Hull%20Inspection%20and%20Maintenance%20Systems
化工企业设备异常情况处理流程

化工企业设备异常情况处理流程1.当设备出现异常情况时,首先需要停止设备运行并切断电源。
(When the equipment has abnormal conditions, first stop the operation of the equipment and cut off the power.)2.紧急情况下,立即通知相关负责人员和维修人员到场处理。
(In case of emergency, immediately notify relevant responsible personnel and maintenance personnel to handle on site.)3.对设备进行初步检查,找出异常原因并进行记录。
(Do a preliminary inspection of the equipment, find out the reasons for the abnormality, and make a record.)4.如果是设备故障导致的异常,需要及时向设备供应商报修。
(If the abnormality is caused by equipment failure, it is necessary to promptly report the repair to the equipment supplier.)5.在等待维修人员到达之前,做好相关记录和报告工作,包括设备运行情况、异常现象和初步处理情况。
(Before the arrival of the maintenance personnel, make relevant records and reports, including the equipmentoperation status, abnormal phenomena, and preliminary treatment.)6.维修人员到场后,配合并协助其进行设备故障排查和修复工作。
FAA-8083-30_Ch08
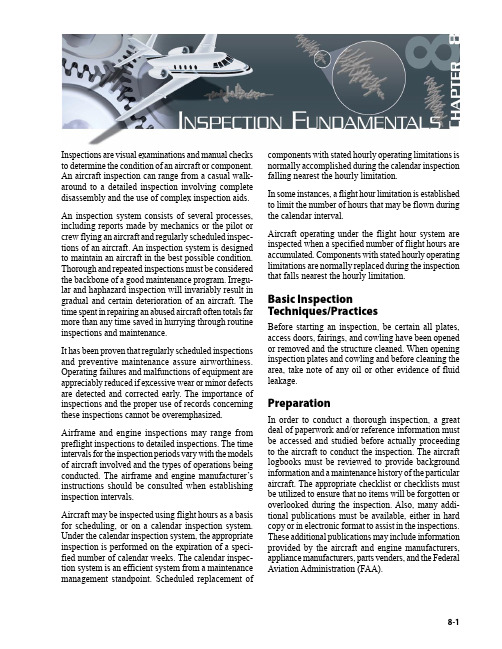
8-1components with stated hourly operating limitations is normally accomplished during the calendar inspection falling nearest the hourly limitation.In some instances, a flight hour limitation is established to limit the number of hours that may be flown during the calendar interval.Aircraft operating under the flight hour system are inspected when a specified number of flight hours are accumulated. Components with stated hourly operating limitations are normally replaced during the inspection that falls nearest the hourly limitation.Basic Inspection Techniques/PracticesBefore starting an inspection, be certain all plates, access doors, fairings, and cowling have been opened or removed and the structure cleaned. When opening inspection plates and cowling and before cleaning the area, take note of any oil or other evidence of fluid leakage.PreparationIn order to conduct a thorough inspection, a great deal of paperwork and/or reference information must be accessed and studied before actually proceeding to the aircraft to conduct the inspection. The aircraft logbooks must be reviewed to provide background information and a maintenance history of the particular aircraft. The appropriate checklist or checklists must be utilized to ensure that no items will be forgotten or overlooked during the inspection. Also, many addi-tional publications must be available, either in hard copy or in electronic format to assist in the inspections. These additional publications may include information provided by the aircraft and engine manufacturers, appliance manufacturers, parts venders, and the Federal Aviation Administration (FAA).Inspections are visual examinations and manual checks to determine the condition of an aircraft or component. An aircraft inspection can range from a casual walk-around to a detailed inspection involving complete disassembly and the use of complex inspection aids.An inspection system consists of several processes, including reports made by mechanics or the pilot or crew flying an aircraft and regularly scheduled inspec-tions of an aircraft. An inspection system is designed to maintain an aircraft in the best possible condition. Thorough and repeated inspections must be considered the backbone of a good maintenance program. Irregu-lar and haphazard inspection will invariably result in gradual and certain deterioration of an aircraft. The time spent in repairing an abused aircraft often totals far more than any time saved in hurrying through routine inspections and maintenance.It has been proven that regularly scheduled inspections and preventive maintenance assure airworthiness. Operating failures and malfunctions of equipment are appreciably reduced if excessive wear or minor defects are detected and corrected early. The importance of inspections and the proper use of records concerning these inspections cannot be overemphasized.Airframe and engine inspections may range from preflight inspections to detailed inspections. The time intervals for the inspection periods vary with the models of aircraft involved and the types of operations being conducted. The airframe and engine manufacturer’s instructions should be consulted when establishing inspection intervals.Aircraft may be inspected using flight hours as a basis for scheduling, or on a calendar inspection system. Under the calendar inspection system, the appropriate inspection is performed on the expiration of a speci-fied number of calendar weeks. The calendar inspec-tion system is an efficient system from a maintenance management standpoint. Scheduled replacementofAircraft Logs“Aircraft logs,” as used in this handbook, is an inclu-sive term which applies to the aircraft logbook and all supplemental records concerned with the aircraft. They may come in a variety of formats. For a small aircraft, the log may indeed be a small 5" × 8" logbook. For larger aircraft, the logbooks are often larger, in the form of a three-ring binder. Aircraft that have been in service for a long time are likely to have several logbooks. The aircraft logbook is the record in which all data con-cerning the aircraft is recorded. Information gathered in this log is used to determine the aircraft condition, date of inspections, time on airframe, engines and propellers. It reflects a history of all significant events occurring to the aircraft, its components, and acces-sories, and provides a place for indicating compliance with FAA airworthiness directives or manufactur-ers’ service bulletins. The more comprehensive the logbook, the easier it is to understand the aircraft’s maintenance history.When the inspections are completed, appropriate entries must be made in the aircraft logbook certifying that the aircraft is in an airworthy condition and may be returned to service. When making logbook entries, exercise special care to ensure that the entry can be clearly understood by anyone having a need to read it in the future. Also, if making a hand-written entry, use good penmanship and write legibly. To some degree, the organization, comprehensiveness, and appearance of the aircraft logbooks have an impact on the value of the aircraft. High quality logbooks can mean a higher value for the aircraft.ChecklistsAlways use a checklist when performing an inspection. The checklist may be of your own design, one provided by the manufacturer of the equipment being inspected, or one obtained from some other source. The checklist should include the following:1. Fuselage and hull group.a. Fabric and skin—for deterioration,distortion, other evidence of failure, anddefective or insecure attachment of fittings.b. Systems and components—for properinstallation, apparent defects, and satisfactoryoperation.c. Envelope gas bags, ballast tanks, and relatedparts—for condition.2. Cabin and cockpit group.a. Generally—for cleanliness and looseequipment that should be secured.b. Seats and safety belts—for condition andsecurity.c. Windows and windshields—for deteriorationand breakage.d. Instruments—for condition, mounting,marking, and (where practicable) for properoperation.e. Flight and engine controls—for properinstallation and operation.f. Batteries—for proper installation and charge.g. All systems—for proper installation, generalcondition, apparent defects, and security ofattachment.3. Engine and nacelle group.a. Engine section—for visual evidence ofexcessive oil, fuel, or hydraulic leaks, andsources of such leaks.b. Studs and nuts—for proper torquing andobvious defects.c. Internal engine—for cylinder compressionand for metal particles or foreign matter onscreens and sump drain plugs. If cylindercompression is weak, check for improperinternal condition and improper internaltolerances.d. Engine mount—for cracks, looseness ofmounting, and looseness of engine to mount.e. Flexible vibration dampeners—for conditionand deterioration.f. Engine controls—for defects, proper travel,and proper safetying.g. Lines, hoses, and clamps—for leaks,condition, and looseness.h. Exhaust stacks—for cracks, defects, andproper attachment.i. Accessories—for apparent defects in securityof mounting.j. All systems—for proper installation, generalcondition defects, and secure attachment.k. Cowling—for cracks and defects.l. Ground runup and functional check—checkall powerplant controls and systems forcorrect response, all instruments for properoperation and indication.8-28-3c. Anti-icing devices—for proper operation and obvious defects.d. Control mechanisms—for proper operation, secure mounting, and travel. 8. Communication and navigation group.a. Radio and electronic equipment—for proper installation and secure mounting.b. Wiring and conduits—for proper routing, secure mounting, and obvious defects.c. Bonding and shielding—for proper installation and condition.d. Antennas —for condition, secure mounting, and proper operation. 9. Miscellaneous.a. Emergency and first aid equipment—for general condition and proper stowage.b. Parachutes, life rafts, flares, and so forth—inspect in accordance with the manufacturer’s recommendations.c. Autopilot system—for general condition, security of attachment, and proper operation.PublicationsAeronautical publications are the sources of informa-tion for guiding aviation mechanics in the operation and maintenance of aircraft and related equipment. The proper use of these publications will greatly aid in the efficient operation and maintenance of all air-craft. These include manufacturers’ service bulletins, manuals, and catalogs; FAA regulations; airworthiness directives; advisory circulars; and aircraft, engine and propeller specifications.Manufacturers’ Service Bulletins/Instructions Service bulletins or service instructions are two of sev-eral types of publications issued by airframe, engine, and component manufacturers.The bulletins may include: (1) purpose for issuing the publication, (2) name of the applicable airframe, engine, or component, (3) detailed instructions for service, adjustment, modification or inspection, and source of parts, if required and (4) estimated number of manhours required to accomplish the job.Maintenance ManualThe manufacturer’s aircraft maintenance manual contains complete instructions for maintenance of all systems and components installed in the aircraft. It contains information for the mechanic who normally4. Landing gear group.a. All units —for condition and security of attachment.b. Shock absorbing devices—for proper oleo fluid level.c. Linkage, trusses, and members—for undue or excessive wear, fatigue, and distortion.d. Retracting and locking mechanism—for proper operation.e. Hydraulic lines—for leakage.f. Electrical system—for chafing and proper operation of switches.g. Wheels—for cracks, defects, and condition of bearings.h. Tires —for wear and cuts.i. Brakes —for proper adjustment.j. Floats and skis —for security of attachment and obvious defects. 