02板料成形数值模拟关键技术
基于数值模拟的拉深成形质量评价方法

基于数值模拟的拉深成形质量评价方法摘要针对板料拉深成形数值模拟过程中的拉深成形质量问题,提出了一种新的评价方法,即采用拉深后板料的最大厚度与最小厚度差值δt作为评价指标,并应用该方法评定了ta2板材的拉深成形质量,为改进拉深工艺和提高拉深成形质量提供了依据。
关键词拉深成形;数值模拟;ta2;评价指标中图分类号 tg3 文献标识码 a 文章编号1674-6708(2010)12-0044-030 引言针对板料拉深成形的有限元数值模拟技术已日趋成熟,模拟过程中的拉深件成形质量判据主要有3种,即拉深件表观质量检验、网格畸变程度检查和成形极限图分析。
拉深件表观质量检验精度较差,且带有明显的主观性;网格畸变程度检查和成形极限图分析均需复杂的数学处理,使用极为不便。
鉴此,本文根据拉深成形的特点结合有限元分析方法,提出了一种更为简单有效的评价方法,即采用板料的最大厚度与最小厚度差值δt作为拉深成形质量好坏的评价指标。
1 厚度差⊿t的提出及其意义板料拉深成形前和拉深成形后的形状如图1所示。
图2给出了典型拉深成形过程中从板料中心到凸缘各单元沿路径oa的厚度变化规律。
图2中平台段a对应图1(b)中的底部区域a,拉深成形过程中该区域的板料厚度几乎没有变化;谷值b对应图1中拉深件筒底圆角区域b,此处厚度减薄很大;峰值c对应图1(b)中筒部边缘c,此处板料厚度最大。
图1 坯料和成形件示意图图2典型拉深成形过程中板料厚度的变化规律(毛坯厚度为1mm) 拉深成形过程中,起皱和拉裂是最常见的缺陷。
起皱现象可以认为是板料在该处的厚度大于某一厚度值twri;而破裂可以认为板坯在该处的厚度小于某一厚度值tcra。
设板坯厚度的最大值与最小值分别为tmax与tmin,最大厚度与最小厚度的差值△t=tmax-tmin。
如果板坯经过拉深成形后同时出现起皱和拉裂,则tmax≥twri且tmin≤tcra。
显然板料既未起皱又未开裂的厚度值t满足不等式tmin﹥t﹥tmax。
板料多步冲压回弹的数值模拟研究

板料多步冲压回弹的数值模拟研究作者:江苏大学陈炜王晓路高霖摘要:回弹是板料冲压成形过程中一种常见但很难解决的现象。
首先研究了板料弯曲变形中卸载回弹的原理,然后以依维柯侧壁上内板为例,采用动态和静态算法相结合的方法,在考虑每道工序板料回弹的基础上,对其进行多步冲压回弹的数值模拟,最后对模拟结果和实验结果进行比较,验证该模拟方法提高回弹计算精度的有效性,为板料冲压成形工艺的制定提供科学依据。
关键词:回弹;多步冲压;数值模拟中图分类号:TG386.41 文献标识码:A 文章编号:1 前言通常,一个完整的冲压过程要经过拉延、整形、修边、冲孔、翻边等多步工序才能完成。
在这一过程中,回弹是板料成形工艺制定中要考虑的关键因素,零件的最终形状取决于成形后的回弹量,当回弹量超过允许容差后,就成为成形缺陷,影响零件的几何精度。
特别是近几年来由于高强度薄钢板和铝合金板材的大量使用,回弹问题更为突出。
目前,板料回弹的精确预测以及如何减小回弹量、降低残余应力成为板料成形模拟中的热点问题。
