板料成形CAE分析
板料成形性能及CAE分析课程设计
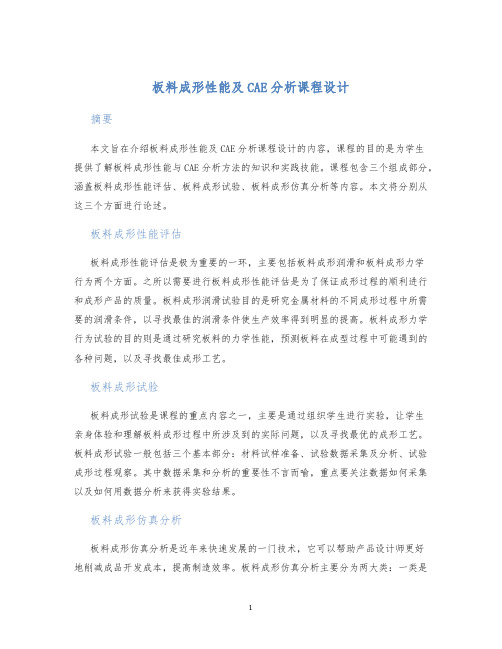
板料成形性能及CAE分析课程设计摘要本文旨在介绍板料成形性能及CAE分析课程设计的内容,课程的目的是为学生提供了解板料成形性能与CAE分析方法的知识和实践技能。
课程包含三个组成部分,涵盖板料成形性能评估、板料成形试验、板料成形仿真分析等内容。
本文将分别从这三个方面进行论述。
板料成形性能评估板料成形性能评估是极为重要的一环,主要包括板料成形润滑和板料成形力学行为两个方面。
之所以需要进行板料成形性能评估是为了保证成形过程的顺利进行和成形产品的质量。
板料成形润滑试验目的是研究金属材料的不同成形过程中所需要的润滑条件,以寻找最佳的润滑条件使生产效率得到明显的提高。
板料成形力学行为试验的目的则是通过研究板料的力学性能,预测板料在成型过程中可能遇到的各种问题,以及寻找最佳成形工艺。
板料成形试验板料成形试验是课程的重点内容之一,主要是通过组织学生进行实验,让学生亲身体验和理解板料成形过程中所涉及到的实际问题,以及寻找最优的成形工艺。
板料成形试验一般包括三个基本部分:材料试样准备、试验数据采集及分析、试验成形过程观察。
其中数据采集和分析的重要性不言而喻,重点要关注数据如何采集以及如何用数据分析来获得实验结果。
板料成形仿真分析板料成形仿真分析是近年来快速发展的一门技术,它可以帮助产品设计师更好地削减成品开发成本,提高制造效率。
板料成形仿真分析主要分为两大类:一类是基于有限元程序的仿真分析,另一类是基于计算机辅助成形(CAE)的仿真分析。
因为仿真分析非常便捷、可重复、稳健,其应用范围得到了快速的发展,从而使得仿真分析在现代工业领域中应用越来越广泛。
总结通过本文对板料成形性能及CAE分析课程设的介绍,可以看出课程包含了板料成形性能评估、板料成形试验、板料成形仿真分析等三部分内容。
课程深入浅出,通过试验和仿真分析,使学生可以在实践中了解板料成形性能及CAE的应用。
“降低制造成本,提高制造效率”是现代制造的关键词,而板料成形性能评估和CAE分析正是帮助企业企业在老的生产模式上实现升级换代。
板料成型CAE在拉深工艺中的应用

讨了 CAE 仿真分析整个过程及其出现的问题, 做出了对应的 工艺参数调整, 实现了零件拉深工艺的优化, 从而节省大量 时间, 提高设计的可靠性。
通过零件的 CAE 仿真分析, 可以预计覆盖件在成形时所 需的各项参数, 较之实际采用压力机进行冲压试验具有其难 以比拟的优越性。目前的 C A E 技术不能完全替代实际冲压试 验过程, CAE 仿真分析技术在不断完善, 随着计算机技术和 有限元理论的进一步发展, CAE 技术将能够更迅速、更真实 地反应冲模成形过程中的各种问题, 从而能够更好地指导生 产实践。
[关键词]板料成型 C A E 分析; 车身模具; 计算机数值模拟; 参数优化
一、引言
板料成形是利用模具对金属板料的冲压加工, 获得质量 轻 、表 面 光 滑 , 造 型 美 观 的 冲 压 件 , 具 有 节 省 材 料 , 效 率 高 和 低 成 本 等 优 点 。在 汽 车 、航 空 模 具 等 行 业 中 占 据 着 重 要 地 位 。 由于板料成形是利用板材的变形得到所需的形状的, 长期以 来, 困扰广大模具设计人员的主要问题就是较长的模具开发 设计周期, 特别是对于复杂的板料成形零件无法准确预测成 形的结果, 难预防缺陷的产生, 只能通过经验或类似零件的 现有工艺资料, 通过不断的试模、修模才能成功。某些特殊复 杂的板料成形零件甚至制约了整个产品的开发进度。
