CLC inte process control
ACI Controls 自动化过程控制解决方案说明书

PROCESS CONTROLSOLUTIONSPerformance that sets the standardWHO IS ACI CONTROLS?Industry Leading Products & SolutionsMANUFACTURING & ASSEMBL YDesign, build and program automation control panels for anyASSEMBLIES & CONVERSIONSOur production staff can integrate (and calibrate) componentsfrom manifolds and transmitters to fittings, hoses and filters.We offer turnkey solutions including drawings, componentselection, sourcing, assembly, inspection and quality control.We offer the complete package (control valve, actuatorand instrumentation) that is assembled, tested and readyStandard and custom valve configurationsComplete documentation including engineering drawingsTROUBLE SHOOTING & FIELD SERVICEPROVIDING REMOTE, ON-SITE, COMMISSIONING & CALIBRATION SERVICESOur experienced field service technicians have worked in a wide variety of industries to improve customer efficiency, safety, productivity and profitability. ACI Service Solutions helps businesses scale-up and down, allowing for a controlled cost structure and minimal overhead. Each service technician is factory trained and fully prepared to troubleshoot, diagnose and repair equipment while in the field; they also provide the documentation and data customers require to maintain their certifications.ACI Controls is accredited by A2LA to ISO/IEC 17025:2017. This ISO standard, used by testing and calibration laboratories, validates ACI’s ability to consistently produce accurate results. Our test and calibration results have been through rigorous management and technical requirements so you can always be confident working with ACI Controls.PROJECT MANAGEMENTOur team overseas component selection, drawing creation,procurement, production and logistics to ensure your projectis completed on time and under budget.REMOTE SUPPORTWeb-enabled monitoring and automated paging capabilitiesprovide remote access and alarm notification.INSTALLATIONOn-site set-up of designated control systems.REPAIR/REPLACEMENTOf existing process equipment with a unique understandingof its characteristics or replacement of unrepairable units.CALIBRATIONVerification, calibration, and documentation of all processcontrol equipment to manufacturer specifications.WIRELESS SURVEYSBy offering preinstallation testing and surveys, we reducerisk by utilizing the most powerful wireless instrumentation,networking and SCADA to optimize your wireless dataacquisition system.For more information, contact our technical service representatives at 1-800-333-7519 or online at .3MECHANICAL DIVISIONPARKER HANNIFINHydraulic, pneumatic hose and tubingFittings: SAE, JIC, 37/45 degree flareDigital and analog mass flow controllersFor more information, contact our technical service representatives at 1-800-333-7519 or online at .PARKER PROCESSFILTRATION (PECO)Parker Hyperchill (plus) water chillersHigh-efficiency, wound and pleated cartridgesPARKER AIRTEKDesiccant air dryersInline high-temp filtersWater separatorsPARKER DOMNICK HUNTERCompressed air filters/dryersIndustrial gas generatorsOil/Water separatorsFor more information, contact our technical service representatives at 1-800-333-7519 or online at .Flow computers, data loggers and piping systemsFor more information, contact our technical service representatives at 1-800-333-7519 or online at .PARKER DRIVESAND AUTOMATIONDC and AC variable speed drivesStand alone and systems drivesMicro drivesV/Hz, open loop and closed loop vector drives WEG MOTORSIEC, NEMA and general purpose AC motors DC motorsGearboxes, Gearmotors and Softstarters RITTALIndustrial enclosuresIndustrial climate controlFor more information, contact our technical service representatives at 1-800-333-7519 or online at .Performance that sets the standard。
全流程质控 英语

全流程质控英语Quality Control in the Full Process。
Quality control is an essential part of any production process, and it is particularly crucial in the field of document creation. In this article, we will discuss the importance of quality control in the full process of document creation, and explore some best practices for ensuring the highest quality in our work.The first step in the document creation process is planning. This involves defining the purpose and audience of the document, as well as outlining the main points and structure. During this stage, it is important to ensure that the objectives of the document are clear and achievable, and that the content is relevant and accurate.Once the planning stage is complete, the next step is research and gathering of information. This may involve conducting interviews, collecting data, or reviewing existing documents. It is important to verify the accuracy and reliability of the information gathered, and to ensure that it is relevant to the document's objectives.After the information has been gathered, the next step is to organize and structure the content. This involves creating an outline, determining the order of the information, and ensuring that the content flows logically and coherently. It is important to pay attention to the overall structure of the document, as well as to the consistency and coherence of the individual sections.With the content organized and structured, the next step is to write the first draft of the document. During this stage, it is important to focus on clarity, conciseness, and accuracy. It is also important to ensure that the tone and style of the document are appropriate for the intended audience, and that the content is engaging and persuasive.Once