颗粒自动包装机验证方案(新版GMP含风险评估)
颗粒自动包装机验证方案(新版GMP-含风险评估)概要

颗粒分装机验证方案申请部门:审核人日期:审核人日期:批准人日期:目录1 引言2人员培训确认3概述4 验证的目的5 验证所需文件6 验证范围7 验证项目和时间安排9 设计确认10 供应商审计和评估11 安装确认IQ12 运行确认13 性能确认14 结果与评价15 验证周期16 设备使用阶段17设备报废阶段1 引言1.1 验证小组:姓名所在部门职务验证分工1.2 验证小组职责1.2.1负责验证方案的审批;1.2.2负责验证的协调工作,以保证验证方案规定项目顺利实施;1.2.3负责验证数据及结果的审核;1.2.4负责验证报告的审批;1.2.5负责发放验证证书;1.2.6负责验证周期的确认;1.2.7验证小组组长负责组织方案起草、方案实施全过程的组织和验证报告;1.2.8验证小组组员分别负责方案实施验证部分具体工作。
1.3工程部1.3.1负责颗粒自动包装机的调试,并做好相应记录;1.3.2负责提供颗粒自动包装机的档案、资料交档案室;1.3.4负责拟定验证周期;1.3.5负责收集各项验证、试验记录,并对数据进行分析、评估,起草验证报告,报验证小组;1.3.6确保验证设备的完好运行,为验证过程中提供有关的技术服务;1.3.7负责颗粒自动包装机的维护保养。
1.3.8负责设备的统筹管理,包括设备的配置、验收、建档、检修和报废等。
1.4 质量部1.4.1 负责对生产部提供的参数要求进行确认;1.4.2 各种检验的准备,取样及样品的测试工作;1.4.3 负责根据检验结果,出具检验报告单;1.4.4负责组织验证方案、验证报告、验证结果的会审会签;1.4.5负责对验证全过程实施监控。
负责验证的协调工作,以保证本验证方案规定项目的顺利实施;1.4.6负责建立验证档案,及时将批准实施的验证资料收存归档;1.4.7负责验证过程的取样、检验、测试及结果报告。
1.5 生产部1.5.1 负责提供与颗粒自动包装机有关的主要参数;1.5.2 负责指定颗粒自动包装机的管理人员及操作人员;1.5.3 负责验证中各种试验材料的准备工作,并派人参加验证工作对机器的操作和清洁维护保养工作;1.5.4组织实施验证方案,参加会签验证方案、验证报告,收集记录验证资料、数据。
颗粒包装机验证方案

颗粒包装机验证方案1. 引言颗粒包装机是一种广泛应用于食品、医药和农业领域的设备,用于自动化地将颗粒物料进行计量、包装。
为了确保颗粒包装机的正常工作和包装质量的稳定性,验证方案是必不可少的。
本文将介绍一种针对颗粒包装机的验证方案,以确保其可靠性和稳定性。
2. 验证目标颗粒包装机的验证目标是验证其在正常工作条件下,能够准确地计量和包装颗粒物料,并保持包装质量的稳定性。
具体的验证目标包括:•计量准确性:验证颗粒包装机的计量系统能够准确地计量颗粒物料,并与标准值相符。
•包装质量:验证颗粒包装机的包装过程中,袋内颗粒物料分布均匀、密封完好,达到预期的质量标准。
•工作稳定性:验证颗粒包装机在长时间连续工作条件下,能够保持稳定性,不发生故障或异常情况。
3. 验证方法颗粒包装机的验证可以按照以下方法进行:3.1 计量准确性验证计量准确性验证主要包括两个方面的内容:计量精度和计量偏差。
3.1.1 计量精度验证计量精度验证是通过比较颗粒包装机的计量结果与标准值进行验证。
具体步骤如下:1.准备标准颗粒物料,并进行预先称量,得到标准值。
2.启动颗粒包装机,将标准颗粒物料进行包装。
3.根据包装后的颗粒物料总重量和袋数,计算出平均包装重量。
4.将平均包装重量与标准值进行比较,计算出计量误差。
3.1.2 计量偏差验证计量偏差验证是通过多次验证计量结果的稳定性来判断颗粒包装机的计量偏差。
具体步骤如下:1.连续进行多次计量操作,记录每次的计量结果。
