微细加工9
微细加工工艺方法

变色龙模板标题
此处文字可编辑
此处文字可编辑此处文字 可编辑此处文字可编辑此 处文字可编辑
第2页/共11页
微细加工方法
1.微细车削加工 2.微细铣削加工 3.微细钻削加工 4.微细冲压加工
第3页/共11页
ቤተ መጻሕፍቲ ባይዱ
第4页/共11页
1、微细切削加工技术 2、微细电火花加工技术 3、微细电化学加工技术 4、高能束流微细特种加工技术(包 括微细 激光加 工技术 、电子 束加工 技术、 离子束 加工技 术) 5、LIGA技术 6、生长型微细加工技术
微细特种加工分类
第5页/共11页
电火花加工的零件
变色龙模板
此处文字可编辑此处文字可编辑
第6页/共11页
微型机械
第7页/共11页
第8页/共11页
第9页/共11页
祝大家假期愉快!
Thanks
第10页/共11页
微细加工和超微细加工以分离或结合原 子、分 子为加 工对象 ,以电 子束、 技工束 、粒子 束为加 工基础 ,采用 沉积、 刻蚀、 溅射、 蒸镀等 手段进 行各种 处。
变色龙模板标题
此处文字可编辑
此处文字可编辑此处文字 可编辑此处文字可编辑此 处文字可编辑
变色龙模板标题
此处文字可编辑
此处文字可编辑此处文字 可编辑此处文字可编辑此 处文字可编辑
1、精度的表示方法
在微小尺寸加工时,由于加工尺寸 很小, 精度就 必须用 尺寸的 绝对值 来表示 ,即用 取出的 一块材 料的大 小来表 示,从 而引入 加工单 位尺寸 的概念 。 2、微观机理
以切削加工为例,从工件的角度来讲, 一般加 工和微 细加工 的最大 区别是 切屑的 大小。 一般为 金属材 料是由 微细的 晶粒组 成,晶 粒直径 为数微 米到数 百微米 。一般 加工时, 吃刀量 较大, 可以忽 略晶粒 的大小 ,而作 为一个 连续体 来看待 ,因此 可见一 般加工 和微细 加工的 机理是 不同的 。 3、加工特征
微细加工的分类与主要指标

微细加工与一般的加工的不同1 加工精度的表示方法不同2 加工机理存在很大的差异3加工特征明显不同微细加工的分类金刚石车削 微细钻削微细磨削 研磨 抛光 砂带研抛弹性发射加工 喷射加工微细电火花加工 电解加工 超声波加工电子束加工 激光束加工 离子束加工 光刻加工电解磨削 电解抛光化学抛光蒸镀 分子束镀膜 分子束外延生长离子束镀膜 电镀 电铸 喷镀 离子束注入 氧化、阳极氧化 扩散 激光表面处理电子书焊接 超声波焊接 激光焊接切削加工磨料加工特种加工复合加工附着加工注入加工结合加工 分离加工结合加工变形加工 压力变形微制造技术一直存在三大主流方向,其一是美国为代表的基于硅平面技术发展起来的硅加工技术;其二是一德国为代表的LIGA 技术;另一个则是以日本为代表的由传统切削加工技术和特种加工方法演化而来的微细加工技术。
微细电火花技工技术与普通的电火花技工技术并无本质的区别。
其加工的表面质量取决于电蚀凹坑的大小和深度,即单个脉冲的能量;其加工精度则与电极损耗、伺服稳定性等因素有关。
当脉冲电压施压到工具电极和工件电极之间时,极间介质击穿并形成一个极小的放电通道。
放电通道中的电子和离子受到放电时的电磁力和周围介质的压缩,因此截面积很小,通道中的电流密度极大,可达 274/)10~10(cm A 。
放电通道是由数量大致相等的正离子和电子以及中性原子组成的等离子体。
在极间电场的作用下,通道中的正离子和负离子分别向阴极和阳极运动并发生剧烈的碰撞,从而产生大量的热量;同时,阳极和阴极表面分别受到电子流和离子流的撞击,动能也转化为热能,在电极表面产生大量的热,整个放电通道形成一个瞬时的热源,其间温度可达10000℃以上。
另外,由于电火花放时的电流会产生磁场,该磁场又反过来对电子流产生向心的磁压缩效应和周围介质惯性动力压缩效应的作用,通道瞬间扩展受到很到的阻力。
故而放电开始阶段通道截面积很小,而通道内由于高温膨胀形成的初始压力可达数十甚至上百个千帕,高温高压的放电通道以及随后瞬时气化形成的气体急速扩展、产生一个强烈的冲击波向四周传播。
微细加工工艺方法

束、粒子束为加工基础,采用沉积、刻蚀、溅射、蒸镀等手段进行各种处。
微细加工方法
1. 微细车削加工 2. 微细铣削加工 3. 微细钻削加工 4. 微细冲压加工
微细特种加工分类
1、微细切削加工技术 2、微细电火花加工技术 3、微细电化学加工技术 4、高能束流微细特种加工技术(包括微细激光加工技术、电子束加工技术、 离子束加工技术) 5、LIGA技术 6、生长型微细加工技术
电火花加工的零件
变色龙模板
此处文字可编辑此处文字可编辑
微型机械
祝大家假期愉快!
