文献翻译—粘接减振片式多头热压机
压铸术语翻译

精心整理压铸及机械英语词汇(2009-09-0120:11:44)压铸及机械词汇A 安装尺寸installdimension凹模固定板retainerplate凹模femaledie,femalemold,negativemoldB 备件变质变质剂扒渣保温炉保压压力表面缺陷C 抽芯侧面抽芯sidecore抽芯油缸coreoilcylinder插拔式结构plug抽芯机构corepuller抽芯油缸支架bracketofcylinder粗糙度roughness/degree铸件表面粗糙度surfaceroughness擦伤galling尺寸公差dimensiontoleranceofcasting 除气degassing吹气净化blowpurifying除气剂degassingflux出渣出渣口沉渣出炉口菜花头重熔D端盖动模垫块锻钢氮化处理nitridingtreatment断裂fracture塑性断裂plasticfracture导柱guidepillar导套guidesleeve导向板guideplate导向件guidepart动型movingdie/ejectordie/movablemould动模座板movingclampplate/bottomclampingplate 定模座板fixedclampplate/topplate定型fixeddie/coverdie定模套版bolster/fixeddie顶杆顶出结构顶出吊装孔吊环镀钛处理多肉缺陷电火花打磨F分流锥分型面附页attachment/appendix复位杆resetbar(rod)附件故障accessory覆盖剂coveringflux废金属料scrap浮渣cinder反射炉reverberatoryfurnace废品reject飞边jointflash仿真simulationG规格specification/standard数值孔径固定段坩埚坩埚炉感应电炉沟槽硅H滑块滑块部件滑块退让焊补welding-on横浇道runner合模dielocking横流道runner回炉料foundryreturns合型moldassembling/closing/dielocking合型力dielockingforce化学成分不合格chemicalconsistenceanalysisJ浇口套spruebush浇排道系统pouringsystem浇不足misrun浇注浇注断裂浇道比浇包精整精度接口击伤金相组织金属残液金相检验金属型涂料diecoating/coatingformetalmold 加压速度rateofpressureincreasing间隙clearance精炼refining精炼剂refiningflux精密铸造precisioncasting静置holding/stewing渗透impregnation集渣装置dirttraps夹杂类缺陷inclusiondefects夹渣entrappedslag/slaginclusion 夹具toolfixturesK壳体开炉孔洞缺陷库存L冷却冷却水管冷却系统冷却水接口coolingwaterconnector 冷裂coldcrack冷隔coldlap铝Aluminum裂纹crack拉伤caughtcasting拉杆孔drawbar螺纹screw/thread螺纹结构screwstructure螺纹公称直径(直径diameter)公称尺寸(名义尺寸)specifiedsize/nominaldimension 漏油leakageofoil棱边倒角炉料炉衬炉气分析炉前分析流痕M毛坯毛坯铸件毛刺模芯core模框frame模槽moldchannel模套chase/bolster/frame模具钢diesteel模具图纸molddrawing内浇口in-gate冒口riser/feederhead冒口浇注系统feederheadgatingsystem 镁Magnesium锰Manganese密闭耐压系统tightnesstestN内浇道镍P配油盘排气块排气槽排气孔排气塞跑铝喷射冶金injectingmetallurgy喷丸清理shotblastingcleaning抛丸清理wheelblastingcleaning偏析segregation破坏性实验destructivetestQ取件机extractor去除浇冒口de-gating清铲chipping缺陷铸件defectingcasting气孔blowhole/gascavity/pinhole/porosity 气孔缩blowholeshrinkage去毛刺de-burring氢清理R热处理热电偶热裂熔炼熔化率熔池bath熔剂flux熔渣slagS水管waterpipe三维造型3D三坐标测量仪coordinate3上模座板upperclampingplate缩孔shrinkage缩松dispersedshrinkage疏松porosity(dispersedshrinkage)渗漏leakage缩陷试块试模T推板推杆铜钛W网状裂纹crazecrack/crazing/checking 未浇满pouredshortX型芯core型腔moldcavity镶拼处splicingplace斜导柱孔holeofinclinedguidepillar 楔紧块wedge型芯弯曲corebending下模座板loweringclampingplate型芯固定板core-retainerplateX光射线检验X-rayinspectionY压铸机压室压实压射压铸型易损件预应力永久型permanentmold硬点hardspot溢流槽overflowwell印痕indentation氧Oxygen荧光检验fluorescenttestZ真空接口vacuumconnector真空排气管vacuumexhaustblock 总接头mainconnector中接头middleconnector直浇道sprue转接处(转口)transit装配图铸钢支架造渣增压针孔沾铝转运包转向器steeringrack柴油式传动叉车Dieselforklift 复印机copyingmachine服务器Server绘图仪Graphicplotter兼容机compatiblemachine材料库warehouse投影仪projector半自动车床semi-automaticlathe半自动立式钻床drillmachine表面粗度测量仪surfaceroughnessgauge 布洛维硬度计Brinellhardnessgauge测氢仪齿轮油泵储气罐电动葫芦电子秤吊斗高压离心风机combustionblower管道泵processwaterpump烘箱oven监控系统monitoringsystem简易数控车床digitallathe交流弧焊机Arewelder抛光机polisher锯床saw空压机aircompressor冷冻式干燥机dryer红外线测温仪冷却塔coolingtower滤油机焊接机模温机平面磨床气动量仪切割机清洗机台式砂轮机abrasivemachine卧式液压拉床broachingmachine 铣床millingmachine钻床drillingmachine液压机hydraulicmachine真空机vacuumpump时效炉agingfurnace电阻炉stressrelieffurnace探伤机diagnosticmachine加工中心machiningcenter车床lathe钻削中心drilling&cuttingcenter别克切边机取件机FL装卸车在建工程捡漏机电磁阀solenoid??valve溢流阀spillovervalve调速阀speedcontrolvalve压力传感器pressuretransducer 三角带wedgeshapedbelt节流阀throttlegovernor同步齿型带timingbelt喷涂机spraycoater轴承(main)bearing浮球阀floatvalve/ballcock行车bridgecrane平衡重式叉车counterbalancedforklift轮毂螺栓制动蹄片制动液叶片侧护板急停按钮三相开关行程开关断路器接触器contactor中间继电器intermediaterelay时间继电器timerelay控制变压器controltransformer开关电源switchingsupply节能灯energy-savinglamp日光灯管fluorescenttube自整流高压汞灯泡self-rectifyinghighpressuremercurylamp 电工胶布garrers/electricaltape焊条weldingrod石笔slatepencil外圆磨床externalgrinderCouplingTie-barHose软管,水龙带Warrantyperiod保修期Nozzle管口,喷嘴Naturetan日晒后的颜色,茶色Electricfitting电装、Rubberpad橡胶垫Shockabsorbingrubberstopper减震橡皮塞Dieheight模子闭合高度Diestroke动模行程Intensificationratiostandard增强比标准Plungerstroke柱塞行程Plungertippenetration冲头穿透力InletMortarManifold总管,集合管Clampforcesensor夹紧力传感器Attenuate削弱Emulsification乳化作用中子线??wireforsliding出模斜度draftangle隔皮bur掉肉misrun研配grindTurbidity浑浊度Refractmeter折光仪Sediment沉淀物GlycolDroolingLithiumSlantCoreslidingface型芯滑面Fluxtreatment熔剂处理Dieclampingcylinder模具夹紧气缸Clogging堵塞,闭合Electrodebar电极棒Fumigationcertificate熏蒸消毒证书Crate条板箱,柳条箱Resinparts树脂零件Oilring油环Gearbox齿轮箱,传动箱,变速箱Draftangle出模斜度Tapanddrillgauge丝锥及钻头规TapborerRackTubes油缸CupSealsFeedPipes输油管Spools卷轴RecuperatingSeal(恢复性密封) InflatorTubes充气. CutSealsSteeringHoses转向胶管Biscuitthickness料柄厚度注油孔oilfilterpoint牛皮纸kraft/brownpaper瓦楞纸flutingpaper崩料chargedownslide/collapse 卡涉现象interferencephenomenon复制模偏心距抽大缸料头抽芯WrenchStopperCheckvalve止回阀Orifice孔,口Pilotvalve领示阀,导阀Coldshut冷疤,冷结Flowmark波纹,流线谱Surgepressure冲击压力,脉动压力Jackbolt定位螺栓Anchorhole锚栓孔Dustseal档尘圈Valvecover气门盖,阀盖Cylindertube汽缸筒AirhoseAtomizerStrainerShaftPulley滑车,滑轮Springwasher弹簧垫圈Inverter电源交换器Cuttingfluid切削液refractioncoefficient折光系数pluggauge塞规colorshade色泽redleadpower红丹粉stressrelief去应力castingfilm铸型薄膜castform铸造成形,铸型castingsealer铸件渗补剂castingstrain铸造应变castingstress铸造应力sparkplug火花塞internal-combustionenginecylinder内燃机汽缸pinion小齿轮pinionbearing小齿轮轴承pinioncage主动[行星]齿轮架,差速器壳,差速盘pinioncuttingmachine齿轴切削机床pinionhead齿轴齿顶pinionshapedcutter插齿刀valvecock阀栓valvecottar气阀制销valvedisc阀盘valvedischargecentrifuge活门卸料式离心机valvefollower阀推杆分层Delaminationfilling-engine梳丝机器fillingagent填充剂;填料fillingauger装载螺旋fillingcompoun填料fillingfunnel注液漏斗车架钣金测板内侧板焊钳焊条焊点前轴后翼子板切削性能cuttingcharacteristic散热性能heatdispersion耐磨性能wearresistantproperty摩擦系数frictioncoefficient灰铸铁grayiron;graphiticcastiron缸套cylinder,sleeve,barreltubepipe 导轨面guideway(face)铣刀盘facemillingcutter/facingcutter 刀盘toolpan/cutterhead磨削余量grindingallowance耐用性endurance钝化刀尖圆弧(刀具)燃烧室磨屑滤器芯差速器废气涡轮增压盲区turboloch喷油器oilsprayer/atomizer汽化器carburetor硬质合金刀具carbidetippedtool精镗刀具fineboringtoolspanner扳子(美作:wrench)double-endedspanner双头扳子adjustablespanner,monkeywrench活扳子,活络扳手boxspanner管钳子(美作:socketwrenchcalipers卡规pincers,tongs夹钳punchscraperreamerhacksawoilcan边刨床插床slottingmachine车刀lathetool车轮车床carwheellathe车削turningBayonet卡口Bearingprocessingequipment轴承加工机Beltdrive带传动Bendingmachines弯曲机Boringheads搪孔头Boringmachines镗床Cablemakingtools造线机CNCtoolingsCNC刀杆CNCwire-cuttingmachines电脑数控线切削机Conveyingchains输送链Crimpingtools卷边工具Disposabletoolholderbits舍弃式刀头Etchingmachines蚀刻机Honingmachines搪磨机Lappingmachines精研机Millingheads铣头Moldpolishing/texturing模具打磨/磨纹Planingmachines刨床bankmarkbiteblisterbloomingblowholeblushingbreaking-in冒口带肉bubble膜泡burnmark糊斑burr毛边camber翘曲centrebuckle表面中部波皱check细裂痕checking龟裂chipping修整表面缺陷clamp-off铸件凹痕collapse塌陷crackcrazingcrazingedgefadingfissureflangewrinkle凸缘起皱flaw刮伤flowmark流痕galling毛边glazing光滑greasepits污斑grindingdefect磨痕haircrack发裂haze雾度incrustation水锈indentation压痕mismatchmottleneckingnickoverflowpeelingpit坑pock麻点pockmark痘斑resinstreak树脂流纹resinwear树脂脱落riding凹陷sagging松垂saponification皂化scar疤痕scrapjam废料阻塞scratch刮伤/划痕scuffing深冲表面划伤seam裂痕sinkmarkstreaksurgingsweatouttorsion扭曲warpage翘曲waviness波痕webbing熔塌weldmark焊痕whitening白化wrinkle皱纹表面处理关联用语时效硬化agehardening气体硬化airhardening空气韧化airpatterning退火阳极效应滚镀滚筒打光染黑法青熟脆性箱位退火封箱渗碳辉面电镀光辉热处理brightheattreatment 旁路热处理bypassheattreatment 化学电镀chemicalplating化学蒸镀chemicalvapordeposition 大气热处理controlledatmosphere 锐角效应cornereffect儒缓放电creepingdischarge 压花embossing部分淬火selectivequenching。
四柱液压机中英文翻译、外文文献翻译
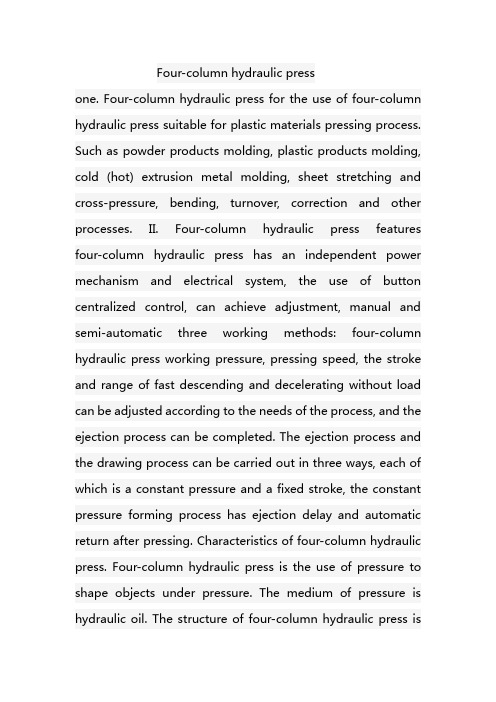
Four-column hydraulic pressone. Four-column hydraulic press for the use of four-column hydraulic press suitable for plastic materials pressing process. Such as powder products molding, plastic products molding, cold (hot) extrusion metal molding, sheet stretching and cross-pressure, bending, turnover, correction and other processes. II. Four-column hydraulic press features four-column hydraulic press has an independent power mechanism and electrical system, the use of button centralized control, can achieve adjustment, manual and semi-automatic three working methods: four-column hydraulic press working pressure, pressing speed, the stroke and range of fast descending and decelerating without load can be adjusted according to the needs of the process, and the ejection process can be completed. The ejection process and the drawing process can be carried out in three ways, each of which is a constant pressure and a fixed stroke, the constant pressure forming process has ejection delay and automatic return after pressing. Characteristics of four-column hydraulic press. Four-column hydraulic press is the use of pressure to shape objects under pressure. The medium of pressure is hydraulic oil. The structure of four-column hydraulic press issimple, economical and practical. OCTAGONAL SHAPE for appearance. Four-column hydraulic machine control electrical box with glass door, PLC computer control or general electrical two, with reliable work, reliable, intuitive action, easy maintenance. Single Button centralized control. It has two operation modes of adjustment and single circulation of both hands. Four-column hydraulic press hydraulic control can be integrated with cartridge valve system, reliable action, long service life, hydraulic impact is small, reducing the connection pipeline and leakage point, or ordinary hydraulic control two kinds. III. Four-column hydraulic press common faults and maintenance methods four-column hydraulic press common faults and maintenance methods: In winter and worse working conditions, four-column hydraulic press system to check, maintenance, often change the working oil. Great attention should be paid to the storage and transportation of the working oil of four-column hydraulic press. The oil drums shall be marked and covered. In winter, do not pay attention to the air condensed into water and oil, do not rust the barrel into the rust pieces. In winter, the four-column hydraulic engine and other mechanical systems to take a number of preventive measures, such as covering anti-freezing, heating and heatpreservation, the use of low viscosity oil, etc. , are applicable to the hydraulic system. In the four-column hydraulic press Hydraulic drive system, are some of the more sophisticated parts. Although people feel labor-saving and convenient to the hydraulic transmission of four-column hydraulic press, they also feel that it is easy to be damaged. The main reason is that the working principle and structure characteristics of four-column hydraulic press are not clear. Hydraulic systems have three basic "disease-causing" factors: pollution, overheating, and entering the air. These three disadvantages are closely interrelated, and the occurrence of any one of them will be associated with the emergence of another problem or problems. By practice, 75% of the hydraulic system "pathogenic" reasons, are caused by these three. 1. The working oil of the four-column hydraulic press is spoiled because of entering the dirt 2. Overheating 3. Entering the air solution: the Cleaning and assembly of some major precision parts in the four-column hydraulic press system should be carried out in a very clean room, indoor should have clean floor and airtight door window, the temperature had better keep in 200C or so. IV. Four-column hydraulic press common general maintenance method four-column hydraulic presscommon general maintenance method (1) four-column hydraulic press action failure electrical wiring is not firm or wrong connection check electrical (2) four-column hydraulic press slipper crawl 1 system accumulated air or pump suction 2 precision adjustment or column Oil 1 check whether the pump suction pipe is in air or not, then move up and down several times and add oil on the 2 columns, readjust the accuracy (3) when the sliders of the four-column hydraulic press descend slowly, the pressure supporting force is too large to adjust the back pressure valve so that the upper chamber of the upper cylinder does not have pressure, the maximum is not more than 1 MPA, four-column hydraulic press after stopping the slide block under serious 1 CYLINDER MOUTH SEAL RING leakage pressure valve adjustment pressure is too small or pressure mouth is not strict 1 watch cylinder mouth, SEND OIL AND GAS 2 adjust pressure check valve mouth 5. Pressure gauge needle of four-column hydraulic press swings badly 1 pressure gauge oil circuit has air 2 pipeline mechanical vibration pressure gauge damage 1 slightly loosen the pipe joint when the pressure is up, 2 deflates the pipe 2 fastens the pipe 3 replace the pressure Gauge 6. Four-column hydraulic press high pressure travelspeed is not enough, up pressure slow 1 high pressure pump flow regulation too small 2 pump wear or burn 3 system leakage serious 1 according to the pump manual adjustment, pUMP ECCENTRICITY can be adjusted to 5 bar 2 at 25 MPA. The pressure drop of four-column hydraulic press is too fast when keeping pressure 1. The valves involved in keeping pressure are not strict or the pipeline is leaking 2. The sealing ring in the cylinder is damaged 1. Check the filling valve, the sealing research of the pressure-keeping Relief Valve 2. Replace the sealing ring 8. The utility model relates to a screw four-column hydraulic press, which belongs to the field of hydraulic press, in particular to a hydraulic press with screw drive, the task of which is to provide a transmission device, the main nut thread is forced only when the slide block presses the workpiece, and the main nut is not pushed by the hydraulic cylinder during the non-pressing workpiece stroke of the slide block, so that the lubricating oil is filled into the screw bearing surface. The screw Rod is located at the center axis of the machine body and is mounted on the machine body through the bearing. The upper end of the screw rod is connected with the inertia wheel, the main nut is matched with the lower part of the screw Rod, and is connected withthe main slide block through the main flange The auxiliary nut is matched with the middle part of the screw Rod, and is connected with the auxiliary slide block through the auxiliary flange. The guide rail is mounted symmetrically in a central axis in the screw four-column hydraulic press, and the main slide block and the auxiliary slide block are slidily connected along the Guide Rail, the end of the Piston