机械制造工艺学PPT课件
合集下载
《机械制造工艺学》说课稿ppt
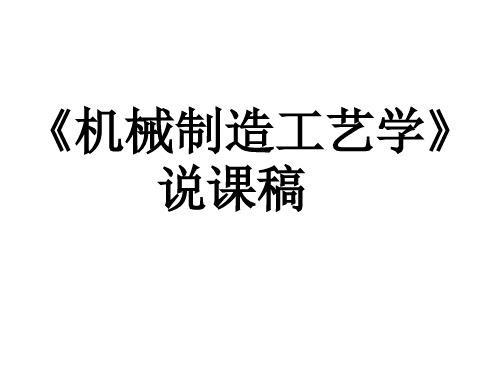
• (一)学情分析 • 1、知识技能 • 学生已经学习了《机械制图》、《工程力学》、等专业基础课的 学习,还参加了金工实习,对金属切削刀具和金属切削机床都有了一 定的感性认识,为这门课的学习奠定了基础。 • 2、学习态度 • 机械类专业的学生男同学较多,学生总体情况比较好,大部分学生 学习态度端正,学习积极性较高,上课活跃,爱动脑子,对实验实践 很感兴趣,具有较强的动手能力。 • (二)教学过程 • 采用”教、学、看”三合一的模式。教学方法与过程如下: • 理论性知识采用课前预习及自学,课上以答疑的方式,既缩短了课 堂教学的时间,同时培养了学生的自主学习意识。课程的重点、难点 采用参观实习的方式来突出重点,化解难点。
《机械制造工艺学》 说课稿
• • • • • • • •
共分七个方面: 一、课 程 定 位 与 目 标 二、课 程 资 源 三、课 程 内 容 四、教 学 过 程 五、教 学 方 法 六、课 程 考 核 与 反 馈 七、课 程 特 色
一、课 程 定 位 与 目 标
• (一)课程定位 • 本课程是数控专业学生的一门必修专业技能领域课程。 • 1、本课程的任务是:使学生掌握机械制造的基本理论和 工艺规程的编制,对工艺问题能进行分析和提出改进措施, 掌握零件加工和机器装配结构工艺性的原则,设计的产品 具有良好的结构工艺性,掌握保证机器装配精度的方法, 掌握机床夹具的设计原理和方法,具有设计机床夹具的初 步能力,具有综合分析和解决实际工艺问题的能力,提出 保证质量,提高劳动效率,降低成本的工艺途径。
六、考 核 与 反 馈
• (一)考 核 • 学习态度10%、作业20%、参观实习10%、 理论考核60% • (二)反 馈 • 促进教学,建立多途径、多级别的反馈系 统。 • 1、不同对象:学生直接反馈、小组反馈、 班级反馈、辅导员反馈。 • 2、不同途径:对话、问卷、网络等。
《机械制造工艺学》 说课稿
• • • • • • • •
共分七个方面: 一、课 程 定 位 与 目 标 二、课 程 资 源 三、课 程 内 容 四、教 学 过 程 五、教 学 方 法 六、课 程 考 核 与 反 馈 七、课 程 特 色
一、课 程 定 位 与 目 标
• (一)课程定位 • 本课程是数控专业学生的一门必修专业技能领域课程。 • 1、本课程的任务是:使学生掌握机械制造的基本理论和 工艺规程的编制,对工艺问题能进行分析和提出改进措施, 掌握零件加工和机器装配结构工艺性的原则,设计的产品 具有良好的结构工艺性,掌握保证机器装配精度的方法, 掌握机床夹具的设计原理和方法,具有设计机床夹具的初 步能力,具有综合分析和解决实际工艺问题的能力,提出 保证质量,提高劳动效率,降低成本的工艺途径。
六、考 核 与 反 馈
• (一)考 核 • 学习态度10%、作业20%、参观实习10%、 理论考核60% • (二)反 馈 • 促进教学,建立多途径、多级别的反馈系 统。 • 1、不同对象:学生直接反馈、小组反馈、 班级反馈、辅导员反馈。 • 2、不同途径:对话、问卷、网络等。
机械制造工艺学课件
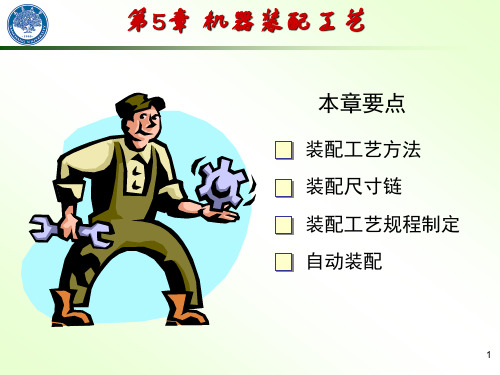
16
二、制定装配工艺规程的步骤
➢3.划分装配单元,确定装配顺序 无论那一级装配单元,都要选定某一零件或比它低一级 的装配单元作为装配基准件。
装配基准件通常应是产品的基体或主干零、部件。 基准件应有较大的体积和重量,有足够的支承面,以满 足陆续装入零、部件时的作业要求和稳定要求。
