第三章机械加工表面质量其控制
机械加工零件表面质量控制措施

机械加工零件表面质量控制措施机械加工工艺在制造业中起着重要的作用,因为它能够加工出复杂、精确的零件,满足不同行业的需求。
而在机械加工过程中,零件表面的质量是至关重要的,因为它直接影响着零件的功能和使用寿命。
因此,为了保证零件表面的质量,需要采取一些控制措施。
1.合理选择机床和刀具在机械加工过程中,机床和刀具是影响表面质量的重要因素。
因此,首先要合理选择机床和刀具。
在选定机床时,应根据工艺要求和零件的形状、尺寸等参数进行选型。
对于刀具的选择,要考虑到刀具的刃口质量、刃口材料、刃口的几何参数等因素。
只有选择合适的机床和刀具,才能够保证零件表面的质量。
2.控制切削参数切削参数是机械加工过程中影响表面质量的另一个重要因素。
控制切削参数包括切削速度、进给量、切削深度等参数。
切削速度太高容易导致表面粗糙度增加,切削速度太低则会使切削力增大,易导致表面毛刺。
进给量和切削深度过大也会影响表面质量,因为加工过程中会产生振动。
因此,要在机械加工过程中精确控制切削参数,以获得更好的表面质量。
3.合理选择冷却液冷却液的选择对机械加工过程中的表面质量也有很大的影响。
合适的冷却液可以起到冷却、润滑、清洗的作用,从而保证零件表面质量。
在选择冷却液时,要考虑加工的材质、刀具的材质等因素。
如果使用不合适的冷却液,会影响切削质量,甚至还会腐蚀零件表面,影响表面质量。
4.检查和调整机床机床的磨损和松动也会影响表面质量。
因此,在机械加工过程中定期检查和调整机床,以确保机床的精度和稳定性。
对于机床的机床导轨、丝杠等部件,需要进行清洗、润滑和保养。
如果发现机床有磨损和松动现象,需要及时更换零部件或进行维修,以保证机床的正常运行。
5.表面质量检测为了保证机械加工零件的表面质量,还需要对零件进行检测。
表面质量的检测包括表面粗糙度、表面平整度、表面硬度等方面。
通过检测,可以及时发现加工过程中存在的问题,并采取相应的措施进行调整。
同时,也可以对加工零件的表面质量进行评价,为改进加工工艺提供参考。
机械加工表面质量及其控制

机械加工后工件表面层的残余应力是冷态塑性变形、热 态塑性变形和金相组织变化的综合结果。切削加工时起主要 作用的往往是冷态塑性变形,表面层常产生残余压缩应力。 磨削加工时起主要作用的通常是热态塑性变形或金相组织变 化引起的体积变化,表面层常产生残余拉伸应力。
三、表面层金相组织变化与磨削烧伤
3.影响磨削烧伤的因素及改善途径
磨削用量
砂轮与工件材料
改善冷却条件
采用开槽砂轮
间断磨削→受热↓ →磨削烧伤↓
图
1)砂轮转速↑ → 磨削烧伤↑
2)径向进给量fp↑→ 磨削烧伤↑ 3) 轴向进给量fa↑→磨削烧伤↓ 4)工件速度vw ↑→磨削烧伤↓
退火烧伤
磨削时,当工件表面层温度超过 相变临界温度Ac3时,则马氏体转变 为奥氏体。若此时无冷却液,表层金 属空冷冷却比较缓慢而形成退火组织。 硬度和强度均大幅度下降。这种现象 称为退火烧伤。
