管线钢精炼渣系的开发与钢中磷硫氮全氧的控制
首钢京唐公司优质管线钢的生产工艺优化

因此 ,首钢京唐公司结合 自己的设备优势优 先采用以转炉 “ 全三脱”冶炼一L F炉精炼一R H 炉精炼一板坯连铸为主 的工 艺路线生产 X 8 0管
展 ,管道运输 已经成为最经济和最方便的主要运 输方 式之 一 ,从 而带 动 了管线 钢 的发 展 。 中国原 油 、成 品油 和天然 气 的运输 基 本上 已经实 现 了管 道运输 。但是与世界上工业发达国家相 比,国内 的管道 运 输在 质量 和数 量上 都存 在很 大差 距 。 中 国虽然 是 世界 的主 要石 油 出产 国之 一 ,但输 油 输 气的管道不足世界管线总长度的百分之一 ,而且 管 道 的输送 压力 低 、管 径小 。随着 我 国天然 气 资 源 的进 一 步开发 利 用 ,油气 管线 向长 距 离 、大 口 径发 展 是必 然趋 势 。根 据 国 内经 济发 展 战 略 ,天 然气长距离输送管道建设 已列入全国重点基础建 设项 目,计划 1 0年 内在 全 国建 设 近 1 0 0 0 0 k m 的管 线 ,预计 共 需管 材 1 0 0 0万 t 左 右 J 。 首钢京唐 钢铁联合 有 限责任 公司 ( 简称 首 钢京唐公 司 )产品定位 以满 足 国民经 济发展 和 国家产业政策 的需要为指导 ,以市场为导 向,建 设了 2 l 世纪国际先进水平 的精品板材基地 ,研
究 开 发优 质管 线 钢生产 技 术具 有重 要 的意 义 。 因
单庆林 :工 程师 。收稿/ 2 O表面缺陷改善等方面有显著提高 。钢 中硫 、磷和氮等元素的平均质量分数分别为 5 . 6 ×1 0 ~,7 9 . 6×1 0 ~,3 4 . 0×1 0 ~,中 间包 全 氧 含量 T [ O]为 1 5×1 0 I ¨ 。
P r o c e s s Op t i mi z a t i o n o f Hi g h Gr a d e P i p e l i n e S t e e l a t
脱氧及精炼渣系分析

• 研究内容: • 1)研究多种脱氧元素的最佳的配比,以控制 脱氧产物的形态,使其形成低熔点的液相脱氧 产物,易于聚合长大; • 2)研究熔池反应促进元素,以保证熔池内的 搅拌强度,促进钢水中夹杂物传输到钢/渣界 面,但同时也须保证熔池反应的平稳性,防止 反应剧烈导致的喷溅事故; • 3)研究精炼基渣——精炼剂,以保证脱氧产 物及时被熔池内的熔渣吸收,吸收氧化物后的 产物必须是低熔点物质,更有利于上浮排除; • 4)精炼剂必须呈高碱性,尽量减少脱氧产物 对钢包渣碱性的降低影响。
22
• 3.2钢包二次精炼剂 • 钢包二次精炼剂用于出钢后钢水在钢 包内的二次精炼作用。其主要作用为: 脱硫、脱氧、吸附夹杂。 • 根据使用钢种不同分为两大类: • *铝酸钙渣系 • *硅灰石渣系
23
• • • • • • • • • • • • •
