北航微小型发动机装配实验
航空发动机装配实训报告

一、引言航空发动机是飞机的心脏,其性能直接影响着飞机的飞行安全、经济性和环保性。
为了提高我国航空发动机的研发水平和制造质量,培养一批具备实际操作能力的航空发动机装配人才至关重要。
本次实训旨在通过实际操作,使学生掌握航空发动机装配的基本技能和知识,提高动手能力和团队协作能力。
二、实训目的1. 使学生了解航空发动机的结构和组成,熟悉各类部件的名称、功能及装配要求;2. 掌握航空发动机装配的基本工艺和操作流程;3. 提高学生实际操作能力,培养严谨的工作态度和团队协作精神;4. 了解航空发动机装配过程中的质量控制要点。
三、实训内容1. 航空发动机基础知识(1)航空发动机的分类及特点;(2)航空发动机的组成及各部件功能;(3)航空发动机的工作原理。
2. 航空发动机装配工艺(1)装配前的准备工作,包括工具、设备、材料等;(2)装配过程中的注意事项,如装配顺序、装配力矩、装配间隙等;(3)各类部件的装配方法,如轴类、齿轮、叶片等;(4)发动机总装的顺序和步骤。
3. 航空发动机装配质量控制(1)装配过程中的质量检查方法,如外观检查、尺寸测量、性能测试等;(2)装配过程中常见问题的处理方法;(3)提高装配质量的措施。
四、实训过程1. 实训前期准备(1)了解实训目的、内容和方法;(2)熟悉实训场地、设备、工具和材料;(3)制定实训计划,明确各阶段任务和目标。
2. 实训过程(1)按照装配工艺要求,进行各类部件的装配;(2)在装配过程中,注意观察各部件的配合情况,确保装配质量;(3)对装配完成的发动机进行质量检查,发现并解决存在的问题;(4)总结实训经验,提高装配技能。
3. 实训总结(1)对实训过程中遇到的问题进行分析和总结;(2)评估实训效果,总结实训经验;(3)撰写实训报告。
五、实训心得1. 航空发动机装配是一项复杂、精密的工作,要求操作人员具备较高的技术水平和严谨的工作态度;2. 装配过程中,要注意各部件的配合情况,确保装配质量;3. 团队协作在装配过程中至关重要,要相互配合,共同完成任务;4. 通过实训,提高了自己的实际操作能力,为今后从事航空发动机装配工作打下了基础。
北航小型航空发动机整机试验报告

北航小型航空发动机整机试验报告一、试验目的本次试验旨在测试和评估北航研发的小型航空发动机整机的性能和可靠性,为将来的工程应用提供参考和指导。
二、试验方法1.实验设备:小型航空发动机整机、测量仪器、数据记录设备等。
2.试验项目:a.静态试验:评估发动机的冷启动、热启动、怠速运行、加速和减速响应等性能指标。
b.动态试验:评估发动机在不同工况下的动力输出、燃油消耗、振动和噪音等指标。
3.试验步骤:a.安装和连接仪器设备,准备试验现场。
b.进行静态试验,记录并分析各项性能指标。
c.进行动态试验,记录并分析各项性能指标。
d.将试验数据进行整理和分析,并撰写试验报告。
三、试验结果1.静态试验结果:a.冷启动:平均启动时间为X秒,启动可靠性达到X%。
b.热启动:平均启动时间为X秒,启动可靠性达到X%。
c.怠速运行:平均转速为X转/分钟,稳定性达到X%。
d.加速响应:平均加速时间为X秒。
e.减速响应:平均减速时间为X秒。
2.动态试验结果:a.动力输出:在不同工况下,发动机的最大推力分别为X牛顿、Y牛顿等。
b.燃油消耗:在不同工况下,发动机的燃油消耗率分别为X升/小时、Y升/小时等。
c.振动:在满负荷运行时,发动机的振动指标为X。
d.噪音:在满负荷运行时,发动机的噪音水平为X分贝。
四、试验结论根据实验结果和数据分析,北航小型航空发动机整机在静态试验和动态试验中的性能表现优秀。