the first draft is complete, the next step is to review and revise the document. This involves checking for errors in grammar, punctuation, and spelling, as well as for inconsistencies in content and style. It is also important to ensure that the documentmeets the objectives defined in the planning stage, and that it is clear, coherent, and well-organized.After the document has been revised, the next step is to seek feedback from others. This may involve sharing the document with colleagues, supervisors, or other stakeholders, and soliciting their input and suggestions for improvement. It is important to be open to constructive criticism and to consider all feedback carefully.Once feedback has been received and incorporated, the final step is to proofread and format the document. This involves checking for any remaining errors or inconsistencies, and ensuring that the document is visually appealing and professional in appearance. It is important to pay attention to details such as font, spacing, and layout, as well as to ensure that any graphics or images are clear and relevant.In conclusion, quality control is essential in the full process of document creation. By following best practices and paying careful attention to each stage of the process, we can ensure that our documents are of the highest quality and effectively communicate our intended message to our audience.。
8259选择题

1、8086/8088CPU的可屏蔽中断请求信号INTR为(A)有效A、高电平B、低电平C、上升沿D、下降沿2、8086/8088CPU的非屏蔽中断请求信号NMI为(C)有效A、高电平B、低电平C、上升沿D、下降沿3、8086/8088CPU响应可屏蔽中断的条件是(D)A、IF=0 TF=0B、IF=1 TF=1C、IF=0 TF无关D、IF=1 TF无关4、响应INTR请求不是必要条件的为(B)A、IF=1B、IF=0C、无DMA请求D、无NMI请求5、IBM PC/XT机开机后,中断向量表存放在(D)A、ROM地址高端B、ROM地址低端C、RAM地址高端D、RAM地址低端6、8086/8088的中断向量表(B)A、用于存放中断类型码B、用于存放中断服务程序入口地址C、是中断服务程序的入口D、是断点7、可屏蔽中断类型号为32H,则它的中断向量应存放在以(C)开始的4字节单元中A、00032HB、00128HC、000C8HD、00320H8、8253/8254为可编程定时/计数器,其占有(B)个口地址A、1B、2C、3D、49、8086/8088CPU中断系统的中断优先级的顺序为(D)A、可屏蔽中断,非屏蔽中断,内部中断B、非屏蔽中断,可屏蔽中断,内部中断C、内部中断,可屏蔽中断,非屏蔽中断D、内部中断,非屏蔽中断,可屏蔽中断10、CPU可访问8259A的端口地址数为(B)A、1个B、2个C、4个D、8个11、外设46个中断源,至少需用(B)片8259A管理A、6片B、7片C、8片D、46片12、若8259A工作在电平触发,单片使用,写ICW4,则初始化命令字ICW1的值为(B)A、11HB、1BHC、13HD、1DH13、8259A的中断屏蔽字OCW1在程序运行中(C)设置A、在设置ICW后B、只允许一次C、可允许多次D、仅屏蔽某中断源时14、若8259A的初始化命令字ICW2的值为2AH,说明8259A8个中断源IR0~IR7所定义中断类型号为(B)A、2AH~32HB、28H~2FHC、22H~2AHD、A8H~AFH15、8259A工作在8086/8088模式时,初始化命令字ICW2用来设置(D)A、中断向量的高8位B、中断类型码的低8位C、中断向量的高5位D、中断类型码的高5位16、某8259A系统中,需对IR7、IR3进行屏蔽,则应将操作命令字OCW1置为(D)A、73HB、37HC、88HD、77H17、8259A的中断屏蔽寄存器为(B)A、IRRB、IMRC、ISRD、PR18、8259A的中断服务寄存器为(C)A、IRRB、IMRC、ISRD、PR19、8259A的中断请求寄存器为(A)A、IRRB、IMRC、ISRD、PR20、8259A操作命令字OCW2写入值为20H,功能为(A)A、正常EOI中断结束B、自动EOI中断结束C、在自动EOI时循环D、在正常EOI时循环21、若将8259A的OCW3设置为0AH,则其后从PC机的20H口中读入的是(D)A、中断查询结果B、ISR寄存器内容C、IMR寄存器内容D、IRR寄存器内容22、80x86 CPU用于中断请求的输入引脚信号是(A)A、INTR和NMIB、INTA和NMIC、INTR和INTAD、INTE和IRET23、响应NMI请求的必要条件是(C)A、IF=1B、IF=0C、一条指令结束且无DMA请求D、无INTR请求24、下面(D)中断的优先级最高A、NMI中断B、INTR中断C、单步中断D、断点中断25、当8086 CPU的INTR=1,且中断允许为IF=1时,则CPU完成(C)后,响应该中断请求,进行中断处理A、当前时钟周期B、当前总线周期C、当前指令周期D、下一个指令周期26、INT n指令中断是(C)A、由外部设备请求产生B、由系统断电引起的C、通过软件调用的内部中断D、可用IF标志位屏蔽27、在8086系统中,响应了INTR中断申请,并从中断服务程序返回后,中断标志IF的值一定是(A)A、肯定等于1B、肯定等于0C、不确定D、按设置可能是1或028、对8259A的初始化,以下说法中正确的是(C)A、只能进行一次初始化,从设置ICW1开始B、只能进行一次初始化,根据需要选择起始的初始化命令字C、可以进行多次初始化,每次从设置ICW1开始D、可以进行多次初始化,每次可根据需要选择起始的初始化命令字29、单片8259A已经设置为电平触发中断,现在若要改为脉冲(边沿)触发,需要写入的初始化命令字至少是(D)A、ICW1B、ICW2C、ICW1、ICW4D、ICW1、ICW230、8259A初始化时,ICW2的值是78H。
关闭起始画面,加快OrCAD启动速度

第二个让执行变慢的原因,可能是因为授权许可的环境变数,相信大家当初在安装时,都设定过电脑的环境变数。CDS_LIC_FILE 和 LM_LICENSE_FILE 这两个参数,一般指向放有授权码的电脑或路径,一旦这两个参数的内容指向到许多不同的位置,那麽搜寻时间就会大大增加。如果电脑裡有其他软体也需要用到 LM_LICENSE_FILE 参数,那麽可以试着再加入一个 CDS_LIC_ONLY 的环境变数,并将它设定为 1。如此一来可以告诉 OrCAD,只搜寻 CDS_LIC_FILE 的路径。
mpsinfo.exe
oncrpc.dll
file
到此为止,希望这些方法对各位有用,也欢迎大家分享各自的测试结果
OrCAD Capture 之所以会龟速启动,主要有两个原因,我们可以经由起始画面来判断应该是哪一种原因造成。
首先,红色的起始画面很快出现,却当住好几分钟 (1-20分钟都有可能),那这很可能是因为 Cadence 程式间的沟通出了问题 (the intertool communication, ITC),Capture 裡面有选项可以将这功能关闭。请在 Capture 裡面寻找 Options -> Preferences -> Miscelaneous 这页,即可将 "Enable Intertool Communication" 的打勾取消。ITC 是 Capture 用来跟 Layout 软体做相互沟通,如果真的有需要用到,可以考虑等要用的时候再开启。
cdscommon.dll
nmp.dll
cdn_og702as.dll n_otp603as.dll
方法二:
将底下的两个档桉,从 "C:\Cadence\PSD_15.1\tools\bin" 裡移除,当然,移除是最危险的方式,为了安全起见,可以考虑更改档名或者移到自己觉得安全的地方备份,只要让 OrCAD 找不到这些档桉就好了。
VSCode任务管理器自动化完成重复性工作

VSCode任务管理器自动化完成重复性工作在软件开发过程中,经常会遇到一些需要不断重复的工作,比如编译、调试、运行测试等。
这些工作虽然不可避免,但却占用了开发者宝贵的时间和精力。
为了提高效率,充分利用现有的工具和技术,VSCode(Visual Studio Code)提供了强大的任务管理器功能,可以帮助开发者自动执行重复性工作,从而提高开发效率。
任务管理器是VSCode的一个内置功能,可以通过配置任务,在编辑器中一键调用。
它支持多种类型的任务,如编译、测试、运行、部署等,开发者可以根据实际需求进行配置,适用于各种编程语言和开发环境。
下面将介绍如何使用VSCode任务管理器来自动化完成重复性工作。
首先,打开VSCode,点击左侧的"查看"菜单,在下拉菜单中找到"任务",点击"运行任务"。
这将弹出一个任务列表,其中包含了VSCode默认提供的一些常用任务。
接下来,点击"任务"列表中的"配置任务",这将打开一个任务配置文件。
在该文件中,可以根据自己的需求进行配置。
配置文件是一个JSON格式的文件,它包含了任务的名称、命令、参数等信息。
开发者可以根据不同的需求进行配置,比如编译代码、运行测试、部署应用等。
配置任务时,需要指定任务的类型、命令和参数。
任务的类型可以是shell、process或ant。
命令是要执行的命令行,可以是系统命令、脚本或其他可执行文件。
参数是传递给命令的一些额外参数,可以根据实际需求进行配置。
配置完成后,保存配置文件,并返回任务列表界面。
在任务列表中,可以看到刚刚配置的任务。
点击任务名称,即可运行该任务。
VSCode会打开一个终端窗口,并执行配置的命令。
在执行过程中,开发者可以查看任务的输出结果和错误信息,以便进行调试和修复。
除了默认提供的任务,开发者还可以自定义任务。
在任务列表中,点击"任务",然后选择"配置任务"。
常用英语缩写
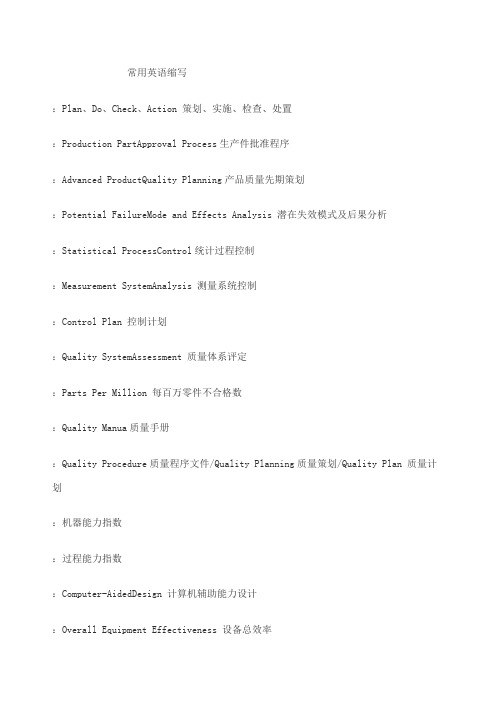