Rod of the hydraulic cylinder is hinged with the auxiliary sliding block, which can improve the lubrication condition of the nut and screw and prolong the service life of the screw four-column hydraulic press. About the hydraulic station of four-column Hydraulic Press: The working principle of the hydraulic station of four-column hydraulic press is as follows: the motor drives the oil pump to rotate, the pump draws oil from the oil tank, converts the Mechanical Energy into the hydraulic oil pressure energy, the hydraulic oil is transmitted to the hydraulic machinery's cylinder or motor through the external pipeline after the direction, pressure and flow are adjusted by the hydraulic valve through the Integrated Block (or valve combination) , it controls the change of direction, force and speed of hydraulic motor, and drives all kinds of hydraulic machinery.Four-column hydraulic press hydraulic station also known as hydraulic pump station, is an independent hydraulic device. It provides oil according to the requirements of the main engine, and controls the direction, pressure and flow of oil flow. It is suitable for the main engine and hydraulic equipment can be separated on a variety of four-column hydraulic press. As long as the user purchase the press station and the host on the executive body (cylinder or motor) connected with the tubing, hydraulic machinery can achieve a variety of specified action, working cycle. The hydraulic station of the four-column hydraulic press is composed of a pump device, a manifold or a valve combination, a fuel tank and an electrical box. The functions of each component are as follows: The pump device is equipped with a motor and an oil pump, which is the power source of the hydraulic station of the four-column Hydraulic Press and converts the Mechanical Energy into the pressure energy of the hydraulic oil. Manifold block-is composed of hydraulic valve and Channel Body. It can adjust the direction, pressure and flow of the hydraulic oil. Valve assembly-is a plate valve mounted on a vertical plate, connected to the pipe behind the plate, with the same function as the manifold block. TANK-A semi-closed, plate-welded vessel with a filter air filter,etc. . It is used for storage, cooling and filtration of oil. Electrical box-in two forms. One is a Terminal Board with external leads; the other is equipped with a complete set of control appliances. Four column Hydraulic Press Pressure is small what reason: 1. Is the oil in the cylinder of the four-column hydraulic press dirty? 2. Are you holding it in? Pressure activated? 3. Four-column hydraulic time long, loose parts with, internal leakage? 1, four-column hydraulic pump wear serious, large internal leakage. 2. Relief Valve malfunctions and is normally open. 3. Directional valve internal leakage is large. 4, four-column hydraulic machine implementation of the original leakage inside the large, small pump pressure. The application of four-column hydraulic forming technology four-column hydraulic forming technology has a wide range of applications in automobile, aviation, aerospace and pipeline industries, the hydraulic forming technology of four-column hydraulic press is mainly applicable to the hollow structure with round, rectangular or special section which varies along the component axis, such as the special-shaped pipe fittings of automobile exhaust system, the hollow frame with non-circular section, such as engine bracket, instrument panel bracket, body frame (about 11% ~15% of the vehicle mass) , hollow shaft parts and complex pipe fittings. The suitable materials for four-column hydraulic forming process include carbon steel, stainless steel, aluminum alloy, copper alloy and nickel alloy. In principle, the materials suitable for cold forming are all suitable for four-column hydraulic forming process. Four-column hydraulic system four-column hydraulic press is the use of hydraulic transmission technology for pressure processing equipment, can be used to complete a variety of forging and pressure forming process. For example, steel forging, metal structural parts of the molding, plastic products and rubber products, and so on. Four-column hydraulic press is one of the earliest machines to use hydraulic transmission. At present, hydraulic transmission has become the main transmission form of pressure processing machinery. Four-column hydraulic press in Heavy Machinery Manufacturing, aviation industry, plastic and Non-ferrous metal processing industries, four-column hydraulic press has become an important equipment. On the four-column hydraulic press non-pressure problem: Q: four-column hydraulic press does not rise, starting up switch has 10MM action, rise after non-pressure, sliding work, how is it? Answer: Check the four-columnhydraulic pump outlet pressure, control system pressure, whether the support valve is stuck. The Piston slipping is related to the insufficient supporting force of the lower chamber, and the non-pressure keeping may be the leakage of the relief valve of the four-column hydraulic press. Four-column hydraulic press system is relatively simple, do not consider overhauling too much trouble. The difference between four-column hydraulic press and pneumatic press the difference between four-column hydraulic press and pneumatic press the pneumatic press has noise, small force, easy maintenance will not leak oil; four-column hydraulic press quiet, strong, slightly more complex maintenance. It's all about the APP. The steel workshop noise is already quite big, may not consider the noise factor. If the force requirements are relatively large, then choose four-column hydraulic press. If, the force requirement is not so big (50kg or less) the barometric pressure is good, is also cheap. The drawing cylinder of the four-column hydraulic press adopts fast cylinder, the speed can reach 280 mm / s, the drawing force can reach 1000 KN, the blank holding force can reach 800 Kn, and the speed and pressure can be adjusted in the prescribed range, users can choose the best drawing speed and blankholder force according to their needs, and can draw out all kinds of products such as high quality stainless steel, which is the ideal equipment for sheet metal drawing. The oil supply system of the Hydraulic Chamber of the four-column hydraulic press is required to meet the technical requirements of hydraulic forming, and the system is not too complicated. Its action as follows: Motor start, pump to oil by the reversing valve flow back to the oil tank, pump unloading. When 1DT power, oil through the valve, one-way valve into the oil plate will be pressed into the Matrix and forming. At the end of the forming, 1DT POWER CUT, 2DT power, oil into the oil injection through the supercharger cylinder, under the action of ultra-high pressure, the sheet metal further close to the concave die to form its small round corner. The key of the hydraulic system of the four-column hydraulic press is frequency converter 5 and supercharger cylinder 10. In the process of hydraulic forming, the working flow and pressure provided to the hydraulic chamber by the hydraulic system should be constantly changing according to the requirements of the process, therefore, the power consumed by the hydraulic system should also be changing with the change of the working flow and pressure. Describe the GeneralMechanical Theory of pressure transfer before proceeding to analyze the phenomenon of pressure shock and to rationalize the fluid equation. It is necessary to transport the liquid between two energy sources by taking part in this result about valve positioning at a longer point with little friction in the pipeline. The valve is connected to the same downstream pipe section as to the upstream pipe section. The pressure impingement flow will be passed between the two lines through the valve operation, assuming that the valve closing speed should not be applied to the solid circle theory. If the valve is closed and the flow of the liquid is in the opposite direction, it moves slowly, resulting in the compression of the liquid and the expansion of the cross section of the pipe. The increased pressure in the valve causes the high-pressure liquid to flow in reverse, extending the time it takes for the liquid to flow through the pipe to the valve. The flow of this high-pressure liquid similar to the propagation of sound, is dependent on the liquid and pipe materials as a medium. Similarly, a delay in the downstream flow of the valve will result in a reduction in pressure at the valve. This result denies that the flow of a high pressure liquid is along a downstream pipe, preventing the flow of the liquid, assuming that the fluidpressure in the downstream pipe does not reduce the fluid pressure or the vapor pressure or the pressure released by the dissolved gas, the considerations of willingness are different. Thus, the closed valve causes the flow of high-pressure fluid to flow along the pipe, although those flows have various symptoms. The flow of pressure relative to the stability of the valve through the open pipe. This effect is related to the liquid flow delay between the two cross-sections of the pipe, the pipe itself is affected due to the reverse high pressure liquid, pipe wall expansion. At the same time, the downstream pipe is shortened and the large cross-section deformation of the pipe due to the reduced pressure flowing through the liquid is due to the pipe material and can be demonstrated. For example, use thin-walled rubber tubing. The high-pressure liquid moves along the flow. It has been proved that the velocity of the liquid is close to that of sound due to the tension flow of the liquid along the pipe wall. In this piping material, however, this is a secondary role, and when it is recognized that its presence can explain part of the pressure transfer time as the valve closes, it has little effect on the application of pressure standards in pressure impact phenomena. After the valve is closed, the time of compression will depend primarily on thesystem boundary conditions, which will be easily illustrated in a number of charts to depict the results of the valve closure on the same system, what happens to the pipeline at each time period. Since the valve closure is instantaneous, a valve with liquid close to each pipe section will bring the valve to a stop, and high-pressure fluid flow may have already passed through each pipe section. At the appropriate velocity C and at time t, the liquid has passed a distance of 1 ct, and in each segment, the Cross section of the pipe is deformed at a distance of 1. The time for the high pressure liquid to reach the storage station is t 1 / C, and an unstable position appears in this distance, which is at the junction of the pipeline and the storage station. Since it is not possible to have laminar flow at the junction of the stations, the maintaining pressure and other values flow through each station before the valve is closed.四柱液压机一.四柱液压机用途四柱液压机适用于可塑性材料的压制工艺。
常用研磨机外文文献翻译、中英文翻译、外文翻译

附录ACommonly used grinding machinePierre H G.Vertical-shaft crusher[J]. 2002.Abstract:As a kind of important ultra-precision processing method,the a dvantage of grinding is high machining accuracy, processing materials ran ge, almost suitable for all kinds of materials processing, grinding can get very high precision and shape accuracy, even can reach the limit, the m achining accuracy of grinding device is simple, does not need a lot of th e complex mechanical and not demanding equipment precision conditions.Keywords:Grind;Machining;Mechanical equipment1.IntroductionAs a super finishing one method, grinding machine is mainly used f or the high precision grinding workpiece plane, the surface of cylindrical workpieces both inside and outside, tapered face inside, sphere, thread face and other type surface. Its main types have dise-type grinding machi ne, shaft type grinding machine, magnetic grinding machine and all kinds of special grinding machine.Dise-type grinding machine points single plate and double-tray two t o double-tray grinding machine used the most common. In double-tray po lishing machine, multiple workpiece and into the mill plate, located on th e cage between inside, maintain frame and workpiece drives by eccentric or planet of plane parallel movement. The mill rotating, the parallel wit h the grinding plate can not turn, or with grinding plate under negative s pin, and can move to pressure workpiece (pressure adjustable). In additio n, with the grinding plate can also turning round pillar rocker to Angle, unloading workpieces. Double-tray grinding machine is mainly used for p rocessing two parallel planes, a plane (two pressure should be increased t o the workpiece accessorie), outside YuanZhuMian and sphere (with belt v-shaped slot grinding plate), etc. YuanZhuMian, because the processing and workpiece to both sliding, shall be reasonable choose to keep rolling type and arrangement plane slots Angle. Only a single plate grinding m achine, used for grinding plate under the grind workpiece under plane, ca n make the different shapes and sizes with plate processing, grinding wor-1-kpiece higher precision. Some grinding machine with the grinding process can be automatic calibration grinding plate institution.2.Whole mechanism researchShaft type grinding machine from positive, negative spin of spindle drive work-piece or inquiry with adjustable grinding ring or abrasive (gre at) rotation, the structure is simple, used for grinding inside and outside cylindrical planes.Magnetic grinding machine is by using magnetic force transmission t o stainless steel mill for high frequency workpiece needle to rotary motio n; But for precision workpiece in the hole and blind Angle, tiny crack ri se obvious good polishing grinding remove burr effect.Special grinding machine by grinding workpiece in accordance with t he different, have central hole grinding machine, steel ball grinding mach ine and gear grinding machine, etc.In addition, still have a kind of adopting similar centerless grinding principle unconditional