水泥粉磨控制系统改造的设计与实现
水泥粉磨系统优化设计方案
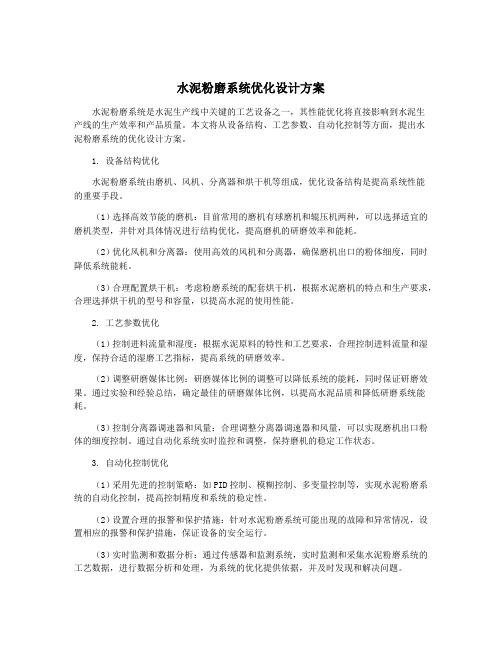
水泥粉磨系统优化设计方案水泥粉磨系统是水泥生产线中关键的工艺设备之一,其性能优化将直接影响到水泥生产线的生产效率和产品质量。
本文将从设备结构、工艺参数、自动化控制等方面,提出水泥粉磨系统的优化设计方案。
1. 设备结构优化水泥粉磨系统由磨机、风机、分离器和烘干机等组成,优化设备结构是提高系统性能的重要手段。
(1)选择高效节能的磨机:目前常用的磨机有球磨机和辊压机两种,可以选择适宜的磨机类型,并针对具体情况进行结构优化,提高磨机的研磨效率和能耗。
(2)优化风机和分离器:使用高效的风机和分离器,确保磨机出口的粉体细度,同时降低系统能耗。
(3)合理配置烘干机:考虑粉磨系统的配套烘干机,根据水泥磨机的特点和生产要求,合理选择烘干机的型号和容量,以提高水泥的使用性能。
2. 工艺参数优化(1)控制进料流量和湿度:根据水泥原料的特性和工艺要求,合理控制进料流量和湿度,保持合适的湿磨工艺指标,提高系统的研磨效率。
(2)调整研磨媒体比例:研磨媒体比例的调整可以降低系统的能耗,同时保证研磨效果。
通过实验和经验总结,确定最佳的研磨媒体比例,以提高水泥品质和降低研磨系统能耗。
(3)控制分离器调速器和风量:合理调整分离器调速器和风量,可以实现磨机出口粉体的细度控制。
通过自动化系统实时监控和调整,保持磨机的稳定工作状态。
3. 自动化控制优化(1)采用先进的控制策略:如PID控制、模糊控制、多变量控制等,实现水泥粉磨系统的自动化控制,提高控制精度和系统的稳定性。
(2)设置合理的报警和保护措施:针对水泥粉磨系统可能出现的故障和异常情况,设置相应的报警和保护措施,保证设备的安全运行。
(3)实时监测和数据分析:通过传感器和监测系统,实时监测和采集水泥粉磨系统的工艺数据,进行数据分析和处理,为系统的优化提供依据,并及时发现和解决问题。
水泥粉磨系统优化设计方案

水泥粉磨系统优化设计方案水泥粉磨系统是水泥生产过程中非常重要的环节,它直接影响着水泥产品的质量和生产效率。
对水泥粉磨系统进行优化设计,提高其工作效率和产品质量,对水泥生产企业来说具有重要意义。
本文将针对水泥粉磨系统进行优化设计方案的制定,进行详细的介绍和分析。
一、水泥粉磨系统的工作原理在水泥生产过程中,水泥生产企业主要采用球磨机或立磨机进行水泥熟料的粉磨工作。
而水泥磨矿机在磨矿过程中,主要是通过水泥磨机的回转部件和磨辊、磨盘、磨头的自转,传动装置使磨辊向外侧翻滚,并等速自转,使熟料通过分散装置均匀的进入磨辊和磨盘之间,形成前磨层。
在冲击,挤压和摩擦作用下,将熟料磨矿成水泥熟料粉,颗粒逐渐减小,颗粒细化,缩小了分散液相间的界面,提高了水泥的水化速度。
水泥粉磨系统的主要工作原理可以总结为:通过磨机的机械作用,将水泥熟料磨成水泥产品所需的细度和颗粒大小,从而保证水泥的质量和水泥产品的性能。
传统的水泥粉磨系统存在一些问题,主要表现在以下几个方面:1. 能耗较高:传统水泥粉磨系统的能耗较高,不利于节能减排。
