型芯零件设计
铸造时型芯的作用

铸造时型芯的作用铸造是一种重要的制造工艺,用于制造各种金属零件。
在铸造过程中,型芯是不可或缺的组成部分。
型芯是一种用于铸造中形成零件内部空腔的模具,它具有重要的作用和功能。
型芯在铸造过程中起到形成零件内部空腔的作用。
在铸造过程中,金属熔体被倒入模具中,通过型芯的布置和定位,使得金属熔体在模具中形成零件所需的内部空腔。
型芯的形状和尺寸决定了最终铸件的内部形状和尺寸。
型芯可以帮助实现复杂几何形状的零件铸造。
有些零件的内部空腔形状非常复杂,无法通过一次铸造得到。
这时,可以使用型芯来实现复杂几何形状的零件铸造。
型芯可以根据零件的内部形状进行设计和制造,通过在模具中布置和定位型芯,使得金属熔体在铸造过程中形成复杂几何形状的内部空腔。
型芯还可以提高铸件的精度和质量。
在铸造过程中,型芯的形状和尺寸决定了铸件的内部形状和尺寸。
如果型芯的制作和使用不当,就会导致铸件的尺寸偏差或形状不合格。
因此,在铸造过程中,需要根据铸件的要求,设计和制造合适的型芯,以确保铸件的精度和质量。
型芯还可以帮助实现一些特殊要求的铸件。
有些零件的内部空腔需要具有特殊的形状或结构,以满足特定的工作要求。
这时,可以使用型芯来实现这些特殊要求。
型芯可以根据特殊要求进行设计和制造,通过在模具中布置和定位型芯,使得金属熔体在铸造过程中形成具有特殊形状或结构的内部空腔。
型芯的使用还可以提高铸造的生产效率。
在铸造过程中,型芯的制作和使用虽然增加了一定的工序和工作量,但可以通过提高铸件的一次成型率,减少废品率,从而提高铸造的生产效率。
此外,型芯的使用还可以减少后续加工工序,节约制造成本。
型芯在铸造过程中具有重要的作用和功能。
它不仅可以帮助形成零件内部空腔,实现复杂几何形状的铸造,提高铸件的精度和质量,还可以实现特殊要求的铸造,提高铸造的生产效率。
因此,在铸造过程中,正确选择和使用型芯是非常重要的。
只有合理设计和制造型芯,合理布置和定位型芯,才能保证铸件的质量和性能,提高铸造的效率和经济效益。
注射模具型芯加工工艺优化设计

方面研究 。
( hj n H N lc i C . Ld , u qn 2 6 3 hn ) Z ei gC I T Eet c o , t. Y e ig3 5 0 ,C ia a r
A s a t h rc si e h i e o naue c c i be k rN 6 一2 i e t n m ud c r a nr— b t c :T e po es g t nq f r n c u mii r i ut ra e B L 3 n ci o l oe w sit t r j o o
工工艺对提高模具精 度和缩短模 具 制造 周期 都起 到重 要作用 。最后 对 N 6 一2触 头 B L3 支持注射模具型 芯两 种不同加工工艺实现过程进行 对 比与分析 。
关 键 词 :工 艺 优 化 设 计 ;单 件 式 加 工 流 程 : 件 拼 接 式 加 工 流 程 多
中 图分 类 号 : M 5 1T 5 5 文 献 标 志 码 :B 文 章 编 号 : 0பைடு நூலகம்15 3 ( 0 2 0 — T 6 : M 0 10 . 1 2 1 ) 3 5
