瓦楞纸板生产过程中出现的问题
瓦楞纸板常见纸病的解决方案

瓦楞纸板常见纸病的解决方案一、开胶、假粘1、里纸开胶原因分析:1.1胶质量不符生产要求或腐败变质;1.2上胶量太小;1.3车速过快,瓦楞辊、压力辊热量不足;1.4压力辊压力不足;1.5瓦楞辊、压力辊的中高严重磨损。
解决方法:1.1更换合格胶液;1.2适量调大涂胶量;1.3提高瓦楞辊、压力辊温度,保证180℃以上开机,同时根据温度情况调整车速;1.4适当调整压力辊压力,以里、瓦纸粘合良好,里纸不露楞、瓦纸不碎为宜;1.5打磨或更换新压力辊、瓦楞辊。
1、面纸开胶、夹芯开胶原因分析:2.1胶量过小、烘干机速度过慢;2.2胶液稀薄,涂胶辊挂胶不足;2.3烘干机热板温度不足,胶液未充分糊化;2.4烘干机车速过快,纸板烘干不足;2.5烘干机传输带上面的压载辊没完全落下。
解决方法:2.1适当加大涂胶量,并酌情提高车速;2.2更换胶液或在原胶液中加入适量乳化剂;2.3升高烘干机热板温度至180℃以上开机;2.4减慢车速;2. 5落下压载浮辊。
原因分析:3.1瓦楞辊温度不足;3.2胶量过小,温度过高;3.3车速缓慢造成萃胶;3.4胶液黏度不够。
解决方法:3.1提高单面机工作温度;3.2调整涂胶量,关闭热源,待温度下降至180℃以下,160℃以上开机;3.3提高单面机速度;3.4适当增加胶液黏度。
2、面纸假粘原因分析:4.1烘干机热板温度不足;4.2胶液沉淀变质;4.3纸板在烘干机内停留时间过长。
解决方法:4.1待温度达到胶液能糊化时开机;4.2更换新胶;4.3尽量减少停机时间,换单换纸和断纸再续时动作要果断迅速。
二、倒楞1、单面纸板倒楞原因分析:1.1瓦楞辊磨损;1.2上下瓦楞辊间隙过大;1.3瓦楞纸定量太高且厚度太厚;1.4瓦楞纸水分过大;1.5瓦楞纸未经预热器,可塑性差。
解决方法:1.1磨削或更换瓦楞辊;1.2调整瓦楞辊间隙至0.5mm;1.3更换瓦楞纸;1.4调大预热包角,增大预热面积;1.5将瓦楞纸穿过预热器。
瓦楞纸板生产线故障与对策

在制造瓦楞纸板时会产生很多故障,其中有原材料问题,粘合剂问题,机械本身问题,操作技术问题及熟练程度的问题,在当今市场需求尤其在生产过程控制特别要求尽量尽快减少。
由上述故障引出的质量问题造成的报废数量和频率是重中之重。
经公司研究决定,由品质部编写本对策以解决生产急需达到降低控制成本之目的。
一、瓦楞纸断裂这是鉴别瓦楞纸适应性的重要指标。
其形原因:1、单面机预热张力。
2、瓦楞纸刹车器。
3、在进入上下瓦楞辊时受到的弯曲与剪切力。
产生原因解决办法:①瓦楞原纸质量不好①更换瓦楞原纸②瓦楞辊磨损②进行简易修复或更换瓦楞辊③瓦楞辊间隙太小③修正和调整瓦楞辊的贴合间隙④运行中机械性损坏④检查并修复机械性不当造成的损伤⑤刹车过紧⑤降低气刹压力减少刹车紧力⑥预热包角过大⑥减少预热包角二、瓦楞折皱产生原因解决办法①瓦楞原纸在抄造或抄宽方向上有湿斑或料斑①增大预热器包角②瓦楞原纸的制动力不强②加大制动力平衡张力③瓦楞辊的平行度不好③修正或调整瓦楞辊的平行度④瓦楞原纸含水平不均衡④适当预热或喷蒸气使其保持平衡的含水三、瓦楞的变形表现为:没有达到规定的瓦楞高度,瓦楞变形,瓦楞形不整齐的现象。
这样的瓦楞成形的纸板本身比较软,平面强度低,刚性也低,做成的纸箱抗压强度也低,戳穿强度也小。
此种原因在流水线上有发生,在制箱过程中也有发生。
