汽车变速箱两端面液压双头组合铣床的设计
卧式双面铣削组合机床的液压系统设计
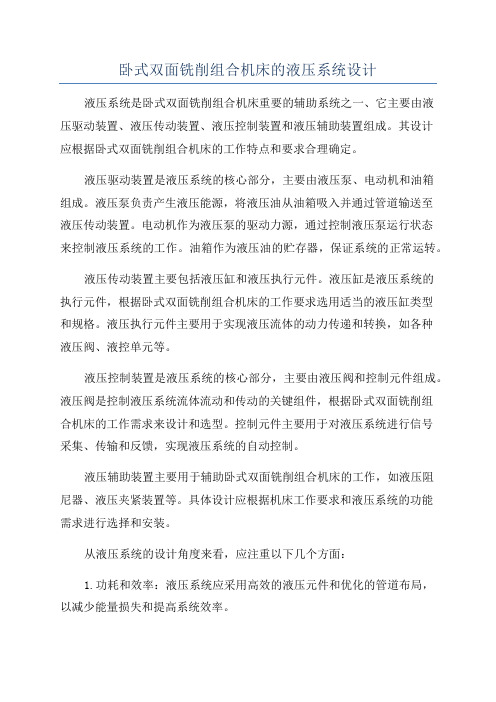
卧式双面铣削组合机床的液压系统设计液压系统是卧式双面铣削组合机床重要的辅助系统之一、它主要由液压驱动装置、液压传动装置、液压控制装置和液压辅助装置组成。
其设计应根据卧式双面铣削组合机床的工作特点和要求合理确定。
液压驱动装置是液压系统的核心部分,主要由液压泵、电动机和油箱组成。
液压泵负责产生液压能源,将液压油从油箱吸入并通过管道输送至液压传动装置。
电动机作为液压泵的驱动力源,通过控制液压泵运行状态来控制液压系统的工作。
油箱作为液压油的贮存器,保证系统的正常运转。
液压传动装置主要包括液压缸和液压执行元件。
液压缸是液压系统的执行元件,根据卧式双面铣削组合机床的工作要求选用适当的液压缸类型和规格。
液压执行元件主要用于实现液压流体的动力传递和转换,如各种液压阀、液控单元等。
液压控制装置是液压系统的核心部分,主要由液压阀和控制元件组成。
液压阀是控制液压系统流体流动和传动的关键组件,根据卧式双面铣削组合机床的工作需求来设计和选型。
控制元件主要用于对液压系统进行信号采集、传输和反馈,实现液压系统的自动控制。
液压辅助装置主要用于辅助卧式双面铣削组合机床的工作,如液压阻尼器、液压夹紧装置等。
具体设计应根据机床工作要求和液压系统的功能需求进行选择和安装。
从液压系统的设计角度来看,应注重以下几个方面:1.功耗和效率:液压系统应采用高效的液压元件和优化的管道布局,以减少能量损失和提高系统效率。
2.安全性:在设计液压系统时,应考虑到系统的安全性,采取相应的安全措施,如选用可靠的液压阀、安全阀等,并设置安全保护装置。
3.可靠性和可维护性:液压系统的设计应考虑到其可靠性和可维护性,方便日常的维护和检修工作。
4.自动控制:液压系统的设计应考虑到其自动控制功能的要求,可以通过采用液压控制元件和控制系统来实现。
总之,液压系统的设计应根据卧式双面铣削组合机床的工作要求和液压系统的功能需求进行合理的配置和选型,以实现系统的高效、安全、可靠的运行。
ZQ250减速机双侧面加工专用铣床设计

ZQ250减速机双侧面加工专用铣床设计ZQ250减速机双侧面加工专用铣床是一种专门用于加工ZQ250减速机的设备。
减速机是一种能够降低旋转速度并增加扭矩的装置,被广泛应用于工业生产中。
这种铣床的设计旨在提高加工效率和质量,同时满足ZQ250减速机的制造要求。
该铣床的设计需考虑以下几个方面:1.结构设计:铣床应采用稳固的结构,可以承受高速铣削带来的振动和冲击力。
主要应该由底座、立柱、横梁、工作台和落料板组成,以确保稳定的加工过程。
2.机床精度:为了保证减速机的加工精度,铣床的各个部件(如导轨、滑块、滚珠丝杠等)都应选择高精度材料和制造工艺。
另外,应该采用伺服驱动系统,以精确控制铣削过程中的速度和位置。
3.加工能力:铣床应具备双面加工能力,可以同时加工减速机的两个侧面。
为了实现这一功能,可以采用双主轴结构,即床身两侧各设置一个主轴,分别装配铣刀,通过同步控制实现双侧面同时加工。
4.自动化控制:铣床应配备先进的数控系统,以实现自动化的加工过程。
数控系统能够实现铣床的高精度控制,提高加工精度和效率。
此外,数控系统还能够实现自动换刀和加工参数的自动调整等功能。
5.安全性考虑:为了确保操作人员的安全,铣床应该配备安全防护装置,如防护罩、急停按钮等。
此外,还应考虑机器的出错判断和自我保护功能,以避免因操作错误或机械故障引起的事故。
6.维护和保养:铣床的设计还应方便进行日常维护和保养。
建议配备自动润滑系统,可以根据加工时间和切削力自动给予润滑油来减少设备的摩擦和损耗。
总之,ZQ250减速机双侧面加工专用铣床的设计应考虑结构稳固、机床精度高、加工能力与自动化控制相结合、安全性考虑以及日常维护和保养的方便性。
这样的设计能够提高加工效率、保证加工质量,并确保操作人员的安全。
汽车变速箱组合机床设计

第一章绪论近年来,随着我国汽车工业的不断发展,汽车业已成为国民经济的支柱产业。
各汽车制造厂在不断提高质量、性能的同时,对变速箱关键零件的加工工艺也在不断地进行探索,以保证变速箱的高性能。