0 6- 3 00 0
陈 煦 ( 94 ) 17 一 ,
男 , 级 技 师 , 事 高 从
模具 开发 与创 造及
自动化设 备 工艺 等
Opi l s n o jcinMo l o eP o es t ma i fI e t ud C r r cs De g n o
CHEN Xu, Y Y n e U a m i
用 , 可在 正常 的情 况 下 作 为 线 路 的不频 繁操 作 也
转换 之用 , 泛应 用 于工 业 、 业 、 层 和 民用住 广 商 高
压铸工艺及模具设计:第7章 成型零件和模架设计
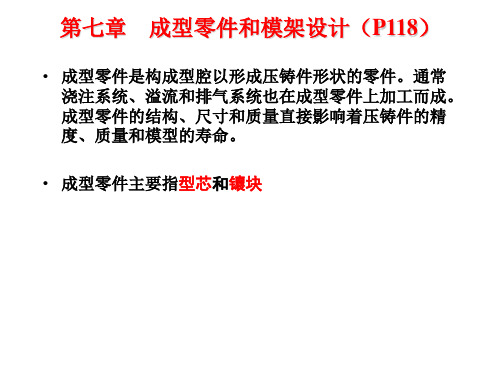
(一)主型芯的结构及固定形式 • 图7-6
(二)小型芯的结构及固定形式 • 图7-7,图7-8。
(二)小型芯的结构及固定形式
六、镶块和型芯的止转形式。
七、镶块和型芯的结构尺寸
(一)镶块壁厚尺寸
(二)整体镶块台阶尺寸
表7-8 整体镶块台阶尺寸推荐值
(三)组合式成型镶块固定部分长度
• 表7-9 组合式成型镶块固定部分长度推荐值
铸件实际尺寸的差与模具成型尺寸之比。即:
• A型-----室温下模具的成型尺寸(mm), • A实-----室温下压铸件的实际尺寸(mm)。
一、压铸件的收缩率 • (二)计算收缩率
• A’-----计算得到的模具成型零件的尺寸(mm), • A-----压铸件的公称尺寸(mm)。
常用压铸合金的计算收缩率腔尺寸(包括型腔深度尺寸) ②型芯尺寸(包括型芯高度尺寸)
③成型部分的中心距离和位置尺寸
(一)成型尺寸的分类及计算要点
成型尺寸计算的要点: • 因型腔磨损后尺寸增大,故计算型腔尺寸时应使得压
铸件外形接近于最小极限尺寸。
• 因型芯磨损后尺寸减小,故计算型腔尺寸时应使得压
铸件内形接近于最大极限尺寸。
• 1.壳体压铸件的成型尺寸分类
压铸件的①、②、③属于型腔尺寸;④、⑤、⑥属于 型芯尺寸;⑦、⑧属于中心距离、位置尺寸。另外, ②、⑤受到分型面的影响,高压、高速的金属液充填 型腔时,闭合的动、定模会出现微小的分离倾向,使 与分型面有关的尺寸略微增大。为消除这种影响,通 常将计算所得的公称尺寸减去0.05mm。
第七章 成型零件和模架设计(P118)
• 成型零件是构成型腔以形成压铸件形状的零件。通常 浇注系统、溢流和排气系统也在成型零件上加工而成。 成型零件的结构、尺寸和质量直接影响着压铸件的精 度、质量和模型的寿命。
型芯零件加工工艺编制 (1)
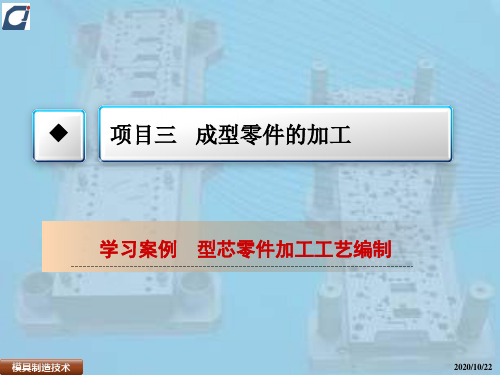
为淬火、低温回火,保证硬度58~64 HRC。 7、设备、工装的选择
设备选择有铣床、平面磨床、线切割机床等;加工过程采用通用
夹具虎钳、磁力吸盘等;刀具有面铣刀,立铣刀等;量具选用游标
卡尺,千分尺等。
模具制造技术
2020/10/22
(二)工艺卡片
模具制造技术
2020/10/22
(二)工艺卡片
模具制造技术
后,可以获得高耐磨性、基体有较高 推杆导向孔配合面。
强度和硬度,淬透性好,能满足定模
板实际工作的力学性能要求。切削加 作表面Ra0.8 μm、
3、主要表面分析
Ra1.6μm,尺寸精度IT7;