产生原因解决办法①使用了低强度的瓦楞原纸本身抗压强度不够①更换高强度瓦楞纸②瓦楞原纸水分过低或过高易变形②加大预热包角或喷雾均衡水分③上、下瓦辊间压力不足时瓦楞成型不好③调整合适压力④瓦楞辊磨损,降低了瓦楞高度④更换瓦辊和压力辊可解决⑤双面机上涂胶辊和压载辊的间隙调节不当⑤调节合适间隙达到正常合适⑥加热部和冷却部的加重辊压力不适当导致压溃⑥调整加大压辊间隙高度⑦瓦楞纸板水分高或热板温度不够不能使其定型⑦加大蒸气压力使温度升高到合适温度,或检查导致温度不好的原因以解决⑧横切机压辊调节太重,导致压溃瓦楞⑧调节重辊铊的间隙距离可解决四、瓦楞的倾斜表现为:瓦楞向纸板运动方向倾斜,但还没倒塌。
关于瓦楞纸板生产技术问答

关于⽡楞纸板⽣产技术问答关于⽡楞纸板⽣产技术问答2009/11/11/10:04 来源:印刷⼯艺⽹【慧聪印刷⽹】在起楞过程中,经常出现的故障以及如何排除?1、⽡楞的⾼度不够,原因可能是压⼒或温度过低,或者纸张含⽔分过⾼。
解决办法是调整压⼒或辊温,或降低车速,使纸张得以⼲燥。
2、⽡楞⾼度不均⼀,压出的⽡楞纸两边长短不同呈扇形。
这是由于⽡楞辊平⾏度不好或两端压⼒不均匀所致。
如左边⽡楞纸⽐右边短,则应适当地将上⽡楞辊左边升⾼,否则逆向调整。
3、⽡楞纸卷曲成筒状,主要原因是上下辊筒温度差过⼤。
应检查上、下辊筒内加热源⼯作情况,或许其中之⼀出现故障,可予以修理或更换。
4、⽡楞纸粘在⽡楞辊⾯上。
辊⾯温度过⾼或原纸⽔分含量过⼤都会出现这种现象。
此时应调整辊⾯温度,使纸张⼲燥后再压楞,若刮⼑与辊槽不贴合,应调整或更换。
国际⽡楞纸加⼯⾏业发展浅析2009/11/11/09:14 来源:商务部【慧聪印刷⽹】长期以来,以美国为⾸的北美洲⼀直位居⽡楞纸产量的世界第⼀印刷⼯具。
但在2003年,亚洲⼀跃超过了北美洲、欧洲,成为⽡楞纸产量世界第⼀⼤洲物资⾏情。
如果以单个国家产量来衡量,美国的⽡楞纸产量仍然处于世界领先地位,中国次之,然后是⽇本印刷技术。
亚洲地区有着强⼤的购买⼒、完整的产业基础、优良的劳动⼒和丰富的⾃然资源,在国际⽡楞纸领域存在着强⼤优势和市场潜⼒印刷⼯具。
⽬前,从技术⽅⾯看,国际⽡楞纸加⼯⾏业主要在以下⼏个⽅⾯发展势头最猛物资⾏情。
1.微细⽡楞纸板国内的微细⽡楞包装还在技术、⽣产上探索时,微细⽡楞包装在国外却已经应⽤到各个领域中国中部。
微细⽡楞纸板除可制作彩印包装盒外,还可以作为内衬替代传统的缓冲材料,也可以⽤于制作海报式⽡楞纸板展⽰架等印刷技术。
近⼏年,美国、瑞典、德国、西班⽛等国的企业开始扩⼤F楞、G楞的⽣产规模,并开始向微型⽡楞纸板的更深⽅向探索,N楞、O楞等更⼩的楞型已经开始应⽤印刷市场。
欧洲所⽤的⽡楞纸板的定量已从550~570gm2降⾄510~520gm2.可以说,在传统由纤维纸板盒占据的领域,如酒类、⼩型器具类、鞋类、五⾦⼯具、微电⼦产品、电脑软件、柜台销售陈列品、快餐等,微型⽡楞纸盒已经发起了与其争夺市场的“⽃争”印刷⼯具。
瓦楞纸板常见质量问题和产生原因及解决办法

修正瓦楞辊的贴合间隙 清理瓦楞表面异物
瓦楞辊贴合间隙大
• 修正瓦楞辊的贴合间隙
瓦画辊贴合间隙不平衡 •
导纸板位置不正、磨损或带
脏
瓦楞原纸含水水均衡
•
瓦楞原纸的张力太小
•
检查并修正或更换导纸 板
加大予热包角 适当调整张力控制
瓦楞纸板常见质量问题和产生原因及 解决办法
质量问题
平行度
• 瓦楞辊表面带脏
• 清理瓦楞辊,保持干净
• 导纸板位置不正,、带脏或磨损 • 检查、修正、清理或更换导
纸板