5. Wing and center section.a. All components—for condition and security.b. Fabric and skin—for deterioration, distortion, other evidence of failure, and security of attachment.c. Internal structure (spars, ribs compression members)—for cracks, bends, and security.d. Movable surfaces —for damage or obvious defects, unsatisfactory fabric or skin attachment and proper travel.e. Control mechanism—for freedom of movement, alignment, and security.f. Control cables—for proper tension, fraying, wear and proper routing through fairleads and pulleys. 6. Empennage group.a. Fixed surfaces—for damage or obvious defects, loose fasteners, and security of attachment.b. Movable control surfaces—for damage or obvious defects, loose fasteners, loose fabric, or skin distortion.c. Fabric or skin—for abrasion, tears, cuts or defects, distortion, and deterioration. 7. Propeller group.a. Propeller assembly—for cracks, nicks, bends, and oil leakage.b. Bolts —for proper torquing and safetying.works on components, assemblies, and systems while they are installed in the aircraft, but not for the over-haul mechanic. A typical aircraft maintenance manual contains:• A description of the systems (i.e., electrical, hydraulic, fuel, control)• Lubrication instructions setting forth the frequency and the lubricants and fluids which are to be used in the various systems,• Pressures and electrical loads applicable to the various systems,• Tolerances and adjustments necessary to proper functioning of the airplane,• Methods of leveling, raising, and towing,• Methods of balancing control surfaces,• Identification of primary and secondary structures,• Frequency and extent of inspections necessary to the proper operation of the airplane,• Special repair methods applicable to the airplane,• Special inspection techniques requiring x-ray, ultrasonic, or magnetic particle inspection, and • A list of special tools.Overhaul ManualThe manufacturer’s overhaul manual contains brief descriptive information and detailed step by step instructions covering work normally performed on a unit that has been removed from the aircraft. Simple, inexpensive items, such as switches and relays on which overhaul is uneconomical, are not covered in the overhaul manual.Structural Repair ManualThis manual contains the manufacturer’s information and specific instructions for repairing primary and sec-ondary structures. Typical skin, frame, rib, and stringer repairs are covered in this manual. Also included are material and fastener substitutions and special repair techniques.Illustrated Parts CatalogThis catalog presents component breakdowns of struc-ture and equipment in disassembly sequence. Also included are exploded views or cutaway illustrations for all parts and equipment manufactured by the aircraft manufacturer.Code of Federal Regulations (CFRs)The CFRs were established by law to provide for the safe and orderly conduct of flight operations and to prescribe airmen privileges and limitations. A knowl-edge of the CFRs is necessary during the performance of maintenance, since all work done on aircraft must comply with CFR provisions.Airworthiness DirectivesA primary safety function of the FAA is to require correction of unsafe conditions found in an aircraft, aircraft engine, propeller, or appliance when such con-ditions exist and are likely to exist or develop in other products of the same design. The unsafe condition may exist because of a design defect, maintenance, or other causes. Title 14 of the Code of Federal Regulations (14 CFR) part 39, Airworthiness Directives, defines the authority and responsibility of the Administra-tor for requiring the necessary corrective action. The Airworthiness Directives (ADs) are published to notify aircraft owners and other interested persons of unsafe conditions and to prescribe the conditions under which the product may continue to be operated. Airworthiness Directives are Federal Aviation Regu-lations and must be complied with unless specific exemption is granted.Airworthiness Directives may be divided into two categories: (1) those of an emergency nature requiring immediate compliance upon receipt and (2) those of a less urgent nature requiring compliance within a rela-tively longer period of time. Also, ADs may be a one-time compliance item or a recurring item that requires future inspection on an hourly basis (accrued flight time since last compliance) or a calendar time basis.The contents of ADs include the aircraft, engine, pro-peller, or appliance model and serial numbers affected. Also included are the compliance time or period, a description of the difficulty experienced, and the nec-essary corrective action.Type Certificate Data SheetsThe type certificate data sheet (TCDS) describes the type design and sets forth the limitations prescribed by the applicable CFR part. It also includes any other limitations and information found necessary for type certification of a particular model aircraft.Type certificate data sheets are numbered in the upper right-hand corner of each page. This number is the same as the type certificate number. The name of the type certificate holder, together with all of the approved8-4models, appears immediately below the type certificate number. The issue date completes this group. This information is contained within a bordered text box to set it off.The data sheet is separated into one or more sections. Each section is identified by a Roman numeral followed by the model designation of the aircraft to which the section pertains. The category or categories in which the aircraft can be certificated are shown in parenthe-ses following the model number. Also included is the approval date shown on the type certificate.The data sheet contains information regarding:1. Model designation of all engines for which theaircraft manufacturer obtained approval for use with this model aircraft.2. Minimum fuel grade to be used.3. Maximum continuous and takeoff ratings of theapproved engines, including manifold pressure (when used), rpm, and horsepower (hp).4. Name of the manufacturer and model designation foreach propeller for which the aircraft manufacturer obtained approval will be shown together with the propeller limits and any operating restrictions peculiar to the propeller or propeller engine combination.5. Airspeed limits in both mph and knots.6. Center of gravity range for the extreme loadingconditions of the aircraft is given in inches from the datum. The range may also be stated in percent of MAC (Mean Aerodynamic Chord) for transport category aircraft.7. Empty weight center of gravity (CG) range (whenestablished) will be given as fore and aft limits in inches from the datum. If no range exists, the word “none” will be shown following the heading on the data sheet.8. Location of the datum.9. Means provided for leveling the aircraft.10. All pertinent maximum weights.11. Number of seats and their moment arms.12. Oil and fuel capacity.13. Control surface movements.14. Required equipment.15. Additional or special equipment found necessaryfor certification.16. Information concerning required placards.It is not within the scope of this handbook to list all the items that can be shown on the type certificate data sheets. Those items listed above serve only to acquaint aviation mechanics with the type of information gener-ally included on the data sheets. Type certificate data sheets may be many pages in length. Figure 8-1 shows a typical TCDS.When conducting a required or routine inspection, it is necessary to ensure that the aircraft and all the major items on it are as defined in the type certificate data sheets. This is called a conformity check, and verifies that the aircraft conforms to the specifications of the aircraft as it was originally certified. Sometimes altera-tions are made that are not specified or authorized in the TCDS. When that condition exists, a supplemental type certificate (STC) will be issued. STCs are considered a part of the permanent records of an aircraft, and should be maintained as part of that aircraft’s logs.Routine/Required InspectionsFor the purpose of determining their overall condition, 14 CFR provides for the inspection of all civil aircraft at specific intervals, depending generally upon the type of operations in which they are engaged. The pilot in command of a civil aircraft is responsible for determin-ing whether that aircraft is in condition for safe flight. Therefore, the aircraft must be inspected before each flight. More detailed inspections must be conducted by aviation maintenance technicians at least once each 12 calendar months, while inspection is required for others after each 100 hours of flight. In other instances, an aircraft may be inspected in accordance with a system set up to provide for total inspection of the aircraft over a calendar or flight time period.To determine the specific inspection requirements and rules for the performance of inspections, refer to the CFR, which prescribes the requirements for the inspection and maintenance of aircraft in various types of operations.Preflight/Postflight InspectionsPilots are required to follow a checklist contained within the Pilot’s Operating Handbook (POH) when operating aircraft. The first section of a checklist includes a section entitled Preflight Inspection. The preflight inspection checklist includes a “walk-around” section listing items that the pilot is to visually check for general condition as he or she walks around the airplane. Also, the pilot must ensure that fuel, oil and other items required for flight are at the proper levels(Continued on page 