箱体是变速箱的关键零件之一,也是机器及部件的基础件,它将机器及部件中的轴、轴承和齿轮等零件按一定的相互位置关系装配成一个整体,并按预定传动关系协调其运动。
对箱体的加工各国都采用了许多特殊的工艺方法来保证加工精度,其关键的加工部位有:孔系、箱体的平面等主要是保证孔的精度尺寸和位置精度,处理好孔和平面的相互关系。
目前,国内外箱体的产品图纸对和箱孔都有如下技术要求:支承孔之间的孔距公差为0.12~0.05mm,平行度公差应小于孔距公差,一般在全长取 0.1 ~ 0.04mm。
同一轴线上孔的同轴度公差一般为 0.04~0.01mm。
支承孔与主要平面的平行度公差0.1~0.05mm。
主要平面间及主要平面对支承孔之间垂直度公差为0.1~0.04mm。
这些精度指标将直接影响变速箱的性能,因此,对箱体平面面及箱孔加工方法的研究是提高变速箱质量的重要手段。
箱体精加工时,为保证平面、箱孔与轴孔公共轴线相关精度的重要因素。
国内外变速箱制造厂及专用机床厂都在不断寻找新的定位方式,如在半精、精加工时采用底面相同三点(面积较小)再配以多点辅助支承来减少因工件变形和多次重复定位所产生的误差;利用精加工后的主轴孔为箱体的主定位基准来保证所需的加工精度。
为保证变速箱外壳的加工精度和提高生产效率,使用组合机床和专用夹具是各汽车生产厂家普遍采用的工艺措施。
这次毕业设计是一次综合运用所学专业知识的工程训练。
通过毕业设计,可使专业知识、技能及自学能力得到全面提升。
在按照相关技术规范和学院毕业设计规范完成设计任务过程中,培养自己严谨认真的职业素质。
现我国机械制造业正向着高效、高精度、大批量方向发展,组合机床就可以满足这样的发展趋势,世界上第一台组合机床于1908年在美国问世,30年代后组合机床在世界各国得到迅速发展。
液压双行程铣床课程设计

液压双行程铣床课程设计一、课程目标知识目标:1. 学生能理解液压双行程铣床的基本结构、工作原理及其在机械加工中的应用。
2. 学生能掌握液压系统在铣床中的作用,如速度调节、力矩控制等关键概念。
3. 学生能描述液压双行程铣床的操作流程,了解其安全操作规程。
技能目标:1. 学生能操作液压双行程铣床,进行简单的铣削加工,并正确调整铣床的各项参数。
2. 学生能通过实际操作,掌握液压系统的基本调试方法,确保铣床正常工作。
3. 学生能运用所学的知识和技能,解决铣床加工过程中出现的简单问题。
情感态度价值观目标:1. 学生能培养对机械加工职业的兴趣和热情,增强对液压双行程铣床操作的自豪感。
2. 学生能树立安全意识,养成遵守操作规程、爱护设备的好习惯。
3. 学生能在团队协作中发挥积极作用,提高沟通与协作能力。
课程性质:本课程为实践性较强的专业课,注重理论与实践相结合,通过实际操作培养学生的技能。
学生特点:学生具备一定的机械基础知识,动手能力强,对新鲜事物充满好奇。
教学要求:教师应结合学生特点,采用启发式、讨论式和现场教学等多种教学方法,引导学生掌握液压双行程铣床的相关知识和技能。
在教学过程中,注重培养学生的安全意识、团队合作精神和职业素养。
通过分解课程目标,确保教学设计和评估具有针对性和实效性。
二、教学内容1. 理论知识:- 液压双行程铣床的结构组成与工作原理。
- 液压系统在铣床中的应用,包括液压泵、液压缸、控制阀等元件的作用。
- 铣削加工的基本概念,如铣削速度、进给量、切削深度等。
2. 实践操作:- 液压双行程铣床的操作流程,包括开机、调试、加工、关机等步骤。
- 液压系统的调试与维护方法。
- 常见铣削加工工艺及操作要领。
3. 教学大纲:- 第一周:液压双行程铣床的基本结构与工作原理学习。
- 第二周:液压系统元件的认识及在铣床中的应用。
- 第三周:铣削加工的基本概念及参数设置。
- 第四周:液压双行程铣床的操作流程及实际操作。
汽车变速箱两端面组合铣床液压系统设计

