LF炉冶炼超低硫钢的工艺条件
超低硫钢冶炼生产中的脱硫工艺

超低硫钢冶炼中的脱硫工艺摘要:炼钢过程中脱硫工艺的好坏是炼钢质量好坏的重要决定因素。
本文研究了超低硫钢冶炼中的脱硫工艺,利用深脱硫工艺,通过转炉冶炼控硫,达到了预期效果。
关键词:脱硫;炼钢;转炉冶炼;炉渣中图分类号:TQ111.16 献标识码:A 文章编号:1674-098X(2010)08(a)-0000-001 炼钢过程脱硫的意义对于大多数钢种,硫是有害的元素。
钢中的含硫量高,会使钢材的加工性能和使用性能大大降低,在热加工过程中甚至会造成“热脆”断裂。
它在钢中所形成的硫化物降低钢的韧性,硫化锰夹杂是钢基体点腐蚀的发源地,钢的氢脆与钢中硫化物夹杂也有密切关系。
随着科学技术的进步,用户对钢材质量的要求越来越高,尤其对钢材的含硫量提出了更严格的要求。
现在很多重要用途的钢中硫含量越来越低,例如一般深冲钢、冷拉钢要求S<0.015%,特殊深冲钢、高强度钢、轴承钢要求S<0.010%,航空、石油、原子能等工业用钢要求S<0.002%。
此外,随着钢铁工业的技术进步,为了节能降耗、提高生产率和产品质量,钢铁企业积极进行优化工艺结构,连铸工艺本身要求钢水的含硫量低才能发挥连铸工艺的优势,一般用于连铸的钢水要求S<0.020%才能保证避免连铸坯出现“热裂”,得到具有良好表面质量的连铸坯。
当S<0.008%时,可使连铸的成坯率增加2%。
因此,脱硫对钢铁企业进行产品结构的调整、扩大产品品种、生产高附加值产品、节能降耗、高产低耗、提高产品的市场竞争力和经济效益等都具有十分重要的意义。
2 影响脱硫的因素2.1 炉渣物理性质对脱硫的影响(l) 炉渣粘度对脱硫的影响炉渣粘度是影响渣一钢界面脱硫反应的重要因素,液相中的传质速率与熔渣的粘度成反比。
在精炼脱硫过程中,若炉渣粘度过大,则恶化了脱硫的动力学条件,造成脱硫困难。
提高炉渣的流动性,可以减小乳化渣滴的平均直径,从而增大渣一钢的接触面积,促进脱硫。
UHPLF电炉冶炼工艺技术操作规程

常州中天EAF、LF炉冶炼工艺技术操作规程1.1冶炼前准备及注意事项1.1.1新炉冶炼第一炉, 只许冶炼无特殊规定旳低碳钢或45#钢。
1.1.2新炉前两炉应注意吹氧操作, 氧气工作压力控制在0.7—0.9Mpa, 防止大喷。
1.1.3冶炼前, 必须清晰冶炼钢种旳条件及配套设备旳运行状况, 否则不得安排生产计划。
1.1.4多种原材料尤其是铁合金和增碳剂, 使用前, 必须知其重要旳成分含量, 如不详或混号者, 不得使用。
1.1.5出钢前, 出钢料仓应按照各钢种规定备料。
6下一炉需出净钢渣时, 一定要精确估测本炉次旳留钢量, 并合理调整装入量, 防止下一炉次旳钢水出不净或钢水欠缺太多。
1.1.7冶炼前应仔细检查各部分水冷系统, 机电设备, 液压设备和控制仪表及钢液测量系统, 如有故障, 及时联络处理。
1. 1. 8如操作人员在操作过程中发现下列报警, 应及时告知有经验旳电气人员及时检修(1)EAF变压器(2)气体吹扫系统旳主电机(3)皮带运送机、泵和振动给料器系统旳所有电机和辅助电气系统。
9冶炼前应检查调整电极长度, 保证冶炼旳正常进行。
1.2 1. 1. 9. 1接电极: 吹净电极螺纹处积灰, 对正, 旋紧电极接头和电极。
1.31.1.9.2放电极:调整电极, 使电极夹持器下到最低位置时,电极头部距炉底高度不得不不小于300mm, 且能满足冶炼需要, 电极夹持器不得夹在电极接缝处正面200mm内(白线以内), 防止电极螺纹处损坏, 折断电极。
1.41.1.9.3换电极:假如电极旳端部已出电炉盖旳弧形坑, 且伸出夹持器旳距离只有几厘米, 则更换电极。
更换电极时, 将一种合适旳吊具挂到行车中, 稍微用力吊住电极, 打开夹持器, 吊出电极至电极接长站, 将接好旳电极放入电极夹持器内, 调整电极长度。
1.5补炉1每炉出钢后, 炉长要对炉壁, 渣线, 炉盖中间耐材部位, 出钢口及水冷元件进行检查。
2。
2出钢口旳检查, 更换, 填充。
LF炉精炼工艺的探讨
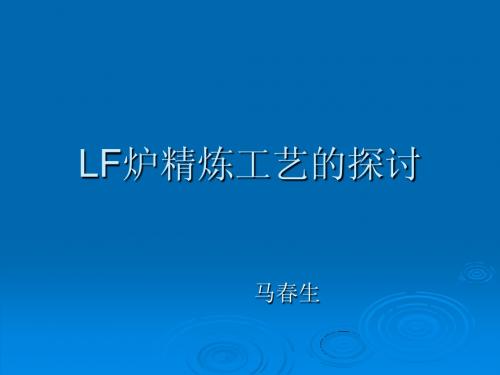
钢包覆盖剂的应用
1、吸附夹杂 2、保温,隔绝空气 3、避免结壳,保持钢包清洁
要求:良好铺展性、保温性、较高熔点
设置挡渣堰坝
改变钢液流动,强制夹杂物上浮
连铸中包渣的应用
中包渣作用: 保温、绝空气、吸附夹杂 半熔融层-10mm
结构:四层结构:
熔融层-5mm
低硅
长效发泡
吸附夹杂
