Toyota lean production system
丰田生产模式流程
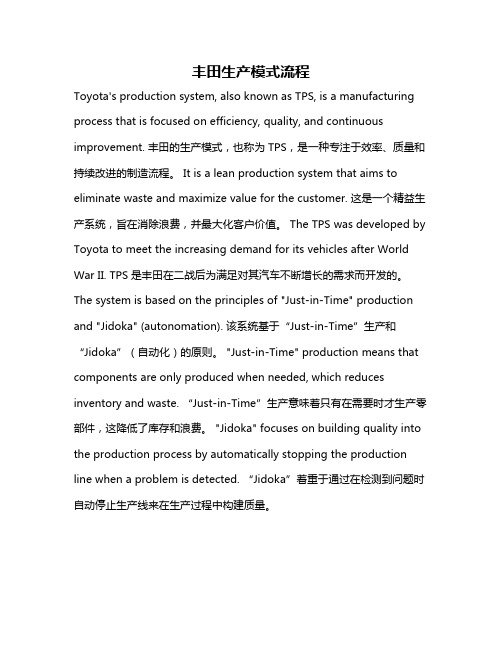
丰田生产模式流程Toyota's production system, also known as TPS, is a manufacturing process that is focused on efficiency, quality, and continuous improvement. 丰田的生产模式,也称为TPS,是一种专注于效率、质量和持续改进的制造流程。
It is a lean production system that aims to eliminate waste and maximize value for the customer. 这是一个精益生产系统,旨在消除浪费,并最大化客户价值。
The TPS was developed by Toyota to meet the increasing demand for its vehicles after World War II. TPS是丰田在二战后为满足对其汽车不断增长的需求而开发的。
The system is based on the principles of "Just-in-Time" production and "Jidoka" (autonomation). 该系统基于“Just-in-Time”生产和“Jidoka”(自动化)的原则。
"Just-in-Time" production means that components are only produced when needed, which reduces inventory and waste. “Just-in-Time”生产意味着只有在需要时才生产零部件,这降低了库存和浪费。
"Jidoka" focuses on building quality into the production process by automatically stopping the production line when a problem is detected. “Jidoka”着重于通过在检测到问题时自动停止生产线来在生产过程中构建质量。
精益生产管理专有名词说明

9
精益生产
10
OEE
11
JIT
准时化(JIT-Just in time)生产。即以市场为龙头在合适的时间、生产合适的数量和高质量的产品,JIT需要以拉动生产 为基础,以平准化(Leveling System)为条件。所谓拉动生产是以看板管理为手段,采用“取料制”即后道工序根据“市 场”需要进行生产,对本工序在制品短缺的量从前道工序取相同的在制品量,从而形成全过程的拉动控制系统,绝不多生 产一件产品。 自働化是指自律地控制不正常的情况和具有人的判断力的自动化, 也就是发现异常或缺陷的装置和出现这些异常或缺陷时能够使生产线或者设备停下来的装置。 它包含了发现不合格零部件就不让该零件通过生产线的机构,因此能够达到以下效果: 因为有了自働化就无须人员去监控异常情况这样一来可以削减作业人员,从而达到降低成本的目的。 由于有生产完所需要的零部件设备就能停下来,而且生产的零部件又都是合格品,因此可以减少库存量,从而可以实现生 产同步化。 该自働化要求对设备及环境持续改善,刺激了员工的能动性,因而增强了对人格的尊重。 看板管理:又成为视板管理、看板方式、看板法等,是20世纪50年代由日本丰田汽车公司创立的一种先进的生产现场管理 方法或生产控制技术,是目视管理的重要工具。 平准化是指工件的被拉动到生产系统之前要进行人为的按照加工时间、数量、品种进行合理的搭配和排序,使拉动到生产 系统中的工件流具有加工工时上的平稳性,保证均衡生产,同时在品种和数量上实现混流加式运动,起到对市场多品种、 小批量需要的快速反应和满足功能。
