酸洗磷化
磷化处理工艺程序及操作方法
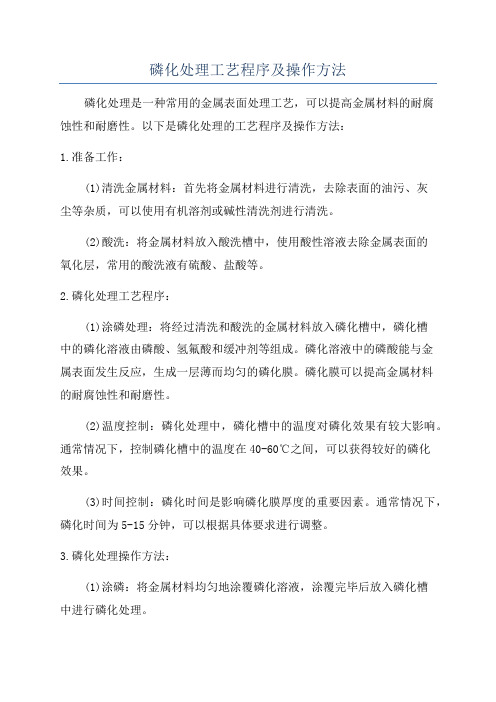
磷化处理工艺程序及操作方法磷化处理是一种常用的金属表面处理工艺,可以提高金属材料的耐腐蚀性和耐磨性。
以下是磷化处理的工艺程序及操作方法:1.准备工作:(1)清洗金属材料:首先将金属材料进行清洗,去除表面的油污、灰尘等杂质,可以使用有机溶剂或碱性清洗剂进行清洗。
(2)酸洗:将金属材料放入酸洗槽中,使用酸性溶液去除金属表面的氧化层,常用的酸洗液有硫酸、盐酸等。
2.磷化处理工艺程序:(1)涂磷处理:将经过清洗和酸洗的金属材料放入磷化槽中,磷化槽中的磷化溶液由磷酸、氢氟酸和缓冲剂等组成。
磷化溶液中的磷酸能与金属表面发生反应,生成一层薄而均匀的磷化膜。
磷化膜可以提高金属材料的耐腐蚀性和耐磨性。
(2)温度控制:磷化处理中,磷化槽中的温度对磷化效果有较大影响。
通常情况下,控制磷化槽中的温度在40-60℃之间,可以获得较好的磷化效果。
(3)时间控制:磷化时间是影响磷化膜厚度的重要因素。
通常情况下,磷化时间为5-15分钟,可以根据具体要求进行调整。
3.磷化处理操作方法:(1)涂磷:将金属材料均匀地涂覆磷化溶液,涂覆完毕后放入磷化槽中进行磷化处理。
(2)温度控制:调节磷化槽中的加热设备控制温度在40-60℃之间。
(3)时间控制:根据具体要求,控制磷化时间在5-15分钟之间。
(4)清洗:磷化处理完毕后,将金属材料从磷化槽中取出,使用清水进行冲洗,去除残留的磷化溶液和杂质。
(5)干燥:将清洗干净的金属材料放置在通风干燥的地方,等待其自然晾干。
4.注意事项:(1)操作安全:在进行磷化处理时,应佩戴个人防护装备,如手套、护目镜等,以保护自己的安全。
(2)剂量控制:在磷化溶液的配置中,应根据具体要求精确计量,以确保磷化效果的一致性。
(3)注意通风:磷化处理过程中会产生一定数量的有害气体,应选择通风条件良好的场所进行操作,以确保作业人员的健康安全。
(4)储存注意:磷化溶液应储存在阴凉、干燥的地方,并防止日晒和雨淋,避免阳光直射引起溶液质量变化。
钣金前处理工艺介绍

钣金前处理工艺介绍
钣金前处理工序流程:酸洗---脱脂——水洗——表调——磷化——水洗
1.酸洗:板材即便没有锈蚀也应酸洗处理一下,去掉板材的表面硬化层,提高磷化质量;
2.脱脂:脱脂的作用是去除板材表面的油脂和油污;
3.水洗:水洗的作用是洗去脱脂剂,防止把脱脂剂带到下个工序,污染下道工序或破坏下道工序的槽液组分平衡;
4.表调:表调的作用是调整板材表面性质,改善表面状态,使磷化的结晶细密,改善磷化质量;
5.磷化:磷化的作用是在前处理合格的板材表面生成一层磷酸盐保护层,磷化膜的作用是提高漆膜的附着力和提高板材的耐腐蚀性能;
6.水洗:磷化后的水洗是把板材表面挂附的磷化液洗干净,防止残留的磷酸盐在日后防腐过程中参与电化学腐蚀。
机柜之酸洗、磷化、热镀锌等工艺详解

机柜之酸洗、磷化、热镀锌等工艺详解本文是对网络服务器机柜生产过程中所采用的酸洗、磷化、热镀锌等流程的详细描述,希望对有兴趣了解网络服务器机柜如何生产的朋友有些许帮助。