例如:床身零件是床身组件的装配基准零件;床身组件 是床身部件的装配基准组件;床身部件是机床产品的装配 基准部件。在划分装配单元,确定装配基准零件以后,即 可安排装配顺序,并以装配系统图的形式表示出来。具体 来说一般是先难后易、先内后外、先下后上,预处理工序 在前。图 5-7 表示卧式车床床身装配简图,图 5-8 表 示床身部件装配系统图。
零 件
机器
部部 件件
组套 件件
图5-2 机器装配系统示意图
6
一、机器装配的基本概念
套件与组件
❖在一个基准零件上,装上一个或若干个零件就构成了一个 套件,它是最小的装配单元。每个套件只有一个基准零件, 它的作用是联接相关零件和确定各零件的相对位置。为形成 套件而进行的装配工作称为套装。 ❖套件可以是若干个零件永久性联接(焊接或铆接等)或是 连接在一个"基准零件"上少数零件的组合。套件组合后,可 能还要需要加工。为形成套件而进行的装配工作称为套装。
19
二、制定装配工艺规程的步骤
➢4.编制装配工艺文件 单件小批生产时,通常只绘制装配系统图。装配时,按 产品装配图及装配系统图工作。 成批生产时,通常还制定部件、总装的装配工艺卡,写 明工序次序,简要工序内容,设备名称,工夹具名称与编 号,工人技术等级和时间定额等项。 在大批大量生产中,不仅要制定装配工艺卡,而且要制 定装配工序卡,以直接指导工人进行产品装配。 此外,还应按产品图样要求,制定装配检验及试验卡片。
二、制定装配工艺规程的步骤
➢3.划分装配单元,确定装配顺序 无论那一级装配单元,都要选定某一零件或比它低一级 的装配单元作为装配基准件。
装配基准件通常应是产品的基体或主干零、部件。 基准件应有较大的体积和重量,有足够的支承面,以满 足陆续装入零、部件时的作业要求和稳定要求。
例如:床身零件是床身组件的装配基准零件;床身组件 是床身部件的装配基准组件;床身部件是机床产品的装配 基准部件。在划分装配单元,确定装配基准零件以后,即 可安排装配顺序,并以装配系统图的形式表示出来。具体 来说一般是先难后易、先内后外、先下后上,预处理工序 在前。图 5-7 表示卧式车床床身装配简图,图 5-8 表 示床身部件装配系统图。
零 件
机器
部部 件件
组套 件件
图5-2 机器装配系统示意图
6
一、机器装配的基本概念
套件与组件
❖在一个基准零件上,装上一个或若干个零件就构成了一个 套件,它是最小的装配单元。每个套件只有一个基准零件, 它的作用是联接相关零件和确定各零件的相对位置。为形成 套件而进行的装配工作称为套装。 ❖套件可以是若干个零件永久性联接(焊接或铆接等)或是 连接在一个"基准零件"上少数零件的组合。套件组合后,可 能还要需要加工。为形成套件而进行的装配工作称为套装。
19
二、制定装配工艺规程的步骤
➢4.编制装配工艺文件 单件小批生产时,通常只绘制装配系统图。装配时,按 产品装配图及装配系统图工作。 成批生产时,通常还制定部件、总装的装配工艺卡,写 明工序次序,简要工序内容,设备名称,工夹具名称与编 号,工人技术等级和时间定额等项。 在大批大量生产中,不仅要制定装配工艺卡,而且要制 定装配工序卡,以直接指导工人进行产品装配。 此外,还应按产品图样要求,制定装配检验及试验卡片。
机械制造工艺学 教学课件 作者 陈明 第一章 机械制造工艺过程基本概念-大学课件-
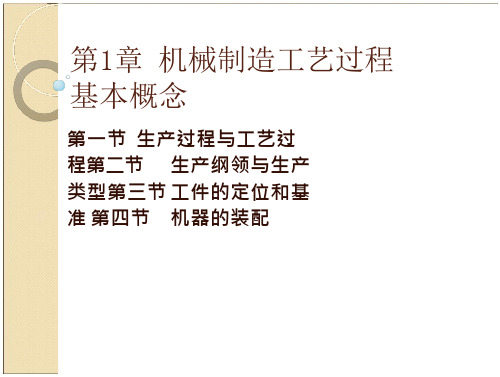
● 3)设置一个定位支承点的平面限制一个自由度,称为止 推定位面或防转定位面。究竟是止推作用还是防转作用, 要根据这个定位支承点所限制的自由度是移动的还是转动 的而定。
● 4)一个定位支承点只能限制一个自由度。
●5)定位支承点必须与工件的定位基准始终贴紧 接触。一旦分离,定位支承点就失去了限制工 件自由度的作用。