从NUMISHEET’93(第二届板料成形三维数值模拟国际会议)开始,每届会议都有关于回弹预测的标准考题(BENCHMARK),在NUMISHEET’99上,专门有一个关于回弹预测和回弹误差控制的会议专题,其中文章达到10篇,约占全部会议文章的11﹪[1];而在NUMISHEET’2002上,关于回弹预测和控制的会议专题论文达20篇之多,占到全部会议论文的21﹪以上[2]。
在实际生产中要控制和补偿回弹,提高回弹预测的精度是至关重要的[3]。
通常我们在进行板料多步冲压的回弹预测时,都忽略了板料每道工序后的卸载回弹,未将其回弹考虑到下一道工序的计算之中,然而板料的最终形状是其整个变形历史的累积效应,其变形历史等对残余应力和回弹计算都有一定影响[4],那么因忽略了每道工序后的回弹而产生的累积误差势必影响最终的回弹预测精度。
本文在进行板料多步冲压数值模拟时以依维柯侧壁上内板为例,采用动态和静态算法相结合的方法[4]来模拟其多步冲压过程,将前一道工序的回弹计算结果作为下一道工序的输入,并通过模拟结果和实验结果的对比来验证该数值模拟过程的正确性及有效性。
复合材料成型数值模拟及其应用

复合材料成型数值模拟及其应用复合材料在现代工业中应用广泛,具有轻质、高强度、高刚度和优异的耐久性等特点。
然而,复合材料的成型过程可谓是一门艺术和技术的结合,需要大量的工程经验,试错和大量的实验验证。
随着计算机技术的不断进步,数值模拟成为一种有效的预测和分析复合材料成型过程的方法。
本文将从数值模拟的角度出发,探讨复合材料在制造过程中的应用。
一、复合材料成型的基本过程复合材料的成型过程一般分为模具设计、预浸料制备、预浸料浸渍、层叠和压缩这几个步骤。
1. 模具设计模具是决定复合材料成型特性的关键因素之一。
合理的模具设计可以提高复合材料的成型质量和生产效率。
目前,常用的模具包括手工模具、金属模具和树脂模具等。
2. 预浸料制备复合材料一般采用热固性环氧树脂作为基体材料,预浸料是将纤维预先浸润在树脂中的半成品材料。
预浸料的制备是浸渍复合材料的基础,质量的高低直接影响到成品的质量。
3. 预浸料浸渍浸渍是将预浸料浸润在纤维上的过程,纤维的含量、树脂的流动性和浸渍过程的参数都是影响浸渍质量的重要因素。
4. 层叠和压缩将浸渍好的纤维层叠起来并进行压缩,以使树脂浸润在纤维之间,形成复合材料。
二、复合材料成型数值模拟的概述数值模拟是一种通过计算机模拟实际过程的方法,可以在虚拟环境中预测实际过程的结果。
数值模拟可以显著缩短调试时间和成本,减少实验次数和避免安全事故的发生。
复合材料成型数值模拟的基础是复合材料的力学行为和传热学理论。
主要包括有限元分析、流体力学分析、热传分析和材料模拟等方法。
可采用数值模拟技术模拟复合材料的成型过程及其过程参数和材料物性对成型过程的影响。
数值模拟可以分为几个步骤:模型的建立、边界条件的确定、求解方案的选择、数值计算和结果的分析等。
模型的建立是数值模拟的基础,复合材料成型过程的模型建立对数值模拟的精度有很大的影响。
应该综合考虑成型过程的物理和化学特性,设计实用、精确、高效、可靠的数值模拟模型。
柔性模具成形的6大关键技术,不是只能做飞机蒙皮零件
