ADA4898-1YRDZ中文资料
UL489翻译稿
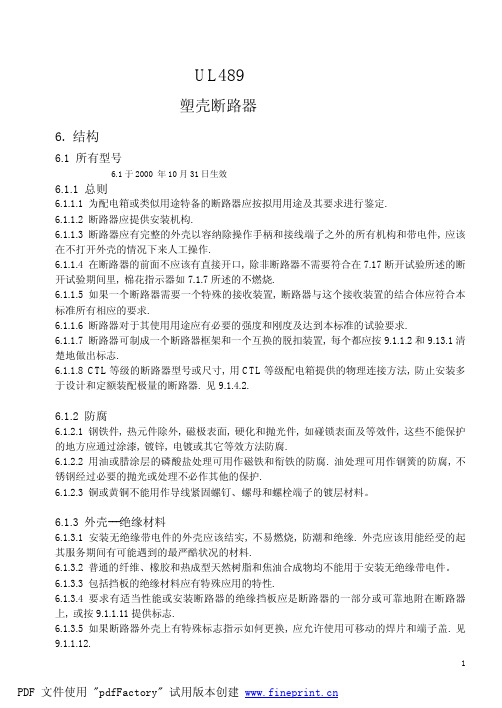
6.1.3.1 安装无绝缘带电件的外壳应该结实, 不易燃烧, 防潮和绝缘. 外壳应该用能经受的起 其服务期间有可能遇到的最严酷状况的材料. 6.1.3.2 普通的纤维、橡胶和热成型天然树脂和焦油合成物均不能用于安装无绝缘带电件。 6.1.3.3 包括挡板的绝缘材料应有特殊应用的特性. 6.1.3.4 要求有适当性能或安装断路器的绝缘挡板应是断路器的一部分或可靠地附在断路器 上, 或按 9.1.1.11 提供标志. 6.1.3.5 如果断路器外壳上有特殊标志指示如何更换, 应允许使用可移动的焊片和端子盖. 见 9.1.1.12.
a) 设备用母线连接; b) 设备用插接件连接; c) 有制造厂商配备的现场安装工具和达到 6.1.4.2.5 的条件; 或 d) 断路器有特殊结构, 如有开关中线极或用于热水器的隔离极及类似的等, 应允许有连
接方法, 考虑到用拟用目的代替压力端子连接器的可接受性.
2
PDF 文件使用 "pdfFactory" 试用版本创建
6.1.4.3 现场接线导线 6.1.4.3.1 参照表 6.1.4.2.1 的尺寸, 导线的差别不能多于两个线号. 导线尺寸不能小于 14 号 AWG(2.1mm2).
5
PDF 文件使用 "pdfFactory" 试用版本创建
6.1.4.3.2 考虑到导线要在温度和电压和其有可能服务的条件, 导线应该由适合于特殊应用的 电线所组成. 6.1.4.3.3 导线的结构应经得起正常的搬运的张力而不使其本身或装置受到损坏. 见 7.1.10.1.2. 6.1.4.3.4 带或不带一条或多条黄条的绿颜色和白色或天然灰色不能用于覆盖导线, 分别用于 接地和接地导线除外. 6.1.4.3.5 导线的自由长度至少应为 152mm(6 英寸).
卡特拉(Caterpillar)产品参数和型号表说明书
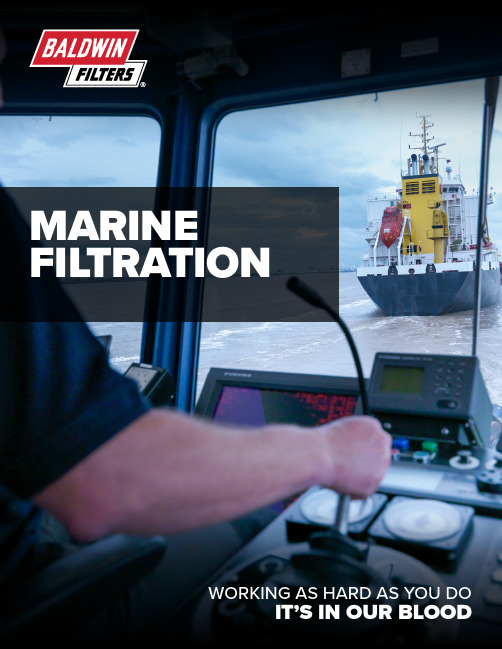
MARINE FILTRATIONWORKING AS HARD AS YOU DOIT’S IN OUR BLOODCATERPILLARBALDWIN OEAIRPA618-S4L9852PA1620-S4L9851PA1629-S4L9853PA1631-S5L1203WPA16496L3313PA17656L4714PA1765 FOAM2N7003PA23847W5313, 8N5313PA25544N0015PA26538N6309PA2653 FOAM8N2555PA28488N2556PA36331059741, 1059742PA39044P0710PA39054P0711PA39321131578PA300692076870FUELBF6141R0712, 4N5823PF823-E5L7564, 6H5932PF9358H4681, 9M2342BF9701P2299, 1R0740, 6L7440 BF75871R0749BF76321R0751, 6I4783BF76331R0750BF76391R0755PF76551R0718, 1R0756, 8N9850 BF7677-D1454501PF77991R0725, 1R0766PF78904P7384CATERPILLAR (CONT’D)BALDWIN OEF/W SEPARATORPF3168N0205BF9126N7617, 8N9803BF12831290373BF1283-SP1290372BF1395-O1335673BF7674-D2053043PF7890-301346307LUBEB751R0714PT88-HD5S0485, 6H9937, 6H9999, 8F1151B991R0716, 2P4005BT2167W2327BT2301R0713BT3649L9200PT670 (Paper)1R0659, 1W7399, 4W4840, 5S0484, 9F6426, 9F6430, 9F6700 B14052201523P70031R0726, 7N7500, 4P2839P70121791502, 1W4136B72991R1808PT7332 (Metal)1R0659, 1W7399, 4W4840, 5S0484, 9F6426, 9F6430, 9F6700 B76001R0739B77001R1807OTHERPT88-HD5S0485PT275-109G6420BW51379N3368BW51381112371BW51399N3367BT8840-MPG 1446691YOU MUSTTHINK RULESARE MADETO BEBROKENIt’s a tough life. It forces you to push your limits.Baldwin pushes limits too. There’s no stopping uswhen it comes to protecting your engine. We have thecoverage, quality, service and availability you need.Baldwin has what it takes to be your one-source filterprovider, keeping your engine running and ensuringyou return home safe.YOUR SINGLE, RELIABLE FILTER PARTNERCUMMINSPA602AF274, 1401089PA1667-FN AF437K, 1401204BF596FF202BF788FF5052BF957-D FF105DBF7879FF5285, 3890017BF46002FF5644, 2881458BF855FF5051, 1491758BF1212FS1212BF1216FS1216BF1226FS1251BF1262FS1013BF1280FS1280BD103LF3000B196LF670B205LF734B281LF3473, 1220550BT339LF3349BT427LF3345C704-L LF500C750-E LF750DB7396LF3325B7577LF777BW5071WF2071BW5073WF2073DETROIT DIESELBF59223518527BF59323518526, 23530640BF78423518528, 23530642BF78523530643PF9025574508BF580023518481, 23530706BF581023530707BF581523518530, 23530645BF7639-D2*******BF769723518529, 23530644BF980020922801PF9924 KIT A0000903451, A0000903551, A0000904251BF581223516189BF581323512317PF768023514049PF774823533816B6-HPG23518668B9523530407B49523530573B703023529744B71355241800310B71805361840001B72295241840301P5092A4722030255DEUTZRS3517P532966RS3717P533781BF5872133943BF587-D1174482PF594W2H4115BF7901174424, WK7123BF900WK94019BF9881160243, 1181917, Q1H4117, WK723 BF1292-O4291642BF7883WK9305BF79151174696BF79971182672P41E1214P52P3H4120B2181174420B2281174416B2361160025, 1174421, A15H4123, W9626 BT2921174418, A1H4123P7145HU9472XP7188HU9453XP7199HU9316XB727612850312JOHN DEERE (6068, 6076, 6081 SERIES)BF959AR86745, RE27091BF7673-D RE50455BF7674-D RE52987BF7677-D RE62420BF7717RE506428BF7853RE522688BF7949-D RE522878BF7949-DM RE521538BF1285-SP RE519608BF1353-SPS RE522372BF1354-SPS RE522687BF7682-D RE508633BF7950-D RE529643BF7971-D RE522966BF9921-O RE503676BT259T19044BT486RE46380, RE57394B7125RE59754P7233RE509672B7322RE504836KOHLERPA602271276PA1712231847PA20674508302, 3508302PA20684708301PA20694708303PA3890253107PA39012408303P40A271271B43-S GM28351BT2235205002B243277233T300-M270197B14101205001B1438GM16703DON’T BE LEFTSTRANDEDThe engine is the heart and soul of your boat and abreakdown is not only costly, it can be dangerous.With Baldwin on board, you can be sure your enginehas protection you can rely on.WORKING AS HARD AS YOU DOIT’S IN OUR BLOODLUGGERBF5962455001BF9542452020BF9592452259BF75462454808BF7673-D2451003, 2451005B22405401B1962404801BT2592400000B71252401002B72232405701BW51392414802, AR87112BW51402415001NORTHERN LIGHTSBF5962455001BF9542452020BF9592452259BF75462454808BF7673-D2451003, 2451005B22405401B372408001B1632403100B1962404801BT2592400000B71252401002BW51392414802BW51402415001PERKINSBF82526560017, 26561117, 2656621, 7111296 BF8847111796BF954130366020BF7674-D2*******BF7681-D2*******PT10832527, 26540132BT2162654403BT2372654407VOLVO-PENTAPA2181876185PA2771823701PA3483842280RS543221377909PA5664858488RS569321196919BF5878385932BF790829913BF825236628, 3581078, 7111296PF950233897BF954861477PF986870065, 876554BF988243004, 3825133, 4669875, 8299132 BF79693852413, 3862228BF4603421879886PF5981147147PF598-10861014BF791855686, 8556862BF1386-O21380475PF7890-103838854BF46101-O3817517VOLVO-PENTA (CONT’D)B2430143B63850559B27835440, 8354409B35-S841750B43-S3827069B75847741B76466634, 4666343, 21707133B76-SS478736B163266286, 418432, 897321, 1266286, 12662862B2363831236BT2516612598B7165834337B740921707132B7685477556WAUKESHAPA1637-FN350123BPA1676-FN208226PA2360-FN207965PA2426-FN208227PA2691169180CPA2693169180GPF116153188PF821-S F1106PLPF902DDED8PF906117900, FBM1124APB, FBM1124APBPF7550F1104B2164830B50176554, 199269B99199395C133-W168660V1656-T167602V1874-T172607AWESTERBEKEBF82514776, 7111296BF88419397B216655B17930220, 36918B20235828YANMARPF71712910055650PF93710450055710BF94012947055701BF753511977355510BF783812957455711PF98612032455760BF753412185755710B161-S11900535100, 12408535111B22711966035150B140011930535151BD702911977090620B748712915035153800.822.5394 | Designed and manufactured in the USA.Form 602 (R 9/21) © 2021 Baldwin Filters, a Parker Hannifin CompanyWARNING: These products can expose you to chemicals, including Diisononyl Phthalate, Carbon black extracts, Nickel, 1,3 Butadiene, Ethylene Oxide, Epichlorohydrin, which are known to the State of California to cause cancer, and Bisphenol-A, Ethylene Glycol, Ethylene Oxide, 1,3 Butadiene, Epichlorohydrin, which are known to the State of California to cause birth defects or other reproductive harm. For more information go to .。
258 Encoders 金属杆壳型绝对类型 EC18A 水抗性强、重力扭矩强 18mm 尺寸 金属

259EncodersMetal ShaftInsulatedShaftThroughShaft TypeRing TypeStandard Codes 1. The ●marks shows the ON position.2. The ●marks : Connections between terminals and the 5 (COM) are ON.Waterproof PropertyImmersion of encoder, not in operation, in water at depth of 1m at normal temperature for 30 minutes.EC18AGAPosition No.123456789101112Rotation angle (° )3060901201501802102402703003301●●●●●●2●●●●3●●●●●●4●●●●5(COM )●●●●●●●●●●●●T E R M I N A L N O .EC18AGB20401Position No.12345678910111213141516Rotation angle (° )22.54567.590112.5135157.5180202.5225247.5270292.5315337.51●●●●●●●●2●●●●●●●●3●●●●●●●●4●●●●●●●●5(COM )●●●●●●●●●●●●●●●●T E R M I N A L N O .EC18AGB20407Position No.123456789101112131415Rotation angle (° )244872961201441681922162402642883123361●●●●●●●●2●●●●●●●●3●●●●●●●●4●●●●●●●●5(COM )●●●●●●●●●●●●●●●T E R M I N A L N O .EC18A /18mm Size Insulated Shaft Type(Two phase A and B )275EncodersMetal ShaftInsulated Shaft Through Shaft TypeRing Type1. When using an infrared reflow oven, solder may sometimes not be applied. Be sure to use a hot air reflow oven or a type that uses infrared rays in combination with hot air.2. The temperatures given above are the maximum temperatures at the terminals of the encoder when employing a hot air reflow method. The temperature of the PC board and the surface temperature of the encoder may vary greatly depending on the PC board material, its size and thickness. Ensure that the surface temperature of the encoder does not rise to 250℃ or greater.3. Conditions vary to some extent depending on the type of reflow bath used. Be sure to give due consideration to this prior to use.NotesEC05E EC21CEC28C, EC35CH250℃ min.230℃ to 245℃260℃230℃ min.220℃ 230℃180℃200℃180℃150℃150℃150℃60s to 120s 60s to 120s 2 min. min.ーー3s30s to 40s 25s to 60s40sー300s max.230s max.2 times max.1 time max.1 time max.Soldering surfacetemperatureSoldering temperatureHeating timeSoldering timeNo. of soldersEC09E, EC111, EC11E, EC11M, EC11N, EC18A,EC21A, EC28A, EC35A, EC35AH, EC50A Series100℃ max.260±5℃2 min. max.5±1s 2 times max.PreheatingDip solderingReference for Dip SolderingExample of Reflow Soldering ConditionReference for Manual SolderingEC10E, EC12D, EC12E EM11BEC40A100℃ max.100℃ max.110℃ max.260±5℃260℃ max.260℃ max.1 min. max.1 min. max.1 min. max.3±1s 3s max.10s max.2 times max.2 times max.1 timeTemperature profile300200100A BC Time (s)G max.F max.H max.E max.RoomtemperatureT e m p e r a t u r e (˚C )Pre-heating DEncoders / Soldering ConditionsEC05E, EC09E, EC10E, EC111, EC11E, EC11M, EC11N, EC12D, EC12E, EC18A, EC21A, EC28A, EC35A, EC35AH, EC40A, EC50A, EM11B, EC21C, EC28C, EC35CHSeries350℃ max.3s max. 1 timeTip temperatureSoldering timeNo. of soldersSeries ABCDEFGHNo. of reflows。
Ultra Flame Propane Canister 8oz 安全数据表说明书

