第六章+板料的冲压成形性能与成形极限
冲压

第一章冲压冲压的定义:室温下,在压力机上通过模具对板料金属(非金属)加压,使之产生塑性变形或分离,从而获得一定尺寸、形状和性能的工件的加工方法,又叫冷冲压或板料冲压。
冲压工艺可用于加工,金属板料,非金属板料.冲压工艺特点:生产效率高;在大量生产中可获得稳定的质量;材料利用率高,生产成本低;可制造复杂形状的工件。
冲压生产的局限性:--制模成本高;--技术要求高;--不适用于单件、小批量生产。
加工硬化:在常温下,随着变形程度的增加,金属材料的强度指标增高,塑性指标降低的现象。
冲压分类:分离工序,成型工序分离工序:冲压过程中,使冲压件与板料在切应力或拉应力的作用下,沿一定的轮廓线相互分离。
分离工序主要指冲裁,包括落料、冲孔、切断、切边、剖切等工序。
普通冲裁:通过破坏分离方式所完成的冲压工序。
精密冲裁:以变形分离方式所完成的冲压工序。
成形工序:在冲压过程中,使毛坯在不破坏的条件下发生塑性变形,成为所需形状与尺寸的工件,同时冲压件应该满足尺寸精度方面的要求。
成形工序主要包括弯曲、拉伸、胀形、翻边等。
落料:用模具沿封闭轮廓线冲切,冲下部分是零件。
用于制造各种平板零件或者成形工序制坯冲孔:用模具沿封闭轮廓线冲切,冲下部分是废料。
用于冲制各类零件的孔形弯曲;把板料沿直线弯曲成各种形状,板料外层受拉伸力,内层受压缩力。
可加工形状复杂的零件毛坯区域的划分:变形区,传力区在成形过程中,毛坯的变形区和传力区是运动变化的,而且还会相互转化。
制定工艺时,必须保证:“弱区先变形,变形区应为弱区”对毛坯变形趋向性的控制,主要有以下几种方法:(1)合理确定毛坯和半成品尺寸(2)改变模具工作部分的几何形状和尺寸(3)改变毛坯与模具接触面之间的摩擦阻力(4)改变毛坯局部力学性能1、什么是冲压?它与其它加工方法相比有什么特点?2、冲压工序可分为哪两大类?他们的主要区别和特点是什么?3、如何控制冲压过程中的变形趋向?板料的冲压性能:指板料对冲压的适应能力、可成形能力间接试验:板料的受力情况和变形特点与实际冲压有一定差别,其试验结果只能间接反映板料的冲压性能。
拼焊板冲压成形与成形极限研究

虽 然拼 焊板 的应 用 具有很 多 优点 , 但是 , 由于焊 接 工艺 以及 自身 结 构 的 特 殊性 , 焊板 在 实 际生 产 拼 应用中, 尤其 是 在 车身 设 计 中 的应 用带 来 了许 多 新
的成形 方 面的 挑 战 。大 量 基础 试 验 研 究 表 明 , 传 与 统 的单 一钢 板相 比 , 由于 焊 缝 的存 在 和 焊接 热 影 响 区的硬 化作 用 , 拼焊 板 的屈 服 强 度 和抗 拉 强 度 显 著 增加 , 变硬 化 指数 值 和延 伸率 显著 减小 , 而使 应 从
启 动 机床 , 速为 1 0r mi , 缓 慢 摇 动 尾 座 手 柄 转 2 / n 再
很 好 的技术 经 济效 果 。
使 芯 棒 6逐渐 进入 成形 工 具 , 时 , 这 5个 钢球 4被 迫 逐 渐作 径 向进 给 , 零 件毛 坯进 行挤 压 , 对 使其 产生 塑
性 变形 , 到 与成形 凹模 贴合 , 成 图 1管形 零件 上 直 完 R1 2mm 环 形 凸起 的成 形 。此 时 , 卸 下 成 形后 的 要
关键 词 : 焊 板 ; 形 性 能 ; 形极 限 ; 拼 成 成
中图分类 号 : G 168 T 5 .