磨削时,如果工件表面层温度只 是超过原来的回火温度,则表层原来 的回火马氏体组织将产生回火现象而 转变为硬度较低的回火组织(索氏体 或屈氏体),这种现象称为回火烧伤。
• v↑→ Ra↓ •f↑→ Ra↑ •ap对Ra影响不大,太小会 打滑,划伤已加工表面
•材料塑性↑→ Ra↑ •同样材料晶粒组织大↑→ Ra↑ ,常用正火、调质处理
刀具材料、刃磨质量
•刀具材料强度↑→ Ra↓ •刃磨质量↑→ Ra↓ •冷却、润滑↑→ Ra↓
(二)磨削加工表面粗糙度
1、 磨削中影响粗糙度的几何因素
四、 影响表面层物理力学性能的 主要因素及其控制
影响表面层物理力学性能的主要因素
影响显微硬度因素
•塑变引起的冷硬
•金相组织变化引起 的硬度变化
机械加工质量及控制

机械加工质量及控制引言机械加工是一种常见的制造方法,用于将原始材料加工成所需形状和尺寸的零件。
机械加工质量的好坏直接影响着零件的性能和使用寿命。
对机械加工质量进行严格的控制是非常重要的。
机械加工质量的要求1. 尺寸精度:机械加工零件的尺寸精度是保证其装配性能和工作稳定性的关键。
通常使用公差来描述尺寸精度的要求,公差越小,零件的尺寸精度要求就越高。
2. 表面质量:机械加工零件的表面质量对摩擦、磨损和腐蚀等性能有着重要的影响。
表面粗糙度是评价表面质量的重要指标,粗糙度越小,表面质量越好。
3. 几何形状:机械加工零件的几何形状要求直接决定了其与其他零件的配合性能。
例如,孔的圆度和直线度要求可以直接影响轴承的配合质量和旋转性能。
机械加工质量控制方法1. 加工设备的选择:选择适合加工要求的设备是保证机械加工质量的关键。
不同加工设备的精度、刚度和稳定性存在差异,需要根据具体的加工要求进行选择。
2. 切削工艺的优化:切削工艺的合理优化可以提高机械加工零件的表面质量和尺寸精度。
通过选择合适的刀具、切削参数和切削液等,可以减小切削力和热变形,降低表面粗糙度。
3. 机床调试和维护:机床的准确定位和运动稳定性是保证机械加工质量的基础。
需要定期检查和维护机床,保持其精度和稳定性。
4. 检测和测量:通过使用合适的测量工具和设备,对机械加工零件的尺寸、形状和表面质量进行检测和测量。
及时发现问题并进行调整和纠正,以确保机械加工质量的有效控制。
机械加工质量控制的挑战1. 加工材料的变化:不同材料的加工特性有所不同,对机械加工工艺和控制要求也存在差异。
需要根据不同材料的特点进行合理的工艺选择和优化。
2. 加工过程的变动:在机械加工过程中,由于刀具磨损、切削力变化等原因,加工过程可能会出现变动。
及时对加工过程进行调整和控制,以确保一致的加工质量。
3. 人为因素的干扰:机械加工过程中,操作人员的技能水平和责任意识也会对加工质量产生影响。
3.1表面质量概述及表面粗糙度的影响因素

谢谢大家!