1)铝酸钙渣系 成分及物性控制范围为: (CaO)50~60%、(FeO)<1%、 (Al2O3)16~35%、(MgO) 7~10%、 (SiO2)5~20%。 熔点1360~1400℃、粘度0.5~0.10P.S。 表面张力490~550×10-5 N/cm。 对粘度的控制,视精炼渣所要求的功能而异。 若以脱硫为主,精炼渣不仅硫容量要高,而且 粘度要低,有利于钢渣界面反应。若是以分离 夹杂为主,则粘度要高,避免渣与钢水混合, 以防二次氧化。所以精炼过程中应控制渣前期 粘度低、终渣粘度高。
11
• 2.4钙、钡脱氧: • 实践表明,含铝的脱氧剂中引入强脱
氧元素Ca可有效地对脱氧产生的高熔点夹 杂物进行变性处理,从而显著改善铝脱氧 钢液的流动性.但由于Ca自身尚存在着如 在钢中溶解度低、比重轻、蒸气压高等弱 点,如何提高其有效利用率成为确定脱氧 剂组成时必须考虑的问题,研究表明,Ba 元素不仅本身是具有比重大、蒸气压低的 强脱氧剂.而且与Ca完全互溶,并随其含 量的增加明显降低Ca的蒸气压.因此研制 和使用含钙的高钡低铝复合脱氧剂代表着 炼钢用脱氧剂的发展方向. 12
精炼渣系对钢中夹杂物的影响
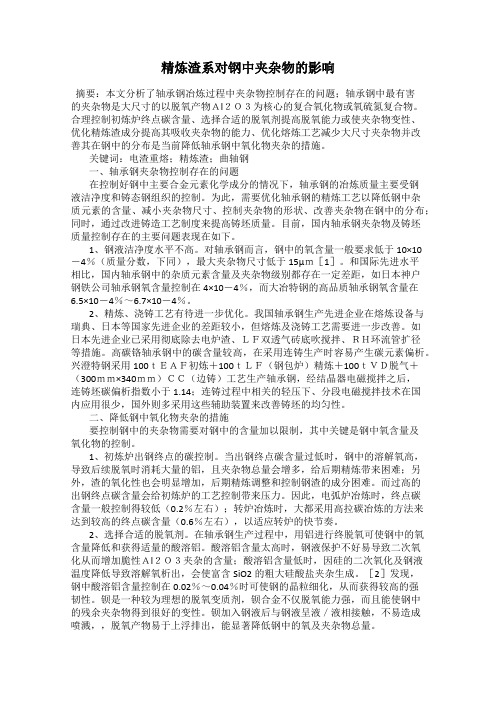
精炼渣系对钢中夹杂物的影响摘要:本文分析了轴承钢冶炼过程中夹杂物控制存在的问题;轴承钢中最有害的夹杂物是大尺寸的以脱氧产物Al2O3为核心的复合氧化物或氧硫氮复合物。
合理控制初炼炉终点碳含量、选择合适的脱氧剂提高脱氧能力或使夹杂物变性、优化精炼渣成分提高其吸收夹杂物的能力、优化熔炼工艺减少大尺寸夹杂物并改善其在钢中的分布是当前降低轴承钢中氧化物夹杂的措施。
关键词:电渣重熔;精炼渣;曲轴钢一、轴承钢夹杂物控制存在的问题在控制好钢中主要合金元素化学成分的情况下,轴承钢的冶炼质量主要受钢液洁净度和铸态钢组织的控制。
为此,需要优化轴承钢的精炼工艺以降低钢中杂质元素的含量、减小夹杂物尺寸、控制夹杂物的形状、改善夹杂物在钢中的分布;同时,通过改进铸造工艺制度来提高铸坯质量。
目前,国内轴承钢夹杂物及铸坯质量控制存在的主要问题表现在如下。
1、钢液洁净度水平不高。
对轴承钢而言,钢中的氧含量一般要求低于10×10-4%(质量分数,下同),最大夹杂物尺寸低于15μm[1]。
和国际先进水平相比,国内轴承钢中的杂质元素含量及夹杂物级别都存在一定差距,如日本神户钢铁公司轴承钢氧含量控制在4×10-4%,而大冶特钢的高品质轴承钢氧含量在6.5×10-4%~6.7×10-4%。
2、精炼、浇铸工艺有待进一步优化。
我国轴承钢生产先进企业在熔炼设备与瑞典、日本等国家先进企业的差距较小,但熔炼及浇铸工艺需要进一步改善。
如日本先进企业已采用彻底除去电炉渣、LF双透气砖底吹搅拌、RH环流管扩径等措施。
高碳铬轴承钢中的碳含量较高,在采用连铸生产时容易产生碳元素偏析。
兴澄特钢采用100tEAF初炼+100tLF(钢包炉)精炼+100tVD脱气+(300mm×340mm)CC(边铸)工艺生产轴承钢,经结晶器电磁搅拌之后,连铸坯碳偏析指数小于1.14;连铸过程中相关的轻压下、分段电磁搅拌技术在国内应用很少,国外则多采用这些辅助装置来改善铸坯的均匀性。
单位内部认证转炉炼钢工考试练习题及答案4_2023_背题版

