磨削烧伤检测操作指导书
磨削烧伤

磨削液的供液方法
磨削液对磨削效果的影响不仅取决于磨削液本身的性能,也 取决于磨削液是否可以有效的注入磨削区。常用的供液方法 有: 浇注法、高压冷却、内冷供液法、喷雾法供液法、超声波供 液法、浸渍砂轮。
• 浇注法
浇注法是用低压泵把磨削液输送到冷却喷嘴,借助磨削液 本身的重力作用,浇注到砂轮和工件的接触部位。 优点:简单易行 缺点:砂轮转速较高时,磨削液很难进入到磨削区。
工件温度的上升程度还 随着磨削液流量的变化 而变化。如右图所示, 流量越大,冷却作用越 明显,温度上升幅度则 越小。
• 清洗作用
磨削液侵入磨粒与工件之间,或砂轮的气孔里,将切屑或 脱落破碎的磨粒冲走洗净,避免影响加工精度或机床保养 。 影响因素: 渗透性、流动性、使用压力。 磨削液的主要作用见下图:
这种方法是使磨削液从 砂轮内孔或侧面进入砂轮 体内,依靠砂轮回转时的 离心作用,将磨削液通过 砂轮的气孔甩出。 优点:能有效地将磨削液 送入磨削区,在内圆磨削 时,效果很好。 缺点:由于砂轮气孔很小 ,磨削液必须经过良好的 过滤,否则,砂轮内气孔 易被杂质堵塞。另外,砂 轮周边会甩出磨削液,需 注意保护。
磨削液
• 使用目的
减小磨削力,降低磨削区温度、同时又迅速带走磨削热以 减少工件变形。
• 磨削液的作用
润滑作用、冷却作用、清洗作用。
• 润滑作用
液体渗透到模具与工件的接触区内,形成润滑膜,以减少 界面之间的摩擦,从而达到降低磨削力,减缓磨粒磨损, 延长砂轮寿命的作用。
• 冷却作用
一 迅速吸收热量以减缓工件温度上升,保证工件尺寸精 度,防止表面质量恶化。 二 磨削液使高温下的磨粒急剧冷却,产生热冲击效果, 促进磨粒的自锐作用。 冷却作用与磨削液导热系数、比 热和汽化有密切关系。
磨削烧伤检测操作指导书
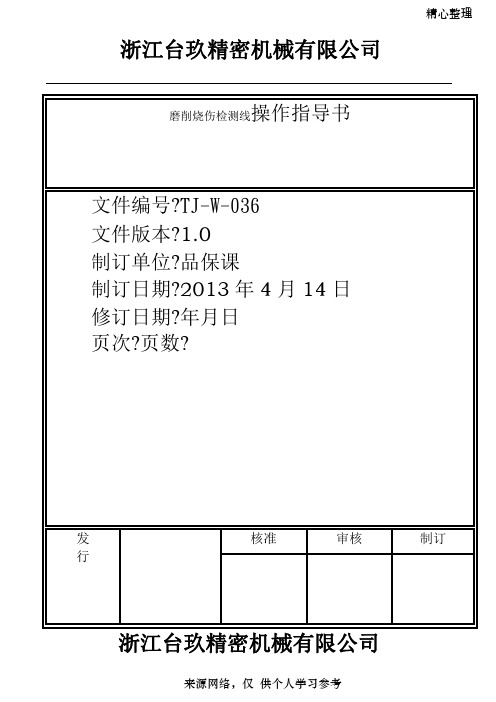
防锈
备注:1.检验必须按池1至池9依次进行检验,时间控制必须符合规定的时间。2.烧伤检验应由经过培训的品保课人员进行。
3.第1池需要加热至50摄氏度以上,所以试验前需加热,试验完成后需关闭开关
2.3检验范围
主要针对蜗杆磨加工工件。即齿部表面烧伤检验。
2.4磨削烧伤检验的判定和记录
A类:无磨削烧伤,表面呈现均匀的灰色.见图2中的无烧伤区域
ph值都须用专门的PH器具或溶度计来检验。
2)浸池定期更换,7、8池12周更换一次;2、4、6池一周更换;1池即洗涤池12周更换
一次;3、5酸池6周更换一次;9浸油池一年更换一次。
当酸溶液更新后,我们需用一件已烧伤的工件来检验腐蚀功能和浸泡时间,并对溶液的腐
蚀效果记录。
品保课
页次/页数
5/7
图1-A级无烧伤
图2B级轻微烧伤
图3D级严重磨削烧伤
图4E级烧伤
2.5检验频率
按客户要求
浙江台玖精密机械有限公司
标题:
腐蚀检测线操作指导书
文件编号
TJ-W-036
文件版本
1.0
制修订日期
2013年4月15日
制订单位
品保课
页次/页数
6/7
2.6磨削烧伤的维护和保养
1)因磨削烧伤线的功能有效性,应每周检验一次,并记录在相应表格中,各池的浓度或
磨削过程中会产生大量的磨削热,一部分被冷却液带走,另一部分被传导入加工件的浅表层内。并使工件表层温度升高。在磨
削热大量产生时会在齿表面形成回火层。当温度达到熔化
温度时,则经冷却液冷却形成二次淬火层,从而形成磨削烧伤。磨削烧伤工件表层会形成回火
