低温余热发电技术
低温余热发电技术简介

-1,000
Time / min
Steam Flow Rate Steam For Generation Steam in/from Accumulator
蒸汽负荷平衡图
低温余热的基本概念
Consideration
EAF
低温余热发电技术简介
余热发电原理
余热发电原理
Rankine Cycle
烧结厂5MW低温余热电站
余热资源基础条件
序号 名称 低温热源成分 N2 空气组成 1 O2 H2O 成分 灰分 含量 平均粒径 烟气流量 烟气进口温度 符号 / / / / / / / Vg tgi / g/Nm3 μm Nm3/h ℃ Vol.% 单位 / 数 据 空气 78 21 1 铁矿石烧结熟料 3 100 150,000 368
650
HT
MT 350~650℃ LT <350℃
350
MT
LT
低温余热的基本概念
Location
烧结生产线 在烧结生产过程中,烧制好的成品温度在500~800℃ ,为了便于运输需将其冷却至常温。烧制好的成品的显热 ,在冷却的过程中随热空气(300~350℃)排放到大 气中,此热空气的流量很大,极具回收价值,是低温余热 发电良好的余热资源。 炼铁 炼铁高炉产生温度高于80℃冲渣循环热水,利用热水的 热量,通过复合闪蒸补汽式纯低温余热发电技术也可以进 行低温余热发电 。
Consideration
350 300 250 200 150 100 50 0 1 3 5 137 122
EAF
304.234 264.941 188.640 153.052 84.121 133
有机朗肯循环低温余热发电系统综述

有机朗肯循环低温余热发电系统综述引言在工业生产过程中,大量的热能会以余热的形式排放到环境中,造成了能源的浪费。
这些废热也可能对环境造成影响。
利用余热进行发电,不仅可以提高能源利用效率,还可以减少对环境的影响。
有机朗肯循环低温余热发电系统正是一种利用余热发电的新型技术,本文将就有机朗肯循环低温余热发电系统的原理、特点、应用及发展前景进行综述。
一、有机朗肯循环低温余热发电系统的原理有机朗肯循环低温余热发电系统是利用有机朗肯循环技术,将低温余热转化为电能的一种系统。
其原理是利用有机朗肯循环工质和低温热源之间的温差来驱动发电机发电。
有机朗肯循环是将有机工质置于一个封闭的循环系统内,利用热能的输入和排出来驱动涡轮机进行发电的一种循环系统。
当有机工质受热使得蒸汽压升高时,蒸汽压推动涡轮机工作,从而带动发电机发电;而在冷凝器中,有机工质又被冷却再次变成液态,完成循环。
有机朗肯循环低温余热发电系统是通过这样一个闭合的循环系统,将低温余热转化为电能。
二、有机朗肯循环低温余热发电系统的特点1. 低温工作:有机朗肯循环低温余热发电系统的工作温度低,通常在100°C以下。
这使得这种系统可以有效利用那些传统热能利用技术无法利用的低品位热能资源,如煤矿瓦斯、生活污水、工业废热等。
2. 环保高效:有机朗肯循环低温余热发电系统的工作过程无需核心机械设备如大型锅炉或锅炉,排放的废气和废水相对较少,具有较高的环保性。
由于其低温工作特点,利用的低品位热能资源不会与食品、药品等高温生产过程相冲突,环保性较好。
3. 经济效益:有机朗肯循环低温余热发电系统具有投资少、成本低、回收期短等特点,从经济角度来看很有吸引力。