15
标准作业
16 17
时间观测 工程别能力表
18
标准作业组合票
19 20 21
标准作业票 山积表 标准手持数
22
丰田生产方式的诞生背景
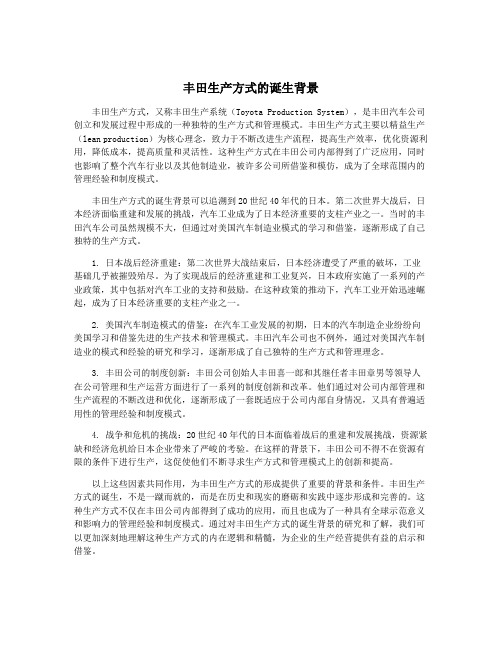
丰田生产方式的诞生背景丰田生产方式,又称丰田生产系统(Toyota Production System),是丰田汽车公司创立和发展过程中形成的一种独特的生产方式和管理模式。
丰田生产方式主要以精益生产(lean production)为核心理念,致力于不断改进生产流程,提高生产效率,优化资源利用,降低成本,提高质量和灵活性。
这种生产方式在丰田公司内部得到了广泛应用,同时也影响了整个汽车行业以及其他制造业,被许多公司所借鉴和模仿,成为了全球范围内的管理经验和制度模式。
丰田生产方式的诞生背景可以追溯到20世纪40年代的日本。
第二次世界大战后,日本经济面临重建和发展的挑战,汽车工业成为了日本经济重要的支柱产业之一。
当时的丰田汽车公司虽然规模不大,但通过对美国汽车制造业模式的学习和借鉴,逐渐形成了自己独特的生产方式。
1. 日本战后经济重建:第二次世界大战结束后,日本经济遭受了严重的破坏,工业基础几乎被摧毁殆尽。
为了实现战后的经济重建和工业复兴,日本政府实施了一系列的产业政策,其中包括对汽车工业的支持和鼓励。
在这种政策的推动下,汽车工业开始迅速崛起,成为了日本经济重要的支柱产业之一。
2. 美国汽车制造模式的借鉴:在汽车工业发展的初期,日本的汽车制造企业纷纷向美国学习和借鉴先进的生产技术和管理模式。
丰田汽车公司也不例外,通过对美国汽车制造业的模式和经验的研究和学习,逐渐形成了自己独特的生产方式和管理理念。
3. 丰田公司的制度创新:丰田公司创始人丰田喜一郎和其继任者丰田章男等领导人在公司管理和生产运营方面进行了一系列的制度创新和改革。
他们通过对公司内部管理和生产流程的不断改进和优化,逐渐形成了一套既适应于公司内部自身情况,又具有普遍适用性的管理经验和制度模式。
4. 战争和危机的挑战:20世纪40年代的日本面临着战后的重建和发展挑战,资源紧缺和经济危机给日本企业带来了严峻的考验。
在这样的背景下,丰田公司不得不在资源有限的条件下进行生产,这促使他们不断寻求生产方式和管理模式上的创新和提高。
丰田JIT

全球的丰田式生产管理系统均致力于制造完美的产品,同时节省时间、付出的心力及原料。这也是TOYOTA为 何能使顾客满意,并保持竞争力,赢得世界各地消费者赞赏的原因。
许多年以来,丰田式生产管理借着加入许多新想法、模式并一再创新、测试而得到强化。举例来说『及时化生产』(Just in Time)、『自动』及『不间断的流程』等,都已经建立在丰田式生产管理中。
5回答者: xytgirl77
自动化如何能省人力呢?如上所述,设备及生产线会自律判断而停止,而且会更明确的将人与机器的工作做彻底分离,所以就可以节省相当的人力。当然,自动化必须配合标准化流程及下一个单元所说的『及时化生产』(Just in Time),才能彻底发挥其效能及目的。
★ 及时化
所谓及时化就是:必要的东西在必要的时间只生产必要的数量。说起来好象很文言文,其实就是当组装需要用到A零件时,A零件才送达组装地。如此一来,就不会产生库存的情形。
★ 少人化