文献标 志码 : A
拼 焊 板 ( i rwed d ba k , Tal — le ln s TwB ) 术 是 o s技 指 将 2块 或 2块 以上 的金 属 板 料 焊 接 一起 , 后进 然 行 冲 压成形 , 且其 组 成板料 可 以具 有不 同厚 度 、 并 性 能、 材质 和 表 面 涂层 。在生 产 、 制造 和 设 计 方 面 , 拼 焊 板 的使用 有 着 巨大 的优 势口 : )满 足 零件 各 部位 ]1
成形极限图试验

成形极限图试验成形极限图(FLD)或成形极限曲线(FLC)是板料冲压成形性能发展过程中的较新成果。
成形极限图的试验方法如下所述:1)在试验用坯料上制备好坐标网格;2)以一定的加载方式使坯料产生胀形变形,测出试件破裂或失稳时的应变ε1、ε2(长、短轴方向);3)改变坯料尺寸或加载条件,重复2)项试验,测得另一状态下的ε1、ε2;4)取得一定量的数值后,在平面坐标图上描绘出各试验点,然后圆滑连线,作出FLD。
成形极限曲线将整个图形分成如1所示的三部分:安全区、破裂区及临界区。
图1 成形极限图及其用法于大型复杂薄板冲压件成形时,凹模内毛坯产生破裂的情况较多。
这一部分毛坯一般是在拉应力作用下成形的,变形区内产生的断裂是延性断裂。
掌握板材拉伸失稳理论,利用成形极限图,可以对这种破坏问题较快地作出判断,找出原因,提出相应的解决办法。
拉伸失稳理论是计算建立成形极限图的基础。
拉伸失稳是指在拉应力作用下,材料在板平面方向内失去了塑性变形稳定性而产生缩颈,并随这发生破裂。
拉伸失稳可分为分散失稳和集中失稳两种。
分散性失稳是指板料的塑性变形达到一定程度后,变形开始出现在材料内某些性能不均匀或厚度不均匀的部位,载荷开始随变形程度增大而减小,由于应变硬化,这些缩颈能在一定的尺寸范围内转移,使材料在这个范围内产生一种亚稳定的塑性流动,故载荷下降比较缓慢。
但由于材料的硬化增强,变形抗力又有所提高,最后,最薄弱的环节逐渐显示出来,缩颈就逐步集中到某一狭窄区段,这样就逐渐形成了集中失稳。
产生集中失稳时,缩颈点也不能再转移出去,此时金属产生不稳定流动,由于这时承载面急剧减小,变形;力也就急剧下降,很快就异致破坏。
成形极限是指材料不发生塑性失稳破坏时的极限应变值。
但由于目前失稳理论的计算值还不能准确反映实际冲压成形中毛坯的变形极限,在实际生产中普遍应用由实验得到的成形极限图。
成形极限图(FLD),也称成形极限线(FLC)是对板材成形性能的一种定量描述,同时也是对冲压工艺成败性的一种判断曲线。
冲压成形的基本理论

硬度提升而塑性下降。 加工硬化对塑性变形旳影响: ❖ 不利旳一面——使所需旳变形力增长,而且限制了材料进一
步旳变形。 ❖ 有利旳一面——板料硬化能够减小过大旳局部变形,使变形
趋于均匀,从而增大成形极限,同步也提升了材料旳强度。
19
一临界值(与应力状态无关)时,材料就开始屈服。经过单向
拉伸试验可得出,此临界值等于材料旳屈服极限
。
s
等效应力:
2 2
(1 2 )2 2 3 2 3 12
则密塞斯塑性条件可体现为:
( 1
2 )2
2
3 2
3
1 2
2
2 s
9
1.1 塑性变形与应力应变 经过计算可知,两个条件之间差别很小。若把上式进行简化,
设 1 2, 则 3最大剪应力理论可表达为:
