冰铜吹炼过程耗氧量及氧利用率仿真计算[1]
冰铜吹炼方案

冰铜吹炼方案冰铜是一种重要的金属材料,广泛应用于电子、航空航天、汽车等领域。
冰铜吹炼是指将含有氧化物杂质的铜化合物加热至高温,通过与氢气反应来除去杂质。
本文将介绍一种高效的冰铜吹炼方案,确保产品质量和生产效率。
一、原材料准备在进行冰铜吹炼之前,需要准备以下原材料:1. 含有氧化物杂质的铜化合物:通常使用氧化铜作为原料,确保其纯度和颗粒度符合要求。
2. 氢气:作为还原剂,用于去除氧化物杂质。
二、设备准备进行冰铜吹炼需要一套专用的设备,包括:1. 吹炼炉:具备高温和密封性能,可以承受冰铜吹炼过程中的高温和压力。
2. 氢气供应系统:确保氢气供应稳定,并具备调节氢气流量的功能。
3. 空气净化系统:用于除去氢气中的杂质,保证吹炼过程的纯净度。
4. 温度监测系统:实时监测吹炼炉内的温度,确保吹炼过程中温度控制在合适的范围内。
三、操作步骤1. 将含有氧化物杂质的铜化合物放入吹炼炉中,并密封好炉门。
2. 打开氢气供应系统,将氢气注入吹炼炉中。
3. 启动吹炼炉,将温度升至设定的吹炼温度。
在升温过程中,需要适当调节氢气流量,确保温度升高的同时,氧化物杂质得以还原。
4. 当吹炼温度达到设定值后,保持一定时间使得冰铜吹炼反应充分进行。
5. 关闭氢气供应系统,停止加热。
待吹炼炉冷却至安全温度后,打开炉门取出冰铜产品。
四、质量控制为确保冰铜吹炼方案的质量稳定,需要进行以下检测和控制:1. 产品纯度检测:使用化学分析方法,检测冰铜中的杂质含量是否符合要求。
2. 产品颗粒度检测:使用粒度分析仪,测量冰铜颗粒的大小分布,确保产品的均匀性。
3. 温度控制:通过温度监测系统实时监控吹炼炉内的温度,确保吹炼过程中温度控制在合适的范围内。
五、优化改进为进一步提高冰铜吹炼方案的效率和质量,可以考虑以下优化改进措施:1. 设备改良:更新吹炼炉和氢气供应系统,提高温度控制和氢气供应的稳定性。
2. 工艺调整:优化吹炼温度、时间和氢气流量的配比,通过实验确定最佳参数组合。
冰铜吹炼

Ni3S2
造渣期:主要以Ni3S2存在; 造铜期:自身的交互反应不能完成,会与 Cu或Cu2O反应生成少量Ni。
CoS
CoS是在冰铜FeS含量非常低时才被氧化。当冰铜 中含铁量低于10%时,CoS开始强烈氧化造渣。也就 是说造渣期末期开始才开始氧化。因此工业上把转炉 渣作为提钴的原料(0.4-0.5%)。
ZnS
造渣期:ZnS被O2或FeO氧化成ZnO,然后与SiO2造 渣。这一部分的锌占冰铜锌总量的70~80%。 15~20%的Zn按下列反应生成锌蒸气进入炉气。 2ZnO + ZnS = 3Zn(g) + SO2(g) ZnS + 2Cu = Cu2S + Zn(g)
造渣期:部分氧化生成的PbO容易与SiO2造渣。部分 PbS被炉气带走,有一部分PbS与PbO反应生成金属 铅。生成的Pb一部分进入烟气中,大部分留在Cu2S 中,到造铜期才被氧化。
PbS
Bi2S3
Bi2S3 在吹炼过程中大部分被氧化为Bi2O3 ,生 成的Bi2O3 与Bi2S3 反应生成金属铋。铋大部分进入 烟气中,少量留在冰铜中。
As与Sb
这 两 种 元 素 的 硫 化 物 大 部 分 氧 化 成 As2O3 和
Sb2O3,少量被氧化成As2O5 和Sb2O5进入炉渣。只有
魏寿昆:《冶金过程热力学》,上海科学技术出版社,1980年
冰铜吹炼分两个阶段的热力学依据
FeS(l) + Cu2O(l) = Cu2S(l) + FeO(l)
ΔG0= -105437-85.48T (J/mol)
实际体系的真实溶液中
[Cu2 S ] 3416 lg 1.72 [ FeS ] T
冰铜吹炼过程耗氧量及氧利用率仿真计算

0 1 2 . / $( *J 渣 E + , 渣 G # * 烟灰 E . J ) ( , 烟灰 ( 、 , 烟灰 ) + + . " ( #G #* 烟灰 E . !