grinding machine, used for grinding cylindrical wo rkpieces.Grinding is by abrasive abrasive effect on surface of workpiece, to t race processing. Grinding workpiece surface dimension accuracy, form an d position precision, abrasive tools, such as life and milling efficiency de pends largely on whether grinding movement.In order to make the surfac e of workpiece grinding uniform, from the perspectives of kinematics con cludes the following plane grinding best kinematics condition: firstly, wor kpiece with relative research of plane movement, should guarantee by gri nding workpiece surface with different points on relative research are the same or similar grinding track; secondly, grinding motion is provided by the workpiece and the relative movement between developed a realizatio n, different points on the surface of workpiece velocity should as far as possible the grinding the same; thirdly, grinding movement direction shou ld constantly change, grinding grain crisscross changeful, favors the surfa ce roughness of workpiece machining, but should avoid reduced by grind ing workpiece surface with different points on the relative research curvat ure grinding track changes too big, fourthly, grind with or pads working surface shape accuracy will reflect on the surface of workpiece, so the tr ajectories of workpiece with throughout the inquiry should be distributed homogeneously, favors the surface and uniform worn with research; finall y, workpiece with relative research by abrasive removal direction a sports freedom, so that can avoid for grinding machines guidance precision and cause errors.Grinding basic principle is to use embedded in coating or pressure with the abrasive particles on grind workpiece with and, through research in the relative movement under certain pressure for processing surface fi nish machining process.The cylindrical plane grinding process is to use free grits are two pl ane of cylinder scraping and extrusion process of removing materials to r educe cylindrical height, improve planar degree and reduce the surface ro ughness purpose. These remove effects through the cylindrical grinding pl ate with the relative movement in grits role down to perform.Abrasive is the main medium grinding process.The grinding process according to abr asive change can be divided into three stages.The first stage: the broken free abrasive stage. At the beginning of precision lapping ,initial larger grits cutting, then first participate in a bel t of edges and abrasive polyhedron, cutting ability. The role of the press ure, the grits size by crushing make more grits are competing in cutting, then on one hand consumption dimensions and cylinder of processes, thi s phase residual surfaces grinding efficiency is higher, size, cylindrical su rface roughness consumed fast. But this stage time is very short.Second stage: the grits particular and Mosaic stage. Due to the effec ts of stress fluctuation grinding plate and cylinder interaction constantly r olling mill grain, make the coarse grinding grain gradually broken into fi ne grits and size to converge, then the highest grinding efficiency, time a lso the longest. With the continuously detailed, all kinds of abrasive is al so relatively stable stage elements, at this stage of the geometry precision ball improved and basically reaches corresponding requirements, the surf ace quality gradually enhance, roughness decline. This phase is gangqiu s tability processing phases.The third stage: grits passivation and grinds light phase. In this phas e abrasive most refined for o. apms m the following three fine grits, grit s by the shape of the original sharp geometry without sharp edges into t he sleek sphere, grinding speed greatly reduced. Passivation of grits only to micro powder cylindrical plane more trace grinding, polishing quantit y Grinding quantity is about from 0.2 to 0.3 microns per hour .This sta ge cylindrical surface roughness further reduce and eventually reach the s tandard.Generally speaking, there are four main grind track: (1) linear grindi ng trajectory. This method is applicable to the steps of long and narrow plane workpiece grinding can obtain higher geometry precision, but not easily get smaller surface roughness. (2) swing linear grinding trajectory. Can achieve good straightness. (3) spiral grinding trajectory. Mainly used for discs shape or cylindrical workpieces grinding, flat end can gain a h igh flatness and smaller surface roughness. (4) "8" glyph grinding trajecto ry. Suitable for flat class overhauled and small plane workpiece of grinding workpiece, can make mutual grinding plane media contact and has ev en developed evenly wear.In the production practice, grinding is a kind of common finishing c raft, grinding method unceasing progress and renewal, to adapt to the dif ferent processing requirements of various literature material reports, there are many methods of grinding, polishing, abrasive flow injection of ultras onic machining, electrochemical polishing, chemical polishing, magnetic a brasive grinding, liquid abrasive grinding etc exterior smooth the whole p rocessing technology. The most commonly used and application most is a mechanical polishing, its characteristic is can obtain higher dimension pr ecision, shape accuracy and low surface roughness, but requires the opera tor has high level of technology and experience, machining efficiency lo w, labor intensive, processing quality not easy to control, the surface resi dual stress is big, surface residual grits can also affect surface quality.Magnetic abrasive law is through magnetic polarity will magnetic abr asive surface processing, suction pressure in surface processing and betwe en the poles for millimeter clearance, can be in magnetic abrasive machi ning gap arrange them along the field, forming elastic magnetic brush an d pressure on the surface of workpiece attached. Rotating magnetic field or rotating product, make magnetic brush and relative motion processing, thus pure polisher a surface. The characteristics of magnetic grinding is t hat no matter how the surface processing, you should just make poles sh ape and processing surface shape can be generally anastomose,it can accu rate grinding a fine curved surface of workpiece surface, and magnetic a brasive act applies to grind cutting and grinding process is usually to co mpetent complex shape parts surface smooth processing.Grinding machine adopts stepless speed regulation control system, ca n be easily adjusted adheasine grind various parts of grinding speed. Usi ng electricity - gas proportional valve close-loop feedback grinding machi ne pressure control, can independence regulation pressure device. Slow fal ling installed in the up-tray to prevent the crash of brittleness slice. Thro ugh a time relay and a grinding counter, can press processing requiremen ts accurately Settings and control of milling time and grinding lap. Work can be adjusted pressure mode, achieve grinding set time or lap will automatically stop alarm prompt, realize half automation.Grinding machine variable speed control method, grinding has three stages, namely beginning, formal stage and end stage, beginning abrasive acc rotation, the official stage abrasive constant speed rotating, end stag e abrasive slow down, whose character is, rotating grinding beginning ingrinding speed, artificially controlled by slow from zero to acceleration o f fast speed increases, when the abrasive ascended to the formal grinding speed, acceleration the half of the changes occur a inflection point, cont rol the acceleration of grinding speed by slowly by almost to the maxim um speed is reduced, until the grinding tools to formally, the acceleration of speed grinding speed reduced to zero.3.SummaryUse the characteristic of a solid abrasive abrasive, according to the r elative movement between grinding workpiece track density distribution, a reasonable design abrasive abrasive density distribution on, in order to make abrasive that occur in the grinding process does not affect the abra sive wear face type, thereby significantly improve the precision of the su rface type precision.Future as people are becoming more demanding to improve product performance, grinding machining accuracy and processing with its high q uality, which has attracted the attention of people. Therefore, ultra-precisi on will be more conspicuous in the future.附录B常用研磨机Pierre H G. Vertical-shaft crusher[J]. 2002.摘要:研磨是超精密加工中一种重要加工方法,其优点是加工精度高,加工材料范围广,几乎适合于各种材料的加工,研磨加工可以得到很高的尺寸精度和形状精度,甚至可以达到加工精度的极限,研磨装置简单,不需要大量复杂的机械并且不苛求设备的精度条件。
机械加工工艺夹具类外文文献翻译、中英文翻译、外文翻译

TOOL WEAR MECHANISMS ON THE FLANK SURFACE OF CUTTINGINSERTSFOR HIGH SPEED WET MACHINING5.1 IntroductionAlmost every type of machining such as turning, milling, drilling, grinding..., uses a cutting fluid to assist in the cost effective production of pa rts as set up standard required by the producer [1]. Using coolant with some cutting tools material causes severe failure due to the lack of their resistance to thermal shock (like AL2O3 ceramics), used to turn steel. Other cutting tools materials like cubic boron nitride (CBN) can be used without coolant, due to the type of their function. The aim of using CBN is to raise the temperature of the workpice to high so it locally softens and can be easily machined.The reasons behind using cutting fluids can be summarized as follows.® Extending the cutting tool life achieved by reducing heat generated and as a result less wear rate is achieved. It will also eliminate the heat from theshear zone and the formed chips.® Cooling the work piece of high quality materia l under operation plays an important role since thermal distortion of the surface and subsurfacedamage is a result of excessive heat that must be eliminated or largelyreduced to produce a high quality product.Reducing cutting forces by its lubricating e ffect at the contact interface region and washing and cleaning the cutting region during machining from small chips. The two main reasons for using cutting fluids are cooling and lubrication.Cutting Fluid as a Coolant:The fluid characteristics and condition of use determine the coolant action of the cutting fluid, which improves the heat transfer at the shear zone between the cutting edge, work piece, and cutting fluid. The properties of the coolant in this case must include a high heat capacity to carry away heat and good thermal conductivity to absorb the heat from the cutting region. The water-based coolant emulsion with its excellent high heat capacity is able to reduce tool wear [44]. Cutting Fluid as a Lubricant:The purpose is to reduce friction bet ween the cutting edge, rake face and the work piece material or reducing the cutting forces (tangential component). As the friction drops the heat generated isdropped. As a result, the cutting tool wear rate is reduced and the surface finish is improved.Cutting Fluid PropertiesFree of perceivable odorPreserve clarity throughout lifeKind and unirritated to skin and eyes.Corrosion protection to the machine parts and work piece.Cost effective in terms off tool life, safety, dilution ratio, and fluid lif e.[1]5.1.1 Cutting Fluid TypesThere are two major categories of cutting fluidsNeat Cutting OilsNeat cutting oils are poor in their coolant characteristics but have an excellent lubricity. They are applied by flooding the work area by a pump and re-circulated through a filter, tank and nozzles. This type is not diluted by water, and may contain lubricity and extreme-pressure additives to enhance their cutting performance properties. The usage of this type has been declining for their poor cooling ability, causing fire risk, proven to cause health and safety risk to the operator [1].® Water Based or Water Soluble Cutting FluidsThis group is subdivided into three categories:1.Emulsion ` mineral soluble' white-milky color as a result of emulsion of oil inwater. Contain from 40%-80% mineral oil and an emulsifying agent beside corrosion inhibitors, beside biocide to inhibit the bacteria growth.2.Micro emulsion `semi-synthetic' invented in 1980's, has less oil concentrationand/or higher emulsifier ratio 10%-40% oil. Due to the high levels ofemulsifier the oil droplet size in the fluid are smaller which make the fluid more translucent and easy to see the work piece during operation. Otherimportant benefit is in its ability to emulsify any leakage of oil from themachine parts in the cutting fluid, a corrosion inhibitors, and bacteria control.3.Mineral oil free `synthetic' is a mix of chemicals, water, bacteria control,corrosion inhibitors, and dyes. Does not contain any mineral oils, andprovides good visibility.23 to the work piece. bare in mind that the lack of mineral oil in this type of cuttingfluid needs to take more attention to machine parts lubrication since it should not leave an oily film on the machine parts, and might cause seals degradation due the lack of protection.5.1.2 Cutting Fluid SelectionMany factors influence the selection of cutting fluid; mainly work piece material, type of machining operation, machine tool parts, paints, and seals. Table 5-1 prepared at the machine tool industry res earch association [2] provides suggestions on the type of fluid to be used.5.1.3 Coolant ManagementTo achieve a high level of cutting fluids performance and cost effectiveness, a coolant recycling system should be installed in the factory. This system will reduce the amount of new purchased coolant concentrate and coolant disposable, which will reduce manufacturing cost. It either done by the company itself or be rented out, depends on the budget and management policy of the company [1].Table 5-1 Guide to the selection of cutting fluids for general workshop applications.Machining operation Workpiece materialFree machining and low - carbon Medium- Carbon steels High Carbon and alloy steels Stainlessand heattreated GrindingClear type soluble oil, semi synthetic or chemical Turning General purpose, soluble oil, semi synthetic or synthetic fluid Extreme-pressuresoluble oil,semi-synthetic orsyntheticfluid Milling General purpose, soluble