汽车变速箱两端面组合铣床液压系统设计董永强【摘要】根据汽车变速箱两端面结构特点,介绍了一种用于加工变速箱两端面的卧式双面铣削组合机床的结构、工作原理,依据机床各阶段工作特点及负载,设计了机床液压系统,并对系统部分重要元件进行了设计选型,最后,对系统油液温升进行了验算.【期刊名称】《许昌学院学报》【年(卷),期】2015(034)002【总页数】4页(P31-34)【关键词】变速箱端面;组合机床;液压系统;元件选型【作者】董永强【作者单位】许昌学院电气工程学院,河南许昌461000【正文语种】中文【中图分类】TH138组合机床是根据零件设计加工要求,以大量基础通用部件为主,配备一些专用部件组合而成的一种高效、专用、自动化程度较高的机床.这种机床不必要按设计加工对象进行具体设计和生产,而是将其组织进行成批生产,然后按被加工零件的具体要求,配以简单的刀具及夹具,即可进行组成加工的高效率设备[1].某型液压双面组合机床结构简图如图1所示,它采用卧式双面双主轴铣削头跨两个工位的大主轴箱配置方案,通过“一面两销”定位方式,靠液压夹紧进而完成铣削汽车变速箱两端面.根据机床的工作原理及加工零件的形状特点,其动作循环过程为:夹紧缸伸出夹紧→工作台快进、接近工件→工作台工进→工作台快退→夹紧缸松开→快退、回到原位停止.已知系统主要参数:工作台重5 000 N,工件以及夹具重量为1 000 N,轴向最大工作负载8 946.3 N,工作台导轨为平动型导轨,静摩擦系数为0.2,动摩擦系数为0.1.在进行系统压力估算时,可以暂时不考虑液压缸回油背压力,这样负载合外力有切削力、惯性力和导轨摩擦力.此时导轨的静摩擦力Ffs=0.2×(5 000+1 000)=1 200 N,动摩擦力Ffd=0.1×(5 000+1 000)=600 N.则惯性负载:加速=1 260 N,减速,制动,反向加速,反向制动Fm5=Fm4=1 260 N.设液压缸机械效率ηm=0.909,则液压缸在各阶段总的外负载见表1所示.根据系统工作特点,拟定的系统液压原理如图2所示.系统主要工作流程如下:(1)定位、夹紧:按下启动按钮,液压油经方向阀7进入定位液压缸下腔,完成定位.定位结束后,系统压力升高,单向顺序阀8打开,夹紧缸上腔进油,实现夹紧.夹紧力由减压阀5保证,夹紧结束后,系统压力进一步升高,压力继电器9发出信号,电磁铁1YA带电.(2)快进:电磁铁1YA带电,压力油经换向阀4左腔、行程阀14进入滑台液压缸无杆腔,有杆腔排出油液经换向阀4和单向阀12也进入无杆腔,此时液压缸为差动连接,得快速前进.(3)工进:滑台快速行至终点,压下行程开关14,其上位工作,液压泵排出的油经换向阀4和调速阀13流入缸无杆腔,所需工作进给速度由调速阀13控制.缸有杆腔排出油液经换向阀4、顺序阀10(由于压力升高顺序阀已经打开)和背压阀11流回油箱.(4)快退:加工结束后压下行程开关,压力继电器16发出信号,电磁铁1YA断电,2YA得电,换向阀4换向,其右位工作.压力油通过换向阀4进入液压缸有杆腔,无杆腔油液通过单向阀15和换向阀4流回油箱,完成快退.(5)拔销、松开:滑台退到原位,压下行程开关,电磁铁2YA断电,换向阀4回到中位,液压缸两腔封闭,滑台停止运动;同时电磁铁3YA带电,换向阀7右位工作,泵排出的油流进定位液压缸上腔和夹紧液压缸的下腔,完成拔销和松开动作. (6)工件装夹:动作结束后,变量泵不停止,系统压力升高,压力继电器18接通,电磁铁3YA断电,4YA得电,变量泵卸荷,待装夹完成,电磁铁4YA断电,重复以上操作.2.1 液压缸主要结构参数根据液压系统设计要求,液压缸采用单活塞杆,快进时实施差动连接,初步选择液压缸工作压力P1=2 MPa,液压缸有杆腔与无杆腔的等效作用面积A2与A1应满足公式A1=2A2.为防止铣削加工后工件向前冲出,液压缸回油腔需要保持一定背向压力,暂时取选背压力P2=0.5 MPa,则液压缸的负载方程式为P1A1=P2A2+F,故液压缸无杆腔的有效面积=79 mm,圆整后液压缸内径取值为D=80 mm,活塞杆直径d=0.7D=56 mm.故液压缸有效面积(D2-d2)=2 563.6 mm2.液压缸差动快进时,有杆腔与无杆腔压力差值约为0.5 MPa,活塞快退时候的回油腔压力损失约为0.5 MPa.经计算得出液压缸在各个工作阶段的压力、流量值如表2所示.2.2 液压泵及泵电机选择计算首先确定液压泵的最高压力,组合机床在工进时流量较小,故取泵至缸间压力损失ΔP=0.5 MPa.初步确定液压泵的最高工作压力为Pp为系统静态工作压力,根据一般情况,泵正常工作时,其压力值约为额定压力的80%,因此选泵的额定压力为液压泵的最大流量计算公式为:qp≥KL(∑q)max,其中qp—液压泵的最大极限流量,KL—系统泄漏系数,取值KL=1.2,(∑q)max—各执行元件同时动作时所需总流量最大值,再加上溢流阀的最小溢流量2~3 L/min.