~_~酸洗工艺酸洗工艺的酸洗液一般为多种酸的混合物,主要有硫酸、硝酸和氢氟酸等,这些混合酸的腐蚀性很强,同时具有很强的氧化性、较高的腐蚀介质的温度,这对防腐材料的耐蚀性能提出了很高的要求。
不锈钢酸洗生产线工艺从生产到废水废气回收系统,各个环节都存在很强的腐蚀状态,因此防腐材料选择的好坏直接关系到设备、车间地坪、地沟、废水废气的环保回收系统等处的正常使用。
如何对酸洗项目防腐进行选材呢?首先是玻璃钢管道和贮罐的结构及原材料选择,其次是车间地坪、设备基础防腐蚀一般采用树脂砂浆地坪结构。
玻璃钢管道和贮罐的结构及原材料选择。
酸洗项目中所用的贮罐和管路系统及酸雾回收系统现在基本选用玻璃钢材质,结构为防渗层+防腐层+结构强度层。
一般情况下防渗层和防腐层至少厚6~8毫米。
树脂选用合适的耐腐蚀环氧乙烯基树脂,专家介绍说--在介质为非氧化性酸、温度条件不是很高时,宜选用双酚A环氧乙烯基树脂;在氧化性酸、温度条件要求高时,宜选用酚醛环氧乙烯基树脂。
为了降低成本结构层大都选用间苯不饱和聚酯树脂,厚度根据具体的结构设计计算。
混酸和废酸贮罐由于腐蚀介质比较复杂,一般选用PVDF/FRP复合罐,但复合罐间PVDF和玻璃钢的粘结是一个亟待解决的问题,而且价格较高造成成本的增加,宜选用海特酸树脂(791H)做为内衬防腐材料,能满足以上介质条件的防腐蚀要求。
车间地坪、设备基础防腐蚀一般采用树脂砂浆地坪结构,总厚度约为7-10毫米,结构为:底漆1-2道+玻璃钢(2布3油)隔离层+树脂砂浆层(5-7毫米)+面层(约1毫米)。
地坪、设备基础的防腐蚀树脂现在都采用环氧乙烯基树脂,但是在底漆的选择上施工单位还习惯采用环氧树脂做底涂材料,以增加树脂和基层的粘结性能。
环氧树脂一般会采用胺类固化剂,固化后表面有油性物质浮出,再和乙烯基树脂粘结时不能够很好的匹配,需要对固化后的表面进行处理方可进行后续的防腐蚀结构施工,若处理不好容易分层、开裂。
机柜之酸洗、磷化、热镀锌等工艺详解

机柜之酸洗、磷化、热镀锌等工艺详解本文是对网络服务器机柜生产过程中所采用的酸洗、磷化、热镀锌等流程的详细描述,希望对有兴趣了解网络服务器机柜如何生产的朋友有些许帮助。
~_~酸洗工艺酸洗工艺的酸洗液一般为多种酸的混合物,主要有硫酸、硝酸和氢氟酸等,这些混合酸的腐蚀性很强,同时具有很强的氧化性、较高的腐蚀介质的温度,这对防腐材料的耐蚀性能提出了很高的要求。
不锈钢酸洗生产线工艺从生产到废水废气回收系统,各个环节都存在很强的腐蚀状态,因此防腐材料选择的好坏直接关系到设备、车间地坪、地沟、废水废气的环保回收系统等处的正常使用。
如何对酸洗项目防腐进行选材呢?首先是玻璃钢管道和贮罐的结构及原材料选择,其次是车间地坪、设备基础防腐蚀一般采用树脂砂浆地坪结构。
玻璃钢管道和贮罐的结构及原材料选择。
酸洗项目中所用的贮罐和管路系统及酸雾回收系统现在基本选用玻璃钢材质,结构为防渗层+防腐层+结构强度层。
一般情况下防渗层和防腐层至少厚6~8毫米。
树脂选用合适的耐腐蚀环氧乙烯基树脂,专家介绍说--在介质为非氧化性酸、温度条件不是很高时,宜选用双酚A环氧乙烯基树脂;在氧化性酸、温度条件要求高时,宜选用酚醛环氧乙烯基树脂。