oil, semi synthetic or synthetic Extreme- pressure soluble oil, semi- synthetic or synthetic Extreme-pressuresoluble oil,semi-synthetic orsyntheticfluid(neat cutting oilsmay beDrillingExtreme- pressure soluble oil, semi- synthetic or GearShapping Extreme-pressure soluble oil, Neat-cutting oils preferable HobbingExtreme-pressure soluble oil, semi-synthetic or synthetic fluid (neat cutting oils may be Neat-cutti ng oils BratchingExtreme-pressure soluble oil, semi-synthetic or synthetic fluid (neat Tapping Extreme-pressure soluble oil, semi-synthetic or Neat-cuttingpreferableNote: some entreis deliberately extend over two or more columns, indicating awide range of possible applications. Other entries are confined to a specific class of work material.Adopt ed f rom Edw ard and Wri ght [2]5.2 Wear Mechanisms Under Wet High Speed M achiningIt is a common belief that coolant usage in metal cutting reduces cuttingtemperature and extends tools life. However, this researchshowed that this is not necessarily true to be generalized overcutting inserts materials. Similar research was ca rried out ondifferent cutting inserts materials and cutting conditionssupporting our results. Gu et al [36] have recorded adifference in tool wear mechanisms between dry and wetcutting of C5 milling inserts. Tonshoff et al [44] alsoexhibited different wear mechanisms on AL 2O 3/TiC inserts inmachining ASTM 5115, when using coolants emulsionscompared to dry cutting. In addition, Avila and Abrao [20]experienced difference in wear mechanisms activated at theflank side, when using different coolants in t estingAL 2O 3lTiC tools in machining AISI4340 steel. The wearmechanisms and the behavior of the cutting inserts studied inthis research under wet high speed-machining (WHSM)condition is not fully understood. Therefore, it was theattempt of this research to focus on the contributions incoating development and coating techniques of newlydeveloped materials in order to upgrade their performance attough machining conditions. This valuable research providesinsight into production timesavings and increase inprofitability. Cost reductions are essential in the competitiveglobal economy; thus protecting local markets and consistingin the search of new ones.5.3 Experimental Observations on Wear Mechanisms of Un-CoatedCemented Carbide Cutting Inserts in High Speed WetMachiningIn this section, the observed wear mechanisms are presented of uncoated cemented carbide tool (KC313) in machining ASTM 4140 steel under wet condition. The overall performance of cemented carbide under using emulsion coolant has been improved in terms of extending tool life and reducing machining cost. Different types of wear mechanisms were activated at flank side of cutting inserts as a result of using coolant emulsion during machining processes. This was due to the effect of coolant in reducing the average temperature of the cutting tool edge and shear zone during machining. As a result abrasive wear was reduced leading longer tool life. The materials of cutting tools behave differently to coolant because of their varied resistance to thermal shock. The following observations recorded the behavior of cemented carbide during high speed machining under wet cutting.Figure5-1 shows the flank side of cutting inserts used at a cutting speed of 180m/min. The SEM images were recorded after 7 minutes of machining. It shows micro-abrasion wear, which identified by the narrow grooves along the flank side in the direction of metal flow, supported with similar observations documented by Barnes and Pashby [41] in testing through-coolant-drilling inserts of aluminum/SiC metal matrix composite. Since the cutting edge is the weakest part of the cutting insert geometry, edge fracture started first due to the early non-smooth engagement between the tool and the work piece material. Also, this is due to stress concentrations that might lead to a cohesive failure on the transient filleted flank cutting wedge region [51, 52]. The same image of micro-adhesion wear can be seen at the side and tool indicated by the half cone27 shape on the side of cutting tool. To investigate further, a zoom in view was taken atthe flank side with a magnification of 1000 times and presented in Figure 5-2A. It shows clear micro-abrasion wear aligned in the direction of metal flow, where the cobalt binder was worn first in a higher wear rate than WC grains which protruded as big spherical droplets. Figure 5-2B provides a zoom-in view that was taken at another location for the same flank side. Thermal pitting revealed by black spots in different depths and micro-cracks, propagated in multi directions as a result of using coolant. Therefore, theii~ial pitting, micro-adhesion and low levels of micro-abrasion activated under wet cutting; while high levels of micro-abrasion wear is activated under dry cutting (as presented in the prev ious Chapter).Figure 5-3A was taken for a cutting insert machined at 150mlmin. It shows a typical micro-adhesion wear, where quantities of chip metal were adhered at the flank side temporarily. Kopac [53] exhibited similar finding when testing HSS-TiN drill inserts in drilling SAE1045 steel. This adhered metal would later be plucked away taking grains of WC and binder from cutting inserts material and the process continues. In order to explore other types of wear that might exist, a zoom-in view with magnification of 750 times was taken as shown in Figure5-3B. Figure 5-3B show two forms of wears; firstly, micro-thermal cracks indicated by perpendicular cracks located at the right side of the picture, and supported with similar findings of Deamley and Trent [27]. Secondly, micro-abrasion wear at the left side of the image where the WC grains are to be plucked away after the cobalt binder was severely destroyed by micro-abrasion. Cobalt binders are small grains and WC is the big size grains. The severe distort ion of the binder along with the WC grains might be due to the activation of micro-adhesion and micro-abrasionFigure 5-1 SEM image of (KC313) showing micro abrasion and micro-adhesion (wet).SEM micrographs of (KC313) at 180m/min showing micro-abrasion where cobalt binder was worn first leaving protruded WC spherical droplets (wet).(a)SEM micrographs of (KC313) at 180m/min showing thermal pitting (wet).Figure 5-2 Magnified views of (KC313) under wet cutting: (a) SEM micrographs of (KC313) at 180mlmin showing micro-abrasion where cobalt binderwas worn first leaving protruded WC spherical droplets (wet ), (b) SEMmicrographs of (KC313) at 180.m/min showing thermal pitting (wet ).SEM image showing micro-adhesion wear mechanism under 150m/min (wet).(a)SEM image showing micro-thermal cracks, and micro-abrasion.Figure 5-3 Magnified views of (KC313) at 150m/min (wet): (a) SEM image showing micro-adhesion wear mechanism under 150m/min (wet), (b) SEM image showing micro-fatigue cracks, and micro-abrasion (wet).Wear at the time of cutting conditions of speed and coolant introduction. Therefore, micro-fatigue, micro-abrasion, and micro-adhesion wear mechanisms are activated under wet condition, while high levels of micro-abrasion were observed under dry one.Next, Figure 5-4A was taken at the next lower speed (120m/min). It shows build up edge (BUE) that has sustained its existence throughout the life of the cutting tool, similar to Huang [13], Gu et al [36] and Venkatsh et al [55]. This BUE has protected the tool edge and extended its life. Under dry cutting BUE has appeared at lower speeds (90 and 60 m/min), but when introducing coolant BUE started to develop at higher speeds, This is due to the drop in shear zone temperature that affected the chip metal fl ow over the cutting tool edge, by reducing the ductility to a level higher than the one existing at dry condition cutting. As a result, chip metal starts accumulating easier at the interface between metal chip flow, cutting tool edge and crater surface to form a BUE. In addition to BUE formation, micro-abrasion wear was activated at this speed indicated by narrow grooves.To explore the possibility of other wear mechanisms a zoom-in view with a magnification of 3500 times was taken and shown in Figure 5-4B. Micro- fatigue is evident by propagated cracks in the image similar to Deamley and Trent [27] finding. Furthermore, Figure 5-4B shows indications of micro-abrasion wear, revealed by the abrasion of cobalt binder and the remains of big protruded WC grains. However, the micro-abrasion appeared at this speed of 120m/min is less severe than the same type of micro-wear observed at 150m/min speed, supported with Barnes [41] similar findings. Therefore, micro-abrasion, BUE and micro-fatigue were activated under wet condition while, adhesion, high levels micro-abrasion, and no BUE were under dry cutting.SEM i m a g e o f(KC313) showing build up e d g e under 120m/min (wet).(a)SEM i m a g e o f(KC3 13) showing micro-fatigue, and micro-abrasion (wet). Figure 5-4 SEM images of (KC313) at 120m/min (wet), (a) SEM image of (KC313). showing build up edge, (b) SEM image of(K C313) showing micro-fatigue and micro-abrasion33 Figure 5-5 is for a cutting tool machined at 90m/min, that presents a goodcapture of one stage of tool life after the BUE has been plucked away. The bottom part of the flank side shows massive metal adhesion from the work piece material. The upper part of the figure at the edge shows edge fracture. To stand over the reason of edge fracture, the zoom-in view with magnification of 2000 times is presented in Figure 5-6A. The micro-fatigue crack image can be seen as well as micro-attrition revealed by numerous holes, and supported with Lim et al [31] observations on HSS-TiN inserts. As a result of BUE fracture from the cutting tool edge, small quantities from the cutting tool material is plucked away leaving behind numerous holes. Figure 5-6B is another zoom-in view of the upper part of flank side with a magnification of 1000 times and shows micro-abrasion wear indicated by the narrow grooves. Furthermore, the exact type of micro-wear mechanism appeared at the flank side under 60 m/min. Therefore, in comparison with dry cutting at the cutting speed of 90 m/min and 60 m/min, less micro-abrasion, bigger BUE formation, and higher micro-attrition rate were activated.Figure 5-5 SEM image showing tool edge after buildup edge was plucked away.SEM image showing micro-fatigue crack, and micro-attrition.(a)SEM image showing micro-abrasion.Figure 5-6 SEM images of (KC313) at 90m/min:(a) SEM image showing micro-fatigue crack, and micro-attrition, (b) SEM image showingmicro-abrasion.5.4 Experimental Observations on Wear Mechanisms of Coated CementedCarbide with TiN-TiCN-TiN Coating in High Speed WetMachiningInvestigating the wear mechanisms of sandwich coating under wet cutting is presented in this section starting from early stages of wear. Figure 5-7 shows early tool wear starting at the cutting edge when cutting at 410m/min. Edge fracture can be seen, it has started at cutting edge due to non-smooth contact between tool, work piece, micro-abrasion and stress concentrations. To investigate further the other possible reasons behind edge fracture that leads to coating spalling, a zoom-in view with magnification of 2000 times was taken and presented at Figure 5-8A. Coating fracture can be seen where fragments of TiN (upper coating) had been plucked away by metal chips. This took place as result of micro-abrasion that led to coating spalling. On the other hand, the edge is t he weakest part of the cutting insert geometry and works as a stress concentrator might lead to a cohesive failure on the transient filleted flank cutting wedge region [51, 52].Both abrasion wear and stress concentration factor leave a non-uniform edge configuration at the micro scale after machining starts. Later small metal fragments started to adhere at the developed gaps to be later plucked away by the continuous chip movement as shown in Figure 5-8A. Another view of edge fracture was taken of the same cutting tool with a magnification of 2000 times as shown in Figure 5-8B. It presents fracture and crack at the honed tool edge. A schematic figure indicated by Figure 5-9, presented the progressive coated cutting inserts failure starting at the insert edge. It was also noticed during the inserts test that failure takes place first at the inserts edge then progressed toward the flank side. Consequently, a study on optimizing the cutting edgeFigure 5-7 SEM image of (KC732) at 410m/min showing edge fractur e and micro-abrasion (wet).SEM image showing edge fracture.(a)SEM image showing fracture and crack at the honed insert edge.Figure 5-8 SEM of (KC732) at 410m/min and early wear stage (wet): (a) SEM image showing edge fracture, (b) SEM image showing fr acture and crack atthe honed insert edge.radius to improve coating adhesion, and its wear resistance, might be also a topic for future work.Figure 5-1.0A was taken after tool failure at a speed of 410m/min. It shows completely exposed substrate and severe sliding wear at the flank side. The coating exists at the crater surface and faces less wear than the flank side. Therefore it works as an upper protector for the cutting edge and most of the wear will take place at the flank side as sliding wear. Figu re 5-10B is a zoom-in view with magnification of 3500 times, and shows coating remaining at the flank side. Nonetheless, micro-abrasion and a slight tensile fracture in the direction of metalchip flow. Ezugwa et al [28] and Kato [32] have exhibited simila r finding. However, the tensile fracture in this case is less in severity than what had been observed at dry cutting. This is due to the contribution of coolant in dropping the cutting temperature, which has reduced the plastic deformation at high temperature as a result. Hence, in comparison with the dry cutting at the same speed, tensile fracture was available with less severity and micro-abrasion/sliding. However, in dry cutting high levels of micro-abrasion, high levels of tensile fracture and sliding wear occurred.Figure 5-11 was taken at early stages of wear at a speed of 360m/min. It shows sliding wear, coating spalling and a crack starting to develop between TiN and TiCN coating at honed tool edge. Figure5-12A shows nice presentation of what had been described earlier regarding the development of small fragments on the tool edge. The adhered metal fragments work along with micro-abrasion wear to cause coating spalling.SEM image showing sliding wear.