板料成型技术中的拉深筋研究
板料成型CAE在拉深工艺中的应用

讨了 CAE 仿真分析整个过程及其出现的问题, 做出了对应的 工艺参数调整, 实现了零件拉深工艺的优化, 从而节省大量 时间, 提高设计的可靠性。
通过零件的 CAE 仿真分析, 可以预计覆盖件在成形时所 需的各项参数, 较之实际采用压力机进行冲压试验具有其难 以比拟的优越性。目前的 C A E 技术不能完全替代实际冲压试 验过程, CAE 仿真分析技术在不断完善, 随着计算机技术和 有限元理论的进一步发展, CAE 技术将能够更迅速、更真实 地反应冲模成形过程中的各种问题, 从而能够更好地指导生 产实践。
[关键词]板料成型 C A E 分析; 车身模具; 计算机数值模拟; 参数优化
一、引言
板料成形是利用模具对金属板料的冲压加工, 获得质量 轻 、表 面 光 滑 , 造 型 美 观 的 冲 压 件 , 具 有 节 省 材 料 , 效 率 高 和 低 成 本 等 优 点 。在 汽 车 、航 空 模 具 等 行 业 中 占 据 着 重 要 地 位 。 由于板料成形是利用板材的变形得到所需的形状的, 长期以 来, 困扰广大模具设计人员的主要问题就是较长的模具开发 设计周期, 特别是对于复杂的板料成形零件无法准确预测成 形的结果, 难预防缺陷的产生, 只能通过经验或类似零件的 现有工艺资料, 通过不断的试模、修模才能成功。某些特殊复 杂的板料成形零件甚至制约了整个产品的开发进度。
板料拉深分析报告1
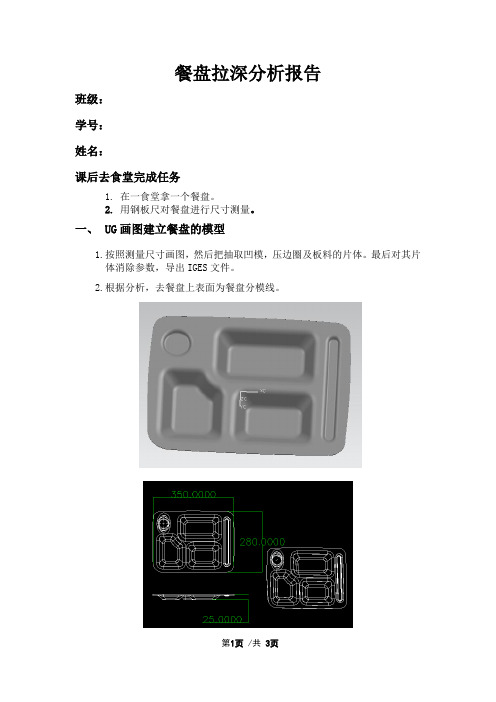
餐盘拉深分析报告
班级:
学号:
姓名:
课后去食堂完成任务
1.在一食堂拿一个餐盘。
2.用钢板尺对餐盘进行尺寸测量。
一、 UG画图建立餐盘的模型
1.按照测量尺寸画图,然后把抽取凹模,压边圈及板料的片体。
最后对其片
体消除参数,导出IGES文件。
2.根据分析,去餐盘上表面为餐盘分模线。
三、用DYNAFORM5.7软件对餐盘拉深成形模拟、采用自动设置的方式进行前置处理
1.打开DYNAFORM5.7软件。
2.导入UG造行的餐盘片体文件。
3.编辑文件名
4.零件单元网格划分
5.零件网格检查
6.定义凸模零件“Punch”
7.创建压边圈“BINDER”
8.自动设置(单动)
四、进行后处理的查看
点击DYNAFORM软件主菜单栏的“PostProcess”命令,进入后处理模块“eta/Post”。
进入后处理主页面后打开后缀为“.d3plot”的文件,只显示“Blank”对文件进行动画演示,分别选择PLD图、料厚分布图、减薄率分布图对其结果进行查看。
对拉深工艺过程的研究及探讨
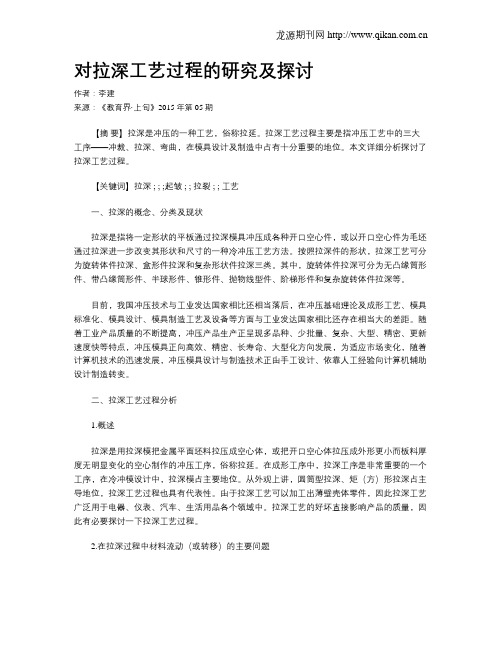
对拉深工艺过程的研究及探讨作者:李建来源:《教育界·上旬》2015年第05期【摘要】拉深是冲压的一种工艺,俗称拉延。
拉深工艺过程主要是指冲压工艺中的三大工序——冲裁、拉深、弯曲,在模具设计及制造中占有十分重要的地位。
本文详细分析探讨了拉深工艺过程。
【关键词】拉深 ; ; ;起皱 ; ; 拉裂 ; ; 工艺一、拉深的概念、分类及现状拉深是指将一定形状的平板通过拉深模具冲压成各种开口空心件,或以开口空心件为毛坯通过拉深进一步改变其形状和尺寸的一种冷冲压工艺方法。
按照拉深件的形状,拉深工艺可分为旋转体件拉深、盒形件拉深和复杂形状件拉深三类。
其中,旋转体件拉深可分为无凸缘筒形件、带凸缘筒形件、半球形件、锥形件、抛物线型件、阶梯形件和复杂旋转体件拉深等。
目前,我国冲压技术与工业发达国家相比还相当落后,在冲压基础理论及成形工艺、模具标准化、模具设计、模具制造工艺及设备等方面与工业发达国家相比还存在相当大的差距。
