直接还原铁代替废钢在鞍钢的践行与业绩
炼钢用直接还原铁的研制与应用

d e n n % b n ig a e t T e h i c y r d c d io s ma u a t r d b tr p o e swi xe a h a t o u iga d 1 i d n g n . h n te d r t u e rn i n fc u e y r o t rc s t e tr l e tmeh d el e e h n
分与铁精矿粉混合制成球团矿或烧结矿供高炉使用 , 另一部分直接供转炉使用, 不能实现氧化铁皮的高效
利用 。包钢耐 火厂现 有两条 9 1 10m 的隧道 0m、 条 2 窑。若 以氧化铁皮为原料 , 焦粉为还原剂 , 采用隧道窑 生产还 原铁。不仅可 以给转 炉炼钢提 供优 质原料 , 实 现氧化 铁皮资源 的有效利用 , 有利 于耐火 厂产业 而且
按配方准确称量 氧化 铁皮 及 还原剂 倒人 试验 室 小混沙机 内, 然后外 加 1 %的糊精 , 干混 5mn然后加 i, 人 20 的水继续混合 5mi .% n出料 , 10t 在 0 液压机上
以 20k 2 N的压 力压制成型 5 n 5 l O/ n× 0in试样 , l n 置
Ab t a t T e mo l e ln sa e p e s d b ln ig w t rn s a e a a tra . d i g2 sr c : h ud d ba k r rs e y b e d n i io c l sr w mae i1 a d n % a c l r t o e h c ee a rr — n f
o d c in o 8  ̄ n o k n i f8 h. h c o d r p a e s e c a n se l fr u t f1 2 0 C a d s a ig t e o me o w ih c u e l c t ls rp i t e —met gwi o v r r . l e ln t c n et s i h e
直接还原铁生产工艺的分析

直接还原铁生产工艺的分析世界上直接还原铁生产技术已经成熟, 技术发展极为迅速, 根据Midrex 公司预测, 2010年全世界直接还原铁产量将超过7300万t。
于高炉流程存在着生产成本过高和环境污染的两大难题, 炼铁工艺由高炉流程逐步向直接还原铁短流程过渡已成为定局。
当今的钢铁企业对这一革命性技术工艺越早开发越能占据主动; 不敢承担风险, 迟疑不前, 必将处于被动和落后的局面。
因此, 直接还原铁的开发不是“有所为”和“有所不为”的问题, 而是生产工艺的选择问题。
1 世界直接还原铁生产技术现状1.1 生产工艺发展态势由于某些国家天然气资源丰富, 直接还原铁生产技术在南美洲、南非和东南亚诸国的发展极为迅速,而印度则后来居上; 特别是委内瑞拉、墨西哥等国, 生产历史已超过20余年, 生产规模不断扩大, 直接还原铁产量已占本国钢铁产量的绝对份额; 而奥钢联、韩国合作开发的直接还原与熔融还原技术与日俱进; 浦项钢铁公司的直接还原铁生产大有代替高炉炼铁之势。
对这样的发展态势, 作为世界钢铁生产大国的中国, 我们绝不可掉以轻心。
1.2 世界直接还原铁主要生产工艺??? 世界直接还原铁生产工艺大致可分为两大类: 一种是气基竖炉生产工艺; 一种是煤基回转窑生产工艺。
前者生产量约占总产量的92%, 而后者约占总产量的8%。