(a)SEM image showing micro-abrasion and tensile fracture.Figure 5-10 SEM images of (KC732) at 410m/min after failure (wet): (a) SEM image showing sliding wear, (b) SEM image showing micro-abrasionand tensile fracture.Figure 5-11 SEM image at early stage of wear of 360m/min (wet) showing coating and spalling developing crack between TiN and TiCN layers.The size of the metal chip adhered at the edge is almost 15g. Since it is unstable it will be later plucked away taking some fragments of coatings with it and the process continues. Another zoom in view with a magnification of 5000 times for the same insert is shown in Figure 5-12B indicating a newly developed crack between the coating layers.Figure 5-13A is taken of the same insert after failure when machining at 360m/min and wet condition. Coating spalling, and sliding wear can be seen and indicated by narrow grooves. In addition, initial development of notch wear can be seen at the maximum depth of cut.Further investigation is carried out by taking a zoom in view with a magnification of 2000 times as shown in Figure 5-13B. A clear micro-abrasion wear and micro-fatigue cracks were developed as shown, which extended deeply through out the entire three coating layers deep until the substrate. Therefore, in comparison with dry cutting, micro-fatigue crack, less tensile fracture, less micro-abrasion wear were activated at wet cutting. While micro- fatigue crack, high levels of micro-abrasion, and high levels of tensile fracture are distinguish the type of wear under dry condition at the same cutting spee d.Next, Figure 5-14A is taken for cutting tools machined at 310m/min. The results are similar to the previous inserts machined at 360m/min, where adhesion of metal fragments occurred at the tool edge, sliding wear and coating spalling. In addition, the black spot appeared at the top of the figure on the crater surface is a void resulting from imperfections in the coating process. At this condition, the crater surface will be worn faster than the flank surface.SEM image showing adhered metal fragments at tool edge.(a)SEM image showing developed crack between coating layers.Figure 5-12 SEM image of (KC732) at early wear 360m/min (wet): (a) SEM image showing adhered metal fragments at tool edge, (b) SEM image showingdeveloped crack between coating layers.(a)SEM image showing coating spalling and sliding wear after tool failure(b)SEM image showing micro-abrasion, and micro-fatigue cracks developedbetween coating layersFigure 5-13 SEM image of KC732 after failure machined at 360m/min(b)(wet): (a) SEM image showing coating spalling and sliding wear after toolfailure, (b) SEM image showing micro-abrasion, and micro-fatiguecracks developed between coating layers.翻译:在高速潮湿机械加工条件下后刀面表层磨损机理5.1 介绍几乎每类型用机器制造譬如转动, 碾碎, 钻井, 研..., 使用切口流体协助零件的有效的生产当设定标准由生产商[ 1 ] 需要。
机械专业毕业论文中英文翻译--在全接触条件下,盘式制动器摩擦激发瞬态热弹性不稳定的研究
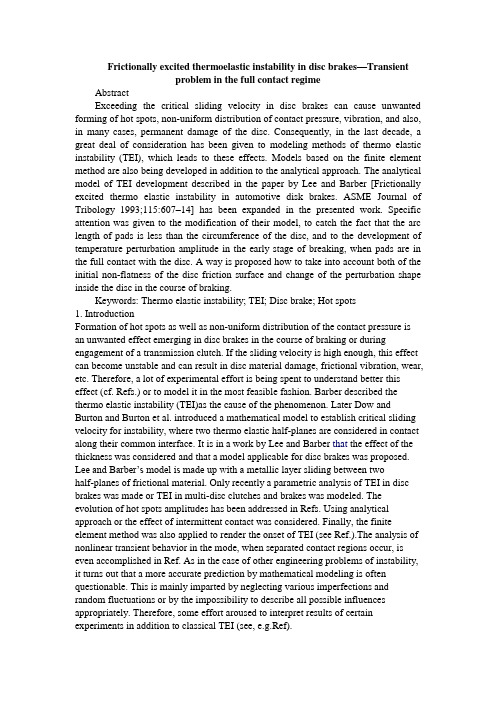
Frictionally excited thermoelastic instability in disc brakes—Transientproblem in the full contact regimeAbstractExceeding the critical sliding velocity in disc brakes can cause unwanted forming of hot spots, non-uniform distribution of contact pressure, vibration, and also, in many cases, permanent damage of the disc. Consequently, in the last decade, a great deal of consideration has been given to modeling methods of thermo elastic instability (TEI), which leads to these effects. Models based on the finite element method are also being developed in addition to the analytical approach. The analytical model of TEI development described in the paper by Lee and Barber [Frictionally excited thermo elastic instability in automotive disk brakes. ASME Journal of Tribology 1993;115:607–14] has been expanded in the presented work. Specific attention was given to the modification of their model, to catch the fact that the arc length of pads is less than the circumference of the disc, and to the development of temperature perturbation amplitude in the early stage of breaking, when pads are in the full contact with the disc. A way is proposed how to take into account both of the initial non-flatness of the disc friction surface and change of the perturbation shape inside the disc in the course of braking.Keywords: Thermo elastic instability; TEI; Disc brake; Hot spots1. IntroductionFormation of hot spots as well as non-uniform distribution of the contact pressure is an unwanted effect emerging in disc brakes in the course of braking or during engagement of a transmission clutch. If the sliding velocity is high enough, this effect can become unstable and can result in disc material damage, frictional vibration, wear, etc. Therefore, a lot of experimental effort is being spent to understand better this effect (cf. Refs.) or to model it in the most feasible fashion. Barber described the thermo elastic instability (TEI)as the cause of the phenomenon. Later Dow and Burton and Burton et al.introduced a mathematical model to establish critical sliding velocity for instability, where two thermo elastic half-planes are considered in contact along their common interface. It is in a work by Lee and Barber that the effect of the thickness was considered and that a model applicable for disc brakes was proposed. Lee and Barber’s model is made up with a metallic layer sliding between twohalf-planes of frictional material. Only recently a parametric analysis of TEI in disc brakes was made or TEI in multi-disc clutches and brakes was modeled. The evolution of hot spots amplitudes has been addressed in Refs. Using analytical approach or the effect of intermittent contact was considered. Finally, the finite element method was also applied to render the onset of TEI (see Ref.).The analysis of nonlinear transient behavior in the mode, when separated contact regions occur, is even accomplished in Ref. As in the case of other engineering problems of instability, it turns out that a more accurate prediction by mathematical modeling is often questionable. This is mainly imparted by neglecting various imperfections and random fluctuations or by the impossibility to describe all possible influences appropriately. Therefore, some effort aroused to interpret results of certain experiments in addition to classical TEI (see, e.g.Ref).This paper is related to the work by Lee and Barber [7].Using an analytical approach, it treats the inception of TEI and the development of hot spots during the full contact regime in the disc brakes. The model proposed in Section 2 enables to cover finite thickness of both friction pads and the ribbed portion of the disc. Section 3 is devoted to the problems of modeling of partial disc surface contact with the pads. Section 4 introduces the term of ‘‘thermal capacity of perturbation’’ emphasizing its association with the value of growth rate, or the sliding velocity magnitude. An analysis of the disc friction surfaces non-flatness and its influence on initial amplitude of perturbations is put forward in the Section 5. Finally, the Section 6 offers a model of temperature perturbation development initiated by the mentioned initial discnon-flatness in the course of braking. The model being in use here comes from a differential equation that covers the variation of the‘‘thermal capacity’’ during the full contact regime of the braking.2. Elaboration of Lee and Barber modelThe brake disc is represented by three layers. The middle one of thickness 2a3 stands for the ribbed portion of the disc with full sidewalls of thickness a2 connected to it. The pads are represented by layers of thickness a1, which are immovable and pressed to each other by a uniform pressure p. The brake disc slips in between these pads at a constant velocity V.We will investigate the conditions under which a spatially sinusoidal perturbation in the temperature and stress fields can grow exponentially with respect to the time in a similar manner to that adopted by Lee and Barber. It is evidenced in their work [7] that it is sufficient to handle only the antisymmetric problem. The perturbations that are symmetric with respect to the midplane of the disc can grow at a velocity well above the sliding velocity V thus being made uninteresting.Let us introduce a coordinate system (x1; y1)fixed to one of the pads (see Fig. 1) thepoints of contact surface between the pad and disc having y1 = 0. Furthermore, let acoordinate system (x2; y2)be fixed to the disc with y2=0 for the points of the midplane. We suppose the perturbation to have a relative velocity ci with respect to the layer i, and the coordinate system (x; y)to move together with the perturbated field. Then we can writeV = c1 -c2; c2 = c3; x = x1 -c1t = x2 -c2t,x2 = x3; y = y2 =y3 =y1 + a2 + a3.We will search the perturbation of the uniform temperature field in the formand the perturbation of the contact pressure in the formwhere t is the time, b denotes a growth rate, subscript I refers to a layer in the model, and j =-1½is the imaginary unit. The parameter m=m(n)=2pin/cir =2pi/L, where n is the number of hot spots on the circumference of the disc cir and L is wavelength of perturbations. The symbols T0m and p0m in the above formulae denote the amplitudes of initial non-uniformities (e.g. fluctuations). Both perturbations (2) and (3) will be searched as complex functions their real part describing the actual perturbation of temperature or pressure field.Obviously, if the growth rate b<0, the initial fluctuations are damped. On the other hand, instability develops ifB〉0.2.1. Temperature field perturbationHeat flux in the direction of the x-axis is zero when the ribbed portion of the disc is considered. Next, let us denote ki = Ki/Qicpi coefficient of the layer i temperature diffusion. Parameters Ki, Qi, cpi are, respectively, the thermal conductivity, density and specific heat of the material for i =1,2. They have been re-calculated to the entire volume of the layer (i = 3) when the ribbed portion of the disc is considered. The perturbation of the temperature field is the solution of the equationsWith and it will meet the following conditions:1,The layers 1 and 2 will have the same temperature at the contact surface2,The layers 2 and 3 will reach the same temperature and the same heat flux in the direction y,3,Antisymmetric condition at the midplaneThe perturbations will be zero at the external surface of a friction pad(If, instead, zero heat flux through external surface has been specified, we obtain practically identical numerical solution for current pads).If we write the temperature development in individual layers in a suitable formwe obtainwhereand2.2. Thermo elastic stresses and displacementsFor the sake of simplicity, let us consider the ribbed portion of the disc to be isotropic environment with corrected modulus of elasticity though, actually, the stiffness of this layer in the direction x differs from that in the direction y. Such simplification is, however, admissible as the yielding central layer 3 practically does not take effect on the disc flexural rigidity unlike full sidewalls (layer 2). Given a thermal field perturbation, we can express the stress state and displacements caused by this perturbation for any layer. The thermo elastic problem can be solved by superimposing a particular solution on the general isothermal solution. We look for the particular solution of a layer in form of a strain potential. The general isothermal solution is given by means of the harmonic potentials after Green and Zerna (see Ref.[18]) and contains four coefficients A, B, C, D for every layer. The relateddisplacement and stress field components are written out in the Appendix A.在全接触条件下,盘式制动器摩擦激发瞬态热弹性不稳定的研究摘要超过临界滑动盘式制动器速度可能会导致形成局部过热,不统一的接触压力,振动分布,而且,在多数情况下,会造成盘式制动闸永久性损坏。
中英文翻译---木工机械+家具机械词汇

