国内外合成氨工艺技术现状及其发展
2024年合成氨市场发展现状
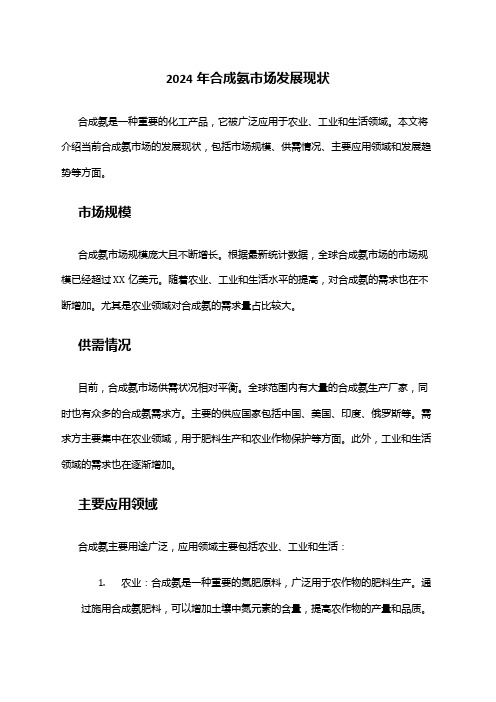
2024年合成氨市场发展现状合成氨是一种重要的化工产品,它被广泛应用于农业、工业和生活领域。
本文将介绍当前合成氨市场的发展现状,包括市场规模、供需情况、主要应用领域和发展趋势等方面。
市场规模合成氨市场规模庞大且不断增长。
根据最新统计数据,全球合成氨市场的市场规模已经超过XX亿美元。
随着农业、工业和生活水平的提高,对合成氨的需求也在不断增加。
尤其是农业领域对合成氨的需求量占比较大。
供需情况目前,合成氨市场供需状况相对平衡。
全球范围内有大量的合成氨生产厂家,同时也有众多的合成氨需求方。
主要的供应国家包括中国、美国、印度、俄罗斯等。
需求方主要集中在农业领域,用于肥料生产和农业作物保护等方面。
此外,工业和生活领域的需求也在逐渐增加。
主要应用领域合成氨主要用途广泛,应用领域主要包括农业、工业和生活:1.农业:合成氨是一种重要的氮肥原料,广泛用于农作物的肥料生产。
通过施用合成氨肥料,可以增加土壤中氮元素的含量,提高农作物的产量和品质。
2.工业:合成氨在工业领域有着广泛的应用。
它可以用于制造各种化工产品,如尿素、硝酸和硫酸等。
此外,合成氨还可以用作工业燃料和催化剂。
3.生活:在生活领域,合成氨主要用于制造清洁剂、洗涤剂和染料等产品。
它还可以用于制造冷却剂和制冷剂。
发展趋势随着全球经济的快速发展和人们对生活质量要求的提高,合成氨市场的发展前景广阔。
未来几年,预计合成氨市场将持续保持增长态势。
以下是一些市场发展的趋势:1.技术进步:随着科技的不断进步,合成氨生产技术将得到进一步改善和创新。
新技术的应用将提高合成氨的生产效率和质量。
2.环保意识增强:人们对环境保护的重视程度不断提高,对有害物质的排放和使用量进行严格限制。
因此,在合成氨生产过程中,将会出现更多的环保技术和设备应用。
3.农业需求增加:随着全球人口的增加和粮食需求的不断上升,对农业肥料的需求也将持续增加。
合成氨作为最重要的农业肥料材料之一,其需求也将随之增加。
合成氨工业发展现状及重要性
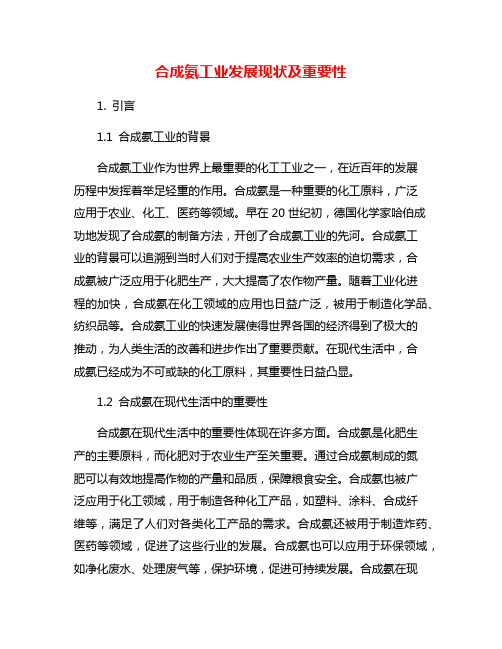
合成氨工业发展现状及重要性1. 引言1.1 合成氨工业的背景合成氨工业作为世界上最重要的化工工业之一,在近百年的发展历程中发挥着举足轻重的作用。
合成氨是一种重要的化工原料,广泛应用于农业、化工、医药等领域。
早在20世纪初,德国化学家哈伯成功地发现了合成氨的制备方法,开创了合成氨工业的先河。
合成氨工业的背景可以追溯到当时人们对于提高农业生产效率的迫切需求,合成氨被广泛应用于化肥生产,大大提高了农作物产量。
随着工业化进程的加快,合成氨在化工领域的应用也日益广泛,被用于制造化学品、纺织品等。
合成氨工业的快速发展使得世界各国的经济得到了极大的推动,为人类生活的改善和进步作出了重要贡献。