在这两种生产技术的基础上, 又发展了熔融还原生产技术。
近年来, 将直接还原与熔融还原技术加以组合, 形成了COREX-Midrex联合流程, 颇受人们的关注。
直接还原铁主要生产工艺见表1。
??? 应该指出, 世界上Midrex法和HYL法应用的比较普遍, 各项技术经济指标亦趋稳定, 生产工艺成熟可靠。
特别是墨西哥的HYL法, 生产技术不断创新, 由于开发了“自重整”技术, 使建设费用减少了26% , 电炉的耗电降低了5%~6%。
印度由于缺乏天然气, 但精煤的资源丰富, 因此多采用煤基回转窑的生产方法。
烧结返矿替代废钢炼钢生产案例分析.doc

YJ0418-烧结返矿替代废钢炼钢生产案例分析案例简要说明:依据国家职业标准和冶金技术专业教学要求,归纳提炼出所包含的知识和技能点,弱化与教学目标无关的内容,使之与课程学习目标、学习内容一致,成为一个承载了教学目标所要求知识和技能的教学案例。
该案例是炼钢原料优化案例,体现了烧结返矿特点、炼钢冶炼过程温度控制、终渣渣系组成、控制返矿加入方式与数量、防止渣层冷凝等知识点和岗位技能,与木专业转炉炼钢课程炼钢主原料与装入单元的教学目标相对应。
某中型转炉炼钢厂,受废钢价格高和资源缺乏的条件限制,废钢合理搭配无法实现。
同时该公司烧结返矿比例高,二次烧结又增加成木,为消化返矿.同时解决废钢不足的现状。
提岀用烧结返矿取代部分废钢的思路,直接将烧结矿加入转炉冶炼就是其中一种较为可行的降低成木的方法,该方法可以最大程度的利用含铁辅料,提高炼钢效率,减少废钢使用量。
1.主要内容2,1.烧结返矿的特性分析烧结返矿是一种反应性良好且具有一定碱度的低熔点含铁熟料,其硫磷含量低,物理化学成分稳定,粒度均匀,而且熔点较低。
在返矿矿相中占相当比例的液相组成熔点是iioo~i5o(rc,在i3oo~i7o(rc的炼钢温度下,其液相很容易熔化成渣;被低熔点液相包裹熔蚀的磁铁矿、赤铁矿在液相熔化后,可迅速参与转炉造渣反应并向熔池供氧。
如果能够成功在转炉使用,其综合效益应该是相当可观的。
(一)物理特性烧结返矿主要是由含铁矿物及脉石两大类组成的液相粘接在一起的多种矿物的复合体,其中含铁矿物有磁铁矿(FsOJ、方铁矿(FexO)和赤铁矿(FezCb), 粘结相主要是铁橄榄石(熔点为1205°C)、钙铁橄榄石(熔点为1093°C)、硅灰石(熔点为1540°C)、硅酸二钙和铁酸钙(熔点为1449°C)等,此外还有少量反应不完全的游离石英(SiO”和游离石灰(CaO)等。
表1该厂2月份烧结返矿具体成分(二)冶金特性烧结矿的冶金特性主要包括还原性和软熔性,其中还原性代表其含铁氧化物供氧能力的强弱;而软熔性则体现其在高温下液化软熔温度的高低和熔化时间的长短。
鞍钢冶金固体废弃物的应用技术与实践
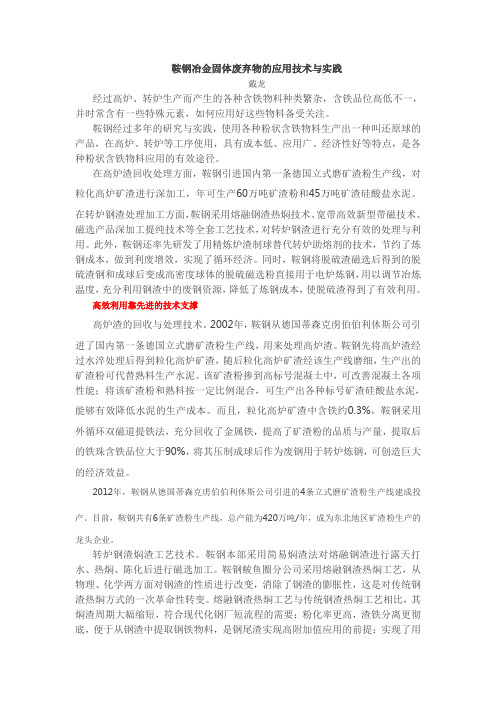
鞍钢冶金固体废弃物的应用技术与实践戴龙经过高炉、转炉生产而产生的各种含铁物料种类繁杂,含铁品位高低不一,并时常含有一些特殊元素,如何应用好这些物料备受关注。
鞍钢经过多年的研究与实践,使用各种粉状含铁物料生产出一种叫还原球的产品,在高炉、转炉等工序使用,具有成本低、应用广、经济性好等特点,是各种粉状含铁物料应用的有效途径。
在高炉渣回收处理方面,鞍钢引进国内第一条德国立式磨矿渣粉生产线,对粒化高炉矿渣进行深加工,年可生产60万吨矿渣粉和45万吨矿渣硅酸盐水泥。