ULTRA COOL PRODUCTS889 BARTON ST. UNIT #1STONEY CREEK, ON L8E 5V1905-643-0060PRODUCT: Ultra Flame Propane Canister 8ozCODE: UF-4949SECTION 01: IDENTIFICATIONProduct Identifier.......................................Ultra Flame Propane Canister 8ozOther means of Identification....................UF-4949Chemical Family........................................Propane.Recommended use and restrictions..........Soldering, braising.Initial Supplier Identifier.............................Ultra Cool Products889 Barton St. Unit #1Stoney Creek, ON L8E 5V1Tel: 905-643-0060Fax: 905-828-8070Email: info@ultracooEmergency telephone number and any ...Ultra Cool Products: 905-643-0060 (9:00 - 5:00; M-F) . In the event of a transportrestrictions on the use of that number emergency contact CANUTEC at (613) 996-6666. .SECTION 02: HAZARD IDENTIFICATIONSignal Word...............................................DANGER.Hazard Classification................................. Flammable Gases — Category 1. Gases Under Pressure — Liquefied Gas. FlammableLiquid - Category 2. Skin Sensitizer — Category 1. Skin Irritation — Category 2.Hazard Statements....................................H220 Extremely flammable gas . H225 Highly flammable liquid and vapour. H280 Containsgas under pressure; may explode if heated . H315 Causes skin irritation. H317 May causean allergic skin reaction. Prevention.................................................P210 Keep away from all sources of heat, sparks, open flames, hot surfaces. No smoking.P233 Keep container tightly closed. P240 Ground and bond container and receivingequipment. P241 Use explosion-proof equipment . P242 Use only non-sparking tools. P243Take precautionary measures against static discharge. P261 Avoid breathing dust, vapor,mist or spray. P264 Wash thoroughly after handling. P272 Contaminated work clothingshould not be allowed out of the workplace. P280 Wear protective gloves/protectiveclothing/eye protection/face protection. Response..................................................P377 Leaking gas fire: Do not extinguish, unless leak can be stopped safely . P381 In caseof leakage, eliminate all ignition sources . P303+P361+P353 IF ON SKIN (or hair)immediately take off all contaminated clothing, rinse skin with water or use emergencyshower. P370+P378 In case of fire - use dry chemical powder, CO2 or foam to extinguish.P302+P352 IF ON SKIN: Wash with plenty of water. P333+P313 If skin irritation or rashoccurs: Get medical attention. P362+P364 Take off contaminated clothing and wash beforereuse. Storage......................................................P403+P235 Store in well ventilated place. Keep cool. P410 + P403 Protect from sunlight.Store in a well-ventilated place . Disposal.....................................................P501 Dispose of contents and empty containers in accordance with local regulations.Other hazards............................................H400 Very toxic to aquatic life . H410 Very toxic to aquatic life with long lasting effects.Avoid release to the environment. Collect spillage.Mixture Statement.....................................This product has been classified based upon the information provided by the supplier.SECTION 03: COMPOSITION / INFORMATION ON INGREDIENTSCHEMICAL NAME AND SYNONYMS CAS #WT. %Petroleum gases, liquefied 68476-85-799.7Ethyl Mercaptin75-08-10.28Cyclohexene, 1-methyl-4-(1-methylethenyl)- 138-86-30.02SECTION 04: FIRST-AID MEASURESFIRST AID MEASURES:Skin Contact.............................................Flush contaminated skin with plenty of water. Remove contaminated clothing and shoes.To avoid the risk of static discharges and gas ignition, soak contaminated clothingthoroughly with water before removing it. Get medical attention if symptoms occur. In caseof contact with liquid, warm frozen tissues slowly with lukewarm water and get medicalattention. Do not rub affected area. Wash clothing before reuse. Clean shoes thoroughlybefore reuse.Eye Contact..............................................Check for an remove any contact lenses. Immediately flush eyes with plenty of water for atleast 15 minutes, occasionally lifting the upper and lower eyelids. . Get medical attentionimmediately.Ingestion...................................................Remove victim to fresh air and keep at rest in a position comfortable for breathing. Getmedical attention if adverse health effects persist or are severe. Ingestion of liquid cancause burns similar to frostbite. If frostbite occurs, get medical attention. Never giveanything by mouth to an unconscious person. . If unconscious, place in recovery positionand get medical attention immediately. Maintain an open airway. Loosen tight clothing suchas a collar, tie, belt or waistband. As this product rapidly becomes a gas when released,refer to the inhalation section.Inhalation..................................................If inhaled, remove to fresh air. If not breathing, give artificial respiration. If breathing isdifficult, give oxygen. Get medical attention. It may be dangerous to the person providingair to give mouth-to-mouth resuscitation. If unconscious, place in recovery position and getmedical attention immediately. Maintain an open airway. Loosen tight clothing such as acollar, tie, belt or waistband.Symptoms and effects...............................May cause an allergic skin reaction. Liquid can cause burns similar to frostbite. Dermalcontact with rapidly evaporating liquid could result in freezing of the tissues or frostbite.Harmful if inhaled. Asphyxiant gas.Medical attention and special treatment....Adverse symptoms may include frostbite. Treat symptomatically. In the event of an incidentinvolving this product ensure that medical authorities are provided a copy of this safetydata sheet.SECTION 05: FIRE-FIGHTING MEASURESSuitable and unsuitable extinguishing e an extinguishing agent suitable for the surrounding fire.mediaSpecific hazards arising from the .............Contains gas under pressure. Extremely flammable gas. In a fire or if heated, a pressure hazardous product, such as the nature of increase will occur and the container may burst, with the risk of a subsequent explosion. any hazardous combustion products The vapor/gas is heavier than air and will spread along the ground. Gas may accumulate inlow or confined areas or travel a considerable distance to a source of ignition and flashback, causing fire or explosion. By fire: Protect against potentially toxic and irritating fumes. Special protective equipment and ............Promptly isolate the scene by removing all persons from the vicinity of the incident if there precautions for fire-fighters is a fire. No action shall be taken involving any personal risk or without suitable training.Move containers from fire area if this can be done without risk. Use water spray to keepfire-exposed containers cool. Cool fire-exposed containers with cold water spray. Heat willcause pressure build up and may cause explosive rupture . Eliminate all ignition sources ifsafe to do so. Use self-contained breathing apparatus and full firefighting gear.Decomposition and combustion products may be toxic. Fire-fighters should wearappropriate protective equipment and self-contained breathing apparatus (SCBA) with a fullface-piece operated in positive pressure mode. Contact supplier immediately for specialistadvice.SECTION 06: ACCIDENTAL RELEASE MEASURESPersonal precautions, protective .............No action shall be taken involving any personal risk or without suitable training. Evacuate equipment and emergency procedures surrounding areas. Keep unnecessary and unprotected personnel from entering. Do nottouch or walk through spilled material. Avoid breathing vapor or mist. Provide adequateventilation. Wear appropriate respirator when ventilation is inadequate. Put on appropriatepersonal protective equipment (see section 8). No flares, smoking or flames in hazardarea. Avoid dispersal of spilled material and runoff the contact with soil, waterways, drainsand sewers. Ensure emergency procedures to deal with accidental gas releases are inplace to avoid contamination of the environment.Methods and materials for containment ..Immediately contact emergency personnel. Stop leak if without risk. Use spark-proof tools and cleaning up and explosion-proof equipment. Ventilate area. Prevent product from entering sewers orwaterways.SECTION 07: HANDLING AND STORAGEPrecautions for safe handling....................Exposure to this product requires prior training and information. Read the information onthe label and the safety data sheet before handling this product. Contains gas underpressure. Put on appropriate personal protective equipment. Wear appropriate respiratorSECTION 07: HANDLING AND STORAGEPrecautions for safe handling....................when ventilation is inadequate. Avoid contact with skin and eyes. Do not swallow. Do notbreathe gas/fumes/vapor/spray. Use only in well-ventilated areas. Handle and opencontainer with care. Launder contaminated clothing before reuse. When using, do not eator drink. Wash hands before eating, drinking, or smoking. Do not enter storage areas andconfined spaces unless adequately ventilated. Store and use away from heat, sparks, openflame or any other ignition source. Use explosion-proof electrical (ventilating, lighting andmaterial handling) equipment. Use only non-sparking tools. Take precautionary measuresagainst electrostatic discharges. Empty containers retain product residue and can behazardous. Do not reuse container. Close valve after each use and when empty. Protectcylinders from physical damage; do not drag, roll, slide or drop.Conditions for safe storage, including any Store in accordance with local regulations. Store in a segregated and approved area. Store incompatibilities away from all sources of heat and ignition. Store away from direct sunlight. Store awayfrom incompatible materials . Keep container tightly closed in a well ventilated area.SECTION 08: EXPOSURE CONTROLS / PERSONAL PROTECTIONACGIH TLV OSHA PEL NIOSH INGREDIENTS TWA STEL PEL STEL RELPetroleum