换时间!)
4.1 什么是Acme的顾客需求速率?
库存
件数 左 件数 右
作业员
库存
材料天数
EPE
生产周期
C/T 开动率 = *实际时间 *可用时间
节拍时间
实际时间 * 可用时间 * = =
C/O
切换时间
可用时间 上班时间
-
停线时间 (吃饭时间
+
休息时间
+
交班时间)
2.3 再把物流标示到价值流图上
密契根钢 铁公司
公家路 装配厂
18400件/月 —12000―左” —6400―右” 每架=20件 2班
总结——价值流的起跑点
•
•
选择一个产品族
由你牵头领导价值流的绘制
•
从“Dock To Dock(码头到码头)”开 要考虑物流和信息流
始
•
2. 绘制现状图
清晰地将现行生产的情况,以物流和信息流的图示加以掌握和分析, 作为未来图的基础,一些建议:
•
依照实际的生产过程,自己将观察物流和信息流的资讯加以收集 和记录。 由发运点往前工程观察,这样可以知道如何与顾客连接。 千万不要使用档案数据,要自己测量,例如工时等。
公家路 装配厂 18400件/月 —12000―左” —6400―右” 每架=20件 2班
冲压 200T 4600左 2400右
C/T=1秒 C/O=1小时 开动率85% 27600秒 EPE=2周
价值流程图
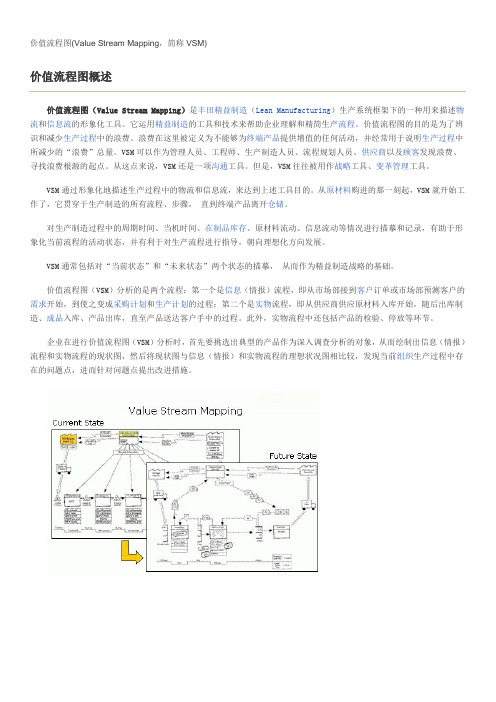
价值流程图(Value Stream Mapping,简称VSM)价值流程图概述价值流程图(Value Stream Mapping)是丰田精益制造(Lean Manufacturing)生产系统框架下的一种用来描述物流和信息流的形象化工具。
它运用精益制造的工具和技术来帮助企业理解和精简生产流程。
价值流程图的目的是为了辨识和减少生产过程中的浪费。
浪费在这里被定义为不能够为终端产品提供增值的任何活动,并经常用于说明生产过程中所减少的“浪费”总量。
VSM可以作为管理人员、工程师、生产制造人员、流程规划人员、供应商以及顾客发现浪费、寻找浪费根源的起点。
从这点来说,VSM还是一项沟通工具。
但是,VSM往往被用作战略工具、变革管理工具。
VSM通过形象化地描述生产过程中的物流和信息流,来达到上述工具目的。
从原材料购进的那一刻起,VSM就开始工作了,它贯穿于生产制造的所有流程、步骤,直到终端产品离开仓储。
对生产制造过程中的周期时间、当机时间、在制品库存、原材料流动、信息流动等情况进行描摹和记录,有助于形象化当前流程的活动状态,并有利于对生产流程进行指导,朝向理想化方向发展。
VSM通常包括对“当前状态”和“未来状态”两个状态的描摹,从而作为精益制造战略的基础。
价值流程图(VSM)分析的是两个流程:第一个是信息(情报)流程,即从市场部接到客户订单或市场部预测客户的需求开始,到使之变成采购计划和生产计划的过程;第二个是实物流程,即从供应商供应原材料入库开始,随后出库制造、成品入库、产品出库,直至产品送达客户手中的过程。
此外,实物流程中还包括产品的检验、停放等环节。
企业在进行价值流程图(VSM)分析时,首先要挑选出典型的产品作为深入调查分析的对象,从而绘制出信息(情报)流程和实物流程的现状图,然后将现状图与信息(情报)和实物流程的理想状况图相比较,发现当前组织生产过程中存在的问题点,进而针对问题点提出改进措施。
价值流程图的历史1980年代,丰田公司的首席工程师Taiichi Ohno与sensei Shigeo Shingo率先运用去除生产浪费的方法来获取竞争优势,他们的主要出发点是提高生产效率,而非提高产品质量。
价值流图训练

价值流图训练学习手册南方中集集装箱制造有限公司无论何时,只要有面向顾客的产品就有价值流挑战在于如何分析价值流本课程是参考Jim Womack and Dan Jones所著的《学习观察――增加价值、消除浪费的价值流图》教材基础上编撰的一套VSM训练课程。
