炼焦新工艺
炼焦新技术

炼焦新技术—煤调湿技术我国现有焦炉生产能力较大,占世界第一位,炼焦煤水分偏高,而且优质炼焦煤日益短缺,围绕现有焦炉和炼焦生产工艺,开发提高焦炭质量和利用炼焦余热的新工艺、新技术是适应企业发展,提高企业经济效益的有效途径。
煤调湿技术可降低入炉煤水分,降低炼焦耗热量,增加入炉煤堆密度,提高焦炭质量。
近几年来,煤调湿技术在国内外炼焦行业异军突起,得到了广泛的应用,究其原因是煤调湿技术具有其独特的优越性:可使焦炭和化工产品增产11%,提高经济效益;焦炉加热用燃料降低,减少耗热量;焦炭质量得到提高;充分利用了焦炉余热,取得了明显的经济和社会效益。
一、煤调湿(Coal Moisture Control ,简称“ CMC ”)技术简述煤调湿技术是通过直接或间接加热来降低并稳定控制入炉煤的水分,该技术不追求最大限度地去除入炉煤的水分,而只把水分稳定在相对低的水平,既可达到增加效益的目的,又不因水分过低而引起焦炉和回收系统操作的困难,使入炉煤密度增大、焦炭及化工产品增产、焦炉加热用煤气量减少、焦炭质量提高和焦炉操作稳定等效果。
二、煤调湿的基本原理利用外界热能将入炉煤在焦炉外干燥,控制入炉煤的水分,从而控制炼焦耗热量、改善焦炉操作、提高焦炭产量或扩大弱粘结性煤的用量。
三、工艺流程及发展煤调湿技术通过直接或间接加热来降低并稳定控制入炉煤水分,并不追求最大限度地去除入炉煤气的水分,而只是把水分稳定在相对较低的水平,就可以达到增加效益的目的,又不会因水分过低而引起焦炉和回收系统操作困难。
煤调湿技术于20世纪80年代初在日本开始应用,历经了3 种工艺技术的变革:第一代是热媒油干燥方式;第二代是蒸汽干燥方式;第三代是最新一代的流化床装置,设有热风炉,采用焦炉烟道废气或焦炉煤气对其进行加热的干燥方式。
1、第一代煤调湿技术第一代CMC是热煤油干燥方式,其工艺见下图。
热媒油式煤调湿工艺流程图利用热油回收焦炉上升管煤气显热和焦炉烟道气的余热,温度升高到195℃的热油通过干燥机将常温的煤预热到80℃,煤的水分由9%左右降到5.7%,调湿后的煤在运输过程中水分还将降低0.7%,装入煤水分保持在5%±0.7%。
焦炉炼焦工艺
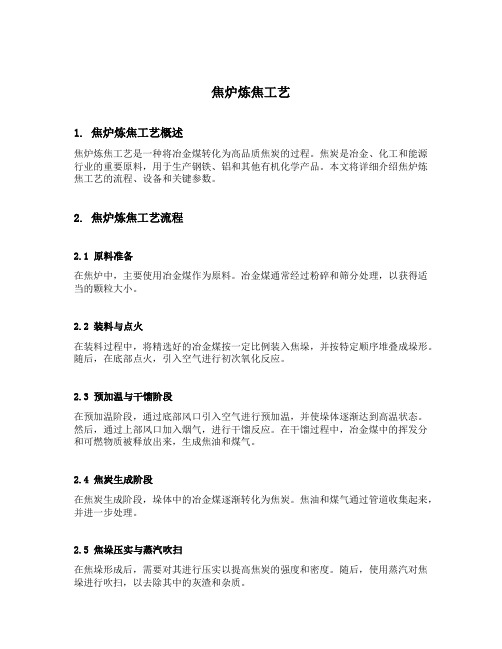
焦炉炼焦工艺1. 焦炉炼焦工艺概述焦炉炼焦工艺是一种将冶金煤转化为高品质焦炭的过程。
焦炭是冶金、化工和能源行业的重要原料,用于生产钢铁、铝和其他有机化学产品。
本文将详细介绍焦炉炼焦工艺的流程、设备和关键参数。
2. 焦炉炼焦工艺流程2.1 原料准备在焦炉中,主要使用冶金煤作为原料。
冶金煤通常经过粉碎和筛分处理,以获得适当的颗粒大小。
2.2 装料与点火在装料过程中,将精选好的冶金煤按一定比例装入焦垛,并按特定顺序堆叠成垛形。
随后,在底部点火,引入空气进行初次氧化反应。
2.3 预加温与干馏阶段在预加温阶段,通过底部风口引入空气进行预加温,并使垛体逐渐达到高温状态。
然后,通过上部风口加入烟气,进行干馏反应。
在干馏过程中,冶金煤中的挥发分和可燃物质被释放出来,生成焦油和煤气。
2.4 焦炭生成阶段在焦炭生成阶段,垛体中的冶金煤逐渐转化为焦炭。
焦油和煤气通过管道收集起来,并进一步处理。
