液压缸的计算
液压缸的设计计算

Comp any numbe液压缸的设计计算[0089WT-8898YT-W8CCB-BUUT-202108] 液 压 缸 的 设 计 计作为液压系统的执行元件,液压缸将液压能转化为机械能去驱动主机的工作机构做 功。
由于液压缸使用场合与条件的千差万别,除了从现有标准产品系列选型外,往往需要根据具体使用场合自行进行设计。
设计内容液压缸的设计是整个液压系统设计中的一部分,它通常是在对整个系统进行工况分析所后进行的。
其设计内容为确定各组成部分(缸筒和缸盖、活塞和活塞杆、密封装置、排气装置等)的结构形式、尺寸、材料及相关技术要求等,并全部通过所绘制的液压缸装配图和非标准零件工作图反映这些内容。
液压缸的类型及安装方式选择液压缸的输入是液体的流量和压力,输出的是力和直线速速,液压缸的结构简单,工作可靠性好,被广泛地应用于工业生产各个部门。
为了满足各种不同类型机械的各种要求,液压缸具有多种不同的类型。
液圧缸可广泛的分为通用型结构和专用型结构。
而通用型结构液压缸有三种典型结构形式:(1)拉杆型液压缸前、后端盖与缸筒用四根(方形端盖)或六根(圆形端盖)拉杆来连接,前、后端盖为正方形、长方形或圆形。
缸筒可选用钢管厂提供的高精度冷拔管,按行程长度所相应的尺寸切割形成,一般内表面不需加工(或只需作精加工)即能达到使用要求。
前、后端盖和活塞等主要零件均为通用件。
因此,拉杆型液压缸结构简单、拆装简便、零件通用化程度较高、制造成本较低、适于批量生产。
但是,受到行程长度、缸筒内径和额定压力的限制。
如果行程长度过长时,拉杆长度就相应偏长,组装时容易偏歪引起缸筒端部泄漏;如缸筒内径过大和额定压力偏高时,因拉杆材料强度的要求,选取大直径拉杆,但径向尺寸不允许拉杆直径过大。
(2)焊接型液压缸缸筒与后端盖为焊接连接,缸筒与前端盖连接有内螺纹、内卡环、外螺纹、外卡环、法兰、钢丝挡圈等多种形式。
焊接型液压缸的特点是外形尺寸较小,能承受一定的冲击负载和严酷的外界条件。
液压缸出力计算

液压缸出力计算
液压缸是工业生产中常用的执行元件之一,其出力大小对于工作效率和产品质量有着重要的影响。
液压缸的出力计算是保证其正常工作的基础,下面我们来详细介绍液压缸出力计算的方法。
液压缸的出力计算需要根据其工作状态和工作参数来确定。
首先需要确定液压缸的有效面积,即液压缸的内径和活塞的有效面积。
然后需要确定活塞的推力大小,这个推力大小可以根据液压缸的工作压力和活塞面积来计算。
液压缸的出力计算公式为:出力 = 压力 x 有效面积。
其中,出力以牛顿或千克力为单位,压力以帕斯卡或磅力/平方英尺为单位,有效面积以平方米或平方英尺为单位。
在实际应用过程中,出力和有效面积的单位需要进行统一换算。
需要注意的是,液压缸的出力大小也受到液压系统的影响。
液压系统中的油液流量和压力都会影响液压缸的出力大小。
因此,在液压缸出力计算时,还需要考虑液压系统中的工作压力和油液流量等参数。
综上所述,液压缸出力计算是液压系统中的重要内容,需要根据液压缸的工作状态和工作参数进行确定。