目 录如何使用这本学习手册 第一章:介绍与入门 第二章:现状图练习1:现状第三章:精益价值流 第四章:理想状态图 练习2:理想状态第五章:实现理想状态 第六章:总结附件术语价值流图析图标参考读物目 录第一章:介绍与入门 第二章:现状图练习1:现状第三章:精益价值流 第四章:理想状态图 练习2:理想状态第五章:实现理想状态 第六章:总结训练介绍定义价值流定义价值流训练介绍绘图步骤产品系列价值流经理从“大门到大门”开始第一章 测验请在几种选择中圈出最佳答案1.价值流图着眼于:A.价值流中人的活动、物料流和信息流。
B.价值流中的物料流和信息流。
C.生产单元中逐条的操作步骤。
D.人们在设计和生产一件产品时的步骤。
2.产品系列矩阵用来:A.为所有产品和工序过程列一个清单。
B.确定哪些产品对于你的顾客是最重要的。
C.以相似的下游工序为基础,确认和划分产品系列。
D.用特殊的图标把图组分入不同系列。
3.价值流经理:A.是一个被任命改善价值流的职员。
B.是一个对理解和改进整个产品系列价值流负有责任的领导。
C.对价值流中的日常运作负责。
D.是一个向高级管理者汇报的第一线管理人员,他了解整个产品系列的价值流,并能推行改进。
4.在绘制整个产品系列价值流图的起步阶段推荐从哪个范围开始:A.公司范围B.在一个单独厂房中的从“大门到大门”的范围C.包含所有范围D.工序范围目 录第一章:介绍与入门 第二章:现状图练习1:现状第三章:精益价值流 第四章:理想状态图 练习2:理想状态第五章:实现理想状态 第六章:总结现状图阿克米冲压公司数据设定阿克米冲压公司为汽车装配厂生产多种不同的零部件。
价值流程图概述
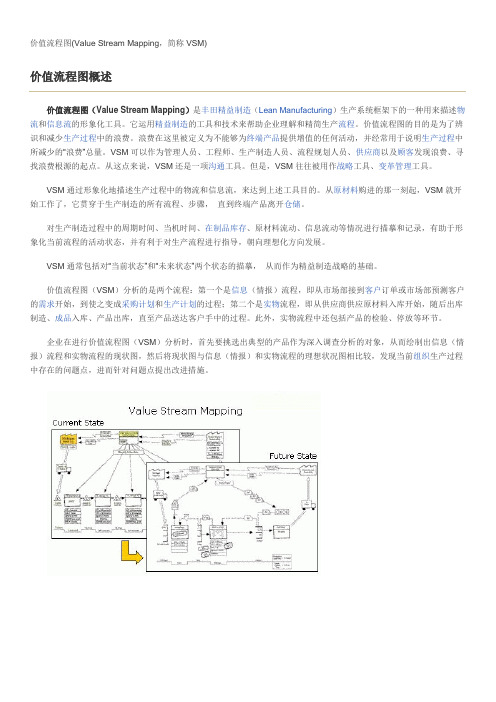
价值流程图(Value Stream Mapping,简称VSM)价值流程图概述价值流程图(Value Stream Mapping)是丰田精益制造(Lean Manufacturing)生产系统框架下的一种用来描述物流和信息流的形象化工具。
它运用精益制造的工具和技术来帮助企业理解和精简生产流程。
价值流程图的目的是为了辨识和减少生产过程中的浪费。
浪费在这里被定义为不能够为终端产品提供增值的任何活动,并经常用于说明生产过程中所减少的“浪费”总量。
VSM可以作为管理人员、工程师、生产制造人员、流程规划人员、供应商以及顾客发现浪费、寻找浪费根源的起点。
从这点来说,VSM还是一项沟通工具。
但是,VSM往往被用作战略工具、变革管理工具。
VSM通过形象化地描述生产过程中的物流和信息流,来达到上述工具目的。
从原材料购进的那一刻起,VSM就开始工作了,它贯穿于生产制造的所有流程、步骤,直到终端产品离开仓储。
对生产制造过程中的周期时间、当机时间、在制品库存、原材料流动、信息流动等情况进行描摹和记录,有助于形象化当前流程的活动状态,并有利于对生产流程进行指导,朝向理想化方向发展。
VSM通常包括对“当前状态”和“未来状态”两个状态的描摹,从而作为精益制造战略的基础。
价值流程图(VSM)分析的是两个流程:第一个是信息(情报)流程,即从市场部接到客户订单或市场部预测客户的需求开始,到使之变成采购计划和生产计划的过程;第二个是实物流程,即从供应商供应原材料入库开始,随后出库制造、成品入库、产品出库,直至产品送达客户手中的过程。
此外,实物流程中还包括产品的检验、停放等环节。
企业在进行价值流程图(VSM)分析时,首先要挑选出典型的产品作为深入调查分析的对象,从而绘制出信息(情报)流程和实物流程的现状图,然后将现状图与信息(情报)和实物流程的理想状况图相比较,发现当前组织生产过程中存在的问题点,进而针对问题点提出改进措施。
价值流程图的历史1980年代,丰田公司的首席工程师Taiichi Ohno与sensei Shigeo Shingo率先运用去除生产浪费的方法来获取竞争优势,他们的主要出发点是提高生产效率,而非提高产品质量。