少人化是因应产品生产量的变化,而对各制程作业人数弹性调整;简单来说,就是在整个制造流程中,因生产量的不同而调整工作人数。
1. 适当的机器设备配置
2. 多种工作能力且受过良好训练的作业员
3. 标准作业流程不断评估及修正
举例来说,U型的机器配置是比一直线的配置好的多,其原因为,当产能需要大增时,U型的机器配置可以一个人负责一边;当产能大减时,一个人就可以很快及很有弹性的负责两边(图丰田式生产体系168),如此可以省去一直线配置人员所需移动的时间及成本(在产能需大减的情况下) 。
自动化的目的有两个:一是无缺点制造;另一个目的是省人工。怎么能做到这两个目的呢?当发现不良品时,机器会自动停止,此时全生产线也跟着就同时停止,停止的目的在保障没有一个不良品会进入下一个流程。在此同时,安全系统就发挥了功能。
精选丰田生产方式简介及JIT准时生产制

该报告的结论性意见是:
全球性的竞争使得市场变化太快,单个企业依靠自己的资源进行自我调整的速度赶不上市场变化的速度。为了解决这个影响企业生存和发展的世界性问题,报告提出了以虚拟企业(Virtual Enterprise)或动态联盟为基础的敏捷制造模式。敏捷制造是一次战略高度的变革。敏捷制造面对的是全球化激烈竞争的买方市场,采用可以快速重构的生产单元构成的扁平组织结构,以充分自治的、分布式的协同工作代替金字塔式的多层管理结构。注重发挥人的创造性,变企业之间你死我活的竞争关系为既有竞争又有合作的“共赢”(Win-win)关系。敏捷制造强调基于互联网的信息开放、共享和集成。
10.2 JIT的实质-2
JIT的实质:在需要的时候,按需要的量,生产所需要的产品(零件)。JIT的是一种理想的生产方式
10.3 看板控制系统
(1)看板的含义 所谓看板,也有人把它称为卡片,但实际上看板的形式并不局限于记载有各种信息的某种卡片形式。看板的本质是在需要的时间、按需要的量对所需零部件发出生产指令的一种信息媒介体,而实现这一功能的形式是可以多种多样的。例如在丰田的工厂中,小圆球、圆轮、台车等均被利用来作为看板。近年来随着计算机的普及程度提高,已经越来越多地引入了在各工序设置计算机终端,在计算机屏幕上显示看板信息的做法。
敏捷制造企业的特征
3)根据用户反应建立组织机构。类似于精细生产中“牵引”(Pull)方式,完全按下游的需要来组织上游的生产活动。从对用户需求及市场竞争做出迅速反应出发,“牵引”出对新的企业组织各方面的要求,根据需求促进新的组织机构的变化。4)多方动态合作。从竞争走向合作,共同抓市场机遇,将是未来制造业的一个重要特征。这种合作关系可以发生在不同层次上,有不同的紧密程度。因为低层的工作人员也都已被授权,在他本人权力范围内通过各种标准过程进入各种合作,只要这样做对满足顾客需求有利就行。
精益生产系统

精益生产系统简介精益生产系统(Lean Production System)是一种以精益思维为基础的生产管理方法。
它起源于日本汽车制造业,由丰田汽车公司的丰田生产方式(Toyota Production System)发展而来。
精益生产系统的目标是通过消除浪费和提高价值流程,实现生产效率的最大化。
核心原则精益生产系统的核心原则包括以下几个方面:价值流观测精益生产系统强调对价值流的观测和理解。
价值流是指产品或服务在整个生产过程中所经过的各个环节。
通过对价值流的观测,可以识别出产生浪费的环节,并制定相应的改进措施。
流程优化精益生产系统鼓励对生产流程进行优化。
优化生产流程可以减少各种类型的浪费,提高生产效率。
流程优化的方法包括实施标准化工作和使用质量管理工具。
持续改进精益生产系统强调持续改进。
持续改进是指通过不断地寻找和消除潜在问题,逐步完善生产过程。