②表面层金属的残余应力的影响
拉伸残余应力将使耐疲劳强度下降;压缩残余应力则使耐疲劳强度提高。
3. 表面质量对耐蚀性的影响 (1)表面粗糙度的影响 表面粗糙度值越大,加工表面与气体、液体接触的面积越大,腐蚀物 质越容易沉积于凹坑中,耐蚀性能就越差。 (2)表面层金属力学物理性质的影响 零件表面层有残余压应力时,能够阻止表面裂纹的进一步扩大,有利 于提高零件表面抵抗腐蚀的能力。 4. 表面质量对零件配合质量的影响 (1) 对于间隙配合表面 原有间隙将因急剧的初期磨损而改变,表面粗糙度越大,变化量就 越大,从而影响配合的稳定性。 (2) 对于过盈配合表面 表面粗糙度越大,两表面相配合时表面凸峰易被挤掉,这会使过盈量 减少,影响配合的可靠性。
(4)表面缺陷 加工表面上出现的缺陷,如砂眼、气孔、裂痕等。
2.表面层金属的力学物理性能和化学性能 由于机械加工中力因素和热因素的综合作用,加工表面层金属的力 学物理性能和化学性能将发生一定的变化,主要反映在以下几方面: (1)表面层金属的冷作硬化
机械加工过程中,工件表面层金属都会有一定程度的冷作硬化,使 表面层金属的显微硬度有所提高。
3.2 影响加工表面粗糙度的工艺因素及其改进措施
3.2.1 切削加工表面粗糙度 其值主要取决于切削残留面积的高度。影响切削残留面积高度的因素 主要有:刀尖圆弧半径r、主偏角kr、副偏角kr’及进给量f等。 车削、刨削时残留面积高 度的计算示意图如图3。其中图 a 是用尖刀切削的情况,切削 残留面积的高度为:
3.2.2 磨削加工后的表面粗糙度 1.几何因素的影响 单纯从几何因素考虑,可以认为:在单位面积上刻痕越多,即通过单位 面积的磨粒数越多,刻痕的等高性越好,则磨削表面的粗糙度值越小。 (1)磨削用量对表面粗糙度值的影响 砂轮的速度越高、工件速度越低、砂轮的纵向进给减小,工件表面的 每个部位被砂轮重复磨削的次数增加,被磨表面的粗糙度值将减小。
机械加工表面质量影响因素及控制措施
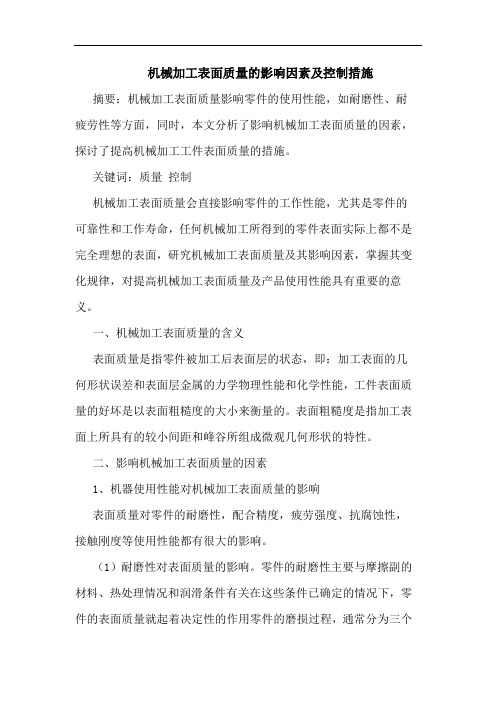
机械加工表面质量的影响因素及控制措施摘要:机械加工表面质量影响零件的使用性能,如耐磨性、耐疲劳性等方面,同时,本文分析了影响机械加工表面质量的因素,探讨了提高机械加工工件表面质量的措施。
关键词:质量控制机械加工表面质量会直接影响零件的工作性能,尤其是零件的可靠性和工作寿命,任何机械加工所得到的零件表面实际上都不是完全理想的表面,研究机械加工表面质量及其影响因素,掌握其变化规律,对提高机械加工表面质量及产品使用性能具有重要的意义。
一、机械加工表面质量的含义表面质量是指零件被加工后表面层的状态,即:加工表面的几何形状误差和表面层金属的力学物理性能和化学性能,工件表面质量的好坏是以表面粗糙度的大小来衡量的。
表面粗糙度是指加工表面上所具有的较小间距和峰谷所组成微观几何形状的特性。
二、影响机械加工表面质量的因素1、机器使用性能对机械加工表面质量的影响表面质量对零件的耐磨性,配合精度,疲劳强度、抗腐蚀性,接触刚度等使用性能都有很大的影响。
