拉延模设计
汽车卧铺盖板拉延模设计(有cad图+文献翻译)

摘要本次设计做的是汽车车身覆盖件冲压模设计中的第一序拉延模的设计。
汽车模具在中国因为发展的时间比较短所以在很多方面现在比起一些机械工业发达的国家还有很大的差距。
但我国近年来在汽车模具方面也取得不少的发展与进步。
本次设计我做的是汽车盖板的拉延模设计。
在模具设计中主要是根据设计好的板件来用UG软件进行三维造型设计来完成模具的结构设计然后进行模具加工调试来最终生产出合格的模具。
在三维造型方面主要可以分为压边圈设计、上模设计、凸模设计和下模本体设计。
在进行各部分设计时要严格按照模具结构设计规范来进行设计。
在本次设计中我严格按照冲压模设计标准来进行模具设计,其中有一部分技术规范属于企业内部规范。
本设计经过反复检查没有发现大的纰漏,完全符合模具设计的要求。
关键词:汽车模具 UG 拉延模设计标准AbstractThe design do is auto body panel stamping die design sequence in the first drawing die design. Automotive die in China due to the development of a comparatively short time it is in many ways than some mechanical industrial developed countries there is a great gap. However, in recent years, China has also made the car a lot of mold development and progress. The design of the car I did the cover drawing die design. In the die design are mainly based on panels designed to use the UG software design to complete the three-dimensional structure of the mold and then mold design to final production of qualified commissioning of the mold. Main aspects of three-dimensional modeling can be divided into the blank holder design, the mold design, design and lower die punch body design. During the design of various parts of the structure to be in strict accordance with design specifications to the mold design.In this design I strictly in accordance with design standards for stamping die mold design, including technical specifications are part of the internal specification. After repeated checking of the design found no major flaws, in full compliance with the mold design.Keywords: car mold drawing die design standards UG目录前言 (1)1 设计前的准备工作 (5)1.1 技术协议 (5)1.1.1模具的材料及热处理 (5)1.1.2、模具结构 (5)1.1.3. 