基于PLC的电动机制动控制系统设计
基于PLC的步进电机控制 (课程设计)

本文介绍了本实验旨在完成使用PLC(Programmable Logic Controller)控制步进电机的整步运行、正反转运行、快慢速运行以及定位运行。
文中指出本次使用的编程思想主要为模块化设计即为完成任务可对程序划分为主程序及子程序。
由于步进电机需要脉冲来运行,所以本程序使用PTO高速脉冲输出脉冲。
在定位程序中则应用到中断子程序命令。
另外,本文为更好的阐述实验内容,加入了与之前完全不同的方式的对比实验。
在对比试验中则应用计时器来完成步进电机的脉冲产生,另步进电机的各种功能则使用了一般的设计方式来实现。
二者完成完全相同的功能。
关键词:PLC 步进电机 PTO高速脉冲1 实验内容 (1)1.1实验任务 (1)1.2实验要求 (1)2 实验设备 (2)2.1步进电机简介 (2)2.2 PLC简介 (2)3 设计过程 (3)3.1设计思想 (3)3.2程序设计 (4)4 对比实验 (12)4.1对比程序思想 (12)4.2对比程序 (14)谢辞 (15)参考文献 (16)1实验内容1.1实验任务本次实验要求改变PLC脉冲输出信号的频率,实现步进电机的速度控制。
同时按下K1、K2、K3按钮,步进电机进行整步运行。
按下慢/快按钮,电机慢/快速运行。
用PLC 输出脉冲的个数,实现步进电机的精确定位。
在整步运行状态下,设脉冲数为一固定值,并用计数器进行计数,实现电机的精确定位控制。
按下停止按钮,系统停止工作。
1.2实验要求本设计要求使用步进电机。
选用的步进电机为二项混合式,供电电压24VDC,功率30W,电流1.7A,转矩0.35NM,步矩角1.8º/0.9º,并配有细分驱动器,实现细分运行,减少震荡。
本设计要求选用PLC设计出输出频率可变的控制程序,实现对步进电机的速度、方向、定位、细分等控制功能。
本设计旨在培养综合设计能力、创新能力、分析问题与解决问题的能力。
掌握PLC 控制的步进电机控制系统的构成及设计方法;掌握PLC控制程序设计、调试的方法。
基于PLC的步进电动机软起、停控制设计

t e se p rmo o a e s f sat/ t p mo t l o e s r h h tp e t rc n b o t r so s s o hy t n u e t e t s
sa iiy On t e o h rtm e,h ma r qu n y l e i c e s d t blt . h t e i te x fe e c wilb n r a e
机时 的平稳性 。同时可 使 步进电 动机 的最高 运行 频率 提高
2—8 而 不 失 步 。 倍 关键 词 :L R MP; 进 电动 机 ; 起 动 P C;A 步 软
中图分类号 : M3 36 T 8 .
Байду номын сангаас
文献标识码 : A
文 章 编 号 :04— 0 8 20 )9— 0 5— 2 10 7 1 (0 6 0 0 2 0
O Y NGS n—ti, H U Qn , U U A a a Z O i O  ̄NGX i ( . n nIstt o E gneig X a g n4 0 C ia 1 Hu a ntue f n ier , int 1 4, hn ; i n a 1 1 2 S a g a Daj U i ri ,h n h i 0 2 0 C ia3 E s C iaJ oo gU i r t, ac a g 3 0 3 C ia . h nh i i i nv sy S ag a 2 0 4 , hn ;. at hn i t nv sy N nh n 0 1 , hn ) n e t a n ei 3
A bsr c Th u c in t e fa u e n h ppy m eh d t a t: e f n to s,h e t r sa d t e a l t o s
