烧结部分复习提纲
第三章烧结Microsoft-Word-文档
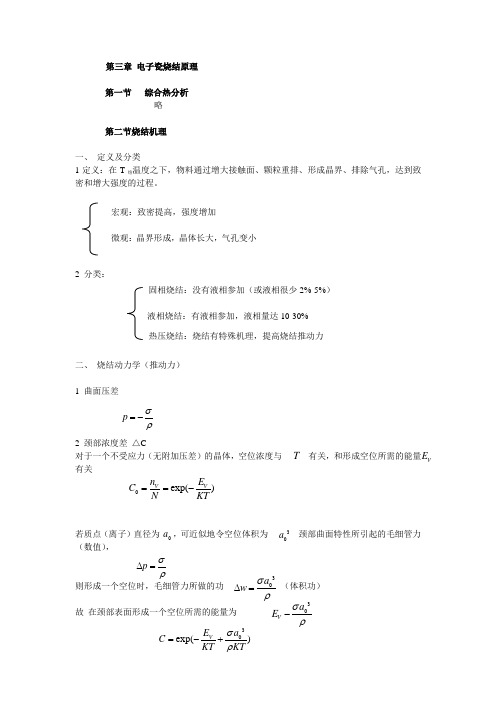
第三章 电子瓷烧结原理第一节 综合热分析略第二节烧结机理一、 定义及分类1定义:在T 熔温度之下,物料通过增大接触面、颗粒重排、形成晶界、排除气孔,达到致密和增大强度的过程。
2 分类:二、烧结动力学(推动力)1 曲面压差2 颈部浓度差 △C对于一个不受应力(无附加压差)的晶体,空位浓度与 有关,和形成空位所需的能量 有关若质点(离子)直径为 ,可近似地令空位体积为 颈部曲面特性所引起的毛细管力 (数值),则形成一个空位时,毛细管力所做的功 (体积功) 故 在颈部表面形成一个空位所需的能量为 p σρ=-V E T 0exp()V V n E C N KT ==-0a 30a p σρ∆=30a w σρ∆=30V a E σρ-3exp()V E a C KT KTσρ=-+宏观:致密提高,强度增加 微观:晶界形成,晶体长大,气孔变小相应空位浓度为:3 气相传质> > 导致:凸 气相 凹 凝聚蒸发 颈部在空位浓度差推动下,空位即从颈部不断地向颗粒其它部位扩散,而固体质点则向颈部逆向扩散,颈部空位源的作用, 与 成正比,由扩散机理进行的烧结过程可知:烧结推动力也为表面能作用的结果三、 烧结的几种机理 1、体积扩散机理颗粒凸部向凹部传质,使颈部长大,形成晶界,相当于颈部空位向凸部扩散,凹空位 > 凸空位 气孔周围的空位源,向晶体其它部位(主要是表面、晶界)扩散,这些部位质点反向迁移到气孔间隙2、蒸发—凝聚机理(气相沉积) >凸部质点进行蒸发,然后通过气相传质到凹部(颈部)凝聚,使颈部长大3、溶解—沉淀机理(液相烧结)在液相中的颗粒 > ,造成小颗粒溶解,溶解后通过熔体在大颗粒和两颗粒的颈部沉淀(形成晶界,颈部长大)4、粘滞流机理A 在液相烧结时,液相量达到一定数量时,物料出现类似液相的粘滞流动现象,导致颗粒重排(液相烧结初期,在液相中的颗粒)21ln p M p RT r σρ=⋅0P 凸0p p 凹300a C C KT σρ∆=C ∆σp 凸p 凹211ln (p M p RT r r σρ=+凸凹凸凹)021ln SL M L L KT r σρ=L 小L 大B 热压烧结当外力P 大于此时颗粒临界强度时,能使物料发生晶面(颗粒)滑动,增大接触面第三节 烧结动力学一、烧结中传质途径1) 从颗粒表面向颈部的表面扩散; 2) 从粒界向颈部的界面扩散; 3) 从颗粒表面向颈部的体积扩散; 4) 从粒界向颈部的体积扩散; 5) 从颗粒内部位错向颈部的扩散; 6) 从颗粒表面向颈部的蒸发-冷凝;7) 从颗粒表面向颈部或从小颗粒向大颗粒的溶解-沉淀 二、烧结模型烧结是从粉状集合体转变成致密集合体的过程,故颗粒的形状和大小直接影响着颗粒间的堆积状态,以及相互的接触情况。
烧结基础知识资料

烧结基础知识资料1、精料目标?答:精料是指原燃料在进入高炉前,采取措施使它们的质量最优化,成为满足高炉强化冶炼要求的炉料,在高炉冶炼使用精料后可获得优良的技术经济指标和较高的经济效益。