为了降低成本结构层大都选用间苯不饱和聚酯树脂,厚度根据具体的结构设计计算。
混酸和废酸贮罐由于腐蚀介质比较复杂,一般选用PVDF/FRP复合罐,但复合罐间PVDF和玻璃钢的粘结是一个亟待解决的问题,而且价格较高造成成本的增加,宜选用海特酸树脂(791H)做为内衬防腐材料,能满足以上介质条件的防腐蚀要求。
车间地坪、设备基础防腐蚀一般采用树脂砂浆地坪结构,总厚度约为7-10毫米,结构为:底漆1-2道+玻璃钢(2布3油)隔离层+树脂砂浆层(5-7毫米)+面层(约1毫米)。
地坪、设备基础的防腐蚀树脂现在都采用环氧乙烯基树脂,但是在底漆的选择上施工单位还习惯采用环氧树脂做底涂材料,以增加树脂和基层的粘结性能。
环氧树脂一般会采用胺类固化剂,固化后表面有油性物质浮出,再和乙烯基树脂粘结时不能够很好的匹配,需要对固化后的表面进行处理方可进行后续的防腐蚀结构施工,若处理不好容易分层、开裂。
脱脂、酸洗、表调、磷化的技术介绍

脱脂、酸洗、表调、磷化表面处理的技术介绍一. 脱脂、酸洗、表调、磷化常作为表面处理的预处理或中间处理工序二. 脱脂定义工件在进行化学成膜之前,必须先除去表面的油脂及附着在表面的灰尘、锈迹、金属细铁屑等污物,才能保证转化膜化学反应的顺利进行,使转化膜与金属基体牢固结合,获得质量优良的转化膜。
除油的方法包括机械法、化学法两类。
机械法主要是:手工擦刷、喷砂抛丸、火焰灼烧等。
化学法主要是:溶剂清洗、强碱液清洗、低碱性清洗剂清洗、酸性清洗剂清洗。
三.酸洗定义1.指清洁金属表面的一种方法。
通常与预膜(pre-passiviting treatment)一起进行。
一般将制件浸入硫酸等的水溶液,以除去金属表面的氧化物等薄膜。
是电镀、搪瓷、轧制等工艺的前处理或中间处理。
2. 方法说明1).利用酸溶液去除钢铁表面上的氧化皮和锈蚀物的方法称为酸洗。
氧化皮、铁锈等铁的氧化物(Fe3O4,Fe2O3,FeO等)与酸溶液发生化学反应,形成盐类溶于酸溶液中而被除去。
2).酸洗用酸有硫酸、盐酸、磷酸、硝酸、铬酸、氢氟酸和混合酸等。
最常用的是硫酸和盐酸。
在酸洗时务必加入酸洗缓蚀剂,防止酸对金属的腐蚀。
3).酸洗工艺主要有浸渍酸洗法、喷射酸洗法和酸膏除锈法。
一般多用浸渍酸洗法,大批量生产中可采用喷射法。
钢铁零件一般在10%~20%(体积)硫酸溶液中酸洗,温度为40℃。
当溶液中含铁量超过80g/L,硫酸亚铁超过215g/L时,应更换酸洗液。
常温下,用20%~80%(体积)的盐酸溶液对钢铁进行酸洗,不易发生过腐蚀和氢脆现象。
由于酸对金属的腐蚀作用很大,需要添加缓蚀剂。
清洗后金属表面成银白色,同时钝化表面,提高不锈钢抗腐蚀能力。
采用浓度为5%~20%的硫酸水溶液,清除工件表面氧化皮和粘附盐类的工艺称为硫酸酸洗法。
四.表调定义1.表调就是表面调整,是把工件放入装有表调液的槽子里进行表面调整处理的过程。
有人说我们的磷化液不需要表调,也可以做的很好,其实这种说法是完全错误的。
磷化与酸洗的区别