2.5 焦垛压实与蒸汽吹扫在焦垛形成后,需要对其进行压实以提高焦炭的强度和密度。
随后,使用蒸汽对焦垛进行吹扫,以去除其中的灰渣和杂质。
2.6 卸料与冷却最后,在一定时间内完成焦化过程后,将形成的焦炭从焦垛中卸出,并送入冷却塔进行快速冷却。
冷却后的焦炭即可用于下游工艺。
3. 焦炉设备3.1 焦垛焦垛是用于装载冶金煤并进行干馏反应的装置。
它通常由耐火材料构成,具有一定的孔隙结构,以便于煤气和焦油的顺利流出。
3.2 风口风口用于控制空气的进入和排出。
它分为底部风口和上部风口,分别用于预加温和干馏阶段的空气供应。
3.3 管道系统管道系统用于收集焦油和煤气,并将其送往后续处理设备。
它包括主管道、分支管道和收集器等组成部分。
3.4 冷却塔冷却塔用于将炼焦过程中产生的煤气快速冷却,以使其中的焦油凝结并收集起来。
冷却塔通常由多级塞式冷却器组成。
4. 焦炉关键参数4.1 温度在焦炉炼焦过程中,温度是一个重要的参数。
适当的温度可以促进冶金煤中挥发分的释放和焦炭生成反应的进行。
炼焦方法

炼焦方法捣固炼焦介绍:一.捣固炼焦的价值与意义捣固炼焦技术是一种可根据焦炭的不同用途,配入较多的高挥发分煤及弱粘结性煤,在装煤推焦车的煤箱内用捣固机将已配合好的煤捣实后,从焦炉机侧推入炭化室内进行高温干馏的炼焦技术。
捣固炼焦是炼焦一项新技术。
其优势明显:技术捣固炼焦技术可多用弱粘结性煤,少用强粘结性煤,增大了炼焦煤料的可选范围,降低炼焦成本、改善焦炭质量,捣固炼焦工艺以其显著的经济技术优势,在国内得到迅猛发展。
捣固炼焦技术对我国焦化广大工作者来说,是一个新的课题,有待探索研究,在实践的过程中不断丰富捣固炼焦技术理论,以指导我国捣固炼焦技术的应用和发展。
捣固炼焦工艺是在炼焦炉外采用捣固设备, 将炼焦配合煤按炭化室的大小, 捣打成略小于炭化室的煤饼, 将煤饼从炭化室的侧面推入炭化室进行高温干馏。
成熟的焦炭由捣固推焦机从炭化室内推出,经拦焦车、熄焦车将其送至熄焦塔, 以水熄灭后再放到凉焦台, 由胶带运输经筛焦分成不同粒级的商品焦炭经研究发现:在相同配煤比之下,捣鼓炼焦大幅度提高了焦炭的冷态强度。
捣鼓可以改善焦炭气孔结构,提高焦炭反应强度。
捣固炼焦是用机械力将煤料的粒子压紧,因压紧而导致:①增加煤料堆密度;②因粒子的压紧而使胶质体填充的空隙减少,而相对扩展了粘结范围;③由于堆密度的增加单位体积内析出的煤气量增加,而提高了膨胀压力。
这些因素导致了焦炭多孔体的气孔壁增厚,气孔率降低且趋向均匀,因而M40、M10都有所改善,CRI和CSR也略有改善。
二.我国捣固炼焦的发展现状与发张趋势现状:捣固炼焦技术在我国炼焦生产中已占重要地位,目前,我国捣固炼焦炉分布在陕西、河北、山东等十三个省份,共有捣固炼焦企业81家,捣固焦炉168座,产能已达5035万吨,占焦炭产能的16.07%。
在现生产的捣固焦炉中,以炭化室高4.3米,炭化室宽500mm的焦炉为主,其次是炭化室高3.2米和炭化室高3.8米的焦炉;我国捣固炼焦炉平均炉龄较短,绝大部分焦炉炉龄在五年之内。
炼焦工艺技术
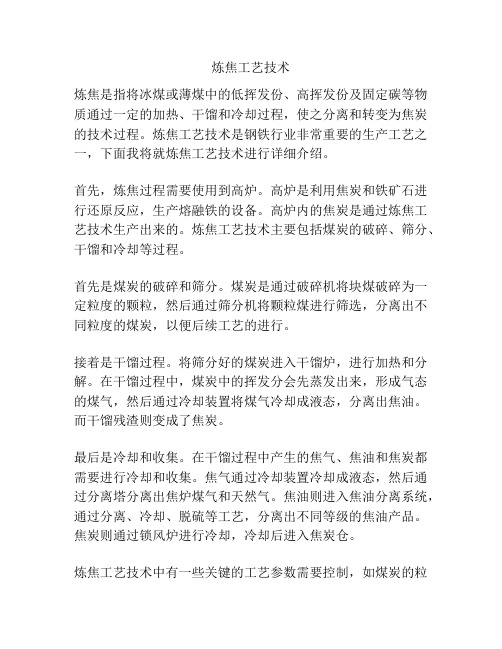
炼焦工艺技术炼焦是指将冰煤或薄煤中的低挥发份、高挥发份及固定碳等物质通过一定的加热、干馏和冷却过程,使之分离和转变为焦炭的技术过程。