8-12)8-58-68-78-88-98-108-118-12and not contaminated. Additionally, it is the pilot’s responsibility to review the airworthiness certificate, maintenance records, and other required paperwork to verify that the aircraft is indeed airworthy. After each flight, it is recommended that the pilot or mechanic conduct a postflight inspection to detect any problems that might require repair or servicing before the next flight.Annual/100-Hour InspectionsTitle 14 of the Code of Federal Regulations (14 CFR) part 91 discusses the basic requirements for annual and 100-hour inspections. With some exceptions, all aircraft must have a complete inspection annually. Aircraft that are used for commercial purposes and are likely to be used more frequently than noncommercial aircraft must have this complete inspection every 100 hours. The scope and detail of items to be included in annual and 100-hour inspections is included as appen-dix D of 14 CFR part 43 and shown as Figure 8-2.A properly written checklist, such as the one shown earlier in this chapter, will include all the items of appendix D. Although the scope and detail of annual and 100-hour inspections is identical, there are two significant differences. One difference involves persons authorized to conduct them. A certified airframe and powerplant maintenance technician can conduct a 100-hour inspection, whereas an annual inspection must be conducted by a certified airframe and powerplant maintenance technician with inspection authorization (IA). The other difference involves authorized over-flight of the maximum 100 hours before inspection. An aircraft may be flown up to 10 hours beyond the 100-hour limit if necessary to fly to a destination where the inspection is to be conducted.Progressive InspectionsBecause the scope and detail of an annual inspection is very extensive and could keep an aircraft out of service for a considerable length of time, alternative(a) Each person performing an annual or 100-hourinspection shall, before that inspection, remove or open all necessary inspection plates, access doors, fairing, and cowling. He shall thoroughly clean the aircraft and aircraft engine. (b) Each person performing an annual or 100-hourinspection shall inspect (where applicable) the following components of the fuselage and hull group:(1) Fabric and skin—for deterioration,distortion, other evidence of failure, and defective or insecure attachment of fittings. (2) Systems and components—for improperinstallation, apparent defects, and unsatisfactory operation. (3) Envelope, gas bags, ballast tanks, andrelated parts—for poor condition. (c) Each person performing an annual or 100-hourinspection shall inspect (where applicable) the following components of the cabin and cockpit group:(1) Generally—for uncleanliness and looseequipment that might foul the controls. (2) Seats and safety belts—for poor conditionand apparent defects.Appendix D to Part 43—Scope and Detail of Items (as Applicable to the Particular Aircraft) To Be Included in Annual and 100-Hour InspectionsFigure 8-2. Scope and detail of annual and 100-hour inspections.(3) Windows and windshields—fordeterioration and breakage.(4) Instruments—for poor condition,mounting, marking, and (where practicable) improper operation. (5) Flight and engine controls—for improperinstallation and improper operation. (6) Batteries—for improper installation andimproper charge. (7) All systems—for improper installation,poor general condition, apparent and obvious defects, and insecurity of attachment. (d) Each person performing an annual or 100-hourinspection shall inspect (where applicable) components of the engine and nacelle group as follows:(1) Engine section—for visual evidence ofexcessive oil, fuel, or hydraulic leaks, and sources of such leaks. (2) Studs and nuts—for improper torquingand obvious defects.(3) Internal engine—for cylinder compressionand for metal particles or foreign matter on screens and sump drain plugs. If there is8-13weak cylinder compression, for improper internal condition and improper internal tolerances.(4) Engine mount—for cracks, loosenessof mounting, and looseness of engine to mount. (5) Flexible vibration dampeners—for poorcondition and deterioration. (6) Engine controls—for defects, impropertravel, and improper safetying. (7) Lines, hoses, and clamps—for leaks,improper condition, and looseness. (8) Exhaust stacks—for cracks, defects, andimproper attachment. (9) Accessories—for apparent defects insecurity of mounting.(10) All systems—for improper installation, poor general condition, defects, and insecure attachment.(11) Cowling—for cracks and defects. (e) Each person performing an annual or 100-hour inspection shall inspect (where applicable) the following components of the landing gear group:(1) All units —for poor condition andinsecurity of attachment. (2) Shock absorbing devices—for improperoleo fluid level. (3) Linkages, trusses, and members—forundue or excessive wear fatigue, and distortion. (4) Retracting and locking mechanism—forimproper operation. (5) Hydraulic lines—for leakage. (6) Electrical system—for chafing andimproper operation of switches. (7) Wheels—for cracks, defects, andcondition of bearings. (8) Tires—for wear and cuts. (9) Brakes—for improper adjustment.(10) Floats and skis—for insecure attachment and obvious or apparent defects.Figure 8-2. Scope and detail of annual and 100-hour inspections. (continued)(f) Each person performing an annual or 100-hourinspection shall inspect (where applicable) all components of the wing and center section assembly for poor general condition, fabric or skin deterioration, distortion, evidence of failure, and insecurity of attachment.(g) Each person performing an annual or 100-hour inspection shall inspect (where applicable) all components and systems that make up the com-plete empennage assembly for poor general condition, fabric or skin deterioration, distortion, evidence of failure, insecure attachment, improper component installation, and improper component operation.(h) Each person performing an annual or 100-hour inspection shall inspect (where applicable) the following components of the propeller group: (1) Propeller assembly—for cracks, nicks,binds, and oil leakage. (2) Bolts—for improper torquing and lack ofsafetying. (3) Anti-icing devices—for improperoperations and obvious defects. (4) Control mechanisms—for improperoperation, insecure mounting, and restricted travel. (i) Each person performing an annual or 100-hourinspection shall inspect (where applicable) the following components of the radio group: (1) Radio and electronic equipment—forimproper installation and insecure mounting. (2) Wiring and conduits—for improperrouting, insecure mounting, and obvious defects. (3) Bonding and shielding—for improperinstallation and poor condition. (4) Antenna including trailing antenna—forpoor condition, insecure mounting, and improper operation. (j) Each person performing an annual or 100-hourinspection shall inspect (where applicable) each installed miscellaneous item that is not otherwise covered by this listing for improper installation and improper operation.Appendix D to Part 43—Scope and Detail of Items (as Applicable to the Particular Aircraft) To Be Included in Annual and 100-Hour Inspections (continued)8-14inspection programs designed to minimize down time may be utilized. A progressive inspection program allows an aircraft to be inspected progressively. The scope and detail of an annual inspection is essentially divided into segments or phases (typically four to six). Completion of all the phases completes a cycle that satisfies the requirements of an annual inspection. The advantage of such a program is that any required segment may be completed overnight and thus enable the aircraft to fly daily without missing any revenue earning potential. Progressive inspection programs include routine items such as engine oil changes and detailed items such as flight control cable inspection. Routine items are accomplished each time the aircraftcomes in for a phase inspection and detailed items focus on detailed inspection of specific areas. Detailed inspections are typically done once each cycle. A cycle must be completed within 12 months. If all required phases are not completed within 12 months, the remain-ing phase inspections must be conducted before the end of the 12th month from when the first phase was completed.Each registered owner or operator of an aircraft desiring to use a progressive inspection program must submit a written request to the FAA Flight Standards District Office (FSDO) having jurisdiction over the area in which the applicant is located. Title 14 of the Code of Federal Regulations (14 CFR) part 91, §91.409(d)Figure 8-3. 14 CFR §91.409(d) Progressive inspection.(d) Progressive inspection. Each registered owner or operator of an aircraft desiring to use a progressive inspection program must submit a written request to the FAA Flight Standards district office having jurisdiction over the area in which the applicant is located, and shall provide—(1) A certificated mechanic holding aninspection authorization, a certificated airframe repair station, or the manufacturer of the aircraft to supervise or conduct the progressive inspection;(2) A current inspection procedures manualavailable and readily understandable to pilot and maintenance personnel containing, in detail—(i) An explanation of the progressiveinspection, including the continuity of inspection responsibility, the making of reports, and the keeping of records and technical reference material; (ii) An inspection schedule, specifyingthe intervals in hours or days when routine and detailed inspections will be performed and including instructions for exceeding an inspection interval by not more than 10 hours while en route and for changing an inspection interval because of service experience;(iii) Sample routine and detailed inspection forms and instructions for their use; and(iv) Sample reports and records and instructions for their use;(3) Enough housing and equipment fornecessary disassembly and proper inspection of the aircraft; and (4) Appropriate current technical informationfor the aircraft.The frequency and detail of the progressive inspection shall provide for the complete inspection of the aircraft within each 12 calendar months and be consistent with the manufacturer's recommendations, field service experience, and the kind of operation in which the aircraft is engaged. The progressive inspection schedule must ensure that the aircraft, at all times, will be airworthy and will conform to all applicable FAA aircraft specifications, type certificate data sheets, airworthiness directives, and other approved data. If the progressive inspection is discontinued, the owner or operator shall immediately notify the local FAA Flight Standards district office, in writing, of the discontinuance. After the discontinuance, the first annual inspection under §91.409(a)(1) is due within 12 calendar months after the last complete inspection of the aircraft under the progressive inspection. The 100-hour inspection under §91.409(b) is due within 100 hours after that complete inspection. A complete inspection of the aircraft, for the purpose of determining when the annual and 100-hour inspections are due, requires a detailed inspection of the aircraft and all its components in accordance with the progressive inspection. A routine inspection of the aircraft and a detailed inspection of several components is not considered to be a complete inspection.§91.409 Inspections.。