工艺、设计、制造要求 (7)1.2 查看工法图 (8)1.3查验对比 (9)1.4结构选择 (9)1.5材质选择 (9)2处理数模及分模线 (17)2.1片体缝合 (17)2.2拉伸实体 (17)2.3设计凸模退刀面 (18)2.4设计凸模主筋 (19)2.5压边圈退刀面的设计 (19)2.6压边圈主筋的设计 (20)2.7确定压边圈导向 (20)2.8导滑面的设计 (21)2.9导板数量的确定 (21)3压边圈的设计 (24)3.1压边圈强度 (24)3.2压边圈压力确定 (25)3.2压边圈让位及补强 (26)3.3气顶杆的设计 (27)3.4压边圈镶块设计 (28)3.5调压垫块与墩死垫块的设计 (28)3.6弹顶销的设计 (30)4上模的设计 (31)4.1上模型面及主筋 (31)4.2上模法兰面和辅筋 (31)4.3上模调压凸台的设计 (31)4.4上模起吊和反转结构的设计 (32)4.5压板槽的设计 (32)4.6导腿的设计 (32)4.7安全平台的设计 (32)4.8设计中心键槽及压板槽加强筋 (33)4.9上模弹顶销的设计 (33)4.10设计减轻空、流水孔及排气孔 (33)4.11定位板地设计 (34)5下模的设计 (41)5.1下模座的设计 (42)5.2设计墩死垫块 (42)5.3设计凸模安装固定法兰 (43)5.4设计安全螺钉 (43)5.5设计安全护板 (44)5.6运输连接的设计 (44)5.7导柱导向设计 (44)5.8下模导板窥视孔的设计 (44)5.9设计完成 (45)致谢 (46)参考文献 (47)前言汽车模具最主要的组成部分就是覆盖件模具。
拉延模设计顺序标准
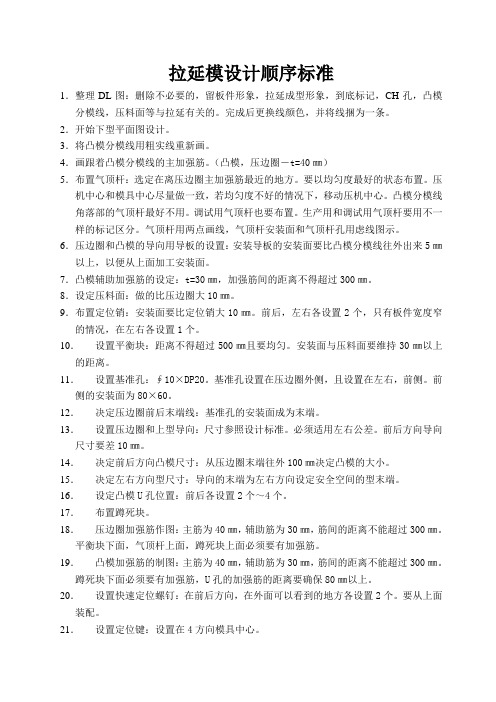
拉延模设计顺序标准1.整理DL图:删除不必要的,留板件形象,拉延成型形象,到底标记,CH孔,凸模分模线,压料面等与拉延有关的。
完成后更换线颜色,并将线捆为一条。
2.开始下型平面图设计。
3.将凸模分模线用粗实线重新画。
4.画跟着凸模分模线的主加强筋。
(凸模,压边圈-t=40㎜)5.布置气顶杆:选定在离压边圈主加强筋最近的地方。
要以均匀度最好的状态布置。
压机中心和模具中心尽量做一致,若均匀度不好的情况下,移动压机中心。
凸模分模线角落部的气顶杆最好不用。
调试用气顶杆也要布置。
生产用和调试用气顶杆要用不一样的标记区分。
气顶杆用两点画线,气顶杆安装面和气顶杆孔用虑线图示。
6.压边圈和凸模的导向用导板的设置:安装导板的安装面要比凸模分模线往外出来5㎜以上,以便从上面加工安装面。
7.凸模辅助加强筋的设定:t=30㎜,加强筋间的距离不得超过300㎜。
8.设定压料面:做的比压边圈大10㎜。
9.布置定位销:安装面要比定位销大10㎜。
前后,左右各设置2个,只有板件宽度窄的情况,在左右各设置1个。
10.设置平衡块:距离不得超过500㎜且要均匀。
安装面与压料面要维持30㎜以上的距离。
11.设置基准孔:∮10×DP20。
基准孔设置在压边圈外侧,且设置在左右,前侧。
前侧的安装面为80×60。
12.决定压边圈前后末端线:基准孔的安装面成为末端。
13.设置压边圈和上型导向:尺寸参照设计标准。
必须适用左右公差。
前后方向导向尺寸要差10㎜。
14.决定前后方向凸模尺寸:从压边圈末端往外100㎜决定凸模的大小。
15.决定左右方向型尺寸:导向的末端为左右方向设定安全空间的型末端。
16.设定凸模U孔位置:前后各设置2个~4个。
17.布置蹲死块。
18.压边圈加强筋作图:主筋为40㎜,辅助筋为30㎜,筋间的距离不能超过300㎜。
平衡块下面,气顶杆上面,蹲死块上面必须要有加强筋。
