热释电传感器英中文翻译(毕业设计、课程设计)
光电传感器(中英文对照版)

Photoelectric sensorKey word: photoelectric effect photoelectric element photoelectric sensor classification sensor application characteristics .Abstract: in the rapid development of science and technology in the modern society, mankind has into the rapidly changing information era, people in daily life, the production process, rely mainly on the detection of information technology by acquiring, screening and transmission, to achieve the brake control, automatic adjustment, at present our country has put detection techniques listed in one of the priority to the development of science and technology. Because of microelectronics technology, photoelectric semiconductor technology, optical fiber technology and grating technical development makes the application of the photoelectric sensor is growing. The sensor has simple structure, non-contact, high reliability, high precision, measurable parameters and quick response and more simple structure, form etc, and flexible in automatic detection technology, it has been widely applied in photoelectric effect as the theoretical basis, the device by photoelectric material composition. Text:First, theoretical foundation - photoelectric effectPhotoelectric effect generally have the photoelectric effect, optical effect, light born volts effect.The light shines in photoelectric material, according to the electronic absorption material surface energy, if absorbed energy large enough electronic electronic will overcome bound from material surface and enter the outside space, which changes photoelectron materials, this kind of phenomenon become the conductivity of the photoelectric effectAccording to Einstein's photoelectron effect, photon is moving particles, each photon energy for hv (v for light frequency, h for Planck's constant, h = 6.63 * 10-34 J/HZ), thus different frequency of photons have different energy, light, the higher the frequency, the photon energy is bigger. Assuming all the energy photons to photons, electronic energy will increase, increased energy part of the fetter, positive ions used to overcome another part of converted into electronic energy. According to the law of conservation of energy:Type, m for electronic quality, v for electronic escaping the velocity, A microelectronics the work done.From the type that will make the optoelectronic cathode surface escape the necessary conditions are h > A. Due to the different materials have different escaping, so reactive to each kind of cathode materials, incident light has a certain frequency is restricted, when the frequency of incident light under this frequency limit, no matter how the light intensity, won't produce photoelectron launch, this frequency limit A -h m 212νν=called "red limit". The corresponding wavelength for type, c for the speed of light, A reactive for escaping.When is the sun, its electronic energy, absorb the resistivity reduce conductive phenomenon called optical effects. It belongs to the photoelectric effect within. When light is, if in semiconductor electronic energy big with semiconductor of forbidden band width, the electronic energy from the valence band jump into the conduction band, form, and at the same time, the valence band electronic left the corresponding cavities. Electronics, cavitation remained in semiconductor, and participate in electric conductive outside formed under the current role.In addition to metal outer, most insulators and semiconductor have photoelectric effect, particularly remarkable, semiconductor optical effect according to the optoelectronics manufacturing incident light inherent frequency, when light resistance in light, its conductivity increases, resistance drops. The light intensity is strong, its value, if the smaller, its resistance to stop light back to the original value. Semiconductor produced by light illuminate the phenomenon is called light emf, born volts effect on the effect of photoelectric devices have made si-based ones, photoelectric diode, control thyristor and optical couplers, etc.Second, optoelectronic components and characteristicsAccording to the outside optoelectronics manufacturing optoelectronic devices have photoelectron, inflatable phototubes and photoelectric times once tube.1. Phototubes phototubes are various and typical products are vacuum phototubes and inflatable phototubes, light its appearance and structure as shown in figure 1 shows, made of cylindrical metal half cathodic K and is located in the wires cathodic axis of anode in A package of smoke into the vacuum, when incident light within glass shell in the cathode, illuminate A single photon took all of its energy transfer to the cathode materials A free electrons, so as to make the freedom electronic energy increase h. When electrons gain energy more than escape of cathode materials, it reactive A metal surface constraints can overcome escape, form electron emission. This kind of electronic called optoelectronics, optoelectronic escaping the metal surface for after initial kinetic energyPhototubes normal work, anode potential than the cathode, shown in figure 2. In one shot more than "red light frequency is premise, escape from the optoelectronic cathode surface by positive potential attracted the anode in photoelectric tube forming space, called the current stream. Then if light intensity increases, the number of photons bombarded the cathode multiplied, unit of time to launch photoelectron number are also increasing, photo-current greatens. In figure 2 shows circuit, current and resistance is the voltage drop across the only a function of light intensity relations, so as to achieve a photoelectric conversion. When the LTT optoelectronic cathode K, electronic escape from the cathode surface, and was the photoelectric anode is an electric current, power plants absorb deoxidization device in the load resistance - I, the voltagePhototubes photoelectric characteristics fig.03 shows, from the graph in flux knowable, not too big, photoelectric basic characteristics is a straight line.2. Photoelectric times had the sensitivity of vacuum tube due to low, so with people developed has magnified the photomultiplier tubes photo-current ability. Figure 4 is photomultiplier tube structure schematic drawing.