在现代生活中,合成氨已经成为不可或缺的化工原料,其重要性日益凸显。
1.2 合成氨在现代生活中的重要性合成氨在现代生活中的重要性体现在许多方面。
合成氨是化肥生产的主要原料,而化肥对于农业生产至关重要。
通过合成氨制成的氮肥可以有效地提高作物的产量和品质,保障粮食安全。
合成氨也被广泛应用于化工领域,用于制造各种化工产品,如塑料、涂料、合成纤维等,满足了人们对各类化工产品的需求。
合成氨还被用于制造炸药、医药等领域,促进了这些行业的发展。
合成氨也可以应用于环保领域,如净化废水、处理废气等,保护环境,促进可持续发展。
合成氨在现代生活中起着不可替代的作用,对农业、化工、医药、环保等领域都具有重要意义。
其发展和应用将继续推动社会经济的进步,为人类生活带来更多福祉。
2. 正文2.1 合成氨工业的发展历程合成氨工业的发展历程可以追溯到20世纪初,当时德国化学家哈伯和鲁认识到合成氨对提高农业生产的重要性。
他们成功地发现了一种合成氨的方法,这种方法后来被称为哈伯-鲁法。
在哈伯-鲁法的基础上,合成氨工业逐渐得到了发展。
20世纪初期,德国率先开始了商业化生产合成氨的尝试。
随后,其他国家纷纷效仿,建立起自己的合成氨工业基地。
第一次世界大战后,合成氨工业得到了进一步的发展,应用领域也逐渐扩大。
全球 合成氨产业发展趋势

全球合成氨产业发展趋势全球合成氨产业发展趋势1. 介绍合成氨产业的背景和意义合成氨是一种重要的化工产品,广泛应用于农业、能源和化学工业等领域。
作为世界上最重要的化工产品之一,合成氨的产业发展具有重要意义。
全球合成氨市场价值巨大,根据最新研究数据,到2025年,合成氨的全球市场规模有望达到500亿美元。
了解全球合成氨产业的发展趋势对于决策者和从业者都至关重要。
2. 全球合成氨产业的现状在全球范围内,合成氨产业呈现出一系列显著特点和趋势:a) 全球需求量不断增长:由于人口增长和农业生产需求的增加,全球对合成氨的需求与日俱增。
农用合成氨的需求尤为突出,它被广泛应用于农作物的肥料生产,以提高农作物的产量和质量。
b) 生产技术不断创新:随着科技的进步,合成氨的生产技术也在不断创新。
传统的合成氨生产工艺已经得到优化,通过改进反应条件和催化剂的性能,可以提高合成氨的生产效率和质量。
c) 持续推进可持续发展:全球范围内,环境保护和可持续发展已经成为产业发展的重要方向。
合成氨产业也积极响应这一趋势,通过采用更环保的生产技术和减少二氧化碳排放,实现绿色合成氨的生产。
d) 行业竞争加剧:全球范围内合成氨产业竞争日益激烈。
主要产业集中在亚洲地区,中国和印度成为全球合成氨的主要生产国家。
在这种竞争环境下,企业需要不断提高生产效率和质量,提供更具竞争力的产品。
3. 全球合成氨产业的发展趋势在未来几年,全球合成氨产业将呈现以下发展趋势:a) 市场规模持续扩大:随着全球农业生产的增加和新兴市场的崛起,对合成氨的需求将持续增长。