船舶工程外文翻译----船舶结构安全性和可靠性
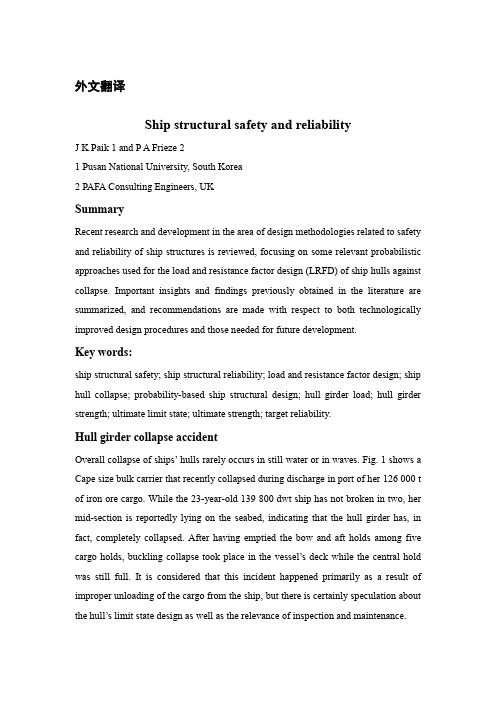
外文翻译Ship structural safety and reliabilityJ K Paik 1 and P A Frieze 21 Pusan National University, South Korea2 PAFA Consulting Engineers, UKSummaryRecent research and development in the area ofdesign methodologies related to safety andreliability of ship structures is reviewed, focusing onsome relevant probabilistic approaches used for theload and resistance factor design (LRFD) of shiphulls against collapse. Important insights andfindings previously obtained in the literature aresummarized, and recommendations are made withrespect to both technologically improved designprocedures and those needed for futuredevelopment.Key words:ship structural safety; ship structural reliability; load and resistance factor design; ship hull collapse;probability-based ship structural design; hull girder load; hull girder strength; ultimate limit state; ultimate strength;target reliability.Hull girder collapse accidentOverall collapse of ships’ hull s rarely occurs in stillwater or in waves. Fig. 1 shows a Capesize bulk carrierthat recently collapsed during discharge in port of her126 000 t of iron ore cargo. While the 23-year-old139 800 dwt ship has not broken in two, her mid-section is reportedly lying on the seabed, indicatingthat the hull girder has, in fact, completely collapsed.After having emptied the bow and aft holds amongfive cargo holds, buckling collapse took place in thevessel’s deck while the central hold was still full. It isconsidered that this incident happened primarily asa result of improper unloading of the cargo from theship, but there is certainly speculation about the hull’slimit state design as well as the relevance of inspectionand maintenance.Fig. 1 A ship hull collapse during unloading of cargo at port(Courtesy of Lloyds List)A ship hull in the intact condition will clearlysustain applied loads smaller than the design loads,and in normal sea and loading conditions it will notsuffer structural failure such as buckling and collapse,except for possible localized yielding. However, theloads acting on the ship hull are uncertain, owing torough seas or unusual loading/unloading of cargo. Inthese cases, applied loads may exceed design loadsand the ship hull may collapse globally. Furthermore,since aging ships may suffer structural degradationdue to corrosion, fatigue and local damage witha consequential reduction of their structuralresistance, the hull may collapse under applied loadseven smaller than the design loads.Probability-based structural designprocedureThe main steps for probability-based ship structuraldesign are normally as follows:●establish a target reliability;●identify all unfavorable failure modes of thestructure;●formulate the limit state function for each failuremode identified above;●identify the probabilistic characteristics (mean,variance, distribution) of the random variables inthe limit state function;●calculate the reliability against the limit state withrespect to each failure mode of the structure;●assess if the predicted reliability is greater than thetarget reliability, and redesign the structureotherwise;●evaluate the reliability analysis results with respectto parametric sensitivity considerations.Modelling of hull girder strengthFour types of limit state can be considered: namely,serviceability limit state, ultimate limit state, fatiguelimit state and accidental limit state . Theserviceability limit state involves deterioration of lessvital functions including:●local damage which may reduce the durability of thestructure or affect the efficiency of structural or non-structural elements;●unacceptable deformations which affect the efficientuse of structural or non-structural elements, or thefunctioning of equipment;●excessive vibrations which cause discomfort topeople or affect non-structural elements, or thefunctioning of equipment.The ultimate limit state represents the collapse of thestructure, from factors such as: ●loss of equilibrium of the structure or part of thestructure, considered as a rigid body (e.g.overturning or capsizing);●attainment of the maximum resistance capacity ofsections, members or connections by gross yielding,rupture or fracture;●instability of the structure or part thereof, such as bybuckling of columns, plates, shells and stiffenedpanels.The fatigue limit state results from damageaccumulation under the action of cyclic loads and theaccidental limit state is due to accidents such ascollisions or grounding. Overall failure of ship hull girders, which rarelyoccurs, is normally governed by buckling and plasticcollapse of the deck, bottom or sometimes the sideshell stiffened panels. Failure of deck, bottom or sideshell stiffened panels can then lead to progressivecollapse and ultimate hull girder failure. For manyyears, ship structural researchers have been workingtowards the goal of reliability-based limit state designof ship structures. However, reliability-based designrequirescalculation of the ultimate limit state, not onlyof the hull girder, but also of all the structural panelsand other members. Also, these calculations must beperformed a large number of times.Therefore, it is notpractical to use iterative finite element analyses forthese calculations. For efficient computations, ultimatestrength formulations must be developed as closed-form expressions, both for structural components andfor the complete hull girder.A number of studies on the ultimate collapsestrength of ships’ hulls have been undertakentheoretically, numerically and experimentally .Some of the results have been reviewed by the ISSCTechnical Committee III.1 on ‘Ultimate Strength’. Theultimate strength reliability of ships’ hulls,considering existing local damage related to corrosion,fatigue and collision/grounding, has also beenstudied.Previous studies on the development ofa formulation for ultimate hull strength predictionmay be classified into three groups. The first is a linearapproach, where the behaviour of the hull up to failureof the compression flange is assumed to be linearelastic, i.e. ignoring buckling, and the ultimatemoment capacity of the hull is basically expressed asthe ultimate strength of the compression flangemultiplied by the elastic section modulus, witha simple correction for buckling and yielding .The second is an empirical approach, where anexpression is derived on the basis of experimental ornumerical data from scaled or real hull models.The third is an analytical approach, based ona presumed stress distribution over the hull section(plane sections remain plane) from which themoment of resistance of the hull is theoreticallycalculated, taking into account buckling in thecompression flange and yielding in the tensionflange.The first approach is quite simple, but its accuracy isusually wanting because, after buckling of thecompression flange, the behaviour of the hull is nolonger linear, and the neutral axis changes position.Empirical formulations (the second approach) mayprovide reasonable solutions for conventional hulls,but one has to be careful in using empiricalformulations for new and general-type hulls, sincethey are usually derived on the basis of limited data, orfor a particular hull form, using an empiricalformulation . On the other hand, analyticalformulations (the third approach) can be applied tonew or general hulls because they include sectioneffects more precisely.The ship hull ultimate strength formula iseventually expressed as a function of designparameters related to geometric and materialproperties including plate thickness, yield strengthand Young’s modulus. When time-variant structuraldegradation (e.g. corrosion) is considered, the value ofmember thickness at any particular time is a functionof such damage. In probability-based design methods,all the design parameters are treated as the randomvariables. The hull ultimate strength formula forhogging normally differs from that for sagging. Limit state functionMathematically, the limit state function for structuralfailure can be given as a function of the randomvariables, as follows:f (X )=f (1x ,2x ,………n x )(1)where f (X) is the limit state function representing themargin between structural capacity and demand (i.e.loads or load effects); x i represents the designparameters.The limit state function f (X) characterizes thecondition of the structure and defines two domains ofsafety with regard to the limit surface (envelope), asfollows:f (X )>0 in the safe domainf (X )=0 on the limit surface (2)f (X )<0 in the unsafe domainWith two independent random variables, theultimate limit state function f (X) for ship hull collapseis usually taken as the margin between ship hullultimate strength u M and total bending moment t M , asfollows:f (X )=u M -t M (3)where u M and t M are functions of the design variables.Methods of reliability analysisThe methods