4. 可操作性强:有机朗肯循环低温余热发电系统的操作比较简便,不需要特别复杂的操作程序,管理维护成本低。
三、有机朗肯循环低温余热发电系统的应用有机朗肯循环低温余热发电系统已经在多个领域得到了应用,主要包括以下几个方面:1. 电厂余热利用:在电厂生产过程中,通常会有大量的低温余热排放,有机朗肯循环低温余热发电系统可以有效地利用这些余热进行发电,提高能源利用效率。
ORC低温余热发电技术
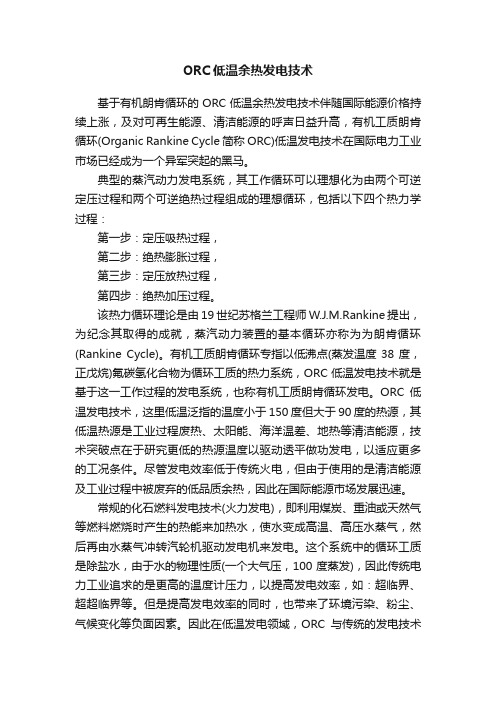
ORC低温余热发电技术基于有机朗肯循环的ORC低温余热发电技术伴随国际能源价格持续上涨,及对可再生能源、清洁能源的呼声日益升高,有机工质朗肯循环(Organic Rankine Cycle简称ORC)低温发电技术在国际电力工业市场已经成为一个异军突起的黑马。
典型的蒸汽动力发电系统,其工作循环可以理想化为由两个可逆定压过程和两个可逆绝热过程组成的理想循环,包括以下四个热力学过程:第一步:定压吸热过程,第二步:绝热膨胀过程,第三步:定压放热过程,第四步:绝热加压过程。
该热力循环理论是由19世纪苏格兰工程师W.J.M.Rankine提出,为纪念其取得的成就,蒸汽动力装置的基本循环亦称为为朗肯循环(Rankine Cycle)。
有机工质朗肯循环专指以低沸点(蒸发温度38度,正戊烷)氟碳氢化合物为循环工质的热力系统,ORC低温发电技术就是基于这一工作过程的发电系统,也称有机工质朗肯循环发电。
ORC低温发电技术,这里低温泛指的温度小于150度但大于90度的热源,其低温热源是工业过程废热、太阳能、海洋温差、地热等清洁能源,技术突破点在于研究更低的热源温度以驱动透平做功发电,以适应更多的工况条件。
尽管发电效率低于传统火电,但由于使用的是清洁能源及工业过程中被废弃的低品质余热,因此在国际能源市场发展迅速。
常规的化石燃料发电技术(火力发电),即利用煤炭、重油或天然气等燃料燃烧时产生的热能来加热水,使水变成高温、高压水蒸气,然后再由水蒸气冲转汽轮机驱动发电机来发电。
这个系统中的循环工质是除盐水,由于水的物理性质(一个大气压,100度蒸发),因此传统电力工业追求的是更高的温度计压力,以提高发电效率,如:超临界、超超临界等。
但是提高发电效率的同时,也带来了环境污染、粉尘、气候变化等负面因素。
因此在低温发电领域,ORC与传统的发电技术相比,具备以下几个优势:1)有机工质具有良好的热力学性质,低的沸点及高的蒸气压力使0RC方法比水蒸气朗肯循环具有较高的热效率,对较低温度热源的利用有更高的效率。
低温余热发电技术简介

第一代余热发电技术定义及特征
1.水泥窑第一代纯低温余热发电技术:在不
影响水泥熟料产量、质量,不降低水泥窑运 转率,不改变水泥生产工艺流程、设备,不 增加熟料电耗和热耗的前提下,采用 0.69MPa~1.27MPa——280℃~340℃整齐将 水泥窑窑尾预热器排出的350℃以下废气余热, 窑头熟料冷却机排出的350℃以下废气余热转 化为电能的技术。
