机械加工零件表面烧伤的金相检验
齿轮零件磨削烧伤的危害、检测和预防

齿轮零件磨削烧伤的危害、检测和预防作者:许红平鲁建锋吴伟明徐嘉军来源:《专用汽车》 2019年第1期齿轮类零件作为机构中的重要零部件,在渗碳淬火后往往要进行磨削加工。
在磨削加工工艺中,砂轮与零件的接触区会因摩擦产生大量热量,而大部分热量会通过传导进入零件浅表层,容易导致表层金相组织的变化。
若磨削参数设置和砂轮选择不当,在加工的过程中,会引起表层金相组织改变,并出现较大的残余应力,形成“磨削烧伤”。
零件磨削烧伤会使零件表层的耐磨性、耐腐蚀性和接触疲劳强度降低,使用寿命大大降低,严重的情况下会出现裂纹,从而引发质量问题。
本文通过研究淬火类齿轮的磨削烧伤现象,总结和分析了磨削烧伤的种类和危害,提出了针对不同种类烧伤的不同检测方法,并在此基础上探讨了磨削烧伤的预防措施。
1.磨削烧伤的种类齿轮零件磨削加工的过程中,接触区域的瞬时高温(可达looooc)使得零件表面的金相组织产生局部变化。
根据磨削烧伤表面组织结构的不同,可以将磨削烧伤分成两类。
1.1回火烧伤当磨削接触区表面层温度显著超过马氏体转变温度,而低于相变临界温度Acl的时候,零件表面马氏体产生回火,转变成硬度较低的索氏体和屈氏体,这种烧伤称为“回火烧伤”,如图l(a)所示。
此时该表面的硬度一般为HRC51~57。
1.2二次淬火烧伤淬火钢的马氏体组织在7500C~8000C以上的磨削高温下转变成奥氏体。
如果冷却速度较低,则会重新变为马氏体,零件表层比原淬火硬度稍有提高,一般在HRC63左右。
但此变质层性能稳定性较差,脆性较高,二次淬火烧伤区域周围通常伴有一圈严重的回火层,如图1(b)所示。
2.磨削烧伤和磨削裂纹磨削烧伤的变质层内存在较大的残余应力,当残余应力超过材料的极限强度时,容易导致裂纹的出现。
磨削烧伤不一定伴随磨削裂纹出现,但是磨削裂纹通常都伴随磨削烧伤产生。
磨削裂纹的方向一般与砂轮的轴向进给方向垂直,如图2(a)所示。
齿面存在裂纹后,润滑油会侵入裂纹。
磨削烧伤的检测方法

磨削烧伤的检测方法可能形成网状裂纹,它会导致齿面剥落.这当然是绝对不允许的。
用硬度测试法鉴别磨削烧伤的方法,并用超声波硬度计进行了实验,证明该方法简单易行,可以广泛应用于磨削加工中。
磨削烧伤及其常用检查方法在机械类产品中,很多重要零部件如轴承、齿轮、曲轴、凸轮轴、活塞销和万向节等,在热处理之后均需经过磨削加工。
相比之下,磨削时单位切削面积上的功率消耗远远超过其它加工方法,所转化热量的大部分会进入工件表面,因此容易引起加工面金相组织的变化。
在工艺参数、冷却方法和磨料状态选择不当的情况下,工件在磨削过程中极易出现相当深的金相组织变化层(即回火层),并伴随出现很大的表面残余应力,甚至导致出现裂纹,这就是所谓的磨削烧伤问题。
零部件的表面层烧伤将使产品性能和寿命大幅度地下降,甚至根本不能使用,造成严重的质量问题。
为此,生产企业一方面通过执行正确、科学的工艺规范,减轻和避免出现磨削烧伤现象;另一方面,加强对零部件的检验,及时发现不合格工件,并判断正在进行的磨削工艺状况。
但长期以来,对工件表面磨削烧伤的检验,除了最简单的目测法外,就是采用已延续多年的传统方法——酸洗法,即在被检零部件表面涂上酸液或将其浸入盛有按规定配制的酸液槽中。
之后(或在把工件取出后)根据表面呈现的不同颜色,对磨削烧伤的程度作出相应的判断。