在出钢过程中已经进行了沉淀脱氧,在此主要是 进行扩散脱氧,要求“ 炉渣有良好的还原性能 有良好的发泡性能(埋弧)、节电0.047kwa/t. ℃ 有良好的捕抓、富聚夹杂物的能力,并且有较大 的容量 提高脱氧材料的利用率 对钢包的侵蚀要少
CaF2的应用
。
4Al+3O2→2Al2O3 96 :96 1 :1 3FeO+2Al →Al2O3+3Fe 216:54 4 :1 Fe2O3+2Al=Al2O3+2Fe 160:54 3 : 4 以上计算全部按FeO计算 为考虑SiO2及MnO等与Al的反应及与空氧燃烧,打折扣30%则G=90+22K
CaC2脱氧剂
渣洗
渣洗的目的:降低炉渣氧化性 形成合适的能脱硫能吸收上浮夹杂物的精炼渣 作用:稀释渣中(FeO)量,为LF冶炼创造条件,缩短时间 个别钢中经改质后可不通过LF炉直接送连然(薄板坯) 适合的熔渣组成,以利于保温,隔绝空气和吸附夹杂 便于LF炉起弧,强化钢中进一步脱氧和提高电能利用率 要求:在钢中迅速熔化 表面能力大,能吸附钢中的脱氧产物并使其上浮 12CaO.7Al2O的熔点为1360℃,表面能力系数为8, 并具有一定的脱硫能力,合成渣的基料设想为: 石灰:保证炉渣碱度为3.5-4 萤石:加入6%萤石可适当提高渣流动性 12CaO.7Al2O:在钢中速熔,并能捕捉夹杂物及脱氧产物 脱氧剂(钝化电石):可脱渣中(FeO)并产生气体脱氧产物不污染钢水 CO3发泡,强化搅拌,促进合成渣熔化及夹杂上浮 镁质材料:保证渣中的(MgO)为8%减少渣对钢包的侵蚀
LF炉深脱硫工艺实践

近年来,为了使钢材的性能更好,硫含量低于50ppm的超低硫钢(如耐氢诱裂纹的管线钢、高强度钢等)的需求不断增长,故钢水的深脱硫技术在整个炼钢过程中起着日益重要的作用。
随着用户对钢质量要求的不断提高, 特别是高质量的管线钢、容器钢、耐酸钢等均要求[S] ≤0.005%甚至[S] ≤0.001%[1]。
日本某厂通过炉外精炼的有关操作已可将钢中的硫降到2ppm的水平而我国的宝钢、武钢,鞍钢、本钢、攀钢现在都可以生产20PPM以下的低硫钢。
脱硫热力学现在我们简单的介绍以下脱硫的基本理论S渣钢间的脱硫反应[S]+(CaO)=(CaS)+[O] △G0=98474-22.82T[S]+(MnO)=(MnS)+[O] △G0=133224-33.49T[S]+(MgO)=(MgS)+[O] △G0=191462-32.70T硫在金属液中存在三种形式:即[FeS]、[S]和S2-。
FeS它既溶于钢液,也溶于熔渣。
渣钢间的脱硫反应:首先钢液中硫扩散至熔渣中即[FeS]→(FeS),进入熔渣中的(FeS)与游离的CaO(或MnO)结合成稳定的CaS或MnS。
根据熔渣的离子理论,脱硫反应为:[S]+(O2-)=(S2-)+[O]上式反应的平衡常数可写为:里查森(Richardson )定义硫容表达了炉渣容纳硫的能力。
将硫分配比定义为:影响钢渣间脱硫反应的因素炼钢温度的影响。
钢渣间的脱硫反应属于吸热反应,吸热在108.2-128kJ/mol之间,因此,高温有利于脱硫反应进行。
温度的重要影响主要体现在高温能促进石灰溶解和提高炉渣流动性。
炉渣碱度的影响。
炉渣碱度高,游离CaO多,或(O2-)增大,有利于脱硫。
但过高的碱度,常出现炉渣粘度增加,反而降低脱硫效果。
炉渣中(FeO)的影响。
从热力学角度可以看出,(FeO)高不利于脱硫。
当炉渣碱度高时、流动性差时,炉渣中有一定量的(FeO),可助熔化渣。
金属液成分的影响。
金属液中[C]、[Si]能增加硫的活度系数f[S],降低氧活度,有利于脱硫。
LF精炼脱硫工艺

行了研究,他们认为铝酸盐与硅酸盐相比脱硫 速度和硫容更大,但该渣系的炉渣流动性稍差。
4
LF炉精炼渣脱硫工艺及理论
3、CaO-Al2O3-CaF2渣系 国内部分钢厂和国外很多钢厂都在CaO-Al2O3
渣系的基础上加入适量的CaF2形成CaO-Al2O3CaF2渣系,但在实际生产过程中,由于炉衬受 到侵蚀等原因会带入一定的MgO,作为脱氧产 物和精炼渣原料中都会带入部分SiO2,因而实 际渣系为CaO-Al2O3-CaF2-MgO- SiO2五元渣 系。
16
LF炉精炼渣脱硫工艺及理论
CaF2与CaO等形成一系列低熔点共晶物来 助熔化渣,但在电弧温度下,将有下述反应发 生。
产生的SiF4为气体,并随炉气散失。
17
LF炉精炼渣脱硫工艺及理论
4、Al2O3在精炼渣中的作用 根据CaO-SiO2-Al2O3三元相图,随着渣中
Al2O3含量在一定范围内的提高,渣的熔化温度 降低。
