SMT印制电路板的可制造性设计与审核
SMT印制电路板设计常见问题及解决方法
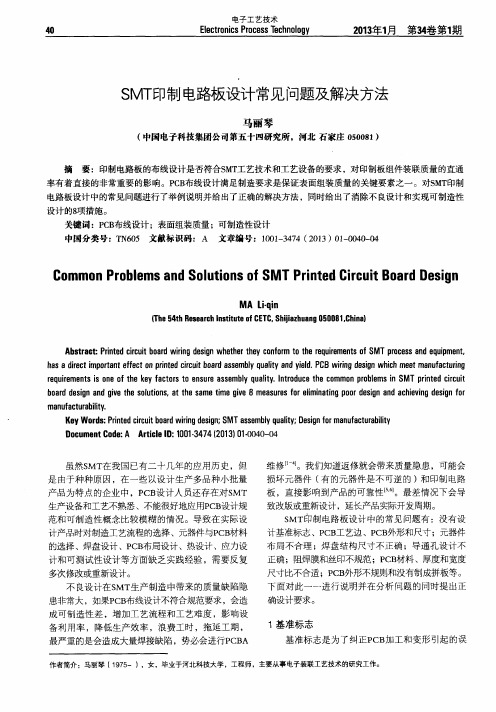
( T h e 5 4 t h R e s e a r c h I n s t i t u t e o f C E T C , S h i j i a z h u a n g 0 5 0 0 8 1 , C h i n a l
A b s t r a c t : P r i n t e d c i r c u i t b o a r d wi r i n g d e s i g n wh e t h e r t h e y c o n f o r m t o t h e r e q u i r e me n t s o f S MT p r o c e s s a n d e q u i p m e n t ,
致改版或重新设计 ,延长产品实际开发周期。 s MT印制 电路 板设计 中的常 见 问题有 :没有 设 计基准标 志 、P C B 工艺边 、P C B  ̄ b 形和尺寸 ;元器件 布 局不合 理 ;焊盘 结构尺寸 不正确 ;导通 孔设 计不
计和可测试性设计等方面缺乏实践经验 ,需要反复
设计 的8 项措施 。
关键词 :P C B 布线设计 ;表 面组装质量 ;可制造性设计 中国分类号 :T N 6 0 5 文献标识码 :A 文章编号 :1 0 0 1 — 3 4 7 4( 2 0 1 3 )0 1 — 0 0 4 0 — 0 4
C o mmo n P r o b l e ms a n d S o l u t i o n s o f S MT P r i n t e d C i r c u i t B o a r d D e s i g n
D o c u me n t C o d e : A A r t i c l e I D : 1 O 0 1 , 3 4 7 4( 2 0 1 3 ) 0 1 . 0 0 4 0 — 0 4
SMT印制板设计规范

SMT印制板设计规范SMT(Surface Mount Technology)印制板设计规范是关于电子产品印制板设计的一系列要求和准则,旨在确保PCB(Printed Circuit Board)的制造过程能够顺利进行,并最终得到高质量的印制板产品。
下面是一些SMT印制板设计规范的重要内容。
1.印制板尺寸和布局:-确定印制板的实际尺寸,包括长度、宽度和厚度,并在设计中使用正确的尺寸参数。
-设计合理的布局,确保所有元件和走线的正确安装和连通,以提高印制板的性能和可靠性。
2.元件安装规范:-元件安装应遵循适当的引脚布局,确保元件安装在正确的位置并正确连接。
-元件的排列应便于制造和维修,并保证元件之间的足够间距和空间。
3.安装孔和固定装置:-印制板上的孔和固定装置应符合标准尺寸和设计规范,并确保能够正确安装印制板。
-孔的位置和尺寸应准确,以确保印制板和配件之间的稳定连接。
4.线宽和间距:-确定正确的线宽和间距参数,以提供足够的电流传输能力,并避免线路之间的干扰或短路。
-确保线宽和间距符合制造商的要求和能力,并能满足所需的电子器件和电流要求。
5.反焊和覆盖层:-在印制板上使用适当的反焊材料,以便在组装过程中保护印制电路和焊点,并提供良好的可焊性。
-配置适当的覆盖层,以保护印制板免受外部环境的影响,并提供适当的绝缘和防护。
6.引脚和焊盘:-准确标记元件引脚的位置和方向,确保正确的引脚连接和组装。
-焊盘的尺寸和形状应适合所使用的元件,并提供良好的焊接质量和可靠性。
