第4章拉深模具设计过程
钣金与成型第4章 拉深

拉
深
航空航天工程学部 主讲: 贺平
重点内容: 1.拉深变形规律及拉深件质量影响因素; 2.拉深工艺计算方法; 3.拉深工艺性分析与工艺方案制定。
难点内容: 1.拉深变形规律及拉深件质量影响因素; 2.拉深工艺计算 ; 3.其它形状零件的拉深变形特点 。
4、 1
圆筒件拉深的变形过程
1 、 圆筒件拉深时的应力应变状态
d d d dt dt 2 d sin t 0 2 d d
首次拉深某瞬间毛坯凸
1) 拉深过程法兰区(凸缘区)的应力分布 (图4-6) 设为无压边拉深,忽略厚向应力,即 确定凸缘区的径向应力 求解过程:建立微分平衡方程:
说明:1) 式中 Rw 是变化的,因此厚度的应变分布规律是动态的; 定
t
2)厚度变化分界线 0.607Rw 是近似的,因为其推导中假 0 。
3)圆筒壁和筒底材料的变形:凸缘区材料经过圆角区拉入凹模型腔时, 在凹模圆角处,材料除受径向拉伸外,同时产生塑性弯曲,使板厚减小。进 一步从凹模圆角区拉向筒壁时,又要被校直,即经受反向弯曲。
说明:1)凸缘外区应力状态以压应力为主,内区以拉应力为主。
即为外区增厚,内区减薄。
2)在凹模型腔入口处,径向应力最大,即:
max | a
a
3)凸缘上切向应力恒为负值,
s
说明增大 , 可减小 。 (图)
特点:
⑴ 径向拉应力在凸缘外边缘处总是零; ⑵ 切向压应力在凸缘外边缘处达最大值, 在筒壁处为最小值; ⑶ 外区切向压应力大于径向拉应力;
2 2 ( R02 H ) ( Rw 2) 2 H R02 2 Rw
第四章第1、2、3、4、5节N
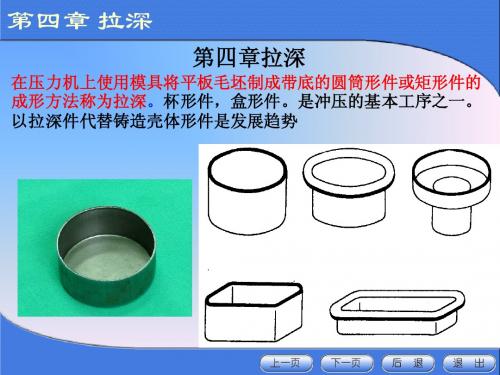
第四章 拉深
特点: 1.反拉深时变形集中在rd区,与rd区包角为1800,摩擦阻力比正 拉深时大,不易起皱,常可不用压边。 2.折弯要减少一半。材料硬化程度要比正拉深时低些。 3.反拉深允许变形程度可大些。 4.拉深系数不能太大。影响凹模壁厚。
结束
第四章 拉深
三、凹模圆角区摩擦对 的影响 将板料流经、区视为皮带绕带轮旋转,便可用欧拉张力公式 进行估算。
第四章 拉深
四、材料硬化对 的影响 当考虑材料硬化对筒壁处拉应力的影响时, 应为瞬时的屈服流动应力。 便不是常数,
缩颈点处断面收缩率 材料,硬化也越强烈,
,越大的
应力的最大值一般出现在板料包满凸模和凹模 圆角时,而这时材料已高度硬化,屈服流动应 力已远远超过其初始值。
第四章 拉深
第三节 影响径向拉应力的因素
一、压边对 的影晌 凸缘区板料在流入凹模过程中将受到压边圈与凹模端面的双重 摩擦阻力作用,使筒壁处拉应力增大
为筒壁截面积的近似值。
第四章 拉深
二、凹模圆角区弯矩对 的影响 处在位置1是平直的,进入rd区被弯曲,中心面曲率半径为R。位 置3,又被反弯拉直。凸缘区板料中被反复两次弯曲。
第四章 拉深
第四章拉深
在压力机上使用模具将平板毛坯制成带底的圆筒形件或矩形件的 成形方法称为拉深。杯形件,盒形件。是冲压的基本工序之一。 以拉深件代替铸造壳体形件是发展趋势
第四章 拉深
第四章 拉深
第一节圆筒形件拉深变形分析
一、拉深变形过程及变形特点 无压边的拉深过程,有压边的拉深。
第四章 拉深工艺与拉深模设计
第四章 拉深