做好精料工作的内容提法很多,例如“高、熟、净、小、匀、稳”,也就是入炉品位要高,多用烧结矿和球团矿,筛除小于5mm的粉末,控制入炉矿的上限,保证粒度均匀,化学成分稳定等。
较全面的提法是“渣量小于300kg/t;成分稳定、粒度均匀;具有良好的冶金性能;炉料结构合理。
”二、含铁矿粉与烧结?答:广义的烧结是在一定温度下靠固体联结力将散状粉料固结成块状的过程。
炼铁领域内的烧结是指把铁矿粉和其他含铁物料通过熔化物固结成具有良好冶金性能的人造块矿的过程,它的产生物就是烧结矿。
三.铁矿粉烧结生产有何意义?答:首先,烧结生产是一种人造富矿的生产过程,有了这种造块方法,自然界中大量存在的贫矿便可通过选矿和烧结成为能满足高炉冶炼要求的优质人造富矿,从而使自然资源得到充分利用。
2、其次,烧结过程中可以利用富矿粉、轧钢皮、铁屑、高炉炉尘、转炉炉尘、硫酸渣等其他钢铁及化工工业的若干废料,使这些废料得到有效利用,做到变“废”为宝,变“害”为利。
经过烧结生产制成的烧结矿,与天然矿相比,粒度合适,还原性和软熔性好,成分稳定,造渣性能良好,保证了高炉生产的顺行。
最后,烧结过程可以除去80%~90%的S和部分F、As等有害杂质,大大减轻了高炉冶炼过程中的脱硫任务,提高了生铁质量。
结主要经济技术指标1-1简述烧结厂的主要技术经济指标。
答:烧结厂的主要技术经济指标包括烧结机的利用系数、作业率、质量合格率、原料消耗等。
1-2试述利用系数和台时产量的含义。
答:1台烧结机每平方米有效抽风面积m2每小时(h)的生产量(t)称为烧结机的利用系数。
单位为t/(m2.h)。
其计算公式为台时产量是1台烧结机1h的生产量。
通常以总产量与运转的总台时之比值表示,这个指标体现烧结机烧结机生产能力量的大小,它与烧结机有效面积的大小有关。
烧结基础知识

1. 烧结基础知识2. 烧结的含义将含铁粉状料或细粒料进行高温加热,在不完全熔化的条件下烧结成块的过程。
铁矿粉烧结是一种人造富矿的过程。
2.1. 烧结的方法(1)鼓风烧结:烧结锅,平地吹;(2)抽风烧结:(a)连续式:带式烧结机和环式烧结机等;(b)间歇式:固定式烧结机,如盘式烧结机和箱式烧结机;移动式烧结机,如步进式烧结机;(3)在烟气中烧结:回转窑烧结和悬浮烧结。
2.2. 烧结生产的工艺流程一般包括:原燃料的接受、贮存,溶剂、燃料的准备,配料,混合,制粒,布料,点火烧结,热矿破碎,热矿筛分,热矿冷却,冷矿筛分,铺底料、成品烧结矿及返矿的贮存、运输等工艺环节。
机上冷却工艺不包括热矿破碎和热矿筛分。
现代烧结工艺流程不再使用热矿工艺,应使用冷矿工艺。
在冷矿工艺中,宜推广具有铺底料系统的流程。
2.3. 烧结厂主要技术经济指标烧结厂的主要技术经济指标包括利用系数、作业率、质量合格率、原材料消耗定额等。
2.3.1. 利用系数每台烧结机每平方米有效抽风面积(m2)每小时(h)的生产量(t)称烧结机利用系数,单位为t/(m2*h)。
它用台时产量与烧结机有效抽风面积的比值表示:利用系数=台时产量有效抽风面积=总产量总生产台时总有效面积台时产量是一台烧结机一小时的生产量,通常以总产量与运转的总台时之比值表示。
这个指标体现烧结机生产能力的大小,它与烧结机有效面积的大小无关。