板料成形性CAE结果分析 2005 10

板料成形性CAE分析报告标准CAE分析的目标是得到可接受的模拟结果;例如成形件无破裂,没有明显的起皱,以得到生产现场试模时减小调模工作量,提高制件质量的效果。
CAE结果分析必须采用或说明以下模拟条件(如特定客户有特定要求则以客户要求为准);●拉延模模面设计等级(设计依据,实型依据还是加工依据)●成形模拟使用的材料和生产实际所用的材料及其机械性能●坯料尺寸的控制(以拉延后坯料轮廓不超过第一道拉延筋中心线为准)●摩擦条件u=0.15,采用更高的摩擦系数时也应该至少保证成型性至少有10%的成型裕度●计算精度(薄板料t<1.2mm, layer=5,厚板料t≥1.2mm layer=7),外板fine,内板standard●压边力(注意依赖AUTOFORM计算压边力不准确,需要通过经验确定或DYNAFORM计算)●总成型力(单动--凸模最大受力+压边力,双动—凸模,计算结果准确度不够,需要通过经验公式确认)●单动和双动的必须按照实际冲压条件,压边圈最小行程(确定是否有凸模顶料)CAE结果分析报告中必须包括以下内容;●重力作用下板料的变形情况(仅压边圈曲度过大时需要,方便板料定位设计)●压边圈闭合后的板料变形情况,AUTOFORM计算应选择合适的算法drawingor binder wrap(incremental step=8)以保证压边圈闭合后情况符合现场(仅压料面曲率过大时需要)●成型后的坯料,带修边线,拉延筋和初始坯料,并标明各个区域的流入量inflow。
●成型性Formability●板料减薄率Thinning(必须严格控制减薄率,所有减薄率小于20%的区域都必须设法改善,厚度增加必须小于0.1mm)●成形到底前5mm板料的起皱情况,不能有明显的起皱现象●起皱趋势Wrinkling Criterion的判断压边圈小于0.05,成型区域小于0.02,平面区域小于0.001(外板),内板小于(0.005)。
基于“板料成形CADCAE4”课程项目式混合教学改革的探索

基于“板料成形CAD/CAE4”课程项目式混合教学改革的探索一、前言板料成形CAD/CAE课程是材料成形与控制工程专业的一门重要的专业核心课,在工程中能够缩短模具设计周期、节省成本,是制造业数字化、智能化的必需技术,也是当前大学生参与后续模具课程设计、毕业设计、各类创新大赛、互联网+大赛必须掌握的一项关键技术。
熟练操作CAD/CAE软件,已经成为工程设计人员不可或缺的基本能力[1]。
当前,此类课程的教学内容和方式主要以建模和有限元理论为基础。
结合CAE软件功能教学,学生依照教学步骤完成示范教学模型的建构和CAE分析。
通过多年教学发现,在此教学模式下,学生严重缺乏创新思维和创新能力。
此外,当前教学还面临学时有限、生师比高、实践教学欠缺、学习兴趣不高、创新能力不足等长期困扰教学的难题。
当前,世界范围内,新一轮的科技革命和产业变革以及席卷全球的新经济的蓬勃发展,对工程教育的改革和发展提出了新的挑战[2]。
国内工程认证和新工科建设又对教学质量和人才培养提出了更高的要求[3]。
课程现有教学内容及方法等难以体现成果导向、以学生为中心、持续改进的基本理念。
为适应这些需求,培养目标、教学内容和教学方式都需要转变,要更加注重提高学生的学习兴趣、学习参与度、学习效果和创新能力培养[4,5]。
为适应时代变化以及国家对高校教学提出的新挑战和新要求,本文针对材料成型与控制工程专业的CAD/CAE系列课程进行了教学改革探索。