常见的装配工作内容有下列几项: 1 清洗 2 联接 3 校正、调整与配作 4 平衡 5 验收
对旋转体内部的不平衡,需要结合校正 方法进行: ●1)用补焊、铆接、胶接或螺纹联接等方法 加配部分质量。 ● 2)用钻、铣、磨或锉等方法去除部分质量。
●3)在预制的平衡槽内改变平衡块的位置和 数量,加以平衡
●6)工件在定位时需要限制的自由度数目以及究 竟是哪几个自由度,完全由工件该工序的加工 要求所决定,应该根据实际情况进行具体分析, 合理设置定位支承点的数量和分布情况。
●7)定位支承点所限制的自由度,原则上不允许 重复或相互矛盾。
(二)完全定位与不完全定位
工件的6个自由度全部被限制而在夹具中占有完全 确定的唯一位置,称为完全定位。
在分析基准问题时,必须注意下列两点:
● 1)作为基准的点、ຫໍສະໝຸດ 、面在工件上不一定具体存在,而 由某些具体的表面来体现,这些表面称为基面。例如,内 孔的中心线是通过内孔表面来体现的,内孔中心线是基准, 内孔表面是基面。因此,选择基准的问题就是选择恰当的 基面的问题。特别地,有时为了叙述方便,可以将基准和 基面统称为基准。
没有全部限制工件的6个自由度,但也能满足加工 要求的定位,称为不完全定位。
图1-6
图1-7
(三)欠定位与过定位
根据加工的要求,工件必须限制的自由度没有达到 全部限制的定位,称为欠定位。
● 4)一个定位支承点只能限制一个自由度。
●5)定位支承点必须与工件的定位基准始终贴紧 接触。一旦分离,定位支承点就失去了限制工 件自由度的作用。
常见的装配工作内容有下列几项: 1 清洗 2 联接 3 校正、调整与配作 4 平衡 5 验收
对旋转体内部的不平衡,需要结合校正 方法进行: ●1)用补焊、铆接、胶接或螺纹联接等方法 加配部分质量。 ● 2)用钻、铣、磨或锉等方法去除部分质量。
●3)在预制的平衡槽内改变平衡块的位置和 数量,加以平衡
●6)工件在定位时需要限制的自由度数目以及究 竟是哪几个自由度,完全由工件该工序的加工 要求所决定,应该根据实际情况进行具体分析, 合理设置定位支承点的数量和分布情况。
●7)定位支承点所限制的自由度,原则上不允许 重复或相互矛盾。
(二)完全定位与不完全定位
工件的6个自由度全部被限制而在夹具中占有完全 确定的唯一位置,称为完全定位。
在分析基准问题时,必须注意下列两点:
● 1)作为基准的点、ຫໍສະໝຸດ 、面在工件上不一定具体存在,而 由某些具体的表面来体现,这些表面称为基面。例如,内 孔的中心线是通过内孔表面来体现的,内孔中心线是基准, 内孔表面是基面。因此,选择基准的问题就是选择恰当的 基面的问题。特别地,有时为了叙述方便,可以将基准和 基面统称为基准。
没有全部限制工件的6个自由度,但也能满足加工 要求的定位,称为不完全定位。
图1-6
图1-7
(三)欠定位与过定位
根据加工的要求,工件必须限制的自由度没有达到 全部限制的定位,称为欠定位。
机械制造过程与工艺PPT课件

工艺规程的分类 ➢机械加工工艺过程卡 ➢机械加工工艺卡 ➢机械加工工序卡
工艺规程的作用
它是机械制造厂最主要的技术文件之一, 是生产一线的法规性文件。新工艺是衡 量生产部门技术力量的标志,是产品设 计和技术革新的内容之一
➢指导生产的主要技术文件
➢组织和管理生产的基本依据
➢新建和扩建工厂的基本资料
划分加工阶段的原因
保证加工质量(粗加工切削力、切削热、夹紧力、 变形都大,不可能达到高精度); 合理利用机床设备; 合理安排热处理和检验工序; 及时发现毛坯缺陷,及时修补或报废; 精加工应放在最后,避免损伤已加工表面。
加工顺序的安排
复杂工件的机械加工工艺路线通常要 经过切削加工、热处理和辅助工序。