7.电源分离和地面规范:-正确的电源分离和地面规范是确保印制电路的稳定性和性能的重要因素。
-确定正确的分离点和连接方式,以确保电源的稳定和地面的良好连接。
8.文件和制造要求:-提供准确和详细的PCB设计文件,包括图纸、尺寸和布局等信息,以供制造商参考。
-了解制造商的要求,并根据实际制造要求进行设计和调整。
总之,遵守SMT印制板设计规范对于确保PCB的制造质量和性能至关重要。
SMT DFM(可制造性设计)检查表

文件编号:LCT-PC-All-QD一、产品基本信息□研发阶段□中试阶段□量产阶段二、SMT技术资料三、PCB制造工艺要求(一)PCB 设计3、PCB之工艺边:定位孔A、定位孔直径(∮=3~4mm);B、定位孔距离板角坐标:X=5mm,Y=5mm。
C、PCB四边均需要工艺边框,其中2个长边宽度应大于8mm以上,短边应大于3mm以上。
D、PCB板顶角成圆弧形。
□□□1、PCB之工艺边定位孔:Ph ilips FCM高速贴装机Carrier传动结构特殊要求。
2、见图示(一)。
4、PCB小板:夹具孔周边1mm内不允许有元器件,以免与夹具干涉。
□□□1、PCB小板夹具孔:通用要求。
2、见图示(一)。
5、PCB焊盘、通孔设计A、同一元件Pad形状、面积要相同;与材料管脚规格匹配。
B、焊盘相邻边间隙要求大于8Mil;若无法达到8Mil,则不能小于6Mil(且须在Gerber文件中指出其位置)。
C、PCB上通孔(via hole)需要密封。
D、Pad上via尽可能小,且必须全部密封。
E、零件间距不会造成放置时互相干涉。
F、BGA焊盘间面积要相等;焊盘上通孔(via hole)尽可能引至边缘或焊盘外。
□□□1、间隙太小,仅0.1mm。
2、间隙要大于8Mil(0.2mm)。
1、BGA焊盘面积不相同。
2、焊盘上通孔移至边缘或焊四、SMT制程控制要求4.1. 锡膏管控1、锡膏选择。
2、运输、存放。
3、生产使用管制。
4.2. 钢板及刮刀、治具管控4.3. 元件选择4.4. 材料Profile 参数设定1、 Profile 量测位置选取原则:大组件、BGA 、QFP 、屏蔽盖内等。
2、 Profile 参数:1) 有铅: 峰值温度为215℃~225℃;179℃~183℃回流时间60~90 S ;上升斜率<3℃/ S 。
2) 局部无铅:Peak 为225℃~230℃;220℃以上30~40S ;回流时间80~110S 。
SMT贴片流程及可制造性
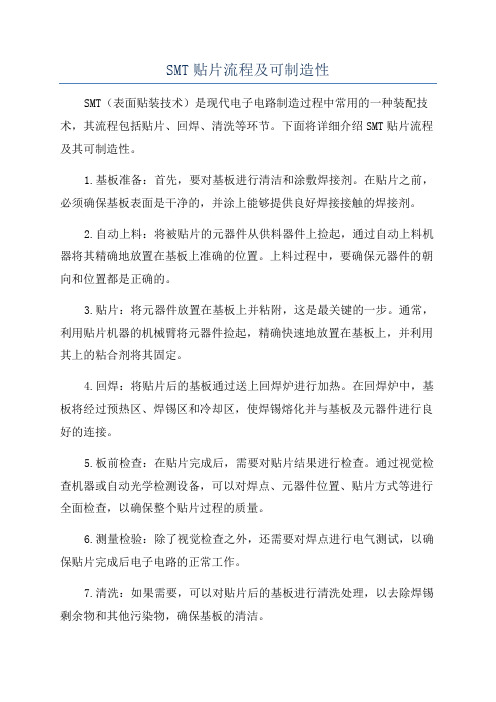
SMT贴片流程及可制造性SMT(表面贴装技术)是现代电子电路制造过程中常用的一种装配技术,其流程包括贴片、回焊、清洗等环节。
下面将详细介绍SMT贴片流程及其可制造性。
1.基板准备:首先,要对基板进行清洁和涂敷焊接剂。
在贴片之前,必须确保基板表面是干净的,并涂上能够提供良好焊接接触的焊接剂。
2.自动上料:将被贴片的元器件从供料器件上捡起,通过自动上料机器将其精确地放置在基板上准确的位置。
上料过程中,要确保元器件的朝向和位置都是正确的。
3.贴片:将元器件放置在基板上并粘附,这是最关键的一步。
通常,利用贴片机器的机械臂将元器件捡起,精确快速地放置在基板上,并利用其上的粘合剂将其固定。
4.回焊:将贴片后的基板通过送上回焊炉进行加热。
在回焊炉中,基板将经过预热区、焊锡区和冷却区,使焊锡熔化并与基板及元器件进行良好的连接。
5.板前检查:在贴片完成后,需要对贴片结果进行检查。