***************************************************************************************试题说明本套试题共包括1套试卷每题均显示答案和解析单位内部认证转炉炼钢工考试练习题及答案4(500题)***************************************************************************************单位内部认证转炉炼钢工考试练习题及答案41.[单选题]经济炉役是指 的生产炉役。
A)高产量.耐火材料消耗高B)高炉龄.高产量、炉役时间长C)炉子生产率高.综合成本低答案:C解析:2.[单选题]耐火材料中气孔体积占材料总体积的百分率称为 。
A)致密度B)气孔率C)体积密度答案:A解析:3.[单选题]在脱硫剂消耗量与脱硫目标值恒定时,脱硫剂效率与原始硫成 。
A)正比B)反比C)无关答案:A解析:4.[单选题]1ppm=()。
A)0.0100%B)0.0010%C)0.00010%答案:C解析:5.[单选题]有关终点控制,下列说法正确的是( )。
A)终点控制实际上是指终点成分和温度的控制B)终点控制实际上是指终点氧含量和温度的控制6.[单选题]转炉大修完后烘炉时,一般采用()。
A)枕木烘炉法B)煤气烘炉法C)焦炭烘炉法答案:C解析:7.[单选题]碱性渣的黏度随温度升高( )。
A)降低不多B)先迅速下降,然后缓慢降低C)迅速升高答案:B解析:8.[单选题]炉帽有正口、偏口之分,近代转炉大多采用 炉帽。
A)正口B)小偏口C)大偏口答案:A解析:9.[单选题]铁水温度在1600℃时,其元素的氧化顺序( )。
A)Si、P、Mn、FeB)Si、Fe、P、MnC)Si、Mn、P、Fe答案:C解析:10.[单选题]铁水中影响转炉热量来源的最重要元素是( )。
A)硅B)碳C)磷答案:B解析:11.[单选题]在容易气体中毒的地方进行作业时,一般要求有( )。
满足钢中DS类等夹杂物及其他严格要求的生产实践

满足钢中DS类等夹杂物及其他严格要求的生产实践摘要经过前期研究钢中Ds类夹杂物的形成机理,配合电镜能谱分析,对比试验前后Ds类夹杂物种类及演变。
通过生产工艺优化试验,包括精炼渣系优化,硅钙线使用量等试验,形成可靠生产控制工艺。
满足客户严格要求,每炉检验四个样,铝脱氧非金属夹杂物B类粗系≤1.0级、DS类≤0.5级,淬透性A、B面差≤4HRC, Ti/N要求控制4~8等。
关键词 Ds类夹杂物非金属夹杂物钙处理铝脱氧高铝渣系镁铝尖晶石随着科技的快速发展,对原材料的质量要求日益提高,下游客户对钢中夹杂物含量的要求也越来越苛刻。
其中大型球状夹杂物(Ds类)会显著降低产品的疲劳寿命,然而在实际生产中处理不当就会产生Ds类夹杂物,且只要产生级别基本都>0.5级。
基于铝脱氧的钢种,在单炉次取样频次提高的基础上,B类夹杂物粗系≤1.0级也比较严格。
同时还要保障生产节奏及成分控制的稳定,以满足淬透性、Ti/N等要求。
为满足客户以上要求,结合装备、工艺,研究理论基础,通过前期的相关试验,制定相关攻关方案。
1.Ds类夹杂物形成机理及形貌研究表明Ds类夹杂物主要分为几种:一种为形核部位为镁铝尖晶石,外层钙铝酸盐的二层复合物;一种为心部含有钙铝酸盐,其外围附有CaS的二层复合物;再有就是三层复合物。
