1苯-甲苯工艺设计
化工原理课程设计-苯甲苯

设计题目:分离苯—甲苯混合液的浮阀精馏塔
学生姓名:
学号:
班级:
指导老师:
写作时间:
1.
1.1
(1)原料液为苯—甲苯混合液,苯含量为45%(质量分率)。
(2)塔顶苯含量不低于98%(质量分率)。
(3)塔底苯含量不高于2%(质量分率)。
(4)进料温度为35℃。
(5)生产能力:年处理苯—甲苯混合液3.5万吨(开工率330天/年)。
进料
出料
项目Βιβλιοθήκη 摩尔分数流量(kmol/h)
项目
摩尔分数
流量(kmol/h)
进料F
0.491
51.84
塔顶产品D
0.983
25.24
塔底产品W
0.024
26.60
合计
51.84
合计
51.84
3.2
苯—甲苯体系为理想物系,故可以使用图解法计算理论塔板数,具体求解过程如下。
表2给出常压(101.33kPa)下苯—甲苯二元物系的汽—液平衡组成。
表2苯—甲苯二元物系的汽—液平衡组成
苯摩尔分数
温度(℃)
苯摩尔分数
温度(℃)
液相x
气相y
液相x
气相y
0.000
0.000
110.6
0.592
0.789
89.4
0.088
0.212
106.1
0.700
0.853
86.8
0.200
0.370
102.2
0.803
0.914
84.4
0.300
0.500
98.6
q线方程为y=9.57x-2.58。
化工原理课程设计苯与甲苯精馏塔

化工原理课程设计苯与甲苯精馏塔本文将针对化工原理课程设计,探讨苯与甲苯精馏塔的工艺设计。
一、工艺流程苯与甲苯精馏塔的工艺流程如下:苯与甲苯混合物在进入塔后,首先通过反应塔抽收制冷剂进行冷却,从而达到冷却效果,然后通过塔顶进入预分离器进行处理,将其中的气相成分与液相成分分离,剩余的液相通过进料口进入塔体,反复上升和下降,与上部的气相进行平衡沸腾,不断提高纯度,最后在顶部凝结出高纯度的甲苯。
二、设计考虑因素1.塔型塔型应根据生产规模和成本考虑。
一般而言,小型的塔型适合处理小流量、高品质的混合物,而大型的塔型则适合处理大流量、低品质的混合物。
2.动力学参数在设计苯与甲苯精馏塔时,要考虑动力学参数,如液相和气相的流速、物料的热量传递效应等等。
这些参数将直接影响塔的效率和产品品质。
3.填料和操作条件由于苯与甲苯混合物具有一定的粘度和密度差异,因此应在填料和操作条件上进行制约,以避免不同成分之间发生混合或分离出现问题。
三、设计基础1.填料设计填料是苯与甲苯精馏塔的重要组成部分,是决定塔效率和塔高的关键因素。
填料材料应具有良好的性能,如高效的传质、良好的气体液体接触、稳定的抗攻击性等等。
常见的填料材料有氧化铝、陶瓷、合金等。
2.除塔器设计除塔器是苯与甲苯精馏塔的一个重要设计组成部分。
它的主要作用是在塔底处收集返回的液相,防止溢出和保持塔内的可控性。
除塔器的设计应根据填料类型、流量、操作温度和压力等多个因素进行综合考虑,以确保塔的正常运行。
3.塔底设计塔底是苯与甲苯精馏塔的重要组成部分,主要用于收集精馏出的液态产品。
由于反应塔存在高温、高压等因素,因此需要考虑塔底的材料和设计。
常见的材料有碳钢、不锈钢、合金等。
此外,塔底还应配备可靠的排放和泄压装置,以确保塔的安全性。
四、结论苯与甲苯精馏塔是一种常见的化工装置,其设计应考虑多种因素,如塔型、填料、动力学参数等等。
从而确保塔的高效、稳定和可靠性。
苯—甲苯

化工原理课程设计设计题目:苯—甲苯连续精馏塔的工艺设计学院石油化工学院专业03高分子材料与工程2班姓名徐峰沈阳工业大学化工原理课程设计苯—甲苯连续精馏塔的工艺设计计:说明书28页表格 2 个插图 4 幅完成日期:指导教师:设计成绩:教研室主任:沈阳工业大学化工原理课程设计任务书专业班级设计人一、设计题目苯—甲苯连续精馏塔的工艺设计二、原始数据及条件1.生产能力:14.5万吨/年(7800小时/年)2.进料温度:30℃3.进料组成:32 %(质量)4.分离要求:塔顶产品95%(质量),塔底产品 3.5 %(质量)。