基于PLC的电动机控制系统设计

第4期(总第173期)2012年8月机械工程与自动化MECHANICAL ENGINEERING & AUTOMATIONNo.4Aug.文章编号:1672-6413(2012)04-0140-02基于PLC的电动机控制系统设计袁连余(盐城生物工程高等职业技术学校,江苏 盐城 224051)摘要:介绍了PLC的工作原理,电动机控制系统采用ARM芯片作为系统主控芯片,搭配具有强大控制能力的PLC,实现了同时对多个电动机的控制,提供多种模式的选择,并且可以实时显示电动机状态。
经实践证明,本系统具有较高的实用价值。
关键词:PLC;电动机;控制系统;设计中图分类号:TM301∶TP273 文献标识码:A收稿日期:2012-02-27;修回日期:2012-03-18作者简介:袁连余(1974-),男,江苏盐城人,讲师,本科,研究方向为自动化及电工技术。
0 引言目前,车间大型生产设备多数是由电动机作为作动器进行工作的,其通过对电动机的启动、停止、转速、角度等的控制达到对生产设备状态进行控制的目的,进而实现对整个工作流程和生产效率的控制。
作为动力之源的电动机负担了整个系统的动力输出和控制,而对电动机的状态控制一般采用继电器来进行操作。
与传统的机械式控制相比,PLC具有可靠性高、易于安装和升级、抗电磁干扰能力强以及故障调试方便等优点,对当前需要自动化控制的大型工业非常适合,得到了行业的认可,并且具有广阔的应用前景。
1 PLC的工作原理可编程序控制器(Programmable Logic Controller),简称PLC,是在继电顺序控制基础上发展起来的以微处理器为核心的通用的工业自动化控制装置。
PLC采用了典型的计算机结构,主要由微处理器(CPU)、存储器(RAM/ROM)、输入输出接口(I/O)电路、通信接口及电源组成。
PLC的内部结构如图1所示。
PLC按控制等效电路可分为输入、输出及控制3个部分。
1.1 输入部分输入部分主要负责采集外部指令及设备状态,以使CPU作出判断。
基于PLC的机电控制课程设计报告

基于PLC的机电控制课程设计报告1. 摘要本文主要介绍了一种基于PLC(可编程逻辑控制器)的机电控制系统设计方法。
本设计以某机电设备为对象,通过分析其控制需求,设计了PLC控制系统,并实现了对机电设备的精准控制。
本报告包括系统硬件选型、软件编程、系统调试和性能评估等部分。
2. 项目背景随着工业自动化技术的不断发展,PLC控制系统在各类机电设备中的应用越来越广泛。
为了提高学生对PLC控制技术的理解和应用能力,本课程设计要求学生针对一个实际的机电设备,设计并实现基于PLC的控制系统。
3. 系统需求分析3.1 控制对象分析本设计以一台电动机为例,对其启动、停止、正反转、速度调节等控制需求进行分析。
3.2 控制功能需求根据电动机的运行特性,本设计需实现以下功能:1. 启动与停止:通过PLC控制电路实现电动机的启动和停止。
2. 正反转控制:通过PLC控制电路实现电动机的正反转。
3. 速度调节:通过PLC控制电路实现电动机转速的调节。
4. 故障保护:当系统发生故障时,PLC应能及时采取措施,保护设备和人员安全。
4. 系统硬件选型根据系统需求分析,选择合适的硬件设备,包括PLC、输入输出模块、传感器、执行器等。
4.1 PLC选型本设计选用西门子S7-200系列PLC,具备足够的输入输出点数,满足系统需求。
4.2 输入输出模块选型根据传感器和执行器的数量,选择相应的输入输出模块。
4.3 传感器选型本设计选用旋转编码器作为速度检测传感器,实现电动机转速的实时检测。
4.4 执行器选型本设计选用继电器作为执行器,实现电动机的启动、停止和正反转控制。
5. 系统软件编程根据系统需求分析,编写PLC控制程序,实现对电动机的精确控制。
5.1 程序结构设计本设计将程序分为以下几个部分:1. 主程序:负责整体控制流程的调度。