Aaccessory equipment 附属设备adhesion test instrument for the wood coating 木材涂层附着力测定仪adz(e) 手斧,刮刀air brake 空气制动器,气闸air compressor 空气压缩机air conditioning unit 风向调节器air nailer 风动钉钉机air operated automatic control 气动自动控制air tacker气(风)动钉钉机air tool 风动工具automatic band saw sharpener 带锯自动锉锯机automatic circular saw sharpener 自动锉(圆)锯机automatic controlled machine 自控机床automatic copy shaper 自动仿型刨边机(单刀)automatic copy shaper(double heads)(with splash guard) 自动仿型刨边机(双轴)(附安全门)automatic feeder for veneer dryer 单板干燥机的自动填料机automatic hydraulic backnife wooden lathe 全自动液压背刀式木工车床automatic loader and unloader 自动装卸机automatic rotary table shaper 自动转台式成型机automatic sponge drum sander 自动鼓式海绵砂光机automatic strake belt sander 自动带式砂光机automatic stroke belt sander 自动(抚摸)砂光机automatic tapping and screwing machine 自动攻牙锁螺丝机automatic turning sander 全自动砂光机,自动圆棒砂光机automatic wide-belt sander 宽带砂光机BBack and arm impact test machine 椅背扶手冲击试验机balance cut-off saw 平衡截断锯Band and circular saw sharpener 带锯圆面积锯两用锉锯机Band resaw 再分带锯机Band saw 带锯Band saw clamp 带锯夹Band saw machine 带锯机Band saw machine with auto-feed carriage 带锯机附自动填料传送车Band saw machine with hand-feed carriage 带锯机附手扒送料车Band saw sharpener 带锯磨锯机Band saw shear 带锯剪(截)机Band saw slasher 多带横切锯Band saw stretcher 带锯滚压机Band saw welding clamp接锯机Band sawing 带锯制材Band scroll saw 细木工带锯,曲线带锯Barefaced tenon 裸面榫Bark-peeler 剥皮机Barking drum 鼓式剥皮机Barking machine 剥皮机Belt conveyor 带式传送器Belt drier 带式干燥机Belt drive 皮带传动Belt grinder 带式磨床Belt sander 带式砂光机Bentwood forming machinery曲木成型机Bevel saw 斜面锯Bifurcated rivet 开叉钉Bit 齿片,钻头Blade 锯条Block plane 短刨Blower通风机,鼓风机Blower kiln 鼓风式干燥窑Bobbin sander 轴式砂光机Body press (家具)装配压床Boring machine 钻床Bow saw 弓锯Brash chopper 枝梢切断机Breathing veneer drier 呼吸式单板干燥机Buffing machine 抛光机Business item 产品Butting saw 截锯,齐头锯CCabinet whole-plant equipment 橱柜整厂设备Carbide tool grinder 炭素钢刀具研磨机Carving machine 雕刻机Centerless sander 圆棒砂光机Centrifugal blower 离心通风机Chain-belt conveyer veneer drier 网带式单项式板干燥机Chain mortiser 插床Chain saw 链锯Chain saw machine 链锯机Chair aim static load test machine 椅扶手静荷试验机Chair back and arm impact test machine 椅背扶手冲击试验机Chair back static load test machine 座椅靠背静荷试验机Chair leg static load test machine椅腿静荷试验机Chair stability test machine座椅靠背耐久性试验机Chair whole-plant equipment 椅子整厂设备Chip board press 碎木板压合机Chip edger 双削齐边锯Chromometer 比色机Circular gang-saw 圆排锯Circular saw bench 简单圆面积锯机Circular saw bench for band feed ripping 手工送料纵切圆锯机Circular-saw sharpener 圆锯锉锯机Coating adhesion test instrument 漆膜附着力试验仪Coating impact instrument 漆膜冲击仪Coating surface impact instrument漆膜表面冲击仪Concave plane 凹底刨Concave saw 凹面(圆)锯Conveyor输送机Copier 复印机Corner locking machine 锁角机Cross cut band saw machine 横切带锯Cup type wheel stone机碗形砂轮Cup wheel杯形砂轮Curtain flow coater 淋幕式平面涂装机Custom 订做Customized solutions 订做胶水Cut-to –size saw 裁板锯Cutting block组合铣刀Cutting head 刀座,刀头Cutting jip 切削夹具Cylinder saw 桶形锯,圆桶锯Cylindircal saw 圆桶锯DDado head 组合刀头Debarder 剥皮机Deck planer大型电刨Decorative tip 装饰物Disc and spindle sander 盘式轴式联合砂光设备Disc planer 圆盘刨Disc sander 圆盘砂光机Door whole-plant equipment 门斗整厂设备Double band saw双边带锯Double belt sander 双边砂光机Double bevel cutter 双斜刨刀Double-edge cutting band saw 双边齿带锯Double-side planer双面刨木机double spindle shaper 双轴铣床Double surface oscillating curve sander 双面震动曲型杪光机Double surface planer双面刨Double surfacer 双(面)压刨Double-swage(set)saw 双压料锯Double thicknesser 双(面)压刨Dovetail machine 鸠尾榫机Dowel making machine暗榫(加工)机Drag saw sharpener狐尾机,锉锯机Drawer durability test machine 抽屉耐久性试验机Dresser 砂轮修整器,砂轮刀Drop test machine 跌落试验机Drum barker 滚筒剥皮机Drum sander 滚筒砂光机Drunken saw 摇摆(圆)锯Dust cleaner conveyor 粉尘清除输送机Dust collector 集尘器KKitchen block /kitchen rock 厨房地砖Kitchen cabinet 餐具柜Kitchen chair, stool and bench 厨房椅、圆凳及条椅Kitchen fitment 厨房固定家具Kitchen table 厨房餐桌Kitchen unit 厨房成套家具LLamp table 灯桌Lath grid 板条格Ledged door 直板门Link chair 写字板椅Living room furniture 起居室家具Locker 衣帽柜Lounge furniture 客厅家具Louvered door 百叶窗柜门Lowback executive chair 低背办公椅Lowback guest chair 低背来宾椅Lowback visitor chair 低背接待椅MManagerial mediumback chair 中背经理椅Margined flush door 镶边平板门Mattress 床垫,席梦思Mediumback executive chair 中背办公椅Metal furniture金属家具Mirror door 玻璃门Mirror for chest of drawers 多屉柜梳妆镜Multi-purpose sofa 多用沙发Multi-purpose table 多用桌NNest 茶几OOccasional table 休闲桌Office furniture 办公家具Office seating 办公座椅Office table 办公桌artition wall 隔断embroke table 折面桌lanters chair 园艺工用椅lastic furniture 塑料家具lay furniture 娱乐家具residential highback chair 高背办公椅ull-out table 伸缩餐具RRattan furniture 藤家具Recliner 躺椅Refectory table长餐桌Rocking chair 摇摆椅Rotary chair 转椅Rustic style furniture 乡村风格家具SSchool table 课桌Screen 屏风Seat痤椅Seating element 痤垫Secretarial chair 秘书椅3-section mirror 三面梳妆镜semi-CKD 半拆装家具serving table送餐桌shelving combination。
机床刀具设计机械类毕业设计外文文献翻译中英文翻译

英语原文:Design Of Tool Machine PropResearch significanceThe original knife machine control procedures are designed individually, not used tool management system, features a single comparison, the knife only has to find the tool knife, knife positioning the shortest path, axis tool change, but does not support large-scale tool.Automatic knife in the knife election, in the computer memory knife-election on the basis of using the Siemens 840 D features, and the election procedures knife more concise, and complete the space Daotao View. ATC use the knife rapid completion of STEP-7 programming, and have been tested in practice. In the positioning of the knife, PLC controlled modular design method, which future production of similar machines will be very beneficial, it is easy to use its other machine. Automatic tool change systems will be faster growth, reduced tool change time, increase the positioning accuracy tool is an important means to help NC technology development.Tool and inventory components of modern production is an important link in the management, especially for large workshop management. The traditional way of account management, and low efficiency, high error rate, and not sharing information and data, tools and the use of state can not track the life cycle, are unable to meet the current information management needs. With actual production, we have to establish a workshop tool for the three-dimensional tool storage system to meet the knife workshop with auxiliary storage and management needs.The system uses optimization technology, a large number of computer storage inventory information, timely, accurate, and comprehensive tool to reflect the inventory situation. The entire system uses a graphical interface, man-machine dialogue tips from the Chinese menu, select various functions can be realized and the importation of all kinds of information. Management system using online help function. Through the workshop management, network management and sharing of information. Have automated inventory management, warehousing management tool, a tool for the management and statistical functions.1.System components and control structureThe entire system, including the structure and electrical machinery control systems.1.1.1Mechanical structure and working principleTool from the stent, drive, drive system, Turret, shielding, control system, and electrical components. Support from the column, beam, the upper and lower guide Central track, and track support component.1) Drive for the system chosen VVVF method. Cone used brake motors, with VVVF by Cycloidreducer through sprocket drive.2) Drag a variable frequency drive system and control technology. VVVF adopted, will speed drive shaft in the normal range adjustment to control the speed rotary turret to 5 ~ 30mm in, the drive shaft into two, two under through sprocket, the two profiled rollers Chain driven rotating shelves. Expansion chain adopted by the thread tight regulation swelling, swelling the regular way. - Conditioned, under the same chain-of-conditioning, so that the chain of uniform.3) Turret and shields the entire total of 14 independent Turret. 13 of them as a socket-Turret, as a drawer-Turret, each Turret back through the pin and, under the conveyor chain link chain plate, installed at the bottom roller, chain driven rotating turret rotation along the track. Outlet-Turret and BT50-BT40 Turret Turret two kinds of forms. To strengthen management, security, landscaping modeling, shelf peripherals and shields. Turret-drawer drawer placed at six other Des V oeux a knife, can be categorized with some of knife auxiliary equipment, such as bits, such as turning tools.1.1.2.Electrical Control SystemThis tool storage systems is the main electrical control their shelves for operational control and position control. Operational control equipment, including operation of the start of braking control. Position Control is the main location and address of the shelves for testing. Control system as shown in Figure 1.图 1 Tool Control System for the1) Electric Transmission horizontal rotary tool storage systems are the mechanical movements are repeated short-term work system. And the run-time system needs some speed, speed transmission needs, the system will use VVVF method can be used simple structure, reliable operation of the motor and frequency inverter.2) Control of the system is divided into two kinds of manual control and automatic control, manual control as a general reserve and debugging methods of work; ways to the system control computer (IPC) and the control unit (inverter contactor , etc.) consisting of a control system.3) location and positioning accuracy of the system automatically identify the site and location using a detection device as proximity switches, relays through the plate-point isolation and the number plate recorded close to the switching signal acquisition and operation of Hutchison with a Optimal Path addressable identify the current location and shelves of the purpose of the shelf location. In order to enable a more accurate positioning system, adopted two photoelectric switches, to detect the two shelves of the two films.1.2.The functions of the knifeknife The is the role of reserves a certain number of tools, machine tool spindle in hand to achieve the fungibility a disc cutter knife is the type of library, the chain knives, and other means, in the form of the knife and capacity according to the Machine Tool to determine the scope of the process.mon typesThe knife is a tool storage devices, the common knife mainly in the following forms:(1) the turret knifeIncluding the first level turret vertical turret and the first two, see Figure 2.6 a) and b):(2) the disc cutterDisc knife in the library with discoid knife, cutting tool along See how vertical arrangement (including radial and axial from knife from knife), along See how radial array into acute or arranged in the form of the knife. Simple, compact, more applications, but are ring-cutter, low utilization of space. Figure 2.7 a) to c). If the knife storage capacity must be increased to increase the diameter of the knife, then the moment of inertia also increased correspondingly, the election campaign long knife. Tool number not more than 32 general. Cutter was multi-loop order of the space utilization knife, but inevitably given the knife from complex institutions,applicable to the restricted space Machine Tool storage capacity and more occasions. Two-disc structure is two smaller capacity knife on both sides of the sub-spindle place, more compactlayout, the number of certificates corresponding increase knife, apply to small and medium-sized processing center.(3) the chain knifeIncluding single-and multi-ring chain ring chain, chain link can take many forms change, see Figure 2.8 a) to c), thebasic structure shown inFigure 2. 8 doFeatures: knife apply tothe larger capacity of theoccasion, the space of thesmall number ofgenerally applicable tothe tool in the 30-120.Only increase the lengthof the chain tool will increase the number should not be increased circumferential speed of itsmoment of inertia of the knife does not increase the disc as large.(4) linear combination knife and the knife libraryThe linear knife simple structure in Figure 2.9, tool single order, the capacity of small knife, used for CNC lathe and drill press on. Because the location of fixed knife, ATC completed action by the spindle without manipulator. The cutter knife is generally the turret combination turret with a combination of the disc cutter knife and the chain combination. Every single knife the knife certificates of smaller, faster tool change. There are also some intensive drum wheel, and the lattice-type magazine for the knife, the knife-intensive though. Small footprint, but because of structural constraints, basically not used for single processing center, the concentration used for FMS for the knife system.1.4 Tool storage capacityTool storage capacity of the first to consider the needs of processing, from the use of point of view, generally 10 to 40 knives, knife will be the utilization of the high, and the structure iscompact.1.5 Tool options(1) choose to order processing tool according to the order, followed Add to the knife every knife in the Block. Each tool change, the order of rotation of a cutter knife on location, and remove the need knives, has been used by the cutter knife can be returned to the original Block, can also order Add Block, a knife. However, as the knife in the tool in different processes can not be repeated use of the knife must increase the capacity and lower utilization rate.(2) most of the arbitrary choice of the current system of using arbitrary NC election knives, divided into Daotao coding, coding and memory-cutter, three. Daotao coding tool code or knives or Daotao need to install the code used to identify, in accordance with the general principle of binary coding coding. Tool knife election coding method uses a special knife handle structure, and each of the coding tool. Each of the tool has its own code, thereby cutting tool can be in different processes repeatedly used, not to replace the tool back at the original knife, the knife capacity can be reduced accordingly. Memory-election this paper knife, in this way can knives and knife in the position corresponding to the Daotao memory of the PLC in the NC system, no matter which tool on the Inner knife, tool information is always there in mind, PLC . On the knife with position detection devices, will be the location of each Daotao. This tool can be removed and sent back to arbitrary. On the knife is also a mechanical origin, every election, the nearest knife selection.1.6.Control of the knife(1) the knife as a system to control the positioning axis. In the ladder diagram in accordance with the instructions for computing T code comparison of the output angle and speed of instructions to the knife the knife servo drive servo motor. Tool storage capacity, rotation speed, and / deceleration time, and other system parameters can be set in such a manner free from any outside influence positioning accurate and reliable but the cost is higher.(2) knife from the hydraulic motor drives, fast / slow the points, with proximity switches count and positioning. In comparison ladder diagram of the current storage system knife (knife spindle) and goals knife (pre-knife) and computing, then output rotation instructions, judging by the shortest path rotation in place. This approach requires sufficient hydraulic power and electromagnetic valve knife the rotational speed can be adjusted through the throttle. But over time may be oily hydraulic, oil temperature and environmental factors impact the change in velocity and accuracy. Not generally used in large and medium-sized machine tool change frequently.