5.操作条件:(1) 精馏塔顶压强 3×103Pa(表压)(2) 回流比自选(3) 单板压降≯8×102 Pa (浮阀塔);≯7×102Pa (筛板塔)三、设备型式设备型式为筛板塔/ 浮阀塔(F1型)四、设计内容及要求编制一份设计说明书,主要内容包括:1.前言2.设计方案及工艺流程说明3.工艺计算及设备的结构计算4.设计结果一览表5.设计结果的讨论和说明6.符号说明7.参考文献8.结束语五、设计日期:2005 年12月19 日至2005年12 月23 日目录1.前言2.设计方案及流程说明3.工艺计算及设备结构计算塔的物料衡算3.1.1 料液及塔顶.塔产品含苯摩尔分率3.1.2 平均分子量3.1.3 物料衡算3.2 塔板数确定3.2.1 理论塔板数的确定3.2.2 塔板效率3.2.3 实际塔板数3.3 塔的工艺条件3.3.1 操作压强3.3.2 温度3.3.3 平均分子量3.3.4 平均密度3.3.5 表面张力3.3.6 液体粘度3.3.7 气液负荷3.4 塔体的工艺尺寸计算3.4.1 塔径计算3.4.2 塔的高度计算3.5 塔板的主要工艺尺寸3.5.1 溢流装置3.5.2 塔板布置3.5.3 塔板布置及浮阀数排列3.6 浮阀流体力学验算3.6.1 气体通过浮阀塔板时压降3.6.2 雾沫夹带量的验证3.6.3 液泛验算3.6.4 漏液验证3.7 塔板负荷性能图3.7.1 雾沫夹带线3.7.2 液泛线3.7.3 液相负荷上限线3.7.4 漏夜线3.7.5 液相负荷下限线4 计算结果一览表5 设计结果说明6 符号说明7 参考文献8 结束语9 附表、图1.前言1.1塔设备的类型随着化学工业的发展,研制了设备结构。
精馏塔课程设计--苯-甲苯板式精馏塔的工艺设计

第一章绪论1.1精馏的特点与分类精馏是分离液体混合物的典型单元操作。
它是通过加热造成气液两相物系,利利用物系中各组分挥发度的不同的特性来实现分离的。
按精馏方式分为简单精馏、平衡精馏、精馏和特殊精馏。
1.1.1蒸馏分离具有以下特点(1)通过蒸馏分离,可以直接获得所需要的产品。
(2)适用范围广,可分离液态、气态或固态混合物。
(3)蒸馏过程适用于各种浓度混合物的分离。
(4)蒸馏操作耗能较大,节能是个值得重视的问题。
1.1.2平衡蒸馏将混合液在压力p1下加热,然后通过减压阀使压力降低至p2后进入分离器。
过热液体混合物在分离器中部分汽化,将平衡的气、液两相分别从分离器的顶部、底部引出,即实现了混合液的初步分离。
1.1.3简单蒸馏原料液在蒸馏釜中通过间接加热使之部分汽化,产生的蒸气进入冷凝器中冷凝,冷凝液作为馏出液产品排入接受器中。
在一批操作中,馏出液可分段收集,以得到不同组成的馏出液。
1.1.4连续精馏操作流程化工生产以连续精馏为主。
操作时,原料液连续地加入精馏塔内,连续地从再沸器取出部分液体作为塔底产品(称为釜残液);部分液体被汽化,产生上升蒸气,依次通过各层塔板。
塔顶蒸气进入冷凝器被全部冷凝,将部分冷凝液用泵(或借重力作用)送回塔顶作为回流液体,其余部分作为塔顶产品(称为馏出液)采出。
1-精馏塔 2-全凝器3-储槽 4-冷却器5-回流液泵 6-再沸器 7-原料液预热器图1连续精馏装置示意图1.2精馏塔的踏板分类1.2.1塔板的结构形式1.泡罩塔板泡罩塔板是工业上应用最早的塔板,它由升气管与泡罩构成。
泡罩安装在升气管的顶部,分圆形和条形两种,以前者使用较广。
泡罩有φ80mm、φ100mm和φ150mm三种尺寸,可根据塔径大小选择。
泡罩下部周边开有很多齿缝,齿缝一般为三角形、矩形或梯形。
泡罩在塔板上为正三角形排列。
它的优点是操作弹性适中塔板不易堵塞。
缺点是生产能力与板效率较低结构复杂、造价高。
图2泡罩塔板(a)操作示意图 (b)塔板平面图 (c)圆形泡罩2.筛孔塔板筛孔塔板简称筛板,其结构特点是在塔板上开有许多均匀小孔,孔径一般为3~8mm。
苯-甲苯课程设计(新改)

邮电与信息工程学院课程设计任务书专业08过控班级1班学生姓名高志芳发题时间:2011 年 6 月22 日一、课题名称苯——甲苯分离过程筛板式精馏塔设计二、课题条件(原始数据)原料:苯—甲苯年处理量:38000t生产时间:320天/年,每天24h运行原料组成(苯的质量分数):0.5塔顶馏出液组成(质量分数):0.955塔底釜液含甲苯量≥0.96(质量分率)塔顶回收率:η=99%料液初温: 21℃冷却水温度:30℃操作压力:4kpa(塔顶常压)回流比自选单板压降:≤0.7kpa进料状态:饱和液体进料塔顶采用全凝器,泡点回流塔釜:饱和蒸汽间接/直接加热塔板形式:筛孔板全塔效率:E T=0.6设备形式:筛板塔厂址:武汉地区三、参考文献[1]陈敏恒等.化工原理.第二版化.学工业出版社.1999[2]谭天恩,麦本熙,丁惠华.化工原理(上、下册) .第二版.北京:化学工业出版社,1998[3]姚玉英.化工原理例题与习题.第三版.北京:化学工业出版社,1998[4]贾绍义,柴诚敬主编.化工原理课程设计.天津:天津大学出版社,2002[5]李功样,陈兰英,崔英德主编.常用化工单元设备设计.