液压缸出力的大小对于工作效率和产品质量有着重要的影响,需要在实际应用中进行合理的调整和优化。
- 1 -。
液压缸设计计算
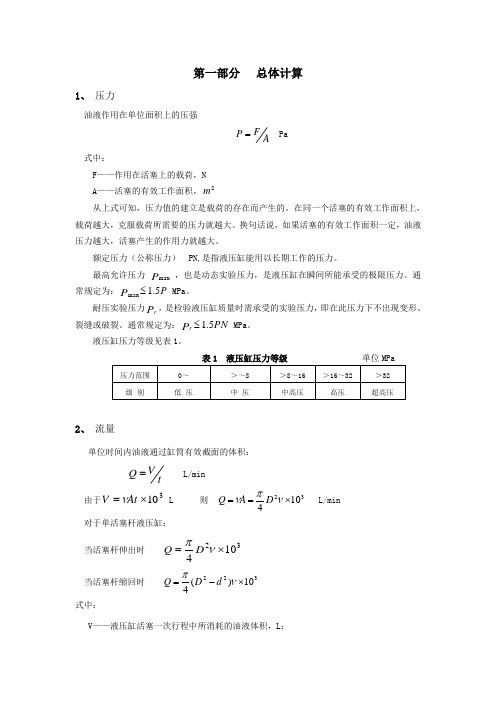
第一部分 总体计算1、 压力油液作用在单位面积上的压强AFP = Pa式中:F ——作用在活塞上的载荷,N A ——活塞的有效工作面积,2m从上式可知,压力值的建立是载荷的存在而产生的。
在同一个活塞的有效工作面积上,载荷越大,克服载荷所需要的压力就越大。
换句话说,如果活塞的有效工作面积一定,油液压力越大,活塞产生的作用力就越大。
额定压力(公称压力) PN,是指液压缸能用以长期工作的压力。
最高允许压力 P max ,也是动态实验压力,是液压缸在瞬间所能承受的极限压力。
通常规定为:P P 5.1max ≤ MPa 。
耐压实验压力P r ,是检验液压缸质量时需承受的实验压力,即在此压力下不出现变形、裂缝或破裂。
通常规定为:PN P r 5.1≤ MPa 。
液压缸压力等级见表1。
2、 流量单位时间内油液通过缸筒有效截面的体积: tVQ = L/min由于310⨯=At Vν L 则 32104⨯==νπνD A Q L/min对于单活塞杆液压缸: 当活塞杆伸出时32104⨯=νπD Q当活塞杆缩回时 32210)(4⨯-=νπd D Q式中:V ——液压缸活塞一次行程中所消耗的油液体积,L ;t ——液压缸活塞一次行程所需的时间,min ; D ——液压缸缸径,m ; d ——活塞杆直径,m ; ν——活塞运动速度,m/min 。
3、速比液压缸活塞往复运动时的速度之比:22212dD D v v -==ϕ 式中:1v ——活塞杆的伸出速度,m/min ; 2v ——活塞杆的缩回速度,m/min ;D ——液压缸缸径,m ; d ——活塞杆直径,m 。
计算速比主要是为了确定活塞杆的直径和是否设置缓冲装置。
速比不宜过大或过小,以免产生过大的背压或造成因活塞杆太细导致稳定性不好。
4、液压缸的理论推力和拉力活塞杆伸出时的理推力: 6261110410⨯=⨯=p D p A F πN活塞杆缩回时的理论拉力: 62262210)(410⨯-=⨯=p d D p F F πN式中:1A ——活塞无杆腔有效面积,2m ;2A ——活塞有杆腔有效面积,2m ;P ——工作压力,MPa ; D ——液压缸缸径,m ; d ——活塞杆直径,m 。
液压缸计算公式
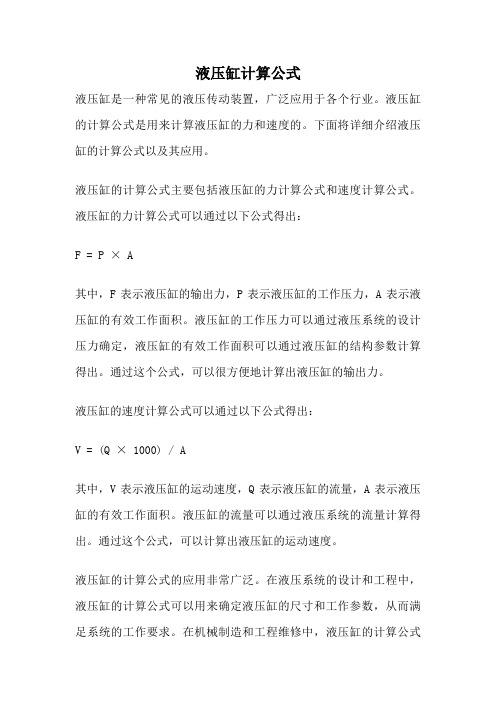
液压缸计算公式液压缸是一种常见的液压传动装置,广泛应用于各个行业。
液压缸的计算公式是用来计算液压缸的力和速度的。
下面将详细介绍液压缸的计算公式以及其应用。
液压缸的计算公式主要包括液压缸的力计算公式和速度计算公式。
液压缸的力计算公式可以通过以下公式得出:F = P × A其中,F表示液压缸的输出力,P表示液压缸的工作压力,A表示液压缸的有效工作面积。
液压缸的工作压力可以通过液压系统的设计压力确定,液压缸的有效工作面积可以通过液压缸的结构参数计算得出。