随着工业产品质量的不断提高,冲压产品生产正呈现多品种、少批量、复杂、大型、精密、更新速度快等特点,冲压模具正向高效、精密、长寿命、大型化方向发展,为适应市场变化,随着计算机技术的迅速发展,冲压模具设计与制造技术正由手工设计、依靠人工经验向计算机辅助设计制造转变。
二、拉深工艺过程分析1.概述拉深是用拉深模把金属平面坯料拉压成空心体,或把开口空心体拉压成外形更小而板料厚度无明显变化的空心制作的冲压工序,俗称拉延。
在成形工序中,拉深工序是非常重要的一个工序,在冷冲模设计中,拉深模占主要地位。
从外观上讲,圆筒型拉深、矩(方)形拉深占主导地位,拉深工艺过程也具有代表性。
由于拉深工艺可以加工出薄壁壳体零件,因此拉深工艺广泛用于电器、仪表、汽车、生活用品各个领域中。
拉深工艺的好坏直接影响产品的质量,因此有必要探讨一下拉深工艺过程。
2.在拉深过程中材料流动(或转移)的主要问题我们可以从一个易拉罐试验做起。
易拉罐是由圆盘形毛坯料在拉深模作用下基本成形,我们暂不谈整个拉深变形过程,反向思维,从另一个角度考虑一下。
板料冲裁拉深成形工艺实验

板料冲裁、拉深成形工艺试验1 试验目(1)建立板料冲裁、拉深工艺感性认识, 深化板料冲裁、拉深成形规律与机理了解;(2)掌握落料件尺寸与模具尺寸对应关系、落料件断面特征;(3)掌握拉深成形时金属流动规律;(4)学习并掌握板料冲裁、拉深成形工艺试验操作方法。
2试验内容(1)完成落料单工序冲压分离工艺试验;(2)完成拉深单工序冲压成形工艺试验。
3试验仪器设备及试样3.1 试验仪器设备液压机、落料模、拉深模、游标卡尺、钢皮直尺、划规、量角器(自备)、工具显微镜等。
3.2 试样坯料: 08钢条料, 厚度0.5mm。
4试验原理4.1冲裁工艺试验利用模具使板料沿着一定轮廓形状产生分离一个冲压工序。
(1)冲裁件尺寸精度尺寸精度: 指冲裁件实际尺寸与基础尺寸差值, 差值越小则精度越高。
这个差值关键是在一定模具制造精度这个前提下, 冲裁件相对于凸、凹模尺寸偏差。
冲裁件相对于凸、凹模尺寸偏差, 关键是工件脱离模具时, 材料在冲裁中所受挤压变形、纤维伸长、穹弯等都要产生弹性恢复而造成。
偏差值可能是正, 也可能是负。
通常规律如图1所表示。
a)黄铜t=4mm; b)15钢t=3.5mm图1 间隙对冲裁件精度影响(2)冲裁件断面特征冲裁件断面通常由圆角带、光亮带、撕裂带和毛刺组织, 如图2所表示。
a-圆角带;b-光亮带;c-断裂带;d-毛刺图2 冲裁件断面特征4.2拉深工艺试验利用拉深模在压力机压力作用下, 将平板坯料或空心工序件制成开口空心零件加工方法。
(1)金属流动规律拉深前在毛坯上画部分由等间距同心圆和等角度辐射线组成网格(如图3所表示), 然后进行拉深, 经过比较拉深前后网格改变来比较材料流动情况。
图3 拉深网格改变拉深后筒底部网格改变不显著, 而侧壁上网格改变很大, 拉深前等间距同心圆, 拉深后变成了与筒底平行不等距离水平圆周线, 愈到口部圆周线间距愈大;拉深前等角度辐射线拉深后变成了等距离、相互平行且垂直于底部平行线;原来扇形网格拉深后在工件侧壁变成了等宽度矩形, 离底部愈远, 矩形高度愈大。
冲压及钣金件制造中的拉深问题研究
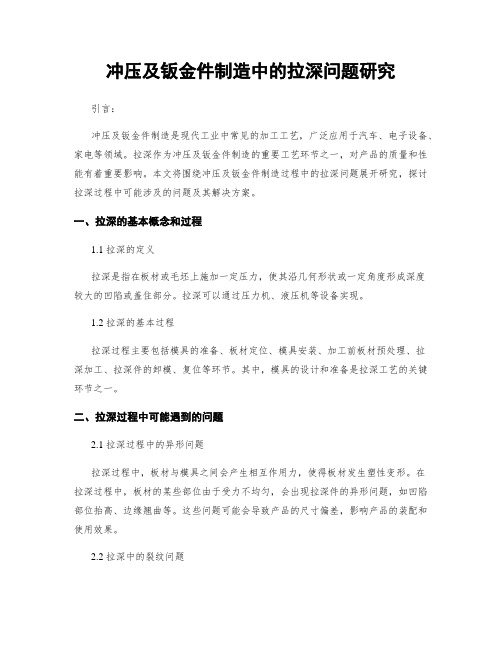
冲压及钣金件制造中的拉深问题研究引言:冲压及钣金件制造是现代工业中常见的加工工艺,广泛应用于汽车、电子设备、家电等领域。
拉深作为冲压及钣金件制造的重要工艺环节之一,对产品的质量和性能有着重要影响。
本文将围绕冲压及钣金件制造过程中的拉深问题展开研究,探讨拉深过程中可能涉及的问题及其解决方案。
一、拉深的基本概念和过程1.1 拉深的定义拉深是指在板材或毛坯上施加一定压力,使其沿几何形状或一定角度形成深度较大的凹陷或盖住部分。