通过视觉检查机器或自动光学检测设备,可以对焊点、元器件位置、贴片方式等进行全面检查,以确保整个贴片过程的质量。
6.测量检验:除了视觉检查之外,还需要对焊点进行电气测试,以确保贴片完成后电子电路的正常工作。
7.清洗:如果需要,可以对贴片后的基板进行清洗处理,以去除焊锡剩余物和其他污染物,确保基板的清洁。
1.元器件封装:不同的元器件封装形式对贴片工艺的要求不同。
例如,表面贴装元器件(SMD)和裸露芯片元器件(BGA)的封装形式对焊接技术和贴片机的要求不同,需要根据不同封装形式进行不同的工艺调整。
2.设计规范:良好的设计规范对贴片工艺的可制造性至关重要。
例如,元器件的布局和间距、组件的定位标记、焊盘和针孔的设计等都需要满足贴片机的要求,以确保贴片的精确度和质量。
3.设备能力:贴片机的性能和能力对贴片工艺的可制造性具有重要影响。
例如,贴片机的速度、精度和稳定性都需要满足生产要求,以确保贴片的质量和效率。
4.材料选择:选择适合贴片工艺的材料也是关键因素。
SMT与AI可制造性标准20101209

须考虑机器轨
5 2、PCB 的 BOT 面上,焊盘至“非轨道便”距离要求:(仅针对双面回流 PCB)
道传输和装夹
定位所要求的 工 元件离板边的 艺
最小距离,必要 组
说明:PCB 下板,所有需印刷锡膏的元件、焊盘等,至“非轨道边”距离要求大于 5.0MM;
序 列
项目
1.1 SMT 可生产 PCB 尺寸要求(如图 A1.1)(依据 SMT 车间机器性能要求) 1、点胶制程(单层板)PCB 的可生产尺寸范围: 最小极限尺寸:X 方向:50MM Y 方向:55MM 最大极限尺寸:X 方向:410MM Y 方向:360MM 2、锡膏制程(多层板)PCB 的可生产尺寸范围: 最小极限尺寸:X 方向:80MM Y 方向:55MM 最大极限尺寸:X 方向:450MM Y 方向:350MM 3、SMT 推荐的 POWRE 板、LCD 主板及 TV 主板尺寸范围:
1、板材的使用应和制程相对应 说明:
边缘有毛刺易 工
造成机器轨道 艺
送板不顺畅或 轨道卡板
组
1) SMT 不同的回流焊制程,其焊接温度不一样,无铅(峰值温度:235-250℃)、点胶(固 化温度 120℃)。
2) 不同板材的 PCB,其耐焊接热性能不一样,这与不同板材 TG 点有关,FR-1 纸基板的 TG 点只有 80℃左右,二 FR-4 玻璃布基板 TG 点位 125℃。因此,为防止 PCB 板砖焊接 过程中产生是产生较大的热应点和变形,选择电子产品的 PCB 集采时应综合成本和性能
<100
≤1.5 ≤2.0 ≤2.5
≤3.0
100-200 ≤1.5 ≤2.5 ≤3.5
SMT与DFM汇总

• (4) 元器件布局不合理
•
a 没有按照再流焊要求设计,再流焊时造成温度不均匀。
• b 没有按照波峰焊要求设计,波峰焊时造成阴影效应。
• (5) 基准标志(Mark)、PCB外形和尺寸、PCB定位孔和夹持边的设 置不正确 • a 基准标志(Mark)做在大地的网格上,或Mark图形周围有阻焊
—印制板电路设计——————测试点
—可靠性设计
—降低生产成本
—焊盘与导线的连接
—阻焊 —散热、电磁干扰等
•
可制造性设计DFM(Design For Manufacture)
是保证PCB设计质量的最有效的方法。DFM就是从产
品开发设计时起,就考虑到可制造性和可测试性,
使设计和制造之间紧密联系,实现从设计到制造一
• → 首批投料
→ 小批试生产
→ 正式投产
传统的设计方法与现代设计方法比较
• •