磷化工艺的早期应用是防锈,钢铁件经磷化处理形成一层磷化膜,起到防锈作用。
经过磷化防锈处理的工件防锈期可达几个月甚至几年(对涂油工件而言),广泛用于工序间、运输、包装贮存及使用过程中的防锈,防锈磷化主要有铁系磷化、锌系磷化、锰系磷化三大品种。
铁系磷化的主体槽液成分是磷酸亚铁溶液,不含氧化类促进剂,并且有高游离酸度。
这种铁系磷化处理温度高于95℃,处理时间长达30min以上,磷化膜重大于10g/m2,并且有除锈和磷化双重功能。
这种高温铁系磷化由于磷化速度太慢,现在应用很少。
锰系磷化用作防锈磷化具有最佳性能,磷化膜微观结构呈颗粒密堆集状,是应用最为广泛的防锈磷化。
加与不加促进剂均可,如果加入硝酸盐或硝基胍促进剂可加快磷化成膜速度。
通常处理温度80~100℃,处理时间10~20min,膜重在7.5克/m2以上。
锌系磷化也是广泛应用的一种防锈磷化,通常采用硝酸盐作为促进剂,处理温度80~90℃,处理时间10~15min,磷化膜重大于7.5g/m2,磷化膜微观结构一般是针片紧密堆集型。
防锈磷化一般工艺流程:除油除锈——水清洗——表面调整活化——磷化——水清洗——铬酸盐处理——烘干——涂油脂或染色处理通过强碱强酸处理过的工件会导致磷化膜粗化现象,采用表面调整活化可细化晶粒。
锌系磷化可采用草酸、胶体钛表调。
锰系磷化可采用不溶性磷酸锰悬浮液活化。
铁系磷化一般不需要调整活化处理。
磷化后的工件经铬酸盐封闭可大幅度提高防锈性,如再经过涂油或染色处理可将防锈性提高几位甚至几十倍一、磷化原理1、磷化工件(钢铁或铝、锌件)浸入磷化液(某些酸式磷酸盐为主的溶液),在表面沉积形成一层不溶于水的结晶型磷酸盐转换膜的过程,称之为磷化。
2、磷化原理钢铁件浸入磷化液(由Fe(H2PO4)2 Mn(H2PO4)2 Zn(H2PO4)2 组成的酸性稀水溶液,PH值为1-3,溶液相对密度为1.05-1.10)中,磷化膜的生成反应如下:吸热3Zn(H2PO4)2 Zn3(PO4)2↓+4H3PO4或吸热吸热3Mn(H2PO4)2 Mn3(PO4)2↓+4H3PO4吸热钢铁工件是钢铁合金,在磷酸作用下,Fe和FeC3形成无数原电池,在阳极区,铁开始熔解为Fe2+,同时放出电子。
磷化与酸洗的区别

磷化工艺的早期应用是防锈,钢铁件经磷化处理形成一层磷化膜,起到防锈作用。
经过磷化防锈处理的工件防锈期可达几个月甚至几年(对涂油工件而言),广泛用于工序间、运输、包装贮存及使用过程中的防锈,防锈磷化主要有铁系磷化、锌系磷化、锰系磷化三大品种。
铁系磷化的主体槽液成分是磷酸亚铁溶液,不含氧化类促进剂,并且有高游离酸度。
这种铁系磷化处理温度高于95℃,处理时间长达30min以上,磷化膜重大于10g/m2,并且有除锈和磷化双重功能。
这种高温铁系磷化由于磷化速度太慢,现在应用很少。
锰系磷化用作防锈磷化具有最佳性能,磷化膜微观结构呈颗粒密堆集状,是应用最为广泛的防锈磷化。
加与不加促进剂均可,如果加入硝酸盐或硝基胍促进剂可加快磷化成膜速度。
通常处理温度80~100℃,处理时间10~20min,膜重在7.5克/m2以上。