尤其是在亚洲地区,农业的快速发展将进一步推动合成氨的市场规模扩大。
b) 技术创新助力产业升级:新技术的引入将使合成氨生产更加高效和环保。
采用新型催化剂和反应工艺可以提高合成氨的转化率和选择性,降低能耗和废弃物排放。
c) 绿色合成氨的兴起:在环境保护压力下,绿色合成氨的发展将成为合成氨产业的重要方向。
通过采用氢气和氮气的电解合成氨技术,未来有望实现零排放的合成氨生产。
合成氨工艺技术的现状及其发展趋势
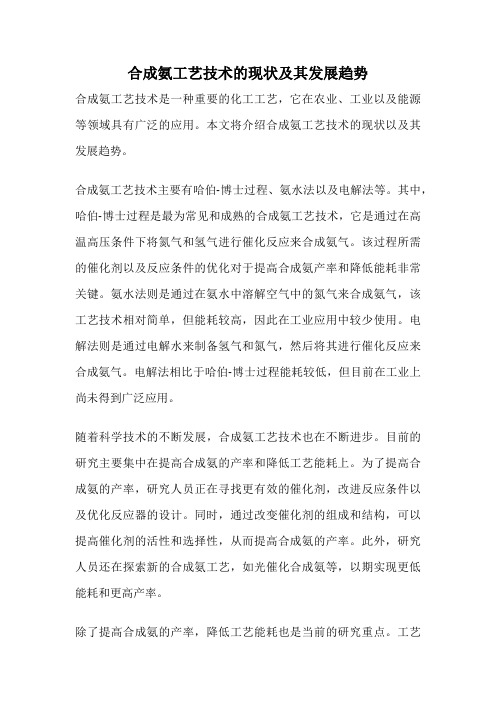
合成氨工艺技术的现状及其发展趋势合成氨工艺技术是一种重要的化工工艺,它在农业、工业以及能源等领域具有广泛的应用。
本文将介绍合成氨工艺技术的现状以及其发展趋势。
合成氨工艺技术主要有哈伯-博士过程、氨水法以及电解法等。
其中,哈伯-博士过程是最为常见和成熟的合成氨工艺技术,它是通过在高温高压条件下将氮气和氢气进行催化反应来合成氨气。
该过程所需的催化剂以及反应条件的优化对于提高合成氨产率和降低能耗非常关键。
氨水法则是通过在氨水中溶解空气中的氮气来合成氨气,该工艺技术相对简单,但能耗较高,因此在工业应用中较少使用。
电解法则是通过电解水来制备氢气和氮气,然后将其进行催化反应来合成氨气。
电解法相比于哈伯-博士过程能耗较低,但目前在工业上尚未得到广泛应用。
随着科学技术的不断发展,合成氨工艺技术也在不断进步。
目前的研究主要集中在提高合成氨的产率和降低工艺能耗上。
为了提高合成氨的产率,研究人员正在寻找更有效的催化剂,改进反应条件以及优化反应器的设计。
同时,通过改变催化剂的组成和结构,可以提高催化剂的活性和选择性,从而提高合成氨的产率。
此外,研究人员还在探索新的合成氨工艺,如光催化合成氨等,以期实现更低能耗和更高产率。
除了提高合成氨的产率,降低工艺能耗也是当前的研究重点。
工艺能耗的降低可以通过改进反应条件、优化反应器的设计以及改良催化剂等手段来实现。
此外,研究人员还在探索利用可再生能源和废弃物资源来替代传统的氢气制备方法,以进一步降低工艺能耗。
在未来,合成氨工艺技术的发展趋势将主要集中在以下几个方面。
首先,随着对环境保护意识的提高,研究人员将更加注重合成氨工艺的环境友好性,努力开发低碳排放的合成氨工艺。
其次,研究人员将继续探索新的催化剂和反应条件,以提高合成氨的产率和选择性。
最后,随着能源资源的日益紧缺,研究人员将更加关注合成氨工艺的能耗问题,努力寻找新的能源替代品,以降低工艺能耗。
合成氨工艺技术是一项重要的化工工艺,它在农业、工业以及能源等领域具有广泛应用。
合成氨工业发展现状及重要性

合成氨工业发展现状及重要性首先,合成氨工业的发展现状。
合成氨工业在全球范围内具有广泛的应用和重要性。
目前,世界上最常用的合成氨工业方法是哈伯-波仑法。
该法利用铁钼催化剂,以高温高压条件下,将氮气和氢气进行催化反应,生成氨气。
这种方法具有产量高、工艺简单等优点,被广泛应用于全球各地的合成氨厂。