(1)耐磨性对表面质量的影响。
零件的耐磨性主要与摩擦副的材料、热处理情况和润滑条件有关在这些条件已确定的情况下,零件的表面质量就起着决定性的作用零件的磨损过程,通常分为三个阶段:摩擦副刚开始工作时,磨损比较明显,称为初期磨损阶段(一般称为走合期)。
经初期磨损后,磨损缓慢均匀,进入正常磨损阶段。
当磨损达到一定程度后,磨损又突然加剧,导致零件不能正常工作,称为急剧磨损阶段。
(2)疲劳强度对表面质量的影响。
在交变载荷作用下,表面粗糙度的凹谷部位容易引起应力集中,产生疲劳纹。
表面粗糙度值愈大,表面的纹痕愈深,纹底半径愈,抗疲劳破坏的能力就愈差。
(3)耐蚀性对表面质量的影响。
零件的耐蚀性在很大程度上取决于表面粗糙度,表面粗糙度值愈大,则凹谷中聚积腐蚀性物质就愈多、抗蚀性就愈差。
表面层的残余拉应力会产生应力腐蚀开裂,降低零件的耐磨性,而残余压应力则能防止应力腐蚀开裂。
2、影响表面粗糙度的因素(1)切削加工影响表面粗糙度的因素。
机械加工表面质量及其控制

机械加工表面质量及其控制概述机械加工表面质量是指工件表面的平整度、光洁度和形状精度等方面的指标。
良好的机械加工表面质量是保证工件性能和使用寿命的重要因素之一。
因此,控制机械加工表面质量是机械加工过程中必须重视和解决的问题。
机械加工表面质量的评价指标机械加工表面质量的评价指标包括粗糙度、平整度、光洁度和形状精度等。
粗糙度是指工件表面的不规则程度,也是表面形态的度量。
常用的粗糙度评价参数有Ra、Rz、Rq等。
粗糙度越小,表面越光滑。
粗糙度对工件的强度、耐磨性、润滑等性能有重要影响。
平整度平整度是指工件表面的平整程度。
平整度的好坏影响着工件的配合质量和密封性能。
平整度可以通过测量工件表面的平坦度、平行度等参数来评价。
光洁度光洁度是工件表面反光性和光滑度的度量。
通过测量表面的反射率、光泽度等参数来评价。
高光洁度的表面不仅具有美观性,还能改善工件的耐腐蚀性能。
形状精度是指工件形状与标准形状之间的偏差程度。
形状精度可以通过测量工件的直线度、圆度、同轴度等参数来评价。
形状精度的好坏影响着工件的装配性能和运动精度。
机械加工表面质量的控制方法为了获得满足要求的机械加工表面质量,需要采用合适的工艺方法和控制技术。
机械加工工艺的选择在机械加工过程中,选择合适的切削参数和切削工具是保证表面质量的关键。
切削速度、进给量、切削深度等参数的合理选择可以减小表面粗糙度,改善表面质量。
加工设备的调整和维护机械加工设备的调整和维护对保证表面质量同样重要。
调整设备的刀具位置、工艺参数的精确控制,以及对设备的定期维护和保养,都能提高机械加工表面质量。
刀具的选择和磨削选择合适的刀具材料和刀具几何参数,以及刀具的定期磨削和修复,可以保证机械加工表面的精度和光洁度。
表面处理技术对于特殊要求的机械加工表面质量,可以采用表面处理技术来改善表面的光洁度和形状精度。
常用的表面处理方法包括抛光、喷砂、阳极氧化等。
总结机械加工表面质量对工件的性能和使用寿命具有重要影响。
浅谈机械加工零件表面的质量控制措施