件、协作关系、工艺装备、工人技术状态 等) ➢工厂的发展前景 ➢国内外的生产技术发展状态等
制订工艺规程的步骤(十大步骤) ➢ 分析零件图和产品装配图; ➢ 选择毛坯; ➢ 拟定工艺路线; ➢ 选择定位基准; ➢ 确定各工序的设备、工装确定各工序的加工余量,计
算工序尺寸和公差; ➢ 确定各主要工序的技术要求及检验方法; ➢ 确定切削用量和工时定额; ➢ 进行经济分析,选择最佳方案; ➢ 填写工艺文件
定位基准的确定
工件加工前,在机床上或夹具中占据某一正确位置的过 程称为定位。
为了使定位的工件在切削力的作用下不发生偏移,还需 将工件压紧夹牢,这个过程称为夹紧。 定位和夹紧过程的总和称为装夹。
工件的装夹方式
划线找正法 直接找正法 夹具找正法
划线找正法
直接找正法
基准的概念
基准-用来确定生产对象上几何要素间的几 何关系所依据的那些点、线、面。
一、生产过程与工艺过程
生产过程的概念
机械产品制造时,将原材料转变为产品的所有劳动过 程 对于机器的制造而言,生产过程包括: ➢ 生产技术准备过程 ➢ 毛坯的制造过程 ➢ 零件的机械加工、热处理和其他表面处理 ➢ 产品的装配、调试、检验和油漆 ➢ 原材料和成品的运输与保管
工艺规程的作用
它是机械制造厂最主要的技术文件之一, 是生产一线的法规性文件。新工艺是衡 量生产部门技术力量的标志,是产品设 计和技术革新的内容之一
➢指导生产的主要技术文件
➢组织和管理生产的基本依据
➢新建和扩建工厂的基本资料
划分加工阶段的原因
保证加工质量(粗加工切削力、切削热、夹紧力、 变形都大,不可能达到高精度); 合理利用机床设备; 合理安排热处理和检验工序; 及时发现毛坯缺陷,及时修补或报废; 精加工应放在最后,避免损伤已加工表面。
加工顺序的安排
复杂工件的机械加工工艺路线通常要 经过切削加工、热处理和辅助工序。
件、协作关系、工艺装备、工人技术状态 等) ➢工厂的发展前景 ➢国内外的生产技术发展状态等
制订工艺规程的步骤(十大步骤) ➢ 分析零件图和产品装配图; ➢ 选择毛坯; ➢ 拟定工艺路线; ➢ 选择定位基准; ➢ 确定各工序的设备、工装确定各工序的加工余量,计
算工序尺寸和公差; ➢ 确定各主要工序的技术要求及检验方法; ➢ 确定切削用量和工时定额; ➢ 进行经济分析,选择最佳方案; ➢ 填写工艺文件
定位基准的确定
工件加工前,在机床上或夹具中占据某一正确位置的过 程称为定位。
为了使定位的工件在切削力的作用下不发生偏移,还需 将工件压紧夹牢,这个过程称为夹紧。 定位和夹紧过程的总和称为装夹。
工件的装夹方式
划线找正法 直接找正法 夹具找正法
划线找正法
直接找正法
基准的概念
基准-用来确定生产对象上几何要素间的几 何关系所依据的那些点、线、面。
一、生产过程与工艺过程
生产过程的概念
机械产品制造时,将原材料转变为产品的所有劳动过 程 对于机器的制造而言,生产过程包括: ➢ 生产技术准备过程 ➢ 毛坯的制造过程 ➢ 零件的机械加工、热处理和其他表面处理 ➢ 产品的装配、调试、检验和油漆 ➢ 原材料和成品的运输与保管
第1章机械制造工艺基础.ppt

1.3 生产纲领与生产类型
1.3.1 生产纲领
1. 生产纲领
生产纲领是指企业在计划期内应当生产的产品产
量和进度计划。因计划期常常定为1年,所以也称为年
产量。
年度生产计划也称作年生产纲领。
零件的生产纲领要记入备品和废品的数量 :
N=Qk(1+i1)(1+i2)
1.3 生产纲领与生产类型
2. 生产类型
机械加工工艺过程组成见图1-2。
1.2 工艺过程及其组成
1.2 工艺过程及其组成
1.2.1 工序 1. 工序及其划分