拉深可以通过压力机、液压机等设备实现。
1.2 拉深的基本过程拉深过程主要包括模具的准备、板材定位、模具安装、加工前板材预处理、拉深加工、拉深件的卸模、复位等环节。
其中,模具的设计和准备是拉深工艺的关键环节之一。
二、拉深过程中可能遇到的问题2.1 拉深过程中的异形问题拉深过程中,板材与模具之间会产生相互作用力,使得板材发生塑性变形。
在拉深过程中,板材的某些部位由于受力不均匀,会出现拉深件的异形问题,如凹陷部位抬高、边缘翘曲等。
这些问题可能会导致产品的尺寸偏差,影响产品的装配和使用效果。
2.2 拉深中的裂纹问题拉深过程中,板材受到的局部应变较大,容易引发板材的应力集中,导致裂纹的产生。
裂纹问题严重影响拉深件的质量,甚至导致拉深件的报废。
2.3 拉深过程中的材料流动问题拉深过程中,板材会发生塑性变形,材料会在模具的作用下流动。
材料流动的不均匀会导致拉深件的厚度不均匀,造成产品质量问题。
三、解决拉深问题的方法与技术3.1 模具设计优化模具的设计优化可以在一定程度上解决拉深过程中可能出现的问题。
通过合理设计模具的结构和形状,可以减少拉深件因受力不均匀而产生的异形问题。
此外,模具的表面处理和涂层选择也能减少板材和模具之间的摩擦,减少拉深过程中的摩擦应力,从而减少模具对板材的损伤。
3.2 材料的选择和预处理选择合适的板材材料可以减少拉深过程中的裂纹问题。
不同材料的机械性能和变形能力不同,因此在拉深过程中应选择合适的材料,根据拉深件的要求进行预处理,如退火、淬火等,以提高材料的塑性变形能力。
基于数值模拟的盒形件拉深成形变拉深筋技术研究
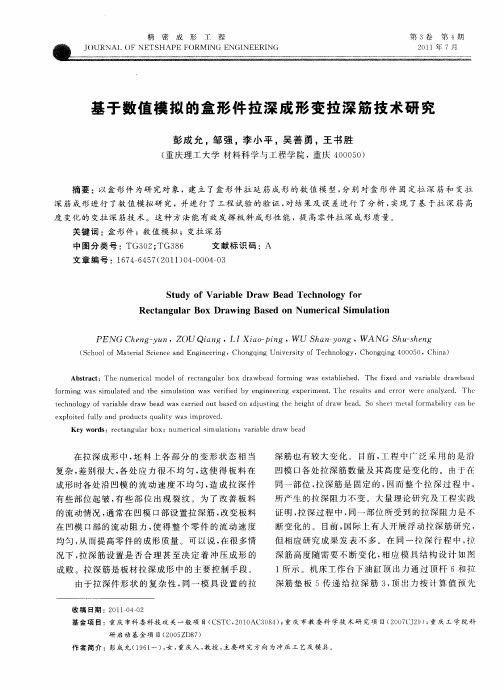
PENG e g y n,ZOU a g ,LIX io p n , U h n y n ,WA NG h —h n Ch n — u Qi n a — ig W S a—og S use g
( h lo a e ilSce ea Sc oo fM t ra inc nd Engie rng,Chon i ni r iy o c olgy,Ch gq n 0 nei gqng U ve st fTe hn o on i g 4 005 0, Ch n i a)
( 庆理 工大学 材 料科 学与工 程学 院 ,重庆 4 0 5 ) 重 0 0 0
摘要 :以盒形 件 为研 究对 象,建 立 了盒形 件拉 延 筋 成 形 的数 值模 型 , 别 对盒 形件 固 定拉 深 筋 和 变拉 分
深 筋 成 形 进 行 了数 值 模 拟 研 究 ,并 进 行 了 工程 试 验 的 验 证 , 结 果 及 误 差 进 行 了分 析 , 现 了基 于拉 深 筋 高 对 实
在 拉深 成形 中, 料上 各 部 分 的变 形 状 态 相 当 坯 复杂 , 差别 很大 , 处应 力 很 不 均匀 , 各 这使 得 板 料 在 成形 时各处 沿 凹模 的 流动 速 度 不 均匀 , 造成 拉 深 件
深筋 也有 较大 变化 。 目前 , 工程 中广 泛 采用 的是 沿 凹模 口各 处拉 深筋数 量及 其高 度是 变化 的 。由于在 同一 部位 , 深筋 是 固定 的 , 拉 因而 整 个 拉深 过 程 中 ,
汽车覆盖件拉深成形拉深筋作用仿真研究
汽车覆盖件拉深成形拉深筋作用仿真研究韩建保 云志刚 韩双庆( 北京理工大学机械与车辆工程学院 ,北京 100081)张小兵( 华北工学院 ,太原 030051)[ 摘要 ] 以韩国现代某型轿车前挡泥板拉深成形为例 ,利用有限元软件 L S - D YNA 的动态显式算法 ,仿真研究了汽车覆盖件拉深成形过程中 ,拉深筋对薄板成形质量的影响 ,其中应用线单元等效拉深筋的功能 。