gases, 1000 ppm Not established1800 mg/m³ (1000 Not established1800 mg/m³ (1000 liquefied ppm)ppm)Ethyl Mercaptin0.5 ppm0.5 ppm10 ppm (25 mg/m3) 0.5 ppm (1.3ceiling mg/m3L) ceiling Cyclohexene, 30 ppm (WEEL)Not established Not established Not established Not established1-methyl-4-(1-methylethenyl)-Appropriate engineering e local exhaust ventilation to maintain airborne concentrations below the TLV. Suitablerespiratory equipment should be used in cases of insufficient ventilation or whereoperational procedures demand it. For guidance on engineering control measures refer topublications such as the ACGIH current edition of 'Industrial Ventilation, a manual ofRecommended Practice. The engineering controls also need to keep gas, vapor or dustconcentrations below any lower explosive limits. Use explosion -proof ventilationequipment.Individual protection measures, such aspersonal protective equipmentEye/Type..................................................Face shield and safety glasses Use equipment for eye protection tested and approvedunder appropriate government standards such as NIOSH (US) or EN 166(EU).Gloves/Type.............................................Wear skin protection equipment. The selection of skin protection equipment depends onthe nature of the work to be performed. Wear chemical resistant gloves to prevent skincontact. Contact glove supplier for additional information.Footwear/Type.........................................Wear safety boots per local regulations.Clothing/Type ..........................................Wear adequate protective clothing to prevent skin contact.Respiratory/Type......................................Where risk assessment shows air-purifying respirators are appropriate use a full-facerespirator with multi- purpose combination (US) or type ABEK (EN 14387) respiratorcartridges as a backup to engineering controls.Other/Type...............................................Handle in accordance with good industrial hygiene and safety practice. Take offimmediately all contaminated clothing. Wash contaminated clothing before reuse.Emergency eye wash station and shower should be available. Anyone handling thisproduct should wash their hands and face before eating, drinking or using tobaccoproducts.SECTION 09: PHYSICAL AND CHEMICAL PROPERTIESAppearance / physical state .....................Gas, compressed. Colour........................................................Colorless. Odour........................................................Odour added. Sulphur like.Odour Threshold (ppm).............................Not available. pH..............................................................Not applicable.Melting/Freezing Point...............................-166.11°C (-267°F) .Initial Boiling Point/Boiling Range..............-34.66°C (-30.4°F) .Flash Point (deg C), Method.....................-60°C (-76°F).Evaporation Rate.......................................Rapid.Flammability (solid/gas).............................Extremely flammable gas.Upper Flammable Limit (% Vol)................8.5.Lower Flammable Limit (% Vol)................ 1.9.Vapour Pressure (mm Hg)........................70 @ 70°F.Vapour Density (Air=1).............................. 1.76.Relative Density/Specific Gravity..............0.54. Solubility....................................................Not available.SECTION 09: PHYSICAL AND CHEMICAL PROPERTIESCoefficient of Water/Oil Distribution..........Not available.Auto Ignition Temperature (deg C)............862.77°C (1585°F).Decomposition temperature......................Not available. Viscosity....................................................Not applicable.SECTION 10: STABILITY AND REACTIVITYReactivity...................................................Contains gas under pressure; may explode if heated. Reacts with oxidants causing fire andexplosion hazard.Chemical stability......................................Stable at normal temperatures and pressures.Possibility of hazardous reactions.............Will not polymerize.Conditions to avoid, including static .........Avoid all sources of ignition: heat, sparks, open flame. Avoid sunlight. Avoid extreme discharge, shock or vibration temperatures.Incompatible materials..............................Strong oxidizing agents.Hazardous decomposition products..........No hazardous decomposition products if stored and handled as prescribed/indicated.SECTION 11: TOXICOLOGICAL INFORMATIONINGREDIENTS LC50LD50Petroleum gases, liquefied 658 mg/L (4 hr.)Not determinedEthyl Mercaptin4420 ppm (4 hr.)682 mg/kg (oral, rat) Cyclohexene, 1-methyl-4-(1-methylethenyl)- Not determined5300 mg/kg (oral, rat)Route of Exposure.....................................Skin contact, eye contact, inhalation. ATEs..........................................................Not determined.Symptoms related to the physical,chemical and toxicological characteristicsEffects of Acute Exposure.........................Harmful if inhaled. Causes skin, eye and respiratory irritation . Exposure may causerespiratory and / or skin sensitization. Skin contact may cause severe irritation. Liquid cancause burns similar to frostbite. Harmful if absorbed through the skin .Effects of Chronic Exposure......................Intentional misuse by deliberately concentrating and inhaling this product may be harmfulor fatal. Sensitization..............................................May cause an allergic skin reaction. May cause allergy or asthma symptoms or breathingdifficulties if inhaled. Mutagenicity..............................................No known mutagenicity effects.Reproductive Effects.................................No known reproductive effects. .Carcinogenicity of Material........................None of the components present in this material at concentrations equal to or greater than0.1% are listed by IARC, NTP, OSHA OR ACGIH as a carcinogen.Specific Target Organ Toxicity - single .....This information, if applicable, can be found in Section 2.exposureSpecific Target Organ Toxicity - repeated This information, if applicable, can be found in Section 2.exposureSECTION 12: ECOLOGICAL INFORMATIONEcotoxicity.................................................H400: Very toxic to aquatic life. H410 Very toxic to aquatic life with long lasting effects .Discharge into the environment must be avoided.Persistence and degradability...................Product data not available.Bioaccumulation Potential.........................Product data not available.Mobility in soil............................................Product data not available.Other adverse effects................................Product data not available.SECTION 13: DISPOSAL CONSIDERATIONSInformation on safe handling for disposal .Dispose of waste in accordance with all applicable Federal, Provincial/State and localand methods of disposal, including any regulations.contaminated packagingSECTION 14: TRANSPORT INFORMATIONTDG Classification.....................................UN1075 - PETROLEUM GASES, LIQUEFIED, 2.1. Limited Quantity: 0.125 L .Refer to Part 1 of Transportation of Dangerous Goods Regulations for additionalinformation.Transport in bulk / IBC Code.....................No data available.SECTION 15: REGULATORY INFORMATIONCEPA Status.............................................Not reviewed.TSCA Inventory Status..............................All components are listed on TSCA .SECTION 16: OTHER INFORMATIONPrepared by ..............................................Trivalent Data Systems Ltd. . Information based on suppliersSDS. rmation for this material safety data sheet was obtained from sources consideredtechnically accurate and reliable. While every effort has been made to ensure fulldisclosure of product hazards, in some cases data is not available and is so stated. Nowarranty, expressed or implied, is made and supplier will not be liable for any losses,injuries for consequential damages, which may result from the use or reliance on anyinformation contained in this form. .Date of the latest revision of the safety ...2019-09-23data sheet。
ADA4898-1YRDZ中文资料

High Voltage, Low Noise, Low Distortion,Unity Gain Stable, High Speed Op AmpADA4898-1 Rev. 0Information furnished by Analog Devices is believed to be accurate and reliable. However, noresponsibility is assumed by Analog Devices for its use, nor for any infringements of patents or other rights of third parties that may result from its use. Specifications subject to change without notice. No license is granted by implication or otherwise under any patent or patent rights of Analog Devices. T rademarks and registered trademarks are the property of their respective owners. One Technology Way, P.O. Box 9106, Norwood, MA 02062-9106, U.S.A. Tel: 781.329.4700 Fax: 781.461.3113 ©2008 Analog Devices, Inc. All rights reserved.FEATURESUltralow noise0.9 nV/√Hz2.4 pA/√Hz1.2 nV/√Hz @10 HzUltralow distortion: −93 dBc at 500 kHz Wide supply voltage range: ±5 V to ±16 V High speed−3 dB bandwidth: 65 MHz (G = +1)Slew rate: 55 V/μsUnity gain stableLow input offset voltage: 150 μV maximum Low input offset voltage drift: 1 μV/°CLow input bias current: −0.1 μALow input bias current drift: 2 nA/°C Supply current: 8 mAPower-down featureAPPLICATIONSInstrumentationActive filtersDAC buffersSAR ADC driversOptoelectronics CONNECTION DIAGRAM NC–IN+IN–V SNC = NO CONNECT07037-1 Figure 1. 