浅谈机械加工零件表面的质量控制措施机械加工零件表面质量对于产品的性能和外观有着重要影响,因此对于机械加工零件表面质量的控制尤为重要。
本文将从机械加工零件表面的质量要求、表面质量的评价和控制措施三个方面进行论述。
一、机械加工零件表面的质量要求机械加工零件表面的质量要求包括光洁度、平整度、粗糙度和表面缺陷等方面。
1. 光洁度要求:光洁度是指零件表面的平滑程度,光洁度的要求取决于零件所处的工作环境以及外观要求。
对于机械零件的表面,要求表面光滑、无明显的划痕和凹凸不平,以保证零件配合的精度和摩擦的稳定性。
2. 平整度要求:平整度是指零件表面的平坦程度,主要包括平面度、轮廓度等指标。
平整度的要求取决于零件的安装和工作要求,例如对于密封面零件,要求平面度较高,以确保密封性能。
3. 粗糙度要求:粗糙度是指零件表面的粗糙程度,常用Ra值来表示。
粗糙度的要求取决于零件的工作环境和功能要求,例如对于滑动副零件,要求表面粗糙度较低,以减小摩擦阻力和磨损。
4. 表面缺陷要求:表面缺陷包括划痕、毛刺、气孔、裂纹等。
表面缺陷的要求取决于零件的功能和外观要求,例如对于高精度的零件,要求表面无明显的划痕和缺陷,以保证零件的性能和外观质量。
二、表面质量的评价机械加工零件表面质量的评价可以通过目视检查、手感检查、测量检查等方法进行。
1. 目视检查:通过肉眼观察零件表面的光洁度、平整度和表面缺陷等方面的质量。
目视检查主要适用于外观质量要求较高的零件。
2. 手感检查:通过手触零件表面来判断光洁度、平整度和表面缺陷等方面的质量。
手感检查主要适用于外观质量要求较低但性能要求较高的零件。
3. 测量检查:通过使用测量仪器对零件表面的光洁度、平整度、粗糙度等指标进行测量,以得到数值化的表面质量数据。
测量检查主要适用于对表面质量有精确要求的零件。
三、控制措施为了保证机械加工零件表面质量的控制,可以采取以下措施。
1. 加工前准备措施:在进行加工前,要对机床、刀具等进行检查和维护,保证加工设备的正常运行。
机械加工表面质量
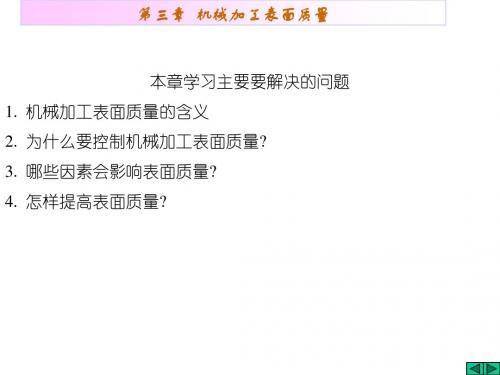
2.表面层物理 力学、化学性能
(1)表面粗糙度 (2)表面波度 (3)纹理方向 (4)伤痕——表面上一些个别位置 上出现的缺陷
(1)表面层加工硬化(冷作硬化)。 (2)表面层金相组织变化。
(3)表面层产生残余应力。
第一节 加工表面质量及其对使用性能的影响
第一节 加工表面质量及其对使用性能的影响
影响表层残余应力的因素
三、表层金属的残余应力——拉应力或者压应力
(一)残余应力产生的原因 1)冷塑性变形——使表层产生压缩残余应力,里层产生拉伸 残余应力。
原因:加工表面受刀具或砂轮磨粒的挤压和摩擦,产生拉伸塑性变形 ,此 时里层金属处于弹性变形状态,切削后里层金属趋于弹性恢复,但受 到已产生塑性变形的表层金属牵制
第三章 机械加工表面质量
本章学习主要要解决的问题 1. 机械加工表面质量的含义 2. 为什么要控制机械加工表面质量? 3. 哪些因素会影响表面质量? 4. 怎样提高表面质量?