故:qp=KL(∑q)max+∑Δq=36.6 L/min.根据以上计算,选用YBS-B40型叶片泵,其额定压力为7 MPa,排量为40 ml/r,额定转速为1 000 r/min.取泵的总效率η=0.8,则所需电机功率为:P=Pp×qp/η=13.1 kW,因此选用Y200L1-6型三相异步电动机,其额定功率为18.5 kW,转速为970 r/min.阀类元件及其它元件型号性能参数见表3所示.执行元件工进时功率损失最大,因而系统发热量也最大,所以只考虑工进时的发热量.执行元件工进时,,即q=0.55L/min,此时泵的效率η为0.8,出口压力为2.86 MPa,那么输入功率P入,输出功率P0=Fv=1.53kW,功率损失ΔP=P入-P出=0.44 kW,散热系数K=20×10-3kW/(cm2·°C),油箱的散热面积,则系统温升℃=6.23℃.温升没有超出允许范围,不必设置热交换器.本文根据汽车变速箱两端面的结构特点,简要介绍了用于加工该变速箱端面的卧式双面铣削组合机床结构特点,并设计出该机床的液压系统,选择符合要求的液压元件.系统完成设计后,通过对系统油液温升进行验算,以保证系统设计符合实际工作需要.【相关文献】[1] 张利平.现代液压技术应用220例[M].北京:化学工业出版社,2009.[2] 张利平.液压传动系统及设计[M].北京:化学工业出版社,2009.[3] 王晔,杨明堂.150T液压机液压系统设计[J].液压与气动,2010,20(8):57-60.[4] 王守城.液压元件及选用[M].北京:化学工业出版社,2007.。
最新组合机床设计

摘要应用组合机床加工大批量零件,快捷高效,生产效率高是机械加工的发展方向。
本次毕业设计的题目是“铣变速箱体两个端面”。
本组合机床要求能实现铣两端面,能进行手动,铣削头能作10mm的微调。
在工艺制定过程中,通过批量的进行铣两端面的加工方案,并寻求最佳的工艺方案,借此说明了工艺在生产过程中的重要性。
本人的设计的主要内容是:进行了机床总体布局设计;对机床的进给和传动部分进行了设计;结合实例,介绍了夹具设计方法;通过此设计,本机床完全能满足设计要求,与传统的机床相比,本机床具有自动化程度高,生产率高,精度高等优点。
关键词:组合机床;铣削头;夹具设计;手动AbstractApplication of combined high-volume machining parts, high efficiency, high productivity is the development direction of machining. The graduation project is entitled "Two face milling gearbox." The combination of milling machine tool required to achieve both ends of surface, can be manual, 10mm milling head can be fine-tuning. Making process in the process, conducted by volume ends face milling processing program, and to seek the best technology solutions, which illustrates the process in the importance of the production process. The main elements of my design are: the general layout for a machine tool design; on the machine feed and transmission parts of the design; Integration for the fixture design; With this design, this machine can meet the design requirements, and the traditional compared to the machine, this machine has high