Cumberland_Models_37B_50B_HD_Series_Manual
HD and ED Series Hysteresis Dynamometers (中低速测功机说明书)

While every precaution has been exercised in the compilation of this document to ensure the accuracy of its contents, Magtrol, Inc./Magtrol SA assumes no responsibility for errors or omissions. Additionally, no liability is assumed for any damages that may result from the use of the information contained within this publication. Copyright Copyright ©2002-2014 Magtrol, Inc. All rights reserved. Copying or reproduction of all or any part of the contents of this manual without the express permission of Magtrol is strictly prohibited. Trademarks LabVIEW™ is a trademark of National Instruments Corporation. Microsoft® is a registered trademark of Microsoft Corporation. National Instruments™ is a trademark of National Instruments Corporation. Windows® is a registered trademark of Microsoft Corporation.
MTA 7.3 反汗式能量节约设备 MT-374B 安装指南说明书

Parker Hannifin CanadaMicro Thermo Technologies TM12855 Brault Street Mirabel, QC J7J 0C4 Office phone 450-668-3033MTA installationand operationAnti-sweat Energy Saver Installation guideIntroduction.The Anti-sweat Energy Saver model MT-374B is an MT-Alliance compatible controller that modulates the power delivered to a maximum of 4 anti-sweat heaters channels according to the dew point in the supermarket where the controller is installed. Temperature and humidity measurement are used tocalculate how much heating it is required to avoid condensing on glass doors. The processor board work without local user interface when networked with an MT-Alliance computer but it can work as standalone with the Local User Interface MT-364B ordered separately.Make all wiring connection accordingly to the diagram connection above or on a drawing provided from Parker Hannifin Engineering advisor. Use a Micro Thermo Temperature and Humidity combo sensor p/n 023-0026. A connection to earth ground must be made for proper 24VAC power filtering, and provide EMC and ESD protection for the FTT-10A transceiver.2 MT-Alliance Installation:The MT-374B can be installed on MTA 7.2.3 or later but it is possible to install it on version 6.0 or later on certain conditions. Before installation in version 6.0 you must install the patch for MT-374B. If you are replacing a 3744 with a 374B on MTA before 7.2.3 you will need to install the patch before executing the replacement.From the moment the node is dropped and installed on a view, Dew Point Alarm is monitored by MTA, the optional Local User Interface will display measurements but controls will be locked.See also the Anti-sweat standalone User Manual PUID 75-PHW-1012 for standalone installation and configuration with the Local User Interface.3Alliance Configurations Step by step procedureIn MT Alliance 7.3 you should create a view with the Configure - Views menuSelect the Refrigeration subsystem then click Add, then Change Image, then select Anti-Sweat.bmp Then change the View identification for Anti-SweatExample with Anti-Sweat.bmpIf you have 2 Anti-Sweat controller you can use Anti-Sweat Dual.bmpIf for any reason you may want blank point location you may change images for“Anti-Sweat no nv.bmp”or “Anti-Sweat Dual no nv.bmp”Dropping the Node and Custom PointsDrop a Custom Node on the Anti-Sweat view:Node type: - CustomManufacturer: - Micro ThermoModel: - Gen Anti-sweat V7.0Click Details tab of the node and enter Identification: AS3Click Commands/Status and install it to get the node ready for configuration. Drop a custom point for Bypass Command:Point Type: - CommandPhysical Type: - SwitchIdentification: Leave defaultClick On the hardware tab of the point:Custom node identification: AS3Network Variable Input Name: nviBypassModeOff/On Description: Normal - BypassButton color – Off: Grey Off Glyph:Button color – On: Green On Glyph:Drop a custom point for Output Status:Point Type: - MeasurePhysical Type: - SwitchIdentification: Leave defaultClick On the hardware tab of the point:Custom node identification: AS3Network Variable Input Name: nviBypassModeOff/On Description: Normal - BypassButton color – Off: Grey Off Glyph:Button color – On: Green On Glyph:Place the pointso nv info gethiddenDrop a custom point for Store Temperature:∙Point Type: - Mesure∙Physical Type: - TemperatureClick On the hardware tab of the point:∙Custom node identification: AS3∙Network Variable Output Name: nvoTemperatureDrop a custom point for Store Humidity:∙Point Type: - Measure∙Physical Type: - HumidityOn the hardware tab:∙Custom node identification: AS3∙Network Variable Output Name: nvoHumidityDrop a custom point for calculated Dew Point:∙Point Type: - Mesure∙Physical Type: - TemperatureClick On the hardware tab of the point:∙Custom node identification: AS3∙Network Variable Output Name: nvoDewPtDrop a custom point for calculated Savings:∙Point Type: - Measure∙Physical Type: - PercentClick On the hardware tab of the point:∙Custom node identification: AS3∙Network Variable Output Name: nvoSMSavingDrop a custom point for Output Power:∙Point Type: - Measure∙Physical Type: - PercentClick On the hardware tab of the point:∙Custom node identification: AS3∙Network Variable Output Name: nvoSMStatusTo use remote sensors you need to make these network connections from the Network menu:nvoRH A\C-X -----------------------> Anti-sweat (AS3) . nviHumiditynvoTemp A\C-X ----------------------> Anti-sweat (AS3) . nviTemperatureIf an nvi sensor is not bound the respective local sensor will be used automatically.If for any reason you may want blank point location you may change images for “Anti-Sweat no nv.bmp” or “Anti-Sweat Dual no nv.bmp”4 Alarm ManagementFrom the moment the Anti-sweat Energy Saving node is dropped and installed on a view, Dew Point Alarm is monitored by MT Alliance and eventually appears on the Alarm panel.To change Dew Point alarm High Limit and Set Time you need to open the Anti_Sweat_Ctrl LonMark Objects in the Node Information window.Dew Point alarm High Limit is defined with UCPTDewPtAlarmSt1 with 0 2:0:0:0 as default value for 0 days, 2 hours, 0 minutes and 0 second.Dew Point Set Time is defined with UCPTDewPtHighLim1 with 25°C as default value.To change any of the CP, double click on it and change the appropriate value. Take special care to change Set Time as the structure is not explicitly shown:Temperature and dew point values are available in Celsius onlyClick OK then Yes to Accept Changes and to program CPs when promptedDays Sec/10 Hours Secs MinsIt is also possible to monitor nvoSMSaving through an alarm config of a sensor of a Sensor Node.By example if you want an alarm in case of there is no saving for more than 24 continuous hours Set Low Limit to 1% and set time to 24h.5 Transfer Function Parameter Setting.The transfer function of the control is based on two points (StPtMin, StPtMax) each oneidentified by two coordinates on a DEW/PWR graphic: StPtMin (DpMin, PwMin) and StPtMax (DpMax, PwMax) used to modulate the output power according to the dew point.6OperationUnless bypass is ON, at power up the UCPTSmOnDelay will prevent heating for 60 sec. When running it will pulse each heater channel sequentially with a duty cycle according to the % power.If dew point is higher than Dew Point High Limit (UCPTDewPtHighLim1) for longer than Dew Point Set Time (UCPTDewPtAlarmSt1) the output power will be forced to Full Power, Dew Point Alarm will appear on the Alarm Panel and the board normally open dry contact will remain close as long as the alarm status is ON. If thereafter the dew point becomes lower than the limit, the Alarm Status will remain but the output power for heating will not be forced to full any more. This alarm function can be used to detect persistent moisture problem.It is also possible to perform a manual bypass to force the Anti-sweat Energy Saver to run at Full Power until the bypass is released. Manual Bypass can be performed locally on the board or by the command point on the Anti-Sweat view either in Overview mode or Configuration mode If the temperature or the humidity value comes from the network via a SNVT and thecommunication fails, the reading will switch to a local sensor. If no remote sensor and no local sensor temperature or humidity is found the temperature sensor display and the dew point display will show "327.7C", the humidity sensor will show "163.8%", the system will put the Outputs to a full power 100% duty cycle and the Output Power will show "100%" and the %Saving will be 0%. You will get the alarm status after the Dew Point Set Time expires.Calibration can be done to the sensors using UCPTTempOffset and UCPTHumOffset.StPtMinStPtMax PwMin (20%) PwMax (95%)100 %0 %-18︒C37︒C(-1)(13) Full PowerDew Point (Default)% Power(Default)If Dew Point < Dew1 then %Power = Pwr1, If Dew Point > Dew2 then % Power = Pwr2 If Dew1 ≤ Dew Point ≤ Dew2 then Pwr1 ≤ %Power ≤ Pwr2 If Dew Point > Alarm Dew Point High Limit then %Power = FP (FP = Full Power = 100%)Output chanel timing diagram (25)Annex A LonMark Objects。
NuMicro N9H30系列开发板用户手册说明书

NuMicro®FamilyArm® ARM926EJ-S BasedNuMaker-HMI-N9H30User ManualEvaluation Board for NuMicro® N9H30 SeriesNUMAKER-HMI-N9H30 USER MANUALThe information described in this document is the exclusive intellectual property ofNuvoton Technology Corporation and shall not be reproduced without permission from Nuvoton.Nuvoton is providing this document only for reference purposes of NuMicro microcontroller andmicroprocessor based system design. Nuvoton assumes no responsibility for errors or omissions.All data and specifications are subject to change without notice.For additional information or questions, please contact: Nuvoton Technology Corporation.Table of Contents1OVERVIEW (5)1.1Features (7)1.1.1NuMaker-N9H30 Main Board Features (7)1.1.2NuDesign-TFT-LCD7 Extension Board Features (7)1.2Supporting Resources (8)2NUMAKER-HMI-N9H30 HARDWARE CONFIGURATION (9)2.1NuMaker-N9H30 Board - Front View (9)2.2NuMaker-N9H30 Board - Rear View (14)2.3NuDesign-TFT-LCD7 - Front View (20)2.4NuDesign-TFT-LCD7 - Rear View (21)2.5NuMaker-N9H30 and NuDesign-TFT-LCD7 PCB Placement (22)3NUMAKER-N9H30 AND NUDESIGN-TFT-LCD7 SCHEMATICS (24)3.1NuMaker-N9H30 - GPIO List Circuit (24)3.2NuMaker-N9H30 - System Block Circuit (25)3.3NuMaker-N9H30 - Power Circuit (26)3.4NuMaker-N9H30 - N9H30F61IEC Circuit (27)3.5NuMaker-N9H30 - Setting, ICE, RS-232_0, Key Circuit (28)NUMAKER-HMI-N9H30 USER MANUAL3.6NuMaker-N9H30 - Memory Circuit (29)3.7NuMaker-N9H30 - I2S, I2C_0, RS-485_6 Circuit (30)3.8NuMaker-N9H30 - RS-232_2 Circuit (31)3.9NuMaker-N9H30 - LCD Circuit (32)3.10NuMaker-N9H30 - CMOS Sensor, I2C_1, CAN_0 Circuit (33)3.11NuMaker-N9H30 - RMII_0_PF Circuit (34)3.12NuMaker-N9H30 - RMII_1_PE Circuit (35)3.13NuMaker-N9H30 - USB Circuit (36)3.14NuDesign-TFT-LCD7 - TFT-LCD7 Circuit (37)4REVISION HISTORY (38)List of FiguresFigure 1-1 Front View of NuMaker-HMI-N9H30 Evaluation Board (5)Figure 1-2 Rear View of NuMaker-HMI-N9H30 Evaluation Board (6)Figure 2-1 Front View of NuMaker-N9H30 Board (9)Figure 2-2 Rear View of NuMaker-N9H30 Board (14)Figure 2-3 Front View of NuDesign-TFT-LCD7 Board (20)Figure 2-4 Rear View of NuDesign-TFT-LCD7 Board (21)Figure 2-5 Front View of NuMaker-N9H30 PCB Placement (22)Figure 2-6 Rear View of NuMaker-N9H30 PCB Placement (22)Figure 2-7 Front View of NuDesign-TFT-LCD7 PCB Placement (23)Figure 2-8 Rear View of NuDesign-TFT-LCD7 PCB Placement (23)Figure 3-1 GPIO List Circuit (24)Figure 3-2 System Block Circuit (25)Figure 3-3 Power Circuit (26)Figure 3-4 N9H30F61IEC Circuit (27)Figure 3-5 Setting, ICE, RS-232_0, Key Circuit (28)Figure 3-6 Memory Circuit (29)Figure 3-7 I2S, I2C_0, RS-486_6 Circuit (30)Figure 3-8 RS-232_2 Circuit (31)Figure 3-9 LCD Circuit (32)NUMAKER-HMI-N9H30 USER MANUAL Figure 3-10 CMOS Sensor, I2C_1, CAN_0 Circuit (33)Figure 3-11 RMII_0_PF Circuit (34)Figure 3-12 RMII_1_PE Circuit (35)Figure 3-13 USB Circuit (36)Figure 3-14 TFT-LCD7 Circuit (37)List of TablesTable 2-1 LCD Panel Combination Connector (CON8) Pin Function (11)Table 2-2 Three Sets of Indication LED Functions (12)Table 2-3 Six Sets of User SW, Key Matrix Functions (12)Table 2-4 CMOS Sensor Connector (CON10) Function (13)Table 2-5 JTAG ICE Interface (J2) Function (14)Table 2-6 Expand Port (CON7) Function (16)Table 2-7 UART0 (J3) Function (16)Table 2-8 UART2 (J6) Function (16)Table 2-9 RS-485_6 (SW6~8) Function (17)Table 2-10 Power on Setting (SW4) Function (17)Table 2-11 Power on Setting (S2) Function (17)Table 2-12 Power on Setting (S3) Function (17)Table 2-13 Power on Setting (S4) Function (17)Table 2-14 Power on Setting (S5) Function (17)Table 2-15 Power on Setting (S7/S6) Function (18)Table 2-16 Power on Setting (S9/S8) Function (18)Table 2-17 CMOS Sensor Connector (CON9) Function (19)Table 2-18 CAN_0 (SW9~10) Function (19)NUMAKER-HMI-N9H30 USER MANUAL1 OVERVIEWThe NuMaker-HMI-N9H30 is an evaluation board for GUI application development. The NuMaker-HMI-N9H30 consists of two parts: a NuMaker-N9H30 main board and a NuDesign-TFT-LCD7 extensionboard. The NuMaker-HMI-N9H30 is designed for project evaluation, prototype development andvalidation with HMI (Human Machine Interface) function.The NuMaker-HMI-N9H30 integrates touchscreen display, voice input/output, rich serial port serviceand I/O interface, providing multiple external storage methods.The NuDesign-TFT-LCD7 can be plugged into the main board via the DIN_32x2 extension connector.The NuDesign-TFT-LCD7 includes one 7” LCD which the resolution is 800x480 with RGB-24bits andembedded the 4-wires resistive type touch panel.Figure 1-1 Front View of NuMaker-HMI-N9H30 Evaluation BoardNUMAKER-HMI-N9H30 USER MANUAL Figure 1-2 Rear View of NuMaker-HMI-N9H30 Evaluation Board1.1 Features1.1.1 NuMaker-N9H30 Main Board Features●N9H30F61IEC chip: LQFP216 pin MCP package with DDR (64 MB)●SPI Flash using W25Q256JVEQ (32 MB) booting with quad mode or storage memory●NAND Flash using W29N01HVSINA (128 MB) booting or storage memory●One Micro-SD/TF card slot served either as a SD memory card for data storage or SDIO(Wi-Fi) device●Two sets of COM ports:–One DB9 RS-232 port with UART_0 used 75C3232E transceiver chip can be servedfor function debug and system development.