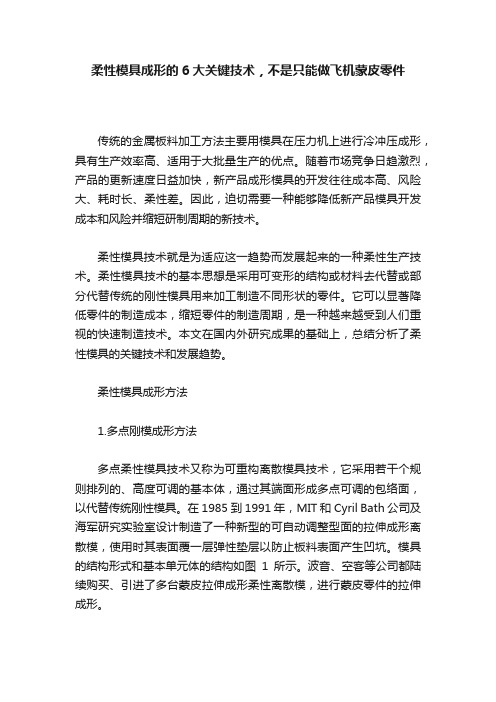
柔性模具成形的6大关键技术,不是只能做飞机蒙皮零件传统的金属板料加工方法主要用模具在压力机上进行冷冲压成形,具有生产效率高、适用于大批量生产的优点。
随着市场竞争日趋激烈,产品的更新速度日益加快,新产品成形模具的开发往往成本高、风险大、耗时长、柔性差。
因此,迫切需要一种能够降低新产品模具开发成本和风险并缩短研制周期的新技术。
柔性模具技术就是为适应这一趋势而发展起来的一种柔性生产技术。
柔性模具技术的基本思想是采用可变形的结构或材料去代替或部分代替传统的刚性模具用来加工制造不同形状的零件。
它可以显著降低零件的制造成本,缩短零件的制造周期,是一种越来越受到人们重视的快速制造技术。
本文在国内外研究成果的基础上,总结分析了柔性模具的关键技术和发展趋势。
柔性模具成形方法1.多点刚模成形方法多点柔性模具技术又称为可重构离散模具技术,它采用若干个规则排列的、高度可调的基本体,通过其端面形成多点可调的包络面,以代替传统刚性模具。
在1985到1991年,MIT和Cyril Bath公司及海军研究实验室设计制造了一种新型的可自动调整型面的拉伸成形离散模,使用时其表面覆一层弹性垫层以防止板料表面产生凹坑。
模具的结构形式和基本单元体的结构如图1所示。
波音、空客等公司都陆续购买、引进了多台蒙皮拉伸成形柔性离散模,进行蒙皮零件的拉伸成形。
国内北京航空制造工程研究所在现有柔性多点模具基础上,针对大型柔性多点模具,采用新型的调形驱动机构及伺服轴离合复用技术,实现与冲头驱动源分合,大大减少了驱动电机的数量,并开发出了具有价格竞争力的蒙皮拉伸成形多点模系统。
李明哲从90年代初期就开始进行离散模冲压技术的研究,开发了专用成形设备,取得了一系列的成果,在建筑结构件与装饰件、高速列车流线型车头覆盖件、船体外板及人脑颅骨修复体等产品的成形上发挥了重要作用。
图2(a)是利用片层式离散模进行的拉弯成形实验装置。
离散模应用拉弯成形时,由于型材拉弯零件截面复杂不同于板料拉形,因此需要模块化的结构。
板料成形的计算机数值模拟仿真技术

成都 6 0 8 ) 1 0 1
摘 要 : 绍 了 板 料 成 形 数 值 模 拟 技 术 的发 展 及 算 法 , 述 了 国 内应 用 较 广 的 三 种 板 料 成 形 C 介 详 AE 软 件 。 提
出 了板 料 成 形 C AE 的 未 来 发 展 方 向 。
关键 词 : 算 机 应用 ; 压 ; 材 ; 值模 拟 ; 计 冲 板 数 CAE
维普资讯
■ E A uAo墨墨圈 RP c l P T
文 章 编 号 : 6 2 01 1 2 0 ) 4 0 9 — 3 1 7 — 2 (0 6 0 — 0 5 0
板 料成 形 的计 算 机 数 值 模 拟 仿 真 技 术
李 明 昆
( 都 市工业 学校 , 川 成 四
开 发 周 期 , 少 调 试 次 数 , 结 构 修 改 设 想 的 快 速
… 何 德誉 . 压 力 机 【 ¨ 京 : 械 工 业 出 版 社 ,9 7 曲柄 M】| £ 机 18 .