然而,合成氨工业也面临一些挑战。
首先,合成氨是高能耗产业,需要大量的氢气和氮气作为原料。
氢气的制备主要依赖于化石燃料,会产生大量的二氧化碳排放,给环境带来负面影响。
其次,合成氨的催化剂需要高温高压条件下操作,会对设备和工艺提出较高的要求。
此外,合成氨产业还面临市场需求波动和价格波动等风险。
其次,合成氨工业的重要性。
合成氨是化肥的主要原料,化肥在农业生产中具有重要的作用。
据统计,全球85%的合成氨用于制造化肥,其中又以尿素为主要产品。
化肥的使用可以提高土壤肥力,促进植物生长,提高农作物产量,对解决粮食安全和人类生存问题具有重要意义。
合成氨工业的发展对农业生产具有重要支撑作用。
此外,合成氨还广泛应用于其他领域。
合成氨可以用作制造塑料、化纤、橡胶等合成材料的原料,具有重要的工业应用。
合成氨还可以用于制造染料、颜料、医药中间体、炸药等化工产品。
合成氨工业的发展对推动其他化工行业的发展也具有重要影响。
综上所述,合成氨工业在全球范围内具有广泛的应用和重要性。
合成氨作为化肥的主要原料,在农业生产中具有重要作用。
合成氨工业的发展还对其他化工行业和工业生产有着重要推动作用。
然而,合成氨工业仍面临一些挑战,包括能源消耗、环境影响等问题。
因此,未来合成氨工业需要进一步推动技术创新,减少能源消耗和环境污染,实现可持续发展。
中国合成氨行业的现状和发展趋势

中国合成氨行业的现状和发展趋势中国的合成氨行业是化学工业的重要组成部分,广泛应用于农用化肥、化工原料、塑料制品等领域。
本文将从现状和发展趋势两个方面对中国合成氨行业进行分析。
一、现状1.产能和生产规模:中国合成氨行业的产能和生产规模在全球处于领先地位。
数据显示,目前中国的合成氨年产能已超过5000万吨,占全球总产能的40%以上。
2.技术水平:中国合成氨行业在技术水平方面也有显著进步。
早期,中国合成氨主要采用卡夫实验室氨合成工艺,但现在已逐渐发展成为以煤炭、天然气为原料的大型化工企业,采用国际先进的合成氨技术,如哈贝法等。
3.国内市场需求:中国作为农业大国,农用合成氨需求量巨大。
由于农业机械化和现代化水平的提高,以及土壤肥力的下降,中国对合成氨的需求将会持续增长。
二、发展趋势1.生产技术:中国合成氨行业将继续提高生产技术水平,加大对新型合成氨工艺的研究和开发,努力降低生产成本,提高产品质量。
2.环境友好型:合成氨是传统化工产品,对环境的影响比较大。
随着环保意识的增强,中国合成氨行业将更加注重环保问题,推动绿色生产,减少污染物的排放。
3.产业升级:合成氨行业将向高端产品和高附加值链条延伸。
除了农用化肥,合成氨还可用于生产尿素、合成氨甲酸等有机化工产品。
同时,合成氨在新能源、新材料等领域也有广阔的应用前景。
4.供给侧:中国合成氨行业将加速供给侧结构性,通过淘汰落后产能、整合资源,推动行业集中度的提高。
同时,政府还鼓励产业园区的建设,提供更好的产业环境和政策支持。
总之,中国合成氨行业在稳步发展的同时,也面临着挑战和机遇。