2.根据记录的计量结果,计算出平均值和标准差。
3.判断平均值是否在一定范围内,判断标准差是否符合要求。
3.2 包装质量验证包装质量验证主要包括颗粒分布均匀性和袋口密封情况的验证。
3.2.1 颗粒分布均匀性验证颗粒分布均匀性验证是通过观察包装袋内颗粒的分布情况来判断颗粒包装机的包装质量。
具体步骤如下:1.包装一定数量的颗粒物料,并使用颗粒包装机进行包装。
2.打开包装袋,观察袋内颗粒物料的分布情况。
新版GMP颗粒自动包装机

新版GMP颗粒自动包装机随着制药行业的持续发展,人们对于药品生产过程的要求也越来越高。
特别是在药品包装环节,自动化技术的应用已经成为了必然的趋势。
而此时,新版GMP颗粒自动包装机的出现无疑是极具意义的。
一、新版GMP颗粒自动包装机简介新版GMP颗粒自动包装机是一款全新的自动包装设备,它主要用于颗粒药品的包装工作。
该设备完全按照GMP要求设计和制造,拥有着新型的外观设计,便于操作和维护。
二、新版GMP颗粒自动包装机的优点新版GMP颗粒自动包装机在设计上进行了全面升级,其优点也是十分明显的,主要包括以下两个方面:1.高效性相比于传统的人工包装方式,新版GMP颗粒自动包装机可以快速地完成颗粒药品的包装工作,大大提高了包装的效率。
其包装速度可以达到20-80袋/分钟,同时还能够实现定量包装和自动计数等功能。
这极大地降低了人工成本,提高了经济效益。
2.可靠性新版GMP颗粒自动包装机在使用过程中,不仅可以保证颗粒药品的安全性和包装质量,还可以避免人工操作所带来的不确定因素。
同时,在保证包装效果的同时,还可以减少能源的消耗,降低了环境污染。
因此,该设备在药品生产过程中的可靠性非常高。
三、新版GMP颗粒自动包装机的适用范围新版GMP颗粒自动包装机的适用范围非常广泛,主要适用于以下领域:1.制药行业:主要用于药品颗粒的包装,满足制药企业对于药品包装方面的需求。
2.食品行业:用于各类粉状或颗粒状食品的包装工作。
3.化工行业:采用自动化包装技术,可以保证化学药品对于人体的安全,以及有效地减少环境污染,成为化工企业进行包装工作的选择。
四、结语总之,新版GMP颗粒自动包装机的出现,使得药品包装方面更加高效、可靠。
适用于制药、食品和化工等多个行业的自动化包装工作。
未来也将继续为药品生产企业提供更高效、更可靠、更安全的包装解决方案。
自动颗粒包装机风险评估

DXDK40II自动颗粒包装机风险评估
一、概述:
公司设备自动颗粒包装机,安装于固体制剂车间颗粒分装间,用于颗粒剂包装操作。
二、评估目的:
对自动颗粒包装机可能因在设计、安装、运行、性能等方面可能存在的缺陷项进行风险评估;并由此制定经过验证或确认的风险控制措施。
从而彻底消除或避免降低自动颗粒包装机可能存在的缺陷项给产品质量、生产环境、人员健康、公共安全等带来的风险隐患。
三、风险评估
应用失败模式影响分析(FMEA)对风险进行评估
风险的严重程度(S)
风险发生概率(P)
可检测性(D)
➢风险评价准则:RPN(风险优先系数)计算: RPN = S×P×D
●高风险水平:RPN≥ 9。
此为不可接受风险。
必须尽快采用控制措施,通过提高可检测性及/或降低风险产生的可能性来降低最终风险水平。
验证应首先集中于确认已采用控制措施且持续执行。
●中等风险水平: RPN=6-8。
此风险要求采用控制措施,通过提高可检测性及/或降低风险产生的可能性来降低最终风险水平。
所采用的措施可以是规程或技术措施,但均应经过验证。
●低风险水平:RPN<6。
此风险水平为可接受,无需采用额外的控制措施
五、风险评估
我们对该设备可能存在的质量风险分别进行评估。
详细内容见以下质量风险评估记录。
风险评估记录。
颗粒包装机验证方案

DXDK4 0 H颗粒包装机验证方案一、概述颗粒包装机是颗粒剂生产中的包装设备,也是颗粒剂生产的关键设备。