for structural reliability analysis areusually classified into four types,namely level I, levelII, level III and level IV . The level I methodcorresponds to the deterministic or partial safety factormethod, using only one characteristic mean value foreach variable. A relevant allowable usage factor foreach variable that may be determined by calibration ofa higher level reliability method-based results isapplied in the level I reliability analysis toapproximately supplement the related uncertainties.The level II method uses two values, i.e. mean andstandard deviation, to describe the characteristics ofeach random variable. The reliability index method,e.g. the first-order second-moment method, is a typicalexample of the level II method. The level III method uses the joint probability density function to describethe characteristics of the random variables. Inreliability analyses by the level III method, eitheranalytical approximations (e.g. first- or second-orderreliability methods) or numerical simulations (e.g.Monte Carlo simulation or directional sampling) areapplied. The level IV method compares the integrityand prospect of an object structure with that ofa reference structure through the engineeringeconomic analysis, considering costs and benefitsassociated with construction, consequences ofstructural failure and maintenance/repair. The levelIV method is employed to establish the targetreliabilities.The ship structural reliability analysis is usuallyundertaken by the level III method. Since the theory ofreliability analysis is discussed in many references,e.g. Mansour and Ditlevsen & Madsen , onlya very brief description for the level III method is givenhere. Generally the probability of failure P f can becalculated as follows: f P =⎰≤0f )(X P (X )dx (4)where p(X) is the joint probability density function ofthe random variables X=1x ,2x ,………n x associated withloading, material properties, geometric characteristics,etc. andf (X) is the limit state function, defined suchthat negative values imply failure. Since f (X) is usuallya complicated nonlinear function, it is not easy toperform the integration of eq. (4) directly. Therefore,the equation is normally solved by use of approximateprocedures .With these approximations, as indicated in Fig. 2,the limit state surface is usually approximated at thedesign (failure) point by either a tangent hyper-planeor a hyper-parabola, which simplifies the mathematicsrelated to the calculation of the failure probability. Thefirst type of approximation results in the use of aso-called first-order reliability method (FORM) and the second type of approximation is central to theso-called second-order reliability method (SORM).Such methods facilitate the rapid calculation of theprobability of failure, by widely available standardsoftware. Apart from the individual probabilitydistributions of the random variables involved, thecorrelation between them can also be readilyaccounted for in such calculations; all randomvariables for various member types are considereduncorrelated. The result of such a standard reliabilitycalculation is a reliability index β which is related tothe probability of failure f P by:f P =)(βφ-(5) where is the standard normal distribution function.Fig. 2Further considerationsWhile a number of useful methodologies for analyzingthe safety and reliability of ship structures have beendeveloped over the past decades, furtherdevelopments are needed.Some furtherconsiderations in probability-based design of shipstructures are as follows:●geometric parameters may be treated asdeterministic, although this may need to beconfirmed in the case of deck and bottom platingthickness;●elastic modulus may be taken as deterministic, butyield stress needs to be treated as a random variablewith a mean value based on a fuller assessment ofstrain-rate effects on yield in large-scalerepresentative ship-type structures than presentedhere. In the first instance, yield stress values couldbe based on tensile coupon test results when wave-induced bending moments dominate, and similarlyderived static values of yield stress for dominantstill water load conditions.●hull girder and stiffened panel ultimate strengthmodels require benchmarking against realisticmechanical collapse test data so that the distributionparameters for their associated modelling errors canbe evaluated;●when time-variant structural degradation, e.g. dueto corrosion and fatigue, is considered, theprobabilistic characteristics of such damageat any particular time should be quantified. Whilesome work continues in this area, there existprobabilistic corrosion rate estimation models fortanker structures and for bulk carrierstructures;●consensus is required about the preferredmethodology for determining an appropriatereturn period of response for ship designand how this might be achieved given thecurrent status of environmental parameters anddata records;●the load factor methodology promoted in theliterature is extremely promising, particularlybecause its form is compatible with limitstate (LRFD) design code formats. Consensusis required concerning its generality andany further development. Classification Societyand naval experiences should be helpful inidentifying load combinations to be addressed.However, in identifying a safety format, accountshould be taken of relevant ISO codes (e.g. ISO 2394)in this area;●target safety and reliability initially requiresa calibration approach to determine appropriatevalues, followed by adjustments based onjudgments concerning successful designs and targetreliabilities in other industries, whilst recognizingthat floating structures probably need one order ofmagnitude (in probability of failure terms)morereliability than comparable bottom-foundedstructures, and an expectation that component andsystem reliabilities should differ by about one orderin probability of failure terms. In the context oflongitudinally stiffened ships, plate buckling shouldbe treated as a serviceability limit state and not as anultimate limit state;●partial factor determination will require some formof simplified modelling of strength, loading or thereliability process in order that such determinationcan proceed efficiently. Curve- or surface- fitting canbe applied in all cases.船舶结构安全性和可靠性J K帕克[1] P A普莱斯[2]1.韩国釜山国家大学2.英国FAFA工程师顾问摘要最近在研究和发展对该地区船舶结构的设计方法,安全性和可靠性的评估,将阻力、负荷作为因子运用概率的方法来对船体的抗损毁能力进行设计。
国际机构关于空气系统组件的指南-AMCA国际有限公司,空气流动和控制协会国际指南-Fire、Smok
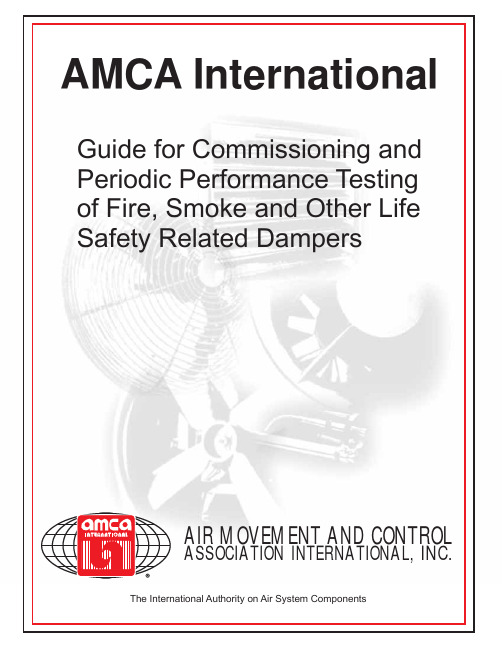
Guide for Commissioning andPeriodic Performance Testingof Fire, Smoke and Other LifeSafety Related DampersPurposeFire Dampers, Smoke Dampers, Combination Fire Smoke Dampers, Ceiling Radiation Dampers, and other types of Dampers that perform as part of a building’s Fire Protection or Life-Safety System must function properly during a fire or life-safety emergency. Proper installation and periodic performance testing are required to ensure these dampers function as intended in a fire emergency.The purpose of this document is to provide recommendations for the proper commissioning of Fire and Life Safety Related Dampers and to describe the appropriate intervals and methods for performing periodic performance testing of these dampers.BackgroundLife Safety Dampers are designed to perform a number of functions in a building’s HVAC, Fire and/or Smoke Control System and are an integral part of the overall life-safety system within the building. Generally, Fire Dampers are designed to close and prevent the spread of fire through an opening in a fire resistive barrier. Ceiling Radiation Dampers are designed to close and reduce the transfer of heat through an opening in the ceiling membrane of floor-ceiling or roof-ceiling assembly. Refer to the specified ceiling design for details regarding penetrations. Smoke Dampers operate to prevent the spread of smoke by closing to stop airflow or by opening to exhaust smoke. They can also be opened or closed to create pressure differences (as in an engineered smoke control system) to reduce the spread of smoke. Combination Fire Smoke Dampers perform the dual role of both Fire Dampers and Smoke Dampers. Underwriters Laboratories (UL) has developed and maintains standards for the testing, qualification,and appropriate labeling of Fire Dampers (UL 555), Smoke Dampers (UL 555S), Combination Fire Smoke Dampers (UL 555 and UL 555S) and Ceiling Radiation Dampers (UL 555C & UL 263). Manufacturers of these dampers, who have complied with these UL requirements, provide classifiedand labeled dampers for installation where required in HVAC and Engineered Smoke Control Systems. Building Codes and several NFPA and ASHRAE Standards identify where Fire, Smoke and Ceiling Radiation Dampers are required to be installed in a building’s HVAC and/or Smoke Control System. Architects and Design Engineers incorporate Code required dampers in their building designs but also may incorporate additional requirements depending on a building’s specific purpose and intended function.Commissioning or Acceptance TestingThe term Commissioning is used to define an inspection process to determine if all components of a building are operating as intended by the building’s design. Ensuring that a building’s mechanical system, its HVAC System, and any Smoke Control or other Life-Safety related systems operate properly (including all Fire and Life-Safety Related Dampers), and documenting their proper operation is the result of the Commissioning process. This process is also known as Acceptance Testing.Below are the AMCA recommended checklists for the commissioning of Fire and Life-Safety Related Dampers. For specific installation requirements of the brand and model damper being commissioned, the damper manufacturer’s installation instructions shall be referenced.Fire Dampers and Combination Fire Smoke Dampers1. Positioning of the Damper in the Opening – Unless specifically allowed by the dampermanufacturer’s installation instructions, the centerline of the fire damper’s frame shall be located in the plane of the fire rated assembly.2. Damper Sleeve – Unless the damper frame is wide enough to provide for direct attachment ofretaining angles, all fire dampers shall be mounted in a sleeve