广州:华南理工大学出版社,2003[6]涂伟萍,陈佩珍,程达芬主编.化工工程及设备设计.北京:化学工业出版社,2000[7]钱颂文主编.换热器设计手册.北京: 化学工业出版社,2002[8]《化工过程及设备设计》.广州:华南工学院出版社,1986[9]《化工设计手册》编辑委员会.化学工程手册,第1篇化工基础数据;第8篇传热设备及工业生产.北京:化学工业出版社,1986[10]阮奇,叶长,黄诗煌.化工原理优化设计与解题指南.北京:化学工业出版社,2001四、设计内容(包括设计、计算、论述、实验、应绘图纸等根据目录列出大标题即可)1 设计方案的选定2精馏塔的物料衡算3塔板数的确定4精馏塔的工艺条件及有关物性数据的计算(加热物料进出口温度、密度、粘度、比热、导热系数)5精馏塔塔体工艺尺寸的计算6塔板主要工艺尺寸的计算7塔板的流体力学验算8塔板负荷性能图(只做精馏段的)9换热器计算10精馏塔接管尺寸计算11绘制工艺流程图1张(带控制点、机绘,A2图纸)12绘制板式精馏塔的总装置图1张(包括部分构件)(手绘,A1图纸)13撰写课程设计说明书一份设计说明书注意事项:●写出详细计算步骤,并注明选用数据的来源●每项设计结束后列出计算结果明细表●设计最终需装订成册上交五、进度计划(列出完成项目设计内容、绘图等具体起始日期)1. 下达设计任务书收集资料,阅读教材,拟定设计进度2天2.初步确定设计方案及设计计算内容5-6天3.绘制总装置图、工艺流程图2-3天4.整理设计资料,撰写设计说明书2天5.答辩1天指导教师(签名):年月日学科部(教研室)主任(签名):年月日说明:1.学生进行课程设计前,指导教师应事先填好此任务书,并正式打印、签名,经学科部(教研室)主任审核签字后,正式发给学生。
化工原理课程设计---苯-甲苯冷凝器工艺设计-(2).
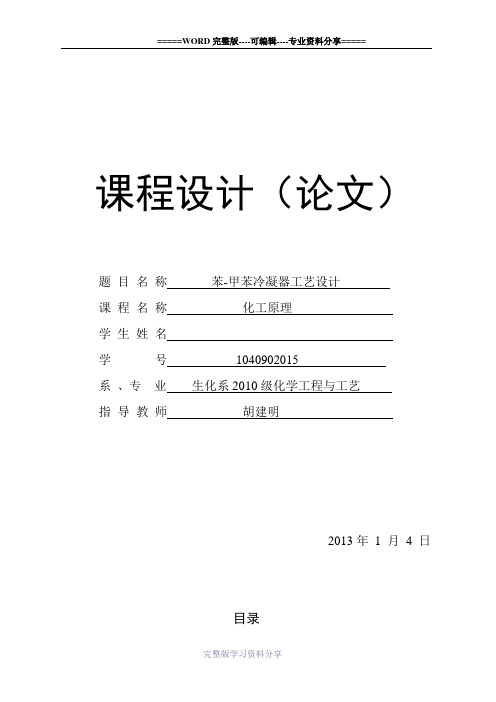
课程设计(论文)题目名称苯-甲苯冷凝器工艺设计课程名称化工原理学生姓名学号1040902015系、专业生化系2010级化学工程与工艺指导教师胡建明2013年1 月4 日目录一、课程设计任务书 (3)二、概述 (5)三、设计依据 (8)四、工艺设计计算 (8)五、物料衡算 (8)2.1 精馏塔物料衡算 (8)2.2 冷凝器物料衡算 (9)六、热量衡算 (11)3.1 冷凝器热量衡算 (11)七、设备设计与选型 (14)八、设备设计 (14)1、流体流径选择 (14)2、冷凝器热负荷 (14)3、流体两端温度的确定 (14)4、总传热系数 (14)5、换热面积 (14)6、初选管程及单管长度 (14)7、筒体直径计算 (15)8、数据核算 (15)九、设备选型 (19)十、总结 (25)十一、参考文献 (26)十二、致谢 (27)十三、附工程图纸 (28)10级化学工程专业《化工原理》课程设计任务书设计课题:苯-甲苯精馏装置进料冷凝器设计一、设计条件1、年产苯:70000吨2、产品苯组成:C6H699.5% (质量分数,下同) 、C6H5-CH30.5%3、原料液为常温液体;原料组成:C6H670%,C6H5-CH330%4、分离要求:塔釜苯含量≤0.5%二、设计内容1、物料衡算(精馏塔、冷凝器)2、热量衡算(冷凝器)3、冷凝器热负荷计算4、冷凝器换热面积计算5、冷凝器结构、材质选择6、冷凝器结构尺寸、工艺尺寸的设计计算等7、冷凝器总传热系数的校核8、冷凝器装配图的绘制三、设计要求1、设计方案简介对给定或选定的工艺流程、主要设备的型式进行简要的论述。
2、工艺设计选定工艺参数,对单个设备作出衡算示意图,进行物料衡算、热量衡算,以表格形式表达衡算结果,其中的数据(非给定数据)及计算公式(经验公式)必须交待来源(即何种参考书目,并在参考文献中列出)。
3、设备计算选择设备的结构形式,并说明理由。
进行设备的结构尺寸和工艺尺寸的设计计算。
化工原理课程设计任务书苯-甲苯板式精馏塔的设计
化工原理课程设计任务书苯-甲苯混合液筛板(浮阀)精馏塔设计2021年6月16日苯-甲苯混合液筛板(浮阀)精馏塔设计一.设计概述塔设备是化工、炼油生产中国最重要的设备之一。
塔设备的设计和研究已经受到化工行业的极大重视。
在化工生产中,塔设备的性能对于整个装置的产品产量、质量、生产能力和消耗定额,以及三废处理和环境保护等各个方面,都有非常重大的影响。
精馏是分离液体混合物(含可液化的气体混合物)最常用的一种单元操作,在化工、炼油。
石油化工等工业中得到广泛应用。