2. 子程序:负责实现具体的功能,如启动、停止、正反转等。
5.2 编程语言本设计采用西门子S7-200系列的编程语言,包括指令表和梯形图。
基于S7-1200PLC的步进电机控制系统
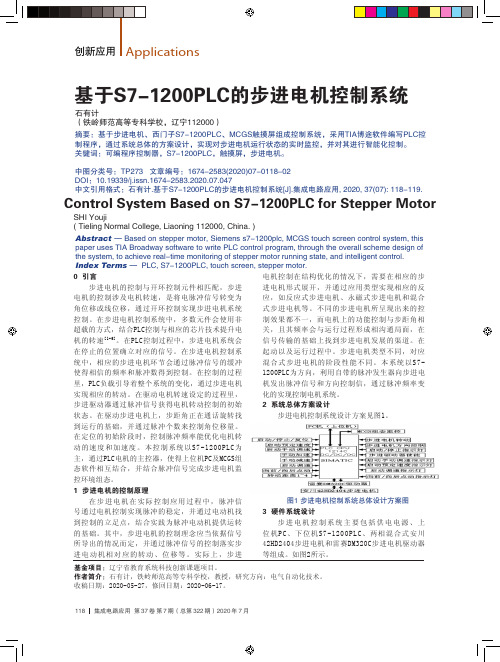
图1 步进电机控制系统总体设计方案图
3 硬件系统设计
步进电机控制系统主要包括供电电源、上
位机PC、下位机S7-1200PLC、两相混合式安川
42HD2404步进电机和雷赛DM320C步进电机驱动器
等组成。
如图2所示。
石有计,铁岭师范高等专科学校,教授,研究方向:电气自动化技术。
在编写PLC程序时,I/O接口会根据接线情况自动分配信号,对应的信号得以分配后。
信号控制会以输入输出口为主,将I/O接口作为主导。
输入变量如下:步进电机起动I0.0、步进电机停止I0.1、步进电机复位I0.2、步进电机向后点动I0.3、启动调速I0.4、启动预订速度I0.5、启动手动调速I0.6、手动加速I0.7、手动减速I1.0、转动距离1(3200)I1.1、转动距离2(32000)I1.3、转动距离3(64000)I1.3、转动距离4(96000)I1.4、步进电机向前点动I1.5。
输出变量如下:步进电机转动Q0.0、步进电机方向控制Q0.1、步进电机启动指示
4.2 PLC程序设计
本文采用S7-1200PLC作为主控器,结合硬件设计情况,对步进电机控制系统进行设计,并通过系6 结语
本文采用西门子S7-1200PLC,使用博途V15编程软件,进行步进电机控制系统设备组态及编程,有效实现步进电机控制要求。
实验结果表明,该系统动态特性好、精度高,达到了步进电机运行状态可视化和控制智能化的目的。
该系统具备控制过程的参考价值,对于高效率、小步距、低振动和低噪
图2 硬件接线设计图
表1 细分数和电流选择
图3 触摸屏运行界面。
基于PLC的伺服电机运动控制系统设计

基于 PLC 的伺服电机运动控制系统设计摘要:近年来,我国各个行业及领域广泛应用了PLC,对企业实现生产自动化奠定了重要的基础。
特别是PLC伺服电机运行控制系统的设计及实施,使电机运动质量与效率得到了进一步提升。
本文结合PLC伺服电机运行控制系统设计标准,以S7-1200为例,利用对程序与硬件的设计,保证了运动控制的精准性。
关键词:PLC;伺服电机;运行控制前言:伺服电机具有多重优点,如扛过载能力强、运行稳定、高速性能好以及精准度高等,已广泛应用在企业生产中。
但由于伺服电机大多使用的是NC数控系统,不仅运行成本高,且控制系统极为复杂,无法有效对接以PLC为主的控制器生产线,使得经济效益不是十分可观。
故而,在生产自动化水平的进一步提升下,为了最大程度保障产品精度性,就必须重视基础设计,通过对伺服电机运行控制准确性的提升,全面改善系统的生产效率与性能,从而实现经济效益最大化,降低企业的生产成本。
1基于PLC伺服电机控制系统设计分析PLC控制系统是一种专门用于工业生产的数字运算操作电子装置,其应用了一类可编程存储器,可满足内部存储、执行逻辑运算、顺序控制、定时、技术以及算数操作等要求,可以说是工业控制的核心。
就我国工业生产现状来看,大部分依然是采用的步进电机运动系统,其应用的步进电机步距角最小为0.36°(与电机转动一圈需要1000个脉冲相当),精度比较低,并且经常会出现失步问题,难以满足高精度生产工艺。
相比来讲伺服电机无论是在精度、速度、抗过载性能、响应速度、运行稳定性以及运行温度等方面均具有更大优势。
基于PLC进行伺服电机控制系统的设计,可以在原来的步进电机运动系统基础上,做进一步的优化,使得系统能够更好的适应高精度生产要求。
其中需要就目前所应用NC数控系统进行优化,解决其与PLC主控制器生产线无法有效对接的难题,满足高效生产的核心要求。
2伺服电机控制系统分析2.1运行控制模型如图1所示,伺服电机运行控制模型可用于构建伺服电机运动控制系统。