发动机启动可靠性高、稳定性良好、加减速响应快。
动力输出优秀,燃油消耗率低。
振动和噪音水平也在合理范围内。
整体上,该发动机适用于小型航空器,并具有潜力用于工程应用。
五、改进建议在试验过程中,发现了一些小缺陷,但对整体试验结果并不产生重大影响。
建议在后续工程应用中进一步改进和优化发动机的细节设计,以进一步提升性能和可靠性。
[1]《航空发动机试验报告实施导则》[2]《飞行器推力性能的试验与分析方法》[3]《飞行器噪声评价方法与试验指南》以上报告为北航小型航空发动机整机试验的初步结果,具体数据和结论会根据后续进一步分析和研究进行完善和修正。
北京航空航天大学 微小型飞行器结构静力试验 大作业

微小型飞行器结构静力试验航空科学与工程学院航空创新实践基地1 综述1.1实验目的1.掌握微小型飞行器结构静力试验的基本原理与方法;2.掌握应变、位移的测量方法,掌握加载的方法;3.掌握结构有限元静力分析与静力试验验证的方法;4.熟悉飞机结构强度规范中对静力试验的要求;5.制定静力试验大纲。
1.2实验内容1.测试翼梁截面尺寸相同的直机翼如错误!未找到引用源。
所示,在其升力作用下的应力、应变和位移。
2.将测试结果与结构有限元静力分析结果进行对比分析。
机翼示意图1.3实验仪器、设备1.支持系统(承力顶棚、承力地坪、承力墙)2.加载系统3.应变测试仪4.位移测试仪5.待测对象1.4实验注意事项1.确保各部位连接安全可靠,尤其注意机翼根部和承力墙之间的连接。
2.试验前制定详细而周密的试验大纲,并组织评审。
试验时严格按照试验大纲进行试验。
3.加载钢丝上悬挂醒目标志物,以防止人员绊倒和损坏试验件。
4.出现异常和紧急情况,应冷静对待,立刻报告试验指导教师。
2 建模计算模型与实验分析2.1仿真并制定加载方案根据附1中的实验对象描述,对飞机机翼建立了气动模型以及结构有限元模型,并计算了气动力。
由于CFD模型(或其他方法)计算所得的气动力数据是分布载荷,而实验的加载方案需要集中载荷,所以需要对CFD模型的气动力数据进行处理,将其转化为分散的集中载荷。
实验加载点的位置已经在附1中给定,在进行载荷转换时,要将分布载荷转换成制定加载点位置的集中载荷。
在将分布载荷转化为加载点位置的集中载荷时,需要保证以下三点:1. 保证分布载荷的合力与集中载荷的合力相等;2. 保证分布载荷的合力矩与集中载荷的合力矩相等;3. 使各个截面上的分布载荷以及集中载荷所产生的合力矩与合力尽量相等。
如上图所示,左侧为分布载荷情况(即CFD计算结果),右侧为集中载荷情况(实验加载方案)。
将分布载荷转化为集中载荷时应当保证,找到一组F1、F2,使得右图中sectionA以及sectionB两个截面上的弯矩以及剪力与左图保持一致。
航空发动机装配难点与装配质量控制措施研究

航空发动机装配难点与装配质量控制措施研究摘要:本文重点研究了航空发动机装配质量的影响因素,通过分析装配过程中的存在的问题找到质量提升的有效措施,为后期的航空发动机装配工作提供重要的参考。
关键词:航空发动机;装配难点;装配质量控制引言:为了提升发动机零配件装配效果与效率,必须在研究影响装配原因的前提下采用针对性质量管理方法。
一、航空发动机装配技术的重要性航空发动机属于飞机机身的动力部分其加工质量的优劣直接关系到飞机使用寿命与使用效果。
众所周知航空发动机的制造与装配属于一项高精尖的工作,所以在常规的装配过程中相关的工作人员一定要提升自身的专业水平,在工作开始前利用高新技术手段做好准备工作有效排除各方面的影响因素,对每一个环节的质量都要进行的把关确保航空发动机装配质量的有效提升。
航空飞机的主要动力来源就是发动机,所以发动机质量的好坏直接影响飞机的使用寿命。