(3) 合适的汽包工作压力。考虑在换热过程中,蒸发 受热面内汽水混合物的温度不变,而烟气同汽水混合物 之间传热温差窄点在20℃以上受热面的布置才合理,汽 水混合物的温度直接受压力的影响,所以选择合理的压 力水平为受热面布置创造条件,以防止锅炉造价过高。 (4) 充分降低废气温度。受窑尾废气要用于烘干生料 的工艺限制,一般窑尾废气温度只能降至225℃左右; 窑头余风可以充分降低,但降低过多则造成传热温差小 使得换热面积布置过多,使锅炉造价提高,同时吸收过 多的低品质热量也无法有效提高发电量,所以窑头余风 的降低以满足为窑头和窑尾余热锅炉提供足量的汽包给 水即可。根据热量分配和能量平衡计算,窑头余风降至 96~98℃即可满足要求。 (5) 合理布置受热面。在布置受热面时要考虑窑尾、 窑头的烟气温度特性以及汽轮发电机的特性进行综合考 虑,同时考虑选用合理温差以降低锅炉造价。
第三代系统特点
将窑头冷却机余风进行梯级利用,原中部抽
风口改为两个抽风口,一个为高温480-500℃, 一个为中温330-380℃。高温风将来自窑头窑 尾余热锅炉的低温过热蒸汽进一步提高到 430℃左右,该工艺较第一代系统提高余热发 电量15-20%左右。
中国第二代水泥窑纯低温余热发电技 术与发达国家先进技术的比较
谢谢观赏
WPS Office
ORC低温余热发电技术
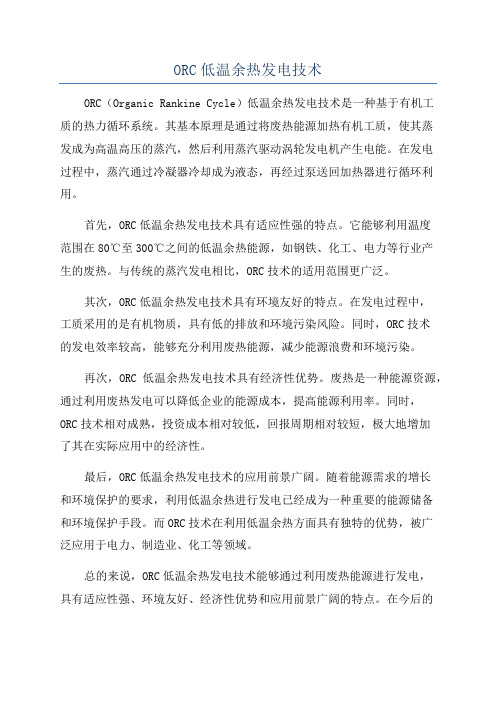
ORC低温余热发电技术ORC(Organic Rankine Cycle)低温余热发电技术是一种基于有机工质的热力循环系统。
其基本原理是通过将废热能源加热有机工质,使其蒸发成为高温高压的蒸汽,然后利用蒸汽驱动涡轮发电机产生电能。
在发电过程中,蒸汽通过冷凝器冷却成为液态,再经过泵送回加热器进行循环利用。
首先,ORC低温余热发电技术具有适应性强的特点。
它能够利用温度范围在80℃至300℃之间的低温余热能源,如钢铁、化工、电力等行业产生的废热。
与传统的蒸汽发电相比,ORC技术的适用范围更广泛。
其次,ORC低温余热发电技术具有环境友好的特点。
在发电过程中,工质采用的是有机物质,具有低的排放和环境污染风险。
同时,ORC技术的发电效率较高,能够充分利用废热能源,减少能源浪费和环境污染。
再次,ORC低温余热发电技术具有经济性优势。
废热是一种能源资源,通过利用废热发电可以降低企业的能源成本,提高能源利用率。
同时,ORC技术相对成熟,投资成本相对较低,回报周期相对较短,极大地增加了其在实际应用中的经济性。
最后,ORC低温余热发电技术的应用前景广阔。
随着能源需求的增长和环境保护的要求,利用低温余热进行发电已经成为一种重要的能源储备和环境保护手段。
而ORC技术在利用低温余热方面具有独特的优势,被广泛应用于电力、制造业、化工等领域。
总的来说,ORC低温余热发电技术能够通过利用废热能源进行发电,具有适应性强、环境友好、经济性优势和应用前景广阔的特点。
在今后的发展中,随着技术进步和应用范围的拓宽,ORC低温余热发电技术有望在能源行业产生更大的社会经济效益。
火力发电厂烟气低温余热利用技术

火力发电厂烟气低温余热利用技术火力发电厂烟气低温余热利用技术1. 简介火力发电厂是一种利用燃煤、燃油或天然气等化石燃料燃烧产生高温烟气,通过锅炉转化为蒸汽,最终驱动汽轮发电机发电的设备。
在这个过程中,发电厂往往会产生大量的废热,其中包括烟气中的低温余热。
如何有效利用这些低温余热成为了一项重要的技术挑战和发展方向。
2. 烟气低温余热的特点和现状烟气低温余热一般指的是温度在150℃以下的废热,由于温度较低,传统的蒸汽循环发电技术无法高效利用。