镁铝尖晶石(熔点2135℃)首先形成夹杂物的核心,钙铝酸盐(熔点1455-1875℃)包裹镁铝尖晶石,最外层为CaS。
镁铝尖晶石是构成Ds类夹杂物的主因之一,不含镁铝尖晶石的纯钙铝酸盐的Ds夹杂物仅占20%。
在显微镜下寻找大级别Ds类夹杂,再用SEM观察形态,并利用能谱分析定性鉴定以及电镜扫描,发现我公司轴承钢Ds类夹杂物分为几种:一是形核部位为镁铝尖晶石,外层钙铝酸盐的二层复合物(见图1+图2);二是Ca-Mg-Al-O复合态夹杂物(见图3);三是外包有硫化物的复合型夹杂物(见图4)。
其中第三类最多,并经常伴有Ba元素。
图1 镁铝尖晶石核心图2 外围钙铝酸盐图3 Ca-Mg-Al-O复合态夹杂物图4 外包有硫化物的复合型夹杂物2.控制Ds类夹杂物的工艺理论、优化及试验2.1转炉终点控制转炉终点C控制在0.10%以上,以降低钢中总氧量,从而避免出钢过程经铝强脱氧后,形成大量细小的Al2O3质点,为Ds类夹杂形成起到形核作用。
钢水精炼处理过程中化学成分的精确控制
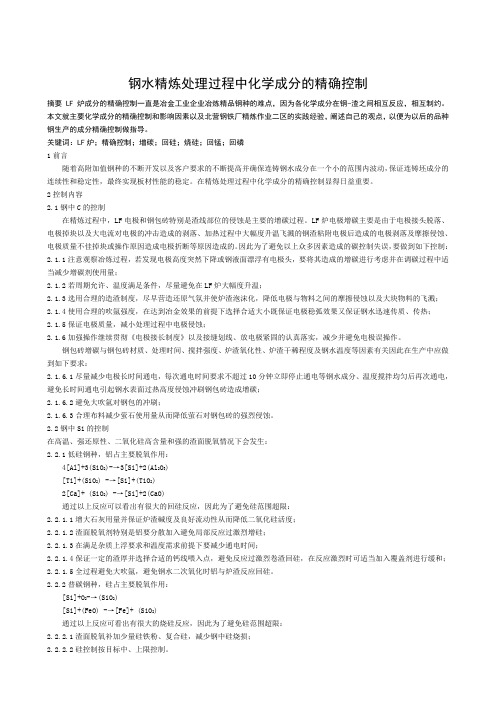
钢水精炼处理过程中化学成分的精确控制摘要 LF炉成分的精确控制一直是冶金工业企业冶炼精品钢种的难点,因为各化学成分在钢-渣之间相互反应,相互制约。
本文就主要化学成分的精确控制和影响因素以及北营钢铁厂精炼作业二区的实践经验,阐述自己的观点,以便为以后的品种钢生产的成分精确控制做指导。
关键词:LF炉;精确控制;增碳;回硅;烧硅;回锰;回磷1前言随着高附加值钢种的不断开发以及客户要求的不断提高并确保连铸钢水成分在一个小的范围内波动,保证连铸坯成分的连续性和稳定性,最终实现板材性能的稳定。
在精炼处理过程中化学成分的精确控制显得日益重要。
2控制内容2.1钢中C的控制在精炼过程中,LF电极和钢包砖特别是渣线部位的侵蚀是主要的增碳过程。
LF炉电极增碳主要是由于电极接头脱落、电极掉块以及大电流对电极的冲击造成的剥落、加热过程中大幅度升温飞溅的钢渣粘附电极后造成的电极剥落及摩擦侵蚀、电极质量不佳掉块或操作原因造成电极折断等原因造成的。
因此为了避免以上众多因素造成的碳控制失误,要做到如下控制:2.1.1注意观察冶炼过程,若发现电极高度突然下降或钢液面漂浮有电极头,要将其造成的增碳进行考虑并在调碳过程中适当减少增碳剂使用量;2.1.2若周期允许、温度满足条件,尽量避免在LF炉大幅度升温;2.1.3选用合理的造渣制度,尽早营造还原气氛并使炉渣泡沫化,降低电极与物料之间的摩擦侵蚀以及大块物料的飞溅;2.1.4使用合理的吹氩强度,在达到冶金效果的前提下选择合适大小既保证电极稳弧效果又保证钢水迅速传质、传热;2.1.5保证电极质量,减小处理过程中电极侵蚀;2.1.6加强操作继续贯彻《电极接长制度》以及接缝划线、放电极紧固的认真落实,减少并避免电极误操作。
钢包砖增碳与钢包砖材质、处理时间、搅拌强度、炉渣氧化性、炉渣干稀程度及钢水温度等因素有关因此在生产中应做到如下要求:2.1.6.1尽量减少电极长时间通电,每次通电时间要求不超过10分钟立即停止通电等钢水成分、温度搅拌均匀后再次通电,避免长时间通电引起钢水表面过热高度侵蚀冲刷钢包砖造成增碳;2.1.6.2避免大吹氩对钢包的冲刷;2.1.6.3合理布料减少萤石使用量从而降低萤石对钢包砖的强烈侵蚀。