2. 生产效率低:传统水泥粉磨系统的生产效率较低,无法满足企业的生产需求。
3. 产品质量不稳定:由于水泥粉磨系统的工艺不够完善,导致水泥产品的质量不稳定,影响产品的市场竞争力。
4. 设备磨损大:传统水泥粉磨系统的设备磨损较大,需要经常进行维护和更换。
针对以上问题,需要对水泥粉磨系统进行优化设计,从而提高其工作效率和产品质量,降低能耗和设备磨损,实现水泥生产的可持续发展。
1. 提高设备的自动化水平通过提高水泥粉磨系统设备的自动化水平,实现设备的智能化控制和运行,从而减少人为操作的干扰,提高生产效率和产品质量。
可以采用先进的自动化控制系统,实现设备的远程监控和智能化运行,实时监测设备的运行状态和生产数据,做到及时发现问题并进行处理,提高设备的可靠性和稳定性。
2. 优化磨矿工艺通过优化水泥粉磨系统的磨矿工艺,实现水泥熟料的高效粉磨,提高产品的细度和颗粒大小,从而提高产品的质量和性能。
水泥粉磨系统优化设计方案

水泥粉磨系统优化设计方案水泥粉磨系统是水泥生产过程中的关键设备之一,其性能优化对于提升生产效率、降低能耗具有重要意义。
本文将从优化设计方案的角度来探讨如何提高水泥粉磨系统的性能。
优化设计方案需要考虑水泥粉磨系统的结构和工作原理。
水泥粉磨系统由进料装置、磨机、粉磨仓和离心风机等组成,任务是将水泥熟料磨成一定粒度的水泥粉末。
在系统结构设计时,需要考虑各个部件之间的协调配合,确保物料顺畅传输和有效处理。
选用高效的磨机也是优化设计方案的重要环节,常用的有球磨机、辊压机和立磨等,根据生产需求和水泥特性选择合适的磨机类型。
优化设计方案需要考虑水泥粉磨系统的控制方式。
通过采用先进的自动化控制系统,可以实现对水泥粉磨系统的精确控制。
通过对进料量、循环负荷和磨机转速等参数的精确控制,可以实现水泥生产过程的精细化管理。
还可以增加粉磨仓的分选机构,减小不合格粉末的含量,提高水泥品质。
优化设计方案需要考虑水泥粉磨系统的能耗问题。
水泥粉磨系统的能耗主要包括磨机功率、磨机系统热能损失和离心风机功率等。
为了降低系统能耗,可以采用节能型的磨机,例如高效球磨机和节能辊压机。
还可以改进磨机系统的散热方式,减少热能损失。
合理设计离心风机参数,选用高效的离心风机,可以降低系统的风阻损失。
优化设计方案还需要考虑水泥粉磨系统的维护和保养。
定期清理磨机内部和粉磨仓,保持设备的正常运行。
建立完善的维护记录和维修保养计划,对设备进行定期检修和维护,延长设备的使用寿命。
水泥粉磨系统优化设计方案应该从系统结构、控制方式、能耗和维护等方面进行综合考虑。
通过合理的设计和控制,可以显著提高水泥粉磨系统的性能,实现生产效率和能耗的双重优化。
水泥粉磨系统优化设计方案
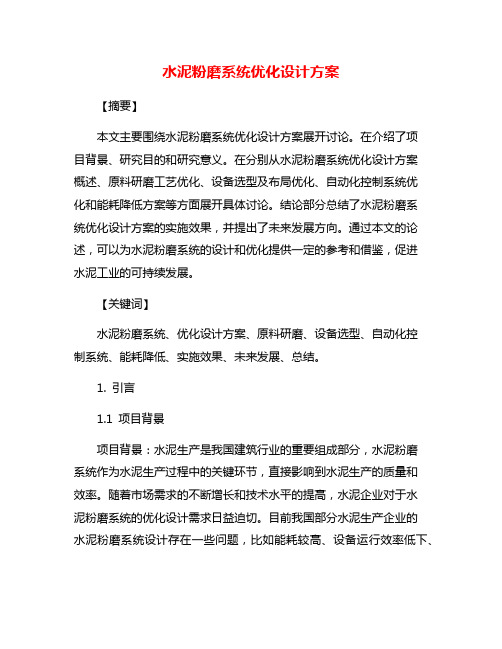
水泥粉磨系统优化设计方案【摘要】本文主要围绕水泥粉磨系统优化设计方案展开讨论。
在介绍了项目背景、研究目的和研究意义。
在分别从水泥粉磨系统优化设计方案概述、原料研磨工艺优化、设备选型及布局优化、自动化控制系统优化和能耗降低方案等方面展开具体讨论。