变形特点:变形区主要 集中在凸缘区,即D与d 之间的环形部分。变形 区任一点在径向受到了 拉伸,而切向受到了压 缩。同一圆周上的各点 的切向压缩变形是相等 的。径向变形不具有均 匀性,越靠近凸缘边缘, 径向拉伸变形与切 拉深
《冲压工艺与模具设计》图文课件ppt 第4章

4.5 带凸缘圆筒形件的拉深
4.5.2 宽凸缘圆筒形件的拉深
当 r凸 = r凹 = r 时,宽凸缘圆筒形件毛坯直径 D 为: 根据拉深系数的定义,宽凸缘圆筒形件的拉深系数为:
目录
4.5 带凸缘圆筒形件的拉深
4.5.2 宽凸缘圆筒形件的拉深
宽凸缘圆筒形件的尺寸
目录
4.5 带凸缘圆筒形件的拉深
4.5.2 宽凸缘圆筒形件的拉深பைடு நூலகம்
拉深系数
拉深系数表示拉深后圆筒形件的直径与拉深前毛坯(或半成品) 的直径之比。
目录
基本概念
极限拉深系数
在实际生产中,拉深系数的减少有个限度,这个限度称为 极限拉深系数 。
拉深模的间隙
凸、凹模之间的间隙,简称为拉深间隙。
修边余量
由于拉深材料厚度有公差,板料具有各向异性,所以拉深后工件 的口部或凸缘周边不齐,必须进行修边,以达到工件的要求。修 边的值称为修边余量。
拉深件的工艺性
拉深件的工艺性是指工件拉深的难易程度。
变薄拉深
变薄拉深主要是在拉深过程中改变拉深件筒壁厚度,而毛坯的直 径变化很小的拉深方法 。
目录
拉深件类型
目录
4.1 拉深变形过程分析
4.1.1 拉深变形的过程及特点
1—凸模; 2—压边圈; 3—凹模; 4—制件
目录
4.1 拉深变形过程分析
4.1.2 拉深过程中板料的应力应变状态
4.2.1 起皱及其控制
(1)采用压边圈。
控
制
(2)采用锥形凹模
起
皱
的 措
(3)采用拉深筋
施
:
(4)采用反拉深
目录
4.2 拉深件的质量控制
4.2.1 起皱及其控制
第四章 拉深

§4.1 圆筒件拉深的变形过程
三、拉深变形过程的力学分析(续)
1、凸缘变形区的应力分析(续) (2)最大径向拉应力σ1max的变化规律:
在变形区的内边缘(即R=r处) 径向拉应力最大,其值为:
1max
1.1 s
ln
Rt r
s:加工硬化
变形区Rt
§4.1 圆筒件拉深的变形过程
三、拉深变形过程的力学分析(续)
角,表面质量要求高,凸、凹模间隙略大于板料厚度。
1-模柄 2
拉
-上模座 3-
深
凸模固定板 4-
模
弹簧 5-压
结
边圈 6-定位 板 7-凹模 8-下模座 9
构 图
-卸料螺钉 10-
凸模
§4.1 圆筒件拉深的变形过程
一、拉深变形过程
圆筒形件是最典型的拉深件。 (一)拉深变形过程及特点(如图)
1、金属的流动过程 在毛坯上画作出距离为a的等距离的同心圆与相同弧
三、拉深变形过程的力学分析(续)
1、凸缘变形区的应力分析(续) (1)拉深中某时刻变形区应力分布(续)
平衡方程:
Rd1 (1 3 )dR 0
屈服条件:
1 3 s 1.1 s
由上述两式,并考虑边界条件(当R=Rt时,σ1=0),经数学 推导就可以求出径向拉应力,和切向压应力的大小为:
d
2 r1 t f
ln
r r1
4 37
拉深力F应等于dW dh
,它在拉深开始时,r
R0
具有最大值,故
Fm a x
2
r1
t
f
ln
R0 r1
模具毕业设计104罩子拉深模具的设计与制造

俗话说“没有规矩不成方圆”,世界上许许多多的东西都有着它们的“规矩”。