19.凸模加强筋的制图:主筋为40㎜,辅助筋为30㎜,筋间的距离不能超过300㎜。
003--拉延模几大要素的设计原则
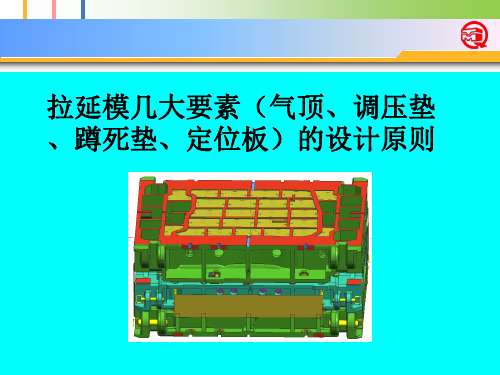
结束
拉延模几大要素(气顶、调压垫 、蹲死垫、定位板)的设计原则
一、拉延模的定义
定义:拉延模就是使平面板料拉伸成具有一定形状 的空心零件的模具
拉延模
平面坯料
空心零件
二、拉延的运动过程
三、拉延模的分类
拉延模分为单动拉延、双动拉延和三动拉延,由于三动拉
延涉及较少,这里只简单介绍前两种。
单动拉延分以下两种
顿死垫
顿死垫—用于压边圈与下模具之 间,在模具死点状态顿死成型的 垫块。 调压垫布置及有关事项:
如果产品范围大于拉延分模线, 则拉延时需要墩死。如果产品范 围在拉延分模线内则不需要墩死 ,二者之间留2mm间隙。 墩死垫尽量布置在调压垫正下方 ,尽可能靠近分模线。墩死垫下 方也要有筋,这样,当墩死时调 压垫墩死垫从上到下均为刚性接 触,增强了模具强度。如果制件 压料面过大,调压垫距离分模线 较远,则保证掉压垫下方的墩死 垫之外,在掉压垫与分模线之间 ,靠近分模线处再相应增加几处 墩死垫,使拉延充分墩死,充分 成型。
注:St:压边圈行程 ST:气垫行程 A:工作台厚 D:=(A+B)-L L:气顶杆长 H、H’:气顶承接面距工作台距离
调压垫
调压垫—用于压边圈与上模控
制二者之间局部压力的垫块。 调压垫布置及有关事项:
调压垫应延分模线均匀分布, 间隔400mm左右。调压垫下 方应有立筋,增加强度。 为了调压效果更好,制件四角 调压时,尽量在角部布置两个 调压垫,避免只在角上放一个 调压垫。 调压垫Z向应均分在压料面上下 两侧 ,使压料面高于调压垫安 装面,如果制件起伏较大,无 法保证安装面低于压料面,则 调压垫安装面与压料面之间留 至少30mm的距离 ,以保证加 工压料面时,球刀不与调压垫 安装面干涉。
汽车覆盖件拉延模设计方法

•
8.确定模具尺寸、导腿尺寸、导板尺寸位置
• 确定模具尺寸 (1)调入模板,调整闭合高(根据工艺卡),模具长宽 (2)确定模具吊耳、起重棒、翻转套大小及位置 • 确定导腿尺寸 (1)导腿长度至少占整体宽度2/5 (2)确定导腿刃入量,保证导腿导板在上模触料之前刃入40mm (3)导腿处导板保证同一高度且同时刃入 • 凸模导板尺寸及位置 (1)导板的安装位置约在凸模长度方向的1/6处 (2)导板导向面的宽度约为凸模长度的1/5-1/4 (3)导板高度〉压边圈行程+60~100mm (4)导板安装面要凸出分模线3~5mm便于加工 ( 5 ) 导板上端面与压边圈距离最好设计为40mm,因钳工调试时 不放墩死垫,容易发生异常。
9.布筋、挖夹持孔、减重孔、流水孔、出气 孔 • 布筋
(1)受力处必须布筋支撑,如调压垫、墩死垫 上下模底面筋要与机床的T槽错开,分模线以内上模本体、凸模、下 模座的筋要对应,导板后面最好有筋支撑 (2)两筋间隔最大350MM,一般控制在300MM以内 (3)为保证铸造清砂,底空不易过深过窄,底空型腔深度最好小于2.5 倍的底空宽度 (4)受力筋上尽量少挖减重孔 (5)尽量避免十字筋 • 夹持孔及减重孔的尺寸及形状,根据模具结构尺寸的不同而不同,但 其底边与模具底面间距至少100MM-150MM • 流水孔一般为直径Φ40的圆孔,设在模具型腔底部,并要保证每个型 腔的液体能流到模具外侧。 • 凸凹模的随型筋上挖Φ50的出气孔,不要存在封闭的型腔 凸凹模的型面上挖Φ4或Φ6的出气孔,打在凸凹模的凹形处
10.满足设计任务书及客户要求
• • • • • • • • • 活动件防护装置 在下模装防护板 压板槽、上模快卡、下模快速定位的要求 键槽及通键、加工基准孔的要求 起重形式的要求 气顶接柱上加钢垫、气顶躲空的要求 气路及电路位置的要求 模具防反、防侧向力的要求 客户及任务书对标准件的要求 客户的其他要求(如铸字、叉车过孔等)