计 软 件 的 开发 . 电 工 程 技 术 ,0 5( )3 . 机 2 0 ,3 :4 【】 Mi oot o . D irr l uy 0 1Mi oo op20 . 5 c sfC r MS N LbayHe Jl 0 . c sfC r.0 1 r p p 2 r t 【】 A nr mot n ni l aC s- ae aoig F u dt n 6 g a Aa d dE rc a .ae B sdResnn: o n ai — a Pz o
中 图 分 类 号 : G3 641 T 8 . 文 献 标 识 码 : A
1
前 言
周 期 、 短 研 发 费 用 以 及 缩 小 整 车 重 量 ( 高 燃 油 效 缩 提
SPCC板材冲压成形过程的数值模拟

SPCC板材冲压成形过程的数值模拟SPCC板材是一种优质的低碳钢板材,常用于制作汽车钣金、电器外壳等产品。
其具有良好的加工性能,但冲压成形过程中容易出现变形和裂纹等问题。
为了提高产品质量和生产效率,数值模拟成为一种重要的工具,可以帮助设计者优化冲压工艺和工装结构。
数值模拟的基本原理是根据材料力学特性和变形规律,通过计算机模拟来预测材料在冲压成形过程中的变形、应力和应变等参数,从而评估产品的质量和可行性。
下面我们以SPCC板材的冲压成形为例,介绍其数值模拟的过程和方法。
一、建立模型数值模拟的第一步是建立三维几何模型,包括产品形状、工艺参数、材料性质等要素。
在SPCC板材的冲压成形中,常见的产品包括箱体、盖板、底板等,需要根据不同产品的尺寸、形状和工艺要求来建立几何模型。
同时,需要设置材料参数,如杨氏模量、泊松比、屈服强度等。
二、网格划分建立几何模型后,需要将其转化为数值网格模型,也称为离散化。
这一过程主要是将复杂的几何体划分成数个小体积或小面积,以便于数值计算和求解。
网格划分的密度和精度决定了数值模拟的精度和速度。
通常,高精度的模拟需要更密的网格划分,但也会增加模拟时间和计算量。
三、建立物理模型在网格划分后,需要建立材料的物理模型,包括材料的本构模型和材料的本构参数。
本构模型是描述材料变形和应力关系的数学模型,常见的本构模型包括各向同性模型、非各向同性模型和弹塑性模型等。
用来描述SPCC板材的本构模型可以使用各向同性的屈服准则或者分段屈服的本构模型。
四、施加载荷和边界条件载荷是指在冲压成形过程中施加在材料表面的力和压力,这些载荷包括空气压力、上下模压力和侧向引伸力等。
边界条件是在数值模拟中必须考虑的约束条件,它们可以限制材料在变形过程中的位移、速度和加速度等。
通常,边界条件包括定位销、卡位、滚动辅助和止口等。
五、数值计算和分析完成模型建立和载荷设置后,就可以进行数值计算和分析。
该过程一般采用有限元分析(FEA)软件来完成,例如ABAQUS、ANSYS等。
板料成形CAE技术
板料成形CAE 技术贵州风华机器厂童春桥一、前言计算机辅助设计技术以其强大的冲击力,影响和改变着工业的各个方面,甚至影响着社会的各个方面。
它使传统的产品技术、工程技术发生了深刻的变革,极大地提高了产品质量,缩短了从设计到生产的周期,实现了设计的自动化。
板料成形是利用模具对金属板料的冲压加工,获得质量轻、表面光滑、造型美观的冲压件,具有节省材料、效率高和低成本等优点,在汽车、航空、模具等行业中占据着重要地位。
由于板料成形是利用板材的变形得到所需的形状的,长期以来,困扰广大模具设计人员的主要问题就是较长的模具开发设计周期,特别是对于复杂的板料成形零件无法准确预测成形的结果,难以预防缺陷的产生,只能通过经验或类似零件的现有工艺资料,通过不断的试模、修模,才能成功。
某些特殊复杂的板料成形零件甚至制约了整个产品的开发进度。
板料成形CAE 技术及分析软件,可以在产品原型设计阶段进行工件坯料形状预示、产品可成形性分析以及工艺方案优化,从而有效地缩短模具设计周期,大大减少试模时间,帮助企业改进产品质量,降低生产成本,从根本上提高企业的市场竞争力。