•
传统的设计方法
串行设计
重新设计 1#
重新设计 n#
生产
•
现代设计方法
并行设计CE 及DFM 重新设计 1# 生产
• •
•
SMT工艺与传统插装工艺有很大区别,对PCB 设计有专门要求。除了满足电性能、机械结构、 等常规要求外,还要满足SMT自动印刷、自动贴装、 自动焊接、自动检测要求。特别要满足再流焊工 艺的再流动和自定位效应的工艺特点要求。 • SMT具有全自动、高速度、高效益的特点,不 同厂家的生产设备对PCB的形状、尺寸、夹持边、
定位孔、基准标志图形的设置等有不同的规定。
•
不正确的设计不仅会导致组装质量下降,还会造成贴
装困难、频繁停机,影响自动化生产设备正常运行,影响
贴装效率,增加返修率,直接影响产品质量、产量和加工
SMT印制板可制造性设计(工艺性)审核
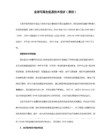
3.4 是否符合SMT工艺对PCB设计的要求
a. 基板材料、元器件及元器件包装的选用是否符合要求;
b. 焊盘(形状、尺寸、间距)是否符合DFM规范;
c. 引线宽度、形状、间距、引线与焊盘的连接是否符合要求;
d. 元器件整体布局、元器件之间最小间距是否符合要求,大器件周围是否考虑了返修尺寸;
(2)为了要满足SMT自动贴装、自动检测的要求
SMT具有全自动、高速度、高效益的特点,不同厂家的生产设备对PCB的形状、尺寸、夹持边、定位孔、基准标志图形设置等有不同的规定,如果设计不正确会导致组装质量下降,会造成贴装困难、频繁停机,影响自动化生产设备正常运行,影响贴装效率;增加返修率,直接影响产品质量和成品率,严重时还会造成印制板报废等质量事故。
e. 再流焊面元器件排布方向是否符合要求;
f. 波峰焊时元器件排布方向是否符合要求;
g. 插装元器件的孔径、焊盘设计是否符合DFM规范;
h. 元器件的极性排列方向是否尽量一致;
i. 阻焊膜及丝网图形是否正确,元件极性与IC第1脚是否标出;
j. 轴向元件插装孔跨距是否合适(或元件成形是否正确);
SMT印制板可制造性设计(工艺性)审核
1. SMT印制电路板可制造性设计审核的目的
2.审核程序
3. PCB可制造性设计审核审核内容
4. PCB可制造性设计审核标准和依据
5. PCB可制造性设计审核方法
6.完成审核后要写出审核报告
(1)为了满足SMT工艺要求
SMT工艺与传统插装工艺有很大区别,对PCB设计有专门要求。
2.审核程序
首先是设计人员自审;
然后由工艺人员逐项审核;
印制电路板可制造性设计审核要点

A面 混 装 B 一 面 既 装 S D 又 装 有 T C M, H 面 仅 贴 简 单 另 二 次 回 流 焊加 一 次 面 仅 装 有 C i 元 h p类 波 峰 焊
一
足够的机械 强度 , 能够承受 组装工 艺中的热处 理和冲击 , 足够 的平整度 以适合 自动化的组装工艺 , 能承受多次的返修 ( 接) 焊
技术市场
印制 电路板 可 制造 性设 计 审核要 点
管 良梅 张卫 民 吕文 锋
( 国电南瑞科技 股份有 限公 司, 江苏 南京 2 6 ) 1 0 1 0 【 摘 要】印制 电路板可 制造性设计 (F ) DM 是提 高加工质 量、 高生产效率 、 高电子产品可靠性 、 提 提 降低 成本 的重要措施。 述 叙
等 。 有 能力 的情 况 下 , 计 人 员 应 该 尽 量 做 到 以 下 的布 局 法 : 在 设 对 于 背 景有 较 高 的反 差 。 光 学 定 位 基 准 中 心 3m以l 要 设 在 m 内不 错 。一 般 采 用 直 径 1 5m的实 心 圆 焊 盘 作 为光 学基 准 。光 学 定 .m