在很长时间内,烟气低温余热往往被直接排放或仅仅用于供热等低效能领域,导致能源的浪费和环境的污染。
3. 烟气低温余热利用技术的发展随着能源需求的增长和环境保护的要求,烟气低温余热利用技术得到了广泛关注和研发。
目前,有以下几种常见的烟气低温余热利用技术:3.1 烟气余热锅炉烟气余热锅炉是将烟气中的低温余热通过锅炉进行回收,产生高温高压蒸汽用于发电或供热。
利用烟气余热锅炉可以将废热转化为有用热能的同时减少对燃料的需求,实现能源和环保的双重效益。
3.2 烟气余热汽轮发电烟气余热汽轮发电是利用烟气中的低温余热直接驱动汽轮机发电。
相比于烟气余热锅炉,这种技术更加高效,能够直接将低温余热转化为动力能源,提高能源利用效率。
3.3 烟气废热换热器烟气废热换热器是在烟气管道中设置换热器,通过与其他介质的热交换,将烟气中的余热传递给其他工艺流体,如空气、水等。
这种技术可以将烟气中的低温余热有效利用,并用于加热或提供热水、热风等需求。
4. 烟气低温余热利用技术的优势和应用烟气低温余热利用技术具有以下几个优点:4.1 节能减排:有效利用废热可以减少对化石燃料的需求,降低能源消耗,减少二氧化碳等温室气体的排放。
4.2 综合利用:烟气低温余热可用于发电、供热、工业生产等多个领域,实现能源的综合利用和优化配置。
4.3 环境友好:废热的充分利用有助于减少大气污染物的排放,改善环境质量。
烟气低温余热利用技术的应用非常广泛,包括钢铁、化工、建材、石油等行业,以及供热和发电领域。
纯低温余热发电技术

Page 23
b、窑尾预热器方面,最重要的改变是利用G级预 热器内筒设置过热器,利用450-600℃废气产生过 热蒸汽。在蒸汽参数达到预定目标时,G级预热 器进口废气温度仅降低20-25℃,这种变化是水泥 生产所允许的变化范围。
c、为了提高窑头熟料冷却机废气余热回收率,窑头 熟料冷却机冷却风采用循环风方式,即将窑头AQC 炉出口废气部分或全部返回冷却机。
Page 13
Page 14
双压技术是根据水泥窑废气余热的品位的 不同, 余热锅炉分别生产较高压力和较低压力 的两路蒸汽。较高压力的蒸汽作为主蒸汽进入 汽轮机主进汽口推动汽轮机转动作功发电。余 热锅炉生产出较高压力的蒸汽后, 烟气温度降 低, 余热品位下降,那么根据低温烟气的品位, 再生产较低压力的低压进汽, 进入汽轮机的低 压进汽口, 辅助主蒸汽一起推动汽轮机作功发 电。
4、发电机,国内采用空冷式发电机;国外 也是。
Page 22
第二代纯低温余热发电技术
采用的重要技术措施有: a、窑头熟料冷却机方面,改变抽取窑头熟料冷 却机废气方式:多阶段抽取废气,使能量实现梯 级利用。即在冷却机进料端设置一抽取400-600℃ 抽废气口,作为过热器热源,产生过热蒸汽;冷 却机中部设置抽取260-360℃废气的抽废气口,作 为窑头AQC锅炉热源.产生饱和蒸汽,并产生0.10.5MP的饱和低压低温蒸汽和85-200℃热水。
余热发电技术

第一节大型干法水泥纯低温余热发电技术概述一、掌握内容1、复合闪蒸补汽式纯低温余热发电系统工艺流程2、复合闪蒸补汽式纯低温余热发电废气的取热方法3、纯低温余热发电技术一是在新型干法生产线生产过程中,通过余热回收装置(余热锅炉)将窑头、窑尾排出大量地品位的废气渔人进行回收换热,产生过热蒸汽推动汽轮机实现热能-机械能的转换,再带动发电机发出电能,并供给水泥生产过程中的用电负荷从而不仅大大提高了水泥生产过程中能源的利用水平,对于保护环境,提高企业的经济效益,提升产品的市场竞争力,起到了巨大的促进作用。