图4光电倍增结构示意图From the graph can see photomultiplier tubes also have A cathode K and an anode A, and phototubes different is in its between anode and cathode set up several secondary emission electrodes, D1, D2 and D3... They called the first multiply electrode, the second multiply electrode,... Usually, double electrode for 10 ~ 15 levels. Photomultiplier tubes work between adjacent electrode, keeping a certain minimum, including the cathode potential potentials, each multiply electrode potential filtering increases, the anode potential supreme. When the incident light irradiation, cathodic K escape from the optoelectronic cathode multiplied by first accelerated, by high speed electrode D1 bombarded caused secondary electron emission, D1, an incident can generate multiple secondary electron photonics, D1 emit of secondary electron wasD1, D2 asked electric field acceleration, converged on D2 and again produce secondary electron emission... So gradually produce secondary electron emission, make electronic increased rapidly, these electronic finally arrived at the anode, form a larger anode current. If a n level, multiply electrodes at all levels for sigma, the multiplication of rate is the multiplication of photomultiplier tubes can be considered sigma n rate, therefore, photomultiplier tube has high sensitivity. In the output current is less than 1mA circumstances, it in a very wide photoelectric properties within the scope of the linear relationship with good. Photomultiplier tubes this characteristic, make it more for light measurement.3 and photoconductive resistance photoconductive resistance within the working principle is based on the photoelectric effect. In semiconductor photosensitive material ends of mount electrode lead, it contains transparent window sealed in the tube and shell element photoconductive resistance. Photoconductive resistance properties and parameters are:1) dark resistance photoconductive resistance at room temperature, total dark conditions stable resistance called dark resistance, at the current flow resistance is called dark current.2) light resistance photoconductive resistance at room temperature and certain lighting conditions stable resistance measured, right now is called light resistance of current flow resistance is called light current.4, volt-ampere characteristics of both ends photoconductive resistance added voltage and current flows through photoconductive resistance of the relationship between called volt-ampere characteristics shown, as shown in figure 5. From the graph, the approximate linear volt-ampere characteristics that use should be limited, but when the voltage ends photoconductive resistance, lest than shown dotted lines of power consumption area5, photoelectric characteristics photoconductive resistance between the poles, light when voltage fixed the relationship between with bright current photoelectric characteristics. Called Photoconductive resistance photoelectric characteristics is nonlinear, this is one of the major drawback of photoconductive resistance.6, spectral characteristics is not the same incident wavelength, the sensitivity of photoconductive resistance is different also. Incidence wavelength and photodetector the relationship between relative sensitivity called spectral characteristics. When used according to the wavelength range by metering, choose different material photoconductive resistance.7, response time by photoconductive resistance after photo-current need light, over a period of time (time) rise to reach its steady value. Similarly, in stop lightphoto-current also need, over a period of time (down time) to restore the its dark current, this is photoconductive resistance delay characteristics. Photoconductive resistance rise response time and falling response time about 10-1 ~ 10-3s, namely the frequency response is 10Hz ~ 1000Hz, visible photoconductive resistance cannot be used in demand quick response occasion, this is one of the main photoconductive resistance shortcomings.8 and temperature characteristic photoconductive resistance by temperature affects greatly, temperature rise, dark current increase, reduced sensitivity, which is another photoconductive resistance shortcomings.9, frequency characteristic frequency characteristics refers to an external voltage and incident light, strong must be photo-current I and incident light modulation frequency, the relationship between the f, photoelectric diode is the frequency characteristic of the photoelectric triode frequency characteristics, this is because of the photoelectrictriode shot "yankees there capacitance and carrier base-combed need time's sake. By using the principle of the photoelectric efficiency of optoelectronics manufacturing frequency characteristics of the worst, this is due to capture charge carriers and release charge need a certain time's sake.Three, photoelectric sensorsPhotoelectric sensor is through the light intensity changes into electrical signal changes to achieve control, its basic structure, it first figure 6 by measuring the change of change of converting the light signal, and then using photoelectric element further will light signals into electrical signal by photoelectric sensor general. Illuminant, optical path and optoelectronics. Three components of photoelectric detection method has high precision, fast response, non-contact wait for an advantage, but measurable parameters of simple structure, sensors, form flexible, therefore, photoelectric sensor in the test and control is widely used.By photoelectric sensor generally is composed of three parts, they are divided into: transmitter and receiver and detection circuit shown, as shown in figure 7, transmitter aimed at the target launch beam, the launch of the beam from semiconductor illuminant, general light emitting diode (LED), laser diode and infrared emission diode. Beam uninterrupted launch, or change the pulse width. Receivers have photoelectric diode, photoelectric triode, composed si-based ones. In front of the receiver, equipped with optical components such as lens and aperture, etc. In its back is detection circuit, it can filter out effective signal and the application of the signal. In addition, the structural components in photoelectric switch and launch plate and optical fiber, triangle reflex plate is solid structure launch device. It consists of small triangle cone of reflective materials, can make a beam accurately reflected back from plate, with practical significance. It can be in with the scope of optical axis 0 to 25, make beams change launch Angle from a root almost after launch line, passes reflection or from the rotating polygon.some basic returns.