层,其表层组织是回火马氏体,会和酸发生腐蚀反应,根据这个原理,我们可以使用硝酸腐蚀
磨削烧伤与其解决方案

磨削烧伤及其解决方案张国耀(郑州超微磨料具有限公司河南郑州450001)摘要:鉴于磨削过程中工件烧伤的问题一直困扰着产品的质量问题,从磨削烧伤的形成的机理、磨削烧伤的检查方法、磨削烧伤的分级、磨削烧伤的避免措施、磨削烧伤的影响因素、磨削烧伤解决方法。
让我们从基础对磨削烧伤形成认识、到对磨削烧伤的解决方法形成一整套的方案,其中:砂轮的选择在磨削烧伤过程中非常重要。
以避免我们生产中避免烧伤、遇到烧伤而找到合理的解决方法。
适用于外圆磨烧伤、内圆磨烧伤、平面磨烧伤、端面磨烧伤、无心磨烧伤等磨削方式。
关键词:磨削烧伤烧伤砂轮的选择烧伤解决方法烧伤原理烧伤级别一、定义:磨削时,由于磨削区域的瞬时高温(一般为900-1500℃)到相变温度以上时,形成零件表层金相组织发生变化(大多表面的某些部分出现氧化变色),使表层金属强度和硬度降低,并伴有残余应力产生,甚至出现微观裂纹,这种现象称为磨削烧伤。
二、磨削烧伤机理:当磨削表面产生高温时,如果散热措施不好,很容易在工件表面(从几十um 到几百 um)发生二次淬火及高温回火。
如果磨削工件表面层的瞬间温度超过钢种的AC1 点,在冷却液的作用下二次淬火马氏体,而在表层下由于温度梯度大,时间短,只能形成高温回火组织,这就使在表层和次表层之间产生拉应力,而表层为一层薄而脆的二次淬火马氏体,当承受不了时,将产生裂纹。
三、损伤的原因:(1)热处理的影响a)残余奥氏体磨削时残余奥氏体由于砂轮磨削时产生的热和压力而转变,同时可能伴随出现表面回火和磨削裂纹。
残余奥氏体量应控制在30%以内。
b)渗层碳浓度渗层碳浓度过高,在渗层组织中容易形成网状碳化物或过多的游离碳化物。
由于这种物质极硬,在磨削过程中可能出现局部过热倾向和发生表面回火。
渗层碳浓度过高,会使工件表面产生过多的残余奥氏体.从而导致烧伤和裂纹。
因此,表面碳浓度增加,则降低了磨削性能,一般表面碳浓度应控制在0.75% -0.95%范围以内。
酸浸法检查磨削烧伤

酸浸法简单易懂,一学就会,现介绍如下(包括样品图),本方法与GB/T17879中的方法略有差别,仅供参考:试剂:5%硝酸溶液3%盐酸酒精溶液5%碳酸钠溶液清水无水乙醇步骤:工件放在5%硝酸溶液浸蚀15~30秒→水中清洗20~30秒→3%盐酸酒精溶液浸蚀20~30秒后→水中清洗30秒→立即放入5%碳酸钠溶液中中和1min→无水乙醇中浸入约10秒→取出立即观察磨削表面是否有黑色区域(如附图),黑色区域的多少即为烧伤程度的大小。
至于合格程度可能要双方协议规定或参照GB/T17879-1999 《齿轮磨削后表面回火的浸蚀检验》这一阵忙,上网本是找个别的问题的,即然来了就说说,酸洗磨削烧伤是每个轴承厂必不可少的检验,但真的在下面进行酸洗的又是些工人,而且酸洗成份控制并不容易(随酸洗量的增加,使用时间变化,酸洗液成份要发生变化)我们酸洗的配方与JB1255的略有不同的,用的是1 脱脂无水碳酸钠25-35 g磷酸三钠25-35 g氢氧化钠10-20 g水玻璃2-3 g水1000毫升2 热水清洗水100%3 流动水清洗水100%4 酸洗硝酸15-25ml水 1000ml5 流动冷水洗水100%6 明化1铬酐130-150g硫酸4 g水1000ml7 流动水清洗水100%8 