板类零件,上、下表面及相邻两侧面 49.98mm×49.98mm的固
作为工艺基准。
2、主要表面加工方法 型芯的工作表面Ra0.8 μm、Ra1.6μm,尺寸精度IT7; 49.98mm×49.98mm的固定端配合面Ra1.6 μm、尺寸精度IT8, 采用粗铣——精铣Ra1.6μm——磨削Ra0.8μm。8处推杆导向孔 配合面,采用线切割加工。
3、零件的安装 8处推杆导向孔配合面,采用与动模板合并线切割加工。
模具制造技术
2020/10/22
(二)零件制造工艺设计
4、零件制造工艺路线(方案) 备料—锻造—退火—铣六面—磨六面—划线—铣台肩、成型面及 槽—修圆角钻穿丝孔—热处理—磨六面—线切割8处导向槽—研 圆角
5、确定各工序余量,计算工序尺寸及公差 6、热处理工序的安排
锻造后经过退火,消除应力,改善切削加工性;零件最终热处理
定端配合面Ra1.6 μm、尺
寸精度IT8。8处推杆导向孔
需要保证位置精度,并且与
推杆固定板一致。上、下表
塑料成型工艺与注射模具设计 (7)
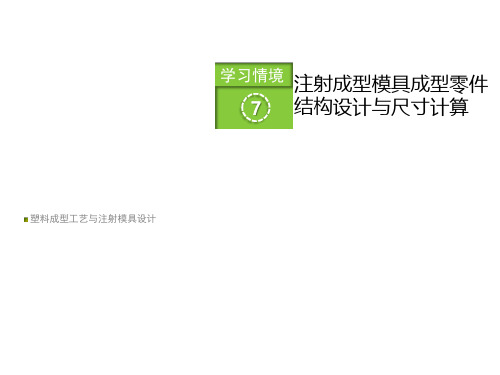
(一)凹模的结构设计
凹模是成型塑件外表面的凹状 零件(包括零件的内腔和实体两 部分)。
它的结构取决于塑件的成型需要和 加工与装配的工艺要求,通常可分为 整体式和组合式
整体式凹模是由整块钢材直接 加工而成的,其结构如图7-2所示。 这种凹模结构简单,牢固可靠, 不易变形,成型的塑件质量较好。 但当塑件形状复杂时,其凹模的 加工工艺性较差(采用一般机械 加工方法)。 因此,在先进的型腔加工机床 尚未普遍应用之前,整体式凹模 适用形状简单的小型塑件的成型。
齿轮型腔的结构设计 模具成型零件的尺寸计算
1
任务引入
图7-1所示为塑料壳体零件简 图,生产批量10万件。 请分小组确定成型零件的结构 并计算工作尺寸。
2
相关知识点
在进行塑料成型零件的结构设 计时,首先应根据塑料的性能和 塑件的形状、尺寸及其他使用要 求,确定型腔的总体结构、压缩 模的加压方向或压注模和注射模 的浇注系统及浇口位置、分型面、 脱模方式、排气等,然后根据塑 件的形状、尺寸和成型零件的加 工及装配工艺要求进行成型零件 的结构设计和尺寸计算。
2
相关知识点
(1)嵌入式组合凹模
1)整体嵌入式组合凹模 对于小型塑件采用多型腔塑料模 成型时,各单个凹模一般采用冷挤 压、电加工、电铸等方法制成,然 后整体嵌入模中,其结构如图7-3所 示。这种凹模形状及尺寸的一致性 好,更换方便,加工效率高,可节 约贵重金属,但模具整体体积较大, 需用特殊的加工法。 其中图7-3(a)、(b)、(c) 称为通孔台肩式,凹模带有台肩, 从下面嵌入凹模固定板,再用垫板 螺钉紧固。
图7-3
2
相关知识点
2)局部镶嵌式组合凹模 为了加工方便或由于型腔某一 部位容易磨损,需要更换部位采 用局部镶嵌的办法,如图7-4所示, 此部位的镶件可单独制成,然后 再嵌入模体。
型芯型腔加工工艺卡
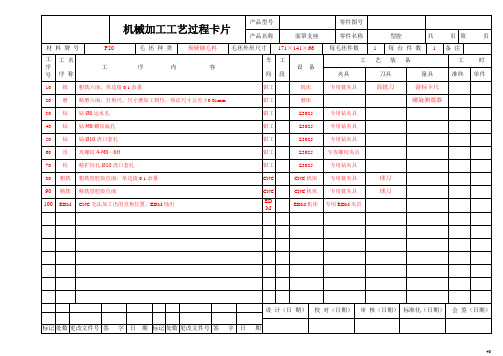
面罩支座
零件名称
型芯
共
页
第
页
材料牌号
P20
毛坯种类
预硬钢毛料
毛坯外形尺寸
171×141×79