• 涂胶辊、浮动辊间隙不当
• 调整二者的贴合间隙
• 粘合剂质量不好
• 检查并重新制作粘合剂
• 瓦楞原纸含水不均衡张力小 • 适当予热并加大张力控制
• 过纸天桥张力不均衡
瓦楞纸板常见质量问题和产生原因及 解决办法
1. 面纸予热包角太大 2. 里纸予热包角太小 3. 过纸天桥堆积过多 4. 单面机涂胶量过大
5.涂胶仙涂胶量偏少
6.车速太低
7.双面机热板温度高
8.重量辊施加压力过大
解决办法
• 减少包角、降低予热 • 增大包角、加强予热 • 减少过纸天桥的堆积 • 适当控制单面机的着胶
量 • 适当增大涂胶机的着胶
7.双面机热板温度高 8.重量辊施加压力过大
解决办法
• 减少包角、降低予热
• 增大包角、加强予热 • 减少过纸天桥的堆积 • 适当控制单面机的着胶
量 • 适当增大涂胶机的着胶
量 • 根据实际运行质量,适
当提高车速
• 提高车速或人为降低热 板
• 适当投放重量辊
PPT文档演模板
瓦楞纸板常见质量问题和产生原因及 解决办法
瓦楞纸板粘合问题及粘合不良的解决
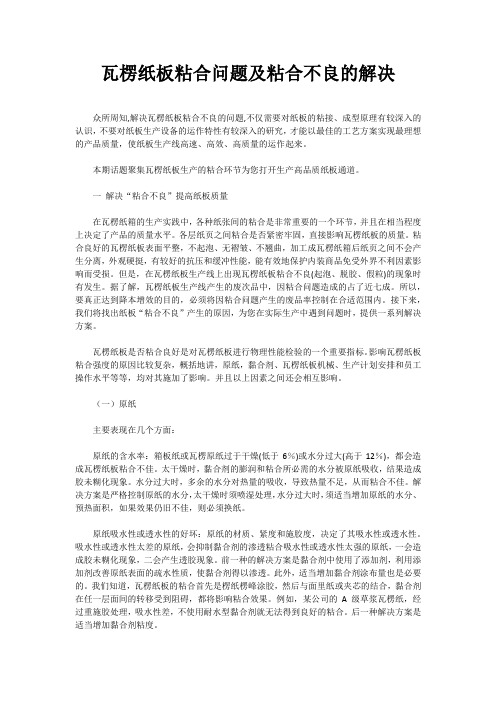
瓦楞纸板粘合问题及粘合不良的解决众所周知,解决瓦楞纸板粘合不良的问题,不仅需要对纸板的粘接、成型原理有较深入的认识,不要对纸板生产设备的运作特性有较深入的研究,才能以最佳的工艺方案实现最理想的产品质量,使纸板生产线高速、高效、高质量的运作起来。
本期话题聚集瓦楞纸板生产的粘合环节为您打开生产高品质纸板通道。
一解决“粘合不良”提高纸板质量在瓦楞纸箱的生产实践中,各种纸张间的粘合是非常重要的一个环节,并且在相当程度上决定了产品的质量水平。
各层纸页之间粘合是否紧密牢固,直接影响瓦楞纸板的质量。
粘合良好的瓦楞纸板表面平整,不起泡、无褶皱、不翘曲,加工成瓦楞纸箱后纸页之间不会产生分离,外观硬挺,有较好的抗压和缓冲性能,能有效地保护内装商品免受外界不利因素影响而受损。
但是,在瓦楞纸板生产线上出现瓦楞纸板粘合不良(起泡、脱胶、假粒)的现象时有发生。
据了解,瓦楞纸板生产线产生的废次品中,因粘合问题造成的占了近七成。
所以,要真正达到降本增效的目的,必须将因粘合问题产生的废品率控制在合适范围内。
接下来,我们将找出纸板“粘合不良”产生的原因,为您在实际生产中遇到问题时,提供一系列解决方案。
瓦楞纸板是否粘合良好是对瓦楞纸板进行物理性能检验的一个重要指标。
影响瓦楞纸板粘合强度的原因比较复杂,概括地讲,原纸,黏合剂、瓦楞纸板机械、生产计划安排和员工操作水平等等,均对其施加了影响。
并且以上因素之间还会相互影响。
(一)原纸主要表现在几个方面:原纸的含水率:箱板纸或瓦楞原纸过于干燥(低于6%)或水分过大(高于12%),都会造成瓦楞纸板粘合不佳。
太干燥时,黏合剂的膨润和粘合所必需的水分被原纸吸收,结果造成胶未糊化现象。
水分过大时,多余的水分对热量的吸收,导致热量不足,从而粘合不佳。
解决方案是严格控制原纸的水分,太干燥时须喷湿处理,水分过大时,须适当增加原纸的水分、预热面积,如果效果仍旧不佳,则必须换纸。
原纸吸水性或透水性的好坏:原纸的材质、紧度和施胶度,决定了其吸水性或透水性。
瓦楞纸板生产中的不良种类及判断调整
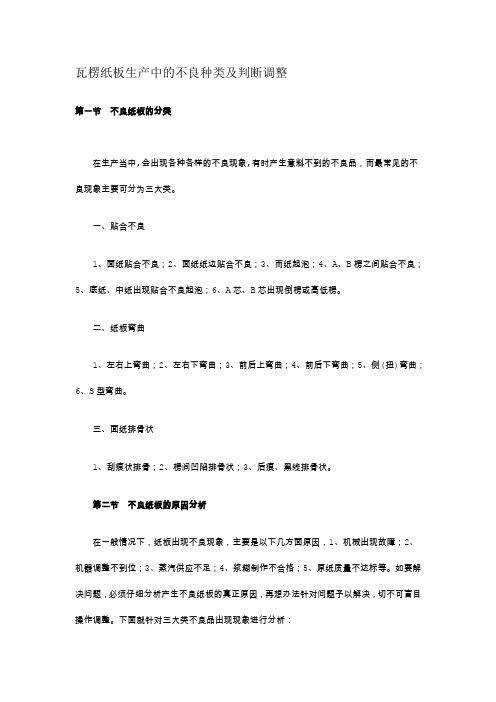
瓦楞纸板生产中的不良种类及判断调整第一节不良纸板的分类在生产当中,会出现各种各样的不良现象,有时产生意料不到的不良品,而最常见的不良现象主要可分为三大类。