常用英语缩写:Plan、Do、Check、Action 策划、实施、检查、处置:Production PartApproval Process生产件批准程序:Advanced ProductQuality Planning产品质量先期策划:Potential FailureMode and Effects Analysis 潜在失效模式及后果分析:Statistical ProcessControl统计过程控制:Measurement SystemAnalysis 测量系统控制:Control Plan 控制计划:Quality SystemAssessment 质量体系评定:Parts Per Million 每百万零件不合格数:Quality Manua质量手册:Quality Procedure质量程序文件/Quality Planning质量策划/Quality Plan 质量计划:机器能力指数:过程能力指数:Computer-AidedDesign 计算机辅助能力设计:Overall Equipment Effectiveness 设备总效率:Quality FunctionDeployment质量功能展开:First in, First out先进先出:Customer OrientedProcesses顾客导向过程:Time、Cost、Quality时间、成本、质量:Management Processes管理性过程:Support Processes支持性过程:Total QualityManagement全面质量管理:Product QualityAssurance产品质量保证(免检):质量三步曲,质量计划-质量控制-质量改进:Quality AssuranceFile质量保证文件:Quality AssurancePlan质量保证计划:Process Flow Chart过程流程图:Quality ManagementSystems质量管理体系:Just In Time准时(交货):EnterpriseRequirement Planning企业需求计划:Quality Control 质量控制:Quality Audit 质量审核/QalityAssurance 质量保证:In Come QualityControl 进货质量控制:In Process QualityControl 过程质量控制:Final QualityControl 成品质量控制:Out Quality Control 出货质量控制:Man、Machine、Material、Method、Environment人、机、料、法、环:Why、What、Who、When、Where、How 为何/做什么/谁做/时间/地点/如何做:Seiri、Seiton、Seiso、Seiketsu、Shitsuke、Safety 整理、整顿、清扫、清洁、素养、安全值:Total Record Injury(三种)可记录工伤值:精明原则,SpecificMeasurable Achievable Result Oriented Timed(具体的描述、可以测量的、可以通过努力实现的、有结果导向性的、有时间性的)企业常用英文缩写:5S管理:作业制成本制度(Activity-BasedCosting):实施作业制预算制度(Activity-BasedBudgeting):作业制成本管理(Activity-BaseManagement):先进规画与排程系统(AdvancedPlanning and Scheduling):应用程序服务供货商(ApplicationService Provider):可承诺量(Available ToPromise):认可的供货商清单(ApprovedVendor List):物料清单(Bill OfMaterial):企业流程再造(BusinessProcess Reengineering):平衡记分卡(BalancedScoreCard):计划生产(Build ToForecast):订单生产(Build To Order):要径法(Critical PathMethod):每一百万个使用者会有几次抱怨(Complaintper Million):客户关系管理(CustomerRelationship Management):产能需求规划(CapacityRequirements Planning):客制化生产(ConfigurationTo Order):限制驱导式排程法(Drum-Buffer-Rope):成熟度验证(DesignMaturing Testing):设计验证(DesignVerification Testing):运销资源计划(DistributionResource Planning):决策支持系统(DecisionSupport System):设计变更/工程变更(EngineerChange):电子商务(ElectronicCommerce):原件规格更改通知(EngineerChange Request Notice):电子数据交换(ElectronicData Interchange):主管决策系统(ExecutiveInformation System):电磁相容(ElectricMagnetic Capability):基本经济订购量(EconomicOrder Quantity):企业资源规划(EnterpriseResource Planning):应用工程师(FieldApplication Engineer):预估(Forecast):弹性制造系统(FlexibleManufacture System):成品质量管理(Finish orFinal Quality Control): 制程质量管理(In-ProcessQuality Control):进料质量管理(IncomingQuality Control):国际标准组织(InternationalOrganization for Standardization):首批样品认可(InitialSample Approval Request):实时管理(Just In Time):知识管理(KnowledgeManagement):逐批订购法(Lot-for-Lot):最小总成本法(Least TotalCost):最小单位成本(Least UnitCost):制造执行系统(ManufacturingExecution System):制令(Manufacture Order):主生产排程(MasterProduction Schedule):请修(购)单(MaintenanceRepair Operation):物料需求规划(MaterialRequirement Planning):制造资源计划(ManufacturingResource Planning):更改预估量的通知Notice forChanging Forecast:委托代工(OriginalEquipment Manufacture):委托设计与制造(OriginalDesign & Manufacture):在线分析处理(On-LineAnalytical Processing):在线交易处理(On-LineTransaction Processing):最佳生产技术(OptimizedProduction Technology):出货质量管理(Out-goingQuality Control):PDCA管理循环(Plan-Do-Check-Action):产品数据管理系统(ProductData Management):计划评核术(ProgramEvaluation and Review Technique):订单(Purchase Order):预估在手量(Product onHand):采购申请(PurchaseRequest):品质保证(QualityAssurance):质量管理(Quality Control):品管圈(Quality ControlCircle):品质工程(QualityEngineering):粗略产能规划(Rough CutCapacity Planning):退货验收(ReturnedMaterial Approval):再订购点(Re-Order Point):供应链管理(Supply ChainManagement):现场控制(Shop FloorControl):策略信息系统(StrategicInformation System):订单(Sales Order):特殊订单需求(Special OrderRequest):统计制程管制(StatisticProcess Control):限制理论(Theory ofConstraints):全面生产管理(TotalProduction Management):全面质量管理(Total QualityControl):全面品质管理(Total QualityManagement):在制品(Work In Process)部门名称的专有名词QS:Quality system品质系统CS:Coutomer Sevice 客户服务QC:Quality control品质管理IQC:Incoming quality control 进料检验LQC:Line Quality Control 生产线品质控制IPQC:In process quality control 制程检验FQC:Final quality control 最终检验OQC:Outgoing quality control 出货检验QA:Quality assurance 品质保证SQA:Source(supplier) Quality Assurance 供应商品质保证(VQA) CQA:Customer Quality Assurance客户质量保证PQA rocess Quality Assurance 制程品质保证QE:Quality engineer 品质工程CE:component engineering零件工程EE:equipment engineering设备工程ME:manufacturing engineering制造工程TE:testing engineering测试工程PPE roduct Engineer 产品工程IE:Industrial engineer 工业工程ADM: Administration Department行政部RMA:客户退回维修CSDI:检修PC:producing control生管MC:mater control物管GAD: General Affairs Dept总务部A/D: Accountant /Finance Dept会计LAB: Laboratory实验室DOE:实验设计HR:人资PMC:企划RD:研发W/H:仓库SI:客验PD: Product Department生产部PA:采购(PUR: Purchaing Dept)SMT:Surface mount technology 表面粘着技术MFG:Manufacturing 制造MIS:Management information system 资迅管理系统DCC:document control center 文件管制中心厂内作业中的专有名词QT:Quality target品质目标QP:Quality policy目标方针QI:Quality improvement品质改善CRITICAL DEFECT:严重缺点(CR)MAJOR DEFECT:主要缺点(MA)MINOR DEFECT:次要缺点(MI)MAX:Maximum最大值MIN:Minimum最小值DIA iameter直径DIM imension尺寸LCL:Lower control limit管制下限UCL:Upper control limit管制上限EMI:电磁干扰ESD:静电防护EPA:静电保护区域ECN:工程变更ECO:Engineering change order工程改动要求(客户)ECR:工程变更需求单CPI:Continuous Process Improvement 连续工序改善Compatibility:兼容性Marking:标记DWG rawing图面Standardization:标准化Consensus:一致Code:代码ZD:Zero defect零缺点Tolerance:公差Subject matter:主要事项Auditor:审核员BOM:Bill of material物料清单Rework:重工ID:identification识别,鉴别,证明PILOT RUN: (试投产)FAI:首件检查FPIR:First Piece Inspection Report首件检查报告FAA:首件确认SPC:统计制程管制CP: capability index(准确度)CPK: capability index of process(制程能力) PMP:制程管理计划(生产管制计划)MPI:制程分析DAS efects Analysis System 缺陷分析系统PPB:十亿分之一Flux:助焊剂P/N:料号L/N:Lot Number批号Version:版本Quantity:数量Valid date:有效日期MIL-STD:Military-Standard军用标准ICT: In Circuit Test (线路测试)ATE:Automatic Test Equipment自动测试设备MO: Manafacture Order生产单T/U: Touch Up (锡面修补)I/N:手插件P/T:初测F/T: Function Test (功能测试-终测)AS 组立P/K:包装TQM:Total quality control全面品质管理MDA:manufacturing defect analysis制程不良分析(ICT) RUN-IN:老化实验HI-pot:高压测试FMI:Frequency Modulation Inspect高频测试DPPM: Defect Part Per Million?