每毛坯件数
每台件数
备注
工
序
号
工名
序称
工序内容
车
间
工
段
设备
工艺装备
工时
夹具
刀具
量具
准终
单件
10
铣
粗铣六面,单边留0.1余量
钳工
铣床
专用铣夹具
面铣刀
游标卡尺
20
磨
精磨六面,打角尺,尺寸磨加工到位,保证尺寸公差±0.01mm
钳工
磨床
螺旋测微器
30
钻
钻Ø8运水孔
钳工
Z3025
专用钻夹具
40
钻
钻M8螺纹底孔
钳工
Z3025
专用钻夹具
50
钻
钻Ø10浇口套孔
钳工
Z3025
专用钻夹具
60
攻
攻螺纹4-M8—6H
钳工
Z3025
专攻螺纹夹具
70
铰
精扩铰孔Ø10浇口套孔
钳工
Z3025
专用钻夹具
80
粗铣
粗铣型腔胶位面,单边留0.1余量
CNC
机械加工工艺过程卡片Fra bibliotek产品型号零件图号
产品名称
面罩支座
零件名称
型腔
共
页
第
页
材料牌号
P20
毛坯种类
预硬钢毛料
毛坯外形尺寸
171×141×66
每毛坯件数
SolidWorks模具设计,很简单
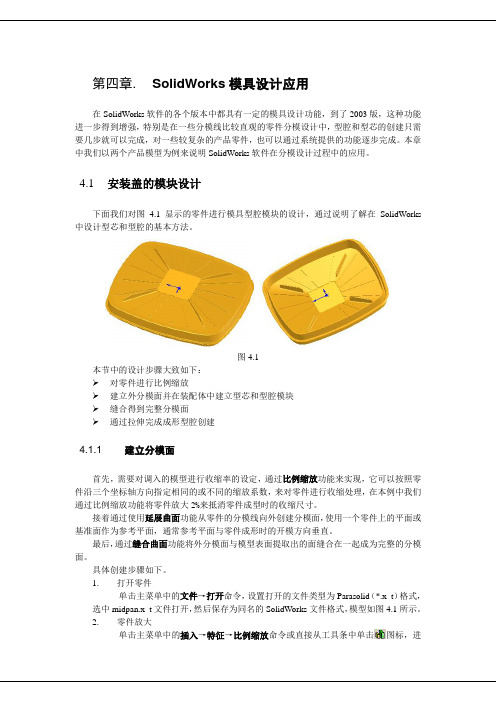
第四章.SolidWorks模具设计应用在SolidWorks软件的各个版本中都具有一定的模具设计功能,到了2003版,这种功能进一步得到增强,特别是在一些分模线比较直观的零件分模设计中,型腔和型芯的创建只需要几步就可以完成,对一些较复杂的产品零件,也可以通过系统提供的功能逐步完成。
本章中我们以两个产品模型为例来说明SolidWorks软件在分模设计过程中的应用。
4.1安装盖的模块设计下面我们对图 4.1显示的零件进行模具型腔模块的设计,通过说明了解在SolidWorks 中设计型芯和型腔的基本方法。
图4.1本节中的设计步骤大致如下:➢对零件进行比例缩放➢建立外分模面并在装配体中建立型芯和型腔模块➢缝合得到完整分模面➢通过拉伸完成成形型腔创建4.1.1 建立分模面首先,需要对调入的模型进行收缩率的设定,通过比例缩放功能来实现,它可以按照零件沿三个坐标轴方向指定相同的或不同的缩放系数,来对零件进行收缩处理,在本例中我们通过比例缩放功能将零件放大2%来抵消零件成型时的收缩尺寸。
接着通过使用延展曲面功能从零件的分模线向外创建分模面,使用一个零件上的平面或基准面作为参考平面,通常参考平面与零件成形时的开模方向垂直。
最后,通过缝合曲面功能将外分模面与模型表面提取出的面缝合在一起成为完整的分模面。
具体创建步骤如下。
1.打开零件单击主菜单中的文件→打开命令,设置打开的文件类型为Parasolid(*.x_t)格式,选中midpan.x_t文件打开,然后保存为同名的SolidWorks文件格式,模型如图4.1所示。
2.零件放大单击主菜单中的插入→特征→比例缩放命令或直接从工具条中单击图标,进入缩放设置界面,在其中选中统一比例缩放选项,输入缩放比例为1.02%,设定比例缩放点为重心或原点,如图4.2所示,单击确定按钮。
图4.23.建立延展曲面单击工具条中的图标,弹出延展曲面的设置界面,从特征树中选择前视图基准面作为参考平面,然后在要延展的边线列表中单击,选中零件分模线上的一条边,再勾选沿切面延伸选项,在延展距离中将默认的10mm改为30mm,如图4.3所示。