二、针对项目式教学的内容再组织(一)基于项目式教学的内容重构当前,课程教材基本按照成形理论、成形工艺特点、有限元理论、CAE分析技术等内容编写,没有按照创新能力培养的特点对课程教学内容进行系统、深入研究。
成形理论和成形工艺相关知识大多已在“金属塑形成形原理”“材料科学基础”和“冲压模具设计”等课程内讲解;有限元理论部分知识过于枯燥,且需要投入较多的教学时间。
这导致CAE分析部分内容只能简单地作为一门计算机刘华,刘红生,尤芳怡(华侨大学机电及自动化学院,福建厦门361021)[摘要]针对当前板料成形CAD/CAE课程面临的主要问题及挑战,对专业课程进行了改革。
板料成形性能及CAE分析

板料成形性能及CAE分析文献综述引言随着强度的提高,高强度钢板塑性变差、成形难度增加。
对典型高强度钢板,如DP 钢、TRIP 钢和BH 钢等在汽车上的应用情况进行介绍,介绍了目前处在实验测试阶段的TWIP钢,具有许多优良的性能,只是投入生产中还存在一些尚待解决的问题。
对高强度钢板冲压生产时成形性差、回弹严重,以及冲模受力恶劣等常见问题进行了分析,最后对高强度钢板冲压成形性能研究现状和回弹影响因素进行了总结。
结果表明,高强度钢板成形性随材料、模具和工艺参数变化而波动,所以须综合研究三者的影响规律,从而提高高强度钢板的成形性能。
1 高强度钢板在汽车上的应用情况高强度钢板的拉伸强度一般在350MPa 以上,它不但具有较高的拉伸强度,还有较高的屈服点,具有高的减重潜力、高的碰撞吸收能、高的成形性和低的平面各向异性等优点,在汽车上得到了广泛的应用[1]。
高强度钢板最初主要用于车身的前保险杠和车门抗侧撞梁。
近年来,随着高强度钢板的研制和开发,其成形性、焊接性、疲劳强度和外观质量都有所提高,现在高强度钢板已被广泛用来代替普通钢板制造车身的结构构件和板件[2]。
1. 1 双相钢( DP 钢)DP 钢是由低碳钢或低碳微合金钢经两相区热处理或控轧控冷而得到,其显微组织主要为铁素体和马氏体,马氏体以岛状弥散分布在铁素体机体上,DP 钢的显微组织示意如图1 所示[3]。
软的铁素体赋予DP钢较低的屈强比、较大的延伸率,具有优良的塑性; 而硬的马氏体则赋予其高的强度。
DP 钢的强度主要由硬的马氏体相的比例来决定,其变化范围为5% ~20%,随着马氏体的含量增加,强度线性增加,强度范围为500 ~ 1 200MPa。
目前大量使用的有DP590、DP780,热镀锌合金化DP980 的研发工作正在进行中[4]。
DP 钢具有低屈强比、高加工硬化指数、高烘烤硬化性能、无屈服延伸和室温时效等特点,一般用于需要高强度、高的抗碰撞吸收且也有一定成形要求的汽车零件,如车轮、保险杠、悬挂系统及其加强件等。
板料成形CAE技术及应用
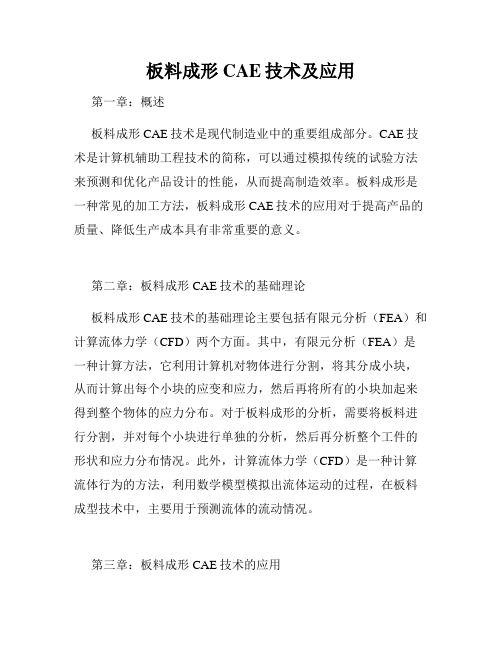
板料成形CAE技术及应用第一章:概述板料成形CAE技术是现代制造业中的重要组成部分。
CAE技术是计算机辅助工程技术的简称,可以通过模拟传统的试验方法来预测和优化产品设计的性能,从而提高制造效率。
板料成形是一种常见的加工方法,板料成形CAE技术的应用对于提高产品的质量、降低生产成本具有非常重要的意义。
第二章:板料成形CAE技术的基础理论板料成形CAE技术的基础理论主要包括有限元分析(FEA)和计算流体力学(CFD)两个方面。
其中,有限元分析(FEA)是一种计算方法,它利用计算机对物体进行分割,将其分成小块,从而计算出每个小块的应变和应力,然后再将所有的小块加起来得到整个物体的应力分布。
对于板料成形的分析,需要将板料进行分割,并对每个小块进行单独的分析,然后再分析整个工件的形状和应力分布情况。