本院的颗粒包装机为DXDK4Q颗粒包装机,采用容积法计量,具有可调计量、充填、封口、分切、计数、热压批号、等功能,袋长在50—100mn之间无极可调。
二、验证目的对颗粒包装机进行验证,确认其供电正常,设备及辅助设施完好,运行正常,性能完好,保证包装效果。
三、验证项目1 、颗粒包装机安装确认2、颗粒包装机运行确认3、颗粒包装机性能确认四、验证组织颗粒包装机验证小组组成及职责如下:组长:杨春云负责验证方案、验证报告的编写,组织本方案实施;成员:唐万贵负责设备检修,指导设备操作;成智负责实施颗粒包装机操作,协助取样;漆立军负责现场监测、取样、检验的协调工作;王勇负责现场监督及取样工作;杨久云负责样品的检验工作;五、验证进度安排2011年2月22日至2011年月日完成验证工作.六、验证的方法和步骤1 安装确认1.1 目的:对设备的档案资料、主机及辅助设施的完整性和供电情况进行确认,确保技术资料的完整性,确保设备的完整性。
1.2 确认方法:安装确认在设备检修阶段进行。
由机修车间到制剂室档案柜对设备的档案资料进行清查,确认设备档案的完善。
到车间设备安装现场对设备的配置及供电情况逐一机修确认,将确认的结果按附表1 进行记录。
2 运行确认2.1 目的:确保设备能正常运行,为设备性能确认奠定基础。
2.2 确认方法:运行确认在设备安装确认完成后进行。
由机修车间人员按颗粒包装机操作规程进行空运行操作,操作过程记录于附表23 性能确认3.1 目的:确认设备的性能满足生产的要求,确保设备能够稳定地生产出合格产品,从而保证生产速度和产品质量。
3.2确认方法:操作人员选择制剂室颗粒包装的老员工,对设备的性能比较了解。
因此,颗粒包装机的性能确认在运行确认合格后正式包装产品时进行。
在产品的包装过程中确认设备的性能,并将设备运行情况及产品包装质量情况按附表3进行记录。
自动颗粒包装机清洁验证
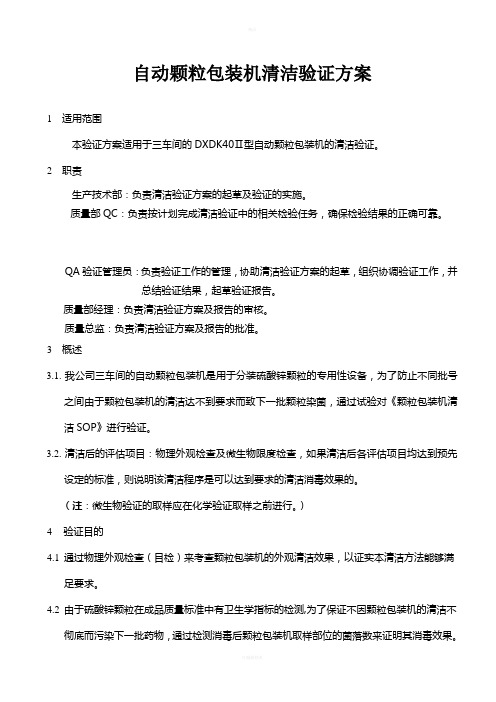
自动颗粒包装机清洁验证方案1适用范围本验证方案适用于三车间的DXDK40Ⅱ型自动颗粒包装机的清洁验证。
2职责生产技术部:负责清洁验证方案的起草及验证的实施。
质量部QC:负责按计划完成清洁验证中的相关检验任务,确保检验结果的正确可靠。
QA验证管理员:负责验证工作的管理,协助清洁验证方案的起草,组织协调验证工作,总结验证结果,起草验证报告。
质量部经理:负责清洁验证方案及报告的审核。
质量总监:负责清洁验证方案及报告的批准。
3概述3.1.我公司三车间的自动颗粒包装机是用于分装硫酸锌颗粒的专用性设备,为了防止不同批号之间由于颗粒包装机的清洁达不到要求而致下一批颗粒染菌,通过试验对《颗粒包装机清洁SOP》进行验证。
3.2.清洁后的评估项目:物理外观检查及微生物限度检查,如果清洁后各评估项目均达到预先设定的标准,则说明该清洁程序是可以达到要求的清洁消毒效果的。
(注:微生物验证的取样应在化学验证取样之前进行。
)4验证目的4.1通过物理外观检查(目检)来考查颗粒包装机的外观清洁效果,以证实本清洁方法能够满足要求。
4.2由于硫酸锌颗粒在成品质量标准中有卫生学指标的检测,为了保证不因颗粒包装机的清洁不彻底而污染下一批药物,通过检测消毒后颗粒包装机取样部位的菌落数来证明其消毒效果。
5清洁方法每批硫酸锌颗粒包装结束后,按《颗粒包装机清洁SOP》对设备进行清洁。
6取样部位确定6.1按《颗粒包装机清洁SOP》清洁包装机后,其清洁部位包括分装机料斗、料盘、成型器、量杯、出料口、辊、以及分装机外壳等。
6.2根据本包装机的特点,确定成型器内壁(M)、料盘(N)是最难清洁的部位,以这两个部位为棉签擦拭取样法的取样部位。
7化学验证物理外观检查取样:清洁结束后,在最难清洁的部位用清洁白稠布进行擦拭取样。