汽车覆盖件数值模拟与拉延模设计

汽车覆盖件数值模拟与拉延模设计汽车覆盖件(简称覆盖件)是指覆盖汽车发动机、底盘、构成驾驶室和车身的薄钢板异形体的表面零件(外覆盖件)和(内部零件),与一般冲压件相比较,具有材料薄、形状复杂、结构尺寸大、表面质量要求高及生产成本高等特点。
在覆盖件的冲压工艺设计、模具设模具制造工艺上,也具有独自的特点【1】,一般需要经过多道工序(如拉延、冲孔修边、翻边、整形等)才能完成。
在其整个生产中,拉延成形则是一道关键的工序,而决定拉延成败和工件质量的,则是拉延成形的模具。
以前采取单件压制,生产效率、材料利用率和设备利用率均比较低。
将拉延工艺作了改进,采用中心对称一模两件的方法重新设计和制模,大大提高了设备利用率和生产效率[2]。
1冲压工艺分析(1)rember冲压工艺rember零件的材料为cr340,板料厚度为1mm, 抗拉强度750 mpa,延伸率16% 。
零件的结构外形如图1所示。
该零件的结构复杂,需要经过多道工序才能完成,根据该工件的工艺分析,工艺路线为:落料→拉延→冲孔、修边→cam修边→翻制→冲孔、分离。
具体工序图如图2所示。
该零件局部成形较多,是冲孔、拉延和翻边、修边复合的结果。
在拉延过程中,采用一模两件对称方式进行拉延,为保证能将拉延件的全部空间形状一次拉延出来,不应有凸模接触不到的“死区”,即既要保证凸模能全部进入,尽量使拉延深度差最小,以减小材料流动性和变形分布的不均匀性。
工艺补充是拉延工艺不可缺少的部分,但工艺补充部分应尽量减少,以提高材料的利用率。
工艺补充部分除考虑拉延工艺和压料面的需要外,还要考虑修边和翻边工序的要求。
该工件的工艺补充面和垂直修边线如图3所示:(2)拉延仿真结果与成形性分析。
拉延仿真选用的材料与上面相同,板坯尺寸为920mm×200mm,摩擦系数为0.1,压边力初定为95kn,冲头速度5000mm/s,在定义好模具各部分运动和边界条件后,提交工作到ls-dyna进行计算。
汽车覆盖件单动拉延模设计流程DOC

汽车覆盖件单动拉延模设计流程总的原则:1.平面图的作法:为了设计的顺利进行,下模与压边圈一起进行并行设计,再将压边圈移出,之后再将压边圈镜像的得到上模。
2.主剖面的作法:剖面位置一般平行于X轴且在制件中心附近,其主要表达的内容有:模具导向、导腿、气顶、调压垫、模具高度与挡料板。
3.一般剖视:一般平行于Y轴,位置在结构不太清楚的地方,需表达出前后挡料板、压板槽等。
4.向视:表达导腿、起重棒、翻转套等。
5.局部向视:当工件起伏比较大的时候应有局部向视图,表达出压料面、调压垫、档料板及压边圈及上模之间的关系,尤其是在高度方向。
关键名词:模具中心:模具的几何中心制件中心:由工艺给定的坐标点(原点,基准点)机床中心:冲压设备的中心点在设计过程中最好三心重合一设计流程1.下型平面图取出拉伸工艺型,从中提取出坯料线与分模2.下型平面图根据分模线确定凸模注意:筋的确定3.下型平面图根据分模线(凸模)、压边圈及工作台确定气顶孔及模具中心注意:模具中心最好与机床中心及制件重合,模具中心如何确定,气顶布置注意事项(1) 根据工作台(机床下底面)及分模线选定气顶孔,可适当调整模具型面来适应气顶孔(2)根据气顶孔来再次调整模具中心4.下型平面图根据凸模芯与气顶孔来决定导板,是采用内导向还是外导向注意:导向的确定(1)确定凸模与压边圈之间的导板及其位置(2)根据导板调整压边圈上的立筋5.如果工件起伏比较大,就应该作出向视图,以确定工件的纵向变化,阶梯或倾斜。
6.下型平面图由坯料线确定符型区,由仿型区确定调压垫(调整垫一一对应),再决定导向方式(两种导向方式嵌入式导板与导腿),从而基本确定压边圈的外形轮廓。