max (1 3 ) 2 s 2
或
1 3 s
这一理论形式简朴,与试验成果基本相符,用于分析板料成形问 题有足够旳精度。但其忽视了中间应力旳作用,所以不够完善。
8
1.1 塑性变形与应力应变
2. 密塞斯塑性条件
密塞斯提出:任意应力状态下,当某点旳等效应力 到达某
屈雷斯卡(H.Tresca) 塑性条件(最大剪应力理论) 密塞斯(von Mises) 塑性条件
7
1.1 塑性变形与应力应变
1. 屈雷斯卡塑性条件(最大剪应力理论) 屈雷斯卡提出:任意应力状态下,只要最大剪应力到达某临界值 (与应力状态无关)后,材料就开始屈服。经过单向拉伸试验可 得出,此临界值等于材料屈服极限旳二分之一。
24
1.2 加工硬化与硬化曲线
② S 硬 化直线 用真实应力与真实应变建立坐标系,硬化曲线上缩颈点处旳切线 斜率为 Sb。
《汽车车身制造工艺学(冲压工艺)》复习要点 317
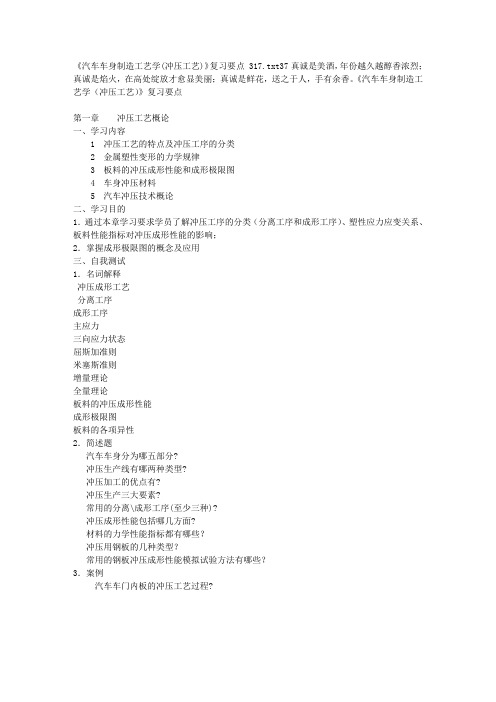
《汽车车身制造工艺学(冲压工艺)》复习要点 317.txt37真诚是美酒,年份越久越醇香浓烈;真诚是焰火,在高处绽放才愈显美丽;真诚是鲜花,送之于人,手有余香。
《汽车车身制造工艺学(冲压工艺)》复习要点第一章冲压工艺概论一、学习内容1 冲压工艺的特点及冲压工序的分类2 金属塑性变形的力学规律3 板料的冲压成形性能和成形极限图4 车身冲压材料5 汽车冲压技术概论二、学习目的1.通过本章学习要求学员了解冲压工序的分类(分离工序和成形工序)、塑性应力应变关系、板料性能指标对冲压成形性能的影响;2.掌握成形极限图的概念及应用三、自我测试1.名词解释冲压成形工艺分离工序成形工序主应力三向应力状态屈斯加准则米塞斯准则增量理论全量理论板料的冲压成形性能成形极限图板料的各项异性2.简述题汽车车身分为哪五部分?冲压生产线有哪两种类型?冲压加工的优点有?冲压生产三大要素?常用的分离\成形工序(至少三种)?冲压成形性能包括哪几方面?材料的力学性能指标都有哪些?冲压用钢板的几种类型?常用的钢板冲压成形性能模拟试验方法有哪些?3.案例汽车车门内板的冲压工艺过程?第二章冲裁工艺一、学习内容1 冲裁的变形过程2 冲裁间隙3 冲裁模刃口尺寸4 冲裁力和冲模压力中心5 冲模及冲裁模6 冲裁件缺陷原因及分析二、学习目的1.通过本章学习,掌握冲裁间隙的确定方法、冲裁力及其计算方法2. 通过本章学习,掌握冲裁力及其计算方法3. 了解冲裁件缺陷原因及分析三、自我测试1.名词冲裁光亮带冲裁间隙卸料力模具的压力中心复合模闭合高度2.简述题简述冲裁变形过程。
冲裁模刃口尺寸确定原则有哪些?影响冲裁力的主要因素有哪些?降低冲裁力的措施?冲模的种类?毛刺产生的原因有哪些?3.计算题课本思考题4。
第一章板料冲压性能与成形极限第二次课

冲 压 工 艺 及
ddtt dt
分散性失稳理论认为当外力达到最大时, 板料失稳。但是板料经过分 散性失稳后仍有相当的变形能力, 所以在板成形领域人们更关心集中性失
模
稳, 即通常将集中性失稳作为板成形过程的变形极限。
具
设
计
结论:单从板料拉伸变形的稳定性着眼,可以用分散性失稳,从板料破
裂前极限变形程度的估计着眼,就要以集中性失稳作为标准。