–One DB9 RS-232 port with UART_2 used 75C3232E transceiver chip for userapplication●22 GPIO expansion ports, including seven sets of UART functions●JTAG interface provided for software development●Microphone input and Earphone/Speaker output with 24-bit stereo audio codec(NAU88C22) for I2S interfaces●Six sets of user-configurable push button keys●Three sets of LEDs for status indication●Provides SN65HVD230 transceiver chip for CAN bus communication●Provides MAX3485 transceiver chip for RS-485 device connection●One buzzer device for program applicationNUMAKER-HMI-N9H30 USER MANUAL●Two sets of RJ45 ports with Ethernet 10/100 Mbps MAC used IP101GR PHY chip●USB_0 that can be used as Device/HOST and USB_1 that can be used as HOSTsupports pen drives, keyboards, mouse and printers●Provides over-voltage and over current protection used APL3211A chip●Retain RTC battery socket for CR2032 type and ADC0 detect battery voltage●System power could be supplied by DC-5V adaptor or USB VBUS1.1.2 NuDesign-TFT-LCD7 Extension Board Features●7” resolution 800x480 4-wire resistive touch panel for 24-bits RGB888 interface●DIN_32x2 extension connector1.2 Supporting ResourcesFor sample codes and introduction about NuMaker-N9H30, please refer to N9H30 BSP:https:///products/gui-solution/gui-platform/numaker-hmi-n9h30/?group=Software&tab=2Visit NuForum for further discussion about the NuMaker-HMI-N9H30:/viewforum.php?f=31 NUMAKER-HMI-N9H30 USER MANUALNUMAKER-HMI-N9H30 USER MANUAL2 NUMAKER-HMI-N9H30 HARDWARE CONFIGURATION2.1 NuMaker-N9H30 Board - Front View Combination Connector (CON8)6 set User SWs (K1~6)3set Indication LEDs (LED1~3)Power Supply Switch (SW_POWER1)Audio Codec(U10)Microphone(M1)NAND Flash(U9)RS-232 Transceiver(U6, U12)RS-485 Transceiver(U11)CAN Transceiver (U13)Figure 2-1 Front View of NuMaker-N9H30 BoardFigure 2-1 shows the main components and connectors from the front side of NuMaker-N9H30 board. The following lists components and connectors from the front view:NuMaker-N9H30 board and NuDesign-TFT-LCD7 board combination connector (CON8). This panel connector supports 4-/5-wire resistive touch or capacitance touch panel for 24-bits RGB888 interface.Connector GPIO pin of N9H30 FunctionCON8.1 - Power 3.3VCON8.2 - Power 3.3VCON8.3 GPD7 LCD_CSCON8.4 GPH3 LCD_BLENCON8.5 GPG9 LCD_DENCON8.7 GPG7 LCD_HSYNCCON8.8 GPG6 LCD_CLKCON8.9 GPD15 LCD_D23(R7)CON8.10 GPD14 LCD_D22(R6)CON8.11 GPD13 LCD_D21(R5)CON8.12 GPD12 LCD_D20(R4)CON8.13 GPD11 LCD_D19(R3)CON8.14 GPD10 LCD_D18(R2)CON8.15 GPD9 LCD_D17(R1)CON8.16 GPD8 LCD_D16(R0)CON8.17 GPA15 LCD_D15(G7)CON8.18 GPA14 LCD_D14(G6)CON8.19 GPA13 LCD_D13(G5)CON8.20 GPA12 LCD_D12(G4)CON8.21 GPA11 LCD_D11(G3)CON8.22 GPA10 LCD_D10(G2)CON8.23 GPA9 LCD_D9(G1) NUMAKER-HMI-N9H30 USER MANUALCON8.24 GPA8 LCD_D8(G0)CON8.25 GPA7 LCD_D7(B7)CON8.26 GPA6 LCD_D6(B6)CON8.27 GPA5 LCD_D5(B5)CON8.28 GPA4 LCD_D4(B4)CON8.29 GPA3 LCD_D3(B3)CON8.30 GPA2 LCD_D2(B2)CON8.31 GPA1 LCD_D1(B1)CON8.32 GPA0 LCD_D0(B0)CON8.33 - -CON8.34 - -CON8.35 - -CON8.36 - -CON8.37 GPB2 LCD_PWMCON8.39 - VSSCON8.40 - VSSCON8.41 ADC7 XPCON8.42 ADC3 VsenCON8.43 ADC6 XMCON8.44 ADC4 YMCON8.45 - -CON8.46 ADC5 YPCON8.47 - VSSCON8.48 - VSSCON8.49 GPG0 I2C0_CCON8.50 GPG1 I2C0_DCON8.51 GPG5 TOUCH_INTCON8.52 - -CON8.53 - -CON8.54 - -CON8.55 - -NUMAKER-HMI-N9H30 USER MANUAL CON8.56 - -CON8.57 - -CON8.58 - -CON8.59 - VSSCON8.60 - VSSCON8.61 - -CON8.62 - -CON8.63 - Power 5VCON8.64 - Power 5VTable 2-1 LCD Panel Combination Connector (CON8) Pin Function●Power supply switch (SW_POWER1): System will be powered on if the SW_POWER1button is pressed●Three sets of indication LEDs:LED Color DescriptionsLED1 Red The system power will beterminated and LED1 lightingwhen the input voltage exceeds5.7V or the current exceeds 2A.LED2 Green Power normal state.LED3 Green Controlled by GPH2 pin Table 2-2 Three Sets of Indication LED Functions●Six sets of user SW, Key Matrix for user definitionKey GPIO pin of N9H30 FunctionK1 GPF10 Row0 GPB4 Col0K2 GPF10 Row0 GPB5 Col1K3 GPE15 Row1 GPB4 Col0K4 GPE15 Row1 GPB5 Col1K5 GPE14 Row2 GPB4 Col0K6GPE14 Row2GPB5 Col1 Table 2-3 Six Sets of User SW, Key Matrix Functions●NAND Flash (128 MB) with Winbond W29N01HVS1NA (U9)●Microphone (M1): Through Nuvoton NAU88C22 chip sound input●Audio CODEC chip (U10): Nuvoton NAU88C22 chip connected to N9H30 using I2Sinterface–SW6/SW7/SW8: 1-2 short for RS-485_6 function and connected to 2P terminal (CON5and J5)–SW6/SW7/SW8: 2-3 short for I2S function and connected to NAU88C22 (U10).●CMOS Sensor connector (CON10, SW9~10)–SW9~10: 1-2 short for CAN_0 function and connected to 2P terminal (CON11)–SW9~10: 2-3 short for CMOS sensor function and connected to CMOS sensorconnector (CON10)Connector GPIO pin of N9H30 FunctionCON10.1 - VSSCON10.2 - VSSNUMAKER-HMI-N9H30 USER MANUALCON10.3 - Power 3.3VCON10.4 - Power 3.3VCON10.5 - -CON10.6 - -CON10.7 GPI4 S_PCLKCON10.8 GPI3 S_CLKCON10.9 GPI8 S_D0CON10.10 GPI9 S_D1CON10.11 GPI10 S_D2CON10.12 GPI11 S_D3CON10.13 GPI12 S_D4CON10.14 GPI13 S_D5CON10.15 GPI14 S_D6CON10.16 GPI15 S_D7CON10.17 GPI6 S_VSYNCCON10.18 GPI5 S_HSYNCCON10.19 GPI0 S_PWDNNUMAKER-HMI-N9H30 USER MANUAL CON10.20 GPI7 S_nRSTCON10.21 GPG2 I2C1_CCON10.22 GPG3 I2C1_DCON10.23 - VSSCON10.24 - VSSTable 2-4 CMOS Sensor Connector (CON10) FunctionNUMAKER-HMI-N9H30 USER MANUAL2.2NuMaker-N9H30 Board - Rear View5V In (CON1)RS-232 DB9 (CON2,CON6)Expand Port (CON7)Speaker Output (J4)Earphone Output (CON4)Buzzer (BZ1)System ResetSW (SW5)SPI Flash (U7,U8)JTAG ICE (J2)Power ProtectionIC (U1)N9H30F61IEC (U5)Micro SD Slot (CON3)RJ45 (CON12, CON13)USB1 HOST (CON15)USB0 Device/Host (CON14)CAN_0 Terminal (CON11)CMOS Sensor Connector (CON9)Power On Setting(SW4, S2~S9)RS-485_6 Terminal (CON5)RTC Battery(BT1)RMII PHY (U14,U16)Figure 2-2 Rear View of NuMaker-N9H30 BoardFigure 2-2 shows the main components and connectors from the rear side of NuMaker-N9H30 board. The following lists components and connectors from the rear view:● +5V In (CON1): Power adaptor 5V input ●JTAG ICE interface (J2) ConnectorGPIO pin of N9H30Function J2.1 - Power 3.3V J2.2 GPJ4 nTRST J2.3 GPJ2 TDI J2.4 GPJ1 TMS J2.5 GPJ0 TCK J2.6 - VSS J2.7 GPJ3 TD0 J2.8-RESETTable 2-5 JTAG ICE Interface (J2) Function●SPI Flash (32 MB) with Winbond W25Q256JVEQ (U7); only one (U7 or U8) SPI Flashcan be used●System Reset (SW5): System will be reset if the SW5 button is pressed●Buzzer (BZ1): Control by GPB3 pin of N9H30●Speaker output (J4): Through the NAU88C22 chip sound output●Earphone output (CON4): Through the NAU88C22 chip sound output●Expand port for user use (CON7):Connector GPIO pin of N9H30 FunctionCON7.1 - Power 3.3VCON7.2 - Power 3.3VCON7.3 GPE12 UART3_TXDCON7.4 GPH4 UART1_TXDCON7.5 GPE13 UART3_RXDCON7.6 GPH5 UART1_RXDCON7.7 GPB0 UART5_TXDCON7.8 GPH6 UART1_RTSCON7.9 GPB1 UART5_RXDCON7.10 GPH7 UART1_CTSCON7.11 GPI1 UART7_TXDNUMAKER-HMI-N9H30 USER MANUAL CON7.12 GPH8 UART4_TXDCON7.13 GPI2 UART7_RXDCON7.14 GPH9 UART4_RXDCON7.15 - -CON7.16 GPH10 UART4_RTSCON7.17 - -CON7.18 GPH11 UART4_CTSCON7.19 - VSSCON7.20 - VSSCON7.21 GPB12 UART10_TXDCON7.22 GPH12 UART8_TXDCON7.23 GPB13 UART10_RXDCON7.24 GPH13 UART8_RXDCON7.25 GPB14 UART10_RTSCON7.26 GPH14 UART8_RTSCON7.27 GPB15 UART10_CTSCON7.28 GPH15 UART8_CTSCON7.29 - Power 5VCON7.30 - Power 5VTable 2-6 Expand Port (CON7) Function●UART0 selection (CON2, J3):–RS-232_0 function and connected to DB9 female (CON2) for debug message output.–GPE0/GPE1 connected to 2P terminal (J3).Connector GPIO pin of N9H30 Function J3.1 GPE1 UART0_RXDJ3.2 GPE0 UART0_TXDTable 2-7 UART0 (J3) Function●UART2 selection (CON6, J6):–RS-232_2 function and connected to DB9 female (CON6) for debug message output –GPF11~14 connected to 4P terminal (J6)Connector GPIO pin of N9H30 Function J6.1 GPF11 UART2_TXDJ6.2 GPF12 UART2_RXDJ6.3 GPF13 UART2_RTSJ6.4 GPF14 UART2_CTSTable 2-8 UART2 (J6) Function●RS-485_6 selection (CON5, J5, SW6~8):–SW6~8: 1-2 short for RS-485_6 function and connected to 2P terminal (CON5 and J5) –SW6~8: 2-3 short for I2S function and connected to NAU88C22 (U10)Connector GPIO pin of N9H30 FunctionSW6:1-2 shortGPG11 RS-485_6_DISW6:2-3 short I2S_DOSW7:1-2 shortGPG12 RS-485_6_ROSW7:2-3 short I2S_DISW8:1-2 shortGPG13 RS-485_6_ENBSW8:2-3 short I2S_BCLKNUMAKER-HMI-N9H30 USER MANUALTable 2-9 RS-485_6 (SW6~8) FunctionPower on setting (SW4, S2~9).SW State FunctionSW4.2/SW4.1 ON/ON Boot from USB SW4.2/SW4.1 ON/OFF Boot from eMMC SW4.2/SW4.1 OFF/ON Boot from NAND Flash SW4.2/SW4.1 OFF/OFF Boot from SPI Flash Table 2-10 Power on Setting (SW4) FunctionSW State FunctionS2 Short System clock from 12MHzcrystalS2 Open System clock from UPLL output Table 2-11 Power on Setting (S2) FunctionSW State FunctionS3 Short Watchdog Timer OFFS3 Open Watchdog Timer ON Table 2-12 Power on Setting (S3) FunctionSW State FunctionS4 Short GPJ[4:0] used as GPIO pinS4Open GPJ[4:0] used as JTAG ICEinterfaceTable 2-13 Power on Setting (S4) FunctionSW State FunctionS5 Short UART0 debug message ONS5 Open UART0 debug message OFFTable 2-14 Power on Setting (S5) FunctionSW State FunctionS7/S6 Short/Short NAND Flash page size 2KBS7/S6 Short/Open NAND Flash page size 4KBS7/S6 Open/Short NAND Flash page size 8KBNUMAKER-HMI-N9H30 USER MANUALS7/S6 Open/Open IgnoreTable 2-15 Power on Setting (S7/S6) FunctionSW State FunctionS9/S8 Short/Short NAND Flash ECC type BCH T12S9/S8 Short/Open NAND Flash ECC type BCH T15S9/S8 Open/Short NAND Flash ECC type BCH T24S9/S8 Open/Open IgnoreTable 2-16 Power on Setting (S9/S8) FunctionCMOS Sensor connector (CON9, SW9~10)–SW9~10: 1-2 short for CAN_0 function and connected to 2P terminal (CON11).