利用系数是衡量烧结机生产效率的指标,它与烧结机有效面积的大小无关。
2.3.2. 烧结机作业率作业率是设备工作状况的一种表示方法,以运转时间占设备日历时间的百分数表示:设备作业率=运转台时日历台时×100%日历台时是个常数,每台烧结机一天的日历台时即为24台时。
它与台数、时间有关。
日历台时=台数×24×天数事故率是指内部事故时间与运转时间的比值,以百分数表示:事故率=事故台时运转台时×100%设备完好率是衡量设备良好状况的指标。
烧结工技能竞赛理论考试复习提纲

烧结工技能竞赛理论考试复习提纲(考试版)一、判断题1.>大烟道废气气流越高,降尘效率越好。
( )答案:×2.>烧结"终点"提前,总管负压升高。
( )答案:×3.>烧结三碳指返中残碳、结矿中残碳及混合料含碳。
( )答案:√三碳是指返矿残碳、烧结矿残碳及混合料固定碳。
返矿残碳要求小于1%,烧结矿残碳要求小于0.4%,混合料固定碳一般在3%左右。
4.>点火器烘炉原则是快速将耐火材料中水份烘干。
( )答案:×5.>烧结矿中MgO含量对改善高炉炉渣流动有影响。
( )答案:√6.>烧结对熔剂要求,SiO2+Al2O3越高越好。
( )答案:×7.>返矿中含碳一般低于结矿中含碳,由固定碳及未分解碳酸盐组成。
( )答案:×返矿残碳的含义?返矿残碳即齐碳,它由安稳碳及已分化的碳酸盐里的非安稳碳所组成化教碳。
8.>一次混合是烧结生产中主要加水环节。
( )答案:√9.>Fe3O4是Fe2O3与FeO结合体,FeO越高,磁性越强。
( )答案:√10.>铁矿物按照不同形态分磁铁矿、赤铁矿、褐铁矿、菱铁矿四大类。
( )答案:√11.>石灰石生烧是指生石灰中含有未分解的石灰石。
( )答案:√12.>浮氏体是Fe3O4在较高温度下还原成FeO的中间体,强度较好,还原性较差。
( )答案:√13.>实现厚料层烧结的主要措施是提高风机能力。
( )答案:×14.>烧结矿碱度高低根据高炉要求原料综合平衡后确定的。
( )答案:√15.>烧结矿的气孔率越高,越有利于还原,因而质量越好。
( )答案:×16.>加钢渣的目的是为了提高烧结矿的品位。
( )答案:×17.>厚料层烧结工艺有利于生产,所以料层越厚越好。
( )答案:×18.>低温烧结的条件是适当的低温和氧化性气氛。
材料科学基础第九章烧结

材料科学基础第九章烧结
二. 溶解-沉淀传质
1. 条件:
❖显著的液相量
❖固相在液相内有显著的可溶性
❖液相润湿固相
2. 原因(推动力):颗粒的表面能
3. 过程: 颗粒重排
溶解-沉淀传质
材料科学基础第九章烧结
❖颗粒重排:
颗粒在毛细管力作用下,通过粘性流动或在一些 颗粒间接触点上由于局部应力的作用而重新排列, 使堆积更致密。 致密化速率与粘性流动相应,线收缩与时间呈线 性关系:
材料科学基础第九章烧结
粘性蠕变通过粘度系数(η)把粘性蠕变速率(ε)与
应力(σ)联系起来 ,
又 KTd 2 8D* 8D* KTd 2
粘性蠕变产生区域:晶界区域、位错区域
材料科学基础第九章烧结
❖动力学关系:
烧结模型:双球模型(中心距缩短)
颈部增长公式:
x
( 3
1
)2
1
r 2
1
t 2