精馏过程在能量剂驱动下(有时加质量剂),使气液两相多次直接接触和分离,利用液相混合物中各组分的挥发度的不同,使易挥发组分由液相向气相转移,难挥发组分由气相向液相转移,实现原料混合液中各组分的分离,根据生产上的不同要求,精馏操作可以是连续的或间歇的,有些特殊的物系还可以采用恒沸精馏或萃取精馏等特殊方法进行分离。
本设计的题目是苯-甲苯混合液筛板精馏塔的设计,即需设计一个精馏塔用来分离易挥发的苯和不易挥发的甲苯。
二.原始数据1.年处理量:50000吨2.料液初温:35℃3.料液浓度:45%(苯质量分率)4.塔顶产品浓度:98%(苯质量分率)5.塔底釜液含甲苯量不低于:98%(以质量计)6.每年实际生产天数:330天(一年中有一个月检修)7.精馏塔塔顶压强:4kkk(表压)8.冷却水温度:30℃9.饱和水蒸气压力:2.5kkk/kk2(表压)10.设备类型:筛板(浮阀)塔三.基础数据1.组分的液相密度(见表-1)温度/℃80859095100105110115苯814.24 808.68 803.08 797.44 791.75 786.01 780.21 774.36甲苯809.80 804.87 799.90 794.90 789.85 784.76 779.63 774.45表-1烃类化合物实测k值多,也有系统的关联工作,最好的关联成果发表在k−k手册中,方程是:k=k+kk+kk2+kk3+kk4关联系数通过查找《化工物性简明手册》得知,k的单位是kk/k3,k的单位是k。
化工原理设计--苯—甲苯分离过程板式精馏塔设计
化工原理课程设计设计题目:常压、连续精馏分离苯一甲苯混合体系目录、化工原理课程设计任务书 (1)、设计计算 (2)一)确定设计方案的原则. (2)二)操作条件的确定. (3)三). 设计方案的选定及基础数据的搜集 (4)四)精馏塔的物料衡算 (8)五)塔板数的确定 (8)(一)理论板层数NT 的求取 (8)(1).......................................................................... 最小回流比的求取;8(2)求精馏塔的气、液相负荷 (9)(3)求操作线方程 (9)(二)实际板层数的求取 (10)六)精馏塔的工艺条件及有关物性数据的计算 (10)(1)操作压力计算 (10)(2)操作温度计算 (11)(3)平均摩尔质量计算 (11)(4)平均密度计算 (11)七)气液负荷计算 (13)八)精馏塔的塔体工艺尺寸计算 (13)(1).................................................................. 塔径的计算13(2)塔高的计算 (14)九)塔板主要工艺尺寸的计算 (14)(1)..................................................................... 溢流装置计算14(2)塔板布置 (15)十)筛板的流体力学验算 (16)(1)气体通过筛板压强相当的液柱高度hp hc hl h. ............................16(2) 液面落差 (17)(3) 液沫夹带 (17)(5) 液泛 (17)塔板负荷性能图 (18)(1)漏液线 (18)(2) 液沫夹带线 (18)(3) 液相负荷下限线 (19)(4) 液相负荷上限线 (19)(5) 液泛线 (19)设计结果一览(表9) (21)三、个人心得体会及改进意见 (22)四、参考文献 (22)附录(符号说明) (23)一、化工原理课程设计任务书板式精馏塔设计任务书(一)设计题目:设计分离苯一甲苯连续精馏筛板塔 (二)设计任务及操作条件1、设计任务:原料处理量:f= 5300kg/h进料组成:X F=0,55 (轻组分苯的摩尔分率,下同) 塔顶产品组成: X D=0.91 分离要求:回收率??=0.95全塔效率:58%2、操作条件:平均操作压力:101.3 kPa 回流比:R=1.8Rmin 单板压降:<=0.7kPa工时:年开工时数7200 小时泡点进料:q=1 Xq=Xe=X F(三)设计方法和步骤:1、设计方案简介根据设计任务书所提供的条件和要求,通过对现有资料的分析对比,选定适宜的流程方案和设备类型,初步确定工艺流程。
苯—甲苯精馏分离板式塔设计