在转炉钢渣处理加工方面,鞍钢采用熔融钢渣热焖技术、宽带高效新型带磁技术、磁选产品深加工提纯技术等全套工艺技术,对转炉钢渣进行充分有效的处理与利用。
此外,鞍钢还率先研发了用精炼炉渣制球替代转炉助熔剂的技术,节约了炼钢成本,做到利废增效,实现了循环经济。
同时,鞍钢将脱硫渣磁选后得到的脱硫渣钢和成球后变成高密度球体的脱硫磁选粉直接用于电炉炼钢,用以调节冶炼温度,充分利用钢渣中的废钢资源,降低了炼钢成本,使脱硫渣得到了有效利用。
高效利用靠先进的技术支撑高炉渣的回收与处理技术。
2002年,鞍钢从德国蒂森克虏伯伯利休斯公司引进了国内第一条德国立式磨矿渣粉生产线,用来处理高炉渣。
鞍钢先将高炉渣经过水淬处理后得到粒化高炉矿渣,随后粒化高炉矿渣经该生产线磨细,生产出的矿渣粉可代替熟料生产水泥。
该矿渣粉掺到高标号混凝土中,可改善混凝土各项性能;将该矿渣粉和熟料按一定比例混合,可生产出各种标号矿渣硅酸盐水泥,能够有效降低水泥的生产成本。
而且,粒化高炉矿渣中含铁约0.3%,鞍钢采用外循环双磁道提铁法,充分回收了金属铁,提高了矿渣粉的品质与产量,提取后的铁珠含铁品位大于90%,将其压制成球后作为废钢用于转炉炼钢,可创造巨大的经济效益。
2012年,鞍钢从德国蒂森克虏伯伯利休斯公司引进的4条立式磨矿渣粉生产线建成投产。
目前,鞍钢共有6条矿渣粉生产线,总产能为420万吨/年,成为东北地区矿渣粉生产的龙头企业。
直接还原铁作为废钢替代品在电弧炉中的应用

摘 要 :为了满足用户对优质钢和纯净钢的要求 ,直接还原铁作为废钢的替代品用 于电弧炉炼钢应是一种可行的选择 。概述了直接还原铁的特点 ,指出高比例使用 DRI 可以得到 N、Cu、Cr 、Ni 、As、Sn 等含量低的钢 ,直接还原铁可认为是一种较好的电弧炉炼 钢原料 。
关键词 :直接还原铁 ; w (N) ;电弧炉 ;泡沫渣 中图分类号 :TF741. 8 文献标识码 :A 文章编号 :1001 - 1447 (2004) 05 - 0053 - 05
Keywords :DRI ; w (N) ; EAF ;foamed slag
1 前 言
电弧炉短流程炼钢工艺投资省 ,见效快 ,因此 发展很快 。但随炉容量的逐渐扩大 ,作为电弧炉 炼钢的主要炉料 ———废钢越来越少 。而废钢经过 多次循环利用 ,残余元素及有害元素 (铬 、铜 、锡 、 铝等) 急剧增加 ,不利于提高产品质量 ,难以生产 出优质的清洁钢 。20 世纪 60 年代以后 ,直接还 原技术进入工业化阶段 ,为缺少废钢地区提供了 发展电弧炉炼钢的可能性 。而直接还原铁具有其 自身的优点 ,残余元素及有害元素含量低 。实践 证明 ,在提高产品的质量方面 ,直接还原铁是比较 理想的废钢替代料 。在使用轻质的废钢时 ,可配 加 DRI ,减轻废钢中的残存元素及有害元素的影 响 ,既能生产出质量比较高的钢 ,又可以合理地利 用废钢资源 。因此在废钢资源越来越少的情况
采用铁矿石替代废钢的炼钢工艺实践

轻烧白云石的热量消耗情况为 28 kg/t,在冶炼前期加完,并保持渣中 w(MgO)≥8%,以减少炉衬蚀损。 冶炼后期根据渣况和溅渣要求确定是否补加轻烧白云石,若渣稀则补加 300~500 kg。
原炼钢工艺中,每炉钢约需添加萤石等化渣材料 300 kg。采用铁矿石替代废钢工艺时,因(FeO)是氧化 剂,且能加速石灰的溶解,故冶炼过程中可不用添加萤石等化渣材料。