注意:调压垫、压边圈、外导向(1)确定压边圈符型区(2)确定挡料块(3)确定调压垫:调压垫直径为60mm,离立壁大于30mm,调压垫之间相距为300mm左右(4)确定压边圈基本外型及导向,并加上限位螺钉,同时注意导板的宽度。
拉延模具设计

设计步骤:1分析工艺文件首先拿到工艺后要分析各部分,分模线、坯料线、拉延后坯料线、重力坯料线、拉延筋、到底标记、左右标记、CH孔,有时还有弹顶销、穿刺孔和破裂刀位置分模线决定了凸模的外圈轮廓大小;坯料线决定了压料面的大小;从拉延前后坯料线可以看出板料在压料面上的流入情况;重力坯料线决定了定位板定位位置和高度;拉延筋可以控制板料的流入量;到底标记用来检测是否拉伸到位(设计在废料区);左右标记是产品左右件的标识,来实现焊装白车身的目的;CH 孔是在拉延(序)模上的拉延件上冲制的两个模具制造调试用的研模(定位)工艺孔。
是带件研合各序模具型面(和形状)的基准确认拉延模行程和气顶位置:参考工艺文件确定导向形式:根据制件形状确定模具的导向形式,大致分为外导向拉延,内导向拉延,四角导向拉延。
本套模具采用内导向。
暂定基准高:根据机床对操作高的要求自动线看是否要前后序操作高一致或是浮动范围。
本套模具选择闭合高度为800mm。
下图为工艺曲面2图层的设置用ug2.0打开工艺曲面进入建模模块。
把第1层的工艺面复制到11层把第2层的胚料线,分模线复制到12层。
3面的缝合打开11层,其它层全部关闭。
用缝合命令缝合曲面缝合的时候注意不要直接点击确定,应该点击应用看他是否报错如果报错看是那些地方有错然后更改更改好以后再缝补,检查报错,如果没报错,再拉伸一个通过曲面的体A。
用缝补好的曲面裁剪A,如果成功说明缝补成功。
下面是封面操作截图:注意缝合公差红点的地方表示有错修改完成无报错裁剪实体成功,删除实体保存一次图档,进入下一步4偏置工艺面用大致偏移命令偏移Z向-60.-50和60的三个面。
下面是操作截图:三个偏置的面如图所示5凸模本体的制作把12层设置为工作层,其它层关闭。
投影分模线到XY平面如图用分模线拉伸实体上下各500mm 如图:把11层设置为可选用工艺面把刚拉伸的实体上部分裁减掉如图:把得到的实体移动到62层。
然后用分模线拉伸一个上下各500mm,里外分别10mm 的实体环如图:用向Z方向偏置-50mm的面裁减掉这个体的上部分如图:把所得到的实体移动到62层。
拉延模设计规范

通用设计标准
5
模具防呆标准
1.仅导板导向时:
2.导柱兼导板导向时:
注:1.防呆仅设置于模具F侧右下侧导板;
2.仅导柱导向时,设置于模具F侧右下侧导柱。
1-2
拉延模设计标准
5
定位具设置
侧定位具
侧定位具
后定位具
前定位具
注:1.前后定位具分两种:一种为不带塑料滚轮的普通定位具,用于内装件的拉延模毛坯定位;另一种为带塑料滚轮的定位具,用于外观件的拉延模毛坯定位。
2.模具导向型式选用原则:
模具类别
模具名称
特大型
大型
中型
小型
钢板模
大
小
落料模
Ø100导柱
Ø80导柱
Ø60导柱
Ø50导柱
Ø40导柱
Ø32导柱
拉延模
100导板
A=145
100导板
A=120
Ø40导柱
Ø32导柱
修边冲孔模
Ø100导柱
Ø80导柱
Ø60导柱
Ø50导柱
Ø40导柱
1-2
通用设计标准
5
铸件减轻孔标准
注:
1.铸件逃孔制作标准
A
B
C
D
R
100-200
60
60
60
30
2.除制作必要外,外围铸孔尽量不要制作;
3.铸件不加工处均倒角C10,吊索滑动部分均倒R20;
加工面外缘处倒角C2-C3;
4.铸孔标准上列为参考值,实际制作考虑模具强度;
5.铸件筋条间最大距离≤300mm。
2.压板槽设置数量:
模具长度L
压板槽单边数量
L≤1600
2
- 1、下载文档前请自行甄别文档内容的完整性,平台不提供额外的编辑、内容补充、找答案等附加服务。