图7Photoelectric sensor is a kind of depend on is analyte and optoelectronics and light source, to achieve the relationship between the measured purpose, so the light source photoelectric sensor plays a very important role, photoelectric sensor power if a constant source, power is very important for design, the stability of the stability of power directly affect the accuracy of measurement, commonly used illuminant have the following kinds:1, leds is a change electric energy into light energy semiconductor devices. It has small volume, low power consumption, long life, fast response, the advantages of high mechanical strength, and can match and integrated circuits. Therefore, widely used in computer, instruments and automatic control equipment.2, silk light bulb that is one of the most commonly used illuminant, it has rich infrared light. If chosen optoelectronics, constitutes of infrared sensor sensitive colour filter can be added to the visible tungsten lamps, but only filter with its infrared does illuminant, such, which can effectively prevent other light interference.3, compared with ordinary light laser laser with energy concentration, directional good, frequency pure, coherence as well as good, is very ideal light sources.The light source, optical path and photoelectric device composition photoelectric sensor used in photoelectric detection, still must be equipped with appropriate measurement circuit. The photoelectric effect to the measurement circuit of photoelectric element of widerange caused changes needed to convert the voltage or current. Different photoelectric element, the measurement circuit required is not identical also. Several semiconductor introduces below optoelectronic devices commonly used measurement circuit.Semiconductor photoconductive resistance can through large current, be in so usually, need not equipped with amplifier. In the output power of demand is bigger, can use figure 8 shows circuit.Figure 9 (a) with temperature compensation given the photosensitive diode bridge type measuring circuit. When the incident light intensity slow change, the reverse resistance photosensitive diode is the slow change, the change of the temperature will cause the bridge output voltage, must compensate. Drift Picture a photosensitive diode as the test components, another into Windows, in neighboring bridge, the change of the temperature in the arms of the influence of two photosensitive diode, therefore, can eliminate the same output with temperature bridge road drift.Light activated triode incident light in work under low illumination, or hope to getbigger output power, also can match with amplifying circuit, as shown in figure 9 shows.Because even in the glare photosensitive batteries, maximum output voltage also only 0.6 V, still cannot make the next level 1 transistor have larger current output, so must add positive bias, as shown in figure 9 (a) below. In order to reduce the transistor circuit impedance variations, base si-based ones to reduce as much as possible without light, when the reverse bias inherit in parallel a resistor si-based ones at both ends. Or like figure 9 (b) as shown by the positive ge diode produces pressure drop and test the voltage produced when exposed to light, make silicon tube e stack, b the voltage between actuators than 0.7 V, and conduction work. This kind of circumstance also can use silicon light batteries, as shown in figure 10 (c) below. Semiconductor photoelectric element of photoelectric circuit can also use integrated operational amplifier. Silicon photosensitive diode can be obtained by integratingop-amp larger output amplitude, as shown in figure 11 (a) below. When light is produced, the optical output voltage in order to guarantee photosensitive diode isreverse biased, in its positive to add a load voltage. Figure 11. (b) give the photocell transform circuit, because the photoelectric si-based ones short-circuit current and illumination of a linear relationship between, so will it up in the op-amp is,inverse-phase input, using these two potential difference between the characteristicsof close to zero, can get better effect. In the picture shows conditions, the output voltageThe photoelectric element by flux the role of different made from the principle of optical measurement and control system is varied, press the photoelectric element (optical measurement and control system) output nature, namely, can be divided into second analog photoelectric sensor and pulse (switch) photoelectric sensor. Analog photoelectric sensors will be converted into continuous variation of the measure, it is measured optical with a single value relations between analog photoelectric sensor. According to be measured (objects) method detection of target can be divided into transmission (absorption) type, diffuse type, shading type (beam resistance gears) three categories. So-called transmission style means the object to be tested in optical path in constant light source, the light energy through things, part of being measured by absorption, transmitted light onto photoelectric element, such as measured liquid, gas transparency and photoelectric BiSeJi etc; speed.gratifying The so-called diffuse style means the constant light by the light onto the analyte from the object to be tested, and projected onto surfaces reflect on after optoelectronic devices, such as photoelectric colorimetric thermometer and light gauge etc; The so-called shading style means the when illuminant issued by the flux of light analyte covered by a part Jing optoelectronics, make projection on the flux change, change the object to be tested and extent of the position with the light path, such as vibration measurement, the size measurement; And in pulse photoelectric sensor in the sensors, photoelectric element acceptable optical signal is intermittent change, therefore photoelectric element in switch work of the state, the current output it is usually only two steady state of the signal, the pulse form used for photoelectric counting and photoelectric speed measurement and so on.And infrared photoelectric sensor classification and working way generally have thefollowing kinds:1, groove photoelectric sensor put a light emitter and a receiver in a slot face-to-face outfit are on opposite sides of the photoelectric groove. Lighter emits infrared light or visible light, and in unimpeded cases light receptors can receive light. But when tested objects from slot zhongtong obsolete, light occluded, photoelectric switches and action. Output a switch control signal, cut off or connect load current, thus completing a control movement. Groove switch is the overall of detection distance because general structure limits only a few centimeters.2, DuiShe type optoelectronic sensor if you put lighter and receive light is separated, can make the detection distance increase. By a lighter and an inbox light sensor into a photoelectric switch is called DuiShe separate photoelectric switches, referred to DuiShe photoelectric switch. Its detection distance can reach a few meters and even a dozen meters. When using light-emitting device and receive light device are installed in test object through the path of the sides, test object by blocking light path, accept light implement action output a switch control signals.3, reflex plate.it