Thanks
般加工时,吃刀量较大,可以忽略晶粒的大小,而作为一个连续体来看待,因此可见
一般加工和微细加工的机变理色龙是模不板同标的题 。 变色龙模板标题
变色龙模板标题
3、加工特征
此处文字可编辑
此处文字可编辑
此处文字可编辑
此处文字可编辑此处文字
此处文字可编辑此处文字
此处文字可编辑此处文字
微细加工和超微细加可 处编 文工辑 字此 可以处编文 辑分字离可编或辑此结合原可 处子编 文辑 字、此 可处 编分文 辑字子可编为辑加此 工对可处象编文,辑字此可以处编文辑电字可子编束辑此、技工
微小尺寸和一般尺寸加工是不同的,其不同点主要表现在以下几个方面:
1、精度的表示方法
在微小尺寸加工时,由于加工尺寸很小,精度就必须用尺寸的绝对值来表示,即
用取出的一块材料的大小来表示,从而引入加工单位尺寸的概念。
2、微观机理
以切削加工为例,从工件的角度来讲,一般加工和微细加工的最大区别是切屑
的大小。一般为金属材料是由微细的晶粒组成,晶粒直径为数微米到数百微米。一
微细加工技术的概念和特点
微细加工工艺技术

微细加工工艺技术微细加工工艺技术是一种应用于微电子、光学、纳米学等领域的高精度加工技术,该技术能够实现对微细结构的精密加工。
在微细加工工艺技术中,常常采用的加工方法有激光刻蚀、化学蚀刻、光刻以及微电子束等。
激光刻蚀是一种应用激光照射,通过激光束的高能量将材料表面局部蚀刻的加工方法。
与传统的机械刻蚀相比,激光刻蚀具有高精度、高效率的优点。
在激光刻蚀中,光束的聚焦度和光斑直径是影响加工精度的重要参数。
化学蚀刻是一种利用特定的化学反应,在材料表面选择性地产生化学蚀刻产物,并将其去除的加工方法。
化学蚀刻通常需要制备特定的蚀刻溶液,通过控制溶液的浓度和温度,来影响化学反应的速率和选择性。
化学蚀刻可以实现微细结构的高精度加工,并被广泛应用于光学元件和微流控芯片等领域。
光刻是一种基于光化学反应的加工方法,通过光阻的选择性暴露和去除,来形成所需的图案结构。
在光刻过程中,首先在材料表面涂敷一层光刻胶,然后利用光刻机的紫外光照射和显影等步骤,实现图案的转移。
光刻具有高精度、高分辨率和高重复性的优点,是微细加工中不可或缺的工艺之一。
微电子束也是一种实现微细结构加工的重要方法。
微电子束利用高能电子束在材料表面定向照射,经过准直、聚焦和偏转等步骤,将电子束的能量转化为对材料的加工作用。
通过控制电子束的参数,如能量、聚焦度和扫描速度等,可以实现对微细结构的精密加工。
微电子束在高精度加工领域具有很大的应用潜力,尤其在微电子器件、光电器件以及半导体器件等方面,具有广阔的发展前景。
总的来说,微细加工工艺技术是一种实现高精度加工的重要方法,包括激光刻蚀、化学蚀刻、光刻和微电子束等。
这些加工方法在微电子、光学、纳米学等领域发挥着重要作用,推动了相关技术的进步和应用的发展。
未来随着科学技术的不断进步,微细加工工艺技术将继续发展壮大,为人类社会带来更多的科技成果和应用产品。
微细加工

光刻技术
①光复印工艺:经曝光系统将预制在掩模版上的器件或电路图形按所要求的位置, 精确传递到预涂在晶片表面或介质层上的光致抗蚀剂薄层上。
光刻技术
基本步骤
1.气相成底模 2.旋转烘胶
3.软烘
4.对准和曝光 5.曝光后烘焙(PEB) 6.显影
7.坚膜烘焙
8.显影检查
三、LIGA技术
□ LIGA即光刻、电铸和注塑的缩写。是一种公认的全新三 维立体微细加工技术。