–SW9~10: 2-3 short for CMOS sensor function and connected to CMOS sensorconnector (CON9).Connector GPIO pin of N9H30 FunctionCON9.1 - VSSCON9.2 - VSSCON9.3 - Power 3.3VCON9.4 - Power 3.3V NUMAKER-HMI-N9H30 USER MANUALCON9.5 - -CON9.6 - -CON9.7 GPI4 S_PCLKCON9.8 GPI3 S_CLKCON9.9 GPI8 S_D0CON9.10 GPI9 S_D1CON9.11 GPI10 S_D2CON9.12 GPI11 S_D3CON9.13 GPI12 S_D4CON9.14 GPI13 S_D5CON9.15 GPI14 S_D6CON9.16 GPI15 S_D7CON9.17 GPI6 S_VSYNCCON9.18 GPI5 S_HSYNCCON9.19 GPI0 S_PWDNCON9.20 GPI7 S_nRSTCON9.21 GPG2 I2C1_CCON9.22 GPG3 I2C1_DCON9.23 - VSSCON9.24 - VSSTable 2-17 CMOS Sensor Connector (CON9) Function●CAN_0 Selection (CON11, SW9~10):–SW9~10: 1-2 short for CAN_0 function and connected to 2P terminal (CON11) –SW9~10: 2-3 short for CMOS sensor function and connected to CMOS sensor connector (CON9, CON10)SW GPIO pin of N9H30 FunctionSW9:1-2 shortGPI3 CAN_0_RXDSW9:2-3 short S_CLKSW10:1-2 shortGPI4 CAN_0_TXDSW10:2-3 short S_PCLKTable 2-18 CAN_0 (SW9~10) Function●USB0 Device/HOST Micro-AB connector (CON14), where CON14 pin4 ID=1 is Device,ID=0 is HOST●USB1 for USB HOST with Type-A connector (CON15)●RJ45_0 connector with LED indicator (CON12), RMII PHY with IP101GR (U14)●RJ45_1 connector with LED indicator (CON13), RMII PHY with IP101GR (U16)●Micro-SD/TF card slot (CON3)●SOC CPU: Nuvoton N9H30F61IEC (U5)●Battery power for RTC 3.3V powered (BT1, J1), can detect voltage by ADC0●RTC power has 3 sources:–Share with 3.3V I/O power–Battery socket for CR2032 (BT1)–External connector (J1)●Board version 2.1NUMAKER-HMI-N9H30 USER MANUAL2.3 NuDesign-TFT-LCD7 -Front ViewFigure 2-3 Front View of NuDesign-TFT-LCD7 BoardFigure 2-3 shows the main components and connectors from the Front side of NuDesign-TFT-LCD7board.7” resolution 800x480 4-W resistive touch panel for 24-bits RGB888 interface2.4 NuDesign-TFT-LCD7 -Rear ViewFigure 2-4 Rear View of NuDesign-TFT-LCD7 BoardFigure 2-4 shows the main components and connectors from the rear side of NuDesign-TFT-LCD7board.NuMaker-N9H30 and NuDesign-TFT-LCD7 combination connector (CON1).NUMAKER-HMI-N9H30 USER MANUAL 2.5 NuMaker-N9H30 and NuDesign-TFT-LCD7 PCB PlacementFigure 2-5 Front View of NuMaker-N9H30 PCB PlacementFigure 2-6 Rear View of NuMaker-N9H30 PCB PlacementNUMAKER-HMI-N9H30 USER MANUALFigure 2-7 Front View of NuDesign-TFT-LCD7 PCB PlacementFigure 2-8 Rear View of NuDesign-TFT-LCD7 PCB Placement3 NUMAKER-N9H30 AND NUDESIGN-TFT-LCD7 SCHEMATICS3.1 NuMaker-N9H30 - GPIO List CircuitFigure 3-1 shows the N9H30F61IEC GPIO list circuit.Figure 3-1 GPIO List Circuit NUMAKER-HMI-N9H30 USER MANUAL3.2 NuMaker-N9H30 - System Block CircuitFigure 3-2 shows the System Block Circuit.NUMAKER-HMI-N9H30 USER MANUALFigure 3-2 System Block Circuit3.3 NuMaker-N9H30 - Power CircuitFigure 3-3 shows the Power Circuit.NUMAKER-HMI-N9H30 USER MANUALFigure 3-3 Power Circuit3.4 NuMaker-N9H30 - N9H30F61IEC CircuitFigure 3-4 shows the N9H30F61IEC Circuit.Figure 3-4 N9H30F61IEC CircuitNUMAKER-HMI-N9H30 USER MANUAL3.5 NuMaker-N9H30 - Setting, ICE, RS-232_0, Key CircuitFigure 3-5 shows the Setting, ICE, RS-232_0, Key Circuit.NUMAKER-HMI-N9H30 USER MANUALFigure 3-5 Setting, ICE, RS-232_0, Key Circuit3.6 NuMaker-N9H30 - Memory CircuitFigure 3-6 shows the Memory Circuit.NUMAKER-HMI-N9H30 USER MANUALFigure 3-6 Memory Circuit3.7 NuMaker-N9H30 - I2S, I2C_0, RS-485_6 CircuitFigure 3-7 shows the I2S, I2C_0, RS-486_6 Circuit.NUMAKER-HMI-N9H30 USER MANUALFigure 3-7 I2S, I2C_0, RS-486_6 Circuit3.8 NuMaker-N9H30 - RS-232_2 CircuitFigure 3-8 shows the RS-232_2 Circuit.NUMAKER-HMI-N9H30 USER MANUALFigure 3-8 RS-232_2 Circuit3.9 NuMaker-N9H30 - LCD CircuitFigure 3-9 shows the LCD Circuit.NUMAKER-HMI-N9H30 USER MANUALFigure 3-9 LCD Circuit3.10 NuMaker-N9H30 - CMOS Sensor, I2C_1, CAN_0 CircuitFigure 3-10 shows the CMOS Sensor,I2C_1, CAN_0 Circuit.NUMAKER-HMI-N9H30 USER MANUALFigure 3-10 CMOS Sensor, I2C_1, CAN_0 Circuit3.11 NuMaker-N9H30 - RMII_0_PF CircuitFigure 3-11 shows the RMII_0_RF Circuit.NUMAKER-HMI-N9H30 USER MANUALFigure 3-11 RMII_0_PF Circuit3.12 NuMaker-N9H30 - RMII_1_PE CircuitFigure 3-12 shows the RMII_1_PE Circuit.NUMAKER-HMI-N9H30 USER MANUALFigure 3-12 RMII_1_PE Circuit3.13 NuMaker-N9H30 - USB CircuitFigure 3-13 shows the USB Circuit.NUMAKER-HMI-N9H30 USER MANUALFigure 3-13 USB Circuit3.14 NuDesign-TFT-LCD7 - TFT-LCD7 CircuitFigure 3-14 shows the TFT-LCD7 Circuit.Figure 3-14 TFT-LCD7 CircuitNUMAKER-HMI-N9H30 USER MANUAL4 REVISION HISTORYDate Revision Description2022.03.24 1.00 Initial version NUMAKER-HMI-N9H30 USER MANUALNUMAKER-HMI-N9H30 USER MANUALImportant NoticeNuvoton Products are neither intended nor warranted for usage in systems or equipment, anymalfunction or failure of which may cause loss of human life, bodily injury or severe propertydamage. Such applications are deemed, “Insecure Usage”.Insecure usage includes, but is not limited to: equipment for surgical implementation, atomicenergy control instruments, airplane or spaceship instruments, the control or operation ofdynamic, brake or safety systems designed for vehicular use, traffic signal instruments, all typesof safety devices, and other applications intended to support or sustain life.All Insecure Usage shall be made at customer’s risk, and in the event that third parties lay claimsto Nuvoton as a result of customer’s Insecure Usage, custome r shall indemnify the damagesand liabilities thus incurred by Nuvoton.。
TPS54620 Step-Down Converter Evaluation Module Use
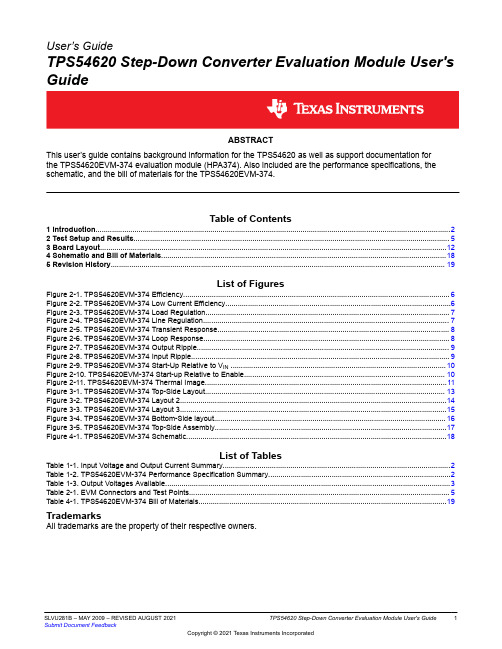
User’s GuideTPS54620 Step-Down Converter Evaluation Module User's GuideABSTRACTThis user’s guide contains background information for the TPS54620 as well as support documentation forthe TPS54620EVM-374 evaluation module (HPA374). Also included are the performance specifications, the schematic, and the bill of materials for the TPS54620EVM-374.Table of Contents1 Introduction (2)2 Test Setup and Results (5)3 Board Layout (12)4 Schematic and Bill of Materials (18)5 Revision History (19)List of FiguresFigure 2-1. TPS54620EVM-374 Efficiency (6)Figure 2-2. TPS54620EVM-374 Low Current Efficiency (6)Figure 2-3. TPS54620EVM-374 Load Regulation (7)Figure 2-4. TPS54620EVM-374 Line Regulation (7)Figure 2-5. TPS54620EVM-374 Transient Response (8)Figure 2-6. TPS54620EVM-374 Loop Response (8)Figure 2-7. TPS54620EVM-374 Output Ripple (9)Figure 2-8. TPS54620EVM-374 Input Ripple (9)Figure 2-9. TPS54620EVM-374 Start-Up Relative to V IN (10)Figure 2-10. TPS54620EVM-374 Start-up Relative to Enable (10)Figure 2-11. TPS54620EVM-374 Thermal Image (11)Figure 3-1. TPS54620EVM-374 Top-Side Layout (13)Figure 3-2. TPS54620EVM-374 Layout 2 (14)Figure 3-3. TPS54620EVM-374 Layout 3 (15)Figure 3-4. TPS54620EVM-374 Bottom-Side layout (16)Figure 3-5. TPS54620EVM-374 Top-Side Assembly (17)Figure 4-1. TPS54620EVM-374 Schematic (18)List of TablesTable 1-1. Input Voltage and Output Current Summary (2)Table 1-2. TPS54620EVM-374 Performance Specification Summary (2)Table 1-3. Output Voltages Available (3)Table 2-1. EVM Connectors and Test Points (5)Table 4-1. TPS54620EVM-374 Bill of Materials (19)TrademarksAll trademarks are the property of their respective owners.Introduction 1 Introduction1.1 BackgroundThe TPS54620 dc/dc converter is designed to provide up to a 6 A output. The TPS54620 implements asplit input power rails with separate input voltage inputs for the power stage and control circuitry. The power stage input (PVIN) is rated for 1.6 V to 17 V while the control input (VIN) is rated for 4.5 to 17 V. TheTPS54620EVM-374 provides both inputs but is designed and tested using the PVIN connected to VIN. Rated input voltage and output current range for the evaluation module are given in Table 1-1. This evaluation module is designed to demonstrate the small printed-circuit-board areas that may be achieved when designing with the TPS54620 regulator. The switching frequency is externally set at a nominal480 kHz. The high-side and low-side MOSFETs are incorporated inside the TPS54620 package along with the gate drive circuitry. The low drain-to-source on resistance of the MOSFET allows the TPS54620 to achievehigh efficiencies and helps keep the junction temperature low at high output currents. The compensation components are external to the integrated circuit (IC), and an external divider allows for an adjustable output voltage. Additionally, the TPS54620 provides adjustable slow start, tracking and undervoltage lockout inputs. The absolute maximum input voltage is 20 V for the TPS54620EVM-374.1.2 Performance Specification SummaryA summary of the TPS54620EVM-374 performance specifications is provided in Table 1-2. Specifications are given for an input voltage of V IN = 12 V and an output voltage of 3.3 V, unless otherwise specified. TheTPS54620EVM-374 is designed and tested for V IN = 8 V to 17 V with the VIN and PVIN pins connect together with the J3 jumper. The ambient temperature is 25°C for all measurements, unless otherwise noted.1.3 ModificationsThese evaluation modules are designed to provide access to the features of the TPS54620. Some modifications can be made to this module.2TPS54620 Step-Down Converter Evaluation Module User's Guide SLVU281B – MAY 2009 – REVISED AUGUST 20211.3.1 Output Voltage Set PointThe output voltage is set by the resistor divider network of R8 and R9. R9 is fixed at 10 kΩ. To change the output voltage of the EVM, it is necessary to change the value of resistor R8. Changing the value of R8 can change the output voltage above 0.8 V. The value of R8 for a specific output voltage can be calculated using Equation 1.)OUT k V -V R V10W(0.88=0.8(1)Table 1-3 lists the R8 values for some common output voltages. Note that V IN must be in a range so that the minimum on-time is greater than 120 ns, and the maximum duty cycle is less than 95%. The values given in Table 1-3 are standard values, not the exact value calculated using Equation 1.1.3.2 Slow Start TimeThe slow start time can be adjusted by changing the value of C7. Use Equation 2 to calculate the required value of C7 for a desired slow start timeTss(ms)Iss(μA)C7(nF)=Vref(V)´(2)The EVM is set for a slow start time of 4 msec using C7 = 0.01 µF.1.3.3 Track InThe TPS54620 can track an external voltage during start up. The J5 connector is provided to allow connection to that external voltage. Ratio-metric or simultaneous tracking can be implemented using resistor divider R5 and R6. See the TPS54620 data sheet (SLVS949) for details.1.3.4 Adjustable UVLOThe under voltage lock out (UVLO) ca be adjusted externally using R1 and R2. The EVM is st for a start voltage of 6.521 V and a stop voltage of 6.065 V using R1 = 35.7 kΩ and R2 = 8.06 kΩ. Use Equation 3 and Equation 4 to calculate required resistor values for different start and stop voltages.ENFALLING START STOPENRISING ENFALLING p h ENRISING V V -V V R1=V I 1-+I V æöç÷èøæöç÷èø(3)ENFALLINGSTOP ENFALLING p h R1×V R2=V -V +R1(I +I )(4) IntroductionIntroduction 1.3.5 Input Voltage RailsThe EVM is designed to accommodate different input voltage levels for the power stage and control logic. During normal operation, the PVIN and VIN inputs are connected together using a jumper across J3. The single input voltage is supplied at J1. If desired, these to input voltage rails may be separated by removing the jumper across J3. Two input voltages must then be provided at both J1 and J2. Test Setup and Results2 Test Setup and ResultsThis section describes how to properly connect, set up, and use the TPS54620EVM-374 evaluation module.The section also includes test results typical for the evaluation module and covers efficiency, output voltage regulation, load transients, loop response, output ripple, input ripple, and start-up.2.1 Input / Output ConnectionsThe TPS54620EVM-374 is provided with input/output connectors and test points as shown in Table 2-1. A power supply capable of supplying 4 A must be connected to J1 through a pair of 20 AWG wires. The jumper acrossJ3 must be in place. See Section 1.3.5 for split input voltage rail operation. The load must be connected toJ7 through a pair of 20 AWG wires. The maximum load current capability must be 6 A. Wire lengths must be minimized to reduce losses in the wires. Test-point TP1 provides a place to monitor the V IN input voltages with TP2 providing a convenient ground reference. TP8 is used to monitor the output voltage with TP9 as the ground reference.Test Setup and Results 2.2 EfficiencyThe efficiency of this EVM peaks at a load current of about 2 A and then decreases as the load current increasesshows the efficiency for the TPS54620EVM-374 at an ambient temperature of 25°C.towards full load. Figure 2-1Figure 2-2 shows the efficiency for the TPS54620EVM-374 at lower output currents below 0.10 A at an ambienttemperature of 25°C.The efficiency may be lower at higher ambient temperatures, due to temperature variation in the drain-to-source resistance of the internal MOSFET. Test Setup and Results 2.3 Output Voltage Load Regulationshows the load regulation for the TPS54620EVM-374.Figure 2-3Measurements are given for an ambient temperature of 25°C.2.4 Output Voltage Line RegulationFigure 2-4shows the line regulation for the TPS54620EVM-374.2.5 Load TransientsFigure 2-5 shows the TPS54620EVM-374 response to load transients. The current step is from 25% to 75% of maximum rated load at 12 V input. Total peak-to-peak voltage variation is as shown, including ripple and noiseon the output.Figure 2-5. TPS54620EVM-374 Transient Response2.6 Loop CharacteristicsFigure 2-6 shows the TPS54620EVM-374 loop-response characteristics. Gain and phase plots are shown for V INFigure 2-6. TPS54620EVM-374 Loop ResponseTest Setup and Results 2.7 Output Voltage RippleFigure 2-7 shows the TPS54620EVM-374 output voltage ripple. The output current is the rated full load of 6 A and V IN= 12 V. The ripple voltage is measured directly across the output capacitors.Figure 2-7. TPS54620EVM-374 Output Ripple2.8 Input Voltage