因此在航空发动机装配的过程中装配人员一定要严格按照相关的工序开展工作,有效发挥各个零部件之间的作用,最大限度地提升发动机的性能。
而且为了有效提升航空发动机装配的质量和效率,需要在工作开始前对影响装配质量的各项因素进行详细的分析,识别其中的问题风险并进行及时的处理,为航空发动机装配质量的提升奠定坚实的基础。
二、影响航空发动机装配质量的主要因素(一)航空发动机本身的结构比较复杂,对装配的技术要求较高航空发动机的装配本就是一项较为系统的工程其中涉及大量的零部件和复杂的工序,每一个环节落实不到位都有可能影响整体航空发动机的性能。
也正因如此航空发动机的装配质量会受到多方因素的共同影响,所以要想从根本上做好质量控制工作就一定要加强装配人员的调度与管理。
众所周知航空发动机的装配虽然工序复杂,但是操作起来还是具有相对的灵活性,因此相关的管理人员可以组织一个优秀的装配团队优先完成难度较大的装配工作,最大限度地提升装配的效率和质量。
(二)航空发动机的装配质量管理意识不强当前我国的高精尖领域仍处于初级探索阶段,所以对于航空发动机的装配工作还需要进行多方面的探索。
微型飞机发动机

篇一:《北航小型航空发动机整机试验报告》北京航空航天大学研究生课程实验报告小型航空发动机整机试验报告共12页(含封面)学生姓名学生学号任课老师联系方式能源与动力工程学院年月一、试验简介1 试验目的了解小型航空发动机整机试验过程,熟悉发动机试车台结构和发动机上下台架操作步骤,了解发动机整机测试系统掌握发动机试车过程操作方法,学习发动机试验数据处理及总体性能计算。
2 试验内容a) 发动机上下台架操作;b) 发动机试车过程控制操作;c) 发动机试验数据处理及总体性能计算。
3发动机、试车台以及CAT系统简介1发动机简介本次试验所用的WPXX发动机是一台小型、单轴、不带加力燃烧室的涡轮喷气发动机,主要由以下几部分构成a) 压气机组合式压气机,由一级跨音轴流压气机和一级单面离心压气机组成;b) 燃烧室轴内供油式环形燃烧室,使用靠离心力甩油的甩油盘供油;c) 涡轮单级轴流式涡轮;d) 尾喷管简单收敛式不可调节的尾喷管。
发动机的主要技术参数为海平面静止最大推力为850公斤,空气流量15kg/s,压气机增压比5,涡轮前温度1200k,转速22000r/min。
发动机的主要工作状态划分2试车台系统a) 燃油系统;b) 数字控制系统;c) 油滤、油路、起动供油系统;d) 滑油系统;e) 起动系统;f) 电气系统测试附件。
3计算机辅助测试系统(CAT)1)传感器选型原则a) 灵敏度高,输入和输出之间应具有良好的线性关系;b) 噪声小,滞后、漂移误差小;c) 常用的测量值大小约为传感器最大量程的2/3左右,最小值不低于1/3;d) 动态特性好;e) 接入测量系统时对测量产生的影响小;2)数据采集系统的主要评定指标a) 分辨率b) 采集速度c) 线性度d) 误差限3)CAT系统与一般系统相比,CAT系统包含了数采数据又高于数采系统。
二、数据处理1相关理论知识发动机工作参数对标准大气条件的换算公式a)发动机转速nc?b) 发动机推力Fc?F{微型飞机发动机}.r/min) ;{微型飞机发动机}.10325(daN) ;p0{微型飞机发动机}.288(K) ;273?t0c) 发动机涡轮后燃气温度Tt5c?Tt5d)发动机燃油消耗量Wfc?Wfkg/h);WfcFc(kg/daNgh)。
航空发动机拆装实训报告

一、实习背景随着我国航空事业的飞速发展,航空发动机作为飞机的核心部件,其性能直接关系到飞机的飞行安全和效率。
为了提高我国航空发动机的维修技术水平,培养一批具备实践操作能力的航空发动机维修人才,我们开展了本次航空发动机拆装实训。