持续改进的方法包括设立改善目标、进行持续的教育和培训、推行团队合作等。
人员参与精益生产系统鼓励人员的参与和贡献。
在精益生产系统中,每个员工都被视为一个问题解决者,并被鼓励积极参与持续改进过程。
实施步骤实施精益生产系统可以按照以下步骤进行:1. 识别价值流程首先,需要对整个生产过程进行价值流分析。
通过观测和分析生产过程中的各个环节,确定价值流程,找出其中的浪费环节。
2. 消除浪费根据浪费环节的识别结果,制定相应的改进措施,并逐步消除浪费。
常见的浪费包括过度生产、等待时间、不必要的运输等。
3. 设立改善目标设立明确的改善目标是实施精益生产系统的关键。
通过设立目标,可以激励员工积极参与持续改进,并监督改进的进展。
4. 推行标准化工作标准化工作是精益生产系统的重要组成部分。
通过制定和推行标准化工作,可以确保工作流程的一致性,并提高工作质量。
5. 实施质量管理工具在实施精益生产系统的过程中,可以借鉴一些质量管理工具,如PDCA循环(Plan-Do-Check-Act)和5W1H方法(What-When-Where-Who-Why-How)等,以帮助分析和解决问题。
精益生产

精益生产精益生产(Lean Production)是一种以减少浪费为核心的生产管理模式,旨在提高生产效率、降低成本、增加价值。
它源自于日本的丰田生产方式(Toyota Production System),并逐渐被许多企业所采用。
精益生产强调通过消除非必要的活动和浪费来优化生产过程,从而实现高质量、高效率、高附加值的产出。
精益生产的理念可以追溯到二战后日本的产业重建阶段。
日本的产业很快崛起,成为世界上最富竞争力的制造业国家之一。
在这个过程中,丰田汽车公司发展出了一套高效的生产方式,即丰田生产方式。
丰田生产方式的核心是精益生产理念,通过不断改进和创新来提高生产效率和质量。
精益生产模式的核心原则是以价值为导向,消除浪费。
在传统的生产管理中,浪费是普遍存在的,如过度生产、库存过多、运输过程中的等待时间、不必要的加工等。
这些浪费不仅会增加成本,还会降低产品的质量和生产效率。
精益生产通过持续改进和优化生产流程,减少无价值的工作,并将集中精力用于为顾客提供真正需要的产品和服务。
精益生产的实践方法主要有五个原则,即价值、价值流、流程、拉动和持续改进。
首先,识别价值是精益生产的基础,企业应该以顾客需求为导向,清楚地定义产品或服务的价值。
其次,通过分析和绘制价值流,可以识别出生产过程中的瓶颈和浪费,并采取措施来消除它们。
接下来,通过改进和优化生产流程,实现连续流动的生产,减少等待和停顿,提高生产效率。
同时,精益生产强调拉动生产方式,即按需生产,避免过度生产和库存积压。
最后,精益生产是一个不断改进的过程,通过提高员工的参与度和意识,进行问题解决和创新,实现持续改进。
精益生产所带来的好处是显而易见的。
首先,它能够提高生产效率和产品质量。
通过消除浪费和优化生产流程,企业可以更快地生产出高质量的产品,满足顾客的需求。
其次,精益生产可以降低成本。
通过减少不必要的活动和浪费,企业可以降低生产成本,并通过提高产品质量和降低维修成本来提高利润率。
TPS丰田生产方式
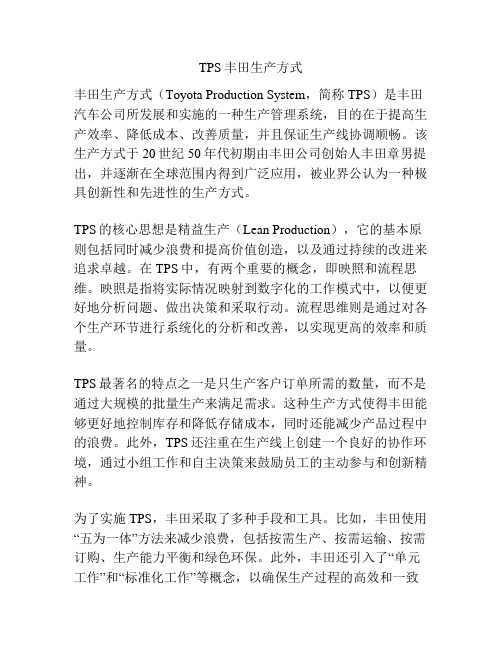
TPS丰田生产方式丰田生产方式(Toyota Production System,简称TPS)是丰田汽车公司所发展和实施的一种生产管理系统,目的在于提高生产效率、降低成本、改善质量,并且保证生产线协调顺畅。
该生产方式于20世纪50年代初期由丰田公司创始人丰田章男提出,并逐渐在全球范围内得到广泛应用,被业界公认为一种极具创新性和先进性的生产方式。