研究结果 表明 ,在模具上设置拉深筋能够明显改善薄板的塑性流动质量 ,抑制发生起皱缺陷 。
叙词 :薄板成形 ,拉深筋 ,动态显式算法A Si m ulatio n St udy o n t he Functio n of Drawbead i nDrawi n g Fo r mi ng of Auto 2bo dy PanelsH an Jian b ao Yun Zhigang & H an ShuangqingS c hool of M echa n ical a n d A ut om o t i ve En g i neeri n g , Bei j i n g I nst i t ute of Tech n ology , Bei j i n g 100081Z hang XiaobingN ort h Chi n a U ni versi t y of S c ience a n d Tech n ology , T a i y u a n 030051AbstractTaking t h e f ro n t fender of a Hyundai ’s car as an exa m ple , a simulati o n st u dy o n t h e effect ofdraw b eads o n t h e fo r m ing qualit y of auto 2bo d y panel is carried o u t using t h e dynamic e xplicit algo r it h m in F E A co d e L S - D YNA . The result s show t h at t h e draw b eads o n blank 2holder o r die can mar kedly im p rove t h e plastic fl ow of sheet metal and to p r event t h e occurring of w r inkling defect .K ey w ords :Sheet m etal f or ming , Dra wbea d , Dyna mic exp l i c i t algorithm薄板冲压成形过程的计算机数字模拟 ,可以大大缩短调试模具所需时间 ,提高模具的设计效率 。
实验一 拉深实验
实验一拉深实验一、实验目的要求。
1.了解拉深过程中拉深系数(或毛坯直径)、润滑、压边圈、凸凹模间隙、拉深高度等因素对拉深件质量的影响。
2.了解液压机的工作原理与基本操作。
二、实验原理板料加工阶段需要的加工的性能叫做冲压性,一般包括冲剪性、成形性、和定形性三个方面,其中成形性是板材适应各种加工的能力,但多数板料零件都需要成形工序,是平板毛料变成一定形状的零件。
板料成形方法很多,所以研究时可对成形方法进行分类,一般按材料再成形过程中所承受的变形方式来分类,可分为:弯曲变形、压延变形、胀形(还包括拉形、局部成形)、拉深成形(包括单向拉深、翻边、凹弧翻边等)、收缩变型(包括收边、管子缩颈、受口、凸翻边等)、体积成形(包括旋薄、变薄压延、喷丸成形、压印等)。
一般所谓的板料的成形性中最为重要的是成形极限的大小,板料成形过程中存在两种成形极限,一是起皱,另一个是破裂。
成形极限可以用“发生起皱前,材料能承受的最大变形程度来表示,可理解为板料在发生破裂前能够得到的变形程度,也就是普通所谓的“塑性”。
由于板料成形性能随变形程度、牌号、成形方式、生产方式等因素影响,所以评定一种板料成形性能的指数既要把各种主要因素考虑进去又要尽量少。
板料的成形性能,目前的主要研究是拉深和胀形两种方式。
