流化床反应器单元
化学反应工程第八章流化床反应器
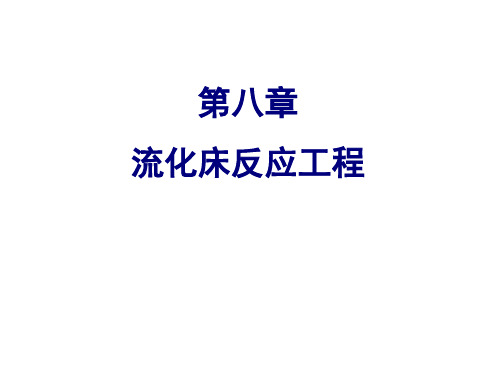
2. 聚式流态化与散式流态化 使用不同的流体介质,固体流态化可分为:
散式流态化(particulate fluidization) 聚式流态化(aggregative fluidization)
2. 聚式流态化与散式流态化
理想流态化是固体颗粒之间的距离随着流体流速增加而 均匀地增加,颗粒均匀地悬浮在流体中,所有的流体都 流经同样厚度的颗粒床层,保证了全床中的传质、传热 和固体的停留时间都均匀,对化学反应和物理操作都十 分有利。理想流态化的流化质量(fluidization quality) 是最高的。 在实际的流化床中,会出现颗粒及流体在床层中的非均 匀分布,越不均匀,流化质量越差。 液体作流化介质时,液体与颗粒间的密度差较小,在很 大的液速操作范围内,颗粒都会较均匀地分布在床层中, 比较接近理想流态化,称为散式流态化。
(2) 聚式流态化
由于气泡在床层径向截面上不均匀分布,诱发了床内密 相的局部以致整体的循环流动,气体的返混加剧。这种 流型称为 鼓泡流态化 (bubbling fluidization),气-固接 触效率和流化质量比散式流态化低得多。 气泡上升到床层表面时的破裂将部分颗粒弹出床面。在 密相床上面形成一个含有少量颗粒的自由空域 (freeboard)。 一部分在自由空域内的颗粒在重力作用下返回密相床, 而另一部分较细小的颗粒就被气流带走,只有通过旋风 分离器的作用才能被捕集下来,经过料腿而返回密相床 内。
快 床 颗 粒 的 径 向 分 布
颗粒含率 高 度 实际分布 模型分布
气流输送 快床 湍流床 鼓泡流化床 0.2 0.4 0.6 密度
图:各种状态 流化床沿床高密度变化
2. 高气速气-固流态化中的流型
流化床反应器的结构

流化床反应器是一种利用气体或液体通过颗粒状固体层而使固体颗粒处于悬浮运动状态,并进行气固相反应过程或液固相反应过程的反应器。
在用于气固系统时,又称沸腾床反应器。
Fluidized bed reactor is a kind of reactors that make use of gas or liquid through granular solid layer to make the solid particles in a state of suspension movement, and conduct reaction process of gas-solid or liquid-solid reactor process.When fluidized bed reactor is used in gas-solid system, it also called ebullient bed reactor.流化床反应器的结构有两种形式:①有固体物料连续进料和出料装置,用于固相加工过程或催化剂迅速失活的流体相加工过程。
②无固体物料连续进料和出料装置,用于固体颗粒性状在相当长时间内,不发生明显变化的反应过程。
The structure of the fluidized bed reactor has two forms:(1)It contains a continuous feeding and discharging device with solid materials which is used in solid phase processing procedure or fluid phase processing procedure where catalyst deactivates quickly.(2)It doesn't contain a continuous feeding and discharging device with solid materials which is used in the reaction process that the properties of solid particles have no obvious changes in a long time.流化床反应器的结构型式很多,但一般均由床层壳体、内部装置、换热装置、气固分离装置等组成。