只有加强科技创新,推动绿色发展,进一步提高产品质量和技术水平,才能在国际市场上保持竞争优势。
合成氨工艺技术的现状及发展趋势
合成氨工艺技术的现状及发展趋势摘要:本文首先阐述了我国合成氨工艺技术现状,接着分析了合成氨的工艺流程,最后对合成氨工艺技术的发展趋势进行了探讨。
希望能够为相关人员提供有益的参考和借鉴。
关键词:合成氨;工艺技术;发展趋势引言:合成氨催化技术是制作化工产品的主要技术,在生产制造氮肥、铵态化肥、硝酸化肥等产品中得到了十分广泛的运用。
在我们国家对化工产业提出了节能减排要求之后,合成氨催化技术也获得了更加有效的提升与完善,今后此项技术将会应用于更多的加工制造产业中。
1我国合成氨工艺技术现状最早的合成氨技术起源于20世纪初,那时合成氨技术主要是用于战争当中,因为炸药的原料之一就是合成氨。
现代的合成氨技术,则主要运用在农业和现代化学当中。
合成氨技术最早出现在我国,是在20世纪30年代。
那时,我国在合成氨工艺技术方面还比较落后,如今我国合成氨技术已经在全世界占有较高的地位。
在合成氨构成原料方面,我国掌握的种类也比较多,无论是利用无烟煤天然气还是油田等材料,都可以用来生产合成氨。
由于我国经济技术的不断发展,对于合成氨的需求量也日益增加。
同时,因为我国在合成氨工艺技术方面已经有较高的水平,所以目前合成氨的产量已经能够满足人们的日常生活需求。
在合成装置方面,因为我国引进的设备在世界领域中比较先进,所以在合成氨合成装置设备上,我国已经占有了绝大的优势,其也增强了我国在国际上的综合竞争力。
2合成氨的工艺流程分析2.1原料气的制取制作合成氨的原材料主要是天然气、重油、石脑油等。
不管是哪一种原材料都可以用来代表。
这些原材料在水蒸气和高温下形成将一氧化碳与氢作为主体的合成氨原材料气。
我们国家制作合成氨原料气的主要方式为煤气化法。
这种方法主要是利用氧、蒸汽以及其他汽化剂高温处理煤,促使其转变成一氧化碳和氢等可以燃烧的气体。
对气态烃类,工业中通常使用二段蒸汽转化法加工制造合成气。
重油部分的氧化法主要是将重油作为原材料,而气态烃类主要是不完全燃烧氧气,促使烃类在高温的作用下出现燃烧和裂解现象,出现的二氧化碳和水蒸气在高温的作用下和甲烷发生转化反应,进而取得将氧化碳和氢气作为主要原料的合成气。
我国合成氨生产工艺技术现状
我国合成氨生产工艺技术现状2009年07月10日09:271装置现状我国合成氨装置是大、中、小规模并存的格局,总生产能力为4260万t/a。
大型合成氨装置有30套,设计能力为900万t/a,实际生产能力为1000万t/a;中型合成氨装置有55套,生产能力为460万t/a;小型合成氨装置有700多套,生产能力为2800万t/a。
目前我国已投产的大型合成氨装置有30套,设计总能力为900万t/a,实际生产能力为1000万t/a,约占我国合成氨总生产能力的23%。