板料成形CAE 技术对传统开发模式的改进作用可以通过图 1 和图 2 进行对比=> 试模催模模具方案僱图1传统板料成形模具开发模式■ - -JJ RBi^a-j ri-BHMnHI _ liHHd I图2 CAE技术模具开发方式通过比较,就可发现板料成形CAE技术的主要优点(1) 通过对工件的可成形工艺性分析,做岀工件是否可制造的早期判断;通过对模具方案和冲压方案的模拟分析,及时调整修改模具结构,减少实际试模次数,缩短开发周期。
(2) 通过缺陷预测来制定缺陷预防措施,改进产品设计和模具设计,增强模具结构设计以及冲压方案的可靠性,从而减少生产成本。
(3) 通过CAE分析可以择优选择材料,可制造复杂的零件,并对各种成形参数进行优化,提高产品质量。
(4) 通过CAE分析应用不仅可以弥补工艺人员在经验和应用工艺资料方面的不足,还可通过虚拟的冲压模拟,提高提高工艺人员的经验。
板料冲压成形及回弹有限元模拟分析
Ku=F
式中K为总刚度矩阵;u为位移向量;F为节点载荷向量。
在隐式算法中,对于第i个给定的加载增量,用Newton-Raphson迭代法,需要求解下面的方程:
板料冲压成形及回弹有限元模拟分析
摘要
回弹是板材冲压成形过程中不可避免的普遍现象,直接影响到冲压件的尺寸精度和零件最终形状。本文利用ANSYS/LS-DYNA有限元软件中的非线性动力的显式、隐式连续求解功能,模拟了板料冲压成形过程与卸载后板料回弹变形的全过程,得到了成形过程中任一时刻各处Von-Mises应力云图和应变值及卸载后板料的回弹结果,帮助我们更好的认识分析板料冲压成形以及回弹过程中物质内部的变化。
ANSYS/LS-DYNA是一个通用的显示非线性动力分析有限元程序,近年来开发的板料冲压成形数值模拟新功能,取得了很大成功。通过计算,可以观察板料冲压成形过程中的变形状态、应力状态和壁厚变化,了解可能出现的起皱和开裂现象。此外,ANSYS/LS-DYNA程序具有显式、隐式求解功能,用显式求解模拟动态成形过程,然后用隐式求解模拟线性回弹变形。这不仅能够模拟材料变形过程,而且也能较好地计算回弹现象,比较准确地得到材料最终成形状态。
关键词:板材冲压,回弹,非线性有限元分析,数值模拟
Sheet metal stamping and rebound finite element simulation analysis
Abstract
The rebound is inevitable common phenomenon in sheet metal forming process, a direct impact on the final shape to the dimensional accuracy of the stampings and parts. In this paper, the nonlinear dynamic finite element software ANSYS / LS-DYNA explicit, implicit sequential solution function to simulate thespringbackdeformation of the sheet after sheet metal stamping process and uninstall the whole process, forming process at any time throughout the Von-Misesstress cloud and strain and after unloading sheetspringbackresults, help us to a better understanding analysis sheet metal stamping and rebound process material internal changes.