对金属薄板冲压成形时,可对某些材料特性或工艺参数提出要求,它们统称为特定成形性能指标评定金属薄板的成形等级时,可对某种模拟的成形性能指标提出要求确定的试验有:a.胀形性能指标;b.“拉深+胀形”复合成形性能;c.拉深性能指标。
三、实验仪器与设备试验冲压模一套、拉深模一套、液压机一台、游标卡尺、棉砂、1mm08Al条料等。
四、实验方法与步骤1.准备实验用工具和样件;2.检查设备,了解设备使用方法;3.将冲压模具整体放到液压机工作台上,提起上模(导柱、导套不要脱开),放入条料后合模,开动液压机,落料4-5片备用;4. 卸下冲压模,将拉深模整体放到液压机工作台上,提起上模(导柱、导套不要脱开),将所落坯料放入下模定位圈内,用略大于坯料厚度的两片料垫起压边圈,开动液压机,将坯料拉深10mm,停车后打开模具,取出工件,观察工件凸缘的起皱现象;5.重复上述拉深过程,此次拉深使压边圈工作,拉深10mm,停车后打开模具,取出工件,观察工件凸缘情况;6.再次拉深,拉深深度20mm,观察圆筒件口部的变形情况。
激光拼焊板制复杂件的成型模拟及拉深筋优化研究
ba k ( ln s TWBswa n lz dAi n ttefr n f h enoc lt fap se g rc r Sf n o gtdn lf mete ) sa ay e . miga omigo erifrepaeo asn e a ’ r t n i ia a , h t o l u r h
Tal r W ede a ksa io - l d Bl n nd Optm ia i n fDr w b i z to o a Ri
W a un a W a Zh ng Ch , n Yi g h ng Ch y n, ng Yu, a iHa n c un
角等 , 文针 对 拉深 筋高 度 对拼 焊板 焊 缝移 动 的影 本
响进行 研究 。
21 拼 焊 板 板 厚 与 拉 深 筋 阻 力 的 关 系 .
导 致 的焊 缝移动 问题 。焊 缝 的存 在及 其在成 型过程 中 的移 动 , 但 影 响成 型 件 质 量 , 且 还 会 导致 拉 不 而
主题 词 : 光拼焊 板 激
焊 缝移 动
成 型模拟
拉 深 筋 优 化
中图分类 号 :G 0 文 献标识 码 : 文章编 号 :0 0 3 0 (0 7 1 — 0 0 0 T 3 A 10 — 7 3 2 0 )2 0 4 - 4
Re e r h o r i g S m u a i n o mp ia e r f s a c n Fo m n i l to fCo l td Pa to c
拉深筋约束力模型及试验研究
Ab ta t Th o m i g p o e so h t ls e tp si g t r u h d a e d i e p d a n s src : e f r n r c s ft e me a h e a sn h o g r wb a n d e rwi g i iv sia e . A i p ea dp a tc l etan o e f rw b a e p a c r i gt h n r y n e t td g sm l n r cia sr i t r m d lo a e di s tu c o dn o t ee e g d s p icpe Fu t e o ea s to e td vc swih s r w c a im sd sg e n n fc u e rn il. rh r r e fts e ie t ce me h n s i e in d a d ma u a t rd m
线段的筋产生的约束力在一定的压边力下, 其值为恒定的值 , 并且理论计算与 实测值基本吻合 , 在
数值 模拟 时, 该模 型 可 以作 为等 效拉 深 筋使 用.