一、贴合不良1、面纸贴合不良;2、面纸纸边贴合不良;3、而纸起泡;4、A、B楞之间贴合不良;5、底纸、中纸出现贴合不良起泡;6、A芯、B芯出现倒楞或高低楞。
二、纸板弯曲1、左右上弯曲;2、左右下弯曲;3、前后上弯曲;4、前后下弯曲;5、侧(扭)弯曲;6、S型弯曲。
三、面纸排骨状1、刮痕状排骨;2、楞间凹陷排骨状;3、后痕、黑线排骨状。
第二节不良纸板的原因分析在一般情况下,纸板出现不良现象,主要是以下几方面原因,1、机械出现故障;2、机器调整不到位;3、蒸汽供应不足;4、浆糊制作不合格;5、原纸质量不达标等。
如要解决问题,必须仔细分析产生不良纸板的真正原因,再想办法针对问题予以解决,切不可盲目操作调整。
下面就针对三大类不良品出现现象进行分析:一、贴合不良1、面纸贴合不良原因:(1)浆糊供应不足(失糊);(2)热板与帆布间隙提的太高;(3)车速太快,造成浆糊糊化时间不足;(4)刮糊辘间隙太小,上糊量不足;(5)浆糊粘度不达标(太高或太低);(6)楞尖浆糊成白色粉状,这是糊化温度太高,浆糊没有熟化;(7)楞尖浆糊成黑线且是亮晶晶的,这是糊化温度太低,在纸板未进入热板以前就已糊化;(8)A、B楞刹车辘刹车压力太低或面纸太松;(9)三重预热缸温度不足或积水;(10)热板温度不足或积水。
2、面纸纸边帖合不良原因:(1)浆糊糊化温度太高;(2)浆糊糊化温度太低;(3)原纸施胶不够或施胶太大;(4)帆布边上磨损太多;(5)面纸纸边水份太高;(6)底纸压力太重;(7)天桥积纸太多或A、B 楞吸风力不够。
3、面纸起泡原因:(1)原纸张力太小;(2)热板与帆布间隙太高;(3)原纸挂浆不匀或太过干燥;(4)A、B楞出现高低楞或倒楞。
4、A楞与B楞贴不良原因:(1)车速太快,浆糊来不及熟化;(2)糊化温度太高或太低;(3)浆糊粘度不达标;(4)上糊量太小(刮糊辘间隙太小;(5)三重预热缸温度不足或积水;(6)热板温度不足或积水;(7)A、B楞吸风力太低;(8)A、B楞在三重工业预热缸上的预热面积太小,导致预热不足;(9)帆布与热板间隙提的太高;(10)A楞、B楞生于潮湿,水份太高。
解决瓦楞纸板粘合不良问题

解决瓦楞纸板粘合不良问题在瓦楞纸板生产线上出现瓦楞纸板粘合不良(起泡、脱胶、假粒)的现象时有发生。
原因是多方面的,有原纸含水率高低问题、有生产中施胶量控制不当问题、也有黏合剂的质量问题等。
而其中黏合剂的粘合机理则是首先应解决的问题。
如若对黏合剂的粘合机理一知半解或知之甚少,那么当生产中出现粘合不良时,必将难于从容应对或是束手无策,或是就表面现象解决表面问题,没有抓住问题的本质,难以彻底根治。
因此,笔者以黏合剂的粘合机理为重点加以阐述。
虽然黏合剂在瓦楞纸板的制造成本中所占的比例微乎其微,但它却对瓦楞纸板的质量起着举足轻重的作用。
所以,关于黏合剂的制作配方与质量控制,成为国内外专家长期研究的课题。
黏合剂种类很多。
如淀粉系列黏合剂、聚乙烯醇等。
目前,大多数厂家都使用淀粉系列黏合剂。
淀粉黏合剂比较其它黏合剂,有下列优点:1、粘着力强,容易渗透到纸质中产生粘着力;2、初粘度好;3、易贮存;4、粘好的纸板纸箱外观坚挺平整,不易跑楞,不易吸潮。
然而在生产中,淀粉黏合剂也存在着反应时间长,氧化深度不易控制,质量不够稳定,反应过程比较复杂等不容忽视的缺点,此外,大部分厂家在生产淀粉黏合剂时机械套用工业氧化淀粉的反应条件,不能有效地控制和调整黏合剂的配方、工艺与氧化深度,不仅浪费了原材料,延长了反应时间,而且黏合剂的质量得不到控制,影响了瓦楞纸板的各种性能。