fabricated per the dampermanufacturer’s installation instructions. The sleeve shall not extend more than 6 inches beyondthe wall or floor opening unless there is an actuator or factory mounted access door on thedamper. When an actuator or factory mounted access door is installed, the sleeve shall notextend more than 16 inches beyond the wall or floor opening. The sleeve is still limited toextending 6 inches beyond the wall or floor opening on the side opposite the actuator or factorymounted access door.3. Clearance between Damper and Wall/Floor Opening – Most dampers are tested with definedclearances between the damper’s sleeve and the wall or floor opening. Unless otherwiseindicated in the installation instructions, the annular space between the sleeve of the damper and the wall/floor opening should not be filled with firestop materials such as fill, void or cavitymaterials. Reference the damper manufacturer’s installation instructions for the specific clearance requirements.4. Securing Damper and Sleeve to the Wall/Floor Openings – Most approved damper installationmethods require the use of retaining angles to secure the damper in the wall or floor opening.Reference the damper manufacturer’s installation instructions for the required material gauge of the retaining angles, the required overlap between the retaining angles and the wall or floor, and the spacing and type of fasteners to be used.5. Duct to Sleeve Connections – Dampers are tested and approved to use specific methods forconnecting the damper sleeve to adjoining ductwork. Reference the damper manufacturer’sinstallation instructions for the allowable duct to sleeve connections.6. Damper Access – Access to the dampers shall be provided. Access shall be large enough toallow inspection and maintenance of the damper and its operating parts. The access points shall be permanently identified on the exterior by a label having letters not less than ½ inch in heightreading: FIRE/SMOKE DAMPER or FIRE DAMPER.7. Damper Flow and Pressure Ratings – For dynamic fire dampers and combination fire smokedampers, it shall be verified that the system airflow and pressure are within the damper’s ratings.8. Operation of the Damper – After the damper is installed it shall be cycled to ensure properoperation. The operation test performed as part of the commissioning process shall follow thesame procedure described in the Periodic Performance Testing section below.Smoke Dampers1. Positioning of the Damper Relative to the Opening – The centerline of the damper shall bemounted within 24 inches of the opening it is protecting. In addition, no ductwork shall branch-off between the damper and the wall or floor opening it is protecting.2. Sealing the Damper Frame to the Ductwork – Many damper installations require that thedamper frame be sealed to the ductwork it is being installed in. Reference the dampermanufacturer’s installation instructions to determine if this requirement applies and to determine the allowable sealants.3. Damper Access – Access to the dampers shall be provided. Access shall be large enough toallow inspection and maintenance of the damper and its operating parts. The access points shall be permanently identified on the exterior by a label having letters not less than ½ inch in heightreading: SMOKE DAMPER.4. Damper Flow and Pressure Ratings – It shall be verified that the system airflow and pressureare within the dampers ratings.5. Operation of the Damper – After the damper is installed it shall be cycled to ensure properoperation. The operation test performed as part of the commissioning process shall follow thesame procedure described in the periodic performance testing section below.Ceiling Radiation Dampers1. Hourly Rating – Ceiling dampers carry a maximum hourly rating for the assembly in which theyare installed. Check that the maximum hourly rating of the damper installed is approved for thesame hourly rating as the ceiling assembly.2. Positioning of the Damper in or Over the Penetration – The damper can be installed on top ofa steel diffuser, sitting directly on the rated ceiling grid, in a steel duct drop, or supported suchthat the frame rest at the penetration. Refer to the manufacturer’s installation instructions for the maximum allowed distance that the closed blades are allowed from the bottom of the ratedceiling. In the case of drywall installation, consult instructions for maximum allowed clearancebetween penetration and damper frame.3. Thermal Blanket – When a damper is not located directly in the penetration and the damperframe is more than 1 inch smaller than the penetration, then a thermal blanket is normallyrequired to reduce heat transfer across the grille back pan. Refer to the manufacturers installation instructions for the recommended material and size of the thermal blanket.4. Clearance between Damper, Grille, Duct, and Wall/Floor Opening – Most dampers are testedwith defined clearances as specified in their instructions. If not specified, a rule of thumb is tokeep tolerances minimal (less than 1/8 inch) between connecting components. If possible, have the largest component extend over the smaller one below it. Reference the dampermanufacturer’s installation instructions for the specific clearance requirements.5. Securing Damper to the Sleeve, Grille, Ductwork – Most of the time, dampers are to beinstalled so that they are supported by the structural members above them or the ceiling grid.Ceiling dampers are not normally supported by the drywall, gypsum, or ceiling tiles alone. They are normally supported via steel wires, hangers, or duct drops with direct fasteners such asscrews, rivets, and bolts. Reference the damper manufacturer’s installation instructions for therequired material and fasteners.6. Grille to Damper to Duct Connections – Unless otherwise stated in the manufacturer’sinstallation instructions, the damper will either lie on the ceiling grid or cover the neck of thediffuser. If connected to duct, the damper should be installed inside the duct connection.7. Operation of the Damper – After the damper is installed, the fuse link shall be removed and thedamper blades allowed to close upon its own mechanics. Cycling the damper ensures properoperation. The operation test performed as part of the commissioning process shall follow thesame procedure described in periodic performance testing section below.Periodic Performance TestingFire Life-Safety related dampers that are properly applied and installed and that have proven the ability to function as intended through a building commissioning process should require no specific on-going maintenance beyond the periodic testing described below to confirm operability.Although the required frequency of this periodic operation testing varies by local jurisdiction, most local requirements reference one of two national standards, either NFPA 80 or NFPA 105. NFPA 80 covers the requirements for fire dampers and NFPA 105 covers the requirements for smoke dampers. Both documents contain the following frequency requirements for periodic operation testing:Each damper shall be tested and inspected one year after installation. The test and inspection frequency shall then be every 4 years, except in hospitals, where the frequency shall be every 6 years.The method used to perform the periodic operation testing depends on the type of damper. More specifically, it depends on how the damper operates. From an operability standpoint, fire life-safety related dampers fall into one of the two following categories:1. Dampers Requiring a Fusible Link to Operate – Most Fire Dampers and Ceiling RadiationDampers, and some Combination Fire Smoke Dampers are held in an open position by a fusible link. The fusible link is designed to melt at a specified temperature allowing gravity or a spring to close the damper. After the fusible link has melted these dampers remain closed until reopened manually and a new fusible link is installed.2. Dampers That Do Not Require a Fusible Link to Operate – Smoke Dampers, some FireDampers and most Combination Fire Smoke Dampers do not use fusible links to operate. These dampers use an electric or pneumatic actuator to operate the damper. Fire Dampers andCombination Fire Smoke Dampers that do not use fusible links use a bi-metallic disc typethermostat to interrupt electrical power or air pressure to the actuator at a specified temperature.Once the electrical power or air pressure is interrupted the spring return feature of the actuatorcloses the damper.Periodic Performance Testing for Fusible Link Operated DampersThe recommended procedure for performing the periodic operation testing on fusible link operated dampers is described below. As always, the damper manufacturer’s installation and operation instructions should be followed:1. For safety considerations, ensure that the fan is off.2. With the damper in the full-open position, remove the fusible link. Care should be taken to ensurethat there are no obstructions, including hands, in the path of the damper blades before thefusible link is removed.3. Once the fusible link is removed, ensure that the damper closes completely without assistance. Ifthe damper is designed with a latch to hold the damper in the full-closed position confirm that the damper latches properly.4. Return the damper to the full-open position and replace the fusible link. If the link appearsdamaged, replace with a functionally equivalent link.Periodic Performance Testing for Dampers That Do Not Use a Fusible Link to OperateThe recommended procedure for performing periodic operation testing on dampers that do not require a fusible link to operate is described below. Two procedures are described. The first describes the procedure for dampers designed with position indication switches to verify that the damper has reached the full-open and full-closed position These switches can be wired to local or remote control panels or building automation systems (BAS) to indicate if the damper is in the full-open position, the full-closed position, or neither. The second procedure describes the procedure for testing dampers without position indication switches. As always, the damper manufacturer’s installation and