第三章 机械加工表面质量
第一节 加工表面质量及其对使用性能的影响
一、机械加工表面质量的含义
1.表面的几何特征
2)热塑性变形——表层产生拉伸残余应力,里层产生压缩残 余应力。
原因:切削和磨削过程中,表层的温度比里层高,表层的热膨胀较大;加 工后零件冷却至室温时,表层金属体积的收缩受到里层的牵制。
影响表层残余应力的因素
3)相变引起的体积变化 金相组织的变化引起表层金属的比容增大,则表层金属将产生 压缩残余应力,而里层金属产生拉伸残余应力; 金相组织的变化引起表层金属的比容减小,则表层金属产生拉 伸残余应力,而里层金属产生压缩残余应力 。
• 提高砂轮速度,降低工件转速,减小纵向进给速度——增大单位面 积的磨粒数
- 1、下载文档前请自行甄别文档内容的完整性,平台不提供额外的编辑、内容补充、找答案等附加服务。
- 2、"仅部分预览"的文档,不可在线预览部分如存在完整性等问题,可反馈申请退款(可完整预览的文档不适用该条件!)。
- 3、如文档侵犯您的权益,请联系客服反馈,我们会尽快为您处理(人工客服工作时间:9:00-18:30)。
<2)工件材料
太硬易使磨粒磨钝→Ra↑;
太软容易堵塞砂轮→Ra↑;
韧性太大,热导率差会使磨粒早期崩落→Ra↑。
<3)砂轮粒度与硬度
磨粒太细,砂轮易被磨屑堵塞,使表面粗糙度值增大,若导热情况不好,还会烧伤工件表面
磨削速度比一般切削速度高得多,且磨粒大多数是负前角,切削刃又不锐利,大多数磨粒在磨削过程中只是对被加工表面挤压,没有切削作用。加工表面在多次挤压下出现沟槽与隆起,又因为磨削时的高温更加剧了塑性变形,故表面粗糙度值增大。
<1)磨削用量
砂轮的转速↑→材料塑性变形↓→Ra↓;
磨削深度↑、工件速度↑→塑性变形↑→Ra↑;
并非冷作硬化程度越高,耐磨性就越高。这是因为过分的冷作硬化,将引起金属组织过度“疏松”,在相对运动中可能会产生金属剥落,在接触面间形成小颗粒,使零件加速磨损。
<3)表面纹理零件耐磨性的影响
表面纹理的形状和刀纹方向对耐磨性也有影响,原因是纹理形状和刀纹方向影响有效接触面积和润滑液的存留,一般,圆狐状、凹坑状表面纹理的耐磨性好,尖峰状的耐磨性差。
在运动副中,两相对运动零件的刀纹方向和运动方向相同时,耐磨性较好,两者的刀纹方向和运动方向垂直时,耐磨性最差。
2.表面质量对零件疲劳强度的影响
<1)表面粗糙度对零件疲劳强度的影响
表面粗糙度越大,抗疲劳破坏的能力越差。
对承受交变载荷零件的疲劳强度影响很大。在交变载荷作用下,表面粗糙度的凹谷部位容易引起应力集中,产生疲劳裂纹。
3)表面层金相组织变化
比容大的组织→比容小的组织→体积收缩,产生拉应力,反之,产生压应力。<密度小,比容大)
回火烧伤:
马氏体→托氏体<或索氏体),密度增大,比容减小,表层金属产生残余拉应力,里层产生残余压应力。
淬火烧伤:
马氏体→二次淬火的马氏体,密度减小,比容增大,表层产生残余压应力,里层产生残余拉应力。
表面质量对零件使用性能还有其它方面的影响:如减小表面粗糙度可提高零件的接触刚度、密封性和测量精度;对滑动零件,可降低其摩擦系数,从而减少发热和功率损失
节小结
介绍表面的几何形状误差和表层金属的力学物理性能和化学性能对工件使用性能的影响。
第一讲
教案目的
认识影响加工表面粗糙度的工艺因素并提出改善措施
教材分析