基于PLC的电机控制系统与实现
基于PLC的电机控制系统与实现摘要:PLC的电机控制系统在现代自动化生产中至关重要的,电机是现代自动化生产中最为常用的动力设备之一,是现代工业生产中必不可少的一环。
本文主要介绍了PLC电机控制系统的软件设计及实现,包括程序设计、编程语言、状态检测、动作控制、故障检测和报警处理等方面。
通过对软件设计的合理搭配和运用,可以构建出功能强大、稳定可靠的PLC电机控制系统,以满足不同工业应用场景的需求。
同时,本文还强调了软件设计在整个系统中的重要性,是整个系统的灵魂所在。
关键字:PLC电机控制系统;软件设计;编程语言0前言现代工业生产中,电机控制系统是必不可少的一环。
PLC(Programmable Logic Controller,可编程逻辑控制器)作为一种通用的工业控制设备,被广泛应用于电机控制系统中。
PLC电机控制系统可以实现电机的启动、停止、正转、反转、变速等控制操作,同时能够实时检测电机状态,监测故障,并给出相应的报警提示。
而这一切的实现离不开系统软件设计与实现。
本文将介绍PLC电机控制系统的软件设计,包括程序设计、编程语言、状态检测、动作控制、故障检测和报警处理等方面,以帮助读者更好地理解PLC电机控制系统的工作原理和软件设计流程。
1PLC的电机控制系统重要性PLC的电机控制系统在现代自动化生产中扮演着至关重要的角色。
电机作为现代自动化生产中最为常用的动力设备之一,其控制对于生产效率、产品质量、节能降耗等方面均具有重要意义。
PLC电机控制系统利用PLC的高效性能和可编程性,实现对电机的精准控制,能够提高生产线的稳定性、减少生产线的故障率、提高生产效率、降低能源消耗、优化生产成本等,从而极大地增强了生产线的竞争力。
因此,PLC的电机控制系统的重要性不言而喻,对于现代自动化生产具有不可替代的作用。
2PLC电机控制系统设计思路设计PLC电机控制系统的基本思路包括确定系统要实现的功能、选择适合的PLC型号、编写控制程序、选择合适的输入输出模块和传感器执行器、进行系统联调和测试、完成系统安装和调试以及完善系统文档和培训。
基于PLC的电机控制系统设计
基于PLC的电机控制系统设计自动化控制技术的革新随着工业自动化的发展,电机控制系统在各个领域的应用日益广泛。
基于PLC(可编程逻辑控制器)的电机控制系统设计应运而生,为电机控制提供了智能化、自动化的解决方案。
本文将详细介绍基于PLC的电机控制系统设计的原理、方法和实际应用,以期为自动化控制技术的革新提供有益的参考。
首先,我们需要了解PLC的基本概念。
PLC是一种可编程逻辑控制器,具有高度可靠性、灵活性和可扩展性。
它可以根据用户的编程逻辑对输入信号进行处理,并输出控制信号,实现对设备的自动控制。
在电机控制系统设计中,PLC可以实现对电机的精确控制,提高控制效率和准确性。
基于PLC的电机控制系统设计主要包括以下几个部分:1. 系统硬件设计:硬件设计是PLC控制系统的基础。
在硬件设计中,需要选择合适的PLC型号、输入输出模块、电源模块等,以满足系统的功能和性能要求。
此外,还需要考虑系统的抗干扰能力,确保在复杂的电磁环境中稳定工作。
2. 系统软件设计:软件设计是PLC控制系统的核心。
在软件设计中,需要编写PLC的梯形图程序,实现对电机的控制逻辑。
梯形图程序应能够根据输入信号的变化,自动调整电机的运行状态,实现电机的精确控制。
3. 系统集成与调试:系统集成是将PLC控制系统与其他设备(如电机、传感器等)相结合的过程。
在系统集成中,需要确保PLC控制系统与其他设施的正常通信和数据交换。
调试则是确保PLC控制系统按照预期工作,包括功能测试、性能测试等。
在实际应用中,基于PLC的电机控制系统具有以下优势:1. 高度可靠性:PLC具有高度可靠性,能够在恶劣的环境下稳定工作,确保电机控制系统的正常运行。
2. 灵活性:PLC控制系统易于编程和修改,可以根据实际控制需求调整控制策略。