模具就是各种东西的规矩。
随着人们的生活不断改善,模具在不同的时代发生着飞跃的变化,随之出现许多不同的制造方式。
由于产品的材料和工艺特性不同,生产用的设备也各异,模具种类繁多,但用的最为广泛的大约有以下几种:冷冲压模、塑料成型模、锻造模、精密铸造模、粉末冶金模、橡胶成型模、玻璃成型模、窑业制品模、食品糖果模、建材用模等。
其中以冷冲压模、塑料模的技术要求和复杂程度较高。
在本人这次设计中,主要介绍的是模具的拉深。
拉深是利用拉深模将板料冲压成各种空心件的一种加工方法,是冲压生产中应用最广泛的工序之一。
我设计的是无凸圆模具拉深设计和制造,材料为10钢板,厚度t=1mm。
传统的加工方法为落料,拉深。
我的加工方法比较简单。
由于材料和厚度的原因,我采用的加工方法为:先计算毛坯的直径、再进行落料后放入模具中进行拉深。
计算拉深次数,判断拉深是否需要压边,来加压边圈。
完成模具的总体设计。
从而完成工件的加工。
关键词:落料拉深压边随着时代的发展,模具已成为当今社会最要的工业的一部分,已经离不开生活的需要。
模具的出现可以追溯到几千年前的陶器烧制和青铜器制造,但其大规模应用却是随着现代工业的崛起而发展起来的。
19世纪,随着军火工业、钟表工业、无线电工业的发展,模具开始得到广泛应用。
第二次世界大战后,随着世界经济的飞速发展,它又成了生产家用电器、车、电子仪器等零件的最佳方式。
从世界范围看,当时美国的模具制造技术在最前列。
20世纪50年代中期以前,模具设计多凭经验,参考已有的图纸和感性认识,根据用户的要求,制作能满足产品要求的模具,但对所设计模具零件的机械性能缺乏了解。
从1955年到1965年,人们通过对模具主要零件的机械性能和受力状况进行数字分析,对金属性加工工艺及原理进行深入探讨,使得模具技术得到迅猛发展,在此期间归纳出模具设计原则,使得压力机械,冲压材料,加工方法和模具材料及制造方法等领域面貌一新,并向实用化的方向发展。
17809-冲压工艺与模具设计-电子教案-模块4
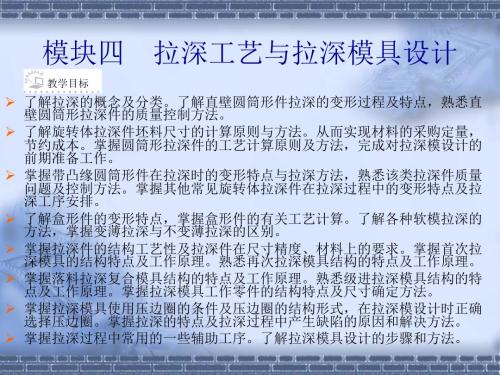
盒形件拉深时的应力分布
项目一 拉深工艺
低盒形件拉深件的毛坯
项目一 拉深工艺
高盒形件拉深件的毛坯
项目一 拉深工艺
任务八 其他拉深方法 变薄拉深件图
项目一 拉深工艺
液体凸模拉深的变形过程
项目一 拉深工艺
聚氨酯橡胶拉深模 强制润滑拉深
项目一 拉深工艺
变薄拉深
项目一 拉深工艺
项目二 拉深模具结构及工作原理
任务一 首次拉深模具的结构及工作原理
1. 无压边首次拉深模具
2. 有压边的首次拉深模具
项目二 拉深模具结构及工作原理
无压边装置的首次拉深模具 工作时,毛坯在定位圈3中 定位,拉深结束后,工件由 凹模底部的台阶完成脱模, 并由下模座底孔落下。由于 模具没有采用导向机构,故 模具安装时由校模圈2完成 凸、凹模的对中,保证间隙 均匀,工作时将校模圈移走。 该模具结构简单,制造方便, 通常用于材料塑性好、相对 厚度较大的零件拉深。由于 其凸模要深入凹模,所以只 适用于浅拉深。
项目二 拉深模具结构及工作原理
任务一 首次拉深模具的结构及工 作原理 任务二 再次拉深模具的结构及工 作原理
模块小结
项目一 拉深工艺
任务一 拉深概念及分类 典型拉深件
项目一 拉深工艺
拉深件的分类