砂轮太硬,磨粒不易脱落,磨钝后不能及时被新的磨粒代替,使表面粗糙度增大;
砂轮选得太软,磨粒易脱落,磨削作用削弱,使表面粗糙度值增大。
<4)冷却润滑液
适当的冷却与润滑可降低表面粗糙度值。
节小结
讲解综合影响加工表面粗糙度的工艺因素并提出改善措施。
第一讲
教案目的
认识影响表面层力学物理性能的工艺因素并提出改善措施
表面粗糙度值越小,表面缺陷越少,工件耐疲劳性越好;反之,加工表面越粗糙,表面的纹痕越深,纹底半径越小,其抗疲劳破坏的能力越差。
<2)表面层冷作硬化与残余应力对零件疲劳强度的影响
适度的表面层冷作硬化能提高零件的疲劳强度。
残余应力有拉应力和压应力之分,残余拉应力容易使已加工表面产生裂纹并使其扩展而降低疲劳强度
切削深度影响不大
切削速度v↑→塑变↓→冷硬↓
f↑→切削力↑→塑变↑→冷硬↑
<2)刀具几何形状的影响
切削刃钝圆半径↑,冷硬程度↑
其他几何参数影响不明显
刀具磨损影响显著<力和热互相作用)
<3)工件材料
材料塑性↑,冷硬倾向↑
2)磨削加工<综合考虑切削力的强化和磨削热的弱化作用
<1)工件材料
材料塑性↑→冷硬倾向↑
重点:加工表面粗糙度的工艺因素
难点:磨削加工表面粗糙度
课时安排
1课时
教案方法
讲授法
教案内容:
第三章机械加工表面质量及其控制
§3.2影响加工表面粗糙度的工艺因素及其改善措施
1、几何因素的影响
切削加工后表面粗糙度的值主要取决于切削残留面积的高度,影响残留面积高度的因素有:刀尖圆弧半径、主偏角、副偏角,进给量。如图所示
淬火钢在磨削时,因为磨削条件不同,产生的磨削烧伤有三种形式。
2.磨削烧伤的三种形式
1)淬火烧伤:
磨削时工件表面温度超过相变临界温度<碳钢为720℃)时,则马氏体转变为奥氏体。在冷却液作用下,工件最外层金属会出现二次淬火马氏体组织。其硬度比原来的回火马氏体高,但很薄,其下为硬度较低的回火索氏体和屈氏体。因为二次淬火层极薄,表面层总的硬度是降低的,这种现象称为淬火烧伤。
<1)表面粗糙度对零件耐腐蚀性能的影响
零件表面越粗糙,越容易积聚腐蚀性物质,凹谷越深,渗透与腐蚀作用越强烈。
因此减小零件表面粗糙度,可以提高零件的耐腐蚀性能。
<2)表面残余应力对零件耐腐蚀性能的影响
零件表面残余压应力使零件表面紧密,腐蚀性物质不易进入,可增强零件的耐腐蚀性,而表面残余拉应力则降低零件耐腐蚀性。
1、表面层金属产生残余应力的原因
1)冷态塑性变形
工件表面受到挤压与摩擦,表层产生伸长塑性变形,基体仍处于弹性变形状态。切削后,表层产生残余压应力,而在里层产生残余拉伸应力。
2)热态塑性变形
表层产生残余拉应力,里层产生产生残余压应力。
工件表面在切削热的作用下,产生热膨胀,此时基体温度较低,因此表面层热膨胀受集体的限制产生压应力,当表面曾的温度超过材料的弹性变形范围时,会产生热塑性变形,当切削结束,温度下降到与基体温度一致时,因为表面层已产生热塑性变形,但受基体的限制产生了残余拉应力,里层产生压应力。
<3)轴向进给量fa↑→磨削烧伤↓
<4)工件速度vw↑→磨削烧伤↓
3)改善冷却条件
采用内冷却法→磨削烧伤↓
4)采用开槽砂轮
间断磨削→受热↓→磨削烧伤↓
能将冷却液直接带入磨削区,还能起扇风作用,改善散热条件。
三、表层金属的残余应力
机械加工中工件表面层组织发生变化时,在表面层及其与基体材料的交界处会产生互相平衡的弹性力。这种应力即为表面层的残余应力。