automation, high productivity and high precision.Keywords:combination tool; milling head; fixture design; Manual目录摘要 0Abstract (1)目录 0第1章绪论 01.1 引言 01.2毕业设计的目的 01.3 组合机床概述 0第2章零件的分析 (6)2.1 生产类型的确定 (6)2.2 零件的作用 (6)2.3 零件的工艺分析 (6)2.4变速箱箱体加工的主要问题和工艺过程设计所应采取的相应措施 (7)2.5工艺过程设计中应考虑的主要问题 (8)2.6变速箱箱体加工定位的基准选择 (11)2.6.1粗基准的选择 (11)2.6.2精基准的选择 (11)2.7变速箱体的机械加工余量、工序尺寸及毛坯尺寸的确定 (12)第3章变速箱体材料及毛坯的确定 (14)3.1 变速箱体的材料 (14)3.2 变速箱体的毛坯 (14)第4章工艺规程设计 (15)4.1 基准的选择 (15)4.2 工艺路线的制定 (15)4.3加工设备及工艺装备的选用 (18)4.4 确定精铣箱体两端面的加工余量、切削用量及基本工时 (21)4.4.1 加工余量的确定 (21)4.4.2 切削用量的确定 (21)4.4.3 基本工时的确定 (22)4.4.4编制机床生产率计算卡 (23)第5章组合机床总体设计 (25)5.1 组合机床配置形式的选择 (25)5.2绘制机床联系尺寸图 (25)5.2.1 动力部件的选用 (25)5.2.2 装料高度的确定 (26)5.2.3 侧底座的选择 (26)5.2.4 绘制机床联系尺寸图 (27)5.3绘制铣削变速箱体两端面工序图 (27)5.4 绘制精铣变速箱体两端面加工示意图 (27)5.4.1 刀具的选择 (27)5.4.2 铣削头的选择 (28)5.4.3 对刀元件的选择 (29)5.4.4 绘制加工示意图 (30)第6章.专用夹具设计 (31)6.1 夹具概述 (31)6.1.1 夹具分类 (31)6.1.2 机床夹具的现状 (31)6.1.3现代机床夹具的发展方向 (32)6.2 夹具设计任务 (32)6.3 拟定夹具结构方案 (33)6.3.1 确定工件定位方案及设计选择定位装置 (33)6.3.2 确定工件夹紧方案及设计选择夹紧装置 (35)6.3.3 对刀装置的选择 (36)6.3.4 夹具体与铣床联接定位键的选择 (37)6.3.5 夹具体设计 (37)6.4 定位误差及夹紧力的计算 (38)6.4.1 定位误差的分析计算 (38)6.4.2 夹紧力的分析计算 (38)6.5夹具操作说明 (39)6.6绘制夹具装配图及夹具体零件图 (39)第7章总结 (40)8.参考文献 (41)致谢 (42)第1章绪论1.1 引言机械加工工艺是实现产品设计,保证产品质量,节约能源,降低消耗的重要手段,是企业进行生产准备,计划调度,加工操作,安全生产,技术检测和健全劳动组织的重要依据,也是企业上品种,上质量,上水平,加速产品更新,提高经济效益的技术保证。
卧式双面铣削组合机床的液压系统的毕业设计

卧式双面铣削组合机床的液压系统的毕业设计如何构成液压系统
液压系统是指液压装置各个部件和运行介质组成的系统,它能够实现源进行有效传递和控制能量。
它是液压装置控制机构的关键部件,是能源传递的和运动控制的重要装置,现代机械和工业生产的原动机大都采用液压系统,正因为液压系统以其集优异性能于一身而备受关注,在液压系统方面有着特别的重要性。
一般来说,液压系统由以下几部分组成:
(1)液压油源。
任何液压系统都必须有一个液压油源,一般选用电动润滑油泵。
液压油源负责将耗能系统润滑油输送到运动组件中,以提供系统所需的能量。
(2)液压传动系统。
液压传动系统包括传动容器和各种液压元件。
传动容器具有装满液压油,接收由液压油源输送的液压油并将其分配到各控制组件的功能,液压传动系统涉及比较复杂的液压运动学,在传动系统中要求用到各种液压元件,比较重要的有液压马达、液压缸、控制阀和安全阀。
(3)液压润滑系统。
液压润滑系统是指在安装完所有液压元件后所采用的技术。
液压传动系统不仅传递润滑油,还传递有来自各部件的热量。
液压润滑系统的目的是满足系统正常工作的需要,此外,还要防止润滑油中的气体和尘埃,以保证系统的正常运行。