除上海吴泾化工厂为国产化装置外,其余均系国外引进,荟萃了当今世界上主要的合成氨工艺技术,如以天然气和石脑油为原料的凯洛格传统工艺(9套)、凯洛格-TEC工艺(2套)、托普索工艺(3套)、节能型的AMV工艺(2套)和布朗工艺(4套);以渣油为原料的德士古渣油气化工艺(4套)和谢尔气化工艺(3套);以煤为原料的鲁奇粉煤气化工工艺(1套)和德士古水煤浆气化工艺(1套)。
我国大型合成氨装置所用原料天然气(油田气)占50%,渣油和石脑油占43%,煤占7%,其下游产品除1套装置生产硝酸磷肥外,其余均生产尿素。
70年代引进的大型合成氨装置均进行了技术改造,生产能力提高了15%~22%,合成氨吨综合能耗由41.87GJ降到33.49GJ,有的以石油为原料的合成氨装置(如安庆、金陵、广石化)用炼油厂干气顶替一部分石脑油(每年大约5 万t)。
另外,我国还有3套大型合成氨装置在建,南化公司计划投料,吉化在设计中,卢天化公司购买的墨西哥二手设备在着手建设,届时,我国大型合成氨装置总生产能力将达1205万t/a。
我国中型合成氨装置有55套,生产能力为460万t/a;约占我国合成氨总生产能力的11%,下游产品主要是尿素和硝酸铵,其中以煤、焦为原料的装置有34套,占中型合成氨装置的62%;以渣油为原料的装置有9套,占中型合成氨装置的16%;,以气为原料的装置有12套,占中型合成氨装置的22%;我国小型合成氨装置有700多套,生产能力为2800万t/a,约占我国合成氨总生产能力的66%,原设计下游产品主要是碳酸氢铵,现有112套的装置经改造生产尿素。
合成氨工业发展现状及重要性
合成氨工业发展现状及重要性合成氨是一种重要的化工原料,广泛应用于农业、化工、医药、能源等行业。
合成氨工业的发展现状和重要性如下。
合成氨工业的发展现状:1. 产量增长:合成氨是全球最大的化工品之一,每年的产量约为1亿吨。
中国是全球最大的合成氨生产国,其产量占到全球总产量的65%以上。
其他重要的合成氨生产国包括印度、美国、俄罗斯等。
2. 技术进步:合成氨工业经历了从传统的合成氨法到现代的合成氨法的发展。
传统的合成氨工业采用哈柏-博仑法,该方法存在能耗高、反应选择性差等问题。
现代的合成氨工业主要采用哈柏-博仑法的改进方法和奥朗斯法。
这些方法优化了反应条件,提高了合成氨的产率和选择性。
3. 综合利用:合成氨工业的发展也注重综合利用。
传统的合成氨工业中,一部分氮气和氢气无法完全转化为合成氨,被释放到大气中,造成资源浪费和环境污染。
现代的合成氨工业引入了废气回收和催化使气工艺,将废气中的氮气和氢气转化为合成氨,提高了资源利用效率。
合成氨工业的重要性:1. 农业应用:合成氨是生产氮肥和农药的重要原料。
氮肥是农作物生长中的重要营养元素,合成氨的生产为农业提供了充足的氮肥资源,提高了农作物产量。
合成氨还可以用于生产替代化肥的有机肥料,减少了化学肥料对环境的污染。
2. 化工应用:合成氨广泛应用于化工行业生产中。
合成氨可以制成硝酸、尿素、甲醇、丙醇等多种重要化工产品。