残余压应力则能够部分地抵消工作载荷施加的拉应力,延缓疲劳裂纹的扩展,从而提高零件的疲劳强度。
3.表面质量对零件工作精度的影响
<1)表面粗糙度对零件配合精度的影响
表面粗糙度较大,则降低了配合精度。
<2)表面残余应力对零件工作精度的影响
表面层有较大的残余应力,就会影响它们精度的稳定性。
4.表面质量对零件耐腐蚀性能的影响
研究加工表面质量的目的,就是要掌握机械加工的各种工艺因素对加工表面质量影响的规律,以便应用这些规律控制加工过程.最终达到提高加工表面质量、提高产品使用性能的目的。
§3.1加工表面质量对使用性能的影响
1、表面的几何形状误差
表面粗糙度:加工表面的微观几何误差,波长与波高比值小于50。
表面波度:加工表面不平度波长与波高比值在50~1000的几何形状误差。
2)回火烧伤
磨削时,如果工件表面层温度只是超过原来的回火温度,则表层原来的回火马氏体组织将产生回火现象而转变为硬度较低的回火组织<索氏体或屈氏体),这种现象称为回火烧伤。
3)退火烧伤
磨削时,当工件表面层温度超过相变临界温度<中碳钢为300℃)时,则马氏体转变为奥氏体。若此时无冷却液,表层金属空气冷却比较缓慢而形成退火组织。硬度和强度均大幅度下降。这种现象称为退火烧伤。
<1)砂轮的磨粒
磨粒在砂轮上的分布越均匀、磨粒越细,刃口的等高性越好。则砂轮单位面积上参加磨削的磨粒越多,磨削表面上的刻痕就越细密均匀,表面粗糙度值就越小。
<2)砂轮修整
砂轮修整除了使砂轮具有正确的几何形状外,更重要的是使砂轮工作表面形成排列整齐而又锐利的微刃。因此,砂轮修整的质量对磨削表面的粗糙度影响很大。
纹理方向:表面刀纹的方向。
伤痕:加工表面个别位置出现的缺陷。
2、表层金属的力学物理性能
表面层金属的冷作硬化
表面层的残余应力
表面层金相组织的变化
1.表面质量对零件耐磨性的影响
<1)表面粗糙度对零件耐磨性的影响
表面粗糙度太大和太小都不耐磨。
表面粗糙度太大,接触表面的实际压强增大,粗糙不平的凸峰相互咬合、挤裂、切断,故磨损加剧;
教材分析
重点:影响表面层力学物理性能的工艺因素及其改进措施
难点:表面层金属的冷作硬化、残余应力、金相组织的变化
课时安排
1课时
教案方法
讲授法
教案内容:
第三章机械加工表面质量及其控制
§3.2影响表面层力学物理性能的工艺因素及其改进措施
一.加工表面层的冷作硬化
1、概述:
<1)定义
机械加工时,工件表面层金属受到切削力的作用产生强烈的塑性变形,使晶格扭曲,晶粒间产生剪切滑移,晶粒被拉长、纤维化甚至碎化,从而使表面层的强度和硬度增加,这种现象称为加工硬化,又称冷作硬化和强化。
<4)其它因素的影响
此外,合理使用冷却润滑液,适当增大刀具的前角,提高刀具的刃磨质量等,均能有效地减小表面粗糙度值。
二、磨削加工表面粗糙度
1、磨削中影响粗糙度的几何因素
工件的磨削表面是由砂轮上大量磨粒刻划出无数极细的刻痕形成的,工件单位面积上通过的砂粒数越多,则刻痕越多,刻痕的等高性越好,表面粗糙度值越小。
<2)衡量表面层加工硬化的指标
衡量表面层加工硬化程度的指标有下列三项:
1)表面层的显微硬度HV;
2)硬化层深度h;
3)硬化程度N
N=(HV-HV0>/HV0×100%
式中HV0—工件原表面层的显微硬度。
2、影响表面冷作硬化பைடு நூலகம்因素