1、 推动力:粉末物料的表面能大于多晶烧结体的晶界 能 2、 衡量指标:通常用晶界能γGB和表面能γ SV之比值来衡 量烧结的难易。 GB S越V 小越易烧结。
❖对球形颗粒:弯曲表面由于表面张力而造成的压差 P 2
r
❖对非球形曲面: P ( 1 1 )
r1 r2
❖烧结的推动力: G VP
烧成后期空隙率:
6D*
Pt 2KT3L(tf t)
材料科学基础第九章烧结
材料科学基础第九章烧结
第三节 液相参与的烧结
液相烧结特点和类型:
凡有液相参加的烧结过程称为液相烧结。 液相烧结与固相烧结的异同点:
相同点:烧结的推动力都是表面能,烧结过程都是 由颗粒重排、气孔充填和晶粒生长等阶段组成 不同点:由于流动传质比扩散传质快,因而液相烧 结致密化速率高,可使坯体在比固态烧结温度低得 多的情况下获得致密的烧结体;影响液相烧结的因 素比固相烧结更为复杂,为定量研究带来困难。
烧结工艺理论知识(全面)

烧结工艺理论知识(全面)第一章烧结生产概述§1-1烧结生产在冶金工业中的地位一、详述热处理工艺的产生和发展烧结方法在冶金生产中的应用,起初是为了处理矿山、冶金、化工厂的废气物(如富矿粉、高炉炉尘、扎钢皮、炉渣等)以便回收利用。
随着钢铁工业的快速发展,矿石的开采量和矿粉的生成量亦大大增加。
据估计,每生产1t生铁须要1.7~1.9t铁矿石,若就是贫矿,须要的铁矿石则更多。
另外,由于长期的采矿和消耗,能够轻易用以炼钢的富矿愈来愈少,人们不得不大量采矿贫矿(含铁25%~30%)。
但贫矿轻易浸出炼钢就是很不经济的,所以必须经过选矿处置。
选矿后的精矿粉,在含铁品位上就是提升了,但其粒度不合乎高炉炼钢建议。
因此,对采矿出的粉矿(0~8mm)和精矿粉都必须经过造块后方可以用作炼钢。
我国铁矿资源多样,但贫矿较多,约占到80%以上,因此,炼钢前大都需经碎裂、筛分、选矿和造块等处理过程。
烧结生产的历史已有一个多世纪。
它起源于资本主义发展较早的英国、瑞典和德国。
大约在1870年前后,这些国家就开始使用烧结锅。
我国在1949年以前,鞍山虽建有10台烧结机,总面积330m2,但工艺设备落后,生产能力很低,最高年产量仅几十万吨。
我国铁矿石烧结领域取得的成就,概括起来包括以下几个方面:(1)热处理工艺:自1978年马钢冷烧技术科技攻关顺利后,一批重点企业和地方骨干企业基本顺利完成了苏烧改冷烧工艺。
部分企业投入使用原料搅匀料场,并投入使用,绝大多数钢铁企业同时实现了自动化配料、混合机加强制粒、偏析布料、加热筛分、整粒及砌底料技术。
(2)新工艺、新技术开发和应用:如高碱度烧结矿技术、小球烧结技术、低温烧结技术、低硅烧结技术等,在钢铁企业得到推广应用,并取得了显著的效益。
(3)设备大型化和自动化:20世纪50年代,我国最小烧结机75m2,60年代130m2,80年代265m,90年代宝钢二、三期和武钢等450m烧结机相继投产,这些都就是我国自行设计、自行生产,并同时实现自动化生产的。
一、烧结基本原理精讲

一、烧结(1)、烧结基本原理烧结是粉末冶金生产过程中最基本的工序之一。
烧结对最终产品的性能起着决定性作用,因为由烧结造成的废品是无法通过以后的工序挽救的;相反,烧结前的工序中的某些缺陷,在一定的范围内可以通过烧结工艺的调整,例如适当改变温度,调节升降温时间与速度等而加以纠正。