因此在使用时,只须加入水和黏合剂,就可得预氧化淀粉黏合剂,用于瓦楞纸板的粘合。
实际上,即使在同一条生产线上,单面机和双面机所使用的淀粉胶也有所不同。
就瓦楞纸板的粘合而言,粘结机理是决定黏合剂配方的前提;而就黏合剂的质量而言,黏度和凝胶点则是衡量质量的两项重要指标。
瓦楞芯纸与面纸的粘合主要是淀粉黏合剂的凝聚粘合,同时辅以渗透粘合和表面粘合。
胶料渗透纸内表面及瓦楞芯纸表面,进入纸板的纤维间隙里引起渗透粘合。
同时,面纸和瓦楞芯纸与黏合剂表面形成有黏合剂间的粘合,即形成表面粘合。
常见的瓦楞纸板缺陷及其解决方法
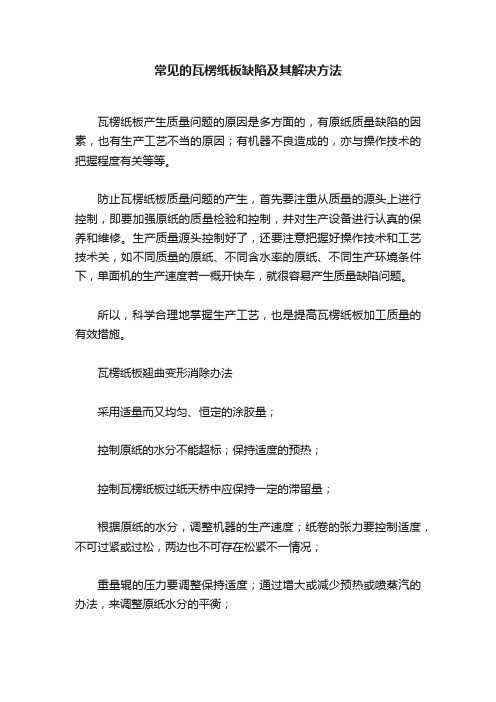
常见的瓦楞纸板缺陷及其解决方法瓦楞纸板产生质量问题的原因是多方面的,有原纸质量缺陷的因素,也有生产工艺不当的原因;有机器不良造成的,亦与操作技术的把握程度有关等等。
防止瓦楞纸板质量问题的产生,首先要注重从质量的源头上进行控制,即要加强原纸的质量检验和控制,并对生产设备进行认真的保养和维修。
生产质量源头控制好了,还要注意把握好操作技术和工艺技术关,如不同质量的原纸、不同含水率的原纸、不同生产环境条件下,单面机的生产速度若一概开快车,就很容易产生质量缺陷问题。
所以,科学合理地掌握生产工艺,也是提高瓦楞纸板加工质量的有效措施。
瓦楞纸板翘曲变形消除办法采用适量而又均匀、恒定的涂胶量;控制原纸的水分不能超标;保持适度的预热;控制瓦楞纸板过纸天桥中应保持一定的滞留量;根据原纸的水分,调整机器的生产速度;纸卷的张力要控制适度,不可过紧或过松,两边也不可存在松紧不一情况;重量辊的压力要调整保持适度;通过增大或减少预热或喷蒸汽的办法,来调整原纸水分的平衡;控制单面机或双面机生产环境保持稳定的温湿度;瓦楞辊、压力辊、活动辊和预热辊要调整保持平衡状态;对使用磨损厉害的瓦楞辊应更换新辊;切忌将含水率高低悬殊过大的瓦楞纸、面纸或里纸(箱板纸)进行配套成型加工。
瓦楞纸板出现搓衣板状变形的原因瓦楞纸板由于受到温度、黏合剂和机器张力和原纸质量等方面的作用,就容易出现搓衣板状变形。
产生原因:1、原纸的纤维组织的伸缩率差异较大;2、面纸或里纸的定量偏低和原纸的纤维组织过于柔软的话,成型后其挺度相应也就差;3、黏合剂涂布量过多或不均匀时,使瓦楞楞顶两侧边缘也有胶液,当其与面纸或里纸黏结干燥后,由于收缩作用导致对面纸或里纸构成一定扭力;4、黏合剂的黏度偏低,与里纸或面纸的纤维组织没有很好地黏结成坚固的整体;5、单面机或双面机的瓦楞辊、压力辊间隙不适、不平衡;6、瓦楞辊楞齿顶磨损严重时,由于楞齿顶面积增大而加大胶的涂布量,使面纸或里纸黏结后容易变形;7、瓦楞辊、压力辊或预热辊的温度过高或过低等情况存在时,都容易使瓦楞纸板成型后出现搓衣板状变形现象。
- 1、下载文档前请自行甄别文档内容的完整性,平台不提供额外的编辑、内容补充、找答案等附加服务。
- 2、"仅部分预览"的文档,不可在线预览部分如存在完整性等问题,可反馈申请退款(可完整预览的文档不适用该条件!)。
- 3、如文档侵犯您的权益,请联系客服反馈,我们会尽快为您处理(人工客服工作时间:9:00-18:30)。
一、概述辩证唯物主义认为,劳动创造了人类。
当今社会人类的生存离不开生产活动,而一切生产活动都离不开产品包装,古今中外无不如此。