关键词 :拉深筋; 约束力; 计算模型 中图分 类号 :TG 8. 2 文献 标识码 :A 文章 编 号 :05 —8 X(O6 O.8 9I 363 239 7 2 O )7I 1.4 ) )
史 东才 ,郭 成 ,程 羽 ,吴 华英 ,宋 志平
( 西安交通 大学 机械工程学院 , 1 0 9 7 0 4 ,西安 )
- 1、下载文档前请自行甄别文档内容的完整性,平台不提供额外的编辑、内容补充、找答案等附加服务。
- 2、"仅部分预览"的文档,不可在线预览部分如存在完整性等问题,可反馈申请退款(可完整预览的文档不适用该条件!)。
- 3、如文档侵犯您的权益,请联系客服反馈,我们会尽快为您处理(人工客服工作时间:9:00-18:30)。
1 前言在汽车覆盖件成形过程中,零件各部分成形条件不同,因此各部分成形所需的成形力不同,通常要采用拉深筋来进行控制。
拉深筋参数的合理取值是控制金属流动、防止出现起皱和破裂的重要手段。
拉深筋的设计是冲压模具设计的关键技术。
拉深筋作为一种改善成形性的有效方法,其作用机理是:当板料渡过拉深筋时,会在A点、C点、E点附近发生弯曲变形,如图1,在B点、D点、F点附近发生反弯曲变形,反复的弯曲和反弯曲变形所产生的变形抗力即为拉深筋的变形阻力。
同时,当板料在AB、CD、E F段上滑动时,会因摩擦而产生摩擦阻力。
拉深筋的变形阻力和摩擦阻力之和即为拉深筋阻力。
也有学者认为,拉深筋阻力还应包括板料通过拉深筋后由于应变强化而导致后续变形抗力增大所增加的变形阻力。
在拉深模具中设置拉深筋就是要利用拉深筋阻力来控制毛坯各部分的成形力,从而起到控制局部变形条件,使零件各部分的变形条件趋于平衡,最终保障零件的顺利成形。
随着现代制造技术的发展,板料冲压成形的有限元模拟已成为模具设计与制造的关键技术。
在有限元模拟中精确模拟真实拉深筋很困难,主要是因为拉深筋尺寸较小,形状复杂。
要精确考虑板料与拉深筋的接触,则必须将拉深筋曲面划分成非常小的网格,但这会大大增加计算量,降低了计算效率,同时对模具几何形状的修改也极其不利。
因此这种做法不常被采用。
通常的做法是采用等效拉深筋模型,也就是将真实拉深筋等效为一条附着在模具表面且能承受一定约束力的拉深筋线。
这就需要计算单位长度的拉深筋需要承受的拉深筋约束阻力,所以拉深筋阻力模型的性能直接影响到计算精度。
为此,近40年来很多学者分别采用实验研究、理论分析和有限元方法对拉深筋的作用机理、拉深筋阻力、拉深筋对成形质量的影响作了研究。
2 拉深筋等效阻力模型的理论研究在板料成形过程中,拉深筋阻力是控制板料流动重要手段之一。
为此,不少学者希望利用塑性成形理论建立合理的数据模型,从而直接计算拉深筋阻力。
1978年,Weidemann将板料通过凸凹筋圆角时必须克服的摩擦力和由于弯曲/反弯曲变形产生的变形阻力,并建立了著名的拉深筋阻力模型(1)。
式中t—板料的初始厚度ω—拉深筋的长度μ—摩擦系数σs—屈服强度ψ—板料弯曲角Rg、Rb—拉深筋的肩部、底部半径P—单位长度上的等效压边力Weidemann模型形式简单,便于使用。
但是该模型存在以下不足:①忽略了材料的硬化特性、各向异性特性和板厚的变化;②防止压边圈被抬起的最小压边力和板料弯曲角都是待定的;③由于假设等效弯曲半径与拉深筋的半径相等,这将导致压筋深度较浅时对弯曲应变估算过高。
1982年,Chrysler公司的N.M.Wang建立了半圆形拉深筋阻力的平面应变数学模型。
他假定已变形板料的形状由平面和曲面构成,曲面半径与拉深筋半径一致,每个曲面部分的变形分为3个过程:圆角处的弯曲、绕圆角的滑动和反弯曲,圆角处的弯曲、绕圆角的滑动和反弯曲。
并假设变形前后法线方向保持不变,材料满足变形应力,与应变速率无关及Hill 的各向异性屈服准则,忽略包辛格效应。