式中: 为- 中*- 为- 物料的质量; .元素的 , + . H 百分含量。 ( ) (不包括底渣中和( 中的( ) 。 # (元素的平衡 * # ( 和产出 ( 分别 (在吹炼全期的投入 ’ ( ,) 0 1 2 ,) 为: ( * 冰铜 E ( , 冰铜 G * 冰铜 E ’ ( ,$ "F!) E+ !E ( ) ( , 渣 G#* 冷料 E , 冷料 ( 、 , 冷料 ) + + + ( ( " ( #G #* 冷料 E ( !
. 0 1 2 " - 3 " 4 5 2 6 4 7 8 4 9 : 5 2 0 6 9 7 ;7 ;" < " = ? 7 ; < " = 6 " = > / 9 ;0 4 : " 2 6 9 ; 2 0 ; 6 B @A
摘 要: 对稳定生产条件下冰铜吹炼过程耗氧量及全期氧气利用率进行仿真计算。根据 ! , , 仿真计 " # $ %三者的平衡关系, 算出吹炼过程的理论耗氧量和全期氧利用率。转炉吹炼全期氧利用率的平均计算值在& 同国外转炉的氧气利用率一致。 ’ (以上,
某些炉次的全期氧气利用率与平均值相差较大, 主要原因是生产记录的失真及生产情况不稳定。
0 理论耗氧量及全期氧率的仿真计算
$ % ! 吹炼过程的物料分析 铜转炉吹炼分造渣期 (简称 % 期) 和造铜期 (简 称 6 期) 两期完成。铜转炉以冰铜为主要原料, 在 转炉中鼓入富氧空气, 于5 + ! 0 5 + F 下开始造渣 期吹炼, 通过氧化和造渣反应除去铁和硫, 倒渣后得 到白冰铜。白冰铜进入造铜期吹炼, 直至得到粗铜。 其中 %期又分为 % , 中间倒出约 & % 0两期, + ( 的熔 渣并加入适量冰铜。某厂炼铜转炉分为新、 老两套 系统, 老系统为期交换作业制度, 造铜期分为 6 , 6 0 两期, 中间停风一次。新系统为炉交换作业制度, 中
冰铜(铜锍)PS转炉熔炼法的工艺过程以及其他吹炼工艺
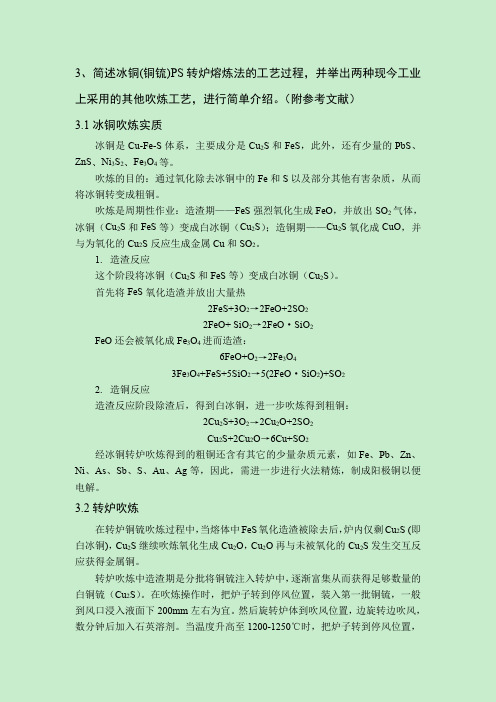
3、简述冰铜(铜锍)PS转炉熔炼法的工艺过程,并举出两种现今工业上采用的其他吹炼工艺,进行简单介绍。
(附参考文献)3.1冰铜吹炼实质冰铜是Cu-Fe-S体系,主要成分是Cu2S和FeS,此外,还有少量的PbS、ZnS、Ni3S2、Fe3O4等。
吹炼的目的:通过氧化除去冰铜中的Fe和S以及部分其他有害杂质,从而将冰铜转变成粗铜。
吹炼是周期性作业:造渣期——FeS强烈氧化生成FeO,并放出SO2气体,冰铜(Cu2S和FeS等)变成白冰铜(Cu2S);造铜期——Cu2S氧化成CuO,并与为氧化的Cu2S反应生成金属Cu和SO2。
1.造渣反应这个阶段将冰铜(Cu2S和FeS等)变成白冰铜(Cu2S)。
首先将FeS氧化造渣并放出大量热2FeS+3O2→2FeO+2SO22FeO+SiO2→2FeO·SiO2FeO还会被氧化成Fe3O4进而造渣:6FeO+O2→2Fe3O43Fe3O4+FeS+5SiO2→5(2FeO·SiO2)+SO22.造铜反应造渣反应阶段除渣后,得到白冰铜,进一步吹炼得到粗铜:2Cu2S+3O2→2Cu2O+2SO2Cu2S+2Cu2O→6Cu+SO2经冰铜转炉吹炼得到的粗铜还含有其它的少量杂质元素,如Fe、Pb、Zn、Ni、As、Sb、S、Au、Ag等,因此,需进一步进行火法精炼,制成阳极铜以便电解。