项目一 拉深工艺
不变薄拉深
项目一 拉深工艺
变薄拉深
项目一 拉深工艺
任务二 直壁圆筒形件拉深的变形过程及特点 圆筒形拉深件
项目二 拉深模具结构及工作原理
无压边圈的再次拉深模具
项目二 拉深模具结构及工作原理
带弹性压边圈的再次拉深模具
项目二 拉深模具结构及工作原理
材料拉深

第4章 拉 深
• 把平面毛坯拉压成空心体,或者把空心体拉压成外形更小而 板厚没有明显变化的空心体的冲压工艺叫拉深,可分为普通 拉深和变薄拉深,拉深属于成形工序。 • 拉深工艺可分为不变薄拉深和变薄拉深两类,变薄拉深应用 较少,本章主要讨论不变薄拉深。 • 用拉深方法可以制成筒形、阶梯形、盒形、锥形、球形和其 它各种不规则形状的薄壁零件,生产效率高、精度较高、材 料消耗少、零件的强度和刚性较高,因而,在电子、电器、 仪表、汽车、航空、以及日常生活用品中,拉深工艺占居相 当重要的地位。
• d1=m1D • d2=m2d1 • …… • dn=mndn-1
• • (2)工序件圆角半径的确定,圆角半径确定方法将在本章第六节详细讨论。 (3)工序件高度的计算,根据无凸缘圆筒形件毛坯尺寸的计算公式推导出各次 工序件高度的计算公式为:
见公式(4-12)
4.3.5 带凸缘圆筒形件拉深方法及工序件尺寸的确定
4.3 圆筒形件的拉深系数和拉深次数的确定
• 4.3.1 拉深系数及其极限
• 拉深变形程度的大小可以用拉深件的高度和直径的比值,即相对高度 表示,比值小的变形程度小,比值大的变形程度大。 • 但在模具设计时,为了确定拉深次数,通常用拉深系数作为计算的依 据。拉深系数是以拉深后的直径与拉深前的毛坯(工序件)直径之比 d1 表示(图4-7)即 第一次拉深系数
4.3.2 影响极限拉深系数的因素
•
极限拉深系数的数值取决于筒壁传力区最大拉应力与危险断面的抗 拉强度。因此,凡是影响筒壁传力区的最大拉应力和危险断面的抗拉 强度的因素都会影响极限拉深系数。 1、材料的力学性能
•
一般来说,材料组织均匀,晶粒大小适当,屈强比小,材料的伸 长率大,塑性好,拉深性能好,极限拉深系数较小。
拉深模具的设计及要求
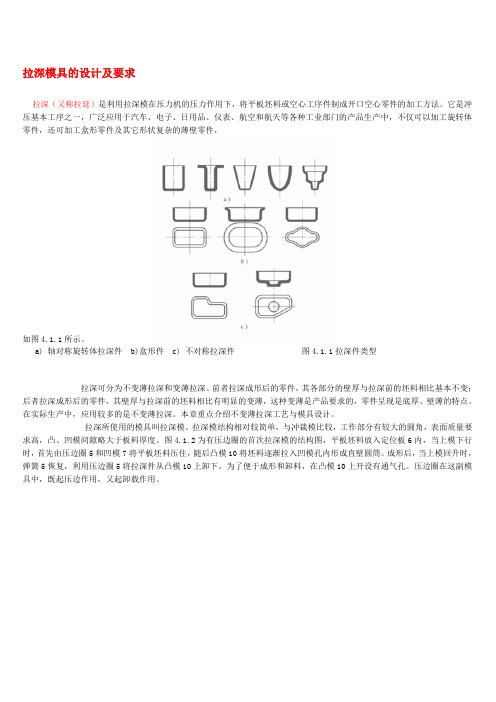
拉深模具的设计及要求拉深(又称拉延)是利用拉深模在压力机的压力作用下,将平板坯料或空心工序件制成开口空心零件的加工方法。
它是冲压基本工序之一,广泛应用于汽车、电子、日用品、仪表、航空和航天等各种工业部门的产品生产中,不仅可以加工旋转体零件,还可加工盒形零件及其它形状复杂的薄壁零件,如图4.1.1所示。
a) 轴对称旋转体拉深件b)盒形件c) 不对称拉深件图4.1.1拉深件类型拉深可分为不变薄拉深和变薄拉深。
前者拉深成形后的零件,其各部分的壁厚与拉深前的坯料相比基本不变;后者拉深成形后的零件,其壁厚与拉深前的坯料相比有明显的变薄,这种变薄是产品要求的,零件呈现是底厚、壁薄的特点。
在实际生产中,应用较多的是不变薄拉深。
本章重点介绍不变薄拉深工艺与模具设计。
拉深所使用的模具叫拉深模。
拉深模结构相对较简单,与冲裁模比较,工作部分有较大的圆角,表面质量要求高,凸、凹模间隙略大于板料厚度。
图4.1.2为有压边圈的首次拉深模的结构图,平板坯料放入定位板6内,当上模下行时,首先由压边圈5和凹模7将平板坯料压住,随后凸模10将坯料逐渐拉入凹模孔内形成直壁圆筒。