结论部分总结了水泥粉磨系统优化设计方案的实施效果,并提出了未来发展方向。
通过本文的论述,可以为水泥粉磨系统的设计和优化提供一定的参考和借鉴,促进水泥工业的可持续发展。
【关键词】水泥粉磨系统、优化设计方案、原料研磨、设备选型、自动化控制系统、能耗降低、实施效果、未来发展、总结。
1. 引言1.1 项目背景项目背景:水泥生产是我国建筑行业的重要组成部分,水泥粉磨系统作为水泥生产过程中的关键环节,直接影响到水泥生产的质量和效率。
随着市场需求的不断增长和技术水平的提高,水泥企业对于水泥粉磨系统的优化设计需求日益迫切。
目前我国部分水泥生产企业的水泥粉磨系统设计存在一些问题,比如能耗较高、设备运行效率低下、操作费时费力等。
开展水泥粉磨系统优化设计方案的研究具有重要意义。
本文旨在通过对水泥粉磨系统进行优化设计,提高水泥生产的效率和质量,降低生产成本,实现可持续发展。
通过研究水泥粉磨系统的优化设计方案,积累经验,为我国水泥行业的技术进步提供参考和借鉴。
希望通过本文的研究,能够为相关水泥企业提供实用的技术支持,促进水泥行业的健康发展。
1.2 研究目的研究目的是为了提高水泥粉磨系统的生产效率和产品质量,降低生产成本和能耗,实现系统的可持续发展。
通过对原料研磨工艺、设备选型及布局、自动化控制系统和能耗降低方案进行优化设计,提高系统的稳定性和可靠性,减少故障率,提高生产线的连续性和自动化水平。
通过优化设计,减少水泥粉磨过程中的能耗消耗,降低生产成本,提高竞争力。
研究目的还包括优化设计方案的实施效果评估,为水泥企业提供可靠的技术支持和决策依据,推动行业的技术进步和发展。
通过本研究,旨在为水泥生产企业提供一套科学、系统的水泥粉磨系统优化设计方案,实现企业效益和环保效益的双赢,推动水泥行业的可持续发展。
水泥粉磨系统优化设计方案

水泥粉磨系统优化设计方案
水泥粉磨系统是水泥生产过程中非常关键的环节之一,也是消耗能源较大的环节之一。
因此,优化水泥粉磨系统设计方案对于提高水泥生产效率和节能降耗非常重要。
首先,优化水泥粉磨系统设计的关键是合理选择磨机及其配套设备。
在磨机的选型过
程中需考虑生产工艺流程、原材料特性、产品质量要求、生产能力等因素,以充分发挥磨
机的性能优势,降低生产成本。
在配套设备的选择上应注重设备的高效性和实用性,如优
化空气输送系统、降低渗漏风量、增加控制系统等。
其次,磨机的结构设计也是影响水泥粉磨系统运行效率的重要因素。
针对不同的磨机
类型应进行设计优化,从设备内部结构到整体系统的布局应考虑最优化方案,以达到最佳
使用效果,提高生产效率。
同时,磨机的维护和检修也是非常关键的环节,应建立健全的
维修保养体系,及时发现并解决问题,提高设备可靠性和使用寿命。
最后,优化水泥粉磨系统设计方案还需要结合实际生产过程进行动态调整。
根据生产
过程中的实际情况,及时采取优化措施,如调整磨机进出料量、优化磨机内部工艺、调整
输送速度等,以使生产过程更加稳定和可靠。
总之,水泥粉磨系统的优化设计方案是提高水泥生产效率和节能降耗的重要手段。
通
过合理选型、优化设计、配套设备等措施,加强设备维护和动态调整,可实现生产效果最