烧结是粉末或粉末压坯,加热到低于其中基本成分的熔点温度,然后以一定的方法和速度冷却到室温的过程。
烧结的结果是粉末颗粒之间发生粘结,烧结体的强度增加。
在烧结过程中发生一系列物理和化学的变化,把粉末颗粒的聚集体变成为晶粒的聚结体,从而获得具有所需物理,机械性能的制品或材料。
烧结时,除了粉末颗粒联结外,还可能发生致密化,合金化,热处理,联接等作用。
人们一般还把金属粉末烧结过程分类为:1、单相粉末(纯金属、古熔体或金属化合物)烧结;2、多相粉末(金属—金属或金属—非金属)固相烧结;3、多相粉末液相烧结;4、熔浸。
通常在目前PORITE微小轴承所接触的和需要了解的为前三类烧结。
通常在烧结过程中粉末颗粒常发生有以下几个阶段的变化:1、颗粒间开始联结;2、颗粒间粘结颈长大;3、孔隙通道的封闭;4、孔隙球化;5、孔隙收缩;6、孔隙粗化。
上述烧结过程中的种种变化都与物质的运动和迁移密切相关。
理论上机理为:1、蒸发凝聚;2、体积扩散;3、表面扩散;4、晶间扩散;5、粘性流动;6、塑性流动。
(2)、烧结工艺2-1、烧结的过程粉末冶金的烧结过程大致可以分成四个温度阶段:1、低温预烧阶段,在此阶段主要发生金属的回复及吸附气体和水分的挥发,压坯内成形剂的分解和排除等。
在PORITE微小铜、铁系轴承中,用R、B、O(Rapid Burning Off)来代替低温预烧阶段,且铜、铁系产品经过R、B、O 后会氧化,但在本体中可以被还原,同时还可以促进烧结。
2、中温升温烧结阶段,在此阶段开始出现再结晶,首先在颗粒内,变形的晶粒得以恢复,改组为新晶粒,同时颗粒表面氧化物被完全还原,颗粒界面形成烧结颈。
烧结工理论知识复习资料

烧结工理论知识复习资料(判断)1、烧结过程中,固体燃料呈分散状分布在料层中,其燃料规律性介于单体焦粒燃烧与焦粒层燃烧之间。
( )√2、烧结过程中,开始出现液相是在燃烧带。
( )√3、烧结过程中,燃烧带是烧结过程中温度最高的区域,温度可达1800℃-2000℃。
( )×4、烧结过程中,随着烧结温度的提高,液相量不断增加。
( )√5、烧结过程中的所有硫均在氧化反应中脱除。
( )×6、烧结过程中高温区温度越高越好。
( )×7、烧结过程中固体碳的燃烧反应速度主要取决于气体扩散速度。
( )√8、烧结过程中硫化物中的硫可脱去90%。
( )√9、烧结过程中燃料比越多,废气温度越高。
( )×10、烧结过程中燃烧层阻力损失约占全部阻力的50~60%。
( )√11、烧结过程中使用无烟煤作燃料时,无需经过破碎环节。
( )×12、烧结过程中水份的蒸发是化学反应。
( )×13、烧结过程中以硫酸盐形式存在的硫则在分解反应中脱除。
( )√14、烧结过程中主要脱硫条件是高温和高碱度。
( )×15、烧结过程中自动蓄热作用的热量约占烧结所需热量的38~40%。
( )√16、烧结过程终点控制的好坏对烧结矿产量有直接影响而对烧结矿质量无影响。
( )×17、烧结混合料的过湿层越薄越有利于生产。
( )√18、烧结混合料中添加生石灰或消石灰可减少燃料层碳酸钙分解的吸热量。
( )√19、烧结机的密封主要目的是降低漏风率。