此外,计算流体力学(CFD)是一种计算流体行为的方法,利用数学模型模拟出流体运动的过程,在板料成型技术中,主要用于预测流体的流动情况。
第三章:板料成形CAE技术的应用1. 模拟板料成形过程板料成形CAE技术可以模拟板料的成形过程,包括板料弯曲、深冲和拉伸等工艺。
通过模拟模具的运动和板料的变形,可以预测板料成形过程中的应力分布、变形和应变等物理量,进而确定合适的加工参数和模具形状,从而达到优化加工效果的目的。
2. 优化模具设计板料成形CAE技术可以预测模具中的应力分布以及板料成形后的形状,可以优化模具的设计,提高模具的使用寿命和板料成形的质量。
3. 优化板料成形过程中的加工参数板料成形CAE技术可以根据模拟出的加工过程来优化板料成形过程中的加工参数,如板料的温度、压力、速度等,以达到最佳的加工效果,并提高板料成形的质量和效率。
第四章:发展趋势随着计算机技术和数值模拟技术的发展,板料成形CAE技术将会迎来新的发展机遇和挑战。
未来,板料成形CAE技术将不断提高计算精度和效率,同时也将不断拓展其应用范围。
例如,在高腐蚀、高温、高压等极端环境下的板料成形技术中,板料成形CAE技术也将扮演着越来越重要的角色。
第十一章材料成形CAD/CAE/CAM的实际应用1

铸造工艺课程设计软件
华铸CAD
(二)三维工艺CAD
二维工艺CAD系统虽然可以帮助技术人员甩 掉红蓝铅笔、绘图板,并且习惯于纸面介质 绘制工艺的工程师也可以较快适应CAD方式 的电子绘图。 但是二维工艺CAD的致命缺陷正是它的二维 描述方式,不能为后续的CAE、CAM乃至 RPM提供必要的三维信息。 如果说甩红蓝铅笔、甩绘图板需要二维工艺 CAD的话,那么实现CAD/CAE/CAM一体 化就必须要求铸造工艺CAD的立体化。因此 三维工艺CAD是铸造工艺计算机辅助设计的 必然发展方向。
液态成型工艺CAD根本功能是应能完成工 艺基本要素的设计与绘制(造型)任务,这些 要素包括浇注系统、冒口系统、分型面、 加工余量、起摸斜度、砂芯及芯头、冷铁、 不铸孔、铸造圆角、工艺卡等等,可以顺 利地完成铸造工艺设计。
因为铸造行业的特殊性,液态成型工艺的 标准没有统一,不同国家、不同行业、不 同工厂所采用的标准和习惯都不一致。这 一现状导致了铸造工艺CAD系统的开发极 其困难,普适性问题至今无法彻底解决。 因此,与液态成型CAE、 CAM比较,工艺 CAD发展相对滞后,在实际生产中的应用 还很少。
摆脱这一困境的途径主要有两条: 一是加紧制定铸造行业的技术标准,规范工艺设 计的各个环节; 二是借助于迅速发展的计算机技术,搭建强大、 灵活的铸造工艺CAD系统框架,利用此框架可以 迅速、方便地生成适合于某一行业、某个工厂的 铸造工艺CAD。 就目前而言,第一条途径困难重重,很难制定一 个大家都能接受、可以迅速推广应用的技术标准。 而第二条路线虽然困难也很大,但随着计算机软、 硬件及信息技术的快速进步,会逐步克服掉各种 障碍,使铸造工艺的设计实现“无图纸”化、计 算机化甚至远程网络化。
2、塑性成形CAE 主要是利用有限元技术对塑性成形的应力、 应变进行模拟分析,预测应力集中、开裂、 变形等缺陷。对于热锻过程的模拟还存在着 传热过程和再结晶过程的模拟分析。 3、塑性成形CAM 模具对于塑性成形而言具有非常重要的地位, 因此塑性成形CAM技术主要是研究如何利用 数控、电火花等加工手段,快速、精确地制 造出塑性成形用模具。
cae分析报告