检验方法:目视检查法可接受标准:目视检查颗粒包装机料斗、成型器、料盘、量杯、接料盒、辊、以及包装机外壳等应无残留药粉,无污迹,用清洁白稠布抹后应无可见污迹。
[整理]07颗粒包装机验证方案
![[整理]07颗粒包装机验证方案](https://img.taocdn.com/s3/m/e45b71f05fbfc77da269b1e8.png)
-------------自动颗粒包装机验证方案编号:修订历史版本修订日期修订原因执行日期变更控制号文件会签本文件应在质量经理授权下由XXXX制药有限公司验证小组起草。
因此,该文件在生效前应由XXXX制药有限公司质量部批准,并由相关部门负责人授权。
起草人部门姓名职务签名日期审核人部门姓名职务签名日期批准人部门姓名职务签名日期目录1.目的 (4)2.范围 (4)3.职责 (4)4.定义与缩略语 (5)4.1定义 (5)4.2缩略语 (5)5.参考文件 (5)6.概述 (5)7.验证/确认前准备 (6)7.1人员培训确认 (6)7.2文件确认 (6)7.3验证/确认用仪器确认 (7)8.验证/确认的实施 (7)8.1安装确认 (7)8.2运行确认 (9)8.3性能确认 (10)8.4偏差管理 (11)8.5变更控制 (11)9 确认总结 (12)10附件清单 (12)1.目的证明该设备能始终如一的生产出符合预定质量要求的产品。
2.范围适用于自动颗粒包装机的验证/确认。
3.职责3.1生产车间3.1.1 参与编写验证方案;3.1.2 实施验证方案,并确保确认顺利进行;3.1.3 负责确认方案和报告的审核;3.2 QA3.2.1 参与编写验证方案;3.2.2 负责确认方案和报告的审核;3.2.3 负责过程监督,确保质量管理的原则体现在验证过程之中;3.2.4 参与及指导验证的实施、结果评价;3.2.5 协调验证中各相关部门;3.3 QC3.3.1 负责对验证方案的实施过程中与检测有关的活动;3.3.2 参与审核验证方案及报告;3.4 质量负责人负责验证文件的批准;3.5 生产负责人负责验证文件的批准;4.定义与缩略语4.1 定义4.1.1校验证明某个仪器或装置在适当的量程范围内所测得的结果与参照物,或可追溯的标准相比在规定限度内;4.1.2确认证明设备或辅助系统,安装正确、工作正常、确实产生预期的结果,并以文件佐证的行为。
自动颗粒包装机验证方案

目的;检查并确认颗粒剂车间自动颗粒包装机的安装、运行是否符合生产工艺要求,资料和文件符合GMP管理要求。
应用范围:固体制剂颗粒内包工序。
责任人:工程部部长、生产部长、质保部长、车间主任。
内容:1引言1.1背景自动颗粒包装机用于非无菌固体制剂生产线中内包装工序,以保证颗粒剂的稳定性及质量要求。
1.2方案概要本设备验证方案包括1.2.1设备介绍,有关文件的检查,设备的检查及相关公用介质的检查情况。
1.2.2设备运行测试。
1.2.3性能测试数据的记录、汇总、分析及评价。
2验证目的:2.1运行性能是否能达到设计技术指标。
2.2满足工艺要求,以保证生产正常运行。
2.3颗粒剂包装后的装量差异、热封效果是否符合工艺要求。
2、验证对象生产厂商:天津轻工包装机械厂型号:B.DZ.F-30A 安装位置:颗粒剂车间内包装间B.DZ.F-30A自动颗粒包装机,本机能自动完成制袋、可调量杯计量、充填、打日期封合部位打口、计数、传送带输出。
本机还采用了无级调整制袋长度机构和光电商标定位控制,还附有敲打辅助下料装置。
本机分为机械部分、电器部分,机械部分又分为无级调速机构、间隔齿轮及锥辊无级调速机构、偏心链轮、行星差动轮系、可调杯机构及量杯另件图、打字、打口、切刀横封辊机构、振荡辅肋下料机构。
电器部分分为主电路、光电控制系统。