炼焦工艺技术是钢铁行业非常重要的生产工艺之一,下面我将就炼焦工艺技术进行详细介绍。
首先,炼焦过程需要使用到高炉。
高炉是利用焦炭和铁矿石进行还原反应,生产熔融铁的设备。
高炉内的焦炭是通过炼焦工艺技术生产出来的。
炼焦工艺技术主要包括煤炭的破碎、筛分、干馏和冷却等过程。
首先是煤炭的破碎和筛分。
煤炭是通过破碎机将块煤破碎为一定粒度的颗粒,然后通过筛分机将颗粒煤进行筛选,分离出不同粒度的煤炭,以便后续工艺的进行。
接着是干馏过程。
将筛分好的煤炭进入干馏炉,进行加热和分解。
在干馏过程中,煤炭中的挥发分会先蒸发出来,形成气态的煤气,然后通过冷却装置将煤气冷却成液态,分离出焦油。
而干馏残渣则变成了焦炭。
最后是冷却和收集。
在干馏过程中产生的焦气、焦油和焦炭都需要进行冷却和收集。
焦气通过冷却装置冷却成液态,然后通过分离塔分离出焦炉煤气和天然气。
焦油则进入焦油分离系统,通过分离、冷却、脱硫等工艺,分离出不同等级的焦油产品。
焦炭则通过锁风炉进行冷却,冷却后进入焦炭仓。
炼焦工艺技术中有一些关键的工艺参数需要控制,如煤炭的粒度、煤炭的含硫量、干馏温度、冷却速度等。
这些参数的控制将直接影响到炼焦过程中产生的产品质量以及炼焦工艺的能耗和环保性能。
总的来说,炼焦工艺技术是一项复杂而重要的工艺。
它不仅直接关系到高炉的高效运行和铁水的质量,同时也与环境保护和能源消耗密切相关。
因此,对于炼焦工艺技术的研究和改进具有重要意义,可以提高钢铁行业的生产效率和环保水平。
中国大型焦炉炼焦工艺技术优化与改进

我国大型焦炉炼焦工艺技术优化与改进一、引言我国作为世界上最大的焦煤生产和消费国,焦炉炼焦工艺技术一直是焦化企业关注的焦点。
随着煤炭产业结构调整和技术进步,炼焦工艺技术的优化与改进变得尤为重要。
本文将对我国大型焦炉炼焦工艺技术的优化与改进进行深入探讨。
二、我国大型焦炉炼焦工艺技术现状1. 炼焦工艺技术概述我国大型焦炉炼焦工艺技术主要包括焦炭生产的原料选择、炉前处理、煤气利用和焦炉运行等环节。
目前,我国大部分焦化企业依然采用传统的炼焦工艺技术,存在能耗高、环境污染严重等问题。
2. 技术优化的迫切性随着国家对环境保护和能源节约的要求日益提高,炼焦企业迫切需要进行工艺技术的优化与改进,提高炼焦效率、减少能耗和污染排放。
三、技术优化与改进的途径1. 原料选择的优化优化煤炭、焦煤和炼焦助剂的选择,提高炼焦质量和产量,减少炼焦过程中的能耗。
2. 高效环保设备的引入引入先进的高效环保设备,如干熄焦技术、煤气余热利用技术等,降低炼焦过程中的二氧化硫和氮氧化物排放,实现清洁生产。
3. 先进控制技术的应用应用先进的控制技术,进行炼焦过程的自动化和智能化控制,提高设备运行稳定性和生产效率。
4. 节能减排技术的推广推广节能减排技术,如余热发电技术、焦炉废气治理技术等,实现能源的最大化利用和环境污染的最小化排放。
四、技术优化与改进的效果通过对我国大型焦炉炼焦工艺技术的优化与改进,可以实现以下效果:1. 提高焦炭的质量和产量,降低炼焦能耗。
2. 减少炼焦过程的环境污染排放,改善周边环境质量。
3. 提升焦炉设备的稳定性和运行效率,降低生产成本。
4. 实现清洁生产,符合国家的环保政策和节能减排要求。