光刻技术
常规光刻技术是采用波长为2000~4500埃的紫外光作为图像信 息载体,以光致抗光刻技术 蚀剂为中间(图像记录)媒介实现图形的变换、转移和处理, 最终把图像信息传递到晶片(主要指硅片)或介质层上的一种工艺 (图1)。在广义上,它包括光复印和刻蚀工艺两个主要方面。
光刻技术
①刻蚀工艺:利用化学或物理方法,将抗蚀剂薄层未掩蔽的晶片表面或介质层除去,从 而在晶片表面或介质层上获得与抗蚀剂薄层图形完全一致的图形。集成电路各功能层是 立体重叠的,因而光刻工艺总是多次反复进行。例如,大规模集成电路要经过约10次 光刻才能完成各层图形的全部传递。在狭义上,光刻工艺仅指光复印工艺,即图1中从④ 到⑤或从③到⑤的工艺过程。
◇ 微细加工起源于半导体制造工艺,加工方式十分丰富, 包含了微细机械加工、各种现代特种加工、高能束加工等 方式。
微细加工的特点
1、体积小,精度高,重量轻 其体积可达亚微米以下,尺寸精度达纳米级,重量可达纳克。目前已经制造出 直径细如发丝的齿轮,有资料表明,科学家们已能在5平米内放置1000台微型 发动机。 2、性能稳定,可靠性好 由于微机械体积小,几乎不受热膨胀、噪声等影响,具有较高的抗干扰性, 可在较差的环境里稳定的工作。 3、能耗低,灵敏度和工作效率高 耗能远小于传统机械的十分之一 4、多功能和智能化 微机械集传感器、执行器、信号处理器和电路控制于一体,故而易于实现多 能化和智能化 5、适用于大批量生产,制造成本低
微细加工技术的研究与应用
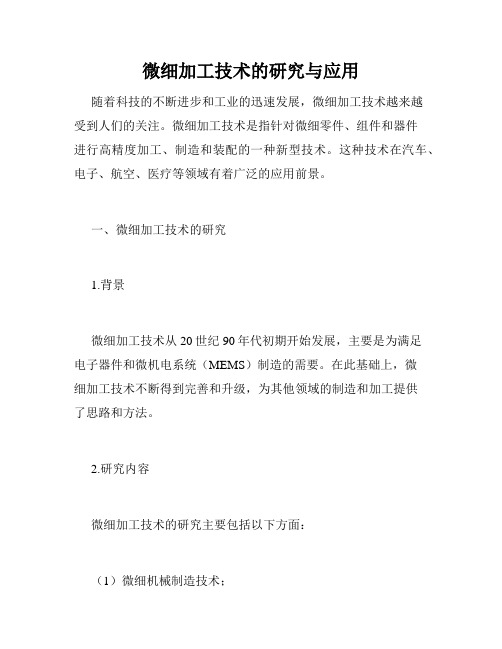
微细加工技术的研究与应用随着科技的不断进步和工业的迅速发展,微细加工技术越来越受到人们的关注。
微细加工技术是指针对微细零件、组件和器件进行高精度加工、制造和装配的一种新型技术。
这种技术在汽车、电子、航空、医疗等领域有着广泛的应用前景。
一、微细加工技术的研究1.背景微细加工技术从20世纪90年代初期开始发展,主要是为满足电子器件和微机电系统(MEMS)制造的需要。
在此基础上,微细加工技术不断得到完善和升级,为其他领域的制造和加工提供了思路和方法。
2.研究内容微细加工技术的研究主要包括以下方面:(1)微细机械制造技术;(2)微细电子制造技术;(3)微细光学制造技术;(4)微细生物制造技术。
其中,微细机械制造技术是应用最为广泛的一项技术,主要针对微型零部件、机械组件和器件等进行加工和制造。
3.研究难点微细加工技术的研究面临着许多难点,其中最主要的难点是如何实现高精度加工。
微细零部件的尺寸通常都在数微米至数百微米之间,而传统加工技术所能达到的精度却远远不够。
因此,如何在微小尺度下进行高精度加工,是微细加工技术研究的核心问题。
二、微细加工技术的应用1.汽车制造领域汽车制造领域是微细加工技术应用的主要领域之一。
在汽车制造中,许多零部件的尺寸都很小,而且对加工精度要求很高。
例如,发动机的火花塞、气门、燃油喷嘴等部件;车身的紧固件、密封件和缝合件等,都需要采用微细加工技术进行加工和制造。
2.电子制造领域电子制造领域也是微细加工技术应用的重要领域之一。
在电子制造中,许多IC芯片、闪存和存储器等器件的结构都非常微小,需要采用微细加工技术进行精密加工和制造。
同时,电子制造领域还需要采用微细加工技术进行导电薄膜的制造、微型电极的加工等工作。
3.医疗领域医疗领域也是微细加工技术应用的一个新兴领域。