炼钢过程中钢水氮含量控制
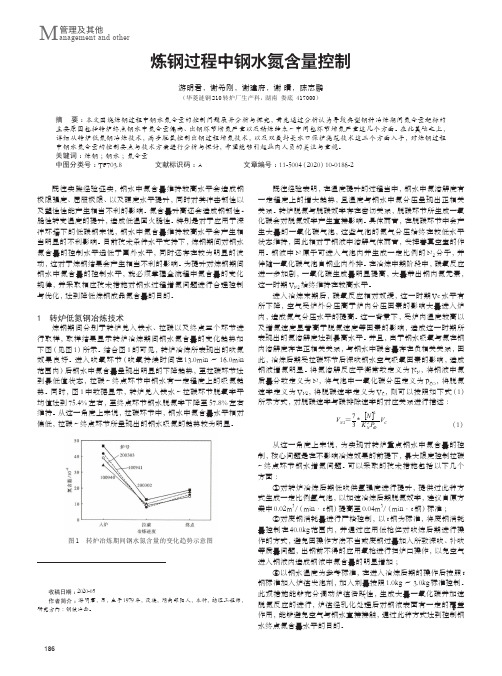
内,造成氮气分压水平的提高。这一背景下,受炉内温度较高以
及增氮速度显著高于脱氮速度等因素的影响,造成这一时期所
表现出的氮溶解度达到最高水平。并且,由于钢水吸氧与氮在钢
ቤተ መጻሕፍቲ ባይዱ
内溶解度存在正相关关系,与钢水中碳含量存在负相关关系,因
此,冶炼后期受拉碳环节后深吹钢水空气吸氧因素的影响,造成
钢液增氮明显。将氮溶解反应平衡常数定义为 KN,将钢液中氮 质量分数定义为 N,将气泡中一氧化碳分压定义为 PCO,将脱氮 速率定义为 VN2,将脱碳速率定义为 VC,则可以按照如下式(1) 所示方式,对脱碳速率与碳排除速率的对应关系进行描述 :
0.0*10-6 ~ 4.0*10-6
脱氧方式 不脱氧
11.0*10-6
3.0*10-6 ~ 22.0*10-6
12.0*10-6
5.0*10-6 ~ 22.0*10-6
铝铁脱氧
表 2 工艺优化前、后出钢环节增氮量示意表
平均值 11.3*10-6
应用前 区间
用。钢液中 N 原子可进入气泡内并生成一定比例的 N2 分子,并 伴随一氧化碳气泡自钢业内外排。在冶炼中期阶段中,碳氧反应
进一步加剧,一氧化碳生成量明显提高,大量带出钢内氮元素,
这一时期 VN2 始终维持在较高水平。 进入冶炼末期后,碳氧反应相对放缓,这一时期 Vc 水平有
所下降,空气受炉外分压高于炉内分压因素的影响大量进入炉
游明君,谢希刚,谢建府,谢 晴,陈志鹏
(华菱涟钢 210 转炉厂生产科,湖南 娄底 417000)
摘 要 :本文围绕炼钢过程中钢水氮含量的控制问题展开分析与探究,首先通过分析认为导致典型钢种冶炼期间氮含量超标的
主要原因包括转炉终点钢水中氮含量偏高、出钢环节增氮严重以及精炼结束 ~ 中间包环节增氮严重这几个方面。在此基础之上,
钢铁冶炼中的炼钢渣体系和控制方法
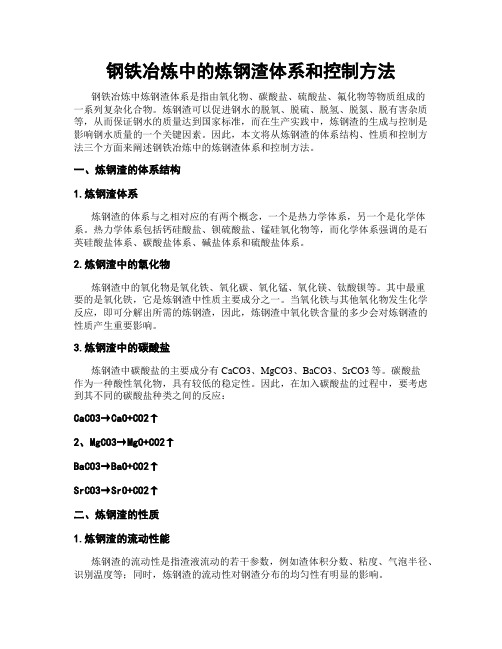
钢铁冶炼中的炼钢渣体系和控制方法钢铁冶炼中炼钢渣体系是指由氧化物、碳酸盐、硫酸盐、氟化物等物质组成的一系列复杂化合物。
炼钢渣可以促进钢水的脱氧、脱硫、脱氢、脱氮、脱有害杂质等,从而保证钢水的质量达到国家标准,而在生产实践中,炼钢渣的生成与控制是影响钢水质量的一个关键因素。
因此,本文将从炼钢渣的体系结构、性质和控制方法三个方面来阐述钢铁冶炼中的炼钢渣体系和控制方法。
一、炼钢渣的体系结构1.炼钢渣体系炼钢渣的体系与之相对应的有两个概念,一个是热力学体系,另一个是化学体系。
热力学体系包括钙硅酸盐、钡硫酸盐、锰硅氧化物等,而化学体系强调的是石英硅酸盐体系、碳酸盐体系、碱盐体系和硫酸盐体系。
2.炼钢渣中的氧化物炼钢渣中的氧化物是氧化铁、氧化碳、氧化锰、氧化镁、钛酸钡等。
其中最重要的是氧化铁,它是炼钢渣中性质主要成分之一。
当氧化铁与其他氧化物发生化学反应,即可分解出所需的炼钢渣,因此,炼钢渣中氧化铁含量的多少会对炼钢渣的性质产生重要影响。