photoelectric switch light-emitting device type and receive light device into the same device inside, in its front pack a reflex plate.the using the reflection principle of complete photoelectric control function is called reflex plate.it reflex (or reflector reflex) photoelectric switch. Under normal circumstances, lighter the light reflected by reflex plate.it is received by accept light; Once the light path be test object to block, accept light, the light is not receive photoelectric switch is action, output a switch control signals.4, diffusion reflective photoelectric switches its detection head with a lighter and also an inbox light ware, but no reflex plate.it ahead. Normally lighter for the light collect light is not found. When test object by blocking the light, and the light reflected light, receive part implement received light signals, output a switch signals.Four, I'm the idea of photoelectric sensorWith the development of science and technology people on measuring accuracy had the higher request, this has prompted the pace with The Times photoelectric sensor have updated, improve the main means photoelectric sensor performance is the application of new materials, new technology manufacturing performance is more superior photoelectric element. For example, today the prototype of the photoelectric sensor is a small metal cylindrical equipment, with a calibration lens, transmitter into receiver focused light, the receiver out of cable to the device got a vacuum tube amplifiers in metal cylinder on the incandescent light bulb inside a small as the light source a strong incandescent lamp sensor. Due to the sensor various defects existing in the fields, gradually faded. To appear, because of it of fiber of excellent performance, then appeared with sensors supporting the use of optical passive components, another fiber without any interference of electromagnetic signal, and can make the sensor of the electronic components and other electrical disturbance in isolation. Have a piece of plastic optical fiber core or glass light core, light outside a metallic core skins and bread this layer metal cortical density lower than light core, so low, the beam refraction in the two materials according to the border (incident Anglewithin a certain range, reflected), is all. Based on optical principle, all beams can be made by optical fiber to transmission. Two incident beam Angle in an Angle (along the fiber length direction within) by multiple reflections from the other end after injection, another incident angles than accept the incident light in metal skin, loss. This accept Angle within the biggest incident Angle than two times, this is because fiber slightly larger from air into density larger fiber materials hitting may have a slight refraction. In light of the optical fiber transmission from inside the influence of fiber bending (whether more than bending radius minimal bending radius). Most optical fiber is flexible, easy to install in the narrow space. Photoelectric sensor is a kind of non-contact measurement small electronic measurement equipment, rely on detect its receives the light intensity change, to achieve measurement purposes, andit's also a vulnerable to external disturbance and lose the measurement accuracy of the device. When be being designed so besides the choice optoelectronic components, still must set GSCC signal and temperature compensating measures used to weaken or eliminate the impact of these factors.Photoelectric sensor must pass a light modulation, like radio waves of light modulation of sends and receives, the radio to a station, can ignore other radio signal sensors without modulation long-focal-length only through the use of mechanical shielded, scenes that receiver transmitter only can receive the emission of light, can make its energy becomes very high. In contrast, through modulation transceivers can ignore ambient light, only to own light or with the same modulation frequencies of light without modulation response. The sensor used to test the infrared rays or around the radiation, if just baked red bottle, in this application situation if use other sensor, may be incorrect actions.Photoelectric sensor due to non-contact, high reliability, etc, and to change in measurement, damage the object to be testedSo since its invention in fields since play a significant role, at present it has been widely used in measuring mechanical quantity, thermal quantity, weight, intelligent vehicle system into etc. Now it in power system automatically grid device plays a very important role, because generator input power grid operation often USES accurate with law, must meet: three-phase line sequence is consistent, frequency, phase agree unanimously, voltage amplitude equal, one of the conditions in system design has been satisfied, after three conditions must also meet to grid, of course, artificially grid is more difficult, photoelectric grid is easier.The development of times, science and technology in the update, photoelectric sensor types are increasing and application domain more and more widely, such as a recent kind of infrared already in intelligent vehicle electrical sensors in to the application, one of which had based on infrared sensor is the core of intelligent vehicle, reflective type infrared sensor using reflex infrared sensor design path detection module and speed monitoring module; Another method based on infrared sensor using the car tracing is to collect infrared sensor data.Photoelectric sensor has cannot be replaced by other sensors superiority, so it development foreground is very good, the application will also become more widespread.光电传感器关键字:光电效应 光电元件 光电特性 传感器分类 传感器应用 摘要:在科学技术高速发展的现代社会中,人类已经入瞬息万变的信息时代,人们在日常生活,生产过程中,主要依靠检测技术对信息经获取、筛选和传输,来实现制动控制,自动调节,目前我国已将检测技术列入优先发展的科学技术之一。
热释电传感器课程设计总结报告(1)

热释电传感器课程设计总结报告(1)
热释电传感器课程设计总结报告
一、课程目标
本课程旨在使学生了解热释电传感器的基本原理、特性、应用和设计方法,培养学生分析和解决实际问题的能力,提高学生的自主学习和实践能力。
二、教学内容
本课程主要包括以下内容:
1. 热释电效应的基本原理和实验验证。
2. 热释电传感器的结构和工作原理。
3. 热释电传感器的特性和参数。
4. 热释电传感器的应用及其优缺点。
5. 热释电传感器的设计方法和实验方案。
6. 热释电传感器的参数测试和分析。
三、教学方法
本课程采用理论讲授、实验演示、课堂讨论、实验报告等教学方法相结合,旨在帮助学生理论与实践相结合,掌握热释电传感器的基本知识和设计方法。
四、教学效果
通过本课程的学习,学生深入了解了热释电传感器的原理、特性和应用,掌握了热释电传感器的设计方法和实验方案,具备了一定的独立分析和解决实际问题的能力。
在实验室实践中,他们积极思考,认真实践,成功设计并测试出热释电传感器,获得了较好的实验结果。
最终,学生通过实验报告的撰写,深化了热释电传感器的理解,同时提
高了他们的分析、表达和写作能力。
五、改进意见
在教学过程中,应更多地引导学生参与实验设计和实践操作,使学生掌握更多的实际技能。
同时,在考核方面,可以增加对学生现场操作和技能演示的要求,以更好地评估其实际操作和技能水平。
毕业设计英文翻译----智能热能表控制器