一设计题目:苯—甲苯精馏分离板式塔设计二、设计任务及操作条件1、设计任务:生产能力(进料量)7000吨/年操作周期300天/年进料组成35%(质量分率,下同)塔顶产品组成99.8%塔底产品组成0.2%2、操作条件操作压力 4 kPa (表压)进料热状态泡点进料单板压降≯0.7 kPa回流比: R=2Rmin 由设计者自选塔顶采用全凝器泡点回流塔釜采用间接饱和水蒸气加热全塔效率为0.63、设备型式筛板精馏塔4、厂址荆门地区三、设计内容:1、设计方案的选择及流程说明2、工艺计算3、主要设备工艺尺寸设计(1)塔和塔板主要工艺结构的设计计算(2)塔板的流体力学校核(3)塔板的负荷性能图(4)总塔高、总压降及接管尺寸的确定4、辅助设备选型与计算5、设计结果汇总6、对本设计的评述或对有关问题的分析与讨论。
四、设计要求1、设计程序简练清楚,结果准确并有汇总表。
2、计算公式、图表正确并注明来源,符号和单位要统一。
五、设计时间:四周注意事项:1、写出详细计算步骤,并注明选用数据的来源;2、每项设计结束后,列出计算结果明细表3、图、表分别按顺序编号4、按规定的时间进行设计,并按时完成任务四、要求(1)对精馏过程进行描述(2)对精馏过程进行物料衡算和热量衡算(3)对精馏塔进行设计计算(4)对精馏塔的附属设备进行选型(5)画一张精馏塔的装配图(6)编制设计说明书符号说明英文字母-阀孔的鼓泡面积m2Aα-降液管面积 m2Af-塔截面积 m2ATb -操作线截距c -负荷系数(无因次)c-流量系数(无因次)D -塔顶流出液量 kmol/hD -塔径 md-阀孔直径 m-全塔效率(无因次)ETE -液体收缩系数(无因次)e-物沫夹带线 kg液/kg气vF -进料流量 kmol/h-阀孔动能因子 m/sFg -重力加速度 m/s2H-板间距 mTH -塔高 mH-清液高度 md-与平板压强相当的液柱高度 mhc-与液体流径降液管的压降相当液柱高度 m hd-与气体穿过板间上液层压降相当的液柱高度 m hr-板上鼓泡高度 mhf-板上液层高度 mhL-降液管底隙高度 mhh-堰上液层高度 m02v-与板上压强相当的液层高度 mhp-与克服液体表面张力的压降所相当的液柱高度 m hσ-溢液堰高度 mh2vK -物性系数(无因次)-塔内下降液体的流量 m3/sLs-溢流堰长度 mLwM -分子量 kg/kmolN -塔板数-实际塔板数Np-理论塔板数NTP -操作压强 PaΔP-压强降 Paq -进料状态参数R -回流比-最小回流比Rminu -空塔气速 m/sw -釜残液流量 kmol/h-边缘区宽度 mwc-弓形降液管的宽度 mwd-脱气区宽度 mwsx -液相中易挥发组分的摩尔分率y -气相中易挥发组分的摩尔分率z -塔高 m希腊字母α-相对挥发度μ-粘度 Cpρ-密度 kg/m3σ-表面张力下标r -气相L -液相l -精馏段q -q线与平衡线交点min-最小max-最大A -易挥发组分B -难挥发组分化工原理课程设计----------筛板塔的设计第一章流程及生产条件的确定和说明第一节概述流程示意图冷凝器→塔顶产品冷却器→苯的储罐→苯↑↓回流原料→原料罐→原料预热器→精馏塔↑回流↓再沸器←~ 塔底产品冷却器→氯苯的储罐→氯苯精馏塔是现在化工厂中必不可少的设备,因此出现了很多种的精馏塔。
分离苯—甲苯混合液的浮阀板式精馏塔工艺设计
分离苯—甲苯混合液的浮阀板式精馏塔工艺设计苯和甲苯是两种常用的有机溶剂,它们通常通过精馏过程进行分离。
浮阀板式精馏塔是一种常用的精馏设备,具有高效、节能、操作方便等特点。
下面就对分离苯和甲苯混合液的浮阀板式精馏塔工艺进行设计。
1.工艺流程:分离苯和甲苯混合液的浮阀板式精馏塔工艺流程一般包括进料、初留、尾留和回流等环节,具体流程如下:1)进料:将苯和甲苯混合液进料到精馏塔的顶部。
进料包括苯和甲苯的混合物以及一部分回流。
2)初留:通过多个塔板的精馏,将苯分离出来,初留液位以下的液体为初馏液,初留液通过凝气冷却器冷却后分为初留顶部产品和初留底部回流。
3)尾留:在塔底通过降温器冷却后,即可得到尾液,尾留底部产品通常作为顶部产品的回流,以保证塔托和稳定操作。
4)回流:回流是为了提高塔板的效率,减小焦失和能耗。
可通过将一部分的顶部产品送回到塔顶部作为回流。
2.浮阀板式精馏塔的设计参数:在进行浮阀板式精馏塔的工艺设计时,需要考虑以下参数:1)塔高:塔高应根据塔板的数量和塔板高度来确定,总体来说,塔高越高,分馏效果越好,但是设备成本和能耗也会增加。
2)塔板数:塔板数的确定需要考虑到初留和尾留的要求,一般根据初留质量分数和尾留质量分数进行迭代计算。
3)流量:进料流量、回流流量以及所需的产品流量都需要根据需求和经验来确定,可通过仪表和流量控制阀来调节。