流化床单元操作手册

文档编号:TSS_FLUID.DOC流化床反应器单元仿真培训系统操作说明书北京东方仿真软件技术有限公司二〇〇六年十月目录一、工艺流程说明 (3)1、工艺说明 (3)2、反应机理 (3)3、设备一览 (4)4、参数说明 (4)二、装置的操作规程 (4)1、冷态开车规程 (4)2、正常操作规程 (6)3、停车操作规程 (6)4、仪表一览表 (8)三、事故设置一览表 (9)四、仿真界面 (10)附:思考题 (12)一、工艺流程说明1、工艺说明该流化床反应器取材于HIMONT工艺本体聚合装置,用于生产高抗冲击共聚物。
具有剩余活性的干均聚物(聚丙烯),在压差作用下自闪蒸罐D-301流到该气相共聚反应器R-401。
在气体分析仪的控制下,氢气被加到乙烯进料管道中,以改进聚合物的本征粘度,满足加工需要。
聚合物从顶部进入流化床反应器,落在流化床的床层上。
流化气体(反应单体)通过一个特殊设计的栅板进入反应器。
由反应器底部出口管路上的控制阀来维持聚合物的料位。
聚合物料位决定了停留时间,从而决定了聚合反应的程度,为了避免过度聚合的鳞片状产物堆积在反应器壁上,反应器内配置一转速较慢的刮刀,以使反应器壁保持干净。
栅板下部夹带的聚合物细末,用一台小型旋风分离器S401除去,并送到下游的袋式过滤器中。
所有末反应的单体循环返回到流化压缩机的吸入口。
来自乙烯汽提塔顶部的回收气相与气相反应器出口的循环单体汇合,而补充的氢气,乙烯和丙烯加入到压缩机排出口。
循环气体用工业色谱仪进行分析,调节氢气和丙烯的补充量。
然后调节补充的丙烯进料量以保证反应器的进料气体满足工艺要求的组成。
用脱盐水作为冷却介质,用一台立式列管式换热器将聚合反应热撤出。
该热交换器位于循环气体压缩机之前。
共聚物的反应压力约为1.4Mpa(表),70℃,注意,该系统压力位于闪蒸罐压力和袋式过滤器压力之间,从而在整个聚合物管路中形成一定压力梯度,以避免容器间物料的返混并使聚合物向前流动。
乙烯氧氯化流化床反应器及典型工艺技术

3.3.3乙烯氧氯化流化床反应器及典型工艺技术
下面我们来认识一下完成氧氯化反应的流化床反应器
反应器的选择由反应类型和反应的特点来确定。
乙烯氧氯化反应器有流化床反应器和固定床反应器。
两者也可以同时使用。
乙烯氧氯化最主要设备也是使用最多是内置旋风分离器的流化床反应器。
流化床反应器的主要结构由三部分组成:下面让我们看看流化床反应器的工作过程。
认识流化床反应器需要注意以下几个要点:
在冷却管内通入循环沸水,以水的汽化形式移走反应热,同时副产蒸汽。
反应器的顶部四组三级旋风分离器,用以收集反应气体中夹带的催化剂。
反应器顶部物料送往急冷塔,作用是除去少量HCl(水吸收),同时冷却物料。
塔底物料经分离器除水,调PH值后送下一工序。
塔顶急冷后的冷凝气体通过洗涤塔碱洗,去除气体中的CO2。
氧氯化反应比较典型的工艺技术有EVC、三井东压及赫斯特技术。
EVC技术用的是固定床反应器。
其缺点是十分明显的∶反应工艺过于复杂,设备投资大,催化剂容易因出现热点而失活,导致反应超温而使副反应增多,系统阻力较大。
流化床反应器的操作弹性大,床层内反应温度趋于均一,设备投资少,工艺流程简单。
采用流化床反应器氧氯化反应又分为:
空气法、贫氧法、富氧法三种。
空气法反应尾气排放量大,乙烯消耗较高;贫氧法和富氧法用循环气体操作,尾气排放量低,贫氧法循环气中含氧一般约为1.5%,单元安全性好。
流化床反应器(1)

1 气固流化床设计基础数据流化床反应器的操作工艺参数为:反应温度为400 ℃,反应压力为 0.3 MPa (绝压),甲醇操作空速为 1~51h -。
MTO 成型催化剂粒径范围为50~140μm ,平均粒径为 80μm 。