(不良率的一种表达方式:百万分之一) 1000PPM即为% Corrective Action: (CAR改善对策)ACC:允收REJ:拒收S/S:Sample size抽样检验样本大小SI-SIV:Special I-Special IV特殊抽样水平等级CON:Concession / Waive特采ISO:国际标准化组织ISA:Industry Standard Architecture工业标准体制结构OBA:开箱稽核FIFO:先进先出PDCA:管理循环Plan do check action计划,执行,检查,总结WIP:在制品(半成品)S/O: Sales Order (业务订单)P/O: Purchase Order (采购订单)P/R: Purchase Request (请购单)AQL:acceptable quality level允收品质水准LQL;Limiting quality level最低品质水准QVL:qualified vendor list合格供应商名册AVL :认可的供货商清单(Approved Vendor List) QCD: Quality cost delivery(品质,交期,成本)MPM:Manufacturing project management制造专案管理KPI:Key performance indicate重要绩效指标MVT:Manufacturing Verification Test制造验证试产Q/R/S:Quality/Reliability/Service质量/可靠度/服务STL:ship to line(料到上线)NTF:No trouble found误判CIP:capacity improvement plan(产能改善计划)MRB:material review board(物料审核小组)MRB:Material reject bill退货单JIT:just in time(即时管理)5S:seiri seiton seiso seiketsu shitsuke(整理,整顿,清扫,清洁,修养)SOP:standard operation process(标准作业程序)SIP:Specification inspection process制程检验规格TOP: Test Operation Process (测试作业流程)WI: working instruction(作业指导书)SMD:surface mounting device(表面粘着原件)FAR:failure aualysis report故障分析报告CAR:Corrective action report改善报告BPR:企业流程再造 (Business Process Reengineering)ISAR :首批样品认可(Initial Sample Approval Request)-JIT:实时管理 (Just In Time)QCC :品管圈 (Quality Control Circle)Engineering Department (工程部)TQEM: Total Quality Environment Management(全面品质环境管理)PD: Production Department (制造)LOG: Logistics (后勤支持)?Shipping: (进出口)AOQ:Average Output Quality平均出货质量AOQL:Average Output Quality Level平均出货质量水平FMEA:failure model effectiveness analysis失效模式分析CRB: Change Review Board (工程变更会议)CSA:Customer Simulate Analysis客户模拟分析SQMS:Supplier Quality Management System供应商品质管理系统QIT: Quality Improvement Team 品质改善小组QIP:Quality Improvement Plan品质改善计划CIP:Continual Improvement Plan持续改善计划Material Quality Feedback Sheet (来料品质回馈单)SCAR: Supplier Corrective Action Report (供货商改善对策报告) 8D Sheet: 8 Disciplines sheet ( 8D单)PDCA:PDCA (Plan-Do-Check-Action) (管理循环)MPQ: Material Packing Quantity (物料最小包装量)DSCN: Delivery Schedule Change Notice (交期变更通知) QAPS: Quality Assurance Process Sheet (品质工程表) DRP :运销资源计划 (Distribution Resource Planning) DSS:决策支持系统 (Decision Support System)EC :电子商务 (Electronic Commerce)EDI :电子资料交换 (Electronic Data Interchange)EIS :主管决策系统 (Excutive Information System)ERP:企业资源规划 (Enterprise Resource Planning) FMS :弹性制造系统 (Flexible Manufacture System)KM :知识管理 (Knowledge Management)4L :逐批订购法 (Lot-for-Lot)LTC :最小总成本法 (Least Total Cost)LUC :最小单位成本 (Least Unit Cost)MES :制造执行系统 (Manufacturing Execution System) MPS :主生产排程 (Master Production Schedule)MRP :物料需求规划 (Material Requirement Planning) MRPⅡ:制造资源计划 (Manufacturing Resource Planning) OEM :委托代工 (Original Equipment Manufacture)ODM :委托设计与制造 (Original Design & Manufacture) OLAP:线上分析处理 (On-Line Analytical Processing) OLTP:线上交易处理 (On-Line Transaction Processing) OPT :最佳生产技术 (Optimized Production Technology) PDCA:PDCA管理循环 (Plan-Do-Check-Action)PDM:产品数据管理系统 (Product Data Management))RCCP:粗略产能规划 (Rough Cut Capacity Planning) SCM :供应链管理 (Supply Chain Management)SFC :现场控制 (Shop Floor Control)TOC:限制理论 (Theory of Constraints)TQC :全面品质管制 (Total Quality Control)FYI/R:for your information/reference仅供参考ASAP:尽快S/T:Standard time标准时间TPM:total production maintenance:全面生产保养ESD Wrist strap:静电环IT:information technology信息技术,资讯科学CEO:Chief Executive Officer执行总裁COO:Chief Operaring Officer首席业务总裁SWOT:Strength,Weakness,Opportunity,Threat优势﹐弱点﹐机会﹐威胁Competence:专业能力Communication:有效沟通Cooperation:统御融合Vibration Testing:振动测试IDP:Individual Development Plan个人发展计划MRP:Material Requirement Planning物料需求计划MAT'S:Material材料LRR:Lot Rejeet Rate批退率ATIN:Attention知会3C:Computer ,Communication , Consumer electronic消费性电子5W1H:When , Where , Who , What , Why , Ho5M: Man , Machine , Material , Method , Measurement人,机器,材料,方法,测量4MIE: Man,Material,Machine,Method,Environment人力,物力,财务,技术,时间(资源)7M1I: Manpower , Machine , Material , Method, Market , Management , Money , Information人力,机器,材料,方法, 市场,管理,资金,资讯Accuracy 准确度Action 行动?Activity 活动?Analysis Covariance 协方差分析Analysis of Variance 方差分析Approved 承认?Attribute 计数值?Average 平均数?Balance sheet 资产负债对照表?Binomial 二项分配?Brainstorming Techniques 脑力风暴法?Cause and Effect Matrix 因果图(鱼骨图)?CL:Center Line 中心线?Check Sheets 检查表?Complaint 投诉?Conformity 合格(符合)?Control 控制?Control chart 控制(管制)图?Correction 纠正?Correlation Methods 相关分析法?CPI: continuouse Process Improvement 连续工序改善?Cross Tabulation Tables 交叉表?CS: Customer Sevice 客(户)服(务)中心?DSA: Defects Analysis System 缺陷分析系统?Data 数据 Description:品名DCC: Document Control Center 文控中心?Decision 决策、判定?Defects per unit 单位缺点数?Description 描述?Device 装置?Do 执行?DOE: Design of Experiments 实验设计?Element 元素?Engineering recbnology 工程技Environmental 环境?Equipment 设备?Estimated accumulative frequency 计算估计累计数?E Equipment Variation 设备变异?External Failure 外部失效,外部缺陷?FA: Failure Analysis 失效分析?Fact control 事实管理?Fatigue 疲劳?FMEA: Failure Mode and Effect Analysis失效模式与效果分析?FP First-Pass Yield (第一次通过)合格率?FQA: Final Quality Assurance 最终品质保证?FQC: Final Quality control 最终品质控制?Gauge system 测量系统?Grade 等级?Histogram 直方图?Improvement 改善Initial review 先期审查?Inspection 检验?Internal Failure 内部失效、内部缺陷?IPQC: In Process Quality Control 制程品质控制?IQC: Incomming Quality Control 来料品质控制?IS International Organization for Standardization 国际标准化组织?LCL: Lower Control limit 管制下限?LQC: Line Quality Control 生产线品质控制?LSL: Lower Size Limit 规格下限?Machine 机械?Manage 管理?Materials 物料?Measurement 测量?Median 中位数?MSA: Measurement System Analysis 测量系统分析?Occurrence 发生率?Operation Instruction 作业指导书?Organization 组织?Parto 柏拉图?PPM arts per Million (百万分之)不良率?Plan 计划?Policy 方针?Population 群体?PQA: Process Quality Assurance 