通过这个公式,可以很方便地计算出液压缸的输出力。
液压缸的速度计算公式可以通过以下公式得出:V = (Q × 1000) / A其中,V表示液压缸的运动速度,Q表示液压缸的流量,A表示液压缸的有效工作面积。
液压缸的流量可以通过液压系统的流量计算得出。
通过这个公式,可以计算出液压缸的运动速度。
液压缸的计算公式的应用非常广泛。
在液压系统的设计和工程中,液压缸的计算公式可以用来确定液压缸的尺寸和工作参数,从而满足系统的工作要求。
在机械制造和工程维修中,液压缸的计算公式可以用来评估液压缸的工作性能和故障排除。
液压缸的计算公式还可以用来优化液压系统的设计。
通过合理选择液压缸的尺寸和工作参数,可以提高液压系统的效率和稳定性。
同时,液压缸的计算公式也可以用来对液压系统进行性能测试和评估,为系统的优化提供依据。
液压缸的计算公式是液压系统设计和工程应用中的重要工具。
通过合理应用这些公式,可以方便地计算液压缸的力和速度,从而满足系统的工作要求。
液压缸的计算公式的应用范围广泛,对于液压系统的设计、制造和维修都具有重要意义。
希望本文的介绍对读者有所帮助。
液压缸计算

液压缸设计计算说明 系统压力为1p =25 MPa本系统中有顶弯缸、拉伸缸以及压弯缸。
以下为这三种液压缸的设计计算。
一、 顶弯缸 1 基本参数的确定(1)按推力F 计算缸筒内径D根据公式 3.5710D -=⨯ ① 其中,推力F=120KN系统压力1p =25 MPa带入①式,计算得D= 78.2mm ,圆整为D = 80 mm (2)活塞杆直径d 的确定确定活塞杆直径d 时,通常应先满足液压缸速度或速比的要求,然后再校核其结构强度和稳定性。
若速比为ϕ,则d = ② 取ϕ=1.6,带入②式,计算得d =48.9mm ,圆整为d =50mm8050D d ϕ===1.6 (3)最小导向长度H 的确定对一般的液压缸,最小导向长度H 应满足202L DH ≥+ ③ 其中,L 为液压缸行程,L=500mm带入③式,计算得H=65mm (4)活塞宽度B 的确定活塞宽度一般取(0.6~1.0)B D = ④ 得B=48mm~80mm ,取B=60mm (5)导向套滑动面长度A 的确定在D <80mm 时,取(0.6~1.0)A D = ⑤ D >80mm 时,取(0.6~1.0)A d = ⑥ 根据⑤式,得A=48mm~80mm ,取A=50mm (6)隔套长度C 的确定 根据公式2A BC H +=-⑦ 代入数据,解得C=10mm 2 结构强度计算与稳定校核 (1)缸筒外径缸筒内径确定后,有强度条件确定壁厚δ,然后求出缸筒外径D 1假设此液压缸为厚壁缸筒,则壁厚1]2D δ=⑧ 液压缸筒材料选用45号钢。
其抗拉强度为σb =600MPa 其中许用应力[]b nσσ=,n为安全系数,取n=5将数据带入⑧式,计算得δ=8.76mm故液压缸筒外径为D 1=D+2δ=97.52mm ,圆整后有 D 1=100mm ,缸筒壁厚δ=10mm (2)液压缸的稳定性和活塞杆强度验算按速比要求初步确定活塞杆直径后,还必须满足液压缸的稳定性及其强度要求。