外文资料与中文翻译外文资料:Intelligent thermal energy meter controllerAbstractA microcontroller based, thermal energy meter cum controller (TEMC) suitable for solar thermal systems has been developed. It monitors solar radiation, ambient temperature, fluid flow rate, and temperature of fluid at various locations of the system and computes the energy transfer rate. It also controls the operation of the fluid-circulating pump depending on the temperature difference across the solar collector field. The accuracy of energy measurement is ±1.5%. The instrument has been tested in a solar water heating system. Its operation became automatic with savings in electrical energy consumption of pump by 30% on cloudy days.1 IntroductionSolar water heating systems find wide applications in industry to conserve fossil fuel like oil, coal etc. They employ motor driven pumps for circulating water with on-off controllers and calls for automatic operation. Reliability and performance of the system depend on the instrumentation and controls employed. Multi-channel temperature recorders, flow meters, thermal energy meters are the essential instruments for monitoring and evaluating the performance of these systems. A differential temperature controller (DTC) is required in a solar water heating system for an automatic and efficient operation of the system. To meet all these requirements, a microcontroller based instrument was developed. Shoji Kusui and Tetsuo Nagai [1] developed an electronic heat meter for measuring thermal energy using thermistors as temperature sensors and turbine flow meter as flow sensor.2 Instrument detailsThe block diagram of the microcontroller (Intel 80C31) based thermal energy meter cum controller is shown in Fig. 1. RTD (PT100, 4-wire) sensors are used for the temperature measurement of water at the collector field inlet, outlet and in the tank with appropriate signal conditioners designed with low-drift operational amplifiers. A precision semiconductor temperature sensor (LM335) is used for ambient temperature measurement. A pyranometer, having an output voltage of 8.33 mV/kW/m2, is used for measuring the incident solar radiation. To monitor the circulating fluid pressure, a sensor with 4–20 mA output is used. This output is converted into voltage using an I-V converter. All these output signals are fed to an 8-channel analog multiplexer (CD4051). Its output is fed to a dual-slope 12-bit A/D converter (ICL7109). It is controlled by the microcontroller through the Programmable Peripheral Interface (PPI-82C55).Fig. 1. Block diagram of thermal energy meter cum controller.A flow sensor (turbine type) is used with a signal conditioner to measure the flow rate. Its output is fed to the counter input of the microcontroller. It is programmed to monitor all the multiplexed signals every minute, compute the temperature difference, energy transfer rate and integrated energy. A real-time clock with MM58167 is interfaced to the microcontroller to time-stamp the logged data. An analog output (0–2 V) is provided using D/A converter (DAC-08) to plot both the measured and computed parameters.A 4×4 matrix keyboard is interfaced to the microcontroller to enter the parameters like specific heat of liquid, data log rate etc. An alphanumeric LCD display (24-character) is also interfaced with the microcontroller to display the measured variables. The serial communication port of the microcontroller is fed to the serial line driver and receiver (MAX232). It enables the instrument to interface with thecomputer for down-loading the logged data. A battery-backed static memory of 56K bytes is provided to store the measured parameters. Besides data logging, the instrument serves as a DTC. This has been achieved by interfacing a relay to the PPI. The system software is developed to accept the differential temperature set points (ΔT on and ΔT off) from the keyboard. An algorithm suitable for on-off control having two set-points is implemented to control the relays.3 Instrument calibrationThe amount of energy transferred (Q) is :Where = mass flows rate of liquid kg/s ; V = volumetric flow rate (l/h) ; ρ = density of water (kg/l) ; Cp = specific heat (kJ/kg°C); and ΔT = temperature difference between hot and cold (°C).The accuracy in energy measurement depends on the measurement accuracy of individual parameters. Temperature measurement accuracy depends on the initial error in the sensor and the error introduced due to temperature drifts in the signal conditioners and the A/D converter. The temperature sensor is immersed in a constant temperature bath (HAAKE Bath-K, German), whose temperature can be varied in steps of 0.1°C. A mercury glass thermometer (ARNO AMARELL, Germany) with a resolution of 0.05°C is also placed along with PT100 sensor in the bath. This is compared with the instrument readings. The accuracy of the instrument in temperature measurement is ±0.1°C. Hence, the accuracy in differential temperature measurement is ±0.2°C.The flow sensor having a maximum flow rate of 1250 l/h is used for flow measurement. It is calibrated by fixing it in the upstream of a pipeline of length 8 m. The sensor output is connected to a digital frequency counter to monitor the number of pulses generated with different flow rates. Water collected at the sensor outlet over a period is used for estimating the flow rate. The K-factor of the sensor is 3975 pulses/l. The uncertainty in flow measurement is ±0.25% at 675 l/h. Uncertainties in density and specific heat of water are ±0.006 kg/l and ±0.011 kJ/kg°C respectively.Maximum amount of energy collection (Q) = 675×0.98×4.184×15/3600 = 11.53kW.Uncertainty in energy measurementωq/Q= [(ωv/V)2+ (ωρ/ρ)2+ (ωcp/Cp)2+(ωt/T )2]1/2.Inaccuracy in electronic circuitry is ±0.03 kW.The net inaccuracy in energy measurement is ±1.5%4 Field testThe instrument is incorporated in a solar water heating system as shown in Fig. 2. It consists of five solar flat plate collectors having an absorber area of 1.6 m2 each. The absorber is a fin and tube extruded from aluminium and painted with matt black paint. The collectors are mounted on a rigid frame facing south at an angle equal to the latitude of Bangalore (13°N). They are arranged in parallel configuration and connected to a thermally insulated 500 l capacity storage tank. A 0.25 hp pump is used for circulating the water through the collector field. All the pipelines are thermally insulated. The temperature sensors and the flow sensor are incorporated in the system as shown in Fig. 2. The data on solar radiation, ambient temperature, water flow rate, solar collector inlet and outlet temperatures and the system heat output are monitored at regular intervals.Fig. 2. Solar water heating system with thermal energy meter cum controller.The performance of the solar water heating system with TEMC on a partial cloudy day is shown in Fig. 3. It is observed that DTC switched OFF the pump around 14:40 h as there is no further energy gain by the collector field. This in turn reduced the heat losses from the collector to ambient. Experiments are conducted with and