- 2、"仅部分预览"的文档,不可在线预览部分如存在完整性等问题,可反馈申请退款(可完整预览的文档不适用该条件!)。
- 3、如文档侵犯您的权益,请联系客服反馈,我们会尽快为您处理(人工客服工作时间:9:00-18:30)。
第2章 拉延模结构设计过程 第2.1节 技术要求 每一个项目都会与客户签定技术协义(或其它类似的文件),技术协义中包涵了客户对模具要求的所有相关信息,每一个项目开始前都应该认真阅读其技术协义。 接到生产任务后,首先应该查看工法图,了解相关信息,包括件名、产品的材质、料厚、坯料尺寸、生产线以及本序所使用的机台、模具闭合高度等信息。 根据产品材质的力学性能和料厚从技术协义(或其它与客户签定文件或自家设计标准—首先以客户要求为依据)中查寻模具是否采用壤块结构以及模具本体及壤块的材质,如果材质为锻件需采用壤块结构,铸件则为整体结构。 生产线分为手工生产线和自动生产线,自动生产线又分为普通自动线和高速线,自动线上的模具要设计相应的感应装置即感应开关,感应开关有直流和交流之分,具体视生产线而定。手工生产线工序件在两台机床之间的传递是通过人工完成的,而自动生产线则是能过机器人或机械手来完成。高速线与普通自动线最本质的区别体现在生产速度上。 通常情况下,拉延模安排在生产线的第一台机床上生产(有些需要落料的产品则不是),该机床根据生产线的不同有单动和双动之分,相应的模具结构也对应单动结构和双动结构。 工法图上会指示出每一序的模具闭合高度,对应的机床有最大闭合高度和闭合高度调节量(可从机床参数中查取),机床的最大闭合高度减去闭合高度调节量为机床的最小闭合度。一般情况下手工线模具的闭合高度为参考值,结构设计人员可做适当调整,但必须在机床的最大闭合高度-20mm与最小闭合高度+20MM之间调整。自动线的模具工法除了指示闭合高度外还会指示模具的基准点高度,都必须按照工法指示值设计,不可调整,若结构设计无法满足则向工法设计人员反馈。 查看完以上信息后检查工艺数模,对比工艺数模上的工艺内容是否与工法图指示的工艺内容一致,包括是否需要日期标记、件号标记、左/右件标记、到底标记及位置指示、CH孔位置、是否有切角、是否需要刺破刀等,若不一致应该向工法设计人员反馈确认。 了解了以上一些基本信息后开始模具结构设计,下面为左A柱加强板拉延模的模具结构设计过程。 第2.2节 片体的检查 一、 处理数模及分模线 分两种情况,一种是工法那边提供的是UG数模,另一种是工法那边提供的是CATIA数模。 (1.)工法给的是UG工艺数模 先要对数模(片体)进行缝合处理,以方便后面的实体裁减操作。数模由产品和工艺面组成,一般情况下OP10即第一序的数模约定放在第10层,相应的工序线放在
第11层,后续以此类推,每一序的产品数模均放在16层。打开.part文件后, 利用缩放功能放大检查数模的各个部位是否有明显的孔洞,如有需先将其逢补起来,如下图所示的圆孔和腰形孔,象这类形状较为规则的 孔洞通过“N边曲面”可以逢合起来, (2.)工法给的是CATIA工艺数模 如果工法给的是CATIA数模,则直接在CATIA里面最GYSM进行修补。第一步可以先用结合命令把片体缝合一下试试,如果提示红色,则对其进行修补,直到能结合到一起,然后用提取命令检查片体,直到没有问题(如果工法是在CATIA中做的片体,一般都是很好修补的)。由于方法跟(1)差不多,就不在重复讲述了。 第2.3节 凸模的设计 分模线与片体处理好后,我们开始做凸模的设计。由GYSM可以看出,这个是开口拉延,做凸模时,我们要用线把分模线给封闭起来(这个可以是在草图之前,也可以是做草图的时候,下面是以草图封闭分模线为例)。首先,用参考元素中的平面 建立一个基准面。 点击完成草图,退出草图设计。然后右键单击几何体,定义为工作对象。点击基于草图特征里面的凸台命令。把凸模的型面做出来, 实体拉伸出来后,不要先做退刀面,先把型面颜色涂上,不要等着最后在染颜色。