在医疗领域中,微细加工技术可以用于制造微型手术器械、医用传感器、微型分析芯片等器件,从而为医疗诊断和治疗提供了新的手段和方法。
现代加工技术-微细加工

电火花加工2♥ 电火花线切割加工3♥
电化学加工4♥
Байду номын сангаас
♥7电子束、离子束加工 现代加工技术-16微细加工
超声波加工5♥
♥7电子束、离子束加工 现代加工技术-16微细加工
激光加工6♥
♥8化学、等离子体、快速成型、磁性磨料加工
电子束、离子束加工7♥
现代加工技术-16微细加工
现代加化工技术学-16微、细加工等离子体、快速成型、磁性磨料加工8♥
♥7电子束、离子束加工 ♥8化学、等离子体、快速成型、磁性磨料加工
磨料喷射加工与水喷射加工9♥
现代加工技术-16微细加精工 密和超精密加工、高速加工、微细加工10♥
♥7电子束、离子束加工
2
现代加工技术-16微细 加工
♥7电子束、离子束加工 ♥7电子束、离子束加工 ♥9磨料喷射加工与水喷射加工 现代加工技术-16微细加工 ♥9磨料喷射加工与水喷射加工
哈工大(威海) 现代加工技术
内容大纲
绪论1♥
现代加工技术-16微细加工 ♥8化学、等离子体、快速成型、磁性磨料加工 ♥7电子束、离子束加工 ♥8化学、等离子体、快速成型、磁性磨料加工 现代加工技术-16微细加工
表面微细加工技术

表面微细加工技术微细加工技术结合了超精增亮和超精抛光两项革新技术,能够有选择性地保留表面的微观结构,以提高表面的摩擦和滑动性能(表面技术),以机械化和自动化取代传统的手工抛光,提高表面的美学功能。
这种微细加工技术应用于切削刀具、冲压和锻造工具,航空、汽车、医疗器械、塑料注射模具等机械零件的表面处理,能够极大地改善零件表面的性能。
微细加工技术采用全自动方式对金属零件表面进行超精加工,通过一种机械化学作用来清除金属零件表面上1~40μm的材料,实现被加工表面粗糙度达到或者好于ISO标准的N1级的表面质量。
微细加工技术主要应用于超精抛光和超精增亮这两个领域。
超精抛光使传统的手工抛光工艺自动化而超精增亮则生成新的表面拓扑结构。
纳米技术其实就是一种用单个原子、分子制造物质的技术。
纳米科技现在已经包括纳米生物学、纳米电子学、纳米材料学、纳米机械学、纳米化学等学科。
从包括微电子等在内的微米科技到纳米科技,人类正越来越向微观世界深入,人们认识、改造微观世界的水平提高到前所未有的高度。
我国著名科学家钱学森也曾指出,纳米左右和纳米以下的结构是下一阶段科技发展的一个重点,会是一次技术革命,从而将引起21世纪又一次产业革命。
•光刻是一种以光复印图形和材料腐蚀相结合的表面精密加工技术。
前者是使图形复印到基片表面的光刻胶上,后者是把图形刻蚀到基片表面的各层材料(如Si02、Si3N4、多晶硅、铝等)上。
光刻胶上图形的复印是通过曝光和显影完成的。
限制图形重复性及分辨率的主要因素,是图形加工过程中所涉及到的物理和化学问题。
•在集成电路生产中,要经过多次光刻。
虽然各次光刻的目的要求和工艺条件有所不同,但其工艺过程是基本相同的。
光刻工艺一般都要经过涂胶、前烘、曝光、显影、坚膜、刻蚀和去胶7个步骤。
•涂胶就是在SiO2或其他薄膜表面涂一层粘附良好、厚度适当、厚薄均匀的光刻胶膜。
涂胶前的基片表面必须清洁干燥。
生产中最好在氧化或蒸发后立即涂胶,此时基片表面清洁干燥,光刻胶的粘附性较好。