一般地说,若色泽没有变化,就表明情况正常;而当颜色变成灰色,则说明已有烧伤情况存在,随着色泽变得越来越深,表示工件表面因温度更高,引起的磨削烧伤更为严重。
酸洗法具体如下:This is only a suggestion from my collegue ( Dino Calvanelli ) to find theburns on the gears此为有关过烧检测的建议:Clean each sample (part) to be inspected (free ofdirt,oil,grease,fingermarks,protective coatings,etc.).清洗产品,确保无灰尘、油污、手印、表面覆盖物等。
磨削烧伤的检测方法

磨削烧伤的检测方法可能形成网状裂纹,它会导致齿面剥落.这当然是绝对不允许的。
用硬度测试法鉴别磨削烧伤的方法,并用超声波硬度计进行了实验,证明该方法简单易行,可以广泛应用于磨削加工中。
磨削烧伤及其常用检查方法在机械类产品中,很多重要零部件如轴承、齿轮、曲轴、凸轮轴、活塞销和万向节等,在热处理之后均需经过磨削加工。
相比之下,磨削时单位切削面积上的功率消耗远远超过其它加工方法,所转化热量的大部分会进入工件表面,因此容易引起加工面金相组织的变化。
在工艺参数、冷却方法和磨料状态选择不当的情况下,工件在磨削过程中极易出现相当深的金相组织变化层(即回火层),并伴随出现很大的表面残余应力,甚至导致出现裂纹,这就是所谓的磨削烧伤问题。
零部件的表面层烧伤将使产品性能和寿命大幅度地下降,甚至根本不能使用,造成严重的质量问题。
为此,生产企业一方面通过执行正确、科学的工艺规范,减轻和避免出现磨削烧伤现象;另一方面,加强对零部件的检验,及时发现不合格工件,并判断正在进行的磨削工艺状况。
但长期以来,对工件表面磨削烧伤的检验,除了最简单的目测法外,就是采用已延续多年的传统方法——酸洗法,即在被检零部件表面涂上酸液或将其浸入盛有按规定配制的酸液槽中。
之后(或在把工件取出后)根据表面呈现的不同颜色,对磨削烧伤的程度作出相应的判断。
一般地说,若色泽没有变化,就表明情况正常;而当颜色变成灰色,则说明已有烧伤情况存在,随着色泽变得越来越深,表示工件表面因温度更高,引起的磨削烧伤更为严重。
酸洗法具体如下:This is only a suggestion from my collegue ( Dino Calvanelli ) to find theburns on the gears此为有关过烧检测的建议:Clean each sample (part) to be inspected (free ofdirt,oil,grease,fingermarks,protective coatings,etc.).清洗产品,确保无灰尘、油污、手印、表面覆盖物等。
金相知识-表面处理金相检验

零件渗碳后直接淬火其金相组织有何特点? 零件的表面渗碳层为粗针状的马氏体和较多的残
留奥氏体,虽然沿晶的网状碳化物不多,但因内应力 过大,容易产生裂纹。零件心部基体为板条马氏体。
简述渗碳淬火工件的常见缺不均匀;
20CrMnTi经渗碳加回火后,从表层到心部的各层 组织是什么?
表层是高碳针状回火马氏体加少量残留奥氏体; 次表层为回火马氏体加回火托氏体;心部为低碳板 条马氏体加少量铁素体。
生产中发现20钢在可控气氛炉920℃渗碳、860℃淬 油后,表层硬度上不去。原因何在?