板料与拉深筋表面的接触摩擦系数μ为常数。
将这种拉深筋阻力模型应用于拉深筋压入深度大于拉深筋半径的情况,计算值与实验值吻合较好,对压入深度较浅的情况误差较大。
1983年,B.S.Levy应用虚原理,考虑材料的各向异性和应变率,根据Nine的实验数据回归出一个拉深筋阻力的预测模型(2)DBRF=α0+(α1+α2μ)X(2)式中X=F(,b,n,R,m,r)R,b—拉深筋的圆角半径和宽度m,r ,n,—板料的应变速率敏感系数、塑性应变比、硬化指数、应变速率和等效应变Levy模型形式也比较简单,但该模型是根据Nine的实验数据回归出来的,缺乏通用性。
1988年,Stoughton基于能量守恒原理提出了如公式(3)所示的拉深筋阻力数学模型。
DBRF=[(F1eμψ+μFe+F2+F3)eμψ+μFe+F4+F5] eμψ+F6 (3)式中μ—摩擦系数ψ—板料弯曲角Fi—对应于图1中A~F的6个弯曲/反弯曲点Fe—拉深筋开始闭合过程中引起板料弹性变形而产生的附加弹性力Stoughton模型具有以下优点:①考虑了材料的硬化特性、各向异性特性和板料在弹性变形时厚度的变化;②给出了拉深筋阻力和防止压边圈被抬起的最小压边力的计算公式;③弯曲角和等效半径都是可计算的。
不足之处在于其形式极为复杂,必须确定每一点弯曲和反弯曲角,实际损伤比较困难。
1992年,Kluge提出了类似于Weidemann模型的拉深筋阻力模型。
与Weidemann模型相比,Kluge模型中除了考虑了材料的硬化特性和给出了弯曲角的计算公式化外,Weideman n模型的不足仍然没有得到解决。
瑞典的Mattiasson提出了一种考虑压边间隙的等效拉深筋阻力模型.荷兰的Meinders用实验和仿真相结合的方法对拉深筋的阻力进行了研究。
波兰的Rojek提出了一种简化的等效拉深筋阻力模型,它不考虑材料流经拉深筋时的应变效应和由于弯曲/反弯曲引起的硬化效应。
国内华中理工大学的李尚健于1991年建立了与N.M.Wang的数据模型相似的拉深筋阻力模型,并将计算结果与实验值进行了比较。
上海交通大学的包友霞等人基于Weidemann模型,考虑了材料硬化、厚向异性系数对拉深筋阻力的影响,建立了一种改进的等效拉深筋阻力模型,该模型能够真实反映拉深筋压入深度对阻力的作用,并给出了弯曲角的计算公式。
3 拉深筋阻力的有限元分析随着计算机技术和非线性有限元理论的发展,有关拉深筋的有限元计算方法逐渐成为研究热点。
1986年,Michigan技术大学的B.Maker,S.K.Samanta等人在大位移、大转动的弹塑性有限元理论的基础上,采用壳单元、库仑摩擦定律,有编写了计算拉深筋阻力和板料经过拉深筋时应变状态的有限元程序。
Carleer等采用基于混合欧拉拉格朗日算法的有限元程序对半圆形拉深筋进行了计算,文中的板料沿厚度(0.7mm)方向划分为4层4结点平面应变单元,仿真结果与实验值吻合很好。
随着非线性有限元软件的商业化,很多学者开始直接借助现有软件研究拉深筋。
J.Cao和M.C.Boyce应用ABAQUS有限元软件研究了拉深筋压入深度对拉深筋阻力的影响。
他们将板料流过拉深筋时的变形状态简化为平面应变状态,不考虑辛格效应和应变速率的影响,有限元模型的几何参数与Nine的实验数据相同。
计算结果与Nine的实验结果相比较,最大误差为18.2%,最小误差为零,T.Meinders建立了一种基于罚约束法的拉深筋等效模型,该模型不仅考虑拉深筋阻力与压实拉深筋所需的压筋力,还将板料厚向应变以一种约束条件代入等效拉深筋模型的刚度矩阵。
应用于杯形件仿真时,仿真结果比只考虑拉深筋阻力的计算结果更接近实际值。
Y.T.Keum等将拉深筋阻力和板料通过拉深筋时的减薄量作为拉深筋附近结点的边界条件,建立了拉深筋阻力的数值计算模型。