制程品质保证?Practice 实务(践)?Prevention 预防?Probability 机率?Probability density function 机率密度函数?Procedure 流程?Process 过程?Process capability analysis 制程能力分析(图)?Process control and Process capability制程管制与制程能力?Product 产品?Production 生产?Projects 项目?QA: Quality Assurance 品质保证?QC: Quality Control 品质控制?QE: Quality Engineering 品质工程?QFD: Quality Function Desgin 品质机能展开(法) Quality 质量?Quality manual 品质手册?Quality policy 品质政策(质量方针)?Random experiment 随机试验?Random numbers 随机数?R:Range 全距(极差)?Reject 拒收?Repair 返修?Repeatusility 再现性?Reproducibility 再生性Requirement 要求?Responsibilities 职责?Review 评审?Reword 返工?Rolled yield 直通率?RPN: Risk Priority Number 风险系数?Sample 抽样,样本?Sample space 样本空间?Sampling with replacement 放回抽样?Sampling without replacement 不放回抽样?Scatter diagram 散布图分析?Scrap 报废?Simple random sampling 简单随机取样?Size 规格?SL: Size Line 规格中心线?Stratified random sampling 分层随机抽样?SOP: Standard Operation Procedure 标准作业书?SPC: Statistical Process Control 统计制程管制?Specification 规范?SQA: Source(Supplier) Quality Assurance 供货商品质保证?Stage sampling 分段随机抽样?Standard Deviation 标准差?Sum of squares 平方和?Taguchi-method 田口(试验)方法?Theory 原理?TQC: Total Quality Control 全面品质控制?TQM: Total Quality Management 全面品质管理?Traceablity 追溯?Training 培训?UCL: Upper Control Limit 管制(控制)上限?USL: Upper Size Limit 规格上限?Validation 确认?Variable 计量值?Verification 验证?Version 版本?VOC: Voice of Customer 客户需求?VOE: Voice of Engineer 工程需求?Inventory stock report:库存清单报告Sales order report:出货报告。
Manufacturing Process Control

Manufacturing Process Control Manufacturing process control is a critical aspect of ensuring the quality and efficiency of production in various industries. It involves monitoring and managing the processes involved in manufacturing to ensure that products meet the required specifications and standards. Effective process control can help companies reduce waste, improve productivity, and enhance product quality. Oneof the key elements of manufacturing process control is monitoring and measuring various parameters during the production process. This can include temperature, pressure, flow rates, and other variables that can impact the quality of the final product. By continuously monitoring these parameters, manufacturers can identify any deviations from the desired values and take corrective actions to ensure that the process stays within the defined limits. Another important aspect of process control is the use of automation and control systems to regulate the manufacturing processes. Automation can help companies streamline their production processes, reduce human error, and improve overall efficiency. By implementing automated control systems, manufacturers can ensure that processes are carried out consistently and accurately, leading to higher quality products and reduced production costs. In addition to monitoring and automation, process control also involves the use of statistical analysis and quality control techniques toidentify and address any issues that may arise during production. By collectingand analyzing data from the manufacturing processes, companies can identify trends, patterns, and potential problems that could affect product quality. This allows them to take proactive measures to prevent defects and ensure that products meet the required specifications. Furthermore, process control also plays a crucialrole in ensuring compliance with regulatory requirements and industry standards.By implementing robust process control systems, manufacturers can demonstrate that their products meet the necessary quality and safety standards, helping them to build trust with customers and regulators. This can also help companies avoidcostly recalls, fines, and damage to their reputation. Overall, manufacturing process control is essential for ensuring the quality, efficiency, and consistency of production in various industries. By monitoring and measuring key parameters, implementing automation and control systems, utilizing statistical analysis andquality control techniques, and ensuring compliance with regulatory requirements, companies can improve their manufacturing processes and deliver high-quality products to customers. Effective process control not only benefits the company but also contributes to the overall success and reputation of the industry as a whole.。
失控处理的一般流程

失控处理的一般流程英文回答:Incident Handling Process.1. Incident Detection and Reporting.Monitor systems and networks for suspicious activity.Establish clear channels for reporting incidents.Implement automated detection and alerting mechanisms.2. Incident Triage.Assess the severity and impact of the incident.Determine the urgency and resources required.Classify the incident based on type (e.g., security breach, system failure, hardware malfunction).3. Incident Containment.Isolate the affected systems or networks.Stop the spread of the incident.Protect sensitive data and critical systems.4. Incident Analysis.Determine the root cause of the incident.Gather evidence and document the incident timeline.Identify potential vulnerabilities and weaknesses.5. Incident Resolution.Implement corrective actions to address the rootcause.Restore affected systems and services.Verify the effectiveness of the resolution.6. Incident Post-Mortem.Review the incident and its handling.Identify areas for improvement in detection, containment, and recovery.Update incident response plans and procedures.中文回答:失控处理的一般流程。
- 1、下载文档前请自行甄别文档内容的完整性,平台不提供额外的编辑、内容补充、找答案等附加服务。
- 2、"仅部分预览"的文档,不可在线预览部分如存在完整性等问题,可反馈申请退款(可完整预览的文档不适用该条件!)。
- 3、如文档侵犯您的权益,请联系客服反馈,我们会尽快为您处理(人工客服工作时间:9:00-18:30)。