3. 可扩展性:PLC控制系统具有良好的可扩展性,可以随时增加或减少控制功能,适应不断变化的控制需求。
4. 易于维护:PLC控制系统采用模块化设计,故障诊断和维护方便,降低了系统的维护成本。
基于plc的电机变频调速系统设计_毕业设计论文
基于plc的电机变频调速系统设计1 绪论1.1本课题研究目的和意义PLC具有结构简单、编程方便、性能优越、灵活通用、使用方便、可靠性高、抗干扰能力强、寿命长等到一系列优点[2]。
可编程控制器(PLC)的核心微处理器,通过将计算机技术与传统的继电器控制系统有机结合起来,能够实现高度灵活、高可靠性的工业控制。
为了进一步提高设备的自动化程度,越来越多的企业将PLC 技术应用于其工厂设备中。
将原有电机控制系统的技术进行改造,引入电机控制系统的数据自动采集、监控以及变频、组态技术完善并改进电机变频调速机构。
该系统能对电机转速实现精确控制,实用性强,具有一定的推广价值随着电力电子技术以及控制技术的发展,交流变频调速在工业电机拖动领域得到了广泛应用[5]。
交流调速取代直流调速和计算机数字控制技术取代模拟控制技术已成为发展趋势。
电机交流变频调速技术是当今节电、改善工艺流程以提高产品质量和改善环境、推动技术进步的一种主要手段。
变频调速以其优异的调速和起制动性能,高效率、高功率因数和节电效果,广泛的适用范围及其它许多优点而被国内外公认为最有发展前途的调速方式[3]。
本文对如何利用变频器连接PLC和控制对象,利用软件操作来控制电机的转速,达到远程自动控制进行了讨论[4]。
在工业生产中,电机交流变频调速技术以其优异的调速和起制动性能,高效率、高功率因数和节电效果,被公认为最有发展前途的调速方式。
PLC控制技术在自动控制系统中被普遍采用。
本文构建了一个变频嚣连接PLC和控制对象,利用软件操作来控制电机转速.以达到远程自动控制的系统[8]。
1.2 交流变频调速技术的研究情况及其发展在21世纪电力电子器件的快速发展,使交流变频调速技术优越的性能得到迅速发展,同时控制理论进步,变频调速以其调速精度高、调速控制范围广、回路保护功能完善,响应速度快、节能显著等优点,现在以广泛的用于电力、制造、运输等国民经济领域[6]。
变频调速技术现在被公认为是最理想、最有发展前景的调速方式之一,采用变频器构成变频调速传动系统的主要目的是为了满足提高劳动生产率、改善产品质量、提高设备自动化程度、提高生活质量及改善生活环境等要求以及节约能源、降低生产成本。
基于PLC电机控制系统设计
科技资讯2016 NO.20SCIENCE & TECHNOLOGY INFORMATION动力与电气工程26科技资讯 SCIENCE & TECHNOLOGY INFORMATION1 电动机工作原理三相异步电动机是由固定不动的定子和利用电磁感应转动的转子组成的,他们之前由空隙分开,当电动机接通电源,定子和转子利用电磁感应,进行相对转动,从而实现电动机由电升动的过程。
具体来说,定子的组成有3个部分,有铁心,铁心上面会缠绕着线圈,即绕组,还有支撑整个结构的机座。
三项异步电动机中还有成对的磁极,目的是用来让定子和转子进行转动,在有不同方向的电流通过的时候,定子和转子的转动角度不同,从而控制电动机的正反转。
具体实现电动机的正转反转原理是当定子中有三相交流电流过,就会产生定子和转子的相对转动,具体转动的方向是通过定子和转子切割磁感应方向决定的。
如果产生的三项交流电的方向和产生顺时针转动的方向一致,三相异步电动机的转动方向就为顺时针方向,如果三相交流异步电动机的转动方向和通入电流逆时针的方向相同,那么三项交流异步电动机的转动方向为逆时针方向。
在不通电的时候,定子和转子都是静止的,当通入三相交流电,定子和转子就会按照所通入交流电的方向产生相应的转动,即同向性。
电磁感应的原理是在通电的导体周围会产生磁场,反过来磁场的变化也会使导体运动,这个电磁感应的原理就是电动机的基础。