29
LF炉精炼渣脱硫工艺及理论
炉渣脱硫反应表明,随着钢中氧含量的提高, 将抑制脱硫反应的进行,应尽量采取措施降低 钢中氧含量。
渣中氧含量也会影响到钢中的溶解氧含量。 在渣-钢间存在着氧的平衡分配,炉渣氧化 性较高时,炉渣会向钢中供氧,增加钢液中的 溶解氧量。
30
LF炉精炼渣脱硫工艺及理论
9、LF炉脱硫的优势: 1) 有良好的还原性气氛; 2) 能造含 Al2O3 的高碱度渣; 3) 包底吹氩搅拌,渣钢充分,脱硫的动力学条件
液相中的传质速率与熔渣的粘度成反比。 若炉渣粘度过大,则恶化了脱硫的动力学条件,
造成脱硫困难。 提高炉渣的流动性,可以减小乳化渣滴的平均直
氧气转炉出钢脱硫-LF精炼生产超低硫钢的工艺

00 0 , . 2 % 通过 B F出钢过程加入 1 0 g二元合 成渣 C O C F 、0 g O 0k 0 a —a 220k 铝粒 , 并加入硅锰 和硅 铝钡合金 , 可使钢中 硫含量降低 0 0 7 . 0 % 00 8 , .0 % 脱硫 率达 3 %。在 L 0 F精炼 时 , 过进一 步加入 合成渣 80 k ,0 9 0L m n 通 0 g 60— 0 / it  ̄ r 氩, 加热后喂 6 0m硅钙线 ,0— 5L mi@  ̄ 1 i, 渣碱 度 R= . 5 5 钢 中硫 含量进 一步降低至0 0 1 ~ 0 3 4 / n , 0mn 终 45— . , .0 %
维普资讯
・
4 ・ 20 4 06年 1 1月
第2 7卷第 6期
特殊 钢
S EC AL S E L P I T E
V0. 7 No 6 12 . . N v mb r 2 o o e e o 6
氧气 转炉 出钢 脱 硫 -F精炼 生产 超 低 硫 钢 的工 艺 L
Ha n oNig 。Wa gXih a ,Wa gHato n n u n i ,L n u mi a iHo g ,C i Ai n ,Wa g G oin ,G n in n iLn n u l o gJa a d L i a ( col f ea ug a a dE ooi l n n e n ,U i r t o c neadTc nl y B i g10 8 ; 1Sho o t lr cl n clg a E g er g nv sy f i c n eh o g , ei 00 3 M l i c i i e i S e o j n 2 Sogn ru op B in 0 0 1 huagGopC r , eig10 ) j 4
LF精炼炉精炼用材料技术条件

LF精炼炉精炼用材料技术条件
1.原材料:
2.温度控制:
3.耐腐蚀性:
在炼化过程中,炉内会存在一定的酸碱性气氛,液态钢水和钢渣中也
可能含有酸性或碱性的化合物。
因此,材料需要具有较好的耐腐蚀性,能
够抵御腐蚀性气体和化学物质的侵蚀。
常用的耐腐蚀金属材料有不锈钢
(如316L不锈钢、904L不锈钢)和耐酸碱陶瓷材料(如氧化铝陶瓷)。
4.导热性:
在炼化过程中,精炼炉需要快速达到设定温度,并保持温度的均匀分布。
因此,材料需要具有较好的导热性,能够快速传导热量并均匀分布。
常用的导热材料有铜、铝和铜合金。
5.尺寸稳定性:
炼化过程中,精炼炉内会受到较大的热膨胀和冷缩的影响,这会对炉
内材料的尺寸稳定性提出要求。
材料应具有较低的热膨胀系数,以避免因
热胀冷缩而导致材料破裂或变形。
常用的低热膨胀材料有石墨和陶瓷材料。
6.密封性:
精炼炉需要具有良好的密封性,以避免炉内气体泄漏。
材料需要具有
较好的密封性能,能够抵御高温气体和化学物质的渗透。
常用的密封材料
有石棉、橡胶和金属密封垫片。
总结:
LF精炼炉炼化用材料的技术条件主要包括耐高温能力、耐腐蚀性、导热性、尺寸稳定性和密封性。
常用的炼炉材料包括耐高温合金、陶瓷材料、不锈钢、铜合金、石墨和陶瓷材料等。
这些材料能够满足高温环境下的需求,并确保精炼炉的炼化效果和使用寿命。
深脱硫钢在LF炉中的脱硫处理工艺分析

深脱硫钢在LF炉中的脱硫处理工艺分析近年来,随着环保要求的不断提高,钢铁行业对钢的质量要求越来越高。
以深脱硫钢为例,它需要通过一些专门的处理工艺来脱除钢中的硫元素,提高产品的质量。
下面,我们将详细介绍深脱硫钢在LF炉中的脱硫处理工艺。
1. 深脱硫钢的特点及脱硫处理工艺需求深脱硫钢是指钢中硫含量较低的钢种,在一般情况下,硫含量应该在0.005%以下,如果无法达到这个标准,其腐蚀性和机械强度将下降,从而影响产品的质量。