优化,同时达到节能降耗的目的。
水泥粉磨系统的控制流程设计和分析
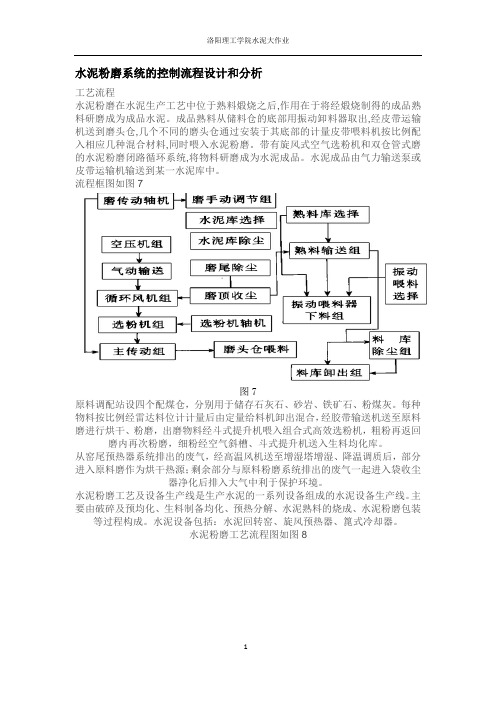
水泥粉磨系统的控制流程设计和分析工艺流程水泥粉磨在水泥生产工艺中位于熟料煅烧之后,作用在于将经煅烧制得的成品熟料研磨成为成品水泥。
成品熟料从储料仓的底部用振动卸料器取出,经皮带运输机送到磨头仓,几个不同的磨头仓通过安装于其底部的计量皮带喂料机按比例配入相应几种混合材料,同时喂入水泥粉磨。
带有旋风式空气选粉机和双仓管式磨的水泥粉磨闭路循环系统,将物料研磨成为水泥成品。
水泥成品由气力输送泵或皮带运输机输送到某一水泥库中。
流程框图如图7图7原料调配站设四个配煤仓,分别用于储存石灰石、砂岩、铁矿石、粉煤灰。
每种物料按比例经雷达料位计计量后由定量给料机卸出混合,经胶带输送机送至原料磨进行烘干、粉磨,出磨物料经斗式提升机喂入组合式高效选粉机,粗粉再返回磨内再次粉磨,细粉经空气斜槽、斗式提升机送入生料均化库。
从窑尾预热器系统排出的废气,经高温风机送至增湿塔增湿、降温调质后,部分进入原料磨作为烘干热源;剩余部分与原料粉磨系统排出的废气一起进入袋收尘器净化后排入大气中利于保护环境。
水泥粉磨工艺及设备生产线是生产水泥的一系列设备组成的水泥设备生产线。
主要由破碎及预均化、生料制备均化、预热分解、水泥熟料的烧成、水泥粉磨包装等过程构成。
水泥设备包括:水泥回转窑、旋风预热器、篦式冷却器。
水泥粉磨工艺流程图如图8图81、辊压机终粉磨:从配料站来的混合料由带式输送机送至生料粉磨车间,带式输送机上挂有除铁器,将物料中混有的铁件除去,同时在该带机上装有金属探测器,发现有金属后气动三通换向,将混有金属的物料由路旁卸出,以保证辊压机的安全运行。
不含金属的物料由气动通经重锤锁风机喂入V 型选粉机,在V 型选粉机中预烘干后,通过提升机进入稳流仓,稳流仓设有荷重传感器检测系统。
物料从稳流仓喂入辊压机中进行挤压,挤压后的料饼通过提升机送入V 型选粉机中进行打散、烘干和分级,细小颗粒被热风选粉机分选出来;粗颗粒与新喂入的混合料一同进入循环挤压过程。
水泥粉磨系统优化设计方案

水泥粉磨系统优化设计方案水泥粉磨系统是水泥生产中的重要部分,它对水泥的质量和产量有着重要的影响。
为了提高水泥生产的效率和质量,优化设计水泥粉磨系统是非常必要的。
本文将针对水泥粉磨系统的优化设计提出一些方案和建议。
一、水泥粉磨系统的特点及存在的问题水泥粉磨系统是水泥生产过程中的重要部分,它的主要工作是将熟料磨成水泥粉。
水泥粉磨系统通常包括磨粉机、风机、分离器、输送设备等组成部分。
在水泥生产中,水泥粉磨系统的运行稳定性、粉磨效率和能耗水平直接影响着水泥生产的质量和成本。
目前,水泥粉磨系统存在一些问题。
现有的粉磨设备运行不稳定,易发生堵机、堵仓等故障,影响了生产的连续性和稳定性。
粉磨效率不高,部分原料未能完全磨碎,导致产品粒度不均匀,品质不稳定。
现有系统的能耗水平较高,磨煤机、风车等设备存在能耗过大的情况,导致生产成本偏高。
二、水泥粉磨系统优化设计的方案和建议1. 更新粉磨设备要提高水泥粉磨系统的运行稳定性和粉磨效率,首先需要更新粉磨设备。