4、纯低温余热发电技术的特点是在不提高水泥生产过程中能耗指标的前提下,完全利用水泥煅烧过程中产生的余热进行回收,最大限度的提高水泥生产过程中热能的利用效率,另外配制纯低温余热发电系统将对原油水泥工艺系统不产生影响当两个系统接口计合理,将融和成为一个更优的大系统。
二、了解内容1、水泥余热发电应用的历史条件和发展方向2、国内余热发电已普遍采用的几种热力循环系统、循环参数及废气取热方式的特点和存在的主要问题讲解资料一、发展水泥窑余热发电技术的目的1. 1降低能耗、保护环境水泥熟料锻烧过程中,由窑尾预热器、窑头熟料冷却机等排掉的400c以下低温废气余热,其热量约占水泥熟料烧成总耗热量30%以上,造成的能源浪费非常严重。
水泥生产,一方面消耗大量的热能(每吨水泥熟料消耗燃料折标准煤为100〜115kg),另一方面还同时消耗大量的电能(每吨水泥约消耗90〜115kwh)。
如果将排掉的400℃以下低温废气余热转换为电能并回用于水泥生产,可使水泥熟料生产综合电耗降低60%或水泥生产综合电耗降低30%以上,对于水泥生产企业:可以大幅减少向社会发电厂的购电量或大幅减少水泥生产企业燃烧燃料的自备电厂的发电量以大大降低水泥生产能耗;可避免水泥窑废气余热直接排入大气造成的热岛现象,同时由于减少了社会发电厂或水泥生产企业燃烧燃料的自备电厂的燃料消耗,可减少CO2等燃烧废物的排放而有利于保护环境。
- 1、下载文档前请自行甄别文档内容的完整性,平台不提供额外的编辑、内容补充、找答案等附加服务。
- 2、"仅部分预览"的文档,不可在线预览部分如存在完整性等问题,可反馈申请退款(可完整预览的文档不适用该条件!)。
- 3、如文档侵犯您的权益,请联系客服反馈,我们会尽快为您处理(人工客服工作时间:9:00-18:30)。
纯低温水泥余热发电技术介绍宁国水泥厂余热发电处前言新型干法水泥生产技术在我国经历了一个逐步完善提升的发展过程。
近年来,新型干法水泥生产技术在应用中不断提升,尤其是海螺集团,在工艺系统优化、自动控制、投资成本、生产规模、劳动生产率和环境保护等生产技术和装备方面,已赶上甚至领先国际先进水平,只是在可燃废料替代率和生产用电自供率方面,与发达国家相比,还存在一定的差距。
近两年来,我国经济发展水平持续高扬,电力需求增长迅猛,电能供应紧张,国家对工业企业节能提出了更高的要求,尤其是对高耗能产业,要求最大限度地回收利用余热,降低能耗,节约能源,实现经济可持续发展战略。
因此,随着水泥市场竞争的日益激烈与残酷,充分利用窑系统排放废气进行余热发电,提高工厂生产用电自供率,降低水泥生产成本,提高产品的性价比,从而占领和扩大水泥市场份额,保持企业可持续发展,是大型水泥企业当前及今后可供选择的技术之一。
一、水泥窑余热发电技术的发展历程简介:水泥窑余热发电技术的发展大致经历了中空水泥窑余热发电技术、带补燃炉的预分解窑余热发电技术和当前的纯低温水泥窑余热发电技术三个阶段,每个阶段的发展都与同时期的水泥发展技术、企业需求、国家产业政策、环境要求等因素息息相关,密不可分。
1、中空水泥窑余热发电技术中空水泥窑余热发电技术已有80多年的历史,我国水泥窑余热发电技术起源于二十世纪三十年代东北及华北地区建设的若干条中空窑配套的高温余热发电系统,很长一段时间内随着小水泥在全国范围的“遍地开花”,中空水泥窑余热发电技术也随之“扎根落户”,得到了较快的发展。