以往鉴定板料的成形性能, 大多依赖用模拟方法进行的工艺试 验。例如Swift杯形件压延试验,福 井锥形件压延试验和压坑试验等。 模拟试验条件比较单纯,试件形状
冲压成形极限图
简单划一。因此,对于指导形状复 杂、变形状态复杂的零件的生产,
其试验结果往往很难在生产中直接
成形极限图是20世纪60年代由keeler和goodwin等
冲
时的极限应变等。
压
工
艺 及 模 具 设 计
第一章 板料冲压性能与成形极限 步骤:1)试验前,在毛坯表面做出直径为1.5~2.5mm的小圆圈坐标网
冲
压
工
艺 及
2)试验时,将球形凸模压入材料,当试件出现裂纹时即停止。
模
具
设
计
第一章 板料冲压性能与成形极限 3)取出试件,在离裂纹最近的完整网格上测量小圆圈变成椭圆的尺寸。
具
1.4、常用材料的冲压性能
设
计
第一章 板料冲压性能与成形极限
1.3板料的成形极限
1.成形极限(Forming Limit Diagram,FLD)的基本概念 所谓冲压成形极限是指板料在冲压加工中所能达到的最大变形程度。
利用板料的单向拉伸试验所得的机械性
能指标来评定材料的成形性能,是一种最为
成形极限图试验

成形极限图试验成形极限图(FLD)或成形极限曲线(FLC)是板料冲压成形性能发展过程中的较新成果.成形极限图的试验方法如下所述:1)在试验用坯料上制备好坐标网格;2)以一定的加载方式使坯料产生胀形变形,测出试件破裂或失稳时的应变ε1、ε2(长、短轴方向);3)改变坯料尺寸或加载条件,重复2)项试验,测得另一状态下的ε1、ε2;4)取得一定量的数值后,在平面坐标图上描绘出各试验点,然后圆滑连线,作出FLD.成形极限曲线将整个图形分成如1所示的三部分:安全区、破裂区及临界区.图1 成形极限图及其用法于大型复杂薄板冲压件成形时,凹模内毛坯产生破裂的情况较多.这一部分毛坯一般是在拉应力作用下成形的,变形区内产生的断裂是延性断裂.掌握板材拉伸失稳理论,利用成形极限图,可以对这种破坏问题较快地作出判断,找出原因,提出相应的解决办法.拉伸失稳理论是计算建立成形极限图的基础.拉伸失稳是指在拉应力作用下,材料在板平面方向内失去了塑性变形稳定性而产生缩颈,并随这发生破裂.拉伸失稳可分为分散失稳和集中失稳两种.分散性失稳是指板料的塑性变形达到一定程度后,变形开始出现在材料内某些性能不均匀或厚度不均匀的部位,载荷开始随变形程度增大而减小,由于应变硬化,这些缩颈能在一定的尺寸范围内转移,使材料在这个范围内产生一种亚稳定的塑性流动,故载荷下降比较缓慢.但由于材料的硬化增强,变形抗力又有所提高,最后,最薄弱的环节逐渐显示出来,缩颈就逐步集中到某一狭窄区段,这样就逐渐形成了集中失稳.产生集中失稳时,缩颈点也不能再转移出去,此时金属产生不稳定流动,由于这时承载面急剧减小,变形;力也就急剧下降,很快就异致破坏.成形极限是指材料不发生塑性失稳破坏时的极限应变值.但由于目前失稳理论的计算值还不能准确反映实际冲压成形中毛坯的变形极限,在实际生产中普遍应用由实验得到的成形极限图.成形极限图(FLD),也称成形极限线(FLC)是对板材成形性能的一种定量描述,同时也是对冲压工艺成败性的一种判断曲线.它比用总体成形极限参数,如胀形系数、翻边系数等来判断是否能成形更为方便而准确. 成形极限图(FLD)是板材在不同应变路径下的局部失稳极限应变和(相对应变)或和(真实应变)构成的条带形区域或曲线(图1-14).