without DTC on both sunny and cloudy days. The DTC operated system shows the savings in electrical energy by 30% on a partial cloudy day and 8% on a sunny day. The variation in system output with and without DTC is around 3%. Thus the controller has not only served as an energy conservation device, but also switches ON/OFF the system automatically depending on the availability ofsolar radiation. The collector field output (shown in Fig. 3) is calculated by measuring the fluid flow rate using volumetric method and the temperature difference with another pair of standard thermometers. It is 16.86 kWh. It is compared with the instrument reading 17.18 kWh. Thus, the deviation is 1.9%. Fig. 3 shows that the solar collector field efficiency is 54% when the incident solar irradiation is 31.75 kWh.Fig. 3. Performance of SWH system with TEMC on a partial cloudy day.5 Concluding remarksTEMC is used as on-line instrument in solar water heating systems for the measurement of thermal energy, temperature, flow rate with simultaneous control on the operation of the pump to save electrical energy and enhance the thermal energy collection. Since several options are provided in the instrument, it can be used for monitoring the energy transfer rate in other thermal systems.AcknowledgementsThe authors are thankful to Department of Science and Technology, Govt. of India for providing the financial assistance to carry out the above work.References1. Shoji Kusui, Tetsuo Nagai. An electronic integrating heat meter. IEEE Trans. on Instrumentation and Measurement, 1990;39(5):785-789.中文翻译:智能热能表控制器摘要适用于太阳能热系统的单片机热能表控制器(TEMC)已经研制成功。
多功能热释电人体感应的设计制作——毕业论文或毕业设计说明书

多功能热释电人体感应的设计制作——毕业论文或毕业设计说明书多功能热释电人体感应的设计制作毕业论文或毕业设计说明书系部: 电子与通信工程系学生姓名: 刘冬梅专业班级: 通信11C3学号: 112231313指导教师: 蒋爱如2014年3月15日摘要由于日益变好的生活的生活现状,人们开始对一些现实社会的核心发展动力-科技开始了真正的追求,随着科技的水平的发展,生活中所用到的产品也越来越趋近于智能化,人性化。
可是,大多数的科技产品的出价却不是每个人都可以接受的,所以一些日常生活中很有需求的产品却不能得到普及化的使用程度,本课题将引进一种价格低廉,1方便推广使用的技术热释电红外传感器,它不仅价格低廉,而且安装和使用都很方便,这是一项真正的符合这个高速发展的社会的产品,这是平常人都能够享受的起的科技发展带来的产品,享受不到科技,再发达,也是惘然。
所以,这项技术有它的优势和发展空间。
热释电红外传感制作本身就不贵,也易购买,它不仅价格低,而且制作简单,且性能很稳定,不会轻易的被外界干扰。
你可以把它安装在通往客厅的过道里,它就变成一套兼备防盗和智能开关的双作用工具。
这套系统主要分为硬件部分和软件部分两大块,硬件主要采用:发光二极管显示模块、单片机模块、报警和照明模块、红外探头模块等。
本次处理器我决定采用51系列单片机STC89C52,程序使用C语言编写关键字:热释电红外传感器、STC89C52、红外线ABSTRACTDue to the rapid progress of economic development , the people's living standards improve, people began to force some of the core development of social reality - Technology started a real quest, with the level of development of science and technology, life products are used by more tends to be more2intelligent and humane. However, the prices of most technology products has discouraged a lot of people still make great demands ofdaily life products but can not get the degree of popularity of the use, the subject will introduce an inexpensive, easy to use thermal diffusion of technology pyroelectric infrared sensors, it is not only inexpensive, but also very easy to install and use, it is a real product in line with the rapid development of society, which is the ordinary people are able to enjoy from technological development to bringproducts not enjoy technology, then developed, also disconsolate. Therefore, this technique has its advantages and development space.Pyroelectric infrared sensor production cost is very low, it is easy to buy these devices, it is not only low prices, but making simple, and the performance is very stable, not easily to be outside interference. You can install it in the hallway leading to the living room, it becomes both a security and intelligent switch double-acting tools. This system consists of hardware and softwarecomponents into two blocks, the main use of the hardware: LEDdisplay module, microcontroller module, alarm and lighting module, infrared sensor module.The processor I decided to use 51 series STC89C52, using C language program.Keywords : pyroelectric infrared sensor , STC89C52, infrared目录一、引言 ..................................................................... . (4)二、方案设计 ..................................................................... . (4)(一)系统设计简介;..................................................................... (5)(二)总体设计框图 ..................................................................... . (5)三、硬件电路设计 ..................................................................... (7)3(一)总原理图 ..................................................................... .. (7)(二)PCB 图...................................................................... (7)(三)红外感应部分 ..................................................................... . (7)1、电源模块...................................................................... (8)2、热释电传感器 ..................................................................... . (8)3、菲涅耳透镜 ..................................................................... . (8)4、BISS0001芯片简介...................................................................... (9)5、信号采集处理模块...................................................................... .. (10)(四)单片机部分 ..................................................................... (11)1. STC89C52单片机简介 ..................................................................... . (11)2. 单片机最小系统 ..................................................................... (12)3.按键控制电路 ..................................................................... .. (12)4.指示灯和报警电路 ..................................................................... ......................... 13 四、软件的程序实现 ..................................................................... (13)(一)主程序工作流程图 ..................................................................... . (13)(二) 报警判断程序(附录一) .................................................................... .. (14)五、系统调试 ..................................................................... .. (14)(一) 硬件调试...................................................................... . (14)(二)软件调试 ..................................................................... (15)1. Keil编译器软件简介 ..................................................................... .. (15)2. 使用Keil软件建立一个Project................................................................. (16)六、总结评价 ..................................................................... .................................................. 21 七、致谢 ..................................................................... (21)八、参考文献 ..................................................................... .................................................. 21 九、附录 ..................................................................... (22)(一)报警判断程序 ..................................................................... ........................................... 22 (二)实物图 ..................................................................... .................................................. 23 (三)程序源代码 ..................................................................... . (23)一、引言随着计算机及网络技术的快速发展,在一切讲究高效率的今天,生活环境的建设也离不开信息化的建设。