二、实习目的1. 通过实习,使学生了解航空发动机的基本结构、工作原理和拆装方法,掌握航空发动机的维修技术。
2. 培养学生严谨的工作态度和良好的职业素养,提高学生的动手操作能力。
3. 巩固和深化所学理论知识,使理论与实践相结合。
三、实习内容1. 航空发动机基础知识实习过程中,我们首先学习了航空发动机的基本结构、工作原理、分类、型号等基础知识,为后续的拆装实训打下了坚实的理论基础。
2. 航空发动机拆装实训(1)拆装工具及设备的使用在实习过程中,我们熟悉了拆装航空发动机所需的工具和设备,如扳手、螺丝刀、锤子、钳子、水平仪、千分尺等。
掌握了这些工具和设备的使用方法,为拆装实训提供了有力保障。
(2)发动机总体拆装在拆装过程中,我们按照以下步骤进行:① 拆卸发动机外罩,暴露发动机内部结构;② 拆卸发动机前端部件,如起动机、发电机、燃油泵等;③ 拆卸发动机中后端部件,如涡轮、压气机、燃烧室等;④ 拆卸发动机附件,如油底壳、机油滤清器、冷却器等。
(3)发动机零部件拆装在拆装发动机零部件时,我们按照以下步骤进行:① 拆卸发动机主要部件,如涡轮盘、压气机盘、燃烧室等;② 拆卸发动机零部件,如涡轮叶片、压气机叶片、燃烧室喷嘴等;③ 检查零部件磨损、损坏情况,进行更换或维修;④ 按照拆卸顺序,将零部件重新装回发动机。
3. 航空发动机装配实训在装配过程中,我们按照以下步骤进行:① 装配发动机零部件,如涡轮叶片、压气机叶片、燃烧室喷嘴等;② 装配发动机主要部件,如涡轮盘、压气机盘、燃烧室等;③ 装配发动机附件,如油底壳、机油滤清器、冷却器等;④ 装配发动机前端部件,如起动机、发电机、燃油泵等;⑤ 装配发动机外罩,完成发动机装配。
航空发动机拆装实习报告
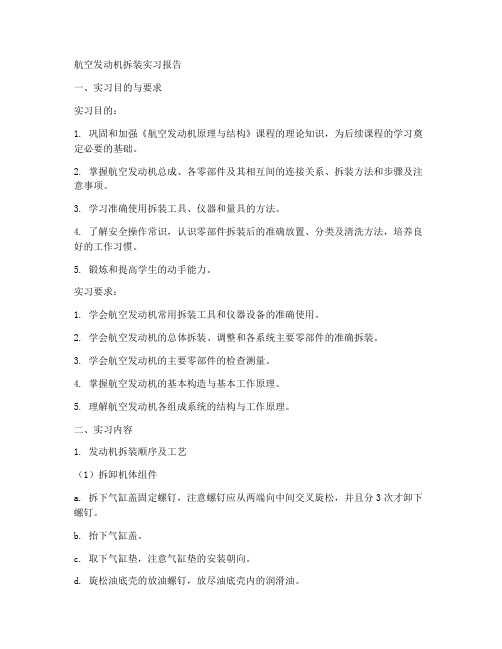
航空发动机拆装实习报告一、实习目的与要求实习目的:1. 巩固和加强《航空发动机原理与结构》课程的理论知识,为后续课程的学习奠定必要的基础。
2. 掌握航空发动机总成、各零部件及其相互间的连接关系、拆装方法和步骤及注意事项。
3. 学习准确使用拆装工具、仪器和量具的方法。
4. 了解安全操作常识,认识零部件拆装后的准确放置、分类及清洗方法,培养良好的工作习惯。
5. 锻炼和提高学生的动手能力。
实习要求:1. 学会航空发动机常用拆装工具和仪器设备的准确使用。
2. 学会航空发动机的总体拆装、调整和各系统主要零部件的准确拆装。
3. 学会航空发动机的主要零部件的检查测量。
4. 掌握航空发动机的基本构造与基本工作原理。
5. 理解航空发动机各组成系统的结构与工作原理。
二、实习内容1. 发动机拆装顺序及工艺(1)拆卸机体组件a. 拆下气缸盖固定螺钉,注意螺钉应从两端向中间交叉旋松,并且分3次才卸下螺钉。
b. 抬下气缸盖。
c. 取下气缸垫,注意气缸垫的安装朝向。
d. 旋松油底壳的放油螺钉,放尽油底壳内的润滑油。
(2)拆卸曲轴轴承盖、连杆轴承盖a. 旋下曲轴轴承盖固定螺钉,取下曲轴轴承盖。
b. 旋下连杆轴承盖固定螺钉,取下连杆轴承盖。
(3)拆卸活塞连杆组a. 取出活塞销,取下活塞。
b. 依次拆下连杆轴承盖、连杆小头盖,取下连杆。
(4)拆卸曲轴a. 拆下曲轴前、后轴承盖。
b. 使用专用工具拆下曲轴。
2. 发动机装配顺序及工艺(1)安装曲轴a. 确认曲轴轴承盖、连杆轴承盖的位置。
b. 按照顺序安装曲轴轴承盖、连杆轴承盖。
c. 紧固曲轴轴承盖、连杆轴承盖固定螺钉。
(2)安装活塞连杆组a. 确认连杆轴承盖、连杆小头盖的位置。
b. 按照顺序安装连杆轴承盖、连杆小头盖。
c. 插入活塞销,安装活塞。