五、结语我国大型焦炉炼焦工艺技术的优化与改进是一个复杂系统工程,需要从原料选择、环保设备引入、控制技术应用和节能减排技术推广等多个方面进行全面优化。
只有不断地改进和完善炼焦工艺技术,才能实现焦炭生产的可持续发展。
希望随着技术的不断进步,我国大型焦炉炼焦工艺技术能够实现更加环保、高效和可持续的发展。
刍议SCOPE21工艺的炼焦新技术

一
2 . 环境 负荷 的降低 将底 部燃 烧室 的空气 入 口和燃 气入 口相对位 置 的直 线布 置 ,变为 错 口布置 ,进 而 将燃烧 室 内的空 气和 燃气 改 为混 合和扩 散状 态 。试验
2 0 0 mm 断面的模拟 气流塔 ,利 用高速 摄像机 对塔 内煤 炭粒 子的运 行轨 迹 实 施 可 视 性 观 察 ,观 察 结 果 表 明 ,塔 内运 动 过 程 中 ,直 径 大 于 0 . 3 am粗 粒相 互之 间的影 响基本 可 以不进行 考 虑 ,并 将 其视 为单 个粒 r 子进 行处理 。直径 小于 0 . 3 mm 的煤粉 ,在 进入模 拟气 流塔 后 ,表 现为 高 密度 的粒 子群 ,并可 视 为单个 粒子 进行 处 理 。选择 2 5 m 有效 高 度 、 1 0 0 mm 直径 的试验塔实施 快速 加热处 理 ,利用这 一试 验过 程所 获得 的 数 据进行数 学模型 的编制 ,模拟计 算 2 4 0 0 m m 直径 的工业 塔和 9 0 0 mm
直径 的放大 试验塔 嘲。
钢铁 等工业 企业 生产 过程 中对 于焦 炭 的需求 量也 呈现 出 了逐年上 升 的 趋势 。但是 ,在 我 国现有 的焦 炭生 产技 术水 平之 下 ,炼 焦工 业要 实现 进一 步发展 也会 面临 极大 的 困难 。只有 进一 步提 高我 国焦炭 生产 企 业 的积 水水平 ,才 有助 于焦 炭生产 量 的进 一步 提高 ,并 实现 资源利 用 面 扩大 ,污染 减少 ,以及能 耗 降低等 节能 环保 目标 的实 现 ,从 而 为我 国 经济 的可持 续发 展提供 物质基 础n l 。 很 长 时间 以来 ,尽管 国 际炼焦 技术 实现 了快 速的发 展 ,然而 ,工 艺过 程和 基本方 法仍 然较 为 传统 ,也就 是在 耐火 材料砌 筑 的焦 炉 中加 入特 定 量水分 的 原煤 ,在温 度达 到 1 0 0 0 o C以上 后 ,经过 干馏 处理 后 , 原 煤 能够 转化 为 焦 炭 。在 焦 炉 内处 理 原煤 的 具体 过 程 包 括 :第 一 , 升温 、脱 水 ;第二 ,形成 胶质 体 、熔融 、热 解 ;第三 ,形 成半 焦 ;第 四 ,焦炭稳 定形成后 ,排 出赤热焦 炭 ,通过 干法或 湿法进 行熄焦 处理 , 并 得到 最终 的 成品 焦 - 。 】 。氮 这 一生 产过 程存 在 下述 问题 :首 先 ,对 于 生产 环境要 求较 高。长 时间的干馏 处理会 导致 NO x 生 成以及 烟气 泄漏 等 问题 ,且湿 法息 焦 也会 造成 较 为严 重 的水资 源和 空 气污 染 。其 次 , 成 本高 、能源 消耗 大 。再次 ,质 量和 能力 限制较 大 。最 后 ,资源 限制 较 大 ,主要 表现 为焦煤 资源分布不 均匀 ,且资料储 备量 日渐减少 。