operation instructions should be followed.Dampers with Position Indication Wired to Indication Lights, Control Panels or BAS1. Use the signal from the damper’s position indication device to confirm that the damper is in thefull-open position.2. Remove electrical power or air pressure from the actuator to allow the actuator’s spring returnfeature to close the damper.3. Use the signal from the damper’s position indication device to confirm that the damper reaches itsfull-closed position.4. Reapply electrical power or air pressure to reopen the damper.5. Use the signal from the damper’s position indication device to confirm that the damper reaches itsfull-open position.Dampers without Position Indication1. Visually confirm that the damper is in the full-open position.2. Ensure that all obstructions, including hands, are out of the path of the damper blades and thenremove electrical power or air pressure from the actuator to allow the actuator’s spring returnfeature to close the damper.3. Visually confirm that the damper closes completely4. Reapply electrical power or air pressure to reopen the damper.5. Visually confirm that the damper is in the full-open position.In addition to these requirements, NFPA 72 and NFPA 92 describe the periodic testing requirements for smoke control systems. Dampers that are part of smoke control systems shall be cycled as part of this testing.List of Publications Referenced in this DocumentUL 555 Standard for Fire DampersUL 555S Standard for Smoke DampersUL 555C Standard for Ceiling DampersUL 263 Standard for Fire Tests of Building and Construction MaterialsNFPA 80 Standard for Fire Doors and Other Opening ProtectivesNFPA 105 Standard for the installation of Smoke Door Assemblies and Other Opening Protectives NFPA 72 National Fire Alarm and Signaling CodeNFPA 92 Standard for Smoke Control SystemsASSOCIATION INTERNATIONAL,INC.30 West University DriveArlington Heights, IL 60004-1893 U.S.A.T el: (847) 394-0150Fax: (847) 253-0088E-Mail:*************Web: The Air Movement and control Association International, Inc. is a not-for-profit international association of the world’s manufacturers of related air system equipment primarily, b ut limited to: fans, louvers, dampers, air curtains, airflow measurement stations, acoustic attenuators, and other air system components for the industrial,commercial and residential markets.。
真空断路器防跳 英语

真空断路器防跳英语Vacuum Circuit Breaker Preventing JumpingVacuum circuit breakers are devices used to protectelectrical systems from overloads, short circuits, and other electrical faults. However, they can also experience jumping, which refers to the rapid opening and closing of theelectrical contacts at extremely high frequencies. This phenomenon can lead to arcing, voltage fluctuations, and other serious problems. To prevent this from happening, vacuum circuit breakers are equipped with various measures and technologies to ensure safe and efficient operation.1. Contact designThe contact design is crucial for avoiding jumping in vacuum circuit breakers. The contacts should be made of high-quality materials with low contact resistance, high stability, and good thermal conductivity. They should also have a large contact area and a suitable contact force to ensuresufficient contact pressure and reduce contact resistance. In addition, the contacts should be designed to minimize the contact bounce and to ensure smooth and stable opening and closing.2. Arc quenching technologyAnother important factor for preventing jumping in vacuum circuit breakers is the arc quenching technology. The arcthat occurs when the electrical contacts separate generates a lot of energy and heat, which can damage the contacts and the surrounding equipment. To avoid this, vacuum circuit breakers use various methods to extinguish the arc quickly and safely, such as magnetic blowout, self-blast interrupter, andcurrent-limiting reactors.3. Vibration and shock resistanceVacuum circuit breakers are subject to various mechanical stresses, including vibration and shock. These stresses can cause the contacts to bounce, resulting in jumping and arcing. To minimize these effects, vacuum circuit breakers are designed with shock-absorbing and vibration-damping materials and features. For example, the contacts may be enclosed in elastomeric material, and the breaker may be mounted onrubber vibration dampers or shock-resistant brackets.4. Temperature controlTemperature control is also a critical factor for preventing jumping in vacuum circuit breakers. The contacts must be designed to withstand high temperatures without degrading or melting. Additionally, the circuit breaker must be equipped with temperature sensors and cooling systems to regulate the temperature and prevent overheating. This can be achieved through various methods, such as forced air cooling, water cooling, or active thermal management.5. Maintenance and testingLastly, proper maintenance and testing are essential for ensuring the safe and reliable operation of vacuum circuit breakers. Regular inspection and cleaning of the contacts, as well as calibration and adjustment of the opening and closing mechanisms, can help prevent jumping and other electrical faults. Additionally, performing routine tests, such as insulation resistance tests, contact resistance tests, and operation tests, can help detect and diagnose problems before they become severe.In conclusion, preventing jumping in vacuum circuit breakers is essential for ensuring the safety and efficiency of electrical systems. By focusing on the contact design, arc quenching technology, vibration and shock resistance, temperature control, and maintenance and testing, we can minimize the risks of jumping and ensure optimal performance.。
国际船舶 货物系固手册
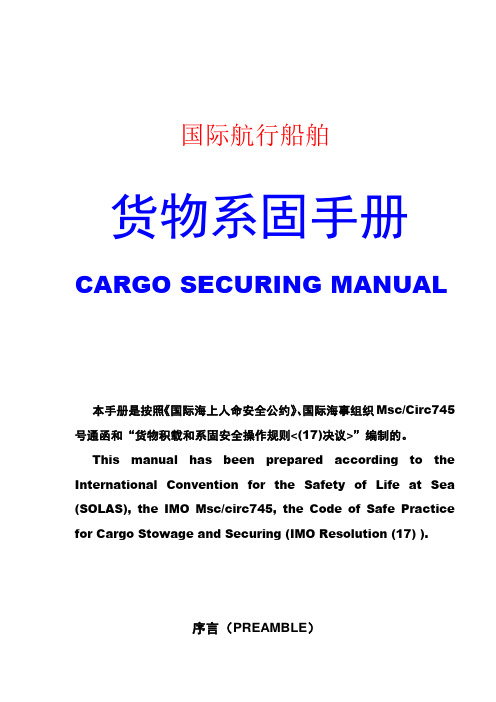
国际航行船舶货物系固手册CARGO SECURING MANUAL本手册是按照《国际海上人命安全公约》、国际海事组织Msc/Circ745号通函和“货物积载和系固安全操作规则<(17)决议>”编制的。
This manual has been prepared according to the International Convention for the Safety of Life at Sea (SOLAS), the IMO Msc/circ745, the Code of Safe Practice for Cargo Stowage and Securing (IMO Resolution (17) ).序言(PREAMBLE)本手册是按照1974年《国际海上人命安全公约》、国际海事组织第Msc/Circ745号通函、国际海事组织决议(17)以及“货物积载和系固安全操作规则”编制的。
This manual has been prepared according to the International Convention for the Safety of Life at Sea , 1974(SOLAS)1994 amendment, the IMO Msc/circ745,the Code of Safe Practice for Cargo Stowage and Securing (IMO Resolution (17) ).本手册应永久保留在船上, 以便船级社的验船师、港口国检查的官员以及其他有关人员的随时检查。
The manual shall always be kept on board and available for inspection by class surveyors , port/flag state inspectors and others to whom it may concern.如系固装置和对系固手册的要求有变化, 本手册应修订并送船级社或主管当局重新批准。
FDA认证检查的六大系统
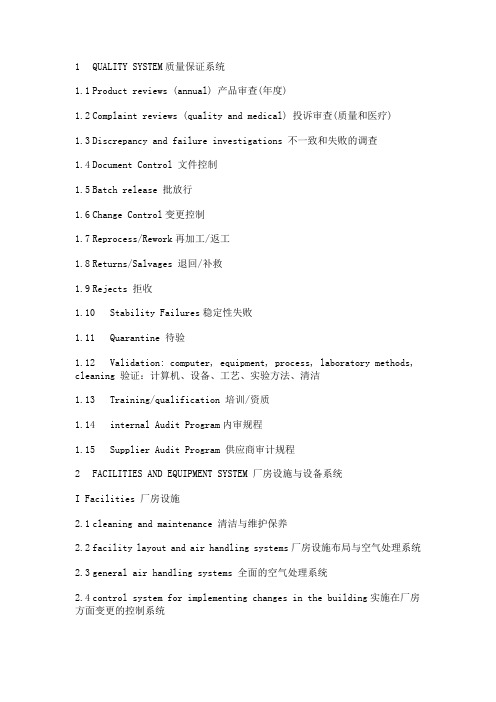
1 QUALITY SYSTEM质量保证系统1.1 Product reviews (annual) 产品审查(年度)1.2 Complaint reviews (quality and medical) 投诉审查(质量和医疗)1.3 Discrepancy and failure investigations 不一致和失败的调查1.4 Document Control 文件控制1.5 Batch release 批放行1.6 Change Control变更控制1.7 Reprocess/Rework再加工/返工1.8 Returns/Salvages 退回/补救1.9 Rejects 拒收1.10 Stability Failures稳定性失败1.11 Quarantine 待验1.12 Validation: computer, equipment, process, laboratory methods, cleaning 验证:计算机、设备、工艺、实验方法、清洁1.13 Training/qualification 培训/资质1.14 internal Audit Program内审规程1.15 Supplier Audit Program 供应商审计规程2 FACILITIES AND EQUIPMENT SYSTEM 厂房设施与设备系统I Facilities 厂房设施2.1 cleaning and maintenance 清洁与维护保养2.2 facility layout and air handling systems厂房设施布局与空气处理系统2.3 general air handling systems 全面的空气处理系统2.4 control system for implementing changes in the building实施在厂房方面变更的控制系统2.5 purified water and compressed air systems纯化水与压缩空气系统2.6 lighting, potable water, washing and toilet facilities, sewage and refuse -disposal照明、饮用水、清洗和盥洗设施、污水及垃圾处理2.7 sanitation of the building, use of rodenticides, fungicides, insecticides, cleaning and sanitizing agents厂房卫生、灭鼠剂、杀真菌剂、杀虫剂、清洗剂及消毒剂的使用2.8 drawings (as built) 布局图(厂房)II Equipment 设备"equipment installation and operational qualification设备安装和运行确认"adequacy of equipment design, size, material, construction and location 适当的设备设计、大小、材质、结构与位置"appropriate use of equipment operations substances, (lubricants, coolants, refrigerants, etc.) contacting products/containers/etc. 适当的设备运行时接触产品/容器等物质的使用(例如,润滑剂、冷却剂、制冷剂等等)"cleaning procedures and cleaning validation清洁规程与清洁验证"controls to prevent contamination, particularly with any pesticides or any other toxic materials, or other drug or non-drug chemicals 预防污染的控制措施、尤其是杀虫剂或其它有毒物质、或其它药物与非药物化学物质"qualification, calibration and maintenance of refrigerators and freezers 电冰箱和冷冻机的确认、校验和维护保养"equipment qualification, calibration and maintenance, including computer qualification/validation and security 设备确认、校准与维护保养,包括计算机确认/验证和安全"control system for implementing changes in the equipment实施在设备方面发生的变更的控制系统"equipment identification practices (where appropriate) 设备验收(如适用)"documented investigation into any unexpected discrepancy记录对任何未期望的不一致的调查3 MATERIALS SYSTEM物料系统3.1 training/qualification of personnel人员的培训/资质3.2 identification of components, containers, closures组分、容器密封件的鉴定3.3 inventory of components, containers, closures组分、容器密封件的目录3.4 storage conditions贮存条件3.5 storage under quarantine在隔离下的贮存3.6 representative samples collected, tested or examined using appropriate means 用适当的方法收集、检验和检查有代表性样品3.7 at least one specific identity test is conducted on each lot of each component每个组分每一批,至少做一个专属性实验3.8 a visual identification is conducted on each lot of containers and closures每批容器和密封件,应做一个目测确认3.9 testing or validation of supplier's test results for components, containers and closures对供应商的组分、容器和密封件的化验结果的检验或验证3.10 rejection of any component, container, closure not meeting acceptance requirements不符合可接受要求的组分、容器和密封件的拒收3.11 appropriate retesting/reexamination of components, containers, closures 组分、容器和密封件适当的复验/复查3.12 first in-first out use of components, containers, closures 组分、容器和密封件的先入先出3.13 quarantine of rejected materials 拒收物料的隔离3.14 water and process gas supply, design, maintenance, validation and operation 水与工艺用气的供应、设计、维护保养、验证和操作3.15 control system for implementing changes in the materials handling operations 实施在物料处理操作方面所发生的变更的控制系统3.16 qualification/validation and security of computerized or automated processes 计算机化或自动化过程的确认/验证和安全3.17 finished product distribution records by lot 最终产品按批的销售记录3.18 documented investigation into any unexpected discrepancy记录任何未期望的不一致的调查4 PRODUCTION SYSTEM生产系统4.1 training/qualification of personnel人员的培训/资质4.2 control system for implementing changes in processes实施在工艺方面所发生的变更的控制系统4.3 adequate procedure and practice for charge-in of components对于控制组分的适当的规程和操作4.4 identification of equipment with contents, and where appropriate phase of manufacturing and/or status 装有内容物的设备的标注,以及适当的生产阶段和/或状态4.5 calculation and documentation of actual yields and percentage of theoretical yields 实际产率和理论产率百分数的计算与记录4.6 complete batch production documentation全部的批生产记录4.7 established time limits for completion of phases of production 针对生产阶段完成而制订的时间限度4.8 implementation and documentation of in-process controls, tests, and examinations (e.g., pH, adequacy of mix, weight variation, clarity)过程控制、检测和检查(例如pH、混合的充分、重量差异和透明度)的实施与记录4.9 Justification and consistency of in-process specification and drug product final specifications 中间体的质量标准和成品的质量标准的合理性及其一致性4.10 final specifications 最终的质量标准4.11 prevention of objectionable microorganisms in non-sterile drug products 在非无菌产品中,有害微生物的预防4.12 pre-processing procedures (e.g., set-up, line clearance, etc.) 