工序是一个(或一组)工人,在一个工作地对同 一个(或同时对几个)工件进行加工所连续完成的那 部分工艺过程 。工序是组成工艺过程的基本单元,也是生产计 划的基本单元。
特点:“三同”和“一个连续”。
1.2 工艺过程及其组成 复合工步举例
1.2 工艺过程及其组成
2.工作行程(走刀) 工作行程,也称走刀,它是切削工具以加工进
给速度,相对工件所完成一次进给运动的工步部分。 当工件表面的加工余量较大,不可能一次工作行程
就能完成,这时就要分几次工作行程(走刀)。工 作行程的次数也称行程次数。
刀具以非加工进给速度相对工件所完成一次进 给运动的工步部分,称作“空行程”。空行程能检 查刀具相对工件的运动轨迹。
是产品除外购件以外的全部零(部)件,在 由毛坯准备到成品包装入库的生产过程中,所经 过的各有关部门(科室、车间、工段、小组或工 种)或工序的先后顺序。
1.2 工艺过程及其组成
工艺过程: 工艺过程就是指改变生产对象的形状、尺寸、相对位置
和性质等,使其成为成品或半成品的过程。 机械加工工艺过程:
机械加工工艺过程是指利用机械加工的方法,直接改变 毛坯的形状、尺寸和表面质量,使其成为成品或半成品的过 程。
机械制造工程学PPT课件3.9磨削

一、砂轮特性及其选择
1. 砂轮 是用结合剂把磨粒粘结起来,经压坯、干燥、焙烧及车整而成。
磨粒---主要起切削作用 气孔---主要起容屑和冷却作用 结合剂---主要起粘接作用
2. 砂轮的特性
砂轮的特性主要由磨料、粒度、结合剂、硬度和组 织等五因素所决定。
1)砂轮的磨料
取决于工件材料的硬度
氧化物
棕刚玉 白刚玉 络刚玉
vc do no m / s 1000
2. 工件的切向进给运动
VW m / s 或m/min
3. 工件轴向进给运动
fa mm/ r 或 mm/st
4. 径向进给量
fr mm
三、磨削过程
1.砂轮工作表面的形貌特征
1)磨粒在砂轮工作表面上是 随机分布的; 2)每一颗磨粒的形状和大小 都是不规则的。
❖ 2.影响磨削温度的因素 ❖ (1)砂轮速度
提高砂轮速度,单位时间通过工件表面的磨粒数增多, 单颗磨粒切削厚度减小,挤压和摩擦作用加剧,单位时 间内产生的热量增加,使磨削温度升高。 ❖ (2)工件速度
增大工件速度,单位时间内进入磨削区的工件材料增 加,单颗磨粒的切削厚度加大,磨削力及能耗增加,磨 削温度上升;
1.砂轮工作表面的形貌特征
2. 磨屑的形成过程 1)单颗磨粒的切削过程 滑擦—耕犁—切削
2)磨削速度与隆起量的关系
3与切削力相比,磨削力有如下主要特征;
❖ 1)单位磨削力值大,原因是磨粒大多以较大的负 前角进行切削。单位磨削力在70KN/mm2以上, 而其他切削加工的值均在7KN/mm2以下。
❖ 6)砂轮形状
3. 砂轮的型号、代号、标记和尺寸
形状—尺寸—磨料—粒度号—硬度—组织号—结合 剂—最高线速度
形状
1. 砂轮 是用结合剂把磨粒粘结起来,经压坯、干燥、焙烧及车整而成。
磨粒---主要起切削作用 气孔---主要起容屑和冷却作用 结合剂---主要起粘接作用
2. 砂轮的特性
砂轮的特性主要由磨料、粒度、结合剂、硬度和组 织等五因素所决定。
1)砂轮的磨料
取决于工件材料的硬度
氧化物
棕刚玉 白刚玉 络刚玉
vc do no m / s 1000
2. 工件的切向进给运动
VW m / s 或m/min
3. 工件轴向进给运动
fa mm/ r 或 mm/st
4. 径向进给量
fr mm
三、磨削过程
1.砂轮工作表面的形貌特征
1)磨粒在砂轮工作表面上是 随机分布的; 2)每一颗磨粒的形状和大小 都是不规则的。
❖ 2.影响磨削温度的因素 ❖ (1)砂轮速度
提高砂轮速度,单位时间通过工件表面的磨粒数增多, 单颗磨粒切削厚度减小,挤压和摩擦作用加剧,单位时 间内产生的热量增加,使磨削温度升高。 ❖ (2)工件速度