4)进料温度:进料温度一般在常温下进行,如果需要提高分离效率,可以适当降低进料温度。
5)塔底温度:塔底温度是通过冷凝器来冷却的,根据具体情况来确定冷凝器的设计参数。
3.优化调整:在实际工艺操作中,可能需要对工艺参数进行优化调整,以达到更好的分离效果和降低能耗。
具体调整方法如下:1)调整回流比:根据实际需要,调整回流比可以提高塔板的效率。
2)改变操作压力:通过改变操作压力,可以改变馏出物的温度和塔板的效果,进而实现优化调整。
3)塔板节流孔调整:通过调整塔板节流孔的大小,可以影响流体的分布和液体在塔板上的停留时间,从而达到更好的分离效果。
- 1、下载文档前请自行甄别文档内容的完整性,平台不提供额外的编辑、内容补充、找答案等附加服务。
- 2、"仅部分预览"的文档,不可在线预览部分如存在完整性等问题,可反馈申请退款(可完整预览的文档不适用该条件!)。
- 3、如文档侵犯您的权益,请联系客服反馈,我们会尽快为您处理(人工客服工作时间:9:00-18:30)。
引言1.1 塔设备的分类塔设备是能够实现蒸馏的气液传质设备,广泛应用于化工、石油化工、石油等工业中,其结构形式基本上可以分为板式塔和填料塔两大类。
板式塔内设置一定数量的塔板,气体以鼓泡或喷射的方式穿过板上的液层,进行传质于传热。
在正常操作下,气相为分散相,液相为连续相,气相组成呈阶梯变化,属于逐级接触逆流操作过程。
填料塔内装有一定高度的填料层,液体自塔顶沿填料表面下流,气体逆流向上(有时也采用并流向下)流动,气体两相密切接触进行传热与传质。
在正常操作过程中,气相为连续相,液相为分散相,气相组成呈连续变化,属于微分接触逆流操作过程。
1.2 塔设备在化工生产中的作用和地位精馏过程的实质是利用混合物中各组分具有不同的挥发度。
即在同一温度下,各组分的饱和蒸汽压不同这一性质,使液相中的轻组分转移到汽相中,汽相中的重组分转移到液相中,从而达到分离的目的。
因此精馏塔操作弹性的好坏直接关系到石油化工企业的经济效益。
在化工生产中,塔设备的性能对于整个装置的产品产量、质量、生产能力和消耗定额,以及三废处理和环境保护等各个方面,都有非常重大的影响。
1.3 设计条件进料量每小时160千摩尔,原料中含苯55%(摩尔分率),以沸点状态送入塔内。
要求塔顶馏出物含苯96%(摩尔分率),塔釜残液中含苯不大于4%,操作回流比取最小回流比的2.5倍。
1.4 问题研究本设计是针对苯—甲苯的分离而专门设计的塔设备。
根据设计条件以及给出的数据描述出塔温度的分布,求得最小回流比以及塔顶的相对挥发度、塔釜的相对挥发度、全塔平均相对挥发度,又根据物料平衡公式分别计算出精馏段和提馏段的汽、液两相的流量。
之后,计算塔板数、塔径等。
根据这些计算结果进行了塔板结构的设计等。
计算和设计这些之后进行了有关的力学性能计算和一系列的校核。
2.板式塔的设计2.1 工业生产对塔板的要求:①通过能力要大,即单位塔截面能处理的气液流量大。
②塔板效率要高。
③塔板压力降要低。
④操作弹性要大。
⑤结构简单,易于制造。
在这些要求中,对于要求产品纯度高的分离操作,首先应考虑高效率;对于处理量大的一般性分离(如原油蒸馏等),主要是考虑通过能力大。
2.2设计方案的确定2.2.1装置流程的确定精馏装置包括精馏塔,原料预热器,再沸器,冷凝器,釜液冷却器和产品冷却器等设备。
蒸馏过程按操作方式不同,可分为连续精馏和间歇精馏两种流程。
在本次的设计中,是为分离苯—甲苯混合物。
对于二元混合物的分离,应该采用连续精馏流程。
2.2.2操作压力的选择蒸馏过程按操作压力不同,可分为常压蒸馏,减压蒸馏和加压蒸馏。
一般除热敏性物系外,凡通过常压分离要求,并能用江河水或循环水将馏出物冷凝下来的物系,都应采用常压精馏。
根据本次任务的生产要求,应采用常压精馏操作。
2.2.3进料热状况的选择蒸馏操作有五种进料热状况,它的不同将影响塔内各层塔板的汽、液相负荷。
工业上多采用接近泡点的液体进料和饱和液体进料,通常用釜残液预热原料。
所以这次采用的是泡点进料。
2.2.4加热方式的选择由于采用泡点进料,将原料液加热至泡点后送入精馏塔内。
塔顶上升蒸汽采用全凝气冷凝,冷凝液在泡点下一部分回流至塔内,其余部分经产品冷却后送至储罐。
2.2.5回流比的选择回流比是精馏操作的重要工艺条件,其选择的原则是使设备费用和操作费用之和最低。
苯—甲苯混合液是属易分离物系,最小回流比较小,故操作回流比取最小回流比的2.0倍。
塔釜采用间接蒸汽加热,塔顶产品经冷却后送至储罐。
3工艺流程图板式塔主要由筒体、封头、塔内构件(包括塔板、降液管和受液盘)、人孔、进出口管和群座等组成。