明化2盐酸(d=1.19)100-200ml二氯化锡2g金属锡100-200g水1000ml9 流动冷水洗水100%10 中和无水碳酸钠4-6%水余量11 流动冷水洗水100%12 防锈亚硝酸钠6-8kg无水碳酸钠1-2kg水余量酸洗后烧伤部位呈黑色,无烧伤呈灰色(白烧伤很少见,一般如磨削发生严重操作失误时可能会出现)磁弹仪测烧伤还是很有效的,但有时磁弹值会受附近电磁信号的干扰,还有就是检测位置比较受限,受探头的影响一些位置测不到,特别是内表面,另外测试效率低,测试仅及一条线,不可能所有表面都测到谢谢各位了.我搜索到了一份操作指导书,原文贴出,供大家参考:磨削烧伤痕迹的显示:1 浸蚀溶液配方:4%硝酸酒精浸蚀:工件在溶液中浸蚀2分钟2 清洗工件在清水中清洗2分钟。
磨削烧伤的检测方法

磨削烧伤的检测方法可能形成网状裂纹,它会导致齿面剥落.这当然是绝对不允许的。
用硬度测试法鉴别磨削烧伤的方法,并用超声波硬度计进行了实验,证明该方法简单易行,可以广泛应用于磨削加工中。
磨削烧伤及其常用检查方法在机械类产品中,很多重要零部件如轴承、齿轮、曲轴、凸轮轴、活塞销和万向节等,在热处理之后均需经过磨削加工。
相比之下,磨削时单位切削面积上的功率消耗远远超过其它加工方法,所转化热量的大部分会进入工件表面,因此容易引起加工面金相组织的变化。
在工艺参数、冷却方法和磨料状态选择不当的情况下,工件在磨削过程中极易出现相当深的金相组织变化层(即回火层),并伴随出现很大的表面残余应力,甚至导致出现裂纹,这就是所谓的磨削烧伤问题。
零部件的表面层烧伤将使产品性能和寿命大幅度地下降,甚至根本不能使用,造成严重的质量问题。
为此,生产企业一方面通过执行正确、科学的工艺规范,减轻和避免出现磨削烧伤现象;另一方面,加强对零部件的检验,及时发现不合格工件,并判断正在进行的磨削工艺状况。
但长期以来,对工件表面磨削烧伤的检验,除了最简单的目测法外,就是采用已延续多年的传统方法——酸洗法,即在被检零部件表面涂上酸液或将其浸入盛有按规定配制的酸液槽中。
之后(或在把工件取出后)根据表面呈现的不同颜色,对磨削烧伤的程度作出相应的判断。
一般地说,若色泽没有变化,就表明情况正常;而当颜色变成灰色,则说明已有烧伤情况存在,随着色泽变得越来越深,表示工件表面因温度更高,引起的磨削烧伤更为严重。
酸洗法具体如下:This is only a suggestion from my collegue ( Dino Calvanelli ) to find theburns on the gears此为有关过烧检测的建议:Clean each sample (part) to be inspected (free ofdirt,oil,grease,fingermarks,protective coatings,etc.).清洗产品,确保无灰尘、油污、手印、表面覆盖物等。
磨削作业指导书SOP

磨削作业指导书SOP
目的
本文档旨在提供磨削作业的详细指导,确保安全和高效地进行磨削作业。
适用范围
本指导书适用于所有从事磨削作业的员工。
安全要求
1. 在进行磨削作业前,员工必须穿戴个人防护装备,包括护目镜、手套和防护服。
2. 严禁穿戴松散的衣物或饰品,在作业时应将长发束起或戴头巾。
3. 确保磨削设备和工作区域的安全,包括检查设备的安全传感器、刀盘的磨损程度和保持工作区域的整洁。