增大工件速度,单位时间内进入磨削区的工件材料增 加,单颗磨粒的切削厚度加大,磨削力及能耗增加,磨 削温度上升;
1.砂轮工作表面的形貌特征
2. 磨屑的形成过程 1)单颗磨粒的切削过程 滑擦—耕犁—切削
2)磨削速度与隆起量的关系
3与切削力相比,磨削力有如下主要特征;
❖ 1)单位磨削力值大,原因是磨粒大多以较大的负 前角进行切削。单位磨削力在70KN/mm2以上, 而其他切削加工的值均在7KN/mm2以下。
❖ 6)砂轮形状
3. 砂轮的型号、代号、标记和尺寸
形状—尺寸—磨料—粒度号—硬度—组织号—结合 剂—最高线速度
形状
机械制造技术ppt课件(完整版)
单击此处添加副标题
机械制造技术课件
汇报人:
目录
01 02 03 04 05 06
机械制造概述 传统机械制造技术 现代机械制造技术 机械制造工艺流程 机械制造质量控制 机械制造的未来发展
01
机械制造概述
机械制造的定义
机械制造是将原材料转化为成品的生产过程。 机械制造包括产品设计、工艺设计、加工制造、检测和质量控制等环节。 机械制造广泛应用于各个领域,如航空、汽车、机床等。 机械制造的核心目标是提高生产效率、降低成本、保证产品质量。
05
机械制造质量控制
质量控制的方法
统计过程控制 测量系统分析 过程能力分析 质量改进方法
质量检测的步骤
检测计划制定 检测工具准备 样品选择与制备 检测数据记录与分析
质量问题的解决
确定问题:明确机械制造过程中出现的质量问题
分析原因:分析问题产生的原因,如材料、工艺、设备等
制定措施:根据分析,制定相应的解决措施,如改进工艺、更换材料、 调整设备等 实施方案:按照制定的措施实施方案,并对实施过程进行监控和调 整
精密加工技术
定义:使用精密机床和精细加工刀具进行加工 分类:超精加工、镜面加工、纳米加工等 应用:航空航天、医疗器械、光学仪器等领域 发展趋势:高精度、高效率、智能化
04
机械制造工艺流程
零件的定位与装夹
定位原理:六点 定位原理,限制 工件的自由度
装夹方法:如三 爪卡盘、四爪卡 盘等,固定工件
定位元件:如V 形块、定位销等, 限制工件的自由 度
焊接工艺及 设备
焊接种类及 特点
焊接应用及 发展
切削加工技术
定义:利用切削 工具从工件上切 除多余材料的加 工方法
分类:车削、铣 削、钻孔、刨削、 磨削等
机械制造技术课件
汇报人:
目录
01 02 03 04 05 06
机械制造概述 传统机械制造技术 现代机械制造技术 机械制造工艺流程 机械制造质量控制 机械制造的未来发展
01
机械制造概述
机械制造的定义
机械制造是将原材料转化为成品的生产过程。 机械制造包括产品设计、工艺设计、加工制造、检测和质量控制等环节。 机械制造广泛应用于各个领域,如航空、汽车、机床等。 机械制造的核心目标是提高生产效率、降低成本、保证产品质量。
05
机械制造质量控制
质量控制的方法
统计过程控制 测量系统分析 过程能力分析 质量改进方法
质量检测的步骤
检测计划制定 检测工具准备 样品选择与制备 检测数据记录与分析
质量问题的解决
确定问题:明确机械制造过程中出现的质量问题
分析原因:分析问题产生的原因,如材料、工艺、设备等
制定措施:根据分析,制定相应的解决措施,如改进工艺、更换材料、 调整设备等 实施方案:按照制定的措施实施方案,并对实施过程进行监控和调 整
精密加工技术
定义:使用精密机床和精细加工刀具进行加工 分类:超精加工、镜面加工、纳米加工等 应用:航空航天、医疗器械、光学仪器等领域 发展趋势:高精度、高效率、智能化
04
机械制造工艺流程
零件的定位与装夹
定位原理:六点 定位原理,限制 工件的自由度