液压油缸压力计算公式液压油缸设计计算公式
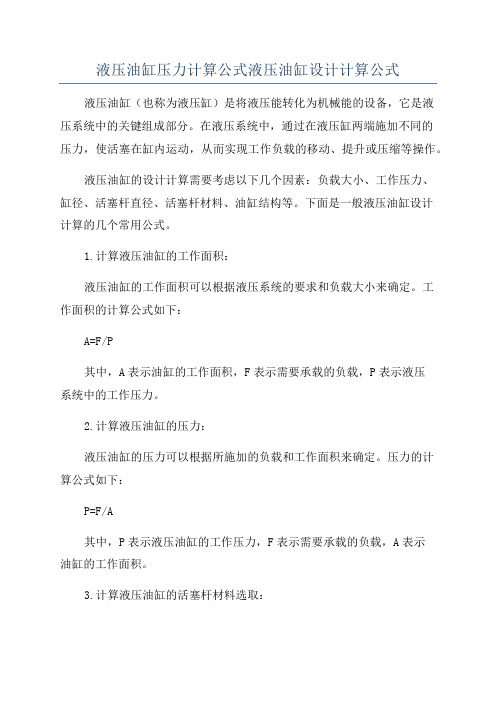
液压油缸压力计算公式液压油缸设计计算公式液压油缸(也称为液压缸)是将液压能转化为机械能的设备,它是液压系统中的关键组成部分。
在液压系统中,通过在液压缸两端施加不同的压力,使活塞在缸内运动,从而实现工作负载的移动、提升或压缩等操作。
液压油缸的设计计算需要考虑以下几个因素:负载大小、工作压力、缸径、活塞杆直径、活塞杆材料、油缸结构等。
下面是一般液压油缸设计计算的几个常用公式。
1.计算液压油缸的工作面积:液压油缸的工作面积可以根据液压系统的要求和负载大小来确定。
工作面积的计算公式如下:A=F/P其中,A表示油缸的工作面积,F表示需要承载的负载,P表示液压系统中的工作压力。
2.计算液压油缸的压力:液压油缸的压力可以根据所施加的负载和工作面积来确定。
压力的计算公式如下:P=F/A其中,P表示液压油缸的工作压力,F表示需要承载的负载,A表示油缸的工作面积。
3.计算液压油缸的活塞杆材料选取:液压油缸的活塞杆材料需要根据所承载负载和工作压力来选择,以满足强度和刚度的要求。
常见的活塞杆材料有碳钢、不锈钢、铬钼合金钢等。
一般用弯曲应力公式进行计算,考虑到材料的抗弯刚度,活塞杆的直径可以根据以下公式得到:d=((32*M*L)/(π*σ))^(1/3)其中,d表示活塞杆的直径,M表示活塞杆所承受的最大弯矩,L表示活塞杆的长度,σ表示选定材料的抗弯应力。
4.计算液压油缸的活塞直径:液压油缸的活塞直径可以通过活塞面积和活塞杆直径计算得到。
计算公式如下:D=(4*A)/(π*d^2)其中,D表示液压油缸的活塞直径,A表示油缸的工作面积,d表示活塞杆的直径。
5.计算液压油缸的油缸容积:液压油缸的油缸容积可以通过活塞面积和活塞行程来计算。
计算公式如下:V=A*l其中,V表示油缸的容积,A表示油缸的工作面积,l表示活塞的行程。
通过上述公式的计算,可以得到液压油缸的设计参数,从而满足液压系统的工作要求。
需要注意的是,在实际设计过程中,还应该考虑其他因素,如密封结构、摩擦损失、液压系统的动态响应等,以确保液压油缸的安全可靠运行。
液压缸的计算

(2)伸缩缸。
伸缩缸由两个或多个活塞缸套装而成,前一级活塞缸的活塞杆内孔是后一级活塞缸的缸筒,伸出时可获得很长的工作行程,缩回时可保持很小的结构尺寸,伸缩缸被广泛用于起重运输车辆上。
伸缩缸可以是如图4-10(a)所示的单作用式,也可以是如图4-10(b)所示的双作用式,前者靠外力回程,后者靠液压回程。
图4-10伸缩缸伸缩缸的外伸动作是逐级进行的。
首先是最大直径的缸筒以最低的油液压力开始外伸,当到达行程终点后,稍小直径的缸筒开始外伸,直径最小的末级最后伸出。
随着工作级数变大,外伸缸筒直径越来越小,工作油液压力随之升高,工作速度变快。
其值为:F i=p124iD(4-30)V1=4q/πD i2 (4-31) 式中的i指i级活塞缸。