RippleFigure 2-8 shows the TPS54620EVM-374 input voltage. The output current is the rated full load of 4 A and V IN =12 V. The ripple voltage is measured directly across the input capacitors.Figure 2-8. TPS54620EVM-374 Input Ripple Test Setup and ResultsTest Setup and Results 2.9 Powering UpFigure 2-9 and Figure 2-10 show the start-up waveforms for the TPS54620EVM-374 . In Figure 2-9, the output voltage ramps up as soon as the input voltage reaches the UVLO threshold as set by the R1 and R2 resistor divider network. In Figure 2-10, the input voltage is initially applied and the output is inhibited by using a jumper at J2 to tie EN to GND. When the jumper is removed, EN is released. When the EN voltage reaches theenable-threshold voltage, the start-up sequence begins and the output voltage ramps up to the externally set value of 3.3 V. The input voltage for these plots is 12 V and the load is 1Ω.Figure 2-9. TPS54620EVM-374 Start-Up Relative to VIN Array Figure 2-10. TPS54620EVM-374 Start-up Relative to Enable Test Setup and Results 2.10 Thermal CharacteristicsThis section shows a thermal image of the TPS54620EVM-374 running at 12 V input and 6 A load. there is no air flow and the ambient temperature is 25°C. The peak temperature of the IC (70°C) is well below the maximum recommended operating condition listed in the data sheet of 150°C.Figure 2-11. TPS54620EVM-374 Thermal ImageBoard Layout 3 Board LayoutThis section provides a description of the TPS54620EVM-374 , board layout, and layer illustrations.3.1 LayoutThe board layout for the TPS54620EVM-374 is shown in Figure 3-1 through Figure 3-5. The topside layer of the EVM is laid out in a manner typical of a user application. The top, bottom and internal layers are 2-oz. copper. The top layer contains the main power traces for PVIN, VIN, V OUT, and VPHASE. Also on the top layer are connections for the remaining pins of the TPS54620 and a large area filled with ground. The bottom and internal ground layers contains ground planes only. The top side ground traces are connected to the bottom and internal ground planes with multiple vias placed around the board including two vias directly under the TPS54620 device to provide a thermal path from the top-side ground plane to the bottom-side ground plane.The input decoupling capacitors (C2, and C3) and bootstrap capacitor (C5) are all located as close to the ICas possible. In addition, the voltage set-point resistor divider components are also kept close to the IC. The voltage divider network ties to the output voltage at the point of regulation, the copper V OUT trace at the J7 output connector. For the TPS54620, an additional input bulk capacitor may be required, depending on the EVM connection to the input supply. Critical analog circuits such as the voltage setpoint divider, frequency set resistor, slow start capacitor and compensation components are terminated to ground using a wide ground trace separate from the power ground pour. Board LayoutFigure 3-1. TPS54620EVM-374 Top-Side LayoutBoard Layout Figure 3-2. TPS54620EVM-374 Layout 2 Board LayoutFigure 3-3. TPS54620EVM-374 Layout 3Board Layout Figure 3-4. TPS54620EVM-374 Bottom-Side layout Board LayoutFigure 3-5. TPS54620EVM-374 Top-Side Assembly3.2 Estimated Circuit AreaThe estimated printed circuit board area for the components used in this design is 0.58 in2 (374 mm2). This area does not include test point or connectors.Schematic and Bill of Materials 4 Schematic and Bill of MaterialsThis section presents the TPS54620EVM-374 schematic and bill of materials.4.1 Schematicis the schematic for the TPS54620EVM-374.Figure 4-1 Schematic and Bill of Materials 4.2 Bill of MaterialsTable 4-1 presents the bill of materials for the TPS54620EVM-374 .5 Revision HistoryNOTE: Page numbers for previous revisions may differ from page numbers in the current version.Changes from Revision A (March 2017) to Revision B (August 2021)Page •Updated the numbering format for tables, figures, and cross-references throughout the document. (2)•Updated the user's guide title (2)Changes from Revision * (May 2009) to Revision A (March 2017)Page •Changed the Load transient response TYP values in Table 1-2 (2)•Changed the Loop bandwidth TYP value From: 45 To 43 kHz in Table 1-2 (2)•Changed the Phase margin TYP value From: 46 To 52° in Table 1-2 (2)•Changed the Output ripple voltage TYP value From: 18 To 20 mVPP in Table 1-2 (2)•Replaced Figure 2-5 (8)•Replaced Figure 2-6 (8)•Replaced Figure 2-7 (9)Revision History •Replaced Figure 4-1 (18)•Changed values of C8, C9, R4, C4, and the Description of U1 in Table 4-1 (19)IMPORTANT NOTICE AND DISCLAIMERTI PROVIDES TECHNICAL AND RELIABILITY DATA (INCLUDING DATA SHEETS), DESIGN RESOURCES (INCLUDING REFERENCE DESIGNS), APPLICATION OR OTHER DESIGN ADVICE, WEB TOOLS, SAFETY INFORMATION, AND OTHER RESOURCES “AS IS” AND WITH ALL FAULTS, AND DISCLAIMS ALL WARRANTIES, EXPRESS AND IMPLIED, INCLUDING WITHOUT LIMITATION ANY IMPLIED WARRANTIES OF MERCHANTABILITY, FITNESS FOR A PARTICULAR PURPOSE OR NON-INFRINGEMENT OF THIRD PARTY INTELLECTUAL PROPERTY RIGHTS.These resources are intended for skilled developers designing with TI products. You are solely responsible for (1) selecting the appropriate TI products for your application, (2) designing, validating and testing your application, and (3) ensuring your application meets applicable standards, and any other safety, security, regulatory or other requirements.These resources are subject to change without notice. TI grants you permission to use these resources only for development of an application that uses the TI products described in the resource. Other reproduction and display of these resources is prohibited. No license is granted to any other TI intellectual property right or to any third party intellectual property right. TI disclaims responsibility for, and you will fully indemnify TI and its representatives against, any claims, damages, costs, losses, and liabilities arising out of your use of these resources.TI’s products are provided subject to TI’s Terms of Sale or other applicable terms available either on or provided in conjunction with such TI products. TI’s provision of these resources does not expand or otherwise alter TI’s applicable warranties or warranty disclaimers for TI products.TI objects to and rejects any additional or different terms you may have proposed.Mailing Address: Texas Instruments, Post Office Box 655303, Dallas, Texas 75265Copyright © 2022, Texas Instruments Incorporated。
AVBits HDBaseT Extender Set 70m 用户手册说明书

User ManualAVB-HD-LTEPowered by PTNHDBaseT Extender Set 70mAll Rights ReservedVersion: AVB-HD-LTE_2015V1.0Read the user manual carefully before using this product. Pictures shown in this manual are for reference purposes only,This manual is only for user operation and not for service or repair. This manual version covers the model up until July 2015. Any further changes or updates of this model from July 2015 will be followed up with an updated manual separately.Please refer to your dealer for the latest information and updates.All product information is valid until 7-9-2015.TrademarksProduct AVBits and its logo are trademarks of Integration Supplies Pty. Ltd. Any other trademarks mentioned in this manual are acknowledged as the properties of the trademark owner. No part of this publication may be copied or reproduced without the prior written consent of Integration Supplies Pty. Ltd.FCC StatementThis equipment may generate or radiate radio frequency (RF) energy. If the product is not installed and used in accordance with the instructions provided, it may cause harmful radio interference. This product has been tested and found to comply with the limits of a Class B Digital Device, pursuant to part 15 of the FCC Rules. These limits are designed to provide reasonable protection against harmful interference in a commercial installation and environment.Operation of this equipment in a residential environment may could cause interference, in which case the user at their own expense, will be required to take whatever measures may be necessary to correct the interferenceAny changes or modifications not expressly approved by the manufacture, will void allwarranty’s and user will be liable for any damages arising from its use.To insure the best performance from the product, please read all instructions carefully before using the device. Save this manual for further reference.l●Unpack the equipment carefully and save the original box and packing material for possible future shipmentl●Follow basic safety precautions to reduce the risk of fire, electrical shock and injury to persons.l●Do not open or dismantle equipment as electric shock or fire hazard may result.l●Using third party supplied parts (e.g. Power Supplies) not meeting the products’ specifications may cause damage, deterioration or malfunction.l●Refer all servicing to qualified service personnel.l●To prevent fire or shock hazard, do not expose the unit to moisture.l●Make sure cable is not crushed by heavy objects.l●Do not open or interfere with internal components within the device, doing so will void warranty and may result in electric shock or other hazards.l●Install the device in a place with plenty of ventilation to avoid possible overheating. l●If a liquid spills into the device, unplug the device immediately.l●Do not twist or pull by force the ends of any connecting cable. This will cause a malfunction.l●Do not use liquid or aerosol cleaners to clean this unit, use a damp cloth to wipe it down, Always unplug the power to the device before cleaning.l●Unplug the power from device if not used for a long period of time.l●Place device in recycle waste bin when no longer required.1. Introduction (1)1.1 Introduction to AVB-HD-LTE (1)1.2 Features (1)1.3 Package List (1)2. Product Appearance (2)2.1 AVB-HD-LTE T (2)2.2 AVB-HD-LTE R (3)3. System Connection (4)3.1 Usage Precautions (4)3.2 System Diagram (4)3.3 Connection Procedure (4)3.4 Application (5)3.5 Twisted Pair Cable Connection (5)4. Specification (6)4.1 Supported Resolution (7)5. Panel Drawing (8)6. Troubleshooting & Maintenance (9)7. After-sales Service (10)1. Introduction1.1 Introduction to AVB-HD-LTEThe extender set consists of a transmitter and receiver pair. HDMI signals are fed into the transmitter, and HDBaseT technology is used to transmit the signal to the receiver up to 70 metres via a Cat6, Cat6A or Cat6A Shielded UTP cable. The receiver then outputs the HDMI signal to a display or switching device.Bi-directional IR is also transmitted across the Cat6,Cat6A or Cat6A Shielded UTP cable. The extender set supports PoC, which can be used to power the receiver via the Cat6, Cat6A or Cat6A Shielded UTP cable. This eliminates the need for power at the receiver end.1.2 Featuresl●Supports full HD: Delivers high-resolution images (1080p 3D, 4Kx2K)l●Maximum transmission distance is 70 Metres for 1080p and 40m for 4Kx2K over a single Cat6,Cat6A or Cat6A Shielded UTP cablel●High Bandwidth: 10.2Gps.l●HDTV Compatible, use HDMI 1.4 and HDCP compliant.l●Support PoC & CEC.l●Uses HDBaseT technology for extended capability and reliabilityl●Bi-directional IR controll●LED indicators show working status.Note: Using Cat6, Cat6A or Cat6A Shielded UTP cable is recommended for good signal transmission.1.3 Package ListØ 1 x AVB-HD-LTE (including TX and RX)Ø 4 x detachable mounting earsØ 4 x screwsØ 8 x plastic cushionsØ 1 x power adapter (DC 12V 1A)Ø 1 x user manualNotes:Please confirm if the product and the accessories are all included, if not, pleasecontact your dealer.2.1 AVB-HD-LTE T1) HDMI IN: Connect to HDMI source.2) IR IN: Connect to an IR receiver, the IR signal received from this port can onlysend out via AVB-HD-LTE R.3) IR OUT: Connect with IR emitter; the sent IR signals are received by AVB-HD-LTER.4) Power Indicator: illuminates when device is powered up5) 12Volt DC in socket for connection of 12Volt DC Power Supply.6) TP OUT: Connect to the TP IN socket on the AVB-HD-LTE R via Cat6, Cat6A orCat6A Shielded UTP cable.2.2AVB-HD-LTE R1) HDMI Out: Connect to HDMI display.2) IR IN: Connect to an IR receiver, the IR signal received from this port can only be send out via AVB-HD-LTE T.3) IR OUT: Connect with IR emitter; the sent IR signals are received by AVB-HD-LTE T.4) Power Indicator: illuminates when device is powered up5) TP IN: Connect to the HDBaseT port on the AVB-HD-LTE T via Cat6, Cat6A or Cat6A Shielded UTP cable6)Note: AVB-HD-LTE boasts 2 indicators to show real-time operation information:Indicator FunctionDetailsGreenShows inputsignal connectionConnected :HDCP Compliant: LED Hardon.Not HDCP Compliant: LED Blinking.Disconnected : LED OffYellow Indicate linking status ofthe transmitter and the receiverConnected : LED IlluminatedDisconnected : LED Off3. System Connection3.1 Usage Precautions1) System should be installed in a clean environment with suitable temp and humidity. 