炼焦行业工艺技术

炼焦行业工艺技术炼焦行业是将煤炭转化为焦炭的过程,是钢铁工业的重要环节之一。
炼焦工艺技术涉及到多个环节,包括煤炭的预处理、炼焦炉的操作、煤气的处理等。
本文将从以下几个方面介绍炼焦行业的工艺技术。
首先,煤炭的预处理是炼焦过程的第一步。
煤炭的质量和性质会直接影响到焦炭的质量和产量。
在炼焦前,需要对煤炭进行筛分、破碎、干燥等处理,以确保煤炭具有合适的粒度和含水量。
此外,化学分析和物理性质测试也是必要的,以便确定煤炭的品质,并根据需要进行混配。
其次,炼焦炉的操作是关键环节之一。
炼焦炉是将煤炭加热至高温的设备,通过控制不同的工艺参数来实现煤炭的分解和转化。
炼焦炉的主要类型有焦炉、卧式炼焦炉和立式炼焦炉等。
在炼焦过程中,需要精确控制炉内的温度、压力和气体流量,确保煤炭得到充分热解和反应。
此外,炼焦炉内还需要合理布置回收设备,以最大限度地回收和利用产生的煤气和煤焦油。
再次,煤气的处理也是炼焦工艺技术中重要的一环。
炼焦过程中产生的煤气主要包含一氧化碳、氢气和烃类等有价值的成分。
为了提高能源利用效率和减少环境污染,需要对煤气进行处理,主要包括脱硫、脱氨、除尘等步骤。
通过脱硫和脱氨,可以减少煤气中的有害物质含量,提高其燃烧效果;通过除尘处理,可以减少煤气中的颗粒物和粉尘,保护环境。
最后,对于炼焦行业而言,技术创新永远是推动行业进步的动力。
随着科技的不断发展,炼焦行业也在不断探索新的工艺技术。
例如,高炉煤气的再利用、煤炭深度加工等都是当前炼焦行业研究的热点。
同时,智能化技术也逐渐应用于炼焦行业,通过自动控制系统和数据分析,实现工艺参数的精确控制和优化。
总之,炼焦行业是一个涉及到多个环节的工艺过程,需要综合运用多种技术手段。
通过煤炭的预处理、炼焦炉的操作、煤气的处理等环节,可以实现高效、环保的炼焦过程。
随着技术的不断进步,炼焦行业将会不断发展,为钢铁工业的发展做出更大的贡献。
炼焦工艺及流程

炼焦工艺简介1.备煤2.捣固炼焦由备煤车间来的洗精煤,由输煤栈桥运入煤塔,装煤车行至煤塔下方, 由摇动给料机均匀逐层给料, 用排锤移动捣固机分层捣实, 然后将捣好的煤饼从机侧装入炭化室。
煤饼在950~1050℃的温度下高温干馏, 经过~22.5小时后, 成熟的焦炭从炭化室推出,经干熄焦系统冷却后由专用皮带运输机运出。
干馏过程中产生的荒煤气经炭化室顶部、上升管、桥管汇入集气管,经吸气弯管和吸气管抽吸至冷鼓工段。
在集气管内冷凝下来的焦油和氨水经焦油盒、吸气主管一起至冷鼓工段。
推焦过程中逸散的粉尘由管道抽吸至设在焦侧的预留出焦地面除尘站, 经站内的布袋除尘器除尘后排入大气。
装煤过程中逸散的荒煤气由设在炉顶的消烟除尘车抽吸至车上的燃烧室燃烧, 燃烧后的废气经车上的文丘里洗涤器, 将废气中的粉尘洗下来,排入大气。
洗涤水送至除尘车下水槽至粉焦沉淀池沉淀分离后回用。
焦炉加热用回炉煤气由外管送至焦炉,经煤气总管、煤气预热器、主管、煤气支管进入各燃烧室,在燃烧室内与经过蓄热室预热的空气混合燃烧,混合后的煤气、空气在燃烧室由于部分废气循环,使火焰加长, 使高向加热更加均匀合理,燃烧烟气温度可达~1200℃, 燃烧后的废气经跨越孔、立火道、斜道,在蓄热室与格子砖换热后经分烟道、总烟道,最后从烟囱排出。