为了达到这样的硫含量,需要使用特定的脱硫剂和设备,并在LF炉中进行脱硫处理。
深脱硫钢需要的脱硫剂一般为2-3mm的石灰石块,它可以在LF炉中迅速分解生成CO2,同时硫元素与钙的化学反应将硫转化为CaS,在渣中形成CaS类物质。
(1)脱硫剂的加入在LF炉的转炉内,需要先加入一定数量的石灰石块(脱硫剂)以达到脱硫的效果。
其加石量一般为顶砖重的0.5%-1.0%。
加入的时间一般为钢水处理的中期,也就是钢水进入LF炉后5-10分钟之后,这样可以让脱硫剂充分产生反应。
(2)温度控制温度控制是LF炉脱硫过程中的关键一步。
石灰石的分解生成CO2的反应速度与温度有关,温度越高,反应速度越快。
因此,在加入脱硫剂后,需要增加炉温,一般控制在1600℃以上,这样可以使脱硫剂充分分解产生反应,为脱除钢水中的硫元素提供充足的时间和工艺条件。
(3)搅拌处理在搅拌过程中,需要将钢水流动起来,以便让脱硫剂能够充分分散和载运。
LF炉的搅拌一般采用氧气喷吹,通过向钢水中注气的方式来搅动钢水,这样可以使石灰石与钢水的接触更加充分。
(4)渣的剔除在脱硫完成后,需要将反应生成的渣进行剔除,这个过程需要控制好剔渣速度和剔渣时间,以避免过剩的渣物质对钢水的影响。
3. 成效评估处理好的钢水,其硫含量应该控制在0.002%-0.005%之间,其机械性能、物理性能和腐蚀性能等指标也需要符合相关的行业标准。
通过合理的工艺处理和评估,可以达到满足深脱硫钢质量要求的目标。
- 1、下载文档前请自行甄别文档内容的完整性,平台不提供额外的编辑、内容补充、找答案等附加服务。
- 2、"仅部分预览"的文档,不可在线预览部分如存在完整性等问题,可反馈申请退款(可完整预览的文档不适用该条件!)。
- 3、如文档侵犯您的权益,请联系客服反馈,我们会尽快为您处理(人工客服工作时间:9:00-18:30)。
收稿日期:2002203218基金项目:国家“九五”重点科技攻关项目(952524202202)・作者简介:姜周华(1963-),男,浙江萧山人,东北大学教授,博士;王文忠(1935-),男,辽宁复县人,东北大学教授,博士生导师・2002年10月第23卷第10期东北大学学报(自然科学版)Journal of Northeastern University (Natural Science )Oct. 2002Vol 123,No.10文章编号:100523026(2002)1020952204LF 炉冶炼超低硫钢的工艺条件姜周华,张贺艳,战东平,王文忠(东北大学材料与冶金学院,辽宁沈阳 110004)摘 要:提出了采用热力学计算分析确定L F 炉冶炼超低硫钢工艺条件的方法・分析表明,可通过提高炉渣碱度、强化渣钢脱氧、控制渣钢原始硫质量分数和渣质量,来实现超低硫钢的冶炼・150t L F 炉生产实践表明,在原始钢水硫平均为010146%条件下,通过控制规定的工艺条件,经L F 处理后的钢水硫质量分数平均可达010044%・再经VD 处理后,可实现成品硫质量分数为010027%的超低硫钢生产・在上述条件基础上,将原始硫质量分数控制在010058%以下或保证渣金硫的分配比在250以上或采用双渣操作,L F 炉可精炼01002%以下极低硫钢・关 键 词:L F 炉;二次精炼;脱硫;超低硫钢中图分类号:TG 113.14 文献标识码:A目前像石油管线、IF 钢和电工钢等超低硫钢成品硫质量分数一般要求在510×10-3%以下,对高质量品种要达到210×10-3%以下・尽管就精炼渣的硫容量及渣钢间硫的分配比前人已做了许多基础研究[1~7],但就L F 炉精炼在超低硫钢实际工艺条件缺少理论分析・1 研究对象本文以某厂150t L F 炉精炼过程脱硫为计算对象・其中每炉造渣料的加入量平均为1300kg (817kg/t ),但由于电炉出钢时下渣,EB T 出钢口填充料,合金元素氧化和包衬耐材侵蚀等炉渣来源,因而实际L F 炉内渣质量约2250kg (即15kg/t 钢)・钢水和炉渣成分见表1・表1 冶炼钢种LF 终点钢水和炉渣成分(质量分数)典型值Table 1 The typical chemical compo sition of liquidsteel and slag after LF refining % CSiMnPSCaO SiO 2Al 2O 3MgO01195012501550101010055510276钢水中全铝质量分数波动在0101%~0105%之间,对应的酸溶铝一般为01005%~0102%之间・而钢水中全氧一般波动在(115~215)×10-3%之间,而采用固体电解质定氧探头测定的钢水溶解氧一般为(5~10)×10-4范围・精炼终点炉渣中(FeO +MnO )通常小于1%・2 L F 炉精炼过程渣金脱硫反应热力学计算与分析211 精炼终点渣金硫的平衡分配比及钢水硫质量分数的计算公式若忽略气相脱硫的作用,根据硫的质量守恒可以导出:w [S ]=w (S )0m sm m +w [S ]01+m sm m LS(1)式中,w [S ]为精炼终点钢水的硫质量分数,%;w (S )0,w [S ]0分别为反应前渣中和钢中的原始硫质量分数,%;m s ,m m 分别为熔渣和钢水的质量,kg ;L S 为渣金间硫的分配比・由式(1)可知,要计算钢水中的硫质量分数关键是获得渣金间硫的平衡分配比L S ・研究表明[8,9],此值可由式(2)计算・lg L S =21920-54640ΛT+4316Λ+lg f S -lg a [O ]-2319(2)可见,影响渣金硫的平衡分配比的因素包括炉渣碱度(Λ)、钢水中的活度系数(f S )、钢水的平衡氧活度(a [O ])和温度(T/K )・其中炉渣光学碱度可根据炉渣成分计算得到,而活度系数(f S )可由钢水成分计算得到(在低硫质量分数下f S ≈1)・而钢水的平衡氧活度可由下面两种途径来计算・1)由与钢水氧活度平衡的炉渣中(FeO )质量分数来计算・根据渣金氧平衡可得[11]:lg a [O ]=lg γFeO +lg x FeO -6150T+2160(3)在1873K 下CaO 2SiO 22Al 2O 32MgO 四元精炼渣系中氧化铁的活度系数(γFeO )的实验回归方程为[12]lg γFeO =01676w (MgO )+01267w (Al 2O 3)-19107w (S iO 2)+010214w (CaO )-01047(4)2)对于铝镇静钢,钢液中氧活度主要由铝质量分数控制・由Al 2O 平衡反应可得:lg a [O ]=13lg a Al 2O 3-23lg a [Al ]-1364900T-20163(5)1873K 下CaO 2SiO 22Al 2O 32MgO 四元精炼渣系中Al 2O 3的活度由以下回归方程表示[10]:lg a Al 2O 3=-01275w (CaO )+01167w (MgO )w (SiO 2)+01033w (Al 2O 3)-11560(6)212 计算结果与分析(1)炉渣氧化性对脱硫效果的影响图1的计算结果表明,随着渣中FeO 质量分数的降低,L S迅速增大・因此,从热力学角度,强化炉渣脱氧对提高脱硫效果至关重要・由图还可知,实际硫分配比也随着渣中(FeO )质量分数的降低而显著提高・但实际值要明显高于理论计算值,其原因是渣金间氧并没有达到平衡・这是因为实际L F 炉中精炼终点(FeO )质量分数通常在015%~110%之间,如果达到平衡,可以算出其对应的氧活度为(2128~4156)×10-3・而根据现场用定氧探头测定钢水溶解氧质量分数通常在(5~10)×10-4,此值大大低于与渣中FeO 平衡的氧・图1 渣中(FeO )质量分数对渣金间硫的平衡分配比的影响Fig.1 E ffect of FeO content inslag on sulfurpartial ratio between slag and steel(2)钢水氧化性对脱硫效果的影响通常精炼终点实际溶解铝质量分数在01005%~0102%之间,计算得到的与铝平衡的氧活度在(2188~7126)×10-4,其范围与定氧探头的实测值相一致・这说明钢水中的氧确实受Al 的控制・由图2可知,随着钢中溶解铝质量分数的增加,渣金平衡分配比也相应增加・因此,加强对钢水的脱氧也有利于脱硫反应的进行・从图中还不难发现,实际L F 炉终点渣金硫的分配比也随着钢中铝质量分数的增加而增加,但实测值要低于计算值,这说明渣本体中的硫质量分数要低于渣金界面的值,即在界面渣相侧存在硫的浓度梯度・图2 钢中溶解铝质量分数对钢水平衡氧活度及渣金硫的平衡分配比的影响Fig.2 E ffect of soluble aluminum content in steelon oxygen activity and sulfur partial ratio(3)光学碱度和温度对脱硫效果的影响当w (Al 2O 3)=27%,w (MgO)=8%,w (CaO )+w (SiO 2)=65%,T =1873K 时,不同CaO 或SiO 2质量分数下光学碱度和硫分配比的计算值见图3・可见,随着渣中CaO 