这些产品被应用于涂料、塑料、橡胶、染料等化工领域,推动了化工行业的发展。
3. 能源应用:合成氨还可作为能源的媒介。
合成氨可以在低温下储存和输送氢气,作为氢能的载体。
在氢能发展的初期,合成氨提供了可行的氢能储存和输送方案,并为氢能技术的研究提供了便利。
4. 环境保护:合成氨工业的发展也注重环境保护。
通过废气回收和催化使气工艺,合成氨工业减少了废气的排放,提高了氮气和氢气的利用效率。
合成氨工业还可以通过废热利用和能源回收等技术,减少能源消耗,实现绿色发展。
合成氨工业的发展现状良好,具有重要的经济和社会意义。
合成氨国内外综述
合成氨国内外综述第一篇:合成氨国内外综述二、设计项目的国内外研究综述及及设计项目的背景、意义和应用前景1、国内研究概况和发展趋势我国的氮肥工业自20世纪50年代以来,不断发展壮大,目前合成氨产量已跃居世界第一位,现已掌握了以焦炭、无烟煤、焦炉气、天然气及油田伴生气和液态烃多种原料生产合成氨的技术,形成了特有的煤、石油、天然气原料并存和大、中、小生产规模并存的生产格局。
我国合成氨在与国际接轨后,具备与国际合成氨产品竞争的能力,今后发展重点是调整原料和产品结构,其技术发展将会继续紧密围绕“降低生产成本、提高运行周期,改善经济性”的基本目标,进一步集中在“大型化、低能耗、结构调整、清洁生产、长周期运行”等方面进行技术的研究开发,进一步改善经济性。
(1)国内天然气蒸汽转化工艺国内就天然气蒸汽转化制氨工艺而言,其发展主要是以节能、降耗、扩产、缩小装置尺寸、降低投资费用以及延长运转周期等为目标进行工艺改进。
例如:将传统流程转化炉的热效率从原有的85%提高到90%~92%,烟气排出温度降至120~125 ℃,增加燃烧空气预热器等;提高一段炉操作压力,由原来的2.8MPa提高到4.0~4.8MPa;转化炉管采用新型材料25Cr235Ni2Nb2Ti,使管壁厚度降低,并使管壁中因温度梯度造成的热应力降低至接近内部压力的水平;增加二段炉燃烧空气量,提高燃烧空气温度至610~630 ℃,采用性能更好的二段燃烧器。
而在转化催化剂方面,主要是围绕不同原料和不同工艺开发新型转化催化剂,并且还要保证开发的新催化剂在适合于不同原料和工艺的前提下,提高催化剂的活性、抗压强度、抗碳性和抗毒性等。
(2)国内天然气脱硫工艺在我国,天然气脱硫是比较成熟的技术,其脱硫方法也很多。
大体上可分为干法脱硫和湿法脱硫两种方法,干法脱硫以氧化铁法和活性炭法应用较广,而湿法脱硫以砷碱法、ADA、改良ADA和栲胶法颇具代表性。
干法脱硫技术最早应用于煤气脱硫。
- 1、下载文档前请自行甄别文档内容的完整性,平台不提供额外的编辑、内容补充、找答案等附加服务。
- 2、"仅部分预览"的文档,不可在线预览部分如存在完整性等问题,可反馈申请退款(可完整预览的文档不适用该条件!)。
- 3、如文档侵犯您的权益,请联系客服反馈,我们会尽快为您处理(人工客服工作时间:9:00-18:30)。
谢谢观看!