3.炼钢渣中的碳酸盐炼钢渣中碳酸盐的主要成分有CaCO3、MgCO3、BaCO3、SrCO3等。
碳酸盐作为一种酸性氧化物,具有较低的稳定性。
因此,在加入碳酸盐的过程中,要考虑到其不同的碳酸盐种类之间的反应:CaCO3→CaO+CO2↑2、MgCO3→MgO+CO2↑BaCO3→BaO+CO2↑SrCO3→SrO+CO2↑二、炼钢渣的性质1.炼钢渣的流动性能炼钢渣的流动性是指渣液流动的若干参数,例如渣体积分数、粘度、气泡半径、识别温度等;同时,炼钢渣的流动性对钢渣分布的均匀性有明显的影响。
2.炼钢渣的稳定性炼钢渣的稳定性指的是渣液在一定条件下中不被分解、产生新的化学反应,能在限制条件下稳定存在的能力,同时炼钢渣的稳定性还与其流动性和抗渗透性等特点有关。
3.炼钢渣的还原性炼钢渣的还原性体现了其在高温下进行还原反应的倾向。
当加热时,炼钢渣中会产生还原性气体,例如CO和H2等,这些还原性气体在炼钢渣中与氧化铁等发生还原反应,从而影响炼钢渣的稳定性及其对钢水的影响。
- 1、下载文档前请自行甄别文档内容的完整性,平台不提供额外的编辑、内容补充、找答案等附加服务。
- 2、"仅部分预览"的文档,不可在线预览部分如存在完整性等问题,可反馈申请退款(可完整预览的文档不适用该条件!)。
- 3、如文档侵犯您的权益,请联系客服反馈,我们会尽快为您处理(人工客服工作时间:9:00-18:30)。
s ew sot l d ( 7 ×0 , t l a cn o e P 0 1 6 S≤2 l3 e rl ≤1 r 0 0 ,N≤5 ×0,t hl0 5 l3 . x 0 l 6 h w o  ̄ 0x0 r e e <
Ke o ds Pi e i e S e l Re n n l g S re ; Ha mf lElme t n r l S c n a y Rei i g y W r : p ln te ; i f igSa eis r u e n s Co to ; e o d r fn n
De eo m e fRe n n l g S re fPi lne St e nd Co t o v lp nto f i g S a e iso pei e la n r l i
P o p o u o e To a y e u f r a d Ni o e si t e h s h r ft t lOx g n S lu n t g n n S e l h r
o epo u t no eiig l eis (0 5 %C 0,6 1% S0 ,2 %- 5 1 3 %- %Mg ). fh rd ci f f n a S r t o R n Sg e 5 %- 5 a %- 0 i2 1 2 %A 2 ,5 8 0 0
Ac o d n ed s n o er f i gsa n i ei es e a r d ce , a d t eh r u l me t e c r i gt t e i f h i n l gma yp p l t l s o u t d n a mf l e n si t oh g t e n n e w p h e nh
21 生产 条件 .