定子上缠绕的线圈即绕组中通过三相交流电,如果是对称的,就会产生一个顺时针旋转的磁场,转子接通后,由静止变成切割磁感应线运动,如果不是对称的,产生的电流也使转子切割磁感应线运动,但是是以逆时针的方向运动。
这个使转子和定子产生相对运动的力称为电磁力,当力与方向相互结合后,产生了电磁转矩,这个电磁转矩就作为驱动电机旋转的真正动力。
只要控制好电机的真正点动力电磁转矩,就能控制电动机正反转。
电动机的正反转是整个工业控制中最基础最常用的控制,小到一个散热风扇的旋转,如控制正转向室内送风,控制反转向室外排风,大到蒸气机中汽轮机的旋转工作,都是通过电动机的正反转为基础,可见,控制好电动机的正反转就是控制了整个工业的核心。
- 1、下载文档前请自行甄别文档内容的完整性,平台不提供额外的编辑、内容补充、找答案等附加服务。
- 2、"仅部分预览"的文档,不可在线预览部分如存在完整性等问题,可反馈申请退款(可完整预览的文档不适用该条件!)。
- 3、如文档侵犯您的权益,请联系客服反馈,我们会尽快为您处理(人工客服工作时间:9:00-18:30)。
目录课程设计任务书 (1)1 课题介绍 (2)1.1 题目 (2)1.2 背景介绍 (2)2 总体方案设计 (4)2.1 设计目的 (4)2.2 控制要求 (4)2.3 设计要求 (4)3 硬件设计 (4)3.1 硬件方案框图 (4)3.2 硬件选型 (5)3.3 主电路原理图的设计 (6)3.4 控制电路原理图的设计 (6)4 软件设计及调试 (8)4.1 控制系统的I/O点及地址分配 (8)4.2系统工作流程框图 (8)4.3 系统调试 (10)5 总结 (12)参考文献 (14)附录 (16)安徽农业大学经济技术学院《电气控制与可编程控制器》课 程 设 计 任 务 书题目 基于PLC 的电动机制动控制系统设计与调试 专业、班级 电气08-2 班 学号 2008010202 姓名 主要内容、基本要求、主要参考资料等:一、主要内容1.熟悉题目、收集资料,充分了解技术要求,明确设计任务;2.总体设计。
正确选定设计方案,画出系统总体结构框图;3.硬件设计。
选择电器元器件,确定电器元器件明细表。
用CAD 画出电气原理图,并作简要分析;4.软件设计。
根据控制要求确定I/O 分配表,画出系统工作流程图,设计程序及编写程序说明,给出编程原件明细表等;5.系统调试;6.整理编写课程设计说明书。
二、课题要求 1.控制要求三相笼型异步电动机具有反接制动电阻的可逆运行反接制动控制。
2.设计要求1)控制系统采用PLC 来实现;2)提供短路、过载、联锁等保护措施; 3)具有紧急停车功能; 三、基本要求1.根据题意, 用CAD 画出电气原理图和PLC 端子接线图。
设计要合理,画图要规范标准。
2.完成程序的编写工作,并利用模拟器和实验室设备完成调试工作。
3. 完成课程设计说明书一份,阐明设计任务与依据,设计原则、方法、设计方案与成果,并力求论证充分、简明通顺、条理清晰、逻辑性强。
四、主要参考文献王永华.现代电气控制及PLC 应用技术.北京航空航天大学出版社.指导教师签名: 课程负责人签名:2012年 5 月 10日学院: 专业班级: 姓名: 学号:装 订 线1 课题介绍1.1 题目基于PLC的电动机制动控制系统设计与调试1.2 背景介绍可编程序控制器简称PLC,是近年来发展极为迅速、应用面极广的工业控制装置,它已成功地应用于工业中几乎所有领域,能完成从重复开关控制单一机器到复杂的制造加工控制的许多控制任务。
应用领域极为广泛,覆盖所有与自动检测,自动化控制有关的工业及民用领域,包括各种机床、机械、电力设施、民用设施、环境保护设备等等。
如:冲压机床,磨床,印刷机械,橡胶化工机械,中央空调,电梯控制,运动系统。
三相异步电动机从切除电源到完全停止旋转,由于惯性的作用,总要经过一段时间,这往往不能适应某些机械工艺的要求。
如万能铣床、卧床铣床和组合机床等。