20钢渗碳后表层变为高碳钢,心部为低碳钢。 淬火温度和保温时间的选择要以既要考虑表层能得 到高硬度,但渗层又不能产生网状渗碳体(变脆)、 心部得到板条马氏体,消除铁素体为原则。在此原 则下淬火温度尽量提高,保温时间不宜过长。
网状和针状的二次渗碳体;表面全脱碳;渗碳过渡层 太陡;碳化物聚集成大块状;过热组织(即粗大马氏 体针);渗层较多的残余奥氏体,心部较多的铁素体; 黑色组织(晶界出现托氏体和贝氏体组织)。
20CrMo钢正火后能获得什么组织组成物,为什么? 钼对正火(或热轧)态钢而言,能使组织从珠光
体形态向贝氏体形态转变,20CrMo钢经正火后即 为贝氏体组织;55SiMnMo弹簧钢,以及近来研制 的超高强度钢32CrMoVA,由于含有元素Mo,正火 或淬火后均能获得贝氏体组织。
要薄,称为软氮化(亦称氮碳共渗)。
举例
轮齿工作 面和齿顶
渗碳
裂纹位置 在齿根槽
底面
3.3 在中温(800 ~ 860 ℃)阶段,基体组织大
部分为奥氏体和铁素体(两相区),碳、氮原子的 扩散速度都比较大,浓度也比较高,称为碳氮共渗 (氰化)。 4、化学热处理的分类
磨削烧伤实验报告
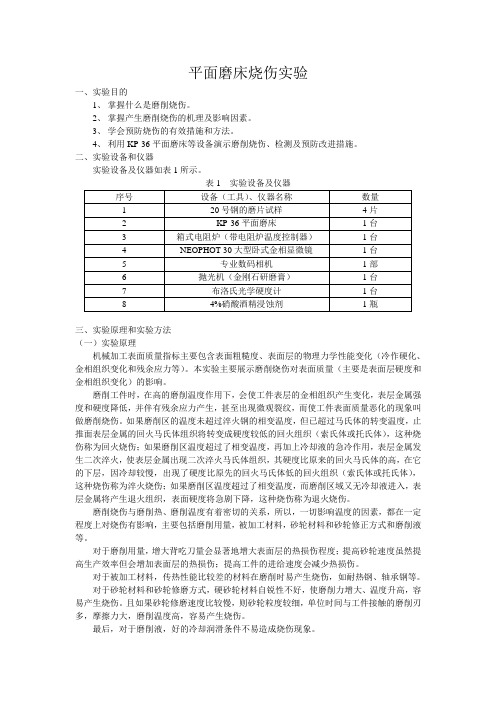
平面磨床烧伤实验一、实验目的1、掌握什么是磨削烧伤。
2、掌握产生磨削烧伤的机理及影响因素。
3、学会预防烧伤的有效措施和方法。
4、利用KP-36平面磨床等设备演示磨削烧伤、检测及预防改进措施。
二、实验设备和仪器实验设备及仪器如表1所示。
三、实验原理和实验方法(一)实验原理机械加工表面质量指标主要包含表面粗糙度、表面层的物理力学性能变化(冷作硬化、金相组织变化和残余应力等)。
本实验主要展示磨削烧伤对表面质量(主要是表面层硬度和金相组织变化)的影响。
磨削工件时,在高的磨削温度作用下,会使工件表层的金相组织产生变化,表层金属强度和硬度降低,并伴有残余应力产生,甚至出现微观裂纹,而使工件表面质量恶化的现象叫做磨削烧伤。
如果磨削区的温度未超过淬火钢的相变温度,但已超过马氏体的转变温度,止推面表层金属的回火马氏体组织将转变成硬度较低的回火组织(索氏体或托氏体),这种烧伤称为回火烧伤;如果磨削区温度超过了相变温度,再加上冷却液的急冷作用,表层金属发生二次淬火,使表层金属出现二次淬火马氏体组织,其硬度比原来的回火马氏体的高,在它的下层,因冷却较慢,出现了硬度比原先的回火马氏体低的回火组织(索氏体或托氏体),这种烧伤称为淬火烧伤;如果磨削区温度超过了相变温度,而磨削区域又无冷却液进入,表层金属将产生退火组织,表面硬度将急剧下降,这种烧伤称为退火烧伤。
磨削烧伤与磨削热、磨削温度有着密切的关系,所以,一切影响温度的因素,都在一定程度上对烧伤有影响,主要包括磨削用量,被加工材料,砂轮材料和砂轮修正方式和磨削液等。
对于磨削用量,增大背吃刀量会显著地增大表面层的热损伤程度;提高砂轮速度虽然提高生产效率但会增加表面层的热损伤;提高工件的进给速度会减少热损伤。
对于被加工材料,传热性能比较差的材料在磨削时易产生烧伤,如耐热钢、轴承钢等。
对于砂轮材料和砂轮修磨方式,硬砂轮材料自锐性不好,使磨削力增大、温度升高,容易产生烧伤。
且如果砂轮修磨速度比较慢,则砂轮粒度较细,单位时间与工件接触的磨削刃多,摩擦力大,磨削温度高,容易产生烧伤。
磨削烧伤、磨削裂纹及控制措施
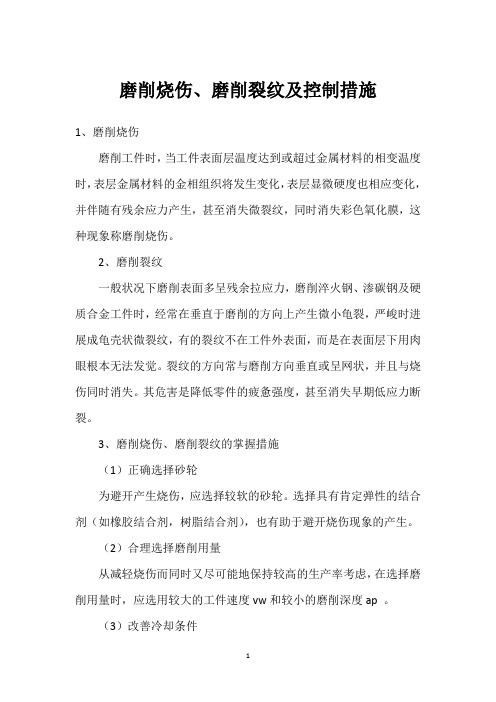
磨削烧伤、磨削裂纹及控制措施1、磨削烧伤磨削工件时,当工件表面层温度达到或超过金属材料的相变温度时,表层金属材料的金相组织将发生变化,表层显微硬度也相应变化,并伴随有残余应力产生,甚至消失微裂纹,同时消失彩色氧化膜,这种现象称磨削烧伤。