(3) the knife from AC asynchronous motor driven cam mechanism (Markov institutions), with proximity switches count, which means stable operation, and generally accurate and reliablepositioning cam used in conjunction with a mechanical hand, A TC fast-positioning.2. ATC, the main types, characteristics, and the scope of application 2.1 Auto Rotary ToolRotary Tool automatically onthe use of CNC machine tool is asimple installation of automatic toolchange, the Quartet and 47.60 TurretTool various forms, such as rotaryturret were installed on four, six ormore of the Tool , NC instructions byATC. Rotary Tool has two verticaland horizontal, relatively simplestructure, applicable to economicCNC lathe.Rotary Tool in the structure musthave good strength and stiffness,resistance to bear rough Cutting Toolin the cutting force and reduce therole of deformation and improveprocessing accuracy. Rotating Toolto choose reliable positioningprogramme structure and reasonable position, in order to ensure that each rotary turret to a higher position after repeated positioning accuracy (typically 0.001 to 0.005mm). Figure 2.1 shows the spiral movements of the Quartet Turret.Auto Rotary Tool in the simplest of ATC, is 180 º rotary ATC devices, as shown in Figure 2.2 ATC instructions received, the machine control system put ATC spindle control to the designated location at the same time, the tool movement to the appropriate location, ATC, with the rotary axis and at the same time, the knives matching tool; drawbars from Spindle Cutting Tools rip, ATC, will be the tool from their position removed; ATC, 180 º rotary tool spindle and the tool and tool away; A TC, the Rotary At the same time, the tool refocusing its position to accept Spindle removed from the cutting tool; Next, ATC, will be replaced with the cutter knives were unloaded into the spindle and tool: Finally, back to the original ATC, "standby" position. At this point, ATC completed procedures to continue to run. This ATC, the main advantage ofsimple structure, the less movement, fast tool change. The main disadvantage is that knives must be kept in parallel with the axis of the plane, and after the home side compared to the tool, chip and liquid-cutting knife into the folder, it is necessary to the tool plus protection. Cone knife folder on the chip will cause A TC error, or even damage knife folders, and the possibility of spindle. Some processing centre at the transfer, and the tool side. When the ATC command is called, the transfer-cutter knives will be removed, the machine go forward, and positioning with the ATC, in line with the position. 180 º "Rotary ATC devices can be used horizontal machine, can also be used for vertical machining centers.2. 2 ATC head-turret installedWith rotating CNC machine tool often used such ATC devices, with a few turret head spindle, each with a spindle on both knives, the first tower interim process can be automatic tool change-realization. The advantage is simple structure, tool change time is short, only about 2 s. However, due to spatial constraints, the number of spindle can not be too much, usually only apply to processes less, not to high precision machine tools, such as the NC drill, such as CNC milling machine. In recent years there has been a mechanical hand and the turret head with a knife for the automatic tool change ATC devices, as shown in Figure 2.3. It is in fact a turret head ATC, and the knife-ATC device combination. The principle is as follows:5 turret on the first two tool spindle 3 and 4, when using the tool spindle 4 processing tool, the manipulator 2 will be the next step to the need for the tool does not work on the tool spindle 3 until after the completion of this process , the first rotary turret 180 º, A TC completed. ATC most of their time and processing time coincidence, the only real tool change time turret transposition of the first time, this approach mainly used for ATC and NC NC drilling file bed. 2. 3.Daidao system for the automatic tool changeFigure 2.4 shows the knife and the whole machine tool CNC machine tools for the appearance of Fig.Figure 2.5 shows the knife and split-type machine to the appearance of CNC machine tool plans.At this point, knife storage capacity, a heavier tool can, and often additional transport unit to complete the knife between the spindle and cutting tool transport.Daidao the knife from the ATC, the election knives, automatic loading and unloading machine tool and tool exchange institutions (manipulator), composed of four parts, used widely.Tool Automatic Tool Change the manipulator system, the whole process more complicated ATC. We must first used in the processing of all installed in the standard tool on the knife handle in the machine outside the pre-size, according to a certain way Add to the knife. ATC, selected first in the knife knife, and then from ATC, from the knife from the knife or spindle, exchange, the new knife into the spindle, the old knife back into the knife.ATC, as the former two knives to accommodate a limited number can not be too many, can notmeet the needs of complex parts machining, CNC machine tool Automatic Tool Change Daidao the use of the automatic tool change devices. The knife has more capacity, both installed in the spindle box side or above. As for the automatic tool change Daidao device CNC machine tool spindle box only a spindle, spindle components to high stiffness to meet the machining requirements. The number of establishments in larger knife, which can meet the more complex parts of the machining processes, significantly improving productivity. Daidao system for the automatic tool change applied to drilling centres and CNC machining centers. The comparison drawn Daidao automatic tool change system is the most promising.3.PLC control of the knife random mode of election3. 1Common methods of automatic election knifeAutomatic control of the knife CNC refers to the system after the implementation of user instructions on the knife library automation process, including the process to find knives and automatic tool change [(63,71]. CNC Machining Center device (CNC) directive issued by the election knife , a knife, the tool required to take the knife position, said the election automatic knife. automatically elected knife There are two ways: random sequence election knives and knife election method.3.1.1 order election knifeTool Selection order is the process tool according to the sequence of the insert knife, the use of knives in order to take place, used knives back at the original knife, can also order Add Block, a knife. In this way, no need Tool identification devices, and drive control is a relatively simple, reliable and can be used directly from the points of the knife machinery to achieve. But the knives in each of the tool in different processes can not be reused, if the tool is installed in accordance with the order of the knife, there will be serious consequences. The need to increase the number of knives and knife the capacity of the tool and reduce the utilization of the knife.3.1.2Random election knifeRandom election under the knife is arbitrary instructions to select the required tools, then there must be tool identification devices. Tool knife in the library do not have the processing in accordance with the order of the workpiece can be arbitrary storage. Each of the tool (or knifeblocks) are for a code, automatic tool change, the rotary cutter, every tool have been the "tool identification device" acceptable identification. When CNC tool code and the code in line with directives of the tool selected, the rotary cutter knives will be sent to the ATC position, waiting to grab manipulator. Random knife election is the advantage of the cutter knife in the order has nothing to do with the processing sequence, the same tool can be used repeatedly. Therefore, the relatively small number of knives, knife the corresponding smaller. Random elections knife on the tool must be coded to identify. There are three main coding.1. Tool coding. Adopt special knife handle structure coding, the drawbars on the knife handle back-end packages such as spacing of the coding part of the lock-nut fixed. Coding diameter ring diameter of a size two, respectively, said that binary "1" and "0" to the two rings are different, can be a series of code. For example, there are six small diameter of the ring can be made to distinguish between 63 (26-1 = 63) of the coding tool. All of 0 normally not allowed to use the code, to avoid the cutter knife Block did not confuse the situation.2. Knife Block coding. On the knife Block coding, coding tool, and tool into line with the number of knives in the Block. ATC knife when the rotation, so that each knife seats followed through knowledge knife, knife found blocks, knives stopped the rotation. At this time there is no knife handle encoding part of the knife handle simplified.3. Annex coding methods. This style of coding keys, coded cards, coding and coding-disc, which is the most widely used coding keys.First to knives are attached to a tool of the show wrapped coding keys, and when the cutter knife to the store at knife in, so put the number of keys to remember knife Block Road, will be inserted into key to the coding Block next to the key hole in the seat for the knife to the numbers.ConclusionFocused on in today's manufacturing environment tool storage and management of new models and methods, practical application of good results in systems integration and optimization, and other aspects of operations will be further explored, so that it has a higher theoretical and practical level.译文:机床刀具设计课题研究意义机床原来的刀库控制程序是单独设计的,没有采用刀具管理系统,功能也比较单一,只实现了刀库刀具的找刀、刀库最短路径定位、主轴换刀,而且不支持大型刀具。
中英文文献翻译-减速器和差速器的调整与装配
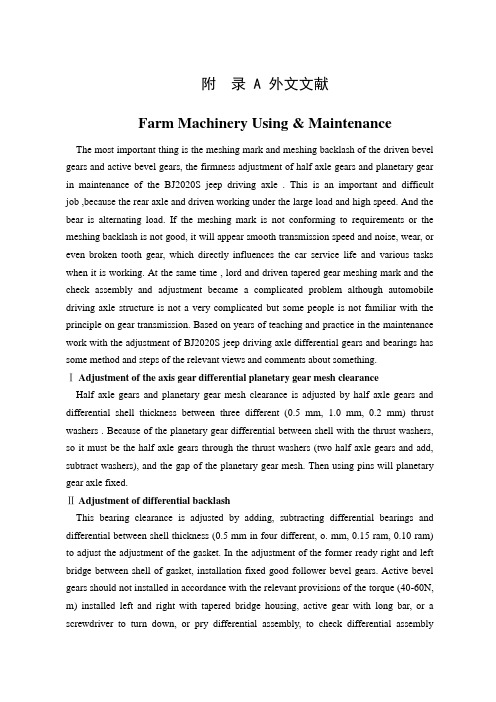
附录 A 外文文献Farm Machinery Using & MaintenanceThe most important thing is the meshing mark and meshing backlash of the driven bevel gears and active bevel gears, the firmness adjustment of half axle gears and planetary gear in maintenance of the BJ2020S jeep driving axle . This is an important and difficult job ,because the rear axle and driven working under the large load and high speed. And the bear is alternating load. If the meshing mark is not conforming to requirements or the meshing backlash is not good, it will appear smooth transmission speed and noise, wear, or even broken tooth gear, which directly influences the car service life and various tasks when it is working. At the same time , lord and driven tapered gear meshing mark and the check assembly and adjustment became a complicated problem although automobile driving axle structure is not a very complicated but some people is not familiar with the principle on gear transmission. Based on years of teaching and practice in the maintenance work with the adjustment of BJ2020S jeep driving axle differential gears and bearings has some method and steps of the relevant views and comments about something.ⅠAdjustment of the axis gear differential planetary gear mesh clearanceHalf axle gears and planetary gear mesh clearance is adjusted by half axle gears and differential shell thickness between three different (0.5 mm, 1.0 mm, 0.2 mm) thrust washers . Because of the planetary gear differential between shell with the thrust washers, so it must be the half axle gears through the thrust washers (two half axle gears and add, subtract washers), and the gap of the planetary gear mesh. Then using pins will planetary gear axle fixed.ⅡAdjustment of differential backlashThis bearing clearance is adjusted by adding, subtracting differential bearings and differential between shell thickness (0.5 mm in four different, o. mm, 0.15 ram, 0.10 ram) to adjust the adjustment of the gasket. In the adjustment of the former ready right and left bridge between shell of gasket, installation fixed good follower bevel gears. Active bevel gears should not installed in accordance with the relevant provisions of the torque (40-60N, m) installed left and right with tapered bridge housing, active gear with long bar, or a screwdriver to turn down, or pry differential assembly, to check differential assemblybearings between differential to feel no axial clearance and rotate freely.ⅢActive bevel gears bearing clearance adjustmentIn active position of bevel gears can be determined by the basic, increase and decrease active bevel gears with active before bearings taper gear bearing thrust ring between four different thickness (0.10 mm, 0.15 ram, 0.25 mm mm) adjustment, 0.50 gasket to adjust, the flexible rotation, no axial and radial clearance.ⅣActive bevel gears and driven bevel gears clearance and meshing mark adjustment Domestic automobile gear for no modifier, assembling widely adopted, the first meshing mark check whether the meshing mark requirements, such as requirements, through the change of bevel gears, driven axial position to get to meet the requirements of meshing mark, the active bevel gears bearing and differential bearing clearance (pre-tightening degrees) basis, rub-up, driven bevel gears, initiative on 3-4 taper gear teeth are coated with thin layer opposite, oil (or face turns into oil), according to the requirements and differential assembly installed left, right, forward and backward bridge housing, then turn active bevel gears decomposition of left and right to bridge housing, driven gear tooth surface of conical whether imprint requirements. If meshing mark requirements, visible to the situation by outward, to the right or left, bevel gears, driven to adjust. When the meshing mark to tooth root cap, the main, small or client, the formula for the Lord: "the Lord, from (i.e., big into bevel gears into active driven gear), small (i.e. driven out from bevel gears removed from active gear)." When the Lord, driven gear cone of meshing mark complies with the standards and inspection, driven bevel gears, active bevel gears and clearance of bevel gears driven backlash should actively bevel gears in the radius of 45mm flanges on the circumference displacement measurement, the arc length) should be in (0.2-0.6 mm. If does not accord with a standard, can increase and decrease active bevel gears and bearings taper gear after the shim between left and right or mobile differential bearing adjustment gasket, driven to adjust the gap, so bevel gears, driven when the bevel gears has adjusted, adjust the marks are not destroyed, small volume, driven tapered gear meshing mark.ⅤDrive and differential assemblyWe can start assemble the drive and differential when the differential gears, driven gear, each bearing, tapered meshing mark adjustment is over. Based on the thickness of the gasket and the bolt torques, we should coated with rubber seal, assembled active bevelgears, mount differential assembly, then closed the bridge housing.附录 B 中文译文减速器和差速器的调整与装配在对BJ2020S吉普车后桥的维修中,最主要的就是减速器主、从动圆锥齿轮的啮合印痕及啮合间隙;差速器半轴齿轮、行星齿轮啮合间隙和各轴承松紧度的调整。