VACUUM VESSEL END FLANGE CAE分析报告产品名称:VACUUM VESSEL END FLANGE分析软件:Autoform4.2分析材质:14301实质材质:304L料厚:3mm成形类型:拉延毛坯尺寸:φ2010产品及工艺补充形状:产品成形性评估分析结果(Draw)板料变薄量图结论:由于现有的材料库没有304L,现用14301进行替代模拟,分析结论本零件拉延基本成功。
THERMAL SHIELD END FLANGE CAE分析报告产品名称:THERMAL SHIELD END FLANGE分析软件:Autoform4.2分析材质:6016 T4实质材质:6061 T6料厚:6.35mm成形类型:拉延毛坯尺寸:φ2124产品及工艺补充形状:产品成形性评估分析结果(Draw)板料变薄量图结论:由于现有的材料库没有6061-T6,现用6016-T4进行替代模拟,分析结论本零件拉延基本成功。
下面是赠送的团队管理名言学习,不需要的朋友可以编辑删除谢谢1、沟通是管理的浓缩。
2、管理被人们称之为是一门综合艺术--“综合”是因为管理涉及基本原理、自我认知、智慧和领导力;“艺术”是因为管理是实践和应用。
3、管理得好的工厂,总是单调乏味,没有任何激动人心的事件发生。
4、管理工作中最重要的是:人正确的事,而不是正确的做事。
5、管理就是沟通、沟通再沟通。
6、管理就是界定企业的使命,并激励和组织人力资源去实现这个使命。
界定使命是企业家的任务,而激励与组织人力资源是领导力的范畴,二者的结合就是管理。
7、管理是一种实践,其本质不在于“知”而在于“行”;其验证不在于逻辑,而在于成果;其唯一权威就是成就。
8、管理者的最基本能力:有效沟通。
9、合作是一切团队繁荣的根本。
10、将合适的人请上车,不合适的人请下车。
11、领导不是某个人坐在马上指挥他的部队,而是通过别人的成功来获得自己的成功。
12、企业的成功靠团队,而不是靠个人。
- 1、下载文档前请自行甄别文档内容的完整性,平台不提供额外的编辑、内容补充、找答案等附加服务。
- 2、"仅部分预览"的文档,不可在线预览部分如存在完整性等问题,可反馈申请退款(可完整预览的文档不适用该条件!)。
- 3、如文档侵犯您的权益,请联系客服反馈,我们会尽快为您处理(人工客服工作时间:9:00-18:30)。
板料成形CAE分析
实验报告
班级:
学号:
姓名:
板料成形CAE分析
一、实验目的和要求:
通过本实验的教学,使学生基本掌握有限元技术在板料塑性成形领域的应用情况,拓宽学生的知识面,开阔视野,使学生对塑性成形过程的数值模拟技术有深刻的理解,预测板料弯曲成形的性能。
二、教学基本要求:
学会使用Dynaform数值模拟软件进行板料弯曲成形过程的仿真模拟,对模拟结果具有一定的分析和处理能力。
三、实验内容提要:
掌握前处理的关键参数设置,如零件定义、网格划分、模型检查、工具定义、坯料定义、工具定位和移动、工具动画、运行分析。
了解后处理模块对模拟结果的分析,如读入d3plot 文件、动画显示变形和生成动画文件、成形极限图分析、坯料厚度变化分析等。
四、实验步骤
1、导入零件模型,保存文件
打开下拉菜单File->Import,如图2所示,在F:\dynaform\BLANK_CAE目录下分别导入文件punch.igs,binder.igs,die.igs和blank.igs。
图1 导入文件窗口
3、更改零件层名
打开下拉菜单Parts->Edit,对应不同的零件更改层名,改好层名后保存文件。
图2 修改层名窗口
4、进行网格划分
以blinder为例进行说明。
(1)、点击,只选择binder1(红色),点击OK退出。
图3
(2)、选择Preprocess—>Element进入如图3界面。
选择,在surf mesh中将max size 改为5.