采用铁矿石替代废钢工艺的造渣操作要点可总结为:前期快速成渣,中期熔渣化透,后期终渣作黏。在 造渣过程中将温度调控结合起来,通过调整矿石加入的时间、批次进行化渣,通过调整枪位控制过程喷溅和 返干。
2.4 温度制度
根据具体情况,正确判断冶炼过程中的温度变化情况,及时调整铁矿石的用量。开吹时加入铁矿石 2 t 左右,占加入总质量的 50%~60%,以取代废钢的冷却作用。冶炼过程的中后期,分批次加入铁矿石,每 批次加入质量不大于 500 kg,否则会造成熔池温度下降过多、渣料结团、石灰块表面形成一层金属凝壳而推 迟成渣。冶炼过程的中后期,铁矿石具体加入方法为:在硅及锰的氧化基本结束、头批渣料已经化好、碳焰 初起的时候(开吹约 5 min)加入 2 批铁矿石,每批约加入 0.5 t。在吹炼中期(开吹约 8~10 min)返干或熔 池温度高时加入 1 批铁矿石,在终点前 3 min 左右,根据熔池温度情况加入铁矿石 1 批,以调整熔池温度。 吹炼末期不再加入铁矿石,主要进行升温和均匀温度工作。
直接还原铁生产技术及现状

直接还原铁生产技术及现状铁生产技术的发展历史可以追溯到公元前2000年左右,最初的铁制品是通过在炭火中烧烤铁矿石来获得的。
这种烧烤技术被称为古老的冶金学,也被认为是人类历史上最早的冶金技术之一古代的铁生产技术在公元前1000年左右经历了重大的革新,这是由于铁矿石的高温还原反应被发现。
这种高温反应是通过将铁矿石与木炭或石炭混合,并在高温环境下加热来进行的。
这项技术的发现使得铁成为了当时最重要的金属之一,但其生产量仍然相对较小。
在一些古代文明中,如中国、印度等,铁的制造和使用逐渐扩大,为社会的农业、战争和工艺生产做出了重要贡献。
到了公元前300年左右,铁生产技术再次得到了改进。
在罗马时代,一种称为“减氧法”的技术被发明,这个技术将铁矿石与木炭放入特殊的炉子中,并且通过控制加热和供氧来获取较高纯度的铁。
这项技术极大地提高了铁的生产效率,使得罗马帝国在铁材料的生产和使用方面取得了巨大的进展。
这种技术的使用也标志着对铁生产的进一步工业化,奠定了现代铁产业的基础。
到了中世纪,铁生产技术进一步发展,很大程度上得益于对炼铁炉的改进。
这些改进包括提高炉子的结构、使用更多供氧装置以及改进燃烧气体的预热系统等。
这些改进使得炼铁过程更为高效,并且提高了产量和纯度。
到了18世纪,随着燃烧技术和冶金科学的进展,铁生产技术又迈上了一个新的台阶。
在这个时候,由于煤炭的大量使用,炼铁工艺发生了革命性的变化。
在这种现代炼铁法中,矿石和煤炭被放入高炉中,在高温环境下进行化学反应。
通过这个工艺,大量的铁矿石可以得到还原,得到高质量的生铁。
这种先进的炼铁法被广泛应用于欧洲的工业革命中,推动了工业化的进程。
随着时间的推移,各种现代技术和创新被应用于铁的生产过程中,这些技术包括用电解法提纯铁、高炉法等。
现代大规模铁生产以高炉和电炉为主,这些炉子能够生成高品质的铁,用于制造各种铁制品。
此外,利用再生铁和废钢再生技术也成为现代铁产业的重要组成部分,以提高资源利用效率和减少环境影响。
直接还原铁在转炉使用效果分析

关键 词 : 直接还原铁 ; 碱度 ; 收得率 中图分 类号 :F 5 T 5 文献标识码 : A
Th r c vv f a in I o e Efe tAn l ssi n e t r e Die tRe i i c t r n Us f c a y i n Co v r e i o