影响板料成形回弹数值模拟精度的因素分析
lt 1 1B da9 t及 B lt 0 3 a9 、 a t74 p ] r a a2 0 嘲等 各 向 异 性 屈 服 准 则 。 尽 管 B r t9是 三 参 数 平 面 应 力 各 向 异 性 屈 服 al 8 a 准 则 , 因 其 表 达 格 式 简 单 , 向异 性 参 数 易 于 实 验 但 各
摘 要 : 析 了 影 响 板 料 回 弹 精 度 的 数 值 模 拟 因 素 : 服 准 则 、 化 模 式 、 元 技 术 及 有 限 元 数 值 计 算 方 分 屈 硬 单
法 。 研 究 结 果 表 明 各 向 异 性 屈 服 准 则 B d t9 更 接 近 于 材 料 的 实 际 屈 服 行 为 ; 于 具 有 B u c ig r效 应 的 a a8 对 a shn e 材 料 及 复 杂 加 载 问 题 , 用 非 线 性 混 合 强 化 材 料 模 型 预 测 板 料 回 弹 量 的 精 度 最 高 ; 于 实 体 壳 单 元 具 有 实 采 由 体 单 元 和 壳 单 元 的 优 点 , 测 回 弹 模 拟 结 果 精 度 高 。 研 究 还 表 明 , 时 间 允 许 的 条 件 下 , 用 较 小 单 元 尺 寸 预 在 采
不 高 ( 7 %)其 原 因 有 : 形 过 程 模 拟 的 应 力 场 精 ≤ 5 , 成
度 不 高 ; 弹 算 法 本 身 不 够 合 理 。 因 此 , 弹 问 题 一 回 回 直 是 板 料 成 形 数 值 模 拟 的 难 点 。 本 文 重 点 分 析 了屈 服 准 则 、 化 模 式 、 元 技 术 和有 限 元 算 法 对 板 料 成 硬 单 形 回弹 模 拟 精 度 的影 响 。
增 加而增 加 , 是在 r 但 <l时 , 个 屈 服 准 则 预 测 相 同 两
金属板料成形数值模拟的研究现状
金属板料成形数值模拟的研究现状一、引言金属板料成形数值模拟是现代制造业中不可或缺的一环。
通过数值模拟可以预测金属板料在成形过程中的变形、应力分布等物理量,从而优化工艺参数,提高成形质量和效率。
本文将介绍金属板料成形数值模拟的研究现状。
二、数值模拟方法1. 有限元法有限元法是目前最为常用的数值模拟方法之一。
它将连续体划分为多个小单元,在每个小单元内近似求解其物理量,最后通过组合得到整体的物理量分布。
有限元法可以考虑材料非线性、边界条件复杂等因素,适用范围广泛。
2. 边界元法边界元法是另一种常用的数值模拟方法。
它将问题转化为求解边界上的物理量分布,避免了对整个区域进行离散化计算。
边界元法适用于具有对称性或者具有复杂几何形状的问题。
3. 网格无关法网格无关法是相对于传统有限元法而言的新兴方法。
它不需要事先确定网格大小和结构,可以自动适应物理量分布的变化。
网格无关法适用于具有较大变形或者复杂几何形状的问题。
三、数值模拟在金属板料成形中的应用1. 成形过程分析数值模拟可以对金属板料成形过程进行分析,预测变形、应力分布等物理量。
通过优化工艺参数,可以避免一些不必要的缺陷和失效。
2. 模具设计数值模拟可以为模具设计提供依据。
通过对成形过程中应力和变形的预测,可以确定合适的模具结构和尺寸,从而达到更好的成形效果。
3. 材料选择数值模拟还可以为材料选择提供参考。
通过预测不同材料在成形过程中的性能表现,可以选择最为适合的材料,提高生产效率和质量。
四、数值模拟存在的问题及发展趋势1. 计算精度问题目前数值模拟存在计算精度不高、计算时间长等问题。
需要进一步发展更加高效精确的数值模拟方法。
2. 跨尺度建模问题金属板料成形涉及到多个尺度,如宏观尺度、晶体尺度等。
如何将不同尺度的模型相结合,进行跨尺度建模是一个重要的研究方向。
3. 多物理场耦合问题金属板料成形涉及到多种物理场,如力学、热学、电磁学等。
如何将这些物理场相互耦合起来进行计算,是数值模拟发展的重要方向之一。
- 1、下载文档前请自行甄别文档内容的完整性,平台不提供额外的编辑、内容补充、找答案等附加服务。
- 2、"仅部分预览"的文档,不可在线预览部分如存在完整性等问题,可反馈申请退款(可完整预览的文档不适用该条件!)。
- 3、如文档侵犯您的权益,请联系客服反馈,我们会尽快为您处理(人工客服工作时间:9:00-18:30)。
思考
• 如何选择单元方程,有什么影响? • 如何选择积分点,为什么?