无论是从提高生产效率,还是从安全及准确定位等方面考虑,都要求能迅速停车,因此要求对电动机进行制动控制。
制动控制方法一般有两大类:机械制动和电气制动。
机械制动使用机械装置来强迫电动机迅速停车;制动实质上是当电动机停车时,给电动机加上一个与原来旋转方向相反的制动转矩,迫使电动机转速迅速下降。
与传统的控制相比,继电器控制系统虽然有较好的抗干扰能力,但使用了大量的机械触点,是设备连线复杂,且触点在开闭时易受电弧的损害,寿命短、系统可靠性差。
可编程序逻辑控制器(PLC,Programmable Logic Controller),简称PLC,PLC的梯形图与传统的电气原理图非常相似,主要原因是PLC梯形图大致上沿用了继电器控制的电路元件符号和术语,仅有个别之处有些不同。
同时,信号的输入/输出形式及控制功能基本也是相同的;但PLC的控制与继电器的控制又有根本不同之处,主要表现在一下几个方面:1)控制逻辑:继电器控制采用硬接线逻辑,利用继电器机械触点的串联或并联,及时间及电器等组合程控制逻辑,其接线多而复杂、体积大、功耗大、故障率高,一旦系统构成后,想再改变或增加功能都很困难。
另外,继电器触点数目有限,每个只有4~8对触点,因此灵活性和扩展性很差。
而PLC采用存储器逻辑,起控制逻辑以程序方式存储在内存中,要改变控制逻辑,只需改变程序即可,故称做“软接线”,因此灵活性和可扩展性很好。
2)工作方式:电源接通时,继电器控制线路中各继电器同时都处于受控状态,即该吸合的都应吸合,不该吸合的都因受某种条件限制不能吸合它属于并行工作方式。
而PLC的控制逻辑中,各内部器件都处于周期性循环扫描过程中,各种逻辑、数值输出的结果都是按照在程序中的前后顺序计算得出的,所以它属于串行工作方式。
3)可靠性和可维护性:继电器控制逻辑使用了大量的机械触点,连线也多。
触点开闭时会受到电弧的损坏,并有机械磨损,寿命短,因此可靠性和可维护性差。
而PLC采用微电子技术,大量的开关动作有无触点的半导体电路来完成,体积小、寿命长、可靠性高。
PLC还配有自检和监督功能,能检查出自身故障,并随时显示给操作人员;还能动态地监视控制程序的执行情况,为现场调试和维护提供了方便。
4)控制速度:继电气控制逻辑依靠触电的机械动作实现控制工作频率低,触点的开闭动作一般在几十毫秒数量级。
另外,机械触点还会出现抖动问题;而PLC 是由程序指令控制半导体电路来实现控制,属于悟出点控制,速度极快,一般一条用户指令的执行时间在微妙数量级,且不会出现抖动。
5)定时控制:继电器控制逻辑利用时间继电器进行时间控制。
一般来说,时间继电器存在定时精度不高,定时范围窄,且易受环境湿度和温度变化的影响,调整时间困难等问题。
PLC使用半导体集成电路做定时器,时基脉冲由晶体整荡器产生,精度相当高,且定时时间不受环境的影响,定时范围最小可为0.001s,最长几乎没有限制,用户可根据需要在程序中设置定时值,然后由软元件来控制定时时间。
6)设计和施工:使用继电器控制逻辑完成一项控制工程,其设计、施工、调试必须依次进行,周期长,而且修改困难。
工程越大,这一点就越突出。
而用PLC 完成一项控制工程,在系统设计完成以后,现场施工和控制逻辑的设计可以同时进行,周期短,且调试和修改都很方便。
从以上几个方面比较可知,PLC在性能上比继电气控制逻辑优异,特别是可靠性高、通用性强、设计施工周期短、调试修改方便,而且体积小、功耗低、使用维护方便。
但在很小的系统中使用时,价格要高于继电气系统。
2 总体方案设计2.1 设计目的1)学会用PLC控制主电路实现电动机正反转,达到综合应用PLC的目的;2)学会用CAD制图;3)学会用PLC S7-200编程软件,通过编写的程序,完成对主电路的控制;4)学会整理并制作课程设计报告,为毕业设计报告做准备。
2.2 控制要求三相笼型异步电动机具有反接制动电阻的可逆运行反接制动控制。
2.3 设计要求1)控制系统采用PLC来实现;2)提供短路、过载、联锁等保护措施;3)具有紧急停车功能。