图4-11齿轮缸(3)齿轮缸。
它由两个柱塞缸和一套齿条传动装置组成,如图4-11所示。
柱塞的移动经齿轮齿条传动装置变成齿轮的传动,用于实现工作部件的往复摆动或间歇进给运动。
二、液压缸的典型结构和组成1.液压缸的典型结构举例图4-12所示的是一个较常用的双作用单活塞杆液压缸。
它是由缸底20、缸筒10、缸盖兼导向套9、活塞11和活塞杆18组成。
缸筒一端与缸底焊接,另一端缸盖(导向套)与缸筒用卡键6、套5和弹簧挡圈4固定,以便拆装检修,两端设有油口A和B。
活塞11与活塞杆18利用卡键15、卡键帽16和弹簧挡圈17连在一起。
活塞与缸孔的密封采用的是一对Y形聚氨酯密封圈12,由于活塞与缸孔有一定间隙,采用由尼龙1010制成的耐磨环(又叫支承环)13定心导向。
杆18和活塞11的内孔由密封圈14密封。
较长的导向套9则可保证活塞杆不偏离中心,导向套外径由O形圈7密封,而其内孔则由Y形密封圈8和防尘圈3分别防止油外漏和灰尘带入缸内。
缸与杆端销孔与外界连接,销孔内有尼龙衬套抗磨。
图4-12双作用单活塞杆液压缸1—耳环2—螺母3—防尘圈4、17—弹簧挡圈5—套6、15—卡键7、14—O形密封圈8、12—Y形密封圈9—缸盖兼导向套10—缸筒11—活塞13—耐磨环16—卡键帽18—活塞杆19—衬套20—缸底如图4-13所示为一空心双活塞杆式液压缸的结构。
液压的计算公式范文
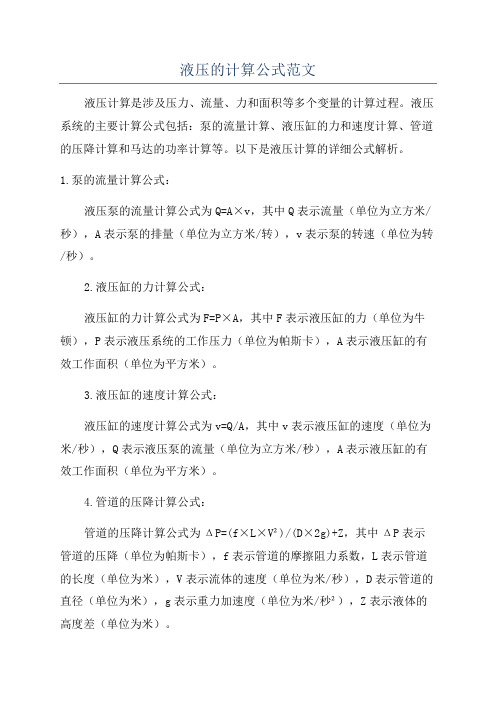
液压的计算公式范文
液压计算是涉及压力、流量、力和面积等多个变量的计算过程。
液压系统的主要计算公式包括:泵的流量计算、液压缸的力和速度计算、管道的压降计算和马达的功率计算等。
以下是液压计算的详细公式解析。
1.泵的流量计算公式:
液压泵的流量计算公式为Q=A×v,其中Q表示流量(单位为立方米/秒),A表示泵的排量(单位为立方米/转),v表示泵的转速(单位为转/秒)。
2.液压缸的力计算公式:
液压缸的力计算公式为F=P×A,其中F表示液压缸的力(单位为牛顿),P表示液压系统的工作压力(单位为帕斯卡),A表示液压缸的有效工作面积(单位为平方米)。
3.液压缸的速度计算公式:
液压缸的速度计算公式为v=Q/A,其中v表示液压缸的速度(单位为米/秒),Q表示液压泵的流量(单位为立方米/秒),A表示液压缸的有效工作面积(单位为平方米)。
4.管道的压降计算公式:
管道的压降计算公式为ΔP=(f×L×V²)/(D×2g)+Z,其中ΔP表示管道的压降(单位为帕斯卡),f表示管道的摩擦阻力系数,L表示管道的长度(单位为米),V表示流体的速度(单位为米/秒),D表示管道的直径(单位为米),g表示重力加速度(单位为米/秒²),Z表示液体的高度差(单位为米)。
5.马达的功率计算公式:
以上是液压的一些常用计算公式,可以通过这些公式进行液压系统的设计和计算。
需要注意的是,不同的液压系统可能存在不同的计算公式和参数,具体计算时应结合实际情况进行分析和计算。
- 1、下载文档前请自行甄别文档内容的完整性,平台不提供额外的编辑、内容补充、找答案等附加服务。