前处理规程(例如安装,清场等)4.13 equipment cleaning and use logs 设备清洁与使用日志4.14 master production and control records主要生产与控制记录(工艺规程)4.15 batch production and control records批生产与控制记录4.16 process validation, including validation and security of computerized or automated processes 工艺验证:包括计算机化和自动化工艺的验证和安全4.17 change control变更控制4.18 documented investigation into any unexpected discrepancy记录任何未期望的不一致的调查5 PACKAGING AND LABELING SYSTEM包装与标示系统5.1 training/qualification of personnel人员的培训/资质5.2 acceptance operations for packaging and labeling materials适当的包装和标示材料的操作5.3 control system for implementing changes in packaging and labeling operations实施在包装和标示操作方面所发生的变更的控制系统5.4 adequate storage for labels and labeling, both approved and returned after issued 标签和标示适当的贮存,包括已批准的和分发后退回的5.5 control of labels which are similar in size, shape, and color for different products对于不同的产品,标签在大小、形状和颜色相似方面的控制5.6 label verification system标签确认系统5.7 is gang printing used?使用大批量的印刷吗?5.8 adequate packaging records that will include specimens of all labels used 适当的包装记录,它应包括所有所用的标签的种类5.9 control of issuance of labeling, examination of issued labels and reconciliation of used labels标示分发的控制,被分发的标签和被使用的标签的物料衡算5.10 examination of the labeled finished product被标示的最终产品的检查5.11 adequate inspection (proofing) of incoming labeling进厂标示的适当的检查(校对)5.12 use of lot numbers, destruction of excess labeling bearinglot/control numbers 批号的使用,多余的带有批号/控制号标示的销毁5.13 physical separation between different labeling and packaging lines在不同标示和包装线之间的物理的分隔5.14 monitoring of printing devices associated with manufacturing lines与生产线相关的打印装置的监测5.15 line clearance, inspection and documentation生产线的清洁、检查和记录5.16 adequate expiration dates on the label关于标签的适当的有效期5.17 validation of packaging and labeling operations包装和标示操作的验证5.18 documented investigation into any unexpected discrepancy记录任何任何未期望的不一致的调查6 LABORATORY CONTROL SYSTEM实验室控制系统6.1 training/qualification of personnel人员的培训/资质6.2 adequacy of staffing for laboratory operations足够的实验室操作人员6.3 adequacy of equipment and facility for intended use适当的设备与设施6.4 calibration and maintenance programs for analytical instruments and equipment分析仪器和设备的校准与维护保养6.5 validation and security of computerized or automated processes计算机化或自动化过程的验证和安全6.6 reference standards; source, purity and assay, and tests to establish equivalency to current official reference standards as appropriate对照标准品:来源、纯度和含量、以及为建立与目前官方的对照标准品等效所做的检测项目6.7system suitability checks on chromatographic systems (e.g., GC or HPLC) 有关色谱系统(例如气相或高压液相)的系统适用性检查6.8 specifications, standards, and representative sampling plans质量标准、标准品和有代表性的取样计划6.9 adherence to the written methods of analysis遵循书面的分析方法6.10 validation/verification of analytical methods分析方法的验证/确认6.11 control system for implementing changes in laboratory operations 实施在实验室操作方面所发生的变更的控制系统6.12 Required testing is performed on the correct samples对于正确的样品,执行所要求的检验6.13 documented investigation into any unexpected discrepancy 记录任何未期望的不一致的调查6.14 complete analytical records from all tests and summaries of results来自所有检验的完整的分析记录和结果的总结6.15 quality and retention of raw data (e.g., chromatograms and spectra)原始数据的质量和保存(例如色谱图和光谱图)6.16 correlation of result summaries to raw data; presence of unused data结果总结与原始数据的相关性,未使用的数据的存在6.17 adherence to an adequate Out of Specification (OOS) procedure which includes timely completion of the investigation遵循一个适当的OOS 的规程,此规程包括调查的及时完成6.18 adequate reserve samples; documentation of reserve sample examination足够的留样、留样检查的文件6.19 stability testing program, including demonstration of stability indicating capability of the test methods稳定性检测的规程,包括检测方法的显示稳定性的证明。
MSC Circ 850 船舶防火系统和设备保养检查指南

.10 all fire hoses are hydrostatically tested;
.11 breathing apparatus air recharging systems checked for air quality;
.12 control valves of fixed fire-fighting systems should be inspected; and
importance of proper maintenance and inspection of fire-protection systems and appliances, approved
Guidelines for the maintenance and inspection of fire-protection systems and appliances, as set out in the
.2 all fixed fire-fighting system stop valves are in the proper open or closed position, dry pipe sprinkler systems have appropriate pressures as indicated by gauges;
.7 all hydrants are tested for operation;
.8 all antifreeze systems are tested for proper solutions;
.9 sprinkler system connections from the ship's fire main are tested for operation;
- 1、下载文档前请自行甄别文档内容的完整性,平台不提供额外的编辑、内容补充、找答案等附加服务。
- 2、"仅部分预览"的文档,不可在线预览部分如存在完整性等问题,可反馈申请退款(可完整预览的文档不适用该条件!)。
- 3、如文档侵犯您的权益,请联系客服反馈,我们会尽快为您处理(人工客服工作时间:9:00-18:30)。
ABS TECHNICAL PAPERS 2009 Hull Inspection and Maintenance Systems 1 Hull Inspection and Maintenance Systems S. G. Kalghatgi (Sr. Engineer, ABS, Houston TX) C. Serratella (Director, ABS, Houston TX) J. B. Hagan (Director, ABS, Houston TX)
Abstract Ship owners and managers strive to maintain a high level of structural integrity. The ship crews and shore staff perform inspections of hull structure on a regular basis to assess the hull condition. The inspection regimes require easy identification of problems. Besides owners, inspections and surveys are carried out by many agencies such as classification societies, insurers, vetting agencies, cargo surveyors, port state, coastal state and flag state authorities. All have an interest in the safe operation of the ship and ensuring that it is properly maintained. The effectiveness of these inspections is being continually challenged by the ever decreasing time that these vessels remain in port. In this paper a holistic, simple and quantifiable approach is proposed. This methodology employs the application of risk-based decision-making techniques. Risk-based techniques have demonstrated great potential in identifying key structural elements and focusing resources for maintenance and inspection. The proposed methodology for rationalizing the hull inspection program is via the development of a vessel-specific inspection program which includes a scoring system for identified inspection criteria and a list of target inspection areas (critical structural areas) for each compartment. The condition for each inspection criteria, depending upon the score, is displayed within the context of a simple traffic light system. This methodology can be applied by a trained and qualified owners’ representative. The scoring system can be utilized and analyzed to view the condition status of compartments, vessels, and a fleet. The scoring system also utilizes a system to trigger anomaly list generation, which can be used to manage the damages and repairs as well as create a repair list for future repair / drydock events. ABS TECHNICAL PAPERS 2009 2 Hull Inspection and Maintenance Systems KEY WORDS Hull inspection; risk-based approach; inspection criteria; critical structural area; compartment scoring system; anomaly.
INTRODUCTION The shipping industry needs a rationalized approach to perform inspections of hull structure and a methodology on what to inspect, when to inspect, where to inspect and how much to inspect. The benefits of hull inspection are usually well answered and known to all the inspection agencies. Traditionally ship owners and vessel managers have their in-house hull inspection schemes and programs to track, assess and maintain the hull structure. Inspections to assess hull condition are also performed by many agencies such as classification societies, insurers, vetting agencies, cargo surveyors, port state, coastal state and flag state authorities. All inspection data is collected in various forms, checksheets and reports. The ship owner is required in most cases to maintain a record of maintenance activities carried out on the hull structure. All the inspection data require the owner to have an effective inspection management system.
Classification societies and most of the other agencies perform inspection in a prescriptive manner or on an as-needed basis to assess the hull condition. The selected compartments are inspected based on the experience and work instructions provided to the inspector by their respective agencies. The presence of critical areas and suspect areas in a compartment may or may not be highlighted by the inspection agencies.
Ideally the inspection results from the various agencies are to be analyzed by the owners / managers and compiled into a repair / drydock specification list. Most of the inspection data may not be formatted to permit owners / managers to convert it easily into a repair specification as it may lack sufficient detail. This requires the owner to have a repair management system. At the time of repair there may be some unknowns and surprises as
the compartment condition is not completely known.
IACS PR33 encourages ship owners to have their own hull inspection and maintenance programs and schemes. Most of the major classification societies offer some form of hull inspection to be implemented by the owners’ representative.
In the following sections of this paper the various stakeholders on hull condition assessment and the various inspection regimes commonly found in marine industry are identified.