质量分数的提高,SiO 2质量分数降低,硫的分配比显著提高・例如,在现有条件下若渣中SiO 2的质量分数从10%下降至5%,则硫的分配比可从8115提高到图3 炉渣成分对光学碱度和硫的平衡分配比的影响Fig.3 E ffect of slag compo sition on its optical basicityand sulfur partial ratio359第10期 姜周华等:L F 炉冶炼超低硫钢的工艺条件22813・设a [O ]=10-3,f S =1,当Λ=01769,精炼温度从1600℃提高到1650℃时,硫的分配比从8115提高到16813・(4)渣质量及渣钢中原始硫质量分数对精炼终点硫质量分数的影响由图4可知,随着渣质量的增加,钢中硫质量分数显著降低・从图5和6可知,随着钢中和渣中原始硫质量分数降低,精炼终点钢水硫质量分数图4 渣质量对LF 精炼终点钢水硫质量分数的影响Fig.4 Relation between sulfur content insteel and slagquantity图5 钢水原始硫质量分数对精炼终点钢水硫质量分数影响Fig.5 Relation between sulfur content in steelafter refining and initial sulfur content insteel图6 渣中原始硫质量分数对钢中精炼终点硫质量分数的影响Fig.6 Relation between sulfur content in steel afterrefining and initial sulfur content in slag也相应降低・相对而言,钢水原始硫质量分数对钢中终点硫影响更大・因此,控制炉料中的硫质量分数对生产低硫钢也非常重要・3 L F 炉冶炼超低硫钢的工艺条件及实践从以上分析计算可知,降低钢水中硫质量分数实现超低硫钢冶炼工艺条件有以下几个方面・(1)控制炉渣成分,提高光学碱度・为此,炉渣中SiO 2的质量分数要控制在10%以下,最好达到5%的水平・对于特殊场合,可以添加BaO ,Na 2O ,Li 2O 等碱度更高的组元・(2)强化对炉渣和钢水的脱氧・向炉渣中加入扩散脱氧剂,使渣中(FeO )质量分数达到1%甚至015%以下・控制钢中酸溶铝质量分数,使钢水中氧活度控制在110×10-3以下・(3)较高的精炼温度和良好的底氩搅拌工艺也是重要脱硫工艺条件・根据式(2)并结合现场实测数据,表2列出了为达到一定的硫的分配比必须达到的实际工艺条件・表2 渣金间硫的分配比与精炼工艺的关系Table 2 Relation between sulfur partial ratio and refining proce ss炉渣成分(质量分数)/%CaO SiO 2Al 2O 3MgO 光学碱度Λ渣、钢氧化性w (FeO )/%w [Al ]/%温度t /℃渣金硫的分配比L S50~55≤1020~306~10≥0175≤110≥010081550~1600100≥55≤820~306~10≥0177≤018≥010101550~1600150≥58≤725~306~9≥0178≤015≥010201550~1600200≥58≤525~306~9≥0179≤013≥010251550~1600250(4)为了保证LF 炉精炼终点的硫质量分数小于某一目标值,在保证上述精炼工艺的条件下,必须对炉渣和钢水的原始硫质量分数进行限制,同时也保证相应的渣质量,必要时可进行换渣操作・表3列出两种硫质量分数目标值下需要控制的工艺条件・根据表3中的工艺条件在某厂150t LF 炉批量生产低硫钢的实绩如下:初炼炉出钢时钢水硫的平均值为010146%,由于在出钢过程加入高碱度的精炼渣,LF 到位时钢水硫降至010108%,在LF 精炼过程中再加入一部分渣料,并加入CaC 2或Al 屑对炉渣扩散脱氧,使渣中(FeO )控制在110%以下,这样L S 可达100以上,至LF 结束时硫质量分数平均459东北大学学报(自然科学版) 第23卷可降至010044%,后步经过VD 处理后可进一步脱硫,最终产品的硫质量分数的平均值为010027%,达到了超低硫的水平・如果要使L F 炉精炼终点硫质量分数达到01002%极低硫水平,如表3所示,有以下几种实现途径・(1)在保证分配比约150,渣质量基本不增加的条件下,重点控制渣钢中的原始硫质量分数,特别是要保证初炼炉出钢时硫小于010058%・但这对于初炼炉难度很大,如果进一步提高碱度强化脱硫,使分配比达到200水平,钢水初始硫质量分数可适当放宽至010065%・表3 