Dielectric and Copper CMP - the Evolution of Integrated Process Control andSolutions Down to 65nm and belowByDr. Moshe Finarov, Mr. Avron Ger, Dr. Giora DishonNova Measuring Instruments Ltd., Rehovoth, IsraelInvited Paper, CMP-MIC February 2005AbstractIntegrated metrology has been first introduced into the production process of semiconductor manufacturing in dielectric CMP in 1995. The new and immature CMP process, the highest COO step, required fast and cost effective incorporation into manufacturing, which helped proving the viability of integrated metrology as a production tool. From the thick dielectric CMP of up to 8 metal layers (down to 0.13um technology node), through advanced STI polishing with angstrom thick residues, to very complex copper polishing with very sensitive low-K and cap layers (65nm and below), integrated metrology has evolved in measurement capabilities, performance and advanced control mechanisms, to provide real time process control needs. Integrated metrology will continue to evolve with 2D metrology capabilities in the CMP process control for 45nm and below with of complex stacks and materials.CMP Integrated Metrology (IM) History at a GlanceThe chemical mechanical planarization (CMP) market is one of the fastest growing technology areas within the semiconductor industry. With equipment and materials revenues estimated at more than $1 billion in 1999, this combined market is slated to exceed $2.4 billion by 2005 (Fig.1). In the early nineties, when oxide CMP was penetrating into semiconductor manufacturing, the process suffered from significant instabilities and non-uniformities, requiring rigorous process control.Two main elements constituted process control as practicedby all advanced semiconductor manufacturers:1. Very high sampling of the oxide thickness of thepolished layers (more than 5 wafers per lot).2. The “Gating” method: polish first wafer, clean, dryand measure – then feedback the result to adjust theprocess for the consecutive wafers in the lot.The first generation polishers were designed as “dry in –wet out” tools, and required cleaning and drying thepolished wafers with a separate cleaner prior tomeasurement on a stand-alone thin-film metrology tool.This procedure took many hours and led to very low CMP equipment efficiency (much less than 50%). The best way to overcome was to install the metrology system inside the polishing equipment.The major challenge was the incorporation of a stand-alone compatible, high-accuracy, large-sized and very sensitive optical measurement system inside the process tool environment, which is characterized by mechanical vibrations, electromagnetic interference and water ambient. Moreover, since the polished wafers were kept in water (until removed, cleaned and dried), it was necessary to carry out the optical measurements in water, something that was not practiced before. Integrating a high precision system with the processing equipment required a metrology tool with higher reliability and higher throughput, so not to affect the polisher’s uptime and throughput. In addition, high tool-to-tool matching of the metrology was needed in order to provide uniform metrology criteria for all polishers in the fab.In Semicon West ’95 show, July 1995, Nova Measuring Instruments presented the first commercial ITM (Integrated Thickness Monitoring) system, the NovaScan 210. The system with its dedicated, compact opto-mechanical design met all above-mentioned requirements, while keeping the wafer stationary and in water during measurement [8]. The system was designed for accurate thickness measurement of dielectric films and stacks (as needed in multilevel interconnects) inside the polisher, and was integrated with Strasbaugh’s 6DS-SP and Westech’s 372M polishers. 1995 was therefore the first year of the Integrated Metrology (IM) era in semiconductor manufacturing, and IM formed a paradigm shift in CMP processing.The main significant advantages realized by the semiconductor manufacturers using the NovaScan IM systems, were:Increased polishing tool efficiencyFaster response and higher sampling rate leading to a significantly better process controlShorter manufacturing cycleElimination of test wafersSavings of labor and clean room space required for SA metrology toolsAll these led to a wide acceptance and fast penetration of the NovaScan IM systems as part of the CMP manufacturing process (with practically all existing and new polishing tool manufacturers and models). However, the close cooperation required between the end-users, the process equipment manufacturers (PEM’s) and IM system manufacturers, did pose a lot of challenges and barriers to overcome, both technologically and commercially. Currently, 10 years after the initial introduction of Integrated Metrology to the market, the penetration level for dielectric CMP is close to 100%.Newer generations of CMP polishers became “dry-in/dry-out”, enabling also the less complex IM “dry integration”: Wafers are measured in-air, after cleaning and drying, before moving to the output cassette [8]. However, many semiconductor manufacturers continue to select the “wet integration” for the “dry-in/dry-out” polishers. This is primarily because the response time to the polish process is faster and enables effective wafer-to-wafer control. Table 1 below summarizes the main differences between the integration concepts for dielectric CMP.Wet Dry• Complex and more costly • Fastest feedback for CLC and excursions control• Significant reduction of rework in