锌系磷化也是广泛应用的一种防锈磷化,通常采用硝酸盐作为促进剂,处理温度80~90℃,处理时间10~15min,磷化膜重大于7.5g/m2,磷化膜微观结构一般是针片紧密堆集型。
防锈磷化一般工艺流程:除油除锈——水清洗——表面调整活化——磷化——水清洗——铬酸盐处理——烘干——涂油脂或染色处理通过强碱强酸处理过的工件会导致磷化膜粗化现象,采用表面调整活化可细化晶粒。
锌系磷化可采用草酸、胶体钛表调。
锰系磷化可采用不溶性磷酸锰悬浮液活化。
铁系磷化一般不需要调整活化处理。
磷化后的工件经铬酸盐封闭可大幅度提高防锈性,如再经过涂油或染色处理可将防锈性提高几位甚至几十倍一、磷化原理1、磷化工件(钢铁或铝、锌件)浸入磷化液(某些酸式磷酸盐为主的溶液),在表面沉积形成一层不溶于水的结晶型磷酸盐转换膜的过程,称之为磷化。
2、磷化原理钢铁件浸入磷化液(由Fe(H2PO4)2 Mn(H2PO4)2 Zn(H2PO4)2 组成的酸性稀水溶液,PH值为1-3,溶液相对密度为1.05-1.10)中,磷化膜的生成反应如下:吸热3Zn(H2PO4)2 Zn3(PO4)2↓+4H3PO4或吸热吸热3Mn(H2PO4)2 Mn3(PO4)2↓+4H3PO4吸热钢铁工件是钢铁合金,在磷酸作用下,Fe和FeC3形成无数原电池,在阳极区,铁开始熔解为Fe2+,同时放出电子。
酸洗磷化工艺

酸洗磷化工艺公司标准化编码 [QQX96QT-XQQB89Q8-NQQJ6Q8-MQM9N]酸洗磷化工艺一、目的:除去线材表面的氧化膜,并且在金属表面形成一层磷酸盐薄膜,以减少线材抽线以及冷墩或成形等加工过程中,对工模具的擦伤。
二、作业流程:(一)、酸洗:将整个盘元分别浸入常温、浓度为20-25%的三个盐酸槽数分钟,其目的是除去线材表面的氧化膜。
(二)、清水:清除线材表面的盐酸腐蚀产物。
(三)、皮膜处理:将盘元浸入磷酸盐,钢铁表面与化成处理液接触,钢铁溶解生成不溶性的化合物(如Zn2Fe(Po4)24H2o),附着在钢铁表面形成皮膜。
(四)、清水:清除皮膜表面残余物。
(五)、润滑剂:由于磷酸盐皮膜的摩擦系数并不是很低,不能赋予加工时充分的润滑性,但与金属皂(如钠皂)反应形成坚硬的金属皂层,可以增加其润滑性能。
酸洗1) 盐酸溶液浓度一般控制在5%~25%。
每天开始工作前要检查酸洗液浓度,并检查每槽酸液位,当酸槽液位不够时,需根据酸槽浓度添加酸或加水,补充到所需液位;当亚铁粒子浓度较高时,一般不再加入新酸。
当酸液浓度小于5%,氯化亚铁含量大于150克/升时,需更换新酸。
2) 两个盐酸槽中配置不同浓度的盐酸,分别为5%<低浓度≤10%,10%<中等浓度≤20%,线材经过酸池顺序为低浓度到中等浓度,对退火后中碳合金钢只在低浓度酸液中酸洗。
酸洗时间与温度、酸液浓度、氧化皮厚度形态及盘料的粗细等有关,3) 为了盘料在酸池中浸泡时间的同步,退火线和非退火线、氧化皮厚与氧化皮薄的盘料不准安排在同一吊钩上生产;4) 待酸洗的材料上不能沾上油污,尤其要防止行车滴油污染材料。
5) 酸洗时要松捆酸洗,不要扎腰。
操作中要认真检查、勤翻料。