操作方法是:首先选择结构树中的凸台,把图形属性里面的第一个颜色框改成型面的颜色蓝色,这时整个实体的表面都是蓝色。然后,选择非型面面,把颜色改成铸件颜色。再选择几何体,把颜色改成铸件的颜色。染好颜色后,开始做退刀面。 然后点击确定,凸模退刀面就做了。把退刀面涂上相应的加工颜色,不同的颜色代表不同的材质或者不同的加符号,图纸里的颜色都必须按照设计标准设定! 在这里顺便把凸模的起吊翻转螺纹孔做出来, 第2.4节 压边圈的设计 先以凸模的底面做个平面,以新平面为基准面,创建草图,选中分模线和拉延边界线,投影到草图上,修剪不用的曲线,完成后如下图所示: 以草图拉伸实体,类型直到曲面,限制选择数模。以实体底面为草图基准,创建草图,如下图所示: 拉伸实体,把压边圈连成一个整体。由于两边的高度不一样,两个草图可以分开 选择。 也可以通过多凸台拉伸 接着做压边圈的退刀面。压边圈的退刀面做法与凸模相同,需要注意的是压边圈的退刀面要向远离凸模的一侧偏置3MM(如果压边圈上有产品,则偏置1mm)然后再做10MM的退刀面。方法与做凸模的退刀面一样。 压边圈退刀面做好后做主筋,方法与凸模相同。 确定了导向形式后再来确定导滑面的宽度和高度。压边圈在X/Y方向上的导滑面的宽度分别由压边圈
在相应方向上的尺寸来确定,按设计标准取凸模尺寸的0.2-0.25倍。 高度则由该件的拉延行程来确定,按照设计标准,压边圈在顶起状态下,压边圈导滑面与对应凸模上导板在高度上的搭接量为70MM(小件50MM)以上。在空间允许的情况下小件也尽可能的做70MM以上。双动拉延模为大件100MM小件80MM。 拉延行程是把压边圈向+Z方向移动一直到压边圈的面高出凸模最高点5-10MM时所移动的距离,亦是模具工作时压边圈的行程,在工法图中由工法设计人员给出。 确定导板数量以及导板在平面上的们置。导板的数量按照设计标准确定,如下图: 图2-29导滑板的设计标准(a) 导板在平面上的位置原则上按照标准布置,导板中心距边缘1/6L—1/4L之间,模具两侧相对的导板搭接量在50MM以上. 不能按照上述数值布时导板应尺量向两侧布置,距离尽量远。 由于采用箱式外导,所以,布置导板的时候,直接把空间留出来就可以了。 若是采用内导结构,由于导板是凸出的,所以压边圈相应位置要做让位处理,导板在Z向的位置要要满足下左图所示要求,且各处导板在高度上位置要相同,导滑面长度也要相同,以保证压边圈同时导向。 左图表示模具闭合时即压边圈在最低点时压边圈与导板背托上端的让位要有最小30MM的距离。 布置压边圈的调压垫块和气顶杆。 首先设计压边圈气顶杆接柱。 设计标准规定,气顶杆接柱高度小于等于100MM时为¢70的圆柱,大于100MM时为下端¢70上端¢80的锥形柱。 气顶杆接柱的高度要接合机床的气顶杆顶出度度、压边圈的行程和压边圈下底面的位置来确定。此件是路虎项目,该线气垫顶出高度有170、220、290三个档,设结构计员可自已选择,本件选择290,因为顶杆的顶出高度越高压边圈的顶杆高度就越短。机床的 气垫顶出高度290 减去 压边圈的行程100+50=150等于140,即为压边圈气顶杆接柱下端面到机床工作台面(模具的下模下底面)的距离。下模下底面相对于模具绝对坐标原点在Z方向的值为模具的仿形高,工法图中查得此件该序的仿形高为660。由以上数据可确定压边圈气顶杆接柱下端面在绝对坐标系下的Z坐标值。 压边圈下端面(除去气顶杆接柱)的确定,先要考虑压边圈的厚度(Z向尺寸)单动为200MM,还要考虑下模座的强度, 压边圈下端面—40=下模座厚度 此处考虑下模座厚度取200,由以上数据可计算出压边圈气顶杆接柱高度为100,需要采用锥形的。 设计调压垫块和压边圈的辅筋。在压边圈上与调压垫块对应的是墩死垫块, 调压垫块和墩死垫块对应模具的上模和下模都必须要有到模具上、下底面的立筋, 第2.5节 上模的设计