以上便是构成一个液压系统的三个主要部分,重要的是要理解液压系统的工作原理、工作程序和各种元件的性能,才能够更好地运用液压系统。
变速箱箱体双面复合式单工位组合机床设计

第一章 机床总体方案的制定1第一章 机床总体方案的制定组合机床是由大量的通用部件和少量专用部件组成的工序集中的高效率专用机床。
下图为典型的双面复合式单工位组合机床。
组合机床具有如下特点:1)主要用于棱体类零件和杂件的孔面加工。
2)生产率高。
因为工序集中,可多面、多工位、多轴、多刀同时自动加工。
3)加工精度稳定。
因为工序固定,可选用成熟的通用部件、精密夹具和自动工作循环来保证加工精度的一致性。
4)研制周期短,便于设计、制造和使用维护,成本低。
因为通用化、系列化程度高,通用零部件占70%~90%,通用件可组织批量生产进行预制或外购。
5)自动化程度高,劳动强度低。
第一章机床总体方案的制定6)配置灵活。
因为结构模块化、组合化。
可按工件或工序要求,用大量通用部件和少量专用部件灵活组成各种类型的组合机床及自动线;机床易于改革:产品或工艺变化对通用部件一般还可以重复利用。
1.1工艺分析及方案确定被加工零件需要在组合机床上完成的加工工序及应保证的加工精度,是制定机床方案的主要依据。
整体工艺分析:1.粗铣、半精铣与上盖联接平面。
2.I钻定位工艺孔,钻定位环沉孔并孔口倒角;II钻定位环孔下部螺纹孔,铰定位工艺孔;III钻油孔。
3.粗铣导向侧面及输送棘爪用平面。
4.第一条自动线粗铣前后端面。
5.半精铣削后端面。
6.粗镗主轴轴承孔,钻倒挡齿轮轴孔。
7.左动力头钻轴-轴承盖紧固螺钉用螺纹孔,钻离合器外壳紧固螺钉用螺纹孔;右动力头钻轴-轴承盖紧固螺钉用螺纹孔,钻倒挡轴锁片螺纹孔,钻后支架紧固螺钉用螺纹孔,钻油孔2- 8通孔。
8.盲孔探测。
9.左动力头攻螺纹6-M10x1.5,攻螺纹6-M18x2.5;右动力头攻螺纹12-M10x1.5,攻螺纹M8x1.25。
10.中间检查。
11.第二条自动线粗铣取力箱联接平面。
2第一章机床总体方案的制定12.钻取力箱紧固用螺纹孔,钻放油螺纹孔。
13.钻刹车器联接螺纹孔及注油孔。
14.盲孔探测。
- 1、下载文档前请自行甄别文档内容的完整性,平台不提供额外的编辑、内容补充、找答案等附加服务。
- 2、"仅部分预览"的文档,不可在线预览部分如存在完整性等问题,可反馈申请退款(可完整预览的文档不适用该条件!)。
- 3、如文档侵犯您的权益,请联系客服反馈,我们会尽快为您处理(人工客服工作时间:9:00-18:30)。
摘要本课题设计一台粗铣汽车变速箱两端面液压双头组合铣床,主要完成组合铣床的总体设计、主轴箱及设计及其液压部分的设计。
根据汽车变速箱的结构特点、加工部位、尺寸精度、表面粗糙度及生产率等要求,确定该机床为双工位卧式组合机床;考虑工件尺寸精度,表面粗糙度,切屑的排除及生产率等因素,选用硬质合金套式面铣刀;根据工件的尺寸、特点及其材料选择切削用量;然后,再经过切削用量来确定组合机床的通用部件;最后进行组合机床的总体设计。
由于是粗铣柴油机汽缸体两端面,则夹具的设计采用“一面两销”定位, 液压夹紧,一次装夹加工柴油机汽缸体的两个端面,保证了加工精度,提高了生产效率。
在设计之中,尽量选用通用件,减少了制造成本,增加了经济效益。
通过本次设计可以达到效果是:所设计的组合铣床和夹具能满足其工作状态的质量要求,使用时安全可靠,易于维修。
关键词:组合铣床汽车变速箱铣刀主轴箱AbstractThis topic design a rough milling automobile gearbox two end milling machine, hydraulic double combination of main machine combination overall design, spindle box and design and the design of hydraulic parts.According to the structure characteristics of the automobile gearbox, machining parts and precision and surface roughness and productivity, determine