3.熄焦4.筛贮焦焦炉生产的焦炭,经干熄焦后由带式输送机送至筛焦楼。
焦炭通过筛分,分为>40mm和<40mm二级,>40mm的焦炭经过溜槽由带式输送机及可逆配仓带式输送机卸入焦仓内贮存。
<40mm 的焦炭则直接经过溜槽进入1530双层振动筛,将其分为40~25mm、25~10mm、<10mm三级,5.冷鼓、电捕脱除焦油及萘焦油产品规格表(表2-2)②煤气干煤气量:45400Nm3/h煤气温度:~34℃煤气压力:~0.017MPa干煤气中的杂质含量表(表2-3)③剩余氨水 (中间产品):产量: 20400kg/h氨水组成表(表2-4)6.脱硫及硫的回收本工段包括脱硫、硫回收及剩余氨水三部分。
- 1、下载文档前请自行甄别文档内容的完整性,平台不提供额外的编辑、内容补充、找答案等附加服务。
- 2、"仅部分预览"的文档,不可在线预览部分如存在完整性等问题,可反馈申请退款(可完整预览的文档不适用该条件!)。
- 3、如文档侵犯您的权益,请联系客服反馈,我们会尽快为您处理(人工客服工作时间:9:00-18:30)。
二、煤干燥与调湿
(2)控制炼焦煤水分的意义 我国目前焦炭产能是24000多万吨/年,消 耗洗精煤约33000多万吨/年,按10%装炉煤 水分计算,约有3300万吨/年水分进入焦炉 ,这些水在焦炉中汽化消耗的热量约 1.27x1014KJ/a,相当于433万吨/年标煤。如 果控制入炉煤水分在5%左右,将节约216.5 万吨/年标煤。
三、型煤炼焦
(3)成型煤的影响因素 1.煤料性质 高煤化度和低黏性的煤,配型煤效果好; 偏低煤化度的强黏煤配型煤炼焦效果差。
原因:配型煤过程中黏结性过强,半焦收缩 应力较大,导致焦炭裂纹增多,反而降低 焦炭强度。
三、型煤炼焦
2.型煤配入量 当型煤配入量超过50%时,进一步增加型煤 配入量,入炉煤堆密度反而降低。 当型煤配入量超过40%时将会引起对炉墙膨 胀压力的急剧提高,影响焦炉寿命。 一般生产中型煤配比以不超过30%为宜,当 煤质较好时,可降低到15%~20%。
(2)变化结果 1.堆密度比湿煤装炉时增加10%~13% 150 ~250℃煤颗粒表面的水膜几乎完全脱 尽,颗粒间的相对阻力减小到最低限度 整个煤饼的高向和长向密度均匀,使得预 热炼焦得出的焦炭具有密度大、强度高、 质量均匀等优点
一、煤预热炼焦技术
2.装炉煤升温速度快 装炉煤温度达到150 ~250℃后,焦炉提供 的热量不在用于蒸发水分,其单位时间内 吸收的热量将大于湿煤,使得装炉煤升温 明显加快,提高炼焦速度 得出焦炭质量真密度大,气孔率低、机械 强度高、反应性低且反应后强度高
二、煤干燥与调湿
(3)煤调湿(CMC)与煤干燥的区别 1.煤调湿不最求最大限度的去除装炉煤水分, 只是将水分稳定在一个较低的值5%~6% 2.煤调湿是充分利用焦炉烟道气或红焦的余热 作为热源去除水分、
二、煤干燥与调湿
(4)煤干燥、调湿效果 1.减少水分,增加堆密度,提高炼焦速度,提 高焦炉的生产率。 2.提高焦炭机械强度,降低焦炭气孔率。 3.降低炼焦热耗 4.增加高挥发分弱黏煤的配用量 5.回收炼焦余热
三、型煤炼焦
(1)型煤炼焦的背景 我国煤炭资源虽然丰富,但炼焦煤炭资 源储量有限仅占13%左右。虽然品种齐全但 分布很不平衡,其中一半以上为高挥发分 气煤,黏结性较弱,强黏结性的肥煤、焦 煤不足30%,优质、易选的炼焦煤更少,且 集中分布在华北地区。