模具设计结构标准

兴旺模具模具设计结构标准一.产品排位1.1 产品的排位二.型芯尺寸结构2。
1 型芯的设计三.冷却水道结构3。
1 冷却水道的设计原则四.流道结构4。
1 喷嘴与定位环4。
2 流道的设计4.3 浇口的设计4.4 其它设计五.定位结构5.1 模板的定位5.2 镶针的定位六.开闭模控制结构6.1 小拉杆6。
2 拉板6。
3 尼龙扣七.滑块结构7.1 滑块的设计7。
2 滑块设计时应注意的问题7.3 滑块的结构八.滑块镶拼结构8.1 滑块镶拼的使用场合8.2 滑块镶拼的几种结构8.3 滑块的导向8.4 滑块压板设计8。
5 耐磨块的设计8。
6 楔紧块的设计九.斜顶结构9。
1 斜顶的设计原则9。
2 斜顶的结构与参数9。
3 斜顶设计时应注意的问题9。
4 斜顶导向9.5 斜顶座十.顶出结构10.1 顶针顶出结构10.2 司筒顶出结构10。
3 直顶顶出结构10。
4 顶块顶出结构10.5 推板顶出结构10.6 气顶顶出结构十一.模具加工及外观标准一.产品排位1.1产品的排位错误!一定要以节约为原则错误!应尽量避免滑块和斜顶产生多重角度,减少模具的加工难度。
○,3一模多腔时,应当优先考虑平衡排列,尽量减少流道的总长度保证塑料的流动性.错误!一模多腔时,当产品之间不通过流道时X、Y向之间的距离要保证在6~25mm,当产品之间过流道时X、Y之间的距离要保证在20~40mm。
二.型芯尺寸结构2。
1型芯的设计错误!在保证强度的前提下,尽可能节约成本。
错误!型芯强度设计标准,如表:错误!当设计深腔模具时,高度大于150mm以上的桶形产品.应考虑原身留的形式,模板之间互锁来加强模具的强度(比如电池槽模具结构)。
错误!型芯订购公差标准:当型芯用硬料(需要热处理的钢材),未热处理之前加工时必须必须把长、宽、高方向各加大0.5~1mm,以补偿热处理时产生的变形。
错误!当用预硬料型芯或硬料型芯热处理回来后必须在磨床修平后加工(六面卡拐),公差如下表:○6型芯螺丝的使用,当型芯的重量超出10kg时应当设计吊模螺丝。
- 1、下载文档前请自行甄别文档内容的完整性,平台不提供额外的编辑、内容补充、找答案等附加服务。
- 2、"仅部分预览"的文档,不可在线预览部分如存在完整性等问题,可反馈申请退款(可完整预览的文档不适用该条件!)。
- 3、如文档侵犯您的权益,请联系客服反馈,我们会尽快为您处理(人工客服工作时间:9:00-18:30)。
序号
工序名称
工序内容
1
备料
毛坯尺寸300*200*200
2
热处理
退火:HB180~220:调质:HRC28~32
3
洗削
洗六面,到要求尺寸
4
平面磨削
磨六面到要求尺寸
5
数控洗
1.加工各表面到相关要求尺寸
2.2.洗分流道及浇口到要求
3.切四角R10圆角到要求
6
钳加工
1.攻丝4—M26
2.打磨成型表面达图要求
2.型腔板零件图及其工艺
序号
工序名称
工序内容
1
备料
标准定模板,已备好加工基准
2
数控洗
1.洗200*100*100mm腔,周边余量0.1mm
2.2.钻孔,钻孔R13穿丝孔
3
线切割
到相关要求
4
钳工
1.划线
2.攻丝攻水孔端口螺纹丝到要求
3.打磨型腔