装夹方法:如三 爪卡盘、四爪卡 盘等,固定工件
定位元件:如V 形块、定位销等, 限制工件的自由 度
焊接工艺及 设备
焊接种类及 特点
焊接应用及 发展
切削加工技术
定义:利用切削 工具从工件上切 除多余材料的加 工方法
分类:车削、铣 削、钻孔、刨削、 磨削等
机械制造工艺学课件第7章 精密、超精密及微细加工工艺
5
第7章 精密、超精密及微细加工工艺
➢ 精密、超精密磨削和磨料加工
超精密磨削和磨料加工是利用细粒度的磨粒和微 粉主要对黑色金属、硬脆材料等进行加工,可分为固 结磨料和游离磨料两大类加工方式。
固结磨料加工主要有:超精密砂轮磨削和超硬材 料微粉砂轮磨削、超精密砂带磨削、ELID 磨削、双 端面精密磨削以及电泳磨削等。
第7章 精密、超精密及微细加工工艺
第7章 精密、超精密及微细加工工艺
7.1 概述
现代制造业持续不断地致力于提高加工精度和加
工表面质量,主要目标是提高产品性能、质量和可靠性
,改善零件的互换性,提高装配效率。超精密加工技术
是精加工的重要手段,在提高机电产品的性能、质量和
发展高新技术方面都有着至关重要的作用,因此,该技
第7章 精密、超精密及微细加工工艺
游离磨料类加工是指在加工时磨粒或微粉成游离状态,如研磨时的研磨 剂、抛光时的抛光液,其中的磨粒或微粉在加工时不是固结在一起的。 游离磨料加工的典型方法是超精密研磨与抛光加工。
① 超精密研磨技术
研磨是在被加工表面和研具之间置以游离磨料和润滑液,使被加工表面
和研具产生相对运动并加压,磨料产生切削、挤压作用,从而去除表面
7
第7章 精密、超精密及微细加工工艺
② 超精密砂带磨削技术 随着砂带制作质量的迅速提高,砂带上砂粒的等高性和 微刃性较好,并采用带有一定弹性的接触轮材料,使砂 带磨削具有磨削、研磨和抛光的多重作用,从而可以达 到高精度和低表面粗糙度值。
砂带磨削机构示意图
8
第7章 精密、超精密及微细加工工艺
③ ELID(电解在线修整)超精密镜面磨削技术
术是衡量一个国家先进制造技术水平的重要指标之一,
第7章 精密、超精密及微细加工工艺
➢ 精密、超精密磨削和磨料加工
超精密磨削和磨料加工是利用细粒度的磨粒和微 粉主要对黑色金属、硬脆材料等进行加工,可分为固 结磨料和游离磨料两大类加工方式。
固结磨料加工主要有:超精密砂轮磨削和超硬材 料微粉砂轮磨削、超精密砂带磨削、ELID 磨削、双 端面精密磨削以及电泳磨削等。
第7章 精密、超精密及微细加工工艺
第7章 精密、超精密及微细加工工艺
7.1 概述
现代制造业持续不断地致力于提高加工精度和加
工表面质量,主要目标是提高产品性能、质量和可靠性
,改善零件的互换性,提高装配效率。超精密加工技术
是精加工的重要手段,在提高机电产品的性能、质量和
发展高新技术方面都有着至关重要的作用,因此,该技
第7章 精密、超精密及微细加工工艺
游离磨料类加工是指在加工时磨粒或微粉成游离状态,如研磨时的研磨 剂、抛光时的抛光液,其中的磨粒或微粉在加工时不是固结在一起的。 游离磨料加工的典型方法是超精密研磨与抛光加工。
① 超精密研磨技术
研磨是在被加工表面和研具之间置以游离磨料和润滑液,使被加工表面
和研具产生相对运动并加压,磨料产生切削、挤压作用,从而去除表面
7
第7章 精密、超精密及微细加工工艺
② 超精密砂带磨削技术 随着砂带制作质量的迅速提高,砂带上砂粒的等高性和 微刃性较好,并采用带有一定弹性的接触轮材料,使砂 带磨削具有磨削、研磨和抛光的多重作用,从而可以达 到高精度和低表面粗糙度值。
砂带磨削机构示意图
8
第7章 精密、超精密及微细加工工艺
③ ELID(电解在线修整)超精密镜面磨削技术
术是衡量一个国家先进制造技术水平的重要指标之一,
典型零件加工工艺过程PPT课件
.