可以选择新型的高效粉磨机,如立磨、辊磨等,这些新型设备具有更高的磨碎效率和更稳定的运行性能。
还可以配备自动化控制系统,对粉磨设备的运行进行实时监测和调整,提高设备的稳定性和可靠性。
2. 优化系统结构水泥粉磨系统的结构优化也是提高粉磨效率和稳定性的关键。
可以对系统的输送设备、分离器、风机等进行优化设计,提高系统的整体工作效率。
特别是在传输链条上的改进,例如采用新型的输送带和提升机等设备,可以提高原料的输送效率,减少系统的能耗。
3. 提高控制精度对水泥粉磨系统的控制精度也是需要重点关注的地方。
可以采用先进的自动控制系统,实现对系统各个部分的精准控制。
通过精准的控制,可以实现对磨煤机、风机等设备的能耗管理,减少不必要的能耗损失。
还可以通过控制系统对粉磨机的出料粒度进行实时监测和调整,提高产品的粒度均匀度和品质稳定性。
4. 加强维护和管理水泥粉磨系统的维护和管理也是优化设计的重要环节。
水泥磨粉DCS控制系统-可用
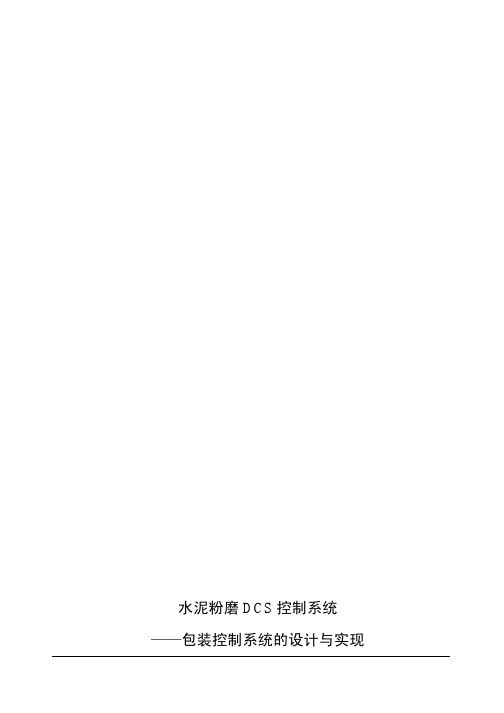
水泥粉磨DCS控制系统——包装控制系统的设计与实现摘要ABSTRACT1概述2方案论证2.1 集散控制系统的简介集散控制系统(Distributed Control System)是以微处理器为基础的集中分散型控制系统。
集中控制系统是进行集中管理的,而系统的体系结构是分布式的,总体上是一种分布结构的控制系统。
DCS控制系统有以下特点:⑴DCS系统作为计算机控制系统中较为完善和成熟的技术,能够对分布于较大范围内的执行机构进行控制,并采用集中管理、分散控制的策略。
⑵DCS系统编程灵活,可以方便地实现历史数据存储、动态显示、报表打印等功能。
⑶DCS可采用组态软件,容易组态,系统集成方便,可靠性高。
2.2 Industial IT控制系统简介Industrial IT系统是ABB公司推出的一种全能综合型开放控制系统,该系统融传统的DCS和PLC优点于一体并支持多种国际现场总线标准。
它既具备DCS的复杂模拟回路调节能力、友好的人机界面(HMI)及方便的工程软件,同时又具有与高档PLC指标相当的高速逻辑和顺序控制性能。
系统既可连接常规I/O,又可连接Remote I/O及Profibus、FF、CAN、Modbus等各种现场总线设备。
系统具备高度的灵活性和极好的扩展性,无论是小型生产装置的控制,还是超大规模的全厂一体化控制,甚至对于跨厂的管理控制应用,Industrial IT都能应付自如。
系统分为两级:操作管理级(操作站OS、工程师站ES及网关GS)和过程控制级(过程站PS及现场控制器AC800F)。
在操作管理级上不仅实现传统的控制系统监控操作功能(预定义及自由格式动态画面显示、趋势显示、弹出式报警及操作指导信息、报表打印、硬件诊断等),而且完成配方管理及数据交换等管理功能。
过程控制级实现包括复杂控制在内的各种回路调节(各种PID、比值、Simith……)和高速逻辑控制、顺序控制以及批量间歇控制功能。