操作指南
1. 首先,检查磨削设备的工作状态和连续性。
2. 将待加工的物体正确固定在磨削设备上,并调整加工角度和加工参数。
3. 启动磨削设备并确保加工物体的稳定性和精准性。
4. 在进行磨削过程中,注意观察磨削效果和加工物体的状态,及时调整操作和参数。
5. 磨削完成后,停止设备并将磨削物体移开。
6. 清理工作区域,包括清除磨屑和保养磨削设备。
故障处理
1. 如果设备出现故障或异常情况,请立即停止操作,并通知相关维修人员。
2. 在维修人员到达之前,严禁私自拆卸设备或进行维修操作。
紧急情况处理
1. 在发生紧急情况时,立即停止设备并按照应急计划执行。
2. 如果发生人身伤害,请及时寻求医疗帮助。
操作纪录和报告
1. 所有磨削作业都应记录操作人员、时间和作业类型。
2. 如出现异常情况、故障或事故,应立即上报相关部门,并详细记录事发经过和处理过程。
以上为磨削作业指导书的主要内容,请所有从事磨削作业的员工严格遵守本指导书的要求和操作流程。
如有任何疑问,请随时咨询相关负责人。
磨削烧伤的检测方法(5篇)

磨削烧伤的检测方法(5篇)第一篇:磨削烧伤的检测方法磨削烧伤的检测方法可能形成网状裂纹,它会导致齿面剥落.这当然是绝对不允许的。
用硬度测试法鉴别磨削烧伤的方法,并用超声波硬度计进行了实验,证明该方法简单易行,可以广泛应用于磨削加工中。
磨削烧伤及其常用检查方法在机械类产品中,很多重要零部件如轴承、齿轮、曲轴、凸轮轴、活塞销和万向节等,在热处理之后均需经过磨削加工。
相比之下,磨削时单位切削面积上的功率消耗远远超过其它加工方法,所转化热量的大部分会进入工件表面,因此容易引起加工面金相组织的变化。
在工艺参数、冷却方法和磨料状态选择不当的情况下,工件在磨削过程中极易出现相当深的金相组织变化层(即回火层),并伴随出现很大的表面残余应力,甚至导致出现裂纹,这就是所谓的磨削烧伤问题。
零部件的表面层烧伤将使产品性能和寿命大幅度地下降,甚至根本不能使用,造成严重的质量问题。
为此,生产企业一方面通过执行正确、科学的工艺规范,减轻和避免出现磨削烧伤现象;另一方面,加强对零部件的检验,及时发现不合格工件,并判断正在进行的磨削工艺状况。
但长期以来,对工件表面磨削烧伤的检验,除了最简单的目测法外,就是采用已延续多年的传统方法——酸洗法,即在被检零部件表面涂上酸液或将其浸入盛有按规定配制的酸液槽中。
之后(或在把工件取出后)根据表面呈现的不同颜色,对磨削烧伤的程度作出相应的判断。
一般地说,若色泽没有变化,就表明情况正常;而当颜色变成灰色,则说明已有烧伤情况存在,随着色泽变得越来越深,表示工件表面因温度更高,引起的磨削烧伤更为严重。
酸洗法具体如下:This is only a suggestion from my collegue(Dino Calvanelli)to find theburns on the gears此为有关过烧检测的建议:Clean each sample(part)to be inspected(free ofdirt,oil,grease,fingermarks,protective coatings,etc.).清洗产品,确保无灰尘、油污、手印、表面覆盖物等。
磨削烧伤检查规定

通常应对有回火显示的零件进行磁粉探伤检验,尤其是渗碳淬火硬化的零件。
7.2. 显微硬度计检查
7.2.1. 7.2.2. 7.2.3.