(3)安装机体组件a. 确认气缸盖的位置。
b. 按照顺序安装气缸盖。
c. 紧固气缸盖固定螺钉。
(4)检查发动机装配质量a. 检查各零部件的装配间隙。
北航小型航空发动机整机试验报告

北京航空航天大学研究生课程实验报告小型航空发动机整机试验报告共12页(含封面)学生姓名:学生学号:任课老师:联系方式:能源与动力工程学院年月一、试验简介1.1 试验目的了解小型航空发动机整机试验过程,熟悉发动机试车台结构和发动机上下台架操作步骤,了解发动机整机测试系统掌握发动机试车过程操作方法,学习发动机试验数据处理及总体性能计算。
1.2 试验内容a)发动机上下台架操作;b)发动机试车过程控制操作;c)发动机试验数据处理及总体性能计算。
1.3 发动机、试车台以及CAT系统简介1.3.1发动机简介本次试验所用的WPXX发动机是一台小型、单轴、不带加力燃烧室的涡轮喷气发动机,主要由以下几部分构成:a)压气机:组合式压气机,由一级跨音轴流压气机和一级单面离心压气机组成;b)燃烧室:轴内供油式环形燃烧室,使用靠离心力甩油的甩油盘供油;c)涡轮:单级轴流式涡轮;d)尾喷管:简单收敛式不可调节的尾喷管。
发动机的主要技术参数为:海平面静止最大推力为850公斤,空气流量13.5kg/s,压气机增压比5.5,涡轮前温度1200k,转速22000r/min。
发动机的主要工作状态划分:1.3.2试车台系统a)燃油系统;b)数字控制系统;c)油滤、油路、起动供油系统;d)滑油系统;e)起动系统;f)电气系统测试附件。
1.3.3计算机辅助测试系统(CAT)1)传感器选型原则:a)灵敏度高,输入和输出之间应具有良好的线性关系;b)噪声小,滞后、漂移误差小;c)常用的测量值大小约为传感器最大量程的2/3左右,最小值不低于1/3;d)动态特性好;e)接入测量系统时对测量产生的影响小;2)数据采集系统的主要评定指标:a)分辨率b)采集速度c)线性度d)误差限3)CAT系统:与一般系统相比,CAT系统包含了数采数据又高于数采系统。
二、数据处理2.1 相关理论知识发动机工作参数对标准大气条件的换算公式:a)发动机转速:/min) c n r =;b) 发动机推力:0101.325() c F FdaN p =; c) 发动机涡轮后燃气温度:55288() 273t c t T T K t =+;d)发动机燃油消耗量:/)fc fW W kg h =;e) 发动机单位推力燃油消耗量: (/)fc cW sfc kg daN h F =g 。
- 1、下载文档前请自行甄别文档内容的完整性,平台不提供额外的编辑、内容补充、找答案等附加服务。
- 2、"仅部分预览"的文档,不可在线预览部分如存在完整性等问题,可反馈申请退款(可完整预览的文档不适用该条件!)。
- 3、如文档侵犯您的权益,请联系客服反馈,我们会尽快为您处理(人工客服工作时间:9:00-18:30)。
2、尺寸链计算 本实验中的尺寸链计算分两步进行:第一,测量所需要的各个尺寸;第二, 根据相应公式计算出不加垫片时的间隙值。 (1)压气机叶轮与前内导流罩之间的间隙 m ={轴套(L)+扩压器 2 总高-2 mm }-{(压气机叶轮高(h)-31.2 mm)+轴 承厚(8mm)+轴(L)} 测量值如下(均为测量 3 组数据取其平均值) : 轴套(L)=96.95mm,扩压器 2 周向宽度=30.02mm,压气机叶轮周向宽度(h) =46.08mm,轴(L)=101.63mm 带入公式,计算得: m=(96.95+30.02-2)-{(46.08-31.2)+8.00+101.63}=0.46mm >0.3mm 选择不加垫片,压气机叶轮与前导流罩之间的间隙值仍为 0.46mm。 (2)涡轮转子与导向器之间的间隙 n ={轴承厚 (8mm) +涡轮转子 (l) }-{轴套 (S ) -转子轴套 (L) +导向器 (h3+h4-h1) } 测量值如下(均为测量 2~3 组数据取其平均值) : 涡轮转子(l)=14.24mm,轴套(S)=106.65mm,转子轴套(L)=96.95mm, 导向器 h3=33.53mm,h4=35.00mm,h1=56.08mm。 带入公式,计算得: n={(8.00+14.24)}-{106.65-96.95+(33.53+35.00-56.08)}=0.09mm>0 选择不加垫片涡轮转子与导向器之间的间隙值仍为 0.09mm。
WWP20 微型发动机装配实验报告
姓 学
名 号
同组学生 日 期
北京航空航天大学能源与动力学院
1、简述发动机结构 在本实验中我们采用的是 WWP20 小型涡轮喷气发动机,其主体结构包括:进气 道、压气机、燃烧室、涡轮、尾喷管。 具体有如下小部件:前外导流罩(外壳体) 、前内导流罩、离心式压气机叶轮、 扩压器 1、扩压器 2、滑油管、轴套、主轴、燃油-丙烷气体总管、环形燃烧室、 涡轮导向器、压紧盘、轴承、涡轮转子、发动机壳体、调整垫片、FESTO 接头、 甩油盘和垫片、密封橡胶圈、锁紧螺母。
4
4、左手持扩压器 2—轴套组件,保持其上顶端滑油孔朝上;右手持燃烧室 组件, 保持燃烧室的火花塞孔朝上,将燃油管和丙烷气体分别插入扩压器 2 的两 个较大的孔,向下用力,将燃烧室组件插到底即可,并调整各管伸出扩压器 2 孔的距离; 5、将扩压器 2 滑油管孔置于 12 点钟方向;扩压器 1 放在扩压器 2 上,使滑 油管孔、燃油管孔,丙烷气孔的位置分别对应,再安装固定扩压气罩的螺钉(实 际装配中应先用手拧,再有限力扳手按对角线顺序拧紧固定) 。拧完后应适当调 整各管使其不出头; 6、安装涡轮导向器,安装过程中注意对准涡轮导向器螺纹孔与燃烧室螺纹 孔的位置,并用螺钉固定。安装压紧盘,用特制扳手拧紧压紧盘。拧紧固定燃烧 室的六角螺钉; 7、安装涡轮侧轴承后安装涡轮转子,用橡皮锤敲击配合安装,最后用螺母 固定; 8、压气机侧轴承孔内垫片、甩油盘、密封圈、轴承以及涡轮轴组合件与静 子组件的安装,使用镊子、橡皮锤和工装配合安装; 9、安装压气机叶轮,利用工装套筒和橡皮锤轻敲使叶轮安装到位,并用前 端螺帽拧紧压气机; 11、将橡胶圈套在前内导流罩的槽中,安装前内导流罩,注意滑油管的位置 应放在 12 点钟方向; 12、在内导流罩上安装压缩空气启动接头、转速传感器,在扩压器 2 上安装 滑油接头、燃油管接头、丙烷气管接头,在发动机壳体上安装点火电热塞座,安 装前外导流罩和发动机壳体。
2
5、动平衡 首先,测量转子的几何尺寸和重量,并计算出转子所允许的振动量。 m=0.0509kg,r1=19.105,r2=19.105,a=18.958mm,b=38.024mm,c=18.958mm, 定标所用的铝螺钉质量为 0.213g,计算所允许的振动量 0.076 g.mm。 然后,打开计算机,进行平衡前调试(调节传感器使屏幕上的转速稳定、观察 待平衡转子是否有轴向窜动) 。 接下来,设置转子参数,并进行平衡机的定标(校准) ,操作过程中参照实验 指导书,不再赘述。 开始平衡测量,根据屏幕所显示的角度和不平衡重量开始加、减配重,注意, 转子两个校正面的角度都以端面 2 所标示的角度为标准,重复操作此步骤,直到 屏幕上显示振动量在合格范围内。 添加配重质量和位置如下表:
1
2
3
4
5
6
7
3