成形后,当上模回升时,弹簧5恢复,利用压边圈5将拉深件从凸模10上卸下,为了便于成形和卸料,在凸模10上开设有通气孔。
压边圈在这副模具中,既起压边作用,又起卸载作用。
图4.1.2 拉深模结构图1-模柄2-上模座3-凸模固定板4-弹簧5-压边圈6-定位板7-凹模8-下模座9-卸料螺钉10-凸模4.2圆筒件拉深的变形分析4.2.1拉深变形过程圆筒形件是最典型的拉深件。
平板圆形坯料拉深成为圆筒形件的变形过程如图图4.2.1 拉深变形过程4.2.2拉深过程中坯料内的应力与应变状态拉深过程中出现质量问题主要是凸缘变形区的起皱和筒壁传力区的拉裂。
凸缘区起皱是由于切向压应力引起板料失去稳定而产生弯曲;传力区的拉裂是由于拉应力超过抗拉强度引起板料断裂。
同时,拉深变形区板料有所增厚,而传力区板料有所变薄。
- 1、下载文档前请自行甄别文档内容的完整性,平台不提供额外的编辑、内容补充、找答案等附加服务。
- 2、"仅部分预览"的文档,不可在线预览部分如存在完整性等问题,可反馈申请退款(可完整预览的文档不适用该条件!)。
- 3、如文档侵犯您的权益,请联系客服反馈,我们会尽快为您处理(人工客服工作时间:9:00-18:30)。
项目四、拉深模具设计过程
任务1:根据设计任务,选择图4.1零件,设计
拉深模具。
1.分析拉深件工艺性并拟定拉深工艺方案
零件为一无凸缘圆筒形件,材料为08F,拉深性
能较好,尺寸为未注公差,可作IT14级精度,壁厚
1mm,高度尺寸不大,整体拉深工艺性较好,采用普
通的拉深工艺应该能满足要求。
图4.1圆盖,20万件/年2.确定冲压模具类型
采用正装拉深模。
3.拉深工艺计算
(1)确定修边余量Δh;
零件的相对高度h/d=59/48=1.21,经查得修边余量Δh=2.5(查表4-3)所以,修正后拉深件的总高应为48+2.5=50.5mm。
(2)计算毛坯直径D;
确定坯料尺寸由无凸缘筒形拉深件坯料尺寸计算公式(4-5)
D=
(3)计算板料相对厚度(t/D)×100,并判断是否采用压边圈
t/D×100=1/121.31×100=0.82<1.5,查表4-8,要压边圈
(4)拉深系数计算,确定拉深次数,求出工序件尺寸
d/D=59/121.31=0.49<[m1]=0.55,不能一次过拉深成形,需要多次拉深。
根据
t/D=0.82,查表4-4得各次拉深的极限拉深系数为[m
]=0.55,[m2]=0.78,
1
[m3]=0.80。
d1=[m1]D=0.55×121.31=66.72mm (4-10)
d1=[m2]D=0.78×67.55=52.04mm
因d2=52.04mm<59mm,所以需采用2次拉深成形。
计算各次拉深工序件尺寸,为了使第2次拉深的直径与零件要求一致,需对极限拉深系数进行调整。
调整后取各次拉深的实际拉深系数为m1=0.57,m2=0.84重新计算各次工序件直径为:
d1=m1D=0.57×121.31=69mm (4-10)
d2=m2d1=0.85×70=59mm
根据公式(4-27和4-28),给出工序件圆角r 1=7,r 2=6.5,计算出各工序件的高度尺寸:
()211111110.250.430.3239.2r D h d d r mm d d ⎛⎫=-++= ⎪⎝⎭