2、磨削裂纹一般状况下磨削表面多呈残余拉应力,磨削淬火钢、渗碳钢及硬质合金工件时,经常在垂直于磨削的方向上产生微小龟裂,严峻时进展成龟壳状微裂纹,有的裂纹不在工件外表面,而是在表面层下用肉眼根本无法发觉。
裂纹的方向常与磨削方向垂直或呈网状,并且与烧伤同时消失。
其危害是降低零件的疲惫强度,甚至消失早期低应力断裂。
3、磨削烧伤、磨削裂纹的掌握措施(1)正确选择砂轮为避开产生烧伤,应选择较软的砂轮。
选择具有肯定弹性的结合剂(如橡胶结合剂,树脂结合剂),也有助于避开烧伤现象的产生。
(2)合理选择磨削用量从减轻烧伤而同时又尽可能地保持较高的生产率考虑,在选择磨削用量时,应选用较大的工件速度vw和较小的磨削深度ap 。
(3)改善冷却条件① 采纳高压大流量法此法不但可以增加冷却作用,而且也增加了对砂轮的冲洗作用,使砂轮不易堵塞。
② 安装带空气挡板的喷嘴此法可以减轻高速回转砂轮表面处的高压附着气流作用,使磨削液能顺当喷注到磨削区。
③ 采纳磨削液雾化法或内冷却法采纳特地装置将磨削液雾化,使其带走大量磨削热,增加冷却效果;也可采纳内冷却砂轮,其工作原理如图所示。
经过严格过滤的磨削液由锥形套1经空心主轴法兰套2引入砂轮的中心腔3内,由于离心力的作用,磨削液经由砂轮内部有径向小孔的薄壁套4的孔隙甩出,直接浇注到磨削区。
图内冷却砂轮结构1-锥形盖2-主轴法兰套3-砂轮中心腔4-薄壁套。
金属学8工件表面处理后的金相检验

渗碳层的金相检验
• 组织检验 评定马氏体、奥氏体、碳化物、心部铁素体
• 渗层深度的测定 ①断口法 ②金相法 ③显微硬度法 ④剥层化学分析法
渗碳后缺陷组织
渗碳后缺陷组织
鉴定高频感应淬火淬硬层
• 感应淬火用钢常选用中碳钢和中碳合金钢,如40钢、45钢、40C r等,感应淬火和普通淬火相比较,有变形小、加热时间短而氧 化脱碳少、表面硬度高、缺口敏感性小等优点。
• 相变特点:加热速度快时间短加热层浅从加热到淬火通常只有 几秒或几十秒,相变在一个温度区域短时间进行
检验硬化层深度
硬度法 • GB/T 11354—2005《钢铁零件渗氮层深度测定和金相检验》标
准规定了硬度法测定渗氮层深度的方法。要求用2.94N(0.3kg) 载荷下,维氏硬度从表面测至高出心部硬度50HV单位(过渡层 平缓时可测至高出心部30HV)处作为渗氮层深度界限。
• 同渗碳层的测定一样,当有争议时,渗氮层的深度测定以显微 硬度法为惟一仲裁方法。
表层显微组织为细针状马氏体和均匀分布的细粒状渗碳 体,硬度高达58~64 HRc;
芯部组织是板条马氏体或铁素体加珠光体,硬度为28~42 HRc,所以芯部具有较高的韧性和适当的强度。
20CrMnTi钢渗碳缓冷组织
珠光体+各种形状碳化物→珠光体→珠光体+铁素体→基体组织
渗碳缓冷后表层过共析层
渗碳淬回火状态组织
20crmnti钢渗碳缓冷组织珠光体各种形状碳化物珠光体珠光体铁素体基体组织渗碳缓冷后表层过共析层渗碳淬回火状态组织针状马氏体各种形状碳化物残余奥氏体针状马氏体残余奥氏体针状马氏体残余奥氏体板条马氏体基体组织板条马氏体渗碳层的金相检验组织检验评定马氏体奥氏体碳化物心部铁素体渗层深度的测定断口法金相法显微硬度法剥层化学分析法渗碳后缺陷组织渗碳后缺陷组织鉴定渗氮层纯铁
浅析利用金相法检验零件是否过热

L I里 垫处 。
浅 析 利 用 金 相 法 检 验 零 件 是 否 过 热
焦作煤业 ( 团)新乡能源有限公司 ( 集 河南 43 3 ) 张 复宝 5 6 4
所谓 过热 ,即晶粒长 大 ,纤维 组织 粗化 ,使 组织 应 力和热应力显著增 加 ,所 以过热常作 为零件 淬裂 的原 因
M W ( 01 0 1 2 0 1 0)
性能达到 图样技术要求。
4 .结语
党 的十七大报告 指出 ,必须 把建设 资源节 约型 、环