不同目标硫质量分数下的精炼工艺条件控制值Table 3 The controlled proce ss conditions forrefining of low sulfur steel 终点硫目标值w [S]a /%分配比L S 渣中初始硫w (S )0/%钢水初始硫w [S]0/%渣金比m s /m m≤01005100~150≤0110≤01015001015≤01002150≤0105≤01005801015200≤0110≤01006501015200≤0110≤01010001025250≤0110≤010********(2)采用双渣操作,使总渣钢质量比达到01025,并保证渣金硫的分配比达到200左右,钢水初始硫质量分数可放宽至0101%・(3)进一步采取措施提高碱度并强化扩散脱氧,加强搅拌,适当延长精炼时间可以使得渣金间硫的分配比达到250以上,这样即使采用单渣操作,也可以使精炼终点钢水达到极低硫水平・4 结 论(1)影响L F 炉精炼终点的主要因素包括炉渣的光学碱度、炉渣和钢水的氧化性、精炼温度、渣钢的原始硫质量分数和渣质量・(2)随着炉渣碱度的提高,渣金间硫的分配比显著提高・提高炉渣碱度的关键不仅在于保证CaO 的质量分数,而且在于尽量降低渣中SiO 2质量分数・(3)某厂150t L F 炉的生产实践证明,采用本文提出的确定L F 炉冶炼超低硫钢的工艺条件的方法是可行的・L F 炉终点的硫质量分数平均可达到010044%,再经VD 处理,铸坯硫质量分数平均为010027%超低硫水平・(4)通过进一步提高炉渣碱度,强化渣金脱氧,控制渣钢中原始硫质量分数以及采取换渣操作等技术措施,LF 炉可冶炼01002%以下极低硫钢・参考文献:[1]Cameron J ,G ibbons J B ,Taylor J.Calcium sulphide solubilities and lime activities in the lime 2alumina 2silica system[J ].J of Iron and Steel Instit ute ,1966,194(12):1223-1228.[2]Ozturk B ,Turkdogan E T.Equilibrium sulphur distribution between molten calcium aluminate and steel ,Part Ⅰ[J ].Metal Science ,1984,18:299-306.[3]Ozturk B ,Turkdogan E T.Equilibrium sulphur distribution between molten calcium aluminate and steel ,Part Ⅱ[J ].Metal Science ,1984,18:306-309.[4]Drakaliysky E ,Du S ,Seetharaman S.An experimental study of the sulphide capacities in the system Al 2O 32CaO 2SiO 2[J ].Canadian Met Qarterly ,1997,36(2):115-120.[5]Hino M ,K itagawa S ,Ban 2ya S.Sulphide capacities of CaO -Al 2O 3-SiO 2slags[J ].IS IJ International ,1993,33:36.[6]Nzotta M M.Experimental determination of sulphide capacities in the Al 2O 32MgO 2S iO 2,Al 2O 32MnO 2S iO 2and Al 2O 32CaO 2MgO slags in the temperature range 1773-1923K[J ].Scan J of Metall ,1997,26:169-177.[7]Nzotta M M ,Du S ,Seetharaman S.Sulphide capacities in some multi component slags systems[J ].IS IJ Inter ,1998,38(11):1170-1179.