技术参数:制袋尺寸:长75-100mm 计量范围:5-10毫升包装速度:50-100袋/分耗电功率:1.5kw4.安装确认4.1文件检查:检查人:检查日期:4.2安装情况检查人:复核人:检查日期:5.运行确认5.1目的:在空载情况下,设备各部分动作功能正常,符合设计要求。
5.2合格标准:按操作规程开启包装机,设备各执行动作按操作指令运转正常,符合设计要求。
5.3运行确认前:应确认各项准备工作就绪5.3.1设备安装稳固5.3.2电气连接正常5.3.3接地保护良好5.3.4润滑良好测试人:复核人:测试日期:6性能确认6.1目的:通过机器运行一定时间确定本机器是否能达到设计指标,是否符合工艺要求。
- 1、下载文档前请自行甄别文档内容的完整性,平台不提供额外的编辑、内容补充、找答案等附加服务。
- 2、"仅部分预览"的文档,不可在线预览部分如存在完整性等问题,可反馈申请退款(可完整预览的文档不适用该条件!)。
- 3、如文档侵犯您的权益,请联系客服反馈,我们会尽快为您处理(人工客服工作时间:9:00-18:30)。
颗粒分装机验证方案申请部门:审核人日期:审核人日期:批准人日期:目录1 引言2人员培训确认3概述4 验证的目的5 验证所需文件6 验证范围7 验证项目和时间安排8 风险评估9 设计确认10 供应商审计和评估11 安装确认IQ12 运行确认13 性能确认14 结果与评价15 验证周期16 设备使用阶段17设备报废阶段1 引言1.1 验证小组:姓名所在部门职务验证分工1.2 验证小组职责1.2.1负责验证方案的审批;1.2.2负责验证的协调工作,以保证验证方案规定项目顺利实施;1.2.3负责验证数据及结果的审核;1.2.4负责验证报告的审批;1.2.5负责发放验证证书;1.2.6负责验证周期的确认;1.2.7验证小组组长负责组织方案起草、方案实施全过程的组织和验证报告;1.2.8验证小组组员分别负责方案实施验证部分具体工作。
1.3工程部1.3.1负责颗粒自动包装机的调试,并做好相应记录;1.3.2负责提供颗粒自动包装机的档案、资料交档案室;1.3.3负责仪器仪表的校正;1.3.4负责拟定验证周期;1.3.5负责收集各项验证、试验记录,并对数据进行分析、评估,起草验证报告,报验证小组;1.3.6确保验证设备的完好运行,为验证过程中提供有关的技术服务;1.3.7负责颗粒自动包装机的维护保养。
1.3.8负责设备的统筹管理,包括设备的配置、验收、建档、检修和报废等。
1.4 质量部1.4.1 负责对生产部提供的参数要求进行确认;1.4.2 各种检验的准备,取样及样品的测试工作;1.4.3 负责根据检验结果,出具检验报告单;1.4.4负责组织验证方案、验证报告、验证结果的会审会签;1.4.5负责对验证全过程实施监控。
负责验证的协调工作,以保证本验证方案规定项目的顺利实施;1.4.6负责建立验证档案,及时将批准实施的验证资料收存归档;1.4.7负责验证过程的取样、检验、测试及结果报告。
1.5 生产部1.5.1 负责提供与颗粒自动包装机有关的主要参数;1.5.2 负责指定颗粒自动包装机的管理人员及操作人员;1.5.3 负责验证中各种试验材料的准备工作,并派人参加验证工作对机器的操作和清洁维护保养工作;1.5.4组织实施验证方案,参加会签验证方案、验证报告,收集记录验证资料、数据。
1.6 仓储部:负责提供物料支持。
1.7人事部1.7.1负责组织验证人员的相关培训。
1.7.2负责培训的考试及档案归档。
2人员培训确认认可标准:检查并确认本验证涉及人员是否经过培训,考试合格,且持有上岗证。
姓名检查项目培训课时检查结果颗粒自动包装机验证方案及各环节确认、与GMP相关理论知识培训,岗前操作技能的培训与验证相关知识的培训,相关考试合格。
一天□合格□不合格□合格□不合格□合格□不合格□合格□不合格□合格□不合格□合格□不合格结论:检查人:复核人:日期:3概述DXDK80C-H型颗粒自动包装机是我公司固体车间的关键设备,主要用于颗粒剂的袋分装,具有装量稳定、热封效果好、产品包装外观平整、无毛边等优点。