2) All of the power switches, plugs, sockets and power cords should be insulated forsafety.3) All devices should be connected before power is switched on.4) The Cat6, Cat6A or Cat6A Shielded UTP cable terminations for HDBaseT devicesshould be a straight-thru TIA/EIA T568B standard.3.2 System Diagram3.3 Connection ProcedureStep1. Connect HDMI source (such as Blue-ray DVD) to HDMI IN port of the transmitterwith an HDMI cable.Step2. Connect TP OUT port of the transmitter to TP IN port of the receiver through aCat6, Cat6A or Cat6A Shielded UTP cable.Step3. Connect a HDMI display (such as HDTV) to HDMI OUT port of the receiver withHDMI cable.Step4. When using the bi-directional IR control, do the following:a) Connect the IR emitter at either end to the IR OUT port on either thetransmitter or the receiver.b) When using a powered IR receiver, connect via a 3.5 mm stereo plug to theIR IN on either the receiver or the transmitter.Step5. Connect with DC 12V power supply to the 12Volt DC IN socket on theAVB-HD-LTE Tx, the AVB-HD-LTE Rx will be powered simultaneously with the with PoC solution.3.4 ApplicationAVB-HD-LTE has many applications (e.g. PC’s, Monitors, Big displays, Meeting rooms, Education, Security) etc.3.5 Twisted Pair Cable ConnectionThe Cat6, Cat6A or Cat6A Shielded UTP cable terminations for HDBaseT devices should be a straight thru TIA/EIAT568B standard. TIA/EIA T568A standard is NOT recommended.Note : To eliminate the risk of RFI into the signal UTP cable, the use of a Cat6A Shielded grade cable is highly recommended. Shield MUST BE continuous from Tx to RX and shielded metal plugs installed onto cables.TIA/EIA T568ATIA/EIA T568B Pin Cable color Pin Cable color 1 green white 1 orange white 2 green 2 orange 3 orange white 3 green white 4 blue 4 blue 5 blue white 5 blue white 6 orange 6 green 7 brown white 7 brown white 8 brown8brown 1st Ground 4--5 1st Group 4--5 2nd Ground 3--6 2nd Group 1--2 3rd Group 1--2 3rd Group 3--6 4th Group7--8 4th Group 7--84. SpecificationNOTE: All nominal levels are at ±10%.4.1 Supported ResolutionFormat ResolutionHDMI 480I, 480P, 576I, 576P, 720P, 1080I, 1080P, 4Kx2K, 1080P 3DDVI 640x480@60Hz, 640x480@72Hz, 640x480@75Hz, 800x600@60Hz, 800x600@72Hz, 800x600@75Hz, 1024x768@60Hz, 1024x768@70Hz, 1024x768@75Hz, 1280x720@60 Hz, 1280x1024@60Hz,1280x1024@75Hz, 1600x1200@60Hz, 1920x1080@60Hz,1920x1200@60HzNote: AVB-HD-LTE supports 4k&1080p 3D HDMI signal please make sure high quality HDMI cables are used compliant with HDMI1.4 for reliable transmission when using this product.5. Panel DrawingAVB-HD-LTE T AVB-HD-LTE R24.00 mm.97mm.95mm24.00 mm.97mm2.95mml●No image on display:l●Ensure that the display device has been set to the correct input.l●Ensure that the HDMI cables used for both the source/transmitter and the receiver/display are properly connected and are working. Test the HDMI cables directly from a source to display and ensure their operation.l●Ensure that the Cat6, Cat6A or Cat6A Shielded UTP cable have not been damaged, and that they have been terminated correctly. A temporary length ofCat6, Cat6A or Cat6A Shielded UTP cable can be used for testing to ensure that the devices are working properly.l●Ensure proper grounding of the Cat6A Shielded UTP cablesl●Ensure proper grounding of the power supply.l●Known issues with HDMI 1.2 source devices:Older compatibility (HDMI 1.2) may result in HDBaseT transmission issues.Please contact Technical Support at Integration Supplies Pty. Ltd. for a solution to these issues. *********************.aul●Colour loss or poor picture quality:l●Ensure that the HDMI cables used are of the best quality.l●Test the HDMI cables directly from a source to display and ensure they work.l●Ensure proper grounding of the power supply.l●If the static or picture quality becomes worse when connecting the video connectors, this may be due to improper grounding.l●Check the grounding and make sure all the components are properly grounded to a common ground. Make sure ALL equipment is on the same phase.l●Improper grounding may cause damage to the receiver.If your problem persists after following the above troubleshooting steps,seek further Technical assistance and help by contacting *********************.au7. After-sales ServiceIf you are experiencing problems when using the device, please refer to user manual. Any transport costs are borne by the users during the warranty period.1) Product Limited Warranty: We warrant that our products will be free from defectsin materials and workmanship for two years, which starts from the first day the product leaves the Integration Supplies warehouse (check the SN mark on theproduct).Proof of purchase in the form of a bill of sale or receipted invoice must be presented to obtain warranty service.2) What the warranty does not cover:l● Warranty expiration.l● Factory applied serial number has been altered or removed from the product.l● Damage, deterioration or malfunction caused by:l●Normal wear and tearl●Use of supplies or parts not meeting our specificationsl●No certificate or invoice as the proof of warranty.l●The product model showed on the warranty card does not match with themodel of the product for repair.l●Product has been altered or interfered with.l●Damage caused by physical force.l●Unauthorized Servicing by others.l●Any other causes which does not relate to a product defectl●Delivery, Installation, Installation Labor, or Setup of the Device or Product. 3) Technical Support:For all product support contact: *********************.auPlease have the following information available:l● Product Model.l● Product Serial Numberl● Detailed failure information.l● Information and details of Devices used and how they are connected etc.。
弗拉迪姆高流筛选器系列产品说明说明书

Catalog 0730-2Hi-Flow F602 SeriesHi-Flow Filters2 & 2-1/2 Inch PortsFeatures• Excellent water removal efficiency • For heavy duty applications with minimum pressure drop requirement • Unique deflector plate that creates swirling of the air stream ensuring maximum water and dirt separation • Large filter element surface guarantees low pressure drop and increased element life• 40 micron filter element standard • Metal bowl with sight gauge standard • Twist drain as standard, optional auto drain• Large bowl capacity• Optional high capacity bowl(s) available • High flow: 2 & 2-1/2" – 1200 SCFM §Drains and Options Blank Manual Twist Drain Q External Heavy Duty Auto Drain R Internal Auto DrainOrdering InformationF 602 — 16 W J /**BowlE 32 oz. Large Capacity Metal without Sight GaugeW 16 oz. Metal with Sight GaugeElement J 40 MicronPort Size 16 2 Inch 20 2-1/2 InchPort Threads — NPT G BSPPEngineeringLevel * Will be Entered at Factory.Standard part numbers shown bold.For other models refer to ordering information below.§SCFM = Standard cubic feet per minute at 90 PSIG inlet and 5 PSIG pressure drop.Port Size NPTTwist DrainAutomatic Pulse DrainMetal Bowl / Sight Gauge - 16 oz.2"F602-16WJ F602-16WJR 2-1/2"F602-20WJ F602-20WJR Metal Bowl without Sight Gauge - 32 oz.2"F602-16EJ F602-16EJR 2-1/2"F602-20EJF602-20EJRAutomaticDrainManual DrainF602 Filter Dimensions A BCD E F F602-16W, F602-20W4.90(124)11.08 (281)13.00 (330) 6.30 (160) 1.92 (48.7) 2.45(62.2)F602-16E, F602-20E4.90(124)14.31(364)16.23(412)6.30 (160)1.92 (48.7)2.45(62.2)inches (mm)BOLD ITEMS ARE MOST POPULAR.Catalog 0730-2Technical Specifications – F602F602 Series, 2 & 2-1/2 Inch Ports Hi-Flow FiltersTechnical InformationF602 Filter Kits & AccessoriesBowl Kits –Aluminum (E) .....................................................................BK603B Zinc with Sight Gauge (W) ..............................................BK605WB Drain Kits –External Auto (E) .................................................................SA603D External Auto (W) ................................................................SA602D Internal Auto (All) ............................................................SA602MD Manual (All) ...................................................................SA600Y7-1Semi-Automatic “Overnight” Drain ...................................SA602A7 (Drains automatically under zero pressure)Filter Element Kits – 40 Micron (All) .....................................................................EK602B Repair Kits –Deflector, Baffle Assembly, and Retaining Rod (All) ..........RK602C External Auto Drain (All) .....................................................RK602D Internal Auto Drain (All) ...................................................RK602MD Metal Bowl Sight Gauge (W) ........................................RKB605WBSpecificationsBowl Capacity –Aluminum (E) .................................................................32 Ounces Zinc (W) ..........................................................................16 Ounces Port Threads .................................................................2, 2-1/2 Inch( ) = Bowl TypeFloat (Inside Bowl) Manual Push ButtonDrain(Outside Bowl)Drain (1/4" NPTF)Connection Through Bowl (1/8" NPSM)“Q” Option External Heavy Duty Auto Drain SA602D / SA603DFor heavy duty applications where the filter is being used to remove large volumes of liquid and/or particulate matter from the airstream, the external automatic drain (“Q” option) should be used.Pressure & Temperature Ratings –Aluminum Bowl (E) ............................0 to 300 PSIG (0 to 20.4 bar) 40°F to 150°F (4.4°C to 65.6°C) Zinc (W) ..............................................0 to 250 PSIG (0 to 17.2 bar) 40°F to 150°F (4.4°C to 65.6°C) With Internal Auto Drain (R) ..........20 to 175 PSIG (1.4 to 11.9 bar) 40°F to 125°F (4.4°C to 52°C) With External Auto Drain (Q) ............30 to 250 PSIG (0 to 17.2 bar) 40°F to 150°F (4.4°C to 65.6°C)Weight –Aluminum Bowl (E) .................................... 10.3 lb. (4.67 kg) / Unit 11 lb. (4.99 kg) / 1-Unit Master Pack Zinc Bowl (W) .............................................. 9.8 lb. (4.45 kg) / Unit 39 lb. (17.69 kg) / 4-Unit Master PackMaterials of ConstructionBody ....................................................................................Aluminum Bowls –(E) ...................................................Aluminum without Sight Gauge (W) ................................................................Zinc with Sight Gauge Drain –Manual Twist & Overnight .......................................................Brass Housing “R” ............................................................................Acetal Housing “Q” .........................................................................Bronze Filter Elements –40 Micron (Standard) ................................................Polypropylene Seals ........................................................................................Buna N Sight Gauge ...............................................................................Nylon2505007501000125012345Flow - SCFMP r e s s u r e D r o p - P S I GP r e s s u r e D r o p - b a r.1.2.3Primary Pressure - PSIG1.7 3.4 5.2 6.9Primary Pressure - bar 0240360480120Flow - dm n 3/s。
AT4202 04 08 多路温度测试仪用户手册说明书

用户手册User’s GuideAT4202/04/08多路温度测试仪Rev.B4固件说明:适用于主程序RevA2.0及以上的版本@Instruments常州安柏精密仪器有限公司.江苏省常州市钟楼区宝龙61-3层销售服务电子邮件: *****************技术支持电子邮件: ****************©2005-2015 Applent Instruments Ltd.AT4202/4204/4208 用户手册2声明根据国际版权法,未经常州安柏精密仪器有限公司(Applent Instruments Inc.)事先允许和书面同意,不得以任何形式复制本文内容。
安全信息为避免可能的电击和人身安全,请遵循以下指南进行操作。
免责声明用户在开始使用仪器前请仔细阅读以下安全信息,对于用户由于未遵守下列条款而造成的人身安全和财产损失,安柏仪器将不承担任何责任。
仪器接地 为防止电击危险,请连接好电源地线。
不可在爆炸性气体环境使用仪器不可在易燃易爆气体、蒸汽或多灰尘的环境下使用仪器。
在此类环境使用任何电子设备,都是对人身安全的冒险。
不可打开仪器外壳非专业维护人员不可打开仪器外壳,以试图维修仪器。
仪器在关机后一段时间内仍存在未释放干净的电荷,这可能对人身造成电击危险。
不要超出本说明书指定的方式使用仪器超出范围,仪器所提供的保护措施将失效。
警告:不要加直流电压或电流到测试端,否则会损坏仪器。
安全标志:设备由双重绝缘或加强绝缘保护废弃电气和电子设备 (WEEE) 指令 2002/96/EC切勿丢弃在垃圾桶内有限担保和责任范围 3有限担保和责任范围常州安柏精密仪器有限公司(以下简称Applent)保证您购买的每一台AT4202/4204/4208在质量和计量上都是完全合格的。
此项保证不包括保险丝以及因疏忽、误用、污染、意外或非正常状况使用造成的损坏。
本项保证仅适用于原购买者,并且不可转让。
自发货之日起,Applent提供玖拾(90)天保换和贰年免费保修,此保证也包括VFD或LCD。
HE17x Series USB Data Logger User Manual