- 2、"仅部分预览"的文档,不可在线预览部分如存在完整性等问题,可反馈申请退款(可完整预览的文档不适用该条件!)。
- 3、如文档侵犯您的权益,请联系客服反馈,我们会尽快为您处理(人工客服工作时间:9:00-18:30)。
(2)单活塞杆双作用缸液压缸作伸出运动时的一般模型如图3-1所示,其阻力 或所需提供的液压力可表示为
(3-2)
式中 -----作用在活塞上的工作阻力, ;
-----液压缸起动(或制动)时的惯性力, ;
-----运动部件处的摩擦阻力, ;
-----运动部件的自重(含活塞和活塞杆自重), ;
-----密封环内径, , ;
----密封环外径, , ;
-----附加密封压力, ,若采用金属材料时, 值即屈服极限点;
----螺钉孔分布圆直径, ;
---法兰材料的许用应力, 。
圆整取
3.4.8缸筒-缸盖的连接计算
缸筒与缸盖采用螺栓连接,螺纹处拉应力为
(3-18)
螺纹处的切应力为
(3-19)
合应力
(3-20)
式中 -----螺纹拧紧系数,静载时,取 ,动载时,取 ;
----螺纹内摩擦系数,一般取 ;
----螺纹外径, ;
----螺纹内径, ,采用普通螺纹时, ;
-----螺纹螺距, ;
----螺栓数量;
---螺纹材料的许用应力, , 。
这里选择6个 的螺栓。
合应力
所以 即
3.5活塞组件设计
3.5.1活塞设计
3.5.3活塞杆设计
(1)基本结构
活塞杆有实心杆和空心杆两种,实心杆强度较高,加工简单,应用较多。空心活塞杆多用于活塞杆与缸径比值d/D较大的大型液压缸中,以减轻活塞杆的重量,或用于缸筒带动工作机构的场合如机床中,或用于活塞杆必须带有传感器的伺服液压缸中。
本课题选用实心杆。
(2)活塞杆的材料和技术要求
活塞材料选用的依据主要从活塞结构形式来考虑。对于有支承环的活塞,常用20号、35号及45号优质碳素钢。对于未采用支承环的活塞多采用高强度铸铁HT200-300、耐磨铸铁、球墨铸铁及锡青铜、铝合金,一些连续工作的高耐久性活塞外表面长烧锡青铜合金或喷镀尼龙等材料。
本课题选用分体式,其材料选用35号钢。
3.5.2活塞与活塞杆的连接结构
(3-16)
式中 -----缸底止口外径, ;
-----油口直径, ;
-----工作压力, ;
----材料许用应力安全系数( ), 。
3.4.7缸筒头部法兰厚度
选择螺钉连接法兰,法兰厚度 为
(3-17)
式中 -----法兰厚度, ;
-----法兰受力总和, ; ;
----密封环平均直径, ; ;
-----工作压力, ;
3.4பைடு நூலகம்筒设计与计算
3.4.1缸筒与缸盖的连接方式
端盖分为前端盖和后端盖。前端盖将活塞杆(柱塞)腔封闭,并起着为活塞杆导向、密封和防尘之作用。后端盖即缸底一端封闭,通常起着将液压缸与其他机件的作用。
缸筒与端盖常见的连接方式有8种:拉杆式、法兰式、焊接式、内螺纹式、外螺纹式、内卡环式、外卡环式和钢丝挡圈式,其中焊接式只适应缸筒与后端盖的连接。
-----液压缸内径, 。