该机器采用CPU集中控制机器的各功能状态,设有人机对话界面;智能型温控仪双路控制横、纵封体温度;在额定范围内无级调整包装速度。
定位张口停机;智能光电定位,亮动、暗动任意转换,抗干扰强,连续三袋光标异常即停机报警;采用容积法计量,制袋精度高,操作维护方便。
设备名称:颗粒自动包装机设备型号:DXDK80C-H型设备编号:出厂日期: 2009年11月生产厂家:北京大松惠基包装机械有限公司使用部门:固体制剂车间主要技术参数项目参数包装速度55-80袋/分计量范围10-50ml制袋尺寸长50-120mm 宽60-85mm电源电压三相四线制380V/50Hz功率0.86kw外型尺寸730 mm×630 mm×1580mm(长×宽×高)重量180kg4 验证的目的对颗粒自动包装机进行设计、安装、运行、性能的验证,以证实符合用户需求标准(URS)的要求,符合药品生产对设备的要求。
确认在规定的SOP操作,设备能稳定运行且各项指标均能达到设计要求,以证明该设备不仅能满足生产需要,而且符合工艺标准要求5 验证所需文件资料名称文件编号文件生效日期存放处颗粒自动包装机说明书--------- --------- 档案室产品合格证--------- --------- 档案室颗粒自动包装机标准操作规程档案室颗粒自动包装机维护保养操作规程档案室颗粒自动包装机清洁标准操作规程档案室结论:文件真实、完整,为现行标准,已经过批准检查人:复核人:日期:6 验证范围本验证方案适用于DXDK80C-H型颗粒自动包装机的验证。
7 验证项目和时间安排计划于2013年 - 月进行颗粒自动包装机设备验证,内容严格按照本验证方案,检查颗粒自动包装机其设计确认、安装确认、运行确认、性能确认达到规定的标准要求。
验证时间:设计确认:从 2013年月日至2013年月日安装确认:从 2013年月日至2013年月日运行确认:从2013年月日至2013年月日性能确认:从 2013年月日至2013年月日起草报告:从 2013年月日至2013年月日8 风险评估8.1目的:降低和控制槽形混合机验证过程中潜在质量风险,保证最终产品质量。
8.2风险因素标准的评定8.2.1风险评估方法:遵循FMEA技术(失效模式效果分析)。
8.2.2失败模式效果分析(FMEA)由三个因素组成:风险的严重性(S)、风险发生的可能性(P)、风险的可测性(D)。
8.3.2.2.1严重性(S):主要针对可能危害产品质量数据完整性的影响。
严重程度分为四个等级:严重性(S) 风险系数风险可能导致的结果高 3 直接影响产品质量要素或工艺与质量数据的可靠性、完整性或可跟踪性。
此风险可导致产品召回或退回;不符合GMP原则,可能引起检查或审计中产生偏差中 2 尽管不存在对产品或数据的相关影响,但仍间接影响产品质量要素或工艺与质量数据的可靠性、完整性或可跟踪性;此风险可能造成资源的浪费。
低 1 尽管此类风险不对产品或数据产生最终影响,但对产品质量要素或工艺与质量数据的可靠性、完整性或可跟踪性仍产生较小影响8.2.2.2可能性(P):测定风险产生的可能性,为建立统一基线,建立以下等级:可能性(P)风险系数风险可能导致的结果高 3 偶尔发生中 2 很少发生低 1 发生可能性极低8.2.3可测性(D):在潜在风险造成危害前,检测发现的可能性,定义如下:可测性(D)风险系数风险可能导致的结果低 3 通过周期性控制可检测到错误中 2 通过应用于每批的常规手动控制或分析可检测到错误高 1 自动控制装置到位,检测错误(例:警报)或错误明显(例:错误导致不能继续进入下一阶段工艺)8.3风险级别评判标准8.3.1风险优先系数(RPN)计算公式RPN=SPD=严重性(S)×可能性(P)×可测性(D)8.3.2风险评价标准风险优先系数RPN风险水平描述RPN>8高风险水平此为不可接受风险。