6、实物装配 装配前进行尺寸链的测量和计算,结果见尺寸链计算部分,在本次装配选择 不加调整垫片。 涡轮导向器的安装、 扩压器 2 的安装以及涡轮转子的安装等热装 配与报告中“过盈配合”部分采用相同的方法,适当调整加热或者冷却温度,但 是出于保护实验器材和节省时间的考虑,不再重复操作,参见过盈装配部分,在 此不再详述。装配过程如下: 1、将轴套和滑油管孔和扩压器 2 的滑油管孔对齐,均垂直朝上,将轴套插 入扩压器 2 中,转动轴套对齐螺纹孔,并用螺钉固定轴套和扩压器 2(在实际的 装配中应该使用限力扳手) ; 2、用手握紧压气机 2 一侧滑油管,扭动滑油管并将油管两端分别插入扩压 器 2 和轴套的滑油管孔中。安装完之后,可用改锥调整滑油管伸出的长度为 8~10mm; 3、将燃油丙烷总管插入燃烧室的定位孔中,燃烧室的火花塞孔垂直朝上, 丙烷气管口与油管口的连线大约垂直于燃烧室的火花塞口。将电炉丝弯成“U” 型,按电炉丝孔的位置穿入并拧紧;
6
7、实验小结 通过本次试验,我对航空发动机的内在结构及相关内容有了更加深刻的认 识,具体可以体现在以下几个方面:1、发动机的装配流程;2、发动机的油路系 统;3、发动机各部件之间的配合要求;4、机械系统的动平衡试验流程;6、部 件的热装配注意事项。
5
6、其它 实验过程是紧张而充实的, 由于在课前预习了实验指导书,再加上老师在操 作前的耐心讲解,小组成员的默契配合,整个实验过程还算顺利,很有成就感。 我们是第一组做动平衡实验的小组,在大家的努力下,两个端面均很快进入 合格范围。热装配和尺寸链测量计算,小组成员一起动手,也顺利完成。 但实际装配过程并不是一帆风顺的, 第一次装配出现一点问题: 装配完成后, 拨动压气机叶轮,发动机并不能很流畅的转动,并且有明显的碰磨声。拆开检查 发现,原来是误将某垫片当成甩油盘安装了。在换上甩油盘,重新安装后,发动 机转动非常流畅,没有一丝异响,得到老师的赞许。 通过这次实验我了解到,发动机的装配是非常精确、严谨的,要想深入了解 发动机,必须了解发动机的装配,这对于现在的我来说还有很长的路要走。同时 通过这次实验发现自己的动手能力有待提高。
1
3、过盈配合 测量轴与压气机盘配合一端的直径、压气机盘内径。 测量值(均为测量 3 组数据取其平均值) : 轴压气机端 D=9.035mm,压气机盘内径 d=9.022mm D-d=+0.015mm,可以进行过盈装配。 装配过程如下: 1、将压气机盘放入加温炉内加热至 400℃,将轴放入液氮冷却箱中降温至 -70℃,保持两者此时的温度 20 分钟。 2、一人戴隔热手套取出冷却的轴,将其插入工装台上相应的孔中,注意与 盘配合的一头朝上并保持竖直,另一人手戴隔热手套用钳子取出加温炉中的盘, 将盘孔对准轴平放,手持橡皮锤敲击使其准确配合。 由于温度变化非常快,对装配的影响很大,故此操作需要快速而有序,两人 紧密配合。
4、无损检测 本实验采用低频磁力探伤仪进行无损检测,其工作原理为: 直流电产生的磁场通常能渗入到零件的内部去, 而交流电产生的磁场都集中 在零件的表面上, 低频磁力探伤仪综合了交流和直流的优点,电流的频率与探伤 的深度成反比。 采用低频电流基本接近于电流的探伤深度,而低频电流是一种脉 动电流,它能使磁粉行列轻微的振动,有助于磁粉的排列并形成磁痕,同时低频 电流又具有交流电的特点,探伤后不用退磁。在本实验中,不采用磁粉探伤的方 式,而采用“磁力探伤缺陷显示膜”来显示试件的缺陷情况。 其操作流程如下: 首先将探头直接与交流连线相连接即可接入 220 V 工频电流使用;然后,将 缺陷显示纸平整的放在试件表面;最后,将探头放在工件上,按下开关可开始探 伤,显示纸即可显示出缺陷位置。探伤之后,再次按下按钮脱开探头与工件,拿 下显示纸,本次检测结束。