颗粒密度为 1200 kg/m3,堆密度为 700 kg/m3。
甲醇在400℃下的粘度根据常压下气体粘度共线图查得为 0.021m Pa.s ,甲醇 400℃下的密度根据理想气体状态方程估算为 1.715kg/m3。
甲醇原料中水含量为 1%。
流化床催化反应器主要包括以下几个组成部分:反应器壳体尺寸、气体分布装置、换热装置、气固分离装置、内部构件、以及催化剂颗粒的加入和卸出装置。
MTO 反应为放热反应,工业装置中为避免反应器床层温度过高,需设置内取热或外取热器,由于小型固定流化床反应器尺度较小,散热效应较大,应考虑在反应器外设置加热炉保持 MTO 反应温度恒定,不必设置取热器。
我们在确定了操作条件(T :400 ℃,P :0.3 MPa )、反应器内气体原料和固体催化剂物化性质的条件下,计算了催化剂装填量、操作气速和反应器主体尺寸,并对气体分布器、气固分离装置和催化剂加卸料口的设置进行了简要介绍。
2 操作气速2.1 最小流化速度计算当流体流过颗粒床层的阻力等于床层颗粒重量时,床层中的颗粒开始流动起来,此时流体的流速称为起始流化速度,记作mf U 。
起始流化速度仅与流体和颗粒的物性有关,其计算公式如下式所示: 对于p mf ep d U R ρμ=20<的小颗粒2()1650p p mf d gU ρρμ-= (1) 对于1000p mf ep d U R ρμ=>的大颗粒1/2()[]24.5p p mf d gU ρρρ-= (2)式中: p d 为颗粒的平均粒径;.p ρρ分别为颗粒和气体的密度; μ为气体的粘度。
本流化床雷诺数:ep R <20将已知数据代入公式(1),25235()(810)(1200 1.715) 2.210/16501650(2.110)p p mf d gU m s ρρμ----⨯⨯-===⨯⨯⨯558100.0022 1.715202.110p mf ep d U R ρμ--⨯⨯⨯==<⨯ 将mf U 代入弗鲁德准数公式 2mf mf p U F d g =作为判断流化形式的依据。
流化床反应器PPT课件

3.1 流化床内的构件
在流化床内设置若干层水平挡板、挡网或 垂直管束,便构成了内部构件。其作用是抑制 气泡成长并且粉碎大气泡,改善气体在床层中 的停留时间分布,减少气体返混合和强化两相 间的结构。
常见的内部构件可分为三类: 横向(水平)构件
纵向(垂直)构件
横向+纵向构件
3.1流化床内的构件
LOREM IPSUM DOLOR
2.1 工业合成甲基氯硅烷的研究 直接合成法反应:
对于综合性生产车间来说,直接法是必不可少的,但还需 辅以其他方法,方能满足生产需要和降低生产成本的要求。
2.2 直接法合成有机硅单体的原理
2.2 直接法合成有机硅单体的原理
反应过程中还可能发生热分解、歧化以及氯硅烷水 解(原料带进的水分)等副反应,致使反应产物变得更 为复杂,甲基氯硅烷产物组分可多达41个。
目前,大多数商用计算流体力学软件如 FLUENT软件都采用有限元法。
4.1 数值计算中的参数影响
在实际计算中,影响的参数因素可以分为以下三方面: (一) 网格的影响 (二) 边界条件的影响
(三) 时间步长的确定
网格是数值计算中求解控制方程的基本单元, 网格的形状及划分数量将直接影响模拟结果的准 确度。它可以分为两大类:结构化网格和非结构 化网格。
目录
02 工艺流程的介绍 05
1.1有机硅在国内外的进展程度
(1)有机硅生产的特点
有机硅单体及中间体生产集中于发达国家,并且生产规模不断扩 大。 有机硅单体生产的原理并不复杂,但是生产工艺复杂、流程长、 技术含量高,长期以来,只有美国、日本、法国、德国等少数发达 国家有这一生产技术,并在行业内形成技术垄断,所以世界上从事 有机硅单体工业生产的厂家并不多。
反应器仿真操作实例