the machine for double-position horizontal combination machine tools . Considered to the factor of the size precision, surface roughness, scrap removes and productivity and so on of the work piece, selects the Hard alloy not grind type surface milling cutter. According to work piece size, characteristic and its material choice cutting specifications;Because of the thick mill diesel engine cylinder body two sides, then the jig design use "two sells the localization at the same time", Manual clamps, an attire clamps processes the diesel engine to be mad the cylinder body two sides;according to will work receives the cutting force to calculate clamps the strength;again according to clamps the strength , choose the determination clamp the special-purpose part.During the design, the standard parts are selected as far as possible, to reduced the production cost, increased the economic efficiency.This design may achieve the effects as fowllows: the modular milling machine and the jig can satisfy its the quality requirement at working status,it’s safe, and easy to service.Keyword:the modular milling machine Auto gearbox milling cutter main spindle目录摘要...................................................................... I ABSTRACT ................................................................... II1 引言 (5)2 总体方案论证 (5)2.1被加工零件分析 (5)2.2工艺方案的制定 (5)2.3加工设备方案选择 (6)2.4确定机床总体布局 (6)3 切削用量的选择及计算 (8)3.1切削刀具的选择 (8)3.2切削用量的选择 (8)3.3切削力、切削转矩、切削功率的确定 (9)4 组合机床总体设计 (12)4.1被加工零件工序图 (13)4.2加工示意图 (14)4.3机床联系尺寸图 (15)4.3.1 动力部件的选择 (15)4.3.2 滑台及相配底座的选择 (15)4.3.3 确定机床的装料高度H (16)4.4机床生产率计算卡 (16)4.4.1 理想生产率Q (16) (17)4.4.2 实际生产率Q1 (18)4.4.3 机床负荷率ŋ负4.4.4 编写机床生产率计算卡 (19)5 主轴箱设计 (21)5.1主轴及传动轴结构设计 (21)5.2主轴箱传动计算 (23)5.2.1 传动比分配 (23)5.2.2 传动系统设计及齿轮的排布 (24)5.3主轴箱的润滑及油泵轴的确定 (26)5.4轴的计算及主轴校核 (26)5.5齿轮的校核 (29)5.6轴承的选择与校核 (32)6 液压系统设计 (35)6.1负载分析 (35)6.2负载图和速度图的绘制 (36)6.3液压缸主要参数的确定 (36)6.4拟定液压系统原理图 (40)6.4.1 液压系统的工作要求的确定 (40)6.4.2 拟定液压系统图 (40)6.5计算和选择液压元件 (44)6.5.1 确定液压泵的最高工作压力 (44)6.5.2 确定液压泵流量 (44)6.5.3 选择液压泵规格 (44)6.6阀类元件的选择 (45)6.7油管的确定 (45)6.8确定其它辅助装置 (46)6.9发热及油箱容量计算 (46)结论 (47)致谢 (48)参考文献 (49)1 引言组合机床是根据工件加工要求,以大量通用部件为基础,配以少量专用部件组成的一种高效专用机床。
组合机床的设计,有以下两种情况:其一,是根据具体加工对象的具体情况进行专门设计。
其二,随着组合机床在我国机械行业的广泛使用,广大工人总结自己生产和使用组合机床的经验,发现组合机床不仅在其组成部件方面有共性,可设计成通用部件,而且一些行业的在完成一定工艺范围的组合机床是极其相似的,有可能设计为通用机床,这种机床称为“专能组合机床”。
这种组合机床就不需要每次按具体加工对象进行专门设计和生产,而是可以设计成通用品种,组织成批生产,然后按被加工的零件的具体需要,配以简单的夹具及刀具,即可组成加工一定对象的高效率设备。
近10年来,许多汽车制造厂商都在推行并行政策,并有不少组合机床制造厂与汽车厂密切合作应用这一方法来加速专用装备的设计制造。
我国机械制造业各企业有大量的通用设备,在发展现代机械自动化技术时,若以原有的设备为主,合理调整机床布局,添加少量的数控设备,引入CAD/CAM技术,充分发挥计算机自动化管理的优势和人的创造性,共同构成一个以人为中心、以信息自动化为先导、树立自主的单元化生产系统,为我国机械制造业自动化技术发展应用提供了一条投资少、见效快、效益高、符合我国国情的机械自动化技术发展应用新途径。
特别是近20年来,随着组合机床的发展,作为组合机床主要用户的汽车和内燃机等行业也有很大的变化,起产品市场寿命不断缩短,品种日益增多且质量不断提高。
这些因素同时也有力地推动和激励了组合机床的不断发展。
组合机床的发展主要有以下2点:(1) 组合机床品种的发展;(2) 组合机床柔性化的发展。
组合机床是一项发展投资少、见效快的低成本自动化技术,它的兴起会带动我国企业的发展,为市场经济带来明显的效益;它的发展促进了我国工业的自动化程度的日益完善,同时带来技术和装备上的革新。
组合机床的使用能够使生产过程全盘自动化,全面提高生产效率和产品质量,大幅度的节省了劳动力,机床上的标准零件和通用部件占全部机床零件总量的70%--80%,设计周期短,易于改装和维修。
本次毕业设计的课题是汽车变速箱两端面铣削液压组合机床设计。
根据汽车变速箱两侧面的位置、加工精度等主要的设计原始数据,设计出技术上先进,经济上合理和工作上可靠的双面粗铣的组合机床。
组合机床的加工精度基本上是由夹具来保证的,因此它与一般机床夹具不同。
本次设计的组合机床夹具主要对汽车变速箱两端面的粗铣,因此采用面两销定位方式,即利用零件上的一个平面和该平面上的两个孔作为定位基准。
一个孔插圆柱销,另一个孔插菱形销。
这种定位方法保证了理论上的六点定定位原则(平面上三个点,圆柱销两个点和菱形销一个点)。
要设计出这种组合机床,要先对汽车变速箱体结构进行工艺性分析,确定整体的设计方案,提出一到两种可行性比较高的初步设计方案;根据目前所提供的工况条件,每天的工作时间、强度等对初步设计方案进行论证,最后根据论证结果选择最合适的设计方案;再进行组合机床方案图样文件设计:被加工零件加工工序图,加工示意图,机床联系尺寸图以及生产率计算卡。
本次设计的组合机床能同时粗铣汽车变速箱体的两端面,大大提高了生产效率,降低了劳动强度,从而降低了零件的加工成本。
2 总体方案论证设计的机床要满足加工要求、保证加工精度;尽可能选用通用件、以降低成本。
因此根据上述要求和汽车变速箱体的加工特点来确定设计方案。
2.1 被加工零件分析被加工零件:汽车变速箱体材料:HT250硬度:HT150年产量:70000件加工部位:两端面,两端面尺寸至加工要求:汽车变速箱体两端面糙度度被加工到 6.3m371±0.25mm。
2.2 工艺方案的制定工艺方案的拟订是组合机床设计的关键一步。