电容式传感器中英文翻译资料毕业设计用
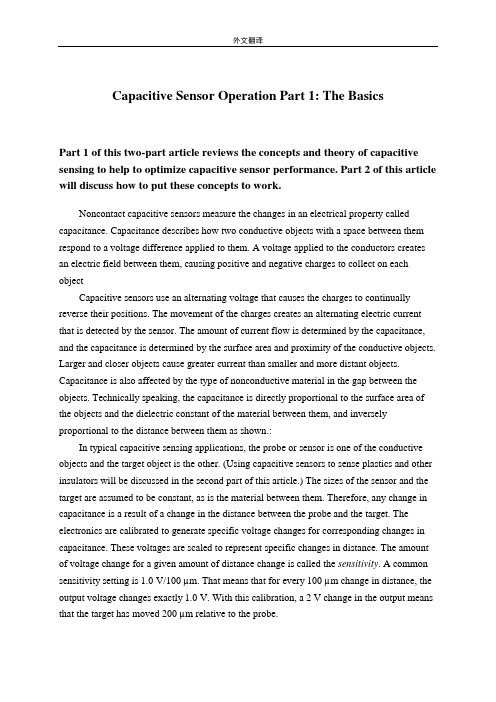
Capacitive Sensor Operation Part 1: The BasicsPart 1 of this two-part article reviews the concepts and theory of capacitive sensing to help to optimize capacitive sensor performance. Part 2 of this article will discuss how to put these concepts to work.Noncontact capacitive sensors measure the changes in an electrical property called capacitance. Capacitance describes how two conductive objects with a space between them respond to a voltage difference applied to them. A voltage applied to the conductors creates an electric field between them, causing positive and negative charges to collect on each objectCapacitive sensors use an alternating voltage that causes the charges to continually reverse their positions. The movement of the charges creates an alternating electric current that is detected by the sensor. The amount of current flow is determined by the capacitance, and the capacitance is determined by the surface area and proximity of the conductive objects. Larger and closer objects cause greater current than smaller and more distant objects. Capacitance is also affected by the type of nonconductive material in the gap between the objects. Technically speaking, the capacitance is directly proportional to the surface area of the objects and the dielectric constant of the material between them, and inversely proportional to the distance between them as shown.:In typical capacitive sensing applications, the probe or sensor is one of the conductive objects and the target object is the other. (Using capacitive sensors to sense plastics and other insulators will be discussed in the second part of this article.) The sizes of the sensor and the target are assumed to be constant, as is the material between them. Therefore, any change in capacitance is a result of a change in the distance between the probe and the target. The electronics are calibrated to generate specific voltage changes for corresponding changes in capacitance. These voltages are scaled to represent specific changes in distance. The amount of voltage change for a given amount of distance change is called the sensitivity. A common sensitivity setting is 1.0 V/100 µm. That means that for every 100 µm change in distance, the output voltage changes exactly 1.0 V. With this calibration, a 2 V change in the output means that the target has moved 200 µm relative to the probe.Focusing the Electric FieldWhen a voltage is applied to a conductor, the electric field emanates from every surface. In a capacitive sensor, the sensing voltage is applied to the sensing area of the probe. For accurate measurements, the electric field from the sensing area needs to be contained within the space between the probe and the target. If the electric field is allowed to spread to other items—or other areas on the target—then a change in the position of the other item will be measured as a change in the position of the target. A technique called "guarding" is used to prevent this from happening. To create a guard, the back and sides of the sensing area are surrounded by another conductor that is kept at the same voltage as the sensing area itself. When the voltage is applied to the sensing area, a separate circuit applies the exact same voltage to the guard. Because there is no difference in voltage between the sensing area and the guard, there is no electric field between them. Any other conductors beside or behind the probe form an electric field with the guard instead of with the sensing area. Only the unguarded front of the sensing area is allowed to form an electric field with the target.DefinitionsSensitivity indicates how much the output voltage changes as a result of a change in the gap between the target and the probe. A common sensitivity is 1 V/0.1 mm. This means that for every 0.1 mm of change in the gap, the output voltage will change 1 V. When the output voltage is plotted against the gap size, the slope of the line is the sensitivity.A system's sensitivity is set during calibration. When sensitivity deviates from the ideal value this is called sensitivity error, gain error, or scaling error. Since sensitivity is the slope of a line, sensitivity error is usually presented as a percentage of slope, a comparison of the ideal slope with the actual slope.Offset error occurs when a constant value is added to the output voltage of the system. Capacitive gauging systems are usually "zeroed" during setup, eliminating any offset deviations from the original calibration. However, should the offset error change after the system is zeroed, error will be introduced into the measurement. Temperature change is the primary factor in offset error.Sensitivity can vary slightly between any two points of data. The accumulated effect of this variation is called linearity erro. The linearity specification is the measurement of how far the output varies from a straight line.To calculate the linearity error, calibration data are compared to the straight line that would best fit the points. This straight reference line is calculated from the calibration data using least squares fitting. The amount of error at the point on the calibration line furthest away from this ideal line is the linearity error. Linearity error is usually expressed in terms ofpercent of full scale (%/F.S.). If the error at the worst point is 0.001 mm and the full scale range of the calibration is 1 mm, the linearity error will be 0.1%.Note that linearity error does not account for errors in sensitivity. It is only a measure of the straightness of the line rather than the slope of the line. A system with gross sensitivity errors can still be very linear.Error band accounts for the combination of linearity and sensitivity errors. It is the measurement of the worst-case absolute error in the calibrated range. The error band is calculated by comparing the output voltages at specific gaps to their expected value. The worst-case error from this comparison is listed as the system's error band. In Figure 7, the worst-case error occurs for a 0.50 mm gap and the error band (in bold) is –0.010.Gap (mm)Expected Value (VDC)Actual Value VDC)Error (mm) 0.50 –10.000 –9.800 –0.0100.75 –5.000 –4.900 –0.0051.00 0.000 0.000 0.0001.25 5.000 5.000 0.0001.50 10.000 10.100 0.005Figure 7. Error valuesBandwidth is defined as the frequency at which the output falls to –3 dB, a frequency that is also called the cutoff frequency. A –3 dB drop in the signal level is an approximately 30% decrease. With a 15 kHz bandwidth, a change of ±1 V at low frequency will only produce a ±0.7 V change at 15 kHz. Wide-bandwidth sensors can sense high-frequency motion and provide fast-responding outputs to maximize the phase margin when used in servo-control feedback systems; however, lower-bandwidth sensors will have reduced output noise which means higher resolution. Some sensors provide selectable bandwidth to maximize either resolution or response time.Resolution is defined as the smallest reliable measurement that a system can make. The resolution of a measurement system must be better than the final accuracy the measurement requires. If you need to know a measurement within 0.02 µm, then the resolution of the measurement system must be better than 0.02 µm.The primary determining factor of resolution is electrical noise. Electrical noise appears in the output voltage causing small instantaneous errors in the output. Even when theprobe/target gap is perfectly constant, the output voltage of the driver has some small butmeasurable amount of noise that would seem to indicate that the gap is changing. This noise is inherent in electronic components and can be minimized, but never eliminated.If a driver has an output noise of 0.002 V with a sensitivity of 10 V/1 mm, then it has an output noise of 0.000,2 mm (0.2 µm). This means that at any instant in time, the output could have an error of 0.2 µm.The amount of noise in the output is directly related to bandwidth. Generally speaking, noise is distributed over a wide range of frequencies. If the higher frequencies are filtered before the output, the result is less noise and better resolution (Figures 8, 9). When examining resolution specifications, it is critical to know at what bandwidth the specifications apply.Capacitive Sensor Operation Part 2: System OptimizationPart 2 of this two-part article focuses on how to optimize the performance of your capacitive sensor, and to understand how target material, shape, and size will affect the sensor's response.Effects of Target SizeThe target size is a primary consideration when selecting a probe for a specific application. When the sensing electric field is focused by guarding, it creates a slightly conical field that is a projection of the sensing area. The minimum target diameter is usually 130% of the diameter of the sensing area. The further the probe is from the target, the larger the minimum target size.Range of MeasurementThe range in which a probe is useful is a function of the size of the sensing area. The greater the area, the larger the range. Because the driver electronics are designed for a certain amount of capacitance at the probe, a smaller probe must be considerably closer to the target to achieve the desired amount of capacitance. In general, the maximum gap at which a probe is useful is approximately 40% of the sensing area diameter. Typical calibrations usually keep the gap to a value considerably less than this. Although the electronics are adjustable during calibration, there is a limit to the range of adjustment.Multiple Channel SensingFrequently, a target is measured simultaneously by multiple probes. Because the system measures a changing electric field, the excitation voltagefor each probe must be synchronized or the probes will interfere with each other. If they were not synchronized, one probe would be trying to increase the electric field while another was trying to decrease it; the result wouldbe a false reading. Driver electronics can be configured as masters or slaves; the master sets the synchronization for the slaves in multichannel systems.Effects of Target MaterialThe sensing electric field is seeking a conductive surface. Provided that the target is a conductor, capacitive sensors are not affected by the specific target material; they will measure all conductors—brass, steel, aluminum, or salt water—as the same. Because the sensing electric field stops at the surface of the conductor, target thickness does not affect the measurement中文翻译电容式传感器操作第一部分:基础 这篇文章的第一部分回顾了电容式传感器的概念和理论来帮助我们优化电容式传感器的性能。
热释电人体红外线传感器电子技术课程设计及实训(1)

热释电人体红外线传感器电子技术课程设计及实训(1)热释电人体红外线传感器电子技术课程设计及实训1. 引言随着技术不断发展,红外传感作为一种非接触式的检测技术得到了广泛应用。
其中,热释电人体红外线传感器作为一种常用的传感器,被广泛应用于安防、灯光控制等领域。
为了培养学生的动手实践能力和创新精神,本文进行了一项关于热释电人体红外线传感器的电子技术课程设计及实训。
2. 课程设计本课程设计旨在让学生了解热释电人体红外线传感器的结构、原理、特点和应用,并让学生在实验中全面掌握传感器的使用。
具体包括以下内容:(1)热释电人体红外线传感器的原理和结构介绍热释电人体红外线传感器的原理和结构,让学生了解传感器的基本工作原理和组成部分。
(2)热释电人体红外线传感器的特点及应用介绍热释电人体红外线传感器的特点和应用,例如在安防、灯光控制等领域的应用。
(3)热释电人体红外线传感器的电路设计根据热释电人体红外线传感器的原理,设计一个简单的电路并进行实验。
让学生了解电路的设计和布局方法,并学会使用示波器、万用表等工具。
(4)热释电人体红外线传感器的信号处理介绍热释电人体红外线传感器的信号处理方法,例如滤波、放大、模数转换等。
让学生了解信号处理的基本流程和方法。
3. 实训内容实训内容主要包括以下内容:(1)热释电人体红外线传感器电路的装配学生将自己设计的电路连接起来,并进行调试。
让学生学会使用电路元件和工具,了解电路的装配方法。
(2)热释电人体红外线传感器信号的测试学生将自己设计的热释电人体红外线传感器连接到示波器上,并进行测试。
让学生了解信号的测试方法和示波器的使用方法。
(3)热释电人体红外线传感器信号处理的实现学生将从传感器中获取的信号进行信号处理,例如进行滤波和放大,让学生了解信号处理的方法和流程。
(4)热释电人体红外线传感器应用的实现学生将热释电人体红外线传感器应用到实际的场景中,例如在安防系统中进行实时监测。
让学生了解传感器的实际应用场景。
传感器技术7-热电式传感器-中英对照
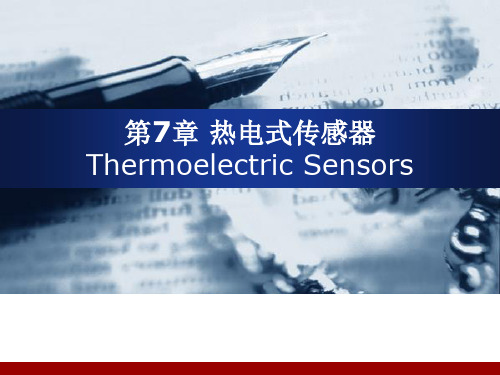
第7章 热电式传感器
2.铂、铜热电阻的特性 铂Platinum、铜Copper为应用最广的热电阻材料。 虽然铁Ferrum、镍Nickel的温度系数和电阻率均比 铂、铜要高,但由于存在着不易提纯(purify)和非线 性(nonlinearity)严重的缺点,因而用得不多。 铂容易提纯,在高温和氧化性(oxidative)介质中化 学、物理性能(physical properties)稳定,制成的铂 电阻输出-输入特性接近线性,测量精度高。
E A (T , T0 ) Adt E A (T0 , T )
T0
T
(7-8)
式中 EA(T,T0)——金属A两端温度分别为T与T0时的温差电势; σ A——温差系数(temperature differential coefficient); T、T0——高、低温端的绝对温度。
第7章 热电式传感器 Thermoelectric Sensors
第7章 热电式传感器
7.1
热电阻传感器 Thermal resistance sensors 热电偶传感器 Thermocouple sensors 热电式传感器的应用 Applications of thermoelectric sensors
第7章 热电式传感器
3.其他热电阻 ⑴.铟(Indium)电阻适宜在-269~-258℃温度范围内使 用,测温精度高,灵敏度是铂电阻的10倍,但是复 现性(repeatability)差。 ⑵.锰(Manganese)电阻适宜在-271~-210℃温度范围 内使用,灵敏度高,但是质脆易损坏。 ⑶.碳(Carbon)电阻适宜在-273~-268.5℃温度范围内 使用,热容量(thermal capacity)小,灵敏度高,价 格低廉,操作简便,但是热稳定性(thermal stability) 较差。
热释电红外传感器讲稿(英语)
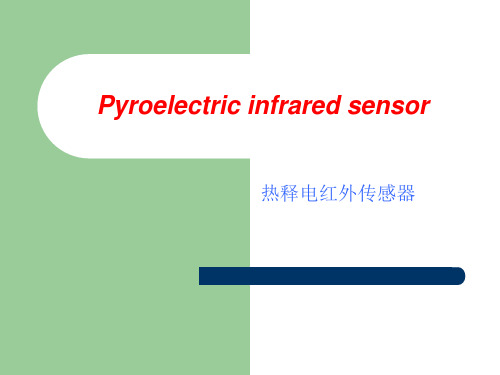
Pyroelectric infrared sensor is a very potential applications of the thermal sensor.It can detect people or animals, the infrared transmitter and converted into an electrical signal output. As early as 1938, it was proposed detection using pyroelectric infrared radiation effect, but not taken seriously. Until the sixties, with the laser, infrared technology is developing rapidly, it has contributed to the pyroelectric effect and research on pyroelectric crystals application development. In recent years, along with the rapid development of integrated circuit technology, as well as the characteristics of the sensor depth study of the relevant application specific integrated circuit processing technology is also growing rapidly.
Pyroelectric
infrared sensors and thermocouples are based on the principle of thermoelectric infrared sensors. The difference is that pyroelectric infrared sensors’ thermoelectric coefficient is much higher than the thermocouple.