所谓包装的定义是:“为在流通过程中保护产品、方便存储、促进销售,按一定技术方法而采用的容器、材料及辅助物的总称。
”在整个包装所用材料中,纸制品包装所占比例最大为45.25%,其它依次为玻璃、塑料、木制品和金属材料包装。
而在纸制品包装中,瓦楞纸板(箱)包装又占绝大多数。
瓦楞纸板包装容器在功能上具有优越于其它种类包装的10 种特性:造型结构的可塑性──可以任意裁切、冲孔、折叠等;包装使用的方便性──使用起来材质轻、结构巧、质地柔韧;刚柔兼备的保护性──能成为包装物与外力作用之间理想的保护介体;美化商品的促销性──能制出各种变异结构及美观的装潢印刷;流动作用的适宜性──能采用不同定量、不同等级原纸,生产出不同大小的容器;包装成本低廉性──主要材料为原纸;利用资源有效性──与传统木制品相比,瓦楞纸箱原纸耗用的木材只占木制品包装的30%;易于回收利用性──基本原材料为原纸,使用后可以方便地回收,回收再生利用率可达75%;优越的绿色环保性──使用后瓦楞纸板可燃烧、无毒害、降解快、不会对环境造成污染;仓储运输经济性──由于是可折叠的轻质硬体包装,可以有效利用仓位和运输装载空间。
综观我国纸箱行业的现状,可以用12 个字来概括,即:快速发展,产能过剩,前途光明。
纸箱行业在过去25 年中经历了第一次大变革,从今年起,将进入第二次大变革,这场变革的特征就是调整。
我国纸箱行业进入初级工业化阶段是从1995 年开始的,当时生产线600 条;2000 年为1600条;至2005 年达4000 条。
1995 年世界瓦楞纸板产量是1104 亿m2,2000 年为1253 亿m2,2003 年是1395 亿m2,年增长率3.3%。
2000 年世界产量排前三位依次是:北美洲(占34%)、亚洲(占31%)、欧洲(占27%)。
我国瓦楞纸板的产量1995 年是74 亿m2,2000 年上升到123 亿m2,2003 年则达到158 亿m2,是亚洲总产量的34%,占世界11.3%。
1995 年至2000 年,我国纸板产量平均增长率为12%,世界平均增长率是2%;2000 年至2003 年我国的纸板产量年增长率是9%,世界年增长率是3%。
我国1996 年产量是80 亿m2,只及日本一半,2003 年是158 亿m2,已超过日本。
我国五层以上纸箱占总量80%以上,美国三层箱占89.4%,日本三层为84.6%,多用两层纸等于浪费2/5 的纸。
这是因为西方国家已认识到,必须节约有限的木材资源。
采用高强度、低克重的原纸已成为必然趋势。
上海烟草集团已完成了跨地域的联合重组,将成为中国烟草总公司下属几个龙头企业的排头兵。
作为其主要专业配套工厂,上海白玉兰烟草材料有限公司承担了集团85%以上纸箱包装生产任务。
二、原始楞型的确定、生产线原纸的选配和粘合剂的调配瓦楞形状是指瓦楞齿形轮廓的波纹形状,它的区别在于波峰与波谷圆弧半径大小。
形状有三种:U 形、V 形和UV 形。
U 形的峰、谷半径较大;V 形较小;UV 形处于中间状态。
不同楞形具有不同性能特点。
综观以上三种瓦楞形状的优缺点,U 形和V 形的利弊是显而易见的,而UV 形状的综合性能是适应大多数瓦楞包装的普遍要求,其优越性彰显无疑。
因此,我国及世界各国大多使用UV 形瓦楞。
了解了瓦楞形状概况后,再从以下两方面简介纸板生产线原纸选配原则:1.等级选配──应选用质量等级近似的瓦楞纸和箱板纸生产纸板。
选用高等级箱板纸和低等级瓦楞纸制成的瓦楞纸板,容易造成塌楞。