TPS的核心思想是精益生产(Lean Production),它的基本原则包括同时减少浪费和提高价值创造,以及通过持续的改进来追求卓越。
在TPS中,有两个重要的概念,即映照和流程思维。
映照是指将实际情况映射到数字化的工作模式中,以便更好地分析问题、做出决策和采取行动。
流程思维则是通过对各个生产环节进行系统化的分析和改善,以实现更高的效率和质量。
TPS最著名的特点之一是只生产客户订单所需的数量,而不是通过大规模的批量生产来满足需求。
这种生产方式使得丰田能够更好地控制库存和降低存储成本,同时还能减少产品过程中的浪费。
此外,TPS还注重在生产线上创建一个良好的协作环境,通过小组工作和自主决策来鼓励员工的主动参与和创新精神。
为了实施TPS,丰田采取了多种手段和工具。
比如,丰田使用“五为一体”方法来减少浪费,包括按需生产、按需运输、按需订购、生产能力平衡和绿色环保。
此外,丰田还引入了“单元工作”和“标准化工作”等概念,以确保生产过程的高效和一致性。
同时,丰田还重视员工的培训和发展,通过提供丰富的培训机会和激励政策来激发员工的潜力和创造力。
TPS的成功和影响不仅体现在丰田公司自身,还对全球汽车制造行业产生了广泛的影响。
丰田的成功案例激发了其他企业对精益生产的兴趣和探索,并在过去几十年中推动了许多企业对生产方式的改革和创新。
TPS的核心原则和思维方式成为了许多生产管理理论和实践的基础,为企业管理者提供了宝贵的借鉴和启示。
总体而言,TPS是基于精益生产原则的一种高效生产方式,通过精细的流程思维和持续的改进来追求极致的效率和质量,并且注重员工的参与和创新。
- 1、下载文档前请自行甄别文档内容的完整性,平台不提供额外的编辑、内容补充、找答案等附加服务。
- 2、"仅部分预览"的文档,不可在线预览部分如存在完整性等问题,可反馈申请退款(可完整预览的文档不适用该条件!)。
- 3、如文档侵犯您的权益,请联系客服反馈,我们会尽快为您处理(人工客服工作时间:9:00-18:30)。
Carl Benze First Motorcyle
Toyota Production System
Carl Benze
Gotlib Daimler
Toyota Production System
Carl Benze
Gotlib Daimler
Carl Benze “Vilo” Model of 1894
Toyota Production System
A Brief History of Car Manufacturing
Invention of Automobile in 1880 The Henry Ford Mass Production System The Toyota or Lean Production System
Shigeo Shingo
Toyota Production System
Ford vs. Toyota model of Production System
Can be best explained as: Mass Production vs. Lean (JIT) Production
Toyota Production System
Toyoda family were among those Japanese industrialists who were observing American industrial strength and wanted to emulate it by investing in Automotive Industry.