模仿为标志为手段。通过艺术特殊的美感作用,可以使儿童 加深对音乐形象的理解,,以舞蹈提高儿童对自然事物的艺 术表现能力。律动教学是幼儿园对儿童进行节奏训练的一门 主课,不仅给儿童以艺术美的享受,而且作为一种教育手段 也能培养儿童良好的生活习惯,陶冶他们的心灵和情操。 • 律动的内容可以是单一动作的模仿,也可以是几个动作的 组合;还可以让儿童在音乐伴随下,全身心地投入活动气氛中 ,按自己的想象,根据音乐的特点,编出各种动作。在这种 欢乐的气氛中,可以很好地发展儿童的想象力和创造力。幼 儿园的律动活动,是为了配合唱歌、音乐游戏和舞蹈学习而 选择的;
上一页 返回
任务2 流化床反应器单元仿真培训系统
• 一、工艺流程说明
• 1.工艺说明 • 该流化床反应器取材于Him。工艺本体聚合装置,用于生产高抗冲击
共聚物。具有剩余活性的干均聚物(聚丙烯),在压差作用下自闪蒸罐 D - 301流到该气相其聚厅府器R一401. • 聚合物从顶部进入流化床反应器,落在流化床的床层上。流化气体 (反应单体)通过一个特殊设计的栅板进入反应器。由反应器底部出口 管路上的控制阀来维持聚合物的料位。聚合物料位决定了停留时间, 从而决定了聚合反应的程度,为了避免过度聚合的鳞片状产物堆积在 反应器壁上,反应器内配置一转速较慢的刮刀,以使反应器壁保持干 净。
上一页 下一页 返回
任务1固定床反应器单元仿真培训系统
• 四、仿真界面
• 仿真界面如图7一1、图7一2所示。
• 五、思考题
• 1.结合本单元说明比例控制的工作原理。 • 2.为什么是根据乙炔的进料量调节配氢气的量,而不是根据氢气的量
调节乙炔的进料量? • 3.根据本单元实际情况,说明反应器冷却剂的自循环原理。 • 4.观察在EH一429冷却器的冷却水中断后会造成的影响。 • 5.结合本单元实际,理解“连锁”和“连锁复位”的概念。
7.1流化床反应器

µ
5.3 × 10 −3 × 0.733 × 10 −3 × 0.058 = = 6.09 × 10 − 4 < 20 3.7 × 10 − 4
(3)计算ut: )计算
• 如果全床空隙率均匀,处于压力最低处的床顶 如果全床空隙率均匀, 粒子将首先被带出,故取最小粒子 粒子将首先被带出,故取最小粒子dp=10µm计 µ 计 算。设Re<0.4
再 生
石油 催化 空气 剂输 消除内扩散;固定床因有△ 限制不能用 消除内扩散;固定床因有△P限制不能用 送
3. 强放热反应 氧化反应:萘氧化剂制苯酐需熔盐冷却; 氧化反应:萘氧化剂制苯酐需熔盐冷却; 丙烯氨氧化法制丙烯腈
流化床反应器的优点:( 流态化技术) 流化床反应器的优点:( 流态化技术)
• 传热效能高,且床内温度易于维持均匀; 传热效能高,且床内温度易于维持均匀; • 大量固体粒子可方便地往来输送; 大量固体粒子可方便地往来输送; • 由于粒子细,可消除内扩散阻力,充分发挥催 由于粒子细,可消除内扩散阻力, 化剂的效能。 化剂的效能。 缺点: 缺点: 1. CSTR:转化率甚至小于CSTR(气泡短路) :转化率甚至小于 (气泡短路) 2. 颗粒磨损:催化剂要贱,设备要被磨 颗粒磨损:催化剂要贱, 3. 气流出口分离粉尘,回收系统麻烦 气流出口分离粉尘, 4. 副反应:∵RTD太宽 副反应: 太宽
压力波动 达极大值 聚式 压力波动 趋于0 快床 Uc 相变 泡分散相 湍床 Cluster 分散相 Ut 夹带
散式
0
Umf
Ub 鼓泡床
快 床 颗 粒 的 径 向 分 布
颗粒含率 实际分布 模型分布 高 度
气流输送 快床 湍流床 鼓泡流化床 0.2 0.4 0.6 密度
- 1、下载文档前请自行甄别文档内容的完整性,平台不提供额外的编辑、内容补充、找答案等附加服务。
- 2、"仅部分预览"的文档,不可在线预览部分如存在完整性等问题,可反馈申请退款(可完整预览的文档不适用该条件!)。
- 3、如文档侵犯您的权益,请联系客服反馈,我们会尽快为您处理(人工客服工作时间:9:00-18:30)。
一、流化床反应器的工业背景 二、流化床反应器的工作原理
1、流化床反应器的工作原理 2、流化床反应器的原理动画
三、流化床反应器的结构及流化现象 四、流化床反应器的工艺仿真说明
1、流化床反应器的DCS图 2、流化床反应器的现场图