每个过程站PS支持5个机架单元,可配置44个I/O模件(1408个I/0点),PS过程站的CPU模件、电源及系统网络接口均可冗余。
- 1、下载文档前请自行甄别文档内容的完整性,平台不提供额外的编辑、内容补充、找答案等附加服务。
- 2、"仅部分预览"的文档,不可在线预览部分如存在完整性等问题,可反馈申请退款(可完整预览的文档不适用该条件!)。
- 3、如文档侵犯您的权益,请联系客服反馈,我们会尽快为您处理(人工客服工作时间:9:00-18:30)。
冶金自动化2001年第2期
47
[摘
要]冀东水泥1#生产线水泥磨控制系统改造,采用了A B PLC5系列控制器。
本文着重介绍系统的硬件配置、
原系统软件功能的替代以及新系统软件的结构和功能的实现。
[关键词]水泥磨;DH +网;PLC [中图分类号]TQ 172.6+3;TP29
[文献标识码]B
[文章编号]1000 7059(2001)02 0047 03
(1 冶金自动化研究院,
北京
100071;2 唐山冀东水泥股份有限公司)
水泥粉磨控制系统改造的设计与实现
[收稿日期]2000 10 17;[修改稿收到日期]2000 11 25
[作者简介]张洪军(1966-),男,江苏响水人,工程师,硕士,主要从事自动化技术的研究和应用工作。
张洪军1
,
王全生1
,
高建明2
,
王亭津2
,
张俊和2
,
刘臣
2
水泥粉磨子系统因为与其它系统相对独立,对生产线的连续性影响较小,且仪表控制回路较少,
故被选择作为实现整个自动化系统改造的第1步目标,本子系统改造从1995年5月开始启动。
1工艺简介
水泥粉磨在水泥生产工艺中位于熟料煅烧之
后,作用在于将经煅烧制得的成品熟料研磨成为成品水泥。
成品熟料从储料仓的底部用振动卸料器取出,经皮带运输机送到磨头仓,几个不同的磨头仓通过安装于其底部的计量皮带喂料机按比例配入相应几种混合材料,同时喂入水泥粉磨。
带有旋风式空气选粉机和双仓管式磨的水泥粉磨闭路循环系统,将物料研磨成为水泥成品。
水泥成品由气力输送泵或皮带运输机输送到某一水泥库中。
2原控制设备状况
冀东水泥生产1#线共有两套水泥粉磨生产
线,分别由两套东芝2000型PLC 控制,称为水泥粉磨A 子系统(F1)和水泥粉磨B 子系统(F2)。
水泥粉磨A 子系统和B 子系统虽然分别控制两套水泥粉磨生产线,但在工艺上两套水泥粉磨生产线共用磨头仓皮带运输机和水泥成品输送线,故两套系统的控制联锁很多。
又因东芝2000型PLC 之间不能相互连网,只能通过直接I /O 方式进行联络,因此两套系统增加了大量的直接I /O 点,也增加了维护量和控制程序的复杂性。
水泥粉磨子系统的仪表系统主要用于温度、压力、阀门开度等数据监测和控制,回路控制较
少,主要是计量皮带喂料机喂料量的回路控制。
3系统改造的硬件设计
水泥粉磨系统的硬件选择了两套PLC -5/
40系统,分别代替A 子系统和B 子系统的东芝2000PLC ,直接I /O 联络信号全部取消,改由DH+网来进行通信,节省了硬件费用。