必须尽快采用控制措施,通过提高可检测性及降低风险产生的可能性来降低最终风险水平。
验证应先集中于确认已采用控制措施且持续执行。
由严重程度为4导致的高风险水平,必须将其降低至RPN最大等于8。
4≤RPN≤8 中等风险水平此风险要求采用控制措施,通过提高可检测性及(或)降低风险产生的可能性来降低最终风险水平。
所采用的措施可以是规程或技术措施,但均应经过验证。
RPN≤4 低风险水平此风险水平为可接受,无需采用额外的控制措施。
风险评估与控制表序号项目风险发生的失败模式风险可能导致的后果严重程度S发生概率p可预知性DRPN值预采取的控制措施1 设计确认设备不符合设计和生产使用要求,不符合GMP要求。
设备不能正常使用 3 2 1 8按照设备用户需求(URS)进行管理2 安装确认设备送货到场后,设备型号不符合,设备损坏,设备及其配件、文件资料不齐。
设备不能正常安装使用,设备资料不齐影响设备的日常使用及培训管理。
3 2 1 8应进行设备开箱验收的确认,确认设备到货部件的名称、型号、数量,是否有损坏及腐蚀,设备配件及文件资料是否齐全。
与药品直接接触的设备材质不符合GMP要求。
影响产品质量。
3218进行设备开箱验收的确认,取得供应商的材质证明。
设备安装环境不符合要求。
缩短设备使用寿命。
污染产品。
3 2 1 8进行安装确认,确认设备安装环境的洁净室等级、温湿度、光线等。
安装定位不合适。
影响日常使用和设备的维修。
2 2 1 4由实际操作员模拟操作,留有足够的安全操作距离及维修空间。
电力供应无接地。
漏电,造成人员伤害。
1 2 1 2有电工在场,进行电力供应有效接地的确认。
电力、压缩空气、水系统等配套设施的连接安装不良;供应的电力、压缩空气压力、水系统等与设备铭牌不符。
设备不能正常使用。
3 2 1 6检查电力安装符合电路图。
检查压缩空气、水系统连接正确。
检测电力、压缩空气、水系统的供应符合设备铭牌的要求。
序号项目风险发生的失败模式风险可能导致的后果严重程度S发生概率p可预知性DRPN值预采取的控制措施.2 安装确认转动设备的主动和被动链轮之间的链条过松或过紧。
设备运行不畅,易打滑、松脱。
2 2 2 8制定管理规程,要求对设备进行定期检查、维护。
各电器元件、接线松动脱落,各零部件安装紧固不良。
设备不能正常安装使用,设备易出现故障。
2 1 2 4制定管理规程,要求对设备定期进行进行电器元件、接线及零部件紧固度的安装确认。
设备与地面间的缝隙不密封或不利于清洁操作。
易积尘,滋生微生物。
2 2 1 4设备安装固定后,检查设备与地面的密封性或规定清洁所需高度。
无紧急停机按钮,或位置不便于应急操作无法应急操作,影响产品质量,对产品造成损失2 1 1 2需确认设备有紧急停机按钮,并方便应急操作电控开关控制功能不符合要求。
设备无法正常操作,易发生安全事故。
2 1 2 4设备安装确认。
检查主电源开关、运行开关情况。
使用的润滑剂不符合要求、设备不润滑。
影响产品质量、影响设备使用寿命。
3 1 2 6检查润滑剂的规格是否符合要求;开机前检查设备的润滑情况和润滑记录。
设备未进行初始清洁、消毒。
设备的初始清洁、消毒不彻底。
污染环境。
2 2 2 8进行设备的初始清洁、消毒确认。
检查清洁效果及清洁、消毒记录。
序号项目风险发生的失败模式风险可能导致的后果严重程度S发生概率p可预知性DRPN值预采取的控制措施.3 运行确认设备未定期维护保养。
设备维护保养不全面。
缩短设备使用寿命;影响正常生产。
3 2 2 12制定设备维护保养SOP,对相关人员进行培训并检查培训记录。
触控面板功能失效。
各种参数不能调整,设备不能正常运转,产品质量无法保证。