流化床反应器的工业背景
• 固体流化技术是近若干年来化工技术发展中的一项重要成就。由于流化 床具有很高的传热效率,温度分布均匀、气固相之间有很大的接触面积, 因而大大强化了操作,简化了流程,为石油、化工、冶金等部门的气固 非均相加工过程开辟了崭新的途径。 由于流化床层内流体和固体剧烈搅动混合,使床层温度分布均匀,避免 局部过热,(或局部反应不完全)。流化床单位体积内气固相之间接触 面积大,提高界面的传热、传质速率。由于床层的流动性,颗粒容易连 续加入或取出,可使反应过程及再生过程连续化。流化床与沉浸在床层 中构件之间的传热速率较高,因此,流化床中换热器所需面积 较小。设 备生产强度大,宜于大规模操作。 由于流化床反应器存在上述优点,流化床反应器比较适用于下速过程: 热效应很大的放热或吸热过程;要求有均一的催化剂温度和需要精确控 制温度的反应;催化剂寿命比较短,操作较短时间就需要更换(或活化) 的反应;有爆炸危险的反应,某些能够比较安全地在高浓度下操作的氧 化反应,可以提高生产能力,减少分离和精致的负担。
返回
流化床反应器的原理动画
返回
流化床反应器的结构及流化现象
• 流化床
• • • • • • • • • • 1、流化床在不同气速下的状态-固定床 2、流化床在不同气速下的状态-流化床 3、流化床在不同气速下的状态-流体输送 4、局部沟流 5、贯穿沟流 6、气固系统流化床的大气泡和腾涌 7、机械搅动流化床 1、气提式生物流化床反应器 2、流化床反应器 3、流化床反应器2
•
• • • • • • •
返回
流化床反应器的DCS图
返回
流化床反应器的现场图
返回
• 流化床反应器的实物图片
返回
流化床在不同气速下的状态-固定床
返回
流化床在不同气速下的状态-流化床
返回
流化床在不同气速下的状态-流体输送
返回
局部沟流
返回
贯穿沟流
返回
气固系统流化床的大气泡和腾涌
返回
机械搅动流化床
返回
气提式生物流化床反应器
返回流化床反Biblioteka 器返回流化床反应器
返回
流化床反应器的工艺流程说明
•
•
返回
流化床反应器的工作原理
• 流化床反应器是将流态化技术应用于流(通常指气体)、固相化学反应 的设备,有气-固相流化床催化反应器和气-固相流化床非催化反应器两种 以一定的流动速度使固体催化剂颗粒呈悬浮湍动,并在催化剂作用下进 行化学反应的设备称为气-固相流化床催化反应器(常简称为流化床), 它是气-固相催化反应常用的一种反应器。而在气-固相流化床非催化反应 器中,是原料气直接与悬浮湍动的固体原料发生化学反映。
• • 该流化床反应器取材于HIMONT工艺本体聚合装置,用于生产高抗冲击共聚物。具 有剩余活性的干均聚物(聚丙烯),在压差作用下自闪蒸罐D-301流到该气相共聚 反应器R-401。 在气体分析仪的控制下,氢气被加到乙烯进料管道中,以改进聚合物的本征粘度, 满足加工需要。 聚合物从顶部进入流化床反应器,落在流化床的床层上。流化气体(反应单体) 通过一个特殊设计的栅板进入反应器。由反应器底部出口管路上的控制阀来维持 聚合物的料位。聚合物料位决定了停留时间,从而决定了聚合反应的程度,为了 避免过度聚合的鳞片状产物堆积在反应器壁上,反应器内配置一转速较慢的刮刀, 以使反应器壁保持干净。 栅板下部夹带的聚合物细末,用一台小型旋风分离器S401除去,并送到下游的袋 式过滤器中。 所有末反应的单体循环返回到流化压缩机的吸入口。 来自乙烯汽提塔顶部的回收气相与气相反应器出口的循环单体汇合,而补充的氢 气,乙烯和丙烯加入到压缩机排出口。 循环气体用工业色谱仪进行分析,调节氢气和丙烯的补充量。 然后调节补充的丙烯进料量以保证反应器的进料气体满足工艺要求的组成。 用脱盐水作为冷却介质,用一台立式列管式换热器将聚合反应热撤出。该热交换 器位于循环气体压缩机之前。 共聚物的反应压力约为1.4Mpa(表),70℃,注意,该系统压力位于闪蒸罐压力和 袋式过滤器压力之间,从而在整个聚合物管路中形成一定压力梯度,以避免容器 间物料的返混并使聚合物向前流动。