STI w/o over polish• Reduction of Gating Wafers cycle time• 100% pre and post • Faster and cheaper• Easier applicationdevelopment• Higher sensitivity to STI oxide residues• Recipe compatibility with Stand Alone metrology tools. • 100% pre and postTable 1. Wet vs. Dry IntegrationsCurrently all leading polishers are offered with on-board IM tools that enable both excursion control and APC for all CMP processes: ILD, IMD, STI, poly-Si, W and Copper. The significant advancement in IM systems development over the last decade led to systems that are fast enough to measure every wafer, before and after CMP, adding the incoming thickness variations in the CLC models.The metrology itself significantly evolved from “simple” visible light Reflectometry in the first models to Scatterometry in the latest models with polarized light in a broad spectral range - from DUV to NIR, enabling also small spot size, very high throughput and ability of both wet and dry integration. In the 65 to 45nm technology nodes we expect that all measurements will be performed on arrays (vs. solid pads today) within the dies or on test sites in order to provide the best correlation with actual effects, such as local planarity, on device patterns.Integration between the IM tool and the CMP polisher has significantly evolved during this period. The first IM tools were installed inside the polishers, but their operation was independent – recipe design, measurement runs, and data collection were separated from the polisher’s computer and with a separate user interface. Currently the integration between the process and the metrology tools is more extensive: all the IM operations are carried out from the polisher’s GUI through SECS/GEM communication. The measurement results are used in real time for CLC, and provide the polishing parameters to the next wafers in the lot.During this decade, Integrated Metrology has experienced fast growth and major changes in the CMP area: currently over 1500 IM tools are operating in all advanced semiconductor fabs. The application areas have broadened and advanced:From measuring thick ILD layers to measuring single Angstrom residues after STI and Copper polishFrom solid test sites measured by visible reflectometry to line arrays measured by DUV scatterometryFrom 2 minutes on 200 mm wafer measured at 5 points to 13 seconds on 300 mm wafer measured at 13 points.From simple SPC to real-time CLC.Examples of IM tools are presented in figures 2 and 3. IM tool development will continue to meet the new requirements of the next ITRS technology nodes.Fig. 2 Wet NovaScan 210 integrated onto a Westech 372 Fig. 3 NovaScan 3060 in Dry Factory Interface moduleWith the introduction of APC methodology and algorithms, Integrated Metrology has moved metrology from its original and historical position of “a non-value added operation” to become an “added-value” operation.IM based Closed Loop Control (CLC)Enhancing the Polishing Process by Using Integrated Metrology with CLCIM tools enable Wafer-to-Wafer and Within-Wafer process control. Closed Loop Control (CLC), utilizing the measurement data (pre- and post-polish) provides real-time adjustment of the CMP process.Fig. 4. Closed Loop Control enabling reduction of output variationsCMP processing suffers from a relative fast drift of process parameters (such as removal rate), which requires continuous monitoring of the process performance and data feedback from each wafer to the process controller. The process controller can then dynamically adjust the process conditions for the following wafer, e.g. by adjusting polishing time for every wafer.The use of classical control theory, advanced filtering methods and extensive accumulated field experience provided a solid basis for the production-reliable CLC option. Sampling rate is very high, as the IM systems measure each wafer, and the process parameters are fed (back) to the next wafer polished. With the new IM tools, enabling 100% pre-and post- measure, the advantages of CLC with the combined feed forward and feedback allow further improvement of productivity and cost of ownership.The benefits of using real time CLC are [4,5]:Improved outgoing CMP qualityReduced cycle time in CMP areaReduced consumables usageImproved polisher utilization and productivityReduced laborDecrease test waferCLC ResultsFig. 5 Open loop control using default polish timeFig. 6. Closed loop control - polish time adjusting for every wafer.IM Role in STI CMPAs device geometries continue to shrink, planarity requirements for Shallow Trench Isolation (STI) chemical mechanical planarization are becoming increasingly stringent and process requirements of STI CMP result in a much narrower process window. One of the greatest challenges in STI CMP involves the achievement of planarization uniformity over both the die level and the wafer level. Uniformity requirements vary with device and application, but typically the thickness uniformity across the wafer (within-wafer non-uniformity, or WIWNU) must be <3%. Dishing of the trench oxide must typically be <20-50nm. Accordingly, the quality of an STI process is measured by the control of trench oxide and nitride thicknessA new approach to STI CMP has been developed through the use of Slurry-Free Fixed Abrasive (FA) technology or High Selectivity Slurry (HSS) that is named “Direct STI”, removing the need of reverse etch-back process steps before CMP or the use of "dummy" patterns. Direct STI improves the cost of ownership and reduces the cycle time. Direct STI