8-Lead SOIC_N_EP (RD-8)GENERAL DESCRIPTIONThe ADA4898-1 is an ultralow noise and distortion, unity gain stable, voltage feedback op amp that is ideal for use in 16-bit and 18-bit systems with power supplies from ±5 V to ±16 V. The ADA4898-1 features a linear, low noise input stage and internal compensation that achieves high slew rates and low noise.With the wide supply voltage range, low offset voltage, and wide bandwidth, the ADA4898-1 is designed to work in the most demanding applications. The ADA4898-1 also features an input bias current cancellation mode that reduces input bias current by a factor of 60.The ADA4898-1 is available in an 8-lead SOIC package that features an exposed metal paddle on its underside that improvesheat transfer to the ground plane. This is a significant improvement over traditional plastic packages. The ADA4898-1 is rated to work over the extended automotive temperature range of−40°C to +105°C.737-2FREQUENCY (Hz)VOLTAGENOISE(nV/√Hz)CURRENTNOISE(pA/√Hz)0.1110Figure 2. Input Voltage Noise and Current Noise vs. FrequencyADA4898-1Rev. 0 | Page 2 of 16TABLE OF CONTENTSFeatures..............................................................................................1 Applications.......................................................................................1 Connection Diagram.......................................................................1 General Description.........................................................................1 Revision History...............................................................................2 Specifications with ±15 V Supply...................................................3 Specifications with ±5 V Supply.....................................................4 Absolute Maximum Ratings............................................................5 Thermal Resistance......................................................................5 Maximum Power Dissipation.....................................................5 ESD Caution..................................................................................5 Pin Configuration and Function Descriptions.............................6 Typical Performance Characteristics.............................................7 Test Circuits.....................................................................................12 Theory of Operation......................................................................13 PD (Power Down) Pin...............................................................13 Current Noise Measurement....................................................13 Applications Information..............................................................14 Higher Feedback Gain Operation............................................14 Recommended Values for Various Gains................................14 Noise............................................................................................15 Circuit Considerations..............................................................15 PCB Layout.................................................................................15 Power Supply Bypassing............................................................15 Grounding...................................................................................15 Outline Dimensions.......................................................................16 Ordering Guide.. (16)REVISION HISTORY5/08—Revision 0: Initial ReleaseADA4898-1SPECIFICATIONS WITH ±15 V SUPPLYT A = 25°C, G = +1, R F = 0 Ω, R G open, R L = 1 kΩ to GND (for G > 1, R F = 100 Ω), unless otherwise noted.Rev. 0 | Page 3 of 16ADA4898-1SPECIFICATIONS WITH ±5 V SUPPLYT A = 25°C, G = +1, R F = 0 Ω, R G open, R L = 1 kΩ to GND (for G > 1, R F = 100 Ω), unless otherwise noted.Rev. 0 | Page 4 of 16ADA4898-1Rev. 0 | Page 5 of 16ABSOLUTE MAXIMUM RATINGSTable 3.Parameter Rating Supply Voltage 36 V Power Dissipation See Figure 3Differential Mode Input Voltage ±1.5 V Common-Mode Input Voltage ±11.4 V Storage Temperature Range −65°C to +150°C Operating Temperature Range −40°C to +105°C Lead Temperature (Soldering, 10 sec) 300°C Junction Temperature 150°CStresses above those listed under Absolute Maximum Ratings may cause permanent damage to the device. This is a stress rating only; functional operation of the device at these or any other conditions above those indicated in the operationalsection of this specification is not implied. Exposure to absolute maximum rating conditions for extended periods may affect device reliability.THERMAL RESISTANCEθJA is specified for the worst-case conditions, that is, θJA is specified for a device soldered in the circuit board with its exposed paddle soldered to a pad on the PCB surface that is thermally connected to a copper plane, with zero airflow. Table 4.Package TypeθJA θJC Unit 8-Lead SOIC with EP on Four-Layer Board47 29°C/WMAXIMUM POWER DISSIPATIONThe maximum safe power dissipation in the ADA4898-1package is limited by the associated rise in junction temperature (T J ) on the die. At approximately 150°C, which is the glass transition temperature, the plastic changes its properties. Even temporarily exceeding this temperature limit can change the stresses that the package exerts on the die, permanently shifting the parametric performance of the ADA4898-1. Exceeding a junction temperature of 150°C for an extended period can result in changes in the silicon devices, potentially causing failure.The power dissipated in the package (P D ) is the sum of thequiescent power dissipation and the power dissipated in the package due to the output load drive. The quiescent power is the voltage between the supply pins (V S ) times the quiescent current (I S ). The power dissipated due to the load drive depends upon the particular application. For each output, the power due to load drive is calculated by multiplying the load current by the associated voltage drop across the device. RMS voltages and currents must be used in these calculations. Airflow increases heat dissipation, effectively reducing θJA . In addition, more metal directly in contact with the package leads from metal traces, through holes, ground, and power planes reduces the θJA . The exposed paddle on the underside of the package must be soldered to a pad on the PCB surface that is thermally connected to a copper plane to achieve the specified θJA .Figure 3 shows the maximum safe power dissipation in the package vs. the ambient temperature for the 8-lead SOIC_EP (47°C/W) on a JEDEC standard four-layer board, with itsunderside paddle soldered to a pad that is thermally connected to a PCB plane. θJA values are approximations.0.51.01.52.02.53.03.54.04.507037-003AMBIENT TEMPERATURE (°C)M A X I M U M P O W E R D I S S I P A T I O N (W )204060801001030507090–40–20–30–10Figure 3. Maximum Power Dissipation vs. Ambient TemperatureESD CAUTIONADA4898-1Rev. 0 | Page 6 of 16PIN CONFIGURATION AND FUNCTION DESCRIPTIONSNC 1–IN 2+IN 3–V S 4PD8+V S7OUT6NC5NC = NO CONNECTADA4898-1TOP VIEW(Not to Scale)07037-046Figure 4. Pin ConfigurationADA4898-1Rev. 0 | Page 7 of 16TYPICAL PERFORMANCE CHARACTERISTICS–12–11–10–9–8–7–6–5–4–3–2–1012311010007037-004FREQUENCY (MHz)N O R M A L I Z E D C L O S E D -L O O P G A I N (d B )Figure 5. Small Signal Frequency Response for Various Gains–12–11–10–9–8–7–6–5–4–3–2–1012311010007037-005FREQUENCY (MHz)C L O S ED -L O O PG A I N (d B )Figure 6. Small Signal Frequency Response for Various Loads–12–11–10–9–8–7–6–5–4–3–2–101211010007037-006FREQUENCY (MHz)C L O S ED -L O O P G A I N(d B )Figure 7. Small Signal Frequency Response for Various Temperatures–12–11–10–9–8–7–6–5–4–3–2–1012311010007037-007FREQUENCY (MHz)N O R M A L I Z E D C L O S E D -L O O P G A I N (d B )Figure 8. Large Signal Frequency Response for Various Gains–12–11–10–9–8–7–6–5–4–3–2–10107037-008FREQUENCY (MHz)C L O S ED -L O O P G A I N (d B )Figure 9. Large Signal Frequency Response for Various Loads–12–11–10–9–8–7–6–5–4–3–2–10121101007037-009FREQUENCY (MHz)C L O S ED -L O O P G A I N (d B )Figure 10. Large Signal Frequency Response for Various TemperaturesADA4898-1Rev. 0 | Page 8 of 16–12–11–10–9–8–7–6–5–4–3–2–101211007037-010FREQUENCY (MHz)C L O S ED -L O O P G A I N (d B )100Figure 11. Small Signal Frequency Response for Various Supply Voltages–12–11–10–9–8–7–6–5–4–3–2–112307037-011FREQUENCY (MHz)C L O S ED -L O O P G A I N (d B )Figure 12. Small Signal Frequency Response for Various Capacitive Loads0.11101101001k10k100k07037-012FREQUENCY (Hz)V O L T A G E N O I S E (n V /√H z )Figure 13. Voltage Noise vs. Frequency–12–11–10–9–8–7–6–5–4–3–2–101211007037-013FREQUENCY (MHz)C L O S ED -L O O P G A I N (d B )100Figure 14. Large Signal Frequency Response for Various Supply Voltages–0.5–0.4–0.3–0.2–0.100.10.20.30.40.50.60.70.80.91.007037-014FREQUENCY (Hz)N O R M A L I Z E D G A I N (d B )Figure 15. 