- 1、下载文档前请自行甄别文档内容的完整性,平台不提供额外的编辑、内容补充、找答案等附加服务。
- 2、"仅部分预览"的文档,不可在线预览部分如存在完整性等问题,可反馈申请退款(可完整预览的文档不适用该条件!)。
- 3、如文档侵犯您的权益,请联系客服反馈,我们会尽快为您处理(人工客服工作时间:9:00-18:30)。
二、电子束与固体之间的相互作用 电子束与固体之间的相互作用有很多种,例如二次电子、 电子束与固体之间的相互作用有很多种,例如二次电子、 散射电子、吸收电子、电子空穴对、阳极发光、 射线、 散射电子、吸收电子、电子空穴对、阳极发光、X 射线、俄歇 电子等。影响电子束曝光分辨率的主要是 散射电子 。 电子等。 1、电子的散射 入射电子与固体中另一粒子发生碰撞, 入射电子与固体中另一粒子发生碰撞,发生动量与能量的 转移,方向改变,能量减少,波长增大。 转移,方向改变,能量减少,波长增大。 电子在光刻胶中的散射次数与光刻胶厚度成正比, 电子在光刻胶中的散射次数与光刻胶厚度成正比,与入射 成反比,典型值为几到几十次。 电子的初始能量 E0 成反比,典型值为几到几十次。
散射角:电子散射后的方向与原入射方向之间的夹角。 散射角:电子散射后的方向与原入射方向之间的夹角。 前散射(小角散射):散射角 前散射(小角散射):散射角 < 90o ): 背散射(大角散射):散射角 背散射(大角散射):散射角 = 90o ~ 180o ): 实验表明, 实验表明,前散射使电子束变宽约 0.1 m,而背散射电子 , 的分布区域可达到 0.1 ~ 1 m 。所以 背散射是影响电子束曝光 分辨率的主要因素。 分辨率的主要因素。
1.225 λ= (nm) Va
考虑到相对论效应后,λ应修正为 考虑到相对论效应后,
λ=
1.225 Va 1+ 0.978×106Va
(nm)
电子束曝光的加速电压范围一般在 Va = 10 ~ 30 kV,这时 , 电子波长λ的范围为 0.012 ~ 0.007 nm。 。
以下, 电子束本身的分辨率极高 ,可以达到 0.01 m 以下,但是 左右的线宽。 在光刻胶上一般只能获得 0.1 m 左右的线宽。限制电子束曝光 分辨率的因素有, 分辨率的因素有, 1、光刻胶本身的分辨率 、 2、电子在光刻胶中的散射引起的邻近效应 、 3、对准问题 、
例如,当电子束分布为 高斯圆形束 时, 例如,
r2 u(r,θ ) = u(r) = exp 2 2β g
r r′ 2 ∞ Eg (r, z) = 2π ∫ Eδ (r′, z)exp r′dr′ 2 0 2βg
式中, 为高斯电子束的标准偏差。 式中,βg 为高斯电子束的标准偏差。
离子注入: 离子注入: > 50 keV
9.2 直写电子束光刻系统
电子束的波长短,因此电子束曝光的分辨率很高, 电子束的波长短,因此电子束曝光的分辨率很高,是目前 获得深亚微米高分辨率图形的主要手段之一。 获得深亚微米高分辨率图形的主要手段之一。 电子、离子等微观粒子具有波粒二象性, 电子、离子等微观粒子具有波粒二象性,由德布罗意关系
2、光刻胶的能量吸收密度 电子束曝光的分辨率主要取决于电子散射的作用范围, 电子束曝光的分辨率主要取决于电子散射的作用范围,而 此范围可用光刻胶的能量吸收密度分布函数来表示。 此范围可用光刻胶的能量吸收密度分布函数来表示。由于能量 密度函数是轴对称的, 无关, 密度函数是轴对称的,与变量 θ 无关,故可表为 E( r, z ) 。