2.定量选配──实验表明,提高瓦楞纸的定量有利于降低成本。
在保持强度不变情况下,瓦楞纸定量每增加1g/m2,则两面箱板纸也可降低1g/m2,因此许多厂家都采用高定量瓦楞纸生产纸箱。
但定量过高的瓦楞纸与低定量箱板纸生产出的瓦楞纸板会出现表面不平整,产生明显瓦楞条纹的现象,影响外观质量和印刷效果。
因此,一般箱板纸与瓦楞纸的定量比控制在2:1 比较好。
如果选配瓦楞纸定量过低,粘合后瓦楞齿形会改变,由圆弧形变成矩形结构,影响纸板厚度、边压强度和缓冲性能。
有关瓦楞纸板生产线粘合剂的调配:纸板生产线粘合剂主要有淀粉(或木薯粉)、糊化剂(NaOH)、交联剂(硼砂)和其它增强剂组成。
其实淀粉本身不具有粘结功能,只有淀粉分子中较活泼的羟基被有限地氧化为醛基、酮基、羧基,分子中的官键部分发生断裂,聚合化降低才具有良好的溶水性、亲和力和粘接性,经碱化后成为性能良好的淀粉粘合剂。
一般情况下,单面瓦楞纸板生产淀粉用量为:150kg/t一170kg/t;三层用量为:170kg/t一200kg/t;五层、七层对粘合剂要求比较高,淀粉用量200kg/t一300kg/t。
工业烧碱(NaOH)用量根据加入淀粉液中主体载体搅拌后,粘合剂的粘度而定。
同等条件下,烧碱用量大,粘度高;烧碱用量小,粘度则降低。
硼砂能使各种配料产生分子结构变化形成络合物,具有交联增粘作用。
而增强剂(又称干燥剂)用量在粘合剂中,每吨用量低于2kg,起不到应有的作用;每吨胶用量高于8kg,又容易产生纸板发脆现象。
正常用量为3kg/t一6kg/t。
三、瓦楞纸板生产过程中产品易出现的问题及解决方法纸板翘曲一般情况下,瓦楞纸板翘曲变形有6 种现象,最为常见的有:1.横向上翘曲产生原因为:里原纸含水率太高(或面纸含水率低);单面瓦楞粘合水分过多;里、面纸的定量等级过于悬殊。
解决方法:(1)增加里纸在单面机滚筒烘缸上的缠绕面;(2)减少里纸在双层预热器上的缠绕面;(3)关闭部分平板烘缸蒸汽阀门;(4)提高复合机运行速度;(5)缩小刮胶辊、施胶辊与下瓦楞辊之间的间隙,减小单面瓦楞的施胶量;(6)更换严重超出水分要求的里纸。
2.横向下翘曲产生原因为:面纸原纸含水率太高;加热部位的温度和速度失常。
解决方法:(1)增加面纸在双层预热器上的加热缠绕面;(2)使用粘度较好的粘合剂,减少复合机的上胶量;(3)减少单面机里纸在滚筒烘缸上的缠绕面;(4)减低复合机处的生产车速;(5)正确调节生产线车速和平板烘缸蒸汽阀门使之匹配;(6)更换严重超出水分要求的面纸。
纸板假性粘合所谓纸板假性粘合是指纸板离机后面纸、里纸与瓦楞纸能随意剥离的一种现象。
产生的主要原因有:(1)粘合剂粘度不够或已变质;(2)瓦楞机或复合机车速过快;(3)瓦楞机压力辊压力不匀或瓦楞辊已磨损;(4)复合涂胶机胶辊间隙过大;(5)纸张含水率太高。
解决方法:(1)提高、稳定粘合剂质量,有关资料提示粘合剂粘度冬季一般为60S一90S;夏季一般为90S一120S。
七层箱一般要比三层箱粘度慢305 左右;(2)确保蒸汽压力1.0MPa一1.2MPa,各辊体及平板烘缸温度为160℃左右;(3)国产瓦楞辊在产量达300 万长米一350万长米时,须及时更换。
搓板现象所谓搓板现象是指制成后的瓦楞纸板,在其表面面纸上沿楞峰与楞峰的脊背之间产生内凹现象,形状如同家用搓衣板一般,故称之为搓板现象。
瓦楞纸板产生搓板现象的根本原因,主要应归咎于粘合剂上胶不当,由聚集到楞峰两侧的过量胶水影响所致。