按照塔内气、液流动的方式,可将塔板分为错流与逆流塔板两类。
工业应用以错流式塔板为主,常用的由泡罩塔、筛板塔、浮阀塔等。
此次设计按照要求选用筛板塔来分离苯-甲苯系。
4.工艺计算及主体设备的计算4.1 精馏塔的物料衡算进料量每小时160千摩尔,原料中含苯55%(摩尔分率),以沸点状态送入塔内。
要求塔顶馏出物含苯96%(摩尔分率),塔釜残液中含苯不大于4%,操作回流比取最小回流比的2.5倍。
苯的摩尔质量=78.11 kg/kmol甲苯的摩尔质量=93.13 kg/kmol原料处理量F=160 kmol/hx=0.55进料苯的摩尔分率Fx=0.96塔顶苯的摩尔分率D塔顶易挥发组分的回收率η=94%总物料衡算:F = D + W易挥发(苯)组分衡算:W F D W F x D x x ⨯=⨯+⨯塔顶易挥发组分(苯)的回收率:η= D D 100%F Fx x ⨯⨯⨯ 联立解得 94%1600.55/86.2/0.96FDF x D mol h mol h x η⨯⨯⨯⨯=== 16086.273.8/W F D mol h =-=-= 1600.5586.20.960.07173.8F D W F x D x x W ⨯-⨯⨯-⨯=== 4.2 塔板数的确定4.2.1理论板层数T N 的求取苯--甲苯属理想物系,可采用图解法求理论板层数。
①由手册查得苯--甲苯物系的气液平衡数据,绘出x-y 图,见图1。
②求最小回流比及操作回流比采用作图法求最小回流比。
在图1中对角线上,自点e (0.55,0.55)作垂线ef 即为进料线(q 线),该线与平衡线的交点坐标为q y = 0.75 q x = 0.55故最小回流比为R min =0.960.75 1.050.750.55D q q q x y y x --==-- 取操作回流比为 R=2=2 1.05=2.1 ③求精馏塔的气、液相负荷2.186.2181.02/L RD mol h ==⨯=(1)(2.11)86.2267.22/V R D mol h =+=+⨯='181.02160341.02/L L F mol h =+=+='267.22/V V mol h ==④求操作线方程精馏段操作线方程181.0286.20.960.6770.310267.22267.22D LDy x x x x V V =+=+⨯=+提留段操作线方程'341.0273.8'0.071 1.2760.0196''267.22267.22W L Wy x x x x V V =-=-⨯=-⑤图解法求理论塔板数采用图解法求理论塔板数,如图1所示。
求解结果为:总理论板层数 N T = 10.5(包括再沸器)进料板位置 N T = 5图1 图解法求理论板层数4.2.2实际板层数的求解精馏段实际板层数N 精= 47.6980.52=≈提留段实际板层数N提=6.512.513 0.52=≈4.3精馏塔的工艺条件及有关物性数据计算以精馏段为例进行计算4.3.1操作压力的计算设塔顶表压 P表= 4 kPa塔顶操作压力 PD= 101.3 + 4 =105.3 kPa 每层塔板压降ΔP = 0.7 kPa进料板压力 PF = 105.30.78110.9+⨯=kPa精馏段的平均压力105.3110.9108.12mP+== kPa4.3.2操作温度计算依据操作压力,由泡点方程通过试差法计算出泡点温度,其中苯、甲苯的饱和蒸气压由安托尼方程计算,计算过程略。
计算结果如下:塔顶温度 tD=82.1℃进料板温度 tF=泡点温度确定在110.9kPa下溶液的泡点需采用试差法。
经过几次试差后,得到泡点 t = 92 ℃进料板温度 tF= 92℃精馏段平均温度 tm=(82.l+92)/2 = 87.05℃4.3.3 平衡摩尔质量的计算塔顶平均摩尔质量计算由xD = y1= 0.96, 查平衡曲线(见图1),得x1= 0.889MVDm= 0.96⨯78.11 + (1-0.96) 92.13 = 78.67kg/kmolMLDm=0.889 ⨯78.11 + (1-0.889) 92.13 = 79.67kg/kmol 进料板平均摩尔质量计算由图解理论板(见图1),得y F = 0.702查平衡曲线 (见图1),得x F = 0.495M VFm = 0.702 ⨯78.11 + (1-0.702) 92.13 =82.29kg/kmolM LFm =0.495 ⨯ 78.11 + (1-0.495) 92.13 = 85.19kg/kmol精馏段平均摩尔质量M