( )√20、烧结机的有效面积就是烧结机的长度。
( )×21、烧结机利用系数是烧结机每小时、每平方米有效烧结面积的生产能力。
( )√22、烧结机有效面积是台车宽度与烧结机总长度的乘积。
( )×23、烧结加生石灰是为了消化后发挥粘结作用,促进颗粒成球。
( )×24、烧结矿的二元碱度就是氧化钙与二氧化硅含量的比值。
- 1、下载文档前请自行甄别文档内容的完整性,平台不提供额外的编辑、内容补充、找答案等附加服务。
- 2、"仅部分预览"的文档,不可在线预览部分如存在完整性等问题,可反馈申请退款(可完整预览的文档不适用该条件!)。
- 3、如文档侵犯您的权益,请联系客服反馈,我们会尽快为您处理(人工客服工作时间:9:00-18:30)。
烧结工艺介绍
一、烧结的发展概况:
世界上第一台烧结机1910年诞生在美国,面积8.325 M2(1.07*7.78),日产烧结矿140吨,我国1926年3月在鞍山建成4台21.63M2(1.067*20.269),日产1200吨。
目前,我国有13、18、24、36、50、75、90、130、182、265、450M2等11个标准设计规格的烧结机。
二、烧结在钢铁工业中的地位和作用:
地位:现代高炉生产技术指标之所以先进,最重要的是精料,烧结厂就是向高炉提供精料的“厨房”
作用:1、造块,利用不能直入炉的铁精粉及贫矿、富矿粉。
2、通过造块改善入炉料的化学物理性能,如孔隙率、粒度组成、机械强度、化学成份、还原性、膨胀性、低温还原粉化性、高温还原软化性、提高冶炼效果,高产、优质、低耗。
3、除去有害元素,硫S、氟F、钾K、钠Na、铅Pb、锌Zn、砷As等。
4、综合利用变废为宝降成本,高炉灰、转炉灰红泥、轧钢皮等,提高经济效益降低焦比。
三、烧结生产工艺流程:
1、原料准备:将焦粉破碎(0-3MM)占80%,白灰、高镁灰、破碎(0-3MM)占85%-90%、装入料仓。
2、配料:圆盘给料机、拖拉皮带秤将(精矿、委拉矿、巴西矿、铁皮、槽返、机返、球返、除尘灰、焦粉、白灰、高镁灰)11种料按比例给到配料皮带上。
3、混料:一次混合机(φ28*7M)将混合料加水润湿、混匀;
二次混合机(φ3*12M)进一步加水、混匀造球。
99.9%的铁粉和0.8%的膨润土混合。
4、布料点火:(φ800*1500MM)经圆辊给料机将料布到台车上,进行点火,把表面点着。
5、烧结: (1M*1.5*0.40M)台车上的料在抽风作用下借助碳的燃烧发生一系列的化学反应。
6、破碎:(φ1100*1860)通过剪切式单辊破碎机将烧结矿破碎到小于150MM。
7、筛分(15*4.5M)由热矿筛将6mm以筛下进入返矿,大于6mm进入带冷机。
8、带式冷却机(34M2)将烧结矿温度降到150℃以下,运至高炉。
7、附烧结生产工艺流程图
四、名词解释:
1、烧结:烧结是为高炉冶炼提供“精料”的一种加工方法,是利用精矿或粉矿制成块状冶炼原料的一个加工过程。
其过程的实质是将准备好了的各种原料(精矿、粉矿、燃料、熔剂、返矿、除尘灰等),根据高炉冶炼要求,按一定比例经配料、混合、制粒、得到符合要求的烧结料,经点火助碳的燃烧和氧化物的氧化而产生高温,使烧结料中的这部分成分软化和熔化,发生化学反应生成一定数量的液相,冷却时相互粘结成块,这一过程叫烧结过程简称烧结,它所得的产品就叫烧结矿。