0.1 dB Flatness for Various Output Voltages07037-035FREQUENCY (Hz)C U R R E N T N O I S E (p A /√H z )1110100101001k 10k 100kFigure 16. Input Current Noise vs. FrequencyADA4898-1Rev. 0 | Page 9 of 1607037-016FREQUENCY (Hz)O P E N -L O O P G A I N (d B )100k1M1G10M100M–70–80–90–100–110–120–130–140–150–160–170–180–190–200O P E N -L O O PP H A S E (D e g r e e s )Figure 17. Open-Loop Gain and Phase vs. Frequency07037-017FREQUENCY (Hz)D I S T O R T I O N (d B c )–140–120–100–80–60–40–200Figure 18. Harmonic Distortion vs. Frequency and Gain07037-018FREQUENCY (Hz)D I S T O R T I O N (d B c )–140–120–100–80–60–40–200100k1M10MFigure 19. Harmonic Distortion vs. Frequency and Loads107073-019OUTPUT VOLTAGE (V p-p)D I S T O R T I O N (d B c )–135–125–120–130–115–110–105–100–9523456Figure 20. Harmonic Distortion vs. Output Amplitude07037-020FREQUENCY (Hz)D I S T O R T I O N (d B c )–140–120–100–80–60–40–200100k1M10MFigure 21. Harmonic Distortion vs. Frequency and Loads–0.04–0.0200.020.040.060.080.100.120.1407037-021TIME (20ns/DIV)O U T P U T V O L T A G E (V )Figure 22. Small Signal Transient Response for Various Capacitive LoadsADA4898-1Rev. 0 | Page 10 of 16–0.04–0.020.020.040.060.080.100.120.1407037-022TIME (20ns/DIV)O U T P U T V O L T A G E (V )Figure 23. Small Signal Transient Response for Various Gains–0.50.51.01.52.02.507037-023TIME (100ns/DIV)O U T P U T V O L T A G E (V )Figure 24. Large Signal Transient Response forVarious Supply Voltages, R L = 100 Ω0.50.40.30.20.100.10.20.30.40.507037-026TIMES (10ns/DIV)S E T T L I N G T I M E (%)Figure 25. Settling Time–0.50.51.01.52.02.507037-025TIME (100ns/DIV)O U T P U T V O L T A G E (V )Figure 26. Large Signal Transient Response forVarious Supply Voltages, R L = 1 kΩ–0.50.51.01.52.02.507037-024TIME (100ns/DIV)O U T P U T V O L T A G E (V )Figure 27. Large Signal Transient Response for Various Gains–20–10010203040506070809007037-028FREQUENCY (Hz)O U T P U T I M P E D A N C E (d B )Figure 28. Output Impedance vs. Frequency–140–120–100–80–60–40–20007037-029FREQUENCY (Hz)C M R R (d B )–120–100–80–60–40–2007037-030FREQUENCY (Hz)P S R R (d B )10k100k1M10MFigure 29. Common-Mode Rejection Ratio (CMRR) vs. FrequencyFigure 32. Power Supply Rejection Ratio (PSRR) vs. Frequency–75–65–55–45100k1M10M100M07037-031FREQUENCY (Hz)P D I S O L A T I O N (d B )1000800600400200007037-032INPUT BIAS CURRENT (µA)C O U N TFigure 33. PD Isolation vs. FrequencyFigure 30. Input Bias Current Distribution1000800600400200007037-033OFFSET VOLTAGE (µV)C OU N T–30–603012090601000800600400200OFFSET VOLTAGE (µV)C O U N T07037-034Figure 31. Input Offset Voltage Distribution, V S = ±15 VFigure 34. Input Offset Voltage Distribution, V S = ±5 VTEST CIRCUITSV INOUT07037-036Figure 35. Typical Noninverting Load ConfigurationOUT +V 07037-037Figure 36. Positive Power Supply RejectionV INV OUT07037-038Figure 37. Common-Mode RejectionVOUT07037-039Figure 38. Typical Capacitive Load ConfigurationV OUT S07037-040Figure 39. Negative Power Supply RejectionTHEORY OF OPERATIONThe ADA4898-1 is a voltage feedback op amp that combines unity-gain stability with 0.9 nV/√Hz input noise. It employs a highly linear input stage that can maintain greater than −90 dBc (@ 2 V p-p) distortion out to 500 kHz while in a unity-gain configuration. This rare combination of low gain stability, low input referred noise, and extremely low distortion is the result of Analog Devices, Inc., proprietary op amp architecture and high speed complementary bipolar processing technology. The simplified ADA4898-1 topology, shown in Figure 40, is a single gain stage with a unity-gain output buffer. It has over 100 dB of open-loop gain and maintains precision specifications such as CMRR, PSRR and offset to levels that are normally associated with topologies having two or more gain stages.OUT07037-041Figure 40. TopologyPD (POWER DOWN) PINThe PD pin saves power by decreasing the quiescent power dissipated in the device. It is very useful when power is an issue and the device does not need to be turned on at all times. The response of the device is rapid when going from a power down mode to full power operation mode. Note thatPD does not put the output in a high-Z state, which means that the ADA4898-1 is not recommended for use as a multiplexer.CURRENT NOISE MEASUREMENTTo measure the very low (2.4 pA/√Hz) input current noise of the ADA4898-1, 10 kΩ resistors were used on both inputs of the amplifier. Figure 41 shows the noise measurement circuit used. The 10 kΩ resistors are used on both inputs to balance the input impedance and cancel the common-mode noise. In addition, a high gain configuration is used to increase the total output noise and bring it above the noise floor of the instrument.07037-042OUTFigure 41. Current Noise Measurement CircuitThe current noise density (I n ) is calculated using the following formula:[]11kΩ202)Hz nV/18.4(112/122×××−=none IAPPLICATIONS INFORMATIONHIGHER FEEDBACK GAIN OPERATIONThe ADA4898-1 schematic for the noninverting gainconfiguration is nearly a textbook example (see Figure 42). The only exception is the feedback capacitor in parallel with the feedback resistor, R F , but this capacitor is recommended only when using a large R F value (>300 Ω). Figure 43 shows the difference between using a 100 Ω resistor and a 1 kΩ resistor. Due to the high input capacitance in the ADA4898-1 when using a higher feedback resistor, more peaking appears in the closed-loop gain. Using the lower feedback resistor resolves this issue; however, when running at higher supplies (±15 V) with 100 Ω R F , the system draws a lot of extra current into the feedback network. To avoid this problem, a higher feedback resistor can be used with a feedback capacitor in parallel. Figure 43 shows the effect of placing a feedback capacitor in parallel with a larger R F . In this gain of 2 configuration, R F = R G = 1 kΩ and C F = 2.7 pF. When using C F , the peaking drops from 6 dB to less then 2 dB.07037-043VOUTFigure 42. Noninverting Gain Schematic–15–12–9–6–303691207037-044FREQUENCY (Hz)C L O S ED -L O O P G A I N (d B )100k10M1M 100MFigure 43. Small Signal Frequency Response forVarious Feedback ImpedancesRECOMMENDED VALUES FOR VARIOUS GAINSTable 6 provides a useful reference for determining various gains and associated performance. Resistor R F is set to 100 Ω for gains greater than 1. A low feedback R F resistor value reduces peaking and minimizes the contribution to the overall noise performance of the amplifier.Table 6. Various Gains and Recommended Resistor Values Associated (Conditions: V S = ±5 V, T A = 25°C, R L = 1 kΩ, R T = 49.9 Ω)Gain R F (Ω) R G (Ω) −3 dB SS BW (MHz),V OUT = 100 mV p-p Slew Rate (V/μs), V OUT = 2 V Step ADA4898-1 Voltage Noise (nV/√Hz), RTO Total System Noise (nV/√Hz), RTO +1 0 NA 65 55 0.9 1.29 +2 100 100 30 50 1.8 3.16 +5 100 24.9 9454.57.07NOISETo analyze the noise performance of an amplifier circuit, identify the noise sources, and then determine if each source has a significant contribution to the overall noise performance of the amplifier. To simplify the noise calculations, noise spectral densities were used rather than actual voltages to leave bandwidth out of the expressions (noise spectral density, which is generally expressed in nV/√Hz, is equivalent to the noise in a 1 Hz bandwidth).The noise model shown in Figure 44 has six individual noise sources: the Johnson noise of the three resistors, the op amp voltage noise, and the current noise in each input of the amplifier. Each noise source has its own contribution to the noise at the output. Noise is generally specified referred to input (RTI), but it is often simpler to calculate the noise referred to the output (RTO) and then divide by the noise gain to obtain the RTI noise.= –R2R1=NG = 1 +R2R1V OUT07037-045Figure 44. Op Amp Noise Analysis ModelAll resistors have a Johnson noise that is calculated by )(4kBTR .where:k is Boltzmann’s Constant (1.38 × 10−23 J/K). B is the bandwidth in Hertz.T is the absolute temperature in Kelvin. R is the resistance in ohms.A simple relationship that is easy to remember is that a 50 Ω resistor generates a Johnson noise of 1 nV/√Hz at 25°C. In applications where noise sensitivity is critical, care must be taken not to introduce other significant noise sources to the amplifier. Each resistor is a noise source. Attention to the following areas is critical to maintain low noise performance: design, layout, and component selection. A summary of noise performance for the amplifier and associated resistors can be seen in Table 6.CIRCUIT CONSIDERATIONSCareful and deliberate attention to detail when laying out the ADA4898-1 board yields optimal performance. Power supply bypassing, parasitic capacitance, and component selection all contribute to the overall performance of the amplifier.PCB LAYOUTBecause the ADA4898-1 can operate up to 65 MHz, it is essential that RF board layout techniques be employed. All ground and power planes under the pins of the ADA4898-1 should be cleared of copper to prevent the formation of parasitic capacitance between the input pins to ground and the output pins to ground. A single mounting pad on a SOIC footprint can add as much as 0.2 pF of capacitance to ground if the ground plane is not cleared from under the mounting pads.POWER SUPPLY BYPASSINGPower supply bypassing for the ADA4898-1 has been optimized for frequency response and distortion performance. Figure 42 shows the recommended values and location of the bypass capacitors. Power supply bypassing is critical for stability, frequency response, distortion, and PSR performance. The 0.1 μF capacitors shown in Figure 42 should be as close to the supply pins of the ADA4898-1 as possible. The 10 μF electrolytic capacitors should be adjacent to but not necessary close to the 0.1 μF capacitors. The capacitor between the two supplies helps improve PSR and distortion performance. In some cases, additional paralleled capacitors can help improve frequency and transient response.GROUNDINGGround and power planes should be used where possible. Ground and power planes reduce the resistance and inductance of the power planes and ground returns. The returns for the input and output terminations, bypass capacitors, and R G should all be kept as close to the ADA4898-1 as possible. The output load ground and the bypass capacitor grounds should be returned to the same point on the ground plane to minimize parasitic trace inductance, ringing, and overshoot and to improve distortion performance.The ADA4898-1 package features an exposed paddle. Foroptimum electrical and thermal performance, solder this paddle to ground. For more information on high speed circuit design, see A Practical Guide to High-Speed Printed-Circuit-Board Layout at .OUTLINE DIMENSIONSCOMPLIANT TO JEDEC STANDARDS MS-012-AACONTROLLING DIMENSIONS ARE IN MILLIMETER; INCH DIMENSIONS(IN PARENTHESES)ARE ROUNDED-OFF MILLIMETER EQUIVALENTS FOR REFERENCE ONLY AND ARE NOT APPROPRIATE FOR USE IN DESIGN.060506-A1.75 (0.069)1.35 (0.053)BSC0.10(PINS UP)Figure 45. 8-Lead Standard Small Outline Package with Exposed Pad [SOIC_N_EP](RD-8-1)Dimensions shown in millimeters and (inches)ORDERING GUIDEModelTemperature Range Package Description Package Option Ordering Quantity ADA4898-1YRDZ 1−40°C to +105°C 8-Lead SOIC_N_EP RD-8-1 1 ADA4898-1YRDZ-R71−40°C to +105°C 8-Lead SOIC_N_EP RD-8-1 1,000 ADA4898-1YRDZ-RL 1−40°C to +105°C 8-Lead SOIC_N_EP RD-8-1 2,5001Z = RoHS Compliant Part.©2008 Analog Devices, Inc. All rights reserved. Trademarks and registered trademarks are the property of their respective owners. D07037-0-5/08(0)。