把要检查的部位用 800-1000 号的砂纸磨削 ,尽量少磨,能检查显微硬度即可。 工件要检查的部位不便于进行显微硬度检测,用线切割切下,并镶样。 用显微硬度计检测时,载荷 0.3Kg。对于用线切割切下零件的检验工件 0.05mm 处硬度≥695HV0.3,不允
7. 检验准则
7.1. 目视的外观与分类 未出现回火的零件在清洗和侵蚀后呈现均匀的灰色。局部回火区域在侵蚀后的零件上呈现深灰或黑色。通常,
随着颜色变的越深暗,说明回火烧伤程度越严重。如果在磨削过程中出现严重过热,将导致再硬化,再硬化
区域是一块白色或浅颜色的未回火马氏体,周围是黑色回火面。
所有的磨削后回火,尤其是再硬化的烧伤(即未回火马氏体)会影响零件的寿命,但零件仍可使用。
a)避免直接接触酸碱、溶剂。
b)将酸加入水中或酒精中,防止加反。
c)浸泡箱不用时加盖盖好。
d)遵守可燃和易燃液体储存及使用的安全措施。
有烧伤
无烧伤
机后要检查磨销烧伤。
做好记录。
10. 维护和管理 根据溶液的使用程度或当新配制溶液时,为检验溶液的性能,建议用该溶液侵蚀已知有回火显示的样品零件。
在侵蚀和检验后,该样品应再防锈保护备用,这类样品应定期更换。
根据使用程度,应定期检验溶液的浓度和杂质。
样品和溶液每 7 天更换一次。
11. 安全和环境保护。
磨削烧伤检查规定 1. 目的
保证工件在磨削工序中质量得到保证。 2. 适用范围
本标准规定了用化学侵蚀方法对磨削表面的局部过热进行检验及其分类的标准操作程序和要求,同时硬度法 作为对化学侵蚀方法的校核。 本标准适用于工件在热处理后,进行磨削工序中的检查。对于调质后、高频淬火后、渗碳淬火后的工件都适 用。 本标准不适用氮化零件和不锈钢零件。 化学侵蚀方法对表面硬度的变化的反映比大多数硬度测试方法更为敏感。 表面回火侵蚀检验应在表面磨削后,并在进一步精加工工序之前进行。比如连杆在珩磨前、曲柄销在研磨前。 3. 引用标准 GB/T 17879-1999 齿轮磨削后表面回火的浸蚀检验 4. 设备 4.1. 容器的材料与容器内溶液不得发生反应,也不得损伤被处理的零件。所有容器都应贴上所盛溶液的标签,并 在不用时盖好。本公司采用玻璃烧杯,并用平板玻璃盖好。 4.2. 被检验区域照明 被检验区域应有充分的照明,没有阴影和反射。摧荐被检验区域的光照度应不低于 3200lx。 4.3. 计时装置 应使用适当的计时器(秒表)。保证一组中的所有零件处理过程一致。 4.4. 清洗装置 应采用碱清洗器、蒸汽去油器、溶液清洗装置或相应的清洗装置。 5. 试剂 所有的化学试剂应为工业级或更纯的等级。 5.1. 清洗材料 所有清洗材料应保证能去除所有的污渍、磨粒和油渍,使被检表面可形成不破水膜。不破水膜是指表面用低 于 40℃的清水漂洗干净后,水膜至少应在 15S 内保持不破。 5.2. 硝酸 硝酸密度ρ=1.42Kg/l 5.3. 盐酸 盐酸密度ρ=1.19Kg/l 5.4. 酒精 应使用清洁的、不含油等杂质的甲醇或变性乙醇。 5.5. 水 清洁、无杂质。 5.6. 碱溶液 应使用 4%——6%的氢氧化钠溶液,其 PH≥10。 6. 检验程序 工件清洗→清洗后零件表面应达到能形成不破水膜→侵蚀→检验 6.1. 清洗 a)采用蒸汽清洗。 b)碱洗或超声波清洗。 6.2. 侵蚀 6.2.1. 腐蚀液的配制。
- 1、下载文档前请自行甄别文档内容的完整性,平台不提供额外的编辑、内容补充、找答案等附加服务。
- 2、"仅部分预览"的文档,不可在线预览部分如存在完整性等问题,可反馈申请退款(可完整预览的文档不适用该条件!)。
- 3、如文档侵犯您的权益,请联系客服反馈,我们会尽快为您处理(人工客服工作时间:9:00-18:30)。
品保课
页次/页数
4/7
表1
浸池
过程
浸池成分
浓度
温度℃
PH值
时间
各部分作用
1
热去脂
碱性去油脂剂
(4-5)%
》50
>10
>15分钟
去油脂
2
冷冲洗
氢氧化钠水溶液
(4-6)%
25
10-11.5
3分钟
去油脂
3
酸蚀
硝酸水溶液
(2-4)%
室温
<7
5-8秒
腐蚀
4
冷冲洗
氢氧化钠水溶液
(4-6)%
室温