[8]S osinsky D J ,S ommerville I D.The composition and temperature dependence of the sulfide capacity of metallurgical slags [J ].Metall Trans ,1986,17B :331-337.[9]姜周华・HU P 电弧炉兑铁水及L F 炉精炼埋弧渣冶炼工艺理论及应用[D ]・沈阳:东北大学,2000・(Jiang Z H.Fundamental research and practice of hot metal charging in the U HP arc furnace and submerged arc forming slag in L F refining process [D ].Shenyang :Northeastern University ,2000.)[10]Ohta H ,Suito H.Activities of SiO 2and Al 2O 3and activity coefficients of Fe t O and MnO in CaO 2SiO 22Al 2O 32MgO slags [J ].Metall M ater Trans ,1998,29B (2):119-129.Determination of Process Parameters for Refining of Ultra 2Low Sulfur Steels in Ladle FurnaceJIA N G Zhou 2hua ,ZHA N G He 2yan ,ZHA N Dong 2ping ,W A N G Wen 2z hong(School of Materials &Metallurgy ,Northeastern University ,Shenyang 110004,China.Corres pondent :J IAN G Zhou 2hua ,professor ,E 2mail :jiang -zhouhua @ )Abstract :A thermodynamic calculation method was used to determine the process parameters of ladle furnace for the refining of ultra 2low sulfur steels.The ultra 2low sulfur content in liquid steel can be reached by using high basicity slag ,deeply deoxidizing both slag and liquid steel ,reducing initial sulfur contents in slag and steel ,and properly controlling slag amount in the furnace.The production practice by a 150t ladle furnace showed that the sulfur content in steel is 010044%after L F refining and 010027%after VD treatment ,under the conditions determined b y the processing parameters proposed by this study.Moreover ,the extremely low sulfur steels with less than 01002%of sulphur content can be produced in a ladle furnace by means of controling the initial sulfur content to less than 01058%,or increasing the sulfure partial ratio between slag and metal to more than 250,or applying double slag operation.K ey w ords :L F ;secondary refining ;desulfurization ;ultra 2low sulfur steel(Received M arch 18,2002)559第10期 姜周华等:L F 炉冶炼超低硫钢的工艺条件。