材料模型/塑性行为
单向拉伸试验验证的塑性行为
P A Initial uniaxial yield point y 0 y y ai experimental curve
– 缺省参数有其局限性 – 新的应用,需要新的参数 – 可以用来调试,
•
参数选择 单元方程(1)
• 在钣金成形仿真中通常使用的单元方程 – #2单元方程( Belytschko-Tsay) – #16单元方程 (全积分单元方程)
#2 单元 – #2单元在平面内一个积分点 – #16单元在平面内四个积分点
参数选择
• 为什么不用统一的参数? – LSDYNA是通用求解器 • 不同的应用需要不同的参数 – 不当参数影响结果预测 • 取决于用户的结果时常发生 – 对于板料成形,我们已经找到了合适的参数 • 做了非常多的分析实例 • 参数一致性得到长足改进 – 对不同的应用采用适当的参数,有利于分析效率 – 大多数参数,DYNAFORM都设定了合理的值 用户的经验仍然重要
1 . 0 7
1 . 2 8
1 . 4 9
2 . 4 5
2 . 8 0
8 . 8 4
2 0 . 0 1
单元方程
Operation counts (for elastic behavior NT=2 is OK)
OPERATION COUNT COMPARI SONS ONE P OINT I NTEGRATION (V ERSION LS 930)
参数选择 厚度上的积分点(2)
• NIP = 2 – Case I中没有错误; – Case II, III, IV中,导致错误 NIP = 3 – Case I中没有错误; – case II, III中,比较小的偏差; – Case IV中,较大偏差 NIP=5,7 – Case I中没有错误; – Case II, III, and IV中,比较小的偏差.
•
•
单元使用提示
单元算法BT,BWC,BL采用面内单点积分,全积分采用四点积分 所有壳单元厚度方向可以用任意多个积分点 对弹性变形沿厚度方向用两个积分点即可 塑性行为沿厚度方向用3到5个积分点,回弹可以用7个积分点 避免使用小单元,以免缩小时间步长。如果使用,请同时使用质量缩放。 减少使用三角形单元。 避免锐角单元和翘曲单元,否则会降低计算精度。
单元方程
Characteristics of the Belytschko-Tsay SE (default)
基于随动坐标系和速度位移方程. 随动坐标系的单元方程 避免了在单元中嵌入坐标系而导致的非线性 动态的复杂性. 单元动量方程假设节点位于同一个平面. 如果是5个积分点, BT单元需要 725数学计算。但是一点HL单元需要 4066次数学计算. HL单元的选择减缩积分需要35,367次数学计算。 由于计算速度效率非常高, BT单元方程通常是壳单元的单元方程的最 佳选择. 正因为如此, 它已经成为4节点板壳单元的缺省的单元方程。
单元方程
为什么提供这么多单元方程?
全积分单元用于弹塑性,金属成形,气囊以及关心精确度的时候。 三角形单元(C0单元)刚度比较硬,不建议采用。但是在混合网格中采 用,因为C0三角形壳单元,比退化的四边形网格算法好。 膜单元不能受弯曲和断面剪应力,适用于非常薄的板料以及拉张为主 的变形中 。 进化的板壳单元有较高的精确度,但是和BT单元相比稳定性较差 BT单元速度非常快!
单元属性
*SECTION_SHELL $PROPERTY NAME:blankpro $ SID 5 $ T1 ELFORM SHRF NIP 5.0 T4 PROPT 1.0 NLOC QR/IRID 0.0 ICOMP
2 0.833E+00 T2 T3
2.500E+00 2.500E+00 2.500E+00 2.500E+00
•
建议:
– 对成形分析#2单元是比较好的选择
• 节省CPU • 降低内存需求
– 对回弹分析, element #16是更好的选择
• 更加精确的应力分布
•
在关键字中选择单元方程
– – – – *SECTION_SHELL ELFORM=2: Element #2 is selected ELFORM=16: Element #16 is selected (ELFORM is the second parameter under the card of *section_shell)
BT单元简单,速度非常快。
单元方程
.