图4 图5
(3)、依次选select surfaces—>displayed surf-->0k-->apply,然后依次退出各个页面。
网格化后的零件如图6所示。
图6网格化后的零件
4、检查工具。
仍然以binder为例。
(1)、点击preprocess—>model check,出现如图7界面。
图7
(2)、点击,选择cursor pick part,点击工具的小格单元,出现如图8界面。
图8
(3)、如果方向正确,则选择yes,否则选择no。
按这种方式检查其他的工具(die punch)。
5、定义工具和坯料材料
(1)定义工具打开Tools-->Define Tools菜单,进入工具定义窗口(如图9所示)。
分别定义凹模(Die),凸模(Punch),压边圈(Binder)。
在定义Punch 和Binder 的时,还需要输入凸模行程和压边力。
本实验中,定义凸模速度为2000,设定凸模行程为100,压边
力设1E6,方法如图9,图10,图11所示。
图9定义凹模过程
图10 定义凸模行程
图11 定义压边力
(2)定义坯料打开Tools-->Define Blank菜单,进入坯料定义界面,点击Add,添加坯料,点击OK,成功添加坯料几何模型,如图12所示。
图12 定义坯料
定义坯料时,还需要定义坯料的材料和属性,如图12(c)所示,分别点击Material和Property,进入材料定义界面和属性定义界面。
在本实验中,选择不锈钢材料BH250,如图13,图14所示。
属性的定义如图15所示。
图13 定义坯料材料
图14 材料库
图15 定义坯料属性
6、移动工具到合适位置。
X负方向移动凹模70mm,Y正方向移动凸模100.5mm。
点击tools—>position tools-->move tool.
图16移动凹模与凸模、
移动之后如图17所示
图17移动之后的模具与工件
6、模具定位
打开Tools-->Position Tools→Auto Position菜单,进入工具定位窗口,在Master Tools 栏中,选中Blank,在Slave Tools 栏中,同时选中 Punch,Binder,Die。
在Method 栏选中Double Side Check,在Deriction栏中选中Z方向,点击Apply完成工具定位。
图18 工具定位对话框图19 求解参数设置对话框
7、成形仿真计算
点击Analysis→LS-DYNA 菜单,进入求解模块,如图19所示。
将Analysis Type 选择为Full Run Dyna 模式,点击OK进行仿真求解计算,求解计算过程如图20所示。
图20求解过程
8、后处理
求解完成后,点击主菜单上的PostProcess,进入后处理,以观察仿真成形结果。
点击后处理窗口中的File,打开d3plot文件。
图19 打开d3plot 文件窗口
点击按钮,将Punch,Die,Binder零件层关闭,只保留Blank零件层。
点击显示成形极限曲线,在Frames栏中,选定Single Frame,用鼠标点击不同的帧,可以看到板料在不同变形时刻的变形状态。
如图20所示,为第中间某帧时板料的变形状态。
图20 后处理界面
9、分析。
由图知材料起皱,分析可能是压边力太大导致,改小了压边力以后。
图21修改后的后处理界面
图22 第16步的厚度分析。