d l t n f n t n t te t rs l h rc e c le e n . I ce s i o a e a p o raey h i e l t n ic a e i i u c o se lwae u p u h mia l me t n r ae l uo i o me d s g p r p it l ,te l me d p ei n r s s o e
杨 怀春
( 宝钢集团八钢公 司 第一炼钢厂 , 新疆 乌鲁木 齐 8 02 ) 30 2
摘
要: 转炉使用直接还 原铁 代替废钢工艺可行 , 理 比例 1% 一 0 ; 合 0 3% 使用还 原铁提 高金属 收得率 , 转炉 吹 降低
损; 使用直接还原铁对转 炉钢水硫元素起到稀释作用 。冶炼 中应 当适 当增加石灰用量 , 转炉吨钢石灰 消耗增 加 4t 0
接还原加入量增加影响熔池前期升温速度 , 因直接
还原 还 原不 足 , 部 分 铁 以 F O形 式 存 在 , 致 前 一 e 导
期熔池 w F O 偏高 , (e ) 冶炼前期 出现溢渣喷溅现象 ,
2 直 接还 原铁试验简介
2 1 实验 条 件 .
随着加入量的增加 , 前期溢渣现象明显增加。直接 还原加入 比例与前期溢渣喷溅的关系如图 l 。 如图 1 所示 , 转炉使用直接还原铁代替废钢 , 直 接还原铁加入 比例小于 5 %时 , 0 喷溅率蓝线在直接
- 1、下载文档前请自行甄别文档内容的完整性,平台不提供额外的编辑、内容补充、找答案等附加服务。
- 2、"仅部分预览"的文档,不可在线预览部分如存在完整性等问题,可反馈申请退款(可完整预览的文档不适用该条件!)。
- 3、如文档侵犯您的权益,请联系客服反馈,我们会尽快为您处理(人工客服工作时间:9:00-18:30)。
直接还原铁代替废钢在鞍钢的践行与业绩
关键词直接还原铁废钢转炉操作
废钢的资源和价格问题一直是制约着我国钢铁业转炉炼钢的生产操作。
由于废钢短缺,转炉只好多吃铁水,大大降低转炉炼钢的废钢比,为了解决转炉炼钢冷却剂,只能用球团矿代替,使炼钢操作带来诸多的负面影响。
预计全面解决我国的废钢的问题还需要10-20年,如何解决我国的废钢问题,鞍钢在20年前率先用直接还原铁代替废钢,经验值得借鉴。
在上个世纪90年代,鞍钢的废钢奇缺,废钢的价格高抬不下,有人提出可否用直接还原铁代替废钢建议。
为此,由马来西亚沙巴煤气厂购进了5万吨直接还原铁热压铁块,在三炼钢的180吨的转炉上进行生产试验,试验取得安全,技术和效益的完全成功,为我国用直接还原铁代替废钢,开辟先河。
鞍钢为践行上述技术方针,在世界个地采购大量的直接还原铁,用于炼钢转炉上代替废钢,见2002年-2013年采购明细表。
2002年-2013年采购明细表
年份原产地数量(万吨)价格CFR(美元/吨)
2002
澳洲20.50 105 俄罗斯 4.10 104
24.60 104.83
2003
澳洲31.00 148 委内瑞拉 5.00 160
36.00 149.67
2004
澳洲15.20 231
委内瑞拉13.20 309
俄罗斯 3.30 180
31.70 258.17
2005 委内瑞拉 3.85 240 委内瑞拉 4.07 240
7.92 240
2009 委内瑞拉 3.60 245 俄罗斯 1.00 235 俄罗斯 1.00 230 俄罗斯 1.8284 235
7.4284 239.17
2010
日本 3.00 295 日本 3.00 295 委内瑞拉 2.0758 310 委内瑞拉 3.00 364.9 委内瑞拉 3.0989 353