10 双 工 位 L 5t F钢 包 精 炼 炉 、 1台 10 双 工 位 5t R H真 空 精 炼 炉 、 1台 2 0 2mm ̄ 0mm板 坯 连 150 铸 机 、 1台 2 0 mx 1m 板 坯 连 铸 机 、 1 2 m 180 m 台 7机 7流 小 方 坯 连 铸 机 。生 产 主要 原 材 料 见
WA G Z igo WE u - o A Gjn Q N S e g mio N h- u I n yu P N I h n - a J a
(o vr r te a igPa t C n et el kn ln) eS m
Ab t a t W ih Ca sr c : t 0—Al03 s 02p a ed a r m O7 2 e r to r a, d sg n e eo me t 2 - i h s i g a 1 Ca AI03 nea i n a e 2 g e in a d d v lp n
夹杂物进行有效控制的条件 。 [ 1 2 磷在管线钢  ̄ 3 中是一种易偏析 的元素 ,尤 其是钢中磷 的质量
分 数 大 于 10 1 时 ,磷 的偏 析 急剧 增 加 ,并 7x0
由于本次 X 0 6 的终端用户在使用性能上的要求 很高, 超过了 X 0 、硫、氮元素的控制要求也 比 较高 ( ≤ 磷
1 前
言
纹 ) 性 能 降低 。 同时 ,磷 还 恶 化 焊 接性 能 ,显 著 降 低 钢 的低 温 冲击 韧 性 ,提 高 钢 的脆 性 转 变
此 次柳 钢 生 产 的 X 0管 线 钢 要 求 对材 料 做 6
落锤撕裂试验 ,具有低温冲击韧性和 良好 的焊
接性 能 要 求 ,因此 ,要 求 冶 炼 的钢水 必须 具有
■
管线钢精炼渣系的开发与钢中磷硫氮全氧的控制
王志 国 韦军尤 庞 军 覃 胜苗
( 炉炼钢 厂) 转 摘 要 :结合 C O A : 。SO 相 图 1 a 7 1 , a - 1 -i2 0 2C O A2 生成 区域 ,设计 开 发 了管 线铜 生产 的精 炼渣 系 0
(0 5%C 0,6 1% SO,2%~5 1 3 %~%Mg ) 5%~5 a %~0 i 1 2%A2 ,5 8 0 O 。根 据设计 的精 炼渣 系大批 量生产 了管线 铜 ,并对钢 中的有害元 素进行 了控制 ( ≤1o1r 磷 7×c、硫 ≤2×0 6 0 1 、氮<5 ̄0、全氧  ̄5x0)  ̄ 0 1- 6 < 0 1-。 6 关键 词 :管线钢 ;精 炼渣 系 ;有 害元素控 制 ;二 次精炼
2 0 lr  ̄5x o、氮 ̄5 x o 0x C、硫 < 0 l 6 < 0 l5。 6
促使偏析带硬度增加 , 使钢材的 H C ( I 抗氢致裂
作 者 :王 志 国 ,大 学 学 历 ,工 程 师 ,现 在 转 炉 炼 钢
厂 炼 三车 间任 副 主任 。 台
I I n
2 冶炼 工 艺
来讲 ,只有 当钢 中硫质量分数降低到 2 x0 0 1 以
下 时 ,硫 对 钢 材 的 低 温 冲 击 韧 性 和 钢 材 的 H C I
性 能影 响才 可 以基 本 消除 。 [ 钢 中的氮 元 素对 4 1 钢 板 的焊 接 性 能 有 不 利 的 影 响 ,因此 ,希 望 将 钢 中的氮质 量控 制在 5x 0 0 1 以 内。
很 低 的磷 、硫 、氮和 全氧 。
温度 ,使钢发生冷脆 。硫是管线钢中最有害的
元 素 之 一 ,它可 以在 很 大 程 度 上 破 坏 钢 的低 温 冲击 韧性 以及 钢 材 的 HI 能 。对 于 中厚板 材 C性
管线 钢 的各 类 性 能要 求 决 定 了钢 材对 冶炼 钢水 洁 净 度 的要 求 很 高 【,选 择 合 理 的精 炼 渣 ” 系具 备 了对 钢 水 的全 氧 、硫 含 量 以及 各 类 有 害