3 硬件设计3.1 硬件方案框图如图3-1所示,系统通过S7-200可控制器及按钮来实现对电动机的控制,同时通过人机界面来进行监视与调节,从而达到电动机可靠、安全、稳定的运行。
图3-1 系统硬件方框图3.2 硬件选型表3-1 系统元器件表3.3 主电路原理图的设计图3-2 系统主电路原理图主电路原理如图3-2所示,具有反接制动电阻的可逆运行反接制动控制线路。
图中RA 是反接制动电阻,在电动机启动时其降压启动的功能,在电动机制动是起着降低反接制动电流的作用;QA1、QA2、QA3三个接触器用于控制电动机的启动、正反转和制动,具有低电压释放保护功能,具有比工作电流大数倍乃至十几倍的接通分断能力,但是不能分断短路电流;BB 利用电流的热效应原理以及发热元件热膨胀原理设计,实现三相交流电动机的过载保护。
3.4 控制电路原理图的设计系统控制原理如图3-3所示,正转启动按钮SF2、反转启动按钮SF3、停止按钮SF1、速度继电器正转常开触点BS1、速度继电器反转常开触点BS2、热继电器BB 常闭触点分别接PLC 的输入端,接触器QA1、QA2、QA3、正常指示灯L1、故障指示灯L2分别接PLC 的输出端。
通过所编程序实现对电动机的控制。
3~M BSMAR A ×3BBQA3QA2QA0QA1L3L2L1图3-3 系统PLC 接线端子图软元件是PLC 内部的具有一定功能的期间,这些器件实际上是由电子电路和寄存器及存储器单元等组成。
例如,输入继电器是由输入电路和输入映像寄。
存器构成;定时器和计数器也都是有特定功能的寄存器构成。
它们都具有继电气特性,但没有机械性的触点。
为了把这种元器件传与统电气控制电路中的继电器区别开来,我们把它们称作软元件或软继电器。
这些软继电器最大的特点是:看不见、摸不着的,也不存在物理性的触点;每个软元件课提供无限多个常开触点和常闭触点;体积小、功耗低、寿命长。
24VDC 传感器电源输出1M 0.00.10.20.32M 0.40.5ML+1L 0.00.10.20.32L 0.40.5N L1L(+)N(-)120/240VAC 电源N(-)L(+)正常指示灯L1故障指示灯L20.60.7.AC SF1SF2SF3BBBS1BS2QA1QA2QA3CPU222AC/DC/继电器nn4 软件设计及调试4.1 控制系统的I/O点及地址分配4.2系统工作流程框图系统的工作流程如图4-1所示,按下正转启动按钮SF2,使中间继电器线圈带电,通过中间继电器使接触器QA1线圈带电常开触点闭合,使定子绕组经3个电阻接通正序三相电源,电动机MA开始降压启动。
当电动机转速上升到一定值时,速度继电器的正转常开触点闭合,通过中间继电器控制接触器QA3线圈带电,使其常开触点闭合,于是三个电阻被短接,定子绕组直接加以额定电压,电动机转速上升到稳定工作转速。
在电动机正常运转的过程中,若按下停止按钮SF1,则QA1、QA3线圈相继断电,由于此时电动机转子的惯性转速仍然很高,使速度继电器的正转常开触点尚未复原,中间继电器仍处于工作状态,所以在接触器QA1常闭触点复位后,接触器QA2线圈便通电,其常开触点闭合,使定子绕组经3个电阻获得反相序三相交流电源,对电动机进行反接制动,电动机转速迅速下降。
当电动机转速低于速度继电器动作值时,速度继电器常开触点复位,中间继电器线圈掉电,接触器QA2释放,反接制动过程结束。
电动机反向启动及制动与正向相同。
图4-1 系统工作流程框图4.3 系统调试系统程序见附录系统调试结果如下图所示:图4-2 电动机的正向降压启动图4-3 电动机正转全压运行图4-4 按下停止按钮图4-5 电动机正转停止时反接制动图4-6 电动机反向启动图4-7 电动机反向全压运行图4-8 电动机反向停止时反接制动图4-9 电动机停止运行图4-10 系统出现故障时5 总结本次课程设计是大学阶段在毕业设计之前的最后一次较为难得的理论,为之后的毕业设计奠下基础的一次机会。