称为 D M 印制板详细 阶段设计完成后, F。 设计者按 以下条 目进行
一
次全面的 自我审查非常必要 , 有助于减少一些显而 易见 的问
基 板 的 选 择
题 , 艺 工 程 人 员 进 行 复 审将 尽 可 能地 提 高 设 计 质 量 。 工
一
S D 又有 T C M, H
、
基板 的作用 , 了提供 组装所需 的架构外 , 除 也提供 电源和
工 作 , 合 P B的制 造 工 艺 , 适 C 良好 的 电气 性 能 ( 阻 抗 、 质 常 如 介
- 1、下载文档前请自行甄别文档内容的完整性,平台不提供额外的编辑、内容补充、找答案等附加服务。
- 2、"仅部分预览"的文档,不可在线预览部分如存在完整性等问题,可反馈申请退款(可完整预览的文档不适用该条件!)。
- 3、如文档侵犯您的权益,请联系客服反馈,我们会尽快为您处理(人工客服工作时间:9:00-18:30)。
A面再流焊,B面波峰焊工艺时, BGA的导通孔应设计盲孔
A面再流焊
B面波峰焊 由于二次熔锡 造成BGA焊点失效
(8) 元器件和元器件的包装选择不合适 由于没有按照贴装机供料器配置选购元器件和元器 件的包装,造成无法用贴装机贴装。
• 1994年SMTA首次提出DFX概念。1995年DFX是表面贴装国际会议 的主题,1996年SMTA发表了6篇相关性文章。 作为一种科学的方法,DFX将不同团队的资源组织在一起,共同 参与产品的设计和制造过程。通过发挥团队的共同作用,实现缩短 产品开发周期,提高产品质量、可靠性和客户满意度,最终缩短从 概念到客户手中的整个时间周期。
环保设计
• DFF: Design for Fabrication of the PCB PCB可加工性设计
• DFS: Design for Sourcing
物流设计
• DFR: Design for Reliability 可靠性设计
• HP公司DFM统计调查表明:产品总成本 60%取决于产品的最初设计,75%的制造成 本取决于设计说明和设计规范,70-80%的 生产缺陷是由于设计原因造成的。
一. 不良设计在SMT生产制造中的危害
1. 造成大量焊接缺陷。 2. 增加修板和返修工作量,浪费工时,延误工期。 3. 增加工艺流程,浪费材料、浪费能源。 4. 返修可能会损坏元器件和印制板。 5. 返修后影响产品的可靠性 6. 造成可制造性差,增加工艺难度,影响设备利用率,
降低生产效率。 7.最严重时由于无法实施生产需要重新设计,导致整个
• 新产品研发过程
方案设计 → 样机制作 → 产品验证 •
→ 小批试生产 → 首批投料 → 正式投产
传统的设计方法与现代设计方法比较
•
传统的设计方法
•
串行设计 重新设计 重新设计
生产
•
1#
n#
•
现代设计方法
•
•
并行设计CE 重新设计 生产
•
及DFM
1#
内容
一. 不良设计在SMT生产制造中的危害 二. 目前国内SMT印制电路板设计中的常见问题及解决措施 三. SMT工艺对PCB设计的要求 四. SMT设备对PCB设计的要求 五. 提高PCB设计质量的措施 六. SMT印制板可制造性设计(工艺性)审核 七. 产品设计人员应提交的图纸、文件 八. 外协加工SMT产品时需要提供的文件 九. IPC-7351《表面贴装设计和焊盘图形标准通用要求》简介
现代设计DFX系列介绍
• DFM: Design for Manufacturing 可制造性设计