参磊 工 ̄n 热 锻 造2 0 第750.com J T 处 WWW.m et0 年ng 期 铸 a1 ki 79 1 wor
j 、 , , t 0、 _ , 、. 、 — j 、 , 、 tP 、 、 0 、 t: 、 0 t 、 0 t ) 0
产 ,以减少不必要的能源浪费 。 热处理工艺参数及工件性能检测结果如下。 加热设 备 :7 k 箱式炉 ;淬 火温度 :8 0C;淬火 5W 2 ̄
显得粗 大些 。故对 中碳 钢来讲 ,只有在过 热 比较严重 的
情况下淬火 ,马氏体才显 出条状 。
之一 。由于零 件的过热 ,使材 料 冲击 韧度显 著下 降 ,虽 不至于报 废 , 但将 严重影响零 件 的使 用寿命 , 别是 零 特
件受到冲击载荷 时 ,反应尤为突 出。 那么 ,如何用金相方法去检验零件是否过热呢?
对 高 碳 钢 和 高 碳 合 金 钢 来 说 ,在 正 常 温 度 下 淬 火 ,得 到 “ 隐针状 ” 组 织 ,称为 隐针 状 马 氏体 。只有
在 过热 较严 重 的情 况 下淬 火 ,马 氏体 才 出现 呈 交叉 分 布 的 叶状组织 ,其 过热 程度 越 大 ,残余 奥 氏体 的量 就
- 1、下载文档前请自行甄别文档内容的完整性,平台不提供额外的编辑、内容补充、找答案等附加服务。
- 2、"仅部分预览"的文档,不可在线预览部分如存在完整性等问题,可反馈申请退款(可完整预览的文档不适用该条件!)。
- 3、如文档侵犯您的权益,请联系客服反馈,我们会尽快为您处理(人工客服工作时间:9:00-18:30)。
收稿日期:20190628 作者简介:焦丽(1975),女,河北石家庄人,高级工程师 ,主要从事金相检测及零部件的失效分析工作。
Email:1025496268@qq.com
《热处理》 2019年第 34卷 第 4期
·39·
部温度超过工件的回火温度(一般高于 300℃),从 而发生再次回火的现象。宏观表现为,由于不同程 度的氧化膜反射光干涉状态的不同而呈现不同的颜 色。从黄、褐、紫、青 灰 到 黑 色,表 示 氧 化 膜 逐 渐 增 厚,也表明磨削烧伤程度的逐次增大。氧化膜颜色 只是磨削烧伤的一种外观特征,有时因表面受热氧 化或冷却的复杂程度的影响,工件外观并无异常,但 酸蚀后却可见明显的斑状、条状缺陷,或黑或白,可 根据显微组织的特征作进一步验证。磨削烧伤有时 会表现为隐性缺陷,所以隐患更大。
cuttingheatislargeenoughtopermitpartcasetoreachahighertemperature,thustransformationtooccursandto
developacasewherenatureischanged.Inviewoftheabove,themeasurespreventingpartfrom burningmaybe
hardness,moreserious,willcauseparttocrack,eventobescrapped.Inaddition,wireelectrodecuttingislikely
toburnpart,too.Substantially,theburningofpartisconcernedwiththateithergrindingheatorwireelectrode
1 磨削烧伤
磨削是提高产品加工精度、保证零件表面质量 的必要手段,通常在零件热处理后进行。磨削过程
包括摩擦、挤压和切削三部分,实质上是磨轮对零件 表面的摩擦和挤压。磨削加工与车、铣和刨等机加 工方法的不同之处在于:磨削速度高(为车、铣加工 的 20倍);磨屑尺寸小,散热效果差,其单位切削面 积消耗的功率 90%以上都转换为热能,磨削热的大 量积累可使磨削面温度高达 800~1000℃甚至更 高[12],从而在表面形成很大的温度梯度,加上切削 应力的产生,不仅会引起零件表层显微组织的变化, 还会产生残余应力,导致零件表层淬火或回火,甚至 产生磨削裂纹,严重影响零件的力学性能和使用寿 命。从磨削烧伤大致有回火烧伤、淬火回火烧伤和 磨削裂纹三种情况。 1.1 磨削烧伤的表现形式和金相检验 1.1.1 回火烧伤