requires greater control of the CMP process and lower sensitivity to pattern density and feature size. The key advantage of using FA is its selectivity to topography up to (>100:1) and the use of HSS that improves the ability to halt polishing on the nitride stop layer.1. Confirm40Å ofas TEM,enhancedmore2. WIWNUa.b.c.Fig 8. STI residues using injection pre/post vs. F5 Stan AloneIM role in Copper CMP Process ControlThe goal in Copper CMP is to stop the first-step polish on the barrier layer without inducing dishing, erosion and non-uniformity, and then remove the barrier and some dielectric films in the second-step polish. Due to the significant differences between polish rates of copper, barriers, cap layers, oxide and low K materials, dishing of copper pads and erosion of copper line arrays are an inherent part of the polish step output. When IC manufacturers are integrating low-k with cap/hard masks films, it is very important to remove the cap layer but leave the low-k dielectric layer intact. These materials protect the porous and mechanically weak low-k dielectrics from destruction that causes reduction of the overall dielectric constant k (k eff) in the CMP. Therefore, very tight thickness control of the cap layer is needed. CLC by the help of IM can be effectively used for this type of application.Various methods are being used to overcome these hurdles of copper and low-k. New polish processes involving low down force are being developed to reduce the mechanical stresses on the films during CMP.Another required capability is a tight control of erosion. Erosion measurements show a strong correlation to the electrical performance of the copper line, and good control of the erosion also reduces the probability of residues in higher metal levels.Measuring the erosion optically directly in the die area or on special test structures [5] reduces cycle time and eliminates the need for HRP measurements. By measuring erosion with an IM system the next stage of Copper APC is enabled. Fig. 9 shows the correlation between 3 wafers on 3 different pitches: on 0.24 and 0.35 um pitch arrays relative to 1 um array.Fig.9. Residues detection and characterization by Integrated MetrologyN ewcomers in Copper CMP usually need the detection and determination of residue (copper or barrier) as an important excursion control. The balance in the multiple step copper CMP between over-polishing, leading to dishing and erosion and under-polishing leaving copper/barrier residues is very subtle. This excursion control may be effectively achieved by the same IM system combining image processing and spectrophotometric measurement [5]. Fig 10. above illustrates this method of residues detection and characterization [6,11].The Combined Residue Identification – The Concept1. Image Processing2. Spectrum AnalysisCleanCu residueon topBuriedresidue3. Residue thickness mappingLive ImageGolden ImageFig. 10 IM residues detection mode of operation.SummaryIntegrated Metrology and the associated Advanced Process Control technologies have become an inherent part of dielectric and Copper CMP. During the 10 years of its use in production, optical measurement systems and APC algorithms evolved continuously with the increasing requirements of the CMP processing. In parallel, multiple technologies for in-situ measurements and control have been developed as well, complementing to the capabilities of integrated metrology. All will continue to evolve to meet the control criteria as defined in the ITRS for technology nodes of 65 and 45 nm, requirements which pose new challenges for Integrated Process Control primarily for STI and Copper/low-k CMP.4812ResiduesAUList of References1. On-Line Integrated Metrology for CMP Processing, G. Dishon, M. Finarov and R. Kipper, NovaMeasuring Instruments, J.W. Curry, T. Schraub and D. Trojan, R.H. Strasbaugh Inc., D.Stambaugh, Y. Li and J. Ben-Jacob, IBM/MiCRUS Corp., CMP-MIC Conference, Feb. 22-23,1996, 1996 ISMIC - 100P/96/0273.2. Dielectric CMP Advanced Process Control based on Integrated Thickness Monitoring, G. Dishon,D. Eylon, M. Finarov, A. Shulman, 1998 CIM-MIC Conference, 1998 IMIC – 300P/98/0267.3. Capabilities and lessons from 10 years of APC success - Solid State Technology February, 2004by Carl Fiorletta4. APC from A Foundry Perspective - AEC/APC XV Symposium September 2003 by Dr. Mark Liu5. US Patent #. 6,292,265 - Method and apparatus for monitoring a chemical mechanicalplanarization process applied to metal-based patterned objects, Finarov et al., January 20016. US Patent #. 6,801,326 - Method and apparatus for monitoring a chemical mechanicalplanarization process applied to metal-based patterned objects, Finarov et al. Oct. 20047. US Patent #. 6,368,181 - Apparatus for optical inspection of wafers during polishing, Dvir et al.April 20028. US Patent # 6,752,689 - Apparatus for optical inspection of wafers during polishing, Finarov etal. June 20049. US Patent # 6,100,985- Method and apparatus for measurements of patterned structures, Schieneret al. August 2000.10. US Patent # 6,292,265 - Method and apparatus for monitoring a chemical mechanicalplanarization process applied to metal-based patterned objects, Finarov et al. September 2001.11. Presented at the 4th European AEC/APC in April 200312. STI Planarization Using Fixed Abrasive Technology, L. Economikos, F-F. Jamin, A.Ticknor and A. Simpson, Future Fab Intl., Volume 12, 200213. Metrology Develops to Measure Thinner Film Better – Alex Braun, Semiconductor International,October 2004.。