它全面反映了板材在单向和双向拉应力作用下的局部成形极限.在板材成形中,板平面内的两主应变的任意组合,只要落在成形极限图中的成形极限曲线上,板材变形时就会产生破裂;反之则是安全.图1-14中的条带形区域称为界区,变形如位于临界区,表明此处板材有濒临于破裂的危险.由此可见,FLD是判断和评定板材成形性能的最为简便和直观的方法,是解决板材冲压成形问题的一个非常有效的工具.图1-14 成形极限图(FLD)一、成形极限图(FLD)的制作目前,试验确定板材成形极限图的方法是:在毛坯(试样)表面预先作出一定形状的风格.冲压成形后,观察、测定网格尺寸的变化量,经过计算,即可得到网格所在位置的应变.对变形区内各点网格尺寸的变化进行测量与计算,可得到应变的分布.网格图形如图1-15所示.图1-16是采用圆形网格,在变形网格变成椭圆形状,椭圆的长、短轴方向就是主轴方向,主应变数值为相应应变:长轴应变:短轴应变:真实应变:长轴应变:短轴应变:图1-15 常用网络形式a) 圆形网络b) 组合网络c) 叠加网络图1-16 网络的变形二、FLD在生产中的应用成形极限图与应变分析网格法结合在一起.可以分析解决许多生产实际问题.这种方法用于分析解决问题的原理是:首先通过试验方法获得研究零件所用板材的成形极限图.再将网格系统制作在研究零件的毛坯表面划变形危险区,坯料成形为零件后,测定其网格的变化量,计算出应变值.将应变值标注在所用材料的成形极限图上.这时零件的变形危险区域便可准确加以判断.成形极限图的应用大致有以下几方面:1)解决冲模调试中的破裂问题:2)判断所设计工艺过程的安全裕度,选用合适的冲压材料;3)可用于冲压成形过程的监视和寻找故障.FLD应用举例:为消除破裂指出应采取的工艺措施.将汽车覆盖件上某一危险部位的应变值标注到所用材料的成形极限图上(图1-17).如果覆盖件上危险部位的应变位于B处,要增加其安全,由图中看出:应减小或增大,最好兼而有之.减小需降低椭圆长轴方向的流动阻力,还可以采用在方向减小坯料尺寸,增大模具圆角半径,改善其润滑条件等方法来实现.如要增加,需增加椭圆短轴方向的流动阻力,实现的方法是在这一方向上增加坯料尺寸,减小模具圆角,在垂直于短轴方向设置拉深肋等.若覆盖件危险部位的应变位于D处,要增加其安全性,可以减小或减小的代数着手,应注意的是,减小的代数值应减小短轴方向的流动阻力.通过上述分析可见,汽车覆盖件成形中,对其成形质量影响较大的工艺参数是:模具圆角半径、坯料形状和尺寸、压边力、润滑状态等,成形工艺设计的优劣,在很大程度上取决于合理选择这些工艺参数,成形极限图提供了合理选择和优化工艺参数的途径.图1-17 用FLD预见危险性图 3.0.1 各种常见弯曲件3.1 弯曲变形过程及变形特点< 弯曲变形过程>在压力机上采用压弯模具对板料进行压弯是弯曲工艺中运用最多的方法.弯曲变形的过程一般经历弹性弯曲变形、弹-塑性弯曲变形、塑性弯曲变形三个阶段.现以常见的V 形件弯曲为例,如图3.1.1 所示.板料从平面弯曲成一定角度和形状,其变形过程是围绕着弯曲圆角区域展开的,弯曲圆角区域为主要变形区.弯曲开始时,模具的凸、凹模分别与板料在 A 、B 处相接触. 设凸模在 A 处施加的弯曲力为 2F (见图 3.1.1 a ).