其水泥窑废气温度为800℃~900℃、熟料热耗为6700KJ~8400KJ/kg,所配套的高温余热发电系统的发电能力为每吨熟料100kW~130kW。
二十世纪八十年代后期,由于新型干法水泥技术的迅猛发展,中空窑等落后生产工艺的高能耗、低产量等劣势凸显,已逐步被淘汰,其中空水泥窑余热发电技术同样也少有发展的空间与意义。
2、带补燃炉的预分解窑余热发电技术带补燃炉的预分解窑余热发电技术已发展了10多年,主要是为解决水泥厂供电紧张而设置。
利用窑头窑尾废气余热生产出低压蒸汽或高温水,再经补燃锅炉加温加压,提高蒸汽品质,可发出更多的电能,以满足水泥生产用电需要。
补燃锅炉能燃用劣质煤、煤矸石,综合利用了资源。
但增设补燃锅炉而多发出的电能部分,与大容量的高温高压蒸汽发电(火电厂)相比,其单位电能煤耗要高40%以上,是不经济的,环境污染也较明显,环保措施难以跟上,同时由于国家产业政策调整、环保要求及煤资源供应日趋紧张,故带补燃炉的预分解窑余热发电技术受到很大局限,未能大范围的推广与应用。
3、纯低温水泥窑余热发电技术纯低温水泥窑余热发电技术是直接利用窑头窑尾排放的中低温废气进行余热回收发电,无需消耗燃料,发电过程不产生任何污染,是一种经济效益可观、清洁环保、符合国家清洁节能产业政策的绿色发电技术,具有十分广阔的发展空间与前景。
4、世界各国应用水泥余热发电技术现状节能降耗是水泥工业持续发展的需要。
在降低水泥熟料烧成热耗和水泥综合电耗的同时,充分利用水泥生产中的中低温废气余热发电,逐步最大限度地满足自身用电需要,减少外供电量,节约成本,是世界水泥工业发展的趋向。
日本水泥工业在回收余热发电方面应用最广,近80%的水泥窑都带有纯低温余热发电系统,平均吨熟料发电量为30~40kWh/t。
欧洲国家水泥余热发电技术应用也较普遍。
我国台湾地区的水泥生产企业配置余热发电系统的比例也很高,也主要是从日本引进技术。
美国在水泥余热发电技术应用上也较积极。
美国水泥协会1995年提出,在降低水泥综合电耗的同时充分利用余热发电技术,提高余热利用率。
二、日本川崎公司纯低温水泥窑余热发电技术、业绩介绍:一九九五年八月,日本新能源产业技术综合开发机构(NEDO)与中国国家计委、国家建材局签订了水泥余热发电设备示范事业基本协定书,由日方提供一套先进且成熟可靠的低温余热发电技术和设备用于中国现有水泥厂,通过科学论证和国内外专家的实地考察,日方提供的这套设备安装在宁国水泥厂4000t/d水泥生产线上,发电机装机容量为6480kW,设计年发电量为4087×104kWh,吨熟料发电能力为33. 88kW.h/t。
1、主要技术特点:水泥厂余热资源的特点是:流量大,品位较低。
以宁国水泥厂4000t/d生产线为例,PH(预热器)和AQC(冷却机)出口废气流量和温度分别为258550Nm3/h、350℃和306600Nm3/h、238℃,余热发电便是充分利用这两部分余热资源进行热能回收。
1)热力系统整个热力系统设计力求经济、高效、安全,系统工艺流程是由两台高效余热锅炉AQC、PH•锅炉、两台高低压闪蒸器和一套汽轮发电机组组成,辅之以冷却水系统、纯水制取系统、锅炉给水系统及锅炉粉尘输送系统。