(2)活塞杆强度校核
活塞杆在稳定工况下,如果只受轴向拉力或推力,可近似按直杆承受拉压载荷的简单强度计算公式进行校核计算:
(3-21)
式中 -----活塞杆输出力, ;
-----活塞杆应力, ;
-----活塞杆直径, ;
---材料的许用应力, ; ;
----材料的屈服强度, ;
3.4.4缸筒的计算
本课题中液压缸承受压力负载,缸筒内径可根据下式求出:
(3-7)
式中 -----拉力负载(取最大值), ;
-----供液压力(假定回液压力为大气压), ;
-----活塞杆直径, 。
由于该式中活塞杆直径为未定值,可根据确定的速度比 及将 代入可求D值,再进一步确定活塞杆直径d。D和d应圆整到标准系列尺寸值。
图3-1 液压系统图
表3-1 液压工作图
元件名称
动作顺序
电磁铁
1YA
2YA
3YA
快退
+
-
+
工退
+
-
-
工进
-
+
-
3.4.2液压泵与电动机的选择
(1)液压泵选择
液压泵是将机械能转换为液压能的能量转换装置。贼液压系统中,液压泵作为动力源,向液压系统提供液压能。
确定液压泵的最大压力
其中 ————从液压泵出口到液压缸或液压马达入口之间总的管道损失,取 为0.3MPa
-----安全系数, ,一般取 。
所以
(3)活塞杆轴肩、螺纹及卡环(键)强度
活塞杆轴肩挤压强度按下式计算:
(3-22)
式中 -----活塞杆轴肩挤压应力, ;
-----活塞杆作用力, ;
-----活塞杆直径, ;
-----活塞孔内径, ;
-----活塞孔部倒角, ;
-----活塞杆轴肩倒角, ;
----轴肩的许用应力, 。
3.4.2对缸筒的要求
缸筒是液压缸的主要零件,有时还是液压缸的直接做功部件(活塞杆或柱塞固定时);它与端盖、活塞(柱塞)构成密封容腔,用以容纳压力油液、驱动负载而做功,因而对其有强度、刚度、密封等方面的要求。
3.4.3缸筒的材料选择
缸筒的毛坯普遍采用退火的冷拔或热轧的无缝钢管,市场上已有内孔经过珩磨或内孔经过精加工的半成品,只需要按所要求的长度切割无缝钢管,材料有20、35、45号钢和27SiMn合金钢。
3液压缸的设计及计算
3.1液压缸的负载力分析和计算
本课题任务要求设备的主要系统性能参数为:
铝合金板材的横截面积为
铝合金板材的强度极限为
型材长度
(1)工作载荷
常见的工作载荷为活塞杆上所受的挤压力,弹力,拉力等,在这里我们可得
铝合金板材所受的最大外力为:
(3-1)
式中 ----强度极限, ;
-----截面面积, 。
-----安全系数,通常可取n=5,见表4-14。
因为 所以
通过上述计算,可得液压缸缸筒外径 为
(3-10)
3.4.5缸筒壁厚的验算
计算求得缸筒壁厚 值后,还应进行一下4个方面的验算,以保证液压缸安全可靠的工作。
(1)液压缸的额定工作压力 应低于一定的极限值,以保证工作安全,即 (3-11)
式中 -----液压缸外径和内径, 或 ;
-----缸筒材料的屈服强度, 。
所以
(2)为了避免缸筒工作时发生塑性变形,液压缸的额定工作压力 应与塑性变形压力 有一定的比例关系:
(3) (3-12)
(3-13)
因为
(4)缸筒的径向变形量 值应该在允许范围内,而不能超过密封件允许的范围:
(3-14)
式中 -----液压缸耐压试验压力, ,取 ;
(5)活塞杆的密封与防尘
活塞杆处的密封圈和防尘圈都是标准零件,密封圈的方程圈沟槽的设计要符合国家标准的规定。
3.5.4活塞杆及连接件强度校核
(1)活塞杆的直径 d
在液压缸中,如果液压缸速度有速度比 要求,活塞杆直径 可根据液压缸内径(活塞外径) 按下式求出
(3-20)
式中 -----活塞杆直径, ;
-----缸筒材料的弹性模数, ;
-----缸筒材料的泊松比,对钢材 。
(5)为确保液压缸安全的使用,缸筒的爆裂压力 应大于耐压试验压力
(3-15)
所以缸筒壁厚符合哟求。
3.4.6缸筒底部厚度
缸底结构形式有四种:a. 平面缸底,有凹口,无孔;
b.平面缸底,无口;
c.半椭球形缸底;
d.半环形缸底。
本课题选择b. 平面缸底,无口。
-----作用爱活塞杆侧环形面积上的液压力(拉力), ;
-----进液腔压力(产生推力时液压缸无杆腔进液;产生拉力时有杆腔进液), ;
-----活塞(无杆腔)面积, ;
-----有杆腔面积(活塞杆侧环形面积), , ;
-----液压缸内径(活塞外径), ;
-----活塞杆直径, ;
-----被推动的负载阻力(与 反向), ;
活塞与活塞杆的连接结构有多种形式,常见的有螺纹型,其优点是连接稳固可靠,活塞与活塞杆之间无轴向公差要求,缺点是螺纹的加工和装配比较麻烦。
还有焊接型,这在结构简单,施工比较方便,但不易拆除,而且,对活塞内外径、活塞杆直径及断面接合处的四个面的同轴度。垂直度要求较高。另外有卡环式,
这种结构简单,拆装方便,活塞借助径向间隙有少量浮动,不易卡滞,但活塞与活塞杆之间有轴向公差,该轴向公差会造成活塞与活塞杆的不必要的窜动。该种结构形式在低速液压缸中得到广泛使用。
根据表4-3 根据负载选择压力,初选系统压力为
根据表4-5 液压缸速比与工作压力的关系,得出速比 =1.33
(3-4)
式中 -----活塞杆直径, ;
-----液压缸内径, 。
根据表4-4 液压缸输出液压力,选择液压缸的内径 ,活塞杆直径
(3-5)
(3-6)
式中 -----作用在活塞上的液压力(推力), ;
(1)活塞的结构形式和密封件形式
活塞的密封件形式要根据液压缸的设计(额定)压力、速度和温度等工作条件来选择,而选择的密封件形式则决定了活塞的结构形式。
活塞常用的结构形式可分为整体式和分体(组合)式两种。整体式活塞要在活塞圆周上开沟槽以安装密封件和支承环,架构简单,件活塞加工困难,另外,密封件安装时也容易拉伤和扭曲,影响密封性能和密封件使用寿命。分体(组合)式活塞大多数可以多次拆装,密封件使用寿命长。在通常情况下,支承环是活塞件的不可缺少的结构原件,它不但可以精确雕像,还可以吸收活塞运动时随时产生的侧向力,因而大多数密封件都与支承环联合使用,大大降低了活塞加工成本。(2)活塞的常用材料
-----被拉动的负载阻(与 反向), 。