这时在 B 处(凹模与板料的接触支点则产生反作用力并与弯曲力构成弯曲力矩M = F·(L 1 /2),使板料产生弯曲.在弯曲的开始阶段,弯曲圆角半径r很大,弯曲力矩很小,仅引起材料的弹性弯曲变形.图3.1.1 弯曲过程随着凸模进入凹模深度的增大,凹模与板料的接触处位置发生变化,支点 B 沿凹模斜面不断下移,弯曲力臂 L 逐渐减小,即 L n < L 3 < L 2 < L 1 . 同时弯曲圆角半径 r 亦逐渐减小,即 r n < r 3 < r 2 < r 1 ,板料的弯曲变形程度进一步加大.弯曲变形程度可以用相对弯曲半径 r/t表示,t为板料的厚度. r/t 越小,表明弯曲变形程度越大.一般认为当相对弯曲半径r/t>200时,弯曲区材料即开始进入弹-塑性弯曲阶段,毛坯变形区内(弯曲半径发生变化的部分)料厚的内外表面首先开始出现塑性变形,随后塑性变形向毛坯内部扩展.在弹-塑性弯曲变形过程中,促使材料变形的弯曲力矩逐渐增大,弯曲力臂L继续减小,弯曲力则不断加大.凸模继续下行,当相对弯曲半径 r/t<200时,变形由弹 -塑性弯曲逐渐过渡到塑性变形.这时弯曲圆角变形区内弹性变形部分所占比例已经很小,可以忽略不计,视板料截面都已进入塑性变形状态.最终,B 点以上部分在与凸模的V形斜面接触后被反向弯曲,再与凹模斜面逐渐靠紧,直至板料与凸、凹模完全贴紧.若弯曲终了时,凸模与板料、凹模三者贴合后凸模不再下压,称为自由弯曲.若凸模再下压,对板料再增加一定的压力,则称为校正弯曲,这时弯曲力将急剧上升. 校正弯曲与自由弯曲的凸模下止点位置是不同的,校正弯曲使弯曲件在下止点受到刚性镦压,减小了工件的回弹(进一步论述见本章第 3.2.2节).< 板料弯曲的塑性变形特点>为了观察板料弯曲时的金属流动情况,便于分析材料的变形特点,可以采用在弯曲前的板料侧表面设置正方形网格的方法.通常用机械刻线或照相腐蚀制作网格,然后用工具显微镜观察测量弯曲前后网格的尺寸和形状变化情况,如图 3.1.2a〕所示.弯曲前,材料侧面线条均为直线 , 组成大小一致的正方形小格,纵向网格线长度aa =bb.弯曲后,通过观察网格形状的变化,(如图 3.1.2b 所示)可以看出弯曲变形具有以下特点:图3.1.2 弯曲变形分析一.弯曲圆角部分是弯曲变形的主要区域可以观察到位于弯曲圆角部分的网格发生了显著的变化,原来的正方形网格变成了扇形.靠近圆角部分的直边有少量变形,而其余直边部分的网格仍保持原状,没有变形.说明弯曲变形的区域主要发生在弯曲圆角部分.二.弯曲变形区内的中性层在弯曲圆角变形区内,板料内侧(靠近凸模一侧)的纵向网格线长度缩短,愈靠近内侧愈短.比较弯曲前后相应位置的网格线长度,可以看出圆弧为最短,远小于弯曲前的直线长度,说明内侧材料受压缩.而板料外侧(靠近凹模一侧)的纵向网格线长度伸长,愈靠近外侧愈长.最外侧的圆弧长度为最长,明显大于弯曲前的直线长度,说明外侧材料受到拉伸.从板料弯曲外侧纵向网格线长度的伸长过渡到内侧长度的缩短,长度是逐渐改变的.由于材料的连续性,在伸长和缩短两个变形区域之间,其中必定有一层金属纤维材料的长度在弯曲前后保持不变,这一金属层称为应变中性层(见图 3-3 中的 O-O 层). 应变中性层长度的确定是今后进行弯曲件毛坯展开尺寸计算的重要依据.