余热锅炉内进行热交换产生压力为25kg/cm2、温度为335℃~350℃、额定蒸发量为31.1t/h的过热蒸汽通入汽轮机,进行能量转换,拖动发电机向电网输送电力。
(1)采用凝汽式两点混汽式汽轮机。
凝汽式是指做过功的蒸汽充分冷凝成凝结水,重新进入系统循环,减少系统补充水量。
混汽式是指汽轮机除主蒸汽外,另有两路低压饱和蒸汽导入汽轮机做功,从而提高汽轮机相对内效率,提高发电机输出功率。
(2)设置具有专利技术、高热效率的余热PH锅炉,采用特殊设计的机械振打装置进行受热面除灰,保证锅炉很高的传热效率。
(3)应用热水闪蒸技术(高压热水进入低压空间瞬间汽化现象),设置一台高压闪蒸器和一台低压闪蒸器,一方面将闪蒸出的饱和蒸汽导入汽轮机做功,进一步提高汽轮机做功功率,另一方面形成锅炉给水系统循环,可以有效地控制AQC炉省煤器段出口水温,保证锅炉给水工况稳定。
(4)由于SP出口废气还要用于原料烘干,所以SP锅炉无省煤器,只设蒸发器和过热器,控制出炉烟温在250℃,仍可满足水泥生产线工艺需求。
(5)采用热水闪蒸自除氧结合化学除氧的办法进行除氧,不另设除氧器,减少了工艺设备,简化了工艺流程。
(6)热力泵均采用一用一备双系列。
在运行泵出现故障时,备用泵自动投入使用,保证了发电系统安全、稳定运行。
2)余热锅炉AQC锅炉设计为立式自然循环锅炉,带汽包,烟气自上而下通过锅炉,锅炉自上而下布置过热器、蒸发器和省煤器,由于废气粉尘为熟料颗粒,具有较强的磨砺性,需设置预除尘器进行预收尘,另外为增大换热面积,强化换热效果,AQC锅炉的传热管设计为螺旋翅片管形式(鳍片管)。
AQC锅炉工艺参数设计:烟气入口温度360℃,出口温度91℃,烟气流量165300Nm3/h,过热蒸汽温度350℃,蒸汽压力26kg/cm2,额定蒸发量11.8t/h。
SP锅炉设计为卧式强制循环锅炉,带汽包,设蒸发器和过热器,烟气在管外水平流动,受热面为蛇形光管,上端固定在构架上,下端为自由端,并焊有振打装置之连杆。
由于SP炉入炉粉尘为生料粉,具有较强的粘附性,影响传热效果,故设计机械振打装置对受热面定期振打,使受热面保持干净无灰,从而保证了很高的传热效果。
由于工作介质在传热管内是上下流动形式,无法利用其重度差进行自然循环,故需用两台强制循环泵进行给水的强制循环。
SP锅炉工艺参数设计:烟气入口温度350℃,出口温度250℃,烟气流量258550Nm3/h,过热蒸汽温度330℃,蒸汽压力26kg/cm2,额定蒸发量19.3t/h。
两锅炉的工艺结构特点对比如下表:SP锅炉AQC锅炉锅炉形式卧式立式工质循环方式强制循环自然循环烟气流向自上而下自下而上管程流向垂直水平管列形式错排错排管形式光管螺旋翅管受热面无省煤器有省煤器除灰装置机械振打无3)汽轮机汽轮机的作用是将余热锅炉产生的过热蒸汽的热能转化为机械能从而带动发电机发电的动力设备。
宁国厂汽轮机为川崎RCM-80型,冲动式、多级、混压凝汽式带减速机型汽轮机,额定蒸汽流量31.1t/h,入口蒸汽压力 2.45MPa,蒸汽温度335℃,排汽绝对压力0.00585MPa,转速5829rpm,级数为9级。
(1)汽轮机为减速式汽轮机,通过减速机后转速为1500rpm,这样汽轮机的整体尺寸较小,暖机和冲转所需的时间较短,便于汽轮机停机后能够在短时间内迅速再投入,适应窑系统工况的波动。