22
CA6140. 车床主轴图
23
主轴的机械加工工艺过程
➢主轴加工工艺过程制订的依据 主轴的结构;技术要求;生产批量;
设备条件 ➢主轴加工工艺过程 批量:大批;材料:45钢;毛坯:模
锻件
.
24
➢工艺过程: 分为三个阶段(参见表5-5):
粗加工:工序 1~6 半精加工:工序 7~13(7为预备) 精加工:工序 14~26(14为预备)
.
63
箱孔与孔的位置精度 引起轴安装歪斜,致使主轴径向跳动 和轴向窜动,加剧轴承磨损 同一轴线上各孔的同轴度误差 孔端面对轴线垂直度误差
.
64
孔和平面的位置精度
主要是规定主要孔和主轴箱安装基 面的平行度
主要平面的精度
影响主轴箱与床身的连接刚度
规定底面和导向面必须平直和相互 垂直
平面度、垂直度公差等级为5级
第二节
典型零件加工 工艺过程
机械制造工程——第五章
.
1
一、轴(杆)类零件的加工
1.轴类零件的分类、技术要求
➢轴类零件的作用 支撑传动零件; 承受载荷; 传递扭矩。
.
2
➢轴类零件的特点 长度大于直径; 加工表面为内外圆柱面、圆锥面、
螺纹、花键、沟轴 阶梯轴 空心轴 异形轴(曲轴、齿轮轴、偏心轴、
.
38
➢加工顺序的安排和工序的确定
三种方案
粗加工外圆→钻深孔→精加工外圆→ 粗加工锥孔→精加工锥孔
粗加工外圆→钻深孔→粗加工锥孔→ 精加工锥孔→精加工外圆
粗加工外圆→钻深孔→粗加工锥孔→ 精加工外圆→精加工锥孔
.
39
工序确定的两个原则
➢工序中所用的基准应在该工序前加工
《机械制造技术》全册优质PPT教学课件
机械制造系统是生产系统中的一个重要组成部分, 完成由原材料变为产品的整个生产过程。按生产流程 的职能和流向,机械制造系统中存在着物质流、信息 流和能量流三类流动,如下图所示。
其中,物质流用于改变物料的形态和地点;信息 流用于规划、指挥、协调和控制物料的流动,使机械
制造系统有效地 运行;能量流为 生产活动提供能 量,保证生产活 动正常进行。
项目一 机械制造技术导论
项目学习要点
• 机械产品生产的相关知识 • 机械产品制造的相关知识 • 关于机械制造技术 • 综合实训 • 项目小结
任务一 机械产品生产的相关知识
机械产品是指机械厂家向用户或市场所提供的 成品或附件,如汽车、发动机、机床等。任何机械 产品按传统习惯都可以看作由若干部件组成,而部 件又可分为组件、套件,直至最基本的零件单元。
通过对本课程的学习,要求: 1.掌握金属切削的基础知识和规律,初步具备根 据具体情况合理选择加工方法的能力。 2.了解常用工艺装备(主要指通用机床、刀具和 夹具),并具备初步设计能力(主要指夹具设计)。 3.了解影响加工质量的各种因素,能对金属切削 加工中出现的常见质量问题进行分析解决。 4.以制造工艺为主线,要求掌握机械加工工艺过 程和装配工艺过程的基本原理和基本知识,具备设计 机械加工工艺规程的能力。
0.4 机械制造技术的发展
21世纪制造业的发展方向和趋势有以下几个方面。
1.柔性化 2.高精度化 3.全球化 4.虚拟化 5.绿色化
0.5 本课程的特点及学习要求
本课程将传统的机械类课程《金属切削原理与 刀具》、《金属切削机床》、《机床夹具设计》和 《机械制造工艺学》进行了有机地整合,紧紧围绕 机械制造技术进行介绍。
3.检验
检验是指采用测量器具对毛坏、零件、成品等 进行尺寸精度、形状精度、位置精度的检测,以及 通过目视检验、无损探伤、机械性能试验及金相检 验等方法对产品质量进行的鉴定。