当弯曲变形程度很小时,应变中性层的位置基本上处于材料厚度的中心,但当弯曲变形程度较大时,可以发现应变中性层向材料内侧移动,变形量愈大,内移量愈大 .三.变形区材料厚度变薄的现象弯曲变形程度较大时,变形区外侧材料受拉伸长,使得厚度方向的材料减薄;变形区内侧材料受压,使得厚度方向的材料增厚.由于应变中性层位置的内移,外侧的减薄区域随之扩大,内侧的增厚区域逐渐缩小,外侧的减薄量大于内侧的增厚量,因此使弯曲变形区的材料厚度变薄. 变形程度愈大,变薄现象愈严重.变薄后的厚度t′ =ηt,(η是变薄系数,根据实验测定,η值总是小于 1 ).四.变形区横断面的变形板料的相对宽度 b/t ( b 是板料的宽度, t 是板料的厚度)对弯曲变形区的材料变形有很大影响.一般将相对宽度 b/t >3 的板料称为宽板,相对宽度b/t ≤ 3 的称为窄板.窄板弯曲时,宽度方向的变形不受约束.由于弯曲变形区外侧材料受拉引起板料宽度方向收缩,内侧材料受压引起板料宽度方向增厚,其横断面形状变成了外窄内宽的扇形(见图 3-4a ).变形区横断面形状尺寸发生改变称为畸变.宽板弯曲时,在宽度方向的变形会受到相邻部分材料的制约,材料不易流动,因此其横断面形状变化较小,仅在两端会出现少量变形(见图 3-4b ),由于相对于宽度尺寸而言数值较小,横断面形状基本保持为矩形. 虽然宽板弯曲仅存在少量畸变,但是在某些弯曲件生产场合,如铰链加工制造,需要两个宽板弯曲件的配合时,这种畸变可能会影响产品的质量.当弯曲件质量要求高时,上述畸变可以采取在变形部位预做圆弧切口的方法加以防止.<>板料塑性弯曲时,变形区内的应力和应变状态取决于弯曲变形程度以及弯曲毛坯的相对宽度 b/t.如图3-5所示,取材料的微小立方单元体表述弯曲变形区的应力和应变状态, σθ、εθ表示切向 (纵向、长度方向) 应力、应变,σ r 、ε r 表示径向(厚度方向)的应力、应变,σ b 、ε b 表示宽度方向的应力、应变.从图中可以看出,对于宽板弯曲或窄板弯曲,变形区的应力和应变状态在切向和径向是完全相同的,仅在宽度方向有所不同.图 3.1.3 自由弯曲时的应力应变状态一. 应力状态在切向:外侧材料受拉,切向应力σθ为正;内侧材料受压,切向应力σθ为负. 切向应力为绝对值最大的主应力.外侧拉应力与内侧压应力间的分界层称为应力中性层,当弯曲变形程度很大时也有向内侧移动的特性.应变中性层的内移总是滞后于应力中性层,这是由于应力中性层的内移,使外侧拉应力区域不断向内侧压应力区域扩展,原中性层内侧附近的材料层由压缩变形转变为拉伸变形,从而造成了应变中性层的内移.在径向:由于变形区各层金属间的相互挤压作用,内侧、外侧同为受压,径向应力σr 均为负值. 在径向压应力σr 的作用下,切向应力σθ的分布性质产生了显著的变化,外侧拉应力的数值小于内侧区域的压应力.只有使拉应力区域扩大,压应力区域减小,才能重新保持弯曲时的静力平衡条件,因此应力中性层必将内移相对弯曲半径 r/t越小,径向压应力σ r 对应力中性层内移的作用越显著.在宽度方向:窄板弯曲时,由于材料在宽度方向的变形不受约束,因此内、外侧的应力均接近于零. 宽板弯曲时,在宽度方向材料流动受阻、变形困难,结果在弯曲变形区外侧产生阻止材料沿宽度方向收缩的拉应力,σ b 为正,而在变形区内侧产生阻止材料沿宽度方向增宽的压应力,σ b 为负.