14.1747 324.67
总计121.8231 200.5
通过采购明细表不难看出,鞍钢在2002--2013年间采购直接还原铁遍及世界四大州五个国家,其中以南美州和澳州为主,委内拉为主要采购国,并直接还原热压块的质量上乘。
从采购量不难看出,最高的年份为2003年,全年采购了36 万吨,全部用于转炉代替废钢,创造还原铁代替废钢的最高纪录,证明技术的成熟,经济效益的合理,市场运行便利。
从2002年---2013年间鞍钢转炉操作总共应用直接还原铁代替废钢达121.8231万吨,创世界转炉炼钢历史上最高纪录,经验值得总结,推广。
从而提升我国转
炉炼钢转型升级水平。
从热压铁块的采购价格上看,热压
铁块的价格逐年上涨,或成倍上涨,高达239.17 CFR(美
元/吨),直到有价无市,只好停用。
从上述的分析中,表
明转炉炼钢工业践行了直接还原铁代替废钢的技术,证明
技术是成熟的,可以看出我国需要大量的直接还原铁。
由
此倒逼我国的直接还原铁的快速发展,适应废钢工业的需要。
鞍钢直接还原铁在转炉上的应用有那些经验和业绩呢?
常年的转炉炼钢实践取得了多方面的应用效果:
1、用直接还原铁代替废钢,大大提高了转炉废钢比,
缓解了重型废钢的供应不足的问题,保证转炉操作的正常运行。
下图为鞍钢三炼钢1999—2002年废钢比的变化概况
在2000年前由于铁水资源的限制,钢产量低迷,为
提高钢产,必须提高转炉中废钢比,多用废钢。
特别是当
鞍钢实现全连铸之后重型废钢减少,造成废钢单槽重下降,
极度降低废钢比,降低炼钢产量,图中可以明显看出,2001年开始利用直接还原铁代替废钢后,废钢比逐年提高,转炉操作回归正常。
直接还原铁在转炉中的另一种使用方法,即将直接还原铁加入高位料槽中作为转炉操作中冷却剂使用。
与提温剂(碳化硅)配合使用,缩短了冶炼周期,又降低了铁水单耗,进一步提高了废钢比。
2、缩短转炉冶炼周期,增加产量
由于直接还原铁块尺寸规格整齐,堆积比重大(比重最大达5.6)单槽重达2.0吨,转炉只加一槽废钢,即可满足转炉操作要求,从而减少废钢车作业率和加废钢的时间,冶炼周期相对平均缩短了1—2分钟。
鞍钢三炼钢1999—2003冶炼周期时间排列图如下。
3、直接还原铁块熔化速度快有利于转炉前期化渣操作
由于直接还原铁中含有FeO(10—30%),SiO2(2—3%)因此,转炉吹炼前期渣比较快,直接还原铁加入废钢占50%
时,化渣时间可提前2分钟左右。
又叠加的缩短了冶炼周期。
4、由于直接还原铁中铁回收率的提高,保证转炉炼钢金属收得率的提高。
金属铁和氧化铁中的铁。
当转炉不采取留渣作业时,采用先加入直接还原铁后加铁水的装料方式,转炉出钢时不会出现直接还原铁“裹”在炉渣中的现象,当转炉采用留渣作业时,采用先兑铁水后加废钢的加料方式,同样保证直接还原铁块全部熔化。
经过长期随机作业,发现转炉出钢时炉渣中的氧化铁含量未因加入直接还原铁而升高。
经过对大量的炉次进行金属平衡计算得出,直接还原铁中铁的回收率,在82—88%之间,保证转炉操作金属收得率的提高。
结论:
1、利用直接还原铁代替废钢,增加了转炉废钢单槽重量,提高了废钢比,增加了产量。
2、冶炼周期平均缩短了1—2分钟
3、直接还原铁熔化速度快,有利于转炉前期化
渣操作。
4、直接还原铁化学成分稳定,S,P及金属元素含量低,对冶炼优质钢及生产高附加值钢有利。
原鞍钢副总工程师王太炎
2015.1.28 于鞍山。