rt8901参数
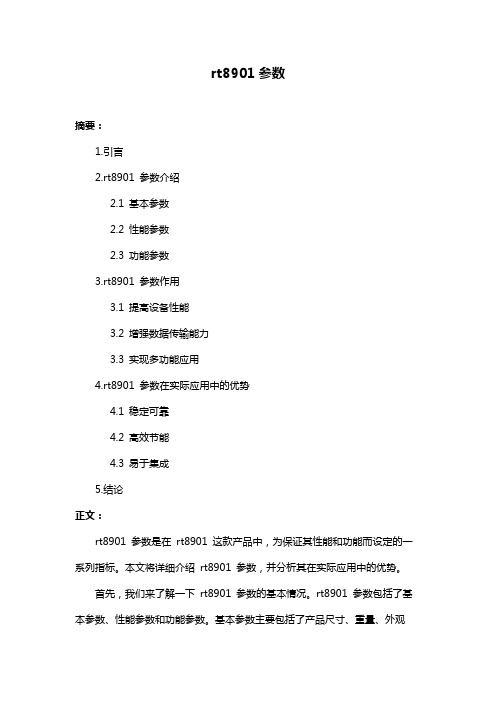
rt8901参数摘要:1.引言2.rt8901 参数介绍2.1 基本参数2.2 性能参数2.3 功能参数3.rt8901 参数作用3.1 提高设备性能3.2 增强数据传输能力3.3 实现多功能应用4.rt8901 参数在实际应用中的优势4.1 稳定可靠4.2 高效节能4.3 易于集成5.结论正文:rt8901 参数是在rt8901 这款产品中,为保证其性能和功能而设定的一系列指标。
本文将详细介绍rt8901 参数,并分析其在实际应用中的优势。
首先,我们来了解一下rt8901 参数的基本情况。
rt8901 参数包括了基本参数、性能参数和功能参数。
基本参数主要包括了产品尺寸、重量、外观等;性能参数主要包括了传输速率、工作电压、功耗等;功能参数主要包括了数据处理能力、通信接口种类等。
rt8901 参数在提高设备性能、增强数据传输能力和实现多功能应用方面起到了关键作用。
例如,通过调整rt8901 参数,可以优化其数据处理能力,使得设备在处理大量数据时更加稳定和高效。
同时,通过调整rt8901 参数,还可以增强其通信接口的种类和数量,从而实现设备的多功能应用。
在实际应用中,rt8901 参数的优势得到了充分体现。
首先,由于rt8901 参数的调整,使得设备在运行过程中更加稳定可靠,大大降低了设备故障的风险。
其次,rt8901 参数的调整也有助于提高设备的节能效果,从而降低了设备的运行成本。
最后,rt8901 参数的调整使得设备更加易于集成到各种应用场景中,提高了设备的灵活性和适应性。
综上所述,rt8901 参数在提高设备性能、增强数据传输能力和实现多功能应用方面起到了关键作用,同时在实际应用中也展现出了其稳定可靠、高效节能和易于集成等优势。
PC400-8, PC400LC-8, PC450-8, PC450LC-8 Shop 说明书

SEN02223-15-8-8-8-870001700017000170001e p c a t al o g s .c ome p c a t a l o g s .c o mPC400, 450-81SEN02225-15HYDRAULIC EXCAVATORPC400-8PC400LC-8PC450-8PC450LC-8Machine model Serial numberPC400-870001 and up PC400LC-870001 and up PC450-870001 and up PC450LC-870001 and up00 Index and forewordIndexComposition of shop manual ..........................................................................................................................2Table of contents (4)e pc at al o g s .c omSEN02225-1500 Index and foreword2PC400, 450-8Composition of shop manualThe contents of this shop manual are shown together with Form No. in a list.Note 1:Always keep the latest version of this manual in accordance with this list and utilize accordingly.The marks shown to the right of Form No. denote the following:Q : New issue (to be filed additionally)q : Revision (to be replaced for each Form No.)Note 2:This shop manual can be supplied for each Form No.Note 3:To file this shop manual in the special binder for management, handle it as follows:•Place a divider on the top of each section in the file after matching the Tub No. with No. indicated next to each Section Name shown in the table below:•File overview and other materials in sections in the order shown below and utilize them accord-ingly.Section TitleForm NumberShop Manual, contents binder, binder label and tabs SEN02223-1500 Index and foreword SEN02224-15IndexSEN02225-15q Foreword and general information SEN02226-0201 SpecificationSEN02227-02Specification and technical dataSEN02228-0210 Structure, function and maintenance standard SEN02229-08Engine and cooling system SEN02230-00Power trainSEN02231-00Undercarriage and frame SEN02232-00Hydraulic system, Part 1SEN02233-00Hydraulic system, Part 2SEN02234-04 Hydraulic system, Part 3SEN02235-02q Work equipmentSEN02236-00Cab and its attachments SEN02237-00Electrical system SEN02238-0320 Standard value tableSEN02239-03Standard service value table SEN02643-0330 Testing and adjustingSEN02240-07Testing and adjusting, Part 1SEN02644-04Testing and adjusting, Part 2SEN02645-06Testing and adjusting, Part 3SEN02662-0240 TroubleshootingSEN02241-04Failure code table and fuse locations SEN02646-03General information on troubleshootingSEN02647-03Troubleshooting by failure code (Display of code), Part 1SEN02648-04Troubleshooting by failure code (Display of code), Part 2SEN02649-03Troubleshooting by failure code (Display of code), Part 3SEN02650-04Troubleshooting of electrical system (E-mode)SEN02651-03Troubleshooting of hydraulic and mechanical system (H-mode)SEN02652-03e pc at al o g s .c om00 Index and foreword SEN02225-15PC400, 450-83Troubleshooting of engine (S-mode)SEN02653-0250 Disassembly and assemblySEN02242-07General information on disassembly and assembly SEN02654-03Engine and cooling system SEN02655-01Power trainSEN02656-02Undercarriage and frame SEN02657-04Hydraulic system SEN02658-01Work equipmentSEN02659-01q Cab and its attachments SEN02660-01Electrical system SEN02661-0290 Diagrams and drawingsSEN02243-04Hydraulic diagrams and drawings SEN02244-01q Electrical diagrams and drawingsSEN02245-03e pc at al o g s .c omBuy nowKomatsu Hydraulic Excavator PC400 -8, PC400LC-8, PC450 -8, PC450LC-8 Shop Manual PDFWith Instant Download。
FortiGate-80D 产品说明书

Multi-threat protection from a single device increases security and lowers costs Unlimited user licensing and comprehensive features Allows implementation of WAN optimization and web cache, as well as extensive internal logging and reporting.
FortiCare
Worldwide 24x7 Support
FortiGuard
Threat Research & Response
HaБайду номын сангаасdware
5
5
5
1
2
3
1 Console Port
Advanced Features
The FortiGate-80D offers beyond the industry’s best firewall with the latest in Advanced Threat Protection including Sandboxing and anti-bot protection, Feature Select Options for simplifying configurations and deployments, and Contextual Visibility for enhanced reporting and management.
2
Highlights
FortiOS — The World’s Most Advanced Security Operating System
- 1、下载文档前请自行甄别文档内容的完整性,平台不提供额外的编辑、内容补充、找答案等附加服务。
- 2、"仅部分预览"的文档,不可在线预览部分如存在完整性等问题,可反馈申请退款(可完整预览的文档不适用该条件!)。
- 3、如文档侵犯您的权益,请联系客服反馈,我们会尽快为您处理(人工客服工作时间:9:00-18:30)。
High Voltage, Low Noise, Low Distortion, Unity-Gain Stable, High Speed Op AmpADA4898-1Rev. AInformation furnished by Analog Devices is believed to be accurate and reliable. However , no responsibility is assumed by Analog Devices for its use, nor for any infringements of patents or other rights of third parties that may result from its use. Specifications subject to change without notice. No license is granted by implication or otherwise under any patent or patent rights of Analog Devices. T rademarks and registered trademarks are the property of their respective owners.One Technology Way, P.O. Box 9106, Norwood, MA 02062-9106, U.S.A.Tel: 781.329.4700 Fax: 781.461.3113 ©2008 Analog Devices, Inc. All rights reserved.FEATURESUltralow noise 0.9 nV/√Hz 2.4 pA/√Hz1.2 nV/√Hz @10 HzUltralow distortion: −93 dBc at 500 kHz Wide supply voltage range: ±5 V to ±16 V High speed−3 dB bandwidth: 65 MHz (G = +1) Slew rate: 55 V/μs Unity gain stableLow input offset voltage: 150 μV maximum Low input offset voltage drift: 1 μV/°C Low input bias current: −0.1 μALow input bias current drift: 2 nA/°C Supply current: 8 mA Power-down featureAPPLICATIONSInstrumentation Active filters DAC buffers SAR ADC drivers OptoelectronicsCONNECTION DIAGRAMNC–IN +IN –V S NC = NO CONNECT07037-001Figure 1. 8-Lead SOIC_N_EP (RD-8-1)GENERAL DESCRIPTIONThe ADA4898-1 is an ultralow noise and distortion, unity gain stable, voltage feedback op amp that is ideal for use in 16-bit and 18-bit systems with power supplies from ±5 V to ±16 V . The ADA4898-1 features a linear, low noise input stage and internal compensation that achieves high slew rates and low noise. With the wide supply voltage range, low offset voltage, and wide bandwidth, the ADA4898-1 is extremely versatile, and it features a cancellation circuit that reduces input bias current.The ADA4898-1 is available in an 8-lead, 150 mil SOIC package that features an exposed metal paddle to improve power dissipation and heat transfer to the negative supply plane. This EPAD offers a significant thermal relief over the traditional plastic packages. The ADA4898-1 is rated to work over the automotive temperature range of −40°C to +105°C. 07037-002FREQUENCY (Hz)V O L T A G E N O I S E (n V /√H z )C U R R E N T N O I S E (p A /√H z )0.1110Figure 2. Input Voltage Noise and Current Noise vs. FrequencyADA4898-1Rev. A | Page 2 of 20TABLE OF CONTENTSFeatures .............................................................................................. 1 Applications ....................................................................................... 1 Connection Diagram ....................................................................... 1 General Description ......................................................................... 1 Revision History ............................................................................... 2 Specifications ..................................................................................... 3 ±15 V Supply ................................................................................. 3 ±5 V Supply ................................................................................... 4 Absolute Maximum Ratings ............................................................ 5 Thermal Resistance ...................................................................... 5 Maximum Power Dissipation ..................................................... 5 ESD Caution .................................................................................. 5 Pin Configuration and Function Descriptions ............................. 6 Typical Performance Characteristics ............................................. 7 Test Circuits ..................................................................................... 12 Theory of Operation ...................................................................... 13 PD (Power Down) Pin ............................................................... 