11-12.5
ph值都须用专门的PH器具或溶度计来检验。
2)浸池定期更换,7、8池12周更换一次;2、4、6池一周更换;1池即洗涤池12周更换
一次;3、5酸池6周更换一次;9浸油池一年更换一次。
当酸溶液更新后,我们需用一件已烧伤的工件来检验腐蚀功能和浸泡时间,并对溶液的腐
蚀效果记录。
B类:轻微烧伤,磨削烧伤不连续,较窄的浅色显示;此类磨削烧伤降低表面硬度不显著。见图2
D类:较重的磨削烧伤,磨削烧伤连续较宽的深色显示。此类磨削烧伤降低表面硬度10HV或更多,如图3
E类:重新硬化,重新硬化的区域为白斑,周围是黑色的D级区域。这些白斑是未回火马氏体,对腐蚀没反应,见图4
国标中,根据磨削烧伤的面积,磨削烧伤又分为3等级,B类分级见表2
页次/页数
2/7
修订履历
修订日期
修订页次
原版本
新版本
修订摘要
标题:
磨削烧伤检测线操作指导书
文件编号
TJ-W-036
文件版本
1.0
制修订日期
2013年4月14日
制订单位
品保课
页次/页数
3/7
1.目的:规定渗碳钢工件做磨削烧伤检查的过程和责任以及对检测结果的判定和记录
2.检验流程
2.1磨削烧伤检验的方法
浙江台玖精密机械有限公司
磨削烧伤检测线操作指导书
文件编号TJ-W-036
文件版本1.0
制订单位品保课
制订日期2013年4月14日
修订日期年月日
页次页数
发
行
核准
审核
制订
浙江台玖精密机械有限公司
标题:
磨削烧伤检测线操作指导书
文件编号
TJ-W-036
文件版本
1.0
制修订日期
2013年4月15日
制订单位
品保课
品保课
页次/页数
5/7
图1-A级无烧伤
图2 B级轻微烧伤
图3 D级严重磨削烧伤
图4 E级烧伤
2.5检验频率
按客户要求
浙江台玖精密机械有限公司
标题:
腐蚀检测线操作指导书
文件编号
TJ-W-036
文件版本
1.0
制修订日期
2013年4月15日
制订单位
品保课
页次/页数
6/7
2.6磨削烧伤的维护和保养
1)因磨削烧伤线的功能有效性,应每周检验一次,并记录在相应表格中,各池的浓度或
磨削过程中会产生大量的磨削热,一部分被冷却液带走,另一部分被传导入加工件的浅表层内。并使工件表层温度升高。在磨
削热大量产生时会在齿表面形成回火层。当温度达到熔化
温度时,则经冷却液冷却形成二次淬火层,从而形成磨削烧伤。磨削烧伤工件表层会形成回火
层,其表层组织是回火马氏体,会和酸发生腐蚀反应,根据这个原理,我们可以使用硝酸腐蚀
表2表面烧伤级别
级别
回火表面积的最大百分比%
B1
10
B2
25
B3
无限制
蜗杆烧伤的验收和判废准则:A类合格,B1、B2、B3需提交客户仲裁。D、E类烧伤则判废
浙江台玖精密机械有限公司
浙江台玖精密机械有限公司
标题:
腐蚀检测线操作指导书
文件编号
TJ-W-036
文件版本
1.0
制修订日期
2013年4月15日
制订单位
1-3分钟
防锈
备注:1.检验必须按池1至池9依次进行检验,时间控制必须符合规定的时间。2.烧伤检验应由经过培训的品保课人员进行。
3.第1池需要加热至50摄氏度以上来自所以试验前需加热,试验完成后需关闭开关
2.3检验范围
主要针对蜗杆磨加工工件。即齿部表面烧伤检验。
2.4磨削烧伤检验的判定和记录
A类:无磨削烧伤,表面呈现均匀的灰色.见图2中的无烧伤区域
的方法检验。这里我们采用浸池的方式进行。
2.2磨削烧伤检测线的结构和检验流程
烧伤检测线的结构如图。检验流程见表1,检验的步骤按池1到池9进行。各池的化学成分及浸泡时间见表1
图1:烧伤检测线结构
浙江台玖精密机械有限公司
标题:
腐蚀检测线操作指导书
文件编号
TJ-W-036
文件版本
1.0
制修订日期
2013年4月15日
5秒
去酸
5
酸蚀
盐酸水溶液
(2-4)%
室温
<7
30-60秒
脱色
6
冷洗
氢氧化钠溶液
(4-6)%
室温
11-12.5
5秒
去酸
7
中和
碳酸钠水溶液
(4-6)%
室温
10-11.5
3分钟
中和酸
8
冷洗
碳酸钠水溶液
(4-6)%
室温
10-11.5
5秒
去碱
9
吹风机
去水
10
浸油
防锈油
----------
室温
----------