2、台时产量:是指一台烧结机一小时的产量(体现烧结生产能力的大小)。
台时产量=烧结机生产总量/烧结机实际运行时间单位:吨/台时
3、利用系数:是指烧结机每平方米有效抽风面积一小时的产量,它是用烧结机台时产量和有效抽风面积的比值表示。
利用系数:台时产量/有效抽风面积单位:吨/M2时
4、工序能耗:是指生产一吨烧结矿所消耗的能源总和(焦粉、煤气、水电等),千克/吨矿。
5、转鼓指数:是衡量烧结矿在常温状态下抗磨、抗冲击的能力。
做法:内径1000MM,试样15Kg/次,24转/分钟,转200转,用6.3MM*6.3MM筛,大于6.3MM的百分数即转鼓指数。
6、落下强度:大于10MM的块从2米高处自由落到铸铁板上4次,筛上大于5MM的部分
即落下强度指数。
7、抗压强度:生球10个平压,1Kg未碎裂球的个数与总球之比。
8、品位:指烧结矿的含铁量。
9、碱度:烧结矿碱性氧化物与酸性氧化物的比值,称为碱度。
碱度>1.5的通常称为高碱矿;
碱度1.0-1.5之间的一般称自溶性矿;
碱度<1.0的称为酸性矿。
五、精料对高炉冶炼的意义,进厂原料质量和精料的关系:
高炉对烧结矿的要求:
1、品位高、杂质少、化学成份稳定。
(FeO上升1%、焦比下降2%、产量上升3%),杂质:S、P、Zn、Pb、Cn、Ac。
为什么要化学成份稳定:品位波动由1%降到0.5%,焦比下降1%产量提高2%,碱度由0.05%降到0.025%,焦比下降0.3%产量提高0.5%;
2、强度好,粒度均匀、粉末少。
强度:粉末多,炉尘吹出多,煤气净化负荷大,恶化料柱透气性,可能出“管道”结瘤,导致炉况失常。
粒度均匀:增加料柱隙度,提高透气性改善气流分布。
为什么要均匀:入炉矿中<5MM,每减少10%增产6-8%;6-50MM每增加10%焦比降低1.8%;
3、易还原、粉化少、高温性能好。
还原性与气孔度和熔化程度有关,大孔薄壁,煤气难于渗透,不好还原。
微孔气孔度高、还原性好。
粉化,是在低温还原条件下产生粉末,严重时影响炉内块状带透气性。
精料的意义就是在于改善入炉料的成份稳定,适应大风量、高风温、高冶强、低炉温冶炼的情况下,炉况顺行,以实现高产、优质、低耗的目的。
进厂原料的质量,就是精料的基础,不把住进厂原料关“精料”就是一句空话。
六、球团竖炉生产工艺流程:
1、配料;经圆盘和拖拉皮带(将精况皂土)按一定比例给到配料皮带上。
2、烘干机:(φ2.4*14)将混合料脱掉一部分水分。
3、润磨机(φ3.5*6.2)将混合料进一步磨细200目占到70%以上。
4、造球(φ6M*2台)进行造球。
5、生球筛(φ3132*1400MM,辊径102,辊数30)将生球中的粉末筛除。
6、布料:经布料车将生球布料到烘干床上。
7、焙烧:(10.58M2)在焙烧带发生一系列的化学反应,焙烧过程完成。
8、热链板:将成品球运到热筛。
9、热筛(115*145):将成品球粉末筛除。
10、带冷机(30M2):将熟球温度冷却到150℃以上,直送高炉。
七、附白灰炉生产工艺流程图。