Ford was so incredibly successful he quickly became
one of the world's richest men and put the world on wheels.
Ford Motor Company produced “A-Bomber an Hour”
Toyota Production System
Invention of Automobile
Carl Benz is generally given credit to
develop world first automobile in 1985
Gotlib Daimler is also contemporary of
Toyoda Automatic Loom Company, under the encouragement of the Japanese government, which needed domestic vehicle production partly due to the worldwide money shortage and partly due to the war with China The Toyota Motor Corporation was founded in September 1933 when Toyoda Automatic Loom created a new division devoted to the production of automobiles under the direction of the founder's son, Kiichiro Toyoda.
production system was based on Mass Production System.
Post WWII Japanese economy was in shambles and Toyota could
not afford Mass Production of vehicles due to smaller market size.
Just-in-Time (JIT) System
Just-in-Time means PRODUCING:
a) Only what is needed
b) in necessary quantity
c) at necessary time
Toyota Production System
Main Components of JIT
To make it worthwhile, mass production requires mass consumption. With precision equipment, large numbers of identical parts could be produced at low cost and with a small work force.
Gotlib Daimler
Toyota Production System
Carl Benze
Gotlib Daimler
Replica of the Benz Patent Motorwagen built in 1886
Toyota Production System
Carl Benze
Gotlib Daimler
• Andon-Fixed Position Stop
System
• Pokayoke- Fail Proofing
System
• Flexible Work Force
• 3 Ms • 5S
Standardized Work
Kaizen (Continuous Improvement)
Toyota Production System
Toyota Production System
What is Lean Production System? Lean Production System is the system designed and evolved in Toyota Motor Corporation. It is the modified form of Henry Fords Mass Production System. In some areas its philosophy seem exactly opposite to the fundamental principles of Mass Production System. This system is generally known as JIT system, which in fact is an important pillar of Lean Production System. The slogan of Lean Production is “Less is best”
He organized all the elements of a manufacturing
system-- people, machines, tooling, and products-and arranged them in a continuous system called conveyer system for manufacturing the Model-T automobile.
What is Mass Production System Mass production is the name given to the method of producing goods in large quantities at low cost per unit.
This system of production is also known as Push System or Just-in-Case System.
Taichii Ohno
Taichii Ohno was the Production Boss of Toyota Motor Corporation and Shigeo Shigo was industrial engineer and consultant of Toyota Motor Corporation.
Toyota’s top bosses begin to design a whole new concept of
Production System which is now also known as Just-in-Time system.
Toyota Production System
Toyota Production System
Henry Ford‟s Mass Production System
In 1910 Henry Ford laid the foundation of first highly
organized assembly line system of automobile manufacturing.
Carl Benze
Carl Benz who is simultaneously developed the automobile with him.
Other contemporaries are Wilhelm
Maybach and Seigfried Marcus known for developing automobile later during the same period.
Toyoda Family in Auto Industry
The Allied victory and the massive quantities of material behind it (“A Bomber an Hour” success) caught the attention of Japanese industrialists.
At Toyota Motor Company, Taichii Ohno and Shigeo Shingo, are known as the brain behind transforming Ford production and other techniques into an approach called Toyota Production System or Lean Production System or Just-in-Time System.