用上述模拟方法对硅上的 PMMA 胶进行计算的结果以及 实际的胶层剖面轮廓如下图所示, 实际的胶层剖面轮廓如下图所示,
模拟结果 实际结果
5、电子束曝光的邻近效应及其修正方法 已知电子的散射特别是背散射, 已知电子的散射特别是背散射,其影响范围可与电子射程 或胶层厚度相当, 邻近效应。 或胶层厚度相当,这称为电子束曝光的 邻近效应。对于一个其 的图形, 线度 L 远大于电子散射范围 R 的图形,虽然其中间部分的曝光 是均匀的,但边缘部分的情况就不同了,如下图所示, 是均匀的,但边缘部分的情况就不同了,如下图所示,
第 9 章 非光学光刻技术
通过使用大数值孔径的扫描步进光刻机和深紫外光源, 通过使用大数值孔径的扫描步进光刻机和深紫外光源,再 结合相移掩模、光学邻近效应修正和双层胶等技术, 结合相移掩模、光学邻近效应修正和双层胶等技术,光学光刻 的分辨率已进入亚波长, 的分辨率已进入亚波长,获得了 0.1m 的分辨率。若能开发出 的分辨率。 适合 157 nm 光源的光学材料,甚至可扩展到 0.07 m。 光源的光学材料, 。 但是这些技术的成本越来越昂贵, 但是这些技术的成本越来越昂贵,而且光学光刻的分辨率 已开发出许多新的光刻技术, 射线、 极限迟早会到来 。已开发出许多新的光刻技术,如将 X 射线、 电子束 和 离子束作为能量束用于曝光。这些技术统称为非光学 离子束作为能量束用于曝光 这些技术统称为非光学 作为能量束用于曝光。 光刻技术, 光刻技术,或 下一代光刻技术 。它们的共同特点是使用更短波 长的曝光能源。 长的曝光能源。
(5) 胶层等能量密度剖面轮廓 实际的曝光图形,既不是 δ 函数,也不是仅仅一个孤立的 实际的曝光图形, 函数, 圆形束斑,如果是一条有宽度的线条, 圆形束斑,如果是一条有宽度的线条,其能量吸收密度应当是 各入射电子束的作用的总和,如下图所示。 各入射电子束的作用的总和,如下图所示。
y
Rn =
(nd )2 + x 2
能量损失与分辨率的关系 分辨率取决于 X 射线的波长与光电子的射程两者中较大的 左右时两者相等, 一个 。当 X 射线波长为 5 nm 左右时两者相等,这时可获得最 射线光刻技术中, 佳分辨率 ,其值即约为 5 nm 。但在 X 射线光刻技术中,由于 掩模版等方面的原因 ,波长取为 0.2 ~ 4 nm ,其相应的光电子 射程为 70 ~ 20 nm。但是实际上这并不是限制 X 射线光刻分辨 。 率的主要因素。 率的主要因素。 后面会讲到, 后面会讲到,限制 X 射线光刻分辨率的主要因素是 掩模版 的分辨率, 的分辨率,以及 半影畸变 和 几何畸变。 几何畸变。
接近式 X 射线 X 射线 射线(极紫外光) 投影式 X 射线(极紫外光) 直写曝光(无掩模) 直写曝光(无掩模) 电子束 投影曝光(有掩模) 投影曝光(有掩模)
离子束
9.1 高能束与物体之间的相互作用
射线、电子束、 本节主要讨论 X 射线、电子束、离子束与固体之间的相互 作用。 作用。 一、X 射线与固体之间的相互作用 X 射线光刻所用的波长在λ= 0.2 ~ 4 nm 的范围,所对应的 的范围, X 射线光子能量为 1 ~ 10 keV。在此能量范围,X 射线的散射可 。在此能量范围, 以忽略 。X 射线光子的能量损失机理以光电效应为主,损失掉 射线光子的能量损失机理以光电效应为主, 的能量转化为光电子的能量。 的能量转化为光电子的能量。