3.2转炉吹炼在转炉铜锍吹炼过程中,当熔体中FeS氧化造渣被除去后,炉内仅剩Cu2S(即白冰铜),Cu2S继续吹炼氧化生成Cu2O,Cu2O再与未被氧化的Cu2S发生交互反应获得金属铜。
转炉吹炼中造渣期是分批将铜锍注入转炉中,逐渐富集从而获得足够数量的白铜锍(Cu2S)。
在吹炼操作时,把炉子转到停风位置,装入第一批铜锍,一般到风口浸入液面下200mm左右为宜。
然后旋转炉体到吹风位置,边旋转边吹风,数分钟后加入石英溶剂。
当温度升高至1200-1250℃时,把炉子转到停风位置,加入冷料,随后继续吹炼。
Peirce-Smith转炉冰铜吹炼过程中的“数理化”

Peirce-Smith转炉冰铜吹炼过 程中的“数理化”
Mathematics and Chemistry in Matte Converting Process of Peirce-Smith Converter
供稿|王任飞1,石志国2 / WANG Ren-fei1, SHI Zhi-guo2
PS转炉从外观看来是一种旋转式圆筒状的吹炼 炉,内衬的材质大多是使用镁质和镁铬质耐火砖砌 筑,纵向安装有一排通风口,从北京 100032;2. 北京科技大学计算机与通信工程学院,北京 100083
22 2018年 第 3 期
有色金属
入炉内熔体中参与氧化反应[2],在转炉上方正中央还 开有一个非常大的炉口,用于注入熔体、填入冷料 和排出烟气等,如图1所示。
图3 铜转炉吹炼物料出入
造渣期的目的在于获得一定量的白冰铜(Cu2S), 然而并不是在注入第一批冰铜之后就能够马上获得 白冰铜,而是要分批加入,逐渐富集。主要操作为
分批加入冰铜,加入石英溶剂,视温度情况加入冷 料。造铜期的目的就是为了除去白冰铜中的硫,得 到较为纯净的铜[4]。主要的化学反应包括:
23
数学建模
降法在训练集较大的情况下十分低效,每次迭代计 算都需要将整个数据集代入。
冰铜吹炼的优化控制中,吹炼时间终点是决定
第二种方法是使用Normal Equation算法求解。
产品品质的关键性因素。各种材料都由工人加入, 该算法直接使用矩阵运算,在因变量不多的情况下
因此每个阶段终点的判断极大地影响冶炼效率[5]。为 此本文建立了基于历史生成数据的吹炼时间终点预
知识园地
Science Corner
冰铜吹炼

魏寿昆.冶金过程热力学.上海科学技术出版社,1980
少量铜的砷化物和锑化物留在粗铜中。
贵金属
在吹炼过程中,冰铜中的Au、Ag以金属形 态留在粗铜中。 电解精炼时,贵金属富集于阳极泥。
三、冰铜吹炼的生产实践
P-S转炉
生产操作
主要工艺参数
冰铜吹炼 Converting of Matte
一、冰铜吹炼的任务
二、冰铜吹炼的基本原理
优先氧化 吹炼步骤及其主要化学反应 吹炼过程中冰铜成分的变化
1、熔融硫化物氧化 MS+0.5O2=MO+SO2 2、金属硫化物与其它金属氧化物的反应 FeS+MO=MeS+FeO 3、同一金属硫化物与氧化物的交互反应 MS+2MO=3M+SO2
不同金属硫化物的优先氧化
转炉正常操作温度:1150-1300℃
1765K
•
FeS最容易被氧化
•