13 Current Noise Measurement .................................................... 13 0.1 Hz to 10 Hz Noise ................................................................ 14 Applications Information .............................................................. 15 Higher Feedback Gain Operation ............................................ 15 Recommended Values for Various Gains ................................ 15 Noise ............................................................................................ 16 Circuit Considerations .............................................................. 16 PCB Layout ................................................................................. 16 Power Supply Bypassing ............................................................ 16 Grounding ................................................................................... 16 Outline Dimensions ....................................................................... 17 Ordering Guide .. (17)REVISION HISTORY8/08—Rev. 0 to Rev. AChanges to General Description Section ...................................... 1 Changes to Table 5 ............................................................................ 6 Changes to Figure 17 ........................................................................ 9 Changes to Figure 28 ...................................................................... 10 Changes to Figure 29 and Figure 32 ............................................. 11 Added 0.1 Hz to 10 Hz Noise Section .......................................... 14 Added Figure 42 and Figure 43; Renumbered Sequentially ..... 14 Changes to Grounding Section ..................................................... 16 Updated Outline Dimensions . (17)5/08—Revision 0: Initial ReleaseADA4898-1SPECIFICATIONS±15 V SUPPLYT A = 25°C, G = +1, R F = 0 Ω, R G open, R L = 1 kΩ to GND (for G > 1, R F = 100 Ω), unless otherwise noted.Rev. A | Page 3 of 20ADA4898-1±5 V SUPPLYT A = 25°C, G = +1, R F = 0 Ω, R G open, R L = 1 kΩ to GND (for G > 1, R F = 100 Ω), unless otherwise noted.Rev. A | Page 4 of 20ADA4898-1Rev. A | Page 5 of 20ABSOLUTE MAXIMUM RATINGSTable 3.Parameter RatingSupply Voltage 36 VPower Dissipation See Figure 3The power dissipated in the package (P D ) is the sum of the quiescent power dissipation and the power dissipated in thepackage due to the output load drive. The quiescent power isthe voltage between the supply pins (V S ) times the quiescentcurrent (I S ). The power dissipated due to the load drive dependsupon the particular application. For each output, the power dueto load drive is calculated by multiplying the load current by theassociated voltage drop across the device. RMS voltages andcurrents must be used in these calculations. Differential Mode Input Voltage ±1.5 VCommon-Mode Input Voltage ±11.4 VStorage Temperature Range −65°C to +150°COperating Temperature Range −40°C to +105°CLead Temperature (Soldering, 10 sec) 300°C Junction Temperature 150°CAirflow increases heat dissipation, effectively reducing θJA . In addition, more metal directly in contact with the package leads from metal traces, through holes, ground, and power planes reduces the θJA . The exposed paddle on the underside of the package must be soldered to a pad on the PCB surface that is thermally connected to a copper plane to achieve the specified θJA . Stresses above those listed under Absolute Maximum Ratings may cause permanent damage to the device. This is a stress rating only; functional operation of the device at these or any other conditions above those indicated in the operationalsection of this specification is not implied. Exposure to absolute maximum rating conditions for extended periods may affect device reliability.Figure 3 shows the maximum power dissipation in the package vs. the ambient temperature for the 8-lead SOIC_N_EP (47°C/W) on a JEDEC standard 4-layer board, with its underside paddle soldered to a pad that is thermally connected to a PCB plane. θJA values are approximations.THERMAL RESISTANCEθJA is specified for the worst-case conditions, that is, θJA is specified for a device soldered in the circuit board with its exposed paddle soldered to a pad on the PCB surface that isthermally connected to a copper plane, with zero airflow. 00.51.01.52.02.53.03.54.04.507037-003AMBIENT TEMPERATURE (°C)M A X I M U M P O W E R D I S S I P A T I O N (W )204060801001030507090–40–20–30–10Table 4.Package TypeθJA θJC Unit 8-Lead SOIC with EP on 4-Layer Board4729 °C/WMAXIMUM POWER DISSIPATIONThe maximum safe power dissipation in the ADA4898-1 package is limited by the associated rise in junction temperature (T J ) on the die. At approximately 150°C, which is the glass transition temperature, the plastic changes its properties. Even temporarily exceeding this temperature limit can change the stresses that the package exerts on the die, permanently shifting the parametric performance of the ADA4898-1. Exceeding a junction temperature of 150°C for an extended period can result in changes in the silicon devices, potentially causing failure.Figure 3. Maximum Power Dissipation vs. Ambient TemperatureESD CAUTIONADA4898-1Rev. A | Page 6 of 20PIN CONFIGURATION AND FUNCTION DESCRIPTIONSNC 1–IN 2+IN 3–V S 4PD8+V S7OUT6NC5NC = NO CONNECTADA4898-1TOP VIEW(Not to Scale)07037-046Figure 4. Pin ConfigurationADA4898-1Rev. A | Page 7 of 20TYPICAL PERFORMANCE CHARACTERISTICS–12–11–10–9–8–7–6–5–4–3–2–1012311010007037-007FREQUENCY (MHz)N O R M A L I Z E D C L O S E D -L O O P G A I N (d B )–12–11–10–9–8–7–6–5–4–3–2–1012311010007037-004FREQUENCY (MHz)N O R M A L I Z E D C L O S E D -L O O P G A I N (d B)Figure 5. Small Signal Frequency Response for Various GainsFigure 8. Large Signal Frequency Response for Various Gains–12–11–10–9–8–7–6–5–4–3–2–1012311010007037-005FREQUENCY (MHz)C L O S ED -L O O PG A I N (d B )–12–11–10–9–8–7–6–5–4–3–2–10107037-008FREQUENCY (MHz)C L O S ED -L O O P G A I N (d B )Figure 6. Small Signal Frequency Response for Various LoadsFigure 9. Large Signal Frequency Response for Various Loads–12–11–10–9–8–7–6–5–4–3–2–101211010007037-009FREQUENCY (MHz)C L O S ED -L O O P G A I N (d B )–12–11–10–9–8–7–6–5–4–3–2–101207037-006FREQUENCY (MHz)C L O S ED -L O O P G A I N (d B )Figure 10. Large Signal Frequency Response for Various TemperaturesFigure 7. Small Signal Frequency Response for Various TemperaturesADA4898-1Rev. A | Page 8 of 20–12–11–10–9–8–7–6–5–4–3–2–101211010007037-010FREQUENCY (MHz)C L O S ED -L O O P G A I N (d B )Figure 11. Small Signal Frequency Response for Various Supply Voltages–12–11–10–9–8–7–6–5–4–3–2–1012307037-011FREQUENCY (MHz)C L O S ED -L O O P G A I N (d B )Figure 12. Small Signal Frequency Response for Various Capacitive Loads0.11101101001k 10k 100k 07037-012FREQUENCY (Hz)V O L T A G E N O I S E (n V /√H z )Figure 13. Voltage Noise vs. Frequency–12–11–10–9–8–7–6–5–4–3–2–101211010007037-013FREQUENCY (MHz)C L O S ED -L O O P G A I N (d B )Figure 14. Large Signal Frequency Response for Various Supply Voltages–0.5–0.4–0.3–0.2–0.100.10.20.30.40.50.60.70.80.91.007037-014FREQUENCY (Hz)N O R M A L I Z E D G A I N (d B )Figure 15. 0.1 dB Flatness for Various Output Voltages07037-035FREQUENCY (Hz)I N P U T C U R R E N T N O I S E (p H z )1110100101001k 10k 100kFigure 16. Input Current Noise vs. FrequencyADA4898-1Rev. A | Page 9 of 2007037-016FREQUENCY (Hz)O P E N -L O O P G A I N (d B )100k1M1G10M100M–70–80–90–100–110–120–130–140–150–160–170–180–190–200O P E N -L O O P P H A S E (D e g r e e s )Figure 17. Open-Loop Gain and Phase vs. Frequency07037-017FREQUENCY (Hz)D I S T O R T I O N (d B c )–140–120–100–80–60–40–200100k1M10M Figure 18. Harmonic Distortion vs. Frequency and Gain07037-018FREQUENCY (Hz)D I S T O R T I O N (d B c)–140–120–100–80–60–40–200Figure 19. Harmonic Distortion vs. Frequency and Loads107073-019OUTPUT VOLTAGE (V p-p)D I S T O R T I O N (d B c)–135–125–120–130–115–110–105–100–9523456Figure 20. Harmonic Distortion vs. Output Amplitude07037-020FREQUENCY (Hz)D I S T O R T I O N (d B c )–140–120–100–80–60–40–200100k1M10MFigure 21. Harmonic Distortion vs. Frequency and Loads–0.04–0.0200.020.040.060.080.100.120.1407037-021TIME (20ns/DIV)O U T P U T V O L T A G E (V )Figure 22. Small Signal Transient Response for Various Capacitive LoadsADA4898-1Rev. A | Page 10 of 20–0.04–0.020.020.040.060.080.100.120.1407037-022TIME (20ns/DIV)O U T P U T V O L T A G E (V )Figure 23. Small Signal Transient Response for Various Gains–0.50.51.01.52.02.507037-023TIME (100ns/DIV)O U T P U T V O L T A G E (V )Figure 24. Large Signal Transient Response forVarious Supply Voltages, R L = 100 Ω0.50.40.30.20.10–0.1–0.2–0.3–0.4–0.507037-026TIMES (10ns/DIV)S E T T L I N G T I M E (%)Figure 25. Settling Time–0.50.51.01.52.02.507037-025TIME (100ns/DIV)O U T P U T V O L T A G E (V )Figure 26. Large Signal Transient Response forVarious Supply Voltages, R L = 1 kΩ–0.50.51.01.52.02.507037-024TIME (100ns/DIV)O U T P U T V O L T A G E (V )Figure 27. Large Signal Transient Response for Various Gains–20–10010203040506070809007037-028FREQUENCY (Hz)O U T P U T I M P E D A N C E (d B )Figure 28. Output Impedance vs. Frequency–140–120–100–80–60–40–20007037-029FREQUENCY (Hz)C M R R (d B )–120–100–80–60–40–2007037-030FREQUENCY (Hz)P S R R (d B )10k100k1M10MFigure 29. Common-Mode Rejection Ratio (CMRR) vs. FrequencyFigure 32. Power Supply Rejection Ratio (PSRR) vs. Frequency–75–65–55–45100k1M10M100M07037-031FREQUENCY (Hz)P D I S O L A T I O N (d B )1000800600400200007037-032INPUT BIAS CURRENT (µA)C O U N TFigure 33. PD Isolation vs. FrequencyFigure 30. Input Bias Current Distribution1000800600400200007037-033INPUT OFFSET VOLTAGE (µV)C OU N T–30–603012090601000800600400200INPUT