针对汽轮机后几级叶片水份较多、易发生水蚀现象的特点,在低压部分特别设计了集水槽和疏水孔,充分利用转子转动的离心力分离水珠,避免水蚀。
另在末两级叶片前部覆盖了一层特殊合金,以减轻水击产生的损伤。
(2)汽轮机的调节系统采用电、液(压)调节方式,感应机构为电磁式,执行机构为液压传动式。
调节系统稳定可靠,保证了汽轮机在设计范围内的任何工况下稳定运行。
(3)根据水泥厂余热性质的特点,汽轮机的运行方式分为速度控制和压力控制两种方式。
在汽轮机启动过程中(提速及升负荷),以汽轮机转速为主要控制参数,以保证汽轮发电机组正常并网;当机组达到额定负荷时,切换到压力控制方式,这时以汽轮机入口蒸汽压力为主要控制参数,调节机组输出功率以保证压力基本稳定,这种控制方式可适应废气余热参数的变化,使整个系统具有较强的适应性和可靠性,并做到“热尽其用”。
机组出力超过限定值(约额定功率的110%),自动开启旁路阀,将部分蒸汽直接导入凝汽器,起到保护发电机组的目的。
4)发电机发电机设计为全封闭内冷式三相交流同步发电机,励磁方式采用无刷励磁,额定输出8100KVA,极数4极,电压6300V,频率50HZ,功率因数80%滞后,电流742A,空气冷却器采取水冷却的方式。
5)DCS控制系统整个余热发电系统采用先进的DCS集散控制系统,现场的各种工艺参数通过传感器转化为电信号送至中央控制室,由计算机进行分析并在CRT上显示。
中控操作通过触摸屏发出指令,调整各烟风阀门、汽水阀门的开度及设备的启停等,使整个系统适应工况变化。
自控系统能够根据相关参数自动进行汽水系统的调整,系统的操作简便可靠,并设有完善的报警和保护程序,使整个发电工艺系统能够长期稳定运行。
2、宁国水泥厂4000t/d熟料生产线余热发电项目运转业绩:1)主要经济技术指标分析自一九九八年三月开始实质性运转至二○○四年底,从统计数据表明,平均吨熟料发电量已达36.12kWh/t,相对窑运转率为96.24%,累计发电量已达3.56亿千瓦时。
系统运行六年来实现了安全、稳定、高效运行。
请参见下面生产数据统计图表:表一年份总发电量 (万kWh)运转时间 (h) 相对窑运转率 (%) 吨熟料发电量(kWh/t) 1998年 4106.545514.1 93.21 37.10 1999年 4108.746766.3 94.35 31.43 2000年 5167.717585.9 95.55 36.42 2001年 5294.377798.8 96.77 36.48 2002年 5613.778109.7 98.48 37.04 2003年 5701.938123.1 98.02 37.88 2004年5619.54 8092.9 97.31 36.45 累计35612.6 51990.8 平均96.24 平均36.12 表二余热发电历年来发电总量、相对窑运转率对比0100020003000400050006000发电量(万kWh )80100运转率(%)年总发电量4106.544108.745167.715294.375613.775701.935619.54相对窑运转率93.2194.3595.5596.7798.4898.0297.3198年99年00年01年02年03年04年表三2)经济效益和社会效益水泥余热发电项目充分利用熟料煅烧生产时排放的大量废气进行回收发电,即可降低水泥熟料的生产成本,提高企业经济效益,又能保护环境,创造良好的社会效益。