1HE17x SeriesUSB Data Logger UserManualCONTENTSB Data Logger Hardware (3)1.1Introduction (3)1.2Features (3)1.3Application (3)1.4USB Data Logger Model (3)1.5USB Temperature Data Logger Appearance(HE170/HE171/HE172) (4)1.6USB Temperature Data Logger Screen(HE170/HE171/HE172) (4)1.7USB Temperature&Humidity Data Logger Appearance(HE173/HE174) (5)1.8USB Temperature&Humidity Data Logger Screen(HE173/HE174) (5)1.9Button (6)1.10Install Battery (6)1.11Fix USB Data Logger (6)Chapter2.Logpro Software (7)2.1The Requirement of the Computer Hardware (7)2.2Install Driver&Software (7)2.3Setting the logger’s properties to start a new measurement (8)2.4Properties Description (9)2.5Start record time description (10)2.6Download the Records after a Measurement (10)2.7Data Listing Window (12)2.8Exporting Logs from Logpro (12)2.9Delete Records in the Logger (13)2.10Check the Save File in File List (13)Chapter3.Attention (14)Chapter4.FAQ (14)4.1LCD Screen Dim (14)4.2Data&Time Error (14)4.3Software"Runtime Error" (14)4.4Check COM Port Number (14)B Data Logger Hardware1.1IntroductionHE170USB series has USB interface,enjoying elegant appearance and compact construction,specially designed for refrigerator and cold-chain transportation as well as container transport applications.HE170USB series adopts friendly USB interface,friendly mounting bracket and the screws.HE170USB series can show temperature/temperature and humidity simultaneously as well as the battery indication.The OK key can help to check the Max/Min/Current value and the upper and lower limits.1.2Features⏹Waterproof and dustproof standard IP67,resisting moisture and dust.⏹Can set temperature and humidity limit value and LED lights will flash when the valuebeing exceeded.⏹Lower consumption design,1/2AA3.6V Lithium battery,working for12months and easyto replace.(Logging Interval:600s)⏹Transfer logging data to PC through software and can be saved as different types toensure the existence.⏹Use high sensitivity sensor,fast reaction and high precision.⏹Size(L x H x D):126mm x34mm x28mm1.3ApplicationWildly use in cold chain Transportation,Containers.1.4USB Data Logger Model1.5USB Temperature Data Logger Appearance(HE170/HE171/HE172)8①LCD Screen⑥Battery Replacement Position.②Button⑦Waterproof Transparent Cover③LED Warming Light When the⑧Fixed BracketTemperature Value Exceeds SettingLimits.④USB Connection Port⑨Model Label⑤Waterproof Ring1.6USB Temperature Data Logger Screen(HE170/HE171/HE172)①Display the High Limit⑤Display the Maximum Value inRecords②Display the Low Limit⑥symbol display shows being thelogging status.③Battery power indication.⑦Temperature Value④Display the Minimum Value in⑧Temperature Unit(℃or℉)Records1.7USB Temperature&Humidity Data Logger Appearance(HE173/HE174)8①LCD Screen⑥Battery Replacement Position.②Button⑦Waterproof Transparent Cover③LED Warming light When the⑧Fixed BracketTemperature or Humidity ValueExceeds the Setting Limits.④USB Connection Port⑨Model Label⑤Waterproof Ring1.8USB Temperature&Humidity Data Logger Screen(HE173/HE174)①Display the High Limit⑤Battery power indication.②Display the Low Limit⑥Units symbol display℃or℉,%RH③Display the Maximum Value in⑦ValueRecords④Display the Minimum Value inRecords1.9ButtonOK Button1.Press this button for long to 5seconds can turn on/off the logger.2.Check the MAX;MIN;High &Low values as well as the current value in the working status.1.10Install Battery1.Open the Battery Cover2.Remove shell3.Install Battery1.11Fix USB Data Loggere Screw to Fix the Bracket onto the Wall.2.Install the Data Logger.Chapter 2.Logpro Software2.1The Requirement of the Computer Hardware1.OS:Windows2000/XP/Vista/Win7/Win8/Win10(32/64-bit ),nonsupport Linux/UnixOS.2.CPU:1.6GHz3.Physical Memory:512MB4.Hard-drive Space:4GBB Port:12.2Install Driver &Software1.Install DriverPut the assigned software disc into the computer driver and open the file tofindand select the driver based on the operating system.OS Win7/Win8/Win10-64select “CH341SER[64bit]”.OS Win XP;Vista;Win7-32select “CH341SER[32bit]”(1)Click 【CH341SER 】;(2)Click 【INSTALL 】—【Confirm】2.Install Logpro SoftwareNotice:Please Install Logpro Software inD:\2.3Setting the logger’s properties to start a new measurement.1.Connect the data logger to the computer.12.Running Logpro software on the PC.3.From the toolbar select Connect.24.Read the logger’s properties.5.Set the properties.6.Sync the properties &time.(The PC time will be synchronized to the logger as well.)7.From the toolbar select Disconnect8.Unplug the logger from the Computer,and then the logger is in Standby mode 3.9.Press OK button on the logger,turn on the Data Logger and start recording.1The windows operating system cannot handle USB devices being unplugged and plugged back too fast.When unplugging the logger,wait for about 5seconds before plugging it in again.If you unplug and plug back a device too quickly,the computer may stop recognizing any USB devices on that port.If this happens you will have to restart the computer.This is a windows USB problem and is not related to Logpro.2If more than one logger is connected to your computer at the same time,the program will ask you to choose COM port manually.3The logger has three modes:1.LOG:In the mode,the logger samples and records data timely.2.Standby:In the mode,the logger stops to sample and record,and the LCD display is OFF.3.OFF:In the mode,the logger stops to sample and record,and the LCD display is off.Logpro cannot connect to the logger also.654732.4Properties DescriptionProperty Text DescriptionName English letters orNumbersName of the loggerSN10Characters Must be the same as the one in the label oflogger.Sampling Interval(s)Number from1to240Sampling frequency in LCD screenLogging Interval(s)Number from2to86400Logging frequency.Logs The count of records in the memory.Capacity The total capacity of the logger’s storage. Temperature type℃The unit of temperature is centigrade℉The unit for Fahrenheit temperatureStart Mode Start Now Start log when the Logger was turn ON.Delay Start Wait Delay Time then start log.Timing Start Start log when Delay Time:HHMMSSe.g.170000means17:00:00Delay Time Input a Delay Time or Timing Time.High&Low Limit CH1:TemperatureCH2:Humidity When the value over the limit,the buzz will sounds and alarm.Offset4CH1:TemperatureCH2:Humidity Input positive number to decrease the value. Input negative number to increase the value.4Calibrate the logger:The logger is factory calibrated to an accuracy given in the device specifications.However, there may be times when you wish to adjust the calibration of your logger.Logpro provides you with the ability to perform a single point offset calibration.This calibration can be used to increase the accuracy of the logger for a restricted data range.2.5Start record time description1.Select the mode to start the record in the property bar:Start Now:the recorder starts immediately to record the data.Delay start:the recorder starts to record the data after the set delay time.Timing start:the recorder starts recording data at the specified time point.(Note:the recorder will start at the turn on state and the recorder will not start the record automatically when the logger at the turn off state).2,Entry delay time or timing time in the property bar.Start Now:the default is0.Delay start:fill in the delay time,the unit is second.For example,fill in120indicates that the instrument starts to record the data after turn on logger two minutesTiming start:fill in the timing time and fill in the format of HHMMSS.For example,fill180000 indicates that the instrument starts to record the data at6:00:00pm3,Synchronization property and time(The PC time will also be synchronized to the recorder).2.6Download the Records after a Measurement.10.Connect the data logger to a free USB port on the computer.11.Running Logpro software on the PC.12.From the toolbar select Connect.13.From the toolbar select Download1213Once the data is transferred from the logger to the PC,the data graph will be displayed.The graph display will be blank if there are not any logs.Tips:Press and hold the left mouse button to drag a box,when the left mouse button is released,the graph will be redraw with the data in the selected rectangle area(Magnified data table).Click right button,then the graph will be redrawing with all the data in thelogs file.2.7Data Listing WindowClick"Data List"button on the toolbar,and then the data listing window is shown below. Channel3unit is Dew Point.The Value is calculated from temperature&humidity.The data pane lists the data samples collected by the logging device.The column width of each column is adjustable by using the left mouse button and dragging the column the desired width.2.8Exporting Logs from Logpro●:Export data list to an Excel file.●:Export data list to a PDF file.●:Export graph to a BMP file.2.9Delete Records in the Logger14.From the toolbar select Delete 5142.10Check the Save File in File List15.From the toolbar select Filelist.616.Click to open the file.1516●Double click left mouse button,then the selected file is opened.●Click right mouse button,a popup menu is shown as below,you can rename or delete orlog file.●The save file is saved in the Logpro software’s installation path in the PC’s hard driver.5Clear the logger's memory.It will not affect downloaded file.6These files are located in the installed path of Logpro.Chapter3.Attention●HE17x water proof level is IP67.Do not put it into the water.●HE17x plastic shell is ABS,flame retardant,not resistant to acid and alkali.●If repair is needed,only authorized technician could do the repair.●The instrument configuration by1x ER14250lithium battery(3.7V)is not rechargeable.●USB power supply(5V)cannot let the Data Logger work.Chapter4.FAQ4.1LCD Screen DimReason:●Insufficient battery or the environment temperature is too low or too high.Solution:●In the case of insufficient battery,please replace the battery.If resulted from environmenttemperature,please immediately take the logger out of the environment.4.2Data&Time ErrorReason:●The battery level is low●The data logger is not synchronous properties,before start recording.Solution:●Replace the battery.●Please sync the properties,before start recording.4.3Software"Runtime Error"Reason:●OS forbid software creating files.Solution:●Run the program(software)as an administrator.●Install software in Disk D:\●A data logger name cannot contain any of the following characters:\/:*?"<>|●Software’s installation path cannot include Chinese character or garbage character.4.4Check COM Port Number●Press“Win”+“R”in keyboard->Run"devmgmt.msc"to Open"Device Manager"inWindows->Expand"Ports(COM&LPT)"->"USB-SERIAL CH340(COM No.)"is the Data Logger。
- 1、下载文档前请自行甄别文档内容的完整性,平台不提供额外的编辑、内容补充、找答案等附加服务。
- 2、"仅部分预览"的文档,不可在线预览部分如存在完整性等问题,可反馈申请退款(可完整预览的文档不适用该条件!)。
- 3、如文档侵犯您的权益,请联系客服反馈,我们会尽快为您处理(人工客服工作时间:9:00-18:30)。