FeS+MeO->MeS+FeO最容易进行
ZnS
造渣期:ZnS被O2或FeO氧化成ZnO,然后与SiO2造 渣。这一部分的锌占冰铜锌总量的70~80%。 15~20%的Zn按下列反应生成锌蒸气进入炉气。 2ZnO + ZnS = 3Zn(g) + SO2(g) ZnS + 2Cu = Cu2S + Zn(g)
造渣期:部分氧化生成的PbO容易与SiO2造渣。部分 PbS被炉气带走,有一部分PbS与PbO反应生成金属 铅。生成的Pb一部分进入烟气中,大部分留在Cu2S 中,到造铜期才被氧化。
思考题
从热力学原理来说,区分熔炼与吹炼有无 必要? 吹炼的两个阶段中烟气成份的变化? 吹炼操作时过早或者过晚进入造铜期的危 害?(筛炉时熔剂的加入量不合适)
冰铜熔炼实验报告

冰铜熔炼实验报告熔炼车间是冶炼厂的主要生产车间,车间的主要任务是生产铜阳极板。
熔炼车间处理的铜精矿均为外购铜精矿,利用电炉和合成炉生产冰铜。
电炉主要是由矿热电炉处理焙烧车间生产的焙砂,合成炉主要处理经蒸汽干燥机干燥后的干精矿,电炉、合成炉产出的冰铜搭配进入转炉进行吹炼,转炉产出的粗铜进入阳极炉精炼,最后由双园盘浇铸系统产出合格的铜阳极板送精炼厂。
在实习期间主要了解了以下几点,现简单介绍如下。
1.冰铜熔炼铜精矿首先熔炼获得冰铜,然后将冰铜吹炼成粗铜。
冰铜熔炼是在高温和氧化气氛条件下将硫化铜精矿熔化生产MeS共熔体的方法,又称造锍熔炼。
冰铜熔炼将精矿中的铜富集于冰铜中,而大部分铁的氧化物与加入的熔剂造渣。
冰铜与炉渣由于性质差别极大而分离。
冰铜熔炼分为鼓风炉熔炼、反射炉熔炼、电炉熔炼、电炉熔炼、闪速熔炼及一步炼铜等。
尽管设备不同,冶炼过程的实质是相同的,都属于氧化熔炼。
高温下,炉料受热后形成低价稳定的化合物,随着形成低熔点共晶组分熔化析出,即形成初冰铜和初渣。
其最终成分的形成是在熔池中完成。
熔炼的主产物冰铜是由Cu2S、Fe S组成的合量,其中还溶解了一定数量铁的氧化物和其它硫化物,如Ni3S2、CoS、PbS、ZnS等。
一般Cu+Fe+S占冰铜总量的80%~90%。
炉料中的金银及铂族元素在熔炼过程中几乎全部进入冰铜中。
Se、Te、As、Sb、Bi等元素也部分地溶解在冰铜中。
冰铜品位的选择取决于下列因素:炉料的性质和成分、熔炼特性、经济条件等。
熔炼生精矿时,冰铜品位不能在大范围内变动,但可用预先焙烧来调整,焙烧程度愈大,熔炼时冰铜品位愈高,反之亦然。
冰铜品位越低,吹炼所需时间愈长,吹炼时能耗愈大,炉衬消耗愈快。
实践证明,选择冰铜品位为37~42%较为合理。
但冰铜品位太高也存在一些问题。
(1)冰铜品位高,铜在炉渣中的损失增多。
(2)产生高品位冰铜,需延长精矿的焙烧时间,降低了焙烧的生产率,并增加烟尘产出量。
氧气底吹铜熔炼过程多相平衡模拟