- 1、下载文档前请自行甄别文档内容的完整性,平台不提供额外的编辑、内容补充、找答案等附加服务。
- 2、"仅部分预览"的文档,不可在线预览部分如存在完整性等问题,可反馈申请退款(可完整预览的文档不适用该条件!)。
- 3、如文档侵犯您的权益,请联系客服反馈,我们会尽快为您处理(人工客服工作时间:9:00-18:30)。
附录1粘接减振片式多头热压机是以系列化、标准化的通用部件为基础,配以少量的专用部件组成的专用机床,因此,机床的制造和调整都很方便。
近期,东营信义集团又引进了几台先进的液压机,这些液压机都综合应用了信息技术、感应传感技术、计算机自动控制技术、机械技术等先进技术,其效率、功能、自动化程度都相对现有机床有很大的提高。
这让我们看到了我国机床使用及制造的发展方向,也看到了机床未来的发展趋势。
本文设计的粘接减振片多头式热压机的主结构是两压头式热压机,其设计的根据是信义集团盘片车间福特生产线的粘接减振片单头热压机。
改进的多头式热压机的加工特点是:1)采用两个压头,在一次压制过程中可以一次加工两个刹车片,先在加工数量上提高一倍;2)工作台上安装滑台循环加工,滑台上安装工装,可以根据刹车片的型号灵活更换,工作台上放有11 个滑台,加工时滑台在PLC 程序控制下依次有顺序的循环加工,所以在工作台上可以同时放11 对刹车片然后连续加工,而且只要一个操作员在出料口等待将工件拿出同时将未加工工件放入工装上就可以完成此工序的加工,省去操作员的等待时间,此种工作台可以提高生产效率数倍甚至数十倍,也可以大幅度的减少劳动人员的劳动强度。
多头式热压机的结构特点:1)两个压头采用立式液压缸提供压力,而且两个液压缸的型号是相同的,因此缩短了设计周期和设计过程;2)两个压头液压缸的进出液压油采用同一个供油系统,而且两液压缸的进出油口分别相连,即在进油口有相同压力,相同流量的压力油,在出油口也一样,实现了两个压头的压制压力相等,解决了由于工装形状公差造成的刹车片在粘接减振片时表面压力不等的问题,是减震片的拉拔力符合工艺要求;3)滑台的动力源也采用液压缸,在工作台的四边分别安装有四个液压缸,它们的供油系统只要加几个控制阀也可以与压头液压缸的供油系统相连,即整个粘接减振片热压机采用一个供油系统,节省了动力能源,也简化了机床的结构;4)粘接减振片的工作过程,无论是主运动,进给运动还是辅助运动都采用一个PLC 程序控制,使控制准确,有序;5)根据两压头原理,可以重新设计液压缸支架,增加压头,由于大部分都是标准件,所以设计和制造比较简单;6)由于主结构比较简单,所以可以在机床上增加两个机械手代替人工操作,一个负责将工件放入工装,一个负责将工件取出,实现机床的自动化和自动生产线。
因此,改进后的粘接减振片多头式热压机不仅提高工作效率,而且可以大幅度的降低工人的劳动强度,可以实现产品的自动生产线和提高机床的自动化程度。
这种机床适合大批量产品的生产,而且造价比较低,改造比较灵活,适合现代工业发展的要求。
液压系统的正确维护1)选择适合的液压油液压油在液压油系统中起着传递压力、润滑、冷却、密封的作用,液压油选择不恰当是液压系统早期故障和耐久性下降的主要原因。
应按随机使用说明书中规定的牌号选择液压油,特殊情况需要使用代用油时,应力求其性能与原牌号性能相同。
不同牌号的液压油不能混合使用,以防液压油产生化学反应、性能发生变化。
深褐色、乳白色、有异味的液压油是变质油,不能使用。
2)防止固体杂质混入液压系统清洁的液压油是液压系统的生命。
液压系统中有许多精密零件,有的设阻尼小孔或缝隙等。
若固体杂质入侵将造成精密零件拉伤,发卡、油道堵塞等,危害液压系统的安全运行。
一般固体物质入侵途径有:液压油不清洁;加油工具不清洁;加油和维修、保养不慎;液压元件脱屑等。
可以从以下几个方面防止固体杂质入侵系统:加油时液压油必须过滤,加油工具应可靠清洁。
不能为了提高加油速度而去掉液压油箱加油口处的过滤器。
加油人员应使用干净的手套和工作服。
保养时拆卸液压油箱加油盖、滤清器盖、检测孔、液压油管等部位,液压系统油道暴露时要避开扬尘,拆卸部位要先彻底清洁后才能打开。
如拆卸液压油箱加油盖时,先除去油箱盖四周的灰尘,拧松油箱盖后清除残留在接合部位的杂物(不能用水冲洗以免水渗入油箱),确认清洁后才能打开油箱盖。
如需使用擦试材料和铁锤时,应选择不掉纤维杂质的擦拭材料和击打面附着橡胶的专用铁锤。
液压元件、液压胶管要认真清洗,用高压风吹干后组装。
选用包装完好的正品滤芯(若包装损坏,虽然滤芯完好,也可能不洁)。
换油同时清洗滤清器,安装滤芯前应用擦试材料认真清除滤清器壳内部污物。
液压系统的清洗油必须使用与系统所用牌号相同的液压油,油温在45—80℃之间,用大流量尽可能将系统中杂质带走。
液压系统要反复清洗3次以上,每次清冼完后趁油热时将其全部放出系统。
清冼完毕再清洗滤清器,更换新滤芯后加注新油。
3)防止空气和水入侵液压系统防止空气入侵液压系统在常压常温下液压油中含有容积比为6%~8%的空气,压力降低时空气会从油中游离出来,气泡破裂使液压元件“气蚀”,产生噪声。
大量的空气进入油液中将使“气蚀”现象加剧,液压油压缩性增大,工作不稳定,降低工作效率,执行元件出现“爬行”等不良后果。
另外,空气还会使液压油氧化,加速其变质。
防止空气入侵应注意以下几点:维修和换油后要按随机使用说明书规定排除系统中的空气;液压油泵的吸油管口不得露出油面,吸油管路必须密封良好;油泵驱动轴的密封应良好,更换该处油封时应使用“双唇”正品油封,不能用“单唇”油封代替,因为“单唇”油封只能单向封油,不具备封气的功能。
4)定期保养注意事项防止水入侵液压系统,液压油中含有过量水分会使液压元件锈蚀,油液乳化变质,润滑油膜强度降低,加速机械磨损。
除了维修保养时要防止水分入侵外,还要注意储油桶不用时要拧紧盖子,最好倒置放置;含水量大的液压油要经多次过滤,每过滤一次要更换一次烘干的滤纸。
在没有专用仪器检测时,可将液压油滴到烧热的铁板上,没有蒸汽冒出并立即燃烧方能加注。
目前有的机床液压系统设置了智能装置,该装置对液压系统某些隐患有警示功能,但其监测范围和准确程度有一定的局限性,所以液压系统的检查保养应将智能装置监测结果与定期检查保养相结合。
液压系统的保养1)250h检查保养检查滤清器滤网上的附着物,如金属粉末过多,往往标志着油泵磨损或油缸拉缸。
对此,必须确诊并采取相应措施后才能开机。
如发现滤网损坏、污垢积聚,要及时更换,必要时同时更换液压油。
2)500h检查保养机床机械运行500h后,不管滤芯状况如何均应更换,因为凭肉眼难以察觉滤芯的细小损坏情况,如果长时间高温作业还应适当提前更换滤芯。
3)1000h检查保养此时应清洗滤清器、清洗液压系统要换滤芯和液压油,长期高温作业换油时间要适当提前。
如能通过油质检测分析来指导换油是最经济的,但要注意延长使用的液压油,每隔100h应检测一次,以便及时发现并更换变质的液压油。
4)7000h和10000h检查维护根据实践,进口液压泵、液压马达工作10000h必须大修,否则液压泵、液压马达因失修可能损坏,对液压系统是致命性的破坏。
随着液压系统在工业生产中的广泛使用,液压系统的正确使用、维护和保养成为机床使用、维护和保养不可缺少的一部分。
在机床的使用过程中,只有正确使用与维护每一个系统,才能降低机床故障率,延长使用寿命,提高工作效率。
附录2The long hot press bonding damping type is generic components to serialization, standardization as the foundation, special machine tools, components with a small number of dedicated components. Therefore, manufacture and adjustment of machine tool is very convenient. Recently, Dongying Xinyi Group and the introduction of several sets of advanced hydraulic machine, the hydraulic machine is the comprehensive application of the information technology, the induction sensor technology, computer automatic control technology, mechanical technology and other advanced technology, its efficiency, function, the degree of automation compared with the existing machine tools have greatly improved. This allows us to see the development direction of China's machine tool use and manufacturing, also see the future development trend of machine tool. The main structural bonding damping piece the long hot press is two head hot press, its design is based on the Ford disc workshop production line Xinyi Group bonding damping sheet single head hot press. The processing characteristics of improved bull type hot press is:1) The two head, can be a processing two brake pads in a pressing process, first in the processing quantity is doubled;2) Table recycling processing is arranged on the working table, the slipway mounting fixture, can replace flexibly according to the brake model, bench with 11 slide, processing slide under the control of a PLC program are circulating processing sequence, so also placed 11 on the brakes and continuous processing can be on the bench., and as long as an operator in the outlet for the workpiece processing at the same time will not take the workpiece into the fixture can complete this process, waiting time save operator, the work table can improve production efficiency several times even dozens of times, but also can greatly reduce the labor intensity of workers.Structural characteristics of multi type hot press:1) Two head adopts a vertical hydraulic cylinder with pressure, and the two cylinder model is the same, thus shorten the design cycle and design process;2) Two head hydraulic cylinder and hydraulic oil with a fuel supply system, and the two hydraulic cylinders are respectively connected with the oil inlet and outlet, which has the same pressure at the inlet, the oil pressure of the same flow, as well as in the oil outlet, the two pressure head pressure is equal, solution will the tooling shape tolerance caused by brake pads in the bonding damping sheet surface pressure range problem, is the damping sheet drawing force comply with process requirements;3) Table power source is also adopts hydraulic cylinder, in the work of the four sides are provided with four hydraulic cylinders, fuel supply system they just add a few control valve can also be connected with the oil supply system head of hydraulic cylinder, the adhesive damping plate hot press with a fuel supply system, saving energy, but also simplify the structure of machine tool;4) The working process of bonding damping sheet, regardless of is the main movement, movement or auxiliary motion using a PLC program control, the control is accurate, orderly;5) According to the principle of two head, can be re design of hydraulic cylinder support, increasing the pressure head, because most of them are standard parts, so the design and manufacture of relatively simple;6) The main structure is relatively simple, so can increase instead of manual operation two manipulators in machine tools, a charge will be put into the fixture workpiece, a workpiece will be responsible for take out, realize automation of machine tools and automatic production line.Therefore, the bonding damping sheet is improved after the long hot press not only improve work efficiency, and can greatly reduce the labor intensity of the workers, the automatic production line can realize products and improve the degree of automation of machine tool. This machine is suitable for mass production, and relatively low cost, improvement is more flexible, suitable for the requirements of the development of modern industry.Proper maintenance of the hydraulic system1) select a suitable hydraulic oilHydraulic oil pressure plays a pass, lubrication, cooling, sealing the role of hydraulic system in oil, hydraulic oil is not appropriate to select the hydraulic system failure and the durability of the early decline. According to the provisionsof the random instructions of the brand choice of hydraulic oil, special circumstances to use for fuel, should strive for the same performance with the original brand performance. Different grade mix of hydraulic oil, hydraulic oil to prevent chemical reaction, change in performance. Dark brown, white, and the hydraulic oil is the smell of oil deterioration, can not be used.2) to prevent the solid impurities mixed with the hydraulic systemCleanliness of hydraulic oil in hydraulic system of life. There are a lot of precision parts in the hydraulic system, some with damping holes or gaps. If the solid impurity invasion will cause a hairpin, precision parts, oil passage blockage, threat to the safe operation of hydraulic system. General solid substance invasion pathways: hydraulic oil is not clean; gas tool is not clean; refueling and repair, maintenance accidentally; scaling and other hydraulic components. Can from the following several aspects to prevent the solid impurity invasion system: on the hydraulic oil must be filtered, gas tools should be reliable clean. Cannot remove the hydraulic gas tank outlet filter in order to improve the gas speed and. Service personnel should use clean gloves and work clothes.Maintenance to remove the hydraulic tank filler cap, filter cover, a detection hole, hydraulic parts, hydraulic system to avoid oil exposure dust, removing parts must first thoroughly cleaned before opening. Such as removing hydraulic gas tank cover, remove the dust around fuel tank cover, unscrew the oil tank cover to remove residual in the engagement portion of the debris (not wash with water to prevent water infiltration tank), confirmed after cleaning to open the fuel tank cap. If you want to use as material and the hammer, hammer should choose not to drop for wiping material and the impact surface fiber impurity attached rubber. Hydraulic components, hydraulic hose to wash, with high pressure air drying after assembly. Selection of good authentic filter packing (if damaged packaging, although the filter intact, may also not clean). Change oil and filter cleaning, filter application installed before wiping material carefully remove the dirt inside the filter shell.Clean the oil hydraulic system must use the same brand of hydraulic oil and the system, the oil temperature is between 45 ℃- 80 ℃, with large flow as far as possible away impurities in. Hydraulic system to be cleaned repeatedly 3 times, each time the Qing Xian wanhou while the oil heat when it all off system. QingXian after filter cleaning, replacement after adding new oil filter.3) to prevent the air and water intrusion in hydraulic systemTo prevent the air intrusion hydraulic system contains a volume ratio of 6% to 8% of the air in the hydraulic oil pressure at room temperature, pressure drop of air will free from oil, bubble rupture of the hydraulic components "cavitation", produce noise. Large quantities of air into the oil will make "cavitation" phenomenon aggravate, compressibility of hydraulic oil increases, unstable work, reduce the efficiency of work, executing element "crawl" and other adverse consequences. In addition, the air will make the hydraulic oil oxidation, accelerate the deterioration. To prevent the air intrusion should note the following points: repair and change according to the provisions of the use of random instructions to exclude air in the system; the suction nozzle hydraulic pump shall not be exposed out of the oil, oil pipeline must be sealed well; pump drive shaft seal should be good, the replacement of the seal should be the use of "lips" authentic seal, do not use the "single lip seal" instead of "single lip seal, because" only one-way sealing oil, does not have the function of sealing gas.4) regular maintenance attentionTo prevent water intrusion in hydraulic system, the hydraulic oil which contains excess water will cause corrosion of hydraulic element, oil emulsion modification, reduces the lubricating oil film strength, accelerate the mechanical wear. In addition to repair and maintenance to prevent moisture intrusion, but also pay attention to the oil tank is not to tighten the lid, the best place to inverted; after filtration with hydraulic oil content of each filter, a minor change a drying filter paper. In the absence of special equipment inspection, the hydraulic oil to the hot iron, no steam and immediately combustion can filler.At present, some machine tool hydraulic system set up a smart device, the device has functions of some hidden trouble of hydraulic system, but its monitoring range and accuracy have certain limitations, so hydraulic system inspection and maintenance should be monitoring results and regular maintenance of intelligent device combination.Hydraulic system maintenance1) 250h inspection and maintenanceCheck the filter screen on the attachments, such as metal powder too much,often marks the pump wear or cylinder scoring. In this regard, must be diagnosed and take corresponding measures in order to boot. Such as the discovery of screen damage, dirt accumulation, must be promptly replaced, if necessary, replace the hydraulic oil.2) 500h inspection and maintenanceMachine running 500h, no matter how the filter should be replaced, because by tiny invisible element damage, if the long time high temperature operation should be appropriately ahead of time to replace the filter.3) 1000h inspection and maintenanceThis should filter cleaning, cleaning of hydraulic system to filter and hydraulic oil, long time to replace the oil temperature homework in advance. Such as oil quality through analysis to guide the oil is the most economic, but attention should be paid to extend the use of hydraulic oil, should be inspected once every 100h, in order to detect and replacement of hydraulic oil metamorphism.4) 7000h 10000h inspection and maintenanceAccording to the practice, imported hydraulic pump, hydraulic motor 10000h must overhaul, or hydraulic motor hydraulic pump, due to disrepair may be damaged, the hydraulic system is a deadly destruction. With the wide use of the hydraulic system in industrial production, proper use of hydraulic system, and maintenance of machine tool use, maintenance and maintenance has become an indispensable part of. In the use process of machine tools, only the correct use and maintenance of each system, can reduce the machine failure rate, prolong the service life, improve work efficiency.。