Shipping InfoUnpacking and InspectionYou should inspect your granulator for possible shipping damage.Thoroughly check the equipment for any damage that might have occurred in transit, such asbroken or loose wiring and components, loose hardware and mounting screws, etc.In the Event of Shipping DamageAccording to the contract terms and conditions of the Carrier, the responsibility of theShipper ends at the time and place of shipment.Notify the transportation company’s local agent if you discover damage.Hold the damaged goods and packing material for the examining agent’s inspection. Do notreturn any goods before the transportation company’s inspection and authorization.File a claim with the transportation company. Substantiate the claim by referring to theagent’s report. A certified copy of our invoice is available upon request. The original Bill ofLading is attached to our original invoice. If the shipment was prepaid, write us for areceipted transportation bill.Advise customer service regarding your wish for assistance and to obtain an RMA (returnmaterial authorization) number.If the Shipment is Not CompleteCheck the packing list as back-ordered items are noted on the packing list. You should have:˛Granulator˛Bill of lading˛Packing list˛Operating and Installation packet˛Electrical schematic and panel layout drawings˛Component instruction manualsRe-inspect the container and packing material to see if you missed any smaller items duringunpacking.If the Shipment is Not CorrectIf the shipment is not what you ordered, contact the shipping department immediately. Forshipments in the United States and Canada, call 1 (800) 229-2919; for all other countries, callour international desk at (508) 399-6400. Have the order number and item number available.Hold the items until you receive shipping instructions.ReturnsDo not return any damaged or incorrect items until you receive shipping instructions from theshipping department.Table of ContentsCHAPTER 1:SAFETY (5)1-1How to Use This Manual (5)Safety Symbols Used in this Manual (5)1-2General Safety Regulations (6)1-3Responsibility (6)1-4Warnings and Precautions (7)CHAPTER 2:FUNCTIONAL DESCRIPTION (9)2-1Models Covered in This Manual (9)2-2General Description (9)2-3Typical Features and Components (10)Hopper (10)Cutting Chamber (10)Drive System (10)Discharge System (10)Base (10)2-4Safety Features (11)Motor Starter (11)Safety Switches (11)Safety Tags (11)Brake Motors (Optional) (11)Sound Reduction Equipment (11)CHAPTER 3:INSTALLATION (12)3-1Uncrating the Equipment (12)3-2Belt Tensioning (12)3-3Electrical Connections (13)3-4Accessing the Cutting Chamber (14)3-5Closing the Cutting Chamber (14)3-6Initial Start-up (15)CHAPTER 4:OPERATION (16)4-1Start-up (16)4-2Feeding the Granulator (16)4-3Clearing a Jammed Cutting Chamber (16)4-4Shut-down (17)CHAPTER 5:MAINTENANCE (18)5-1Preventative Maintenance Schedule (18)5-2Lubrication (19)New Bearings (19)Re-Lubrication (19)5-3Replacing and Adjusting the Knives (20)Rotor Knives (20)Bed Knives (21)5-4Sharpening the Knives (21)5-5Adjusting Belt Tension (22)5-6Rotor Bearing Replacement (23)CHAPTER 6:TROUBLESHOOTING (24)6-1Introduction (24)6-2Electrical Faults (25)6-3Processing Faults (26)6-4Mechanical Faults (27)CHAPTER 7:APPENDIX (28)7-1Customer Satisfaction Warranty Program (28)7-2Recommended Torque for Screws (29)7-3Technical Specifications (30)Features (30)Specifications (30)Dimensions (31)7-4Recommended Spare Parts (32)37 B Model (32)7-5Technical Assistance (33)Parts Department (33)Service Department (33)Sales Department (33)Chapter 1: S afety1-1 How to Use This ManualUse this manual as a guide and reference for installing, operating, and maintaining yourgranulator. The purpose is to assist you in applying efficient, proven techniques that enhanceequipment productivity.This manual covers only light corrective maintenance. No other maintenance should beundertaken without first contacting a service engineer.The Functional Description section outlines models covered, standard features, and safetyfeatures. Additional sections within the manual provide instructions for installation, pre-operational procedures, operation, preventive maintenance, and corrective maintenance.The Installation chapter includes required data for receiving, unpacking, inspecting, and setupof the granulator. We can also provide the assistance of a factory-trained technician to helptrain your operator(s) for a nominal charge. This section includes instructions, checks, andadjustments that should be followed before commencing with operation of the granulator.These instructions are intended to supplement standard shop procedures performed at shift,daily, and weekly intervals.The Operation chapter includes a description of electrical and mechanical controls, inaddition to information for operating the granulator safely and efficiently.The Maintenance chapter is intended to serve as a source of detailed assembly anddisassembly instructions for those areas of the equipment requiring service. Preventivemaintenance sections are included to ensure that your granulator provides excellent, longservice.The Troubleshooting chapter serves as a guide for identification of most common problems.Potential problems are listed, along with possible causes and related solutions.The Appendix contains technical specifications, drawings, schematics, parts lists, andavailable options. A spare parts list with part numbers specific to your machine is providedwith your shipping paperwork package. Refer to this section for a listing of spare parts forpurchase. Have your serial number and model number ready when ordering.Safety Symbols Used in this ManualThe following safety alert symbols are used to alert you to potential personal injury hazards.Obey all safety messages that follow these symbols to avoid possible injury or death.DANGER! DANGER indicates an imminently hazardous situation that, if not avoided,will result in death or serious injury.WARNING! WARNING indicates a potentially hazardous situation or practice that, ifnot avoided, could result in death or serious injury.Caution! CAUTION indicates a potentially hazardous situation or practice that, ifnot avoided, may result in minor or moderate injury or in property damage.1-2 General Safety RegulationsThis machine uses knives for the performance of its intended use. Consequently, it can be adangerous machine to operate and maintain unless these safety regulations are followed.These regulations should be read, understood, and periodically reviewed by all personnelinvolved in any way with this machine.Never operate or remove any machine components that are secured by wrench-type fasteners unless the motor is electrically locked out and the rotor is motionless.Never operate the machine or jog the rotor unless the cutting chamber covers, dischargechute, or any guards or covers are in place and secure. Do not circumvent the safetyinterlocks.Prior to clearing a jam or performing any maintenance, the motor should be turned off andelectrically locked out. Be sure that the rotor has come to a stop. Hands must not be inserted into the machine to clear the jam.Do not extend any part of the body into feed roll openings or discharge area unless the motors are electrically locked out and the rotor and feed rolls are motionless.Never extend fingers through holes in screen.Be sure that the v-belts are properly aligned and that tension is at its maximum.Extreme care should be taken to see that all bolts are properly tightened at all times. Duringthe operation of the machine, rotor knife bolts may come loose. Although fine threads areused on the rotor knife bolts because vibration does not easily loosen them, you shouldinspect the tightness of the bolts frequently.This machine is designed for the granulation of plastic materials. Do not feed any othermaterials into the machine.1-3 ResponsibilityThese machines are constructed for maximum operator safety when used under standardoperating conditions and when recommended instructions are followed in the maintenanceand operation of the machine.All personnel engaged in the use of the machine should become familiar with its operation as described in this manual.Proper operation of the machine promotes safety for the operator and all workers in itsvicinity.Becoming familiar with materials, inspection, speed limitations, screens, and guardmaintenance and total user responsibility will assist you in learning potential areas in need of observation for danger.Each individual must take responsibility for observing the prescribed safety rules as outlined.All caution, warning and danger signs must be observed and obeyed. All actual or potentialdanger areas must be reported to your immediate supervisor.1-4 Warnings and PrecautionsOur granulators are designed to provide safe and reliable operation when installed andoperated within design specifications, following national and local safety codes.To avoid possible personal injury or equipment damage when installing, operating, ormaintaining this granulator, use good judgment and follow these safe practices:˛LEARN AND OBEY your company’s safety policy regarding granulatingequipment.˛MOVING OR LIFTING THE GRANULATOR: Although our equipment is built and engineered for great ruggedness in operation, care must be taken when movingthe machine along the floor or lifting it. Damage may occur to sheet metal covers,electrical cabinets, or small brackets if pressure is applied to them when moving thegranulator. When lifting the granulator, be certain of total machine weight and thecapability of the lifting equipment. (See the Granulator Specification Sheets formachine weights and dimensions.)˛GRANULATOR LOCATION: Adequate area for routine maintenance should be provided in order to open the machine for knife, screen, or cleanout service. Properservice area clearances also should allow people who are working on the machine tobe clearly visible to others, thereby reducing the potential safety hazards.˛SAFE HOUSEKEEPING: The work area must be kept clean and uncluttered during periods of operation or maintenance. No hand tools or other metal objects should beleft on or around the machine. Any tools or other metal objects that mistakenly fallinto the hopper feed opening can cause severe damage to internal cutting chamber,rotor and screen components.˛SAFETY GLASSES OR A FACE SHIELD MUST ALWAYS BE WORN when servicing or operating the machine. Although our machines are designed for themaximum in flyback control, caution must be used when operating near the hopperfeed opening in order to guard against unexpected material flyback.˛EAR PROTECTION may be required when operating the machine duringgranulation of very hard or noisy materials. The Occupational Safety and Health Actof 1970 has established guidelines for Permissible Noise Exposures (OSHA 1910.95)that should be followed.˛NEVER attempt to operate the granulator unless it is fully assembled with all guards and interlocks in place and functional.˛OBSERVE all danger, warning, caution and safety labels on the equipment.˛Upon completion of any machine maintenance, be certain ALL SAFETY GUARDS AND COVERS are securely and properly fastened prior to resuming machineoperation. All fasteners must be in place and properly tightened. ANYSHORTCUTS MAY RESULT IN INJURY TO PERSONNEL OR DAMAGETO EQUIPMENT.˛NEVER wear any loose fitting clothes, neckties, or dangling items such as earrings, belts, or shoestrings. Jewelry, such as wristwatches, bracelets, or rings shouldNEVER be worn. Long hair must be tied back or placed in a tight fitting hairnet.NEVER lean against or rest hands or feet on the granulator when it is in operation oropen for maintenance. NEVER stand on the granulator when it is in operation.˛ROTATION OF MOTORS: The correct rotating direction for the granulator motor is clearly marked on the machine. Always check for proper rotation of motors.Incorrect rotation direction can cause severe damage.˛ELECTRICAL GROUNDING: All electrical equipment on the granulator must be grounded in accordance to all local codes and Article 250 of the National ElectricCode.˛ALWAYS DISCONNECT AND LOCKOUT the main electrical power to the granulator before performing any service.˛SAFETY INTERLOCKS MUST NOT BE BYPASSED. The mechanical and electrical safety interlocks ensure the safety of personnel. They should never betampered with or removed for ANY reason. They should be checked frequently by a qualified mechanic for proper operation.˛NEVER modify the machine configuration or any individual component without written notice from the factory.For further information on granulator safety, installation, and operation, see the American National Standard for Plastics MachineryæGranulators, Pelletizers, and Dicers Used for Size Reduction of PlasticsæConstruction, Care, and Use. ANSI B151.11-1982.We have long recognized the importance of safety and have designed and manufactured our equipment with operator safety as a prime consideration. We expect you, as a user, to abide by the foregoing recommendations in order to make operator safety a reality.2-3 Typical Features and ComponentsHopperThe hopper is an upright enclosure bolted to the top of the cutting chamber. The hopper isdesigned to facilitate feeding of material to the rotary knives and to prevent chips thrownfrom the cutting chamber from reaching the operator.Cutting ChamberThe cutting chamber is a rectangular enclosure comprising the main frame, the bed knives,the bed knife shields, a balanced rotor, and a screen.The main frame of the cutting chamber carries the bed knives and the bed knife shields*. Thedownstroke bed knife shield is adjustable.The screen is supported in position below rotor and acts as a separating barrier to thegranulated material, retaining the material in the cutting chamber until the particle size is suchthat it will pass through the screen holes.The rotor carries the rotor knives. The rotation of the rotor produces a cutting action betweenthe rotor knives and the stationary bed knives, thus reducing the material size.Drive SystemThe rotor is indirectly driven by the motor through v-belts. The motor shaft pulley, v-belts,and the rotor shaft pulley are shielded by safety guards or sound enclosure.The motor is mounted on an adjustable sliding base, which is mounted at the left end of thegranulator.Discharge SystemThe granulated material that falls through the screen is collected by the customer’s Gaylordbox.On models fitted with an airveying system (optional), the granulated material that has fallenthrough the screen is collected in a transition piece located beneath the cutting chamber. Thetransition piece is connected to a blower, which conveys the granulated material throughducting to the cyclone separator. The cyclone separator allows the granulated material to dropout of the air system into a container.BaseThe base is a floor mounted drum and gaylord type supporting the cutting chamber on its topsurface and the gaylord chute from below the top surface. This base should be fastenedsecurely to the surface beneath it.