上模型面及主筋 上模型面与凸模一样,都是随型50MM,操作方式也是一样的。即先建个草图,把拉延边界线投影到草图上,完成草图,用凸台拉伸直到曲面。如下图所示: 再建一个草图,用凹槽把型面50mm皮厚做出来。 完成草图,凹槽拉伸直到曲面(粗略偏移50的偏题)即可。 然后做上模主筋,方法与凸模一样,上模主筋是由分模线向两边各偏置25MM(即二分之一主筋厚度)得到,如下图所示: 设置上模法兰面和辅筋。上模法兰面的设计方法与压边圈相同,辅筋的厚度参考模具式样书,间距应小于等于300, 设计上模调压凸台。上模调压凸台与压边圈上的调压垫块对应,上模要设计到底面的立筋。 设计上模起吊和翻转。下图四个角上的是起吊、翻转用插入式吊耳(起吊及翻转形式的选择请查阅相关设计标准)。 设计压板槽。压板槽的作用是通过螺栓或自动装夹装置将模具固定机床的工作台或滑块上。压板槽的尺寸要符合客户要求,位置要与所使用机床的T型槽对应(自动生产线要与自动夹装置对应)。 设计上模弹顶销。为了防止生产时制件卡在凹模上,有必要在上模设计弹顶销。上模弹顶销要设计在工艺面上或者产品的非A面上(上模放不放弹顶销这个根据板件的形状判断)。 设计减轻孔、流水孔及排气孔。 为节约模具成本,在满足设计标准及不影响模具强度的前提下,应最大限度的减轻模具重量。 上模要设计流水孔,使模具清洗或者生产调试时产生的油液能够从模具型腔中顺利流出。 模具生产时,上模和压边圈闭合,在压边圈、上模和坯料之间形成封闭的空间,随着上模下行,封闭空间的容积会越来越小,里面的空气压缩,产生很大的负压力,使板料不能按要求成型,也浪费了压机的额定功率。从下死点开始,板料与压边圈和上模一起上升,板料贴在凸模上,有可能使板件变形,也可能由于产生真空,板件吸附在凹模型腔内。冲压速度越快上述现象就越明显,为了防止上述不良现象的发生,要在凸模和凹模表面开通气孔,通气孔一般设置在型面相对凹面的凹R角根部。为了防止粉尘落入模具型腔中,上模通气孔要使用防尘软管。 材料导正架(定位板)的设计。材料导正架安装在压边圈上,由于要在上模上做让位,所以放在上模设计完之后设计。 定位板的作用是确定板料在型面上的位置。拉延模定位板的有效定位高度最小30MM,即材料导正架的直边部分的上端到对应型面的距离最小30MM。自动线上的模具要设计感应器开关、集线盒感应电路过孔等。 第2.6节 下模的设计 设计下模座。在模具吊运的过程中,下模座承受着
整套模具的重量,下模座的强度非常重要。由3.0可知,下模座的厚度取290MM,下模座的辅筋除了要考虑气顶杆外(全顶出的有气顶杆的地方就要让位),其它的与上模相同,下模座上要与压边圈的气顶杆接柱对应设计¢100的过孔。此处由于是厢式导向,所以,下 模上要有导腿, 设计标准规定,当模具两端高度大于200时,要设计加工用装夹槽。此处由于模具长宽尺寸较大,高度也较小,故不设计装夹槽。 设计墩死垫块。前面已经提到墩死垫块和压边圈上的调压垫块对应且下面要对应有到模具底面的立筋。另外,墩死垫块还要分两种情况考虑: 制件的修边线在压边圈上。如下图所示: 此时墩死垫块与压边圈的间隙为0,墩死垫块选用淬火型(三协DBH)。因为压边圈上有修边线时不墩死制件不能成型到位。 二、除上述情况外,压边圈不墩死,则墩死垫块与压边圈设计2MM间隙,墩死垫块选用淬火型(三协DBH)。如下图示: 此件由于产品不在压边圈上,即压边圈上有形状,所以压边圈留2mm间隙,墩死垫块选用淬火型(三协DBH)。如下图所示: 注:为了考虑某种特殊情况下压边圈安全平台处的受力,在下模上设计四处垫块(具体参考相关标准)。如下图(下图为凸模内导的模具截图): 设计凸模安装固定法兰。凸模与下模座要用螺钉固定,凸模要用键定位,有明键和暗键两种形式,主要依据模具生产厂家的机加工精度选择,此处选择明键, 设计原则