水泥粉磨A 子系统共有5个16槽框架配1块PLC 5/40L 组成,水泥粉磨B 子系统共有6个16槽框架配1块PLC 5/40L 组成,在中控室设置1个操作台和1个控制柜,在F 电气室设置两台控制柜分别控制水泥粉磨A 和B,在G 电气室设置1台控制柜,从而组成了包括3个远程站和2个主站的PLC 网络系统。
具体结构见图1。
因水泥粉磨是整个自动化系统改造的第1步目标,因此采取了比较稳妥的策略,在接入新系统时,旧系统保留不动,以防万一改造失败,可以随时恢复旧系统。
4系统改造的软件设计
4 1原系统控制软件的功能及特点
原东芝PLC控制系统软件采用逻辑图编程语言,直接寻址,利用8位或16位寄存器进行算术运算,结果传送到U400计算机显示。
该控制软件完成从熟料上料、水泥磨制到水泥输送的完整的水泥粉磨工艺过程控制,涉及上百个设备,包括A、B两套互备份系统。
为了减少控制的复杂程度,将设备按工艺功能划分为组,每组中由若干设备共同完成特定功能,组与组之间又有联锁制约关系。
水泥磨制部分和熟料上料部分工艺分组见图2。
原软件通过组将控制功能分解为一个个子模块,按模块顺序依次处理。
在每个模块内对单个设备编程完成条件检查、起动联锁、停止联锁、设备控制、显示驱动等功能。
这样的设计思想分解了控制难度,增加了控制可靠性。
但在具体实现时,由于东芝PLC编程功能较弱,因此无法完成子程序调用,整个软件只能放在一个程序中,且内存仅有8KB。
为了最大限度精简程序,软件以工艺过程为主索引、组为副索引顺序编排。
结果导致软件结构化程度差,非常难读,涉及某一设备的控制分散到程序的许多处,给技术人员的修改、维护带来很多困难。
4 2编制新控制软件的困难点及解决方法
鉴于原控制软件的结构特点,想通过逐条读程序来回推工艺过程的难度大、耗时多,但若对原程序推倒重来,彻底按新思路重写则风险很大。
由于对程序的理解深度可能不够,会造成细节的错误或疏漏,导致整个软件的可靠性下降,不可避免地会延长现场调试时间。
另外,新软件需要保留原软件的多数功能,并要扩充原仪表完成的监视与控制功能,增加设备状态监测等功能。
因此,必须设计合理的软件结构框架,最大限度地移植原有程序。
通过简单的次序调整或指令、地址的替代,不必完全摸透细节,即可继承原软件功能的完整和可靠性,同时保证程序扩充部分的正确衔接。
4 3新控制软件的结构及功能
新控制程序选用梯形图语言,从结构上分为数据区和程序区两部分。
(1)数据区设计
N9:50、N10:50、N11:50、N12:50标志区
O:117、I:117输出、输入区
B3/927上位机开关量传送区
N15:50上位机模拟量通信区
B13/1199中间状态区
B14/200中间标志区
N7:500模拟量输入控制区
F8:99模拟量显示区
BT16:20块传送区
M G17:5信息区
经过精简,数据区共占用3KB内存,所有数据按规律分配地址,满足程序编制所需的变量要求,利于程序编制的高效率,且留有一定的扩充裕量。
(2)程序区设计
程序整体结构框图见图3。
其中主程序是唯一一个PLC主扫描程序,完成变量初始化、PLC间通信数据读取、通信文件生成、灯测试、工艺过程的模拟屏及上位机报警、电源检查、公用脉冲及标志的生成、子程序调用等功能。