* H Series, helical hog models do not have downstroke bed knife shields.2-4 Safety FeaturesMotor StarterA magnetic motor starter with control transformer must be used when safety switches areinstalled. Manual starters should not be used under any conditions.Safety SwitchesSafety switches at all access covers are wired into the starter control circuit. The machinecannot be started when these parts are open. However, for safety purposes, the machineshould be disconnected from the power lines by a disconnect switch or by removing the plug from its receptacle. Check all safety switches periodically for proper operation.Safety TagsA set of metal plates is attached to the machine to warn of potential danger.Brake Motors (Optional)An integral brake stops the motor within a few seconds of actuation of the stop button, greatly reducing the time required for the rotor to stop.Sound Reduction EquipmentSound reduction equipment will bring the sound level of your machine to within thelimitations of the Occupational Safety and Health Act. Material, part configuration, feed rate, and ambient noise level must be specified at the time of inquiry.Chapter 3: I nstallation3-1 Uncrating the EquipmentThe complete granulator, including accessory and auxiliary equipment, is skidded forshipment. Refer to the Appendix for detailed dimensional data and pertinent weights.Prepare in advance the site you have selected for installation of the granulator. Be certainthat the area to be occupied by the machine is clean, level, and free of obstructions. Themachine should be set on a concrete floor, and care must be taken when moving the machineacross a hollow timber floor, so that the point loading of the casters does not cause damage.The site you have selected must have a floor rating to adequately support the weight of themachine. If necessary, use steel shims to level the machine.Locate the machine so that access is given to electrical components, screen, and hopper.Maintenance personnel should have unobstructed access to the units on which they will beworking.To avoid squeezing people working near a machine, there should be adequate clearancemaintained between machines, walls, or partitions. Hinged doors and covers should have fullswing. Restrictions may force work in cramped quarters. An off-balance operator with anawkward reach into a partially obscured area is unsafe.If inspection after shipment has revealed no shipping damage, unpack the unit by removingall hold-downs, tie-downs, bolts, nuts, etc. Remove the envelope with the electricalschematics and instruction manual from the base evacuation area.You can now have the machine lifted from the skid. To lift and move the granulator safelyand correctly, cover any sharp corners or edges, and use the type of equipment that has themost appropriate features and capacity. Use the designated lifting points, and do NOT lift themachine by the hopper handles or guards.Caution! Because of the size and weight of the granulator, we recommend that onlyqualified riggers be employed to unpack and locate the granulator.3-2 Belt TensioningTension the belts at the maximum recommended force. Check the tension at least twiceduring the first day of operation. See Section 5-5 on page 22 for the belt tensioningprocedure.3-3 Electrical ConnectionsGranulator controls (if ordered) are shipped separately for mounting at a suitable location.The safety switches are connected to a common terminal box for ease of wiring. Thecustomer is required to provide a suitable fused supply with a disconnect switch and a cablefor the incoming line to the starter.Refer to the technical specifications in the Appendix for horsepower, voltage, phase, andfrequency requirements to determine the size and rating of the supply cable required.If optional controls are required, an electrical wiring diagram will be provided with themachine in addition to the basic electrical diagram.When the customer is providing either the motor or the starter, the machine must be wired in accordance with the basic electrical diagram and the starter manufacturer’s instructions.Use the following procedure to complete the electrical connections:1.Check to be certain that the starter heater elements correspond with the motorrequirements. If controls are not supplied, the limit switches supplied on the machinemust be wired into the circuit at the common terminal box.2.Check that the limit switches are closed.3.Turn switch ON at main power supply.4.Jog motor by pressing the START and then the OFF button. This starts and stops themotor.5.With the electrical power ON, check that the motor rotates in a clockwise direction atthe viewing port in the belt guard. If motor rotation is correct, continue to the nextstep. If rotation is incorrect, complete the following procedure:a.Shut power OFF and disconnect incoming power supply.b.Reverse any two of the three power line connections to the machine.c.Re-connect the incoming power supply line and turn ON the main powerswitch to recheck motor drive rotation.6.If Airveying system (optional) is fitted, press the Airveyor START button, and checkthe blower motor rotation. The blower motor should rotate in a counterclockwisedirection. If blower motor rotation is correct, continue to step 7. If blower motorrotation is incorrect, complete the following procedure:a.Shut power OFF and disconnect incoming power supply line.b.Reverse any two of the three power line connections to the blower motor.c.Re-connect the incoming power supply line, and recheck the blower motorrotation.7.Allow all motors to run up to speed for at least 30 seconds.3-4 Accessing the Cutting ChamberYou will need to access the cutting chamber before initial startup and for variousmaintenance procedures. Use the following procedure to access the cutting chamber:1.Turn the main power off, remove the line fuses, and tag the machine as out ofservice.2.Remove the hex head bolts along the top of the cutting chamber covers.3.Swing the covers downward using the handles that are provided on each cover. Donot allow the covers to drop freely of their own weight.4.Remove the two screws holding the screen closure on the end of the machineopposite the drive, and remove the screen through the curved slot in the end plat.Note:It may be necessary to back out the screws that hold the screen down on the screen supports, along the sides of the machine.3-5 Closing the Cutting ChamberAfter completing any maintenance or adjustments inside the cutting chamber, use thefollowing procedure to close the cutting chamber and resume use of the granulator:1.Replace the screen and the screws holding the screen closure on the end of themachine.2.Swing the cutting chamber doors back into their closed position and replace bolts.3.Rotate the rotor by hand from outside the machine to check that no tools, gauges, orloose parts have been left on or in the machine.4.Replace line fuses, turn power on, and remove the out of service tag from themachine.3-6 Initial Start-upThis machine has been run under power and tested at the factory prior to shipment. Thenecessary settings and adjustments have been made so that a minimum amount of setting upor re-adjustment is required when starting up the machine in its new location.With all electrical, mechanical connections and lubrication requirements having beenattended to, the following start-up steps should be carefully carried out before attempting toplace any material into the infeed hopper. Use the following procedure to prepare themachine for initial start-up:WARNING! Before operating the granulator, insure that the granulator has beencorrectly assembled and wired.1.Access the cutting chamber as described in Section 3-4 on page 14.2.Thoroughly clean the rust preventative materials or grease from the inside of thecutting chamber and screen.3.Check all rotor knives to make sure they are properly seated on the rotor and securelyfastened. Although they are ground as a set, one knife will probably be .001” to .002”higher than the others. This should be marked and used when adjusting the bedknives for proper clearance.e a feeler gauge to check the clearance between the rotor and the bed knives byturning the rotor backwards. Rotating the rotor backwards gives a better feel and doesnot cut the gauge, should the knives be too close. Check the knives on each end only.Proper clearance is 0.005” to 0.008” for most materials; 0.014” to 0.016” for solidwall pipe with 0.187” wall thickness or greater. This clearance is slightly greater atthe center of the knives.Note:Recheck knife clearance after the first 24 to 36 hours of operation.5.To make the adjustment on the bed knives, the bed knife bolts should be handtightened to hold the knife firmly against the knife seat while adjusting the knifeforward using push and pull screws. After the clearance is set, torque the screwsaccording to Section 7-2 on page 29.6.With the exposed parts of the machine thoroughly clean, and all knife clamping boltssecurely fastened, close the cutting chamber as described in Section 3-5 on page 14.Note:After initial start-up, the rotor knife retaining screws should be checked after 8 hours running to be assured that the proper torque is maintained. Thereafter,rotor knife retaining screws should be checked weekly.Note:The rotor must be rotated at least two rotations every 30 days to preventbrinnelling and corrosion of raceways.Chapter 4: O peration4-1 Start-upBefore starting the machine, check that the rotor rotates freely by rotating it by hand fromoutside the machine using either the coupling or the sheave depending on the type of drive.Inspect the cutting chamber carefully to insure that nothing has fallen into it. Make sure allscrews and bolts are properly secured. Check all electrical connections and motor rotations.See Chapter 3 on pages 12-15 for detailed set-up instructions. Allow all motors to run up tospeed for at least 30 seconds.4-2 Feeding the GranulatorFeed the granulator through the opening in the hopper. The method of feeding the granulatordepends on the physical form and nature of the material being processed.For maximum efficiency, the granulator should be fed at a rate that is consistent with itscapacity; i.e., if the granulator is rated at 3000 lbs./hr. (1360 Kg/hr.), then the general feedrate is 50 lbs./min (23 Kg/min.). Under these operating conditions, the correct proportions ofcut and uncut particles will be present in the cutting chamber.WARNING! Under no circumstances should the operator attempt to reach into thehopper to dislodge any bridged or jammed material while the granulator isin operation. To clear the hopper of bridged or jammed material, themachine main power must be turned off and the machine isolated.4-3 Clearing a Jammed Cutting ChamberNever attempt to free a jammed machine by placing hands on the rotor, rotor knives, or insidethe cutting chamber. Hands must be kept clear of the rotational path of the rotor knives.Good footing on a clean floor is essential and the body should be well braced to guard againstloss of balance should the jam suddenly come free. Use the following procedure to clear ajammed cutting chamber:1.Disconnect and lock out power.2.Be certain that the rotor is motionless.3.Open the machine as instructed in Section 3-4 on page 14.e a pry bar to exert force on the rotor, usually in the direction opposite normalrotation. A leather mallet and a block of wood of sufficient length to keep handsaway from path of knives can be used if necessary.e pliers to remove material from the cutting chamber, keeping in mind that theremoval of material may cause rotation of the rotor and rotor knives.6.After clearing the jam, be certain that the screen and all guards and covers aresecured in place before connecting power and starting the machine.。