6) 对于退火异常线材表面氧化皮难以除去或表面污垢难以去除的线材应在弱酸中浸泡10~20分钟后进行水洗,水洗过后放在酸洗区域外生锈1~2天后,再次酸洗;7) 酸洗作业中,若遇行车损坏或停电等其他特殊状况而不能继续操作时,要注意浸泡在酸中线材的品质,并向主管反映处理。
- 1、下载文档前请自行甄别文档内容的完整性,平台不提供额外的编辑、内容补充、找答案等附加服务。
- 2、"仅部分预览"的文档,不可在线预览部分如存在完整性等问题,可反馈申请退款(可完整预览的文档不适用该条件!)。
- 3、如文档侵犯您的权益,请联系客服反馈,我们会尽快为您处理(人工客服工作时间:9:00-18:30)。
一、什么是酸洗磷化
酸洗磷化处理是针对金属表面处理的工序,酸洗就是用一家浓度的酸清洗金属以除去表面的锈。
磷化就是用磷化液浸泡酸洗过的金属,以表面形成一层氧化膜,一是可以防锈,二是可以提高油漆的附着力,为下一步工序作准备。
酸洗除锈、除氧化皮的方法是工业领域应用最为广泛的方法。
利用酸对氧化物溶解以及腐蚀产生氢气的机械剥离作用达到除锈和除氧化皮的目的。
酸洗中使用最为常见的是盐酸、硫酸、磷酸。
硝酸由于在酸洗时产生有毒的二氧化氮气体,一般很少应用。
盐酸酸洗适合在低温下使用,不宜超过45℃,使用浓度10% ~45%,还应加入适量的酸雾抑制剂为宜。
硫酸在低温下的酸洗速度很慢,宜在中温使用,温度50~80℃,使用浓度10%~25%。
磷酸酸洗的优点是不会产生腐蚀性残留物(盐酸、硫酸酸洗后或多或少会有少会有Cl-、SO42-残留),比较安全,但磷酸的缺点是成本较高,酸洗速度较慢,一般使用浓度10% ~40%,处理温度可常温到80℃。
在酸洗工艺中,采用混合酸也是非常有效的方法,如盐酸-硫酸混合酸,磷酸-柠檬酸混合酸。
在酸洗除锈除氧化皮槽液中,必须加入适量的缓蚀剂。
缓蚀剂的种类很多,选用也比较容易,它的作用是抑制金属腐蚀和防止"氢脆"。
但酸洗"氢脆"敏感的工件时,缓蚀剂的选择应特别小心,因为某些缓蚀剂抑制二个氢原子变为氢分子的反应,即:2[H]→H2↑,使金属表面氢原子的浓度提高,增强了"氢
脆"倾向。
因此必须查阅有关腐蚀数据手册,或做"氢脆"试验,避免选用危险的缓蚀剂。
二、磷化工艺对环境的影响
目前市售的低温、常温磷化液绝大多数为单独添加亚硝酸盐的多组份产品。
亚硝酸盐在磷化液中的危害主要有两个方面:一、影响磷化液的稳定性。
亚硝酸盐在酸性条件下极不稳定,在极短的时间内就分解了。
因此,不得不经常添加。
亚硝酸盐的这种特性,往往引起磷化液的主盐不稳定,磷化液沉淀增多,磷化膜挂灰严重,磷化液使用过程中控制困难,磷化质量不稳定;二、毒性与致癌危害性。
亚硝酸盐是世界公认的致癌物质,长期接触个别人有皮肤过敏现象,且进入体内毒性较大。
磷化废水其中包含大量的有害因子,且具有较强的腐蚀性,容易对环境产生一定的危害。
如果不加治理直接排放,会腐蚀灌渠和建筑物;排入水体,会改变水体的酸碱度,废液中的含磷量会使水体出现大量藻类植物,让河流生出蓝藻,干扰并影响水生植物的生长和渔业生产;排入农田,会改变土壤的性质,使土壤酸化或盐碱化,严重危害农作物的生长;酸碱原料的流失也是一种浪费。