60
50
40
30
20
10
0
加权平均
煤
天然气
油
焦炉气
2006 2007 2008
2.4 不同原料、不同规模,装置能耗逐年降低
大型合成氨天然气工艺最低综合能耗30GJ/t.NH3,煤气 化工艺最低在49 GJ/t.NH3;
中小规模最先进的企业吨氨消耗:原料煤耗1119千克、 电耗1278 千瓦时,综合能耗与大型水煤浆加压气化装置 指标基本相当。
新建天然气、煤原料的大型合成装置单套能力达到50万t/a;
中小规模装置逐步调整改造达到8-18-30万t/a。企业数量由 1500多家,减少至435家。
2008年不同规模合成氨产量比例
单厂产量 (万吨)
≥50 ≥ 30 ≥ 18 ≥8
<8 Sum
企
业
产量
数
7
462.72
33
1486.97
80
较先进的技术。
上世纪七八十年代引进的装置,经过节能和增产技术改造,产能、消
耗、质量、环保等仍处于国内领先水平;主要技术经济指标仍可跟踪 上世界先进工艺技术的水平。
以油为原料的装置在结构调整中,引入洁净煤气化技术提升了原料多
元化进的技术水平。
大型合成氨生产技术荟萃了当今世界上主要的先进工艺技术,是世界
贸易量(百万吨)
2006-2008年合成氨贸易量
160 140 120 100
80 60 40 20
0
2006
2007 年份
2008估计
产量 贸易量 海运贸易量
1.2 合成氨贸易量及利用
每年全球合成氨贸易量约占总产量的12%以上。2008年
约为1870万吨,比2007年下降2.4%。
中国的商品液氨很少,主要用于生产肥料,非肥料需求不
3 合成氨工业的发展趋势
合成氨工业是化肥工业的基础,其发展要与农业、资源和环境 相协调。重点仍是推动结构调整、创建资源节约型和环境友好 型产业, 提高竞争力,实现可持续发展。
一是结构调整 产业组织结构向规模化、集团化方向发展 新建装置产能布局向资源地、消费集中地转移 装置结构优化,能耗高、环保落后装置逐步淘汰 原料结构合理适宜,拓宽资源利用范围
2.3 注重技术改造,节能降耗和改善装置运行水平
烟气余热回收技术 换热转化工艺技术; 新型蒸汽转化催化剂 合成回路增设分子筛干燥器; 深冷分离或膜分离 新型高效节能型转子、先进防喘振控制和调速
系统; 大机组状态监测和故障诊断技术; 工艺余热回收
不同原料的合成氨综合能耗(GJ/吨氨)
到10%,用于浓硝酸、己内酰胺、丙烯腈等。
2008年合成氨产量规模比例 (%)
35 30 25 20 15 10
5 0
≥50万吨 ≥ 30万吨 ≥ 18万吨 ≥ 8万吨
<8万吨
2007 2008
1.3 合成氨装置大中小并存,规模趋于合理
引进合成氨装置经扩能改造,单套日产能力提高20%-50%, 年产45万t/a。
2007
年份
2008
全球总计 中国总计 大型装置
1.1 产能快速增长
中国现有合成氨生产企业 522个,2008年合成氨总产能约5700万吨,2009年 底预计达到6000万吨以上。
产能增加主要是新建装置和部分装置扩能改造的贡献。
2008年合成氨产量5050万吨,占世界总产量1.53亿吨的33%,居世界首位。
国内外合成氨工艺技术现状及其发展
主要内容
1、 合成氨工业的概况 2 、 合成氨工业技术进步 3 、 合成氨工业的发展趋势
1 合成氨工业的概况
2005年-2008年合成氨产量
产量(万吨)
18000 16000 14000 12000 10000
8000 6000 4000 2000
0
2005
2006
上原料路线和工艺技术最全的国家。
中小型合成氨装置工艺技术、装备水平通过技术改造和结构调整得到
提升。
2.2 开发创新,提升成套工艺与装备技术水平
以煤为原料30万吨/年合成氨工艺 以天然气为原料的20万吨/年合成氨工艺 国产大型空分装置成套技术 煤碳气化技术和装备 酸性气体脱除技术 高浓度一氧化碳耐硫变换工艺和催化剂技术 合成氨系列大型机组国产化 国产合成氨系列催化剂技术
煤炭+石油焦
65
76.3
77.2
77.2
石脑油(燃油)
21
2.0
2.0
2.1
焦炉气
0.4
0.6
0.6
全球合成氨原料结构占产能的比例(%)
天然气 煤炭+石油焦
2000 72 20
石脑油(燃油)
8
2008 66 28
6
2013 68 28
5
2 合成氨工业技术进步
2.1 总体技术水平不断提高
大型合成氨装置均为引进装置,不同年代引进的装置均代表了当期比
2584.88
201
3954.67
321
1094.84
522
5049.51
占全国 (%)
9.16 29.45 51.19 78.32 21.68 100.00
ห้องสมุดไป่ตู้
1.4 原料以煤为主,适合中国资源特点
合成氨原料结构占产能的比例(%)
年份
2000
2006
2007
2008
天然气
14
21.3
20.2
20.1