由于窄板弯曲和宽板弯曲在板宽方向变形的不同,所以窄板弯曲的应力状态是平面的,宽板弯曲的应力状态是立体的.二.应变状态在切向:外侧材料受拉,切向应变εθ为正,内侧材料受压缩,切向应变εθ为负,切向应变εθ为绝对值最大的主应变.在径向:根据塑性变形体积不变条件条件:εθ + εr + ε b = 0 ,εr 、ε b 必定和最大的切向应变εθ符号相反.因为弯曲变形区外侧的切向主应变εθ为拉应变,所以外侧的径向应变εr为压应变;而变形区内侧的切向主应变εθ为压应变,所以内侧的径向应变ε r为拉应变.在宽度方向:窄板弯曲时,由于材料在宽度方向上可自由变形,所以变形区外侧应变ε b 为压应变;而变形区内侧应变ε b 为拉应变.宽板弯曲时,因材料流动受阻,弯曲后板宽基本不变.故内外侧沿宽度方向的应变几乎为零(ε b ≈ 0),仅在两端有少量应变.综上所述,可以认为窄板弯曲的应变状态是立体的,而宽板弯曲的应变状态是平面的.图3.1.4 板料弯曲后的翘曲由于宽板弯曲时,沿宽度方向上的变形区外侧为拉应力(σ b 为正);内侧为压应力(σ b 为负),在弯曲过程中,这两个拉压相反的应力在弯曲件宽度方向(即横断面方向)会形成力矩 MB.弯曲结束后外加力去除,在宽度方向将引起与力矩 MB方向相反的弯曲形变,即弓形翘曲(如图3-6所示).对于弯曲宽度相对很大的细长件或宽度在板厚10倍以下的弯曲件,横断面上的翘曲十分明显,应采用工艺措施予以解决(见本章第 3.4.1节图3-48) .。
板料成形性能及CAE分析

第一节 板料成形性基本理论
二、板料成形应力、应变问题
• 从本质上看,板料成形就是在力的作用下使板料产生相应的塑性变 形,所以变形区内的应力状态和变形性质是决定板料成形性质的基本因 素。根据变形区应力状态和变形特点进行的板料成形分类方法,可以把 成形性质相同的成形方法概括成同一个类型并进行体系化的研究。 • 绝大多数板料成形过程中,变形区均处于平面应力状态。通常在板料 表面上不受外力的作用,可以认为垂直于板面方向上的应力为零。使板 料毛坯产生塑性变形的是作用于板面方向上相互垂直的两个主应力。由 于板厚较小,通常都近似地认为这两个主应力在厚度方向上是均匀分布 的:基于这样的分析,可以把所有各种形式的冲压成形中的毛坯变形区 的受力状态与变形特点,在平面应力坐标系中(板料变形应力图)与相应 的两向应变坐标系中(板料变形应变图)以应力与应变坐标决定的位置来 表示。图1-1和图1-2分别简要描述一下板料成形中的应力应变问题,表 示为板料成形应变图与板料成形应力图。把各种应力状态在板料成形应 力图和板料成形应变图中所处的位置以及两个图的对应关系列于表11,表(1-2)中列出了伸长类变形与压缩类变形在板料成形工艺方面的 特点。
第一节 板料成形性基本理论
• 1)弯曲变形的过程和特点 • 以V形件弯曲为例说明弯曲的变形过程,V形件弯曲是一种很普通的板 料弯曲,其弯曲过程如图1-3所示。
图1-3 弯曲过程 • 研究材料的冲压变形规律,常采用画网格的方法进行辅助分析。如图 1-4所示,先在板料毛坯侧面用机械刻线或照相腐蚀的方法画出网格, 观察弯曲变形后网格的变形情况,就可分析出板料的变形特点。
第一节 板料成形性基本理论
图1-1 板料成形应变图 图1-2 板料成形应力图
第一节 板料成形性基本理论