氧气底吹铜熔炼过程多相平衡模拟王亲猛;郭学益;王松松;廖立乐;田庆华【期刊名称】《中国有色金属学报(英文版)》【年(卷),期】2017(027)011【摘要】基于氧气底吹工艺特性和最小吉布斯自由能原理,构建了氧气底吹铜熔炼热力学计算模型.模拟结果表明:在给定的稳定生产条件下,铜锍中Cu、Fe和S含量分别是71.08%、7.15%和17.51%,渣中Fe、SiO2和Cu含量分别是42.17%、25.05%和3.16%.微量元素在底吹熔炼过程中气相、渣相和铜锍相三相间的模拟分配比例为:砷82.69%、11.22%和6.09%;锑16.57%、70.63%和12.80%;铋68.93%、11.30%和19.77%;铅19.70%、24.75%和55.55%;锌17.94%、64.28%和17.79%.将模拟结果和实际生产数据进行验证,结果一致,表明了该多相平衡热力学计算模型具有可靠性,可以指导氧气底吹铜熔炼生产实践,优化工艺操作参数.%A computational thermodynamics model for the oxygen bottom-blown copper smelting process (Shuikoushan, SKS process) was established, based on the SKS smelting characteristics and theory of Gibbs free energy minimization. The calculated results of the model show that, under the given stable production condition, the contents of Cu, Fe and S in matte are 71.08%, 7.15% and 17.51%, and the contents of Fe, SiO2 and Cu in slag are 42.17%, 25.05% and 3.16%. The calculated fractional distributions of minor elements among gas, slag and matte phases are As 82.69%,11.22%, 6.09%, Sb 16.57%, 70.63%, 12.80%, Bi 68.93%, 11.30%, 19.77%, Pb 19.70%, 24.75%, 55.55% and Zn 17.94%, 64.28%, 17.79%, respectively. Thecalculated results of the multiphase equilibrium model agree well with the actual industrial production data, indicating that the credibility of the model is validated. Therefore, the model could be used to monitor and optimize the industrial operations of SKS process.【总页数】9页(P2503-2511)【作者】王亲猛;郭学益;王松松;廖立乐;田庆华【作者单位】中南大学资源加工与生物工程学院长沙 410083;中南大学冶金与环境学院,长沙 410083;中南大学冶金与环境学院,长沙 410083;中南大学冶金与环境学院,长沙 410083;中南大学冶金与环境学院,长沙 410083【正文语种】中文因版权原因,仅展示原文概要,查看原文内容请购买。