Vm = ( 78.67+82.29) /2 = 80.48kg/kmolM Lm = (79.67 + 85.19) / 2 = 82.43kg/kmol4.3.4平均密度的计算①气相平均密度计算由理想气体状态方程计算,即Vm ρ=m Vmm RT M P = 108.180.488.314(87.05273.15)⨯⨯+ = 2.91kg/m 3②液相平均密度计算液相平均密度依下式计算,即1i i i a ρρ=∑塔顶液相平均密度的计算由t D =82.1℃,查手册得A ρ = 812.7 kg/m 3B ρ = 807.9 kg/m 3LDm ρ = 1(0.96/812.70.04/807.9)+ =812.5kg/m 3进料板液相平均密度的计算由t F =92℃,查手册得A ρ= 734.1kg/m 3B ρ = 734.3 kg/m 3进料板液相的质量分率a A =0.49578.110.49578.110.50592.13⨯⨯+⨯ = 0.454 1734.20.4540.546()734.1734.3LFm ρ==+ 精馏段液相平均密度为Lm ρ=(812.5+734.2)/2 = 773.35kg/m 34.3.5液体平均表面张力计算液相平均表面张力依下式计算,即Lm i i x σσ=∑塔顶液相平均表面张力的计算由t D =82.1℃,查手册得A σ=21.24 mN/mB σ =21.42 mN/mLDm σ= 0.96+⨯24.210.04⨯21.42 = 21.25mN/m进料板液相平均表面张力的计算由t F =92℃,查手册得A σ=19.82mN/mB σ =20.61mN/m0.49519.820.50520.61=20.22mN/m LFm σ=⨯+⨯精馏段液相平均表面张力为Lm σ=(21.25+20.22)/2 = 20.74mN/m4.3.6液体平均粘度计算液相平均粘度依下式计算,即lg lg Lm i i x μμ=∑塔顶液相平均粘度的计算由t D =82.1℃,查手册得A μ =0.302 mPa·sB μ =0.306 mPa·slg LDm μ= 0.96×lg(0.302)+ (1-0.96)×lg(0.306)LDm μ=0.302 mPa·s进料板液相平均粘度的计算由t F =92℃,查手册得A μ =0.276 mPa·sB μ =0.283 mPa·slg LFm μ= 0.495×lg(0.276)+ (1-0.495)×lg(0.283)LFm μ=0.280 mPa·s精馏段液相平均表面张力为Lm μ = (0.302 +0.280)/2 = 0.291mPa •s4.4精馏塔的塔体工艺尺寸计算4.4.1塔径计算精馏段的气、液相体积流率为V s = Vm vm VM ρ3600= 3267.2280.482.053/3600 2.91m s ⨯=⨯L s = Lm LmLM ρ3600 = 3181.0282.430.00536/3600773.35m s ⨯=⨯由 u max = C VVL ρρρ-式中C 由式5-5计算,其中的由图5-1查取,图的横坐标为h h L V (2/1)V L ρρ =0.0053636002.0533600⨯⨯(1/2773.35)2.91 = 0.0426取板间距H T =0.40m ,板上液层高度h L = 0.06m,则H T - h L = 0.40-0.06 = 0.34m查图5-1得,C 20 = 0.075C = C 20(2.0)20L σ = 0.075(0.220.74)20 = 0.0755u max= 1.228 m/s取安全系数为0.7,则空塔系数为u = 0.7 u max = 0.7⨯1.228 = 0.860 D = uV s π41.744m = 按标准塔径圆整后为D =1.8 m塔截面积为A T =4πD 2= 4π⨯ 1.82=2.543 m 2 实际空塔系数为 u = 2.0530.807/2.543m s = 4.4.2精馏塔有效高度的计算精馏段有效高度为Z 精 = (N 精 -1)H T = (8-1) ×0.4=2.8m提馏段有效高度为Z 提 = (N 提 -1)H T =(13-1)×0.4=4.8m在进料板上方开一人孔,其高度为0.8m故精馏塔的有效高度为Z= Z 精+ Z 提+0.8=2.8+4.8+0.8=8.4m4.5.塔板主要工艺尺寸的计算4.5.1溢流装置计算因塔径D =1.8m ,可选用单溢流弓形降液管,采用凹形受液盘。