内邻近效应 无散 射时 互邻 近效 应 能量密度
邻近效应的后果 (1) 对 L >> R 的孤立图形,使边缘模糊。 的孤立图形,使边缘模糊。 (2) 对 L <= R 的孤立图形,使边缘曝光不足,图形变小、 的孤立图形,使边缘曝光不足,图形变小、 变圆,甚至曝不出来。 变圆,甚至曝不出来。 (3) 对间距 a <= R 的多个图形 ,使间距变小,甚至相连。 使间距变小,甚至相连。 减小电子邻近效应的方法 减小入射电子束的能量( 先大后小), ),或采用低 减小入射电子束的能量(因β 随 E0 先大后小),或采用低 原子序数的衬底与光刻胶。 原子序数的衬底与光刻胶。
修正电子邻近效应的方法 电子束图形 曝光显影后 有邻近效应
几何修正
剂量修正
三、离子束与固体之间的相互作用 离子束与固体之间的相互作用有:散射(碰撞)、辐射损 离子束与固体之间的相互作用有:散射(碰撞)、辐射损 )、 伤(产生位错)、溅射(刻蚀及镀膜)、俘获(离子注入)、 产生位错)、溅射(刻蚀及镀膜)、俘获(离子注入)、 )、溅射 )、俘获 激发、电离、电子发射、二次离子发射等。 激发、电离、电子发射、二次离子发射等。 这些效应的强弱随入射离子的能量不同而不同。用于集成 这些效应的强弱随入射离子的能量不同而不同。 电路制造技术的入射离子能量范围为 刻蚀、镀膜: 刻蚀、镀膜:< 10 keV 曝光: 曝光: 10 keV ~ 50 keV
h h p = mv = , λ = = λ p mv
1 2 2qVa 代入波长λ中,得 又由 mv = qVa , v = , 2 m h λ= (2mqVa )1 2
越大, 越小。 质量 m 和加速电压 Va 越大,则波长λ越小。
1 2
h
绝对静电单位, 将 h = 6.62×10-27 erg/s ,q = 4.8×10-10 绝对静电单位,电 × / × 代入, 子质量 m = 9.1×10-27 g 代入,得 ×
x
P
nd d
设电子束的束流为 IB ,在每个 点上停留的时间为 t ,则每个束斑 上的入射电子数为 ( IB t / q ) ,每个 束斑产生的吸收能量密度为
(IB t / q)Eg (r, z)
则在离线条距离为 x 的点 P 下面深 度为 z 处的能量吸收密度为
∞ IB t El (x, z) = Eg (x, z) + 2∑Eg (Rn , z) q n=1
(3) 对此模拟结果进行 曲线拟合,可得到近似的分析函数, 曲线拟合,可得到近似的分析函数, 为 双高斯函数 ,即
Eδ (r, z) = ff (r, z) + fb (r, z) r2 r2 = k(z) exp 2 +ηE exp 2 2α 2β
通过模拟计算,发现 Eδ (r, z) 有以下特点, 有以下特点, 通过模拟计算, a、β>>α ,所以背散射是影响分辨率的主要因素; 、 所以背散射是影响分辨率的主要因素; b、光刻胶较薄时,能量密度的分布范围较小; 、光刻胶较薄时,能量密度的分布范围较小; c、入射电子初始能量 E0 的影响是:对 ff ,E0 越大,则α 、 的影响是: 越大, 越小; 增大时, 先增大 然后减小; 先增大, 越小;对 fb ,当 E0 增大时,β先增大,然后减小; d、低原子序数材料中的散射一般要小一些。 、低原子序数材料中的散射一般要小一些。