三、型煤炼焦
(1)型煤炼焦的背景 而现在高炉容积不断扩大,对冶金焦的 要求也不断提高,同时优质炼焦煤日趋匮 乏,因此改善焦炭质量或者降低优质炼焦 煤的配比的新工艺研究,在世界各国受到 重视。
三、型煤炼焦
5.黏结剂的影响 一般黏结剂(煤沥青、石油沥青)适当的 增加可以改善型煤的强度和密度,但是黏 结剂的来源有限,价格较贵,添加量增多 ,生产成本增加,经济上不合算。一般软 沥青的配量宜控制在5.5%~6.5%间。
三、型煤炼焦
(4)生产效果 1.配煤比相同的前提下,M10提高1%~2% ,M40提高2%~3%。 2.保持焦炭质量不变的前提下,强黏结性 煤可少配10%~15%。 3.焦炭筛分组分改变 >80mm级的有所下降, 25~80mm级的增 加5%~10%,<25mm级的变化不大。
炼焦新工艺
一、煤预热炼焦
二、煤干燥与调湿 三、配型煤炼焦
一、煤预热炼焦技术
(1)原理 将装炉煤在惰性气体热载体中快速预热 到煤软化温度以下(150~250℃),此时 装炉煤固有的性质五明显变化,但是这种 预热煤在炭化室内随结焦过程的进行,其 软化、熔融、热解、固化、收缩的过程发 生显著变化。
一、煤预热炼焦技术
三、型煤炼焦
(2)型煤炼焦原理 型煤炼焦能改善焦炭质量和减少弱黏 结性煤用量的原因: 1.型煤内部煤粒接触紧密,在炼焦过程 中促进了粘结组分和非黏结组分的结合, 从而改善煤的结焦性。 2.型煤与煤粉混合炼焦时,在软化熔融 阶段,型煤本生体积膨胀;另一方面产生 的大量气体压缩周围散煤,其膨胀压力较
三、型煤炼焦
散装煤料显著提高,使煤粒间接触更加紧 密,形成结果坚实的焦炭。 3.配有型煤的装炉煤,由于型煤致密, 其导热性比煤粉好,升温速率快,延长煤 料的塑性温度区间,增强煤粉间的表面结 合。 4.型煤的炼焦煤料,散密度高,炼焦过 程中收缩小,焦炭裂纹少 5.型煤中添加一定量的黏结剂,对焦炭 有一定程度的改善作用
一、煤预热炼焦技术
(3)工业化问题 1.预热煤储运过程中氧化变质和黏结性发生变 化的 2.膨胀压力和推焦电流增大
3.粉尘不易控制
二、煤干燥与调湿
(1)原理 利用外加热能将炼焦煤料在炼焦炉外 进行干燥、脱水以降低入炉水分,或对入 炉煤的水分调节,以控制炼焦耗热、改善 焦炉操作、提高焦炭质量或扩大弱黏结性 煤的用量的炼焦技术。
三、型煤炼焦
3.水分含量 水分过高,成型时煤料含量减少,压紧程 度差,直接影响它的密度和压溃强度。同 时对黏结剂(沥青)黏合不利。 水分过低,影响压球时脱模,降低型煤成 品率。
三、型煤炼焦
4.粉碎粒度 过粗易出现裂纹,影响压溃强度,过细, 不仅混合困难,而且必须增大黏结剂的使 用量。 一般控制成型原料煤的粉碎粒度以<3mm 的占80%~85%为宜。
一、煤预热炼焦技术
A、提高煤料的流动度、加宽塑性温度区间 B、热解速度增大、缩聚速度减小、胶质体液 相产物增多 C、提高胶质体的平均温度,降低其黏度、增 加其流动性
一、煤预热炼焦技术
3.结焦过程的影响 A、炭化室内距炉墙不同距离处炉料的温度梯 度减小 B、焦饼中心温度曲线发生变化,达到相同焦 饼中心温度所需时间缩短