(4-12) ()222222220.250.430.3250.5r D h d d r mm d d ⎛⎫=-++= ⎪⎝⎭
画出工序草图,如图1工序件草图。
(5) 确定凸、凹模圆角半径
首次拉深凹模圆角半径:
,
(公式4-25),比选取的工序件圆角半径小,故取
r A1=6.5。
首次拉深凸模圆角半径:
mm 56r 170r 1A 1T .)~.(==。
(公式4-27) 第2次拉深凹模圆角半径:r A1=6mm 。
第2次拉深凸模圆角半径:r T1=6mm ,取制件底部圆角半径。
(6) 计算压边力,拉深力
圆筒形件首次拉深压边力: ()()2222112121.31692 6.5 2.515.744Y A F D d r p kN ππ⎡⎤⎡⎤=-+=+⨯⨯=⎣⎦⎣
⎦ 公式(4-18),P 值查表4-9。
圆筒形件首次拉深力:
116914100.9382.6b F d t K kN πσπ==⨯⨯⨯⨯=
公式(4-13),σb 值查表1-2,K 1查表4-7。
圆筒形件第2次拉深力:225914100.7053.2b F d t K kN πσπ==⨯⨯⨯⨯= 公式(4-14),σb 值查表1-2,K 2查表4-7。
4.选择压力机型号
圆筒形件首次工艺总压力:
F Z =F+F Y =82.6+15.7=98.3kN 。
所选压力机公称压力应大于工艺总压力,本题属于浅拉深,一般地压力机的公称压力:F g ≥(1.6~1.8)F Z =1.8×98.3=176.9kN ,预选压力机型号J23-25。
5.确定凸、凹模的间隙,计算凸、凹模工作部分尺寸
有压料装置的拉深模,凸、凹模单边间隙,Z/2=(0.9-1.05)t=1×1=1mm 中间拉深工序件凸、凹模尺寸计算
mm t d D r A 8.51)7031.121(8.0)(8.011=⨯-=-
=图1工序件草图
凹模05000A 70D D A .++==δ,凸模00300
T 68Z 2D D T .)(--=-=δ
最终拉深工序,工件标注内形尺寸,故应以凸模为基准:
凸模()00300
0300
T 358740405840d d p ..min ...).(---=⨯+=∆+=δ 凹模05.00
05.0003.60)23.58()2(+++=+=+=d Z d d T A δ 6.计算或选择模具工作零件(凹模、凸模或凸凹模)的外形尺寸
根据工序件图首次拉深模具工作零件尺寸:
凹模厚度H=55mm ;(工序件h 1=39.2mm )
凹模长宽:A ×B=200×200mm
凸模长度尺寸:L=h 1+h 2+h 3+h 4=39.2+20+15+50=125mm
其中h 2、h 3、h 4分别为凸模固定板、卸料板和压缩后橡胶高度。
第二次拉深模具工作零件尺寸:
凹模厚度H=65mm ;(零件h 1=50.5mm )
凹模长宽:A ×B=200×200mm
凸模长度尺寸:L=h 1+h 2+h 3+h 4=50.5+20+10+40=120mm
其中h 2、h 3、h 4分别为凸模固定板、定位板、预留高度。
7.选择模具材料
凸模采用T10A ,淬火热处理,硬度为HRC58~60,凹模选用Cr12,淬火热处理,硬度为HRC60~62、固定板材料一般采用Q235,垫板材料为45钢。
8.绘制模具总图和工作零件图(另附机械制图图纸)。