duregrindingprocess,forexample,excessivegrindingallowance,unsufficient
cooling,useofunallowableabrasivewheelandsoon.Theburningwillcauseparttoexhibitlowersurface
MetallographicTestingforSurfaceBurningofMachinedParts
JIAOLi,ZHAOYingjun,XUXiangyang
(HebeiHuabeiDieselEngineCo.,Ltd.,Shijiazhuang050081,HebeiChina)
Abstract:Thehardenedpartsofhighcarbonsteelorthepartscarburizedandhardenedallaresubjectedtoburning
adopted.
Keywords:grinding;wireelectrodecutting;burning;heattreatment
0 引言
众所周知,机械零件均需采用车、铣、刨、镗、钻、 磨或线切割等方法进行加工。在加工过程中,可能 会因机床等加工设备或工艺和操作不当等因素而损 伤工件,对后续的加工及使用产生不良影响。本文 对经磨削和线切割加工的零件的表面烧伤进行了金 相检验,分析了烧伤表面的形貌和发生烧伤的机制, 结合生产实践中的案例,揭示了金相检验与烧伤的 类型和严重程度之间的内在联系,为准确判断磨削 烧伤和线切割烧伤提供参考。
的显微组织为回火屈氏体(400℃左右)、回火索氏 体(500℃左右)或二者的混合组织,见图 2(c)。从 相变机制分析,磨削产生的高温致使马氏体分解并 析出碳化物,降低了材料的耐蚀性,从而呈现深灰色 或黑色。因相变所形成的索氏体或屈氏体硬度一般 为 32~45HRC,远低于 50HRC以上的回火马氏 体,所以回火烧伤会造成零件表面不同程度的软化, 导致材料进一步损伤。
金相检验表明,回火烧伤的微观形貌为带状、条 状擦伤或斑点状缺陷。图 1为 T10钢零件淬火后精 磨外圆时产生的烧伤形貌,为烧伤部位的垂直切面, 表面至 0.7mm深度处为回火烧伤带,呈青灰色,由 表及里渐渐变淡。图 2为 45钢零件激光淬火后磨 削时产生的烧伤形貌,均为平行于烧伤部位的切面, 可见浅色基体(马氏体)上有深灰色烧伤痕迹,呈条 状擦伤,见图 2(a),而在同一个试样的不同部位表 现为不均匀分布的黑色斑点状缺陷,见图 2(b)。回 火烧伤虽然表现形式不同,但本质上都是零件局部 被高温回火所致。根据磨削产生的热量不同,最终
櫡櫡櫡櫡櫡櫡櫡櫡 ~测试与分析 ~
櫡櫡櫡櫡櫡櫡櫡櫡
机械加工零件表面烧伤的金相检验
焦 丽,赵英军,徐向阳
(河北华北柴油机有限责任公司,河北 石家庄 050081)
摘 要:高碳钢淬硬件和渗碳淬硬件等在磨削时,会由于磨削工艺不当,如磨削余量过大、冷却不充分或砂
轮选用不当等,产生烧伤,不仅降低零件的表面硬度,严重时还会产生裂纹,甚至导致零件报废。此
外,线切割加工也会使零件发生烧伤。零件的烧伤实质上与过大的磨削热或线切割热使零件表层
达到高温而发生相转变产生变质层有关,可根据这一点采取防止零件发生烧伤的措施。
关键词:磨削;线切割;烧伤;热处理
中图分类号:TG157 文献标识码:B
文章编号:10081690(2019)04003905