• DFT: Design for Test
可测试性设计
• DFD: Design for Diagnosibility 可分析性设计
• DFA: Design for Aseembly
可装配性设计
• DFE: Desibn for Enviroment
b 导轨传输时,由于PCB外形异形、PCB尺寸过大、过 小、或由于PCB定位孔不标准,造成无法上板,无法实 施机器贴片操作。
c 在定位孔和夹持边附近布放了元器件,只能采用人 工补贴。
d 拼板槽和缺口附近的元器件布放不正确,裁板时造 成损坏元器件。
(6) PCB材料选择、PCB厚度与长度、宽度尺寸比不合适 a 由于PCB材料选择不合适,在贴片前就已经变形,
• DFM具有缩短开发周期、降低成本、提高产品质 量等优点,是企业产品取得成功的途械行业用于简化产品结构和减少加工成本。 • 1991年,DFM的应用对美国制造业竞争优势的形成做出贡献,美
国总统布什给创始人G.布斯劳博士和P.德赫斯特博士颁发了美国国 家技术奖。DFM很快被汽车、国防、航空、计算机、通讯、消费类 电子、医疗设备等领域的制造企业采用。
SMT印制电路板的 可制造性设计及审核
• 印制电路板(以下简称PCB)设计是表面组装技术 的重要组成之一。PCB设计质量是衡量表面组装技术水平 的一个重要标志,是保证表面组装质量的首要条件之一。
PCB设计包含的内容:
—基板材料选择
—布线
—元器件选择
—焊盘
—印制板电路设计——————测试点
PCB设计——可制造(工艺)性设计 —导线、通孔
—可靠性设计 —降低生产成本
—焊盘与导线的连接 —阻焊
—散热、电磁干扰等
• 可制造性设计DFM(Design For Manufacture) 是保证PCB设计质量的最有效的方法。DFM就是从产 品开发设计时起,就考虑到可制造性和可测试性, 使设计和制造之间紧密联系,实现从设计到制造一 次成功的目的。
制造加工精度差造成的。其结果造成虚焊或电气断路。
• (4) 元器件布局不合理 • a 没有按照再流焊要求设计,再流焊时造成温度不均匀。
• b 没有按照波峰焊要求设计,波峰焊时造成阴影效应。
(5) 基准标志(Mark)、PCB外形和尺寸、PCB定位孔和夹 持边的设置不正确
a 基准标志(Mark)做在大地的网格上,或Mark图形周 围有阻焊膜,由于图象不一致与反光造成不认Mark、 频繁停机。
产品的实际开发时间延长,失去市场竞争的机会。
二. 目前国内SMT印制电路板设计中的 常见问题及解决措施
1. PCB设计中的常见问题(举例)
(1) 焊盘结构尺寸不正确(以Chip元件为例)
a 当焊盘间距G过大或过小时,再流焊时由于元件焊端不能与焊 盘搭接交叠,会产生吊桥、移位。
•
焊盘间距G过大或过小
b 当焊盘尺寸大小不对称,或两个 元件的端头设计在同一个焊盘上时, 由于表面张力不对称,也会产生吊 桥、移位。
• (2) 通孔设计不正确
•
导通孔设计在焊盘上,焊料会从导通孔中流出,会造
成焊膏量不足。
•
不正确
•
正确 印制导线
• (3) 阻焊和丝网不规范
•
阻焊和丝网加工在焊盘上,其原因:一是设计;二是PCB
造成贴装精度下降。 b PCB厚度与长度、宽度尺寸比不合适造成贴装及再
流焊时变形,容易造成焊接缺陷,还容易损坏元器件。 特别是焊接BGA时容易造成虚焊。 • • 虚焊
(7) BGA的常见设计问题
a 焊盘尺寸不规范,过大或过小。 b 通孔设计在焊盘上,通孔没有做埋孔处理 c 焊盘与导线的连接不规范 d 没有设计阻焊或阻焊不规范。