Y.M.Heo等定量分析了拼焊板拉深成形时拉深筋形状尺寸对焊缝移动的影响。
H.Naceur等基于一步法,对拉深变形中的拉深筋阻力进行了优化,并开发了优化算法。
用此优化算法计算的结果与OPTRIS计算结果吻合较好。
M.Samuel基于平截面假设,分析了板料通过拉深筋时的弯曲/反弯曲的变形特点以及应力应变状态,建立了拉深筋数值仿义模型,并将该模型植入MARC软件中,仿真结果与实验值吻合较好。
Ludovic等人基于弹塑性理论和1oveKirchhoff假设,建立了拉深筋的有限元分析模型。
国内有许多学者进行了这方面的研究。
邢忠文等等应用弹性大变形有限元理论,开发出针对半圆形拉深筋的数值模拟软件。
杨玉英等人基于自已开发的成形模拟软件,分析了拉深筋的几何形状对压边力和拉延筋约束阻力的影响。
李硕本、金淼等人通过数值模拟和实验相结合的方法研究了拉深筋的作用机理以及几何参数对拉深筋阻力的影响。
叶又等利用Ls-Dyna 软件,采用了基于随动强化材料模型和平面应变假设,计算了板料经过半圆形拉深筋时受到的阻力和板料厚向应变,计算结果比采用各向同性强化材料模型的计算结果更接近实验值。
4 拉深筋的实验研究通过各种模拟实验或真实实验来研究拉深筋的作用一直是研究的重点Lloyd,M.J.Paiter在拉深实验仪上对半圆形的拉深筋进行研究,得出拉深筋阻力随筋压入深度、摩擦系数、拉延速度的变化而变化的结论。
80年代初,通用汽车公司的H.D.Nine专门设计了一个拉深筋阻力模拟测试仪,这一实验仪已经成为目前拉深筋机理研究的主要仪器。
该实验仪可以分离出拉深筋阻力的两个组成部分:弯曲/反弯曲力和摩擦力。
他指出弯曲变形力约占整个拉深筋阻力的65%~85%,该研究为以后拉深筋方面的研究工作捉供了非常有价值的实验方法和数据。
1991年,Chrysler公司的N.M.Wang和V.C.Sha在MTS成形性能测试仪上,针对半圆形筋、矩形筋、拉深槛、矩形筋与拉深槛的组合筋这4种拉深筋,以凸模负载曲线为参照,研究了不同润滑、不同夹紧力时的拉延阻力大小及其对冲压件极限拉延深度的影响,指出拉深筋的几何形状是影响阻力大小的重要因素。
Waterloo大学的John A.Schey等人应用Nine设计的拉深筋模拟测试仪研究了润滑条件、筋表面粗糙度对普通钢板和镀层钢板的摩擦系数的影响。
国内哈尔滨工业大学的邢忠文和杨玉英等人也在大量实验的基础上研究了拉深筋阻力的形成机理及其影响因素,指出拉深筋阻力是由板料通过拉深筋时的弯曲/反弯曲变形力和摩擦力以及因变形硬化引起的在变形抗力3部分共同组成,拉深筋阻力的影响因素包括拉深筋的形式、拉深筋参数、材料特性、润滑条件、变形速度、压边力等,其中拉深筋参数和形状对拉深筋阻力的影响最大。
5 拉深筋研究的发展方向经过半个多世纪的发展,拉深筋的研究已经进入工业实用,在改善成形性、提高产品质量方面发挥了及其重要的作用。
几乎所有的车身覆盖件在拉延成形中都需要拉深筋来调节拉延阻力,拉深筋的合理布置是车身覆盖件成形的磁键技术。
目前,该领域的发展趋势是:l)继续完善拉深筋阻力模型,提高计算精度,使等效拉深筋模型尽可能准确地反映真实拉深筋的特点。
2)开发功能较强的拉深筋优化算法,以便有效地根据零件形状、成形特点而进行修改,实现优化设计程序自动化。
3)随着环境的要求,车身覆盖件将越来越多的使用高强度钢板和铝合金等轻量化材料,与普通钢板相比,这些材料的成形性较差。
要提高这些难成形材料的成形性需要多方面的研究,其中包括新型拉深筋的设计。
如图2所示的是美国Auto/SteelPartnership提出的一种针对高强度钢板的新型拉深筋。
他们认为这种拉深筋有利于缓解拐角处的压应力,减小角部破裂的趋势。