OFFSET VOLTAGE (µV)C O U N T07037-034Figure 31. Input Offset Voltage Distribution, V S = ±15 VFigure 34. Input Offset Voltage Distribution, V S = ±5 VTEST CIRCUITSV INV OUT07037-036Figure 35. Typical Noninverting Load ConfigurationOUT +V 07037-037Figure 36. Positive Power Supply RejectionV INV OUT07037-038Figure 37. Common-Mode RejectionVOUT07037-039Figure 38. Typical Capacitive Load ConfigurationOUT +V S07037-040Figure 39. Negative Power Supply RejectionTHEORY OF OPERATIONThe ADA4898-1 is a voltage feedback op amp that combines unity gain stability with 0.9 nV/√Hz input noise. It employs a highly linear input stage that can maintain greater than −90 dBc (at 2 V p-p) distortion out to 500 kHz while in a unity-gain configuration. This rare combination of low gain stability, low input-referred noise, and extremely low distortion is the result of Analog Devices, Inc., proprietary op amp architecture and high voltage bipolar processing technology.The simplified ADA4898-1 topology, shown in Figure 40, is a single gain stage with a unity gain output buffer. It has over 100 dB of open-loop gain and maintains precision specifications, such as CMRR, PSRR, and offset, to levels that are normally associated with topologies having two or more gain stages.OUT07037-041Figure 40. TopologyPD (POWER DOWN) PINThe PD pin saves power by decreasing the quiescent power dissipated in the device. It is very useful when power is an issue and the device does not need to be turned on at all times. The response of the device is rapid when going from power-down mode to full power operation mode. Note thatPD does not put the output in a high-Z state, which means that the ADA4898-1 is not recommended for use as a multiplexer.CURRENT NOISE MEASUREMENTTo measure the very low (2.4 pA/√Hz) input current noise of the ADA4898-1, 10 kΩ resistors were used on both inputs of the amplifier. Figure 41 shows the noise measurement circuit used. The 10 kΩ resistors are used on both inputs to balance the input impedance and cancel the common-mode noise. In addition, a high gain configuration is used to increase the total output noise and bring it above the noise floor of the instrument.07037-042OUTFigure 41. Current Noise Measurement CircuitThe current noise density (I n ) is calculated by[]11kΩ202Hz nV/18.4(112/122×××−=none I0.1 Hz TO 10 Hz NOISEFigure 42 shows the 0.1 Hz to 10 Hz voltage and current noise of the ADA4898-1. The peak-to-peak noise voltage is below 0.5 μV . Figure 43 shows the circuit used to measure the low frequency noise. It uses a band-pass filter of approximately 0.1 Hz and 10 Hz and a high gain stage feeding into an instrumentation amplifier.0.50.40.30.20.10–0.1–0.2–0.3–0.4–0.52468101214161820TIME (s)O U T P U T V O L T A G E (µV )07037-047Figure 42. 0.1 Hz to 10 Hz Noise07037-048Figure 43. Low Frequency Noise CircuitAPPLICATIONS INFORMATIONHIGHER FEEDBACK GAIN OPERATIONThe ADA4898-1 schematic for the noninverting gainconfiguration is nearly a textbook example (see Figure 44). The only exception is the feedback capacitor in parallel with the feedback resistor, R F , but this capacitor is recommended only when using a large R F value (>300 Ω). Figure 45 shows the difference between using a 100 Ω resistor and a 1 kΩ resistor. Due to the high input capacitance in the ADA4898-1 when using a higher feedback resistor, more peaking appears in the closed-loop gain. Using the lower feedback resistor resolves this issue; however, when running at higher supplies (±15 V) with an R F of 100 Ω, the system draws a lot of extra current into the feedback network. To avoid this problem, a higher feedback resistor can be used with a feedback capacitor in parallel. Figure 45 shows the effect of placing a feedback capacitor in parallel with a larger R F . In this gain-of-2 configuration, R F = R G = 1 kΩ and C F = 2.7 pF. When using C F , the peaking drops from 6 dB to less than 2 dB.07037-043VOUTFigure 44. Noninverting Gain Schematic–15–12–9–6–303691207037-044FREQUENCY (Hz)C L O S ED -L O O P G A I N (d B )100k10M1M 100MFigure 45. Small Signal Frequency Response forVarious Feedback ImpedancesRECOMMENDED VALUES FOR VARIOUS GAINSTable 6 provides a useful reference for determining various gains and associated performance. R F is set to 100 Ω for gains greater than 1. A low feedback R F resistor value reduces peaking and minimizes the contribution to the overall noise performance of the amplifier.Table 6. Various Gains and Recommended Resistor Values Associated With It (Conditions: V S = ±5 V, T A = 25°C, R L = 1 kΩ, R T = 49.9 Ω)Gain R F (Ω) R G (Ω) −3 dB SS BW (MHz),V OUT = 100 mV p-p Slew Rate (V/μs), V OUT = 2 V Step ADA4898-1 Voltage Noise (nV/√Hz), RTO Total System Noise (nV/√Hz), RTO +1 0 NA 65 55 0.9 1.29 +2 100 100 30 50 1.8 3.16 +5 100 24.9 9454.57.07NOISET o analyze the noise performance of an amplifier circuit, identify the noise sources, and then determine if each source has a significant contribution to the overall noise performance of the amplifier. T o simplify the noise calculations, noise spectral densities were used rather than actual voltages to leave bandwidth out of the expressions (noise spectral density, which is generally expressed in nV/√Hz, is equivalent to the noise in a 1 Hz bandwidth). The noise model shown in Figure 46 has six individual noise sources: the Johnson noise of the three resistors, the op amp voltage noise, and the current noise in each input of the amplifier. Each noise source has its own contribution to the noise at the output. Noise is generally specified referred to input (RTI), but it is often simpler to calculate the noise referred to the output (RTO) and then divide by the noise gain to obtain the RTI noise.= –R2R1=NG = 1 +R2 R1OUT07037-045Figure 46. Op Amp Noise Analysis ModelAll resistors have a Johnson noise that is calculated by)(4kBTRwhere:k is Boltzmann’s Constant (1.38 × 10−23 J/K). B is the bandwidth in Hertz.T is the absolute temperature in Kelvin. R is the resistance in ohms.A simple relationship that is easy to remember is that a 50 Ω resistor generates a Johnson noise of 1 nV/√Hz at 25°C. In applications where noise sensitivity is critical, care must be taken not to introduce other significant noise sources to the amplifier. Each resistor is a noise source. Attention to the following areas is critical to maintain low noise performance: design, layout, and component selection. A summary of noise performance for the amplifier and associated resistors is shown in Table 6.CIRCUIT CONSIDERATIONSCareful and deliberate attention to detail when laying out the ADA4898-1 board yields optimal performance. Power supply bypassing, parasitic capacitance, and component selection all contribute to the overall performance of the amplifier.PCB LAYOUTBecause the ADA4898-1 can operate up to 65 MHz, it is essential that RF board layout techniques be employed. All ground and power planes under the pins of the ADA4898-1 should be cleared of copper to prevent the formation of parasitic capacitance between the input pins to ground and the output pins to ground. A single mounting pad on a SOIC footprint can add as much as 0.2 pF of capacitance to ground if the ground plane is not cleared from under the mounting pads.POWER SUPPLY BYPASSINGPower supply bypassing for the ADA4898-1 has been optimized for frequency response and distortion performance. Figure 44 shows the recommended values and location of the bypass capacitors. Power supply bypassing is critical for stability, frequency response, distortion, and PSR performance. The 0.1 μF capacitors shown in Figure 44 should be as close to the supply pins of the ADA4898-1 as possible. The 10 μF electrolytic capacitors should be adjacent to but not necessarily close to the 0.1 μF capacitors. The capacitor between the two supplies helps improve PSR and distortion performance. In some cases, additional paralleled capacitors can help improve frequency and transient response.GROUNDINGGround and power planes should be used where possible. Ground and power planes reduce the resistance and inductance of the power planes and ground returns. The returns for the input and output terminations, bypass capacitors, and R G should all be kept as close to the ADA4898-1 as possible. The output load ground and the bypass capacitor grounds should be returned to the same point on the ground plane to minimize parasitic trace inductance, ringing, and overshoot and to improve distortion performance.The ADA4898-1 package features an exposed paddle. For optimum electrical and thermal performance, solder this paddle to negative supply plane. For more information on high speed circuit design, see A Practical Guide to High-Speed Printed-Circuit-Board Layout , Analog Dialogue: PCB Layout at .OUTLINE DIMENSIONSCOMPLIANT TO JEDEC STANDARDS MS-012-AACONTROLLING DIMENSIONS ARE IN MILLIMETER; INCH DIMENSIONS(IN PARENTHESES)ARE ROUNDED-OFF MILLIMETER EQUIVALENTS FOR REFERENCE ONLY AND ARE NOT APPROPRIATE FOR USE IN DESIGN.072808-A0.17 (0.0067)4.00 (0.157)3.90 (0.154)3.80 (0.150)BSC0.31 (0.012)COPLANARITY0.10(PINS UP)FOR PROPER CONNECTION OF THE EXPOSED PAD, REFER TOFigure 47. 8-Lead Standard Small Outline Package with Exposed Pad [SOIC_N_EP](RD-8-1)Dimensions shown in millimeters and (inches)ORDERING GUIDEModelTemperature Range Package Description Package Option Ordering Quantity ADA4898-1YRDZ 1−40°C to +105°C 8-Lead SOIC_N_EP RD-8-1 1 ADA4898-1YRDZ-R71−40°C to +105°C 8-Lead SOIC_N_EP RD-8-1 1,000 ADA4898-1YRDZ-RL 1−40°C to +105°C 8-Lead SOIC_N_EP RD-8-1 2,5001Z = RoHS Compliant Part.NOTESNOTESNOTES©2008 Analog Devices, Inc. All rights reserved. Trademarks andregistered trademarks are the property of their respective owners.D07037-0-8/08(A)。