30
20
P e r f o r m a n c e
10
1 . 2 5
1
0 BT BTW BL BWC Element T ype CHL HL F BT CFHL FHL Fully in t eg rat e d elem ent s
The cost of shell elements vary by formulation
NIP = 3 Real stress
•
•
参数选择 厚度上的积分点(3)
• NIP > 7 – 精确度没有明显提高 – 增加不必要的CPU – 需要更多的内存 • 不推荐 Suggestions: – 重力载荷 (可以认为是纯弹性变形) • NIP = 2 可以增加计算速度 – 成形分析: (Case II and III) • NIP=3,5 – 回弹分析: (Case IV) • NIP=5, 7 注意: 参数NIP 在 *SECTION_SHELL
时间步长
Timestep
临界(或最小)时间步长:
t min
Imin C
• 其中C声音在3D连续介质中传播的速度
C
E1 1 1 2
E = Y oung 抯 modulus
= Poisson抯 ratio
= specif ic mass density
3. 4.
例如:所关心的最小圆弧半径是6mm,成形的最后阶段的最小单元尺寸大约是:
3mm=(6*sin(90/6)*2)如果网格细分等级是3,那么初始单元尺 寸大约12 mm=3*2*2).
工具网格基本参数说明
• • • • 工具网格尺寸大小,不参与时间步长的计算 要能精确地描述模具的几何形状,导角或曲率大的区域 要采用较密的网格; 要能高效地划分模具的型面,如比较平的面可以采用较 稀疏的网格; Surface mesh parameters:
时间步长
声波在不同材料中传播速度例子
空气 水 钢 铝 钛 树脂玻璃 331 m/s 1478 m/s 5240 m/s 5328 m/s 5220 m/s 2598 m/s
声音在两种最常见的金属铁,铝中的传播速度范围是5000.m/s. 在两种材料中,单元特征值是5.mm, 时间步长是1.µs, 通常被设为行业标准。
2. 3.
4. 5. 6.
7.
思考
• 如何选择单元尺寸? • 如何选取时间步长? • 如何检查和修补工具网格?
单元方程
Shell Elements
EQ.1: EQ.2: EQ.3: EQ.4: EQ.5: EQ.6: EQ.7: EQ.8: EQ.9: EQ.10: EQ.11: EQ.12: EQ.13: EQ.14: EQ.15: EQ.16: Hughes-Liu Belytschko-Tsay (default) BCIZ triangular shell C0 triangular shell Belytschko-Tsay membrane S/R Hughes Liu S/R co-rotational Hughes Liu Belytschko-Leviathan fully integrated membrane Belytschko-Wong-Chiang Fast Hughes-Liu Plane stress 2D element (x-y plane) Plane strain 2D element (x-y plane) Axisymmetric Petrov-Galerkin 2D solid Axisymmetric Galerkin 2D solid fully integrated (BWC)
– – – – Max. size: 单元最大尺寸 Min. size: 单元最小尺寸 Chordal: 弦高 Angle: 相邻单元边的夹角
<20o
<0.15mm
工具网格质量基本要求
• 模具单元
– 不能有重叠单元、崩溃的单元。
1 (4) 4 3(2) 1(5) 2(6) 2 (3)
4 1
3 2 5 6
Overlapping
1
4 3 8
2
7 4(8)
1(2)
3(7)
工具网格的检查内容
工具网格检查内容: 1. Boundary Display 通过边界的显示,可以看出模具网格是否有缺失、错误, 提供修补的依据 Auto Plate Normal 自动的使单元发向一致(在单元修补完,一定要使用一次) Overlap Element 检查出重叠的单元,只检查完全重叠的单元(一个单元的节 点和另外一个单元的节点完全重叠),如果单元的叠加, 边界显示可以方便的检查出来 Coincide Node:检查重合节点,并判断是否合并。 Interior Angle 考虑:删除掉内角小于1度的单元 Element Size 考虑:删除掉单元尺寸过小的单元,比如单元尺寸0.1mm. 检查的同时,退化的单元也得到修正 Die Lock 考虑:删除或修改掉负角单元,同时思考负角单元出现 的原因