通信处理子程序完成上位机传送信号从状态到脉冲的转换,以及信号处理后的回送,另外还控制上位机外挂扬声器,在工艺或设备报警时做出响应。
模拟量输入及转换子程序处理原仪表标准温度、压力等信号和铂电阻输入信号,经计算转化为整型或浮点数,传送给上位机显示。
Metallur g ical Industr y Automation2001No2
48
水泥粉磨控制系统改造的设计与实现
PID控制子程序分别用3个闭环回路调节水泥中熟料、石膏、石灰石的比例,以控制水泥质量。
石膏自动上料子程序完成对A和B水泥粉磨磨头仓的注料控制,设置了自动、手动功能,在手动方式下由操作工控制起停,在自动方式下由限位开关控制起停变化。
双水泥粉磨自动取料子程序控制熟料供应,4个熟料库和1个次料库经过搭配,开启相应的挡板,熟料经过振动喂料器下送到短皮带,通过长距离输送带和斗式提升机,注入磨头仓。
该程序可完成单磨自动、单磨手动、双磨循环自动上料的控制。
水泥粉末工艺控制程序主要是移植原控制软件内容,在子程序的结构下重新编排顺序,发挥6200编程软件高效的文件指令功能,缩并原程序,增加通信功能。
每个组独立构成子程序,通过组通信互传信号,协调完成磨进料、磨制、选粉、除尘、回粉、气动输送、水泥入库的生产过程。
5应用效果分析
本控制系统一次调试成功,基本未做改动即于1995年12月投入试生产运行。
目前已正式通过验收,改造双方对这次合作非常满意。
至今的运行实践表明:
(1)系统设计构思严谨,功能稳定可靠,基本不需要维护。
既保证了原软件固有的高运转率,又实现了原分散在操作台、模拟屏、仪表间的集中操作,且操作简便、直观。
(2)调试和故障诊断方便、快速,新增的故障诊断功能使操作员能及时发现产生的故障并确定其位置,缩短了排除故障的时间。
程序设计了电子索引文件,无需翻阅任何文字资料,即可在计算机上快速定位故障点或设备I/O点。
(3)系统动、静态性能好,能够满足水泥质量控制和仪表计量的精度要求。
[编辑:沈黎颖]
(上接第34页)
次,造成转炉作业率低,修炉费用大,成本高。
1999年7月,湘钢采用 溅渣护炉新技术,2#转炉炉龄大幅度攀高,2000年7月25日上午11: 30,创造突破1万炉的首次炉役的全国纪录,一年节省修炉费800多万元。
利用计算机的快速、准确的特点,控制溅渣时的氮气压力(流量)、枪位和溅渣时间、速度,在千变万化的炉底、炉身状态和外界条件下,可随时调整控制。
比如炉底上涨时,能迅速控制增大氮气压力和降低枪位,从而使溅渣主要挂在耳轴附近,效果更加明显,使溅渣率稳定在90%以上。
[参考文献]
[1]龚尧 转炉炼钢[M] 北京:冶金工业出版社,1991 252~
257
[2]崔健,杨文远 宝钢300t转炉溅渣护炉工艺研究[J] 钢
铁,1998,33(10):15~18
[3]苏天森,刘浏,王维兴 转炉溅渣护炉技术[M] 北京:冶金
工业出版社,1999 106~256
[4]叶江祺,何作然,李世俊 热工仪表和控制设备[M] 北京:水
利电力出版社,1983 88~187
[编辑:魏方]
冶金自动化2001年第2期 49。