这种情况对于定量低的箱板纸危害尤其突出。
控制纸板搓板现象的具体方法有:调整面纸的定量,改用定量较高的箱板纸是消除、减轻搓板状最直接有效的办法(但会增加成本);采用高品质粘合剂可以减少楞峰的施胶量;控制好面纸在预加热器上的加热缠绕面,因为箱板纸过于干燥对胶水的摄取量较多,易产生搓板现象;调节好复合胶水机施胶辊和纸导辊的平行度和它们之间的间隙,严格导辊(压辊)的压力程度,防止塌楞后上胶量增大。
纸板含水量的控制在生产瓦楞纸板过程中,纸板含水量控制十分重要,当水分过高时,加工出的纸板会出现偏软、不挺、成箱后易塌箱等。
当水分偏低时,加工出的纸板发硬、发脆、成箱后易爆裂。
纸板水分的控制是一件比较复杂的事情,它主要由以下两方面因素决定:对进厂原纸的水分要严格控制,按现行标准:原纸交货状态的水分应为(8±2)%。
而存放原纸最好设立单独库房,温度一般在(18±3)℃,湿度一般在(35±5)%。
千万不能放在露天,否则易引起水分变化且两端与中间不一样。
温度是影响瓦楞纸板质量的决定因素之一。
它既能调整原纸的水分,又能使原纸升温,是糊液固化的重要条件。
因此纸板生产线设置许多预热器和平板烘缸,用来调节原纸和单面纸含水率,并使糊液固化最终达到粘合的目的。
为有效控制成品瓦楞纸板水分,必须关注以下事项:如果纸板水分过高,预热辊温度达不到要求,须增加锅炉蒸汽压力,使之供出的蒸汽达到饱和蒸汽,一般情况下蒸汽压力应该保持在1.1Mpa±0.2Mpa。
如果水分偏低,就要调节导纸辊,减少预热面积,同时要充分利用单面机上喷雾装置(湿润辊),对原纸进行喷雾,增加原纸水分,使之达到标准要求。
平板烘缸在工作时,不到万不得已时,不能停车。
单面机要更换原纸前应提速,在桥架上多积累些纸;复合机在接到信号后应降速,待单面机完成接纸后,再行提速。
若设备发生故障等必须停车时,应将输送毛毯提升,以防停留在平板烘缸上纸板水分过度流失。
对于单面机而言,要调节好上胶辊与刮胶辊的间隙。
一般情况下,上胶辊与刮胶辊的间隙为0.2mm一0.25mm,涂胶辊与主瓦楞辊在热机状态下的间隙应比所用瓦楞纸的厚度大0.02mm。
对于双面机而言,刮胶辊和上胶辊的间隙也为0.2mm一0.25mm,压辊与上胶辊之间间隙应比所通过的单面瓦楞纸板高度小0.05mm一0.1mm,且两辊两端间隙应保持一致,可用塞尺测量。
四、结束语以上是本人近十年来从事瓦楞纸箱生产技术管理,结合学习有关专业书籍后的一些体会及尚未成熟的思考,如有不妥,敬请各位专业人士指正。
总之,只要我们的操作者努力学习、刻苦钻研、仔细观察、认真调整,就一定能生产出合格的瓦楞纸板来。
在起楞过程中,经常出现的故障以及如何排除?1、瓦楞的高度不够,原因可能是压力或温度过低,或者纸张含水分过高。
解决办法是调整压力或辊温,或降低车速,使纸张得以干燥。
2、瓦楞高度不均一,压出的瓦楞纸两边长短不同呈扇形。
这是由于瓦楞辊平行度不好或两端压力不均匀所致。
如左边瓦楞纸比右边短,则应适当地将上瓦楞辊左边升高,否则逆向调整。
3、瓦楞纸卷曲成筒状,主要原因是上下辊筒温度差过大。
应检查上、下辊筒内加热源工作情况,或许其中之一出现故障,可予以修理或更换。
4、瓦楞纸粘在瓦楞辊面上。
辊面温度过高或原纸水分含量过大都会出现这种现象。
此时应调整辊面温度,使纸张干燥后再压楞,若刮刀与辊槽不贴合,应调整或更换。
如何对瓦楞辊进行维护与保养呢?1、使用前要检查瓦楞辊的平行度和紧固情况,调整好辊间配合压力。